
Archives: Gmedia Albums


Turbopump 3D CAD
3D CAD model images of the A4/V2 rocket engine’s steam turbine powered propellent pumps – all images by Ray Matter. To see Ray Matter’s blog 3D CAD modelling the V2 rocket turbopump introducing these images, just click the link.

Sectioned general assembly view of the V2 turbo-pump (TP) dated September 1942. This image has been edited to show TP and document data closer together than the original.
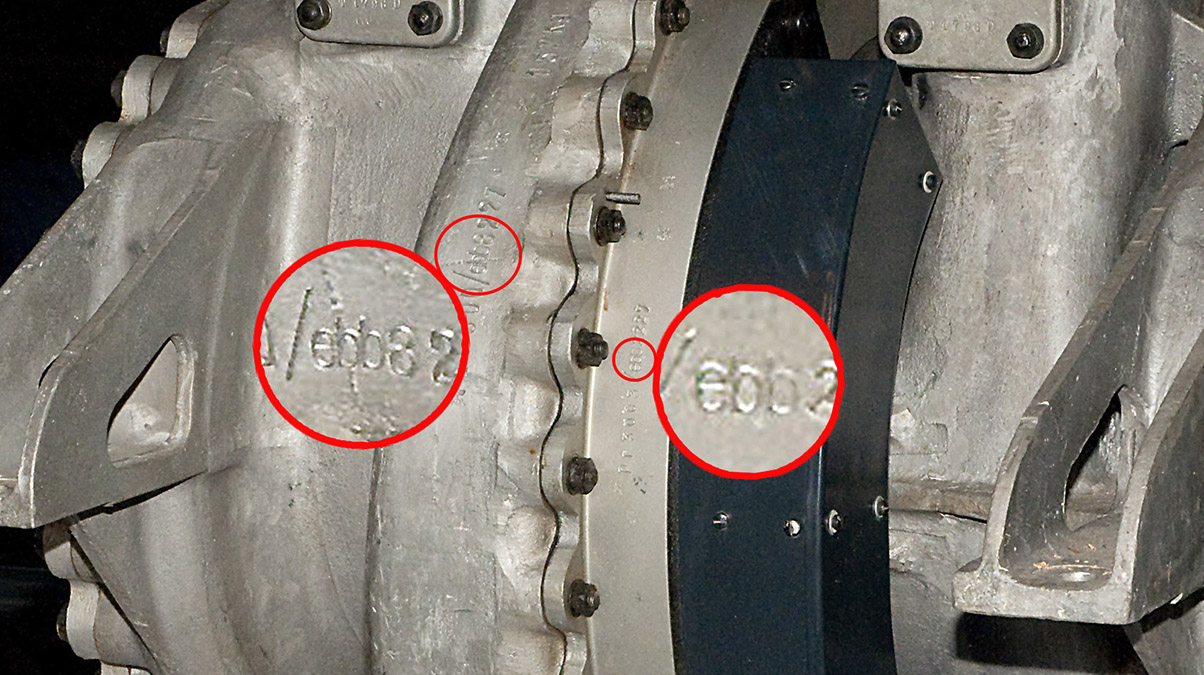
A complete V2 rocket turbo-pump on public display in the USA at the Smithsonian National Air and Space Museum in Washington DC showing Klein Schanzlin & Becker’s wartime contractor armament code – ebb. Smithsonian National Air and Space Museum exhibit.
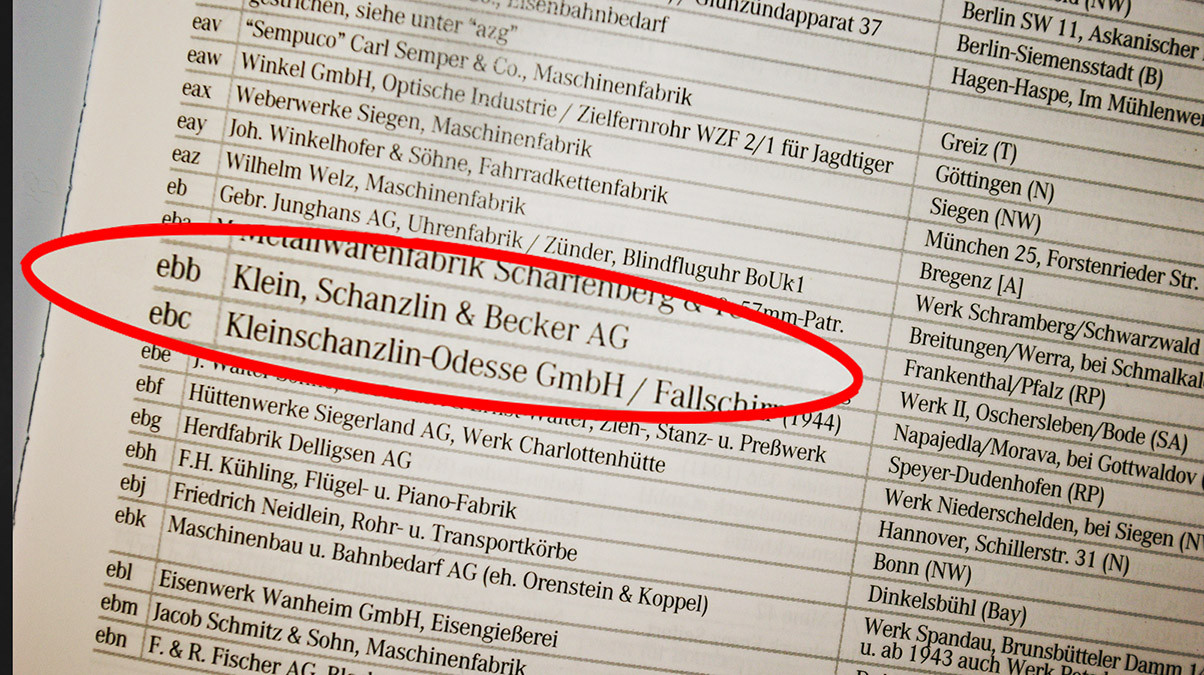
Page from the book, German Secret Armament Codes until 1945 by Michael Heidle (Visier Edition 2016) showing Klein Schanzlin & Becker’s wartime contractor armament code – ebb and Klein Schanzlin Odesse as ebc. ISBN: 978-3-944196-18-3
Album | Turbopump parts and relics |
Category | Turbo-pump |
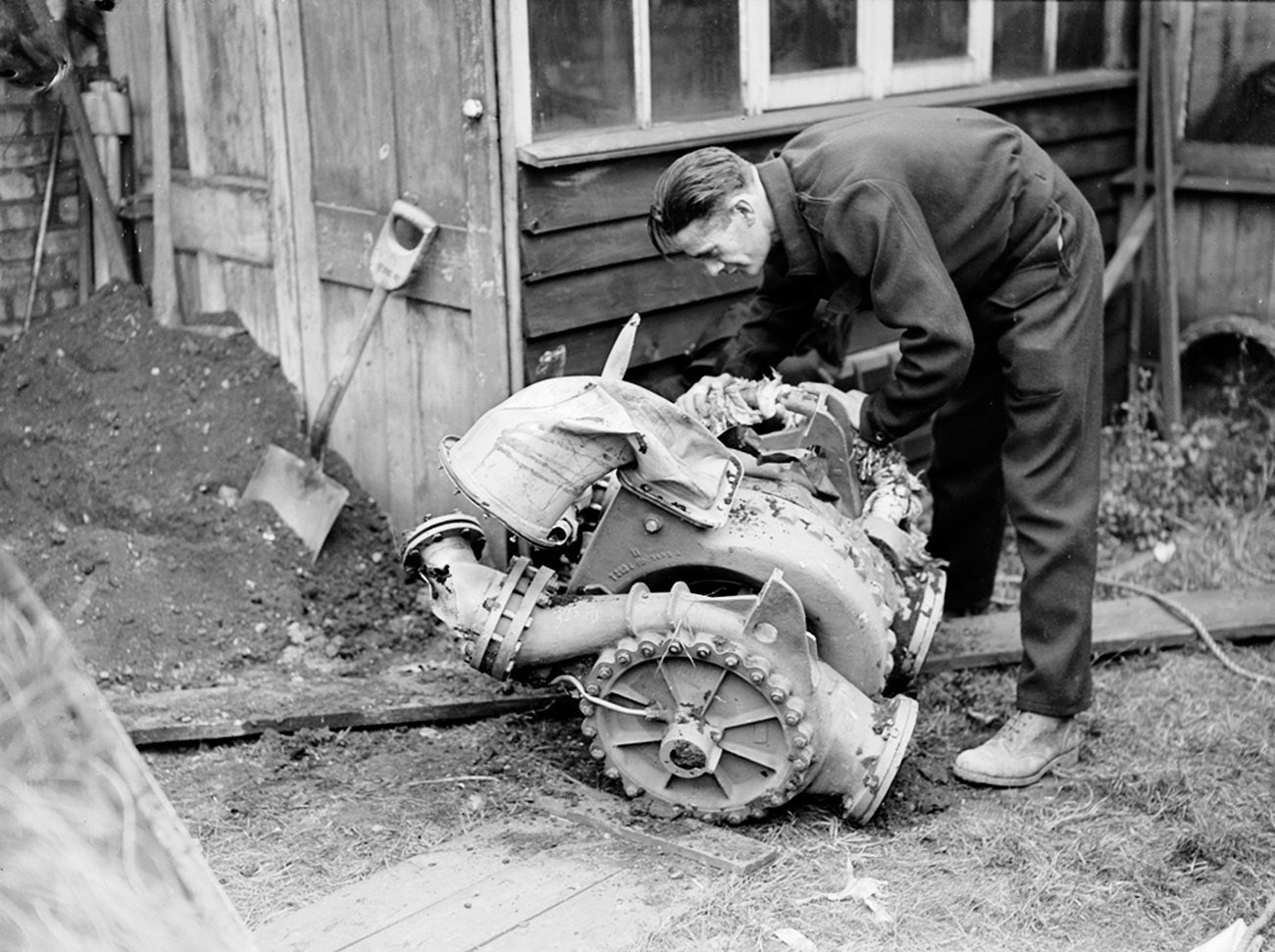
V2 rocket turbo-pump from a missile fired from Walcheren, Serooskerke, Vrederust, by battery no 444, at around 7am on September 17th 1944. The missile impacted East Ham with a direct hit on houses. Killing 6 people with 15 seriously injured. Much of the rocket debris was taken to the East Ham police station for examination by the military authorities. The serviceman in the picture is feeling the steam inlet manifold as it is still warm to the touch. Information porovided by www.v2rocket.com.
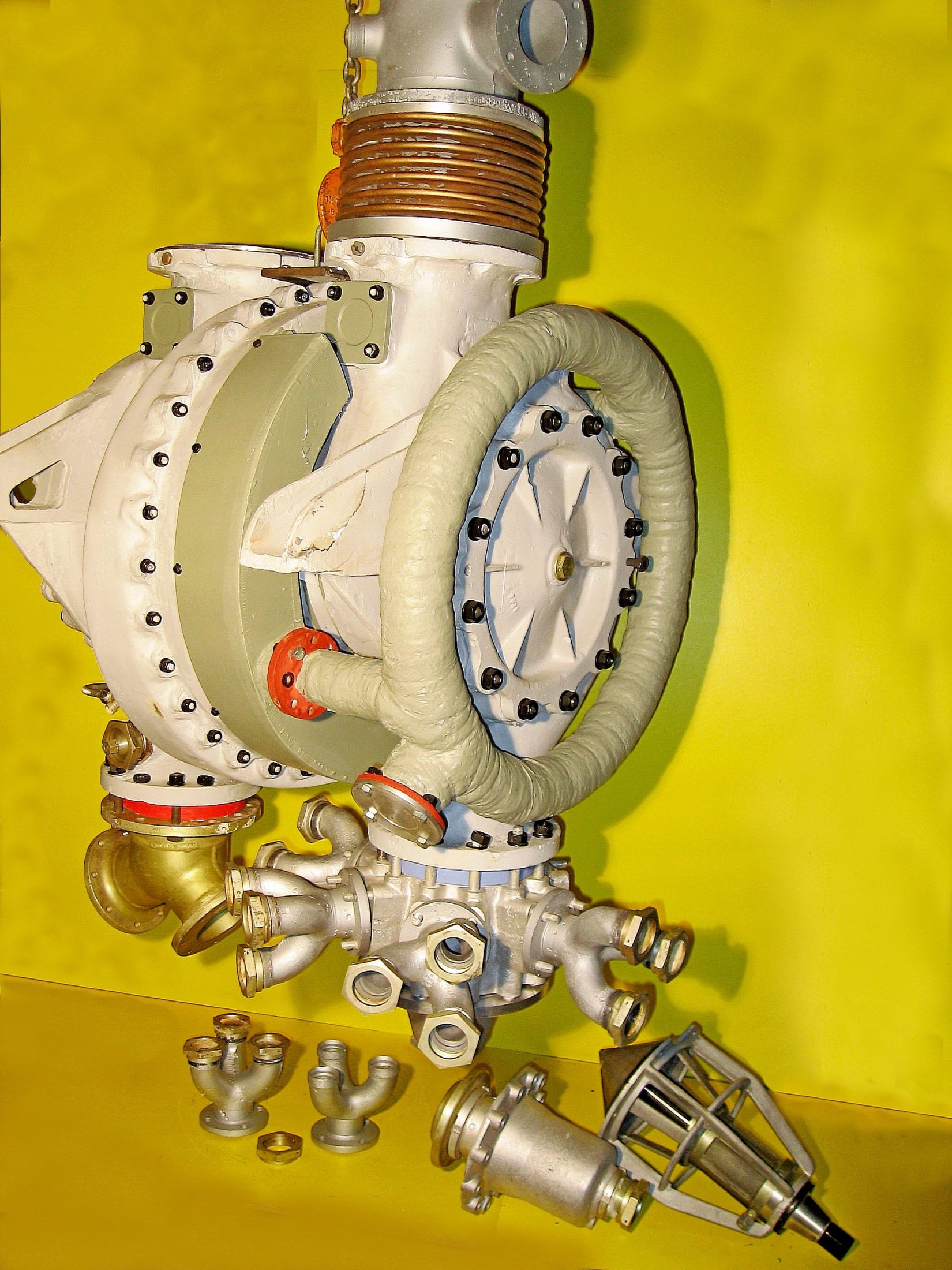
A4-V2 turbo-pump (TP) assembled from original unflown and refurbished flown parts by Horst Beck. Although this rebuilt TP is an accretion of parts from various origins and eras (from 1943 to 1945) the main cast parts of the TP, the turbine housing, and pump cases, were manufactured no earlier than December 1944.
The TP is orientated so that the LOX pump is to the right and the lagged steam inlet and distribution manifold is well shown, running around the circumference of the LOX pump face plate.
The manifold flange, that connects to the output of the steam generation plant, is shown capped off. One of the two TP steam inlet points can be seen above and to the left of this flange. The other inlet pipe can just be seen 180 degrees away on the other side of the manifold.
It is worth noting that he TP presented here is marked ebb (ebb = KSB) in various locations, if any demonstration was needed that KSB was still a primary supply contractor for this critical component in December 1944. See next image in this sequence for an explanation of the blue and red spacers that can be seen where the TP outlet flanges connect to the fuel and liquid oxygen (LOX) outlet splitters. Image courtesy Horst Beck Collection
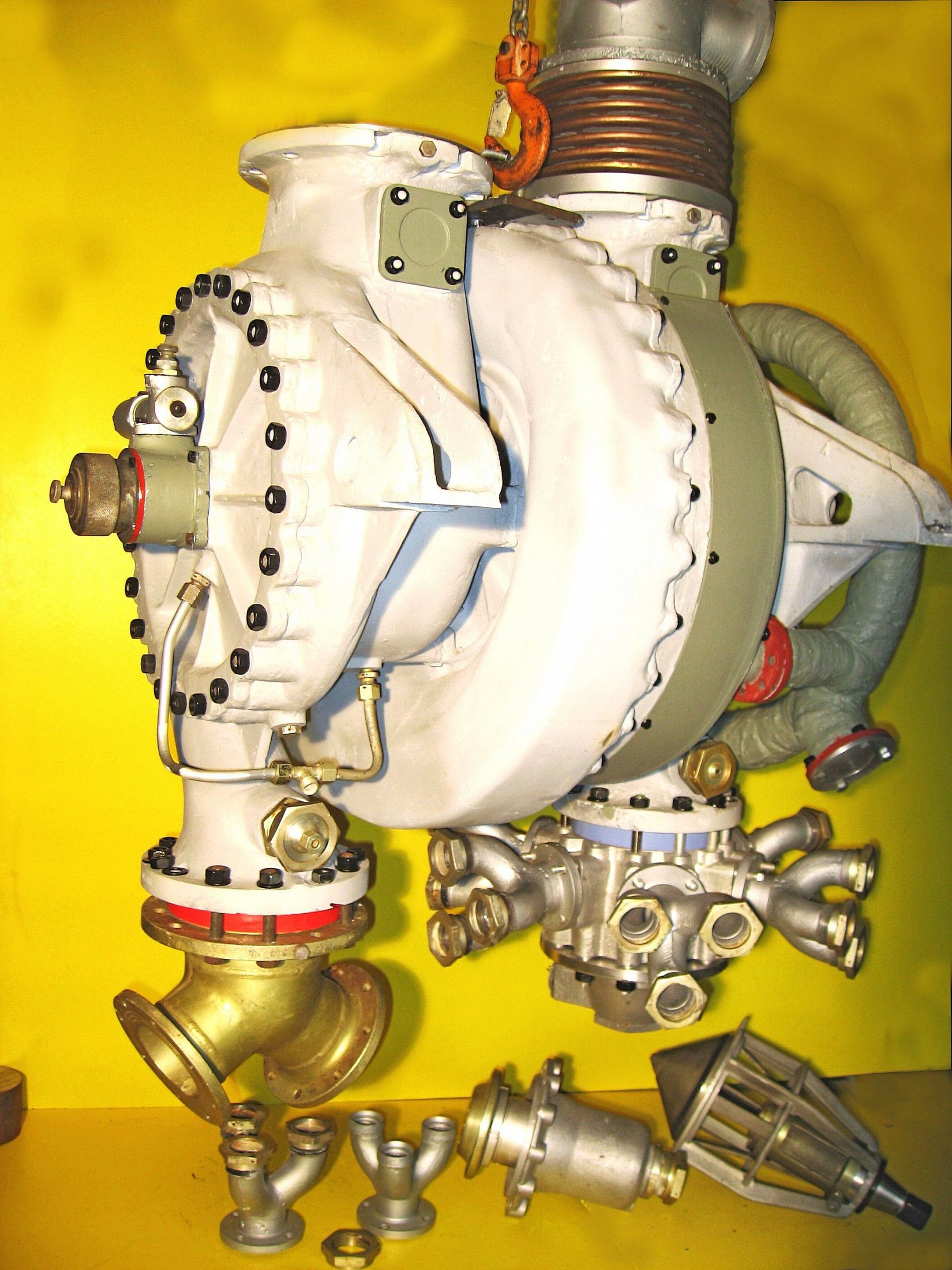
A4-V2 turbo-pump (TP) assembled from original and refurbished parts by Horst Beck. See previous image in this album for more details of TP.
The pale blue spacer that can be seen inserted between the lower LOX outlet flange (on the right of the TP) and the red spacer located in a similar position on the fuel outlet side (left) are critical adaptions to standardise the propellant flow on the basis of test runs performed on each TP. The red and blue spacers are chokes (essentially large washers) that were sized according to the needs of each individual pump. One or sometimes both spacer/washers would have a reduced holes to choke the flow volume to the correct rating relative to the other pump and the overall specifications.
The small pipe network, shown linking the underside of the fuel inlet case, with the bottom of the fuel pump (FP) case and the bearing area of the FP face plate, was used to allow a small continuous flow of propellant pass to the bearings as lubricant – the surplus was dumped overboard via the unconnected union in the middle of the pipework (and nearest viewer). A similar propellant lubrication system was used on the LOX pump – critically LOX can not be allowed to come into contact with conventional organic lubricants as there is a risk of an explosion. So using the material being pumped as the bearing lubricant is a good solution to this problem. Image courtesy Horst Beck Collection
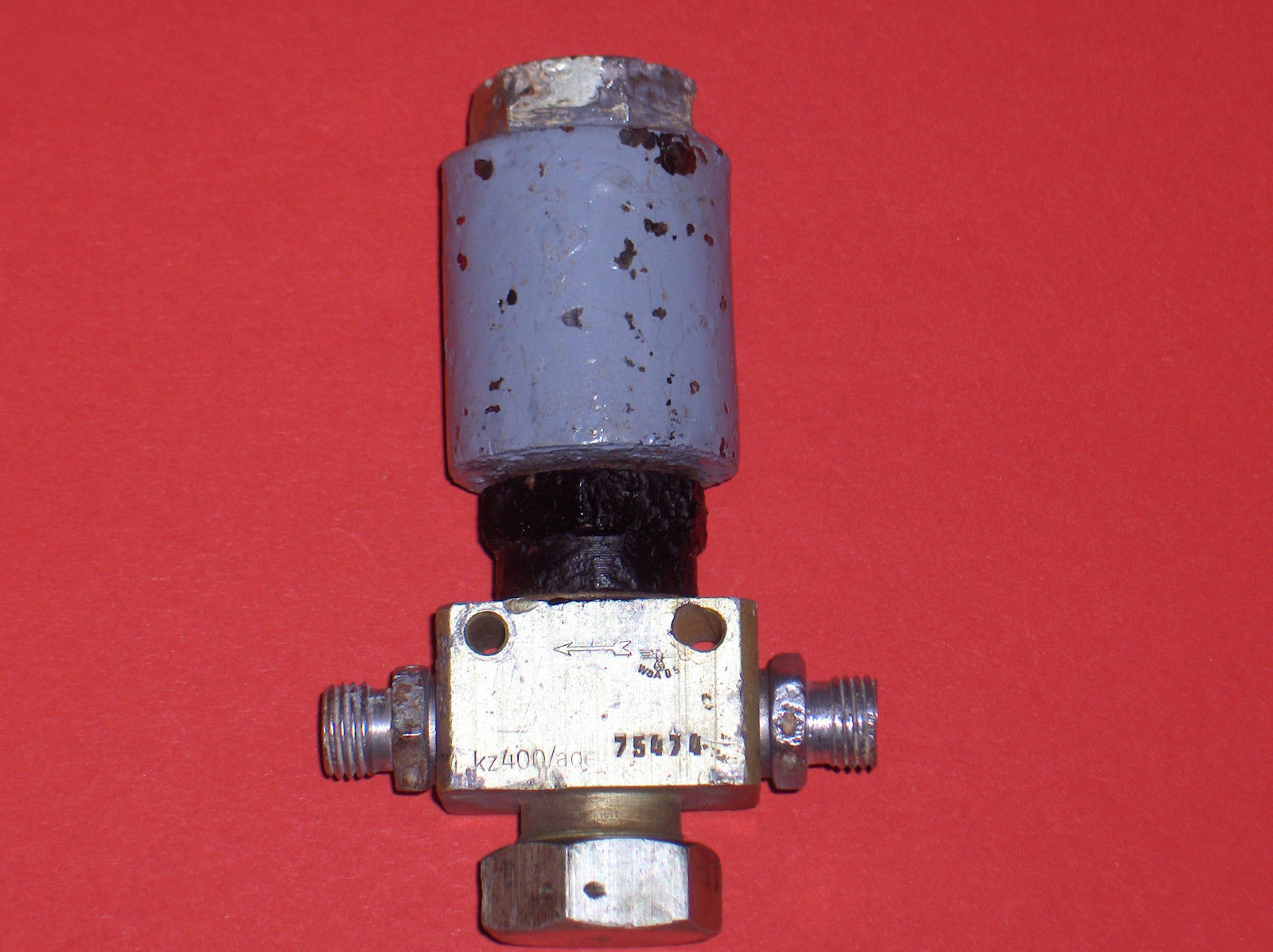
Solenoid electro-magnetic air valve. The This valve type is used numerous times to control equipment in the V2 missile. Variations of this electrically activated valve can be used to control high pressure air or fluids.
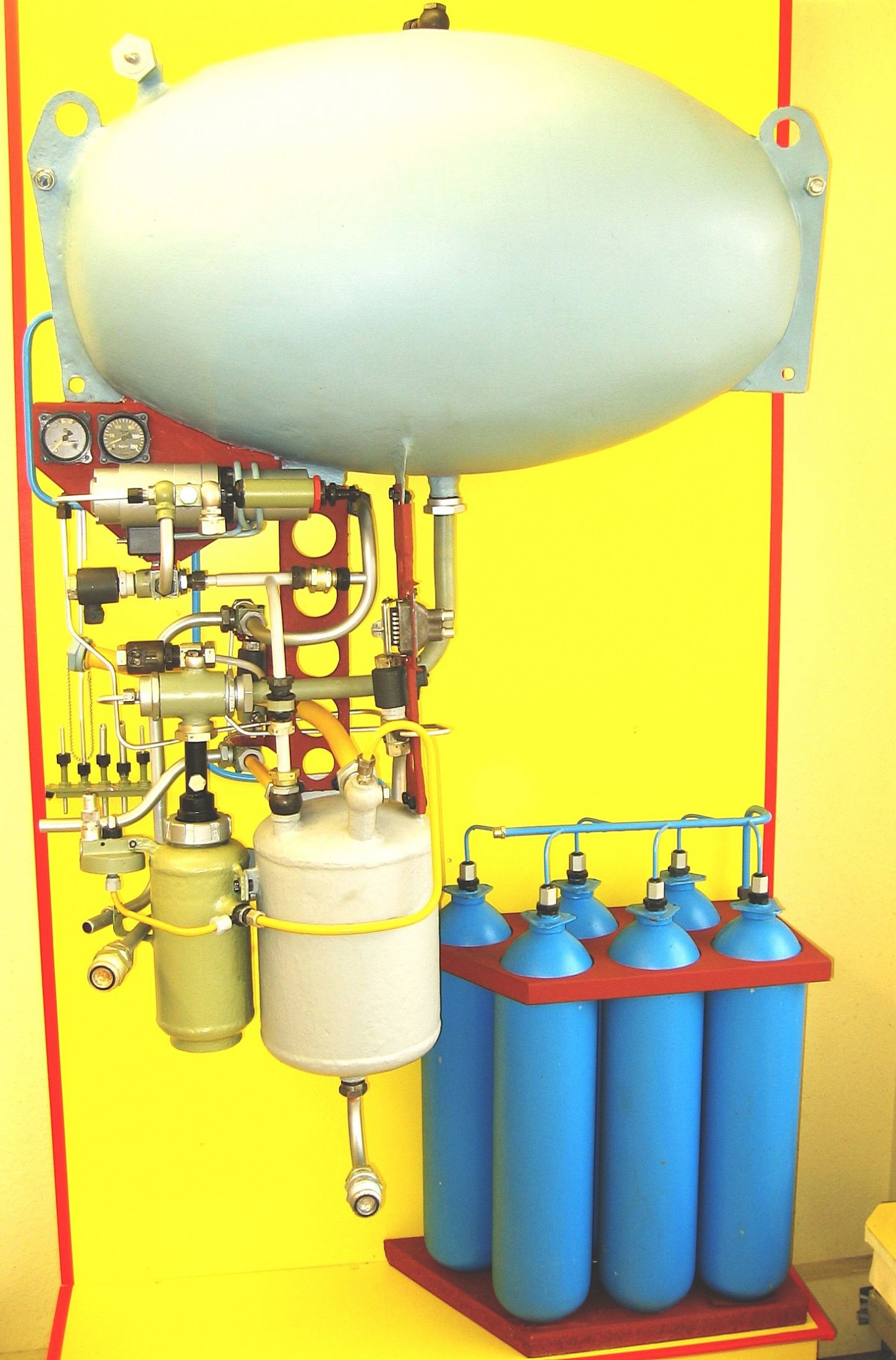
This photo shows an excellent presentation of the gas (steam) generation plant assembled from carefully refurbished flown and unflown V2 missile parts by Horst Beck.
The display shows the large elliptical H2O2 (80% test strength hydrogen peroxide) tank at the top of the assembly and the smaller sodium permangenate reservoir below. The smaller cylinder to the left of the sodium permanganate tank is the steam generation chamber sometimes referred to as ‘the disintegrator’. The rack of blue painted cylinders, that look and function just like ‘scuba’ tanks, are part of the V2’s on-board nitrogen gas (air) reservoir employed to power the missile’s various pneumatic control valves. A second nitrogen reservoir was held in the equipment bay near the top of the missile. Image courtesy Horst Beck Collection
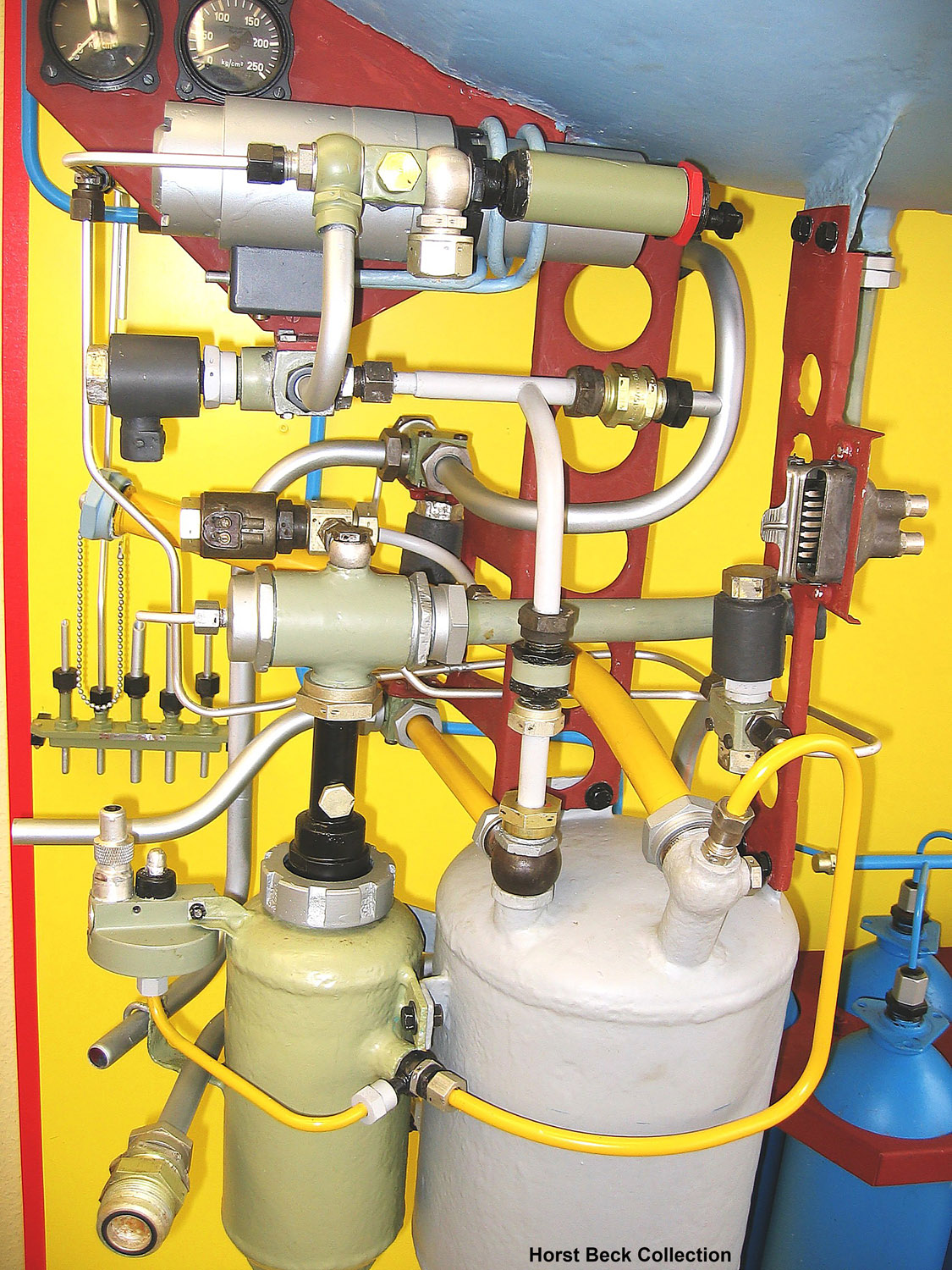
A4 missile steam generator detail. This excellent presentation was rebuilt from original refurbished parts by Horst Beck. See our video article The V2 Rocket Turbo-Pump for a technical exposition of the parts shown in this photo. Image courtesy The Horst Beck Collection
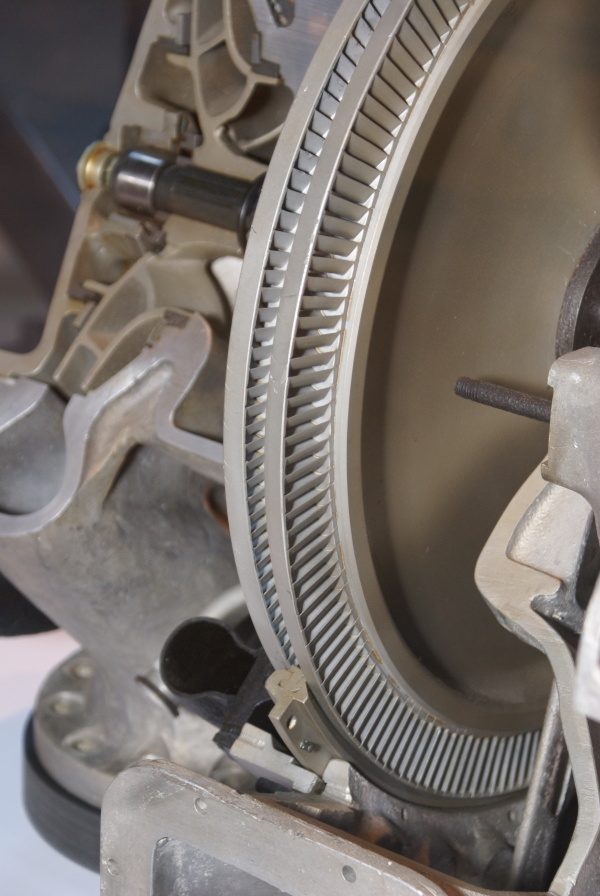
This image shows a cutaway of an A4-V2 turbo-pump. The section reveals the Curtis type 2-stage steam-turbine rotor and you can also see part of the stater inserted between the blades (bottom middle) and the adjacent steam distribution pipe (black open pipe on stater’s immediate left). Top left, a centrifugal pump rotor can be seen – cut through, it shows a multi-splined shaft running through the centre, simple bearing and end-cap.
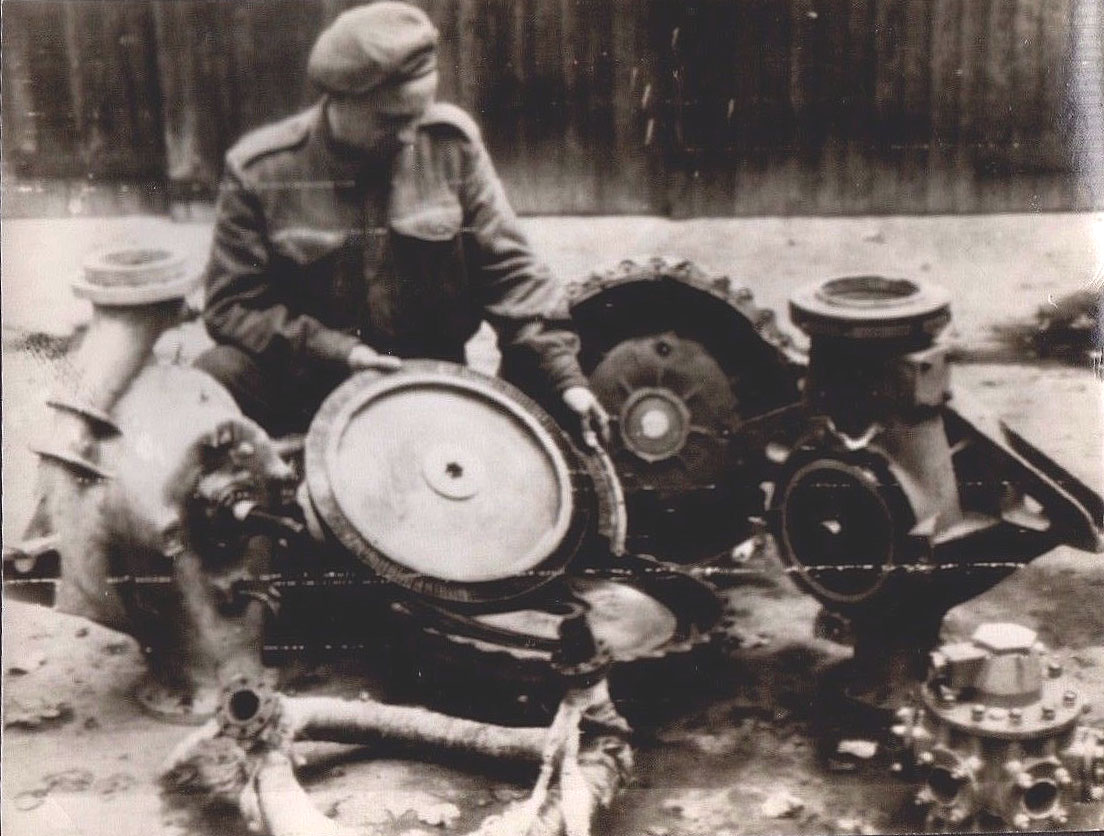
Image shows allied soldier examining remains of V2 rocket turbo-pump after impact. The soldier is holding the steam turbine rotor – the large size of this part is well shown in this photo. The still lagged steam inlet manifold can be seen in the left foreground and the LOX outlet manifold (and valve, topmost) can be seen in the lower right corner.
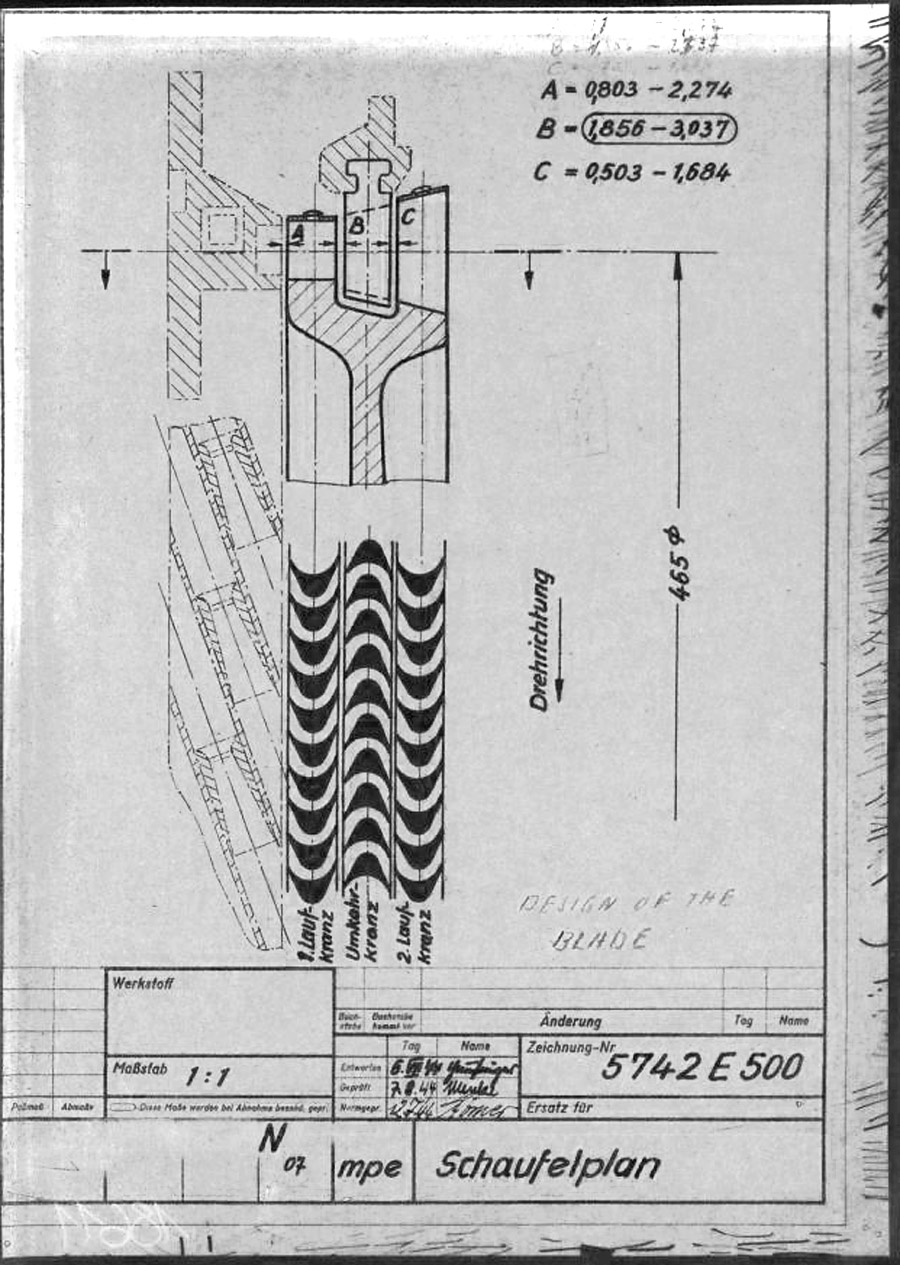
This mpe* drawing from 1945 shows the individual steam buckets or blades (labeled A and C) mounted to the rim of the rotor disk. As well as the fixed (i.e. stationary) stater blade B, positioned such that blades A & C can pass either side of it. The steam expansion is well shown by the increasing surface area of the blades from A to C, and growing larger, from left where the high pressure super heated steam enters the turbine, to right where it exits the blade pathway and passes in to the exhaust outlet. The lower graphic shows the way the super-heated high pressure steam is passed from the initial A blade and deflected by the reversed B stator blade for its energy to to be harvested for a second time by the C rotor blade. * mpe is the secret three letter armament code for Karlshagen, Werk Nord (North Works).
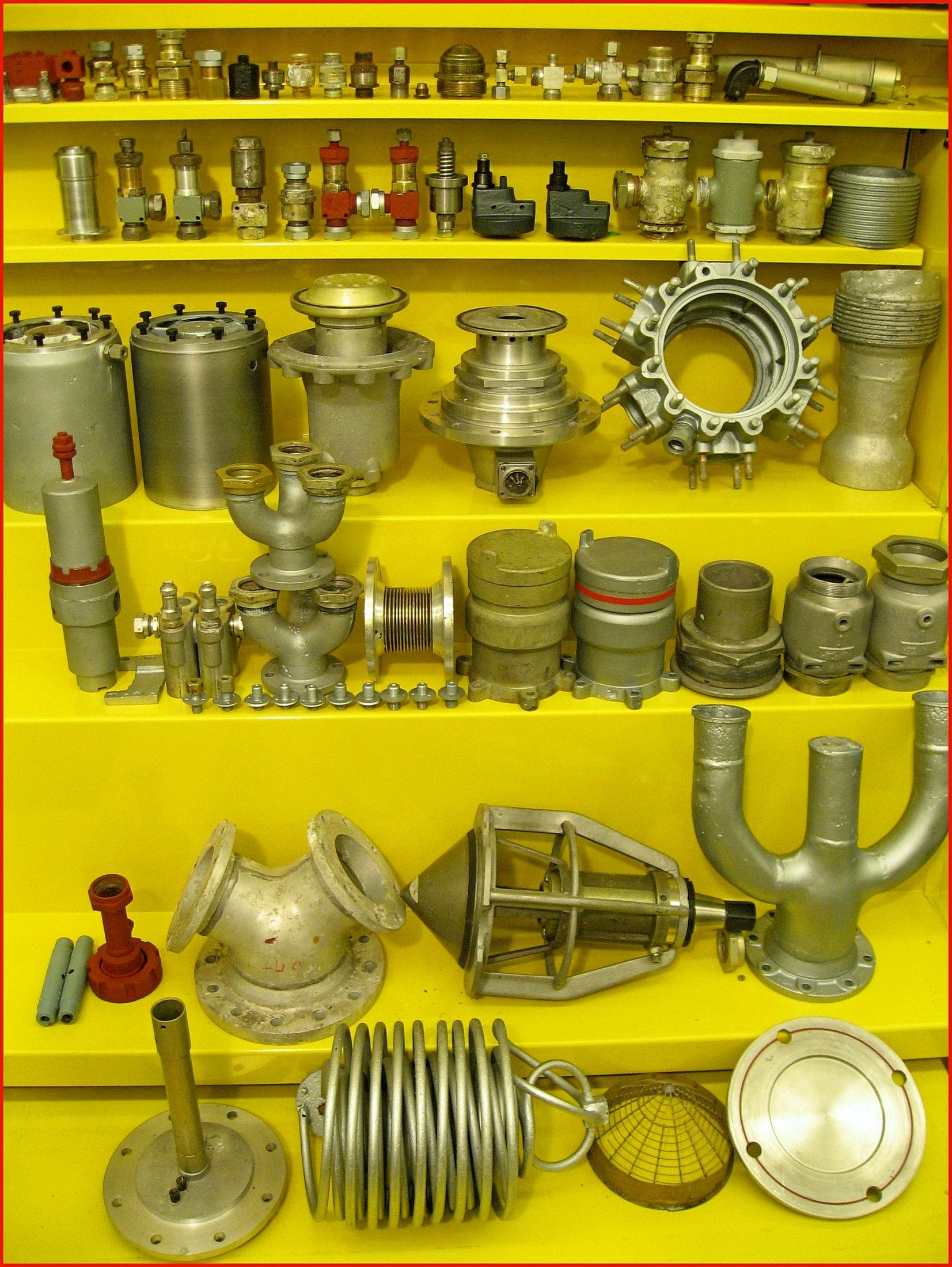
Looking rather like a a display in a V2 rocket shop window, this terrific display, centered on propellant supply parts, is part of the Horst Beck Collection and provides an unparalleled opportunity to view original A4-V2 missile components in a near-new condition and isolated from other equipment. Rare items include: a heat exchanger coil, for the volatilisation of LOX (2nd from left bottom shelf). An H²O² choke pipe and steam generator pot cap, (in red oxide paint, 2nd shelf up from bottom) Alcohol tank valve (2nd from right on the same shelf). Alcohol down-pipe 3-way splitter (1st item on right same shelf). LOX manifold 3 to 1 splitter (two with one resting on the other, 3rd shelf up on left). Two LOX main tank valves, (4th shelf up, first two item from left). Injector head main alcohol valve (same shelf, 3rd item from left). And on its right, a main Lox dual valve, and on its right LOX distribution body, minus valve. A ‘Preshona’ non-return valve can be seen (2nd shelf from top, 5th item from left). The two same shape black items (2nd shelf from top, middle) are two Sodium Permanganate diaphragm contact switches (Backfile code D2R). The next 3 items to the right of these are all H²O² 25ton valves. The large brass item in the middle of the top shelf is a LOX spray cap. Image courtesy Horst Beck Collection
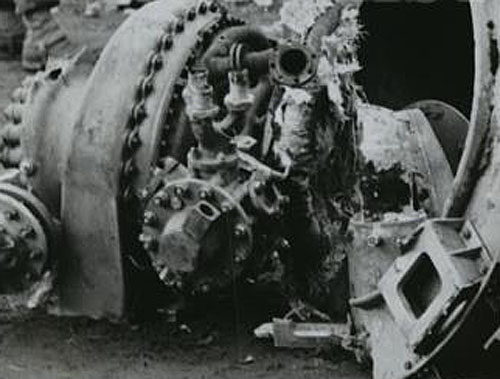
Picture shows tubo-pump debris from impact site. LOX manifold clearly seen (3 in 1 outlet pipes, upper center of image – the one to its right, 2 o’clock position, and left, 11 o’clock position are both broken off).The LOX flow electric control valve is also well displayed in this image (LOX valve head is slightly low and left of center, part nearest camera). The electrical connection to the LOX valve has broken away leaving its empty socket pointing upwards and to the right.
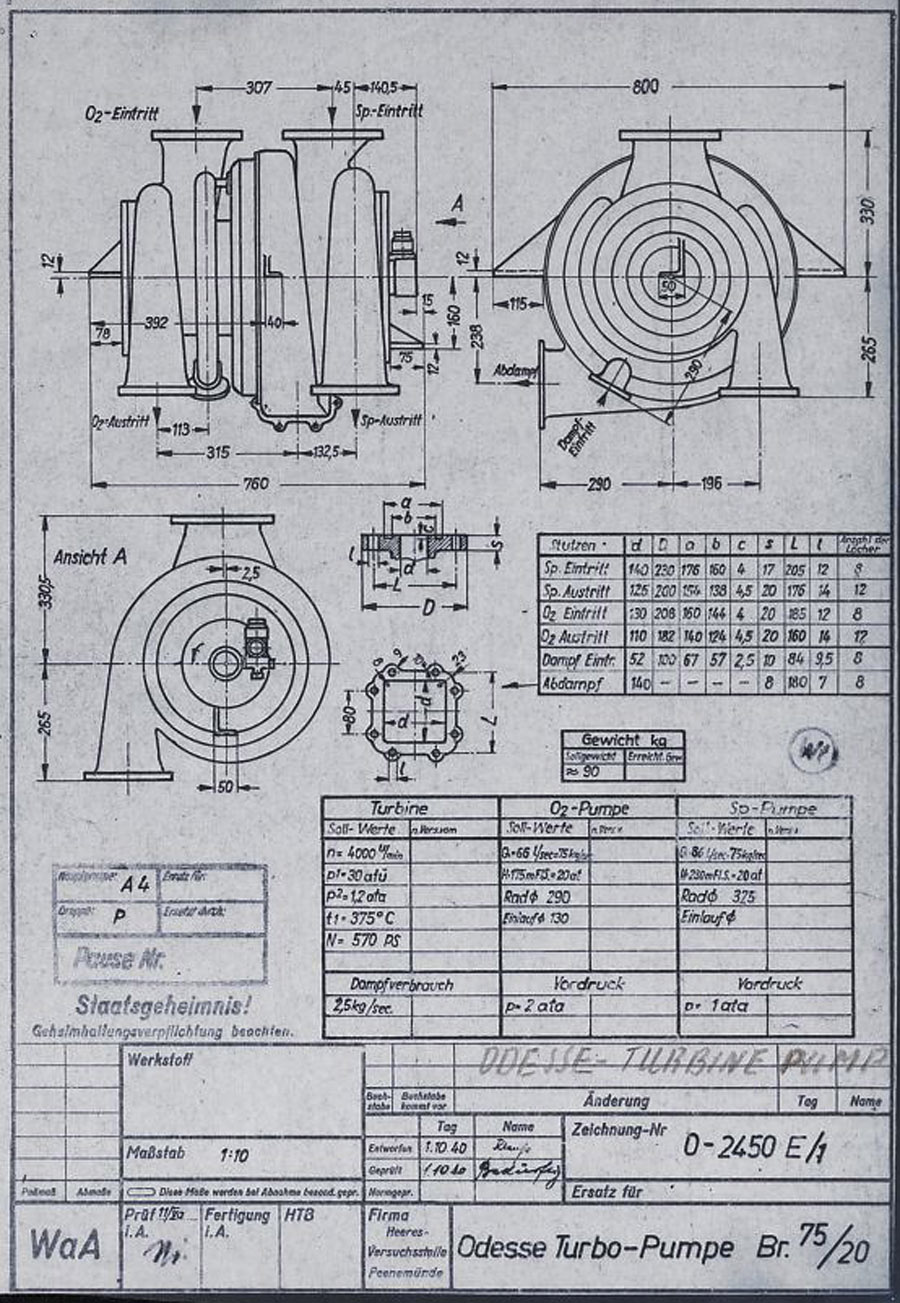
This HVP technical drawing from October 1940, shows a proposal from the Oddesse company – the full title of this company is KLEIN SCHANZLIN ODDESSE GmbH. Klein, Schanzlin & Becker A.G. (waffenamt code: ebb) took over Oddessa in 1929 and the company became formally known as KLEIN SCHANZLIN-ODDESSE GmbH (code ebc) in 1939. (NB: The company name has nothing to do with a similar sounding place name Odessa. The Oddesse trading name was formed from the partnership of English engineer Oddie, and German businessman Hesse.). The dual centrifugal turbo-pump shown in the drawing is a variant of a high pressure fire-fighting pump manufactured by Oddesse. Note the off-center outflow ports – not also that the outlet flanges are still level at this stage. Note also the incorrect spelling of the company name in the details panel lower right. (Digipeer.de image)
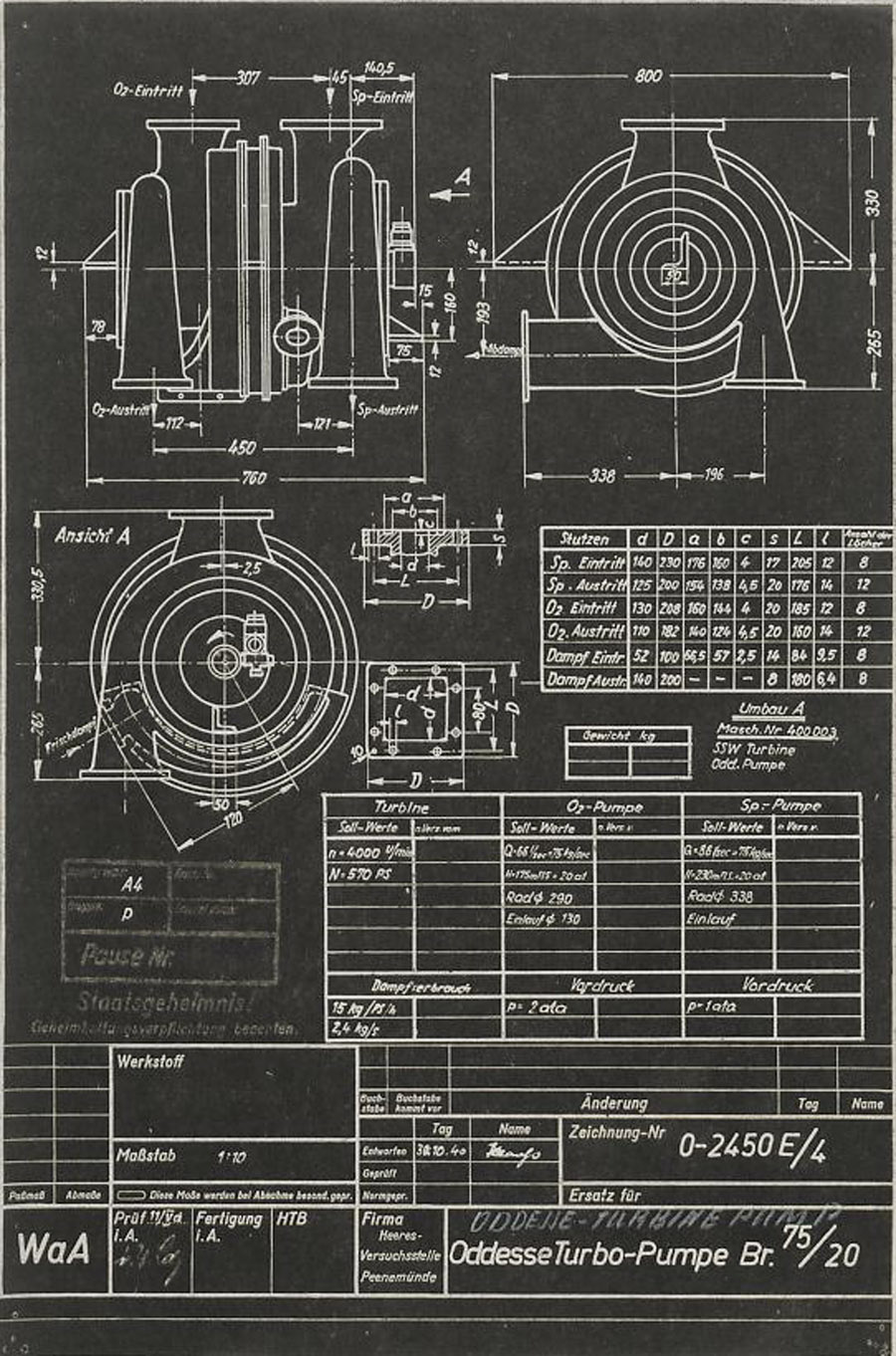
Another HVP technical drawing from later in October 1940, shows further data from the KLEIN SCHANZLIN ODDESSE (ebc) company A4-V2 turbo-pump project. See previous image for company details. The dual centrifugal turbo-pump shown in the drawing is a variant of a high pressure fire-fighting pump manufactured by Oddesse. Note the off-center outlet ports. Note also the corrected spelling of the company name in the details panel lower right (see previous Oddesse image) and the small note below the top table that indicates that the pumps are from Oddesse (ODD) and the turbine from a company indicated as SSW. (Digipeer.de image)

Signatur FA 014/21241 (Digipeer.de image)
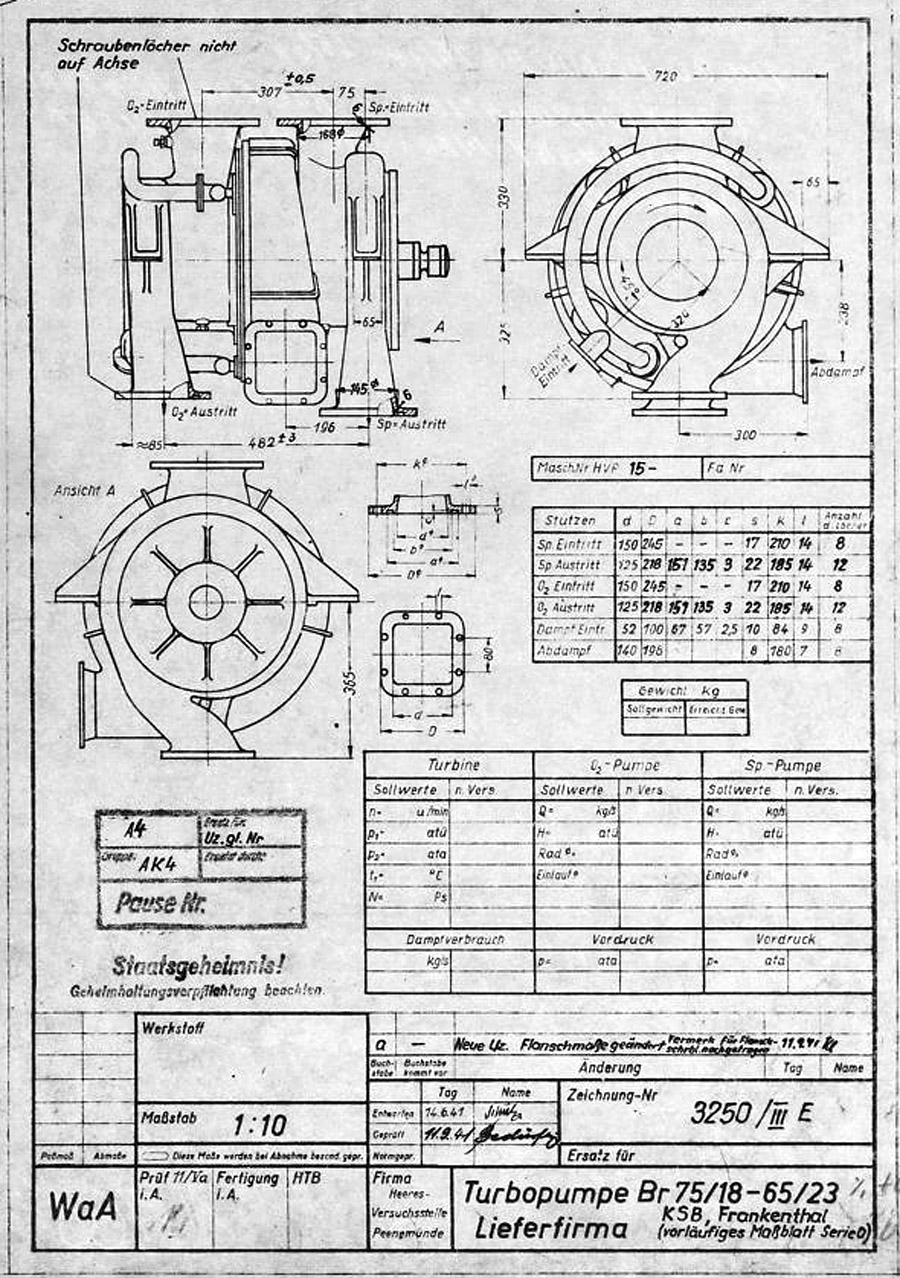
V2 rocket turbo-pump preliminary dimension sheet for O series, drawing. Many of the final elements of the turbo-pump design can be seen in this ‘preliminary’ drawing and table form 1941. The word lieferfirma in the data box btm right mean supply company – and this is indicated to be KSB or Klein Schanzlin & Becker AG, Frankenthal. Signatur FA 014/14769
(Digipeer.de image)
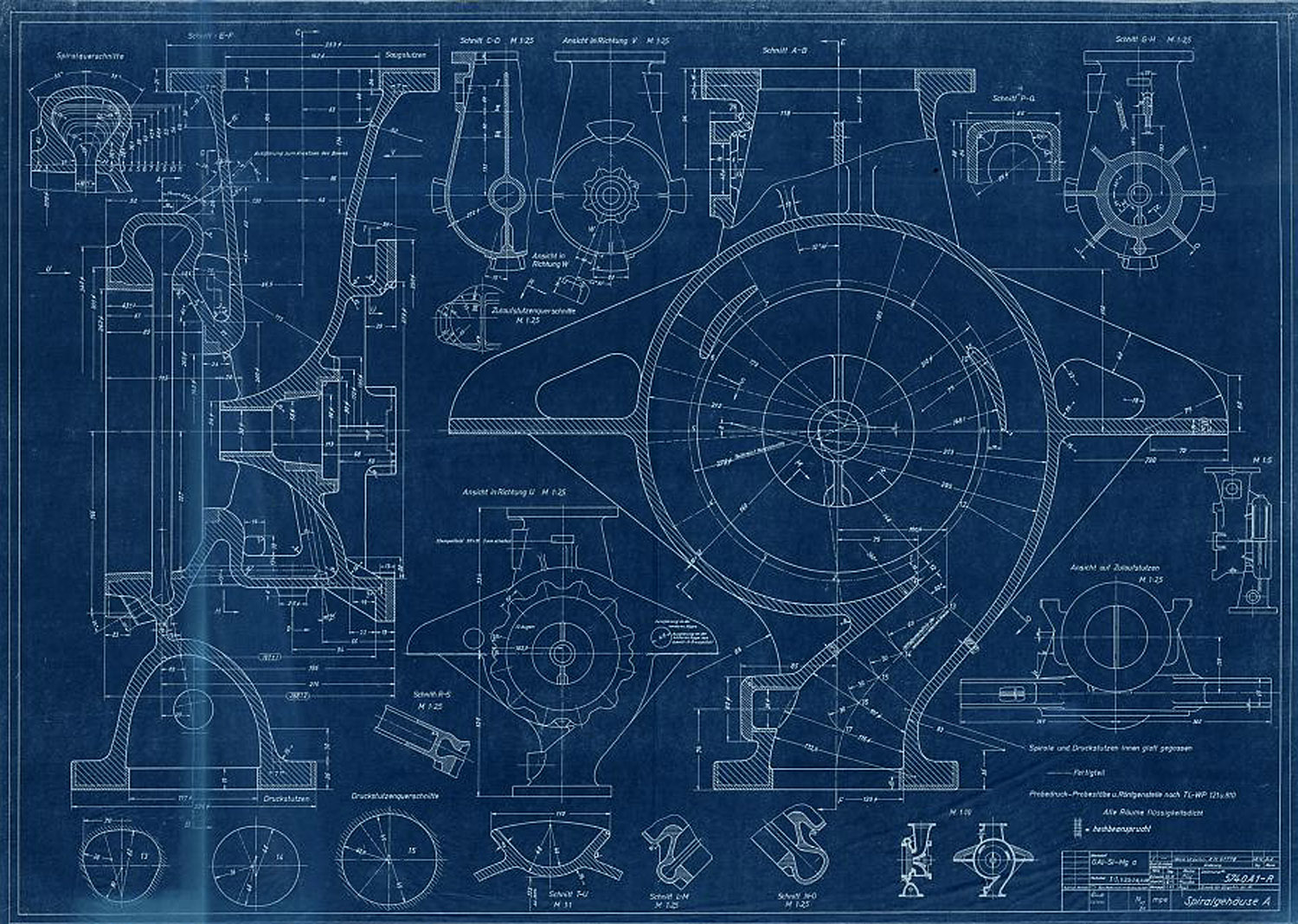
Signatur FA 014/02537
Abmessungen: 42,9×59,8
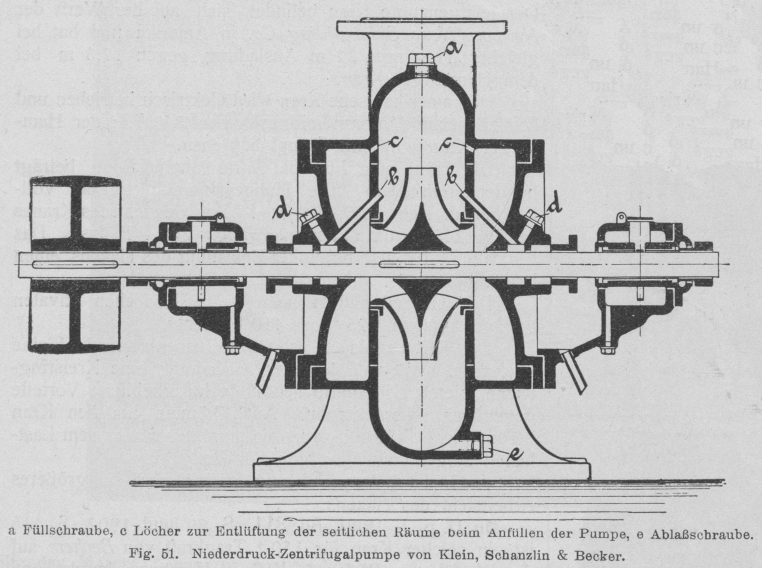
Early belt powered centrifugal pump by Klein Schanzlin & Becker. This schematic shows an early 20th century centrifugal pump designed and manufactured by KSB. The drawing appears to show auto-purge pathways at points marked C as well continuous lubrication pathways at B. Both of these important ideas would later feature in the propellant pump of the A4-V2 missile.
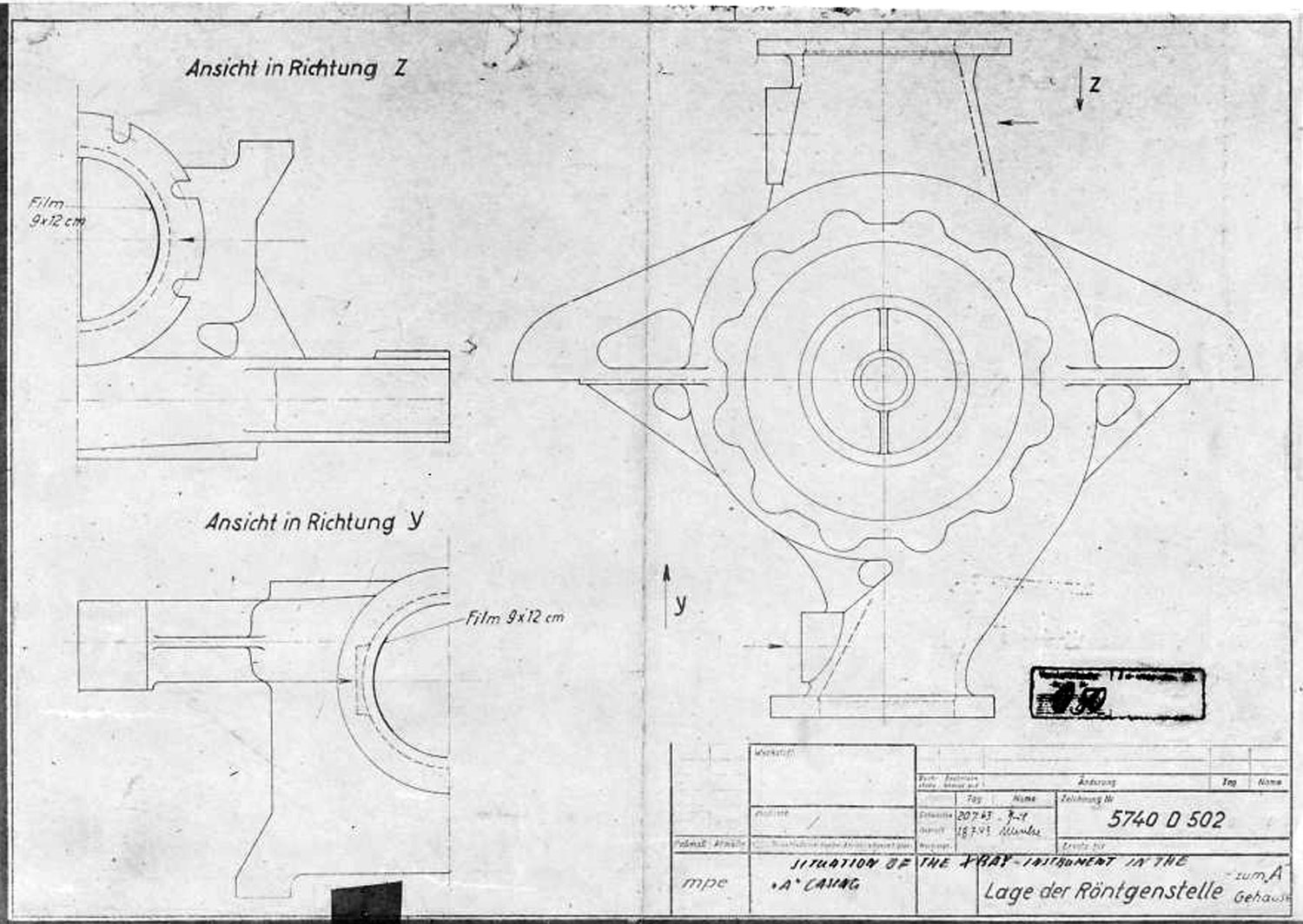
A Stoff (liquid oxygen) pump casing diagram showing stress points that require X ray quality control photography before use. The diagram shows the specific locations where photographic film is to be placed for X-ray analysis.
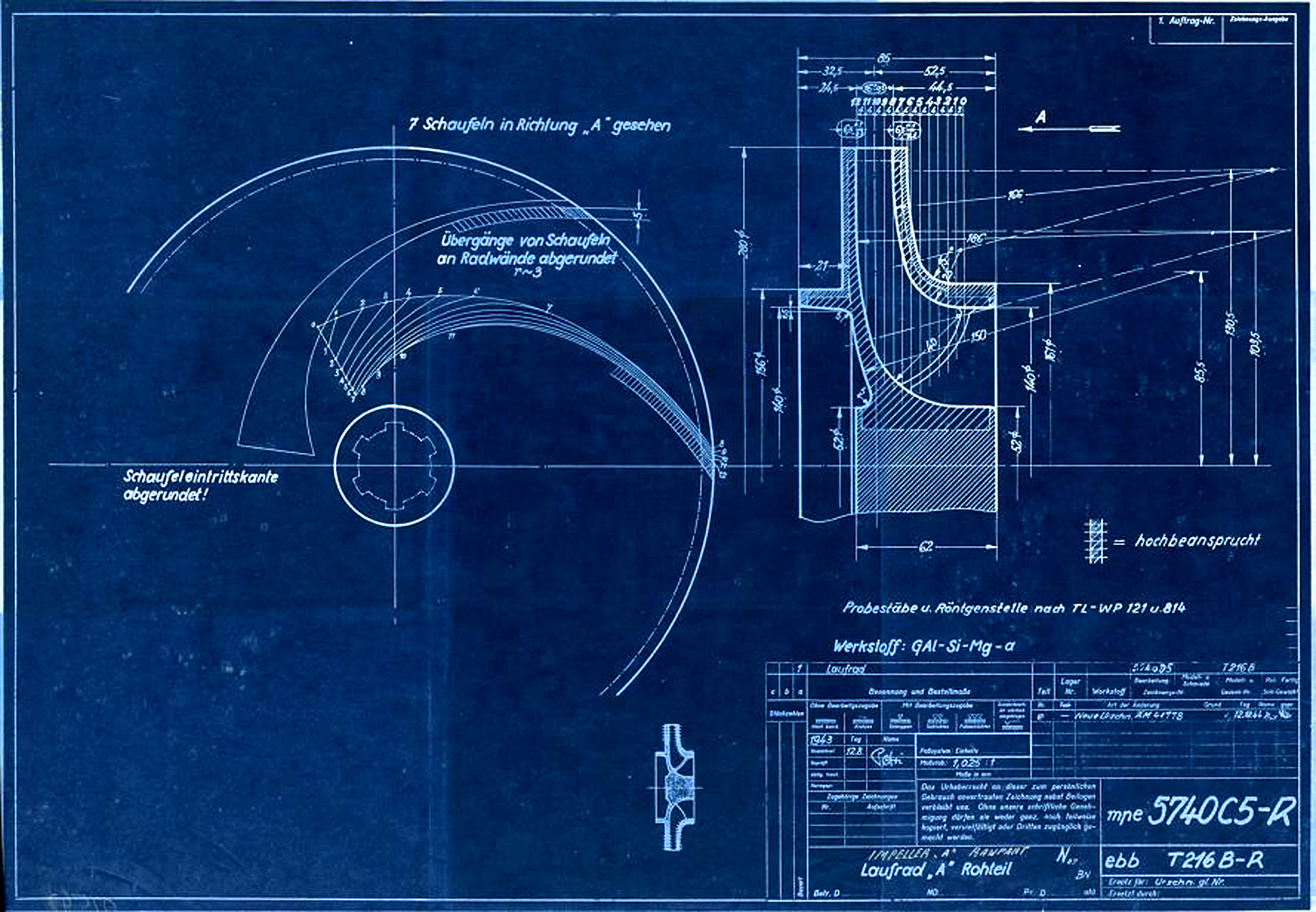
Centrifugal impeller for A or liquid oxygen (LOX) pump. The drawing originated in Aug 1943 and was superseded in December 1944. A key to the image hatching can be seen with the label ‘Hochbeansprucht’ which in English means Highly Stressed. Next to the drawing numbers two secret three letter armament codes can be seen indicating the ‘origination’ of the document. The top one mpe = Heimat Artillerie Park 11 (HAP or Army Artillery Range). The lower code ebb = Klein Schanzlin & Becker AG, Frankenthal.
Signatur FA 014/02542 (Digipeer.de image)
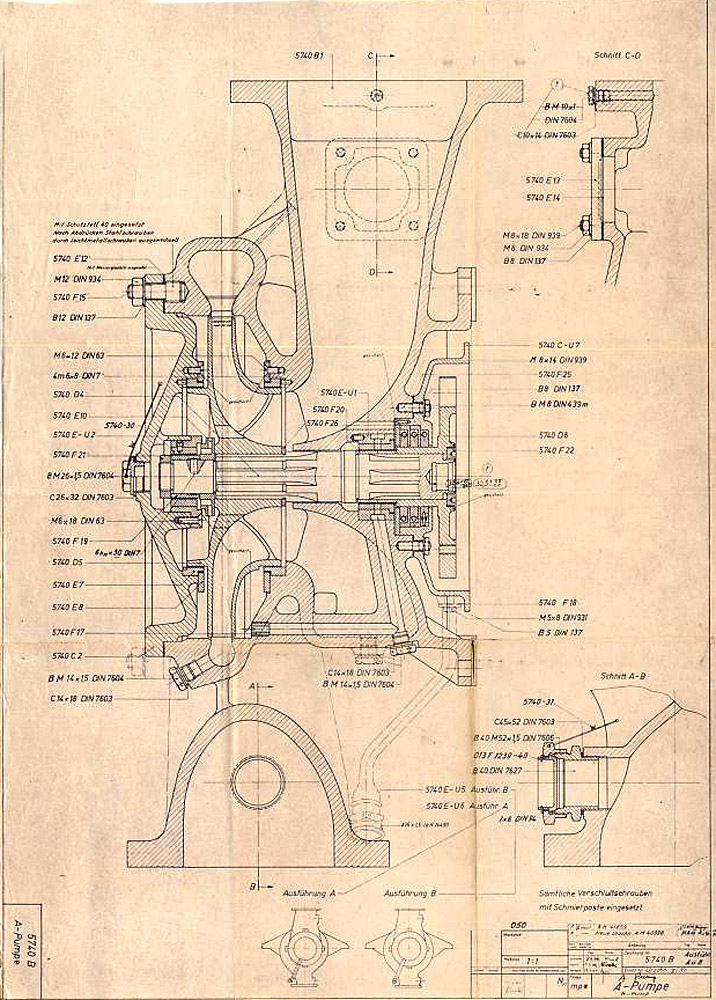
Signatur FA 014/02534
Abmessungen: 60,5×82,9
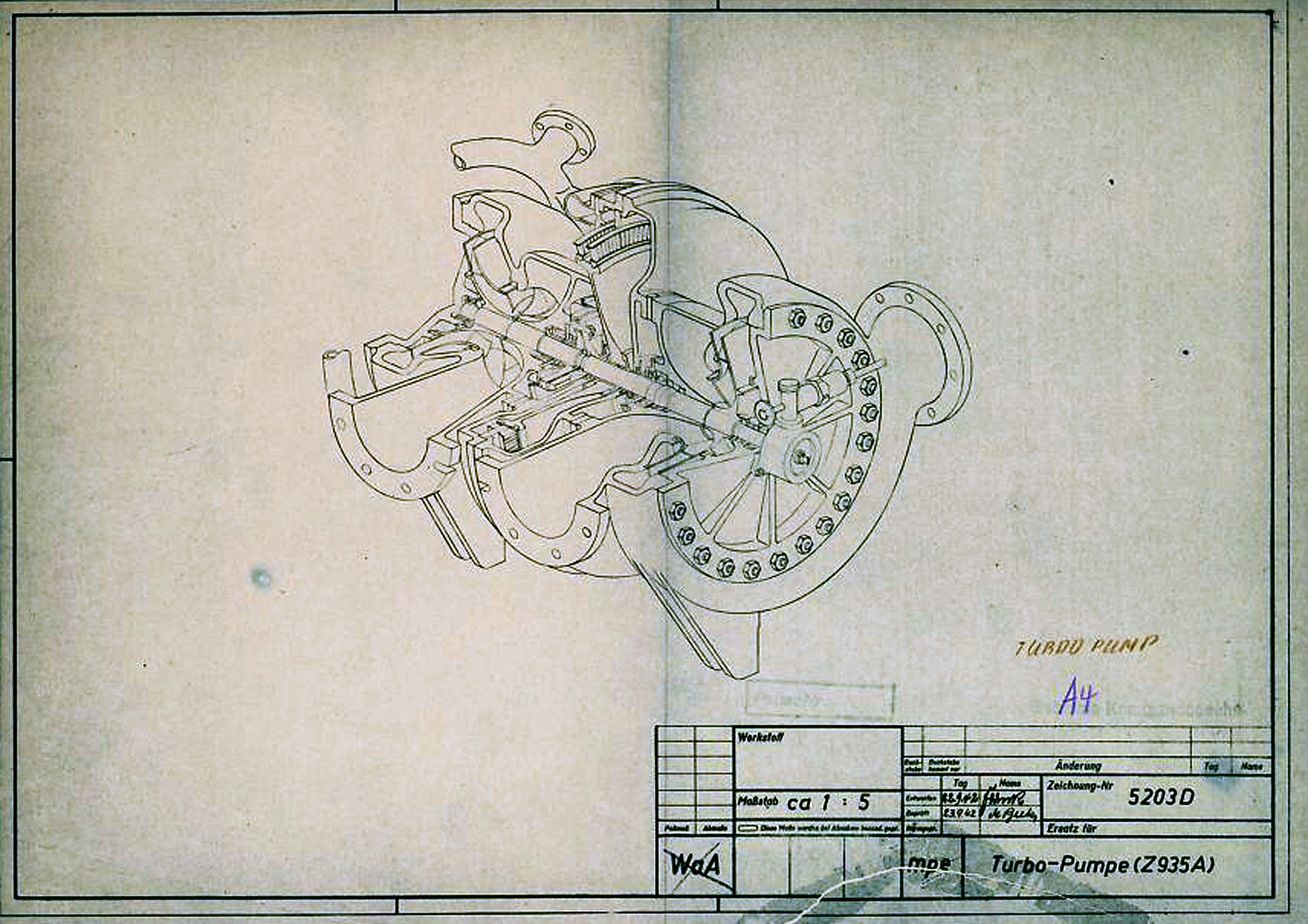
In this diagram the V2 Turbo-pump is shown in a cutaway presentation and rotated 90 degrees counter clockwise. The B stoff (fuel) pump is nearest the viewer – the over-speed device can be seen on the B stoff pump’s case end-plate. The low pressure inlet ports our shown to the left, and high-pressure outlet ports are on the right. The steam distribution manifold can be seen at the furthest point from the viewer – the steam inlet pipe flange can also be seen. The feed pipe from the steam generator attaches to thus flange.
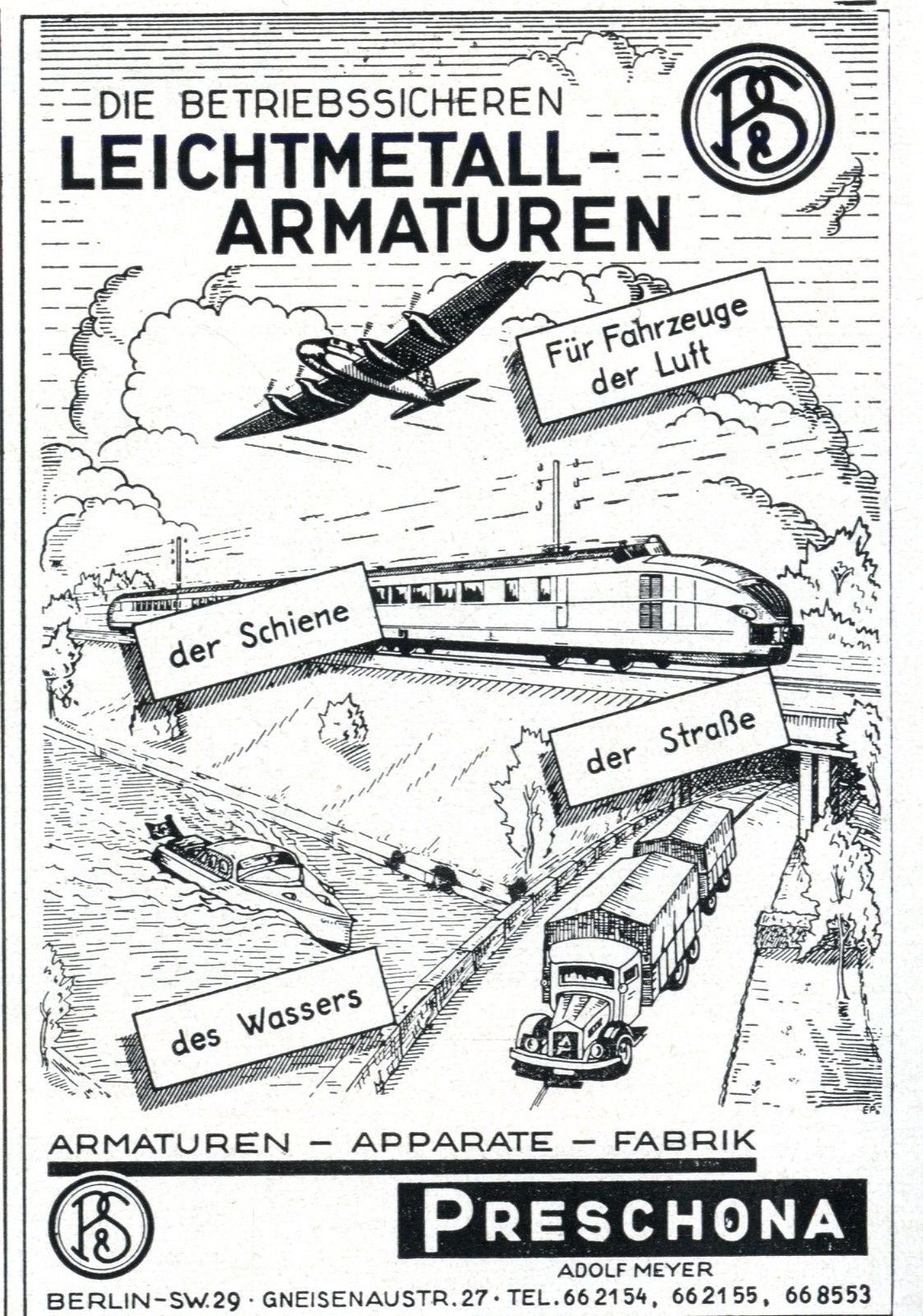
Trade literature advert for the Preschona company (Adolf Meyer) in Berlin, Germany. The company was a supply contractor and (among other items) manufactured the non-return valve for the steam turbine exhaust heat exchanger, employed to volatilise a small portion of liquid oxygen (LOX) to pressurise the LOX tank to maintain critical flow volume to the LOX turbo-pump.
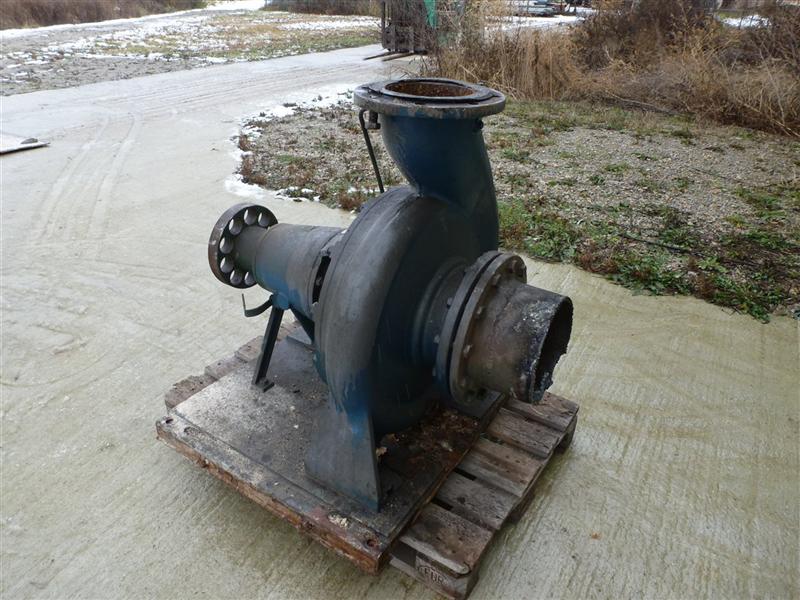
Large industrial volute case centrifugal pump by Klein Schanzlin & Becker. This image highlights the ‘genetic’similarity and family resemblance between KSB’s current and historical product range and the visible features of the A4-V2 missile Turbo-Pump (TP). Apart from the general shape of the cast spiral-volute case and its connection flanges, the ‘soft’ shaft connection (disk with holes on the extreme left of the pump) is very reminiscent of the semi-flexible shaft connection point linking one side the steam turbine rotor shaft to the shaft carrying a propellent pump rotor seen in the A4-V2 missile TP. Family photo? Industrial volute case centrifugal pump by KSB
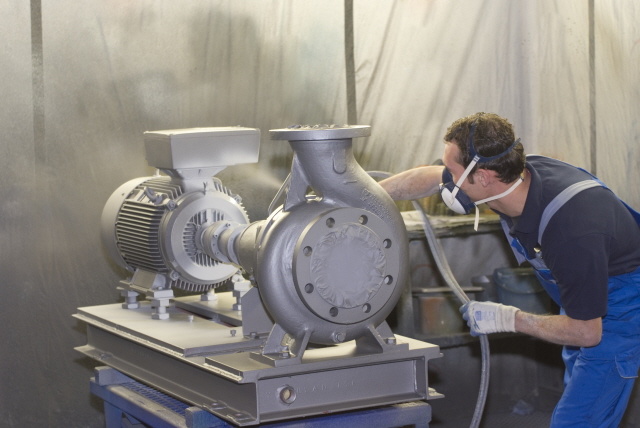
Electric industrial volute case centrifugal pump by Klein Schanzlin & Becker. This image highlights the ‘genetic’similarity and family resemblance between KSB’s current and historical product range and the visible features of the A4-V2 missile Turbo-Pump (TP). Assembly is shown being spray painted.
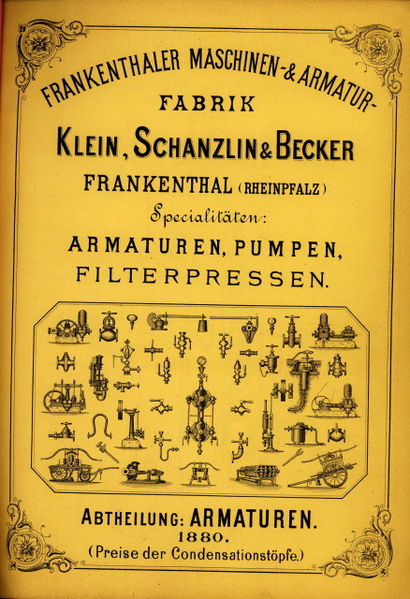
Cover of catalogue published in 1880 showing the KSB product range
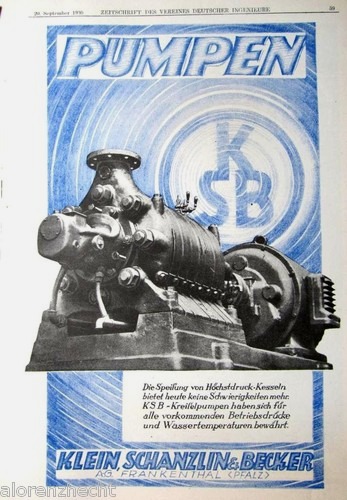
Klein Schanzlin & Becker electric centrifugal-pump advert.

Valves
Images of the main valves involved in the propellant flow of the A4 / V2 liquid fuelled rocket engine
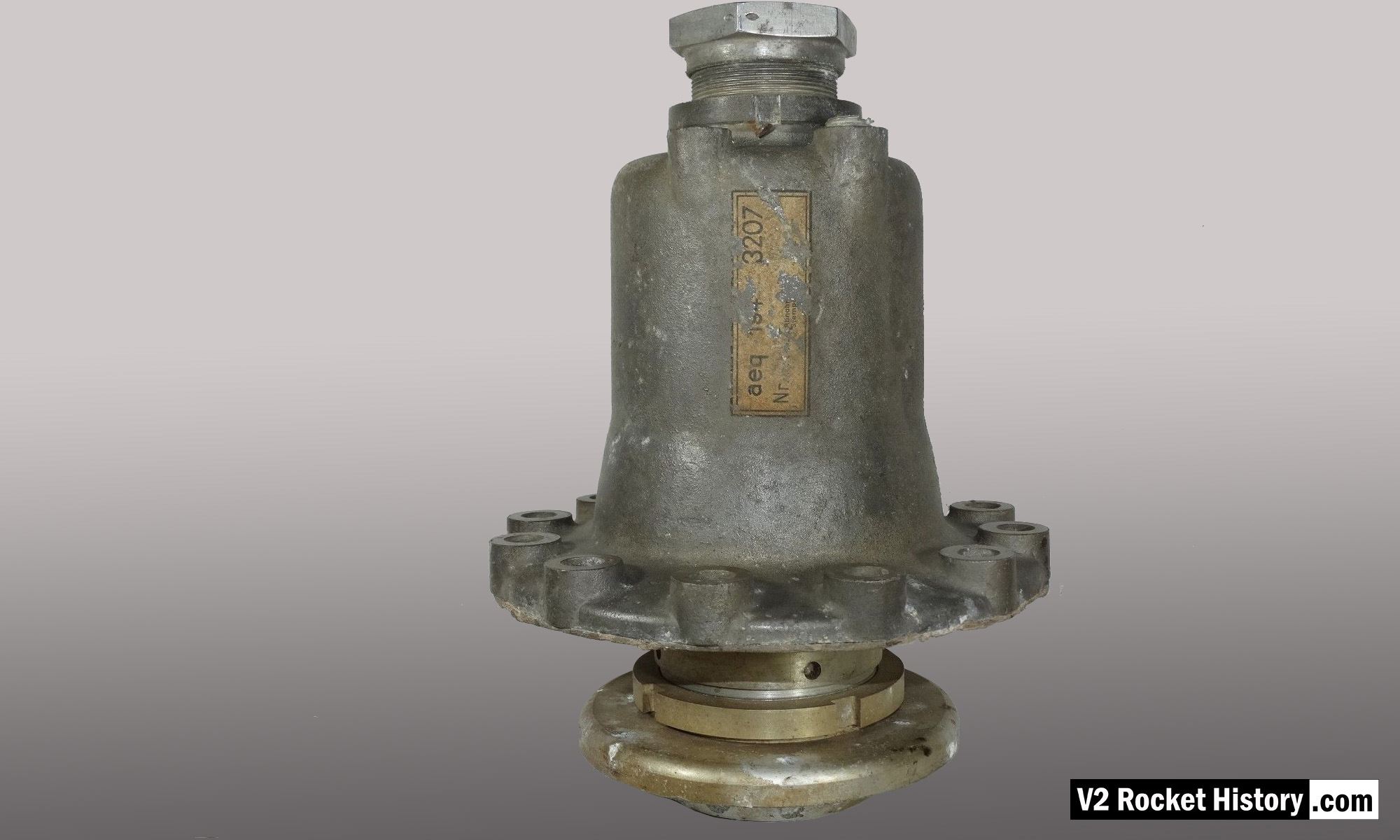
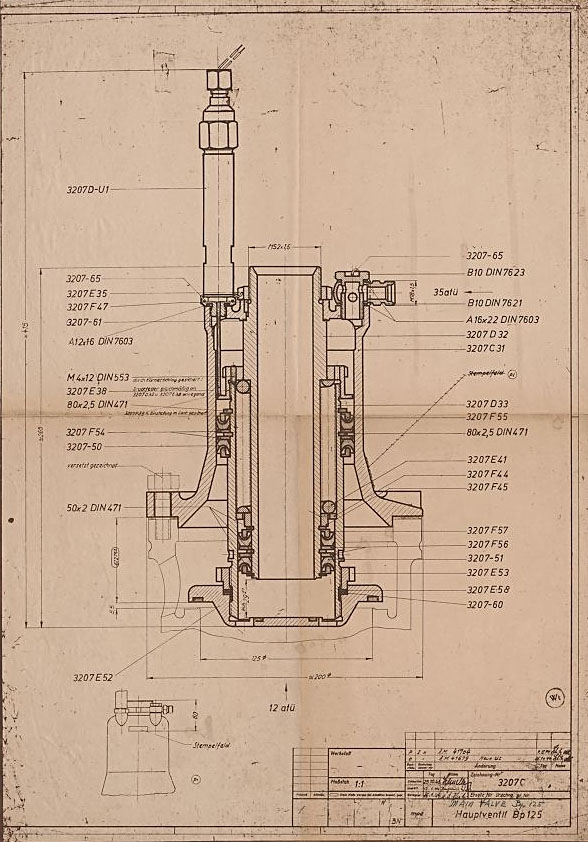
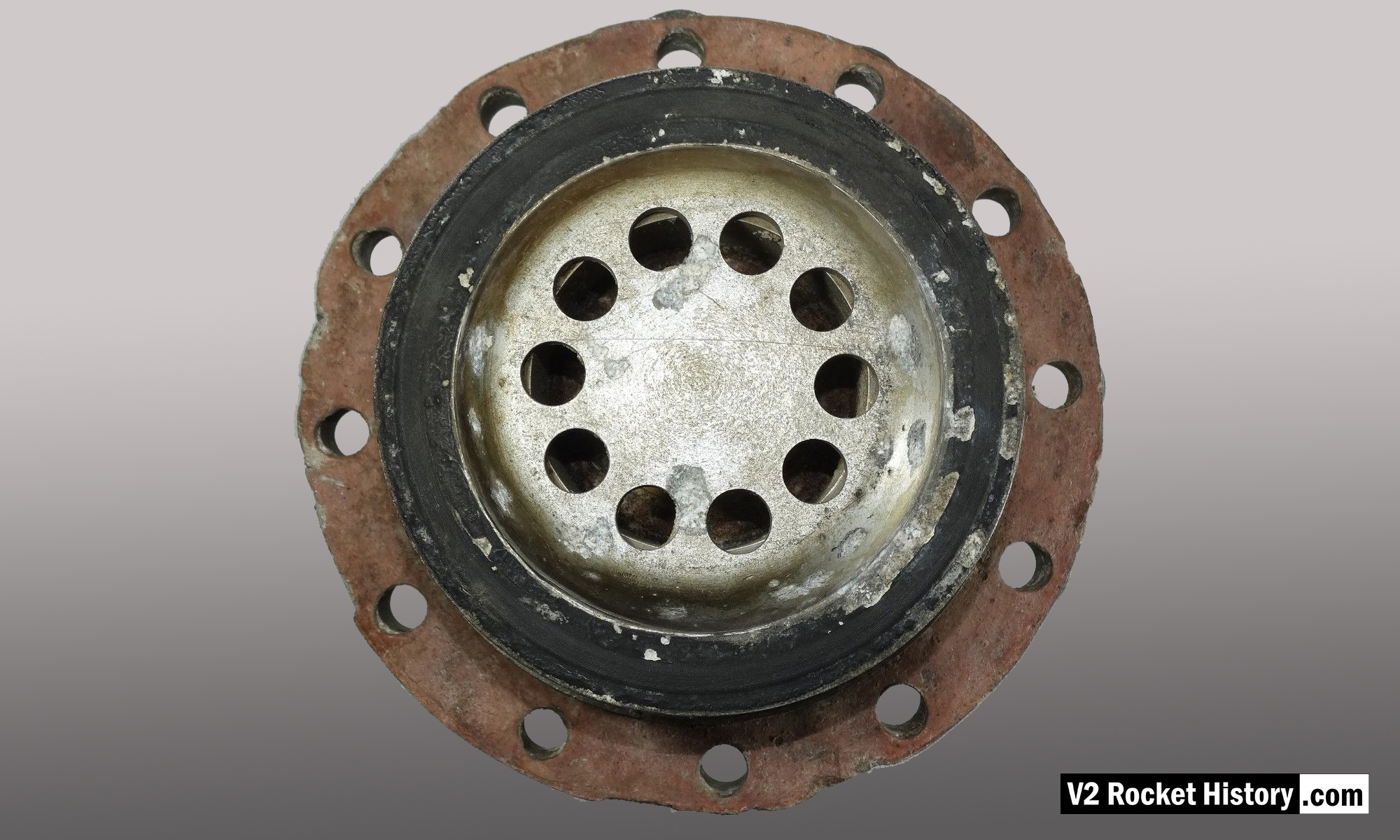
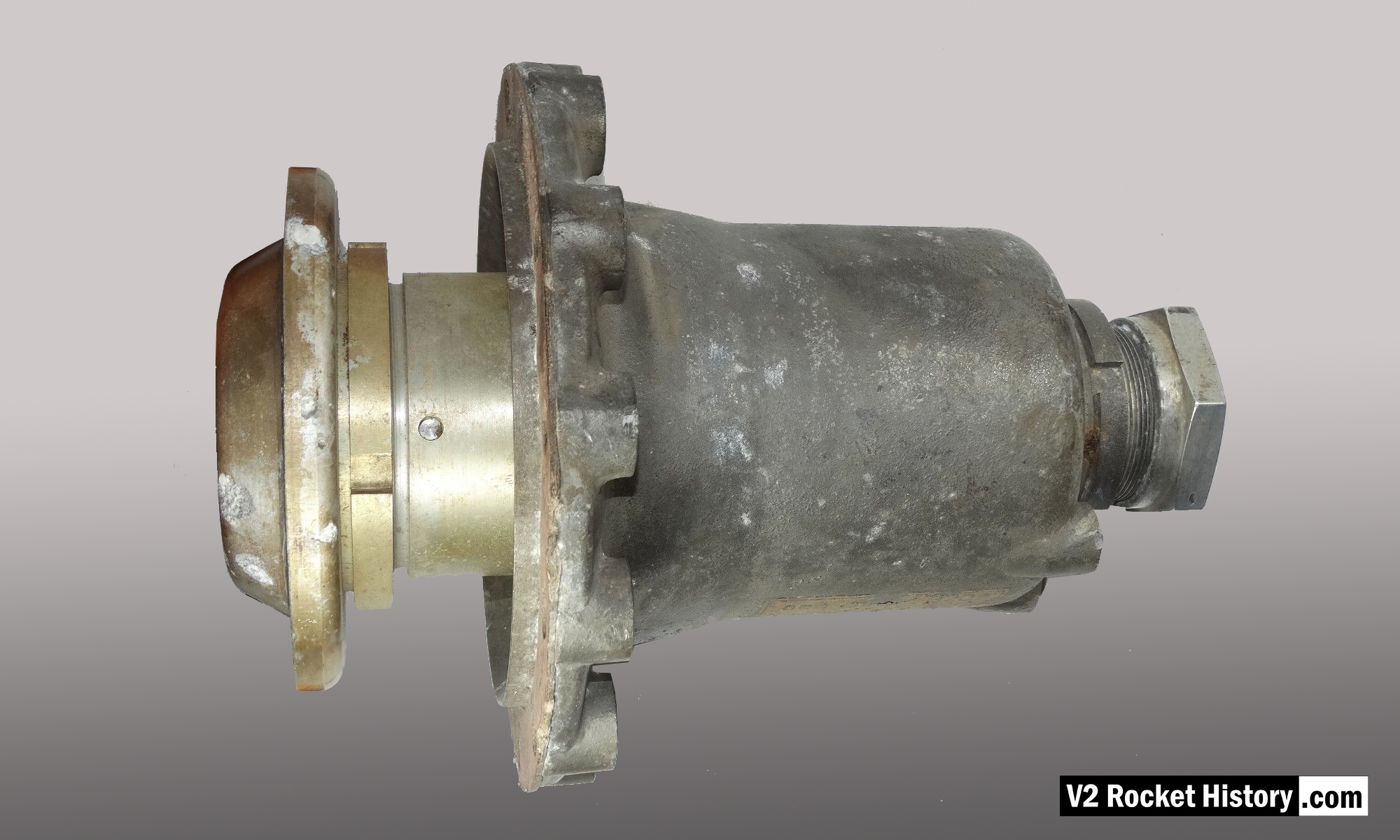
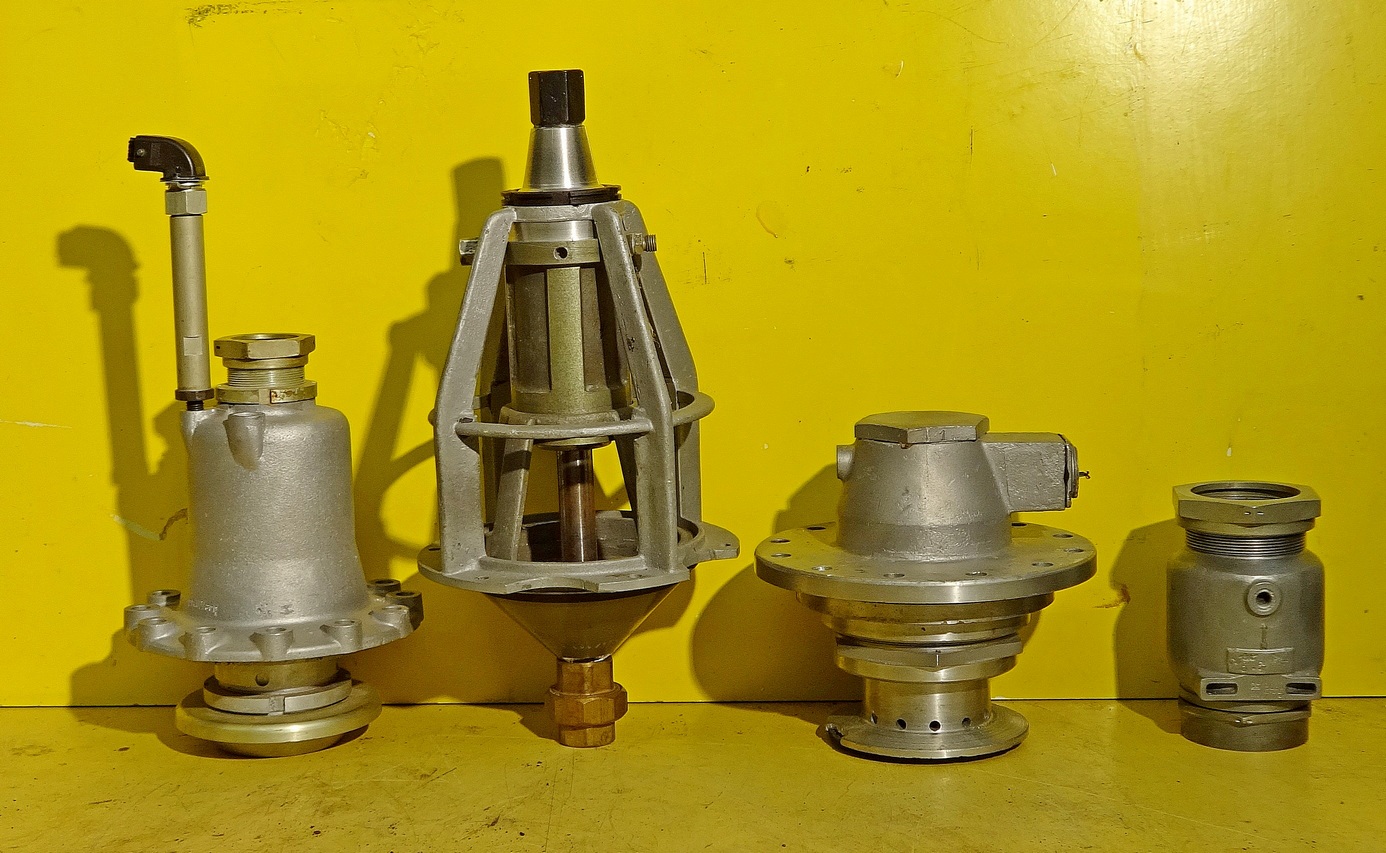
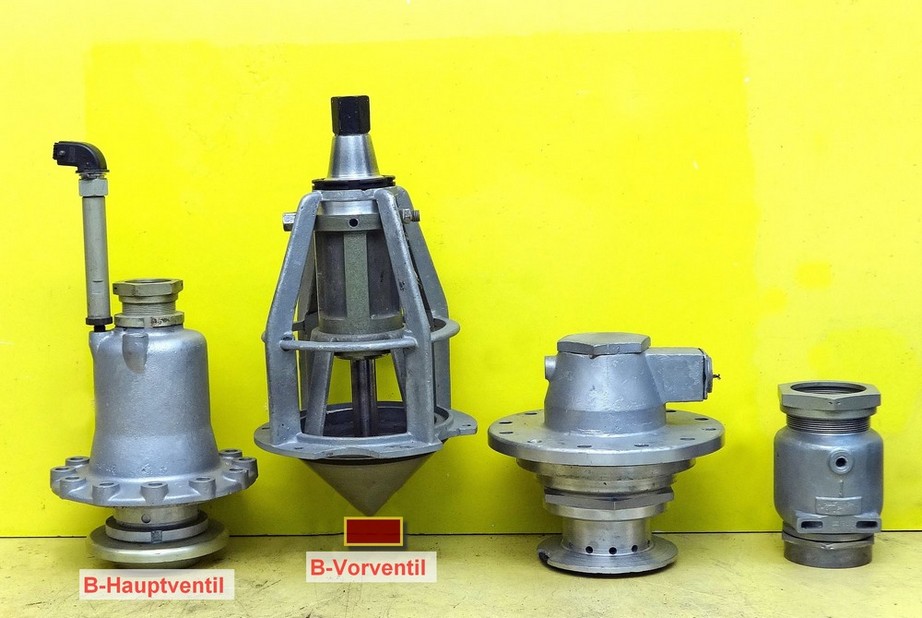
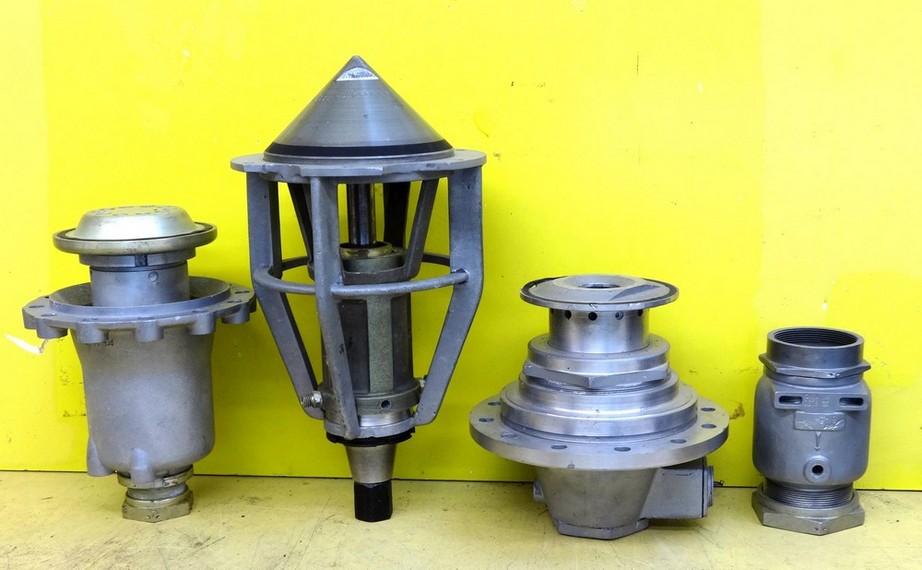
Images of the main valves involved in the propellant flow of the A4 / V2 liquid fuelled rocket engine
Relic of main alcohol valve with manufacturer code aeq (aeq = Bartoc & Co., Maschinenfabrik u. Giesserei Hedwikow,bei Caslau (Caslav) Czech Republic). An air (nitrogen) inlet pressure of 440 to 530 psi (30 to 36 Bar) was required to close this valve against its internal spring and the force of the turbo-pump. The large nut at the top is the connection for the fuel return (or ‘revolving’line) pipe, and the air and electrical input ports can be seen to the right (air), and left (elec.) just below this point. V2RH image

Anatomy of the V2: 18-pot injector head

V2 rocket engine fuel injector inserts – a part of our collection used for the water tests with various types shown. The tool shown is a pin-wrench used to fit the inserts into the test apparatus. V2RH collection image

The injector head fragment shown here, is from an 4B 1000 kg thrust engine that was developed at Kummersdorf in 1938/39 by Dr Walter Thiel’s combustion research group. The fragment, clearly the remains of an explosion, was actually found in a scrap pile in Peenemüde but the engine was probably tested (and destroyed) at the Kummersdorf army testing station. V2RH collection image.
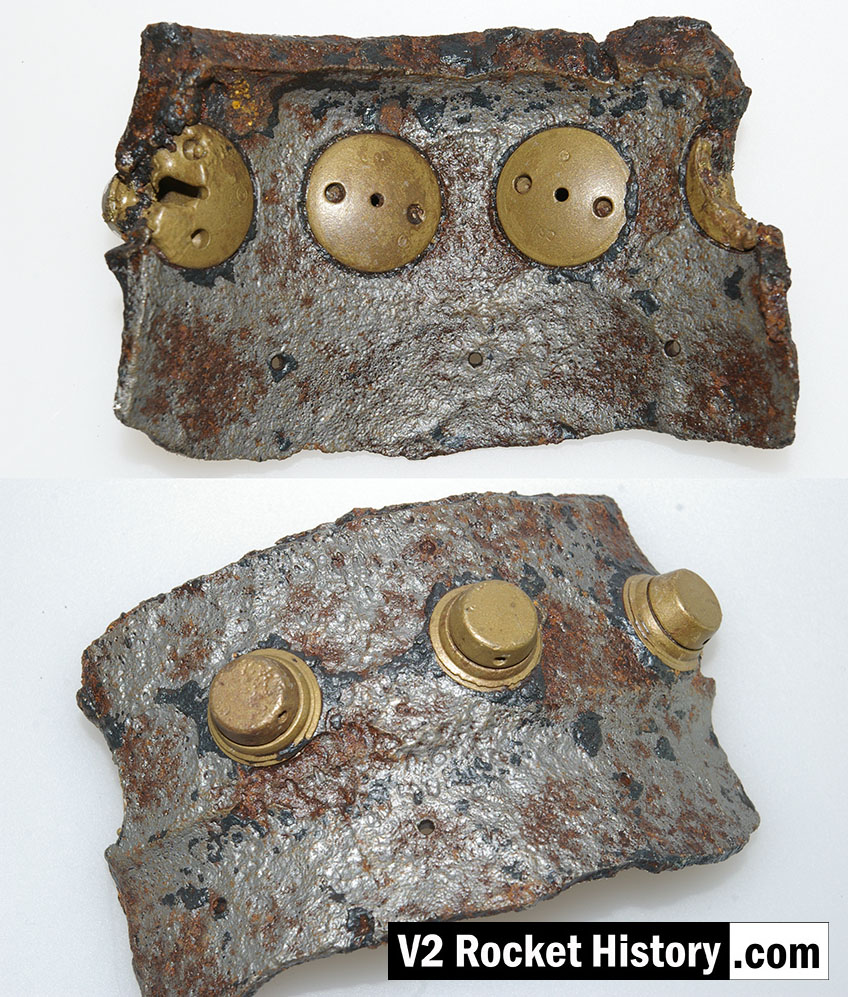
Photo shows a small section of the burner cup with row A (2131E) fuel injector inserts with three row B drilled holes below. The two undamaged inserts carry the armament code ‘csl’. The relic was found near a workshop in the Development works Pennemünde. Slag from the cutting flame and damage to the inserts at both ends of the relic would indicate that the section was cut from a steel burner cup using a gas cutter (fuel and oxygen) for purposes unknown. V2RH collection image
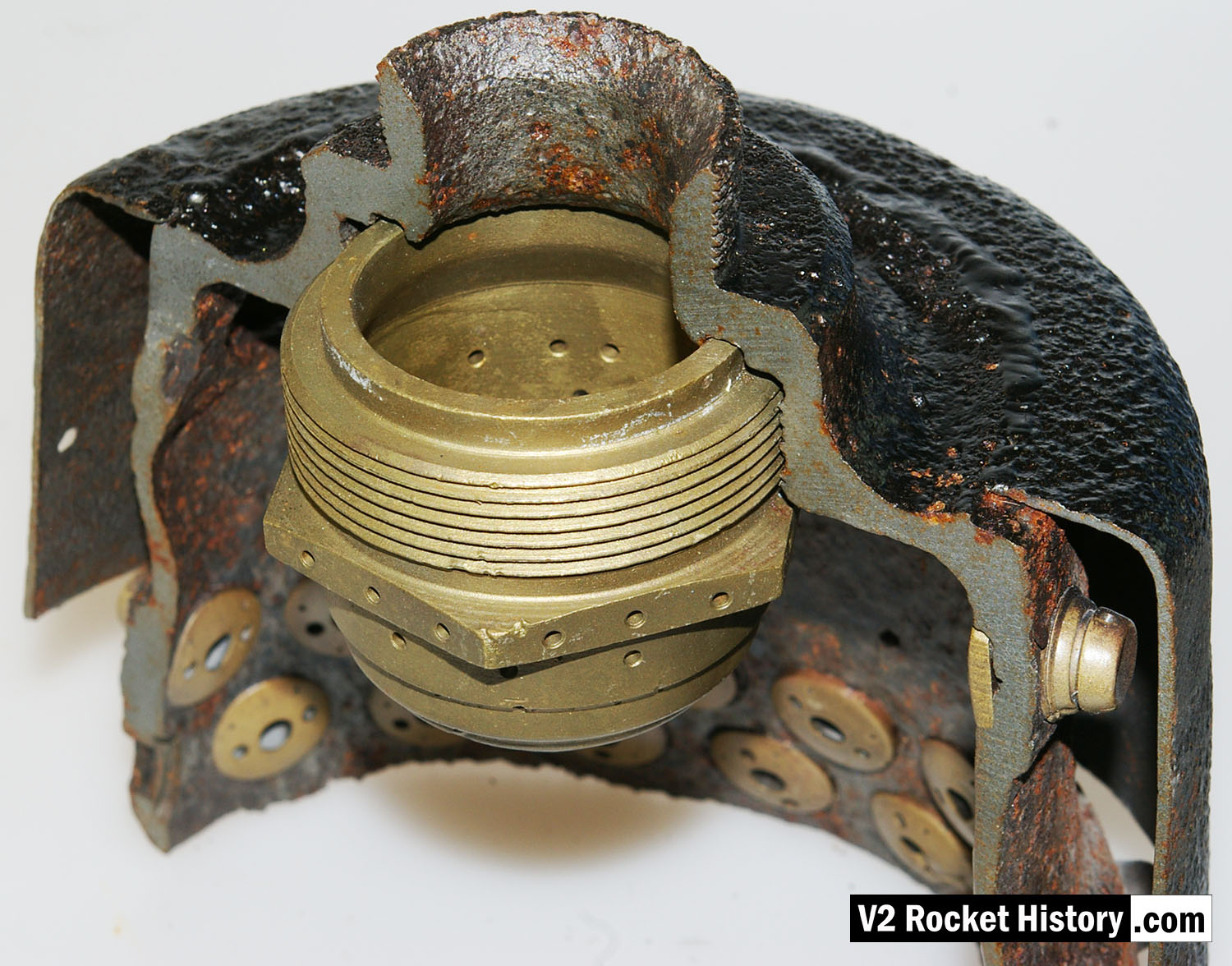
Cutaway section of fuel and liquid oxygen (LOX) injector pot. The exhibit shows the bell shaped thick inner wall of the burner with three tiers of fuel injector inserts (A,D, and E). The central copper alloy LOX spray injector is also well displayed in this image. The thin steel outer shell of the burner cup is shown and affords a good view of the head cavity that supplies fuel to the injector inserts – one A type injector is shown party cut through on the right, its rear portion showing inside the fuel cavity. V2RH image
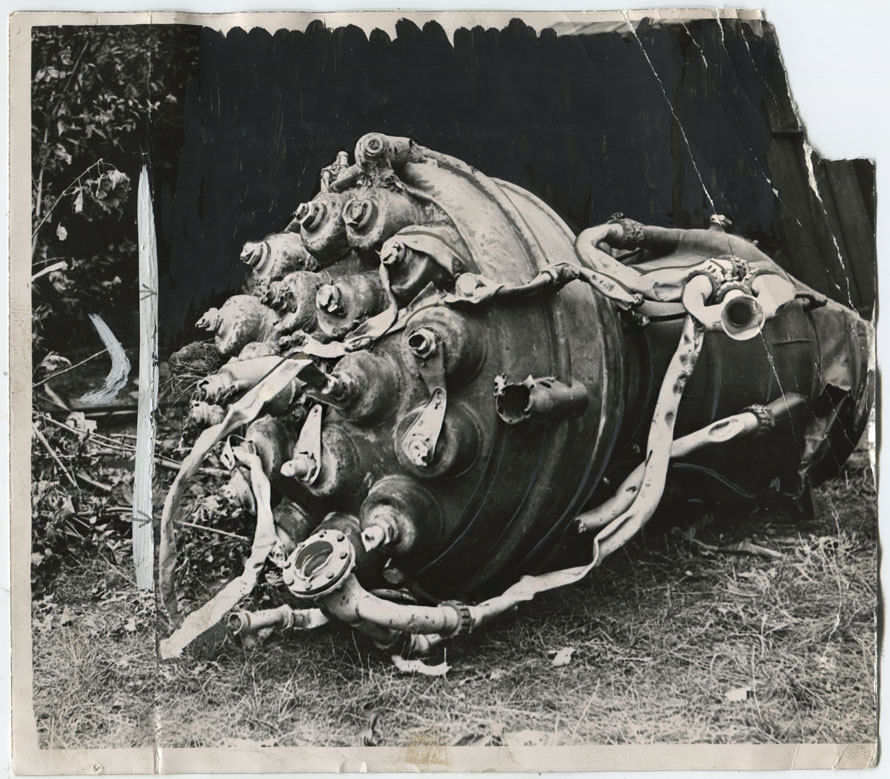
Wreckage of V2 combustion chamber with a tangle of connection pipes laying in a garden in Southern England – winter 1944. The censor has obscured the background to avoid providing the enemy with useful information. The injection head shows two connected lock ‘spanners’ securing the nuts of oxygen inlet pipes. Prior to impact all 18 of the LOX pipe input nuts would have been secured by these lightweight pressed steel ‘spanners’.
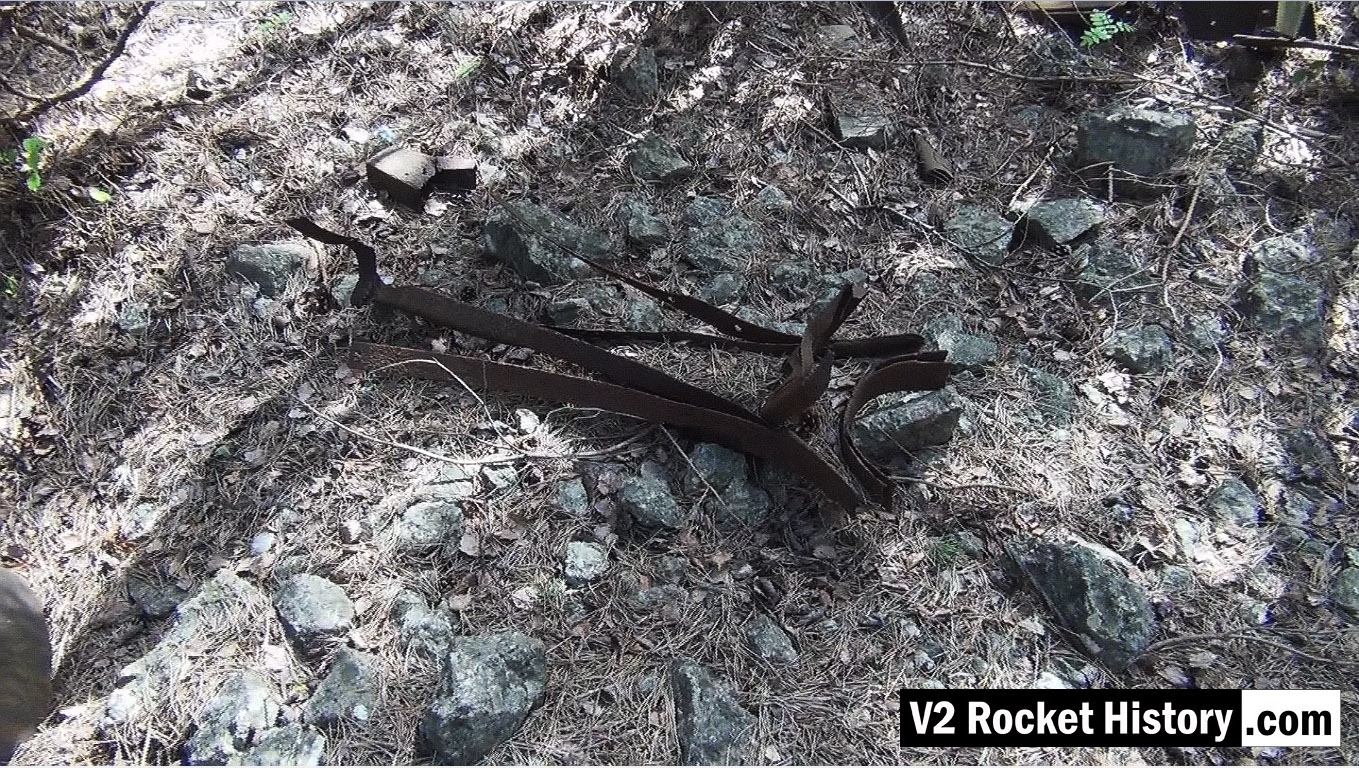
Picture shows parts of V2 missile fin structure laying on open ground near area between admin offices and F1 (near Admin. block railway platform, see map).

This picture shows a small debris field of steel fragments from the V2 missile 130m South-East of F1, and just 20m to the North East of the foundations of a small heat distribution building. Various body and frame parts can be seen and in the middle foreground a 350mm segment of curved missile body ring is visible. These parts have almost certainly been dug up and exposed by the action of metal detectorists. The metal fragments have been abandoned by their finders as they are perceived to have no financial value and hence are not worth removing from the site.
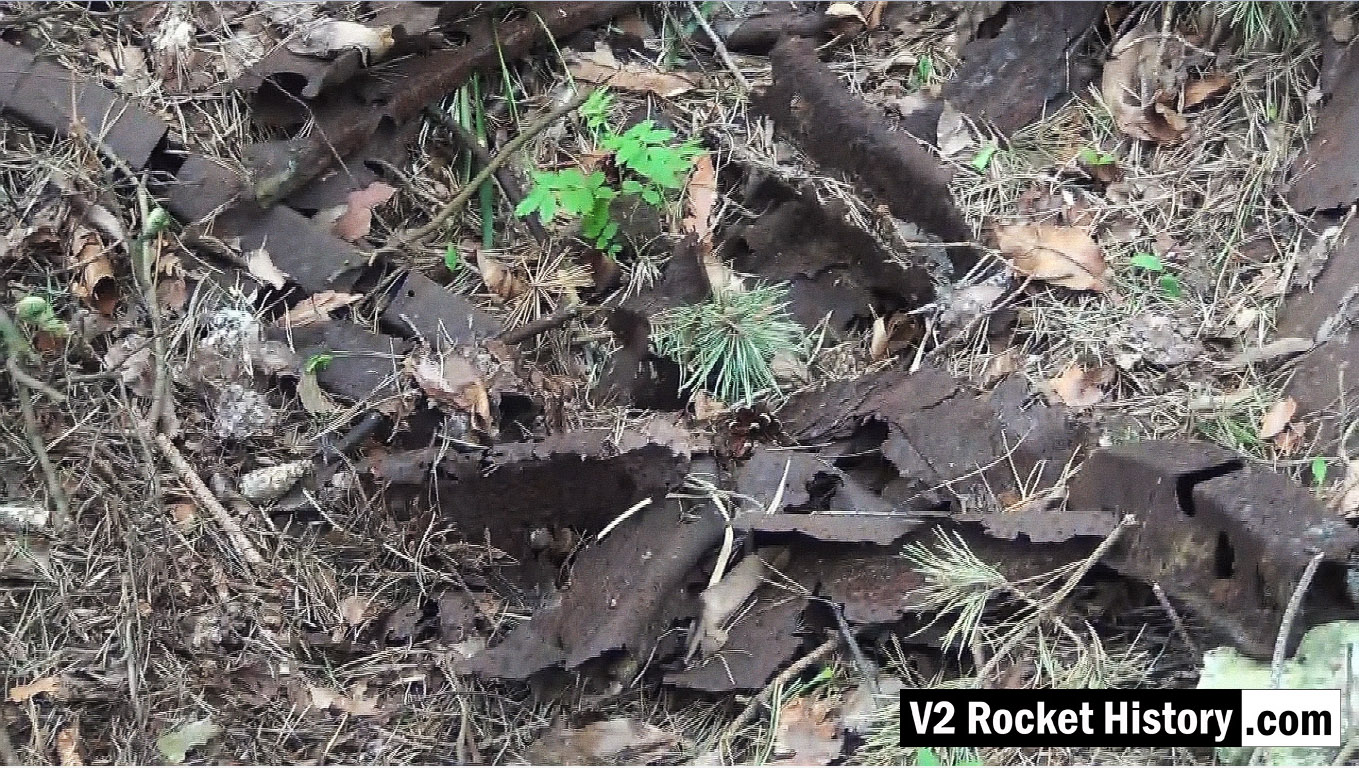
This picture shows a close up detail of parts in a small debris field of steel fragments from the V2 missile 130m South-East of F1, and just 20m to the North East of the foundations of a small heat distribution building. Various body and frame parts can be seen and in the upper left and two segments of curved missile body ring are visible. See previous.
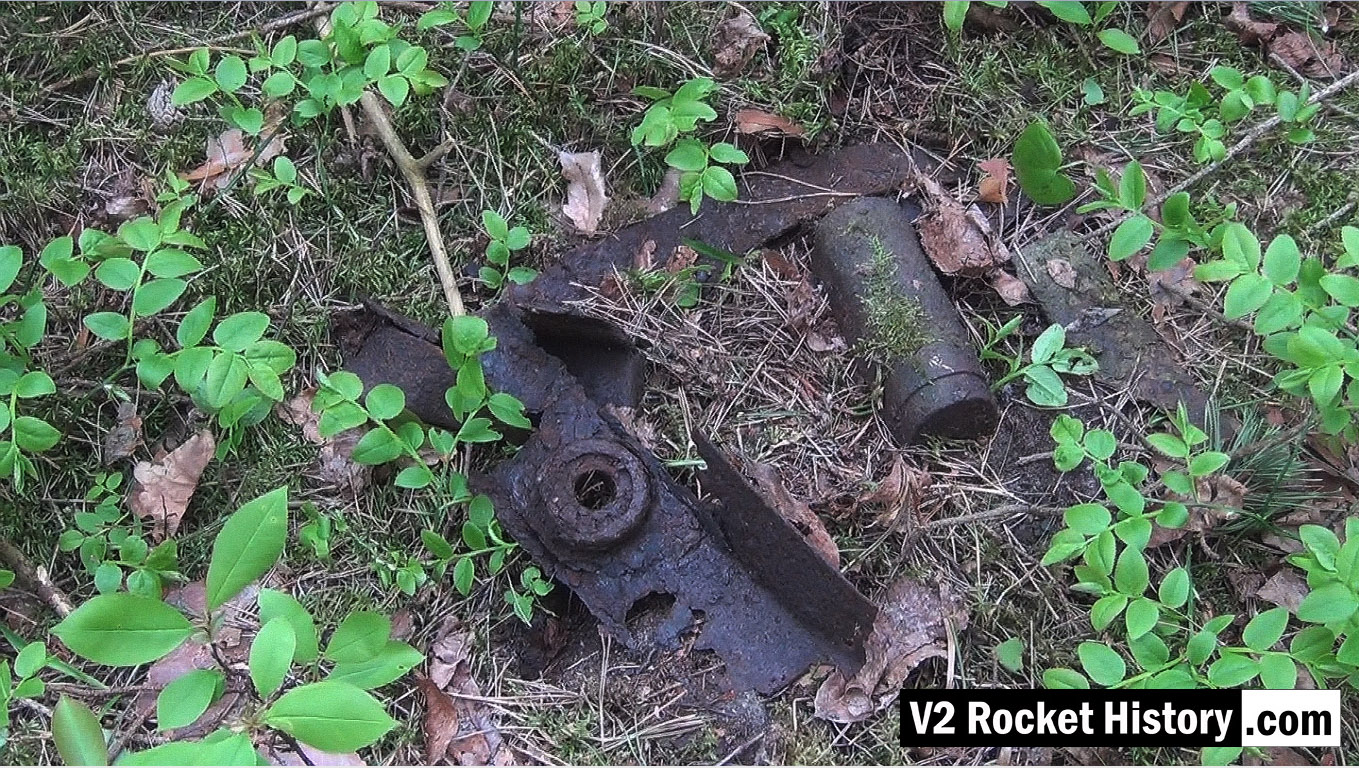
V2 missile parts in F1 prisoner turn-out or ‘free movement’ area. The location referred to is a large triangular shaped area situated on the South-East side of the pre-propuction hall Fertigungshalle Eins (F1). The area was fenced off with a high barbed wire fence (a portion of which was electrified) with guard towers every 60 metres.
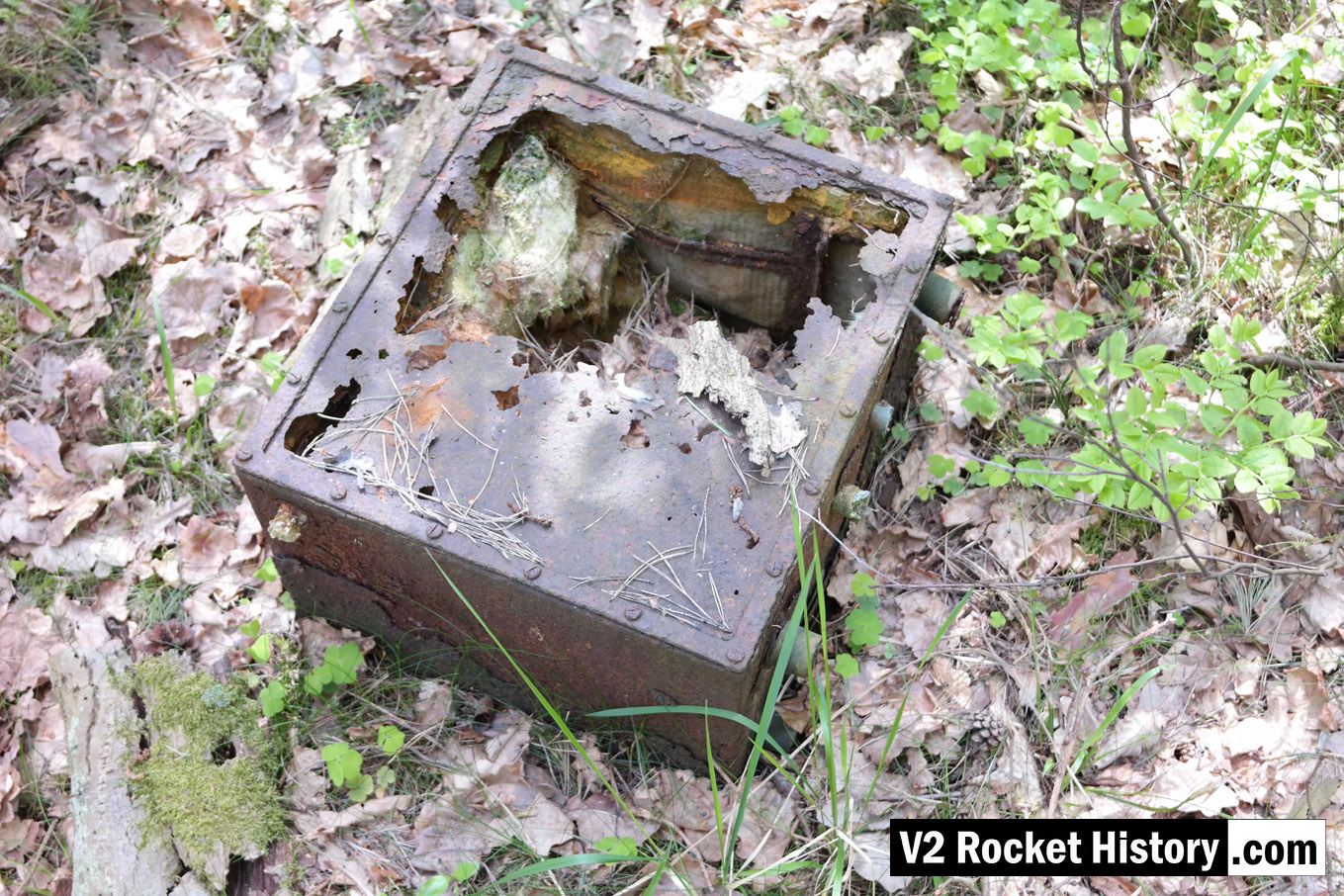
The photo shows a Lichtstrahl empfänger (In English: Light-beam receiver) environmental protection case, originally one of a group of 40 or so we first found in 2010 abandon in an area adjacent to the train platform for the administration block. On subsequent visits this number has declined to just ten or so, mostly very decayed examples. The environmental casing was vital to the Lorentz Light-Beam equipment on-board the V2 missile as the critical radio frequency would otherwise drift with the large change in temperature as the missile climbed into the stratosphere. The case was thickly insulated with rock wool or fibre-glass strands and designed to help maintain a stable temperature – indeed, the same temperature as the radio equipment was when at ground level when calibration and adjustment was completed before launch. The F1 pre-production hall is located about 200m North-West of the point where this photo was taken. Scroll down to see map below (click map and switch to ‘satellite view’ for clearer indication of location).
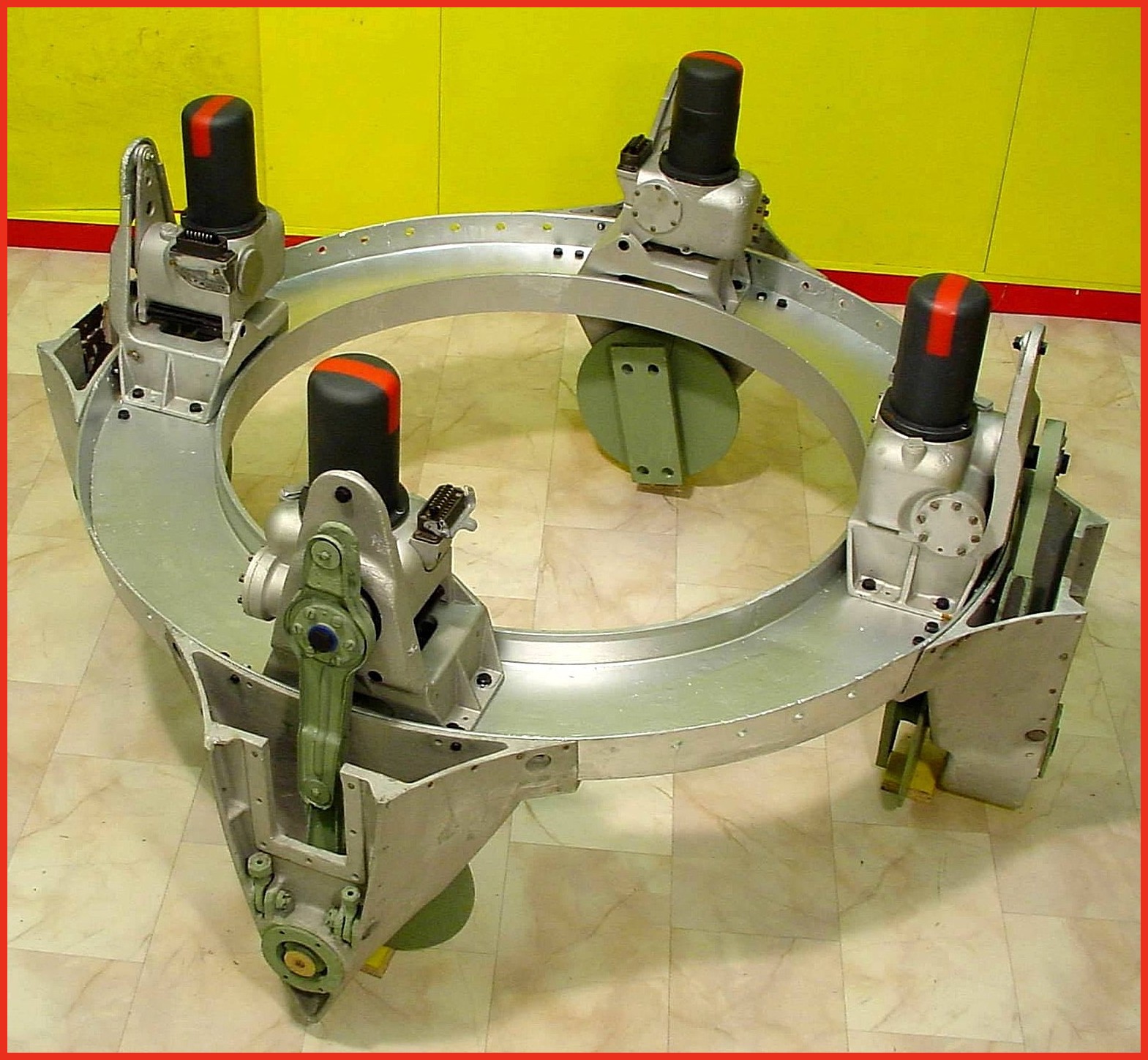
Photo shows cast aluminium thrust ring with electro-hydraulic servos in position. Note different crank lever shapes (pale green arm on servo) for fins 1/3 and 2/4 This excellent restoration is the work of Horst Beck. Photo copyright: The Horst Beck Collection
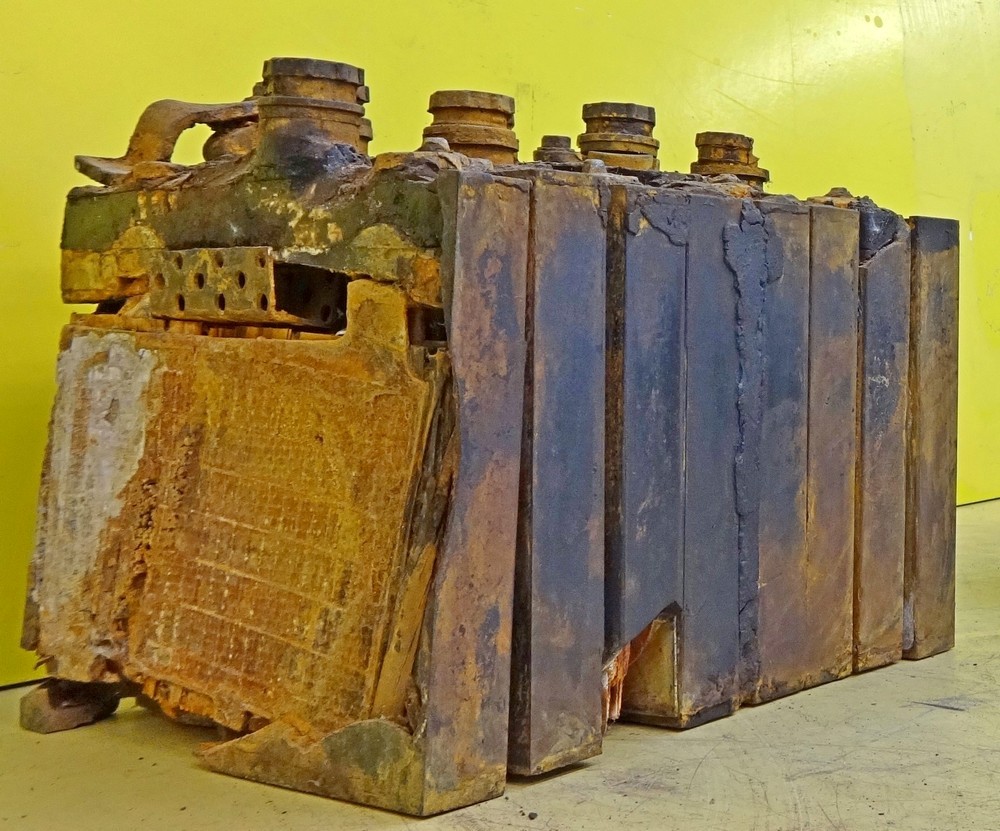
Photo shows rare surviving complete set of 8 lead acid battery cells from one of the V2 rocket’s 32 volt (100 amp) lead acid batteries. Two sets of batteries like this were used to provide the direct current (DC) voltage used aboard the V2 missile to power the DC to 3-phase alternating current (AC) generators, that in turn, powered the gyroscopes, electro-hydraulic servos, trim motors and other vital guidance and control devices. Photo copyright: The Horst Beck Collection
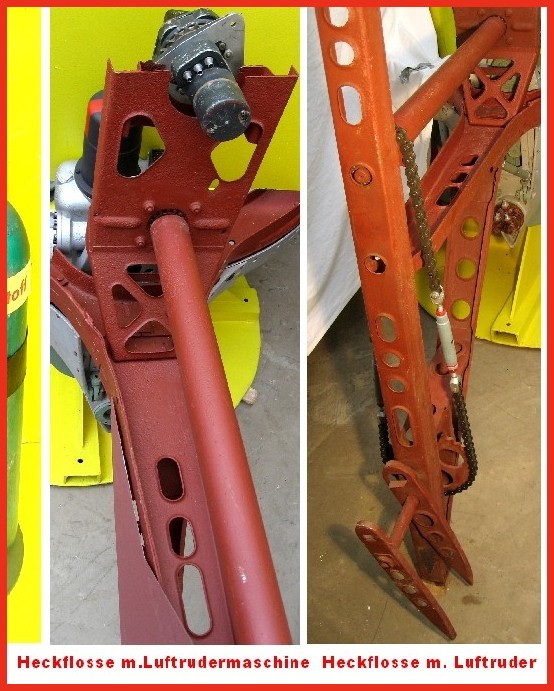
Photo shows partially restored air-rudder and fin detail. The image on the left shows the relationship of the trim motor to the air rudder drive shaft on fins 2 and 4. A chain similar in gauge to the type used on a push-bike and yet, at the other end of the shaft, the chain transmitting the torque of the trim motor to the air-rudder drive sprocket has a heavy gauge chain similar to that found on a 1000CC motor-cycle! This excellent restoration is the work of Horst Beck. Photo copyright: The Horst Beck Collection
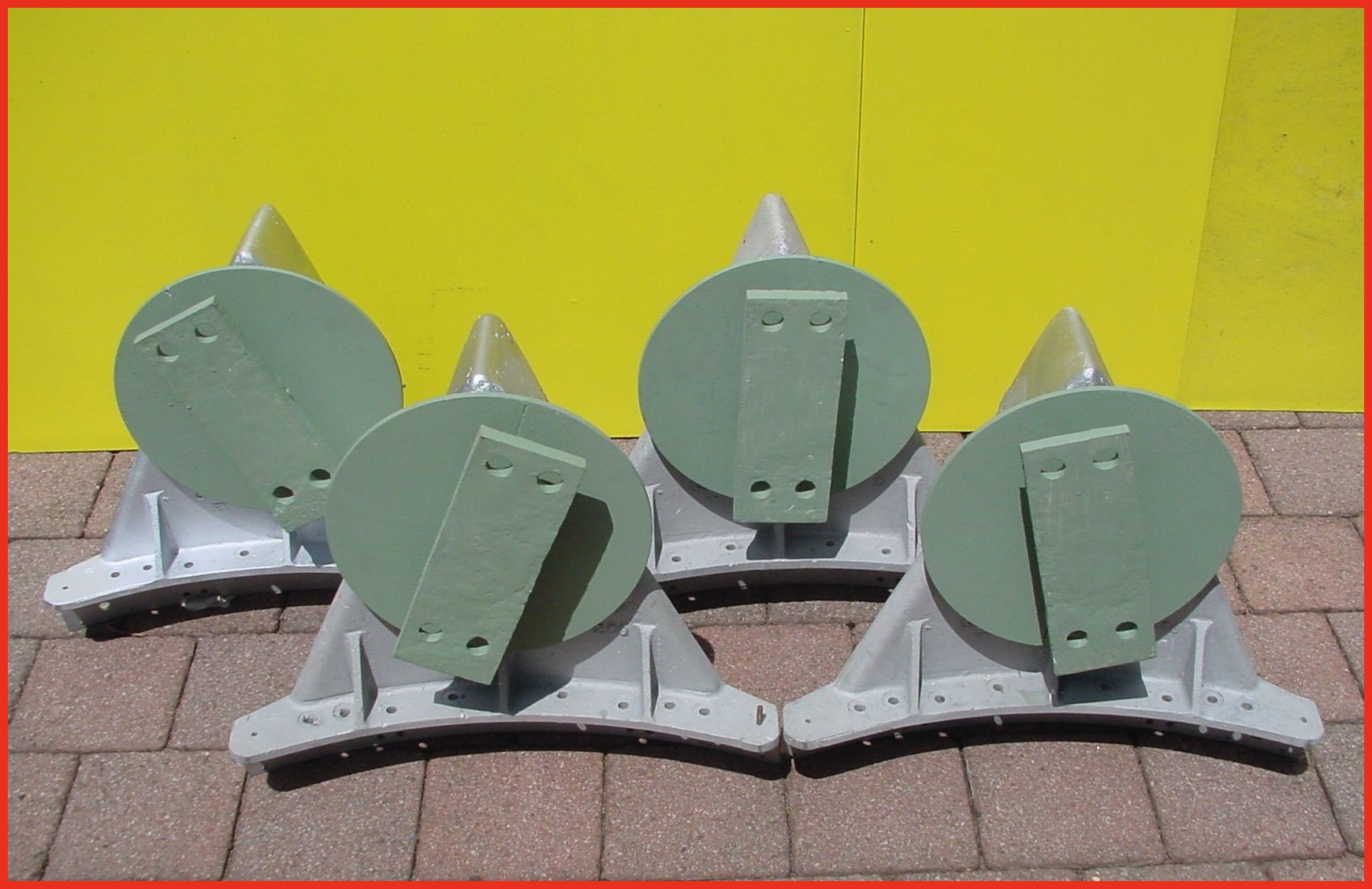
Photo shows four restored graphite jet vane support blocks and bearing housings. The round plates we can see here act as heat sinks and allow heat to radiate away from the support block and bearing to help prevent expansion due to relatively rapid and uneven temperature distribution accumulation. The graphite vanes were quite brittle and cracking caused by rapid and uneven expansion could cause the vane to disintegrate. The area around the graphite vanes was exposed to the accumulation of heat not merely as a result of duration of the motor burn time but temperature was also increased at higher rates as the jet plume expanded with the decreasing atmospheric pressure as the missile gained altitude. This excellent restoration is the work of Horst Beck. Photo copyright: The Horst Beck Collection
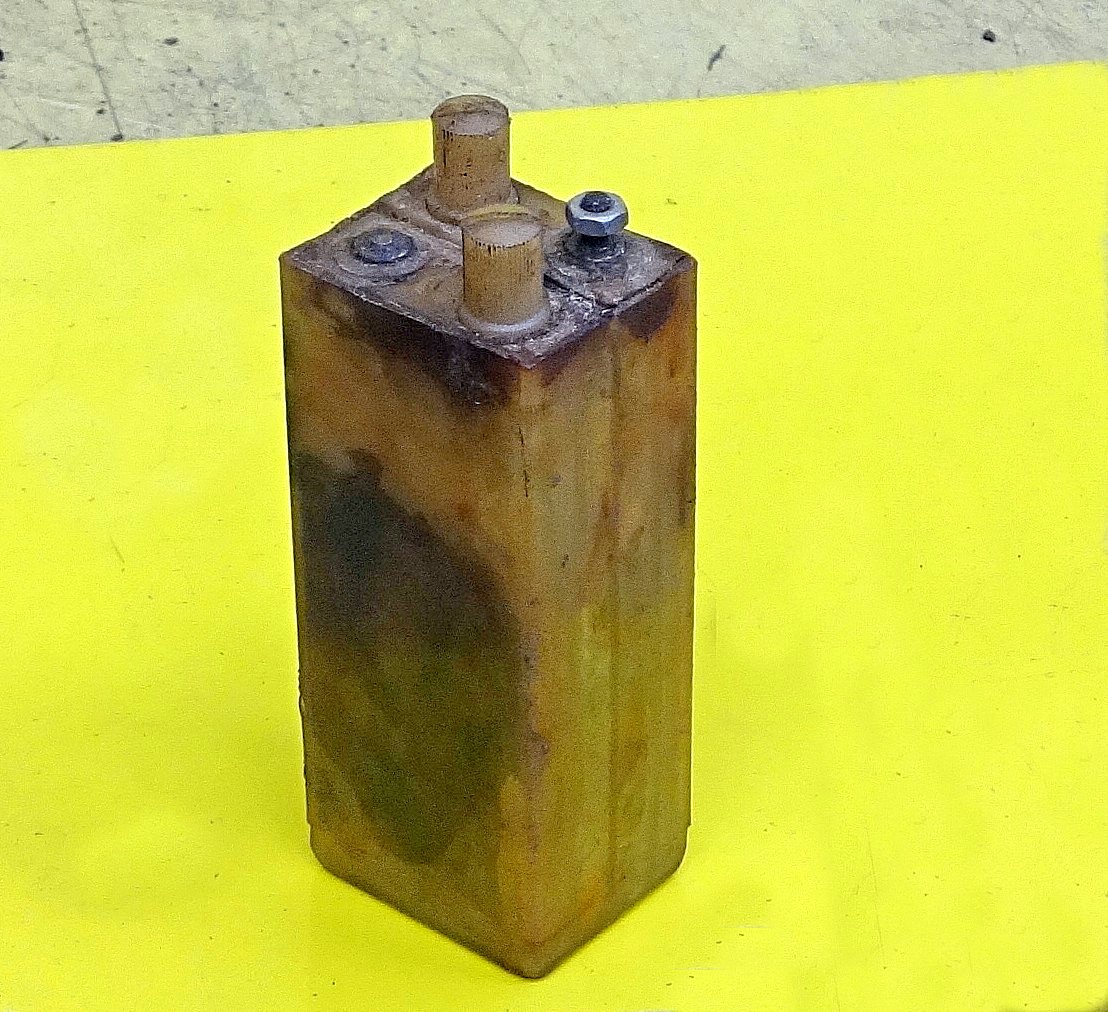
Photo shows rare surviving 1.2 volt cell from the V2 missile’s 50 volt command or signalling battery used in its gyro guidance system (note, the terminal connection on the left is missing from this exhibit, it would be identical to the one on the right). This wet nickel-cadmium battery cell was combined in pairs to a total set of 21 providing a 50.4 voltage at 300mA. The cells were contained in a wooden box that was held on a rack in equipment bay III. Its function was to provide the direct current (DC) signalling voltage that communicated the moment to moment resistance of the gyroscope’s potentiometers to the analog guidance computer (Mischgerät = Mixer-device or control amplifier) aboard the V2 missile. It was critical that the signalling voltage was maintained between 48 and 50.4 volts. Photo copyright: The Horst Beck Collection
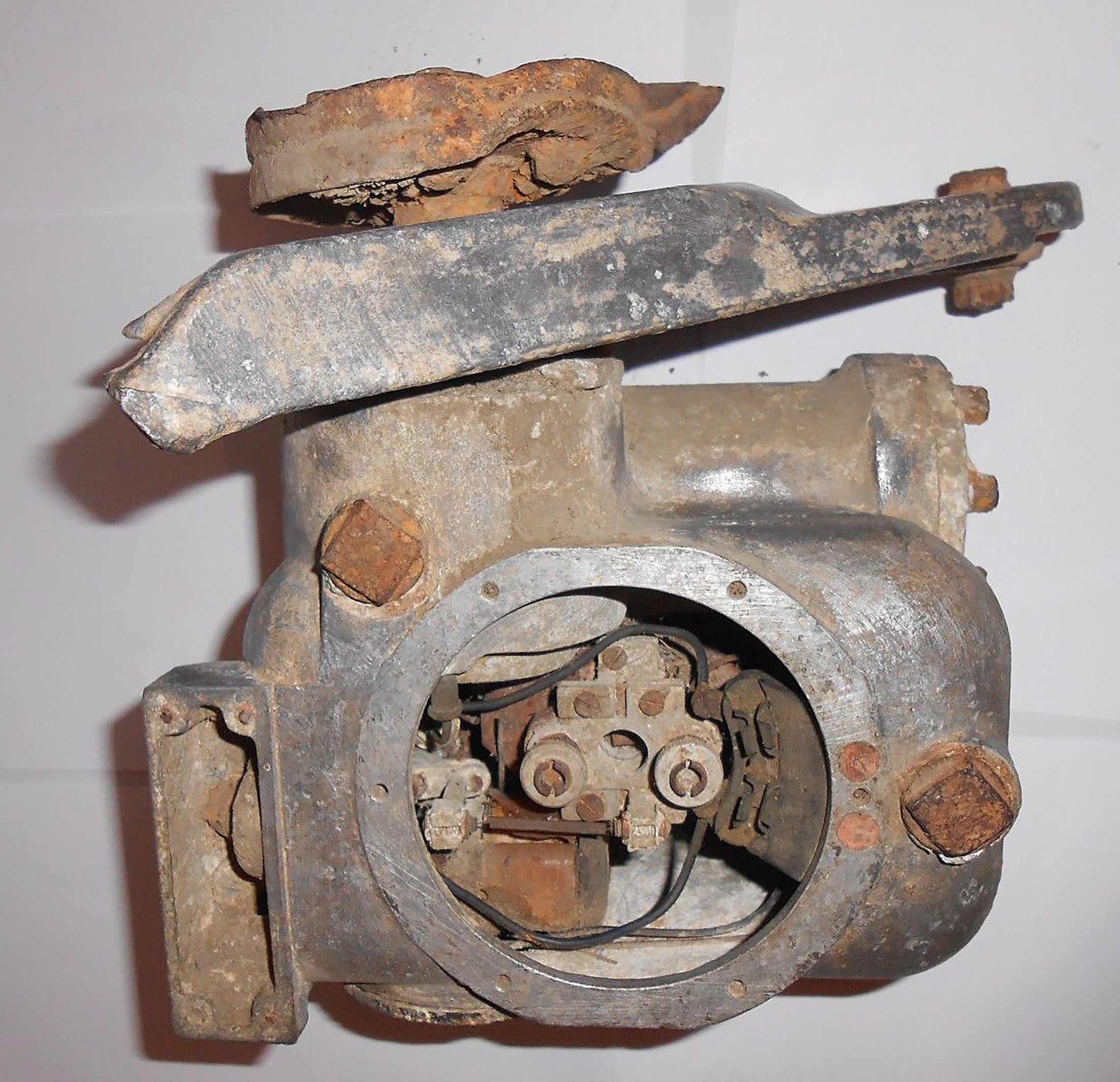
Wreckage of hydraulic servo from fin 2 or 4 of V2 missile that fell on a farm in Essex in March 1945. The motor has been removed and we can see details of the oil gear pump and valve control gear. The 3 position electromagnetic relay switch is visible at the 7 to 8 o’clock position within the open aperture. The push rod that connects the relay to the gear pump valves is also visible as a short brown coloured rod with a fine wire connector at each end, running in towards the gear-valves from the 9 o’clock position. The point that provides electrical current for the motor (which runs all the time and in one direction only) can be seen at the three o’clock position. The black housing has two sets of brass tongues that receive the matching brass spades mounted on the base of the motor for power input. The motor drive shaft has a female square socket coupling to connect the motor to the middle drive gear of the gear pump. A small portion of the square drive shaft of the central gear can just be seen in the photo – in the centre of the valve control block.
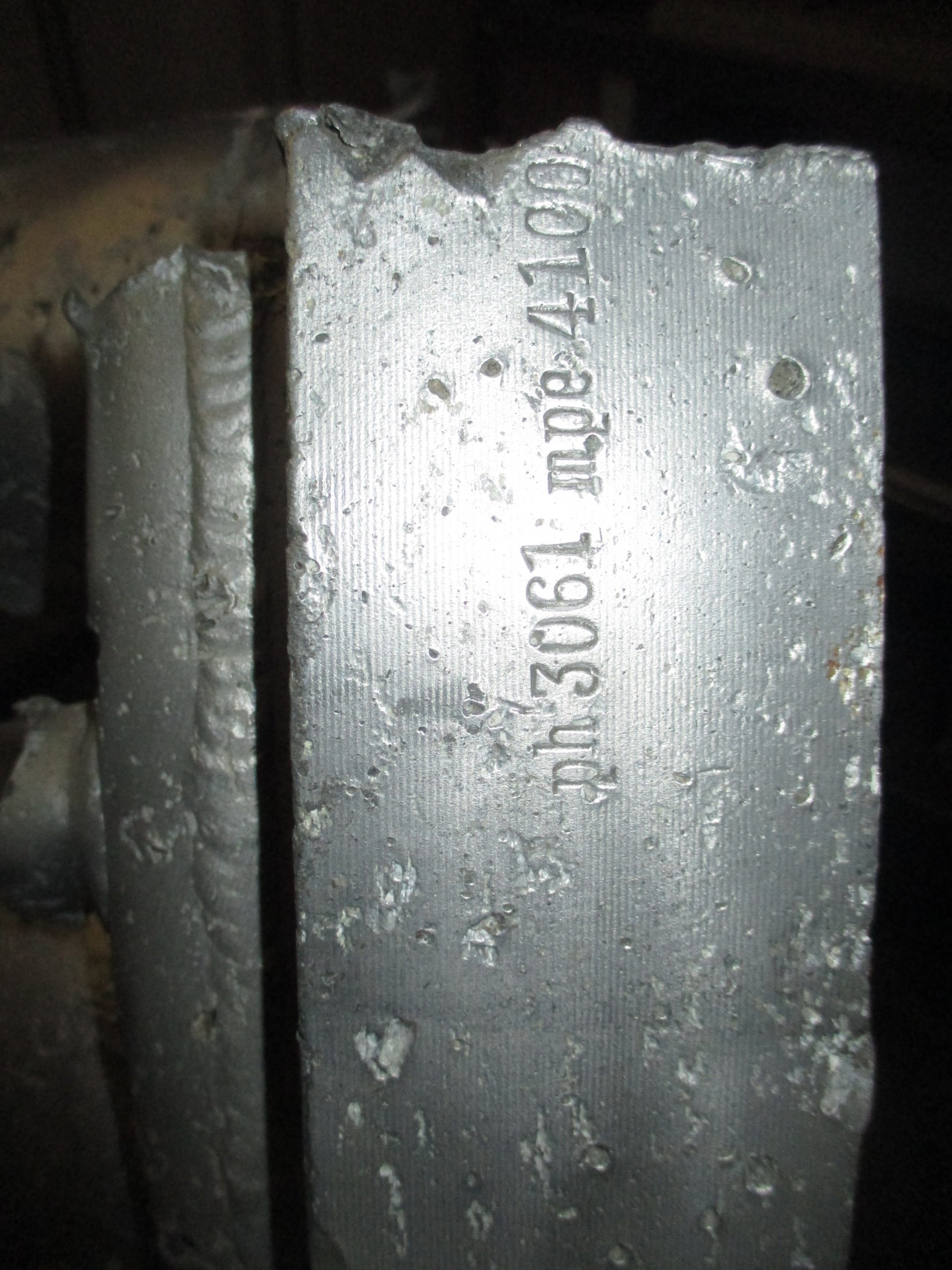
25-Ton aluminium injector head showing mpe armament code for the Heimat-Artillerie-Park 11 (HAP11) Karlshagen Werk Nord.
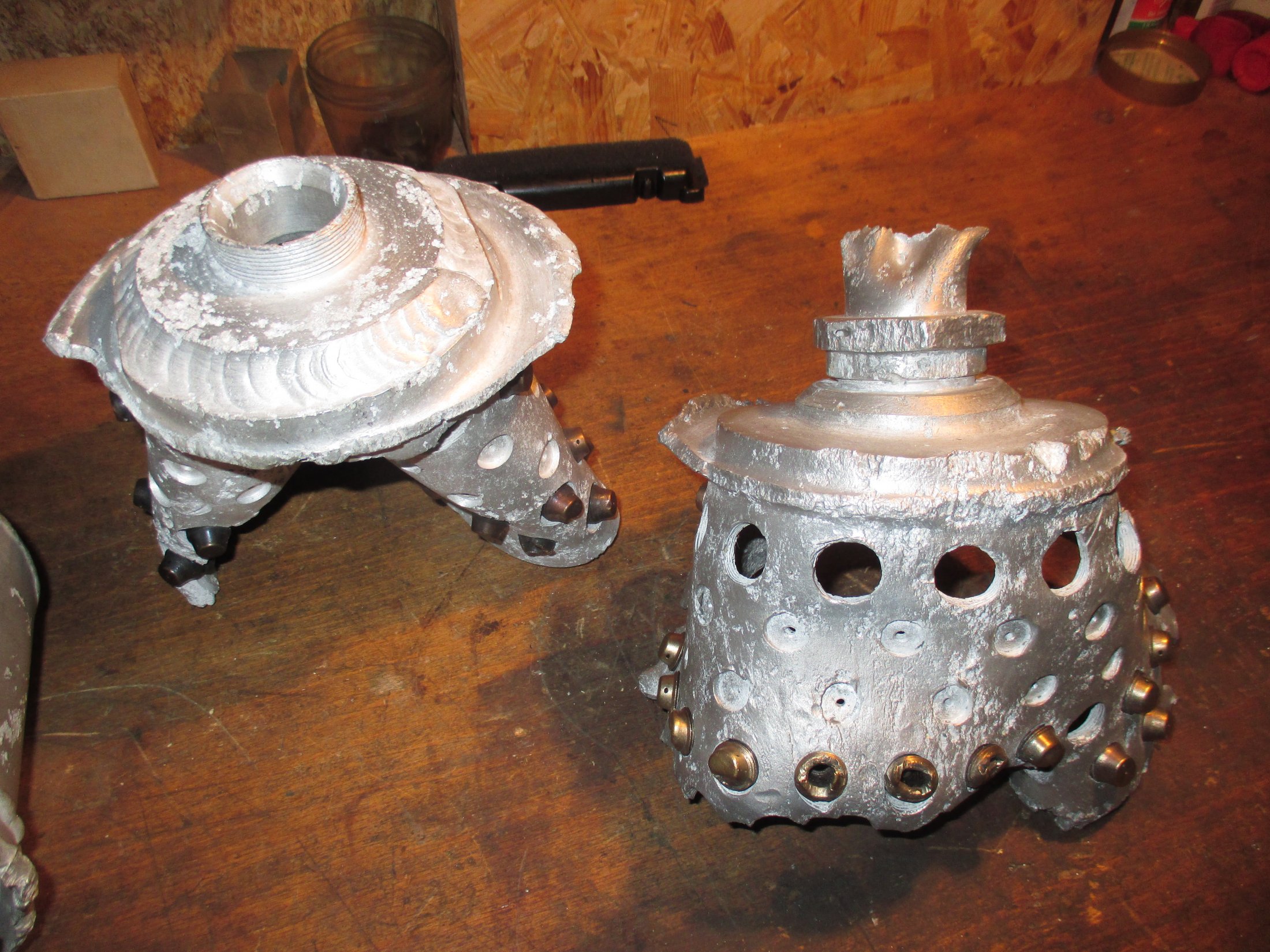
Relics of the A4 25-ton 1941 aluminium injector head. See other photos in this series for more detail. Photo courtesy Horst Beck Collection
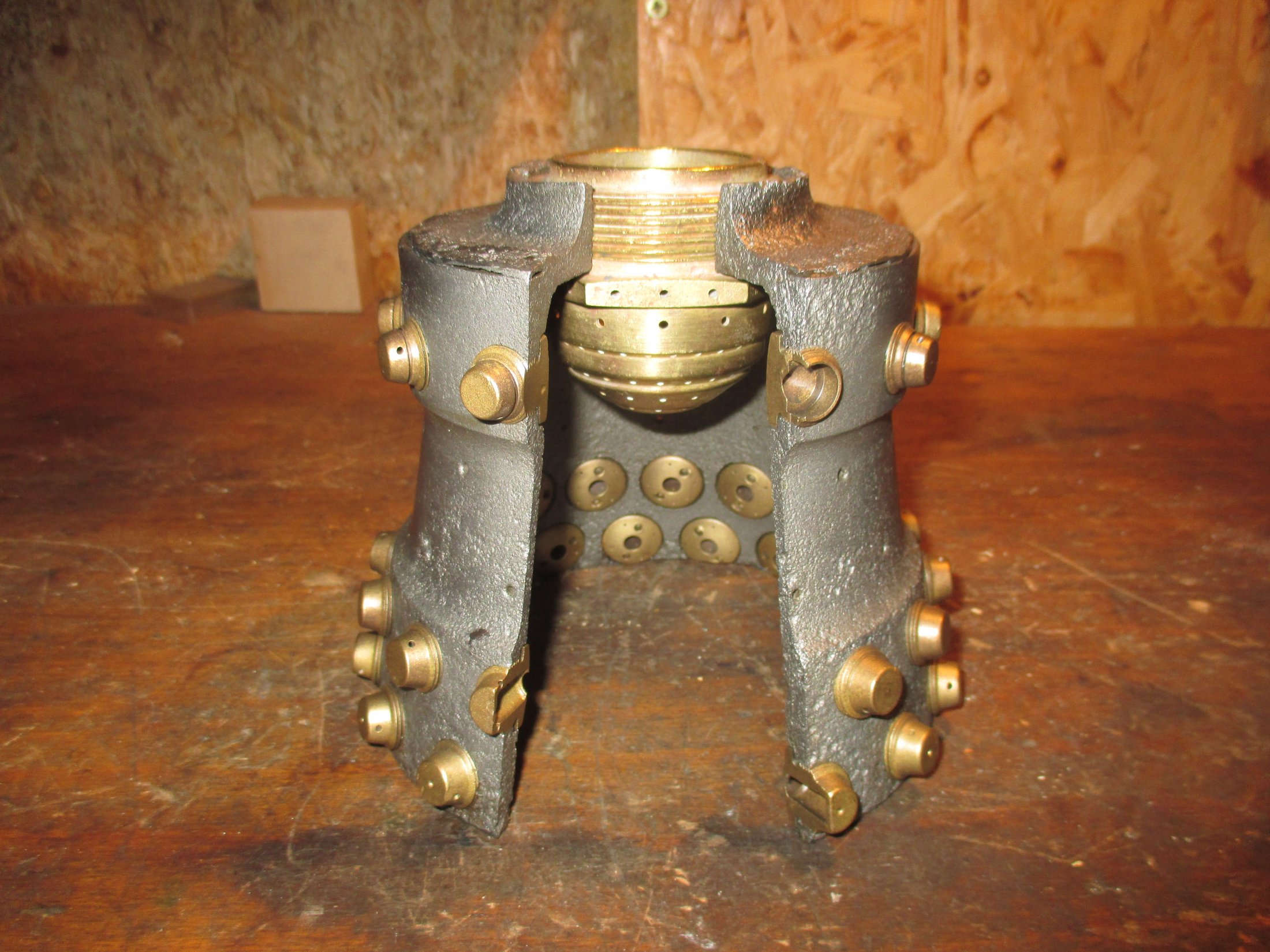
Part of the ‘Standard’ series A aluminium head from 1941 to early 1942. Showing the position of standard type LOX injector. The brass fuel injector inserts type and position pattern on the relic seem to be of the standard type with the row of 3 inlet aperture type inserts positioned furthest from the LOX injector. Photo courtesy Horst Beck Collection
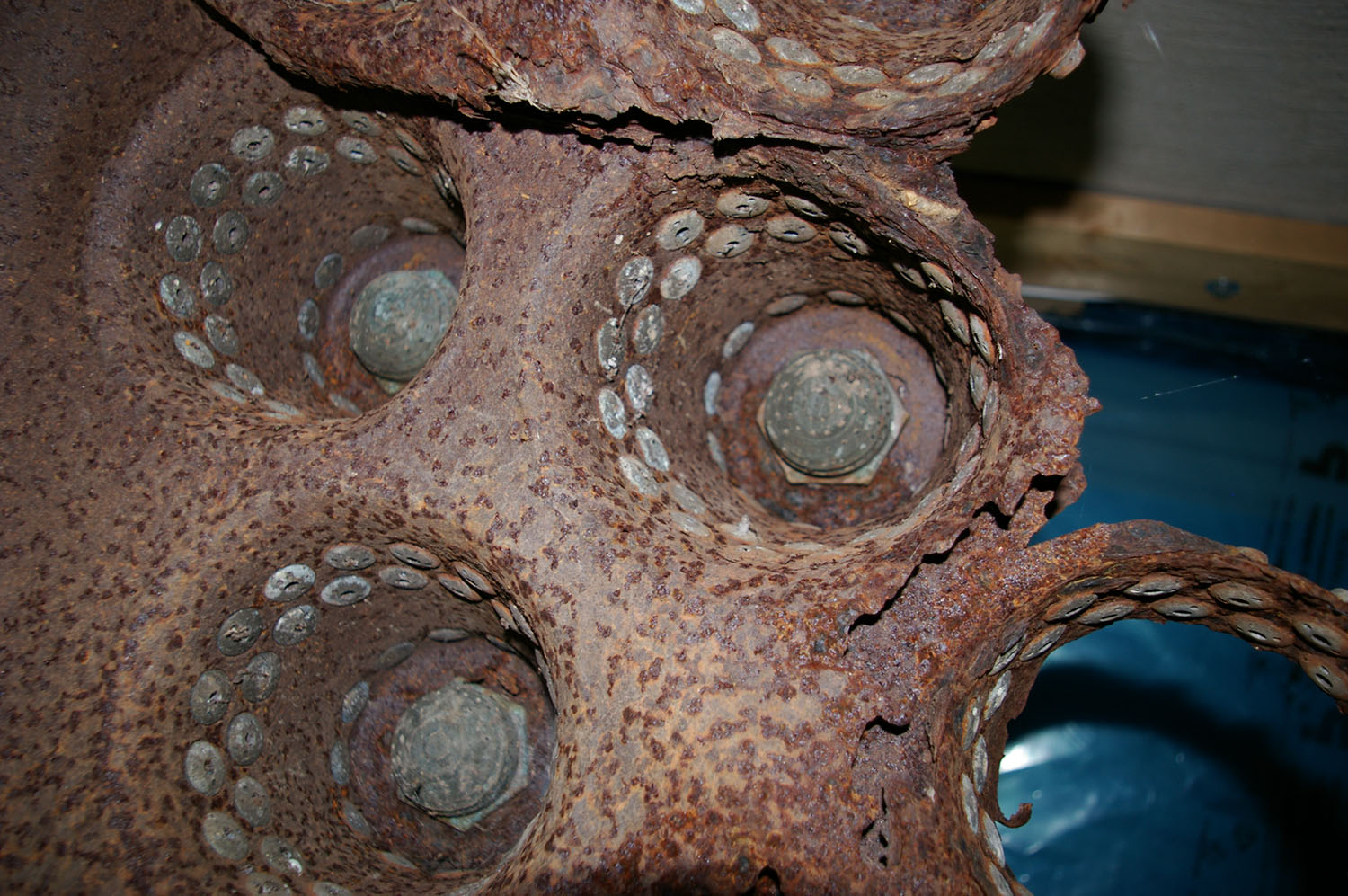
Injector head relic from February 1945 showing injector insert type and pattern. Photo www.v2rockethistory.com
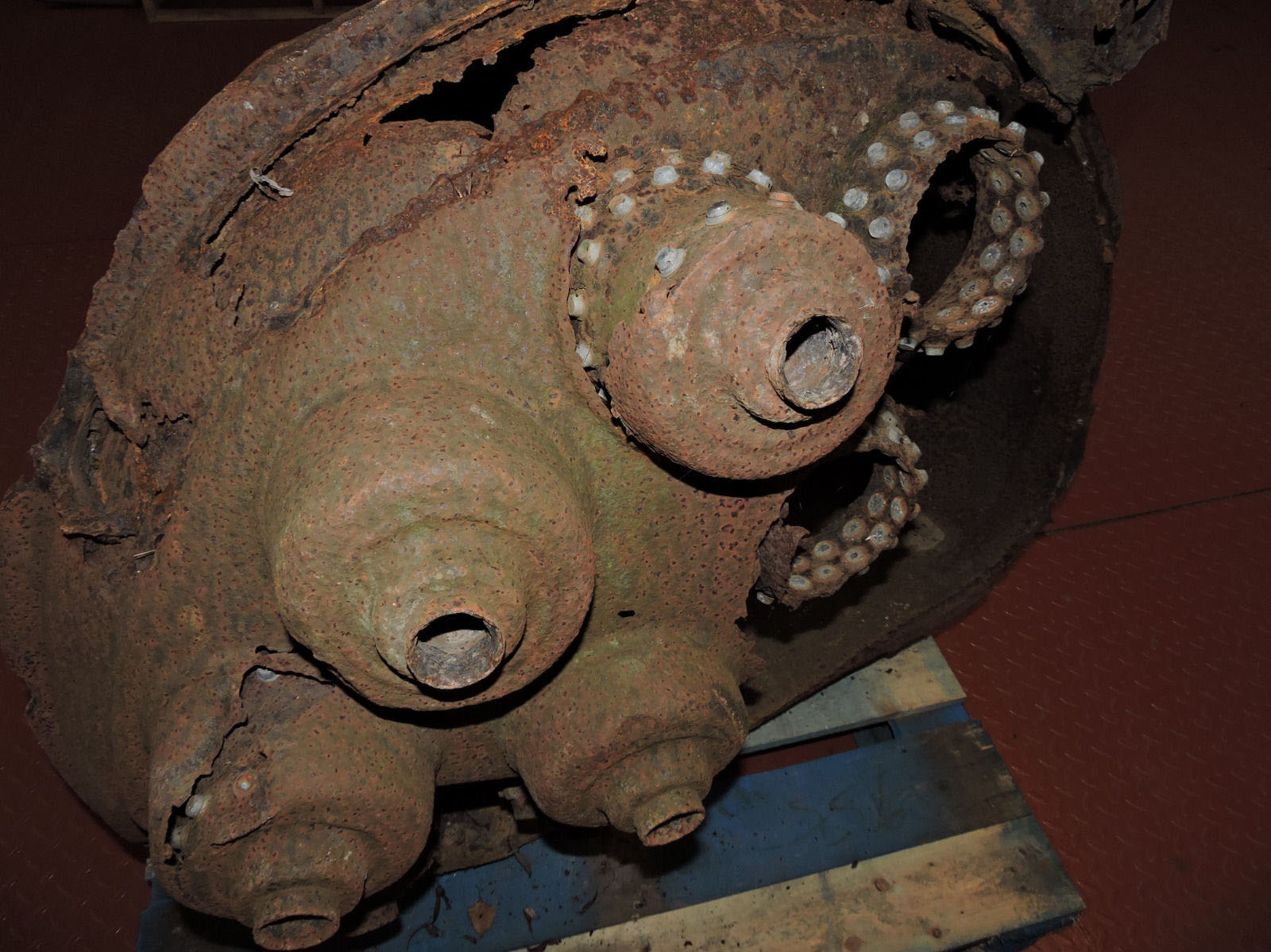
Flown V2 thrust chamber relic from February 1945. Badly damaged from impact, this head shows 4 intact LOX input pipe connections as well as exposed fuel injector inserts positioned in the inner wall of the injector pots. The inner and outer walls of the head are also conveniently exposed on this exhibit. Photo www.v2rockethistory.com
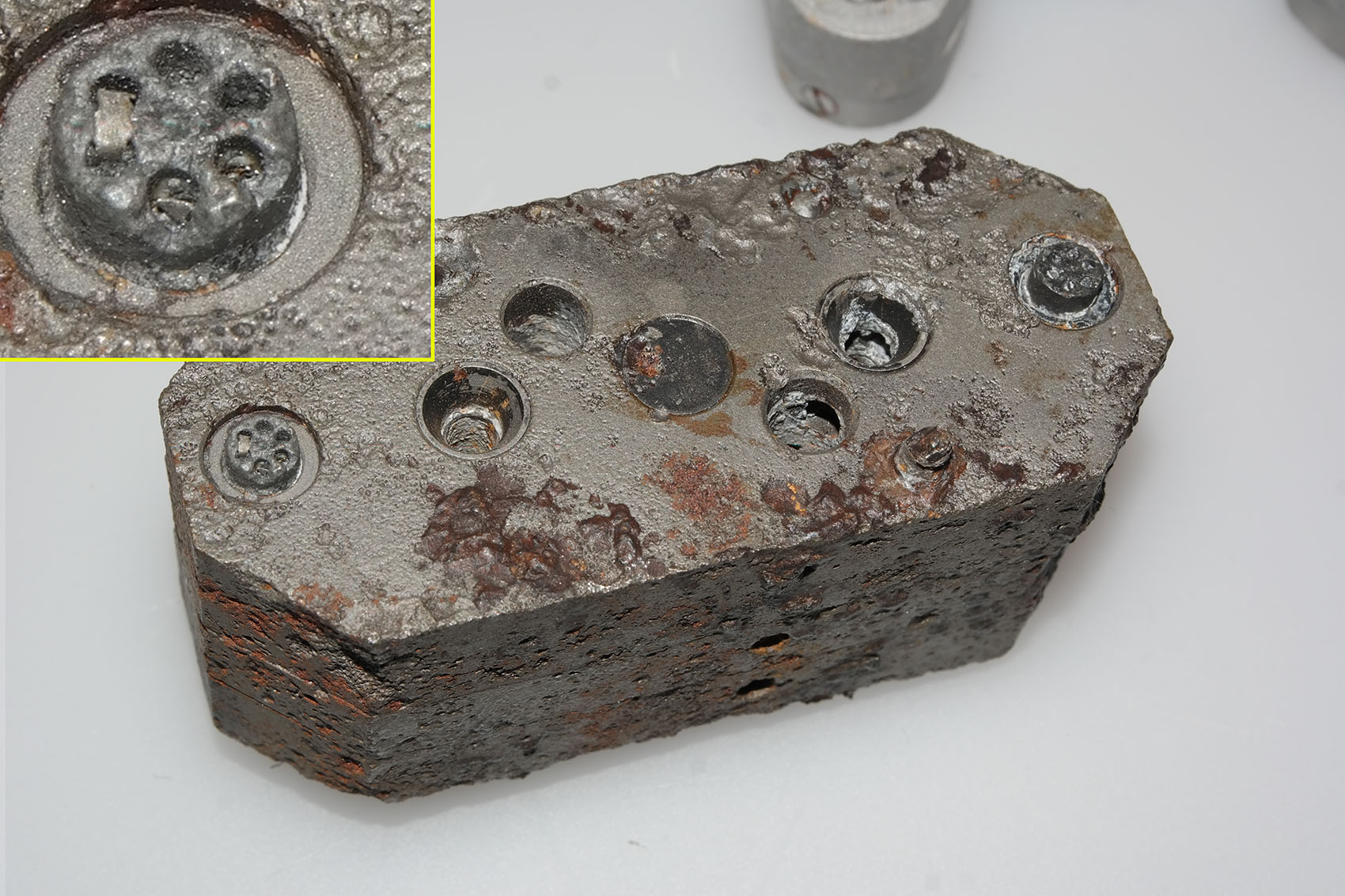
Hydraulic gear pump with close up detail showing ceramic heater element insulators with flat, possibly nichome, metal strip element threaded through them. This oil heating system was designed to maintain a specific viscosity of the oil regardless of environmental temperature, to better maintain oil flow rates and thus pump efficiency. The heating system is found only rarely on surviving relics.
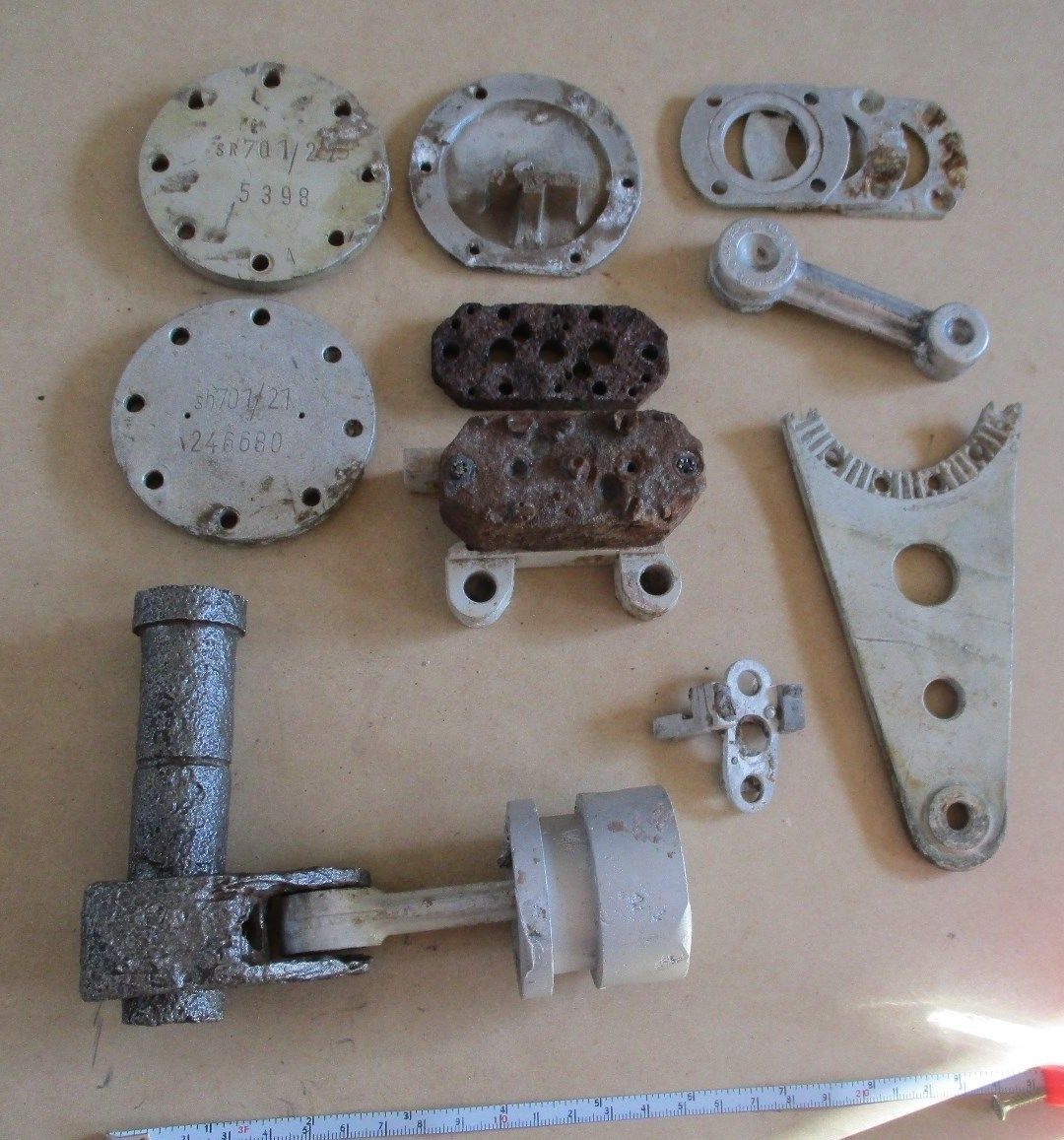
This collection of parts were all found in vicinity of the Nordhausen manufacturing facility. parts include servo crankcase caps -top left, electro-magnetic switch installation plate – middle top, crank bearing covers – top right, gear pump blocks with base – centre, and crank-shaft, piston rod, and hydraulic piston – btm left. The deep recess on the piston circumference is for a rubber seal and is an interesting variation in ring seal design (at least 4 variations of piston design were employed, with three designs flown on combat missiles). A valve tilt seat is visible a little to the right of the piston. A broken servo mount stabiliser is shown – middle right. The cast piston rod, top right, has not been drilled and milled – the part is ‘raw’ as supplied by the manufacturer before machining has been completed. Normally the manufacturer’s details are machined off the metalwork – but not in this rare case. The three letter code gfa is clearly visible on the part and stands for the firm of Otto Fuchs Metallwerke.
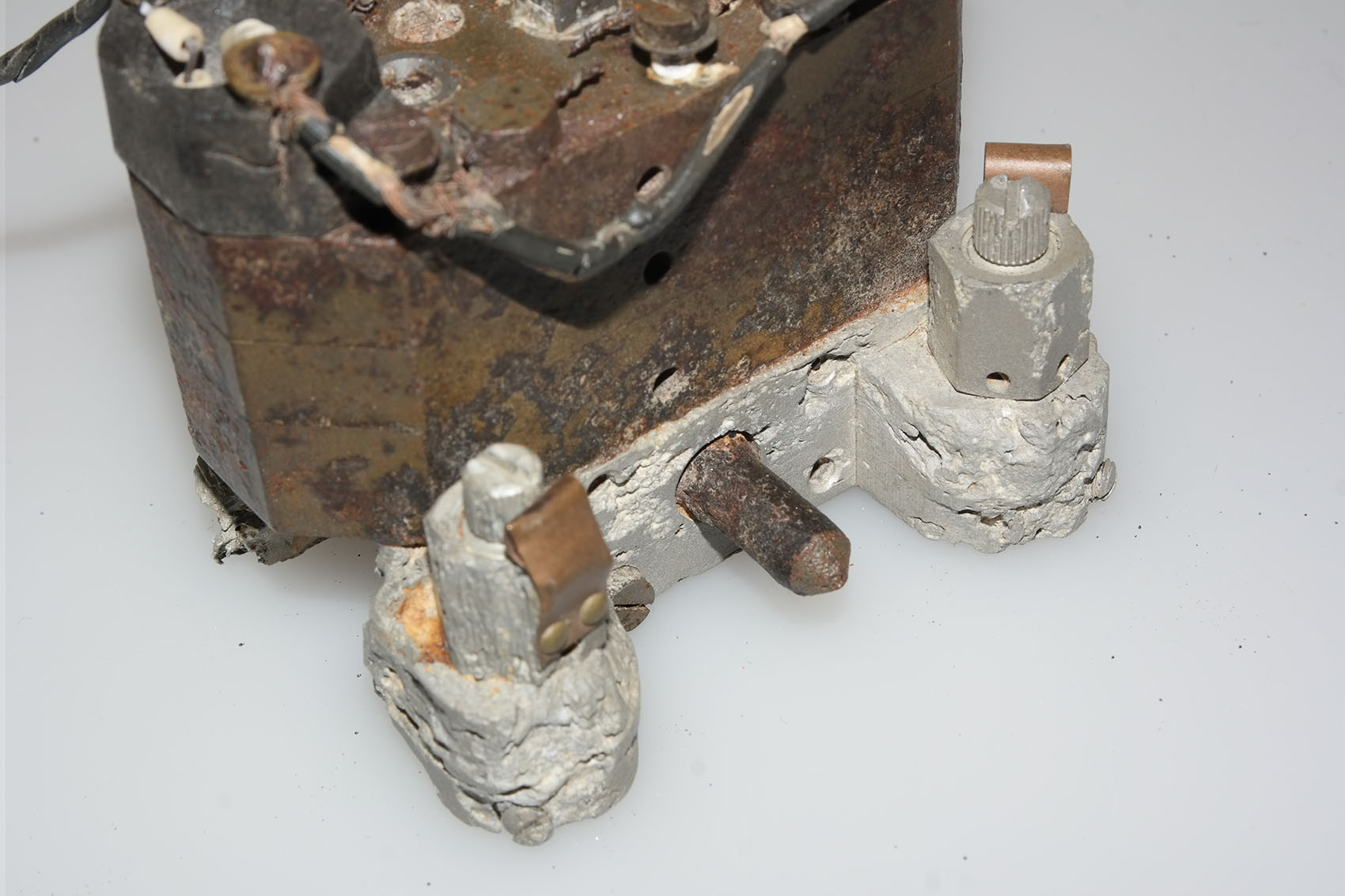
Close-up of Askania gear pump relic with oil heaters. This picture shows an unusual feature on the otherwise normal cast aluminium base of this gear pump. The knurled knob positioned between the oil flow balance adjusters has a purpose that is unknown to us. The two oil-flow balance adjuster valves visible in the picture have slot head adjuster screws and you can also see the knurled circumference on each screw. This parallel knurling is engaged by a crease formed in the facing surface of the copper spring strips. The function of these strips is to create tactile feedback that the technician making the adjustment can feel in the handle of the screwdriver. This was done because the gear pump needed to be adjusted in a dark and narrowly confined space.
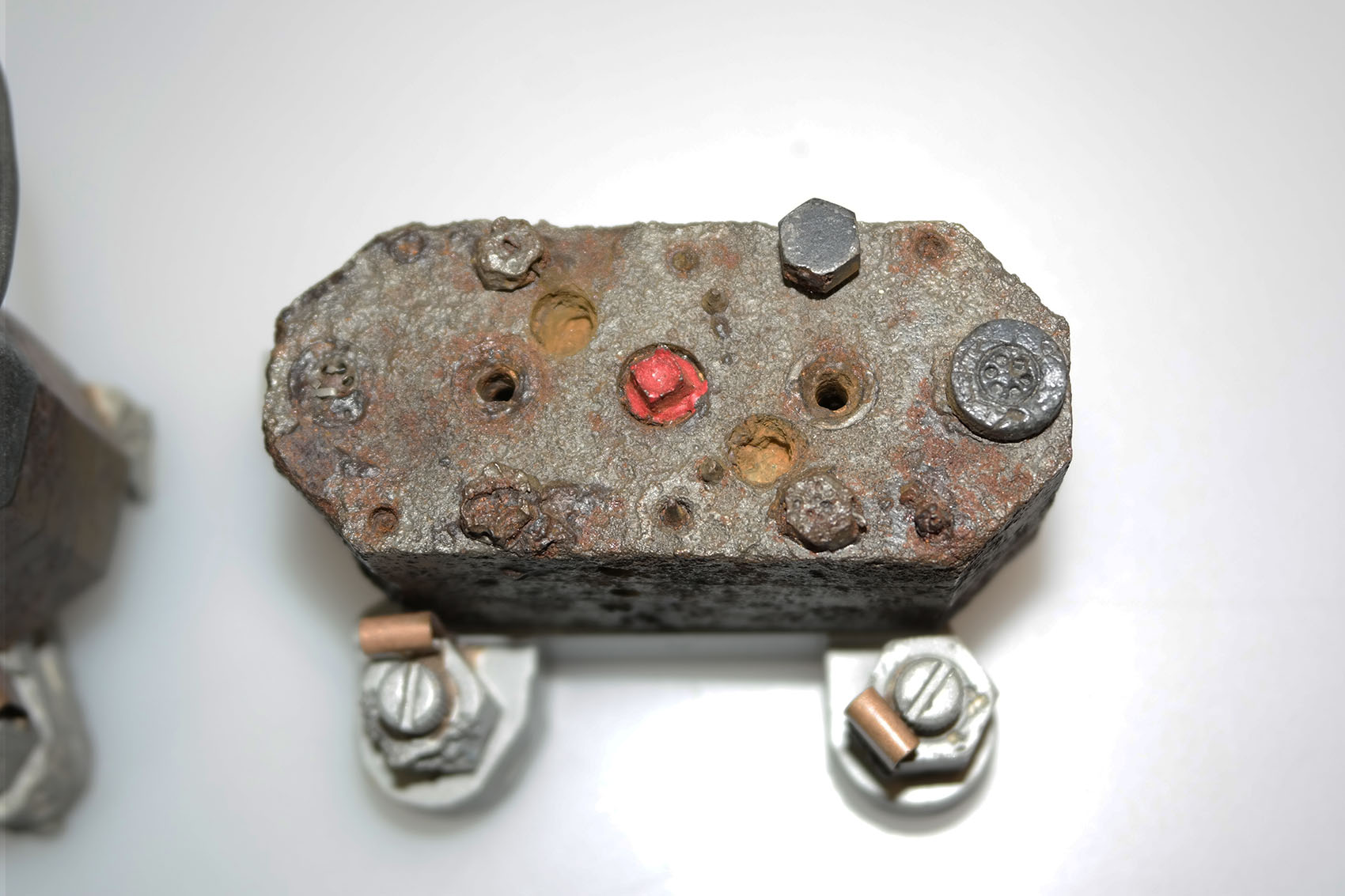
Gear pump showing flow adjusters (two slot head screws nearest bottom of picture) and ceramic heater elements situated at each end of the block. The square drive shaft coupler (corroded but still identifiable) has been highlighted in red paint. The open holes either side are the main control valve guides. The copper spring strips visible on each oil flow adjuster provide locking and tactile feed-back for the adjusting process. This relic was recovered from Usedom island.
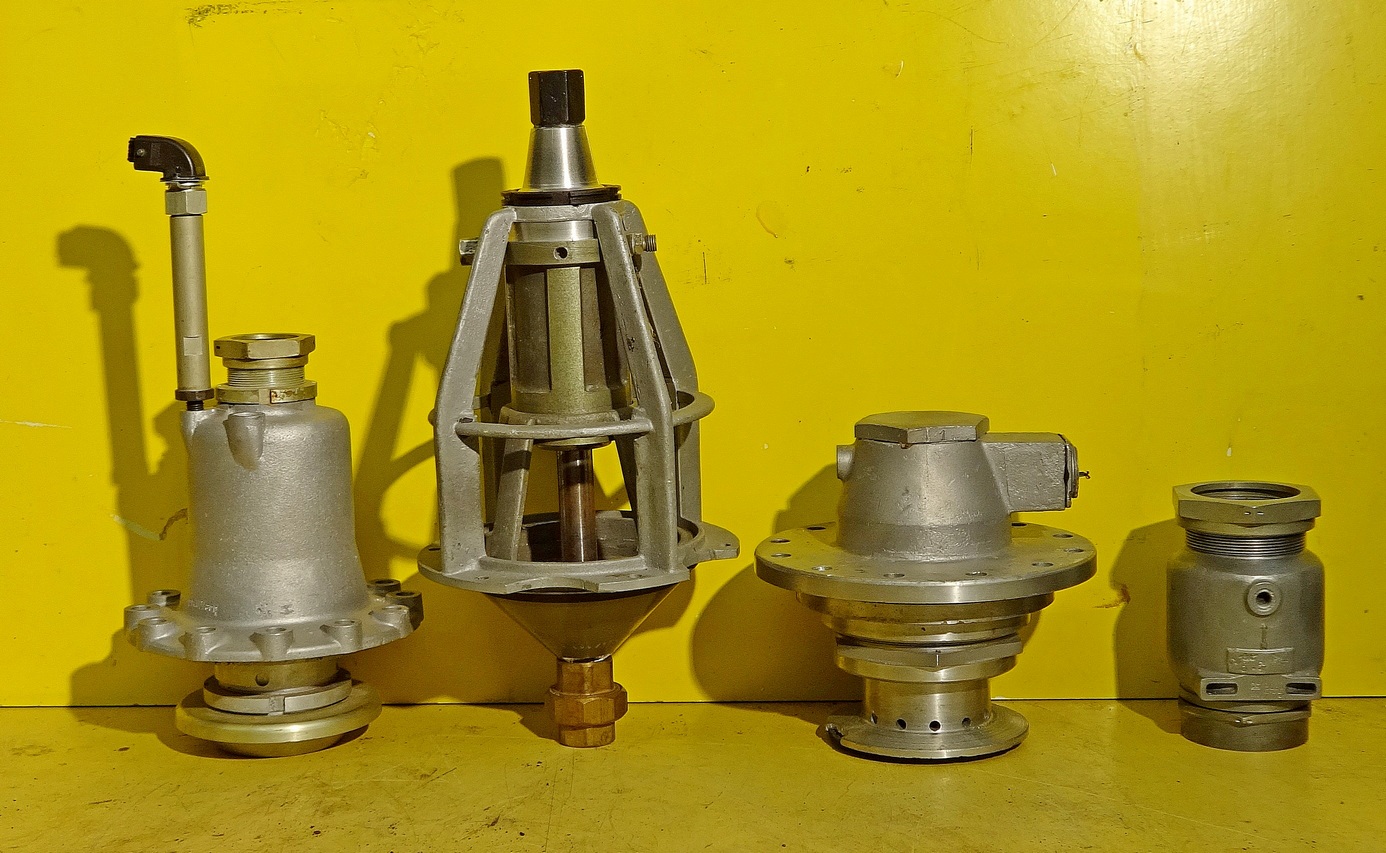
Photo shows main valves. Photo copyright: The Horst Beck Collection
Album | Valves |
Category | V2 Missile relics |
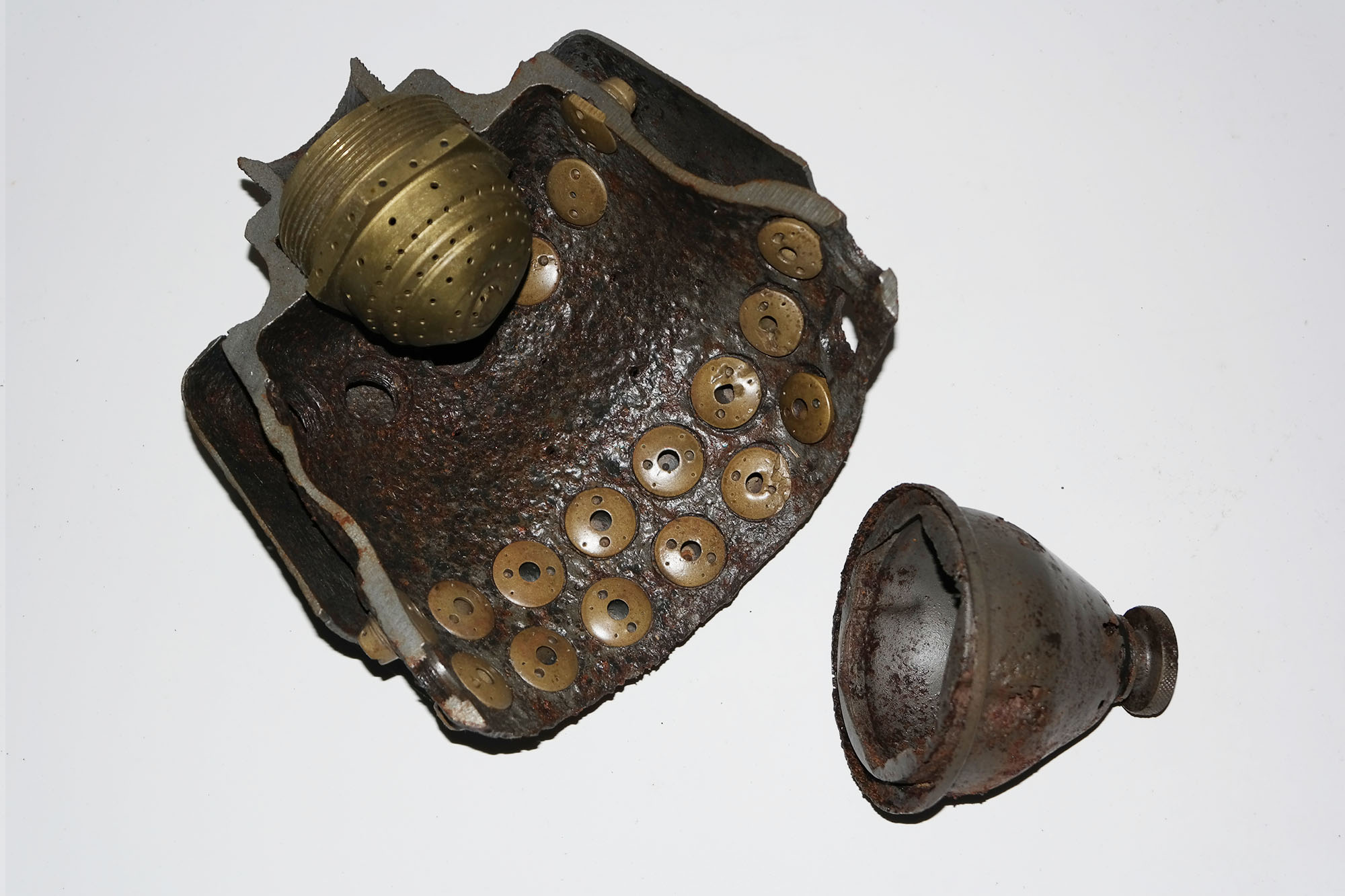
V2 Rocket History Museum Relic: This cutaway presentation shows one of the V2’s 18 combined fuel and liquid oxygen (LOX) injector ‘pots’. The LOX injector transit cap is also shown. The pot shown here is sometimes incorrectly referred to as a pre-burner or pre chamber – a mixer or diffuser pot probably describes its role more accurately.
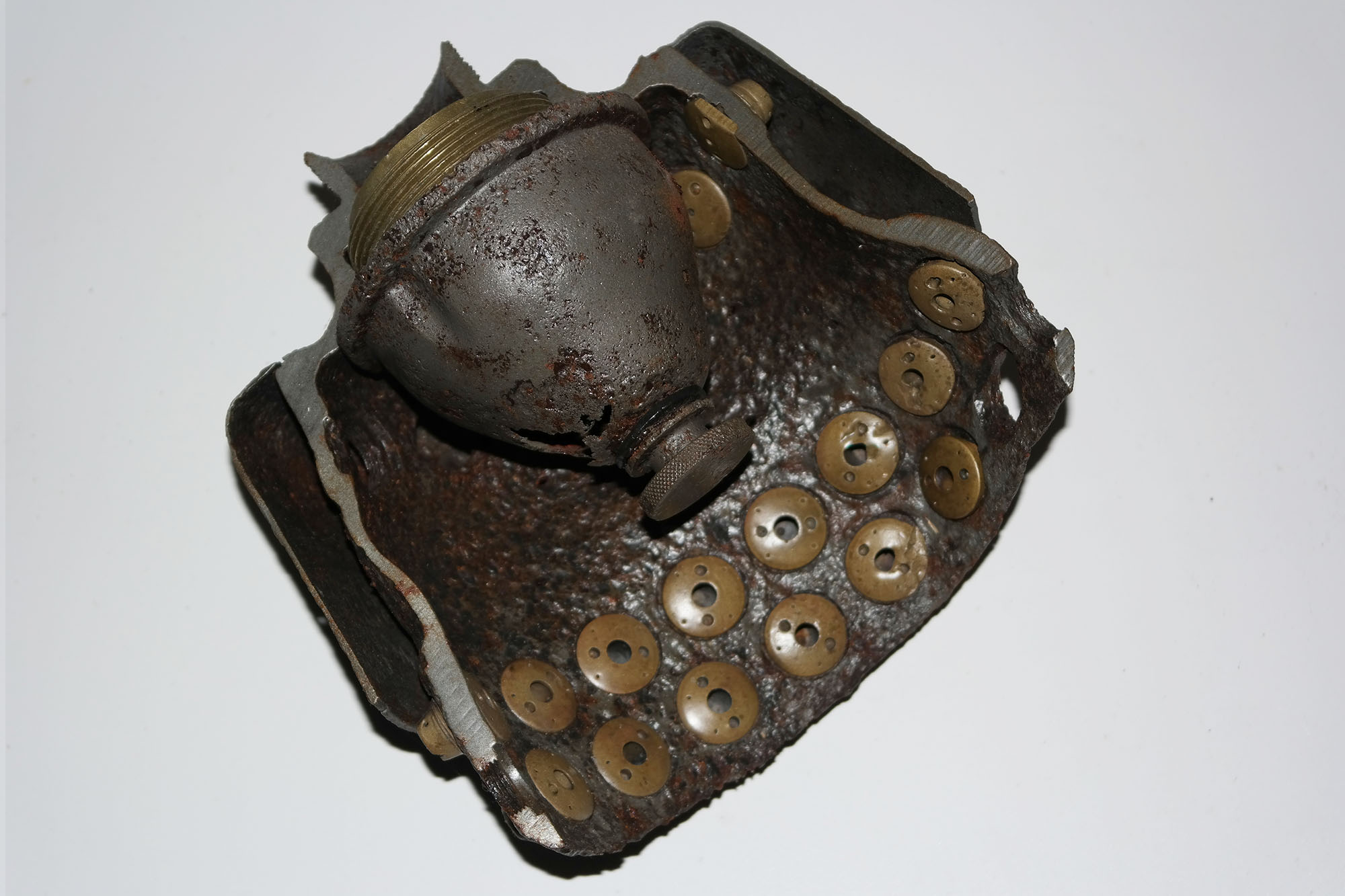
This relic from the V2 Rocket History collection shows a cutaway presentation of one of the V2’s 18 combined fuel and liquid oxygen (LOX) injector ‘pots’. The LOX injector transit cap is also shown fitted over the LOX injector.
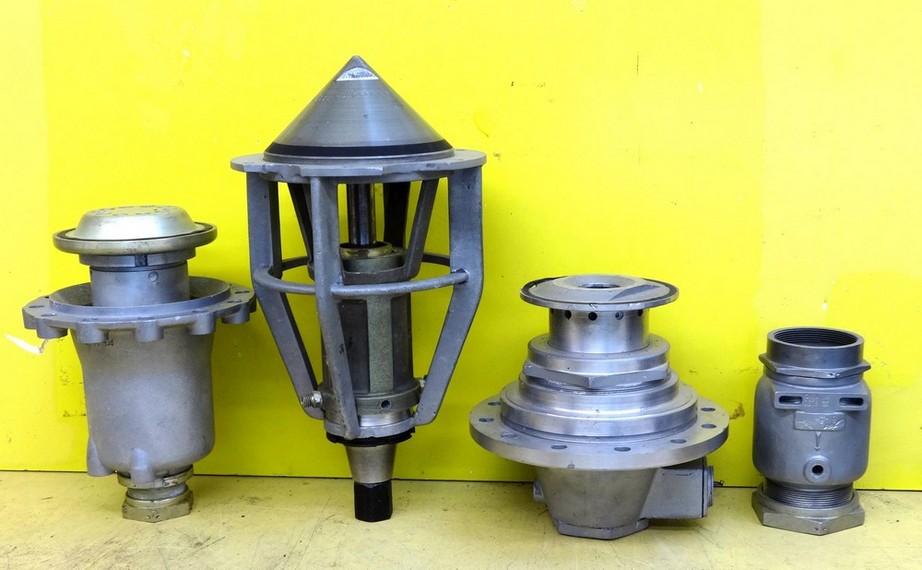
Photo shows main valves. Photo copyright: The Horst Beck Collection
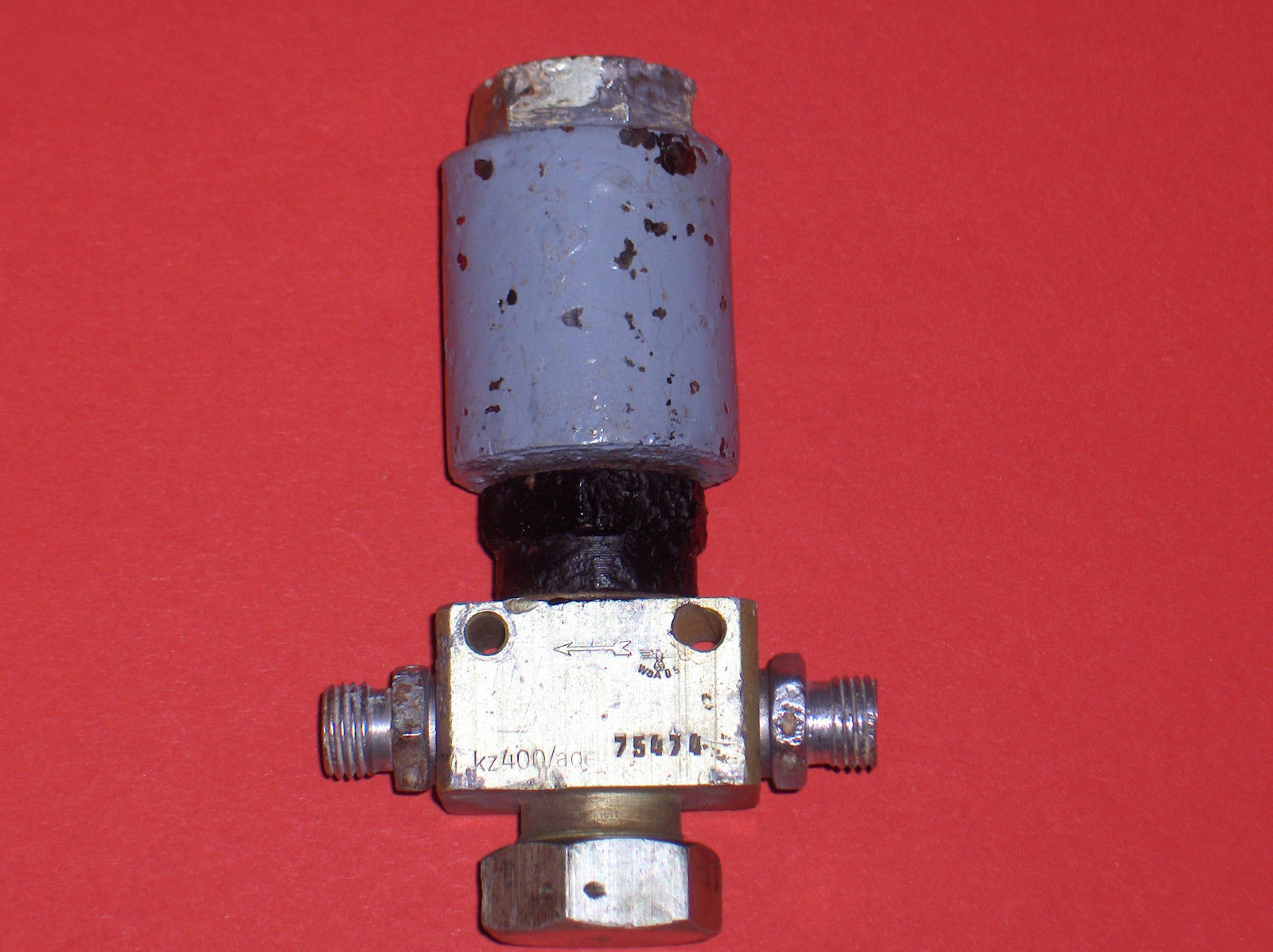
Solenoid electro-magnetic air valve. The This valve type is used numerous times to control equipment in the V2 missile. Variations of this electrically activated valve can be used to control high pressure air or fluids.
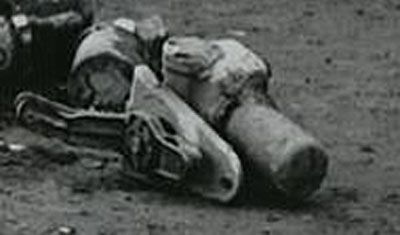
Hydraulic servo from fin 1 or 3 of the V2 missile, collected with other debris following a combat impact.
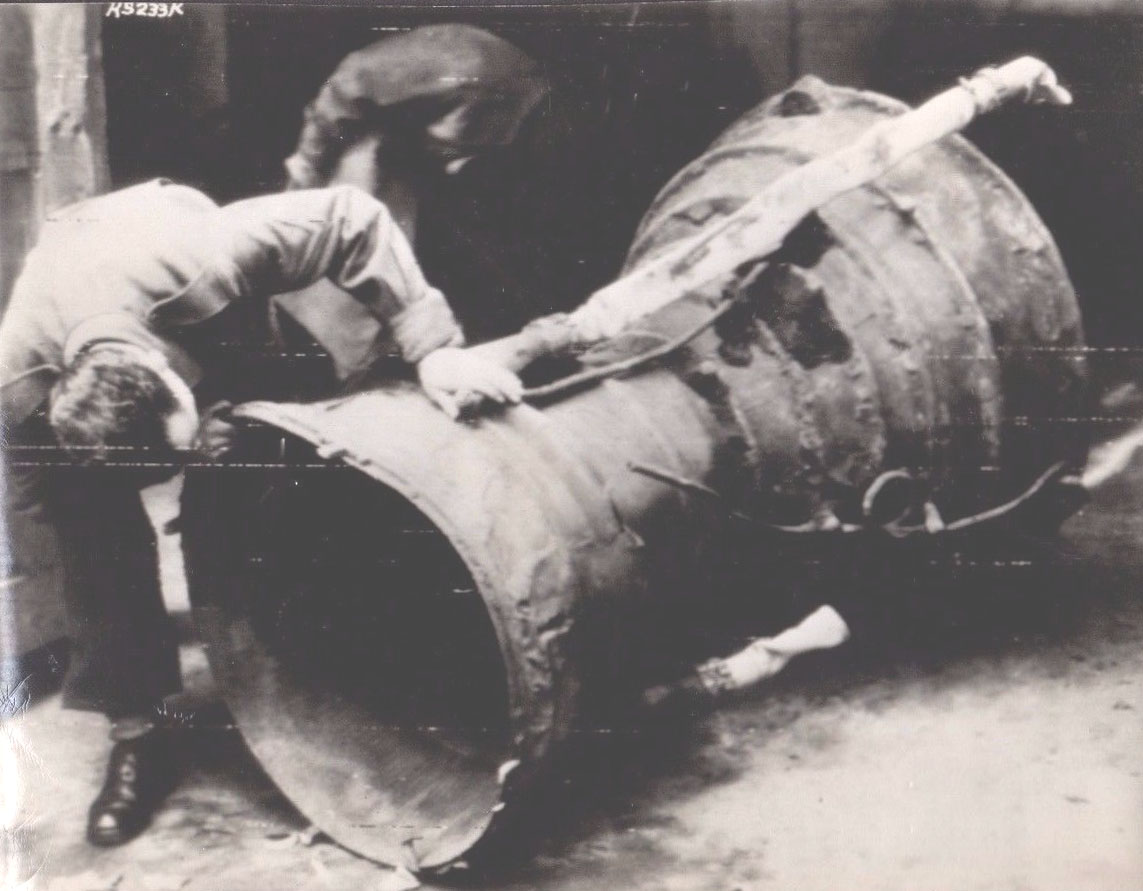
Examination of V2 missile thrust chamber. Sections of two of the large bore aluminium alcohol inlet manifold feed pipes and two thin steel veil colling supply pipes are still attached. The distinctive heat expansion relief loop can be seen on one of the pipes.
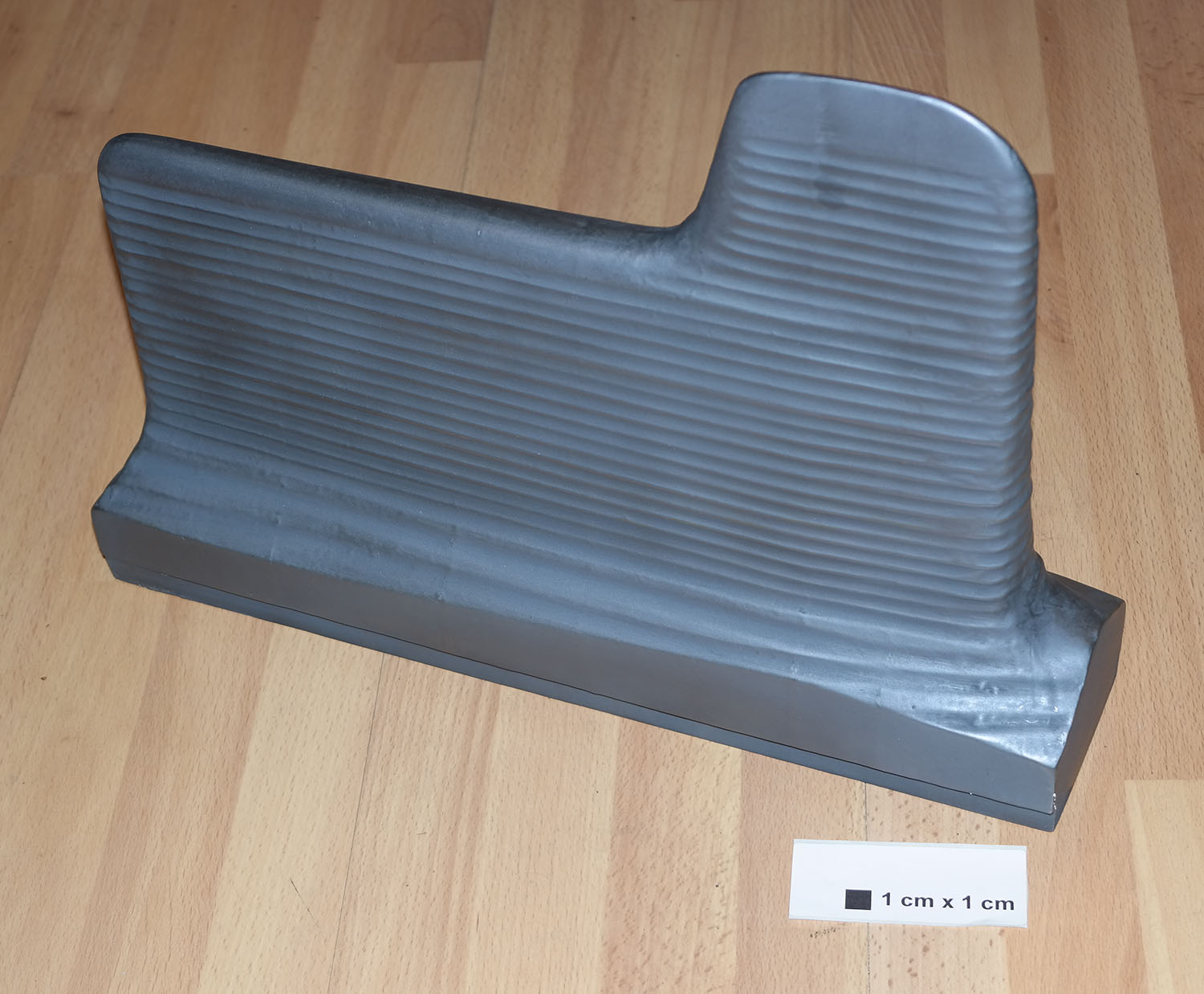
This image shows a full size replica of the A4 missile graphite jet vane held at our ‘Wernher von Braun rocket academy’ museum.
Category | V2 Missile relics |
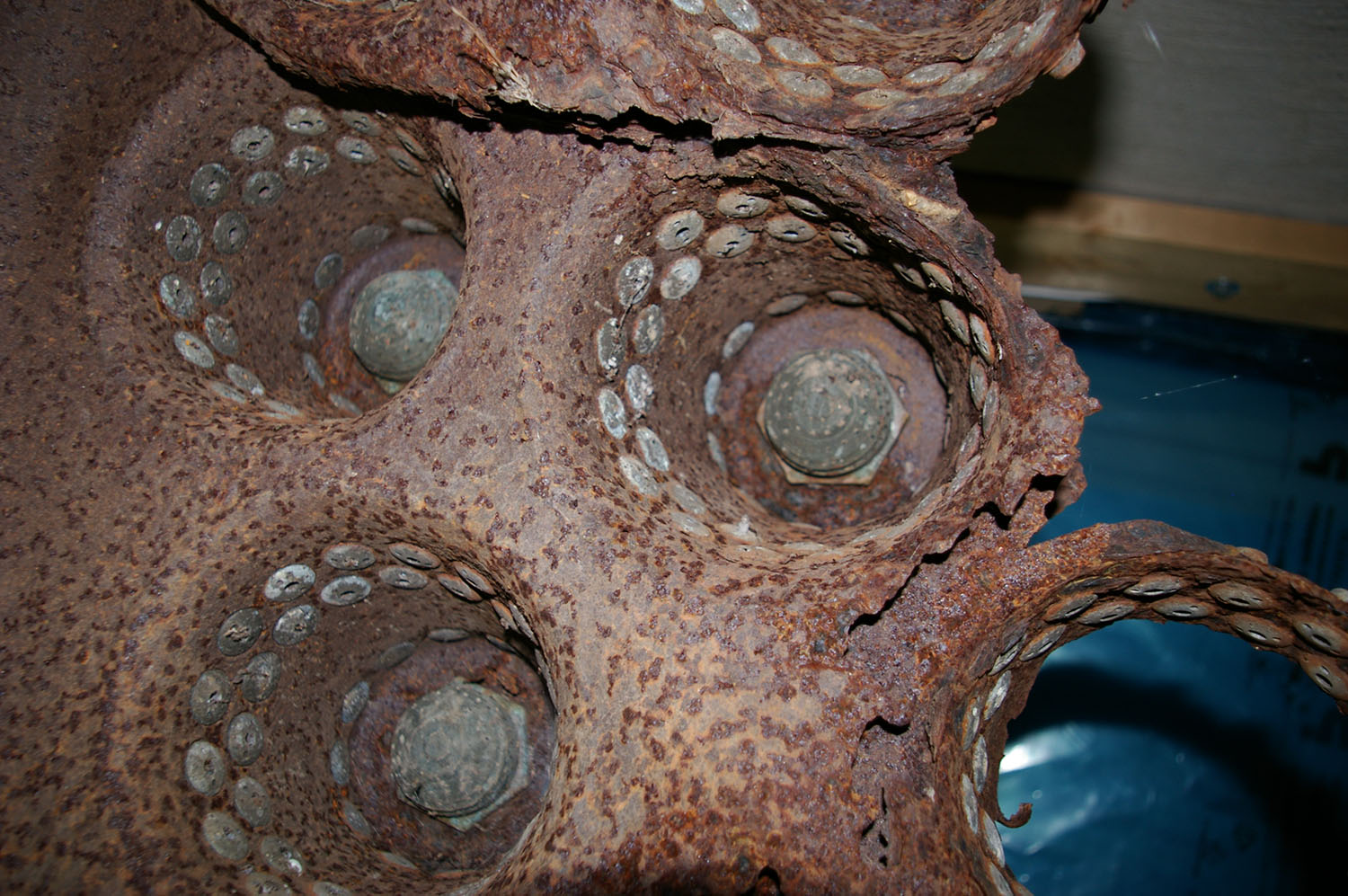
Image shows interior of production series (combat relic) V2 missile propellent injector pre-mixer pots. Three post in the picture are intact, others seem in the picture have been destroyed in the impact. This engine part was recovered from a combat impact East of London. Impact date: February 1945
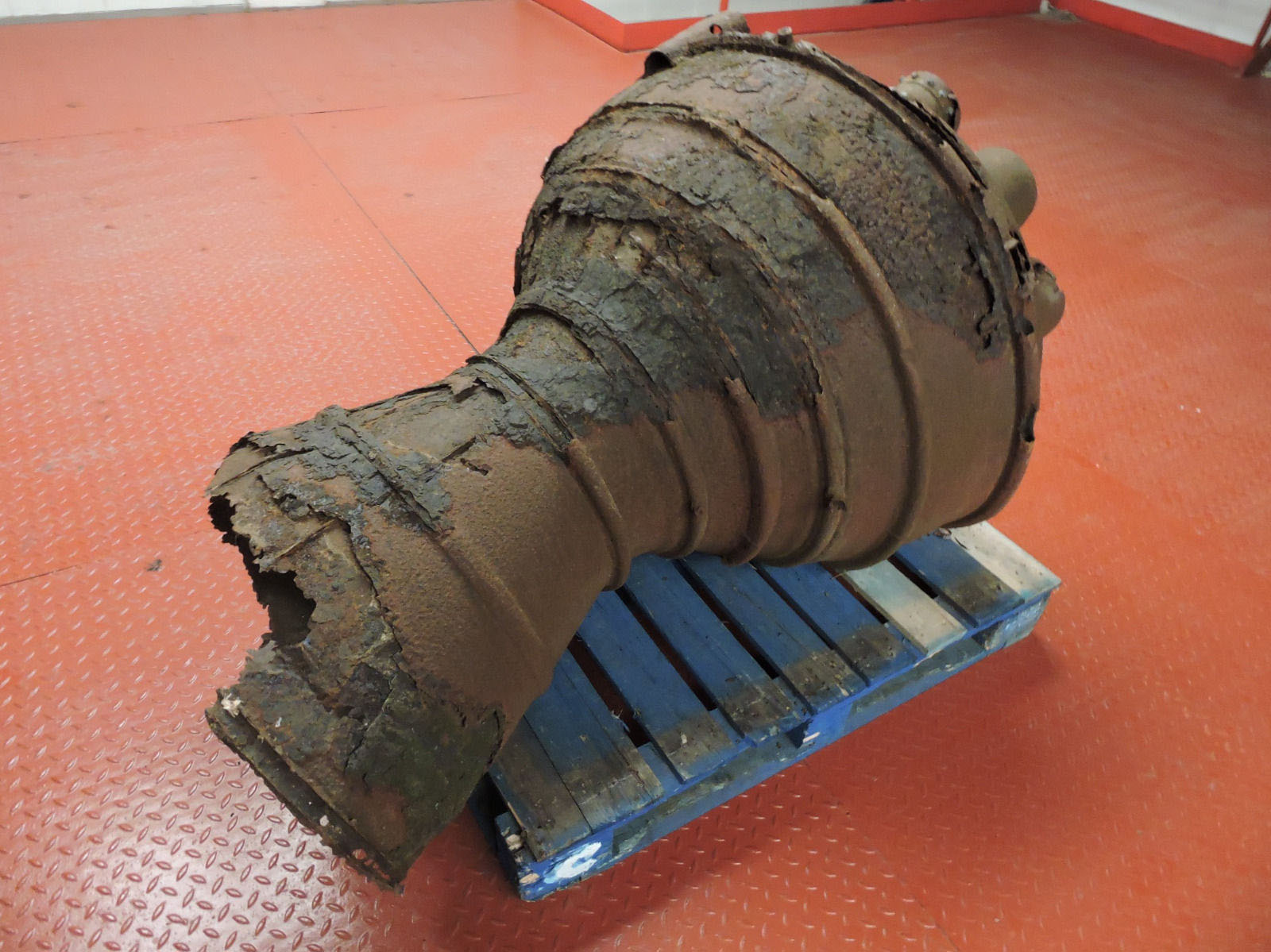
Recovered from Great Warley impact: February 1945. This chamber has a production use order number of 33 painted crudely on topmost segment. This number, to indicate rank in batch, was added shortly after manufacture to ensure the chamber was selected by the missile assembly crews in the correct order; that is on a newest-last basis to make sure that the oldest chambers were employed in missile construction operations first.
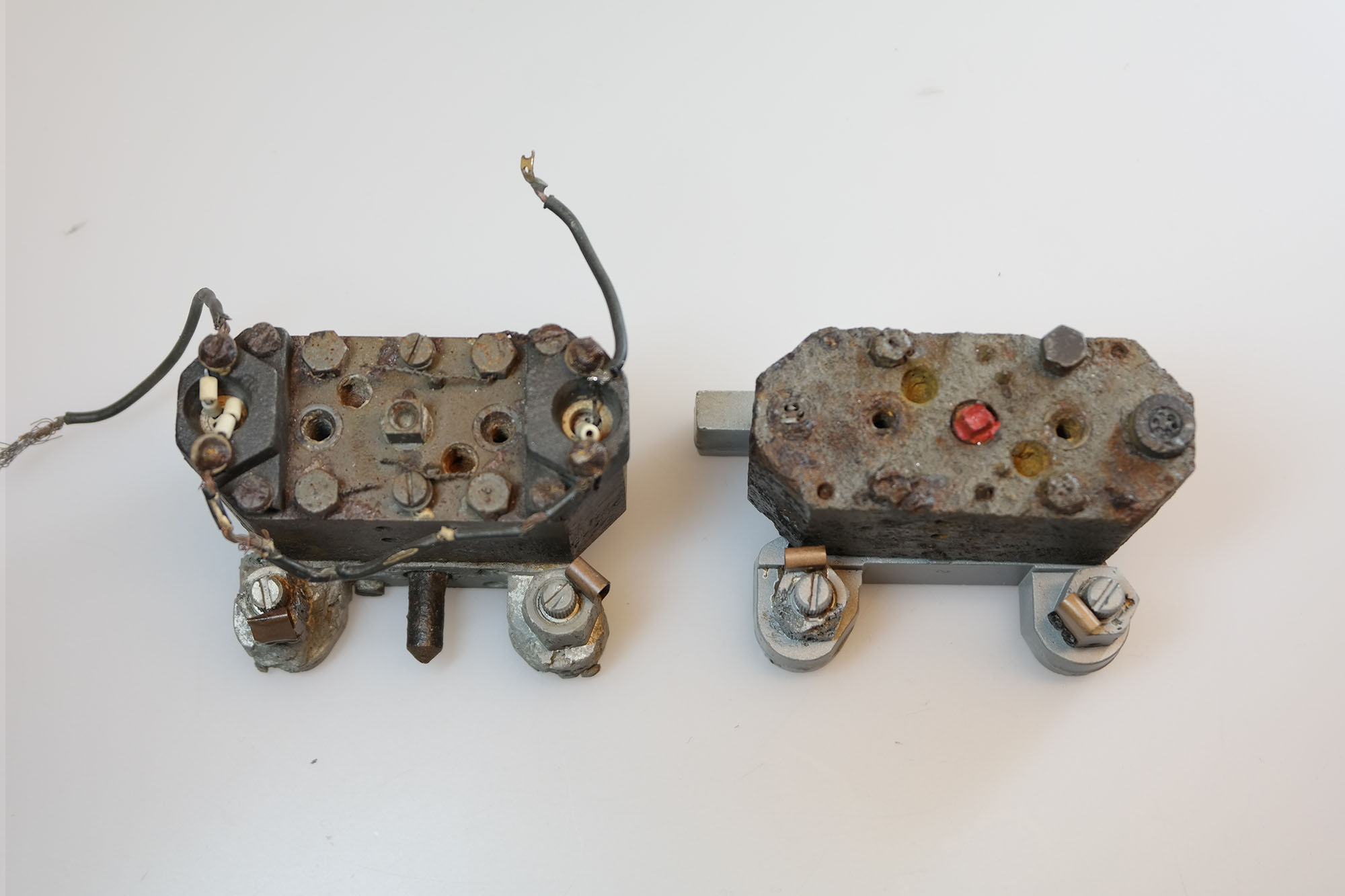
Two Askania (designed) hydraulic gear pumps – the examples shown here have two ceramic insulators with with Nichrome wire type heating elements. The heaters are located at each end of the pump on the long axis. The pump on the right still has its power supply wires attached and was easily repaired and restored to full function in our workshop.This type of pump (with heaters) seem to be rare among the debris of European combat impact sites but fairly common in debris collections emanating from research flights in Peenemünde and parts of Poland. An explanation maybe that the oil could be warmed up sufficiently simply by starting all four hydraulic gear pumps sooner in the pre-launch sequence. The only downside being that the already noisey missile would be making yet more noise in the risky period leading up to launch.

Testing fuel injectors
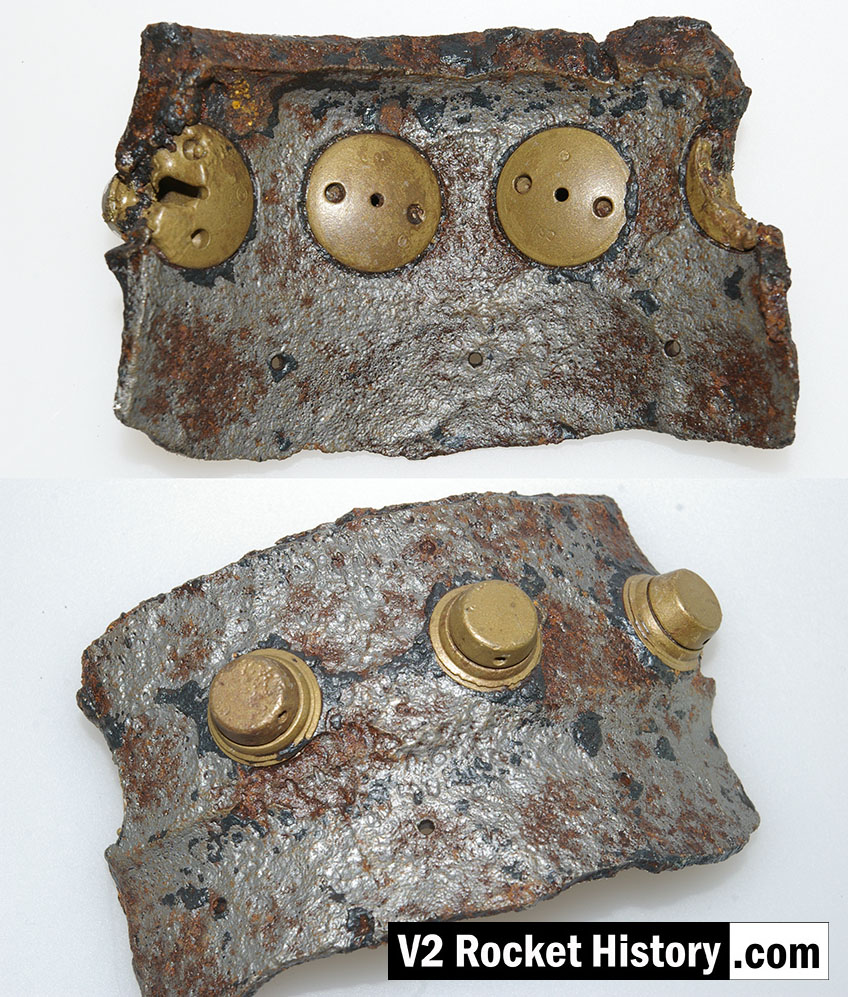
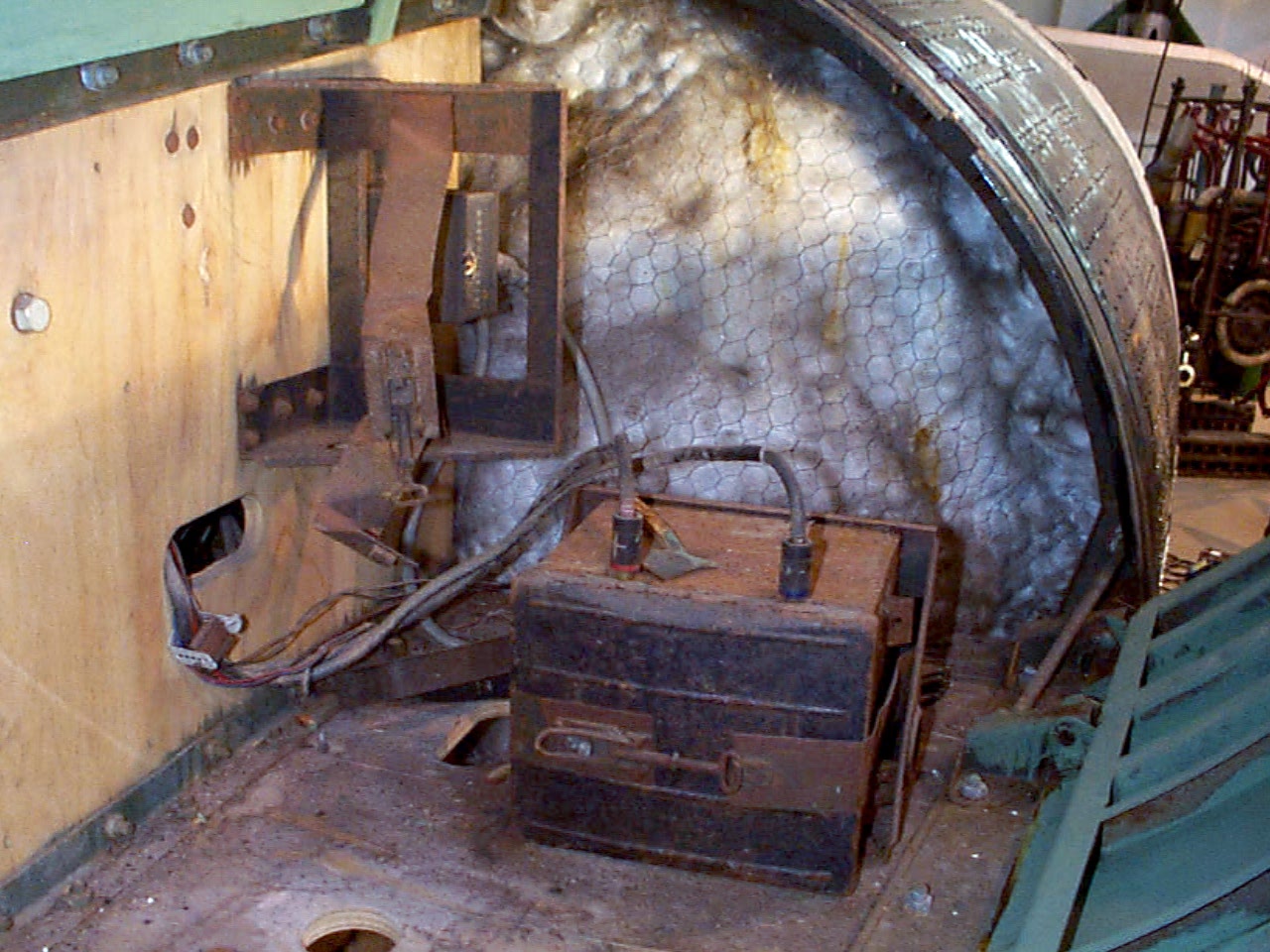
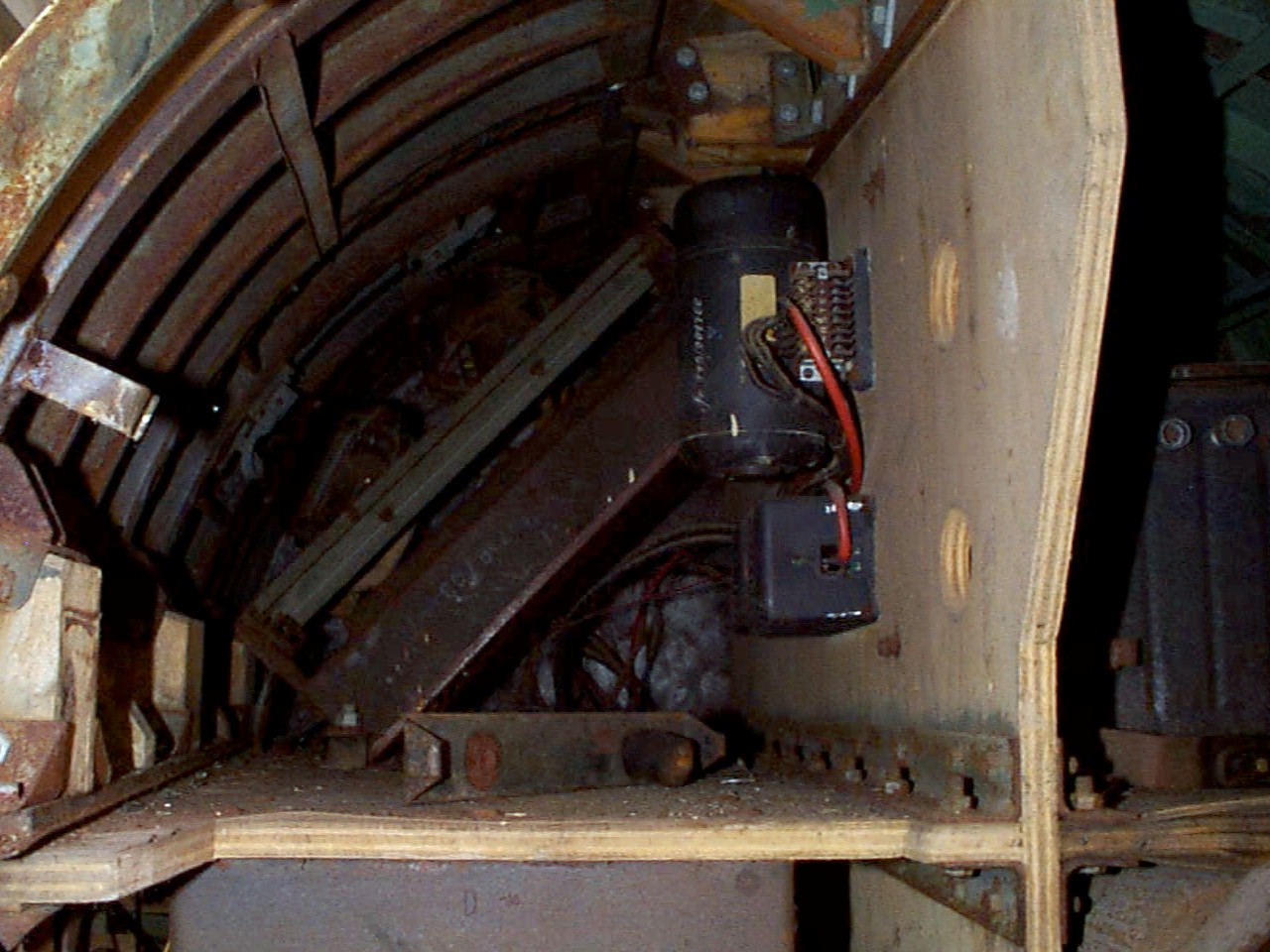

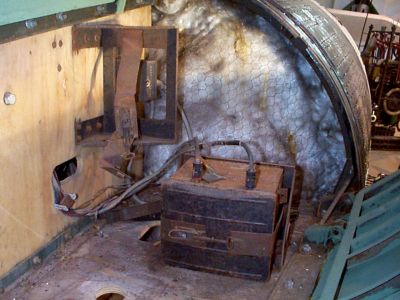
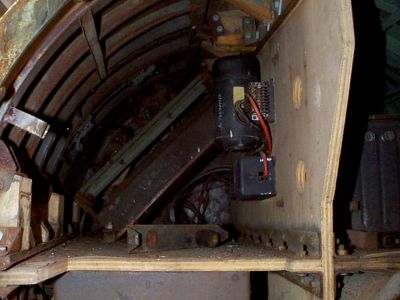
Photo shows a small section of the burner cup with row A (2131E) fuel injector inserts with three row B drilled holes below. The two undamaged inserts carry the armament code ‘csl’. The relic was found near a workshop in the Development works Pennemünde. Slag from the cutting flame and damage to the inserts at both ends of the relic would indicate that the section was cut from a steel burner cup using a gas cutter (fuel and oxygen) for purposes unknown. V2RH collection image