
Archives: Gmedia Albums


Turbopump 3D CAD
3D CAD model images of the A4/V2 rocket engine’s steam turbine powered propellent pumps – all images by Ray Matter. To see Ray Matter’s blog 3D CAD modelling the V2 rocket turbopump introducing these images, just click the link.
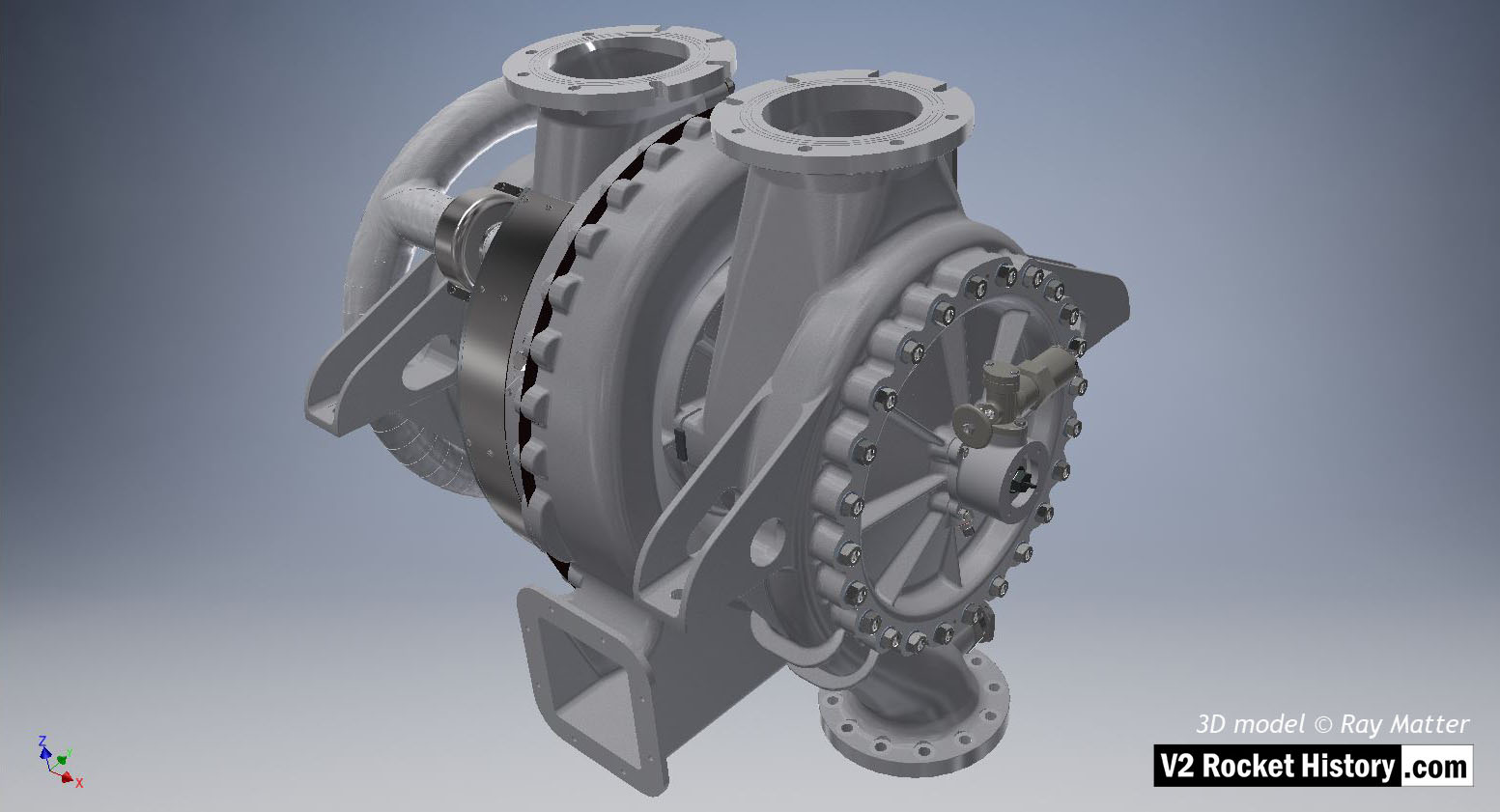
Turbine powered propellant pumps for A4/V2 rocket engine – fuel pump on right. Full perspective assembly showing tubular ring steam inlet manifold with asbestos bandage extreme left, inlet flanges at top, frame support brackets, steam exhaust outlet square shape lower center. The overspeed trip switch can be seen just above center on fuel pump face plate. The fuel outlet flange can also been seen btm right of center. 3D model by Ray Matter
Album | Turbopump 3D CAD |
Category | Turbo-pump |
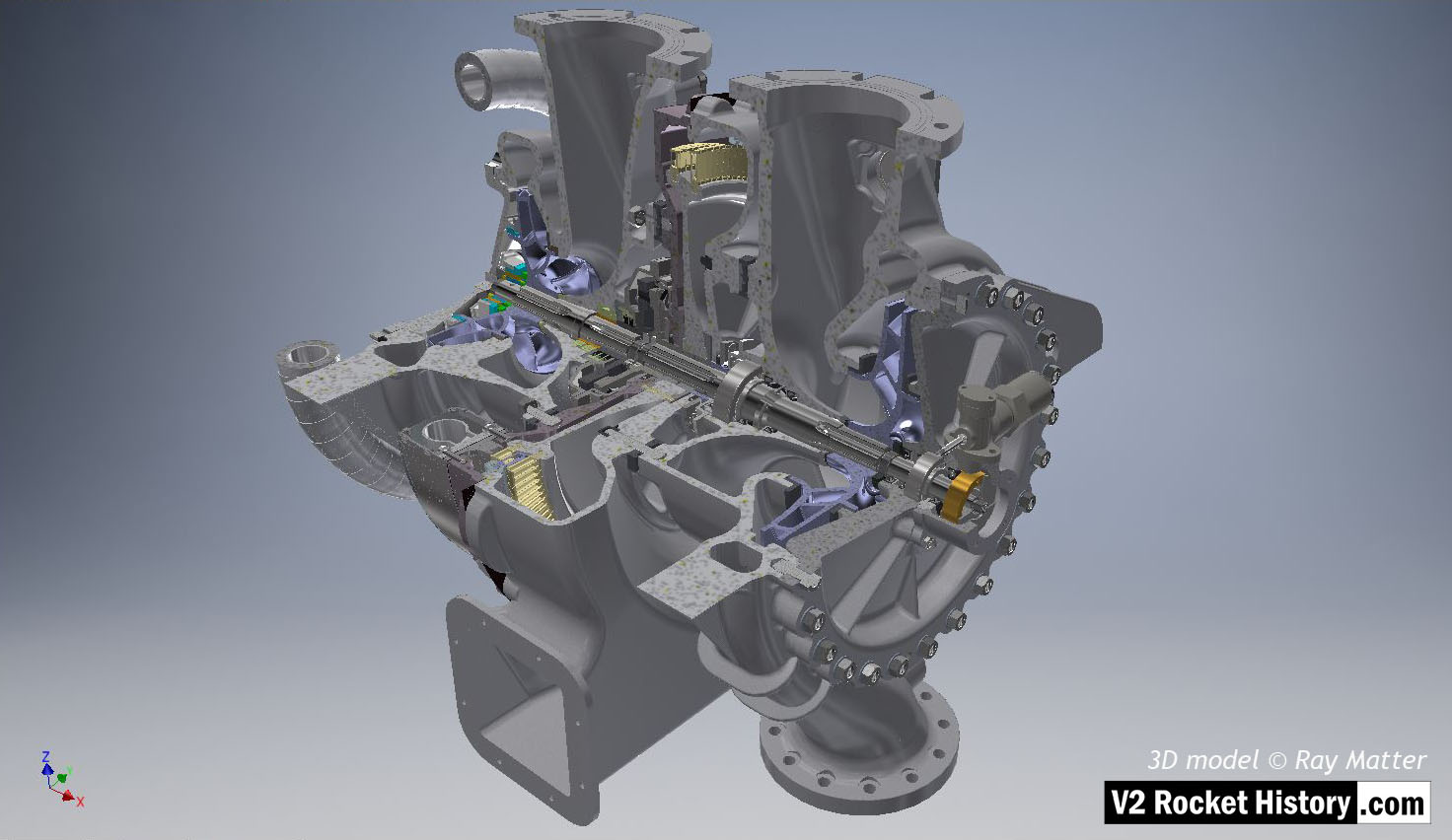
Turbine powered propellant pumps for A4/V2 rocket engine – fuel pump on right. Full assembly showing steam inlet manifold on left, inlet flanges at top, support brackets, steam exhaust outlet square shape lower center. The over-speed trip switch can be seen just above center on fuel pump face plate. The fuel outlet flange can also been seen btm right of center. 3D model by Ray Matter
Album | Turbopump 3D CAD |
Category | Turbo-pump |
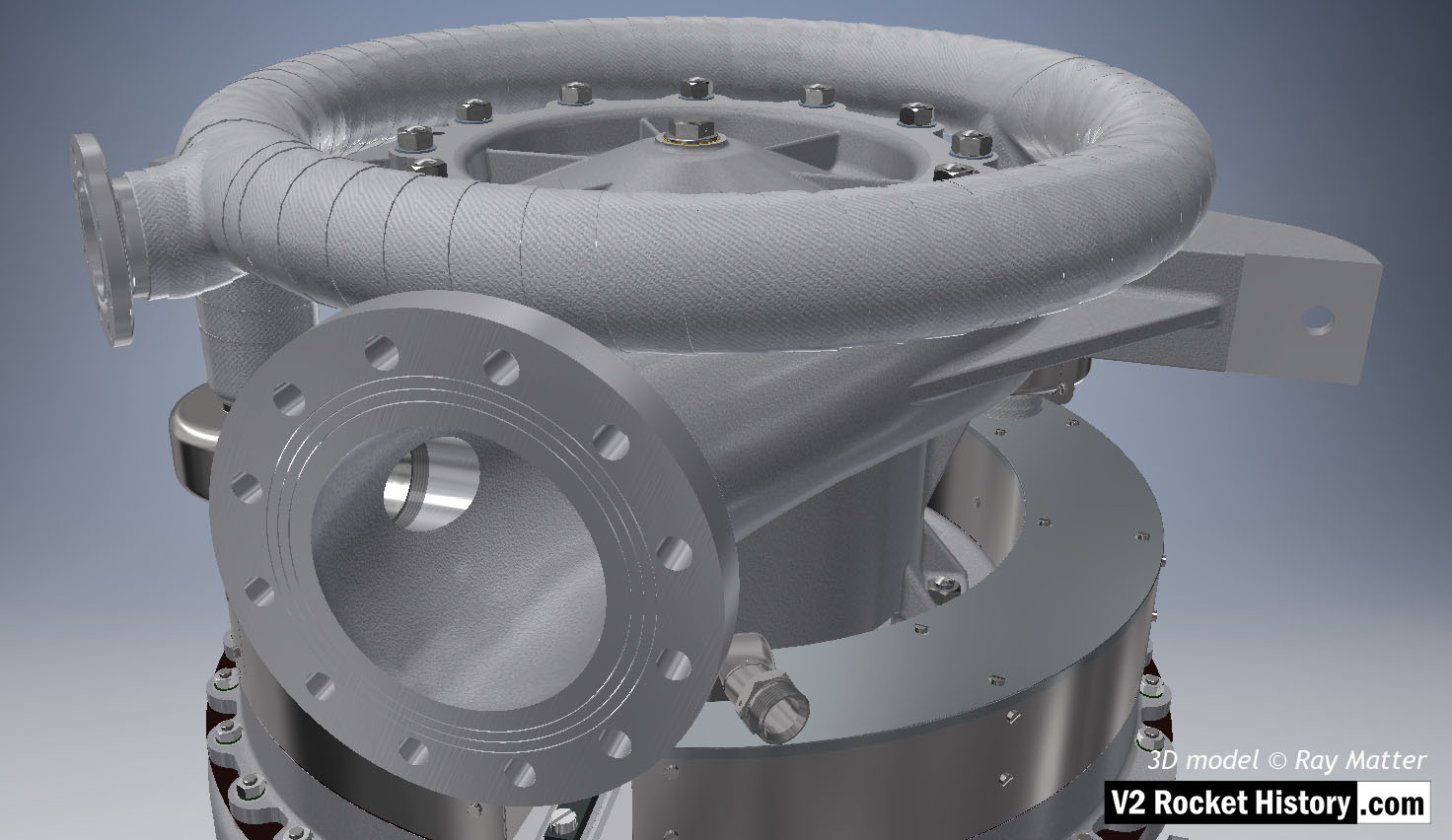
Full assembly showing, from top, steam inlet ring manifold, LOX pump and portion of steam turbine assembly. View shows outlet flange facing camera. Note the three fine rings milled into flange face. The rings were designed to improve keying for the sealing ‘putty’ that was used to seal the connection between the flange face and the inlet pipe. 3D model Ray Matter
Album | Turbopump 3D CAD |
Category | Turbo-pump |
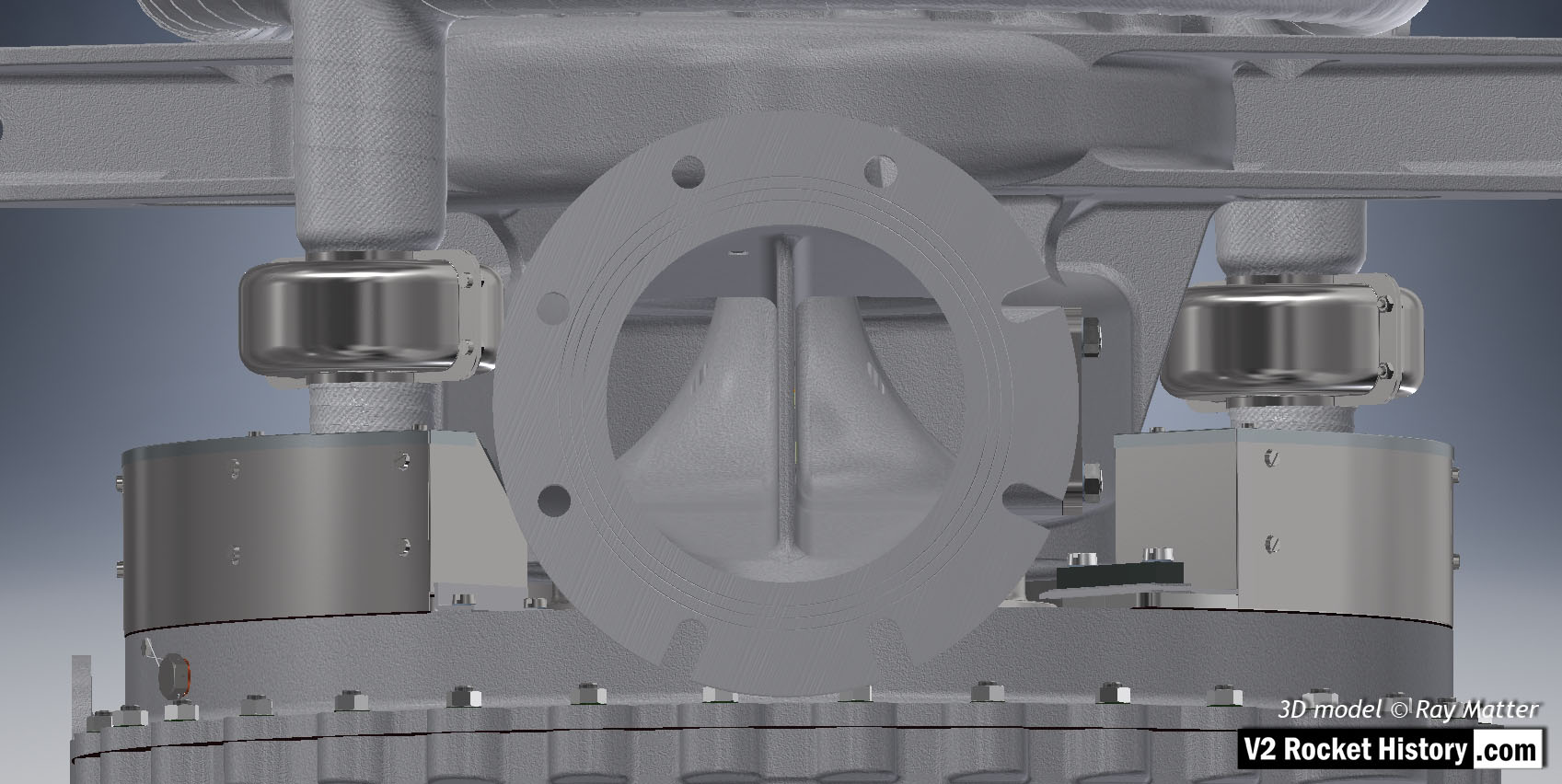
A (LOX) Pump close-up showing inlet flange, with fastener slots and holes, as well as the throat baffle. To the right and left of the flange, the steam inlets are shown – with steel cases covering the steam manifold connection flanges. Of special note in this view is the self-purge orifice seen at the top right-hand side of the inlet throat baffle. This hole allowed gas to escape from the top of the LOX volute space back to the low-pressure inlet throat and proved problematic in manufacturing and was revised in late 1944. 3D model Ray Matter
Album | Turbopump 3D CAD |
Category | Turbo-pump |
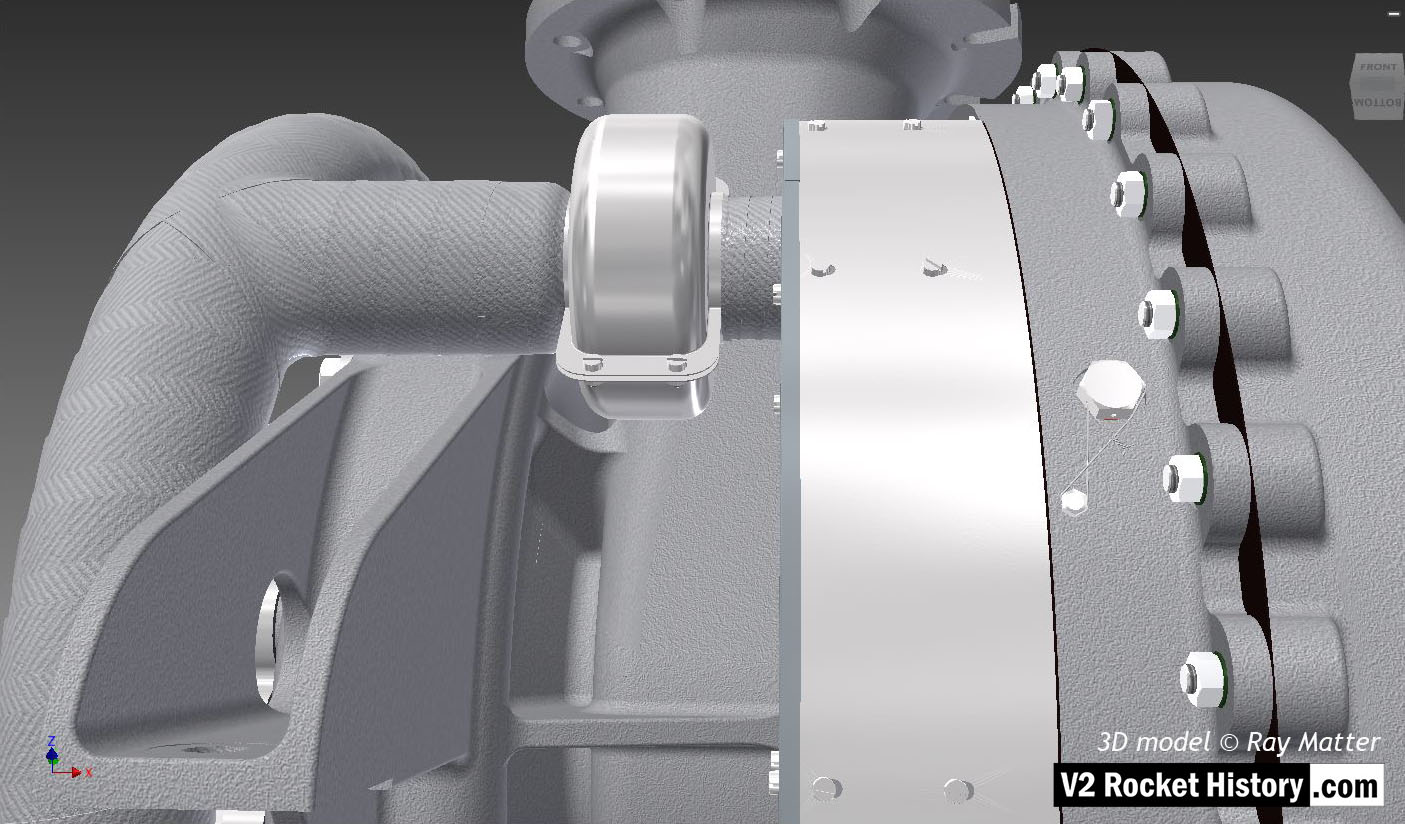
Close-up of turbine steam inlet ring manifold showing one of the entry points. The thin steel case that fits around the steam manifold mating flanges is clearly shown as is the wire restraint fastener locking system (see close-up in gallery). 3D model by Ray Matter
Album | Turbopump 3D CAD |
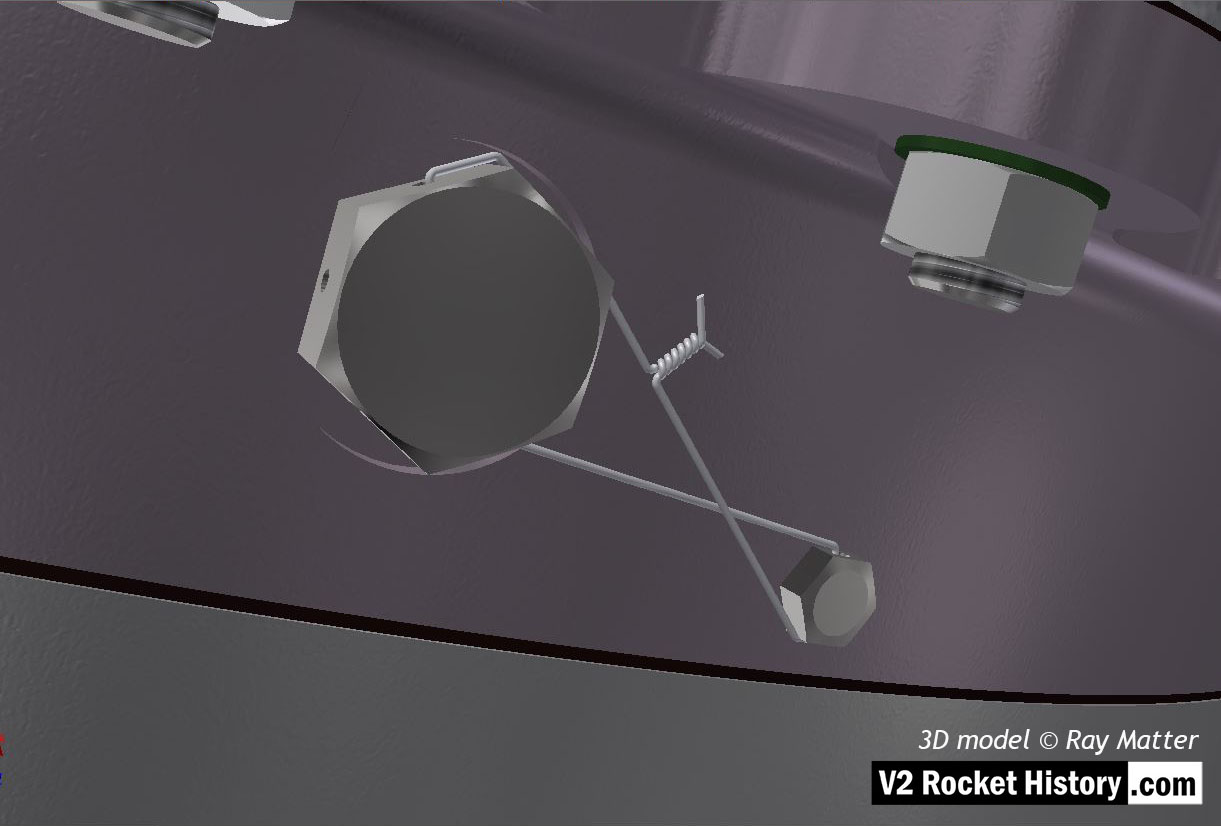
Turbine powered propellant pumps for A4/V2 rocket engine – close-up of turbine casing shows wire restraint fastener locking system. 3D model by Ray Matter
Album | Turbopump 3D CAD |
Category | Turbo-pump |
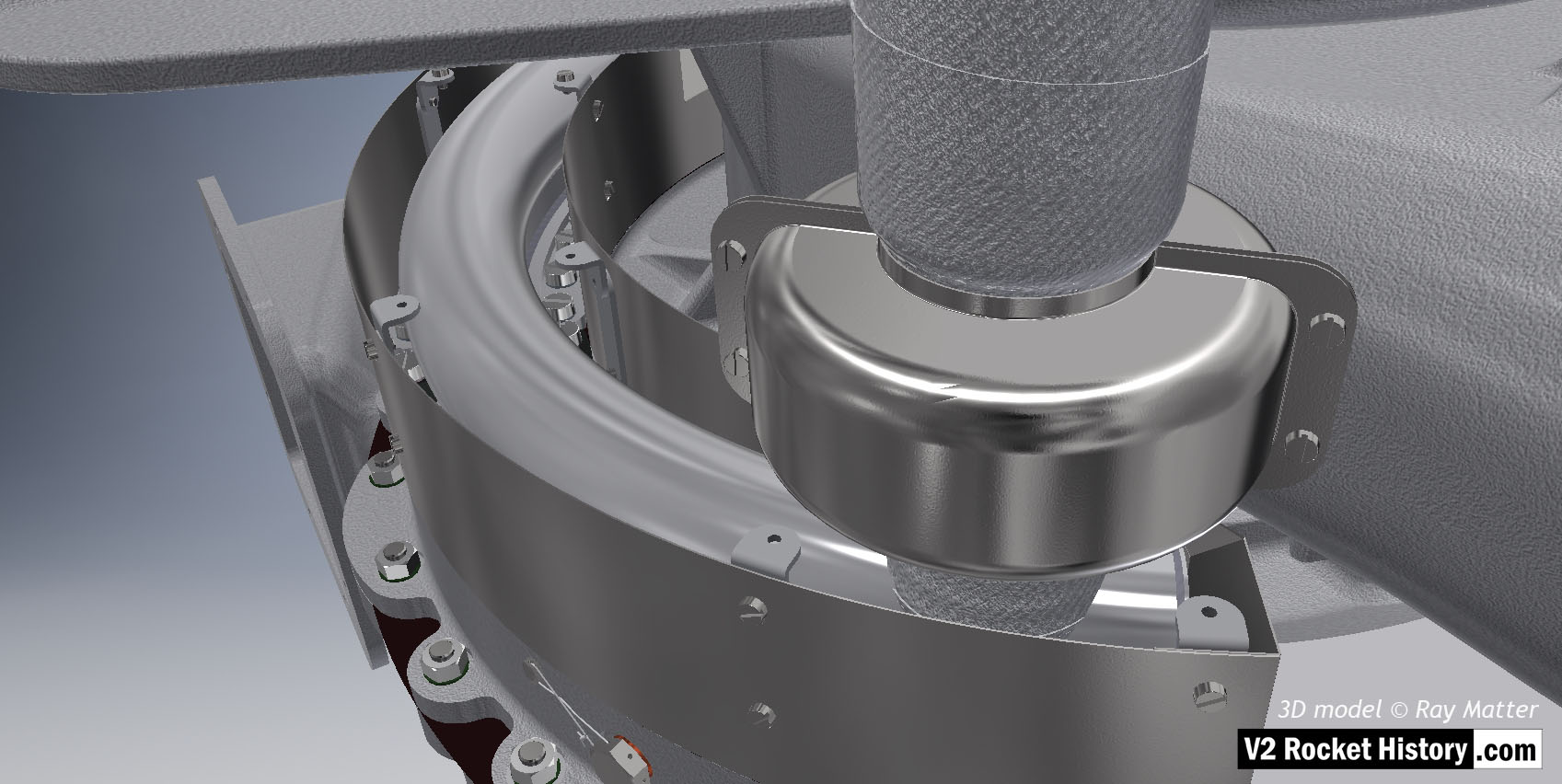
Close-up of turbine showing steel case with lid removed to show steam inlet ring manifold. The thin steel case that fits around the steam manifold mating flanges is clearly shown as is the wire restraint fastener locking system (see close-up in gallery). 3D model by Ray Matter
Album | Turbopump 3D CAD |
Category | Turbo-pump |
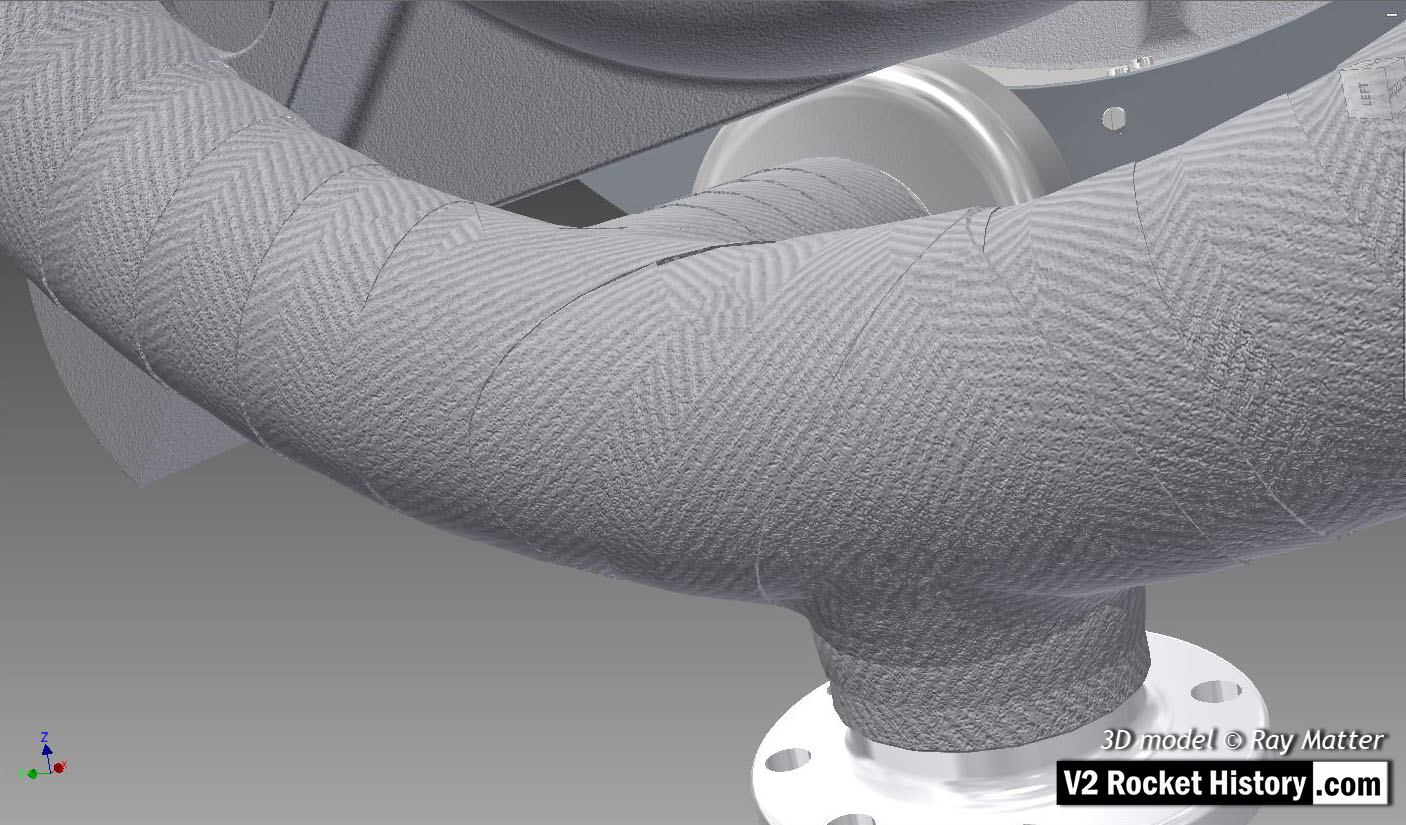
Close-up of turbine steam inlet ring manifold showing asbestos bandage wrapped around the tubular ring. Sometimes a thin wire was used to help retail the heat resistant material. This bandage is often missing from museum exhibits. 3D model by Ray Matter
Album | Turbopump 3D CAD |
Category | Turbo-pump |
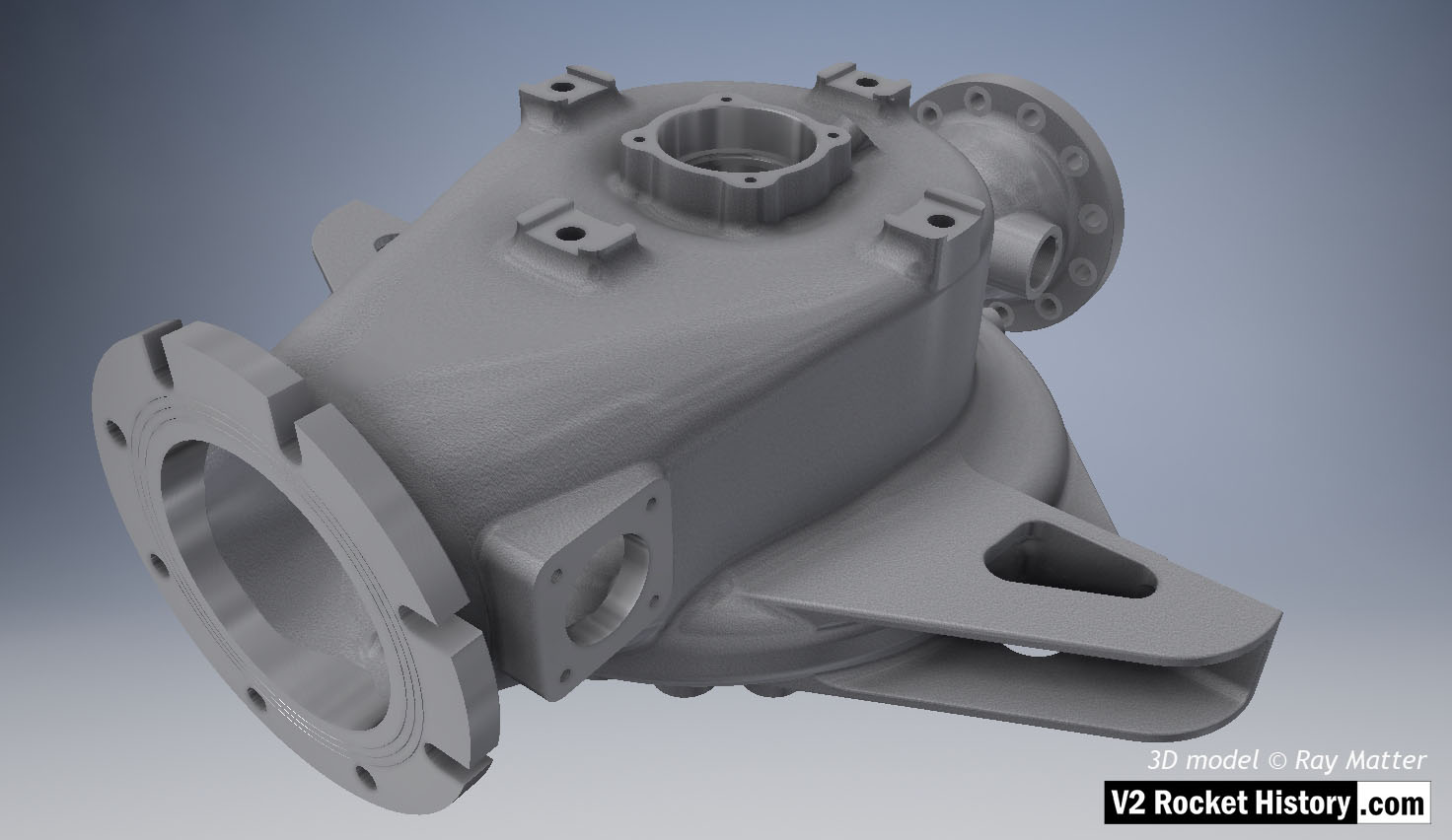
B (fuel) Pump sub-assembly, single piece casting showing machined (milled) areas without fittings. View shows inlet flange fastener slots and the throat aperture – facing right, initially blanked off by square plate, but towards the end of 1944 used for fuel return from the main fuel valve situated in the center of the thrust chamber injection head. 3D model Ray Matter
Album | Turbopump 3D CAD |
Category | Turbo-pump |
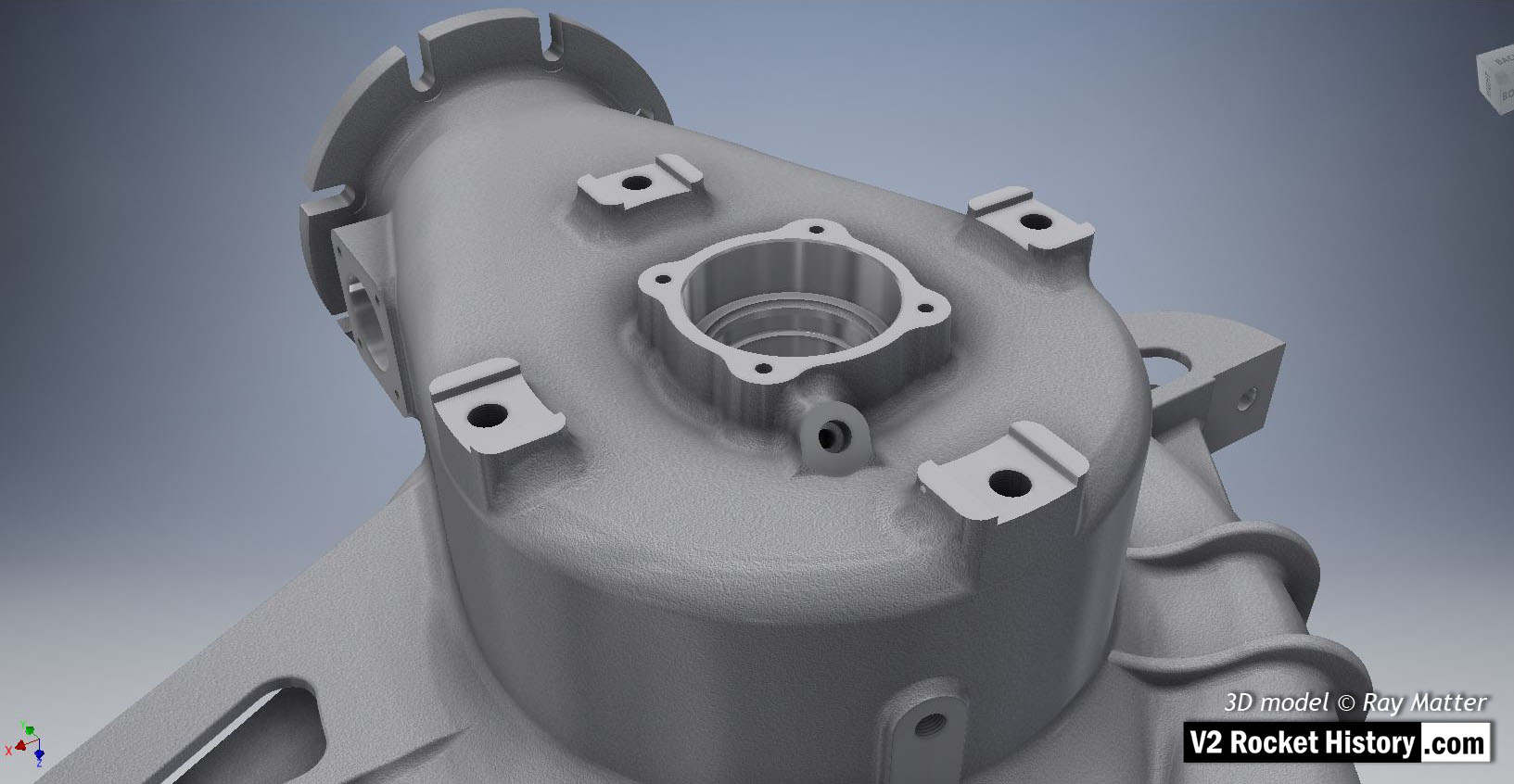
B (fuel) Pump sub-assembly, single piece casting showing machined (milled) areas and without fittings. 3D model Ray Matter
Album | Turbopump 3D CAD |
Category | Turbo-pump |
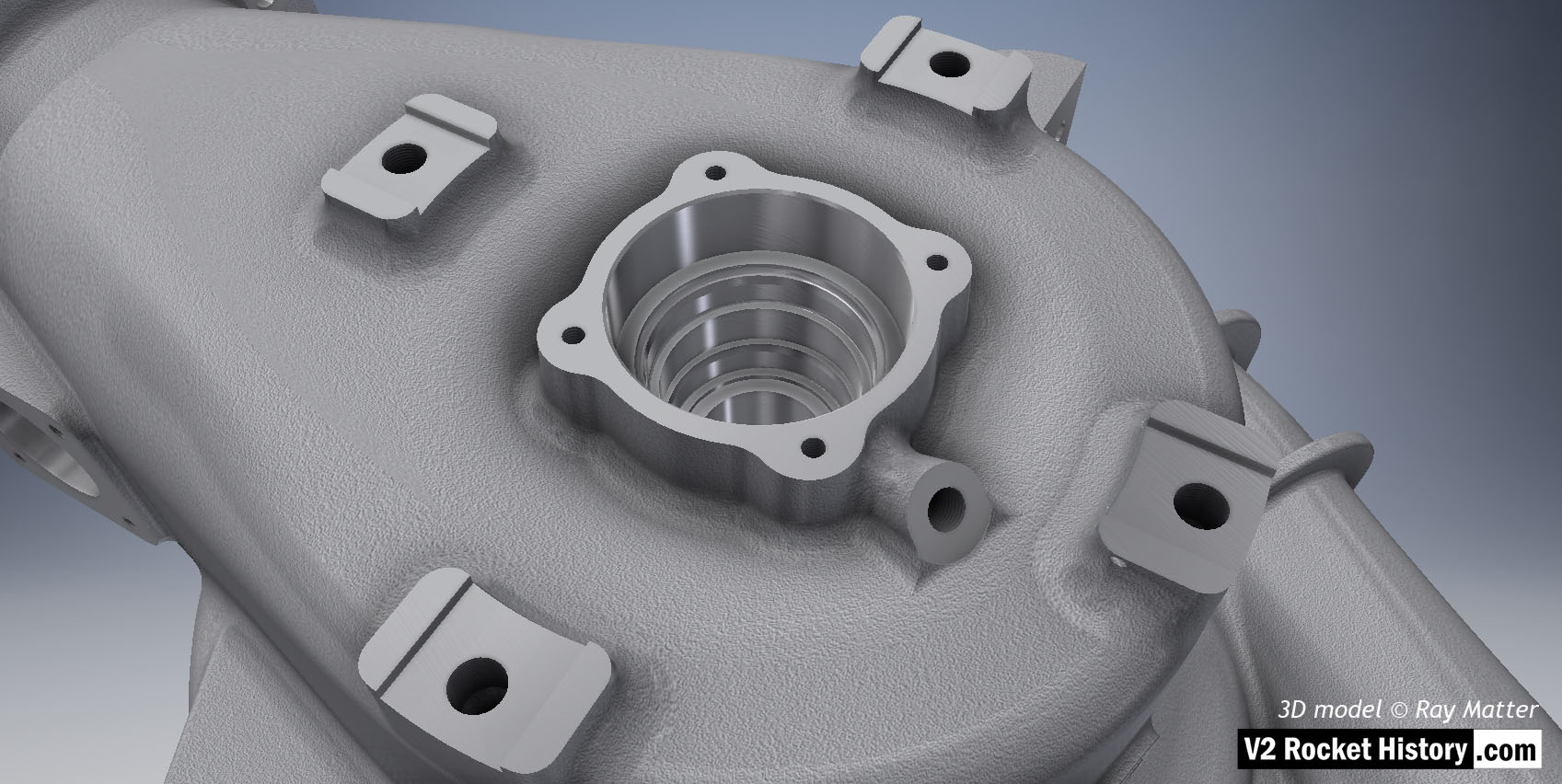
B (fuel) Pump sub-assembly shown without fittings. Single piece casting showing detail of bearing and seal cavity as well as threaded fuel bleed connection. 3D model Ray Matter
Album | Turbopump 3D CAD |
Category | Turbo-pump |
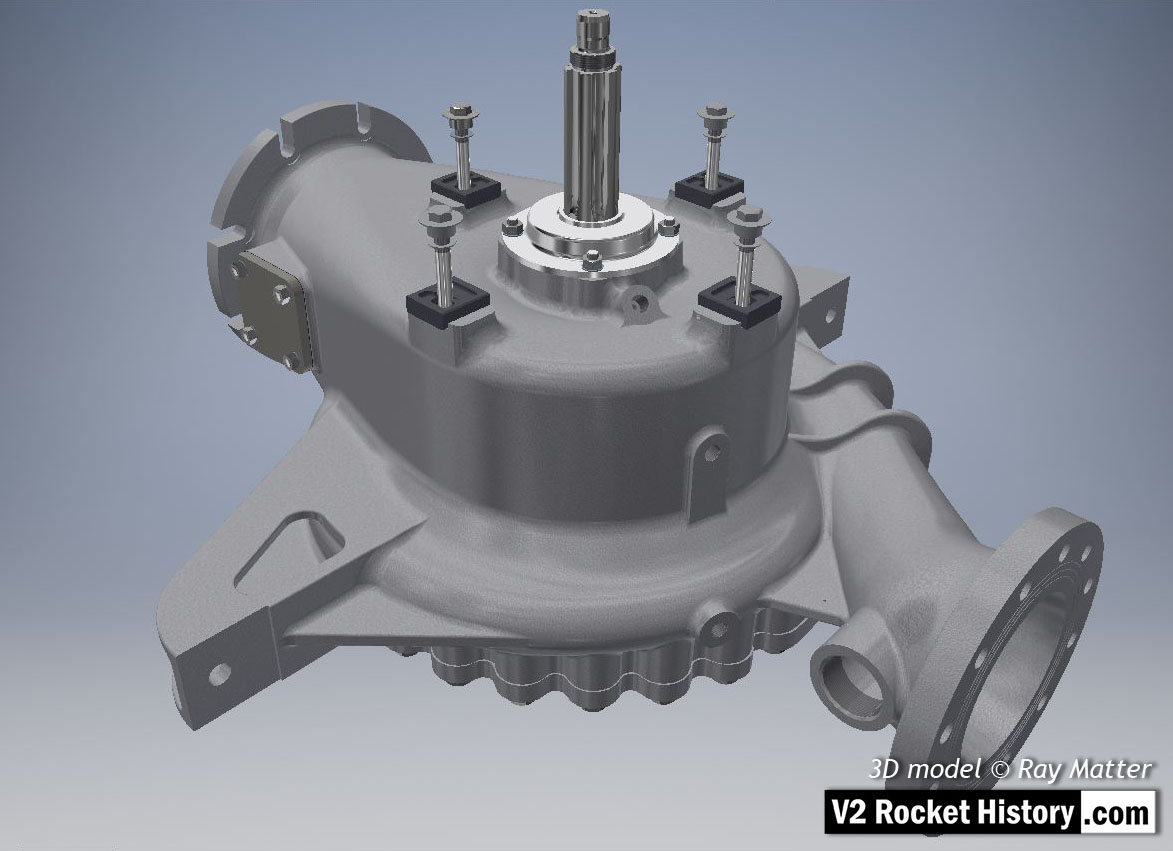
B-Pump sub-assembly, showing earlier version square inlet throat blanking plate (later versions employed a fuel return connection point mounted on this plate).
Fastenings, turbine case contact furniture, splined turbine connection shaft, and shaft seal cap are also shown. 3D model Ray Matter
Album | Turbopump 3D CAD |
Category | Turbo-pump |
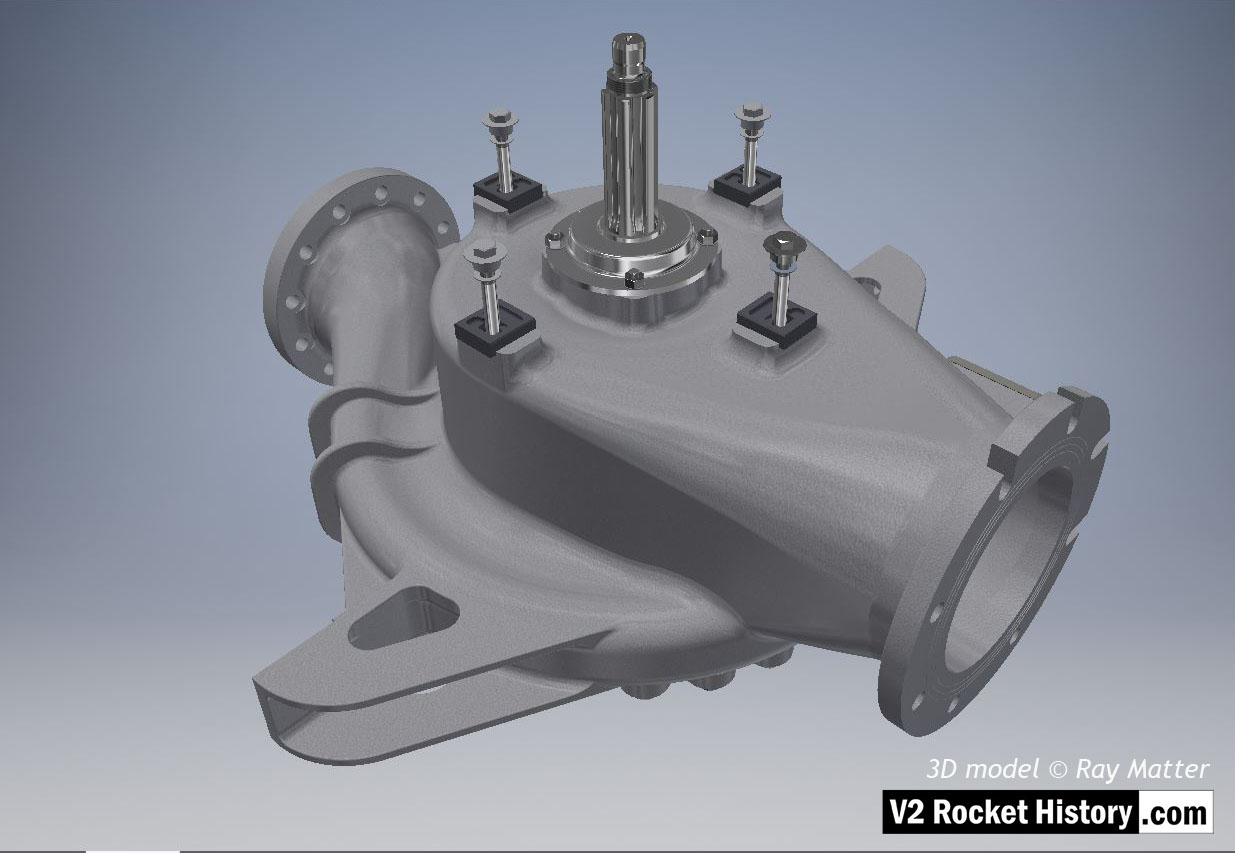
B-Pump sub-assembly complete with fastenings, turbine case contact furniture, splined turbine connection shaft, and shaft seal cap. 3D model Ray Matter
Album | Turbopump 3D CAD |
Category | Turbo-pump |
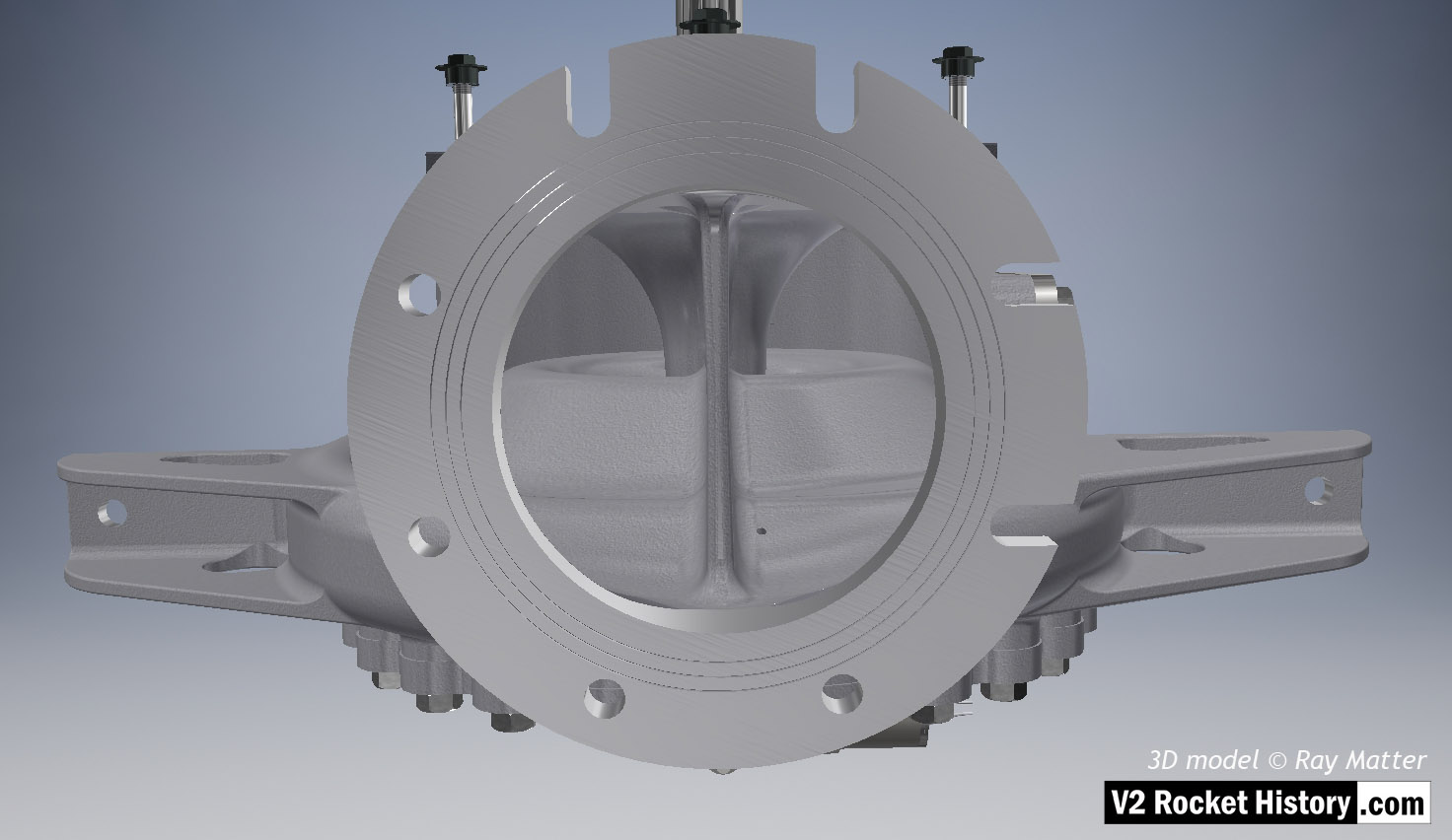
B-Pump Sub-assembly shown from top. View shows outlet flange facing camera – the splined drive shaft can just be seen at the top of the screen. Note the three fine rings milled into flange face.The rings were designed to improve keying for the ‘putty’ that was used to seal the connection between the flange face and the inlet pipe. Note, small self-purge orifice on the lower left of the inlet throat baffle. Unlike the upper purge hole in the LOX casing, the shallower face angle at the location of the hole in the fuel pump casing, was more accessible to drilling and was therefore not problematic. 3D model Ray Matter
Album | Turbopump 3D CAD |
Category | Turbo-pump |
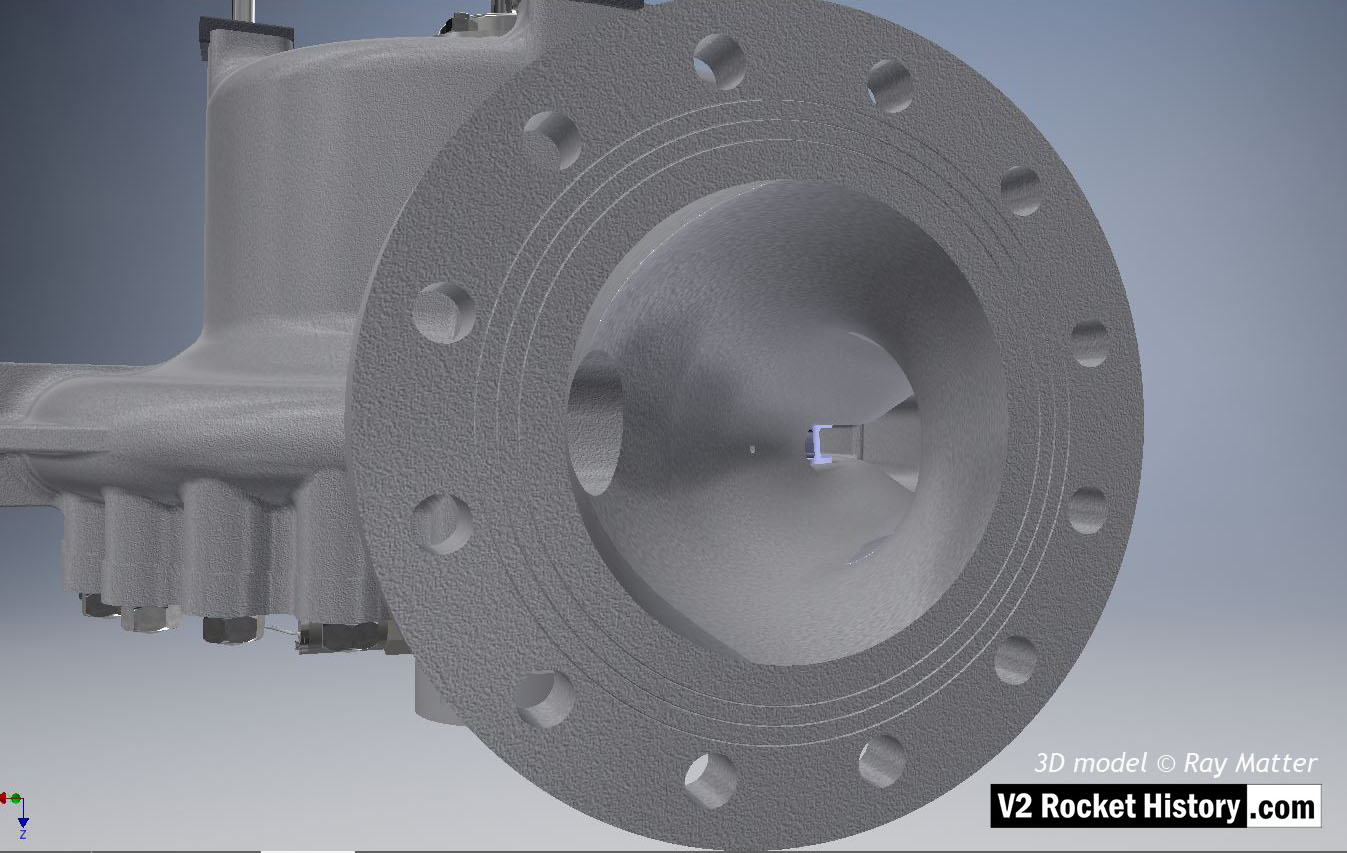
B-Pump sub-assembly close-up showing fuel outlet flange. Note the three fine rings milled into the flange face. The rings were designed to improve keying for the ‘putty’ that was used to seal the connection between the flange face and the flow choke. Both faces of the choke and top face of the fuel outflow connector had similar rings. 3D model Ray Matter
Album | Turbopump 3D CAD |
Category | Turbo-pump |
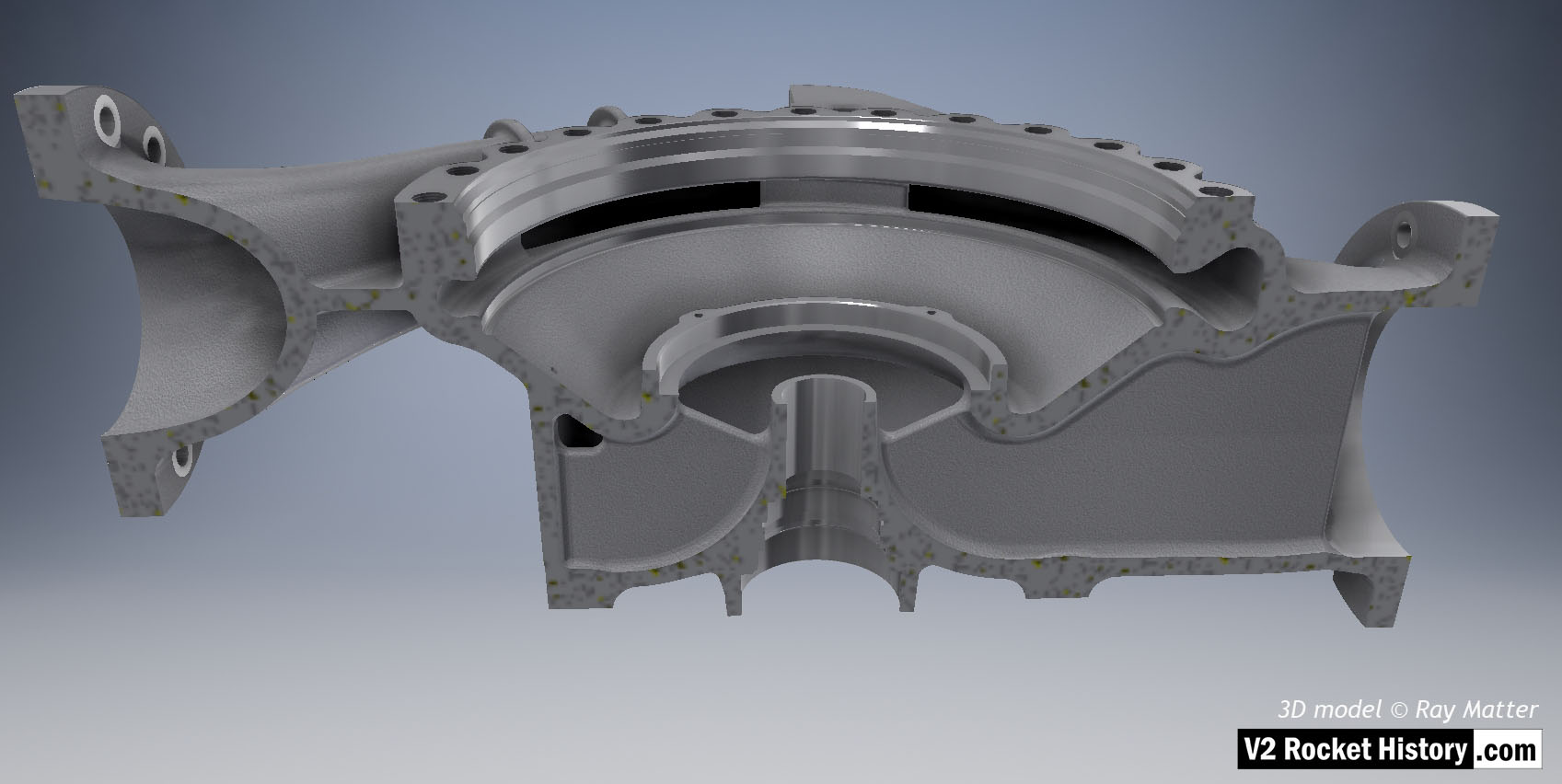
B Pump housing sectioned to show baffle and volute space area expansion as flow passes from inlet (right) to outlet (left). 3D model Ray Matter
Album | Turbopump 3D CAD |
Category | Turbo-pump |
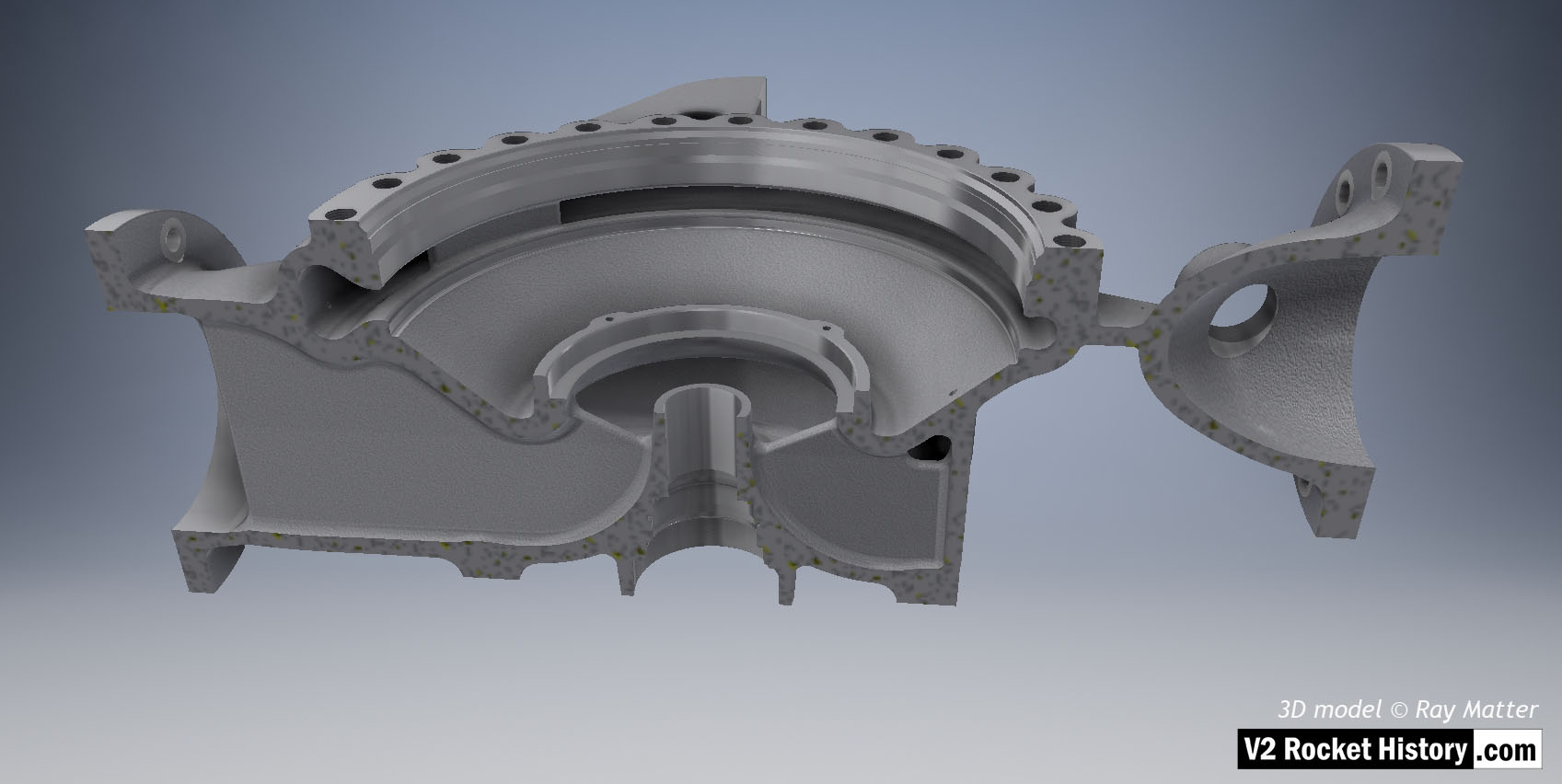
B Pump housing sectioned to show baffle with vent and volute space area expansion as flow passes from inlet (left) to outlet (right). 3D model Ray Matter
Album | Turbopump 3D CAD |
Category | Turbo-pump |
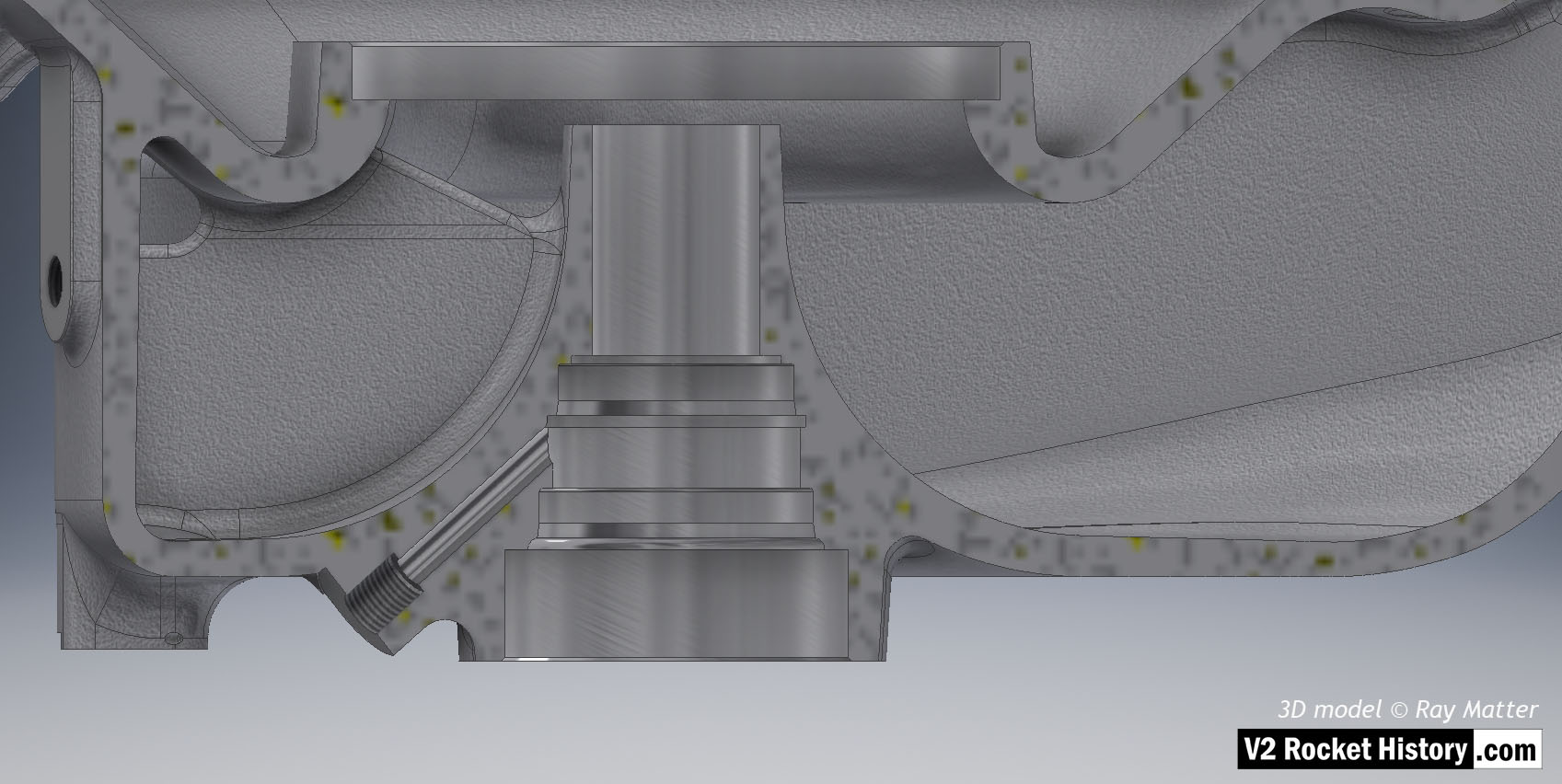
B pump housing showing sectioned area for shaft and bearing cavities with fuel pathway to left. 3D model Ray Matter
Album | Turbopump 3D CAD |
Category | Turbo-pump |
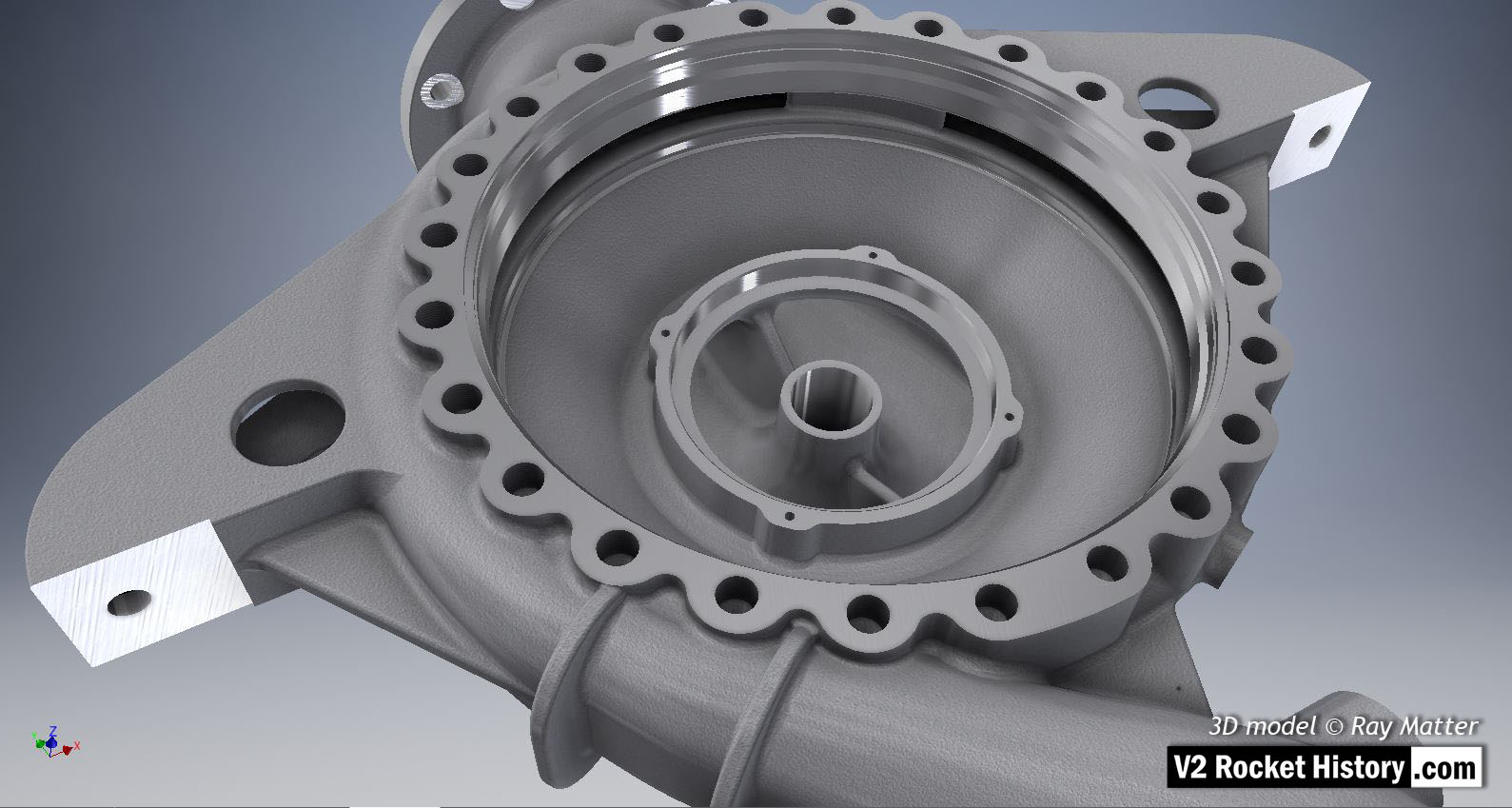
‘B’ fuel pump housing for V2 rocket engine turbopump showing cast and machined surfaces – some machined areas with obvious specular reflections. Of note are the rarely seen machined contact points on the integral support brackets and the larger areas in two locations in the ring of double ended bolt fixing holes seen at 12 and 6 o’clock. These areas allowed two ‘push’ screws to be threaded into corresponding locations in the face plate. These could then be screwed down to provide a pushing force to remove the face plate from the main housing seat. This retraction system was required owing to the very tight fit of the face plate due to the narrow ‘piston fit’ tolerances and the vacuum effect of a soft gasket that was employed between the faces. 3D model by Ray Matter
Album | Turbopump 3D CAD |
Category | Turbo-pump |
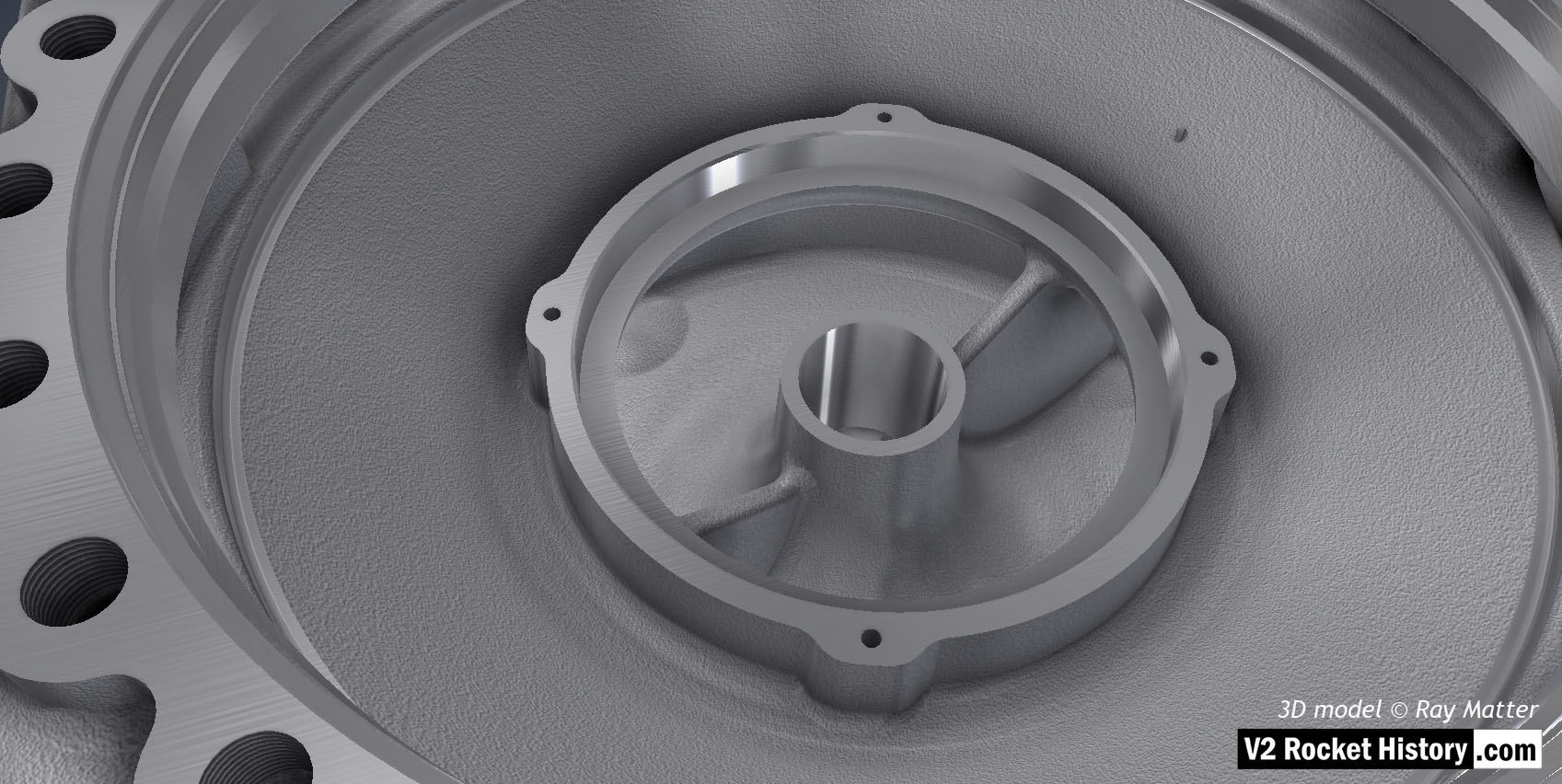
Close-up of ‘B’ fuel pump housing displaying cast and machined surfaces. Fuel inlet aperture shown with small purge orifice shown at 2 o’clock. 3D model by Ray Matter
Album | Turbopump 3D CAD |
Category | Turbo-pump |
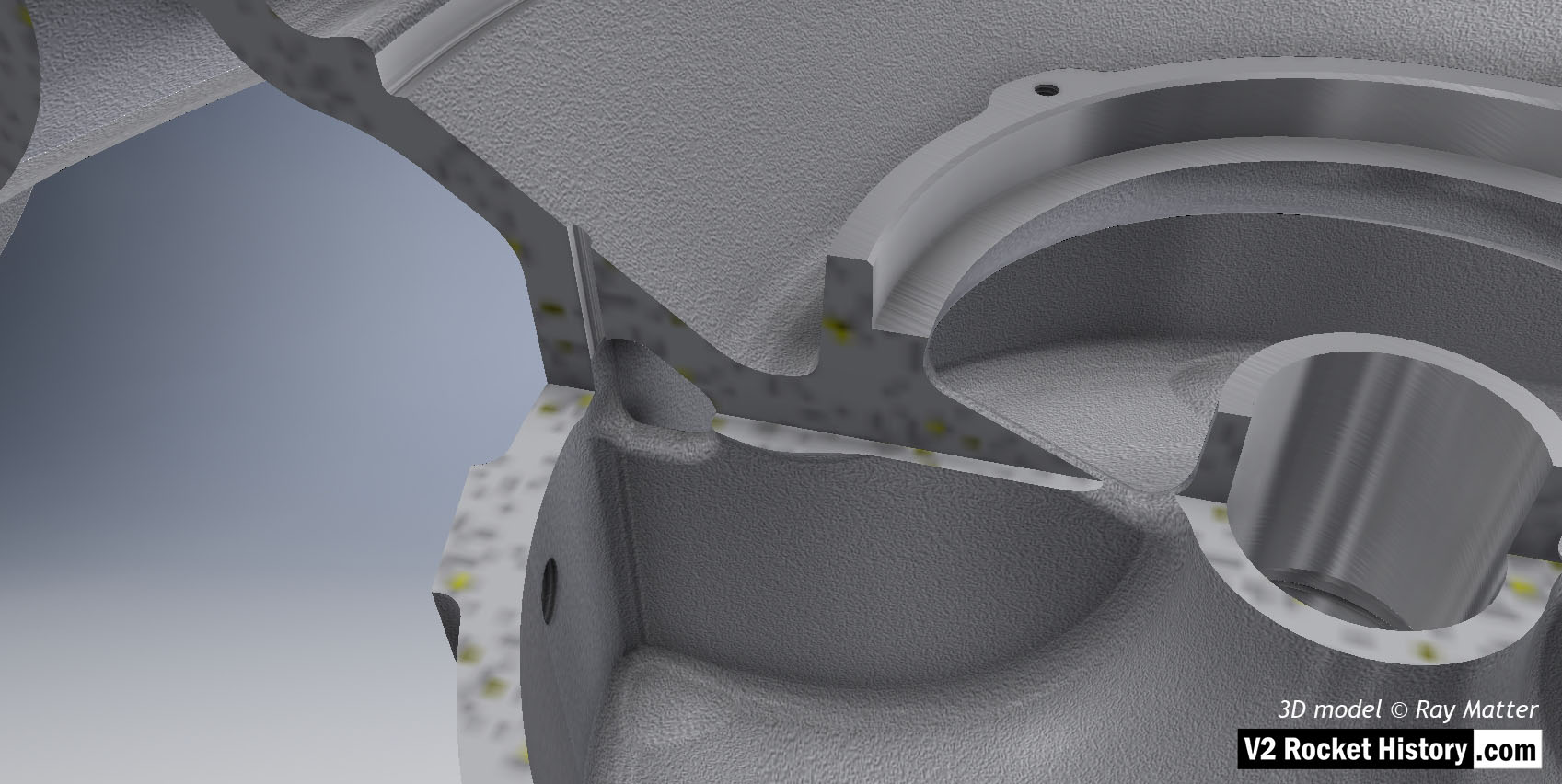
B Pump Housing, sectioned to show close-up of fuel bleed aperture and baffle vent for fuel pressure equalization between cavities inside the B pump casing. 3D model by Ray Matter
Album | Turbopump 3D CAD |
Category | Turbo-pump |
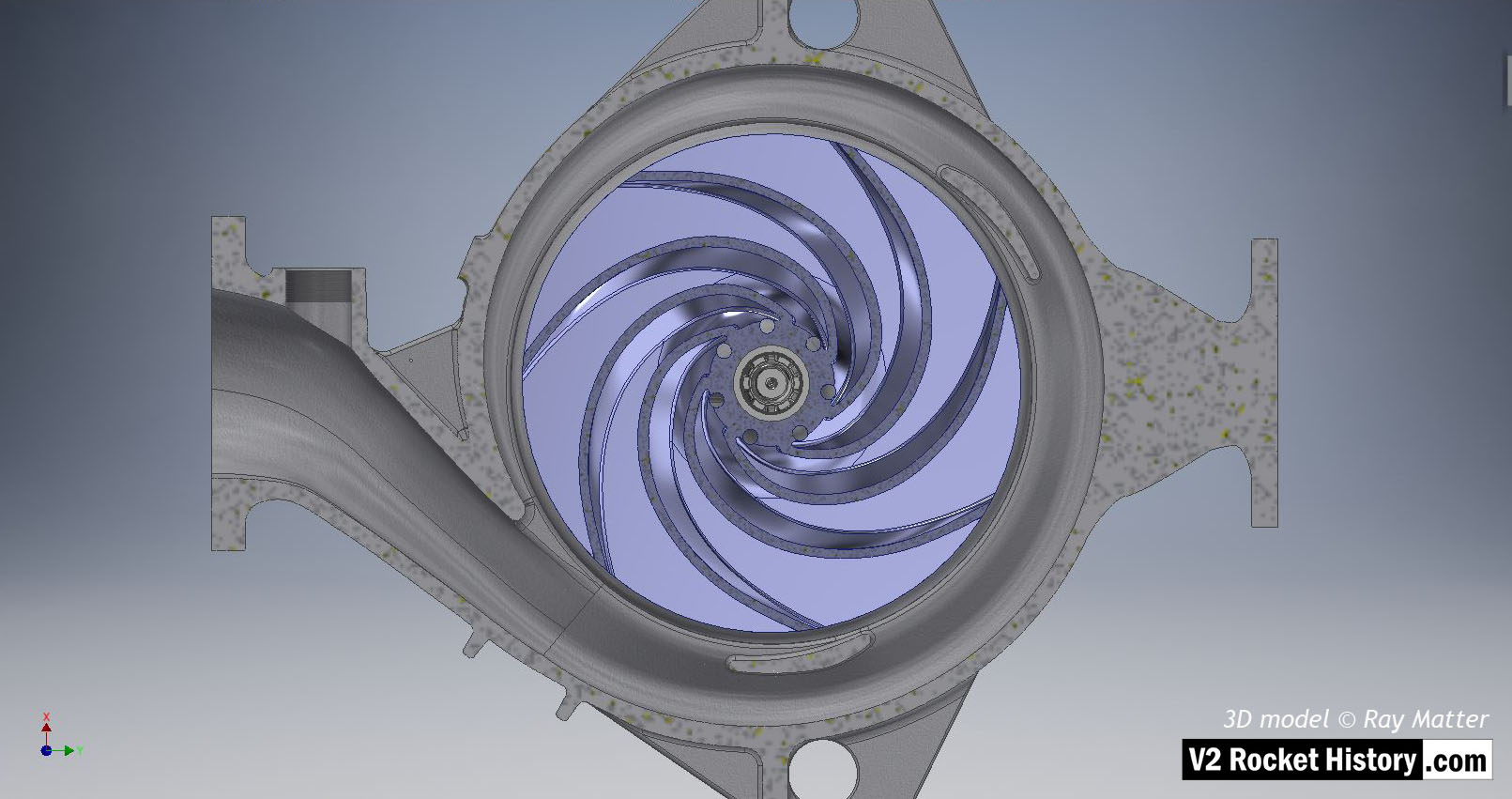
B (fuel) pump sub-assembly elevation view showing sectioned casing to reveal centrifugal pump impeller (in light purple for visibility). Outlet to left. The centrifugal pump impeller has been sectioned to remove one impeller face and reveal the curved vanes. The hub pass holes and end view of splined shaft are also shown. The spiral volute shape is very clear in this image. 3D model Ray Matter
Album | Turbopump 3D CAD |
Category | Turbo-pump |

B (fuel) pump sub-assembly showing sectioned casing to reveal centrifugal pump impeller (in light purple for visibility). Outlet to top right. The centrifugal pump rotor has been sectioned to remove one impeller face and reveal the curved vanes.The shaft and spiral volute space shape is very clear in this image. 3D model Ray Matter
Album | Turbopump 3D CAD |
Category | Turbo-pump |

B (fuel) pump sub-assembly showing sectioned casing to reveal centrifugal pump impeller. Outlet to btm right. The centrifugal pump impeller has been sectioned to remove one rotor face and reveal the curved vanes. The shaft and spiral volute space shape are shown in this image. 3D model Ray Matter
Album | Turbopump 3D CAD |
Category | Turbo-pump |

B-Pump sub-assembly sectioned to show fuel pump impeller inlet (purple area), baffle, and other shaft details. 3D model Ray Matter
Album | Turbopump 3D CAD |
Category | Turbo-pump |
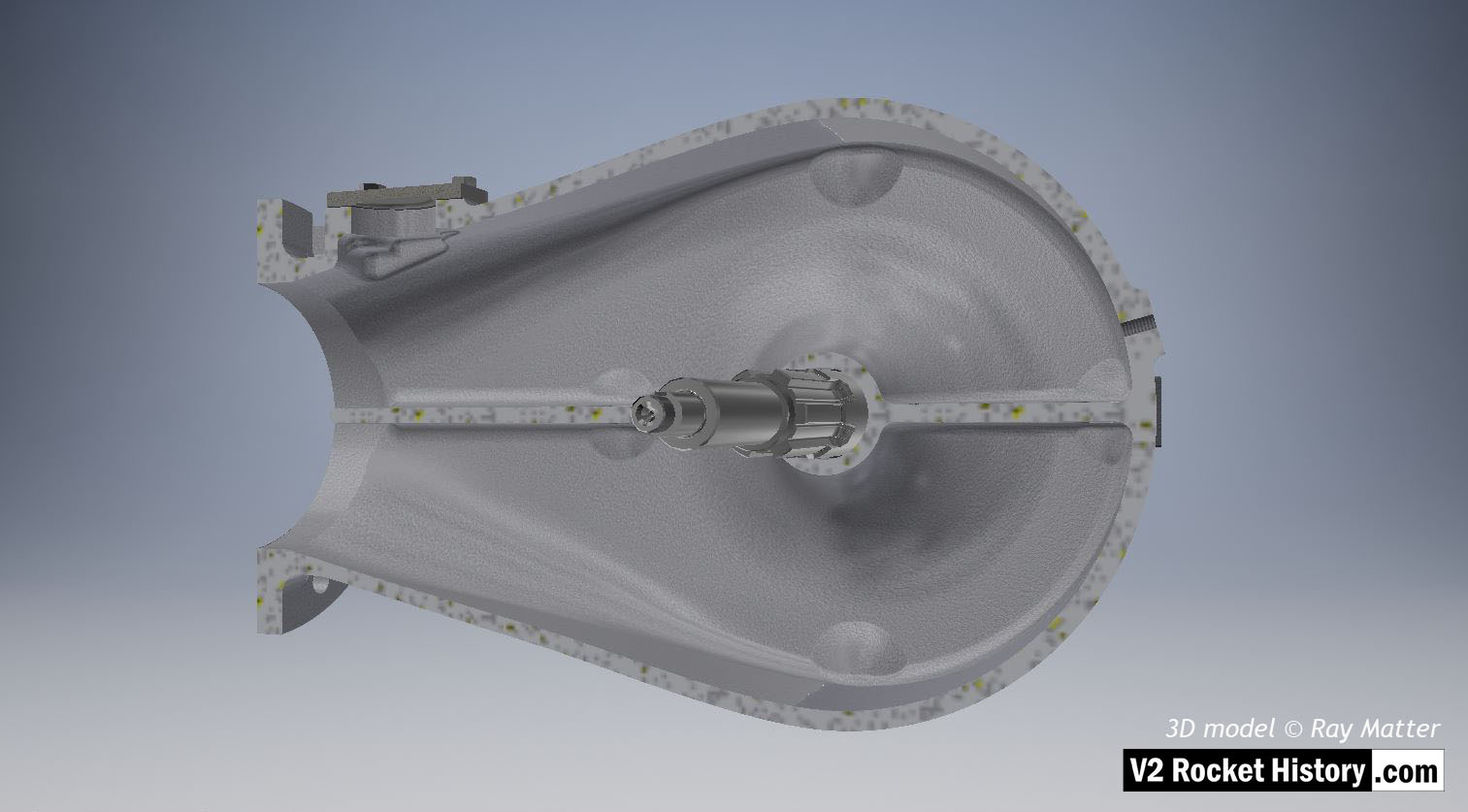
B-Pump sub-assembly casing sectioned to show shaft and fuel inlet chamber details. The throat blanking plate can be seen top left. 3D model Ray Matter
Album | Turbopump 3D CAD |
Category | Turbo-pump |
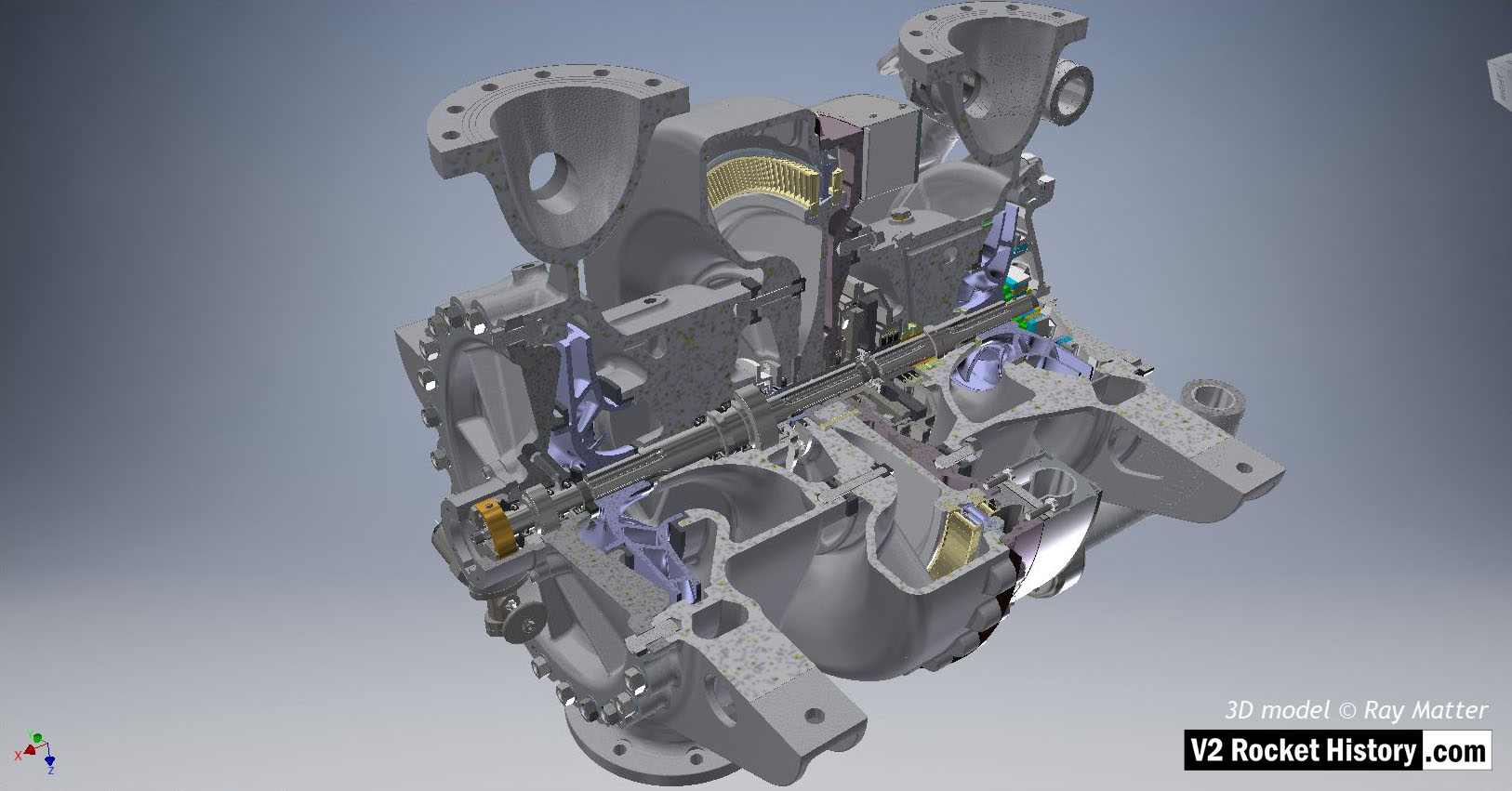
Turbine powered propellant pumps for A4/V2 rocket engine. The assembly is shown quarter sectioned and inverted with the propellant outlet flanges to the top and fuel pump on left, with inlet flanges at btm. The overspeed trip switch can be seen just below center on fuel pump face plate – the copper alloy centrifugal trip rotor is clearly visible in the trip-switch housing. 3D model by Ray Matter
Album | Turbopump 3D CAD |
Category | Turbo-pump |
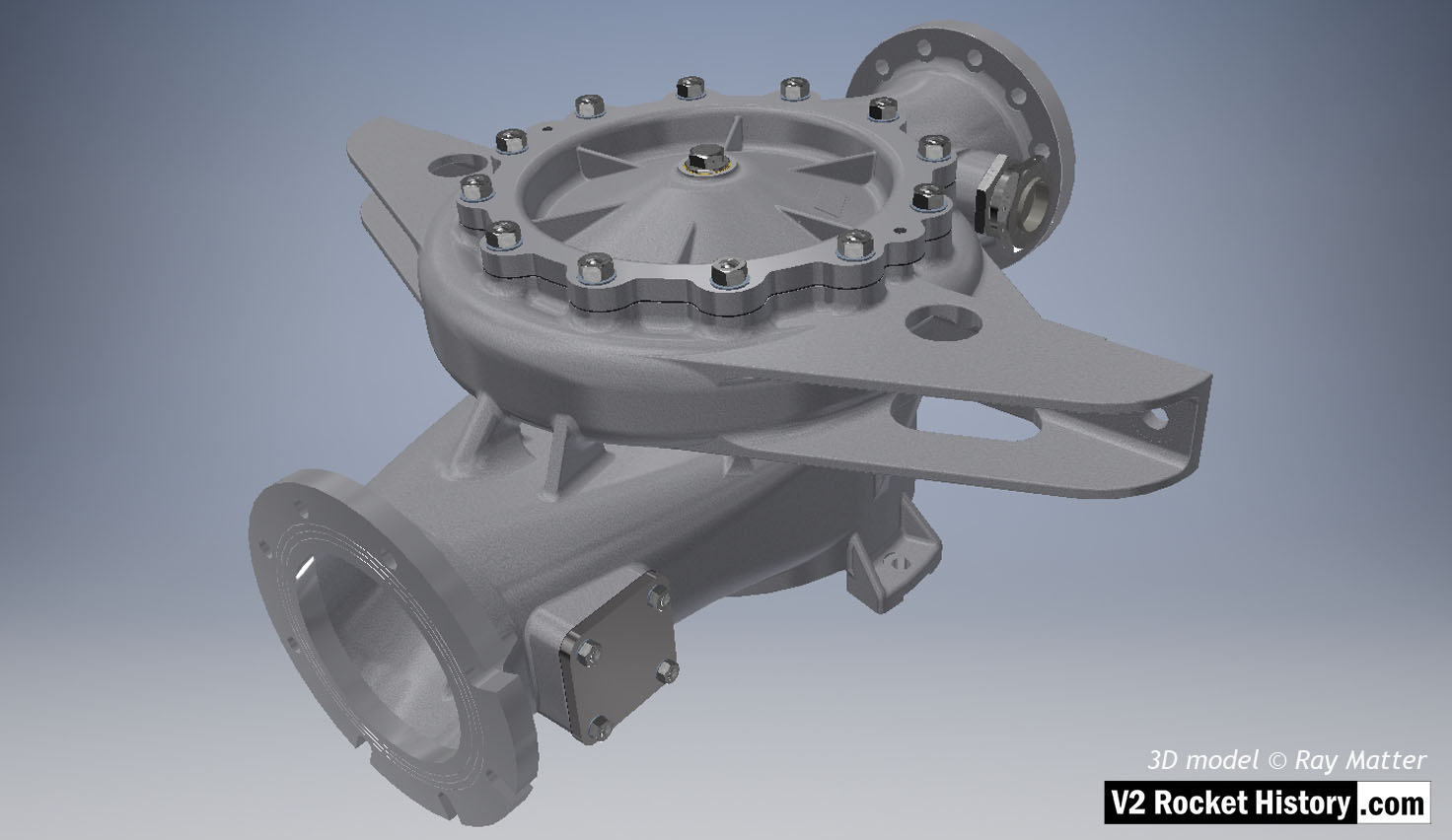
A-Pump LOX sub-assembly complete with face plate and fastenings as well as outlet throat plug. Shows square inlet throat blanking plate.
3D model Ray Matter
Album | Turbopump 3D CAD |
Category | Turbo-pump |
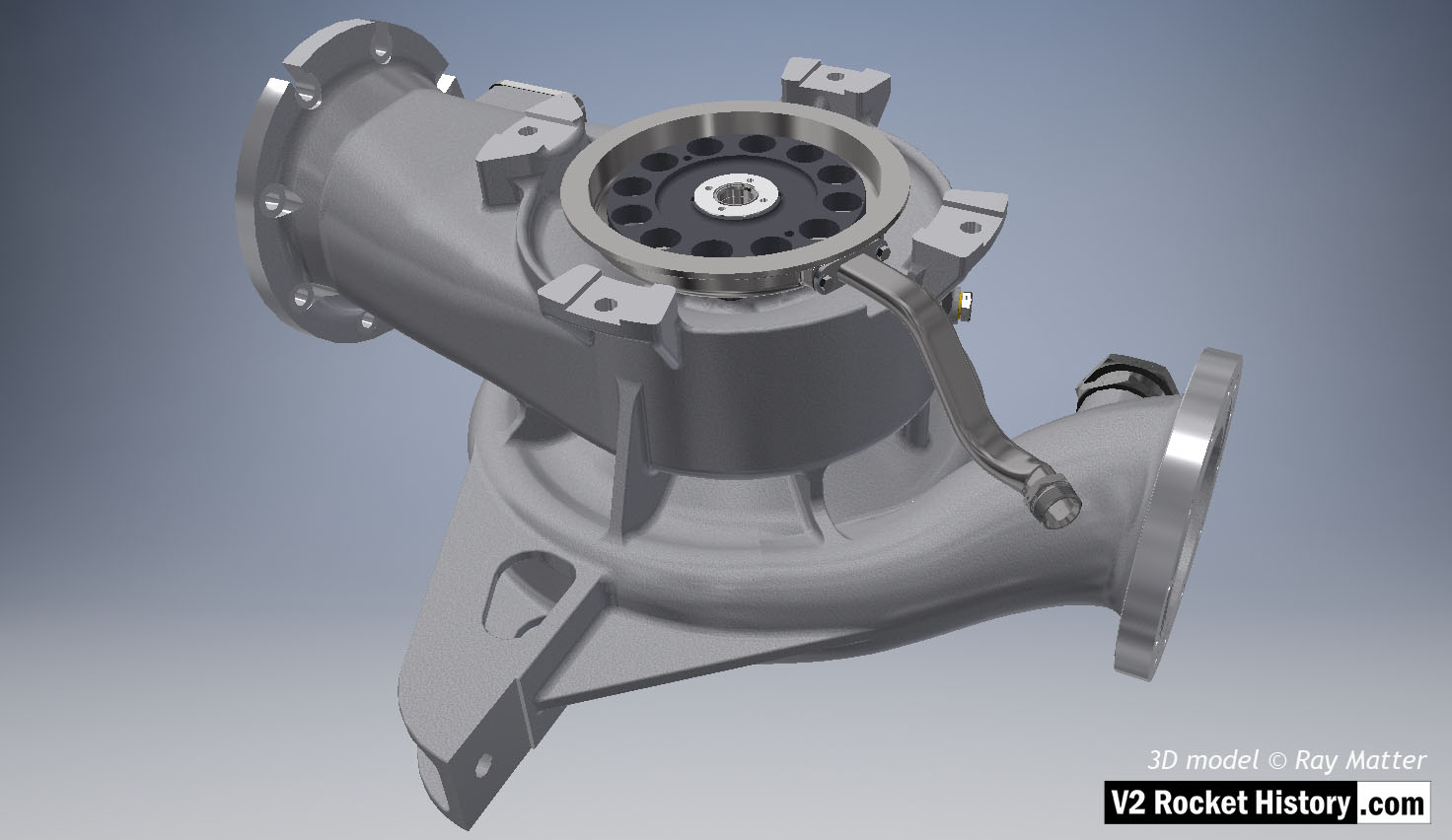
A (LOX) Pump sub-assembly, showing the face nearest the steam turbine. Turbine side of LOX pump showing flexible shaft connection disk (back component with 12 holes). The connection cavity drain pipe is shown (running across the outflow to the btm right). 3D model Ray Matter
Album | Turbopump 3D CAD |
Category | Turbo-pump |
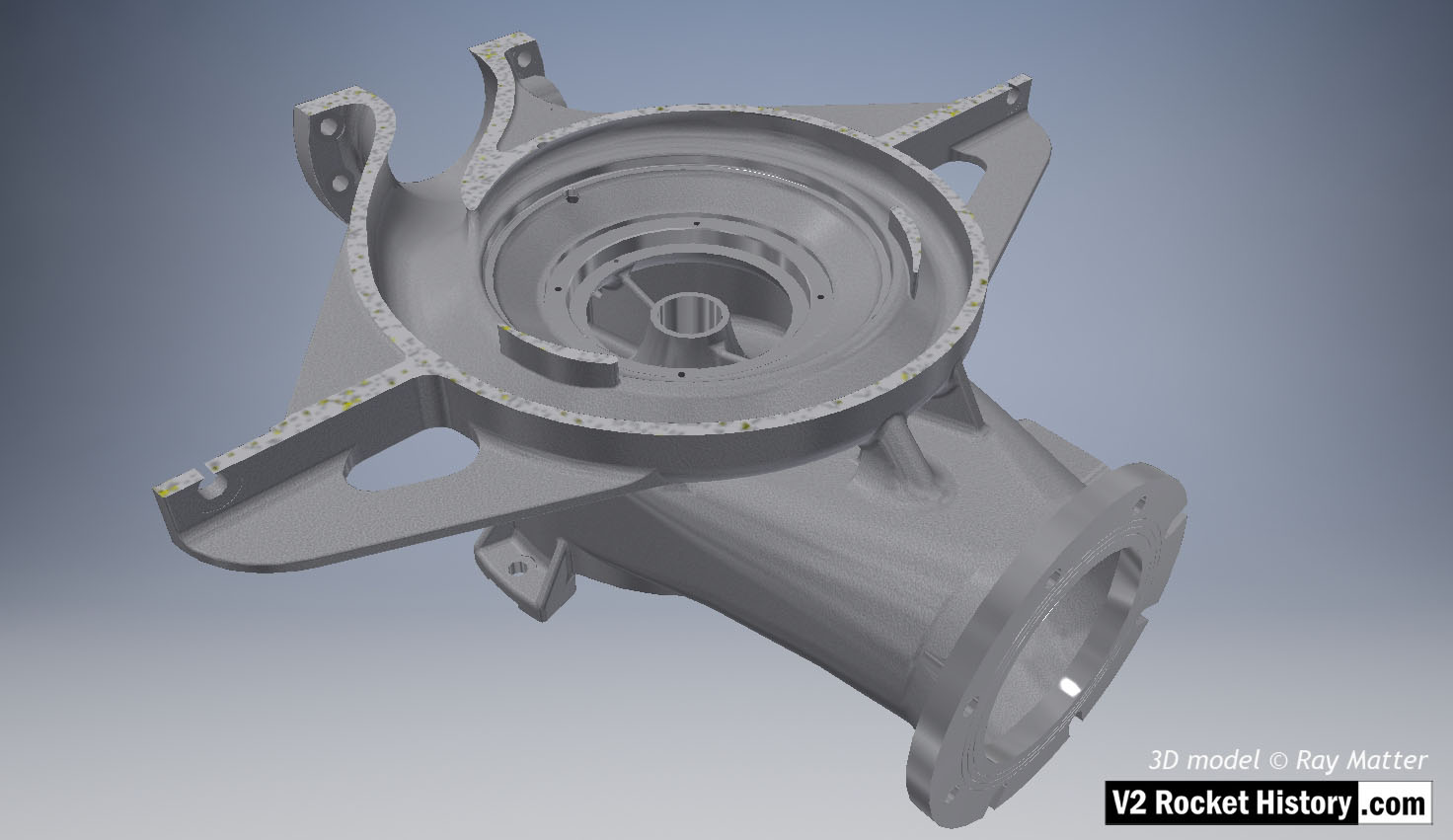
A (LOX) pump housing cutaway to reveal pump rotor side. The casing has been cut to show the internal rotor space detail. The outlet throat, right, and spiral volute space are displayed in this view as is the central LOX inlet. The web with the self-purge passageway can be seen on the outside center of the inlet throat, and connecting to the volute casing. The web or buttress seen to the upper right is to provide additional support between the structures whilst keeping the casting to an even density. 3D model Ray Matter
Album | Turbopump 3D CAD |
Category | Turbo-pump |

Close-up of ‘A’ LOX pump housing displaying cast and machined surfaces. LOX inlet aperture shown wand external threaded hole for manual bleed plug shown on far right. 3D model by Ray Matter
Album | Turbopump 3D CAD |
Category | Turbo-pump |
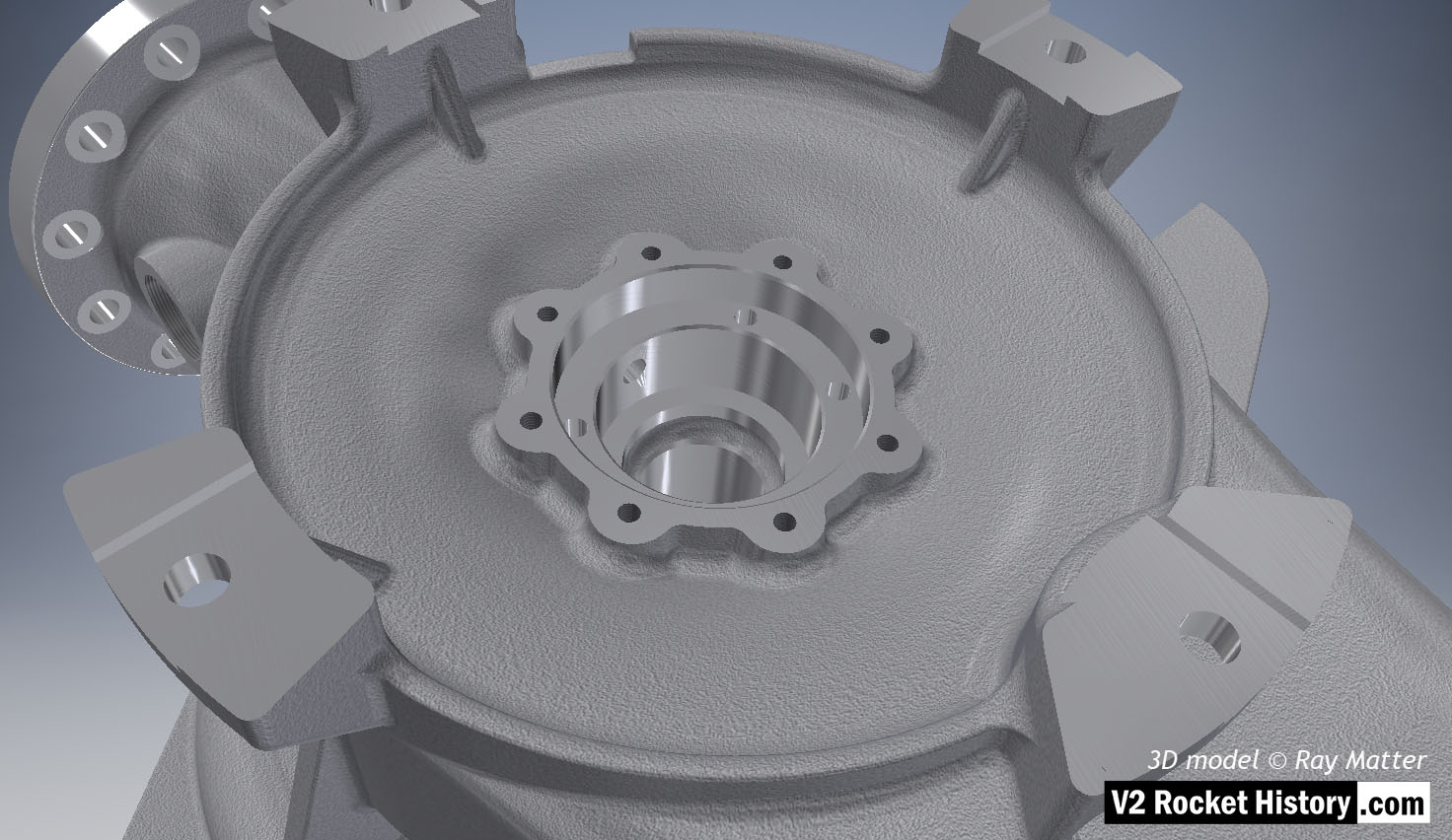
A (LOX) Pump sub-assembly, showing the face nearest the steam turbine. Single piece casting showing machined (milled) areas and detail of bearing and seal cavity. The four turbine case fitting brackets are displayed. 3D model Ray Matter
Album | Turbopump 3D CAD |
Category | Turbo-pump |
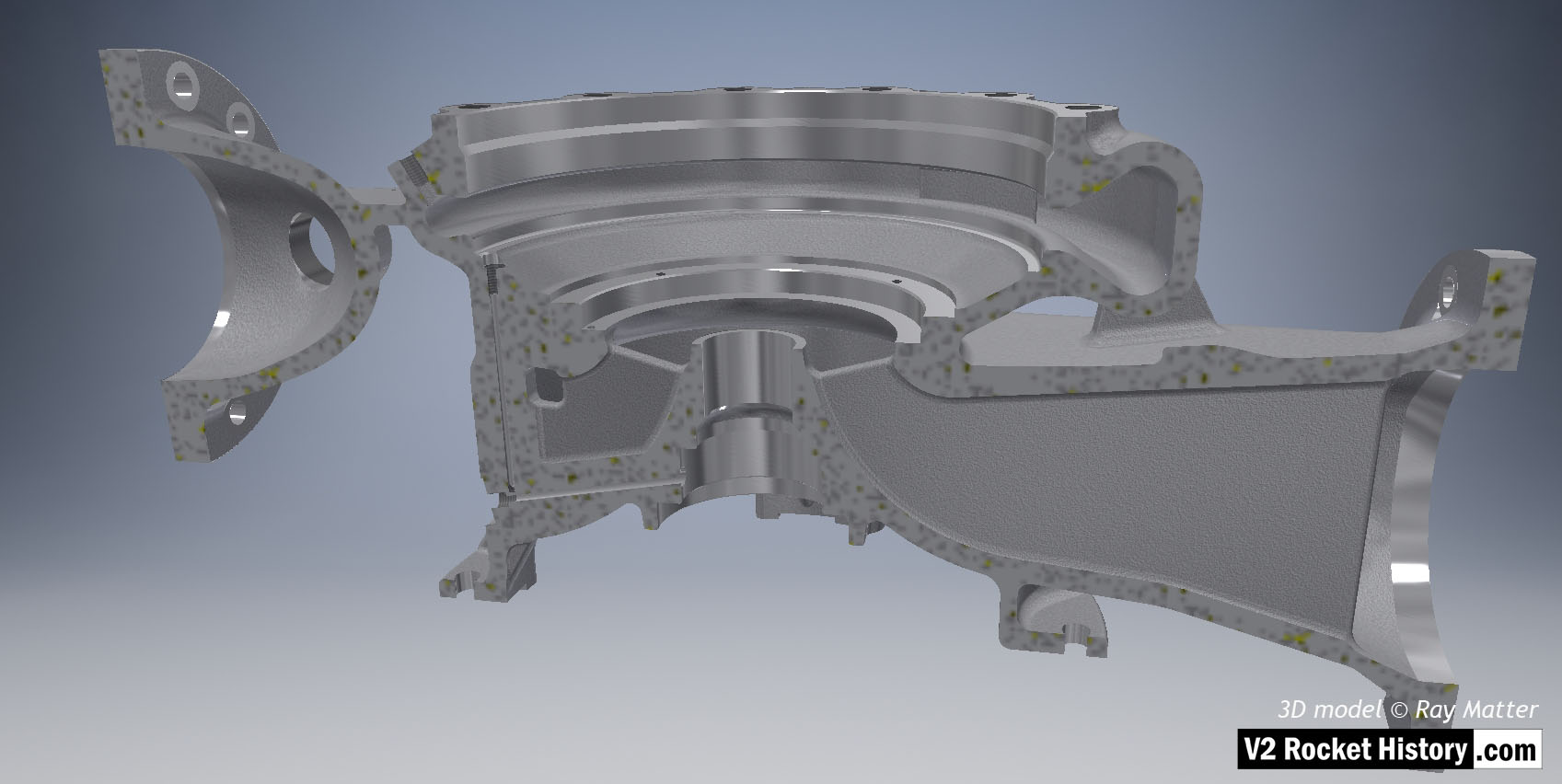
A (LOX) Pump housing sectioned to show baffle and volute space area expansion as flow passes from inlet (right) to outlet (left). Note cast and machined (milled) areas shown in this image – especially inlet aperture. 3D model Ray Matter
Album | Turbopump 3D CAD |
Category | Turbo-pump |
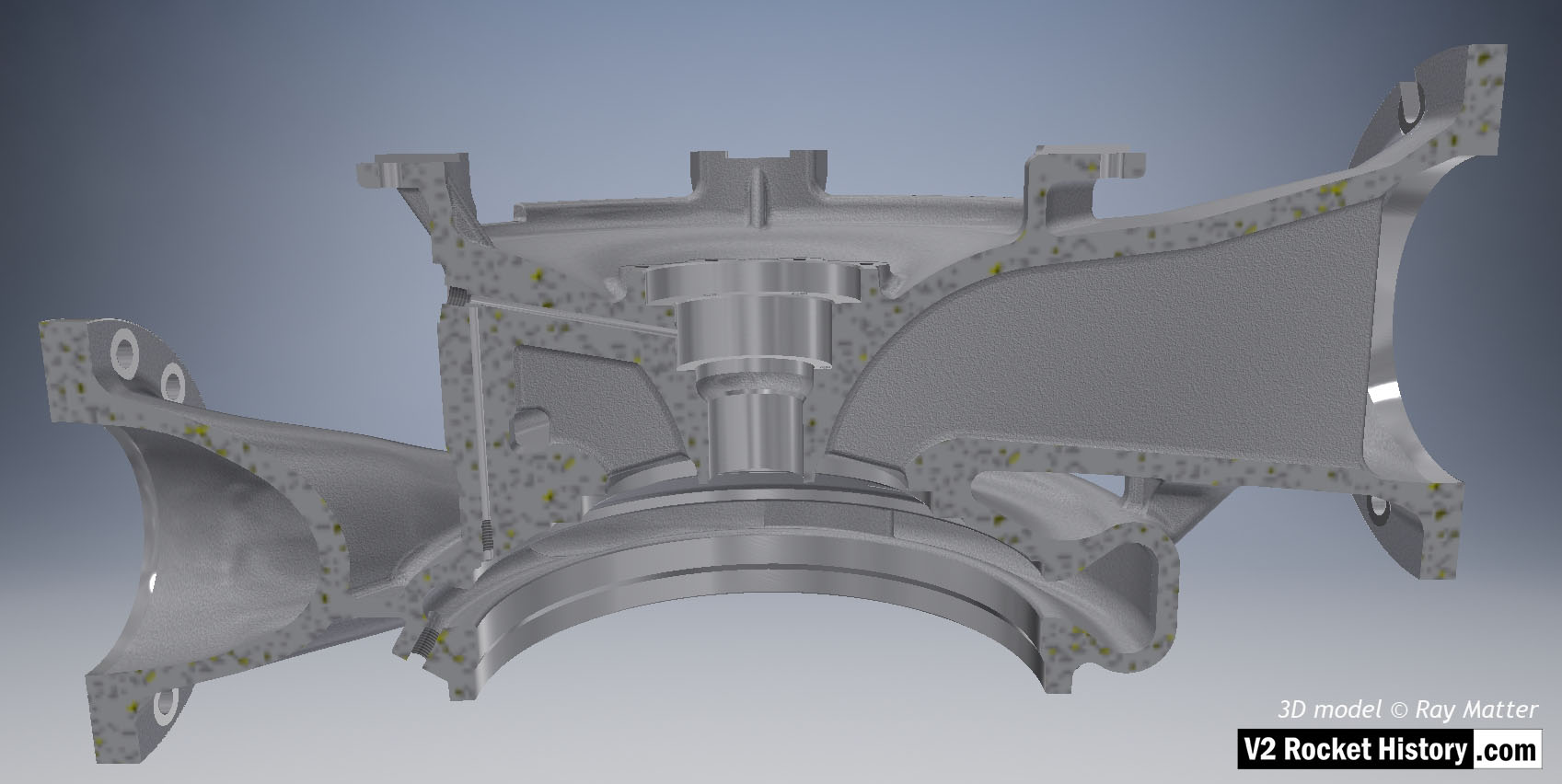
A (LOX) Pump housing sectioned to show baffle and volute space area expansion as flow passes from inlet (right) to outlet (left). Note the small LOX passageways on left from high-pressure volute space to bearing cavity. 3D model Ray Matter
Album | Turbopump 3D CAD |
Category | Turbo-pump |
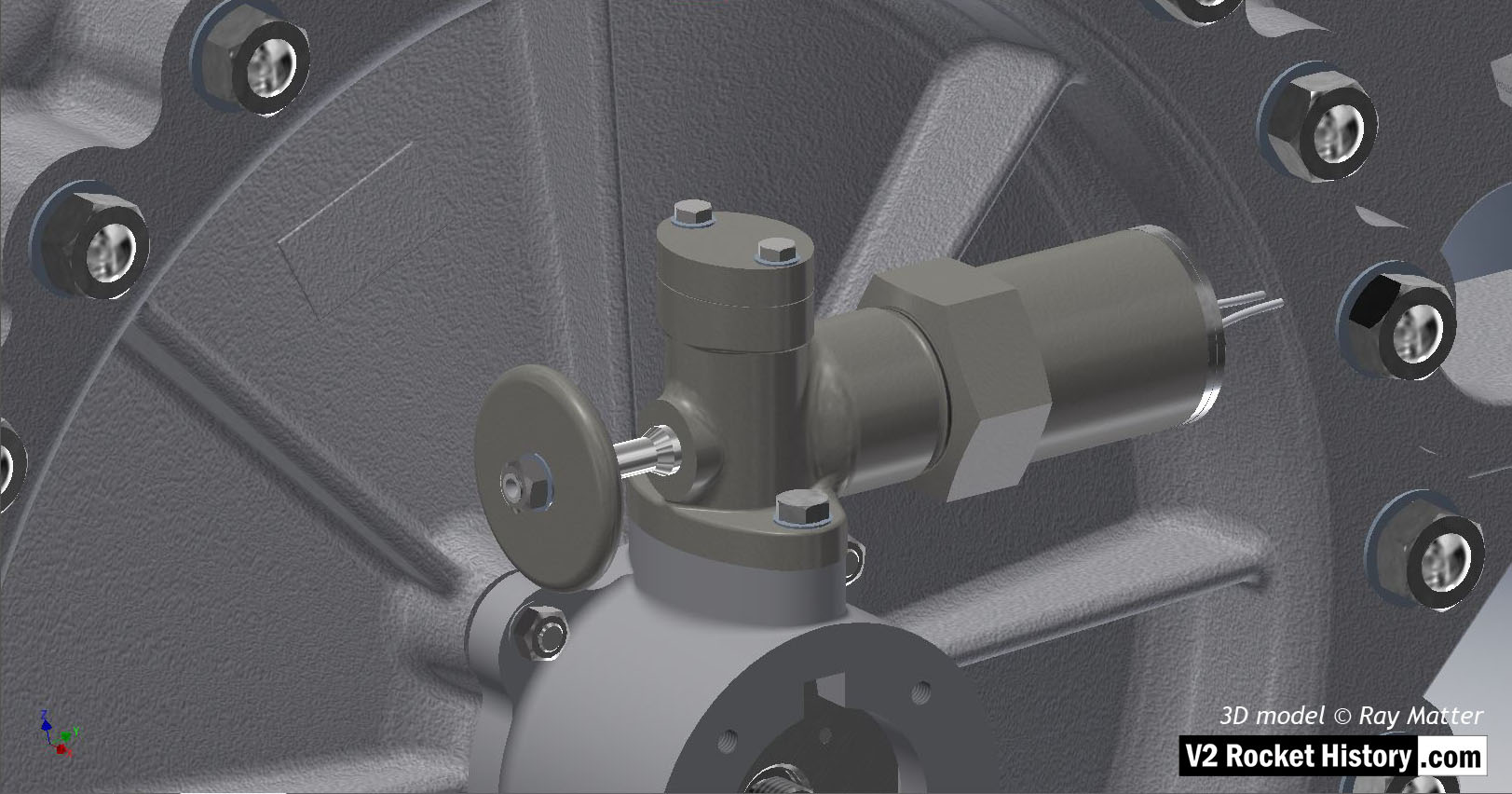
Detail of fuel pump face plate showing over-speed switch and mounting. The switch plunger (part with disc shaped hand knob on left) is shown in the out or armed position. The RPM of the tubo-pump (TP) was not governed but this safety mechanism shut the TP down permanently when the RPM reached 5000. Although rarely changed, thin shims could be used to reduce or increase this speed. 3D model Ray Matter
Album | Turbopump 3D CAD |
Category | Turbo-pump |
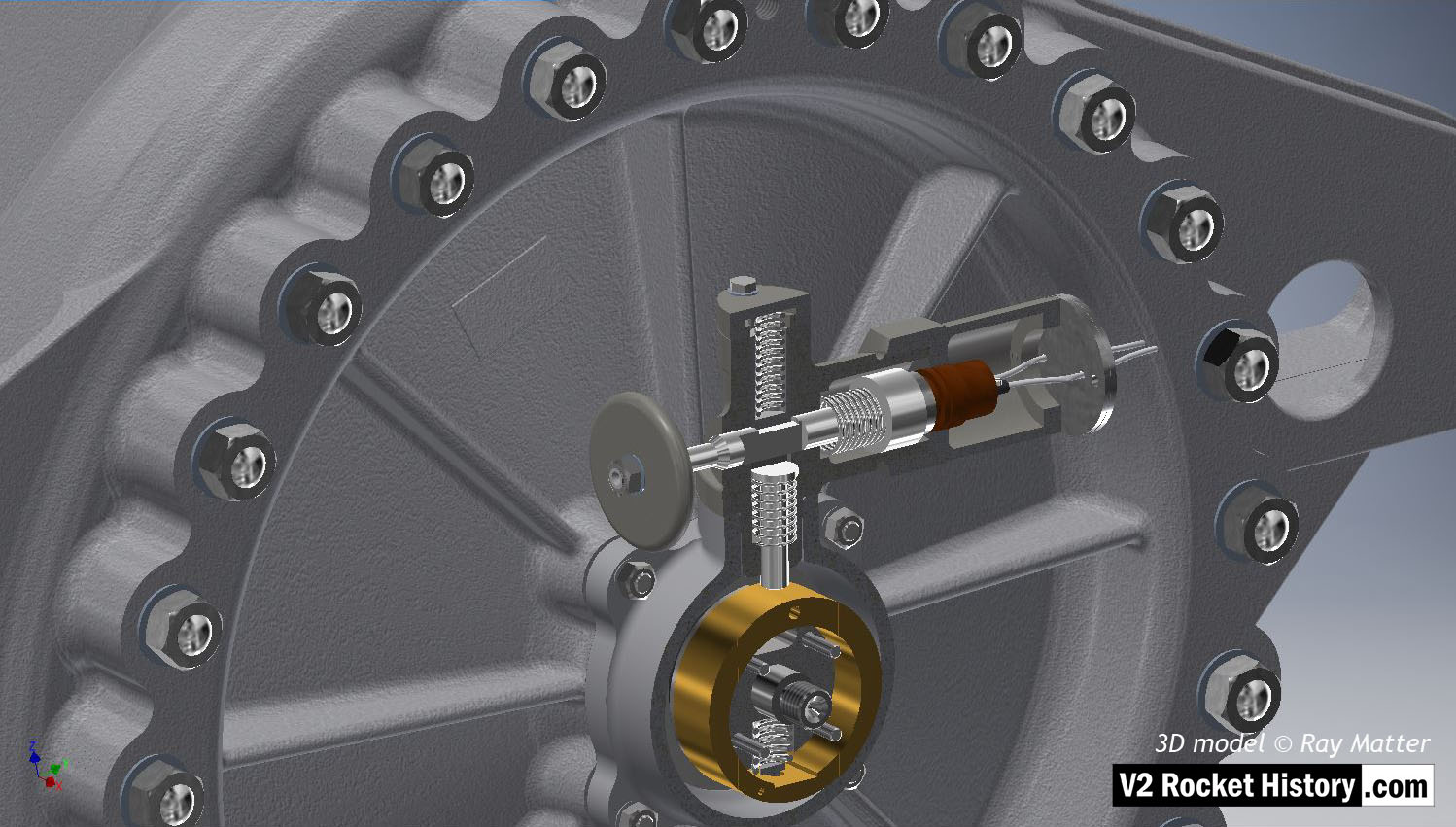
Detail of fuel pump face plate showing over-speed switch and mounting. The eccentric centrifugal rotor can be seen (brass coloured part). This unbalanced part rotates against a spring load that allows the thicker (proportionally heavier) section of the rotor to move outwards from the center as the rotational speed rises and push the release rod clear of a keyed section of the plunger shaft (part with disc shaped knob on left) thus operating a relay switch that shuts down the flow of steam to the turbine. 3D model Ray Matter
Album | Turbopump 3D CAD |
Category | Turbo-pump |
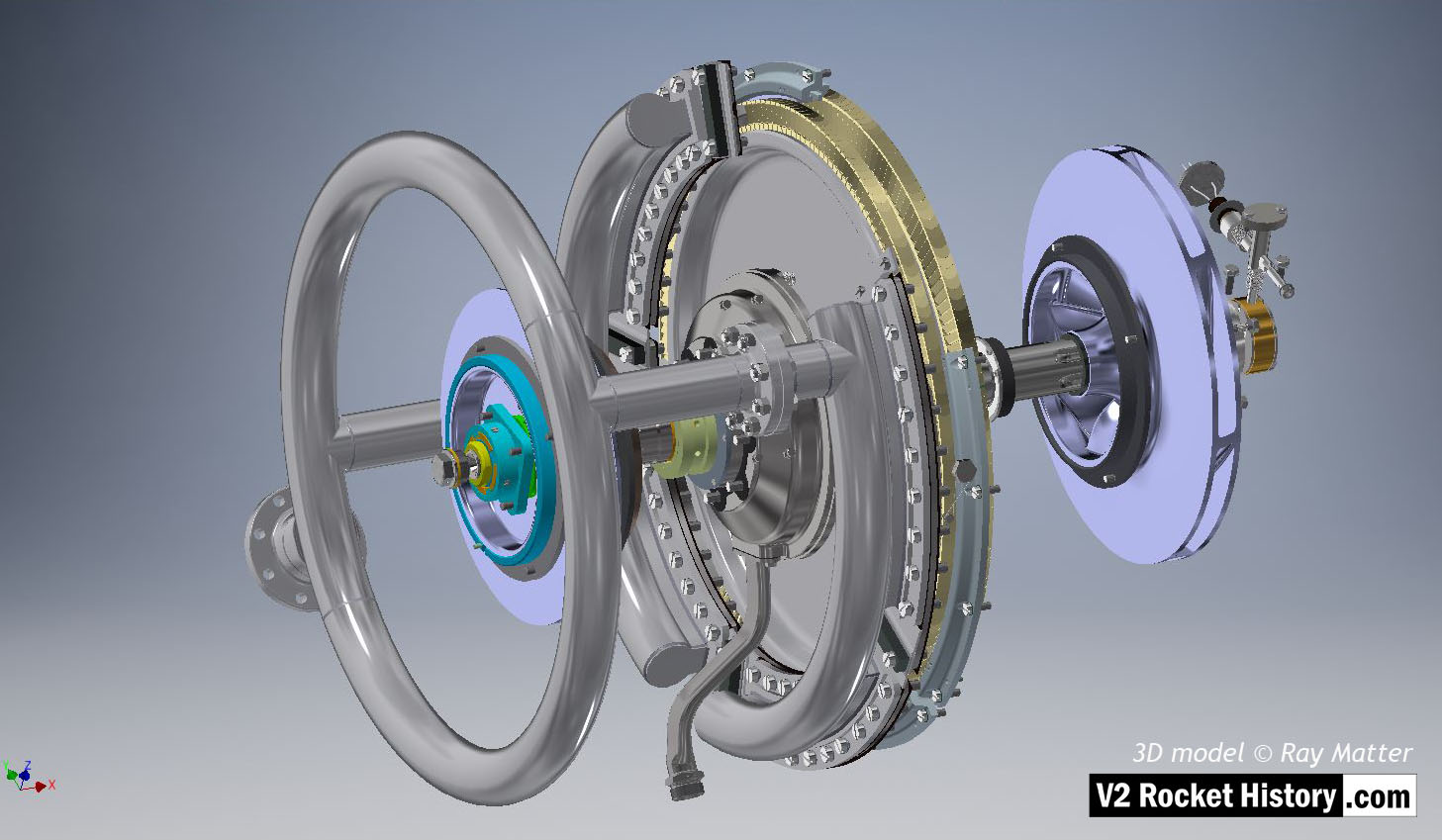
V2 turbo-pump turbine and pump impeller shaft assembly showing steam turbine rotor with nozzle assembly and steam inlet manifold distributor ring. The two rows of steam buckets can seen on rotor rim. Fuel pump impeller (purple) and over-speed switch are shown to the right. LOX pump impeller (purple) with journal bearing box and four sectional bronze bearings visible. An overboard dump pipe can be seen lower left of steam rotor. 3D model Ray Matter
Album | Turbopump 3D CAD |
Category | Turbo-pump |
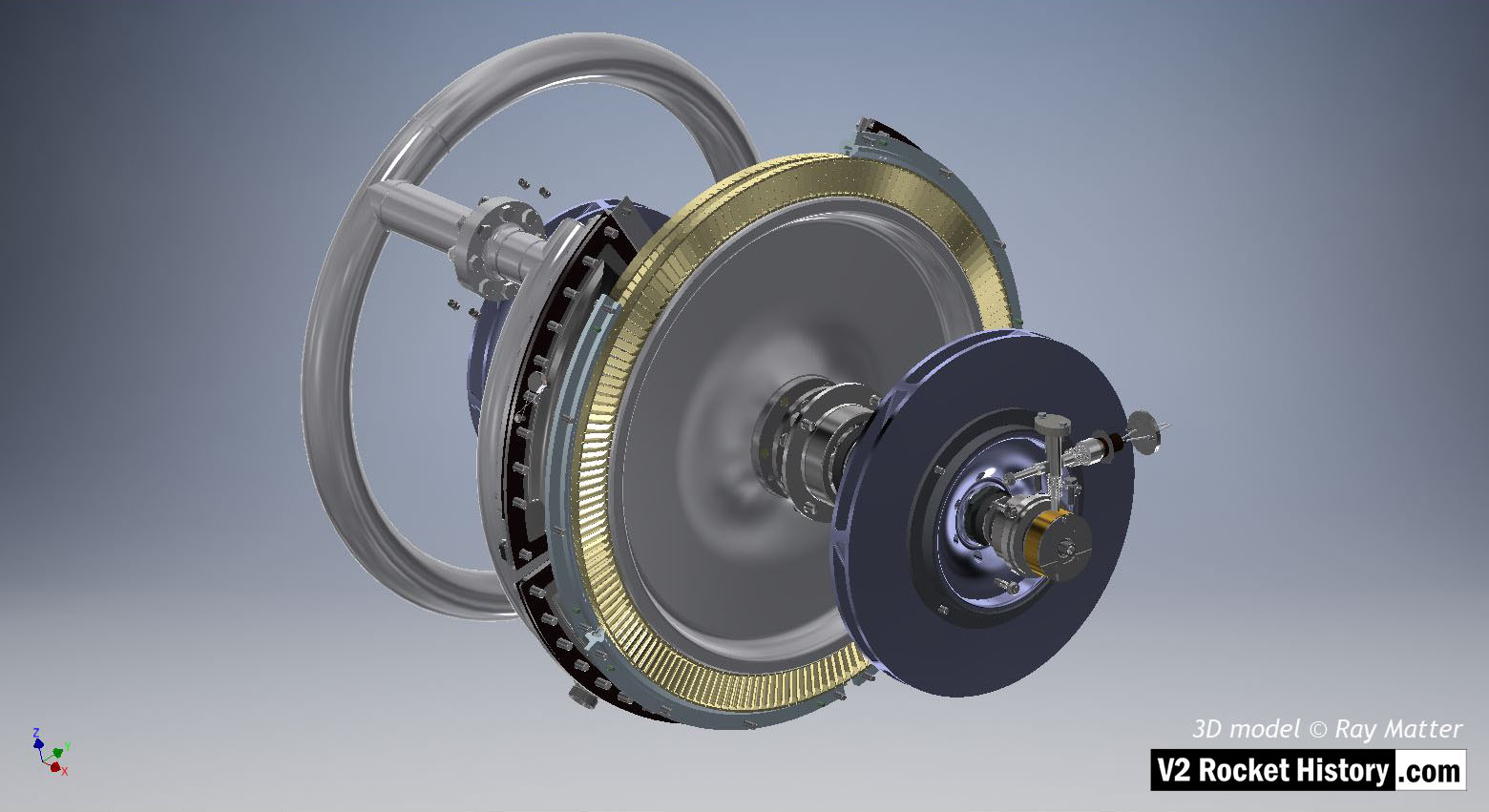
V2 turbo-pump turbine and pump impeller shaft assembly showing steam turbine rotor with nozzle assembly and steam inlet manifold distributor ring to left. The two rows of steam buckets can seen on rotor rim as well as three of the four sets of stationary steam return blades. Fuel pump impeller and over-speed switch are shown to the right. 3D model Ray Matter
Album | Turbopump 3D CAD |
Category | Turbo-pump |
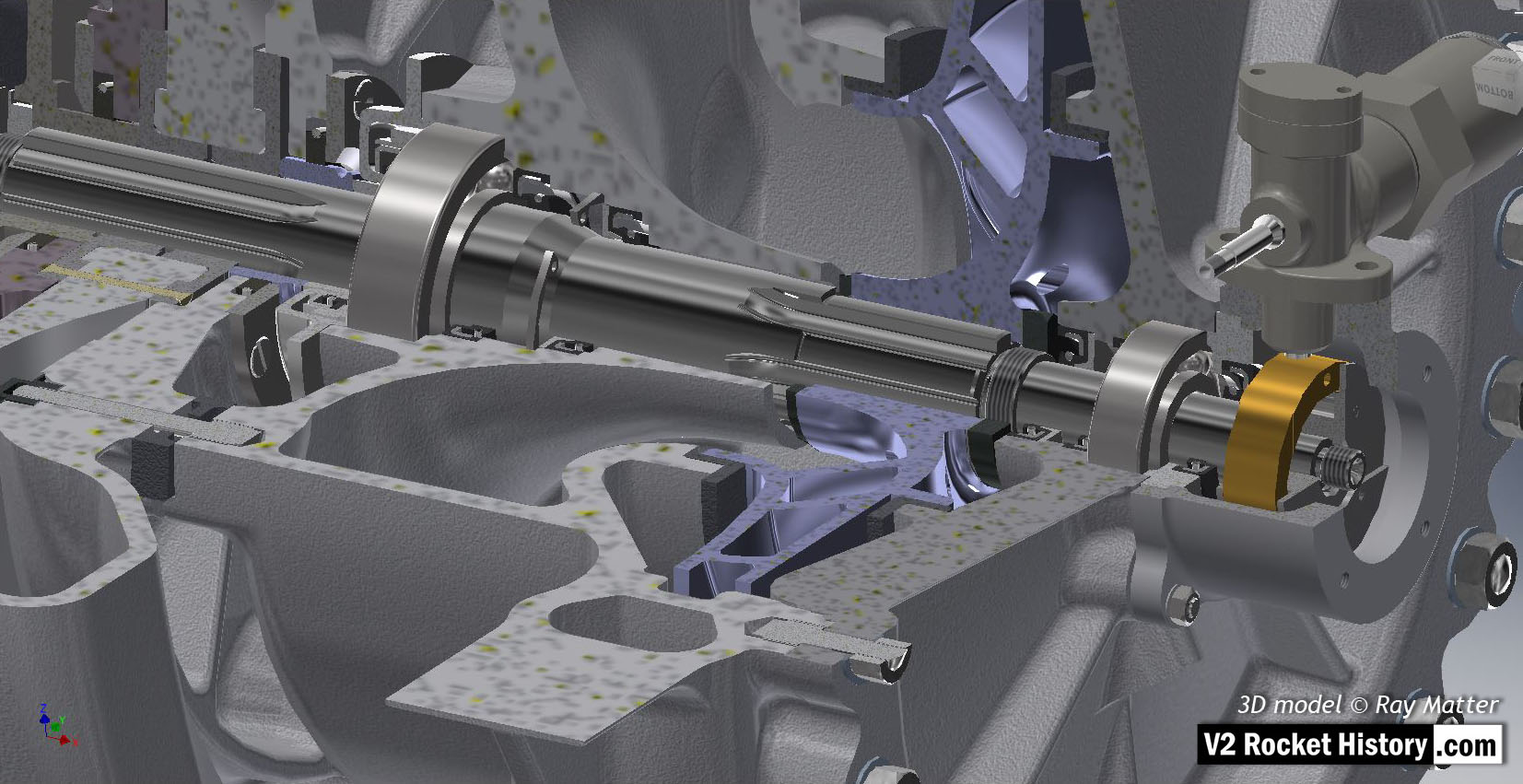
B (fuel) Pump: Close-up of sectioned turbine and pump impellers. Pump impeller (purple) and turbine rotor, top left, showing, seals, bearings and over-speed centrifugal rotor assembly. 3D model Ray Matte
Album | Turbopump 3D CAD |
Category | Turbo-pump |
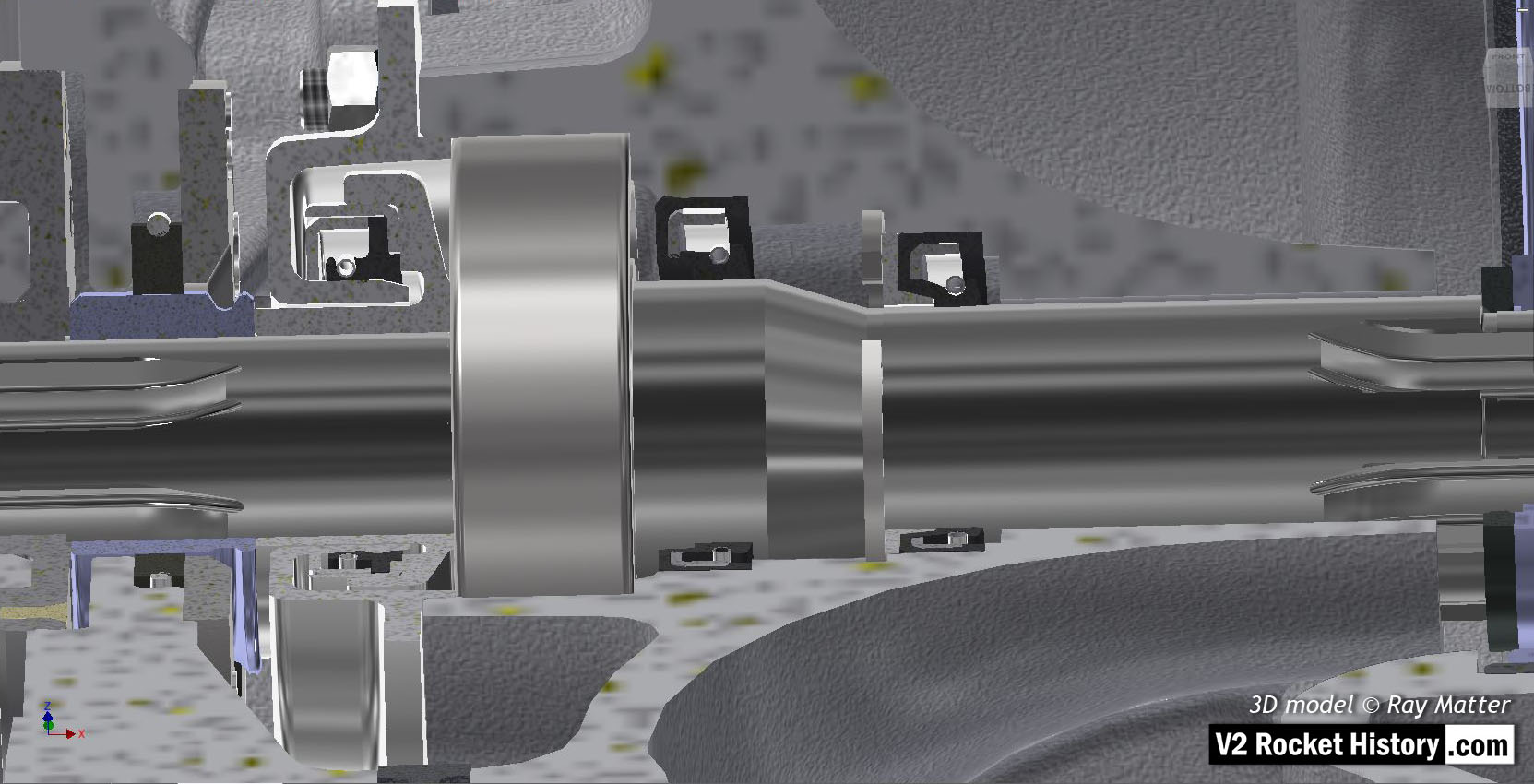
06 B Pump close-up showing shaft bearing and isolation seals at at pump to turbine mating point. 3D model Ray Matter
Album | Turbopump 3D CAD |
Category | Turbo-pump |
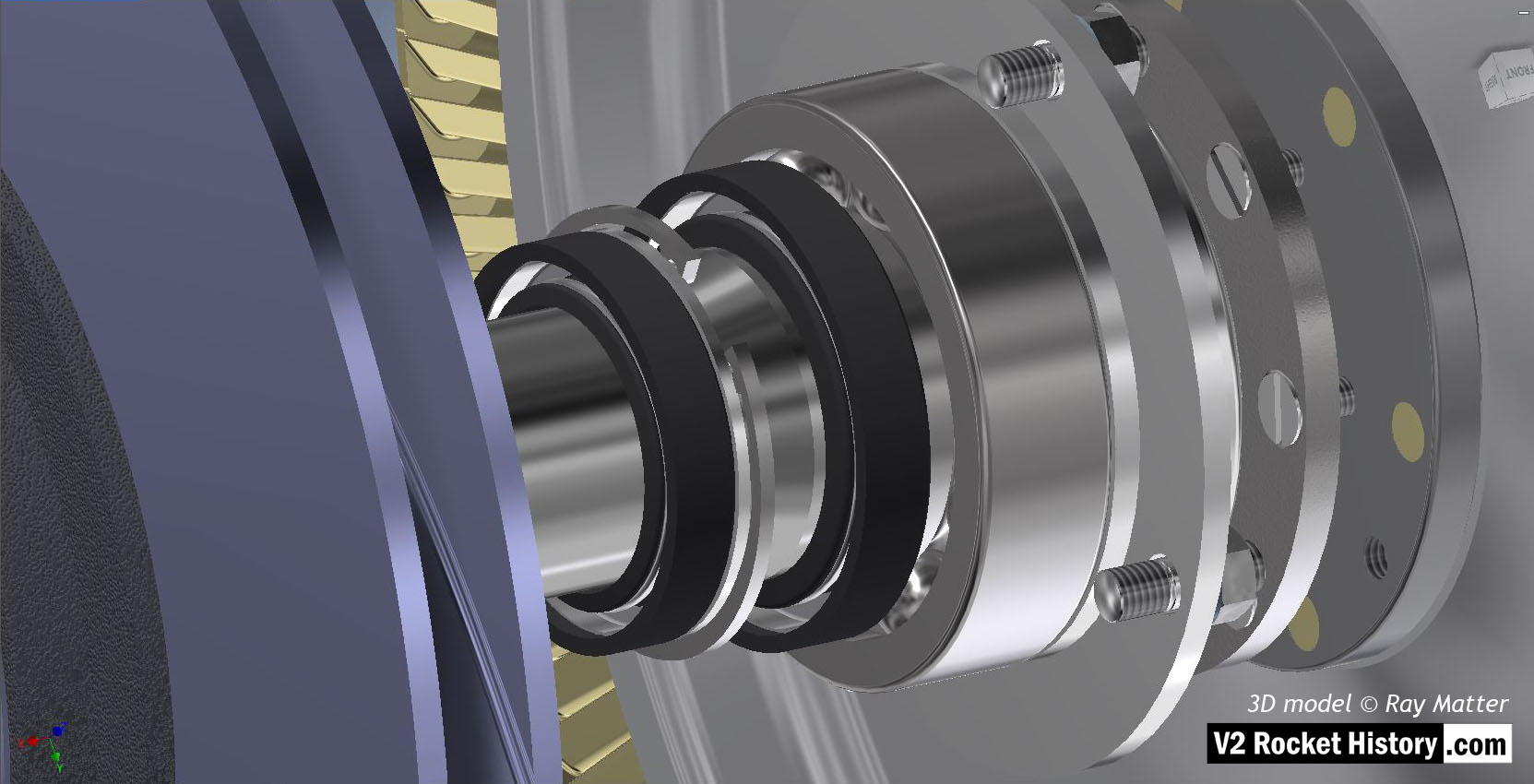
06 B Pump showing shaft area from fuel pump impeller, left (purple), to steam rotor. Shows seals, packer, circlip, and steam rotor hub. 3D model Ray Matter
Album | Turbopump 3D CAD |
Category | Turbo-pump |
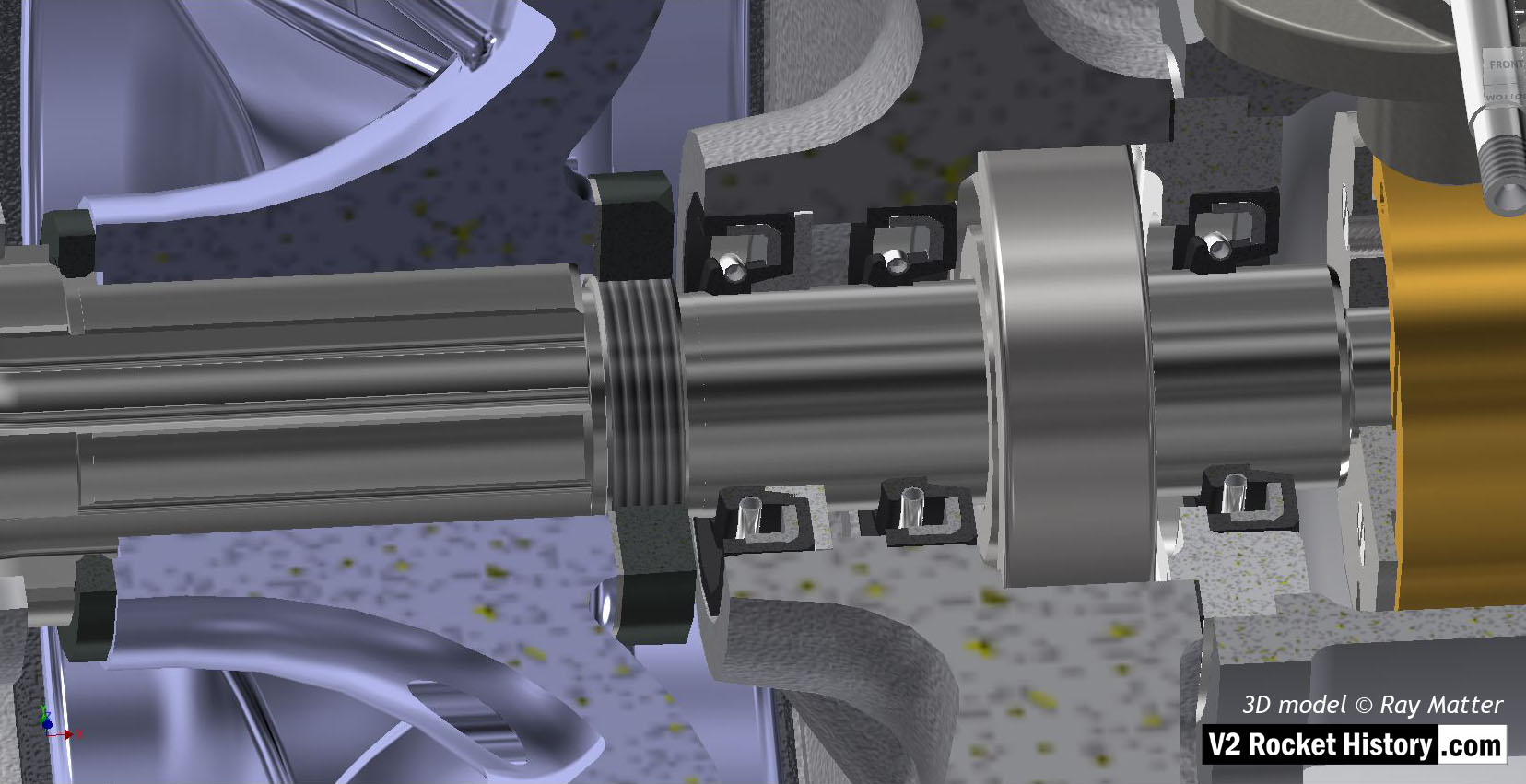
B (fuel) Pump: Close-up of sectioned pump impeller hub (purple) showing, left to right, seals, bearing and over-speed centrifugal rotor. 3D model Ray Matter
Album | Turbopump 3D CAD |
Category | Turbo-pump |
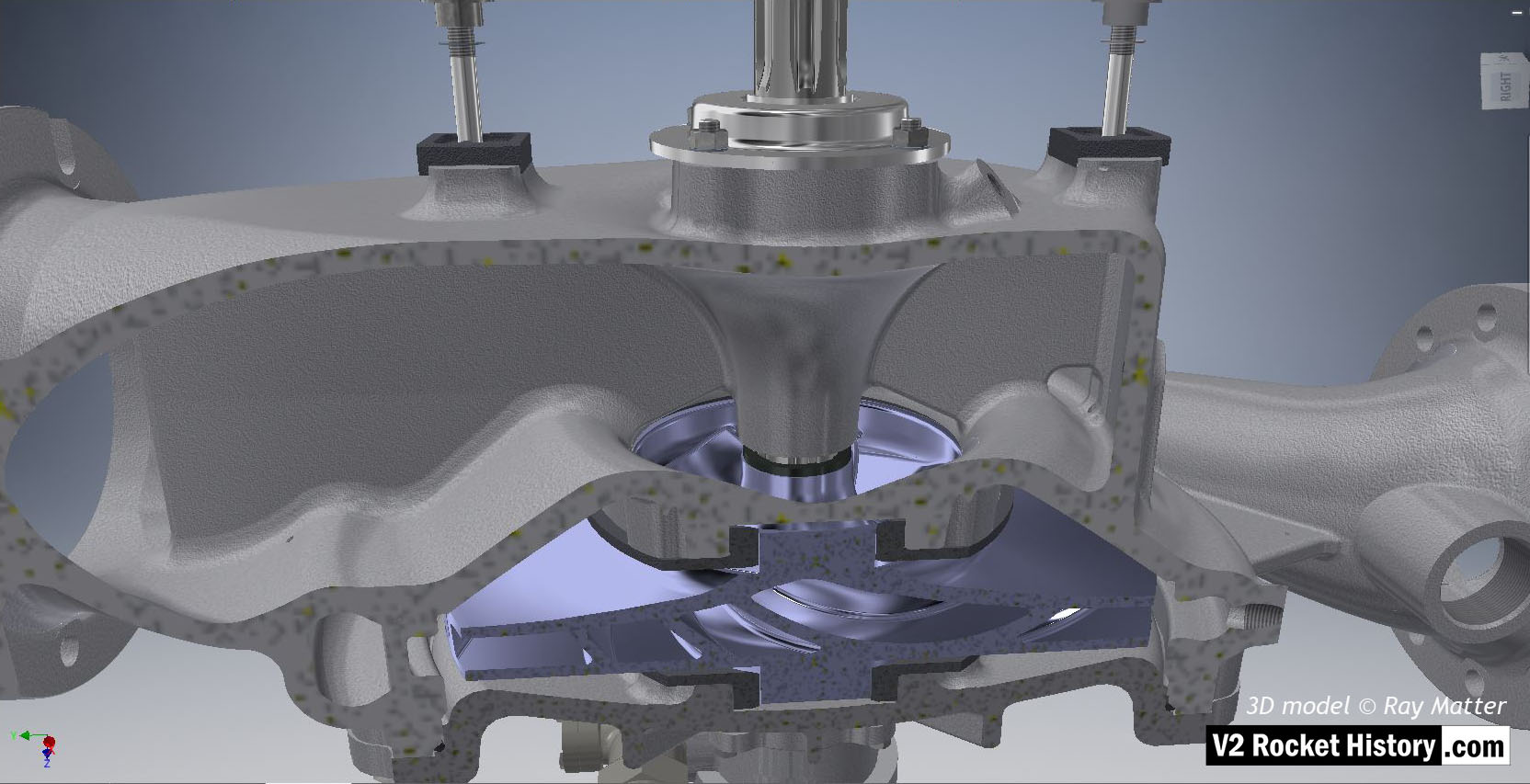
B (fuel) pump sub-assembly showing sectioned casing to reveal centrifugal pump impeller (in light purple for visibility). Outlet to right. Note inlet throat purge aperture of left. 3D model Ray Matter
Album | Turbopump 3D CAD |
Category | Turbo-pump |
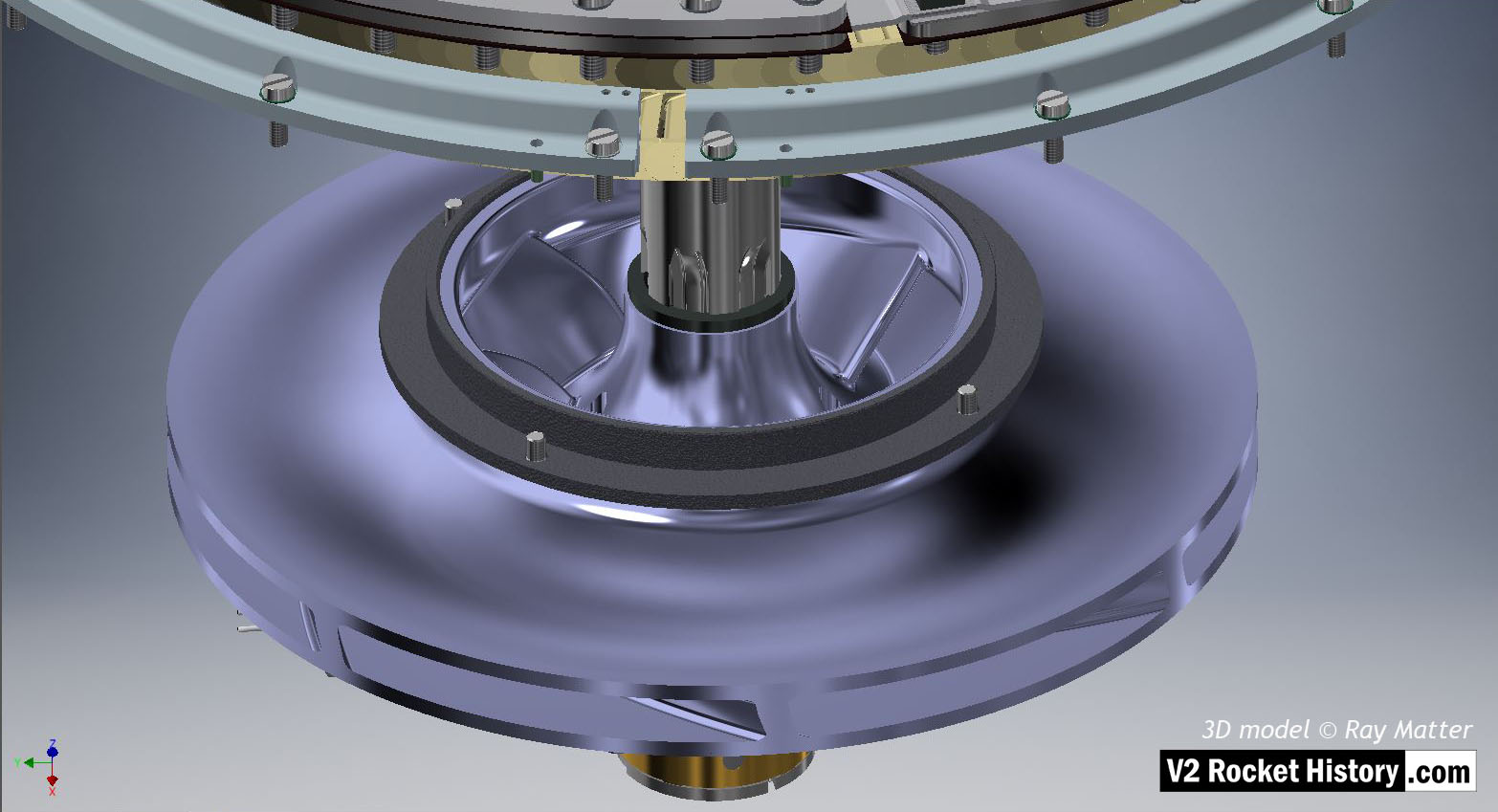
B pump casing removed to show fuel pump impeller and bearing ring. The steam rotor assembly can be seen at the top of the image and two sets of the stationary steam blades, or stators, are also visible.
Album | Turbopump 3D CAD |
Category | Turbo-pump |
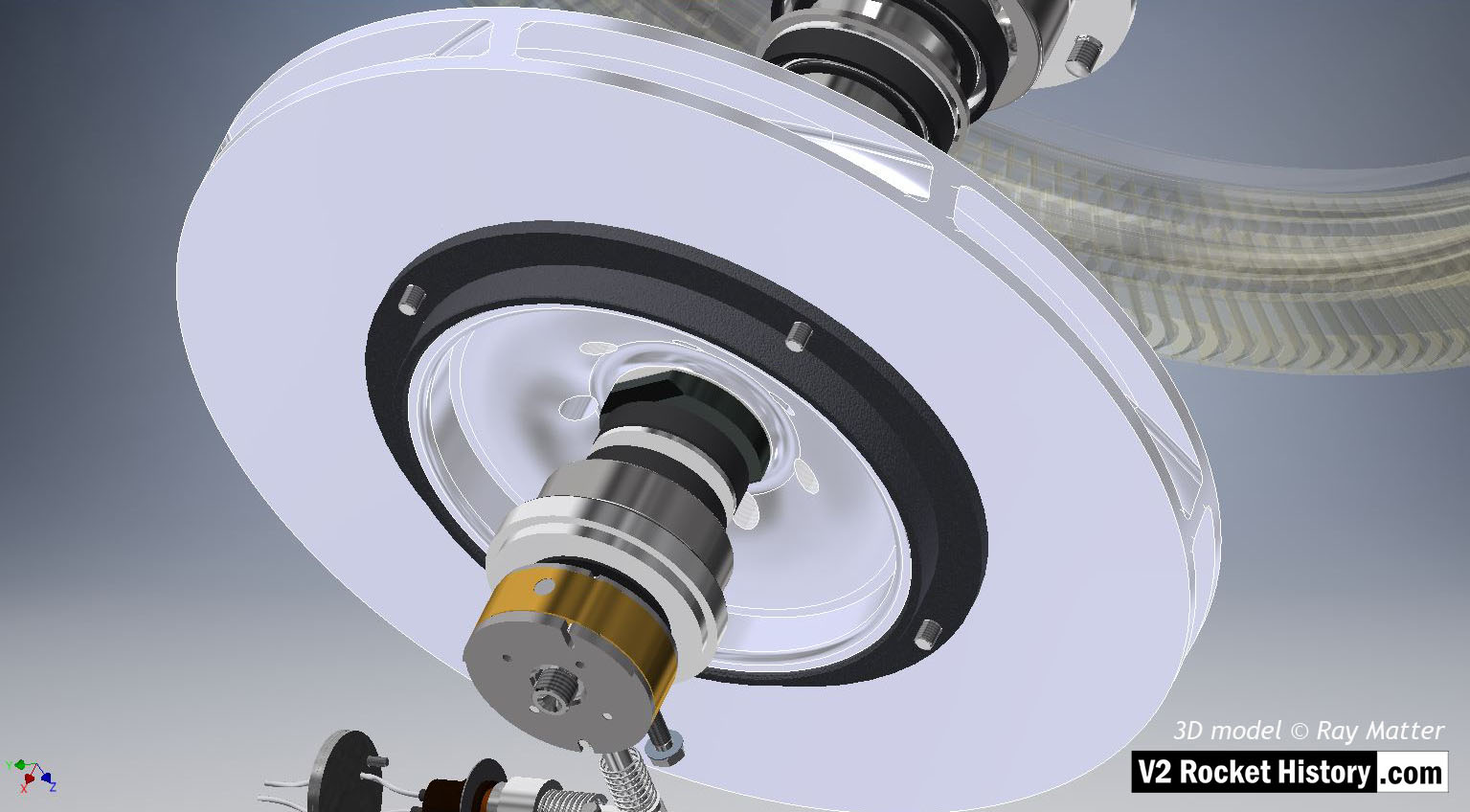
B (fuel) Pump exposed to show pump impeller, large bearing surface, and parts of over-speed device. 3D model Ray Matter
Album | Turbopump 3D CAD |
Category | Turbo-pump |
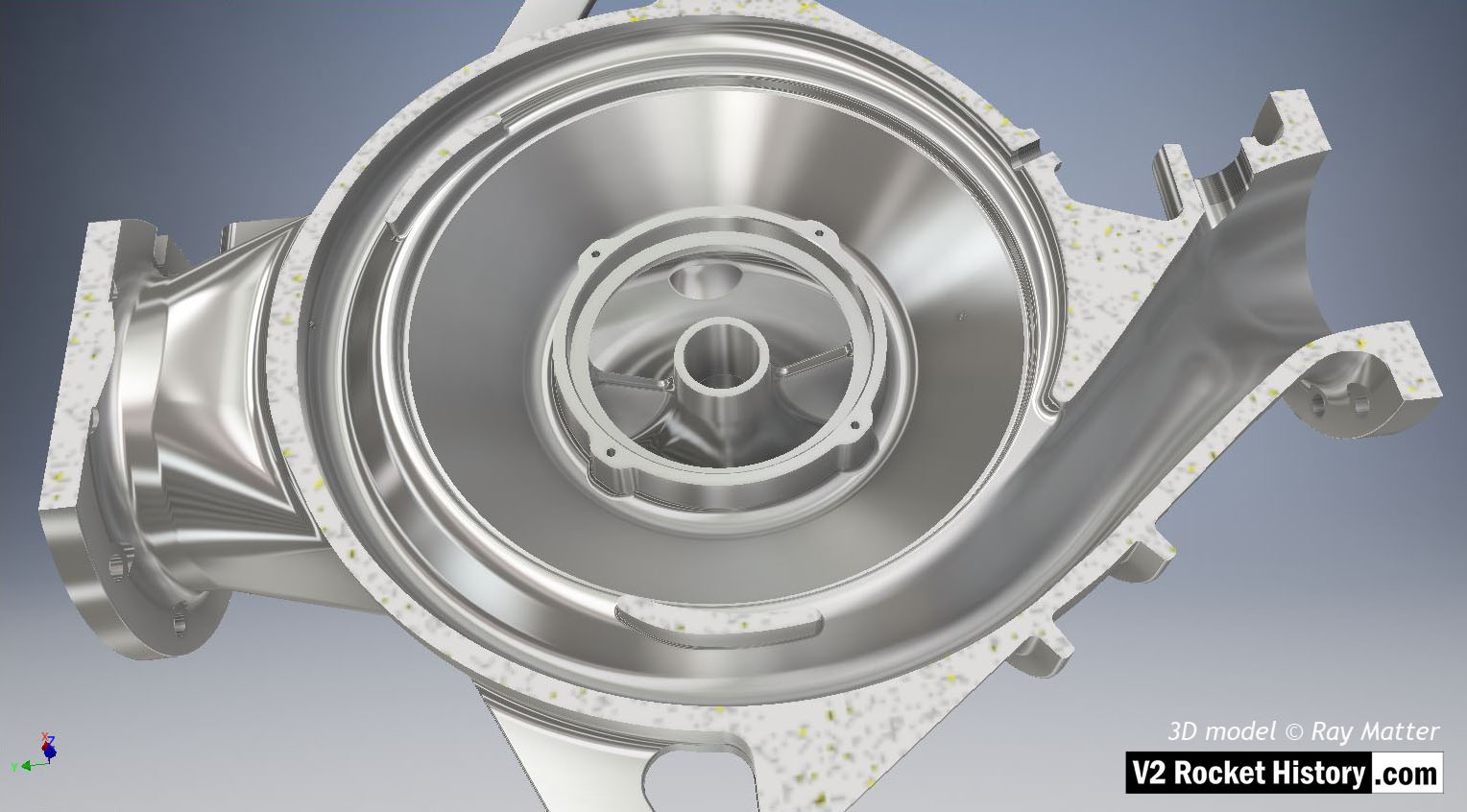
B pump housing from pump rotor side – notional surface polish to show shape and detail (such a surface was not used on the actual pump parts). The casing has been cut to show the internal rotor space detail. The outlet throat, right, and spiral volute space are displayed in this view as is the central fuel inlet. 3D model Ray Matter
Album | Turbopump 3D CAD |
Category | Turbo-pump |
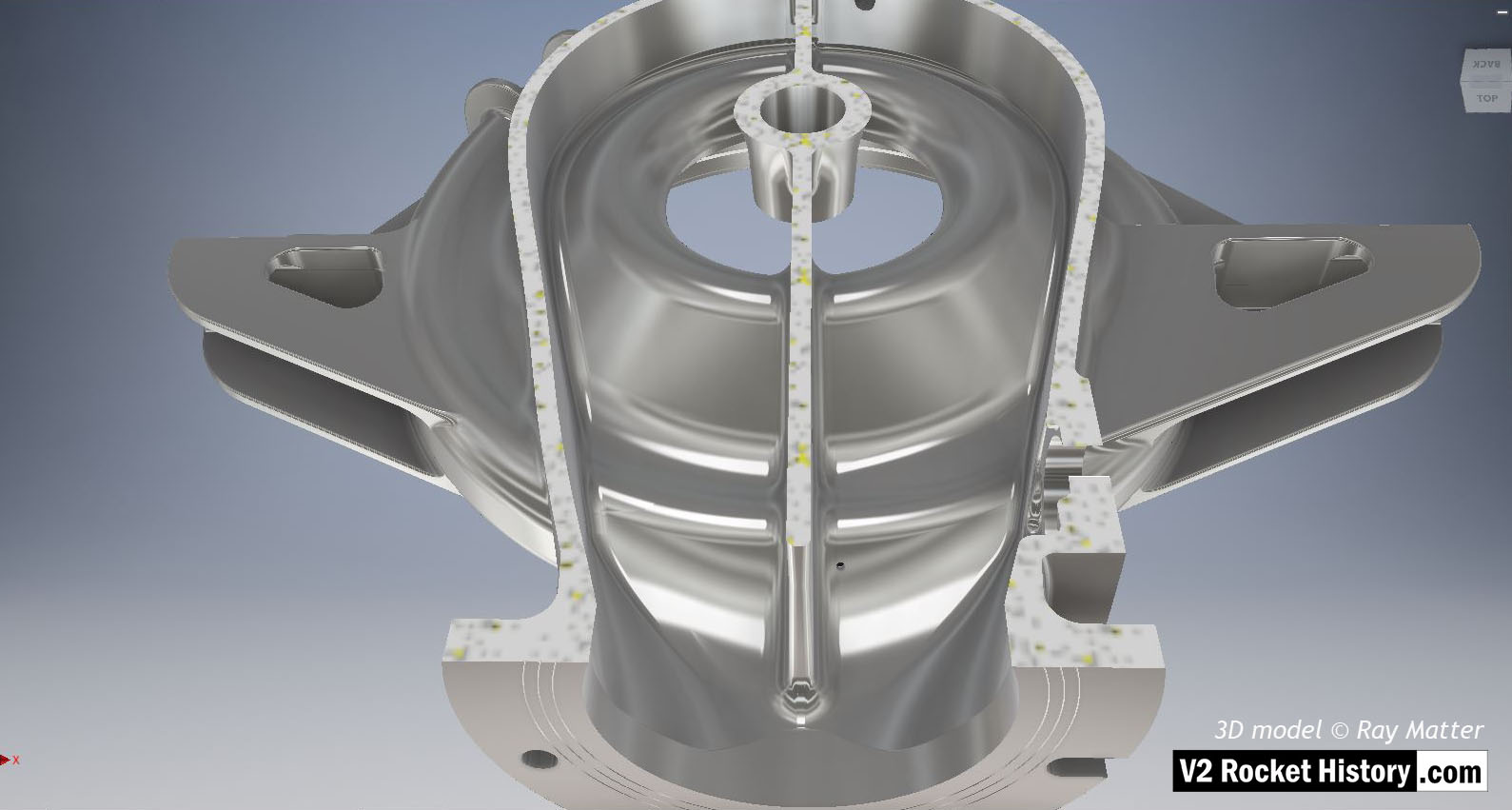
B pump housing with notional surface polish to show shape and detail (such a surface was not used on the actual pump casing). The casing nearest the turbine has been cutaway to reveal internal detail. The small self-purge orifice can be seen in this view, lower middle to the right of separator. 3D model Ray Matter
Album | Turbopump 3D CAD |
Category | Turbo-pump |
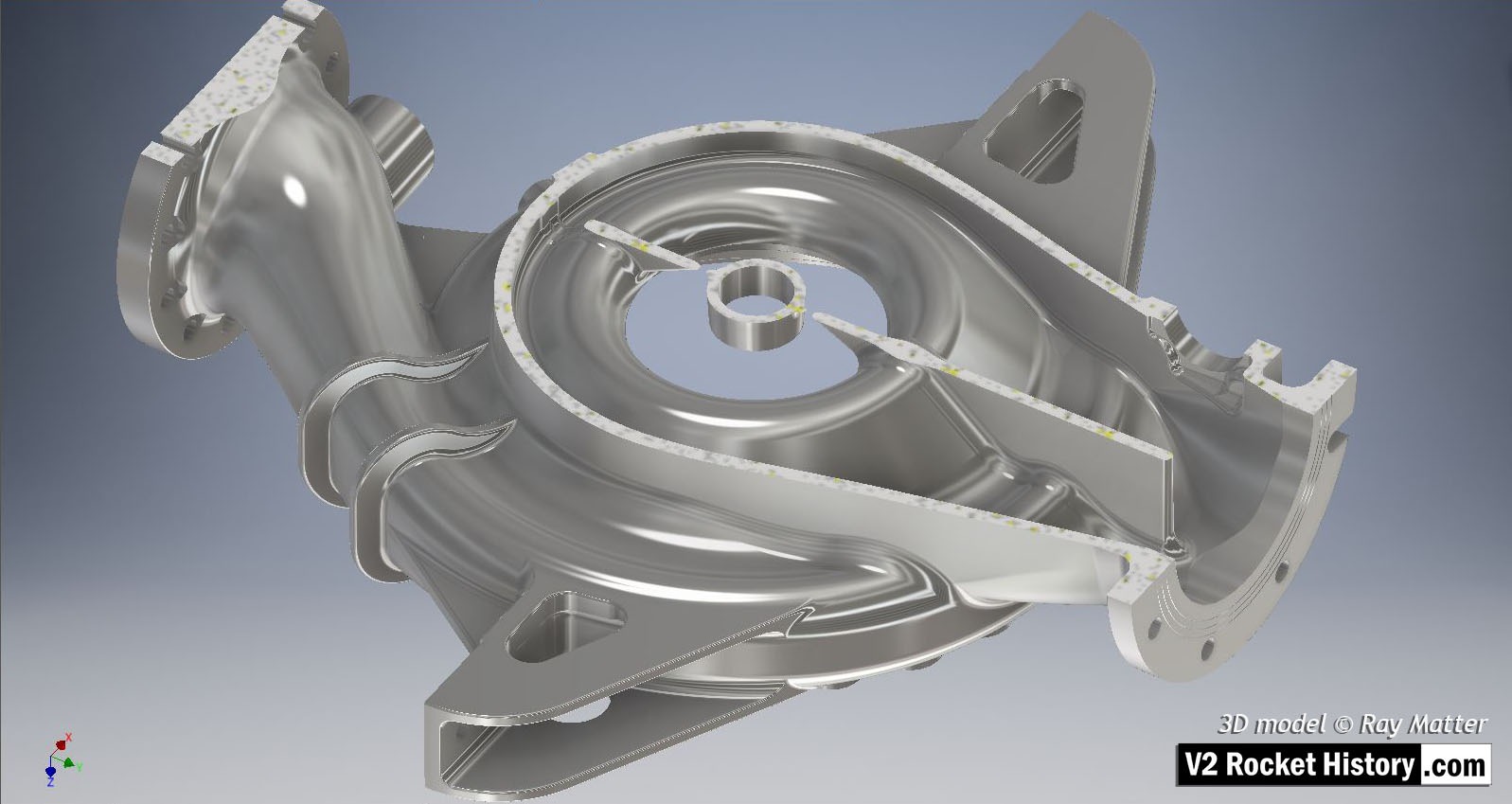
B pump housing with notional surface polish to show shape and detail (such a surface was not used on the actual pump casing). The casing nearest turbine has been cut to show internal detail. Inlet flange and split throat detail are clear in this view.
Album | Turbopump 3D CAD |
Category | Turbo-pump |

Valves
Images of the main valves involved in the propellant flow of the A4 / V2 liquid fuelled rocket engine
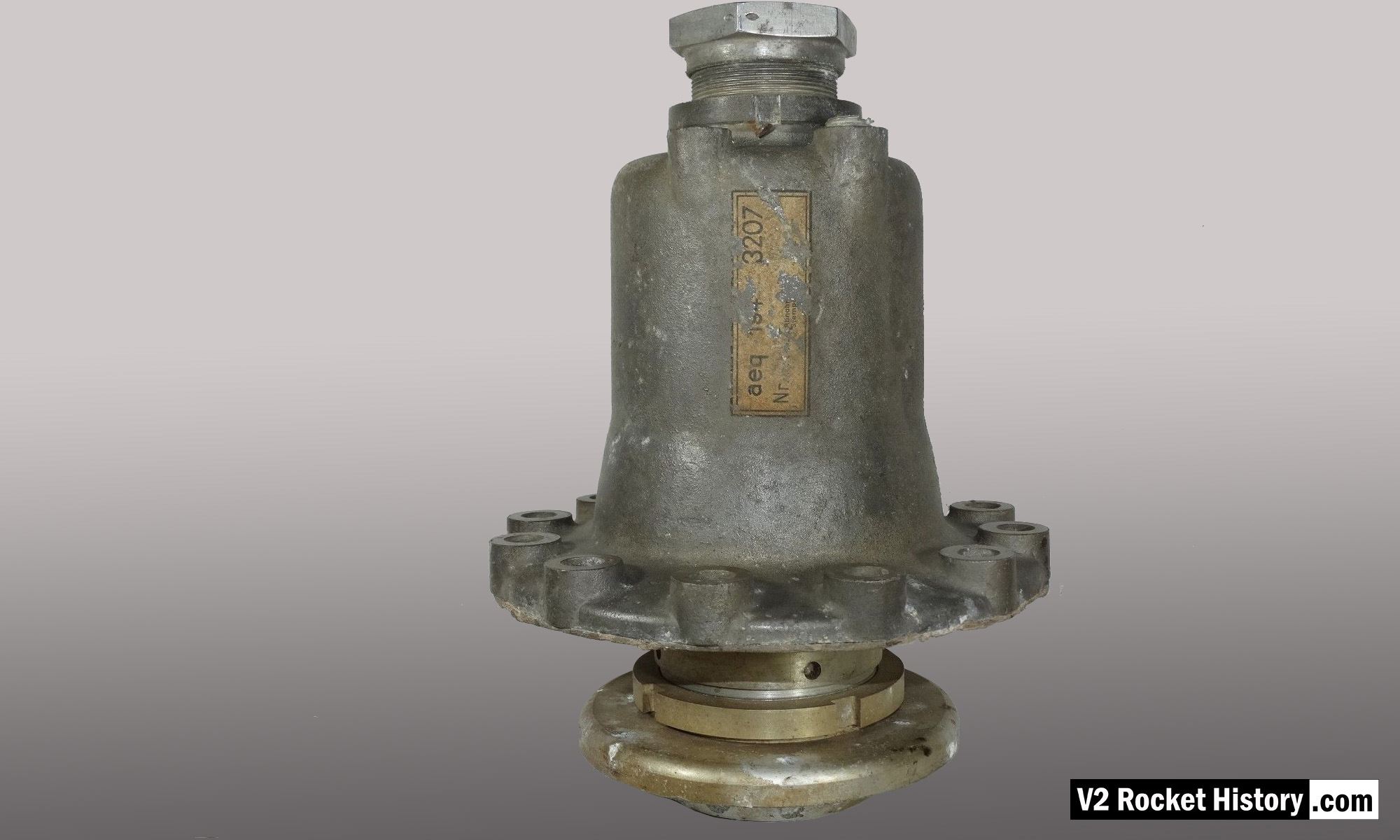
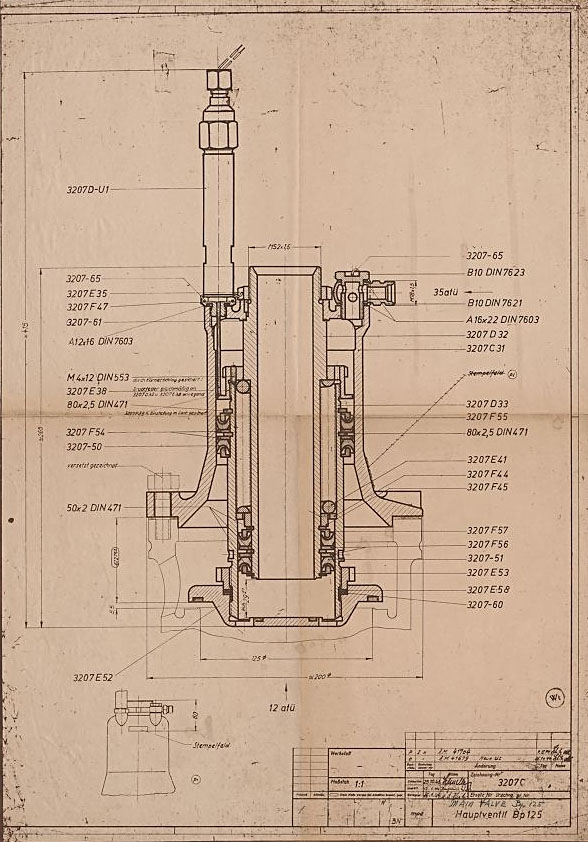
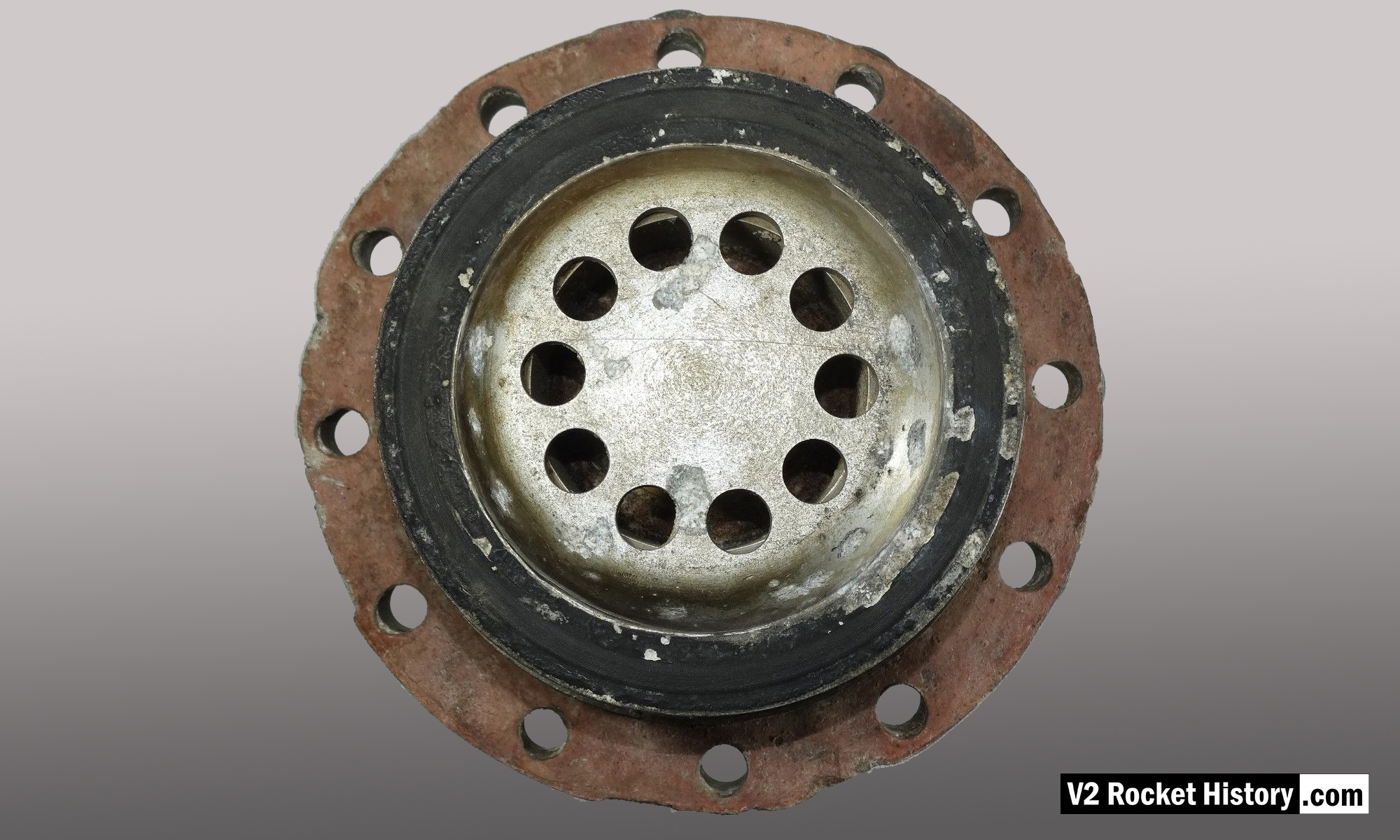
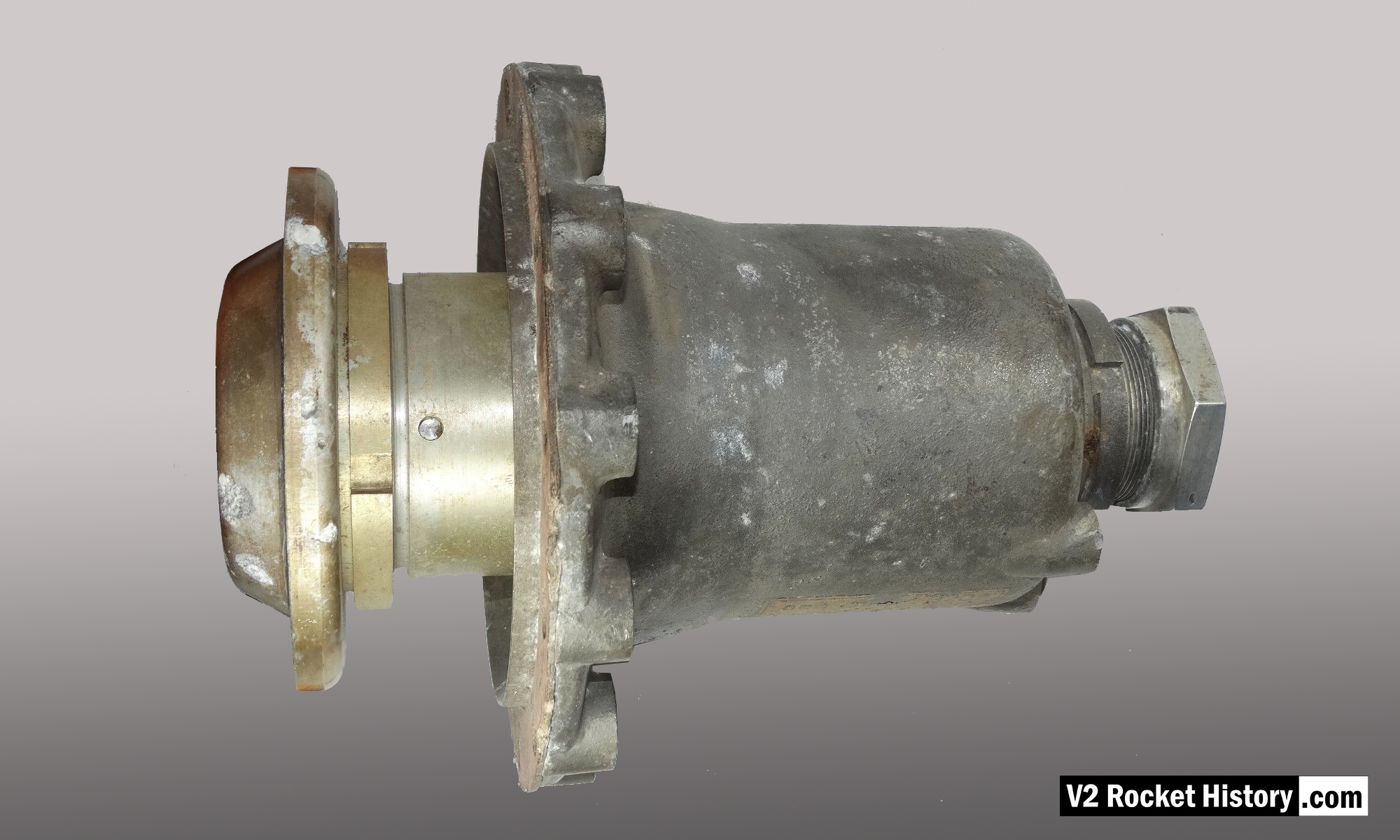
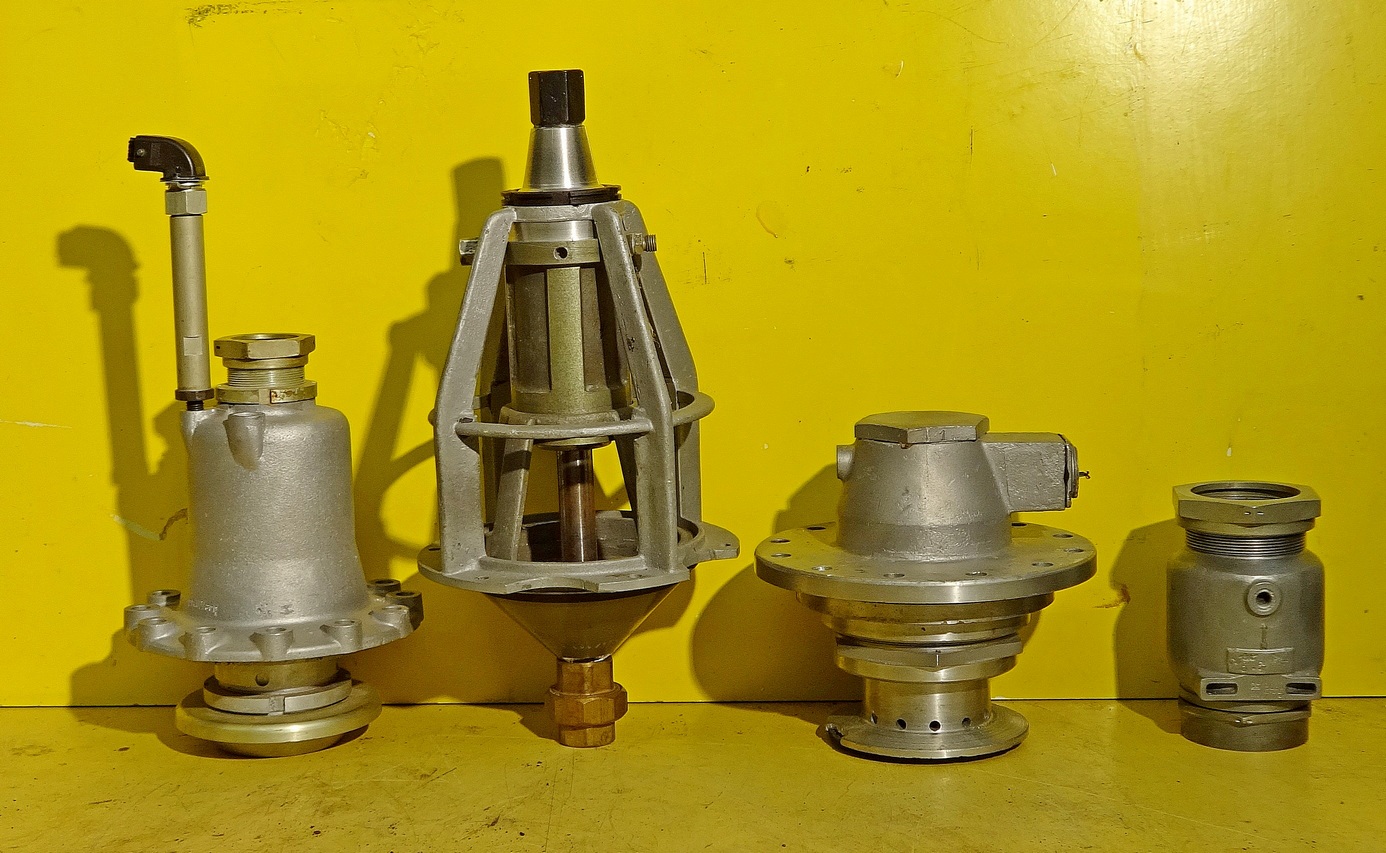
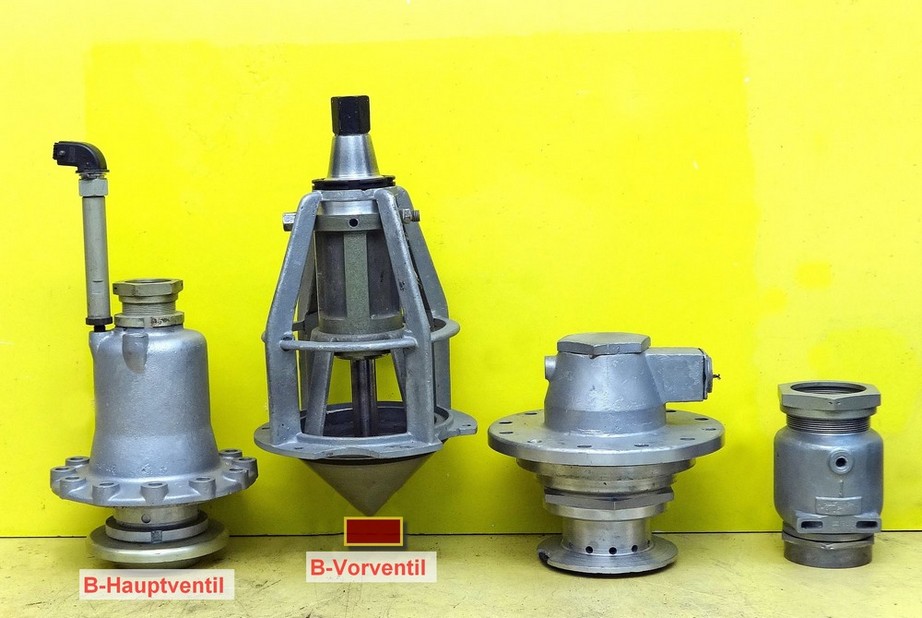
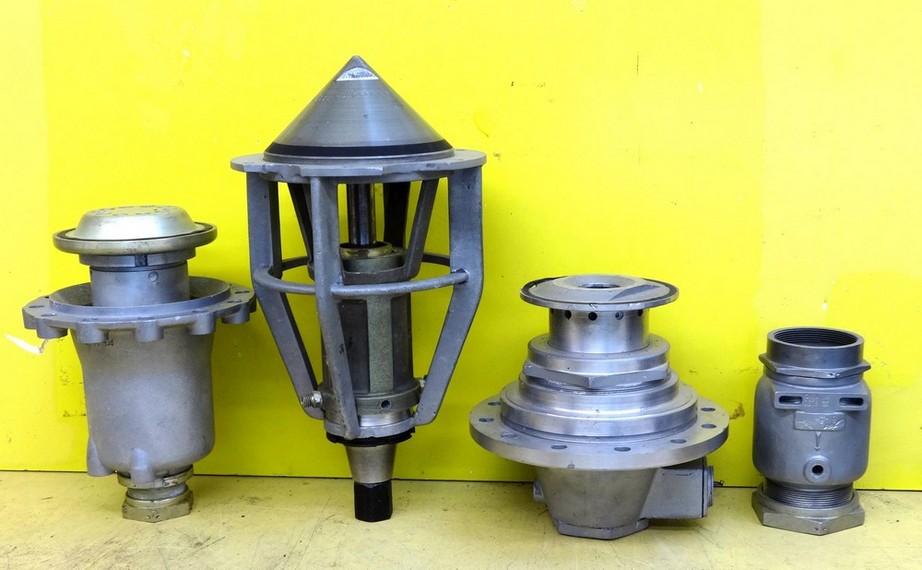
Images of the main valves involved in the propellant flow of the A4 / V2 liquid fuelled rocket engine
Relic of main alcohol valve with manufacturer code aeq (aeq = Bartoc & Co., Maschinenfabrik u. Giesserei Hedwikow,bei Caslau (Caslav) Czech Republic). An air (nitrogen) inlet pressure of 440 to 530 psi (30 to 36 Bar) was required to close this valve against its internal spring and the force of the turbo-pump. The large nut at the top is the connection for the fuel return (or ‘revolving’line) pipe, and the air and electrical input ports can be seen to the right (air), and left (elec.) just below this point. V2RH image

Anatomy of the V2: 18-pot injector head
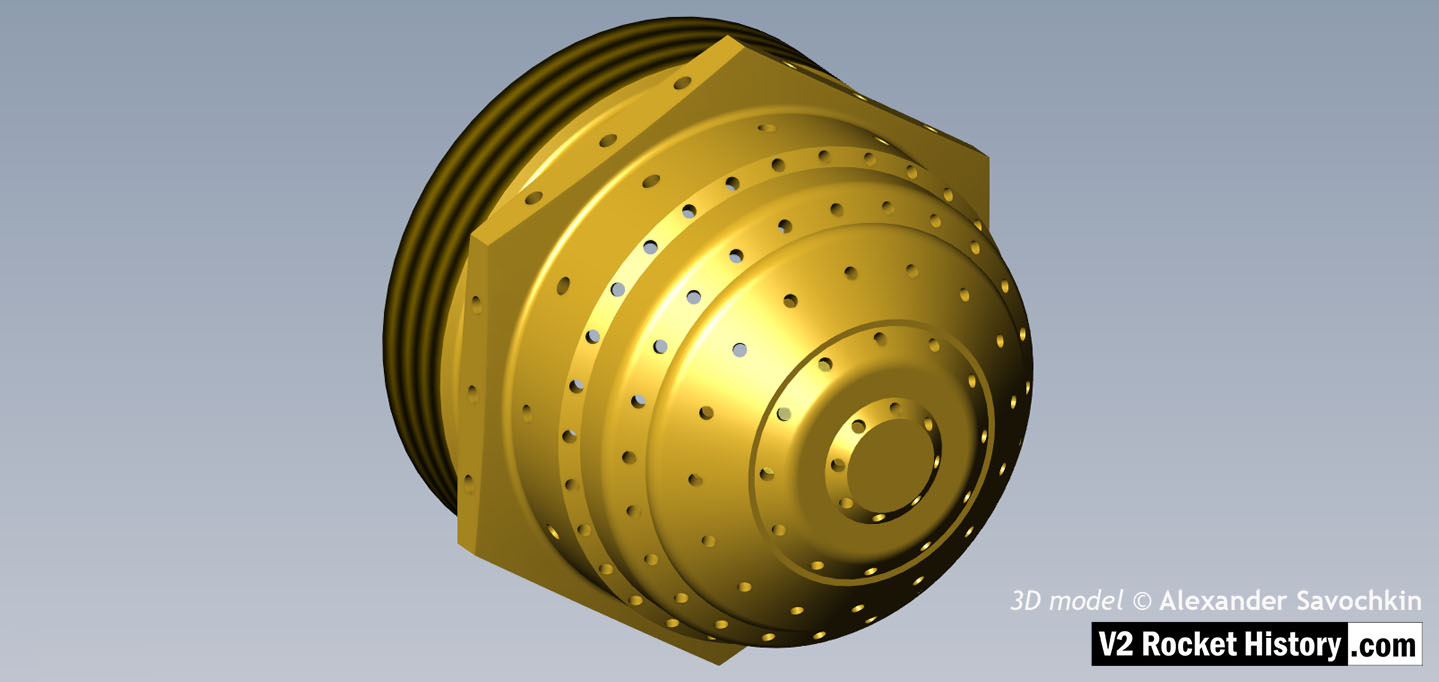
Brass liquid oxygen (LOX) spray nozzle.Note: the thread is shown in simplified graphic form. 3D model by Alexander Savochkin
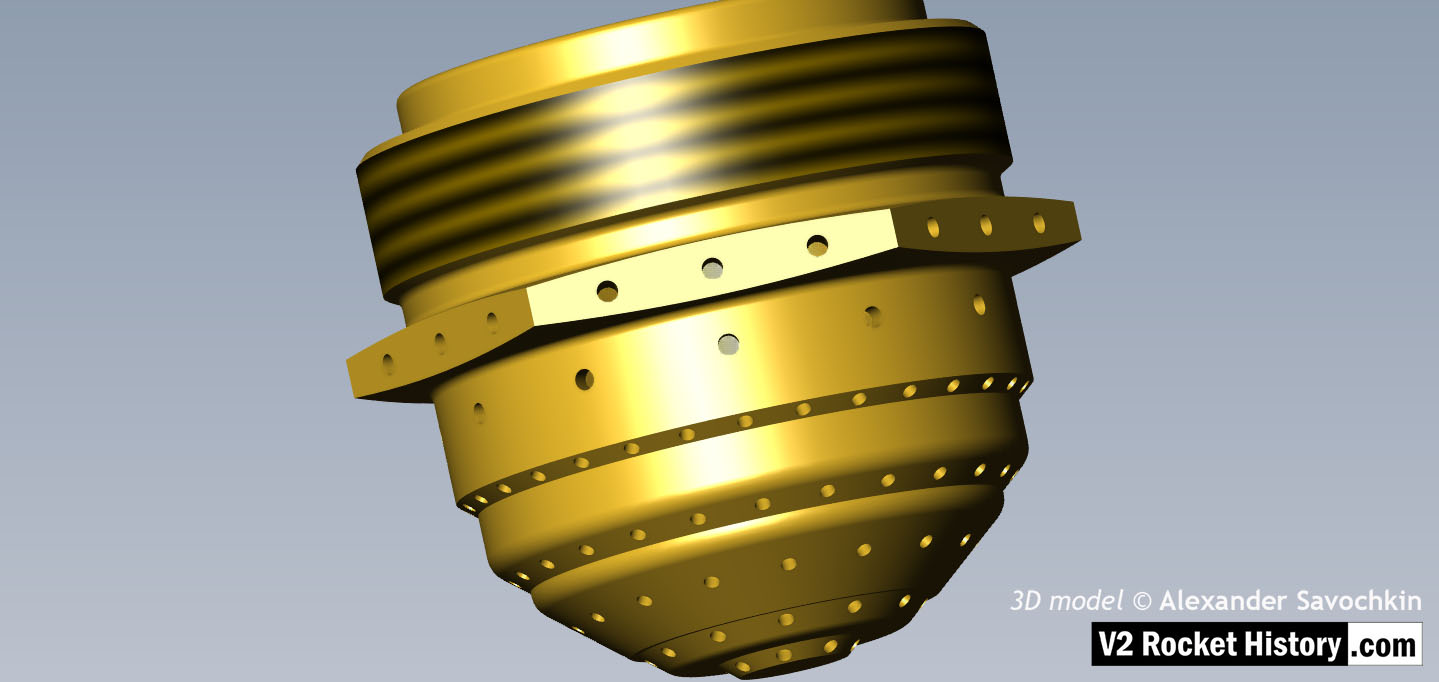
Brass liquid oxygen (LOX) spray nozzle. Note: the thread is shown in simplified form. 3D model by Alexander Savochkin

One of the 18 liquid propellant (LOX and fuel) diffuser cups, showing three rows or echelons (A,D,& E) of brass injector inserts as well as two rows of drilled fuel feed holes. The LOX spray head is shown in the centre. 3D model by Alexander Savochkin
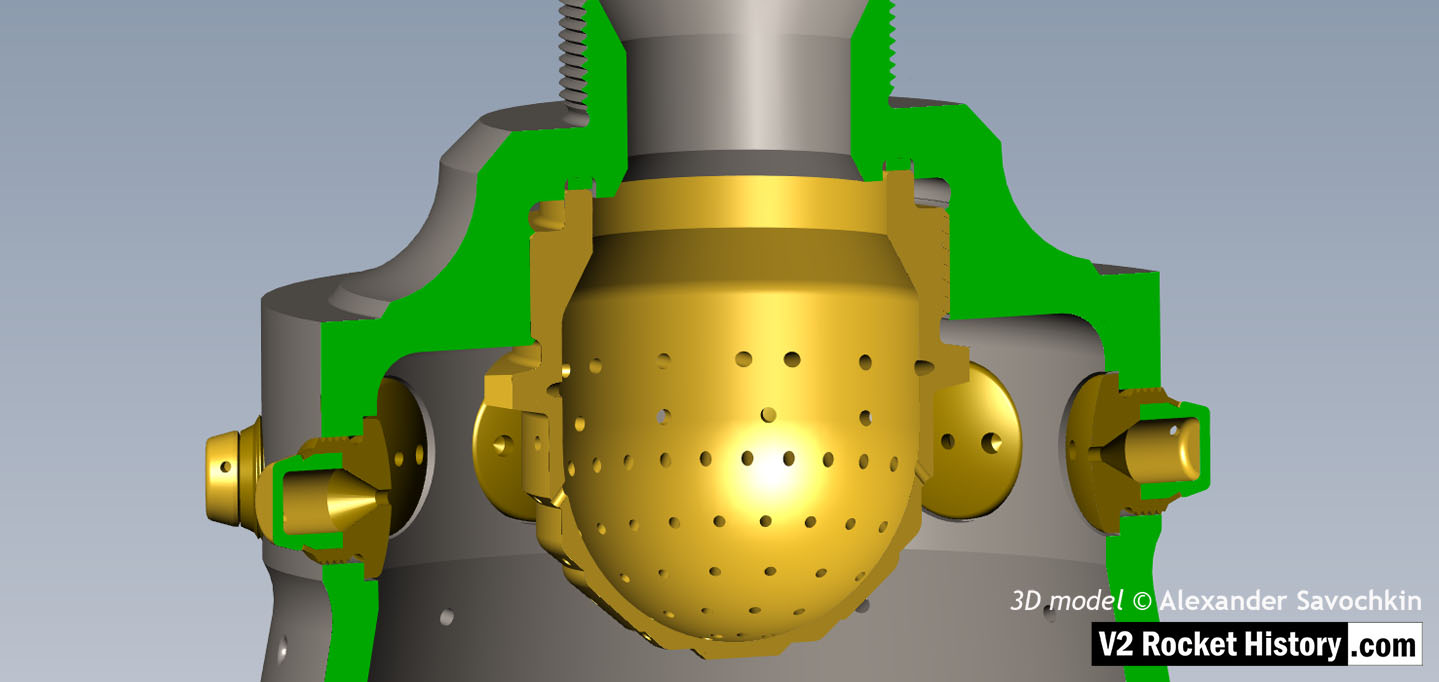
Cutaway showing echelon A with 2-part 2131E fuel injector inserts at the top of a propellant diffuser cup. Note the close proximity of the injector inserts to the simple ‘watering can’ type LOX spray head. One row of drilled fuel feed holes can be seen below the inserts. 3D model by Alexander Savochkin
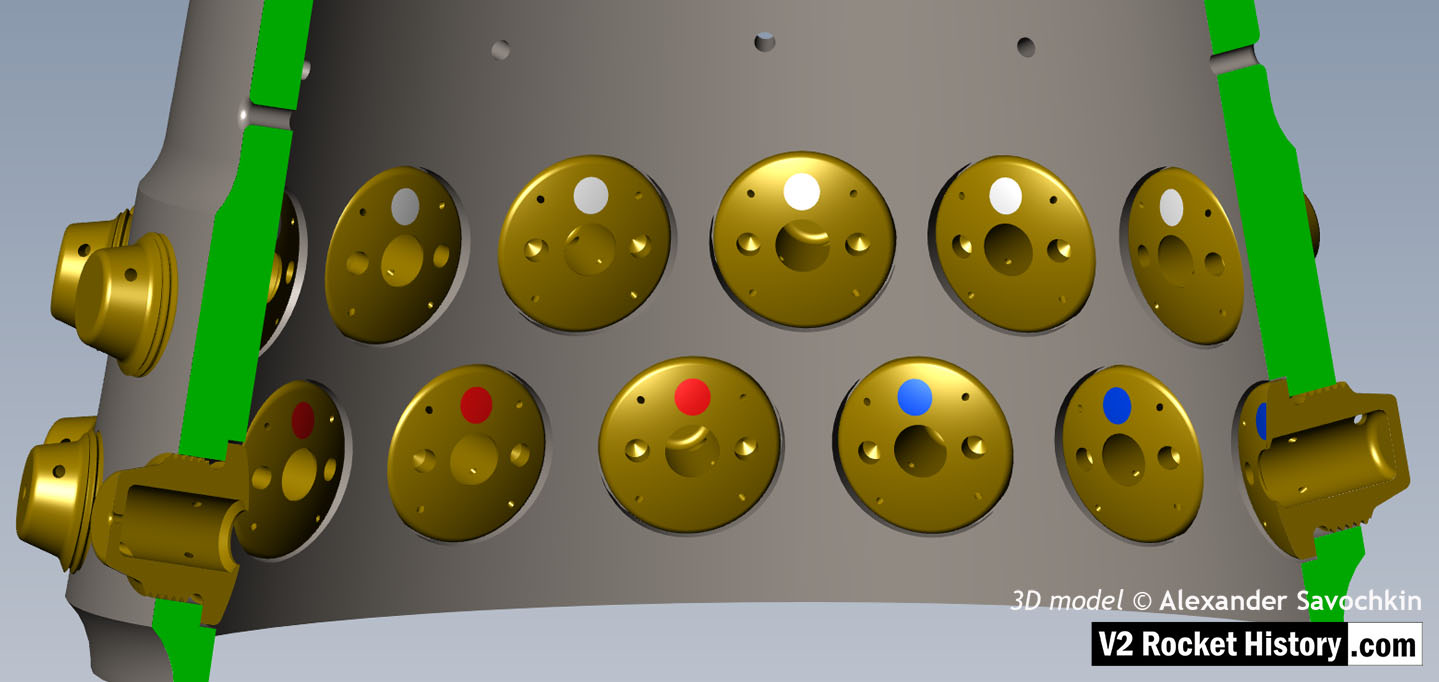
This images shows a cutaway of a burner cup from outer Ring I of the injector head and shows injector insert eschelon D, & E as well as one row of drilled feed holes. Three fuel injector insert types can be seen: Top D, = 3303D (white), lower E, = 3304D (red), and E, = 3305D (blue). 3D model by Alexander Savochkin

This images shows a burner cup from outer Ring I of the injector head and the cutaway shows injector insert eschelon A,D, & E as well as two rows of drilled feed holes. Four fuel injector insert types can be seen: Top, A = 2131E, lower D, = 3303D (white), lowest E, = 3304D (red), and E, = 3305D (blue). 3D model by Alexander Savochkin
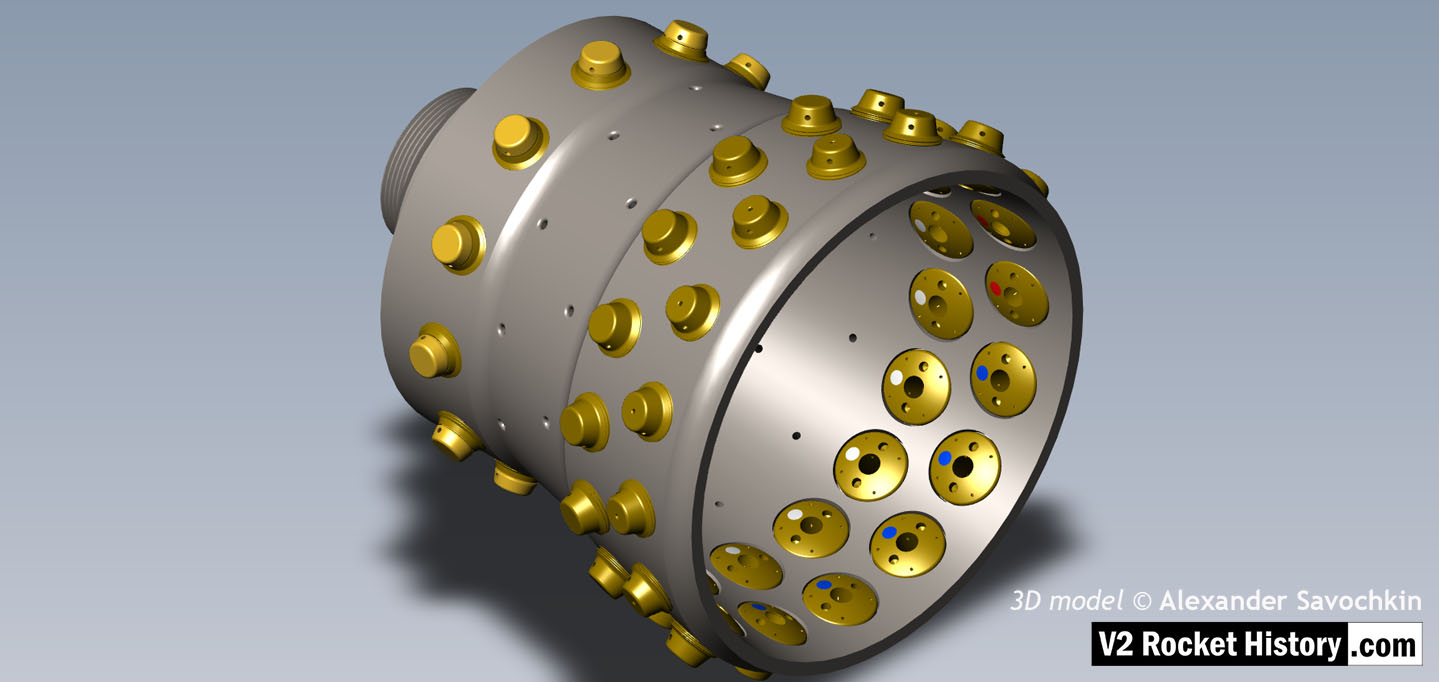
General view of the propellant diffuser cup inner core. The swirl caps of fuel injector inserts in positions A,D,& E can be seen clearly on the outside of the core as well as the central holes in the 3304D (red) inserts.The two rows of drilled fuel feed holes are also well shown. 3D model by Alexander Savochkin
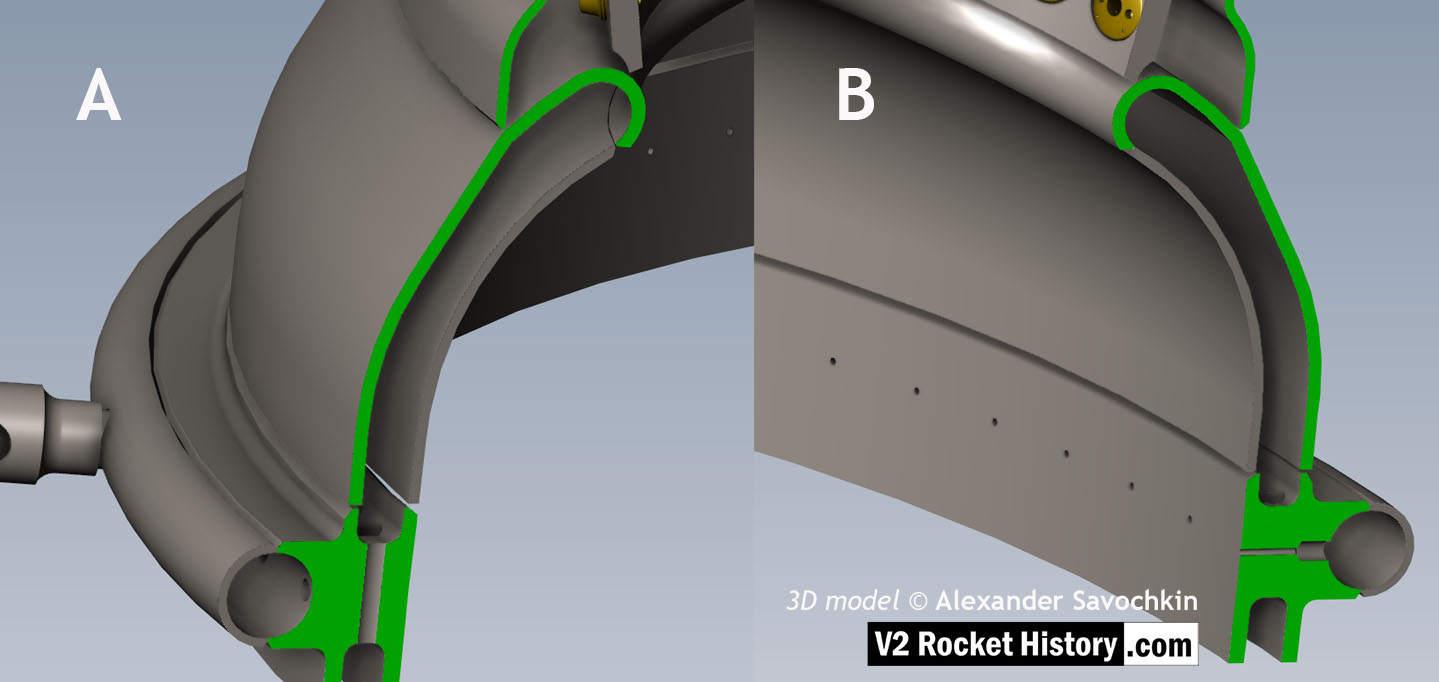
Close-up detail showing independent pathway for fuel passing into injector head and fuel passed down from the head to be used for veil cooling system. Fig. A shows vertical passages for overall fuel feed to the head and Fig.B shows horizontal pathway for veil coolant fed from the head via the veil coolant distributor ring or manifold. 3D model by Alexander Savochkin

Underside view of injector head showing liquid propellant (LOX and fuel) diffuser cups, (see other images for insert and position nomenclature). Of note in this image are the pointing angles of the cups, positioned on a parabolic section to focus the propellant nebular stream into the central axis of the combustion space. Also of note are the large areas between each cup NOT employed in the injection process – initiating ‘clumpy’ and uneven propellant mixing initially below the injector face but also carried forward into the combustion space. The LOX spray head is shown in the centre of each cup. 3D model by Alexander Savochkin

Inverted view of injector head showing liquid propellant (LOX and fuel) diffuser cups, (see other images for insert and position nomenclature). Of note in this image are the pointing angles of the cups, positioned on a parabolic section to focus the propellant nebular stream into the central axis of the combustion space. Also of note are the large areas between each cup NOT employed in the injection process leading to structured propellant mixing as opposed to even homogeneous mixing. The four veil cooling inlet connectors are well shown. 3D model by Alexander Savochkin

View of injector head showing 18 liquid propellant (LOX and fuel) diffuser cups and head fuel valve seating ring at centre, (see other images for insert and position nomenclature). Visible immediately below the valve seat are the large connecting holes that allow fuel to flow from the inlet manifold and cooling jacket to the injector space (some brass injector inserts can be seen through the holes) after the head fuel valve is released to be opened by the turbo-pump supply pressure. The four veil cooling inlet connectors are well shown as are two of the outlet connection holes immediately above them. 3D model by Alexander Savochkin

View of the top of the injector head, with outer cups and pressed steel capping piece removed, showing, propellant diffuser inner cores with injector inserts and LOX supply pipe connection thread. The LOX spray head can be seen inside the LOX pipe connector. The swirl caps of fuel injector inserts in positions A,D,& E can be seen clearly on the outside of the cores and the two rows of drilled fuel feed holes are also well shown. 3D model by Alexander Savochkin
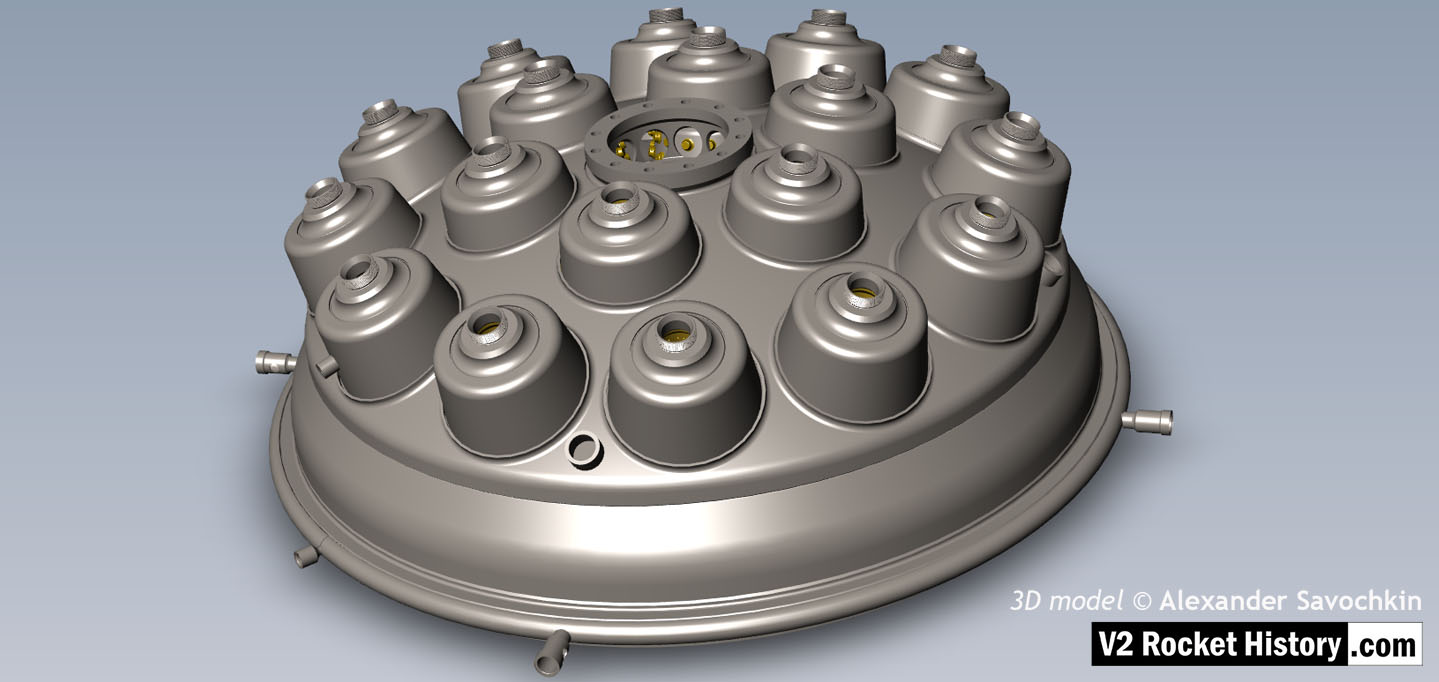
Another view of injector head showing liquid propellant (LOX and fuel) diffuser cups and head fuel valve seating ring at centre, (see other images for insert and position nomenclature). Visible immediately below the valve seat are the large connecting holes that allow fuel to flow from the inlet manifold and cooling jacket to the injector space (some brass injector inserts can be seen through the holes) after the head fuel valve is released to be opened by the turbo-pump supply pressure. The four veil cooling inlet connectors are well shown as are two of the outlet connection holes immediately above them. 3D model by Alexander Savochkin

A close-up view of the head fuel valve mounting flange (showing 12 fastener holes). Visible immediately below the top flange are the large connecting holes that allow fuel to flow from the inlet manifold and cooling jacket to the injector space (some brass injector inserts can be seen through the holes) after the head fuel valve is released to be opened by the turbo-pump supply pressure.
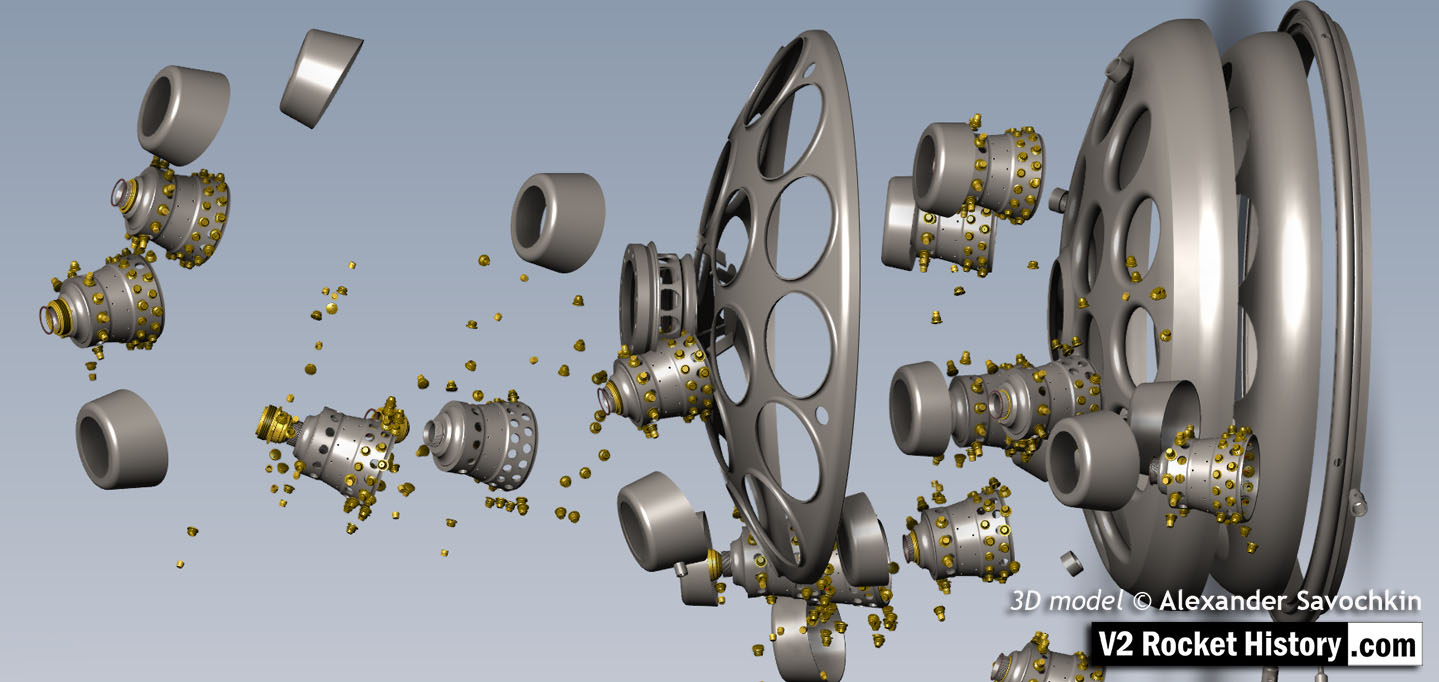
Exploded view showing some of the 1100 parts required for the complicated 18-pot injector head of the V2 25-ton thrust rocket engine. 3D model by Alexander Savochkin
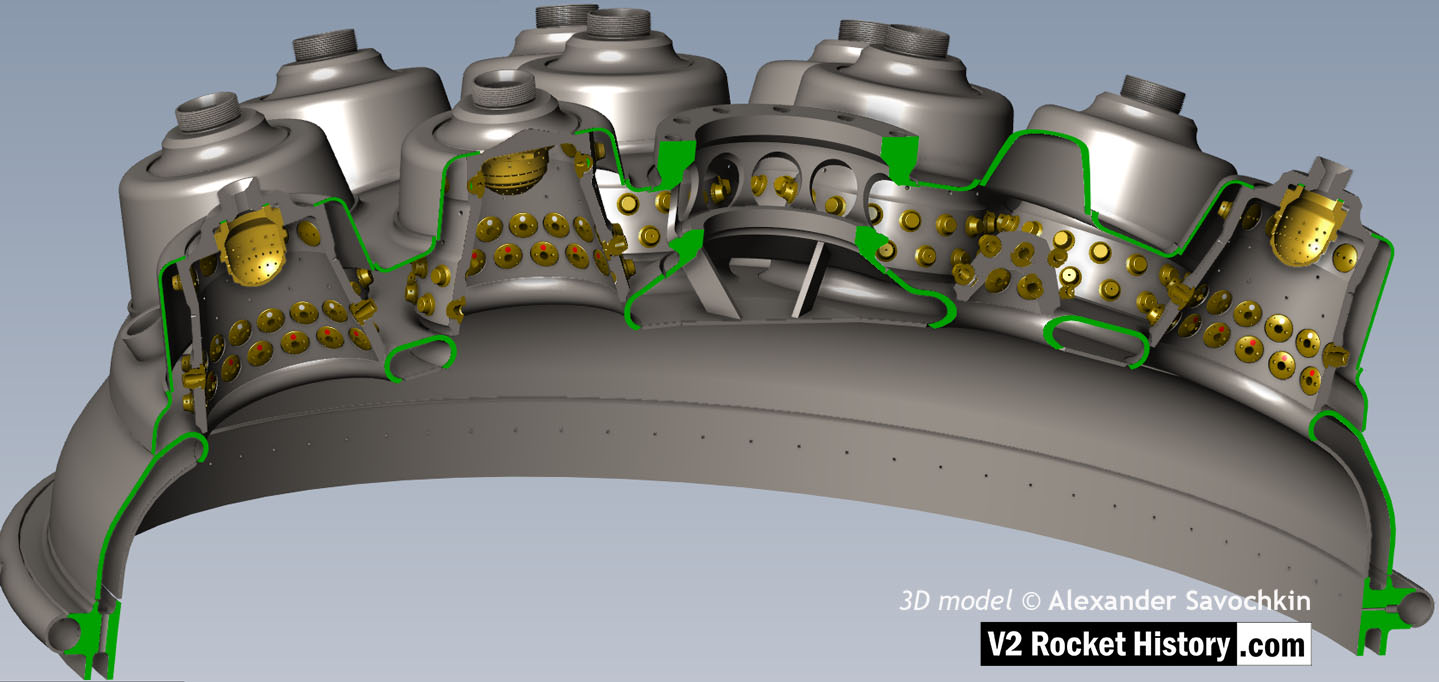
Here the 18-pot head model has been cutaway to show the fuel cooling and fuel delivery spaces. the cooling jacket layer can be seen in the lowermost area of the head – below the centrally positioned fuel valve seat, between each cup at the lowest point, and ruining down toward the first set of veil cooling pores and the topmost coolant distributor ring. Note that the veil cooling system does not communicate with the regenerative cooling jacket and has its own feed pipes drawing fuel from the head injector space and not the cooling space. Visible immediately above the valve seat are the large connecting holes that allow fuel to flow from the inlet manifold and cooling jacket to the injector space after the head fuel valve is released to be opened by the turbo-pump supply pressure. 3D model by Alexander Savochkin

Liquid propellent (LOX and fuel) diffuser cup, showing three rings or echelons (A,D,& E) of brass injector inserts as well as two rows of drilled fuel feed holes. The LOX spray head is shown in the centre. Note the simple ‘shower head or watering can’ design of the LOX diffuser. A sealing washer can be seen fitted between the LOX diffuser and the steel cup. 3D model by Alexander Savochkin

The chart shows water delivery in litres per minute per injector
Album | Testing fuel injectors |
Categories | Combustion, Propellant flow |
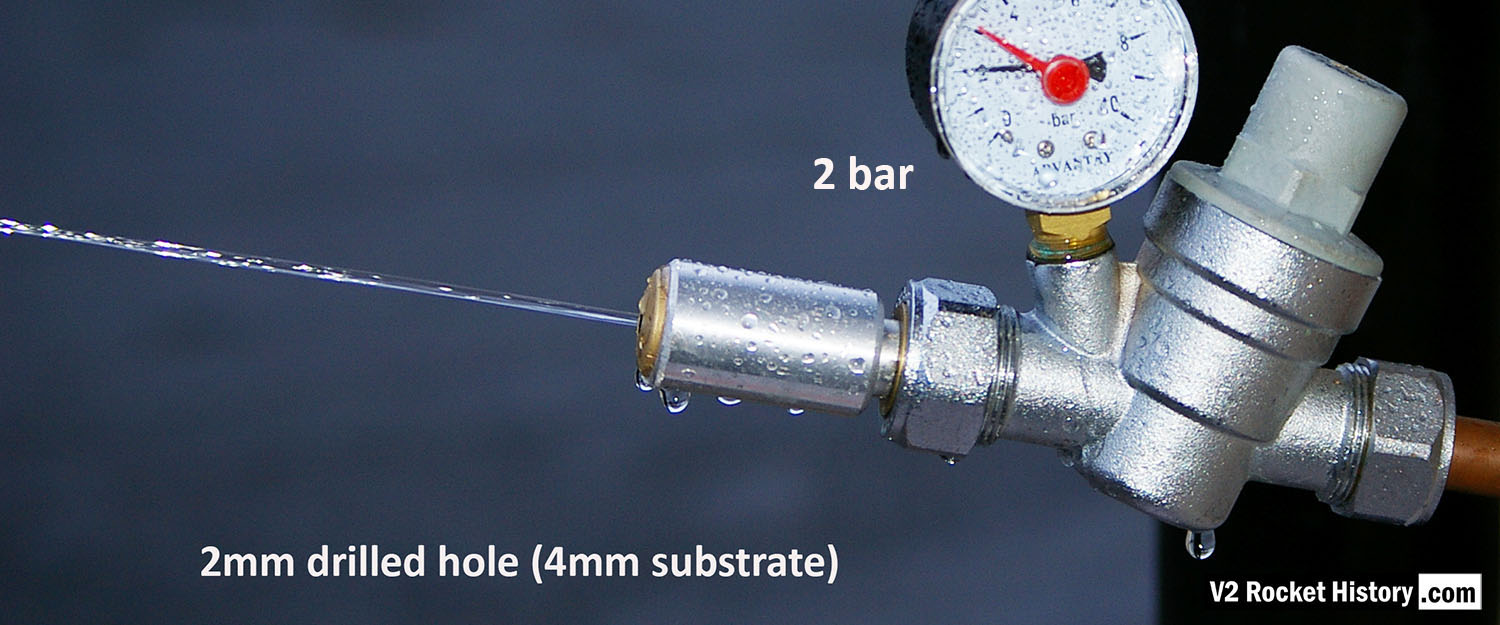
Each burner cup of the V2 rocket engine injector system has forty-four brass inserts, but each cup also has twenty-four 2mm diameter plain holes, 30 deg apart, drilled into the cup’s central wall. To mimic this for testing purposes, we created a brass insert that has a base with just a 2mm central hole. The base is sized to be consistent with the 4 to 5mm cup wall. V2RH image

V2 rocket engine fuel injector inserts – a part of our collection used for the water tests with various types shown. The tool shown is a pin-wrench used to fit the inserts into the test apparatus. V2RH collection image
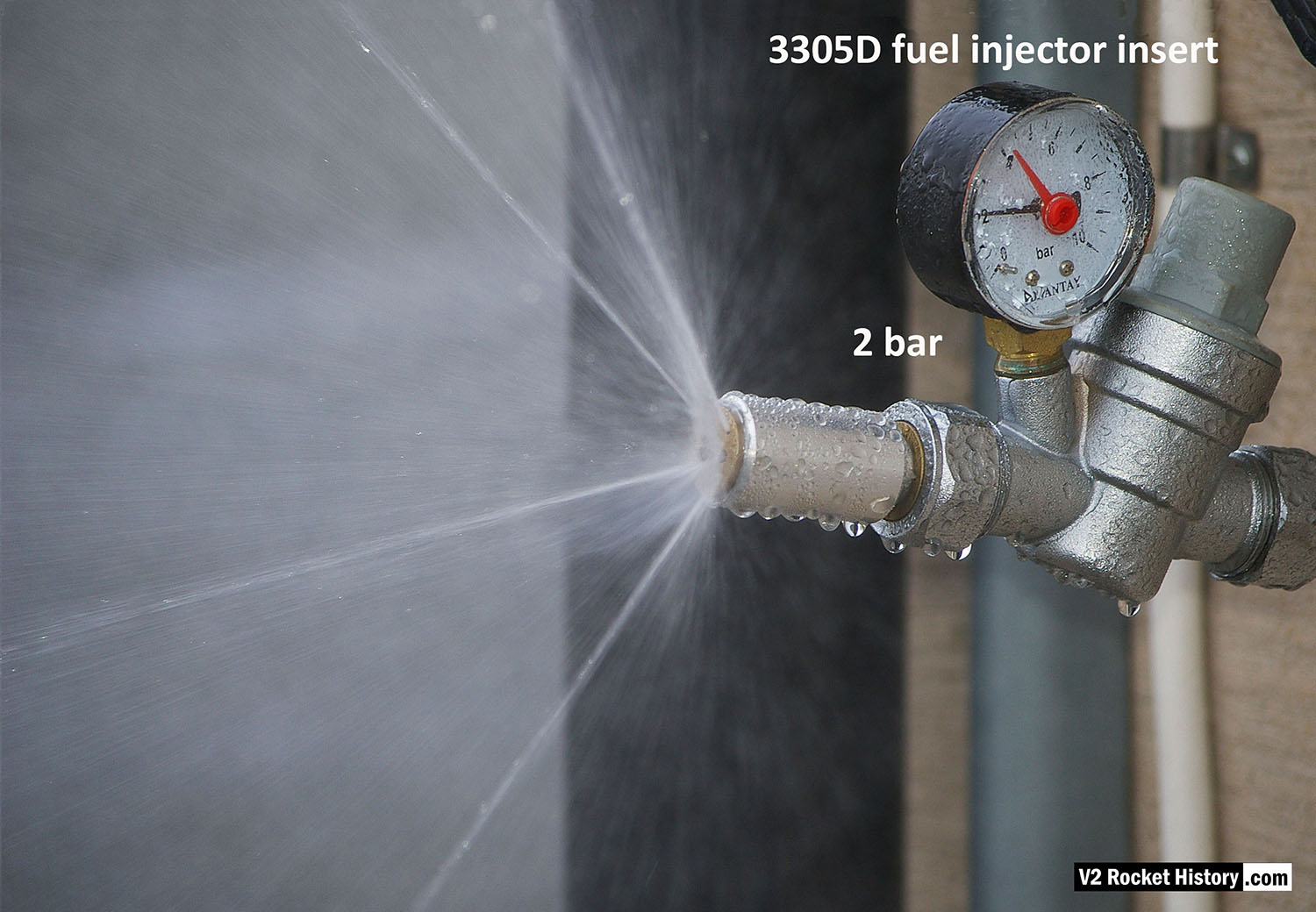
3305D fuel injector insert showing swirl cone nebular, and 4 steady steams emanating from cooling pores.
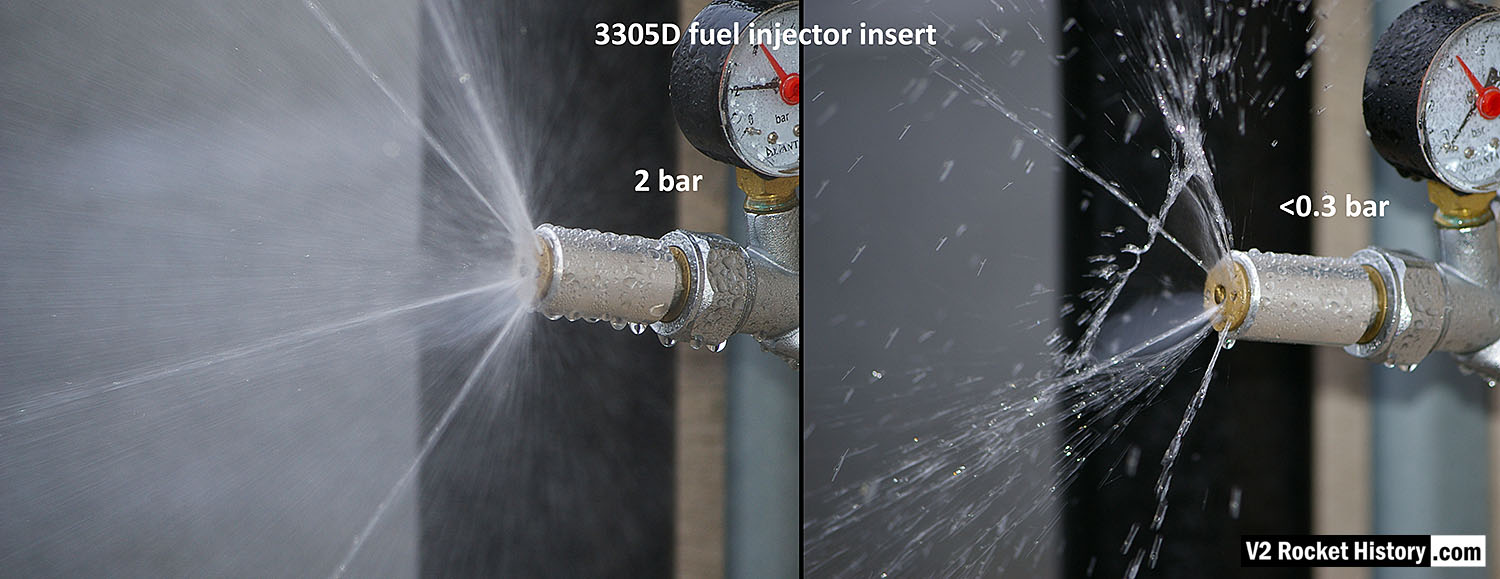
3305D fuel njector insert showing comparison nebular and jet stream pattern with high and low pressure. Left image shows correct hollow cone-shaped aerosol effect from central 6mm orifice, that is also creating a fine mist around and within the cone, and 4 steady steams emanating from cooling pores. Right image shows the effect of reduced pressure: a dropping poorly formed cone, composed of larger slower moving droplets, and a tendency for the thicker spray to combine and cause ‘dribbeling’ with much fluid failing to clear the injector face.
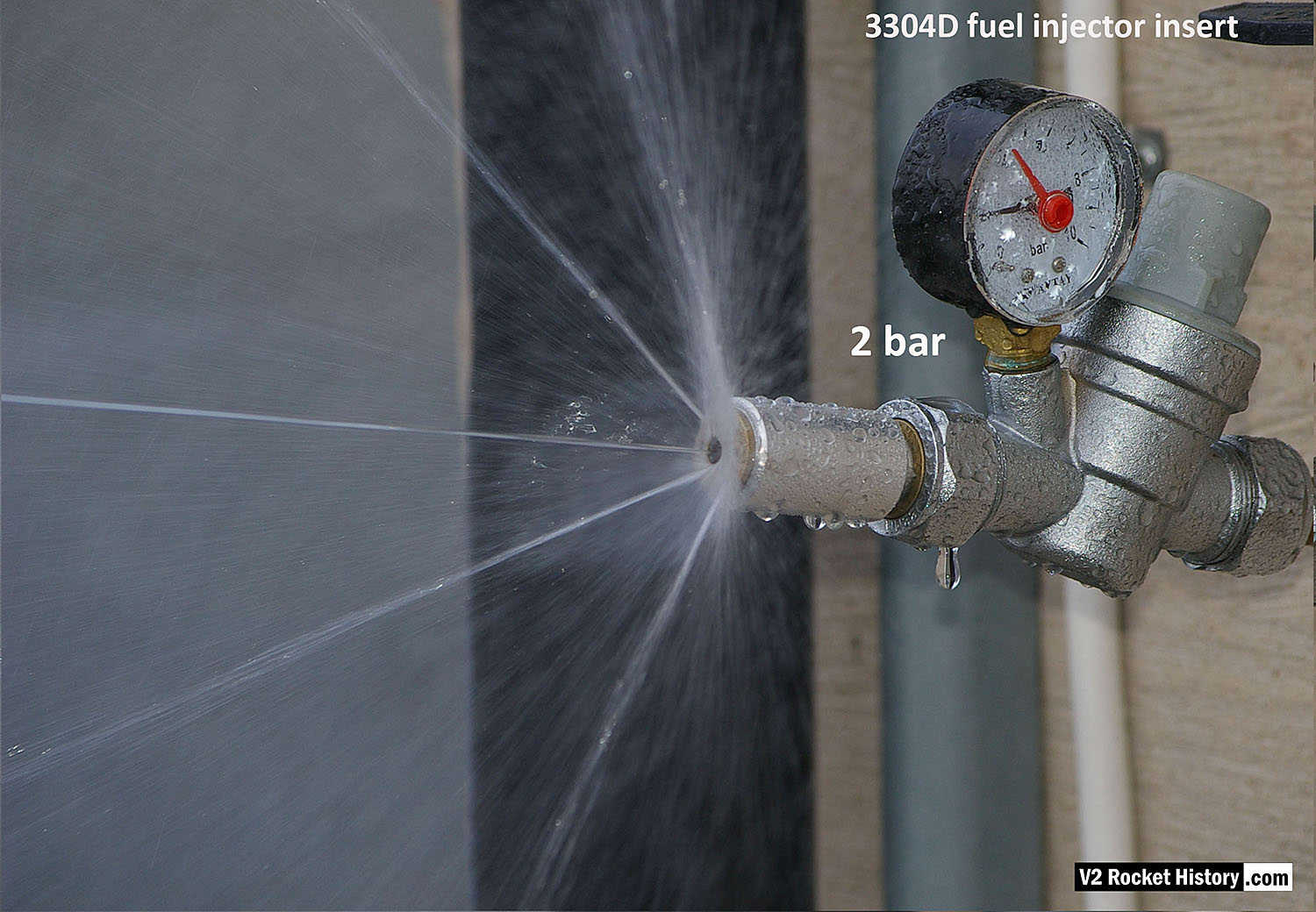
3304D higher volume fuel injector insert (with three inlet apertures: 2 swirl, 1 jet) showing swirl cone nebular, steady central jet, and 4 steady steams emanating from cooling pores.
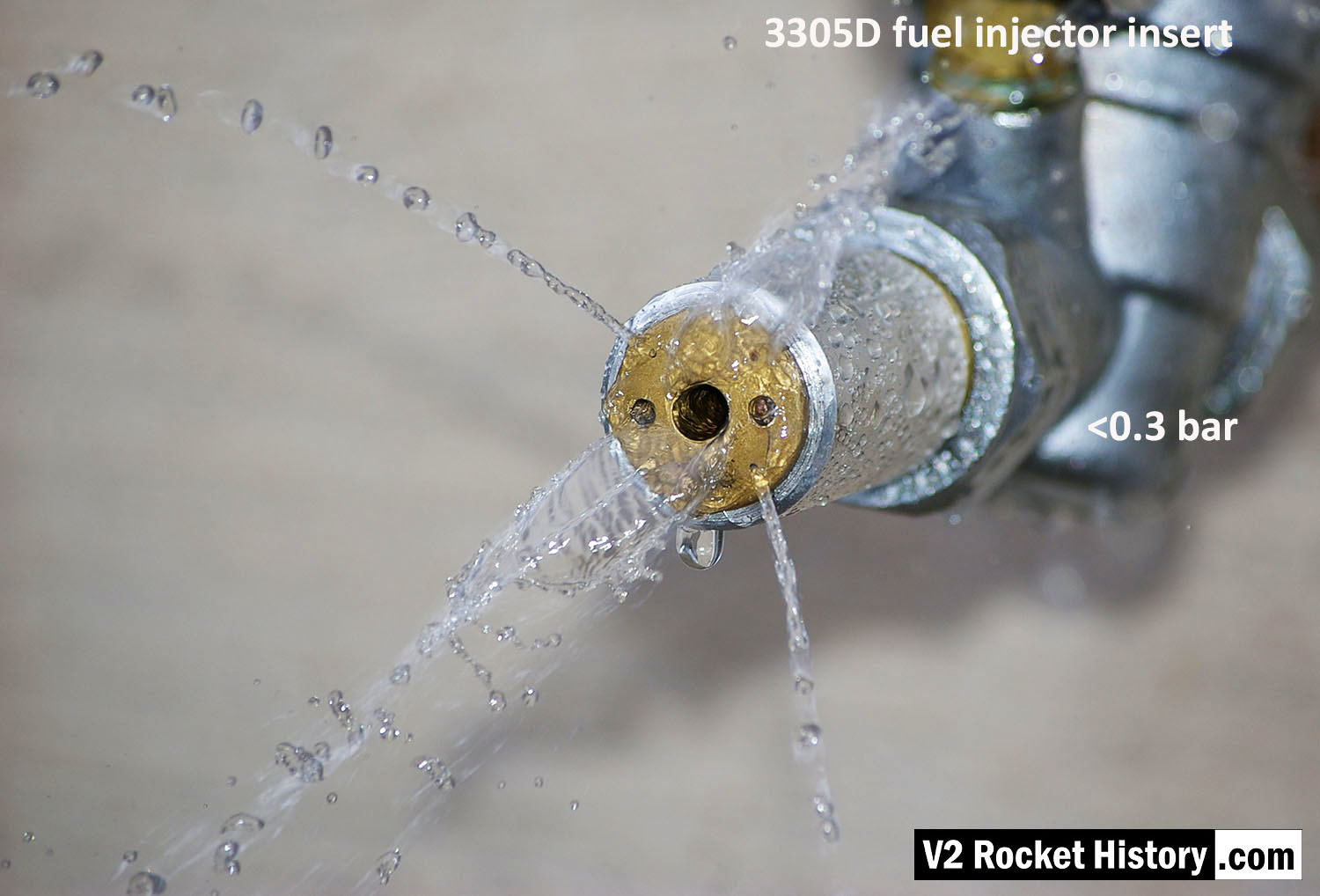
3305D injector insert showing larger low-velocity droplets and ‘dribbly’ performance due to insufficient pressure. The cone shaped aerosol is not functioning. Broken streams can be seem emanating from the four cooling pores.
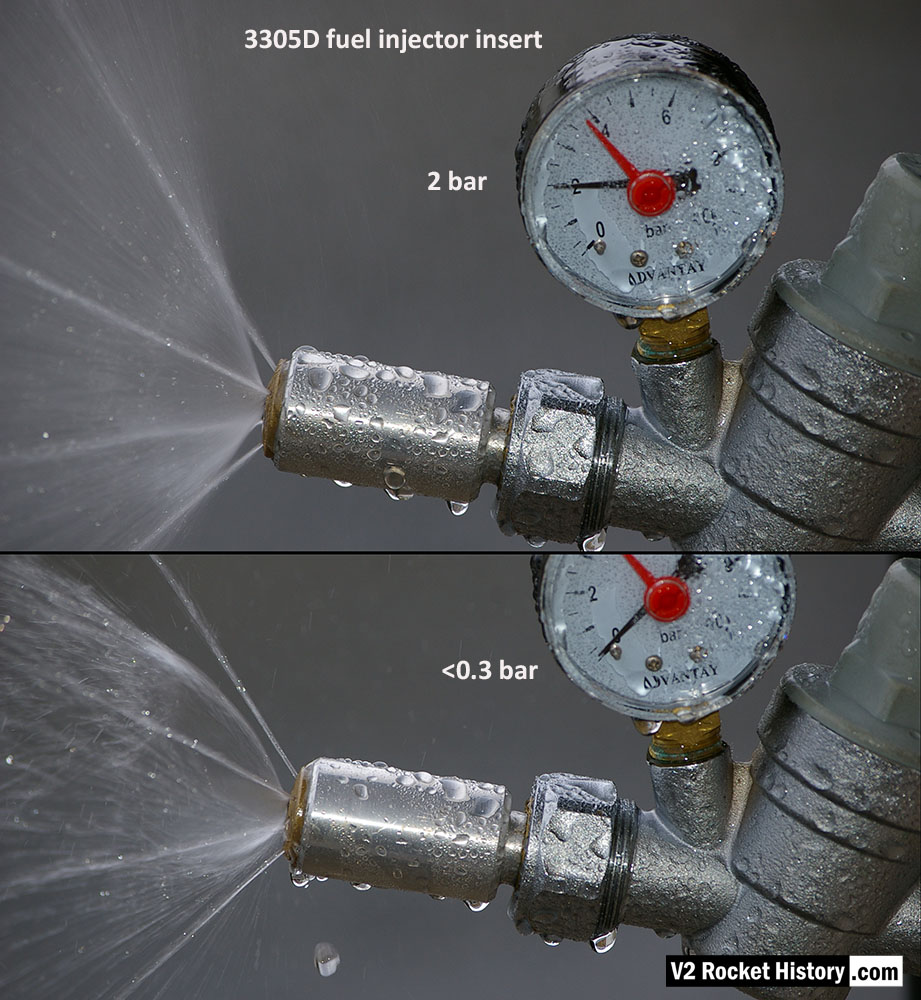
3305D injector insert showing comparison nebular and jet stream pattern with high and low pressure. Top image shows correct hollow cone-shaped aerosol effect, from central 6mm orifice, that is also creating a fine mist around and within the cone, and steady steams emanating from cooling pores. Bottom image shows the effect of reduced pressure: a dropping poorly formed cone, composed of larger slower moving droplets, and a tendency for the thicker spray to combine and cause ‘dribbeling’ with much fluid failing to clear the injector face – unlike the image above, where the injector face is clear of drips.
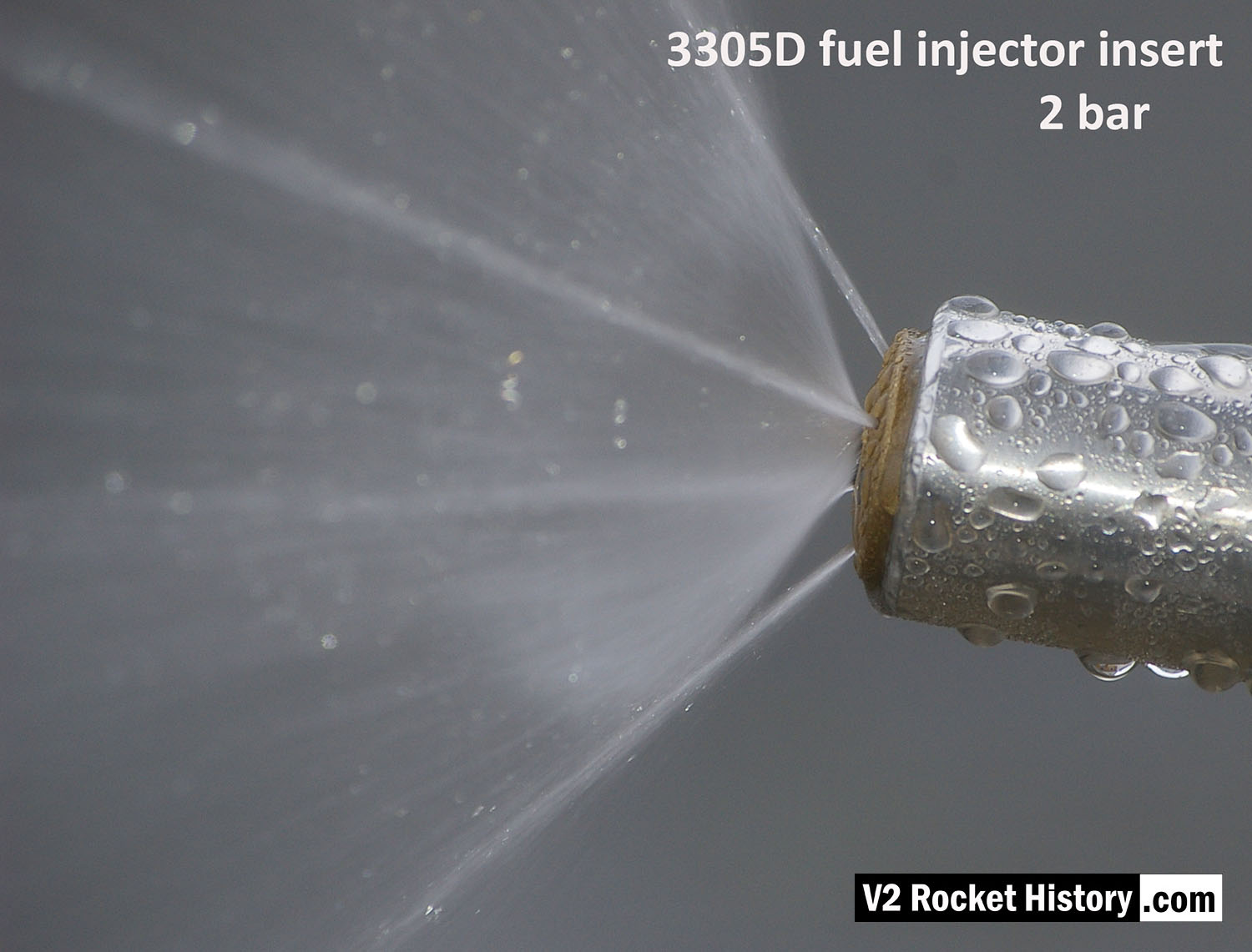
Image shows a correctly formed nebular cone attended by a fine mist. the four injector cooling jets are well shown, and although fluid beading can be seen on the face of the injector, there is insufficient liquid to cause dripping.
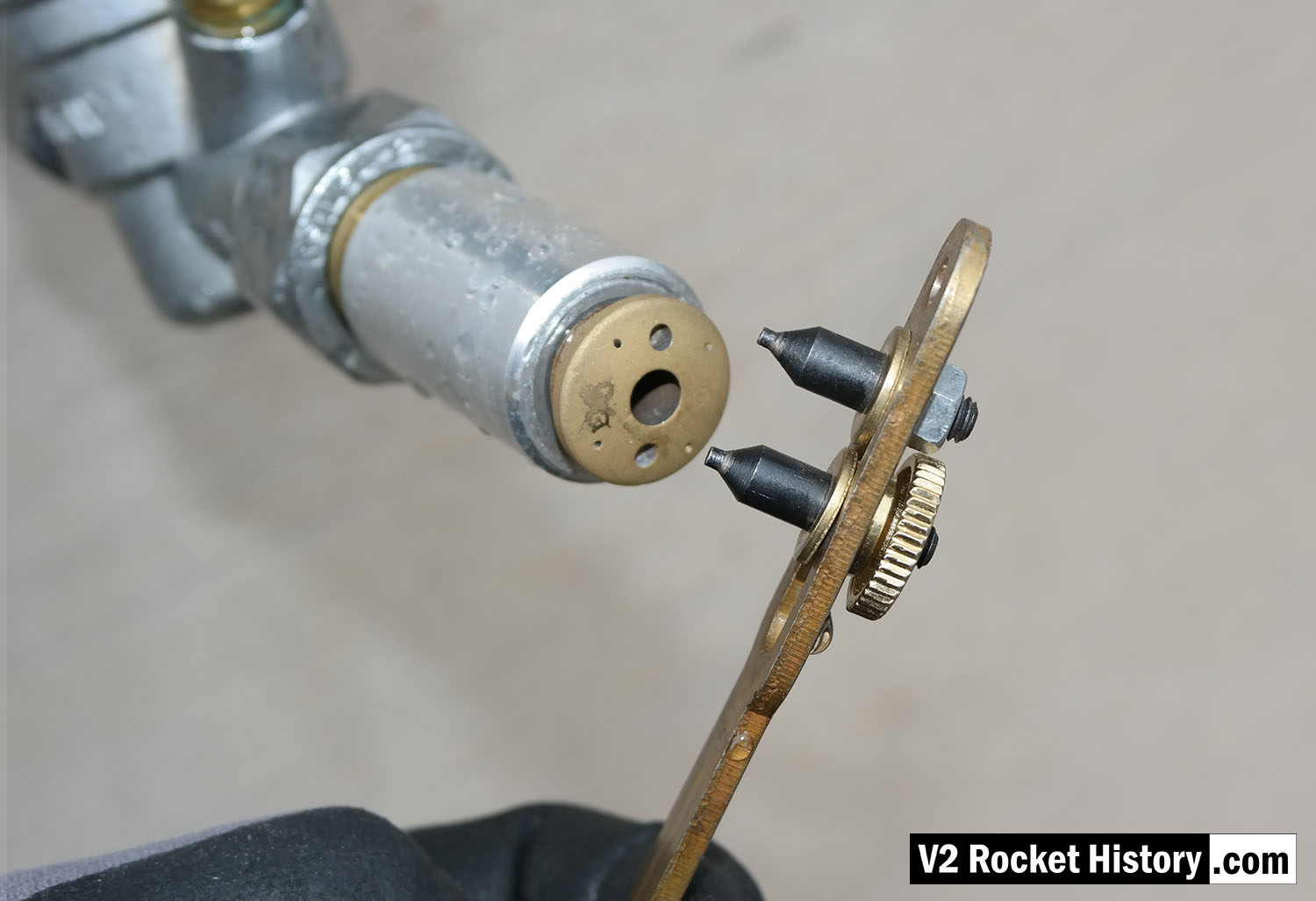
Single fuel injector water test rig showing a 3305D bress insert about to be tightened home using a pin-wrench. V2RH image

3304D higher volume injector insert (with central jet) showing comparison nebular and jet stream pattern with high and low pressure. Top image shows correct hollow cone-shaped aerosol effect from central 6mm orifice, that is also creating a fine mist around and within the cone, and strong single central (non-swirl) jet can be seen as well as 4 steady steams emanating from cooling pores. Bottom image shows the effect of reduced pressure: a dropping poorly formed cone, composed of larger slower moving droplets, and a tendency for the thicker spray to combine and cause ‘dribbeling’ with much fluid failing to clear the injector face. The appearance of central jet however seem largely unchanged.
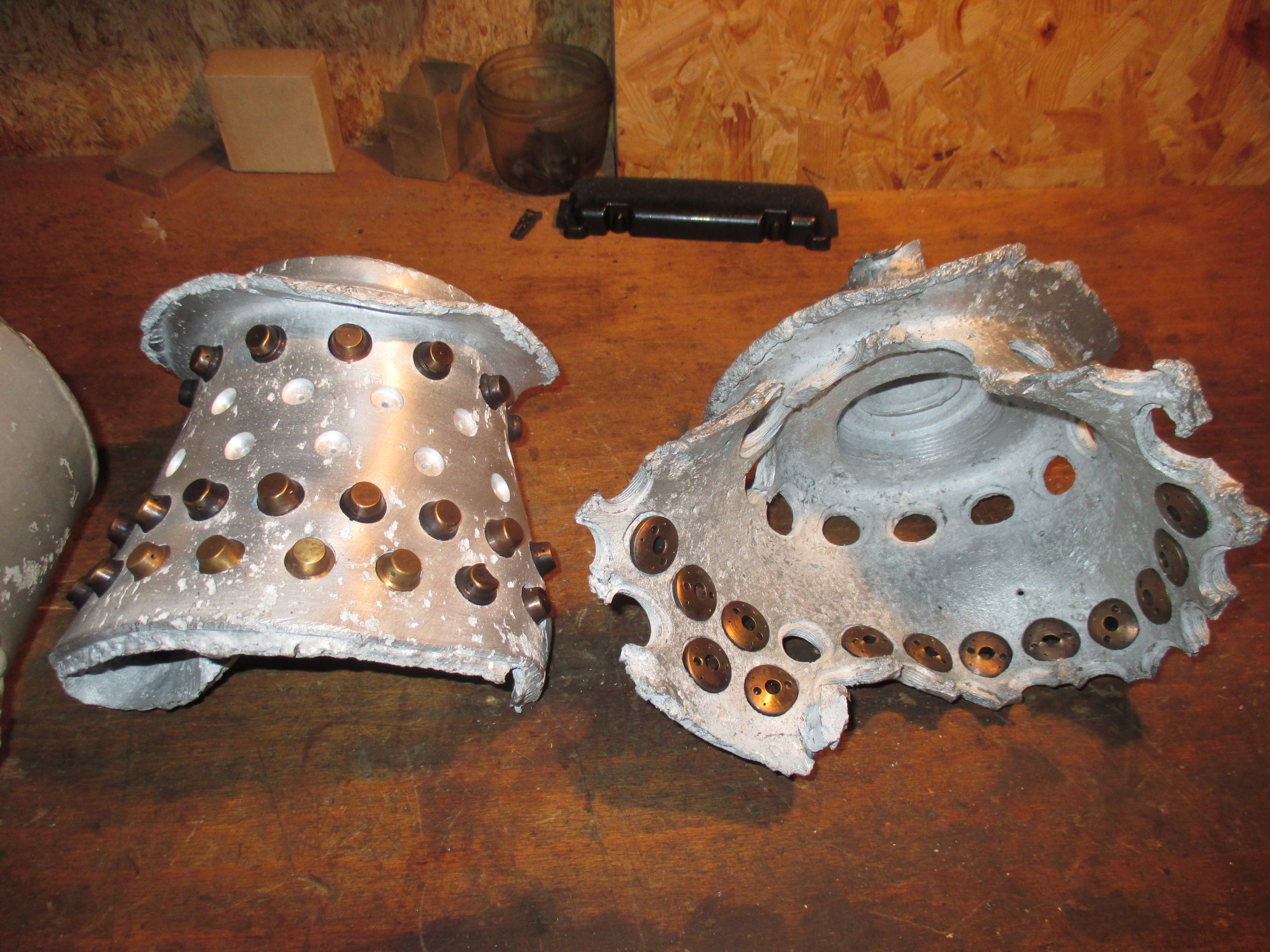
Parts of the ‘Standard’ series A aluminium head from 1941. The brass injector insert type and position pattern on the relics seem to be of the standard type but the pattern is non-standard in that higher volume injectors with three inlet apertures (two centrifugal and one central) have been place nearest the LOX
injector. Photo courtesy Horst Beck

Industrial magazine advert for Gustav Schlick printed in 1918 and showing graphic of steam boiler jets. The company, formed in 1902, had a wide expertise in all aspects of industrial spray technology and were able to steer the direction of fuel injector development along fruitful lines after they became consulting contractors to Dr Walter Thiel’s combustion research group in 1937.
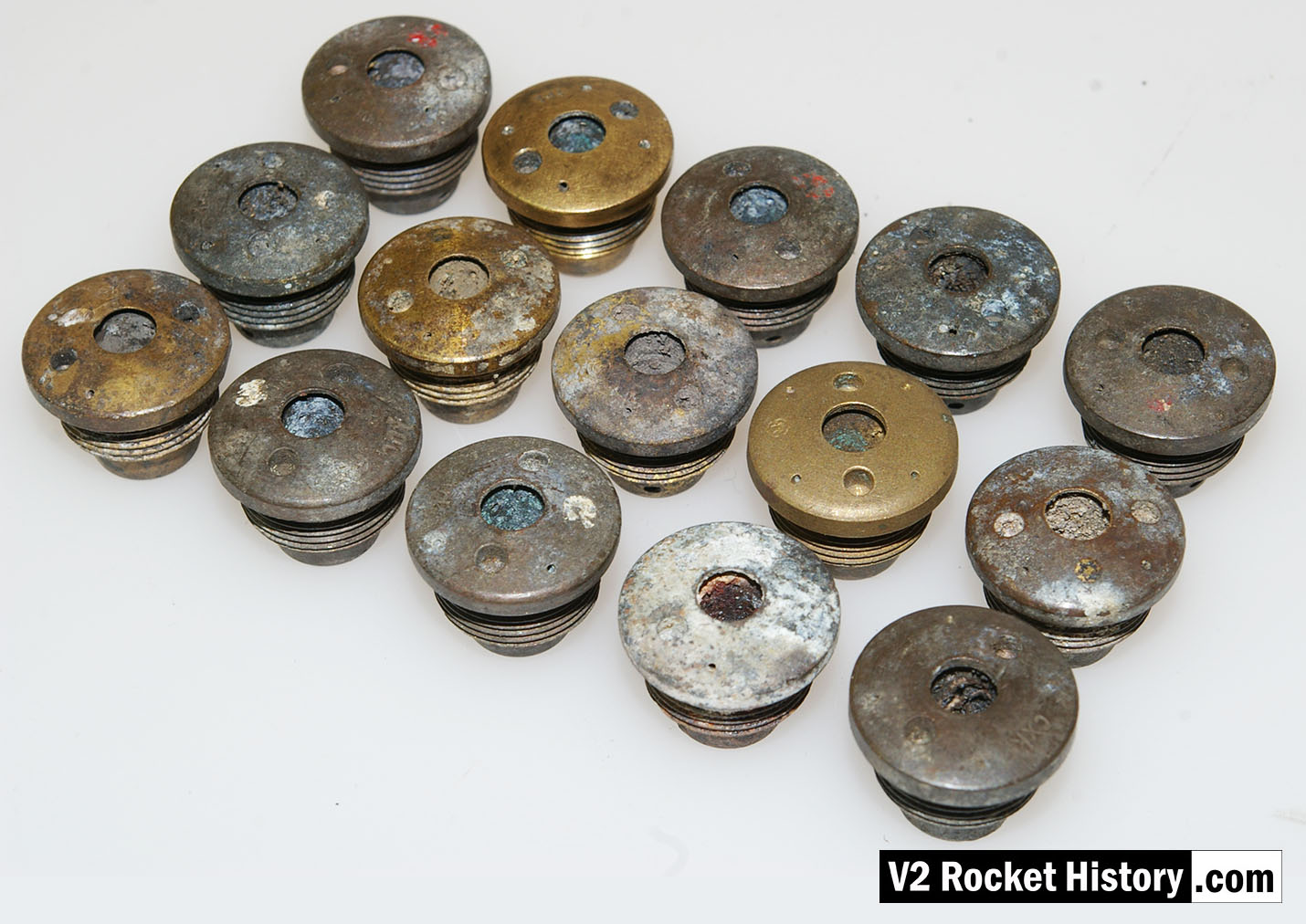
Sample set of 3303D type fuel injector inserts that were found in Peenemünde in part of a group that were bunched together in a space about 300mm in diameter with the remains of packaging. They appear to be manufacturing samples and and some have been graded with numbers 1,2,3, as well as with red and white paint to show the burner cup echelon position (C or D). Five different manufacturers are represented in this group. V2RH collection image

The injector head fragment shown here, is from an 4B 1000 kg thrust engine that was developed at Kummersdorf in 1938/39 by Dr Walter Thiel’s combustion research group. The fragment, clearly the remains of an explosion, was actually found in a scrap pile in Peenemüde but the engine was probably tested (and destroyed) at the Kummersdorf army testing station. V2RH collection image.

The injector head section of the 4B 1000kg thrust rocket engine is a precursor to the injector pot or ‘pre-chamber’ design used later for each of the 18-pots of the 25-ton V2 rocket engine. Most of the essential ingredients are shown in this drawing from 1940. Drawing no 1848E Deutsches Museum München online archive ref FA 014/12829
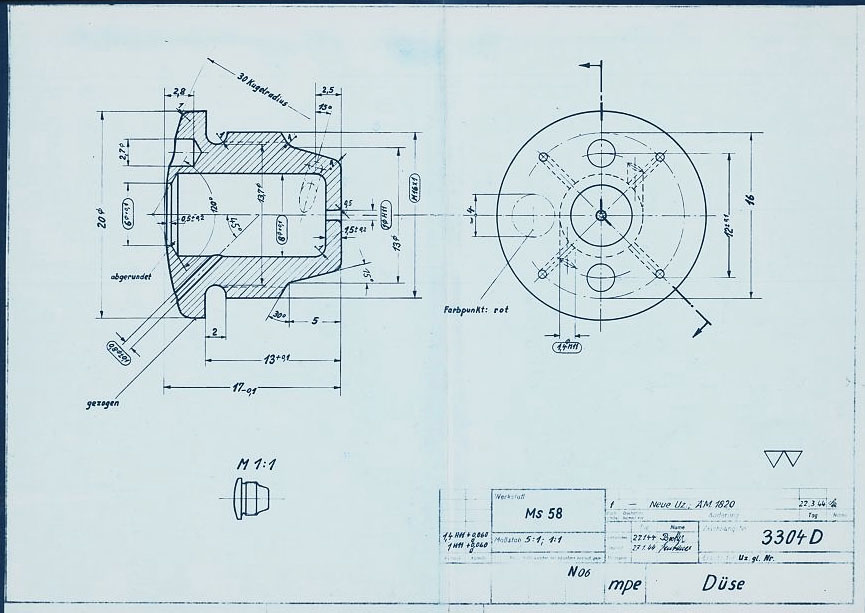
HAP11 drawing of standard 3304D fuel injector screw insert. showing details of primary swirl cavity and orrifice and all additional apertures including the four small cooling pores. HAP11 (Heimat-Artillerie-Park 11, AKA armament code: mpe), drawing number 4554D, Deutsches Museum München
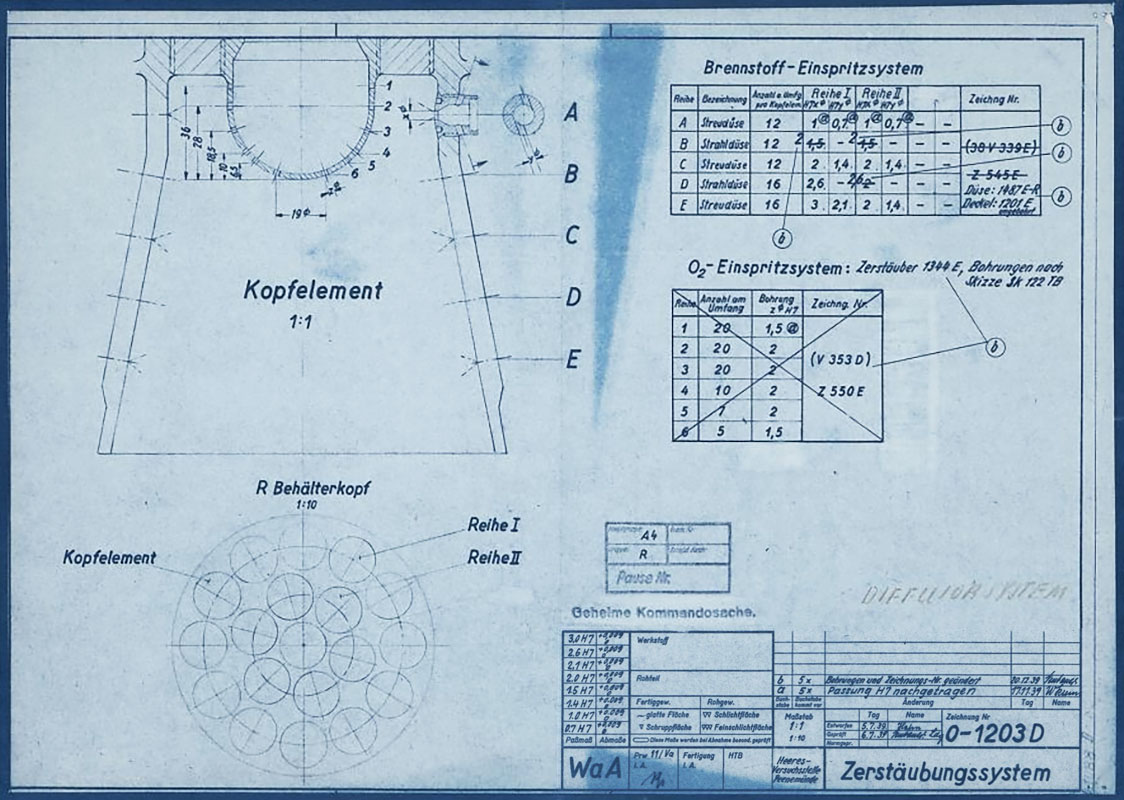
HVP drawing no 1203D showing burner cup ‘diffuser system’ disposition for 19-pot head (at this stage the 25 ton thrust injector head had nineteen so called ‘pre-chambers’ or pots as no central fuel valve was present). HVP drawing dated 1939.
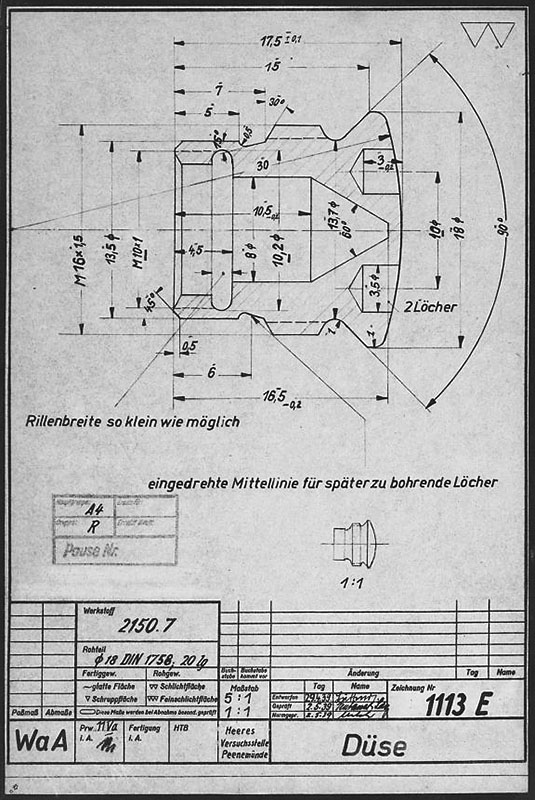
Drawing from the Army Experimental Station Peenemünde dated 1939. The specification describes an insert template that could be used for a range of outlet and inlet orifice sizes. The German text beginning (eingedrehte …) translates as ‘Center-line of screw used for holes to be drilled later’, and the hole dimensions are not specified on this document. HVP drawing number 1113 E, Deutsches Museum München
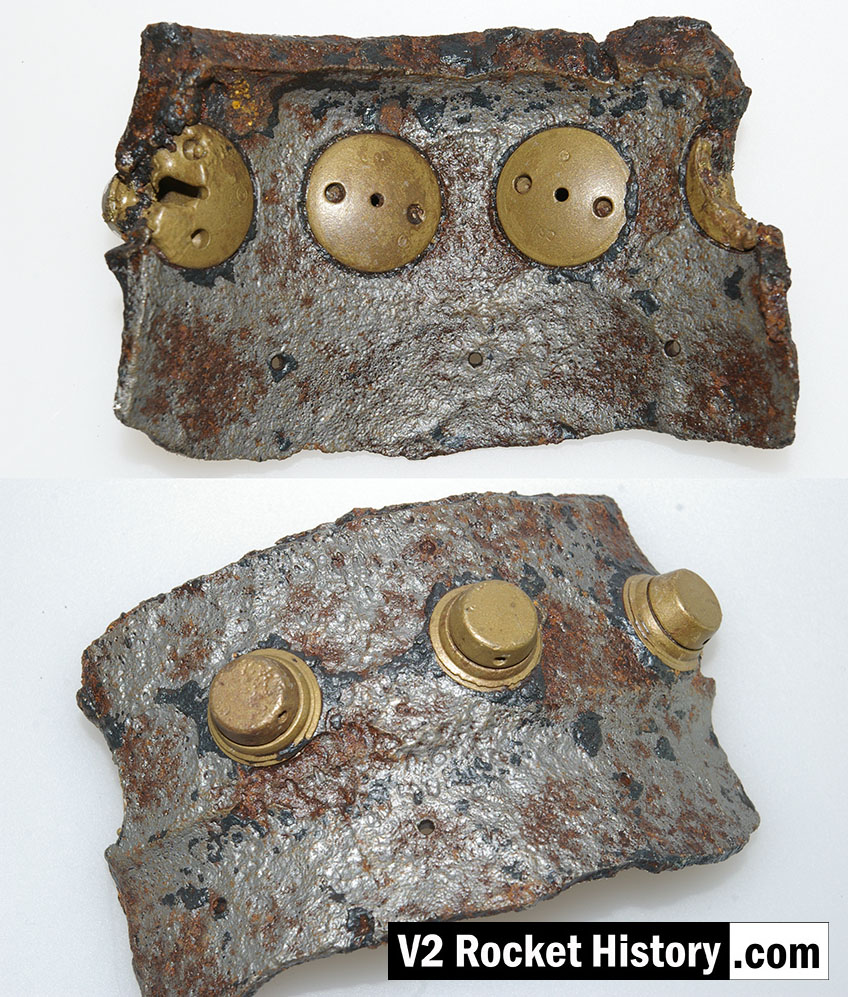
Photo shows a small section of the burner cup with row A (2131E) fuel injector inserts with three row B drilled holes below. The two undamaged inserts carry the armament code ‘csl’. The relic was found near a workshop in the Development works Pennemünde. Slag from the cutting flame and damage to the inserts at both ends of the relic would indicate that the section was cut from a steel burner cup using a gas cutter (fuel and oxygen) for purposes unknown. V2RH collection image
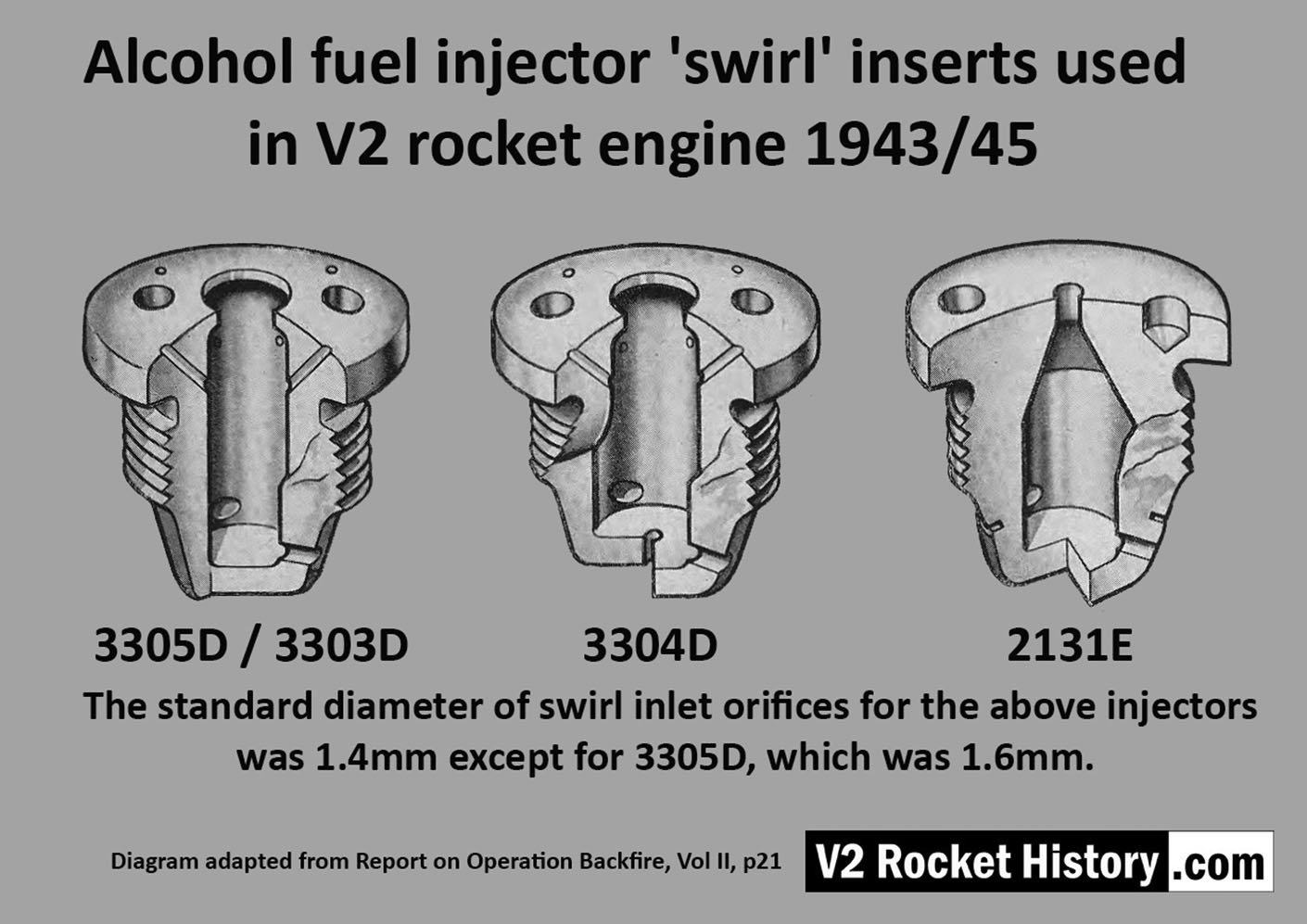
Diagram showing cut-away presentations of the settled configuration of standard four ‘swirl’ inserts used in the V2 rocket engine’s 18-pot head from 1943 until the end of the war. The inserts are shown with their drawing code identification. All of the insert types used in the injector head are shown, however there were additional screw-in type fuel supply inserts, used to provide a fuel cooling balance function, located radially in the lower part of the combustion cavity.
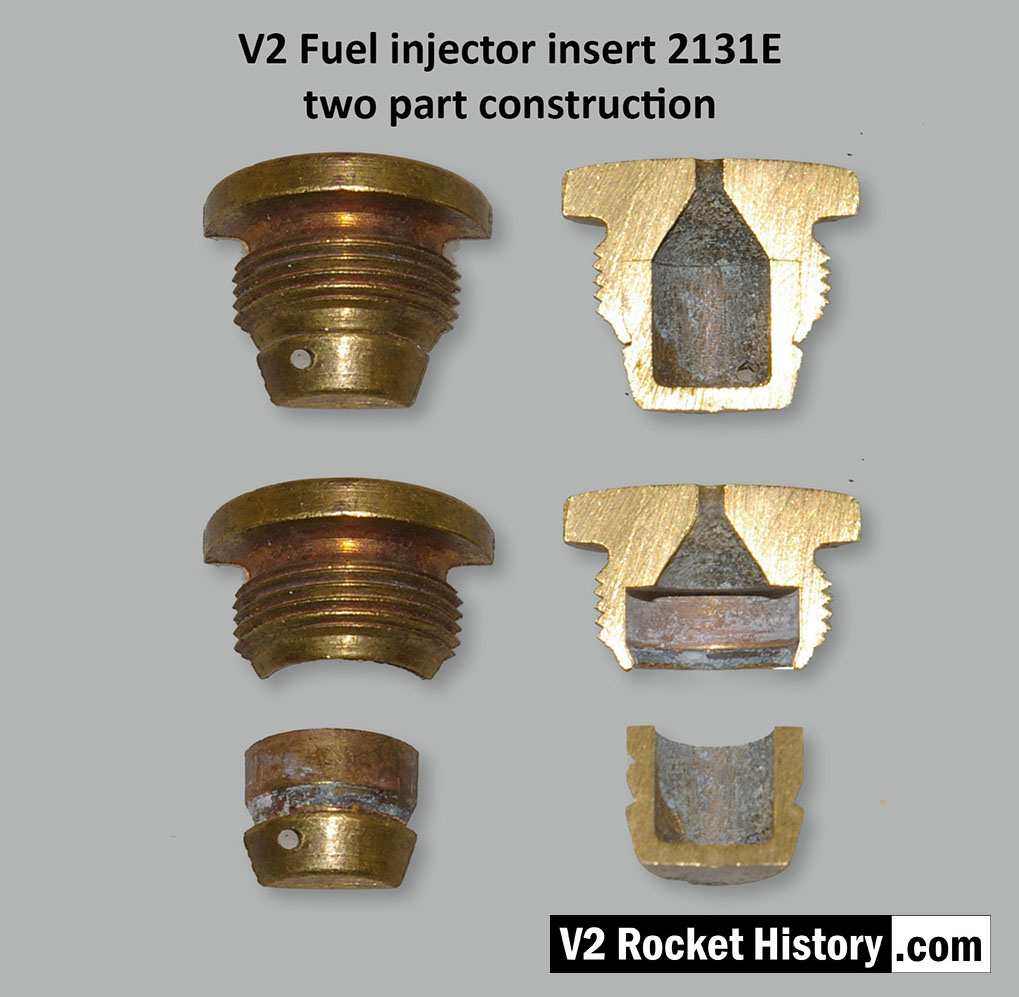
V2 Fuel Injector insert: part code 2131E from injector pot echelon A (nearest to LOX spray head). The push-together two part construction of the insert is shown here. The two parts were pushed together in a specially shaped tool set that compressed the thin skirt on the female part into a recess cut into the male part. The failure test for this component required that the mated parts resist a separating force of 300kg. The two part design was dictated by the small size of the 2mm exit orifice and the funnel shaped introduction to the exit orifice. In the case of the other three standard inserts, the large 6mm exit orifice allowed a sub 6mm milling cutter, with a thin support shaft and a top chamfer, to be used in such a way that the area below the exit orifice could be undercut to create an injector cavity with a diameter larger than the 6mm entry point.

Single nozzle insert test rig used by V2 Rocket History to test spray shape and volume at fluid supply pressures consistent with fuel pressures specified for the injector head of summer 1944. A 2131E fuel injector insert is installed in the holder at the front of the test rig, but as the thread was the same on all inserts the nozzle can be changed for other models easily with aid of a pin spanner. See video for a demonstration of this simple test system.
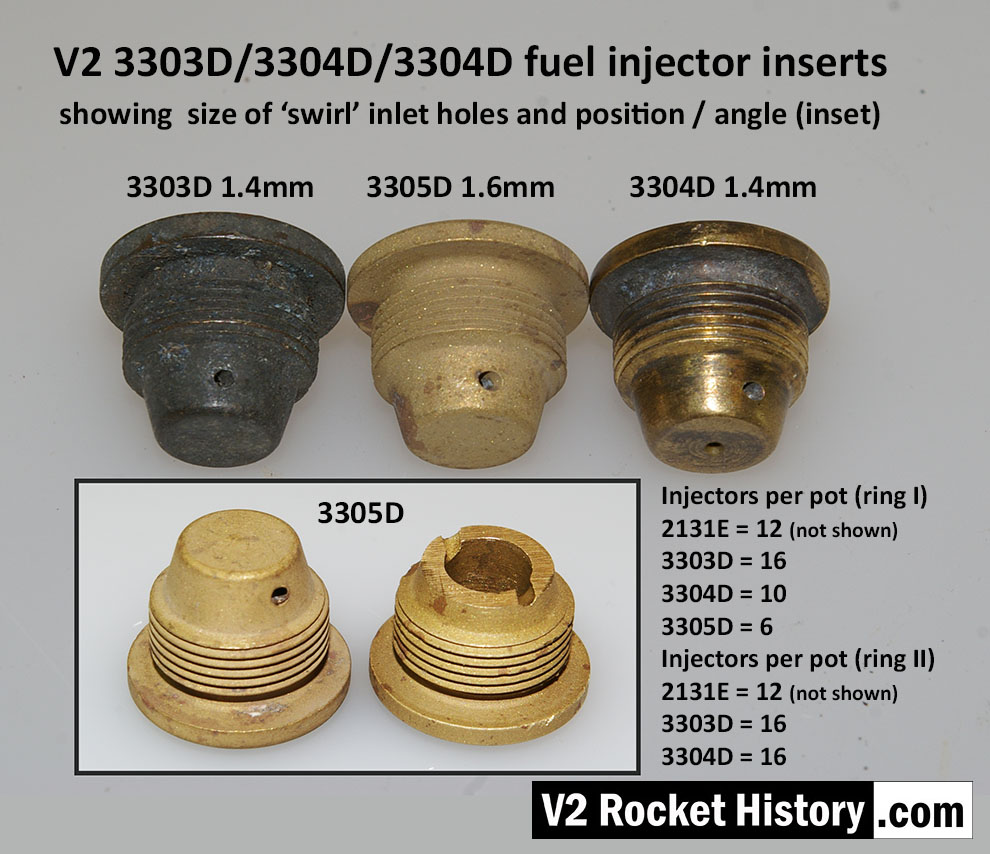
V2 fuel injector inserts 3303D, 3304D, and 3305D for injector pot echelons D and E. Photo shows swirl inlet aperture size and position.The total number of each insert type is shown, each of the 18 pots carried a total of 44 inserts. An additional 24 feed holes were drilled into the burner cup, occupying two rows B and C having 12 holes each. V2RH image
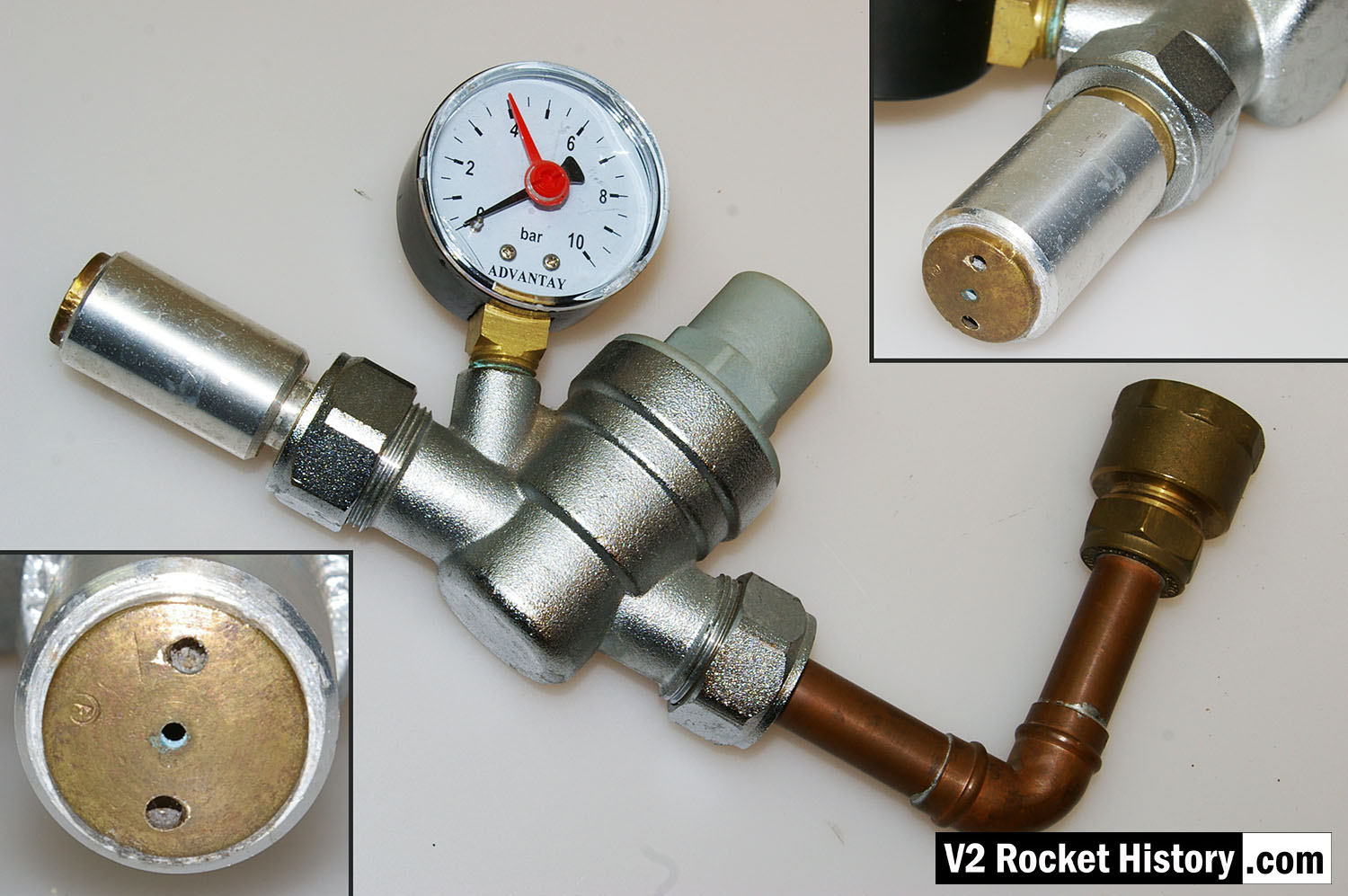
Single nozzle insert test rig used by V2 Rocket History to test spray shape and volume at supply pressures consistent with fuel pressures specified for the injector head of summer 1944. The test system features an adjustable pressure regulator and fluid pressure gauge. For test purposes the device was simply connected to a relatively high pressure mains water supply. And although water does not have the same viscosity of the 75% Ethenol to 25% water mix of the V2’s fuel it was considered close enough by the German technicians, who regularly used plain water as a substitute when testing issues related to furl flow rather than combustion. A 2131E fuel injector insert is shown installed in the holder at the front of the rig, but as the thread was the same on all inserts the nozzle can be changed for other models easily with aid of a pin spanner. See video for a demonstration of this simple test system.
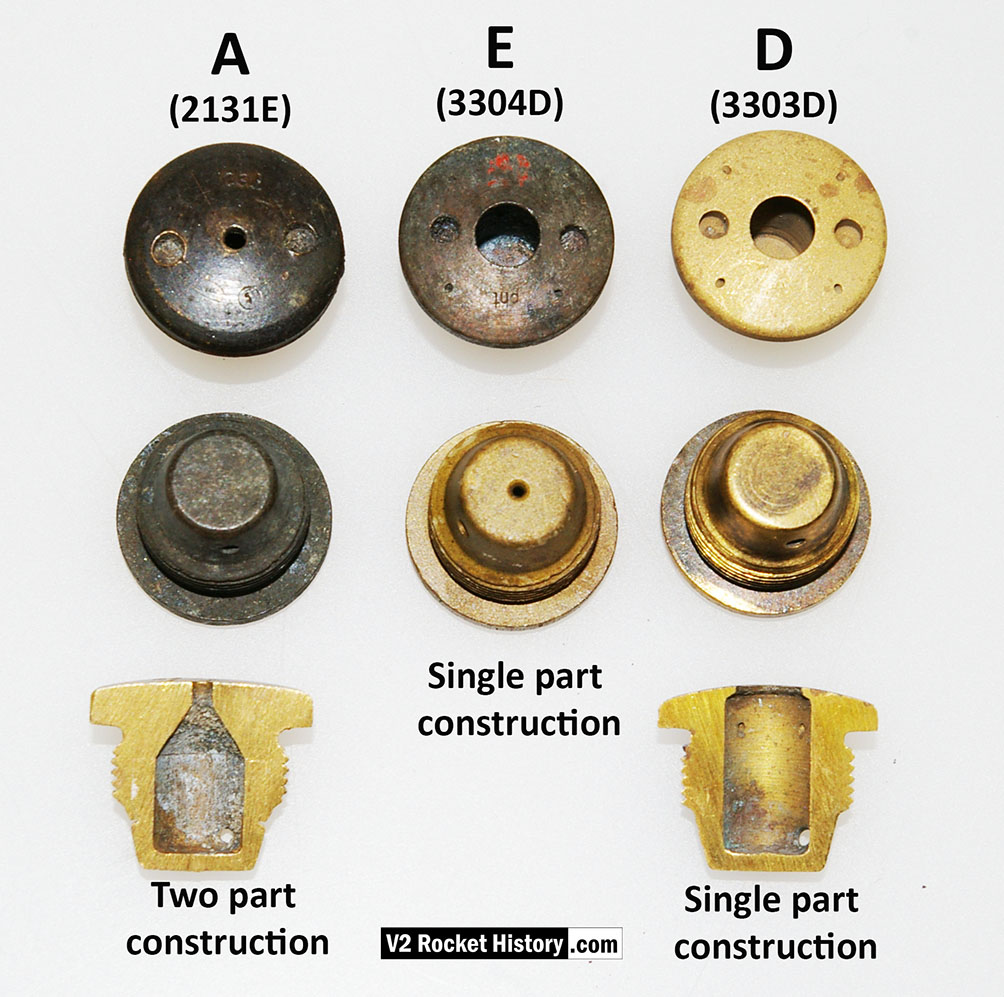
Fuel injector inserts for production series 18-pot injector head. The top row shows the injector face, second row shoes the same types from the rear. The lowermost insert have been halved to reveal the cavity shape, orifice edge, inlet and cooling apertures. Note that the insert in column A, 2131E, is two piece construction, and pressed together for assembly (see additional photo). On test, the parts had to remain together under a separation force of 300kg.
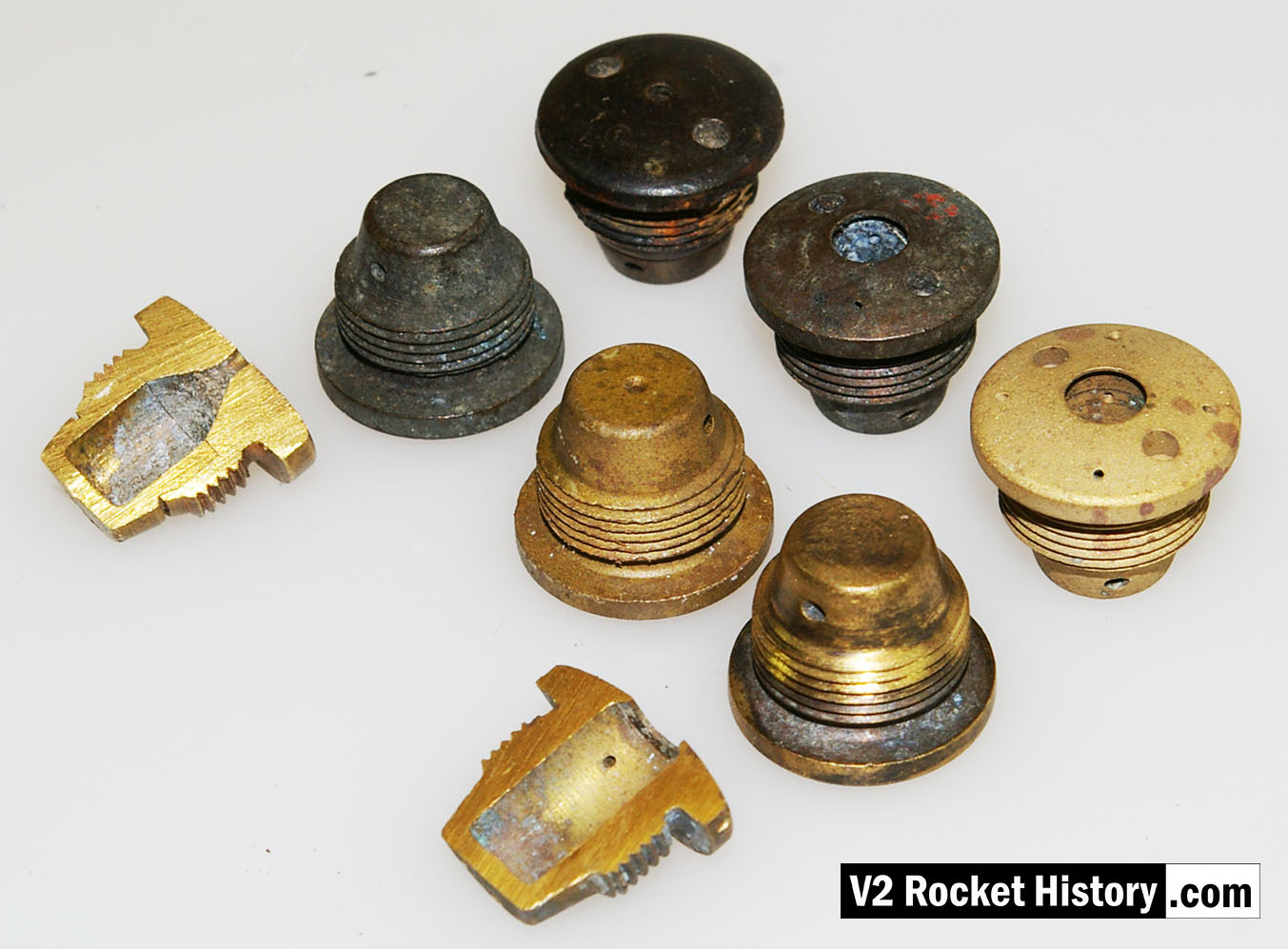
Fuel injector inserts for production series 18-pot injector head showing general shape and thread position. For further details see associated image. The lowermost insert have been halved to reveal the cavity shape, orifice edge, inlet and cooling apertures. V2RH image
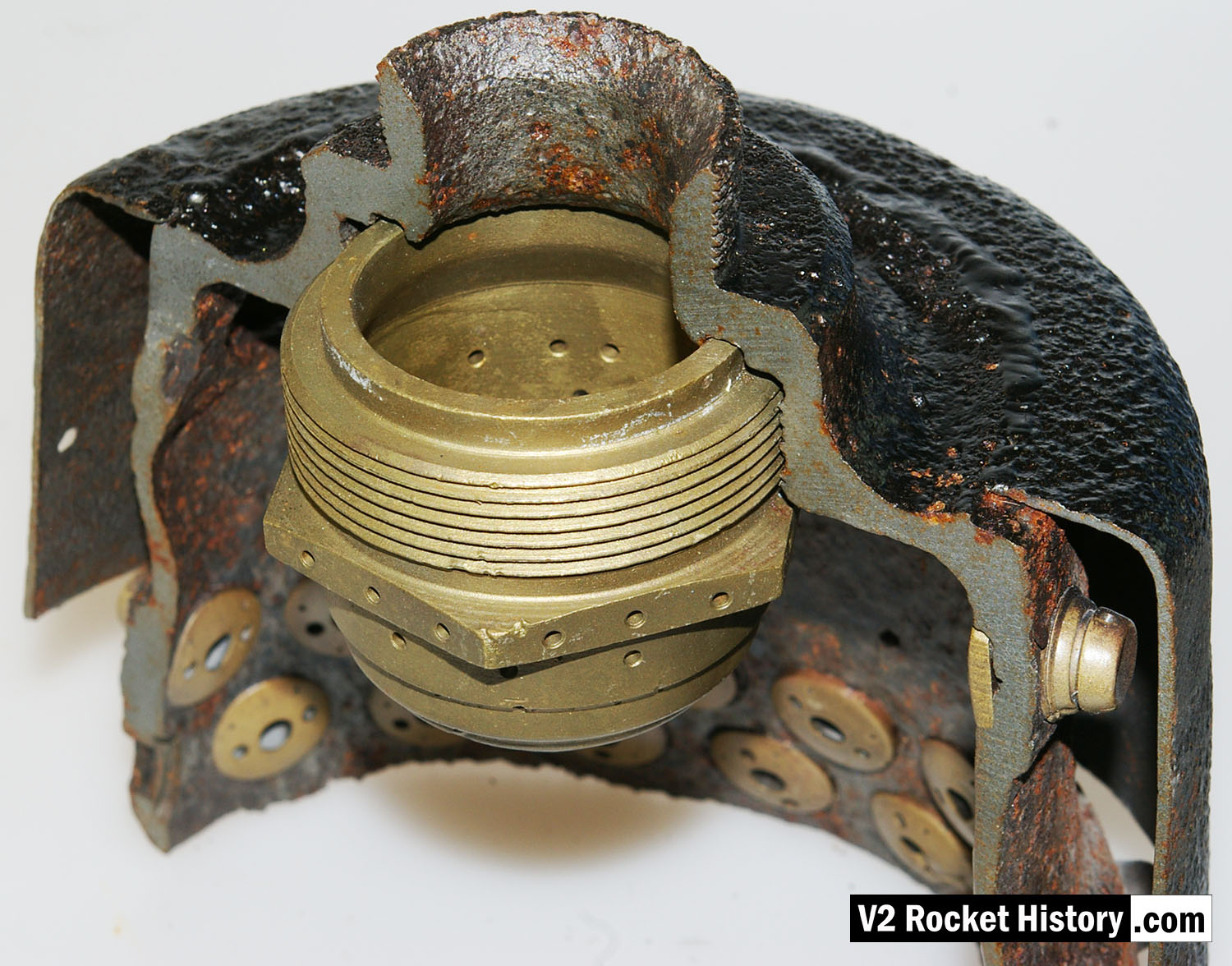
Cutaway section of fuel and liquid oxygen (LOX) injector pot. The exhibit shows the bell shaped thick inner wall of the burner with three tiers of fuel injector inserts (A,D, and E). The central copper alloy LOX spray injector is also well displayed in this image. The thin steel outer shell of the burner cup is shown and affords a good view of the head cavity that supplies fuel to the injector inserts – one A type injector is shown party cut through on the right, its rear portion showing inside the fuel cavity. V2RH image

Cutaway section of fuel and liquid oxygen (LOX) injector pot. The exhibit shows the bell shaped thick inner wall of the burner with three tiers of fuel injector inserts (A,D, and E). As well as the two rows of plain drilled apertures B and C. The central copper alloy LOX spray injector is also well displayed in this image and shows the three letter armament code of the manufacturer (elr = H.K. Rudolf, Pilsen) and the 1943 date of manufacture on one face of the hex nut. Note the close proximity of the tier A injector inserts to the LOX injector. The spary from these injectors plays directly onto the lower section of the LOX spray head. This section of the burner cap had the lowest temperature and as a result tier A insert did nor require cooling pres. See associated picture. V2RH image
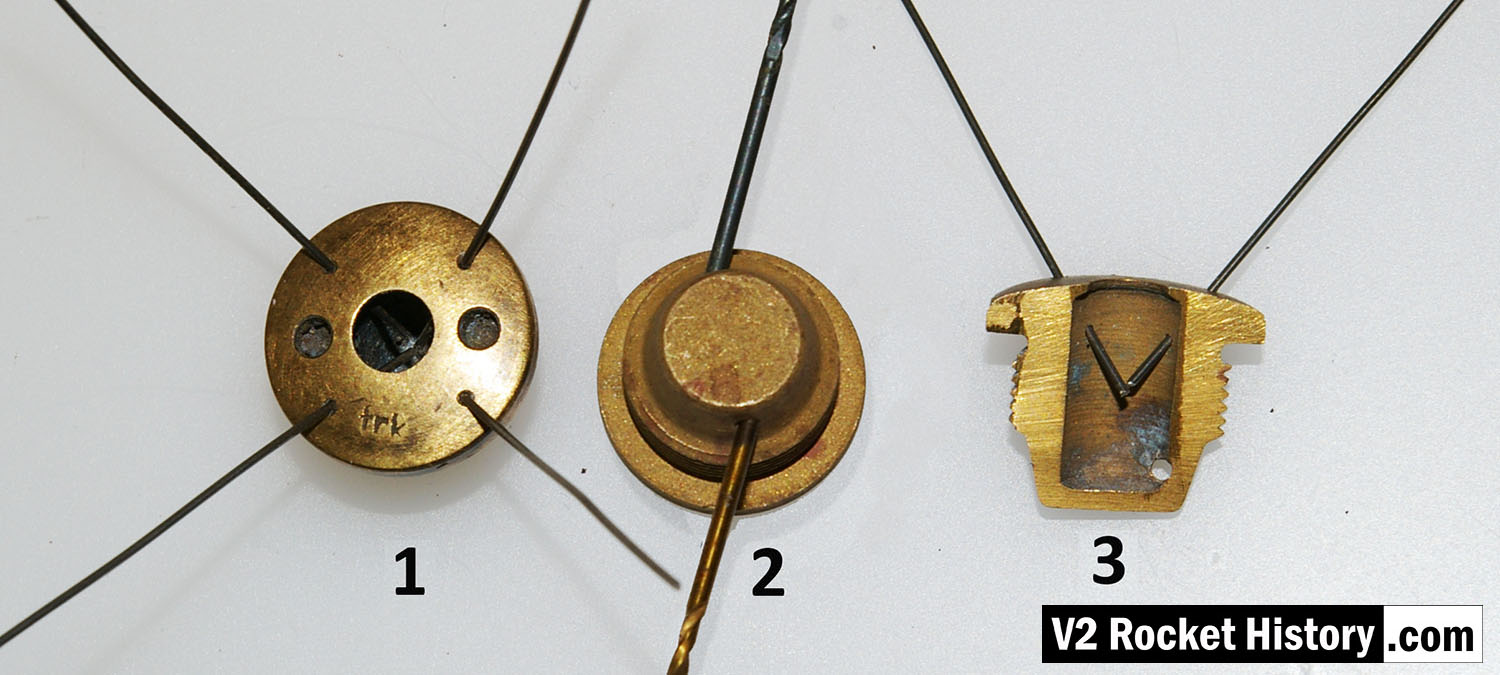
Standard fuel injector inserts for production series 18-pot injector head. Insert 1 (3304D/3305D) shows four thin wires demonstrating the angles of all four ‘cooling’ pores. Insert 2 (3305D/2131E) has two 1.3mm twist drill showing the edge bores for the gyroscopic swirl inlets. Insert 3 (3305D) shows another view of the cooling pore angle and origin. V2RH image
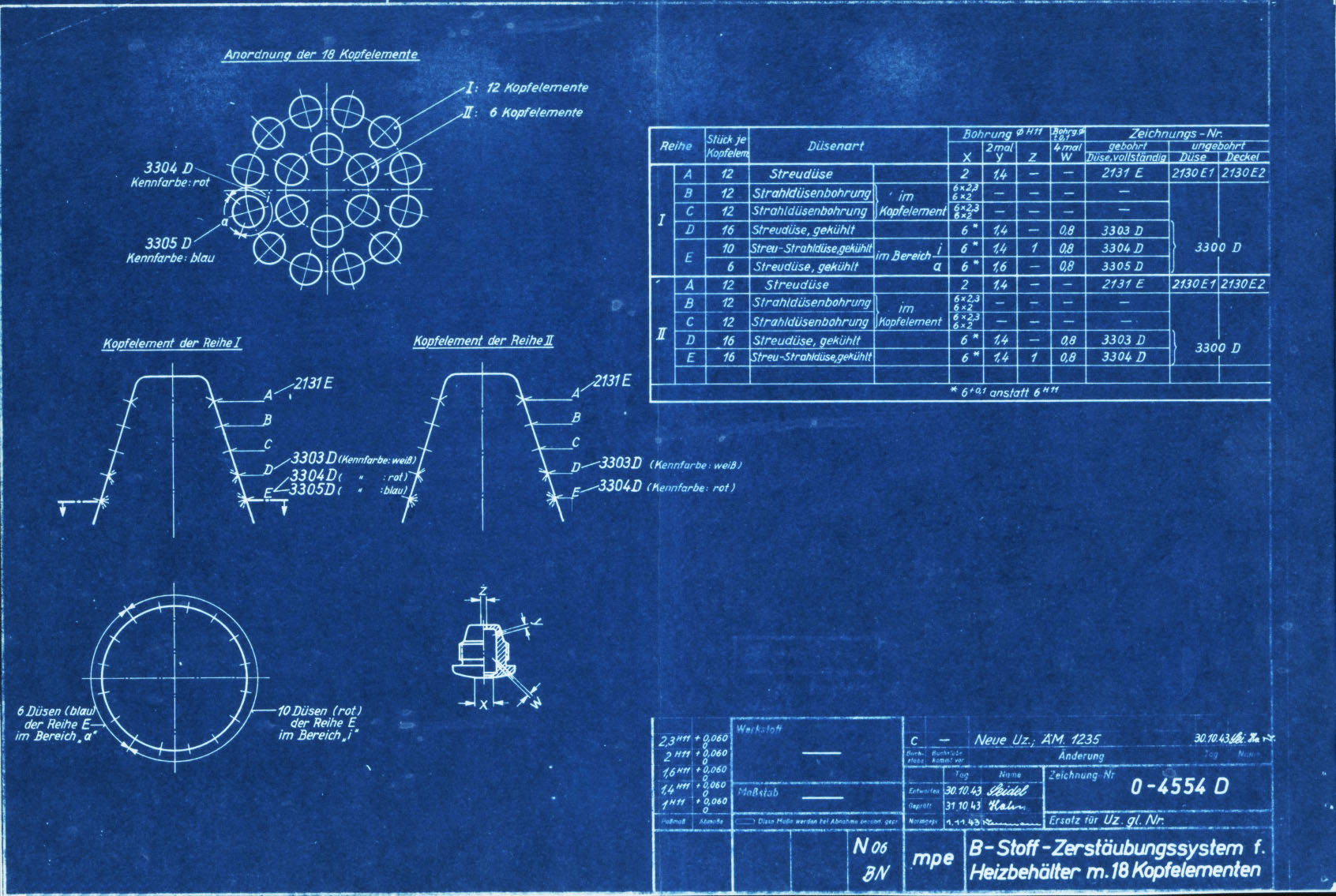
Specification for fuel injector inserts showing orifice size, type, and A to E echelon position. Peenemünde document dated 30th October 1943. Of note on this document is the combination of high and low volume injector inserts (3304D and 3305D) in the echelon E position of the 12 cups comprising outer ring I. It shows that each cup or pot on this outer ring had 16 inserts at the lowermost position E with 12 of the inserts with three inlet apertures (3305D) and 6 with only two inlet apertures (3304D being lower flow volume) positioned in the segment covering 165 degrees and closest to the outside edge of the head. HAP11 (Heimat-Artillerie-Park 11, AKA armament code: mpe), drawing number 4554D, Deutsches Museum München
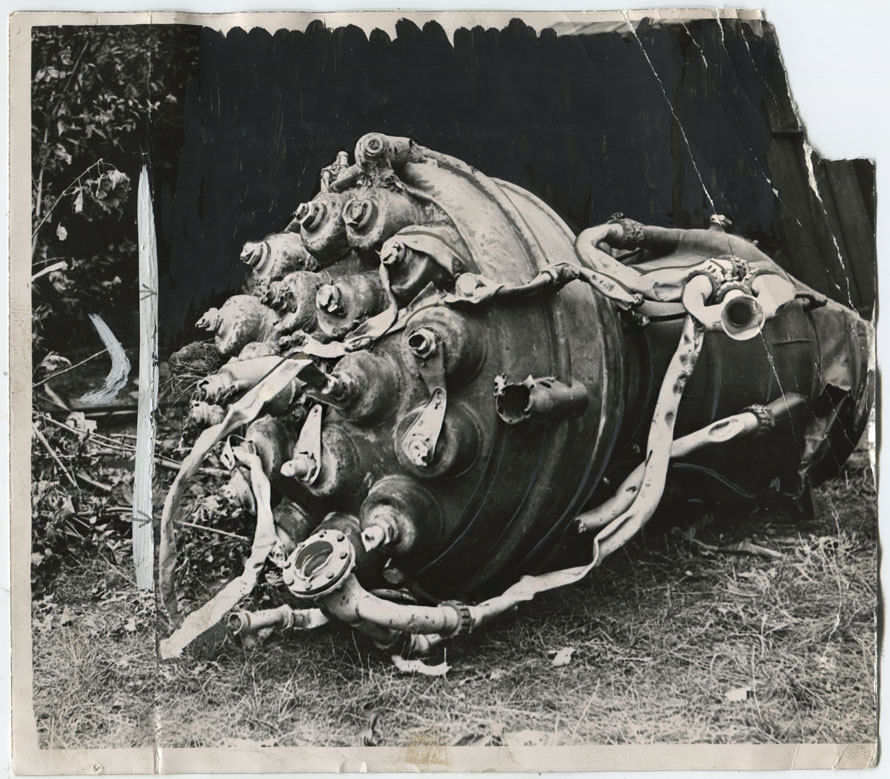
Wreckage of V2 combustion chamber with a tangle of connection pipes laying in a garden in Southern England – winter 1944. The censor has obscured the background to avoid providing the enemy with useful information. The injection head shows two connected lock ‘spanners’ securing the nuts of oxygen inlet pipes. Prior to impact all 18 of the LOX pipe input nuts would have been secured by these lightweight pressed steel ‘spanners’.
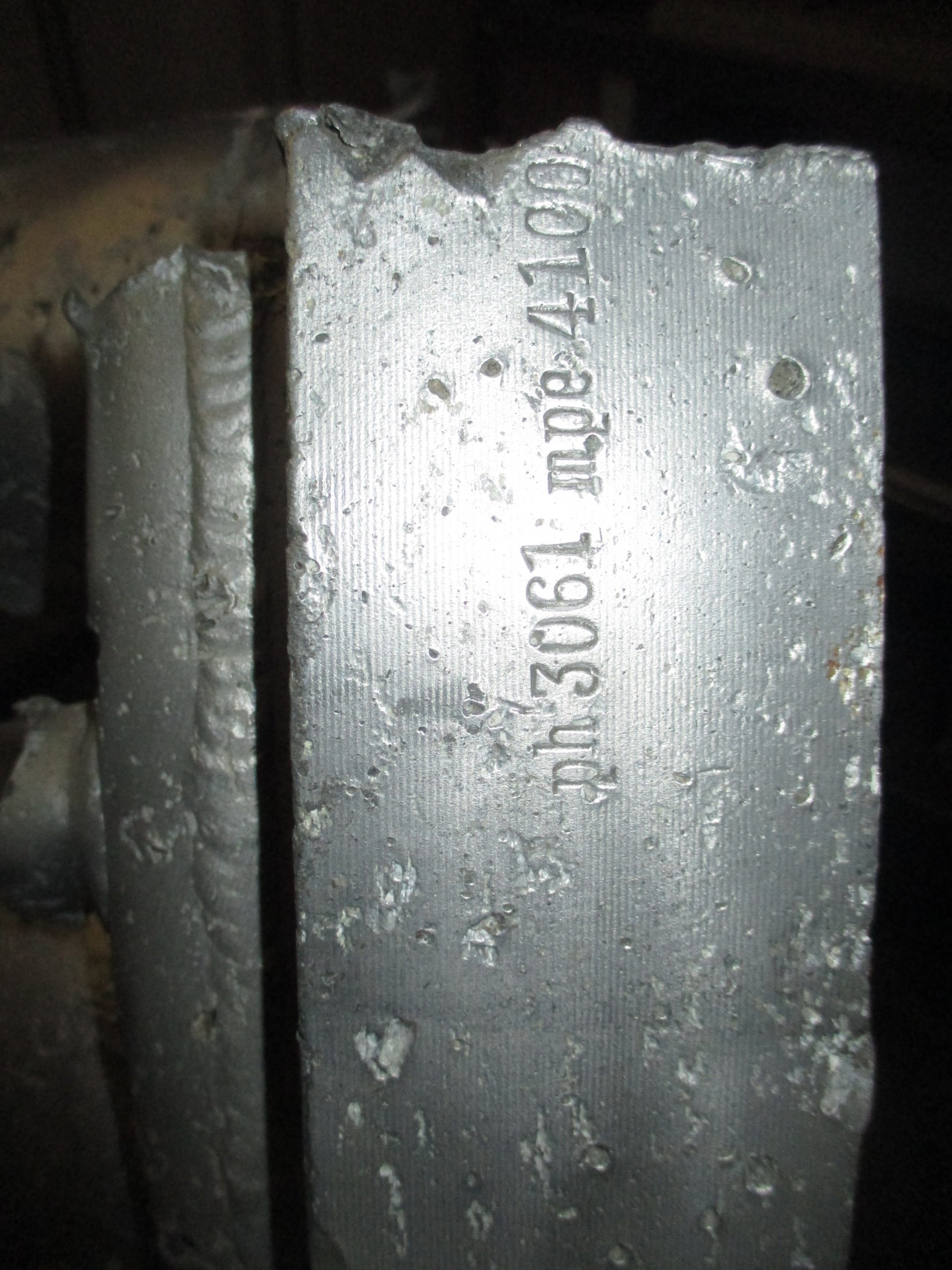
25-Ton aluminium injector head showing mpe armament code for the Heimat-Artillerie-Park 11 (HAP11) Karlshagen Werk Nord.
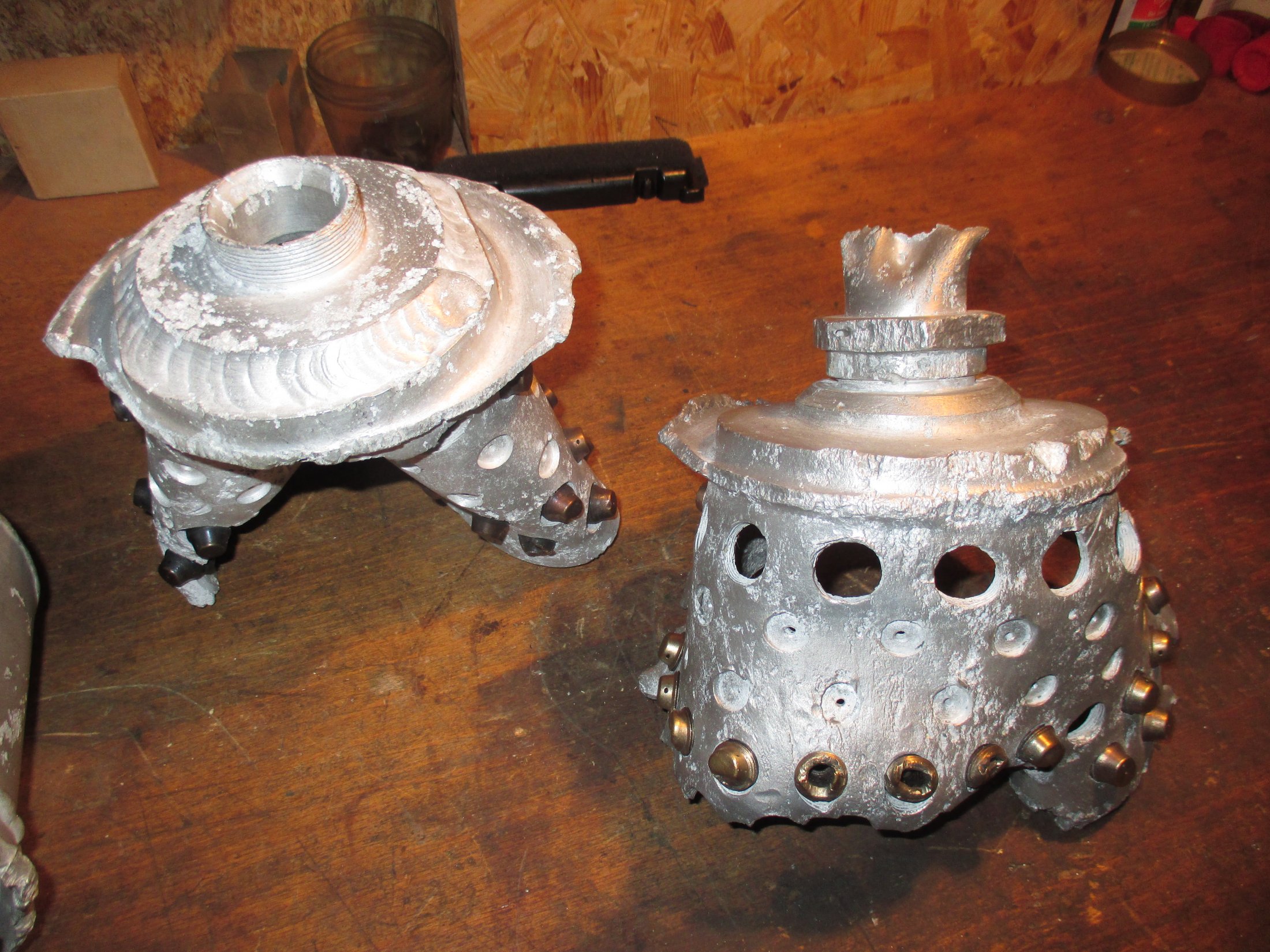
Relics of the A4 25-ton 1941 aluminium injector head. See other photos in this series for more detail. Photo courtesy Horst Beck Collection
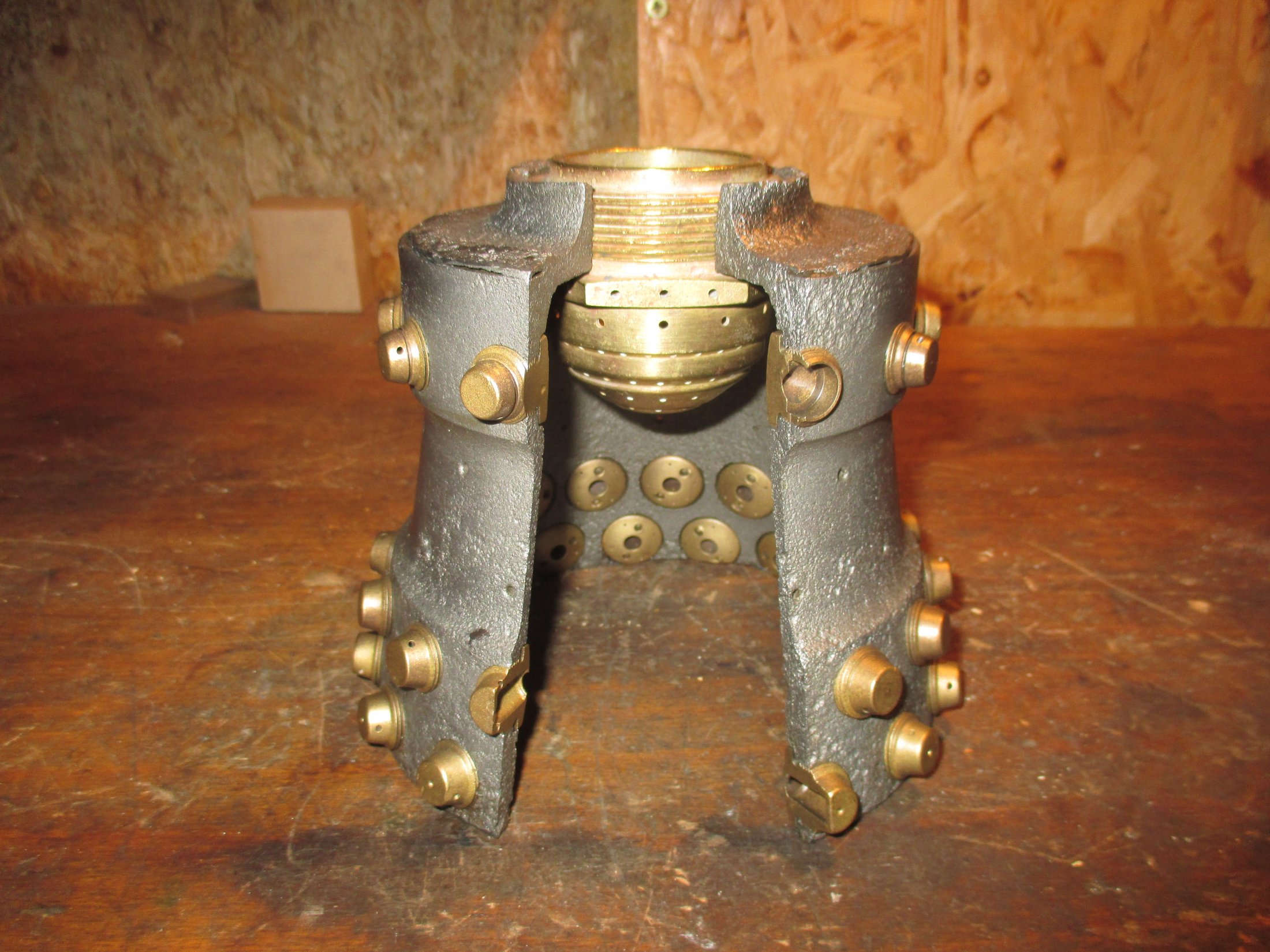
Part of the ‘Standard’ series A aluminium head from 1941 to early 1942. Showing the position of standard type LOX injector. The brass fuel injector inserts type and position pattern on the relic seem to be of the standard type with the row of 3 inlet aperture type inserts positioned furthest from the LOX injector. Photo courtesy Horst Beck Collection
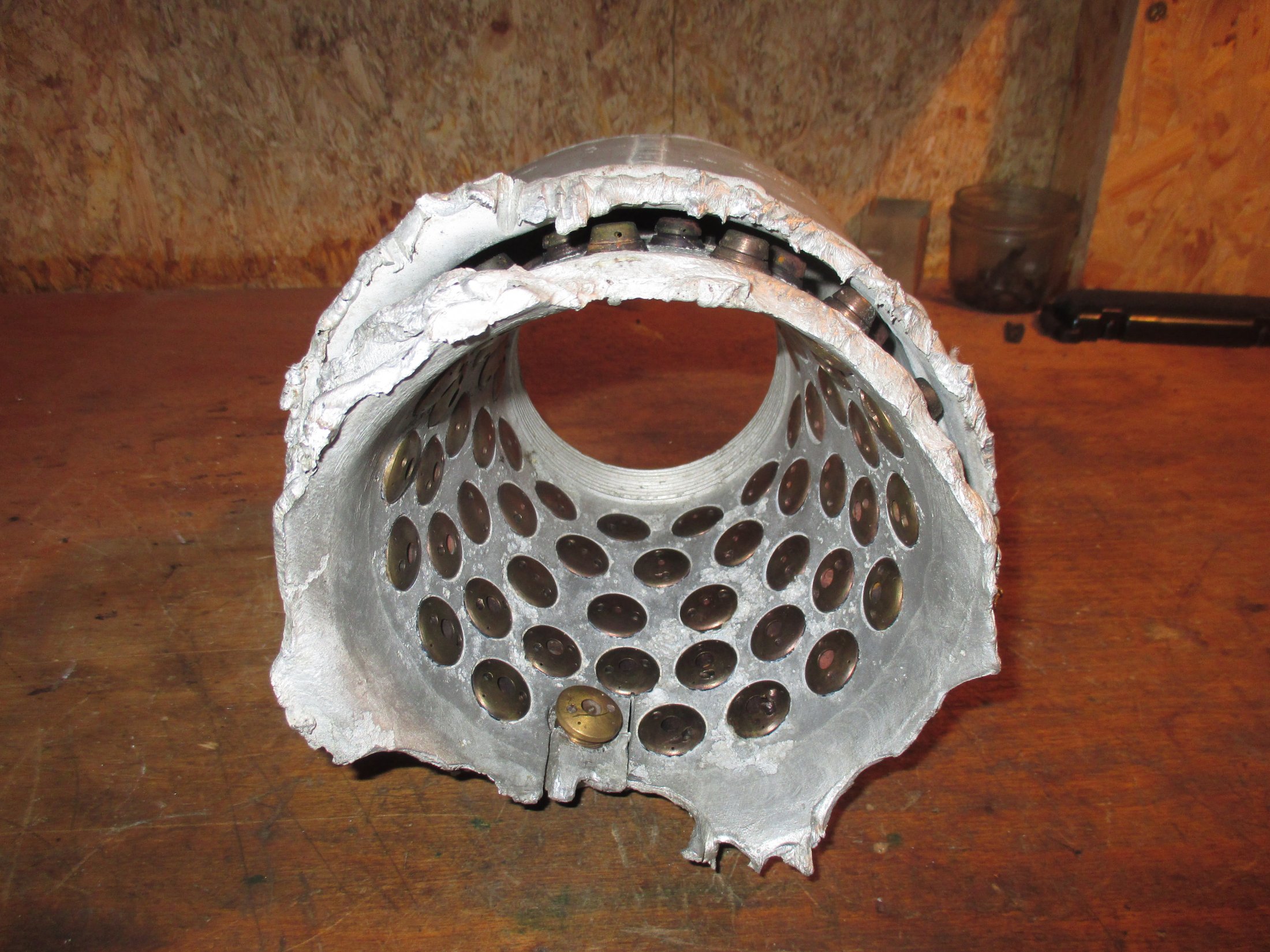
Relic of prototype A4 25-ton 1940/41 aluminium injector head basket (or pre-chamber) showing 68 copper alloy inserts in 5 rows. The standard configuration would later become 44 inserts in 3 rows 25 2mm diameter drilled holes in two rows situated at row 3 and 4 (counting from nearest the camera). Photo courtesy Host Beck Collection
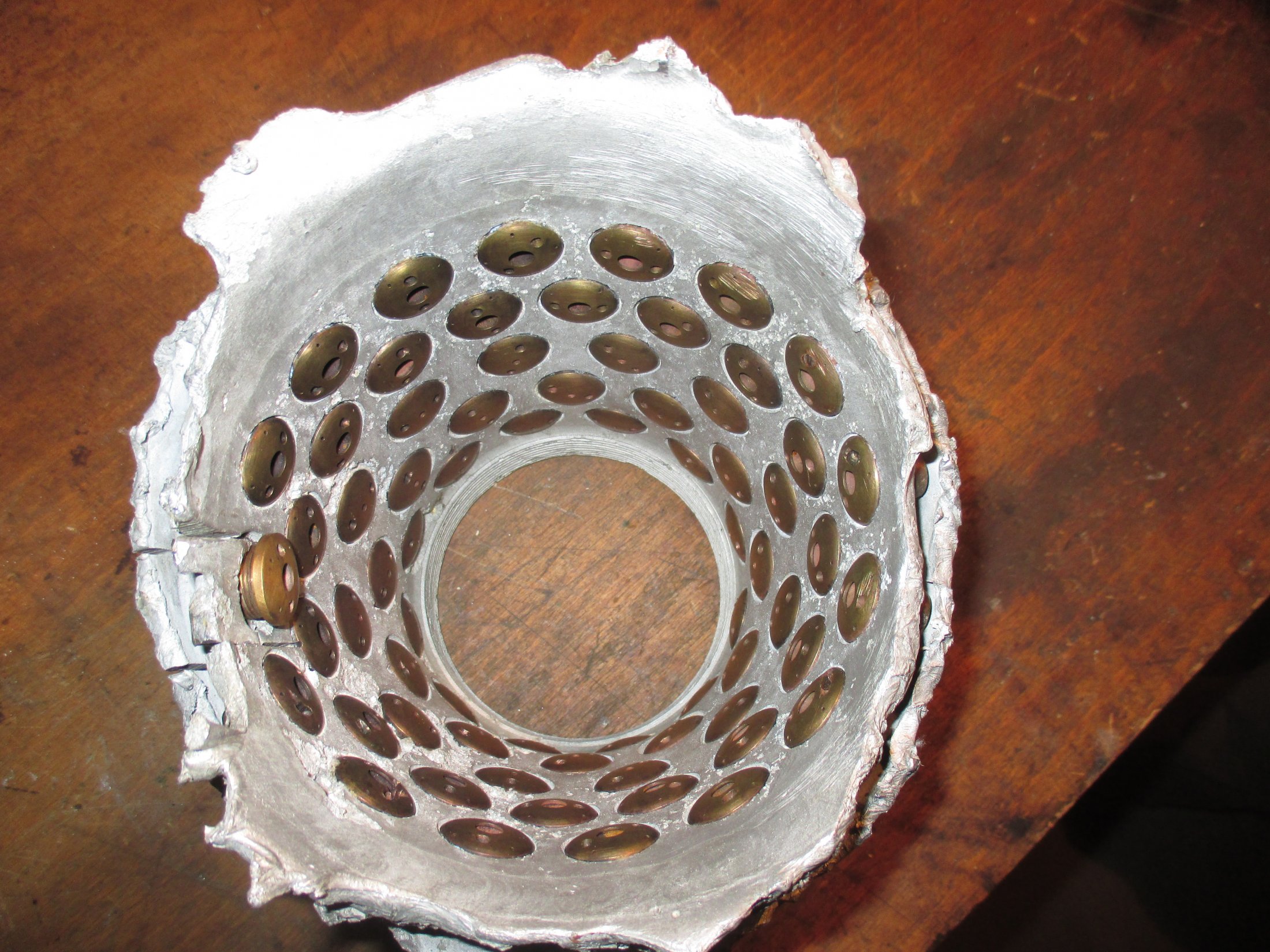
Relic of A4 25-ton 1940/41 aluminium injector head basket (or pre-chamber) showing 68 copper alloy inserts in 5 rows. The standard configuration would later become 44 inserts in 3 rows 25 2mm diameter drilled holes in two rows situated at row 3 and 4 (counting from nearest the camera). Photo courtesy Host Beck Collection
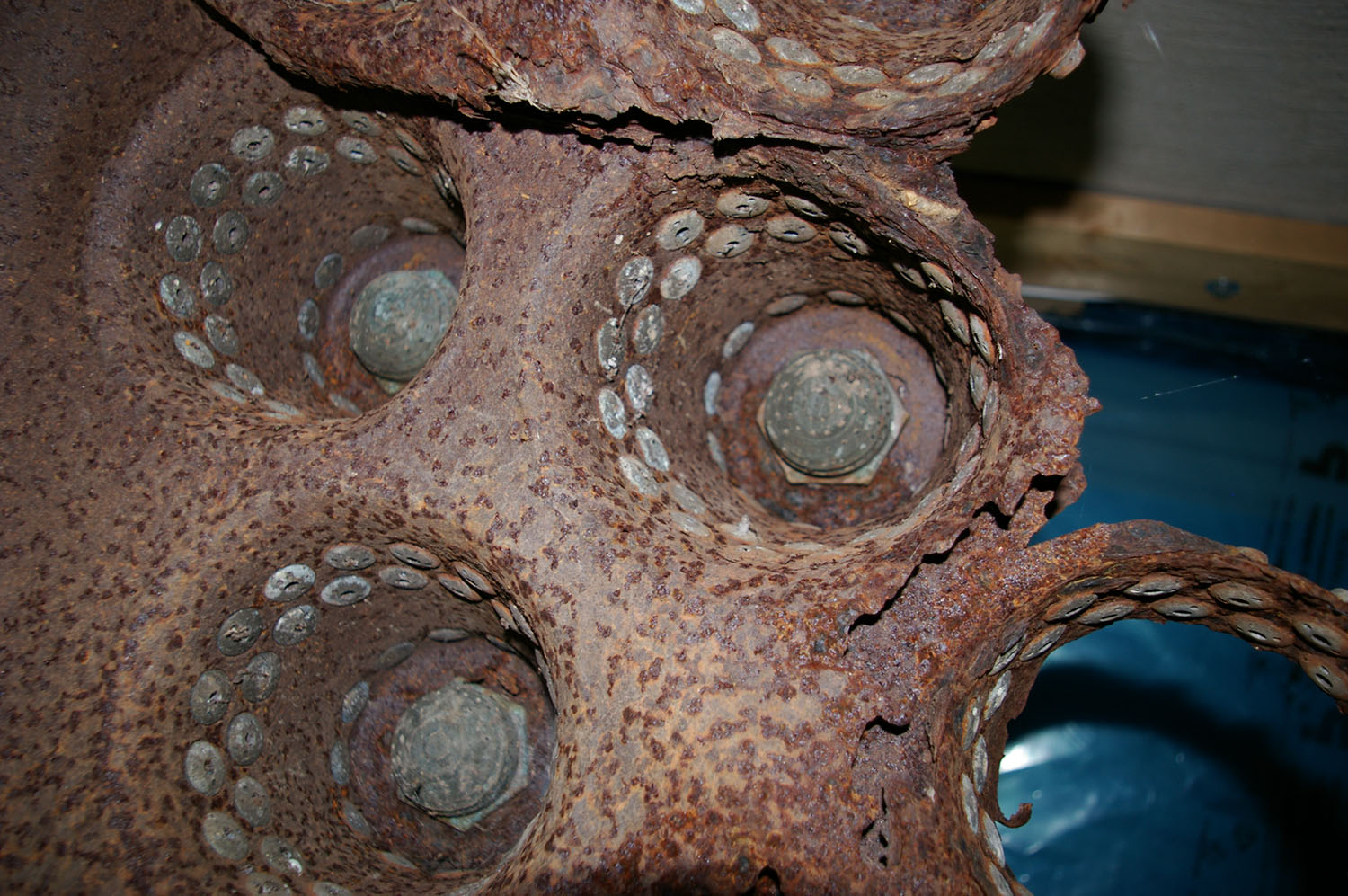
Injector head relic from February 1945 showing injector insert type and pattern. Photo www.v2rockethistory.com
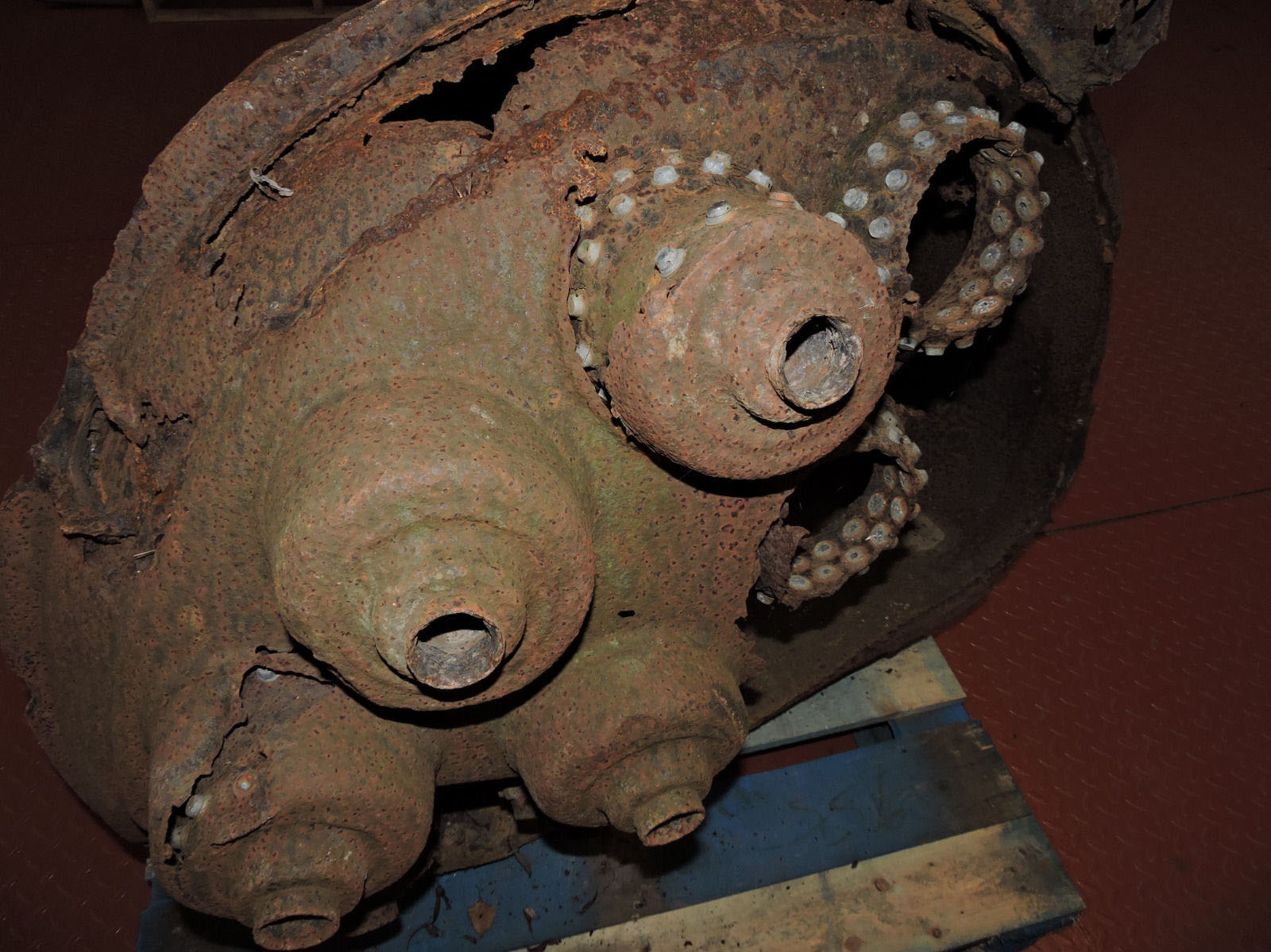
Flown V2 thrust chamber relic from February 1945. Badly damaged from impact, this head shows 4 intact LOX input pipe connections as well as exposed fuel injector inserts positioned in the inner wall of the injector pots. The inner and outer walls of the head are also conveniently exposed on this exhibit. Photo www.v2rockethistory.com
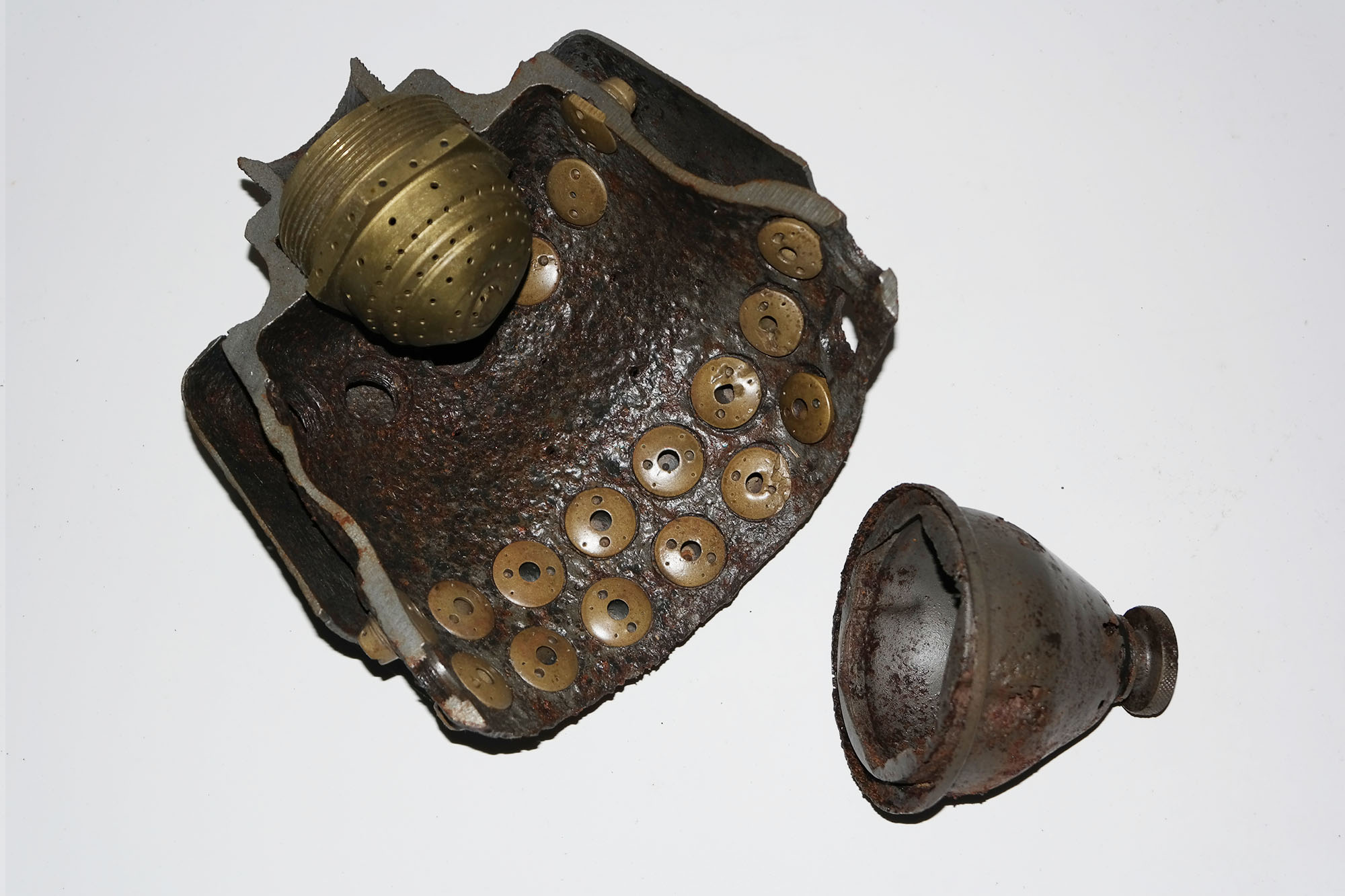
V2 Rocket History Museum Relic: This cutaway presentation shows one of the V2’s 18 combined fuel and liquid oxygen (LOX) injector ‘pots’. The LOX injector transit cap is also shown. The pot shown here is sometimes incorrectly referred to as a pre-burner or pre chamber – a mixer or diffuser pot probably describes its role more accurately.
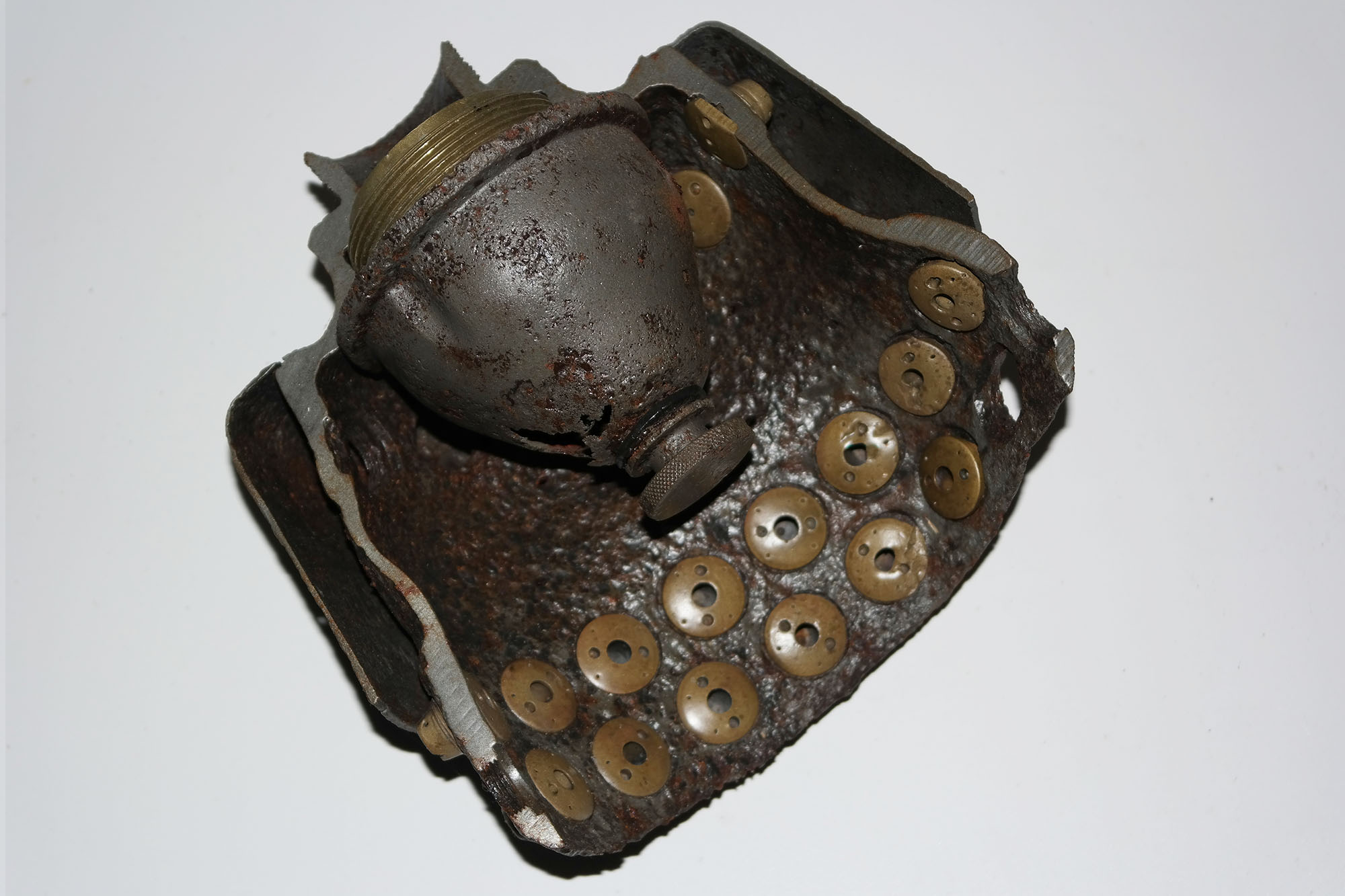
This relic from the V2 Rocket History collection shows a cutaway presentation of one of the V2’s 18 combined fuel and liquid oxygen (LOX) injector ‘pots’. The LOX injector transit cap is also shown fitted over the LOX injector.
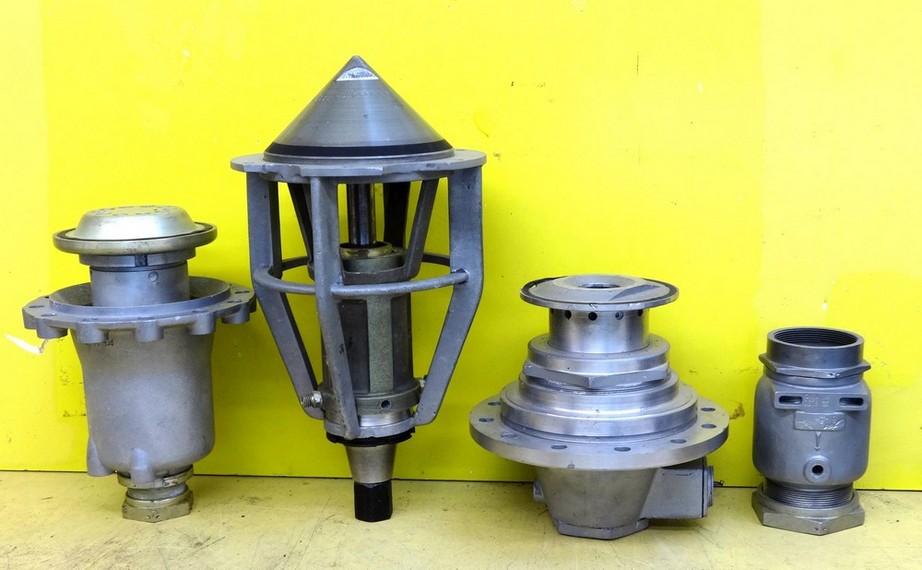
Photo shows main valves. Photo copyright: The Horst Beck Collection
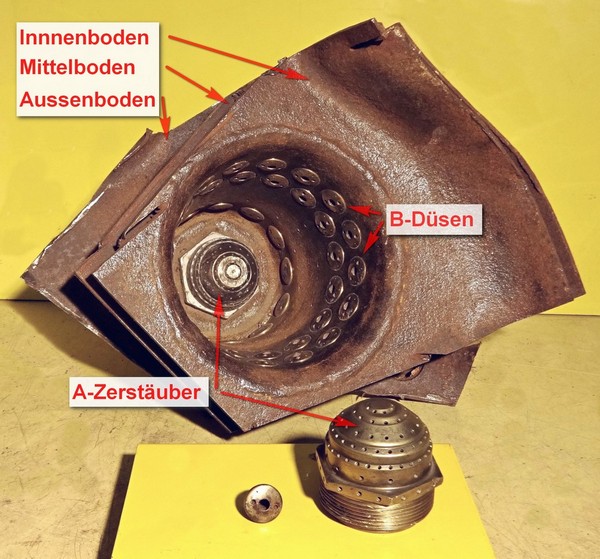
One of the V2’s 18 injector pots showing fuel and LOX injector copper alloy inserts. The spray head A is for liquid oxygen (LOX) and the numerous small injectors lining the chamber are for the fuel. The term pre-chamber is a throw-back to a time when combustion systems developed at the Kummersdorf test facility had a closed structure rather than the open bucket design seen here. Image Horst Beck Collection
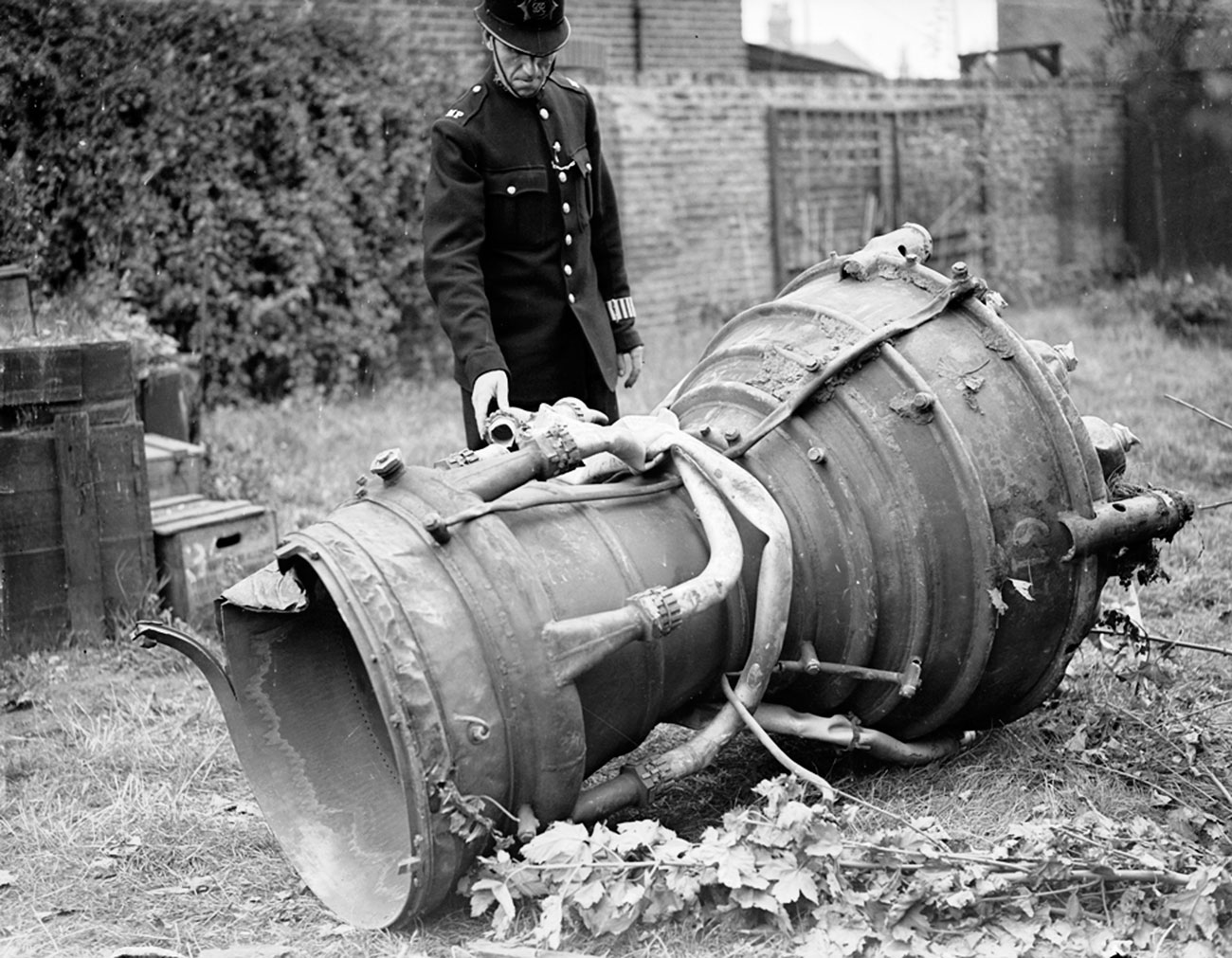
V2 engine part from a missile fired from Walcheren, Serooskerke, Vrederust, by battery no 444, at around 7am on September 17th 1944. The missile impacted East Ham with a direct hit on houses. Killing 6 people with 15 seriously injured. Much of the rocket debris was taken to the East Ham police station for examination by the military authorities. Information porovided by www.v2rocket.com.
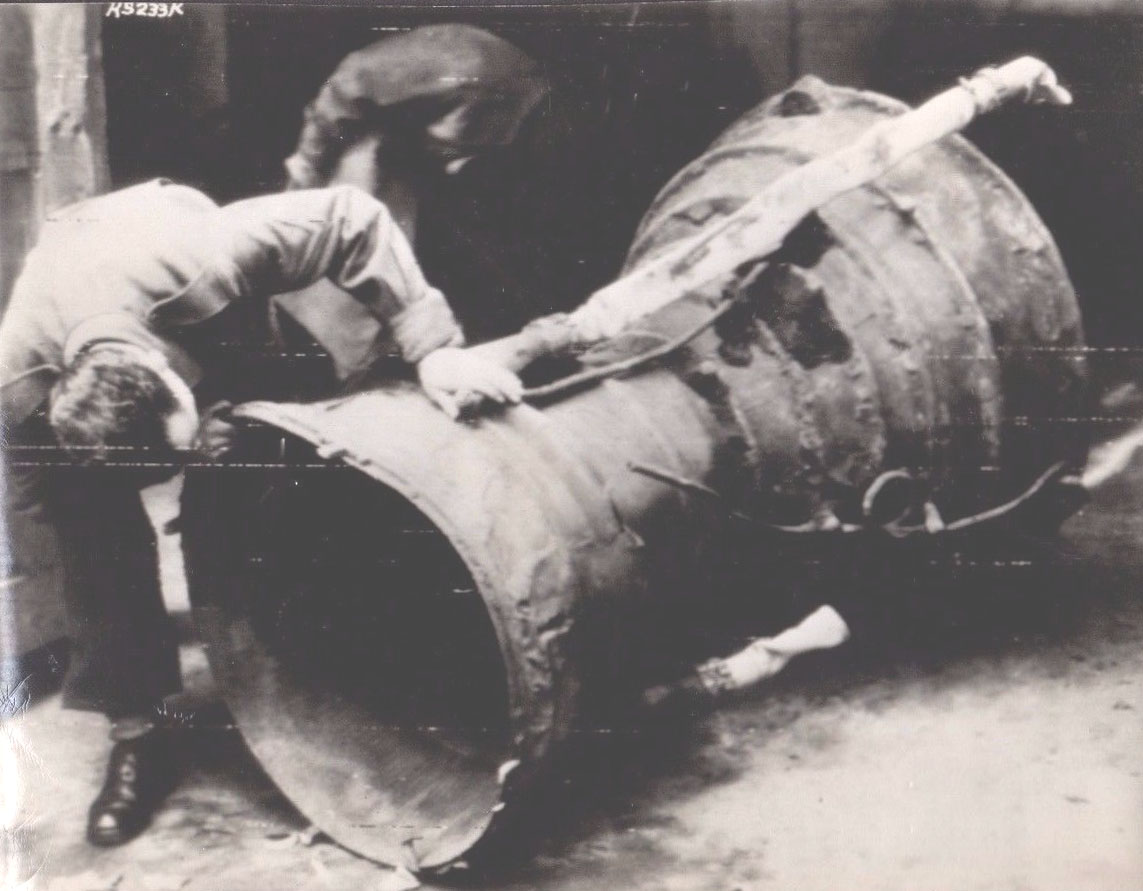
Examination of V2 missile thrust chamber. Sections of two of the large bore aluminium alcohol inlet manifold feed pipes and two thin steel veil colling supply pipes are still attached. The distinctive heat expansion relief loop can be seen on one of the pipes.
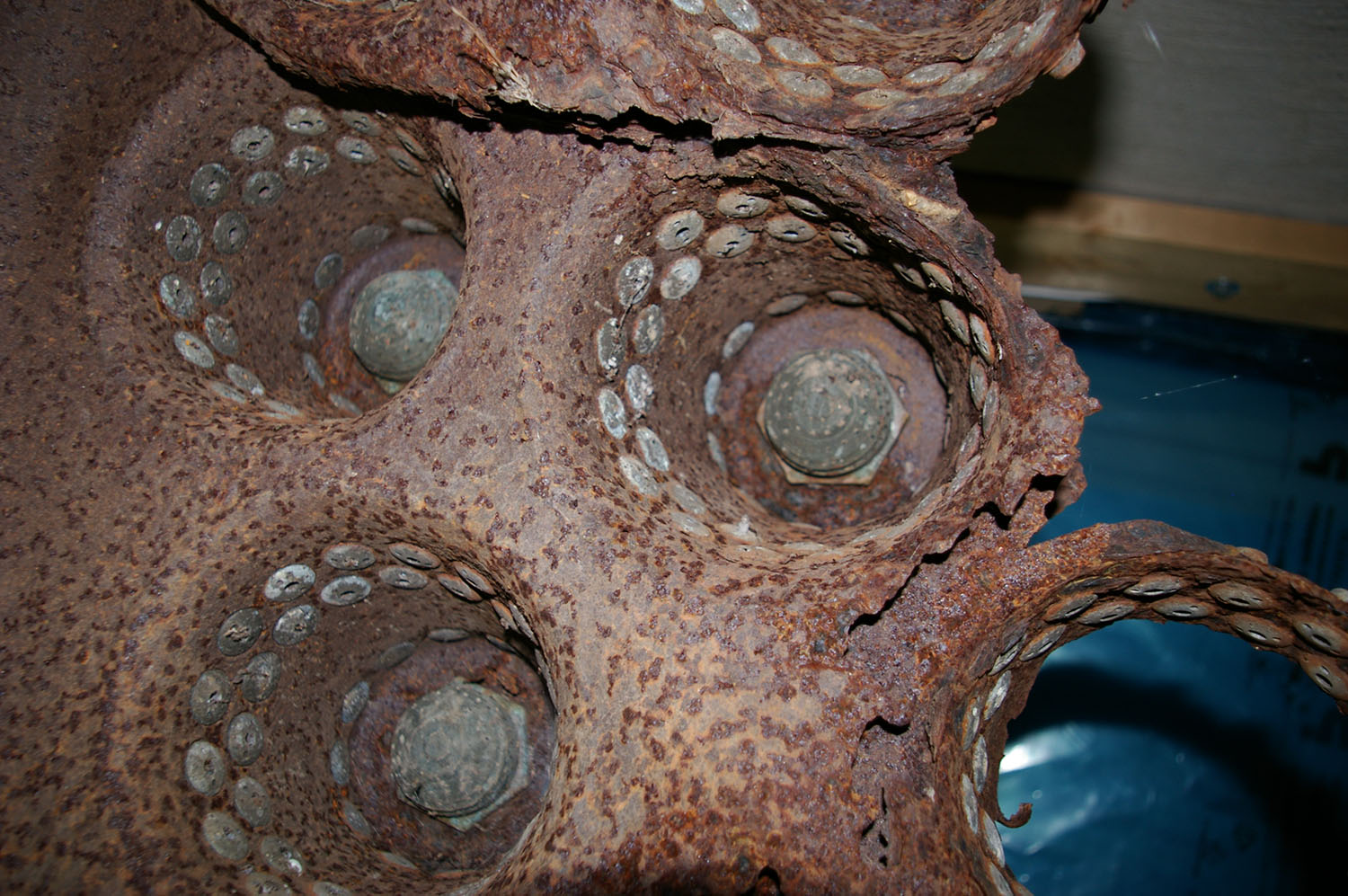
Image shows interior of production series (combat relic) V2 missile propellent injector pre-mixer pots. Three post in the picture are intact, others seem in the picture have been destroyed in the impact. This engine part was recovered from a combat impact East of London. Impact date: February 1945

Testing fuel injectors
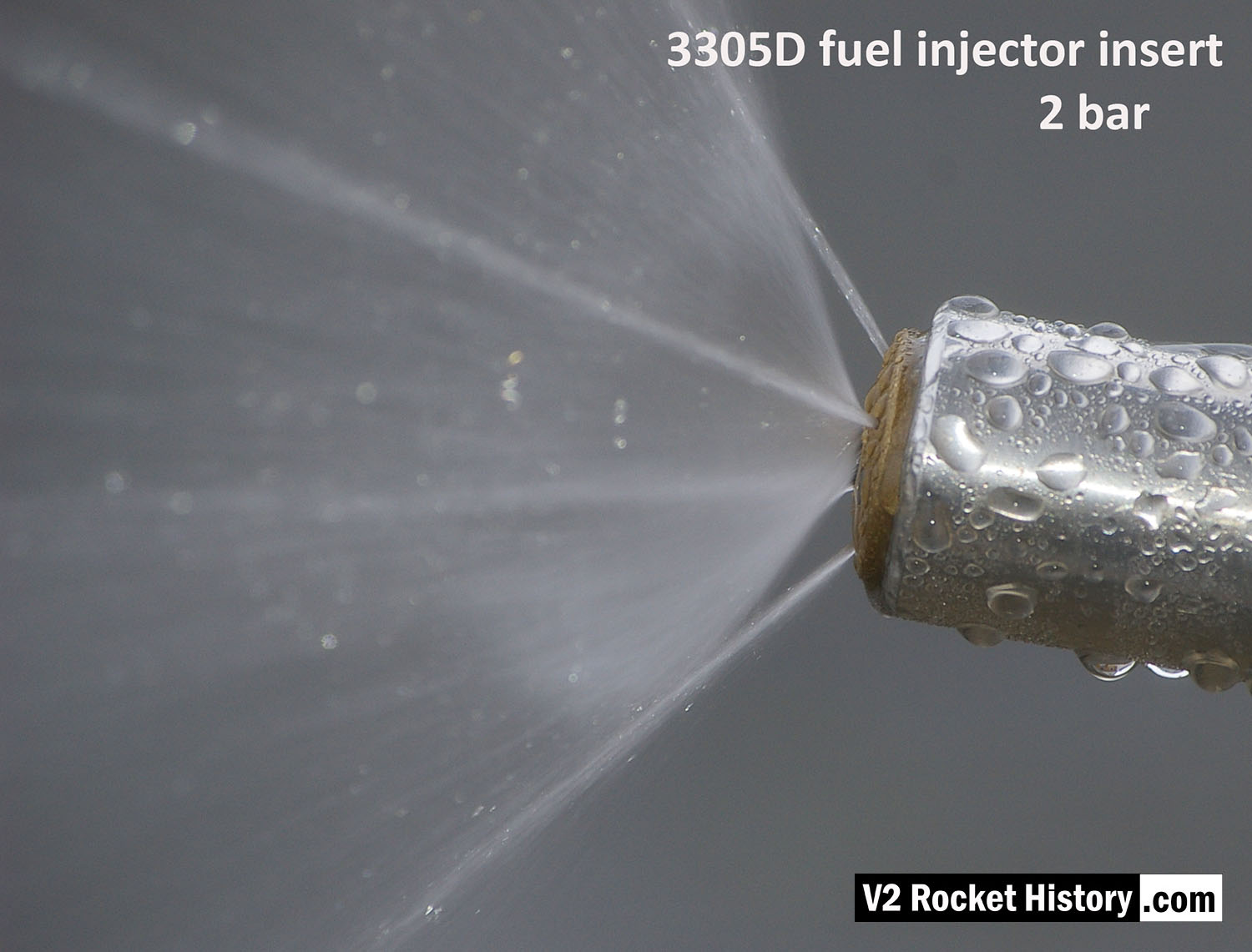
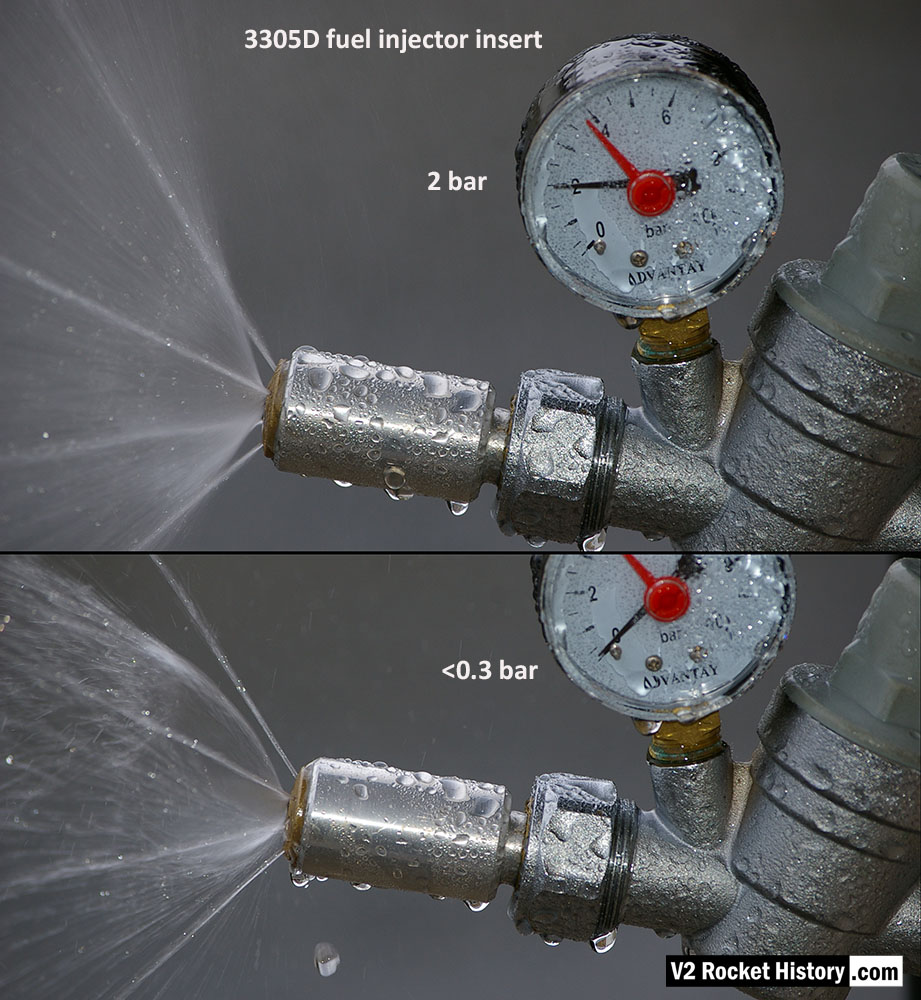
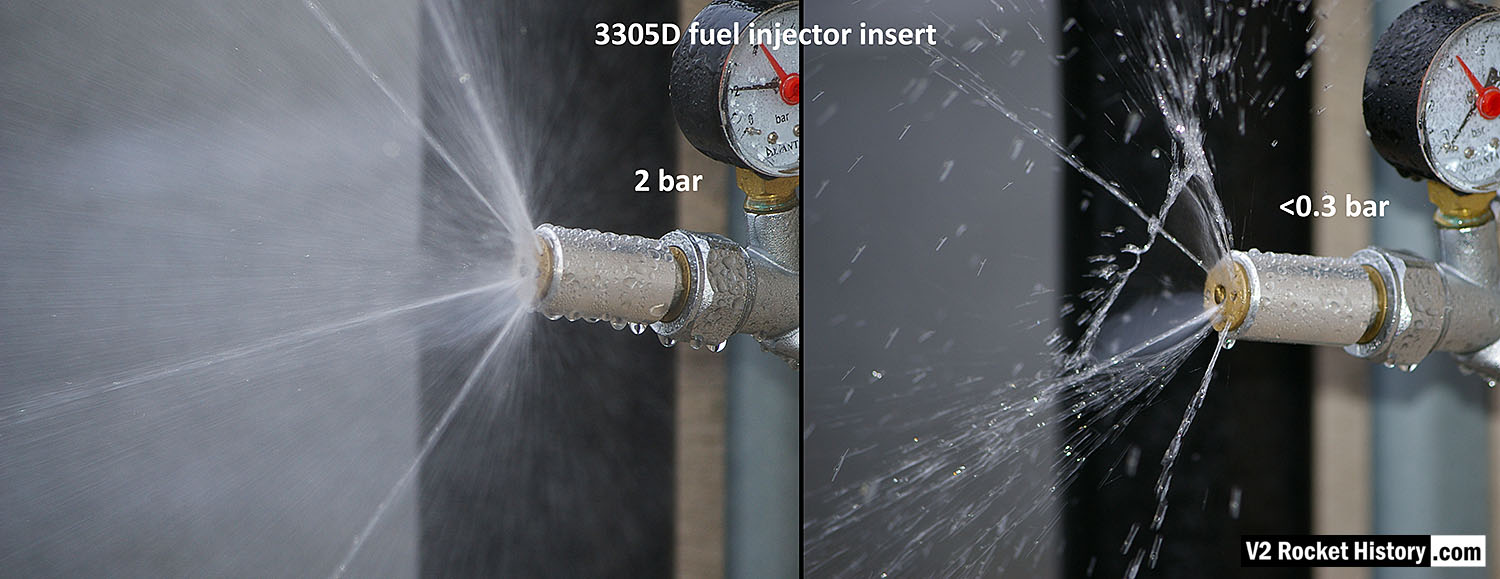
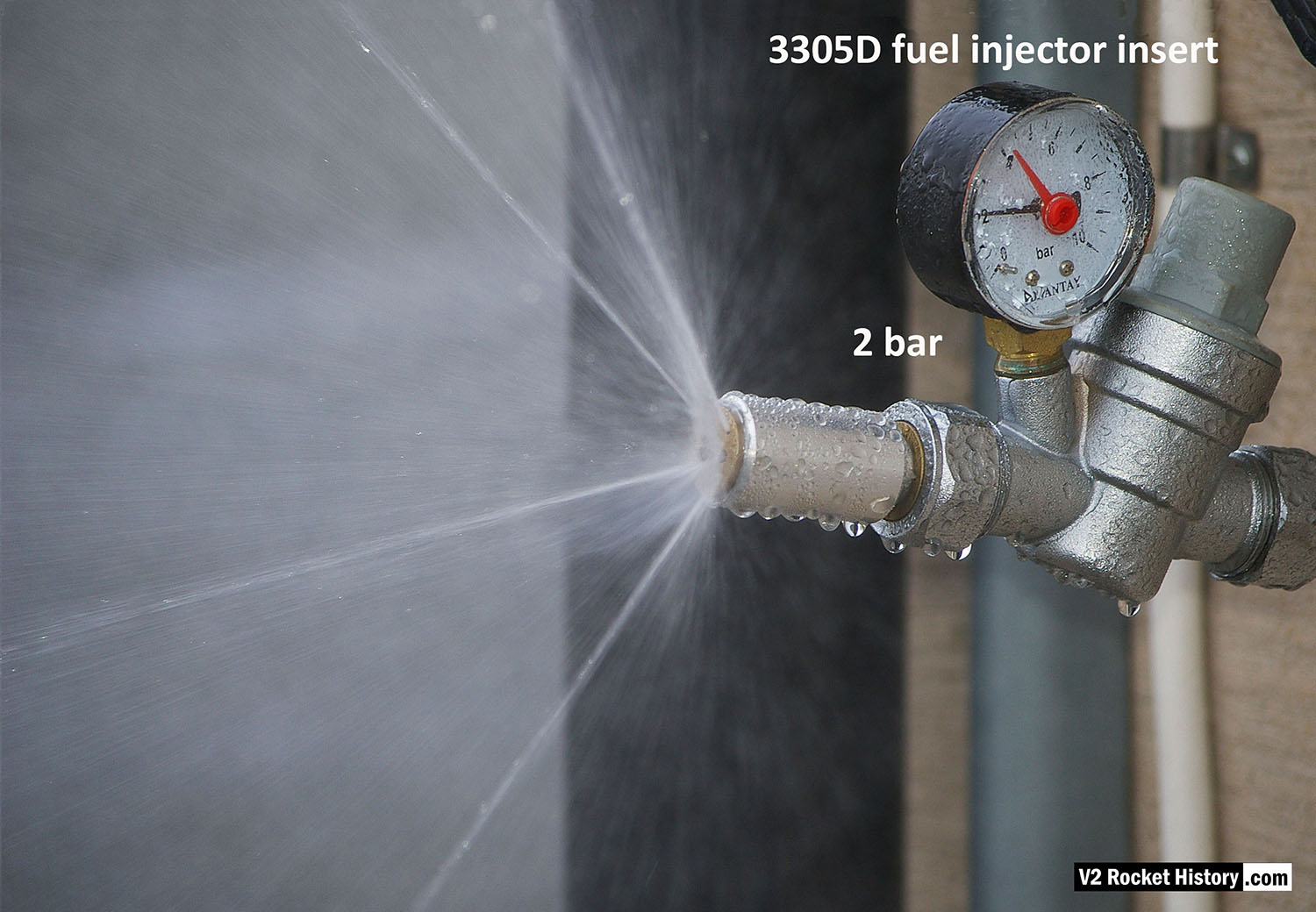

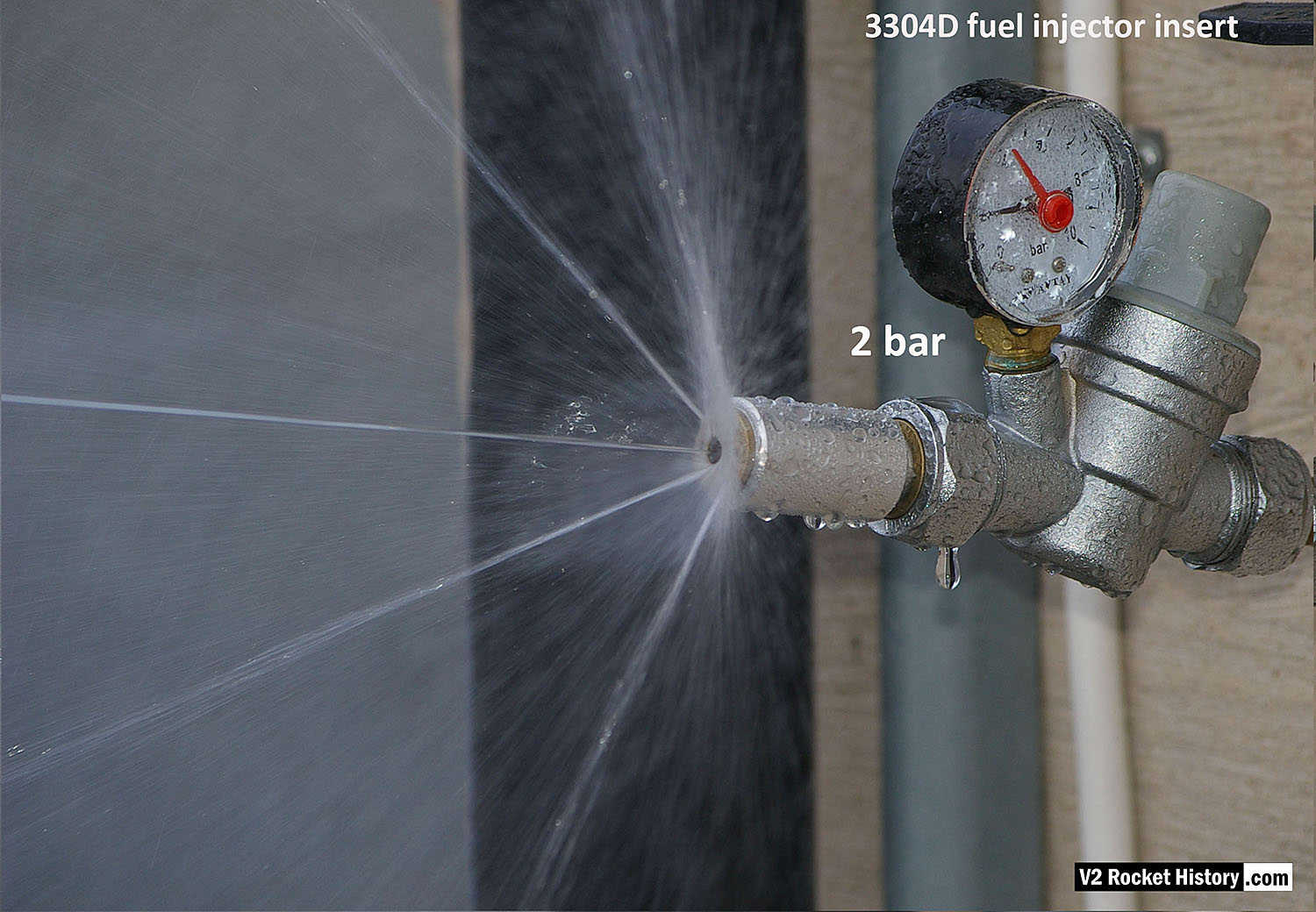
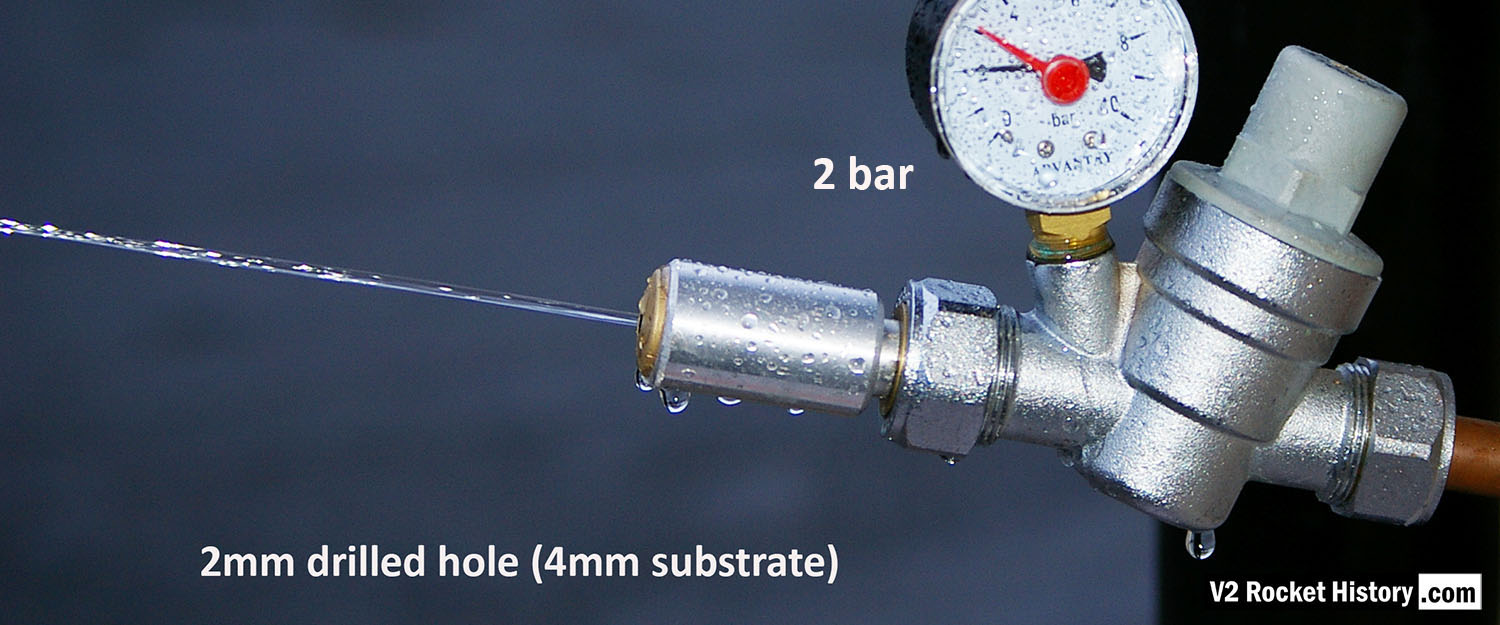
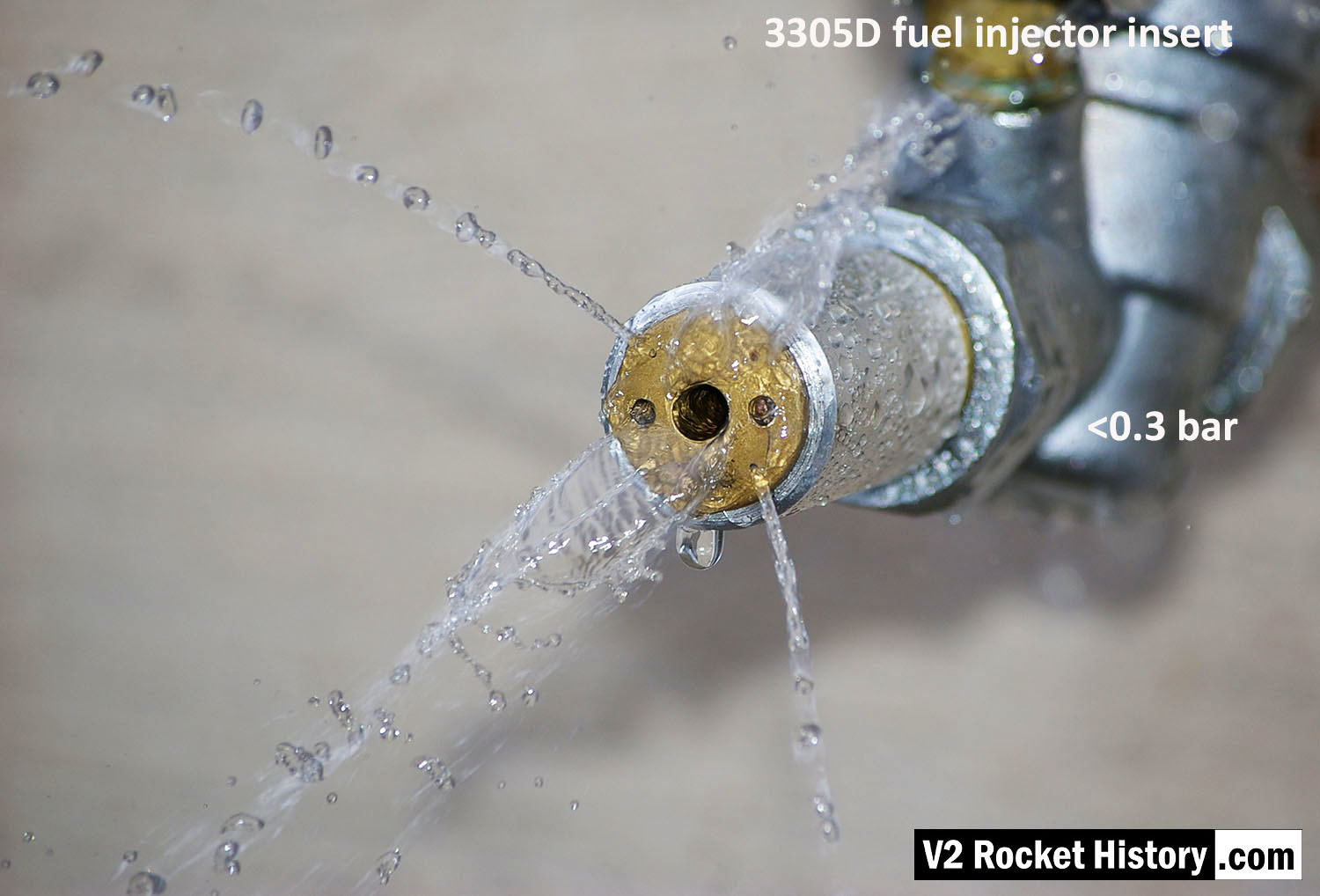
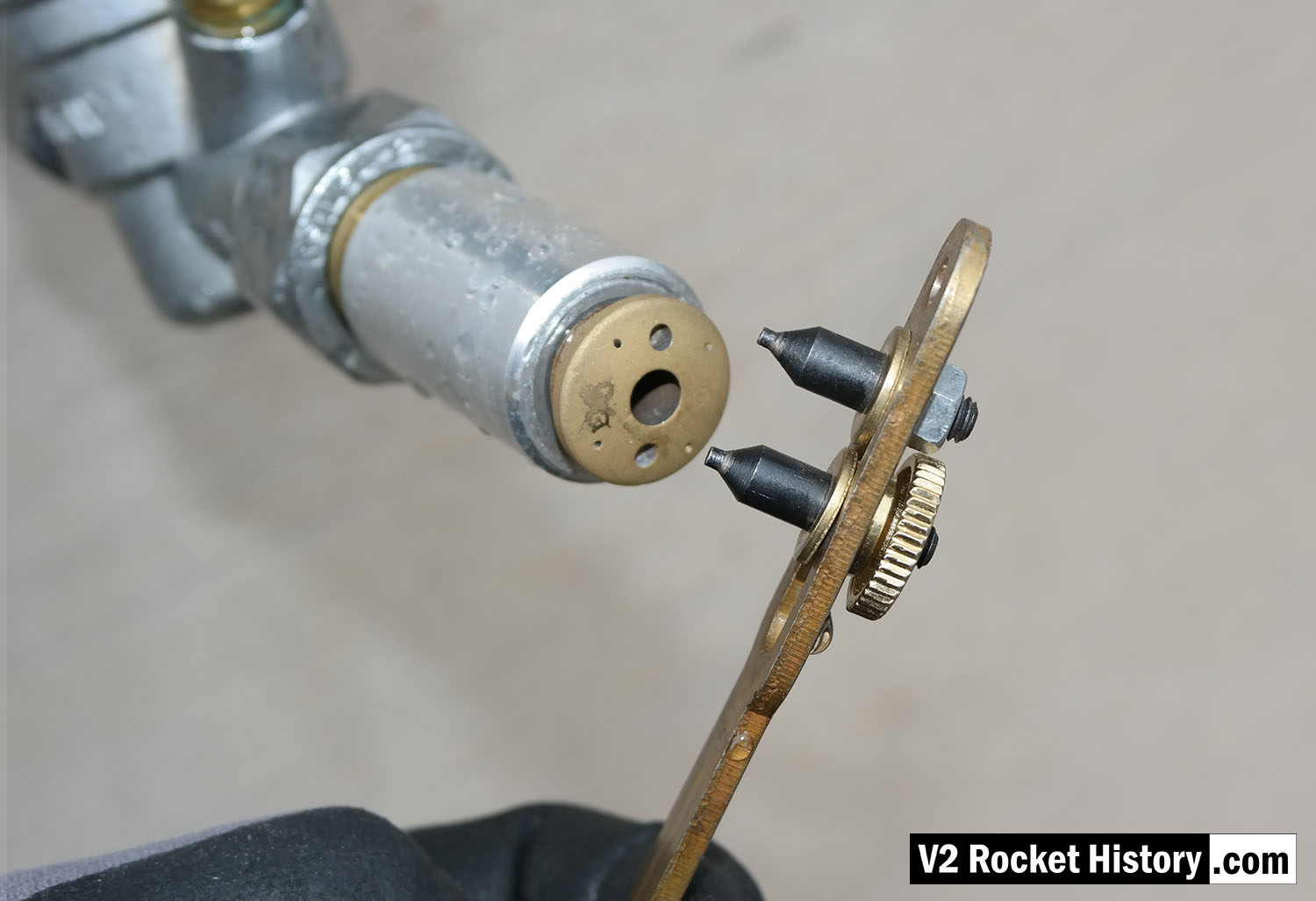
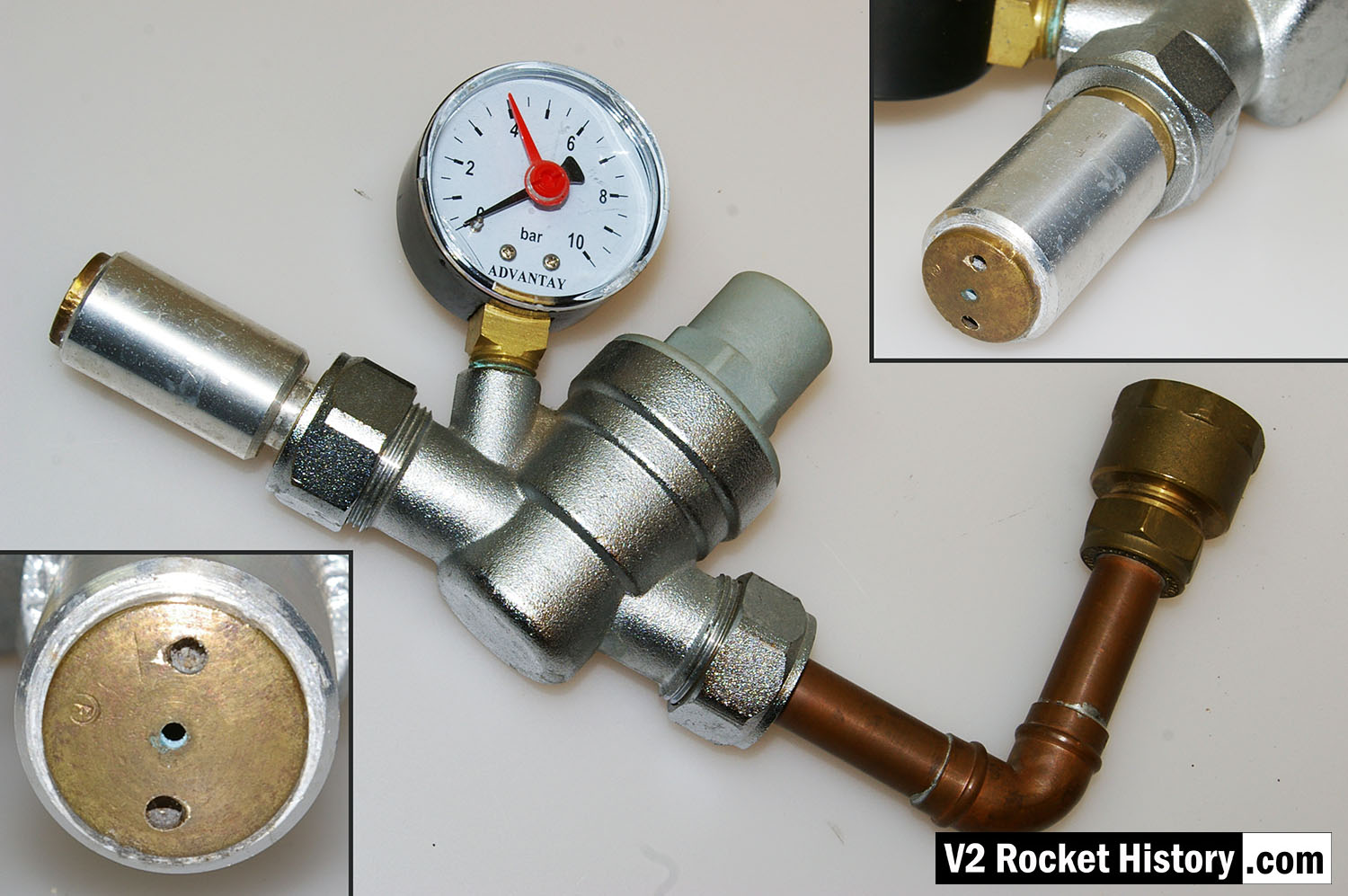



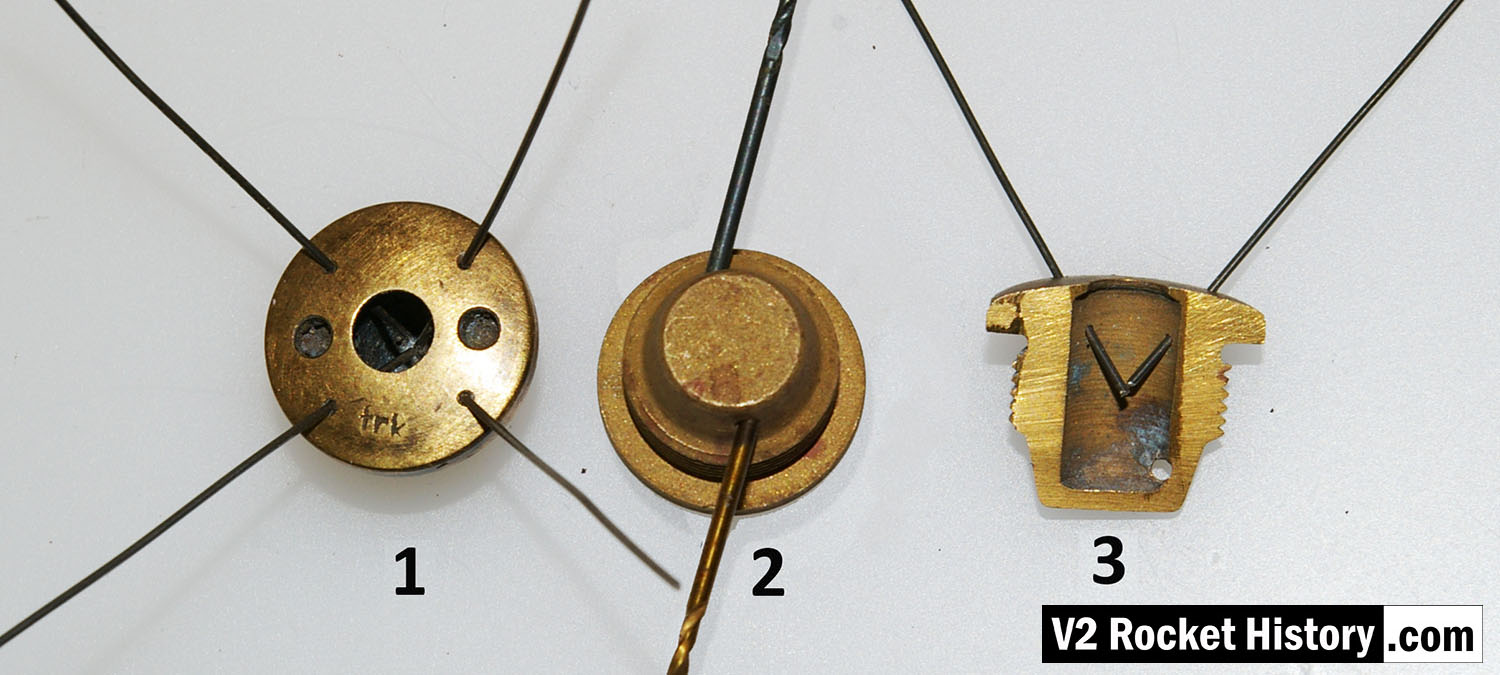
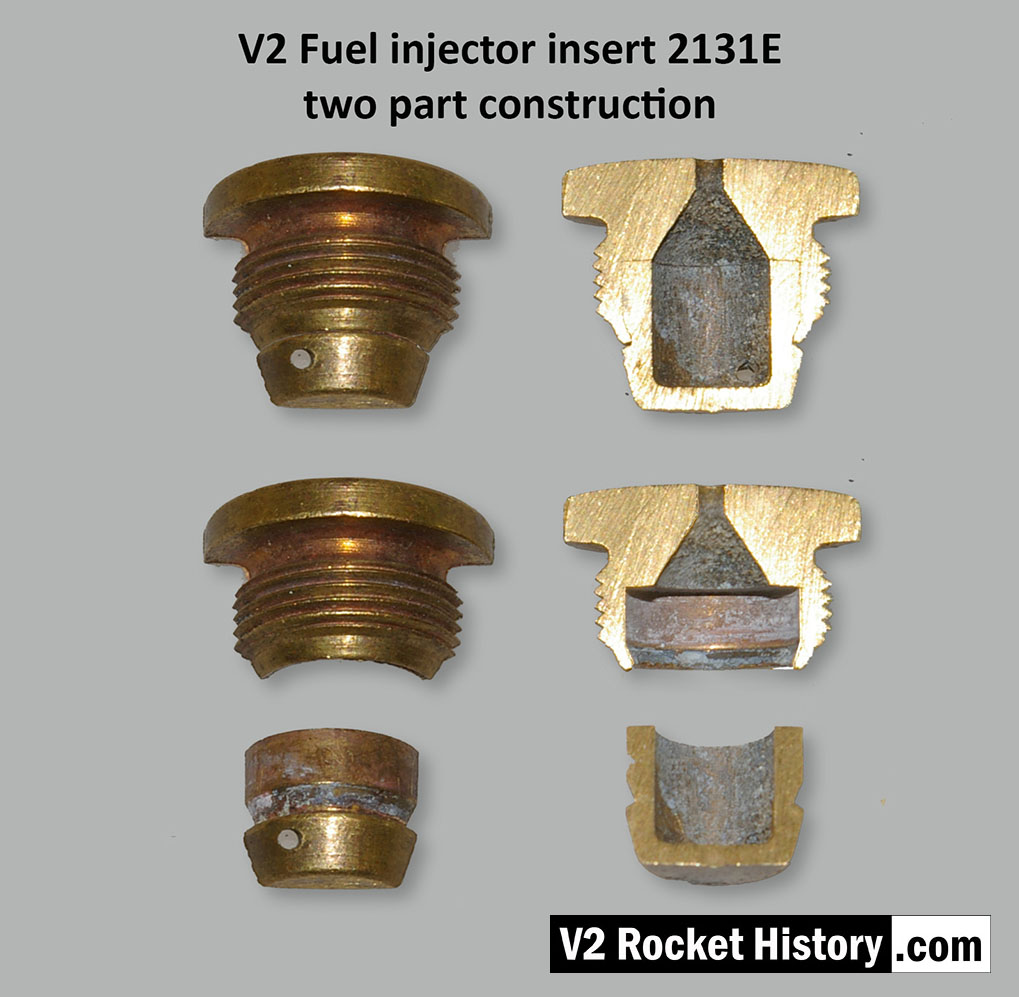
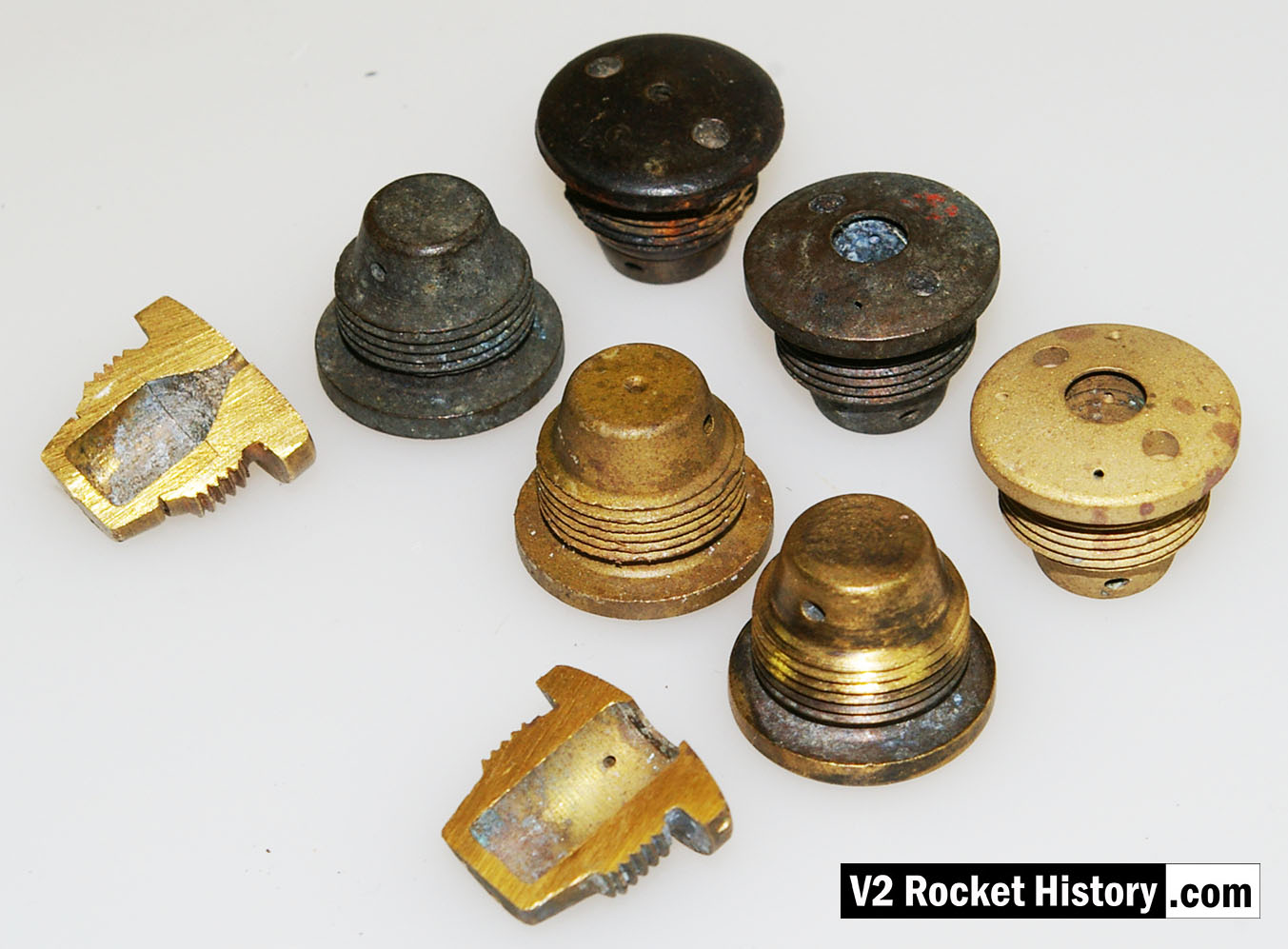
Image shows a correctly formed nebular cone attended by a fine mist. the four injector cooling jets are well shown, and although fluid beading can be seen on the face of the injector, there is insufficient liquid to cause dripping.