
Archives: Gmedia Albums


Turbopump 3D CAD
3D CAD model images of the A4/V2 rocket engine’s steam turbine powered propellent pumps – all images by Ray Matter. To see Ray Matter’s blog 3D CAD modelling the V2 rocket turbopump introducing these images, just click the link.
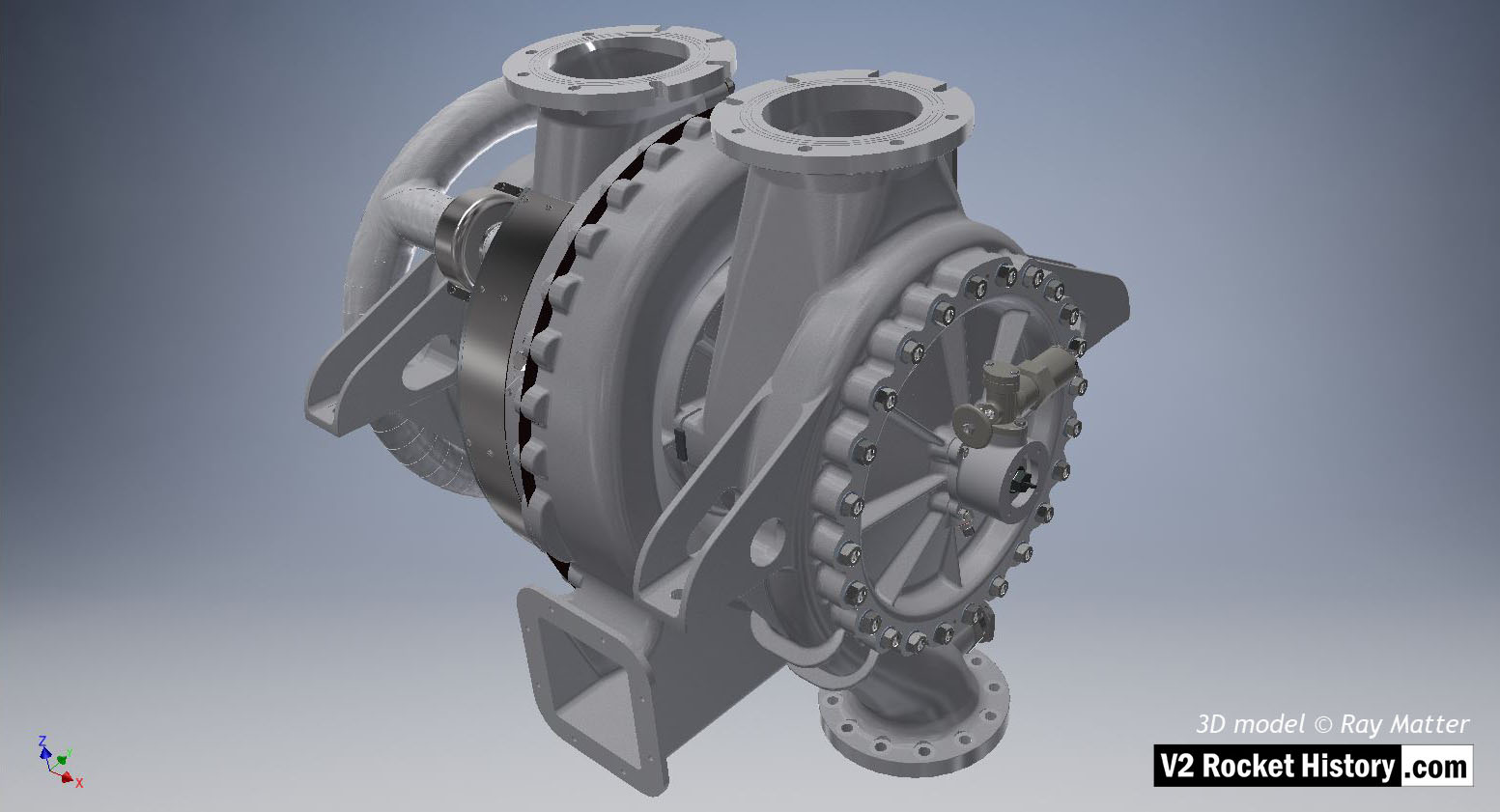
Turbine powered propellant pumps for A4/V2 rocket engine – fuel pump on right. Full perspective assembly showing tubular ring steam inlet manifold with asbestos bandage extreme left, inlet flanges at top, frame support brackets, steam exhaust outlet square shape lower center. The overspeed trip switch can be seen just above center on fuel pump face plate. The fuel outlet flange can also been seen btm right of center. 3D model by Ray Matter
Album | Turbopump 3D CAD |
Category | Turbo-pump |
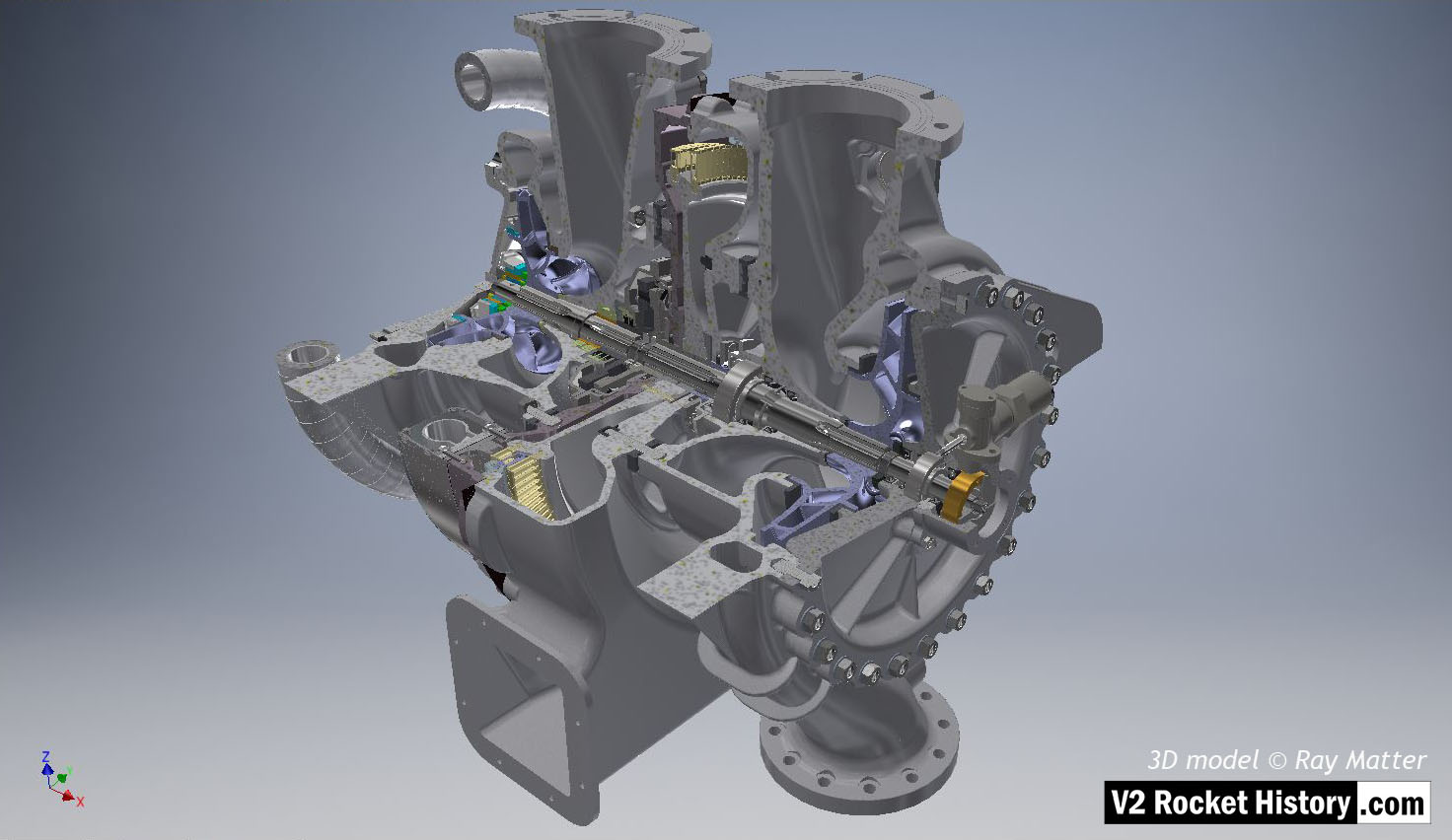
Turbine powered propellant pumps for A4/V2 rocket engine – fuel pump on right. Full assembly showing steam inlet manifold on left, inlet flanges at top, support brackets, steam exhaust outlet square shape lower center. The over-speed trip switch can be seen just above center on fuel pump face plate. The fuel outlet flange can also been seen btm right of center. 3D model by Ray Matter
Album | Turbopump 3D CAD |
Category | Turbo-pump |
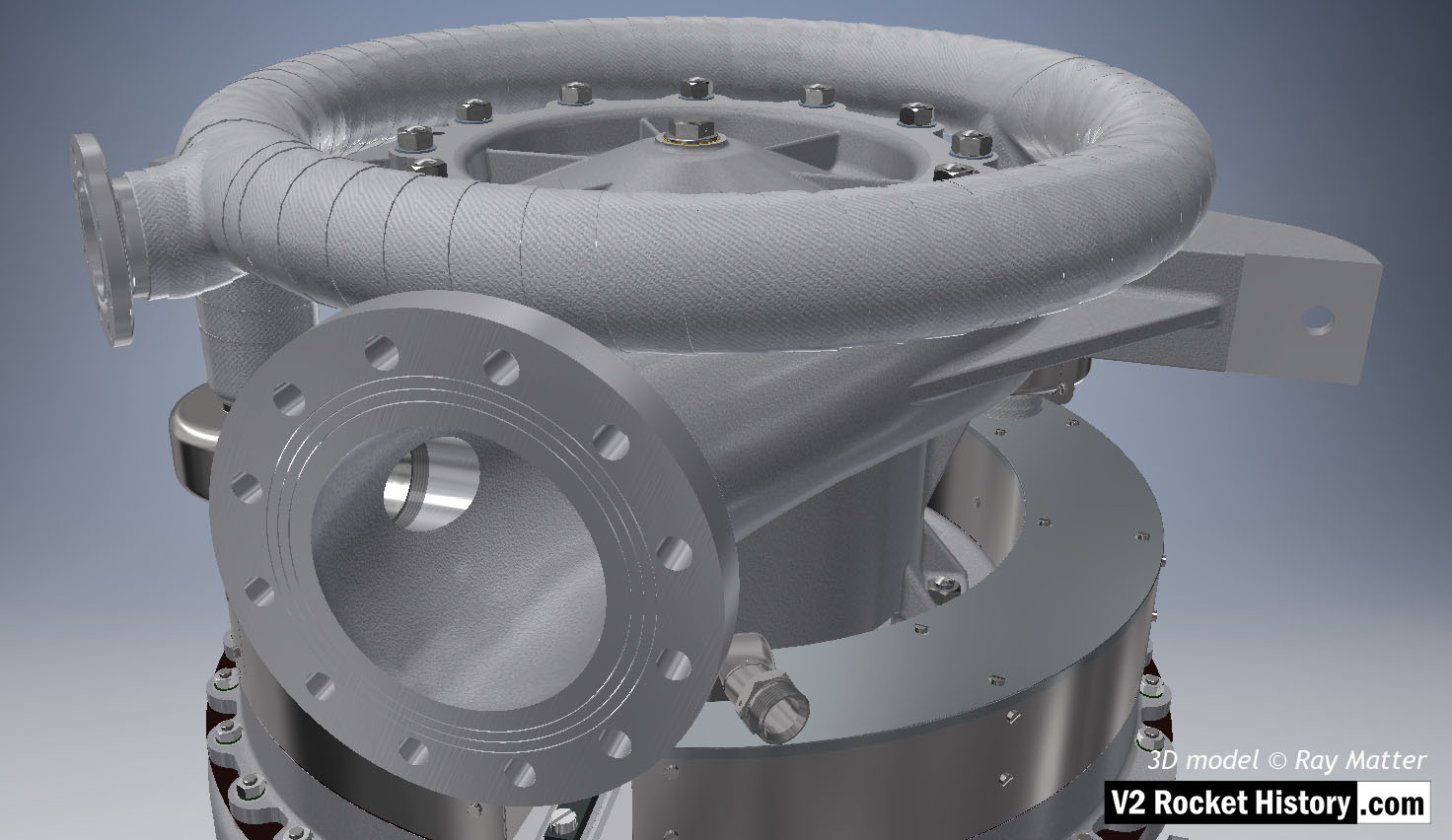
Full assembly showing, from top, steam inlet ring manifold, LOX pump and portion of steam turbine assembly. View shows outlet flange facing camera. Note the three fine rings milled into flange face. The rings were designed to improve keying for the sealing ‘putty’ that was used to seal the connection between the flange face and the inlet pipe. 3D model Ray Matter
Album | Turbopump 3D CAD |
Category | Turbo-pump |
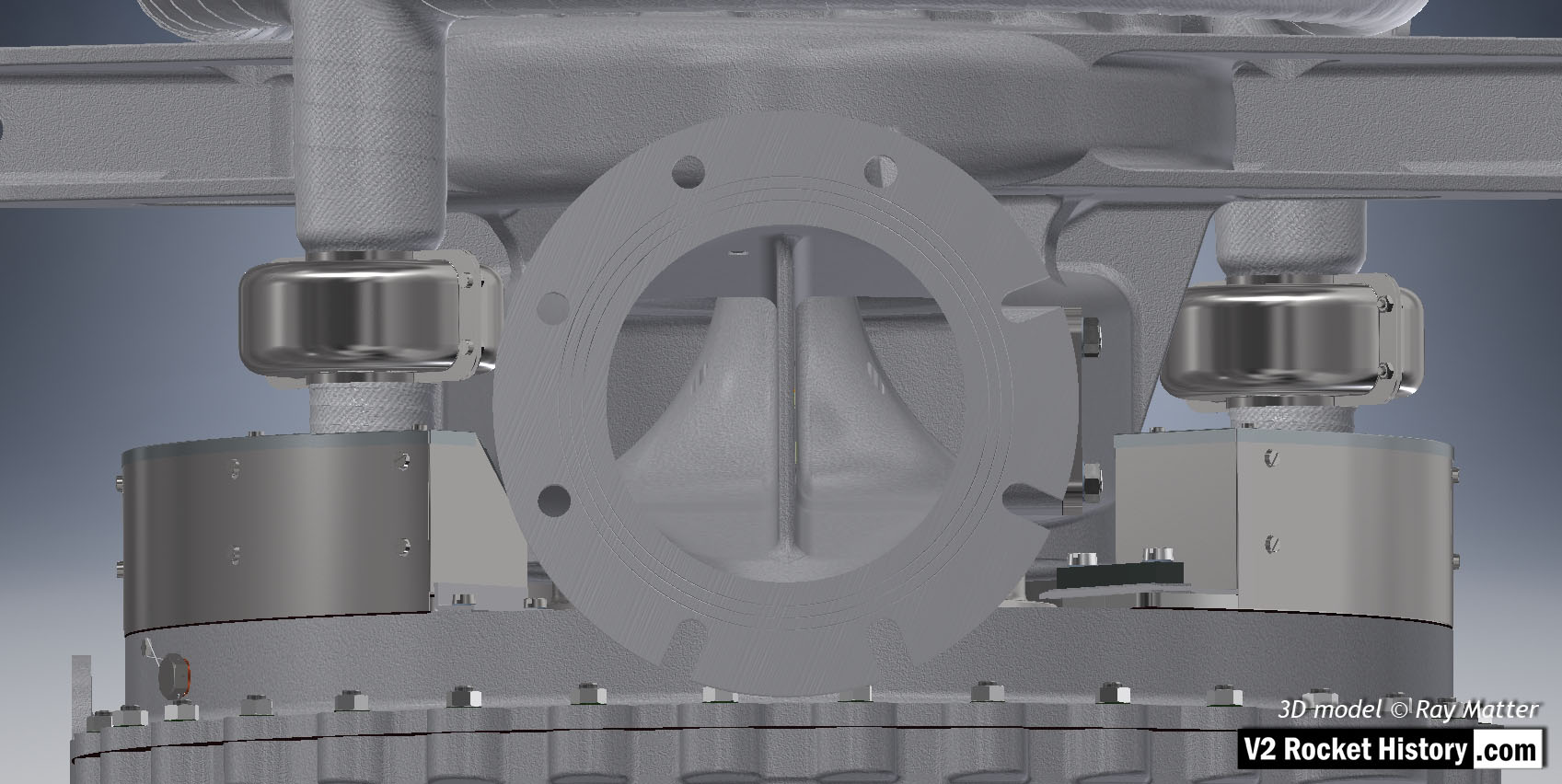
A (LOX) Pump close-up showing inlet flange, with fastener slots and holes, as well as the throat baffle. To the right and left of the flange, the steam inlets are shown – with steel cases covering the steam manifold connection flanges. Of special note in this view is the self-purge orifice seen at the top right-hand side of the inlet throat baffle. This hole allowed gas to escape from the top of the LOX volute space back to the low-pressure inlet throat and proved problematic in manufacturing and was revised in late 1944. 3D model Ray Matter
Album | Turbopump 3D CAD |
Category | Turbo-pump |
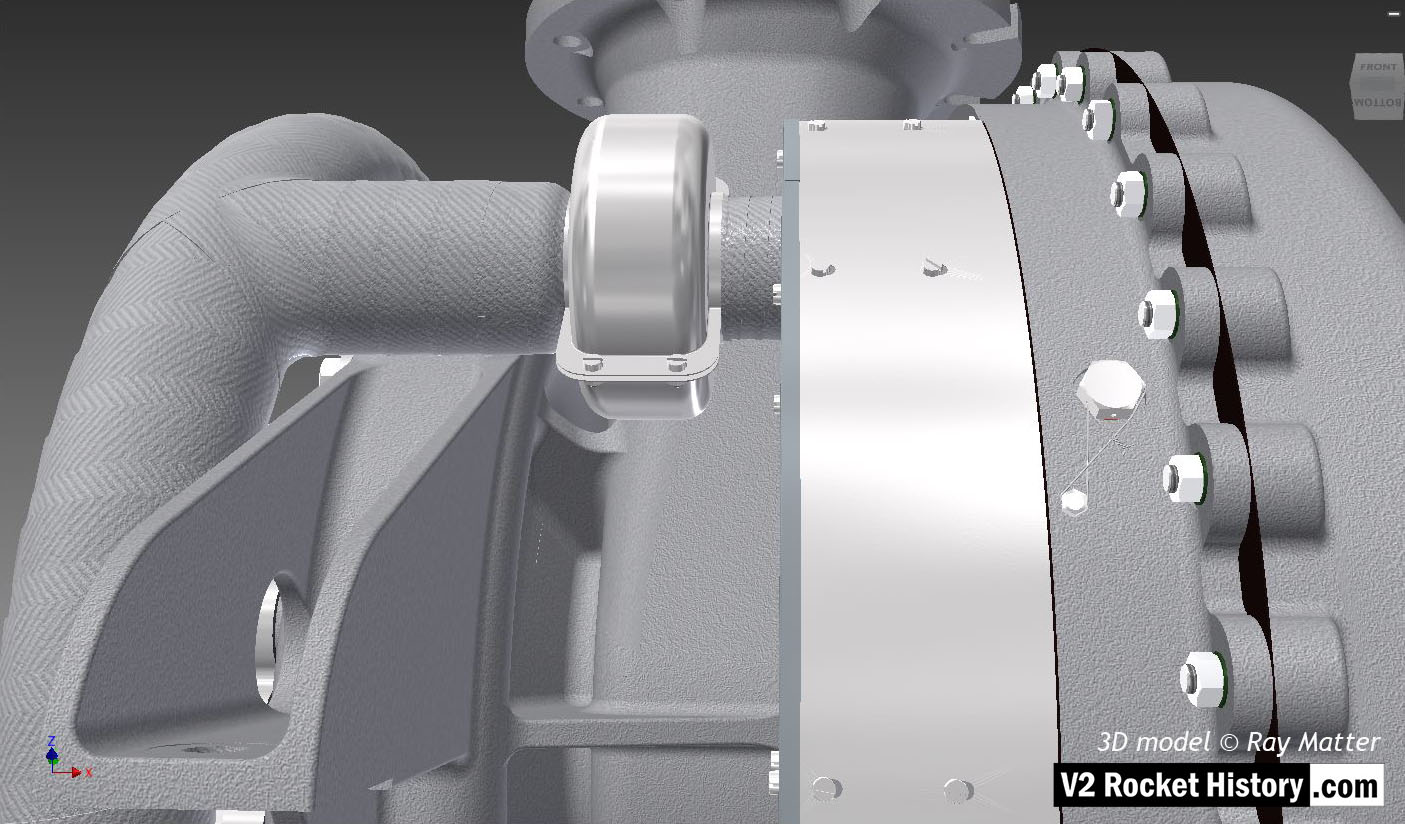
Close-up of turbine steam inlet ring manifold showing one of the entry points. The thin steel case that fits around the steam manifold mating flanges is clearly shown as is the wire restraint fastener locking system (see close-up in gallery). 3D model by Ray Matter
Album | Turbopump 3D CAD |
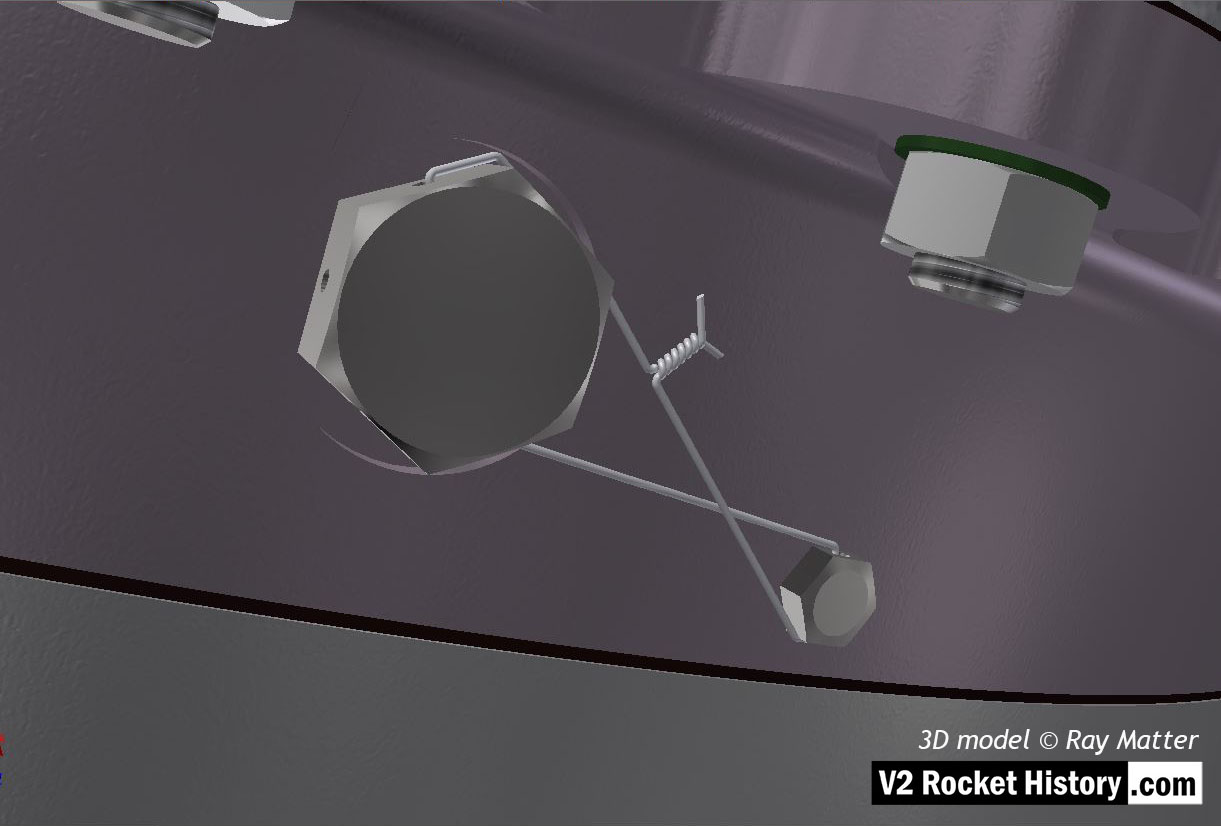
Turbine powered propellant pumps for A4/V2 rocket engine – close-up of turbine casing shows wire restraint fastener locking system. 3D model by Ray Matter
Album | Turbopump 3D CAD |
Category | Turbo-pump |
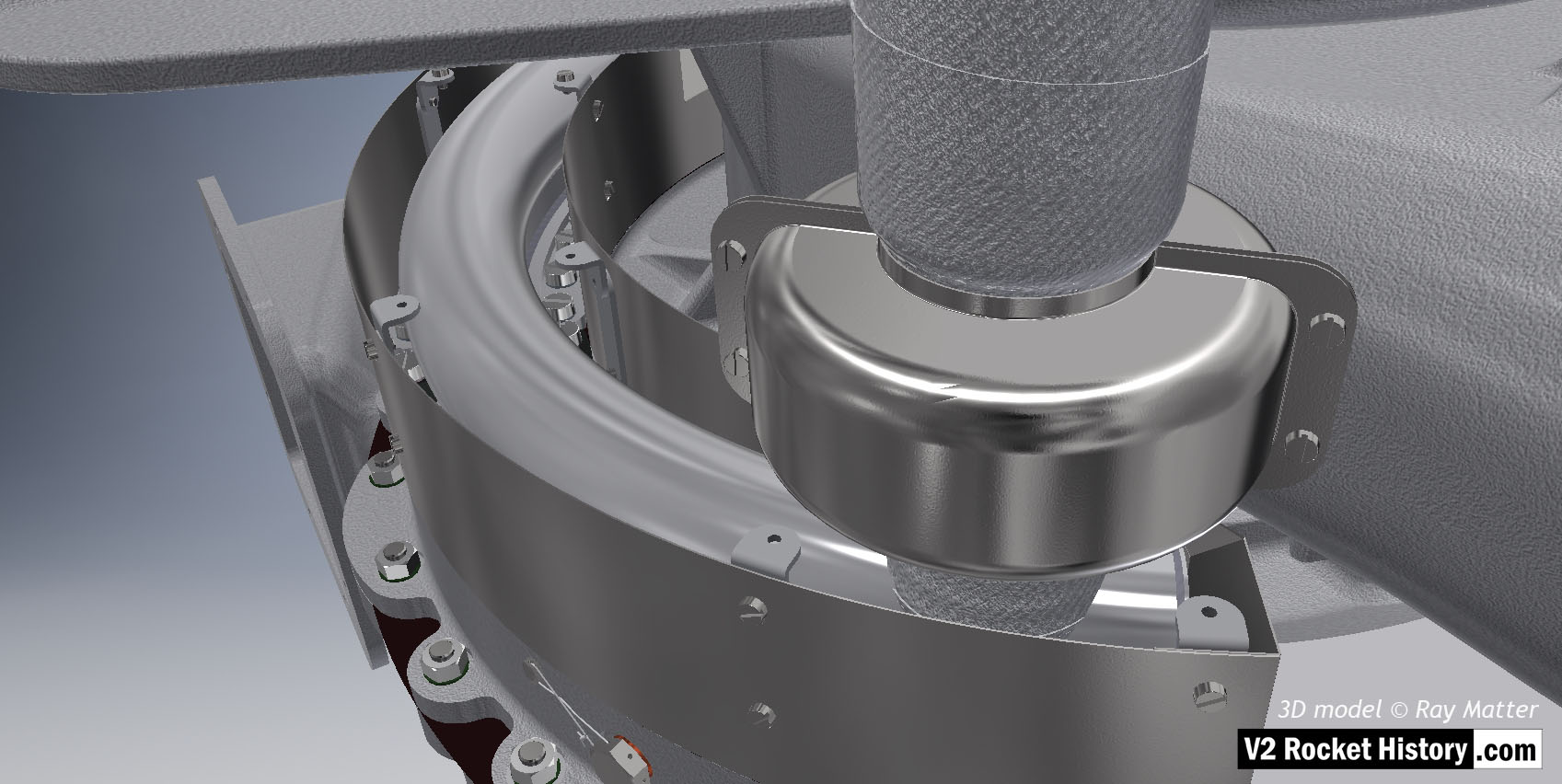
Close-up of turbine showing steel case with lid removed to show steam inlet ring manifold. The thin steel case that fits around the steam manifold mating flanges is clearly shown as is the wire restraint fastener locking system (see close-up in gallery). 3D model by Ray Matter
Album | Turbopump 3D CAD |
Category | Turbo-pump |
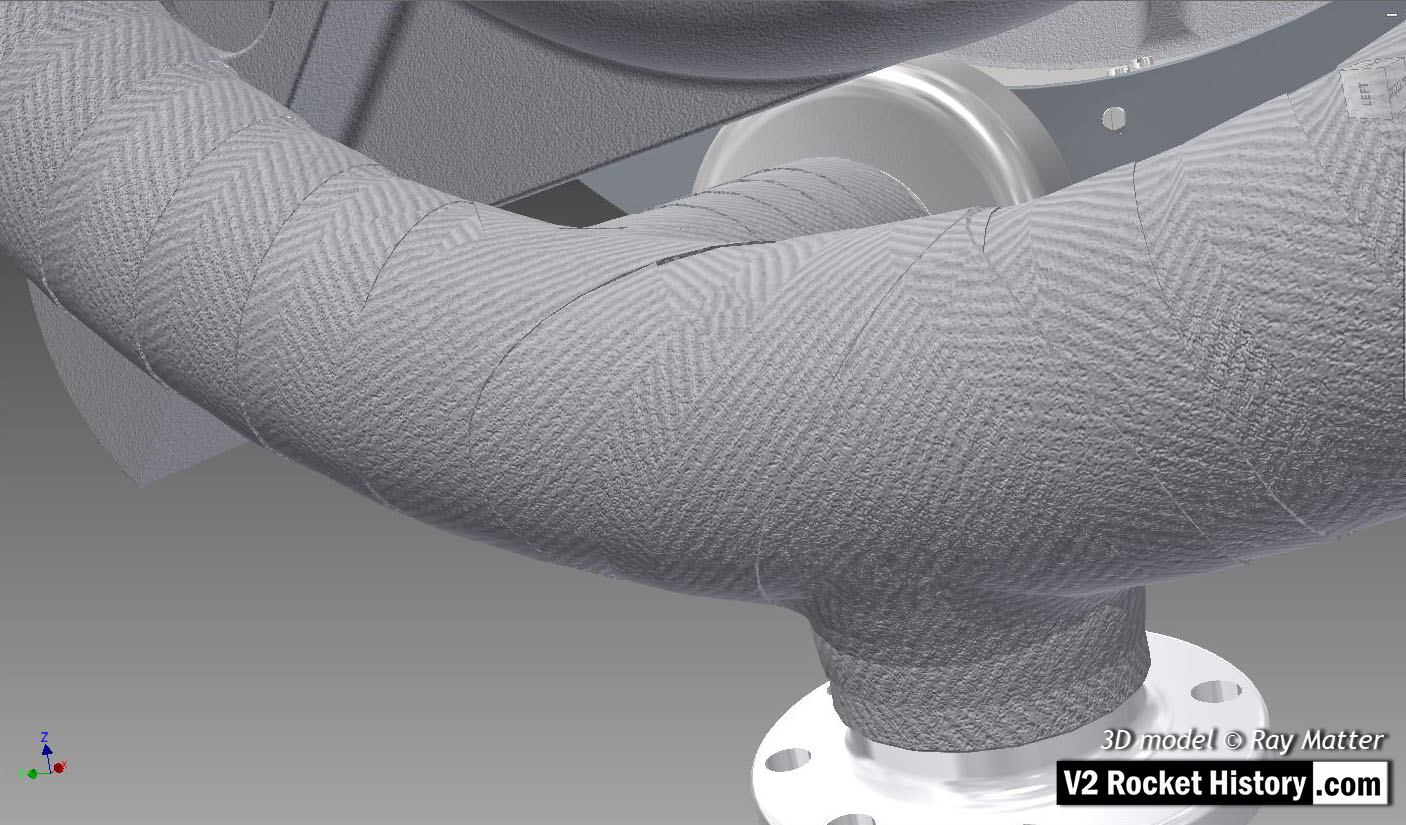
Close-up of turbine steam inlet ring manifold showing asbestos bandage wrapped around the tubular ring. Sometimes a thin wire was used to help retail the heat resistant material. This bandage is often missing from museum exhibits. 3D model by Ray Matter
Album | Turbopump 3D CAD |
Category | Turbo-pump |
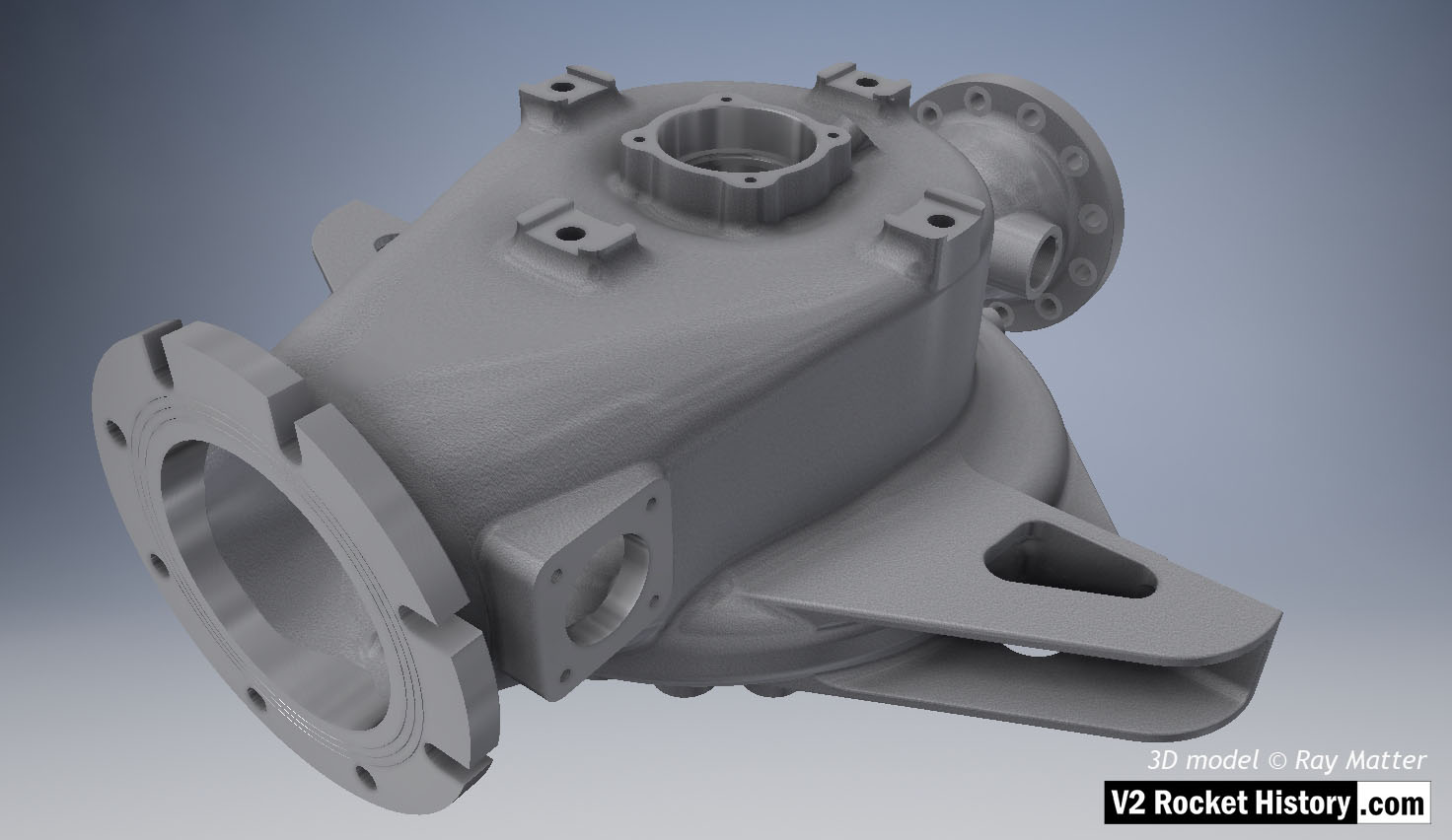
B (fuel) Pump sub-assembly, single piece casting showing machined (milled) areas without fittings. View shows inlet flange fastener slots and the throat aperture – facing right, initially blanked off by square plate, but towards the end of 1944 used for fuel return from the main fuel valve situated in the center of the thrust chamber injection head. 3D model Ray Matter
Album | Turbopump 3D CAD |
Category | Turbo-pump |
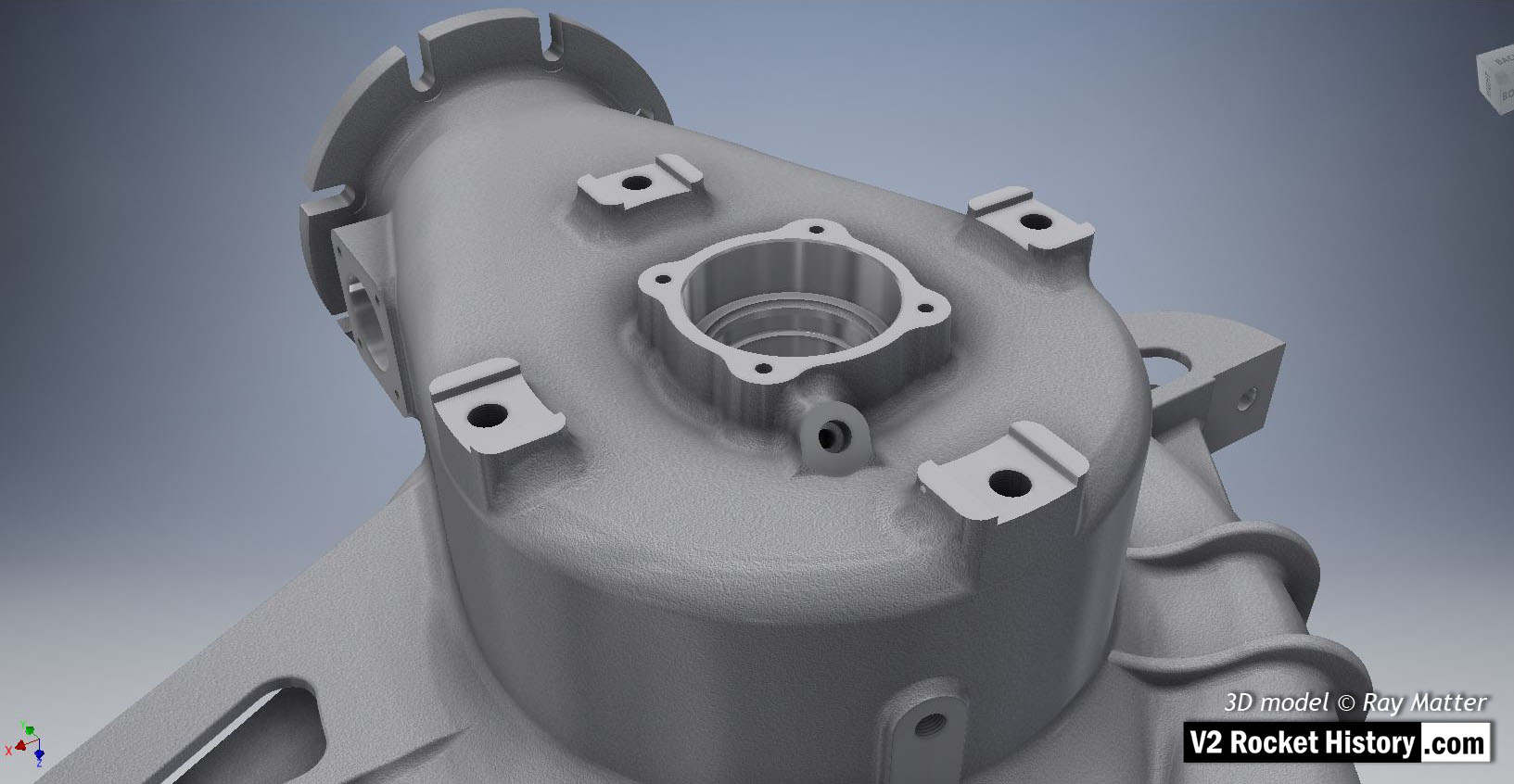
B (fuel) Pump sub-assembly, single piece casting showing machined (milled) areas and without fittings. 3D model Ray Matter
Album | Turbopump 3D CAD |
Category | Turbo-pump |
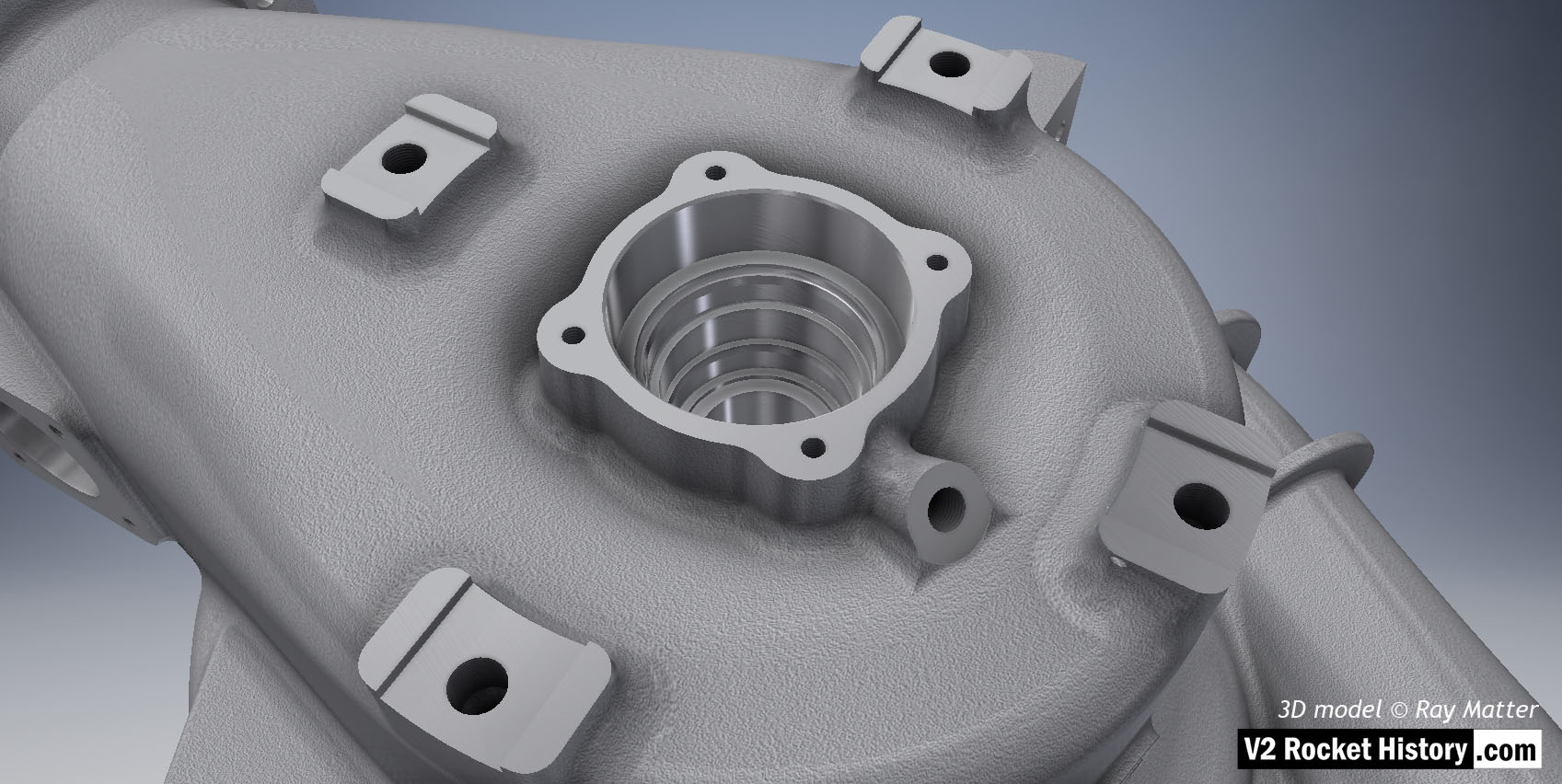
B (fuel) Pump sub-assembly shown without fittings. Single piece casting showing detail of bearing and seal cavity as well as threaded fuel bleed connection. 3D model Ray Matter
Album | Turbopump 3D CAD |
Category | Turbo-pump |
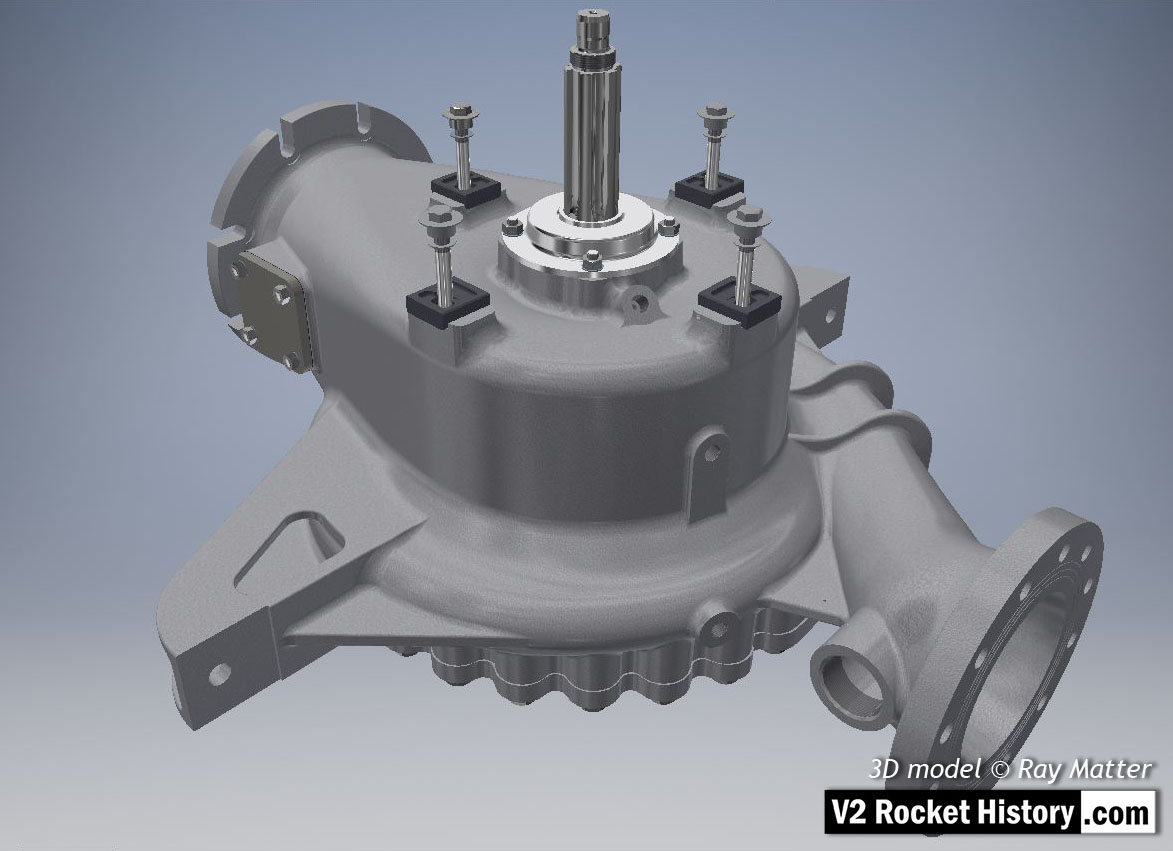
B-Pump sub-assembly, showing earlier version square inlet throat blanking plate (later versions employed a fuel return connection point mounted on this plate).
Fastenings, turbine case contact furniture, splined turbine connection shaft, and shaft seal cap are also shown. 3D model Ray Matter
Album | Turbopump 3D CAD |
Category | Turbo-pump |
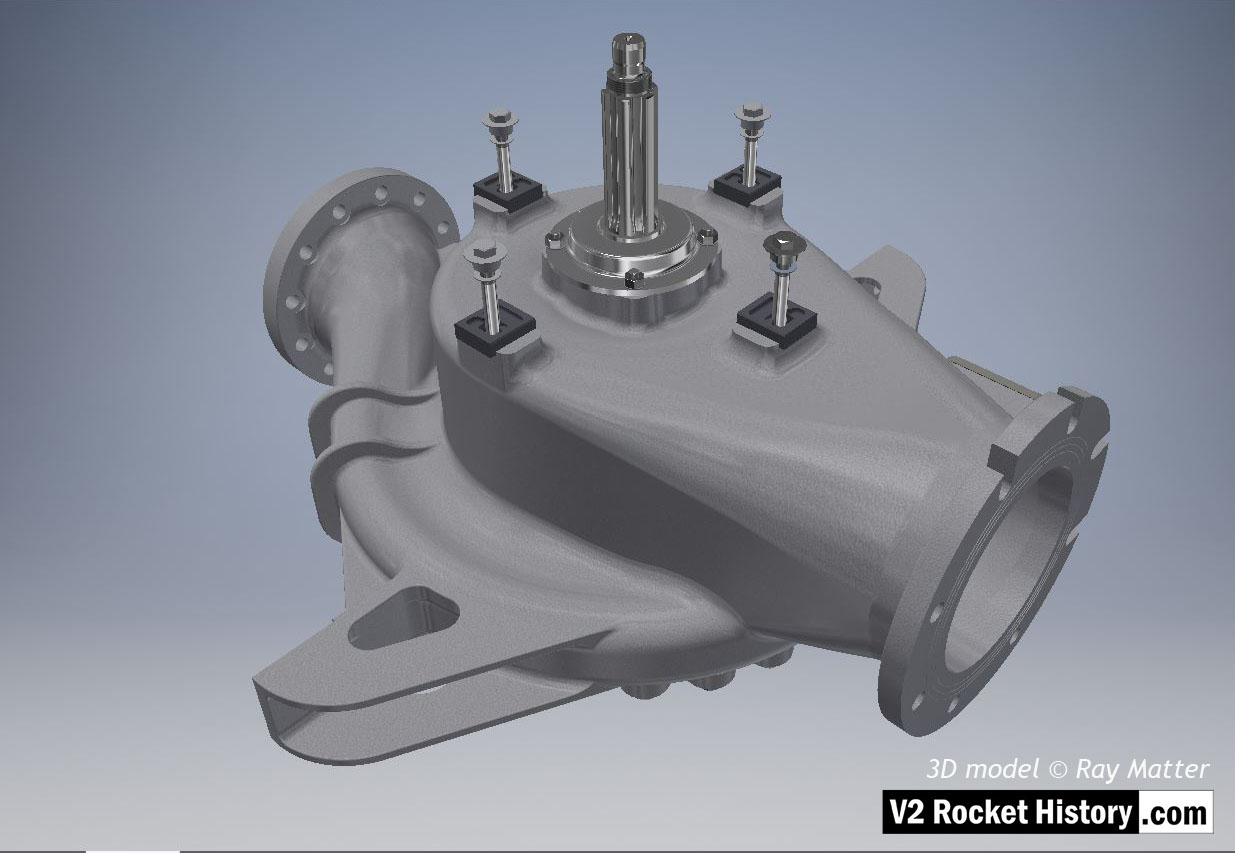
B-Pump sub-assembly complete with fastenings, turbine case contact furniture, splined turbine connection shaft, and shaft seal cap. 3D model Ray Matter
Album | Turbopump 3D CAD |
Category | Turbo-pump |
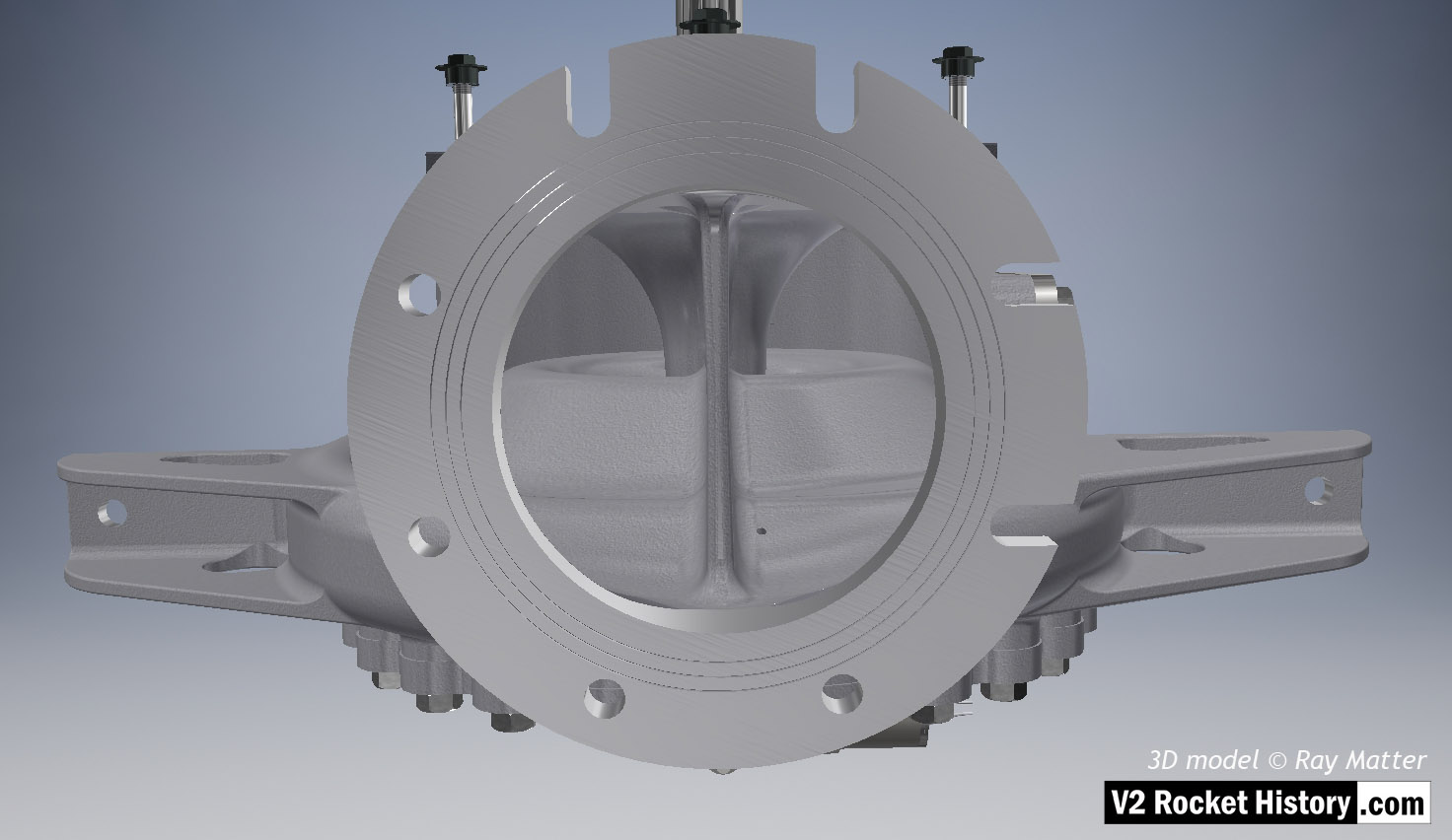
B-Pump Sub-assembly shown from top. View shows outlet flange facing camera – the splined drive shaft can just be seen at the top of the screen. Note the three fine rings milled into flange face.The rings were designed to improve keying for the ‘putty’ that was used to seal the connection between the flange face and the inlet pipe. Note, small self-purge orifice on the lower left of the inlet throat baffle. Unlike the upper purge hole in the LOX casing, the shallower face angle at the location of the hole in the fuel pump casing, was more accessible to drilling and was therefore not problematic. 3D model Ray Matter
Album | Turbopump 3D CAD |
Category | Turbo-pump |
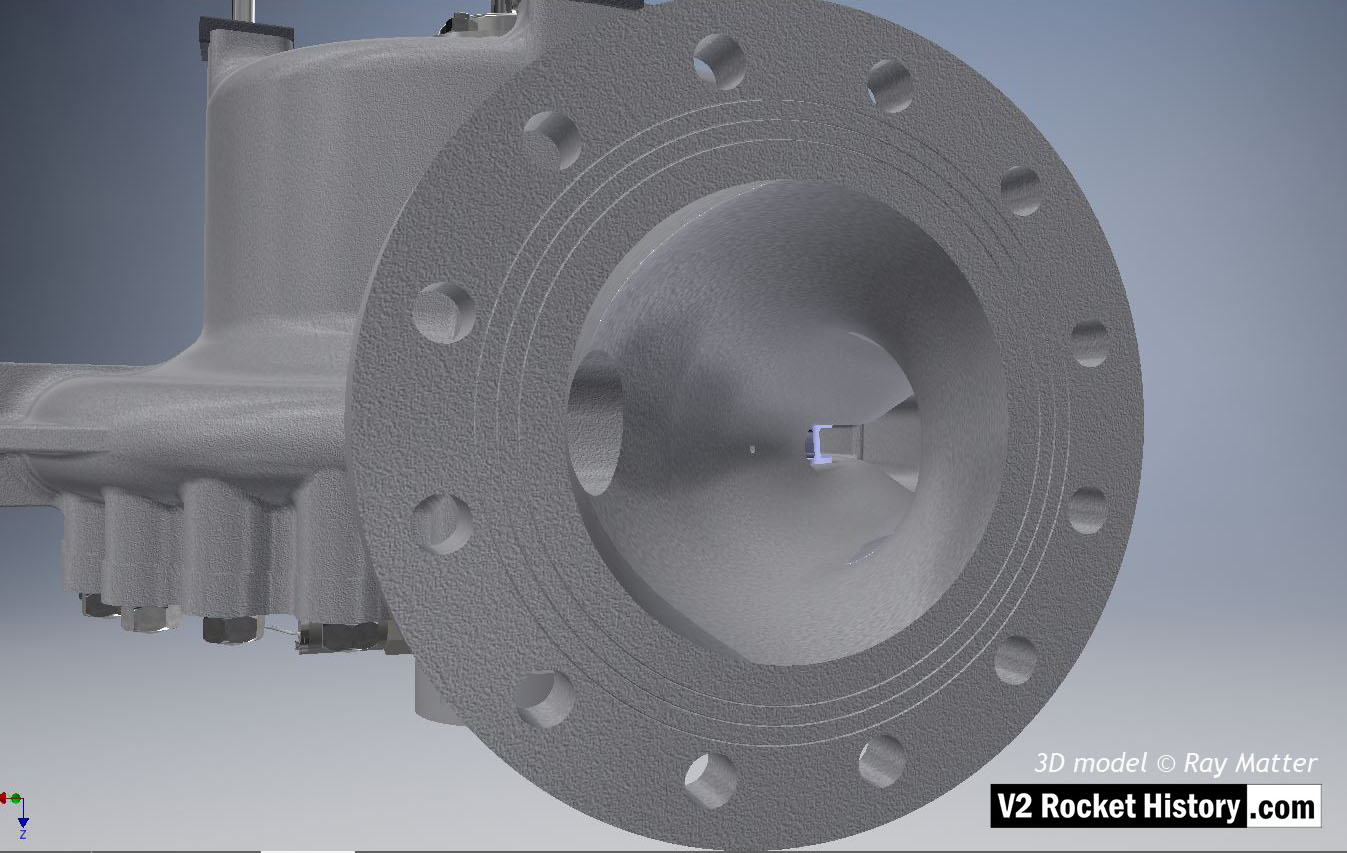
B-Pump sub-assembly close-up showing fuel outlet flange. Note the three fine rings milled into the flange face. The rings were designed to improve keying for the ‘putty’ that was used to seal the connection between the flange face and the flow choke. Both faces of the choke and top face of the fuel outflow connector had similar rings. 3D model Ray Matter
Album | Turbopump 3D CAD |
Category | Turbo-pump |
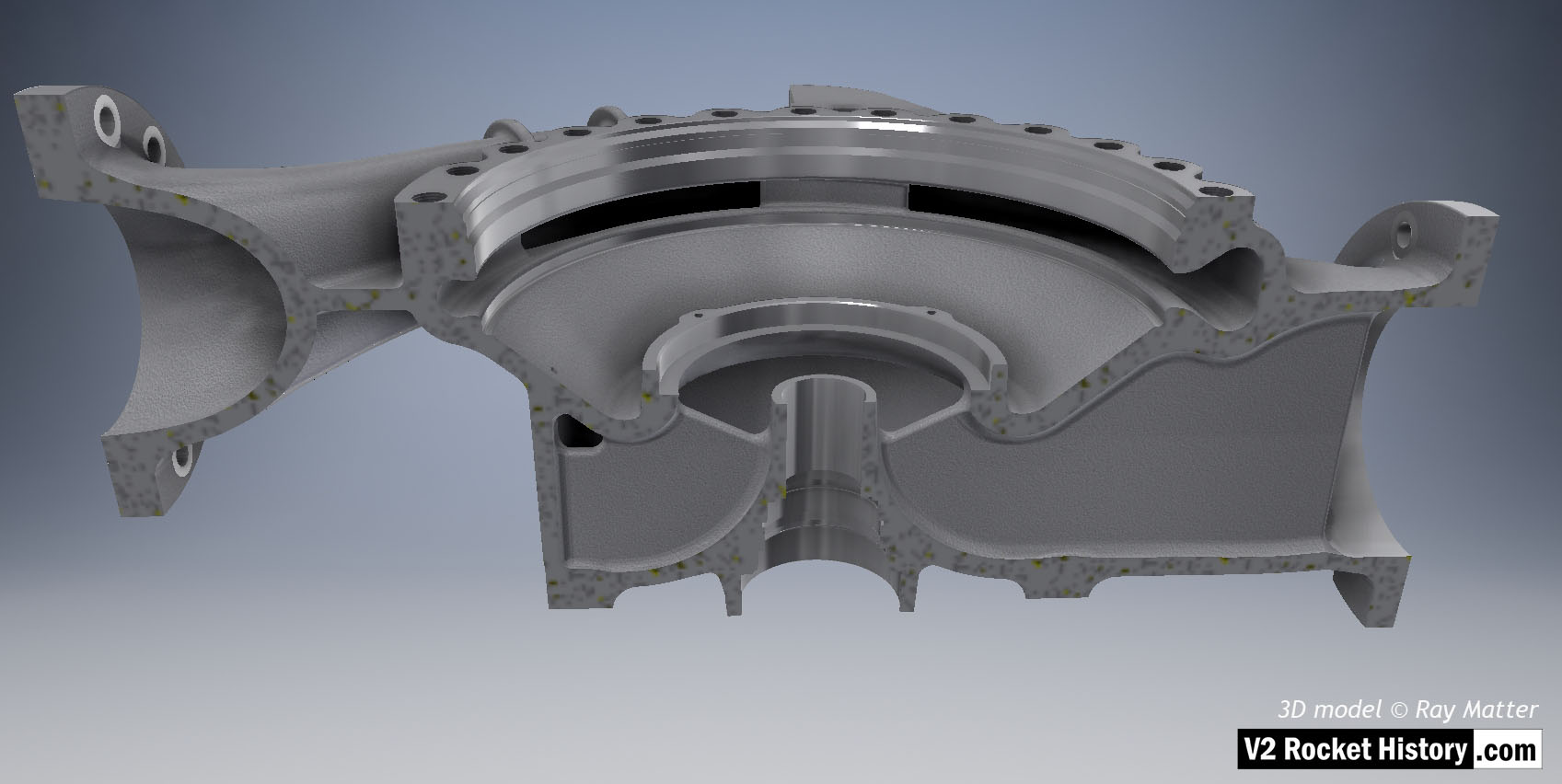
B Pump housing sectioned to show baffle and volute space area expansion as flow passes from inlet (right) to outlet (left). 3D model Ray Matter
Album | Turbopump 3D CAD |
Category | Turbo-pump |
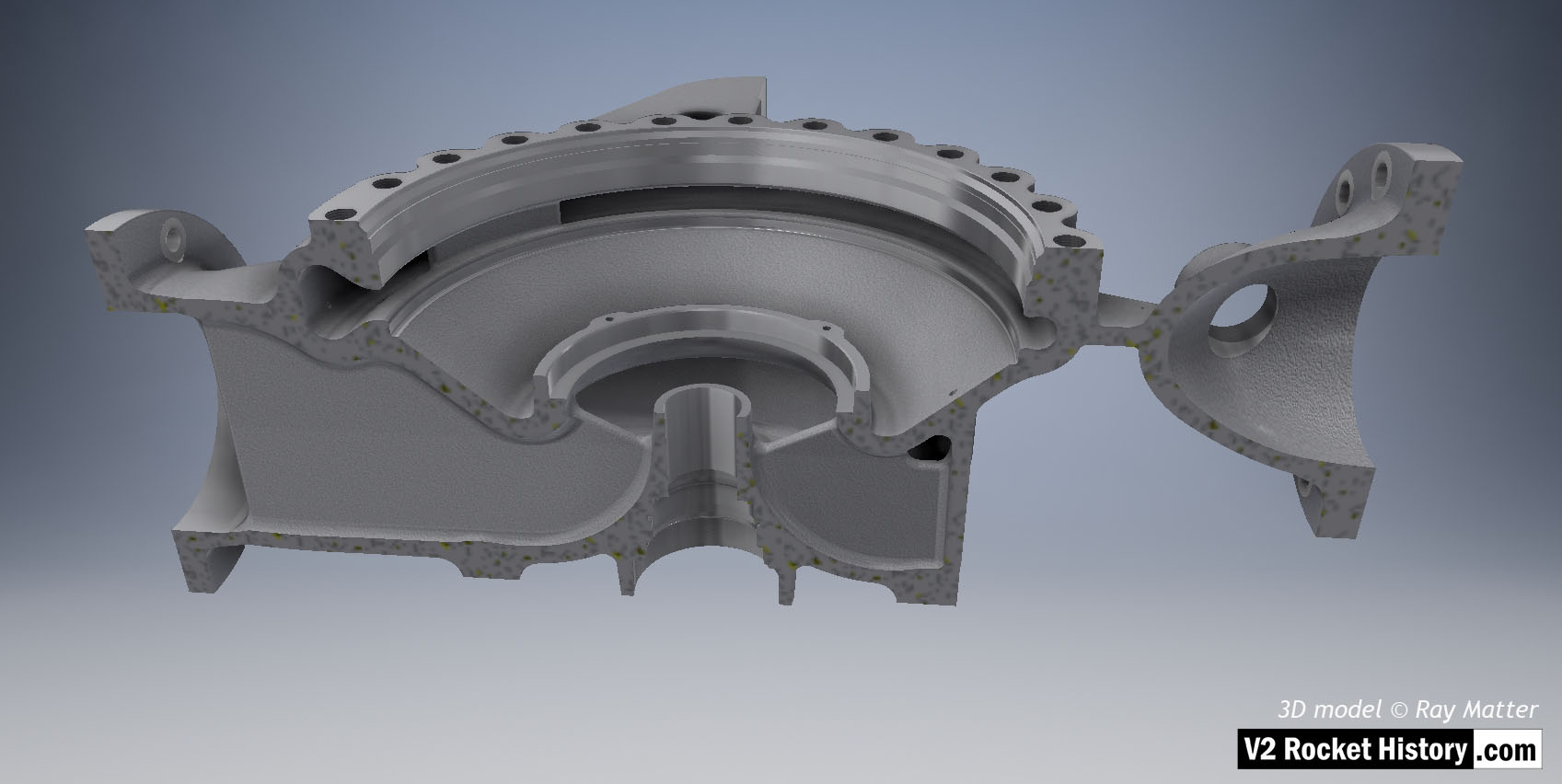
B Pump housing sectioned to show baffle with vent and volute space area expansion as flow passes from inlet (left) to outlet (right). 3D model Ray Matter
Album | Turbopump 3D CAD |
Category | Turbo-pump |
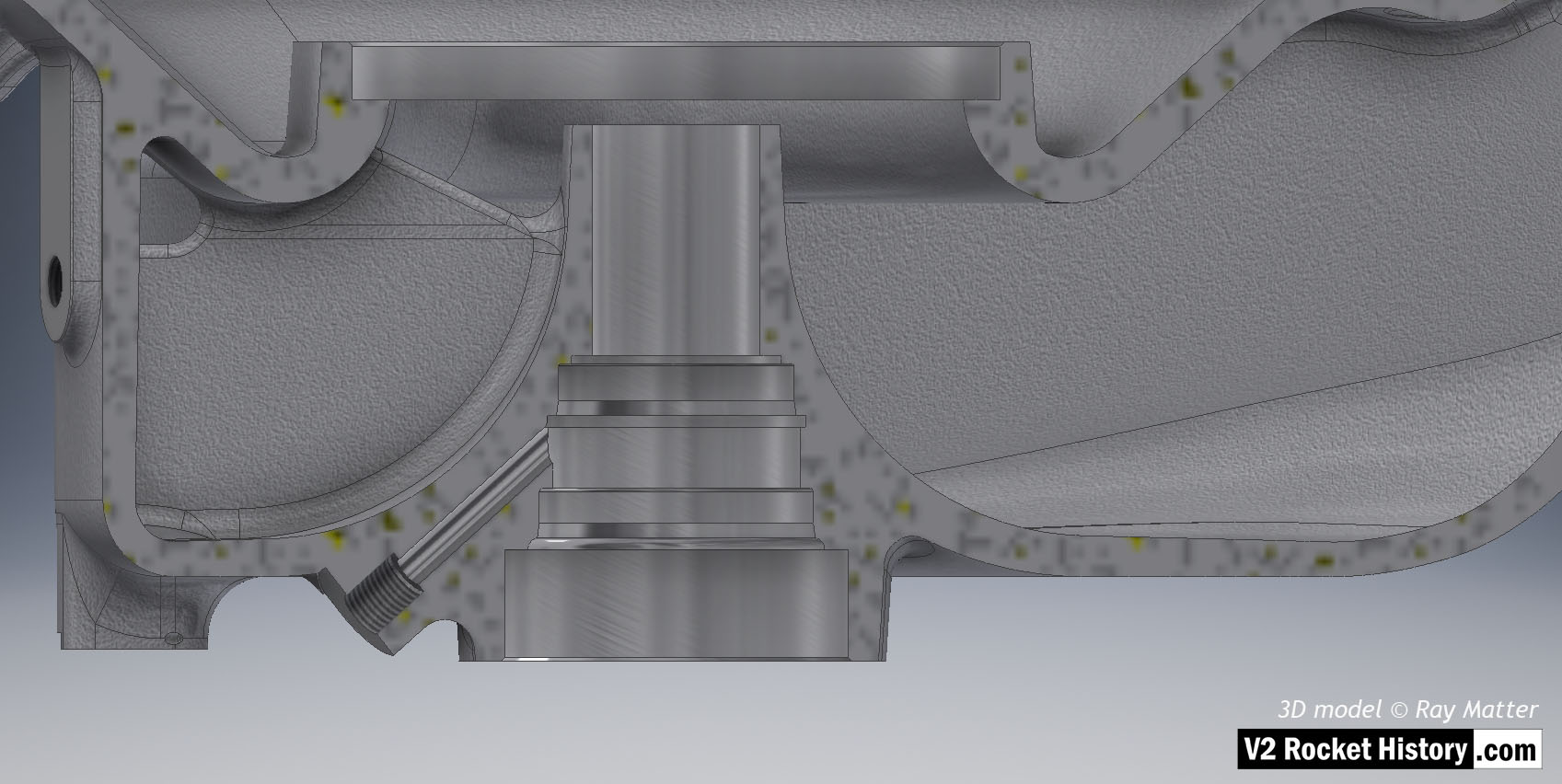
B pump housing showing sectioned area for shaft and bearing cavities with fuel pathway to left. 3D model Ray Matter
Album | Turbopump 3D CAD |
Category | Turbo-pump |
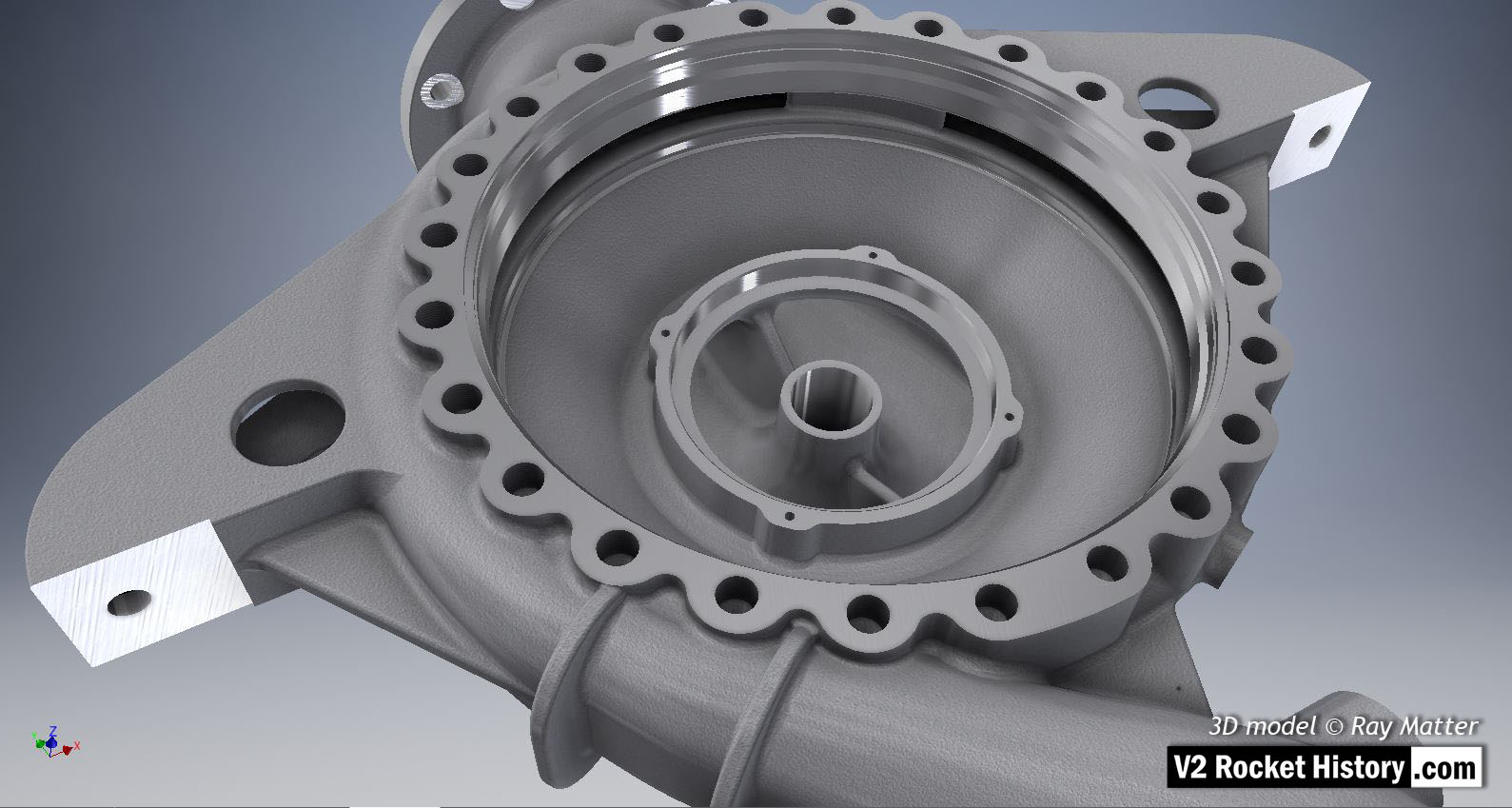
‘B’ fuel pump housing for V2 rocket engine turbopump showing cast and machined surfaces – some machined areas with obvious specular reflections. Of note are the rarely seen machined contact points on the integral support brackets and the larger areas in two locations in the ring of double ended bolt fixing holes seen at 12 and 6 o’clock. These areas allowed two ‘push’ screws to be threaded into corresponding locations in the face plate. These could then be screwed down to provide a pushing force to remove the face plate from the main housing seat. This retraction system was required owing to the very tight fit of the face plate due to the narrow ‘piston fit’ tolerances and the vacuum effect of a soft gasket that was employed between the faces. 3D model by Ray Matter
Album | Turbopump 3D CAD |
Category | Turbo-pump |
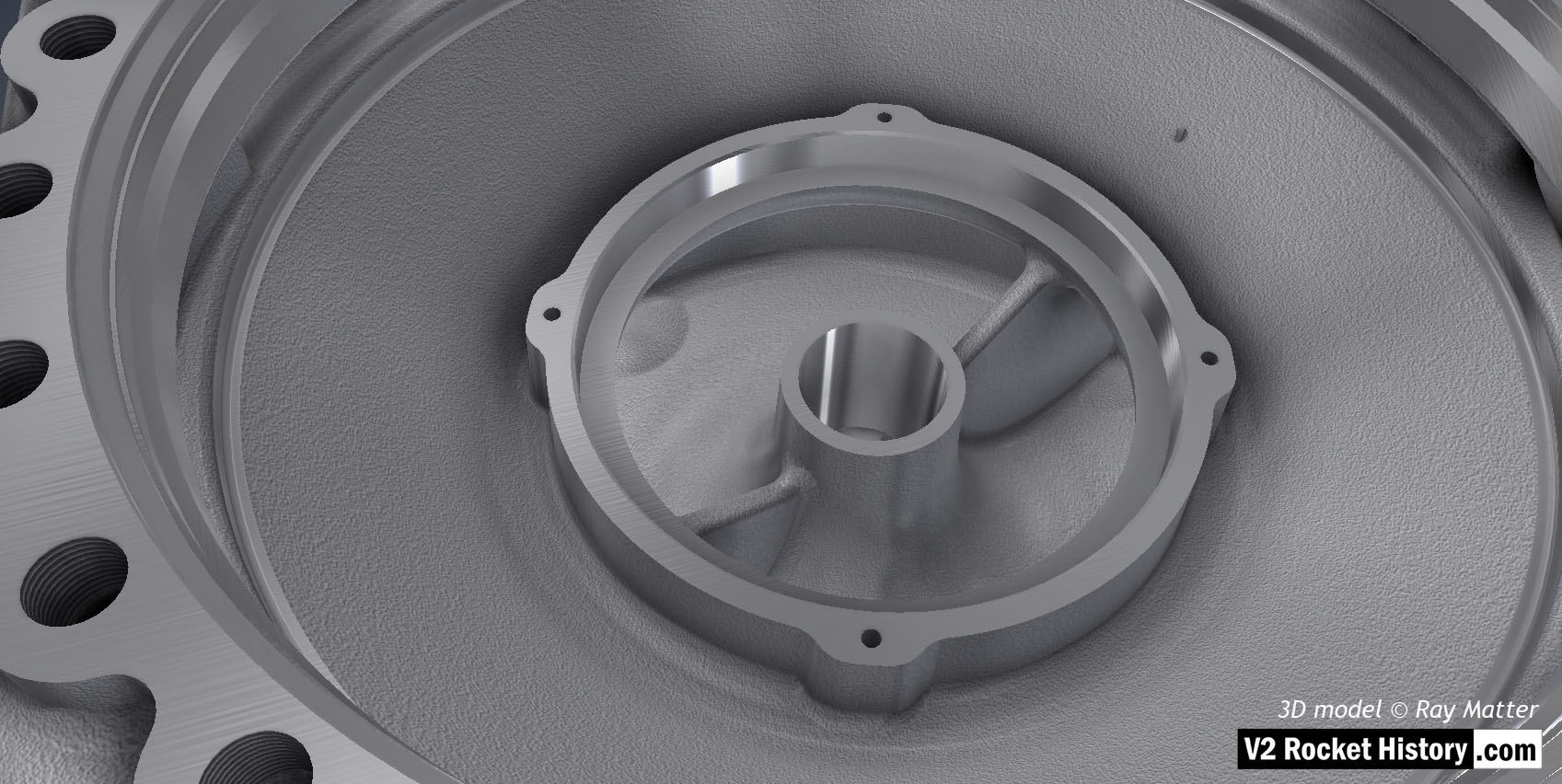
Close-up of ‘B’ fuel pump housing displaying cast and machined surfaces. Fuel inlet aperture shown with small purge orifice shown at 2 o’clock. 3D model by Ray Matter
Album | Turbopump 3D CAD |
Category | Turbo-pump |
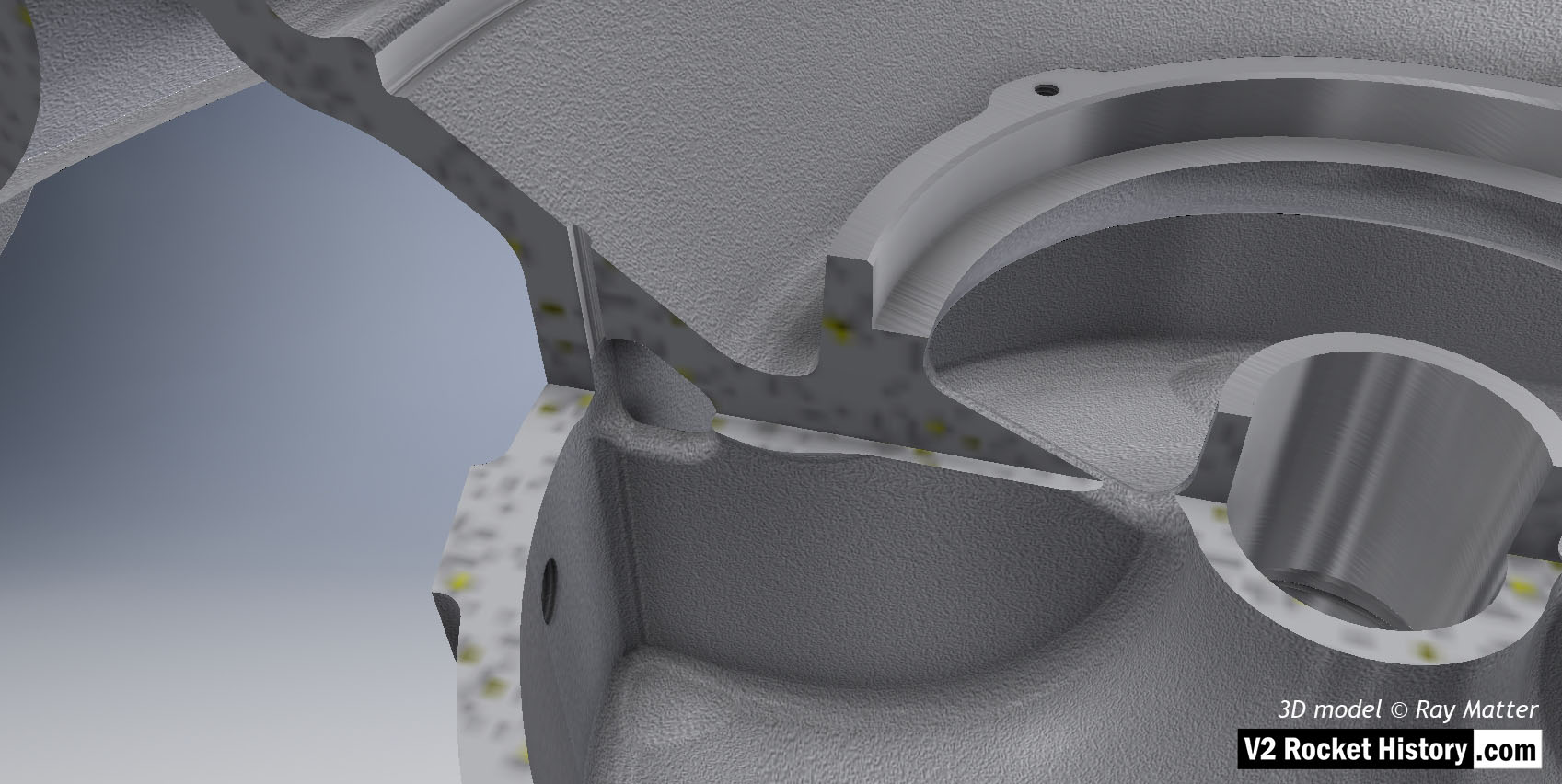
B Pump Housing, sectioned to show close-up of fuel bleed aperture and baffle vent for fuel pressure equalization between cavities inside the B pump casing. 3D model by Ray Matter
Album | Turbopump 3D CAD |
Category | Turbo-pump |
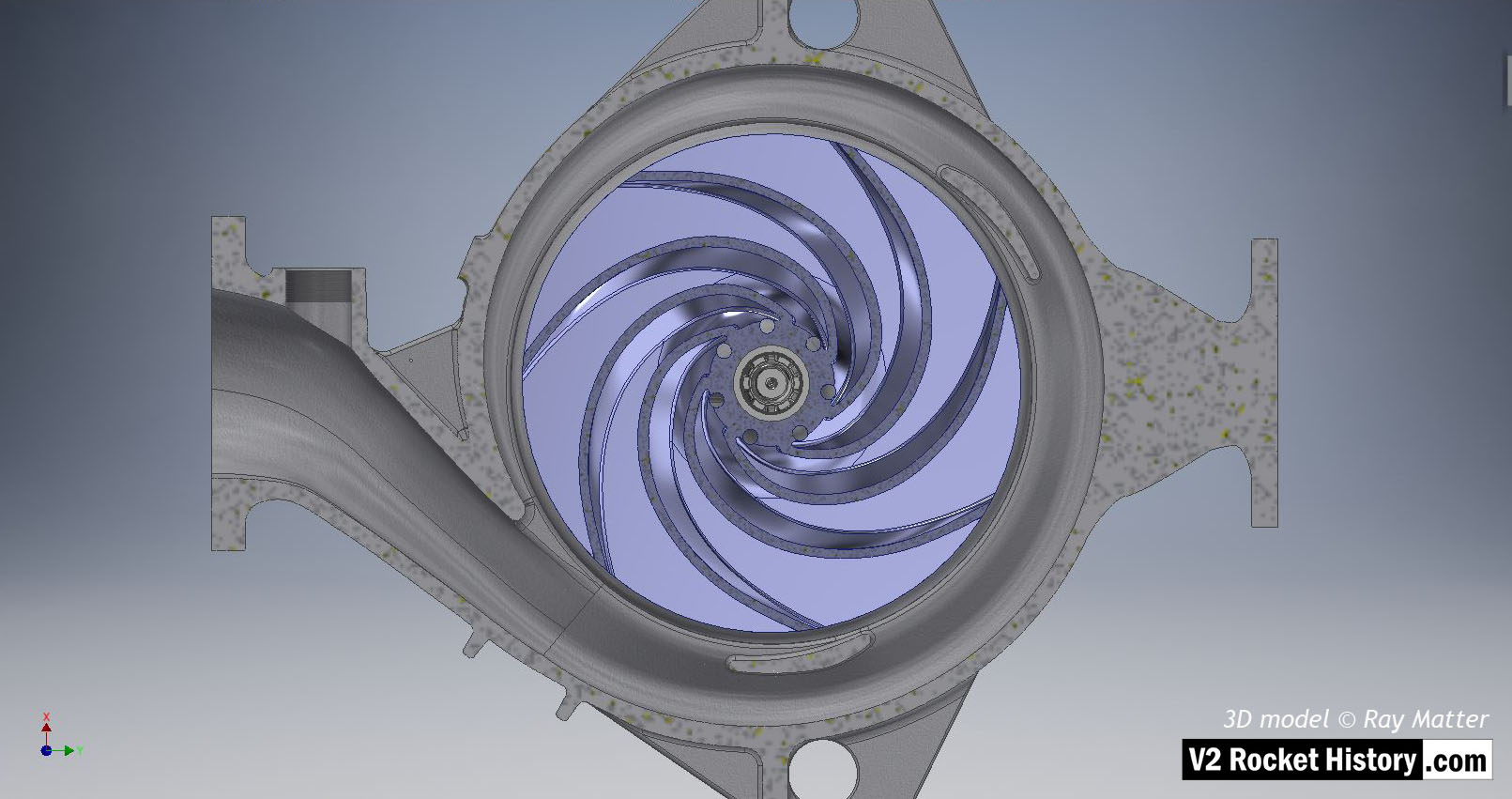
B (fuel) pump sub-assembly elevation view showing sectioned casing to reveal centrifugal pump impeller (in light purple for visibility). Outlet to left. The centrifugal pump impeller has been sectioned to remove one impeller face and reveal the curved vanes. The hub pass holes and end view of splined shaft are also shown. The spiral volute shape is very clear in this image. 3D model Ray Matter
Album | Turbopump 3D CAD |
Category | Turbo-pump |

B (fuel) pump sub-assembly showing sectioned casing to reveal centrifugal pump impeller (in light purple for visibility). Outlet to top right. The centrifugal pump rotor has been sectioned to remove one impeller face and reveal the curved vanes.The shaft and spiral volute space shape is very clear in this image. 3D model Ray Matter
Album | Turbopump 3D CAD |
Category | Turbo-pump |

B (fuel) pump sub-assembly showing sectioned casing to reveal centrifugal pump impeller. Outlet to btm right. The centrifugal pump impeller has been sectioned to remove one rotor face and reveal the curved vanes. The shaft and spiral volute space shape are shown in this image. 3D model Ray Matter
Album | Turbopump 3D CAD |
Category | Turbo-pump |

B-Pump sub-assembly sectioned to show fuel pump impeller inlet (purple area), baffle, and other shaft details. 3D model Ray Matter
Album | Turbopump 3D CAD |
Category | Turbo-pump |
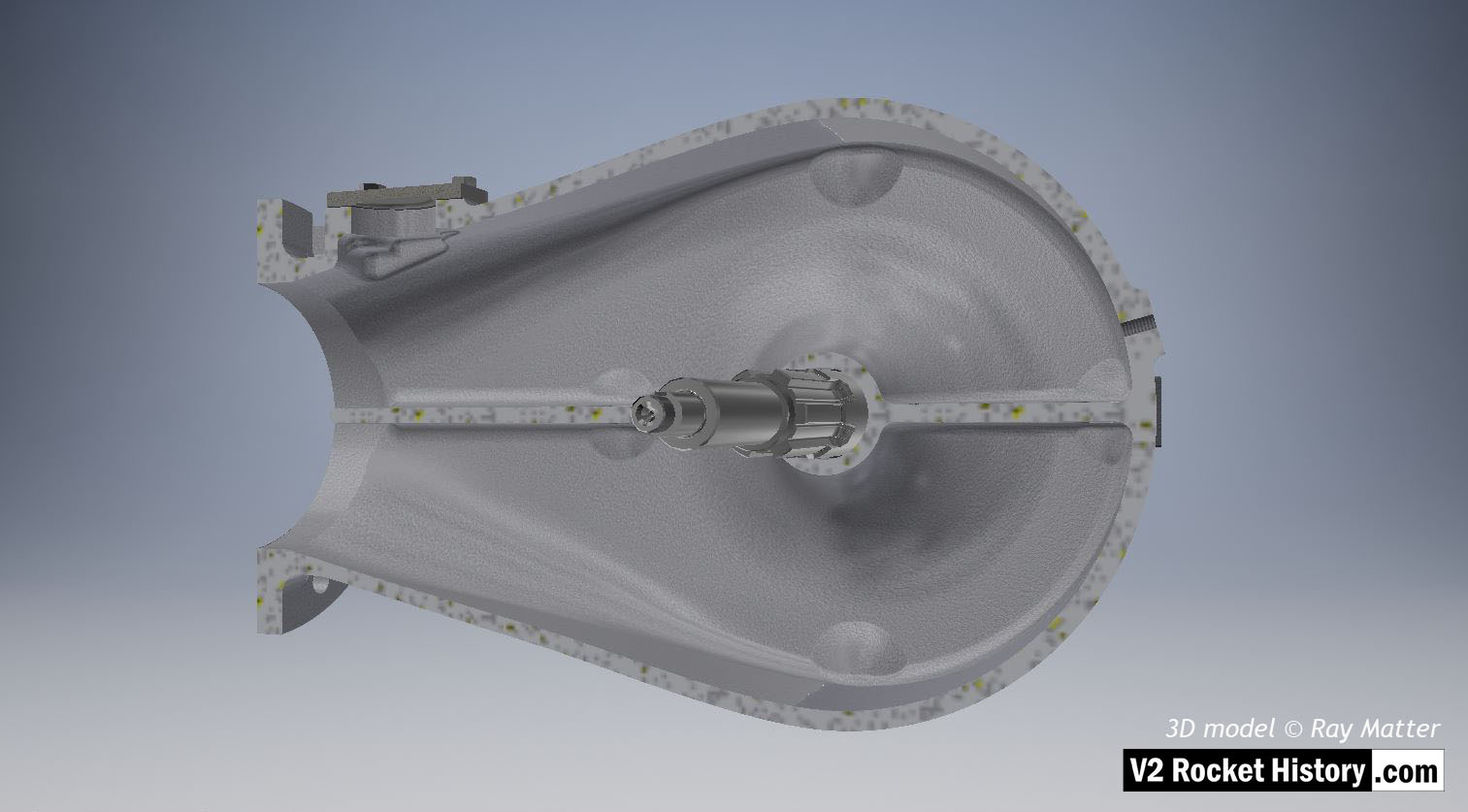
B-Pump sub-assembly casing sectioned to show shaft and fuel inlet chamber details. The throat blanking plate can be seen top left. 3D model Ray Matter
Album | Turbopump 3D CAD |
Category | Turbo-pump |
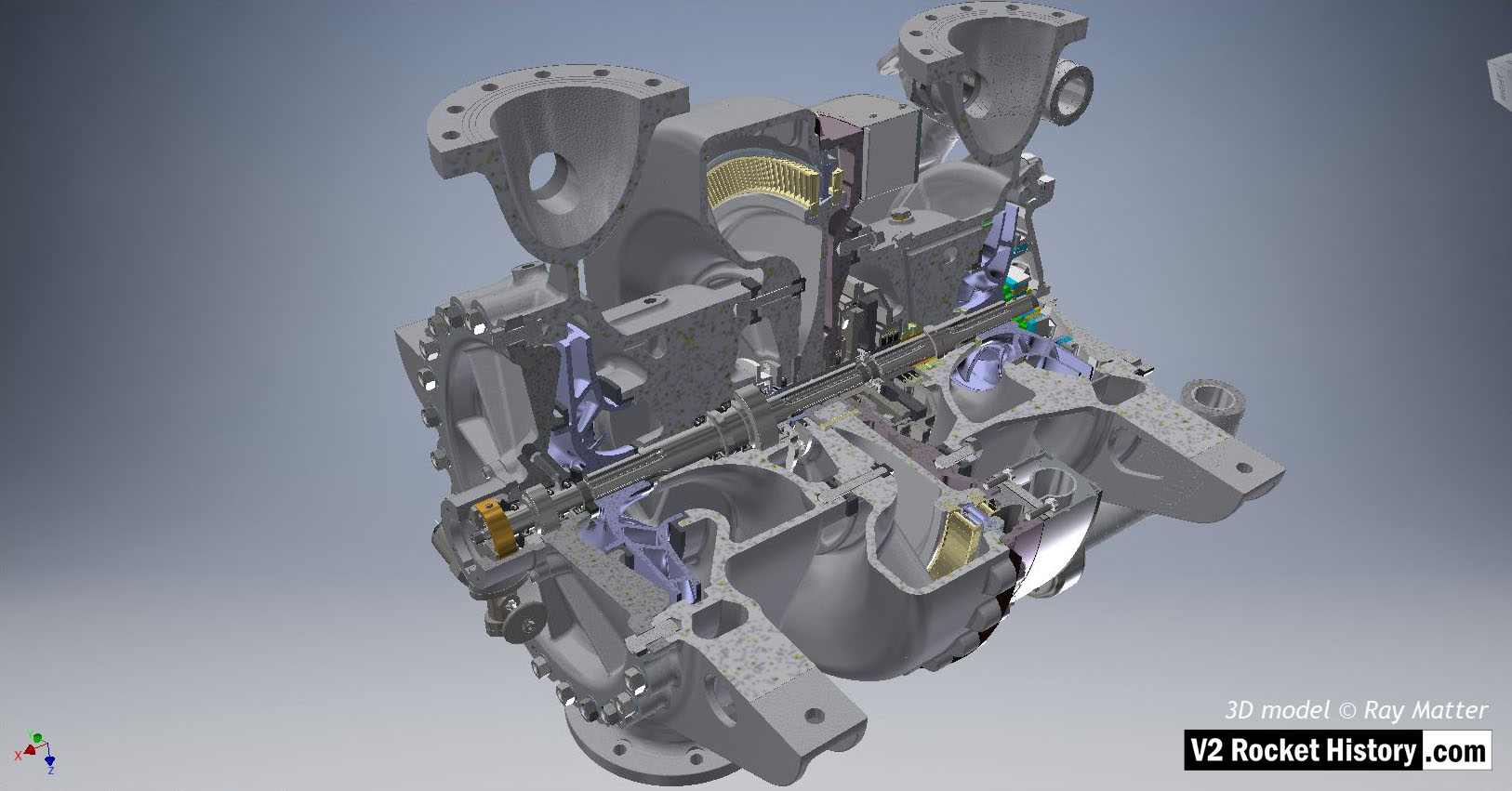
Turbine powered propellant pumps for A4/V2 rocket engine. The assembly is shown quarter sectioned and inverted with the propellant outlet flanges to the top and fuel pump on left, with inlet flanges at btm. The overspeed trip switch can be seen just below center on fuel pump face plate – the copper alloy centrifugal trip rotor is clearly visible in the trip-switch housing. 3D model by Ray Matter
Album | Turbopump 3D CAD |
Category | Turbo-pump |
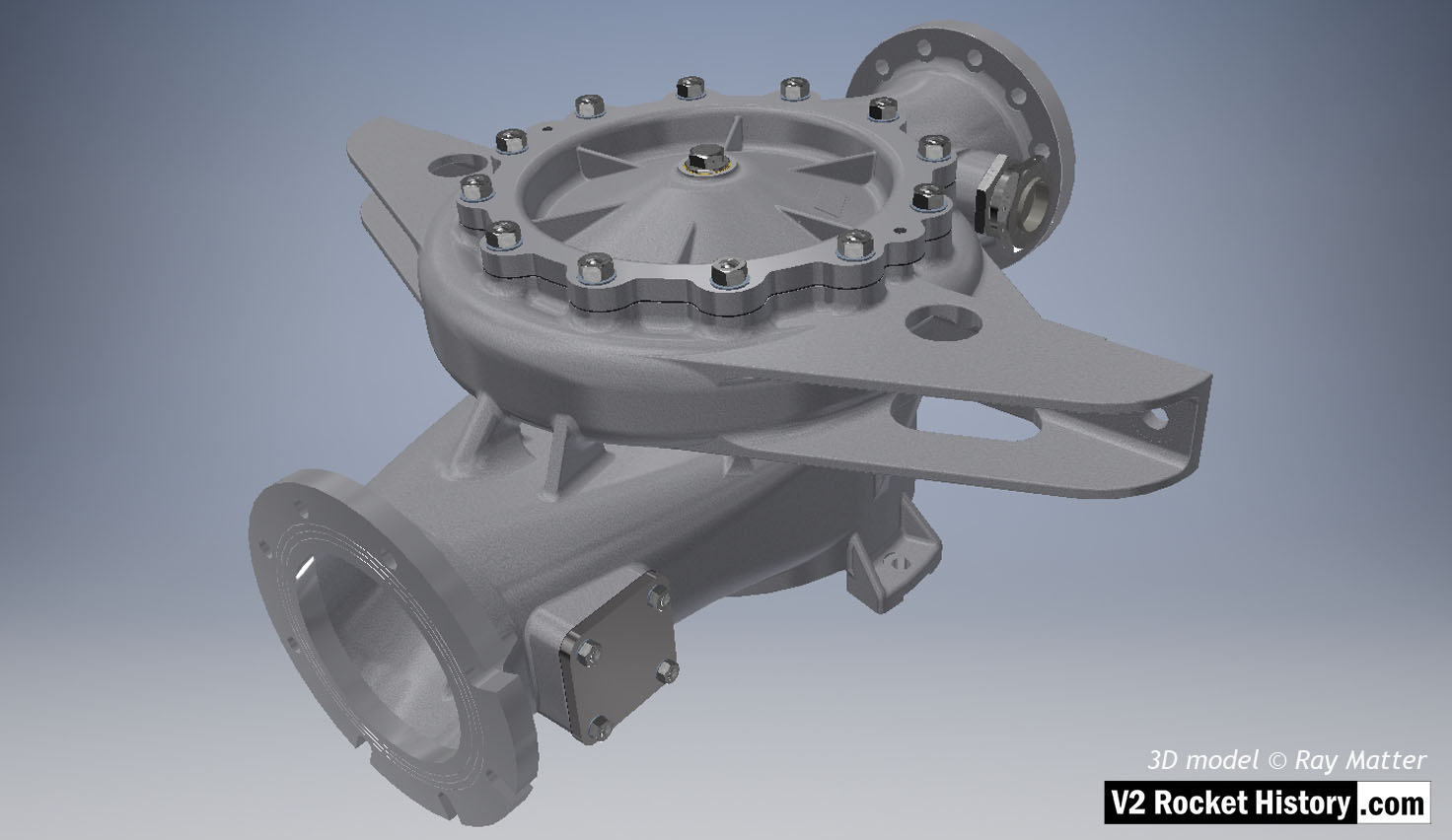
A-Pump LOX sub-assembly complete with face plate and fastenings as well as outlet throat plug. Shows square inlet throat blanking plate.
3D model Ray Matter
Album | Turbopump 3D CAD |
Category | Turbo-pump |
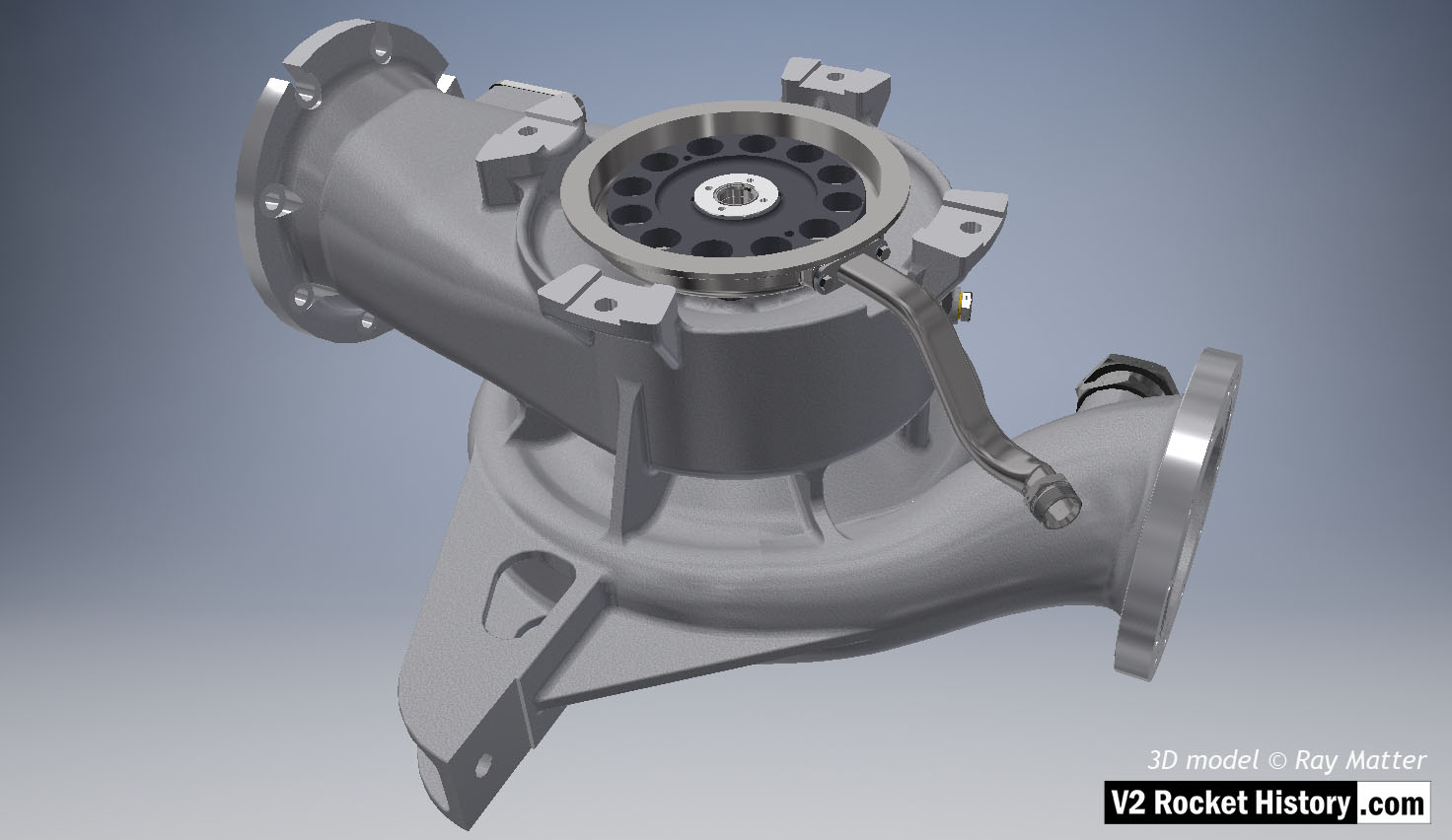
A (LOX) Pump sub-assembly, showing the face nearest the steam turbine. Turbine side of LOX pump showing flexible shaft connection disk (back component with 12 holes). The connection cavity drain pipe is shown (running across the outflow to the btm right). 3D model Ray Matter
Album | Turbopump 3D CAD |
Category | Turbo-pump |
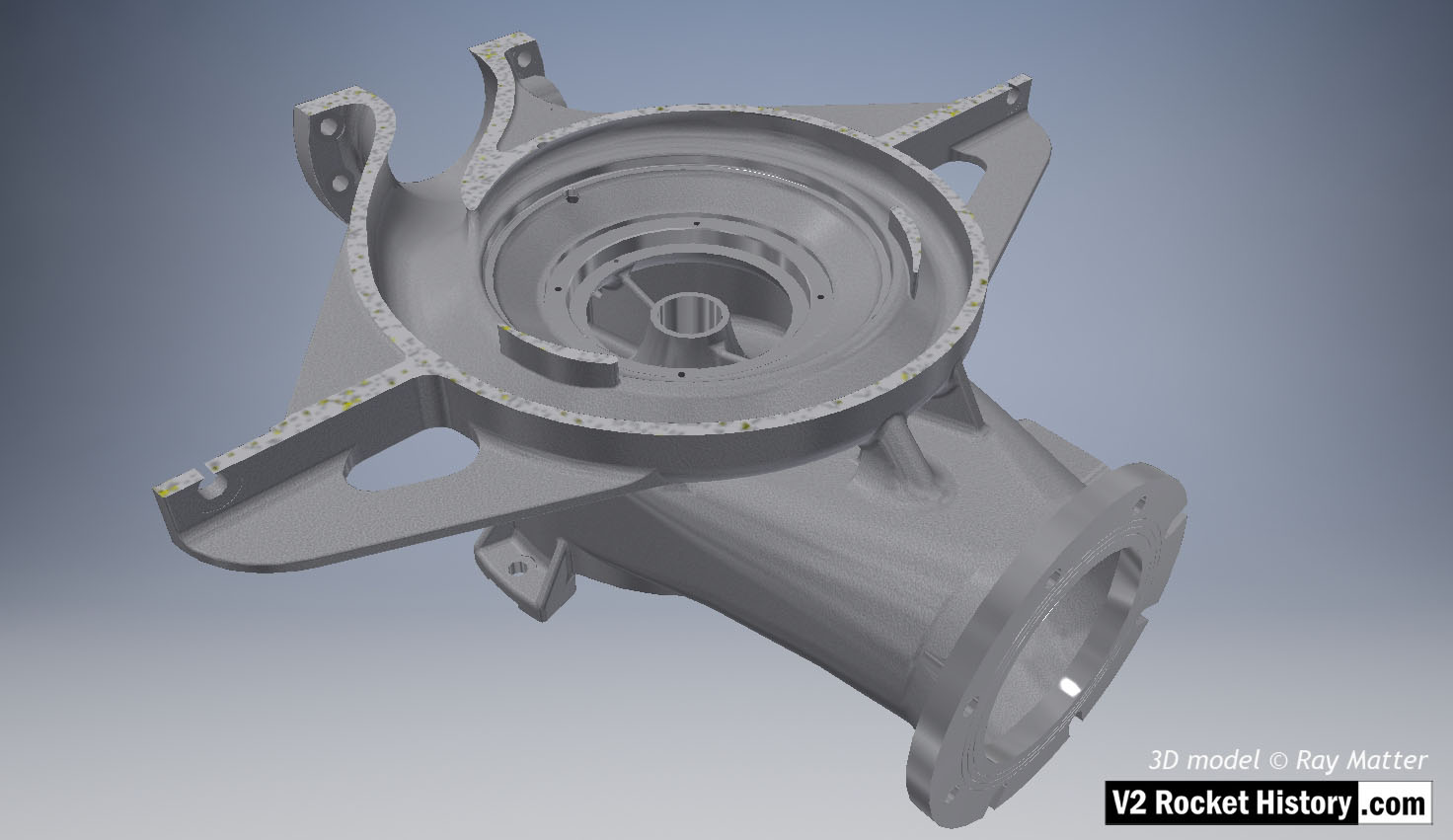
A (LOX) pump housing cutaway to reveal pump rotor side. The casing has been cut to show the internal rotor space detail. The outlet throat, right, and spiral volute space are displayed in this view as is the central LOX inlet. The web with the self-purge passageway can be seen on the outside center of the inlet throat, and connecting to the volute casing. The web or buttress seen to the upper right is to provide additional support between the structures whilst keeping the casting to an even density. 3D model Ray Matter
Album | Turbopump 3D CAD |
Category | Turbo-pump |

Close-up of ‘A’ LOX pump housing displaying cast and machined surfaces. LOX inlet aperture shown wand external threaded hole for manual bleed plug shown on far right. 3D model by Ray Matter
Album | Turbopump 3D CAD |
Category | Turbo-pump |
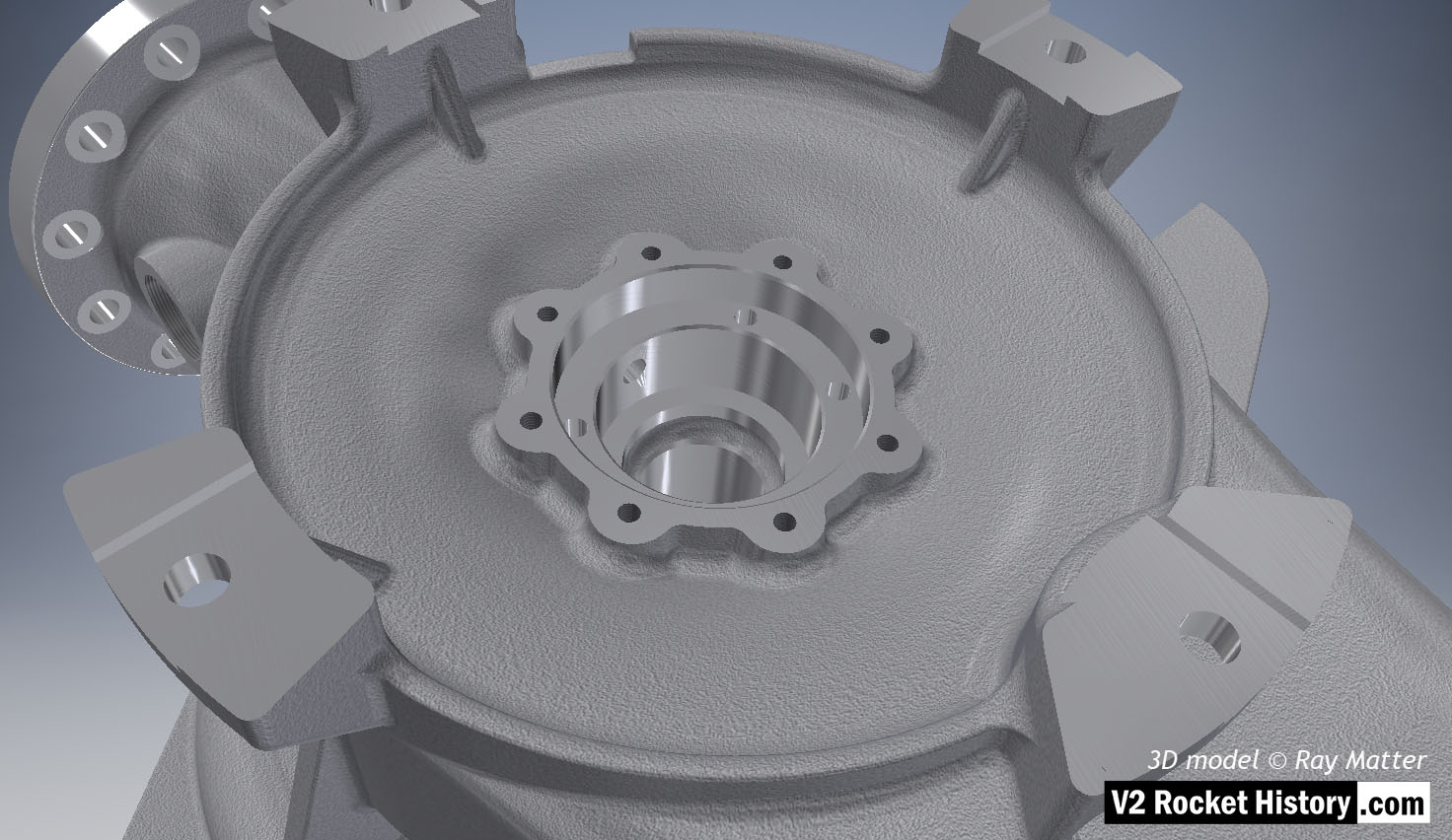
A (LOX) Pump sub-assembly, showing the face nearest the steam turbine. Single piece casting showing machined (milled) areas and detail of bearing and seal cavity. The four turbine case fitting brackets are displayed. 3D model Ray Matter
Album | Turbopump 3D CAD |
Category | Turbo-pump |
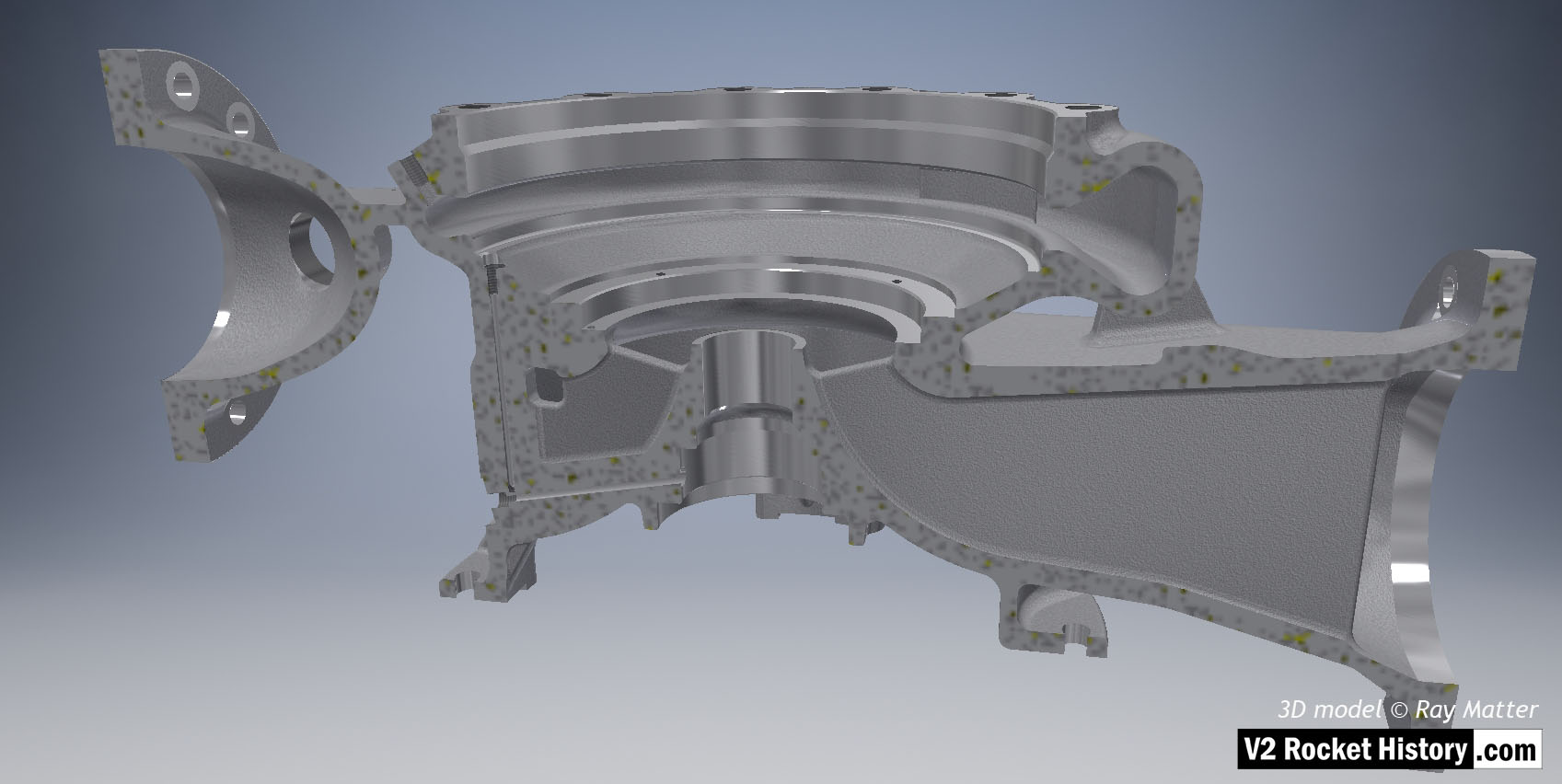
A (LOX) Pump housing sectioned to show baffle and volute space area expansion as flow passes from inlet (right) to outlet (left). Note cast and machined (milled) areas shown in this image – especially inlet aperture. 3D model Ray Matter
Album | Turbopump 3D CAD |
Category | Turbo-pump |
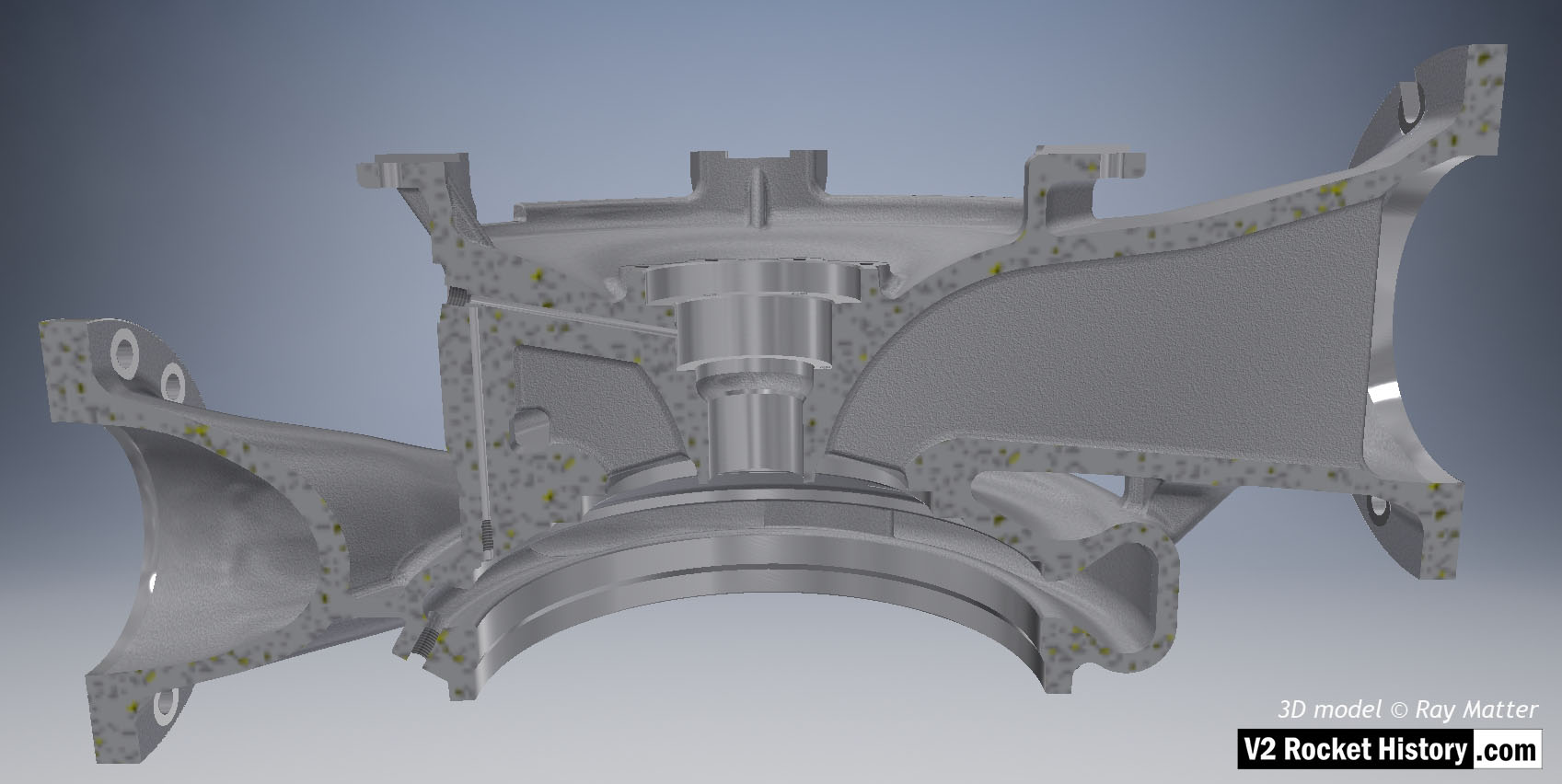
A (LOX) Pump housing sectioned to show baffle and volute space area expansion as flow passes from inlet (right) to outlet (left). Note the small LOX passageways on left from high-pressure volute space to bearing cavity. 3D model Ray Matter
Album | Turbopump 3D CAD |
Category | Turbo-pump |
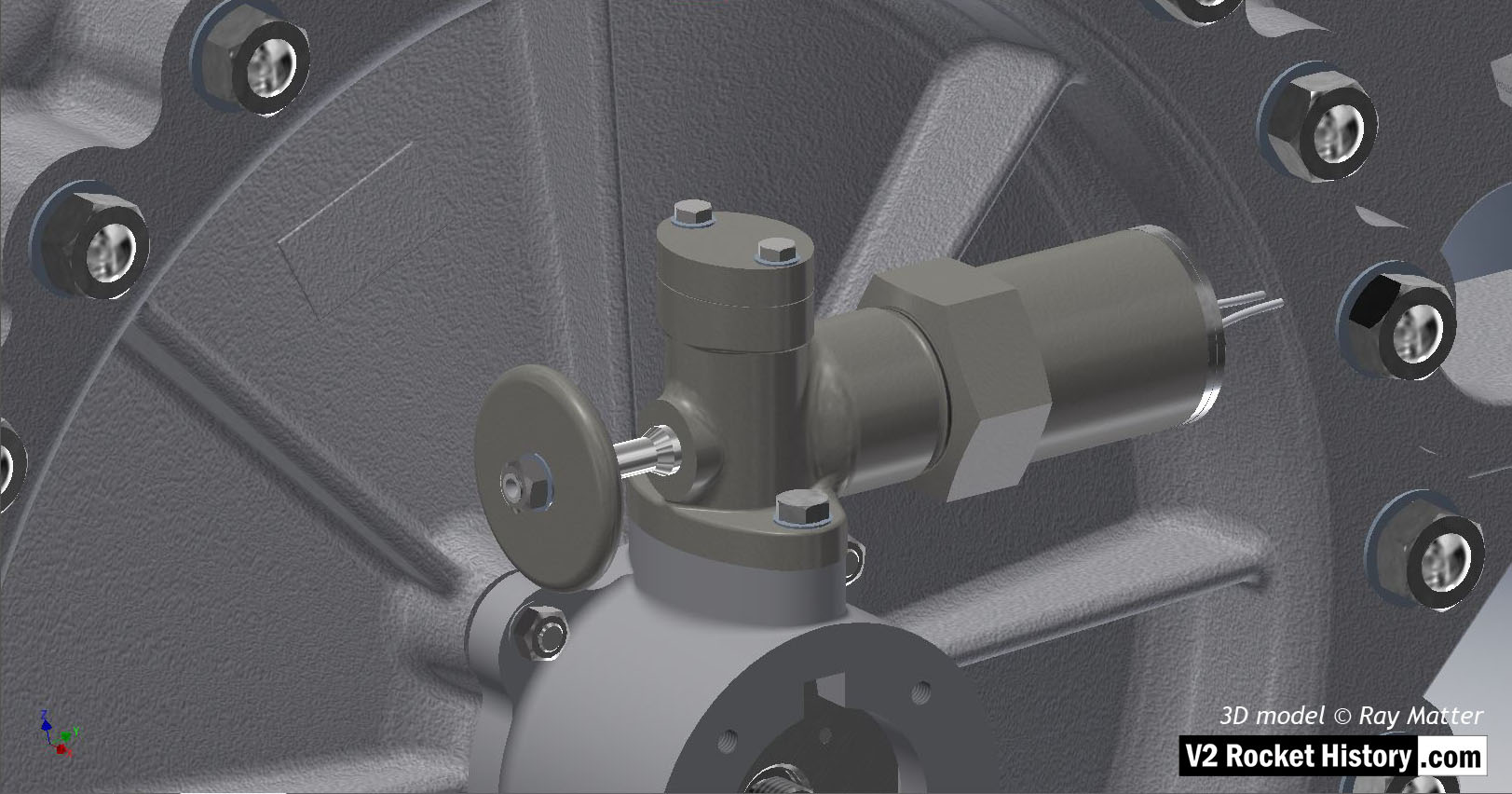
Detail of fuel pump face plate showing over-speed switch and mounting. The switch plunger (part with disc shaped hand knob on left) is shown in the out or armed position. The RPM of the tubo-pump (TP) was not governed but this safety mechanism shut the TP down permanently when the RPM reached 5000. Although rarely changed, thin shims could be used to reduce or increase this speed. 3D model Ray Matter
Album | Turbopump 3D CAD |
Category | Turbo-pump |
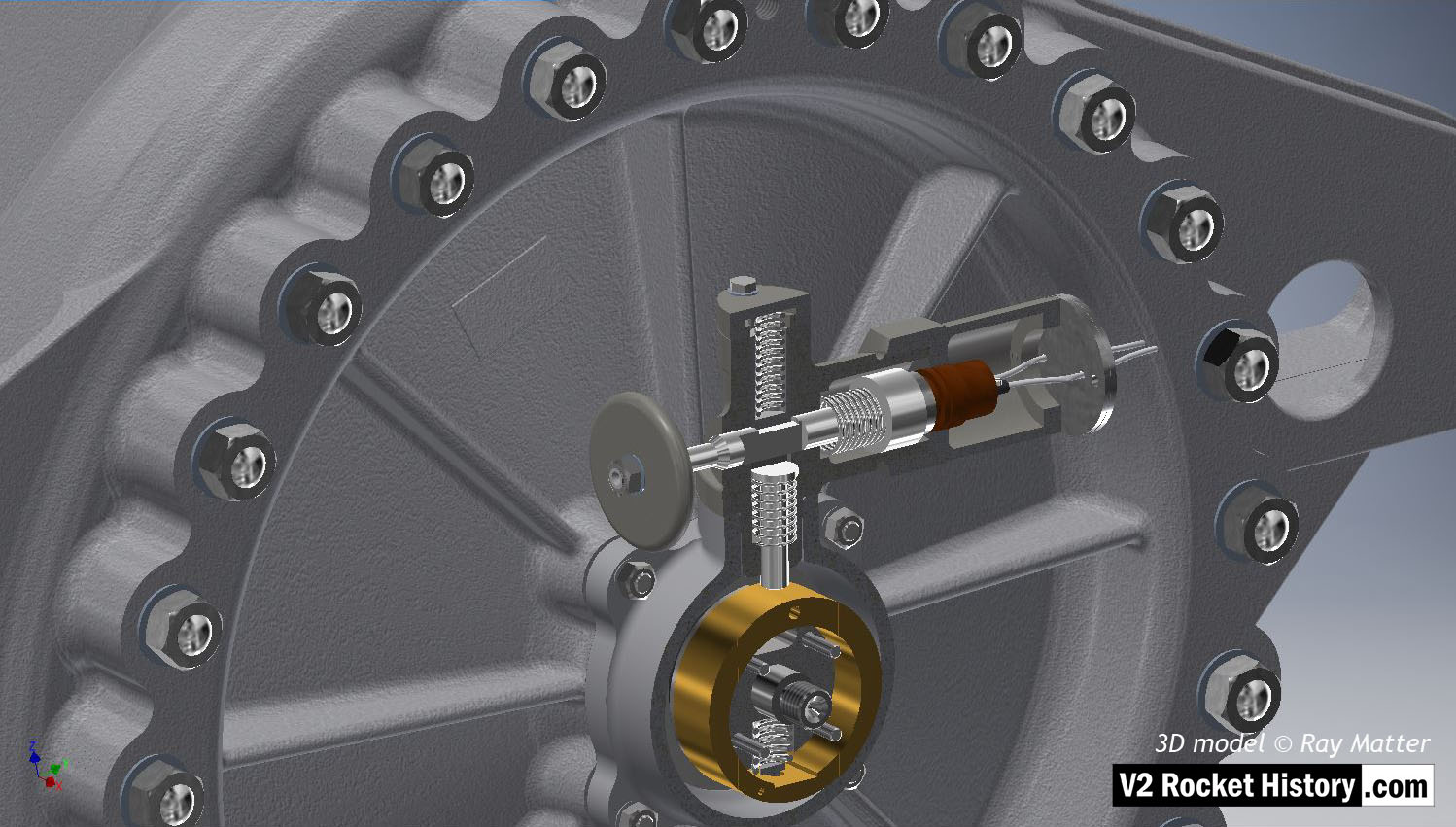
Detail of fuel pump face plate showing over-speed switch and mounting. The eccentric centrifugal rotor can be seen (brass coloured part). This unbalanced part rotates against a spring load that allows the thicker (proportionally heavier) section of the rotor to move outwards from the center as the rotational speed rises and push the release rod clear of a keyed section of the plunger shaft (part with disc shaped knob on left) thus operating a relay switch that shuts down the flow of steam to the turbine. 3D model Ray Matter
Album | Turbopump 3D CAD |
Category | Turbo-pump |
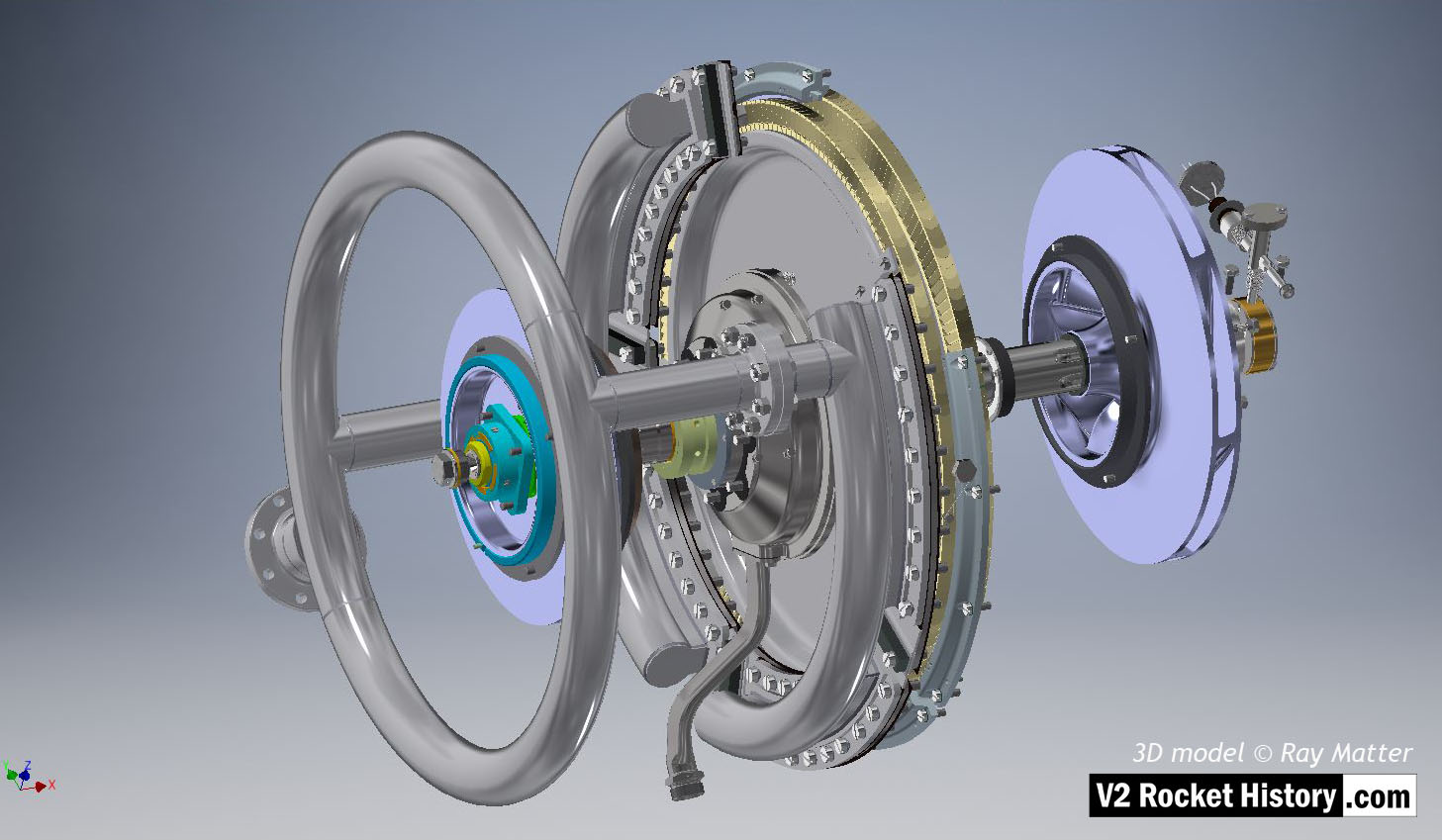
V2 turbo-pump turbine and pump impeller shaft assembly showing steam turbine rotor with nozzle assembly and steam inlet manifold distributor ring. The two rows of steam buckets can seen on rotor rim. Fuel pump impeller (purple) and over-speed switch are shown to the right. LOX pump impeller (purple) with journal bearing box and four sectional bronze bearings visible. An overboard dump pipe can be seen lower left of steam rotor. 3D model Ray Matter
Album | Turbopump 3D CAD |
Category | Turbo-pump |
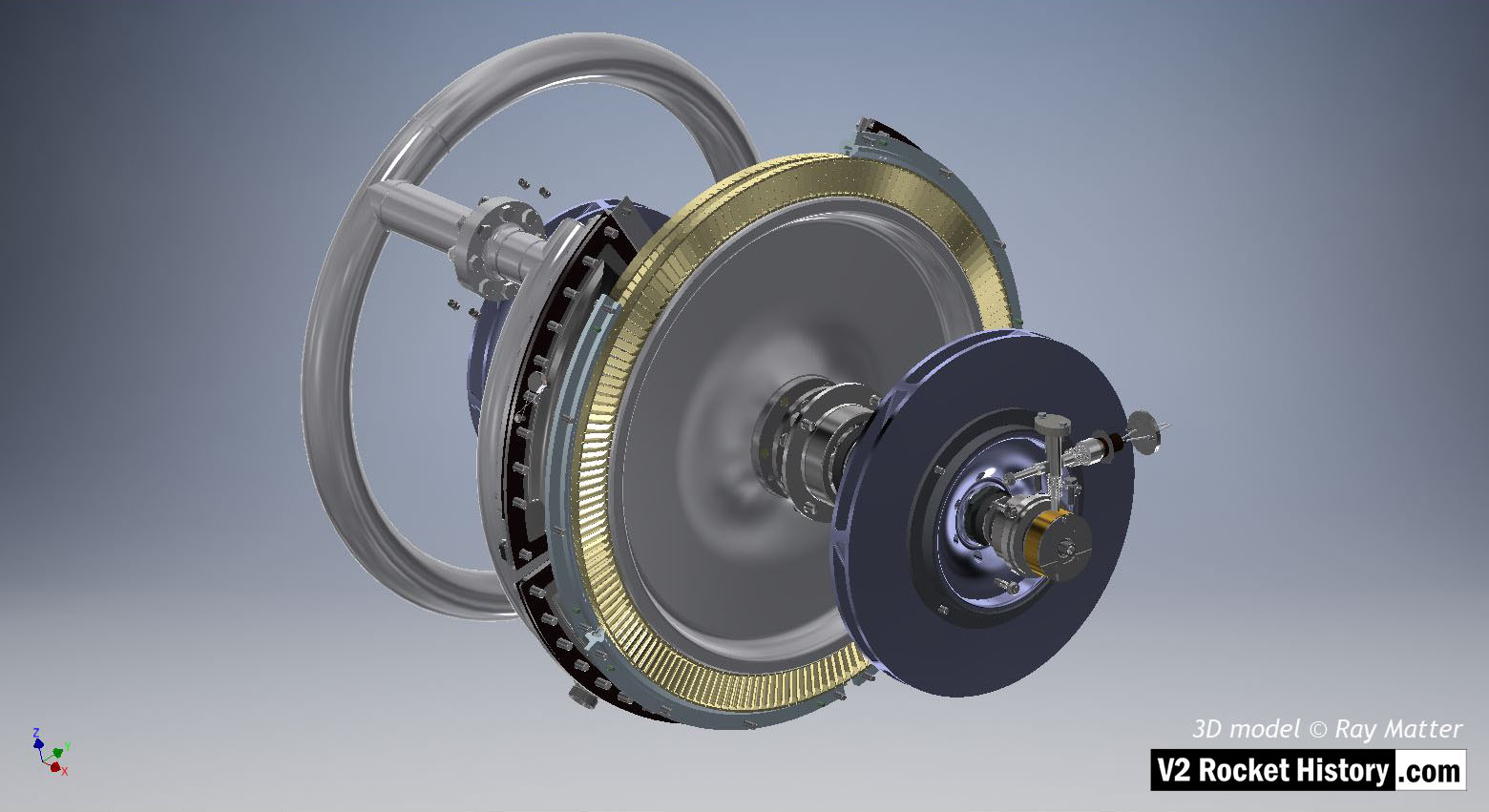
V2 turbo-pump turbine and pump impeller shaft assembly showing steam turbine rotor with nozzle assembly and steam inlet manifold distributor ring to left. The two rows of steam buckets can seen on rotor rim as well as three of the four sets of stationary steam return blades. Fuel pump impeller and over-speed switch are shown to the right. 3D model Ray Matter
Album | Turbopump 3D CAD |
Category | Turbo-pump |
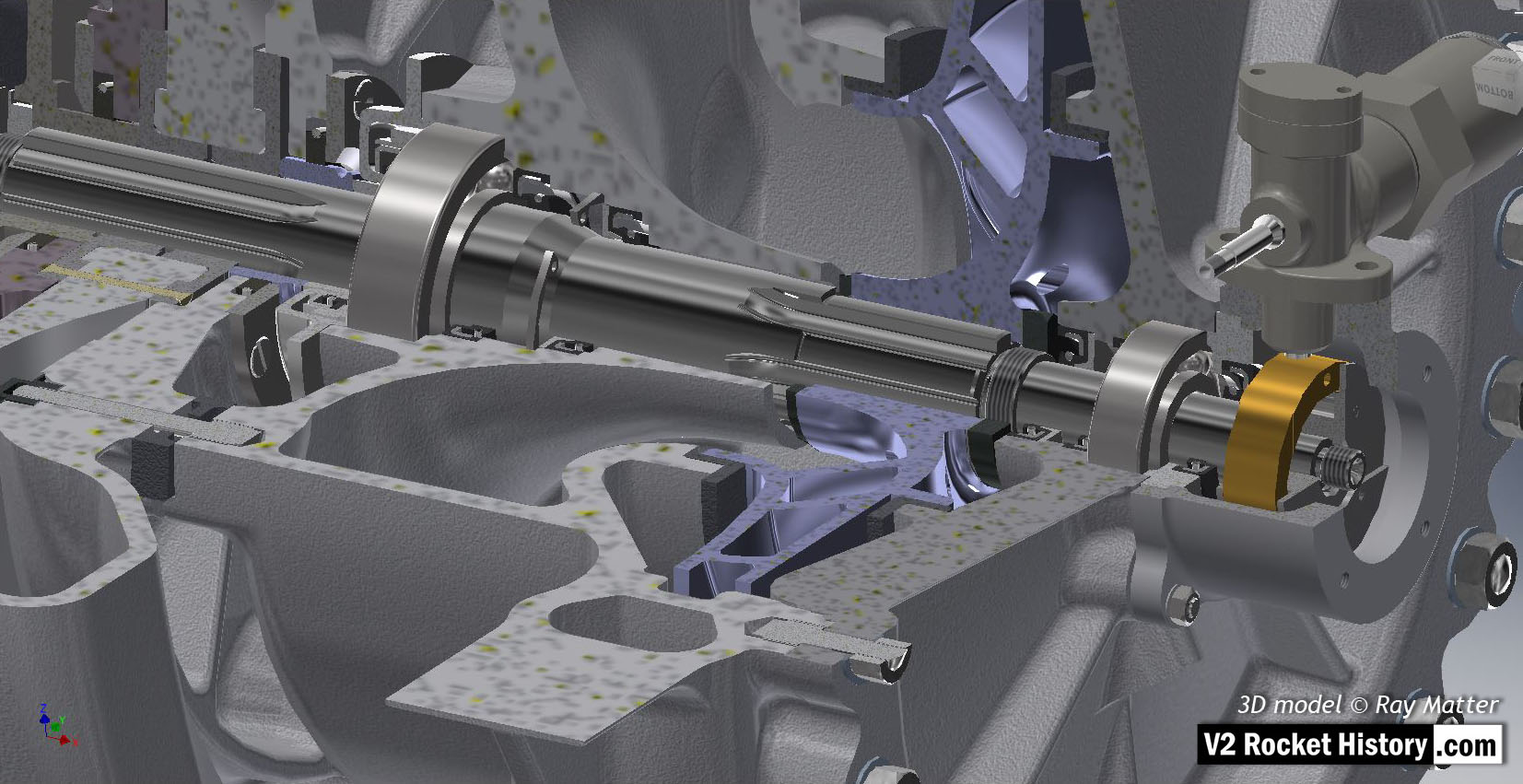
B (fuel) Pump: Close-up of sectioned turbine and pump impellers. Pump impeller (purple) and turbine rotor, top left, showing, seals, bearings and over-speed centrifugal rotor assembly. 3D model Ray Matte
Album | Turbopump 3D CAD |
Category | Turbo-pump |
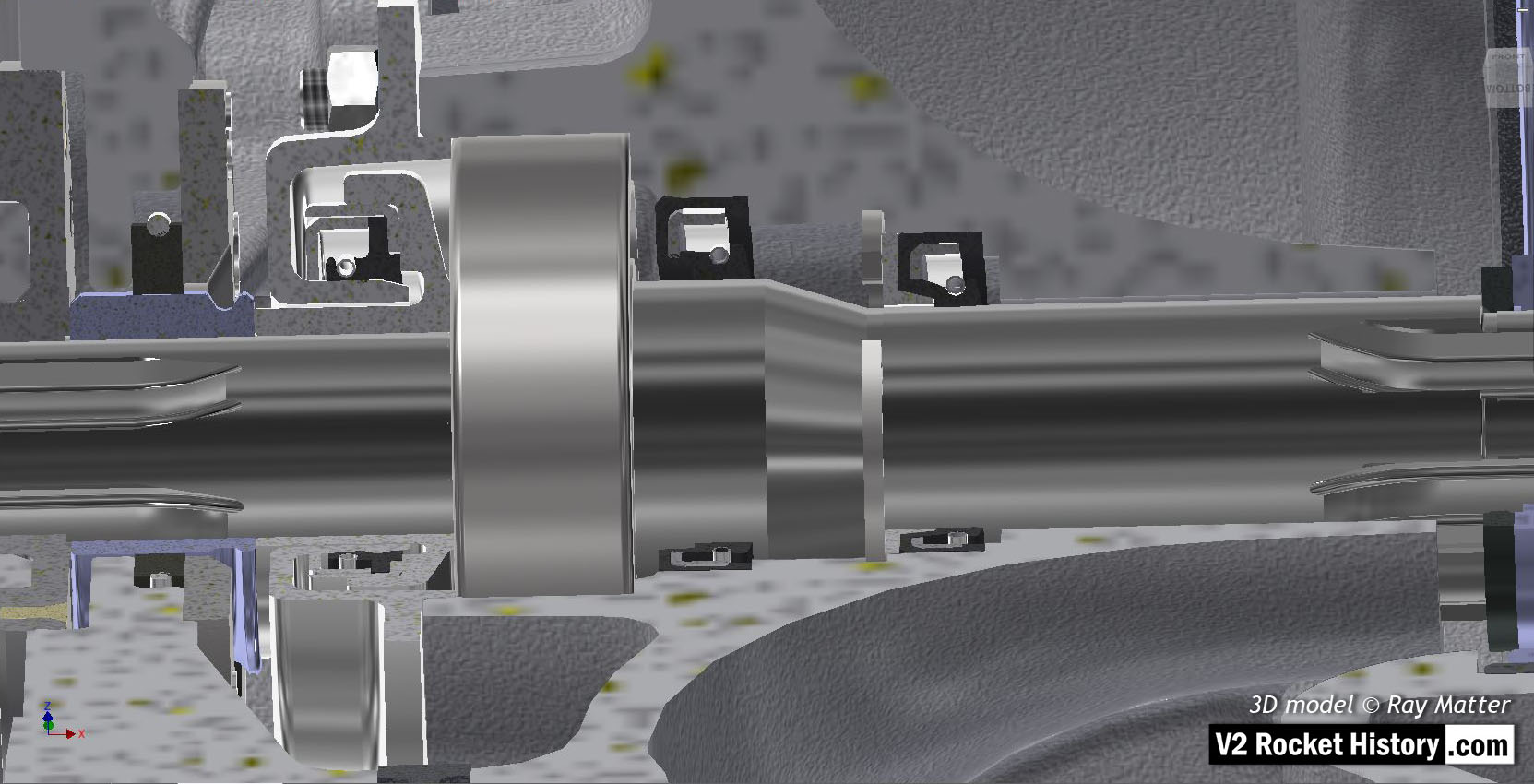
06 B Pump close-up showing shaft bearing and isolation seals at at pump to turbine mating point. 3D model Ray Matter
Album | Turbopump 3D CAD |
Category | Turbo-pump |
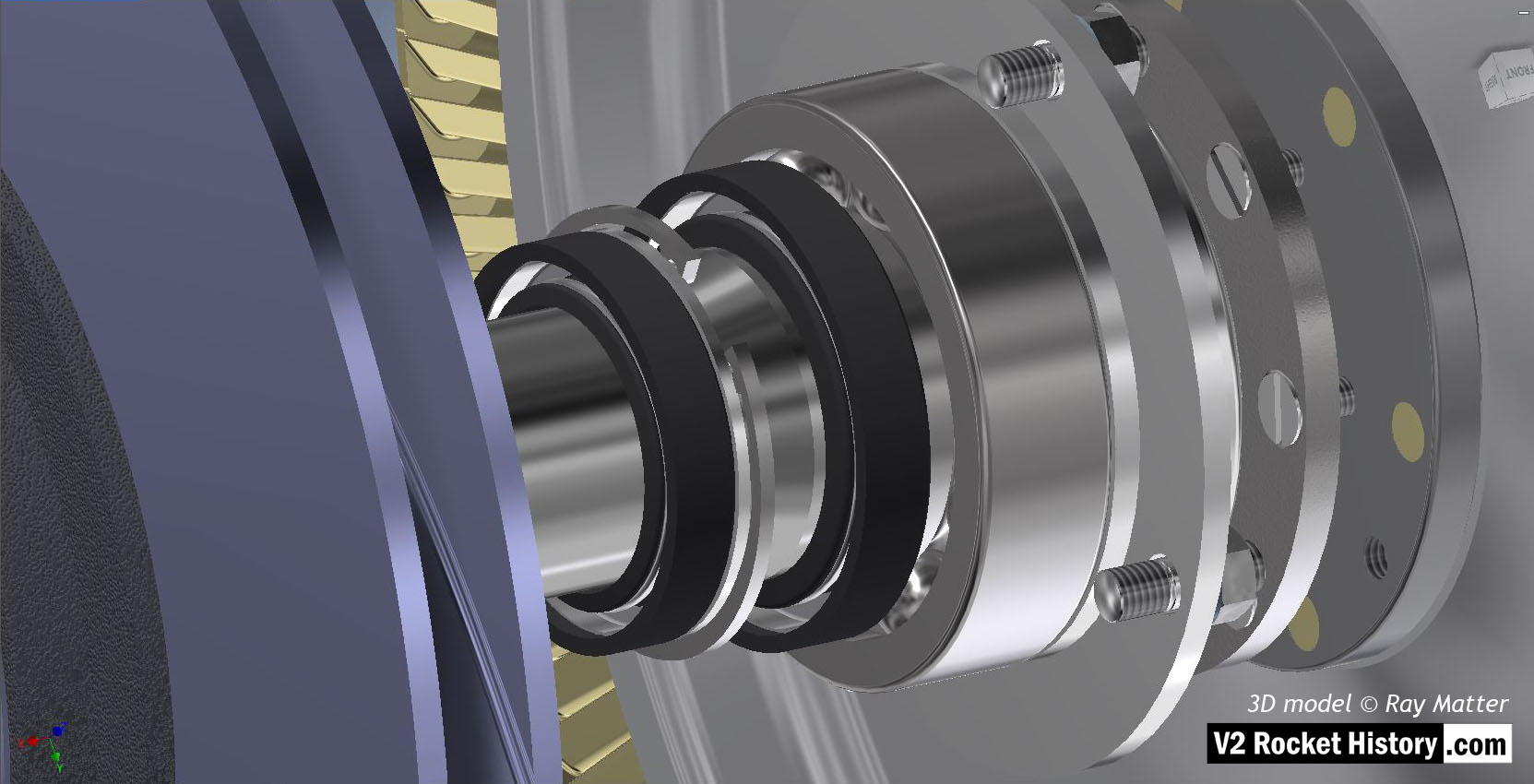
06 B Pump showing shaft area from fuel pump impeller, left (purple), to steam rotor. Shows seals, packer, circlip, and steam rotor hub. 3D model Ray Matter
Album | Turbopump 3D CAD |
Category | Turbo-pump |
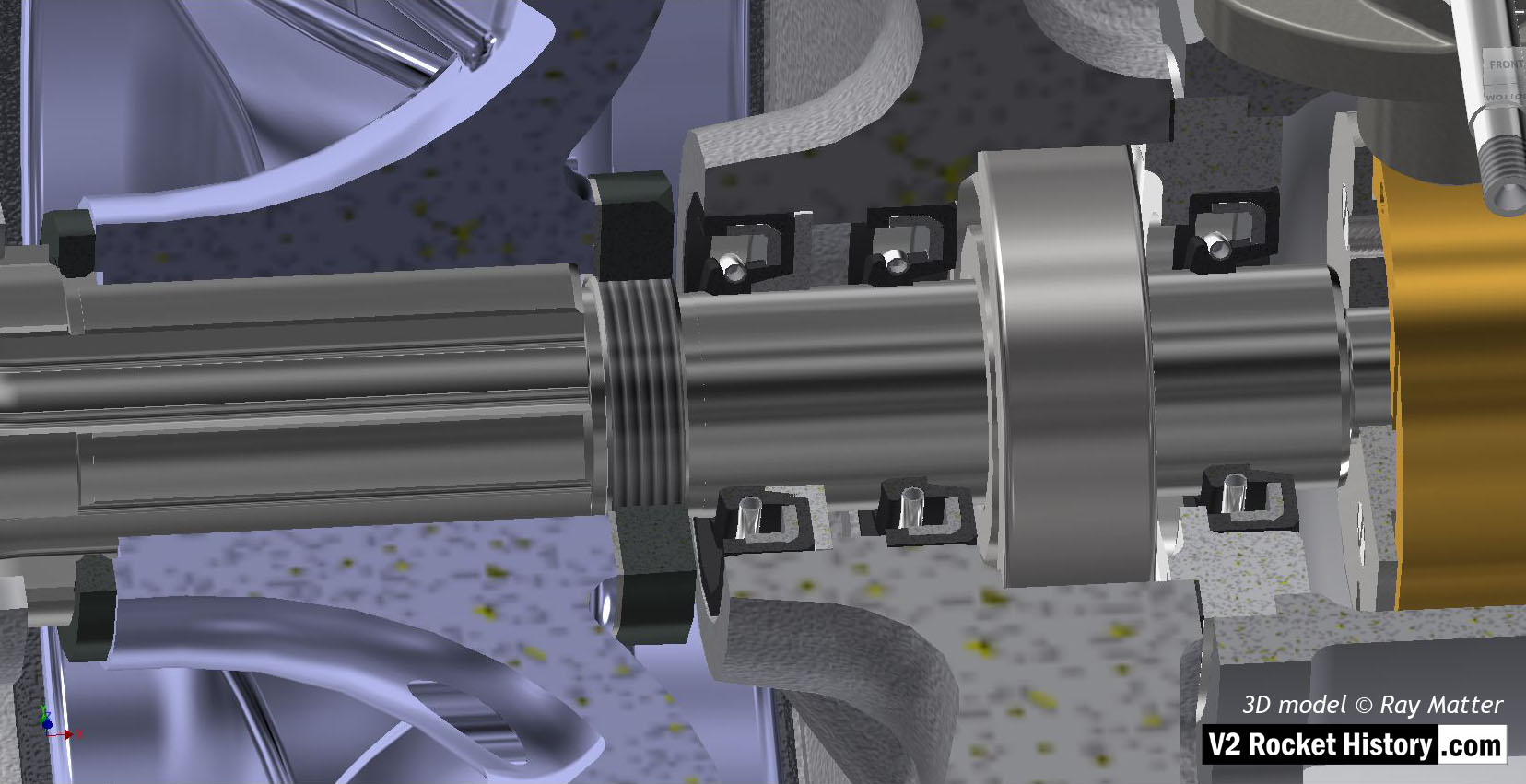
B (fuel) Pump: Close-up of sectioned pump impeller hub (purple) showing, left to right, seals, bearing and over-speed centrifugal rotor. 3D model Ray Matter
Album | Turbopump 3D CAD |
Category | Turbo-pump |
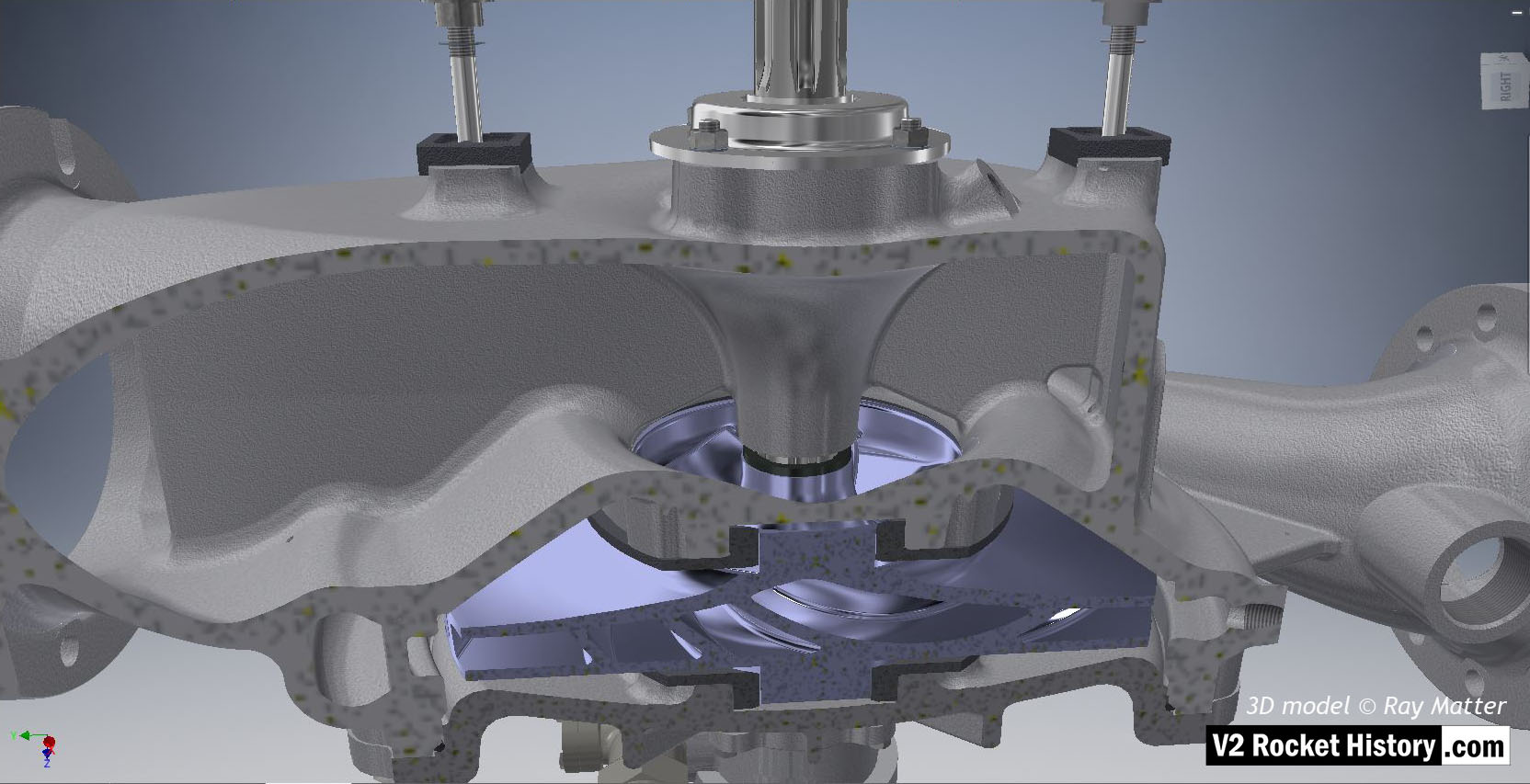
B (fuel) pump sub-assembly showing sectioned casing to reveal centrifugal pump impeller (in light purple for visibility). Outlet to right. Note inlet throat purge aperture of left. 3D model Ray Matter
Album | Turbopump 3D CAD |
Category | Turbo-pump |
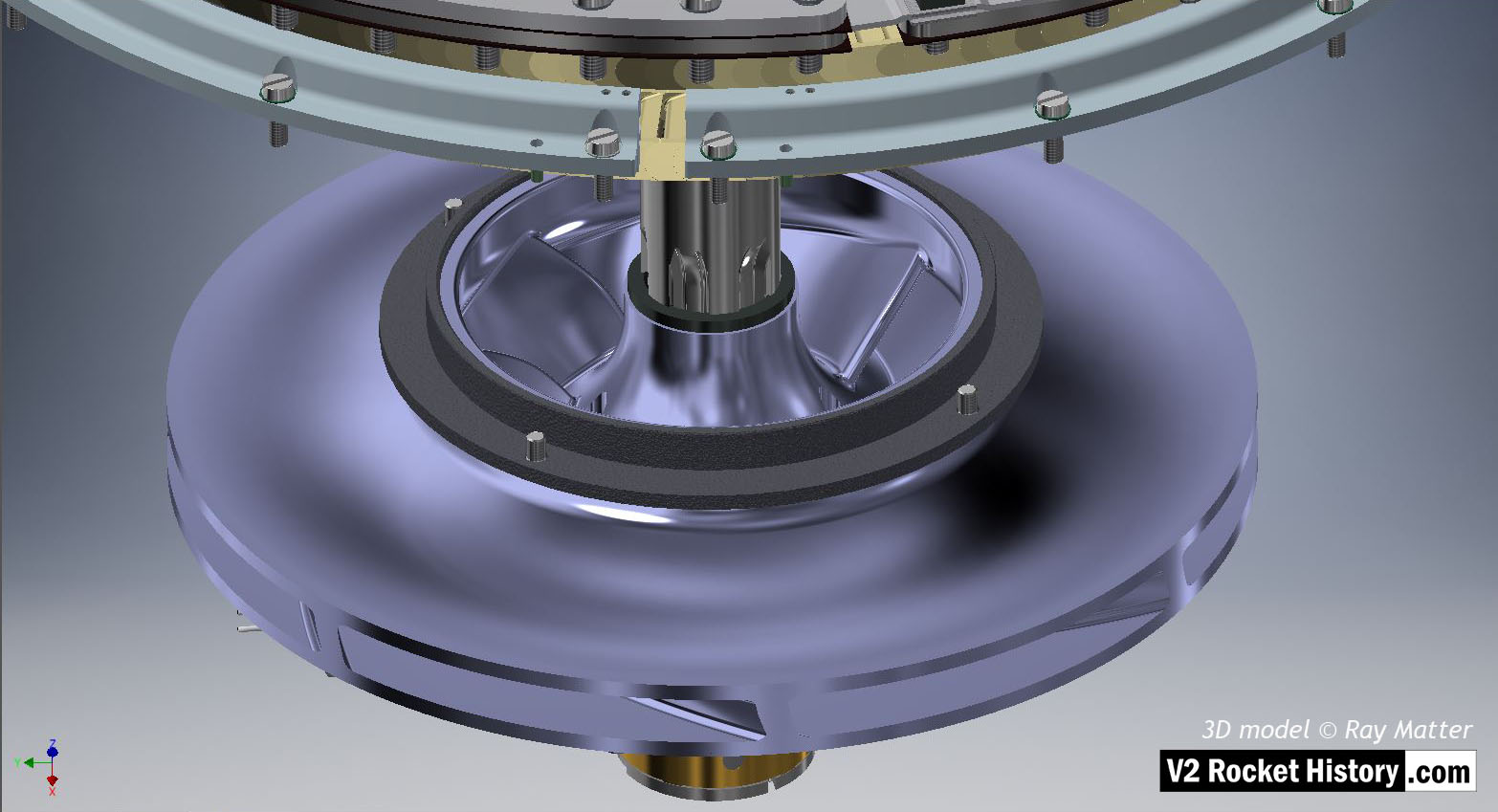
B pump casing removed to show fuel pump impeller and bearing ring. The steam rotor assembly can be seen at the top of the image and two sets of the stationary steam blades, or stators, are also visible.
Album | Turbopump 3D CAD |
Category | Turbo-pump |
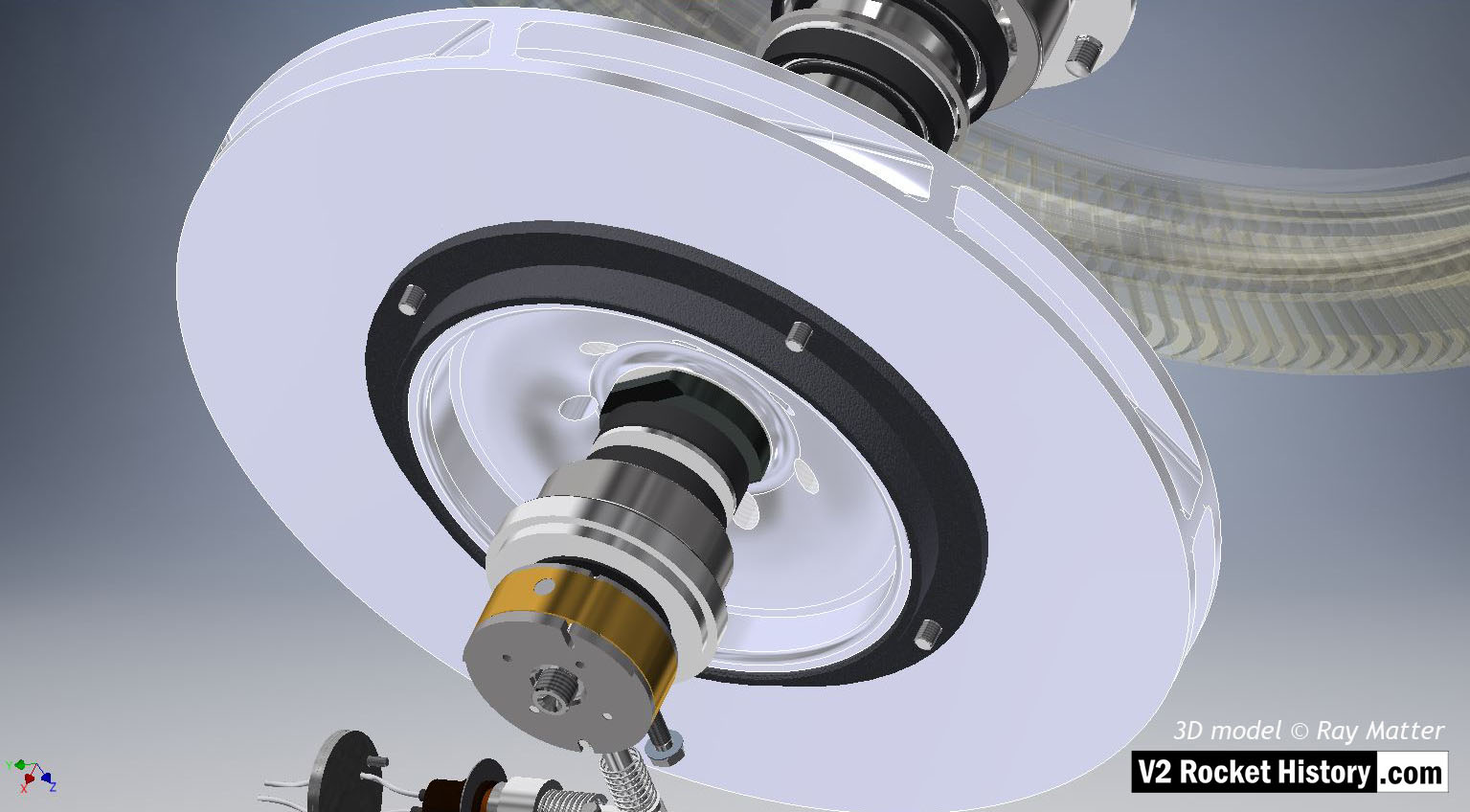
B (fuel) Pump exposed to show pump impeller, large bearing surface, and parts of over-speed device. 3D model Ray Matter
Album | Turbopump 3D CAD |
Category | Turbo-pump |
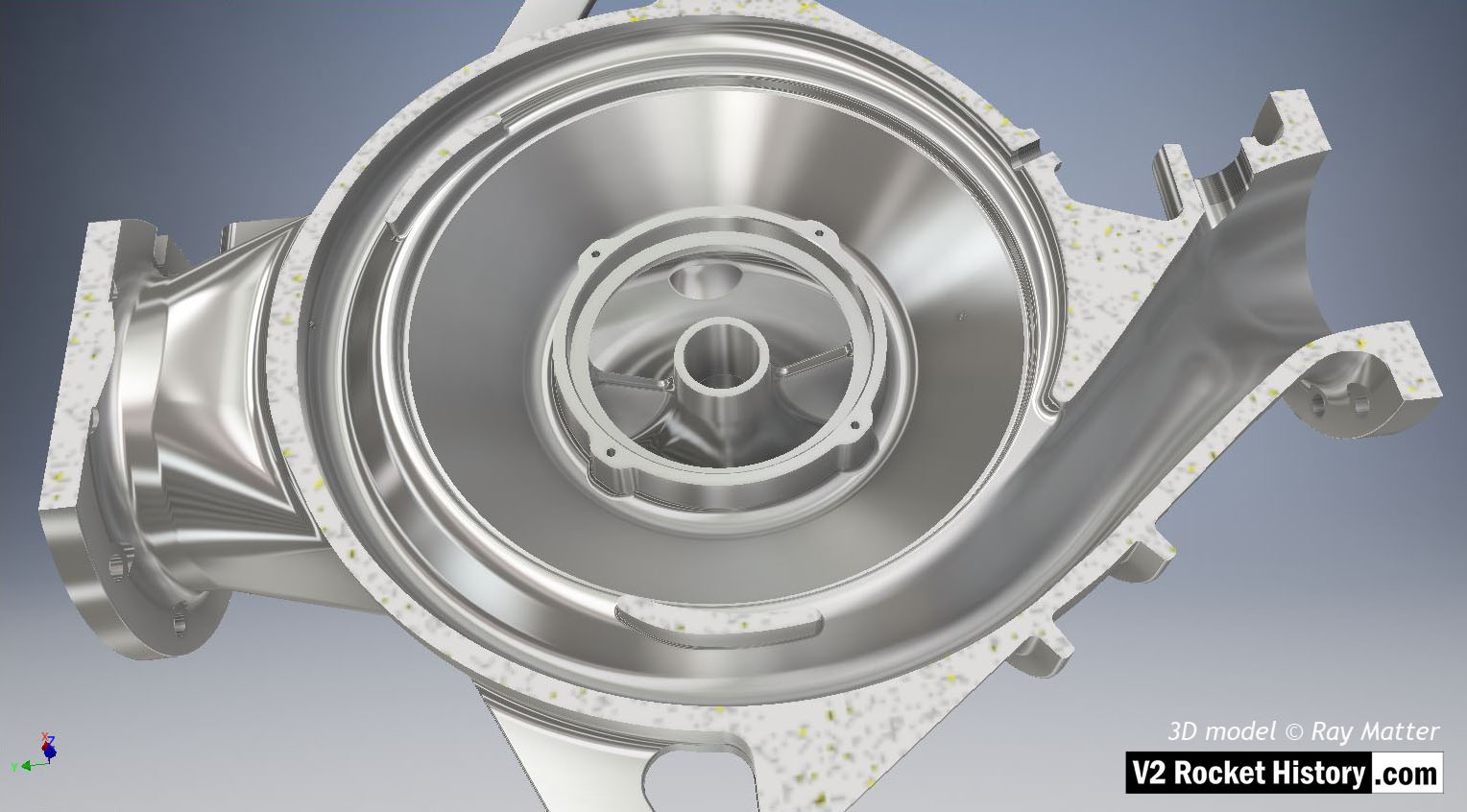
B pump housing from pump rotor side – notional surface polish to show shape and detail (such a surface was not used on the actual pump parts). The casing has been cut to show the internal rotor space detail. The outlet throat, right, and spiral volute space are displayed in this view as is the central fuel inlet. 3D model Ray Matter
Album | Turbopump 3D CAD |
Category | Turbo-pump |
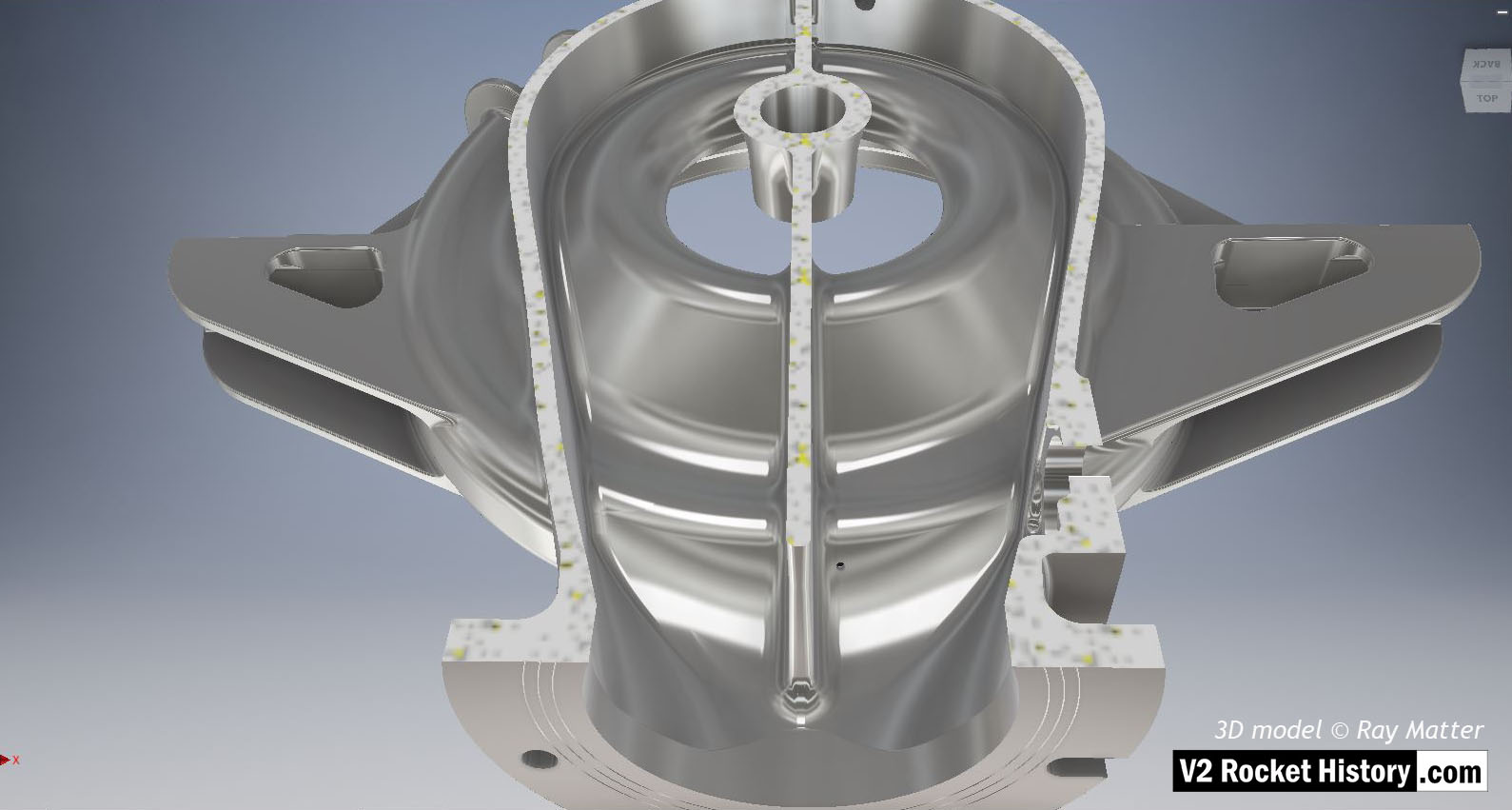
B pump housing with notional surface polish to show shape and detail (such a surface was not used on the actual pump casing). The casing nearest the turbine has been cutaway to reveal internal detail. The small self-purge orifice can be seen in this view, lower middle to the right of separator. 3D model Ray Matter
Album | Turbopump 3D CAD |
Category | Turbo-pump |
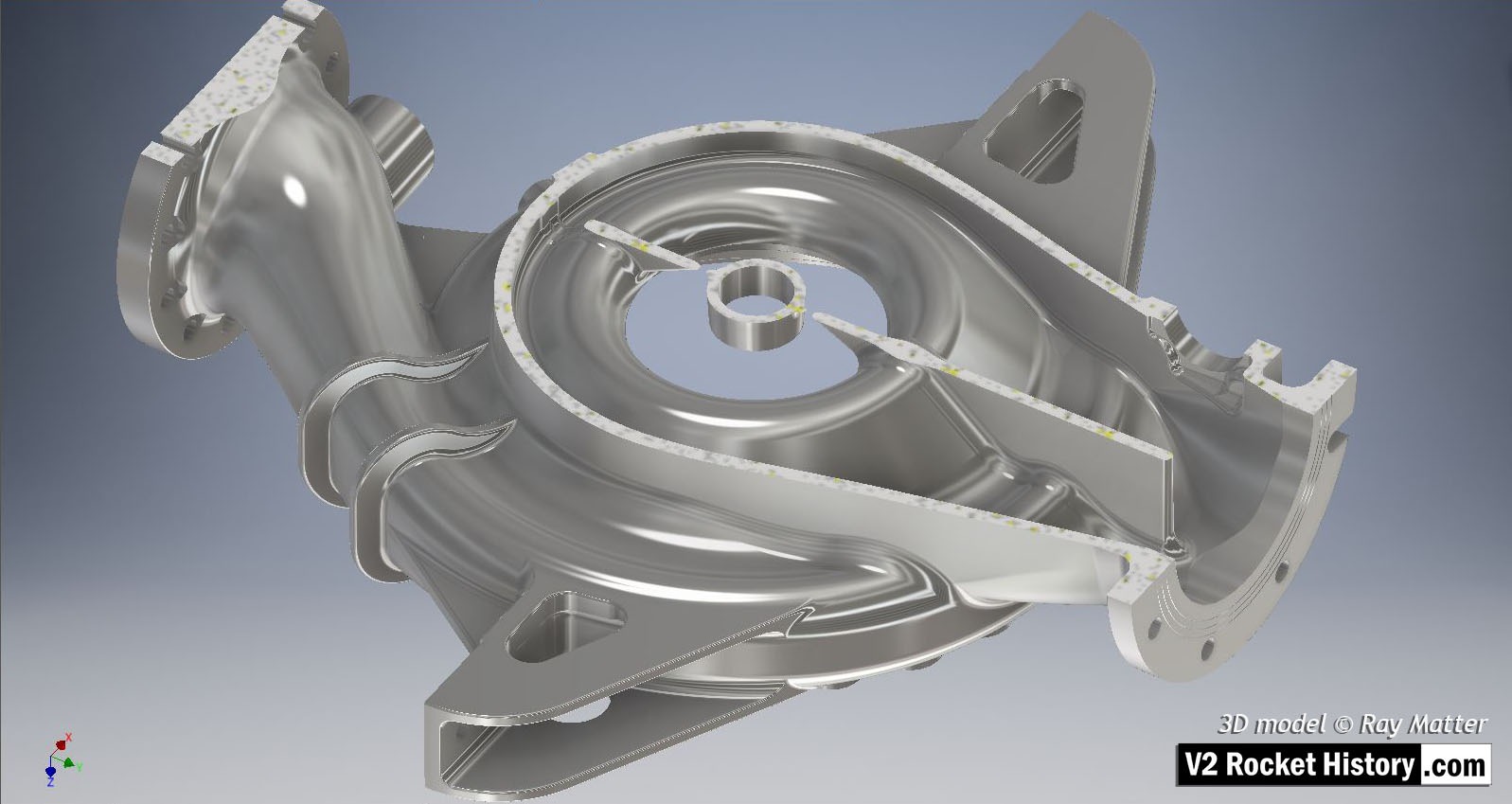
B pump housing with notional surface polish to show shape and detail (such a surface was not used on the actual pump casing). The casing nearest turbine has been cut to show internal detail. Inlet flange and split throat detail are clear in this view.
Album | Turbopump 3D CAD |
Category | Turbo-pump |

Valves
Images of the main valves involved in the propellant flow of the A4 / V2 liquid fuelled rocket engine
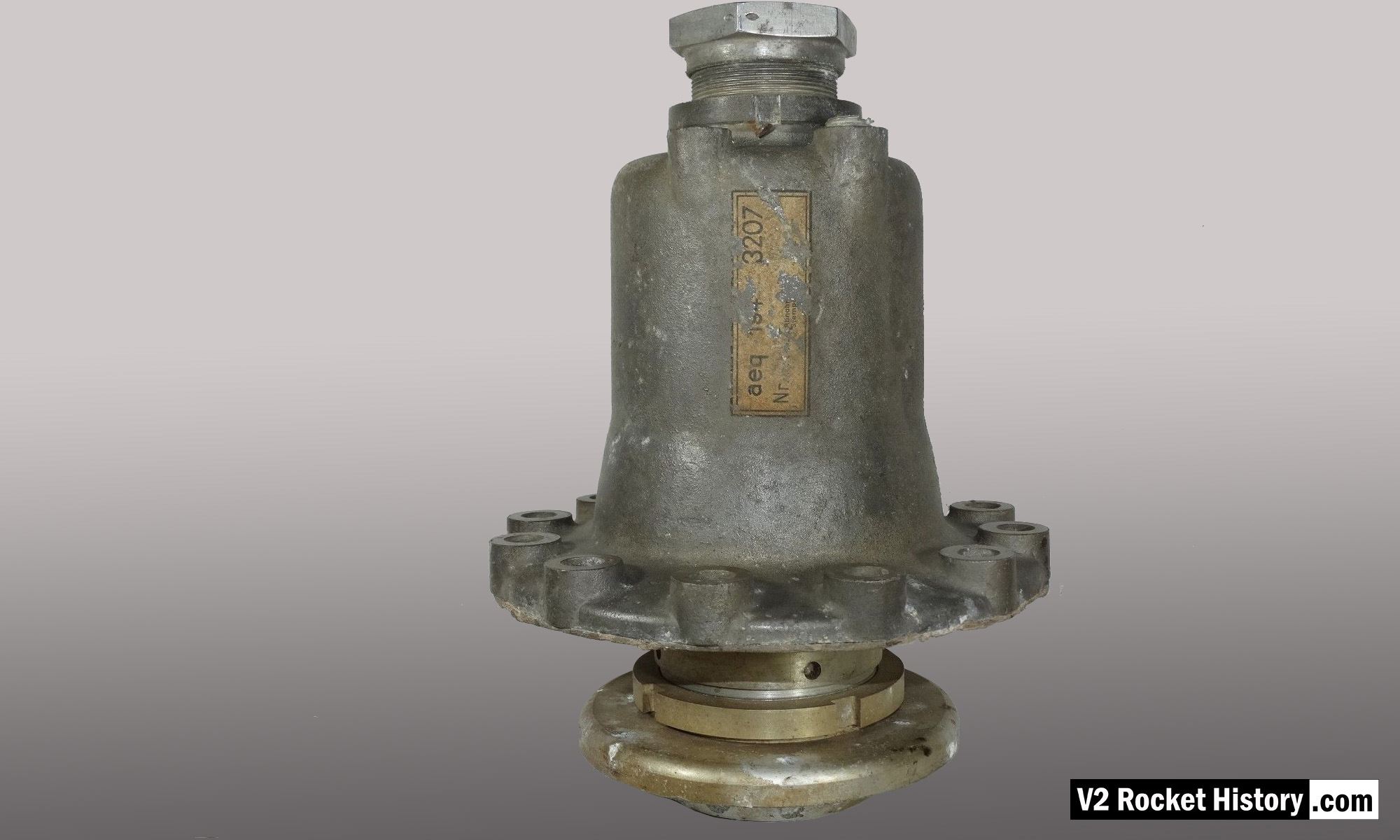
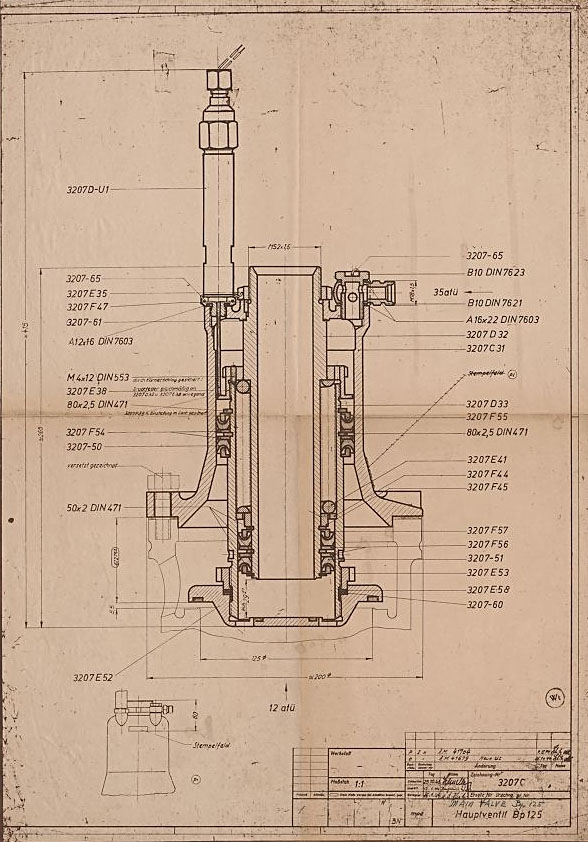
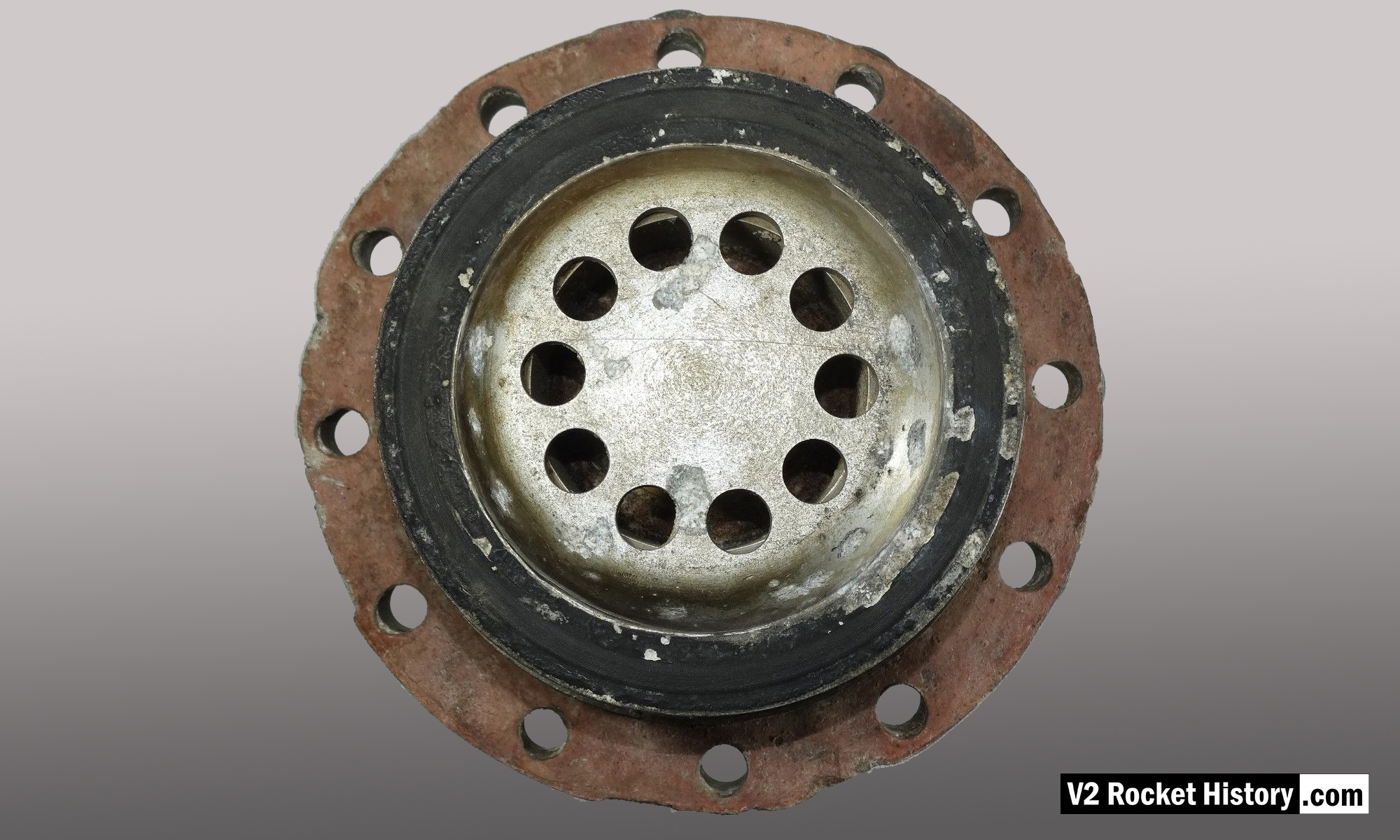
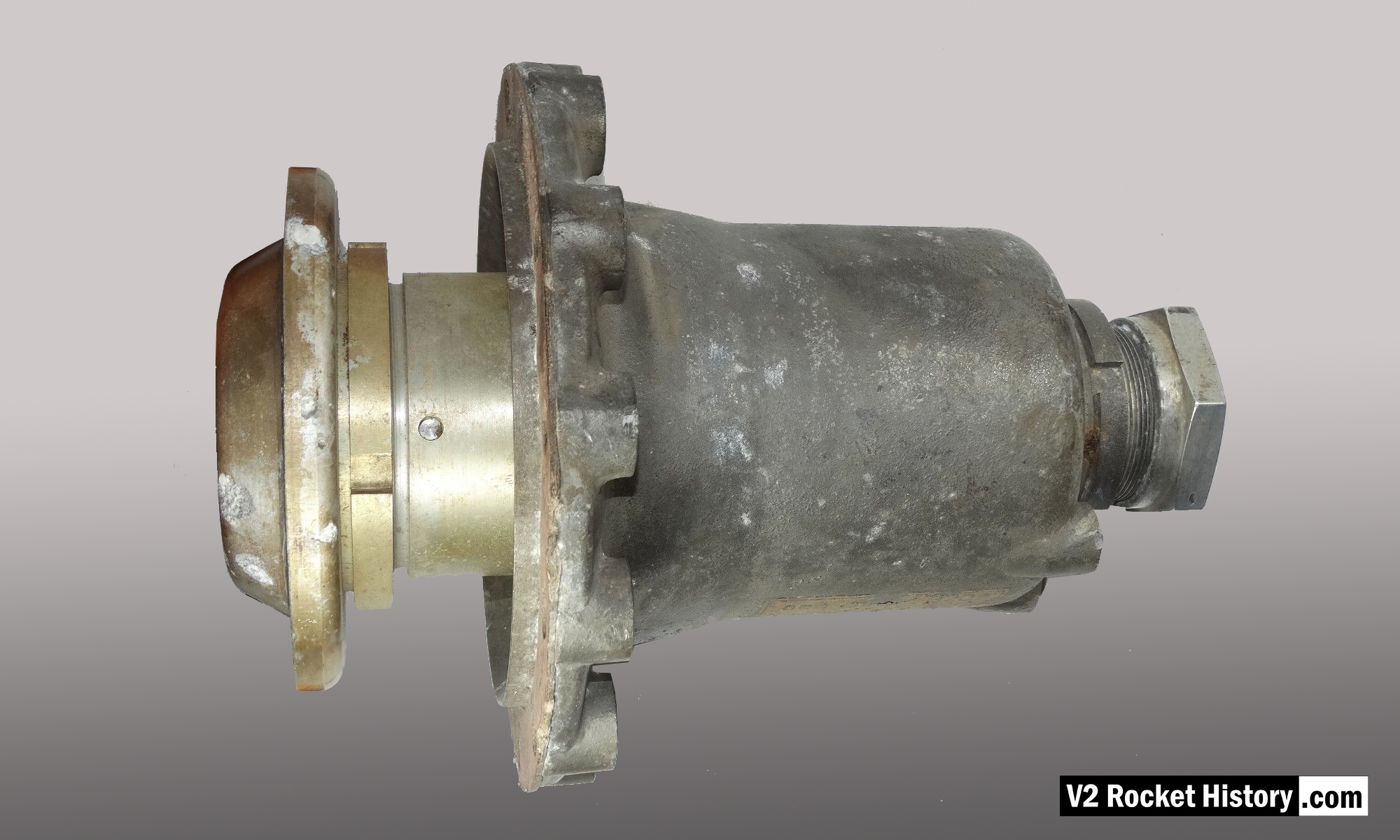
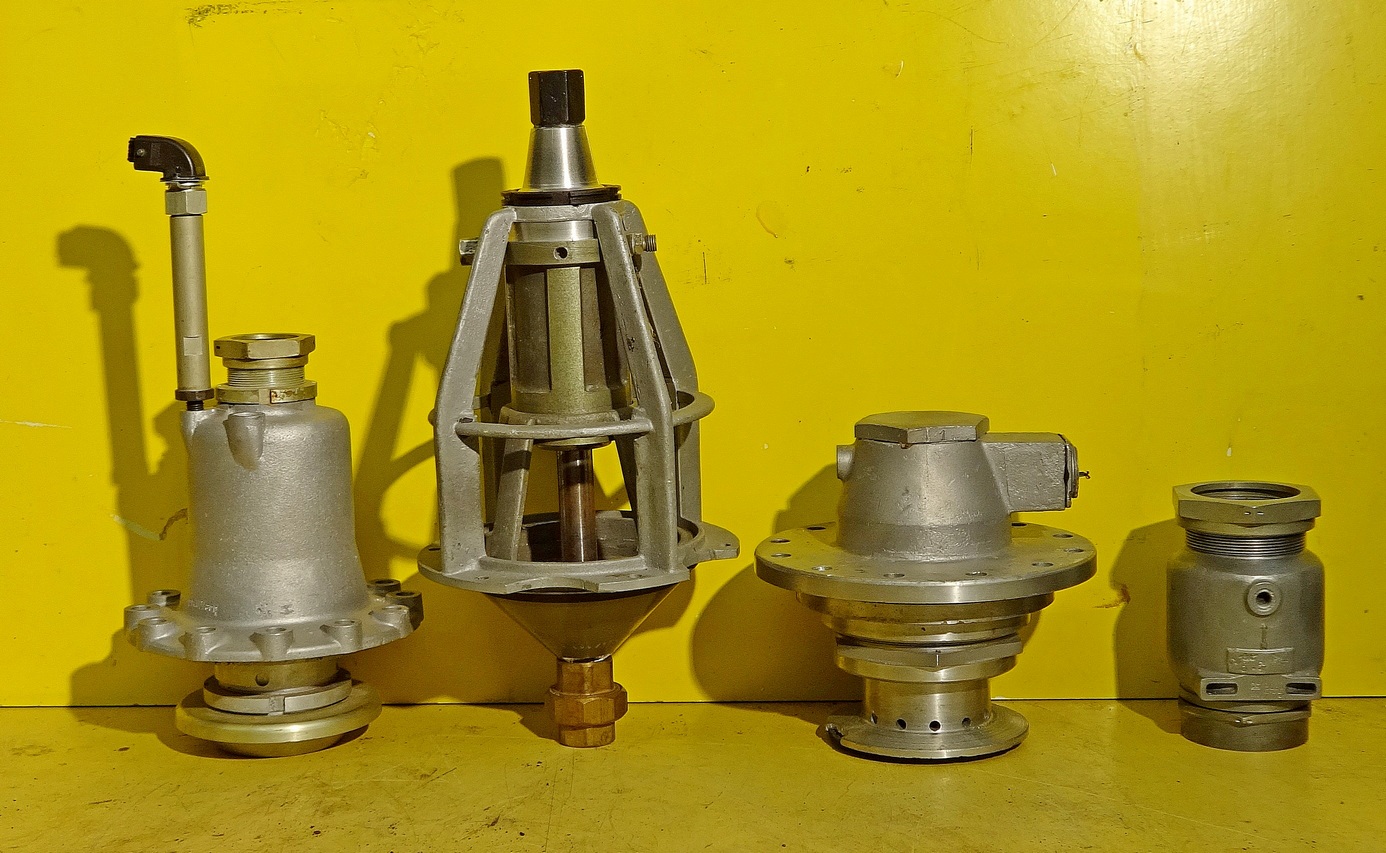
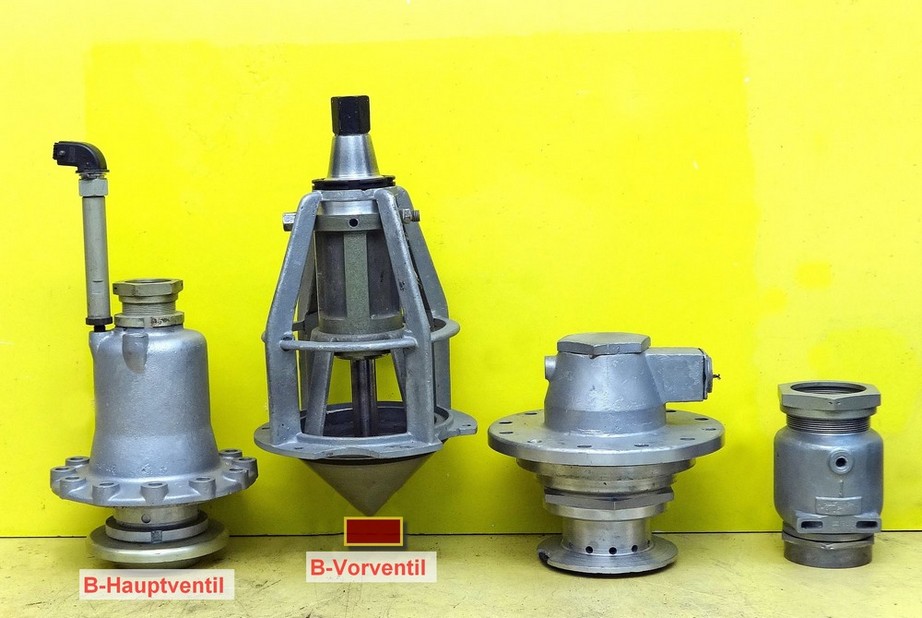
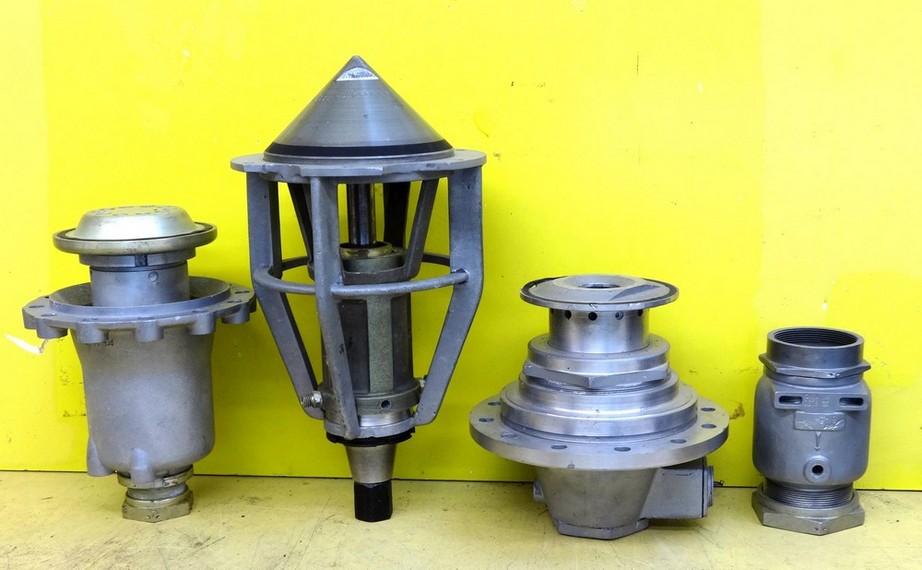
Images of the main valves involved in the propellant flow of the A4 / V2 liquid fuelled rocket engine
Relic of main alcohol valve with manufacturer code aeq (aeq = Bartoc & Co., Maschinenfabrik u. Giesserei Hedwikow,bei Caslau (Caslav) Czech Republic). An air (nitrogen) inlet pressure of 440 to 530 psi (30 to 36 Bar) was required to close this valve against its internal spring and the force of the turbo-pump. The large nut at the top is the connection for the fuel return (or ‘revolving’line) pipe, and the air and electrical input ports can be seen to the right (air), and left (elec.) just below this point. V2RH image

Anatomy of the V2: 18-pot injector head
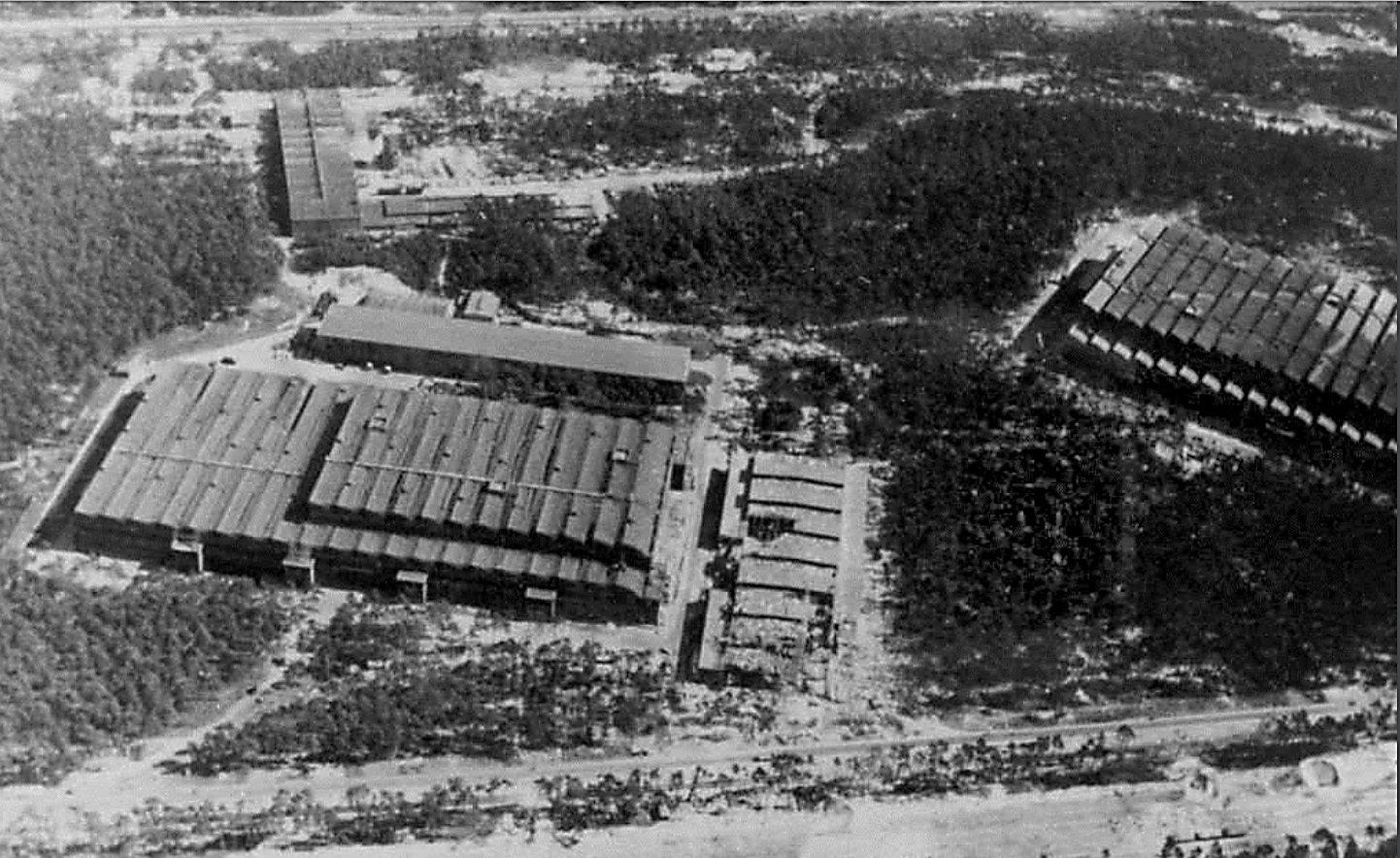
Photo showing Werk Süd with IW on the left and F1 on the right taken on 19th August 1943. The photo shows only light damage to the main halls, although F1 was actually hit at least 11 times, and hits to the separate single storey workshops to the right of the IW hall. The long storage (oil and paint?) shed above IW and the woodworking shop at the top of the picture appear undamaged. Anti-aircraft platforms (at least 3) can be seen on the roof of IW but that seem to be empty of guns. F1 shows two AAA platforms (there was at least 3 at this stage and maybe more) and they may have guns installed. General W. Dornberger mentions defensive AA artillery fire from the from the roof of F1 in his 1952 book V2 (1954 in English).
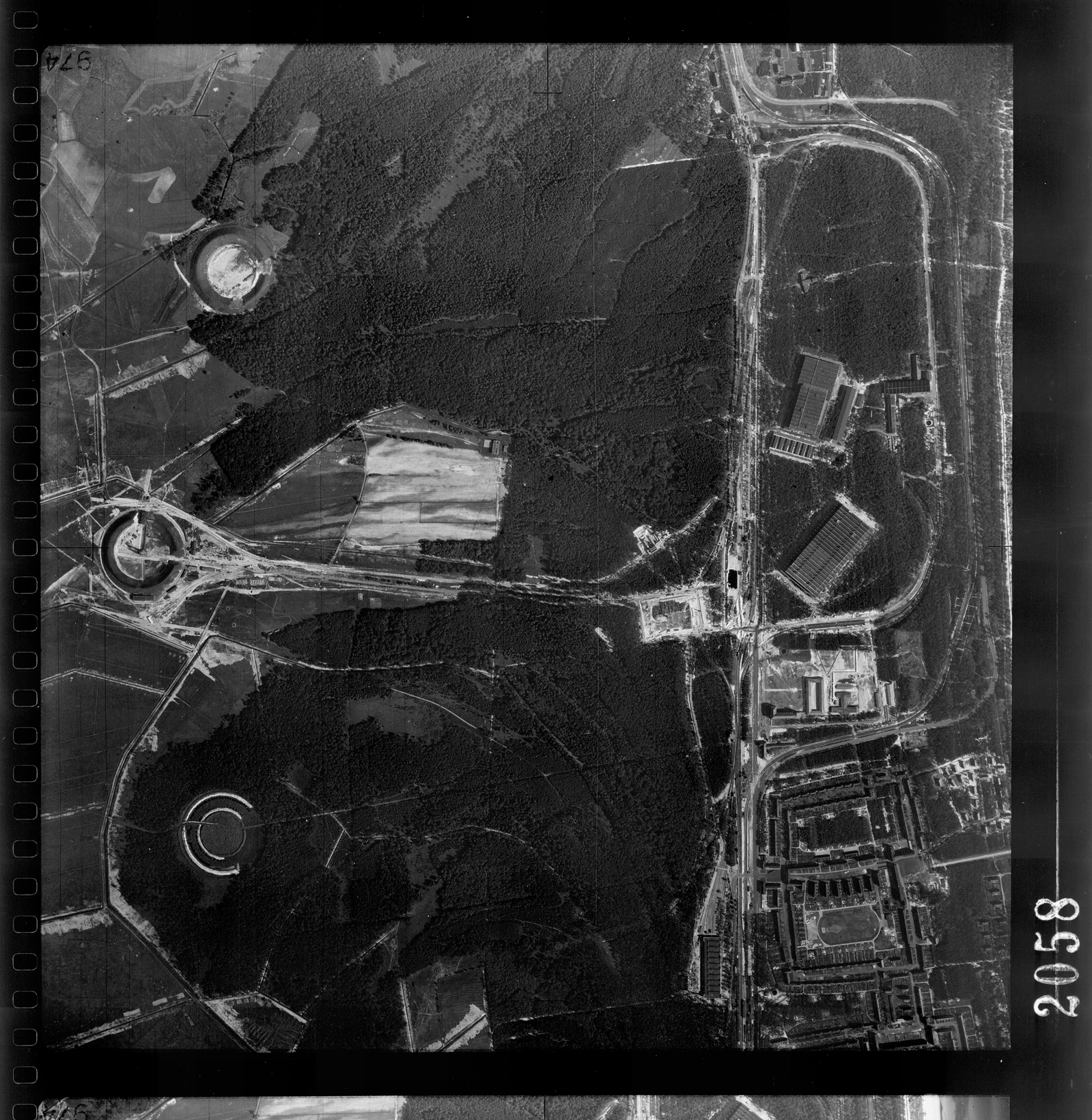
RAF reconnaissance photo showing the Werk Süd region with the F1 pre-production hall and to the north the IW repair and maintenance hall, centre right, and road rail links to Prüfstand XI (Test Stand 11, circular rampart centre left) heading directly left from F1. P-XI was conceived to provide engine test facilities for the nearby pre-production hall. Scroll down to see GPS map, the marker index is set to the centre of P-XI, click map and switch to satellite view and you will see that only a small section of the circular rampart remains visible. You can easily zoom out to cover the coast area where F1 and the equally large Repair & Maintenance Workshops are located. The area immediately surrounding P-XI is now contained within a commercial farming operation with sheep appearing to be the staple – or was anyway, at the time of our first visit to the vicinity in 2010 and our last in 2017 – none of the sheep seemed to recognise us though so they may have changed. (for access to restricted areas click here)
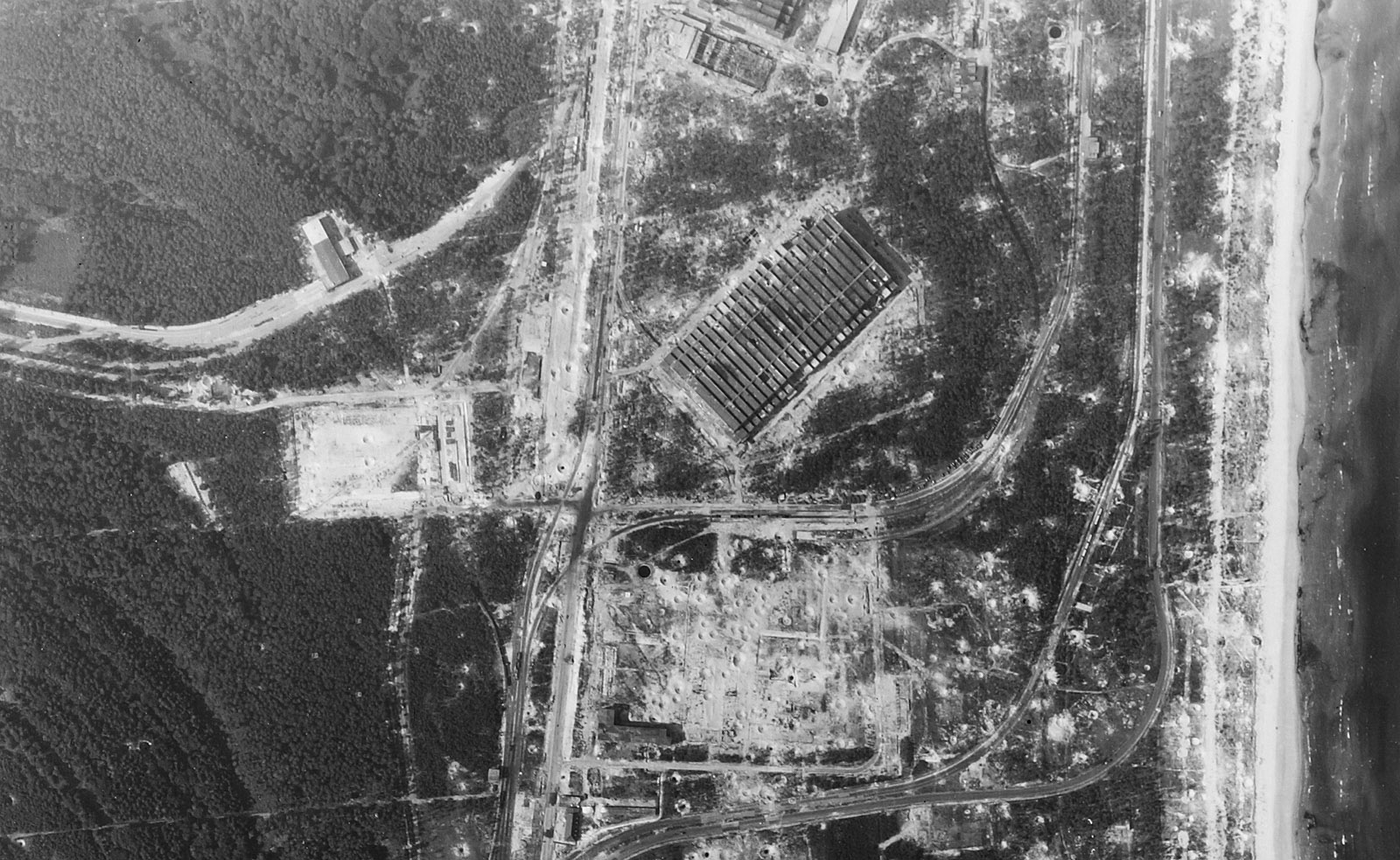
RAF Recce photo taken 21st August 1944 of region around F1. The GPS marker for this photo is pegged on the lowest of the three fire fighting cisterns clearly visible in the image (in the center about a third the way up from the bottom of the image). Scroll down below this text for map and switch to ‘Satellite view’ where the fire fighting cistern can still be clearly seen today.(for access to restricted areas click here)
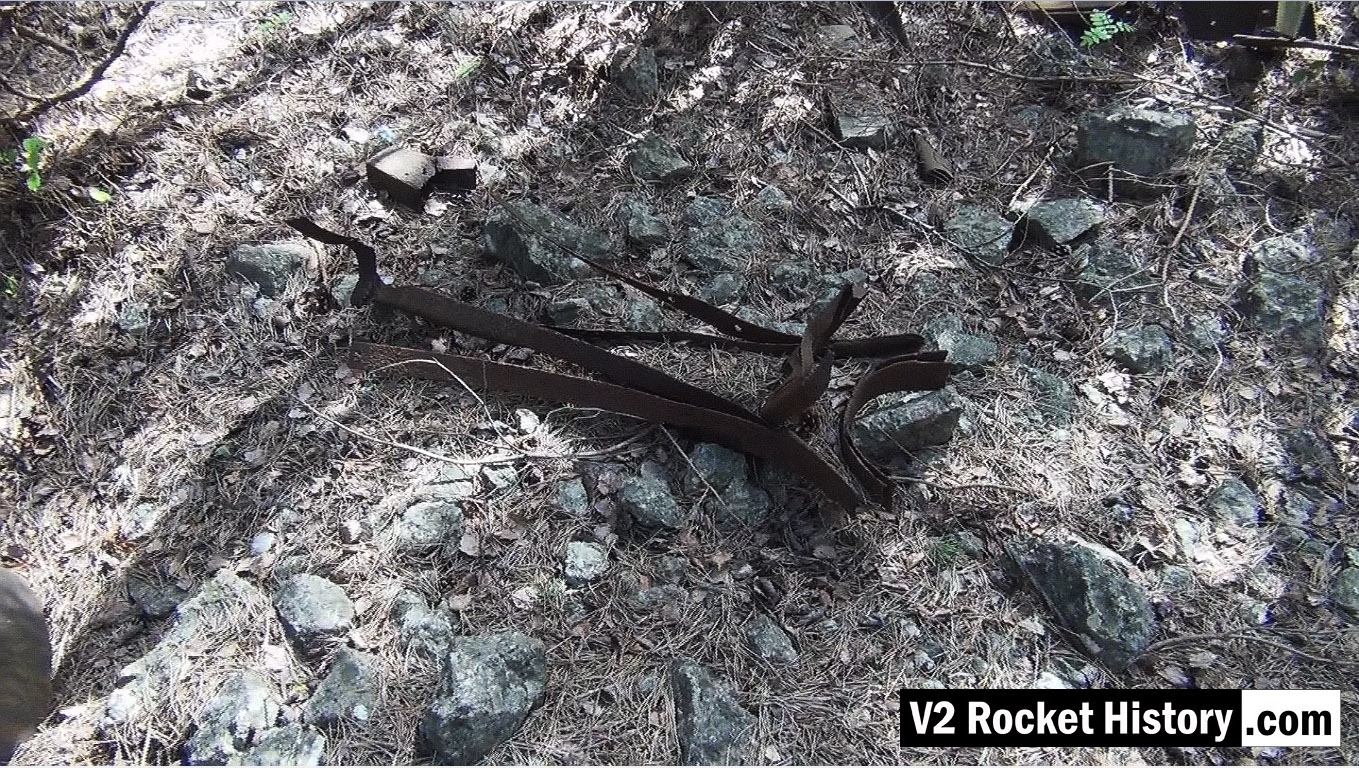
Picture shows parts of V2 missile fin structure laying on open ground near area between admin offices and F1 (near Admin. block railway platform, see map).
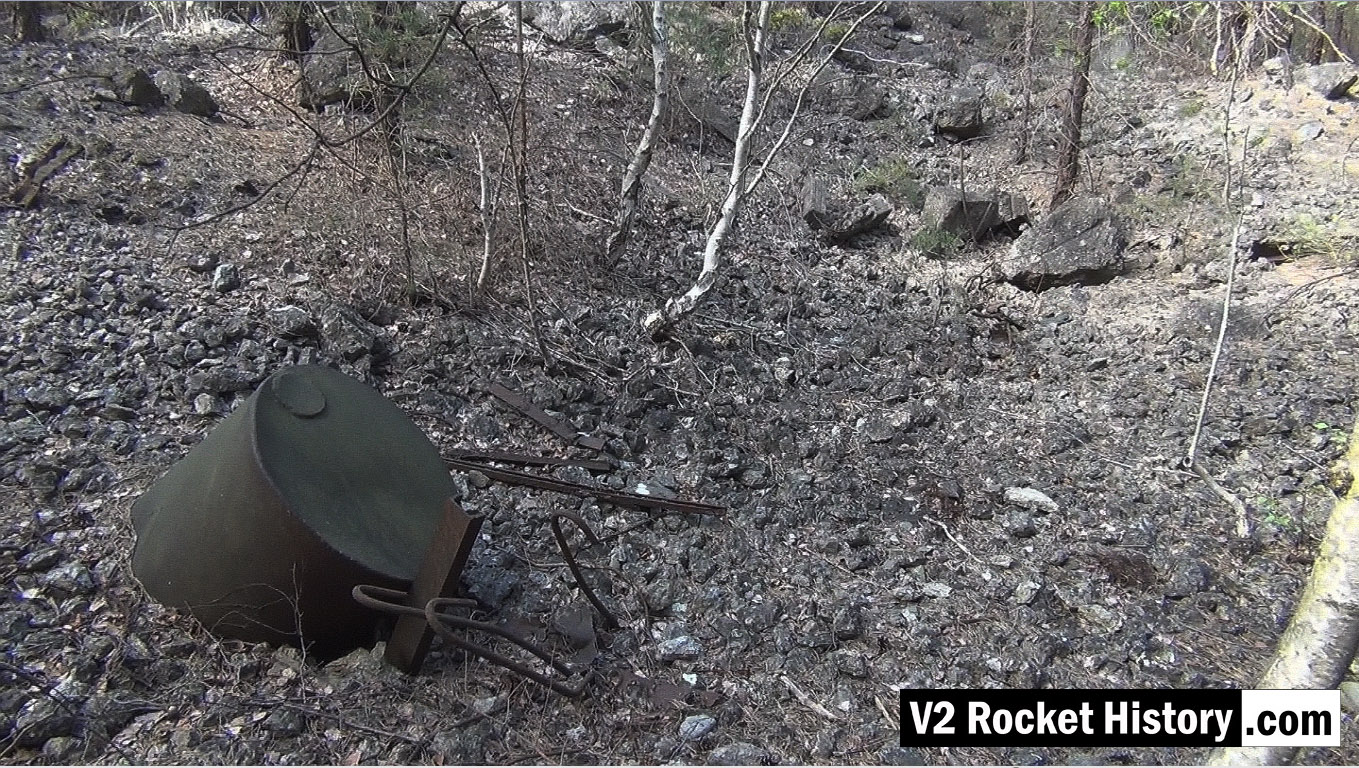
Picture shows metal debris within the F1 factory boundary walls. The purpose of the part buried liquid storage vessel in the foreground is unknown but it is not a vessel capable of being pressurised. Other assorted metal debris include pipe and cable wall cleats, as well as steel armature rods from reinforced concrete castings (powerful demolition explosions have freed the steel rods from the concrete). These reinforcement rods are a common sight in the environs of Fertigungshalle Eins (F1) and the nearby Repair & Maintenance Hall (R&MH).

This picture shows a small debris field of steel fragments from the V2 missile 130m South-East of F1, and just 20m to the North East of the foundations of a small heat distribution building. Various body and frame parts can be seen and in the middle foreground a 350mm segment of curved missile body ring is visible. These parts have almost certainly been dug up and exposed by the action of metal detectorists. The metal fragments have been abandoned by their finders as they are perceived to have no financial value and hence are not worth removing from the site.
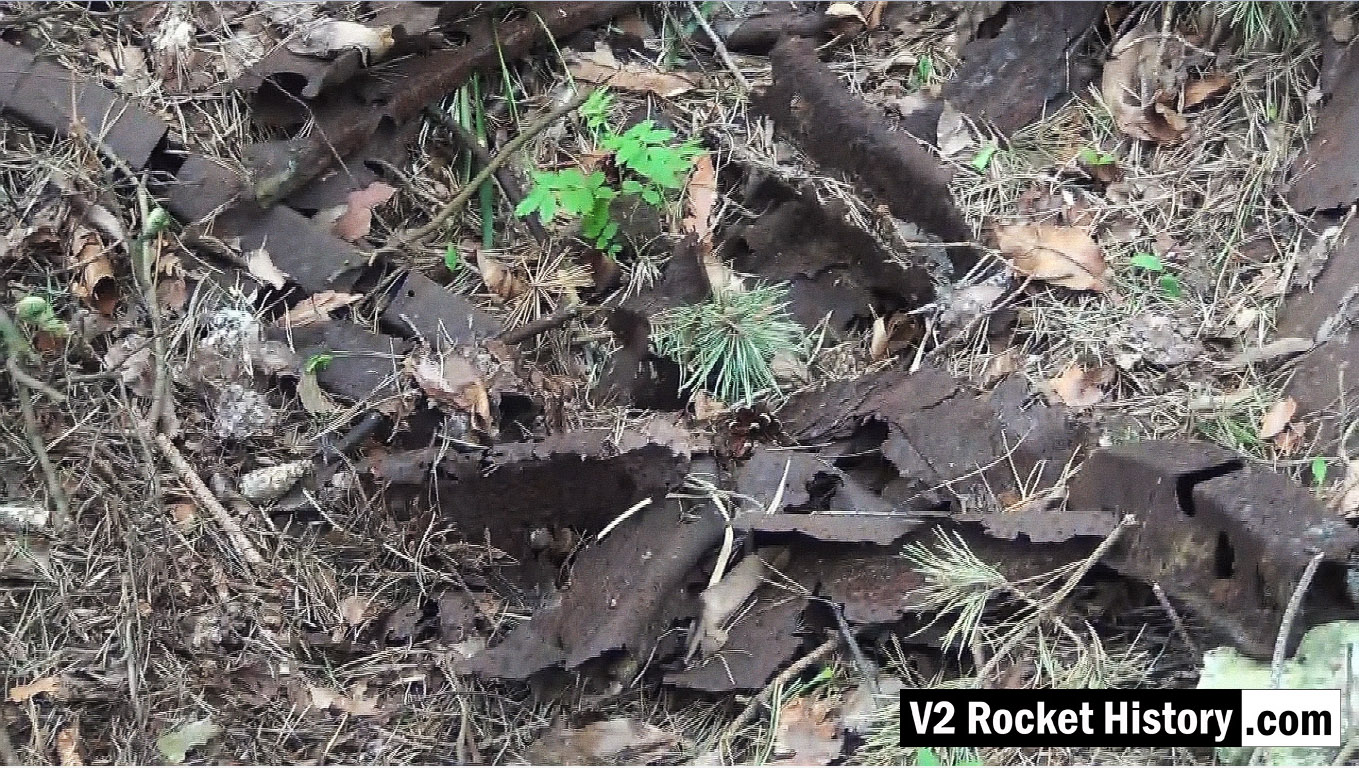
This picture shows a close up detail of parts in a small debris field of steel fragments from the V2 missile 130m South-East of F1, and just 20m to the North East of the foundations of a small heat distribution building. Various body and frame parts can be seen and in the upper left and two segments of curved missile body ring are visible. See previous.
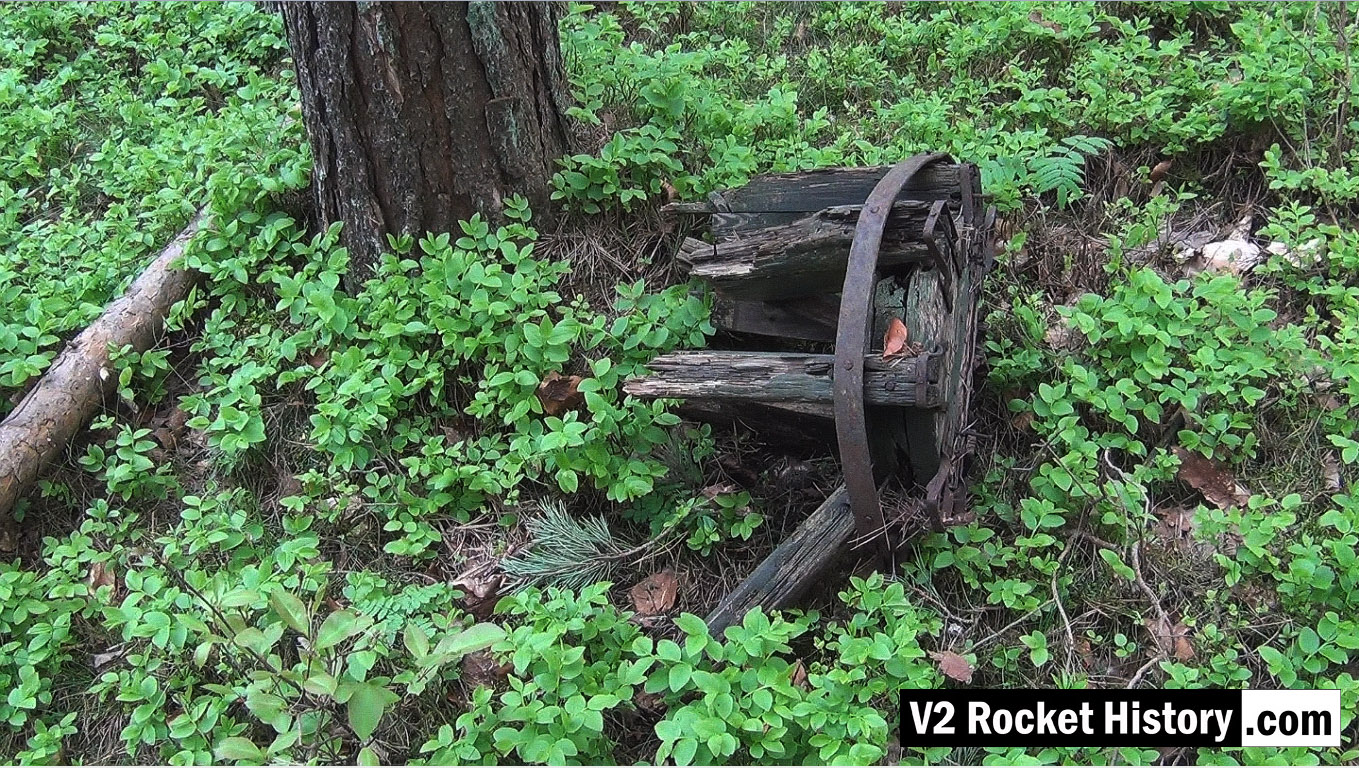
Wooden carboy frame from WW2 (possibly used for transporting small quantities of corrosive and dangerous liquids employed in the V2 steam plant, (such as T-Stoff) laying among trees 190m East of F1 in a location used as an emergency rail freight loading area to F1 due to damage caused by US air raids in August 1944.
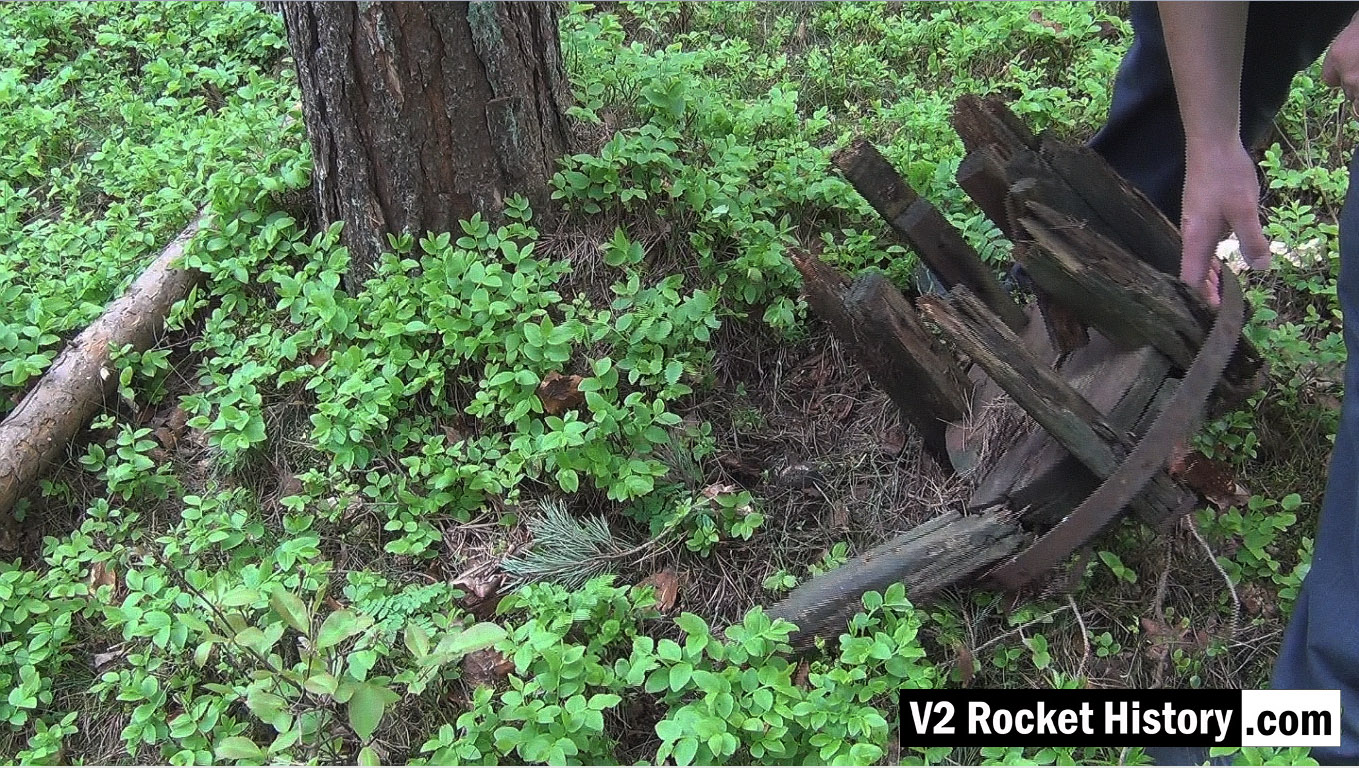
Wooden carboy frame from WW2 (possibly used for transporting small quantities of corrosive and dangerous liquids employed in the V2 steam plant (such a T-Stoff) laying among trees 190m East of F1 in a location used as an emergency rail freight loading area for F1 due to damage caused to rail track by US air raids in August 1944.
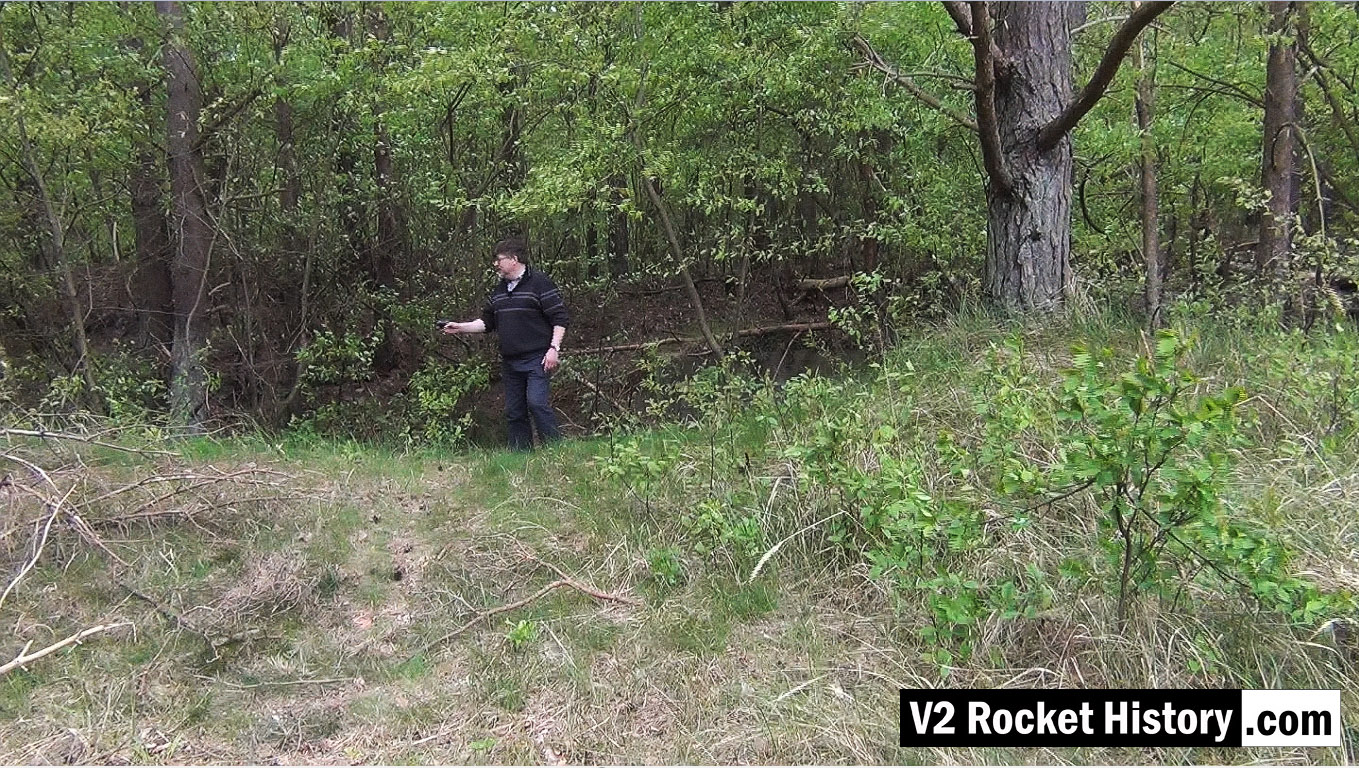
This picture shows Robert Dalby collecting GPS data with a mapping camera just North of the East end of the Admin office rail platform (near the ruins of the small admin/F1 heat distribution hub building). In all of our explorations we routinely collect GPS track and data points to be able to accurately locate finds and establish a precise correlation between areas of interest identified on historical reconnaissance photography and the modern ground terrain. In the picture Robert is pointing a Contour video camera at details of the terrain that automatically captures the camera’s GPS location information. This data can then be combined with satellite imagery, via Google maps, and provide a detailed graphic mapping track alongside the video footage.
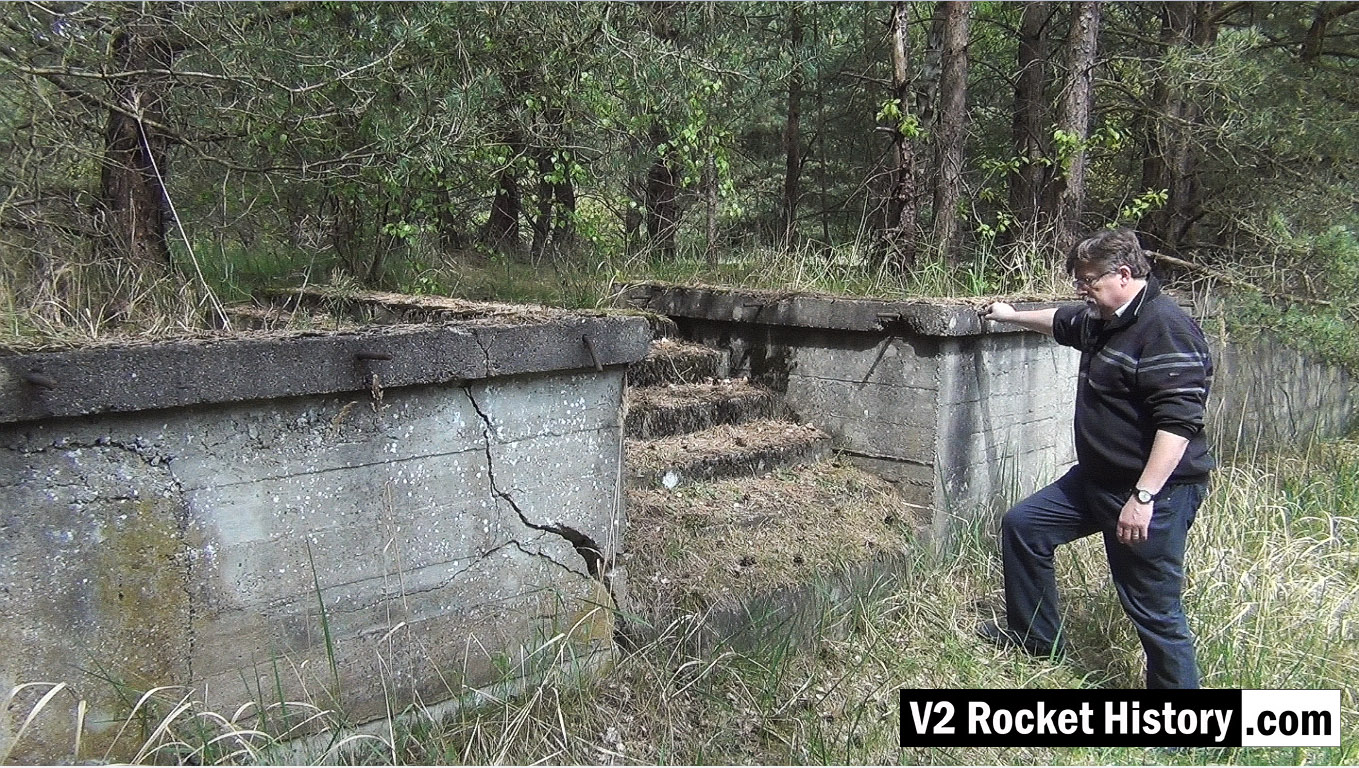
This video screen grab shows Robert about to climb the steps up onto the rail and road loading station 9 (also called Die Verladerampen or in English, The loading ramps). This storage and loading facility was never finished during the war and was intended to be a more elaborate with large storage buildings – but the pressure of war and constant use of the area prevented further development. The area is still surprisingly intact today with a strong correspondence between modern ground detail and historical reconnaissance photography.
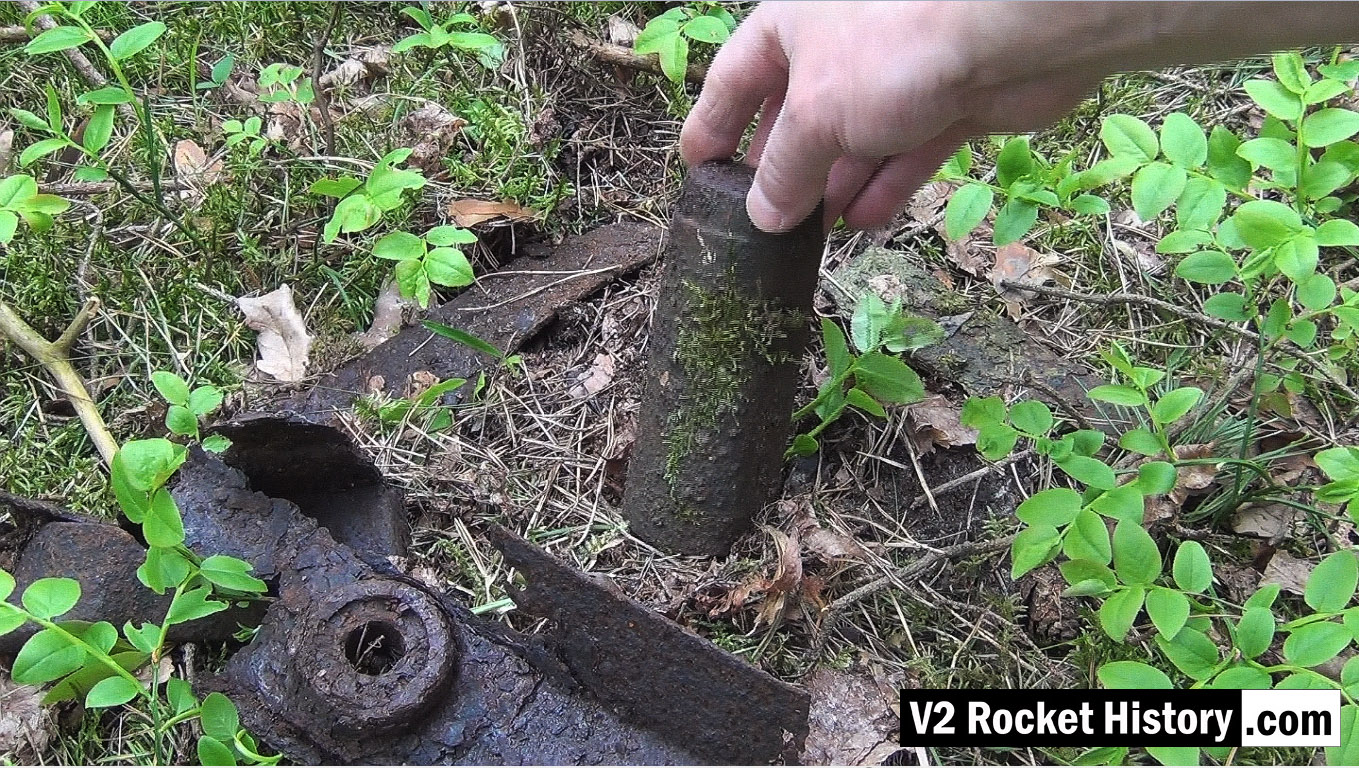
V2 missile parts in F1 prisoner ‘exercise’ area. Image grab from Fertigungshalle Eins (F1) video.
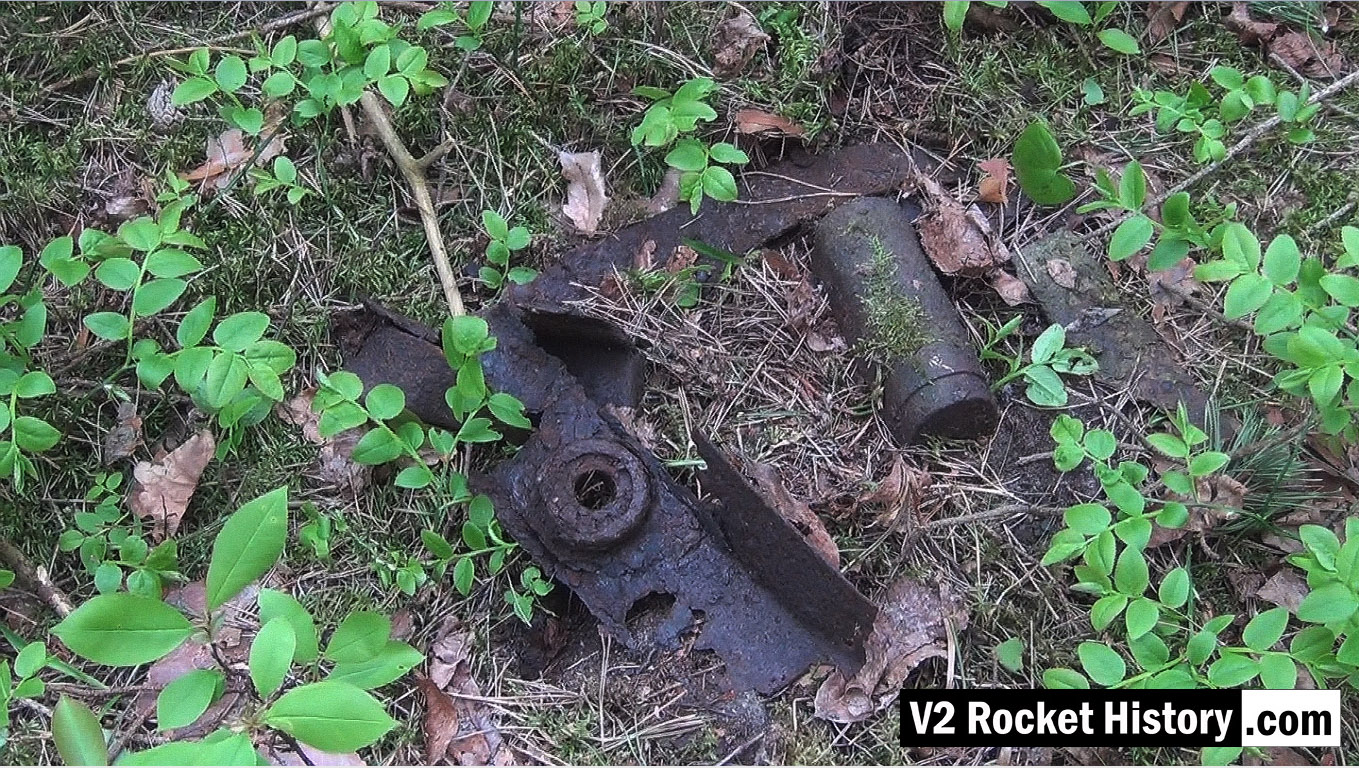
V2 missile parts in F1 prisoner turn-out or ‘free movement’ area. The location referred to is a large triangular shaped area situated on the South-East side of the pre-propuction hall Fertigungshalle Eins (F1). The area was fenced off with a high barbed wire fence (a portion of which was electrified) with guard towers every 60 metres.
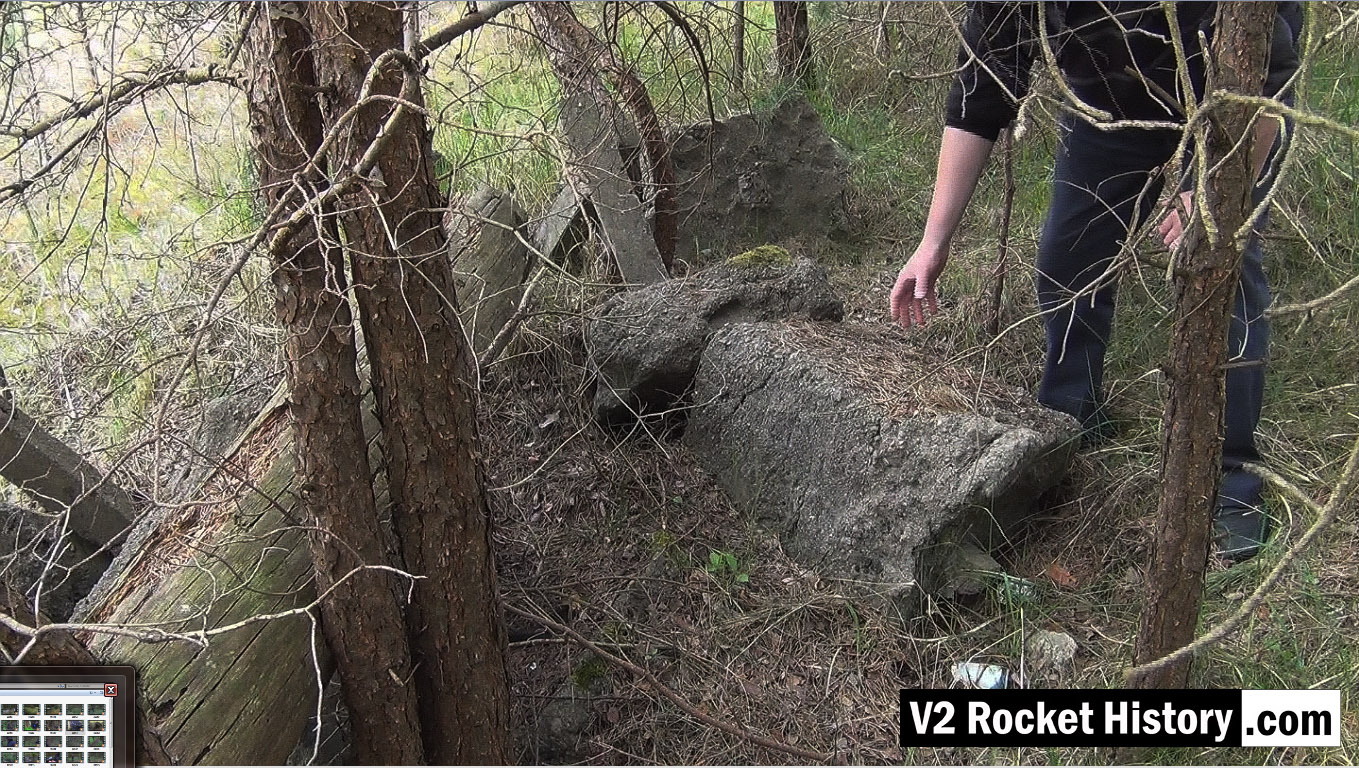
This image shows part of a pile of concrete castings that form the below ground foundations for part of the electrified fence that was built around F1 in the summer of 1943. The fence was built on the instructions of Arthur Rudolf, who was responsible for F1, by the first 200 forced labourers to arrive at the F1 labour camp in June 1943. These crude castings are the result of digging a narrow hole in the ground for the concrete fence post and filling the area around the post with the concrete mix. The sizable variation in the depths of the concrete castings, and the fact that in a number of casting blocks the post has plunged through the concrete mix and penetrated from 100 to 300mm into the ground below, strongly suggests this work was carried in hast and/or by men inexperienced in the normal procedures of this type of basic ground-work.
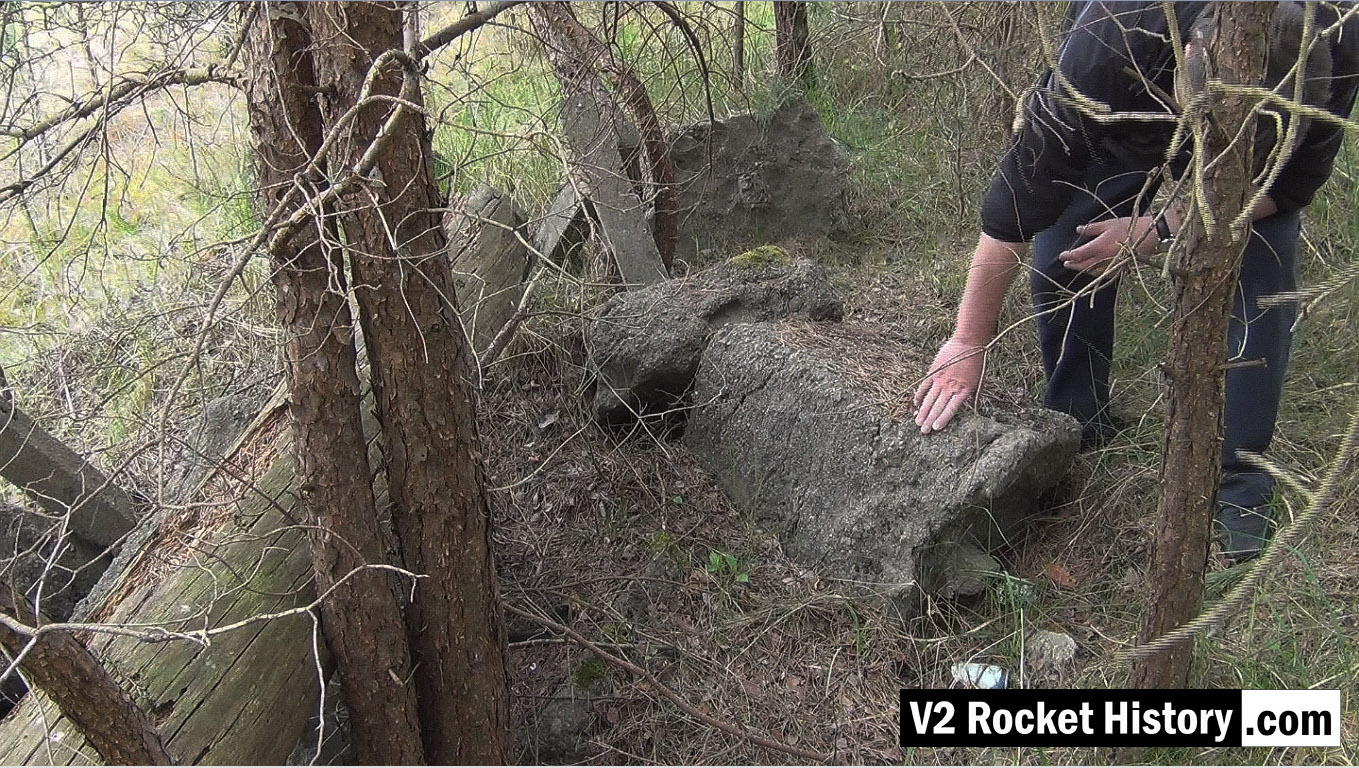
This image shows part of a pile of concrete castings that form the below ground foundations for part of the electrified fence that was built around F1 (see previous photo for details). You can see the area that these posts once secured in the second black and white recce image in this gallery. The fenced off area is the large triangular shape you can see joining the North-East South-East corners of F1 (ie the long wall of F1 facing the shore). Quite why and exactly when someone mustered men or machines to pluck these lumps of concrete out of the ground and move them 100 to 200m is beyond me – why not just bulldoze them under like everything else on this site?
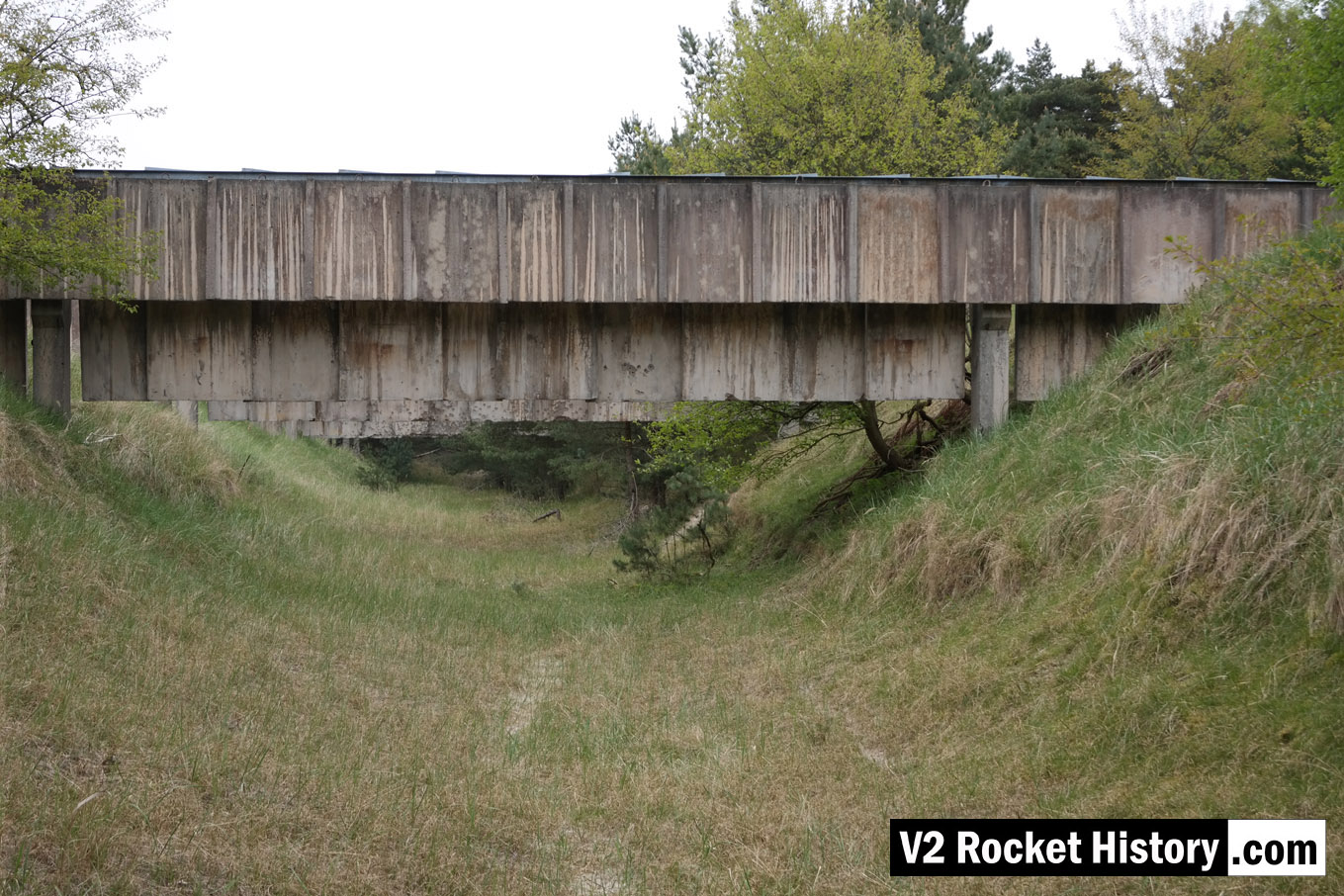
Photo shows the remains of a shooting range built by the East German Army. In 1944 the area about 200m in front of the camera and to the left of this picture is the emergency rail-loading area used after US air raids in August damaged rail lines and other regular freight loading infrastructure. Today, it is a peaceful thoroughfare used mostly by deer and rabbits.
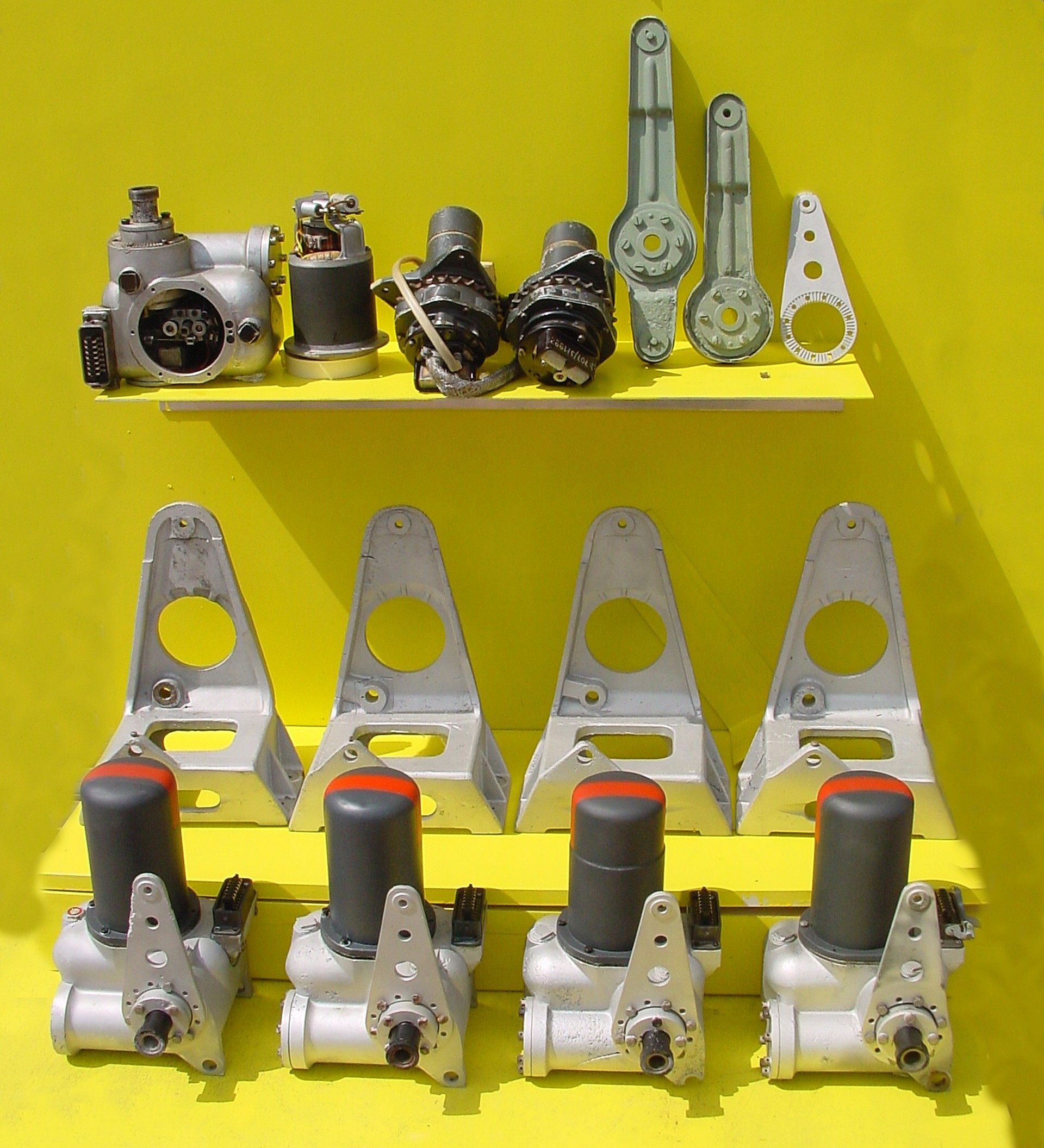
Photo shows a unique display at the Horst Beck Collection (HBC). Over many years Mr Horst Beck has painstakingly acquired and restored many A4-V2 missile parts – and in some cases, reassembled them into complete sub-assemblies. Shown here is part of the collection’s hydraulic servos and trim motor parts display. In the foreground we see four hydraulic servos, and behind them their A frame mounting ‘chairs’. The top shelf, from left to right, shows a servo with motor removed (and placed on its right). In the middle, two trim motors and chain sprocket gear-boxes for the aerodynamic trim surfaces on the trailing edge tips of fins 2 and 4. Next the pale green crank levers, the first longer one is for the hydraulic servo that controls the jet vanes and trimmers on fins 1 and 3. The shorter version minus the top horn, is used on the servos for fins 2 and 4. The last, silver coloured item,os a servo stabiliser (all the servos shown have one already fitted). Photo copyright: The Horst Beck Collection
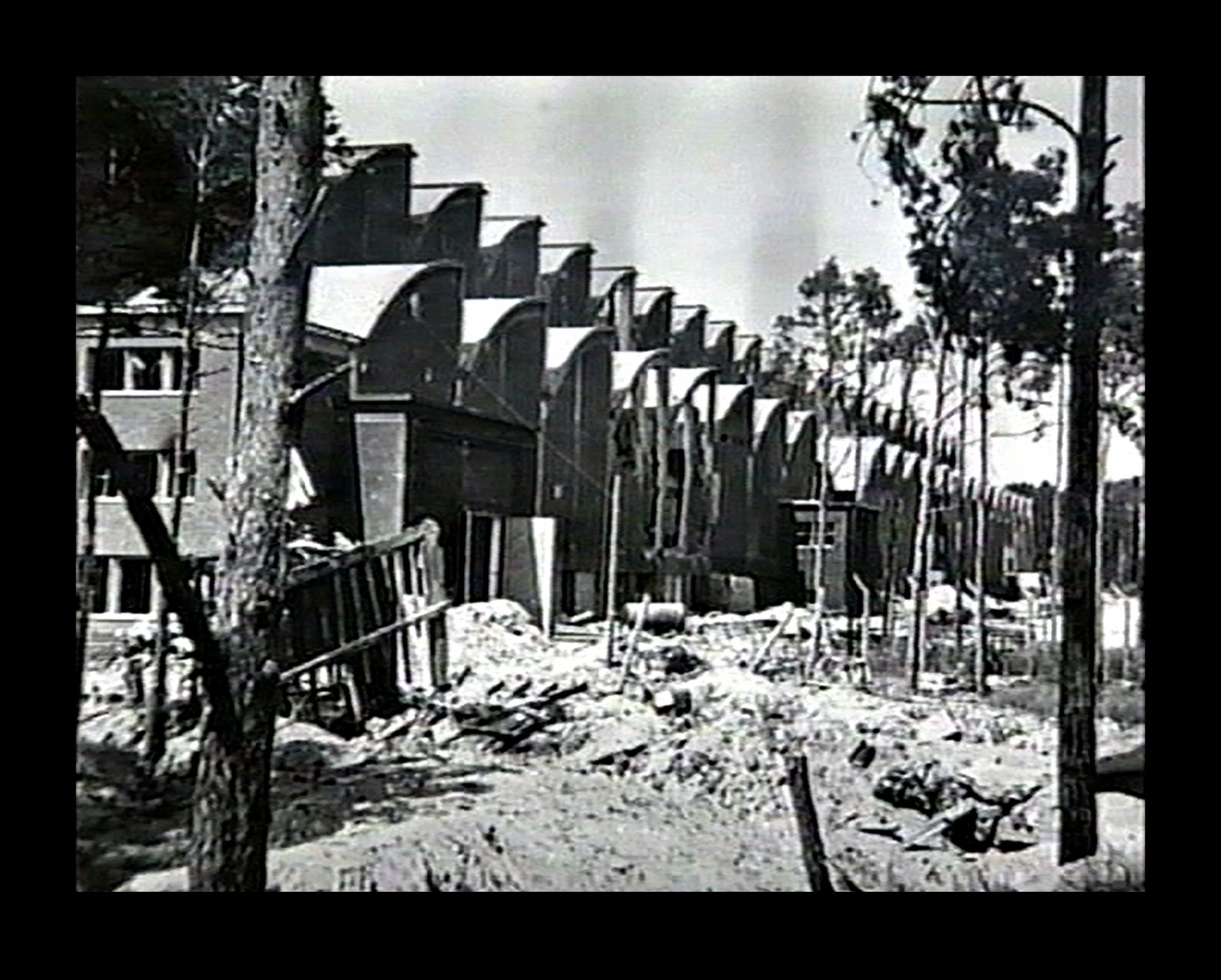
Bomb damaged F1 factory 1945. The huge V2 rocket factory shown badly damaged by air attack at the end of the war in May 1945
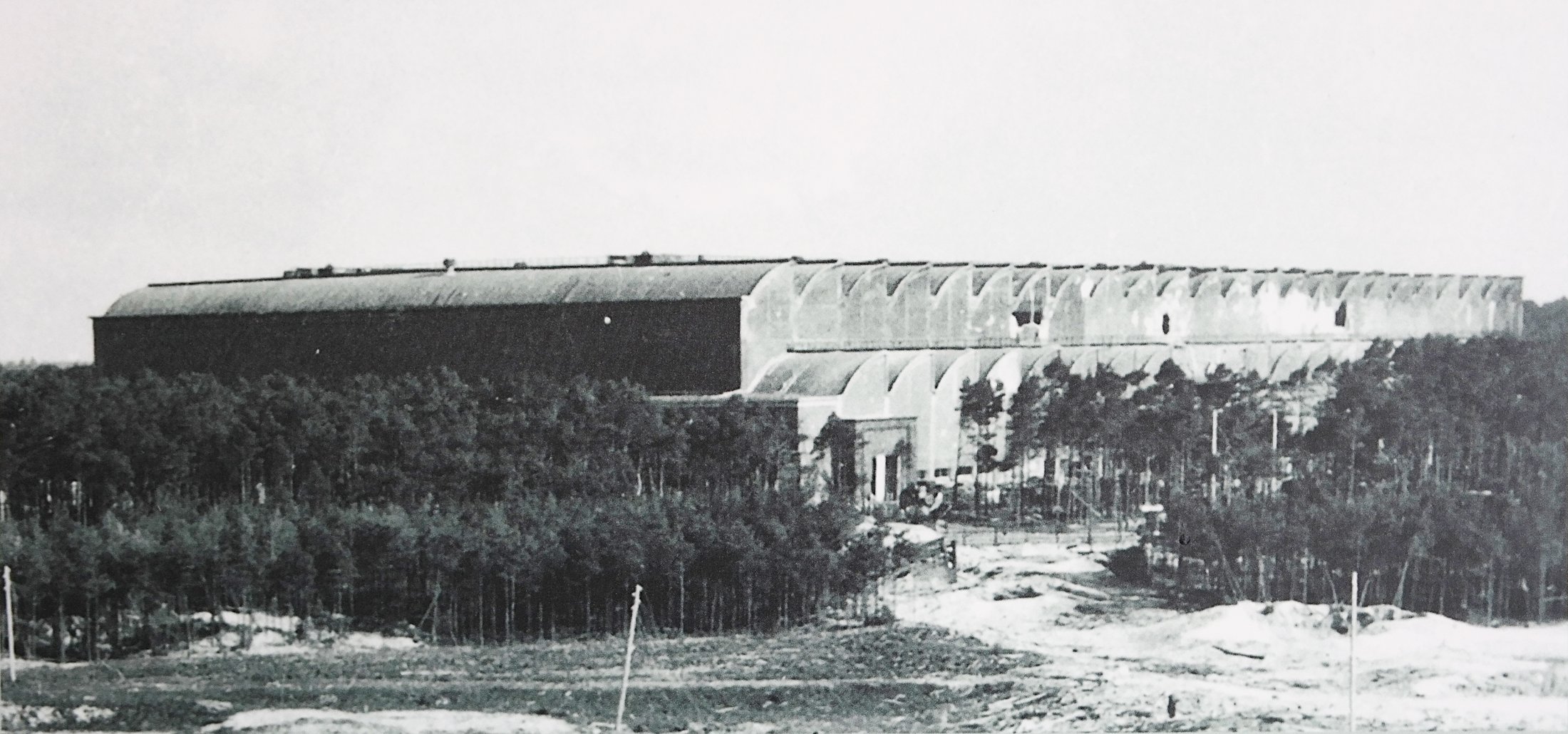
A rare photo of the giant F1 production hall taken not long after the RAF raid of 17/18th August 1943. F1 was a forced labour camp with at least 600 prisoners living within the factory and at least eleven were killed in the raid. Parts of the electrified barbed wire fence can be seen close to the factory building, in the clearing in the middle of the photo. Two anti aircraft gun emplacements can be seen on the roof at the front of the building. Holes in the side walls of the upper vaults can be seen as well as the damage to lower vaults 9 and 10 (counting from left) from a direct hit in this region. Also of note are the numerous guy ropes, attached to the upper roof of the front of the building – and running down towards the trees, that are just visible in the photo. These may be supports for camouflage netting that was in the process of being fitted (by prisoner gangs) just before the raid. The work was never completed.

Testing fuel injectors

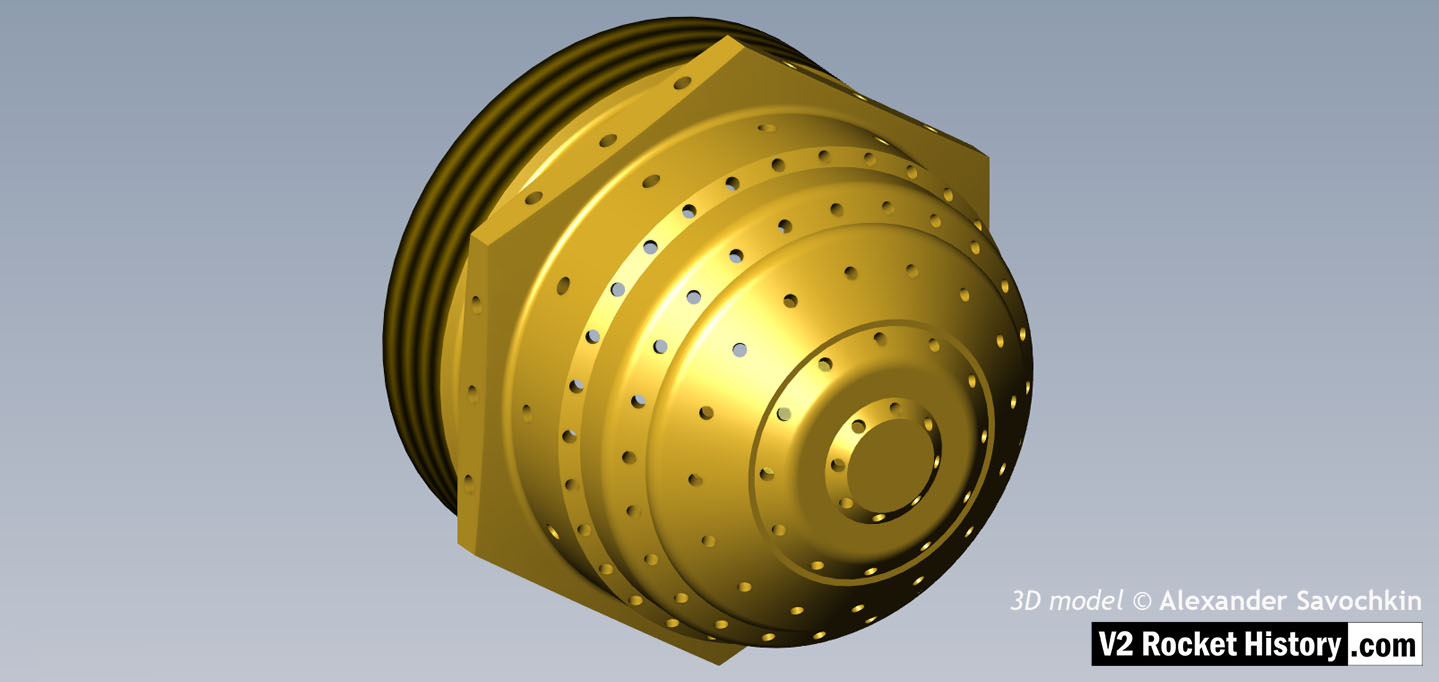
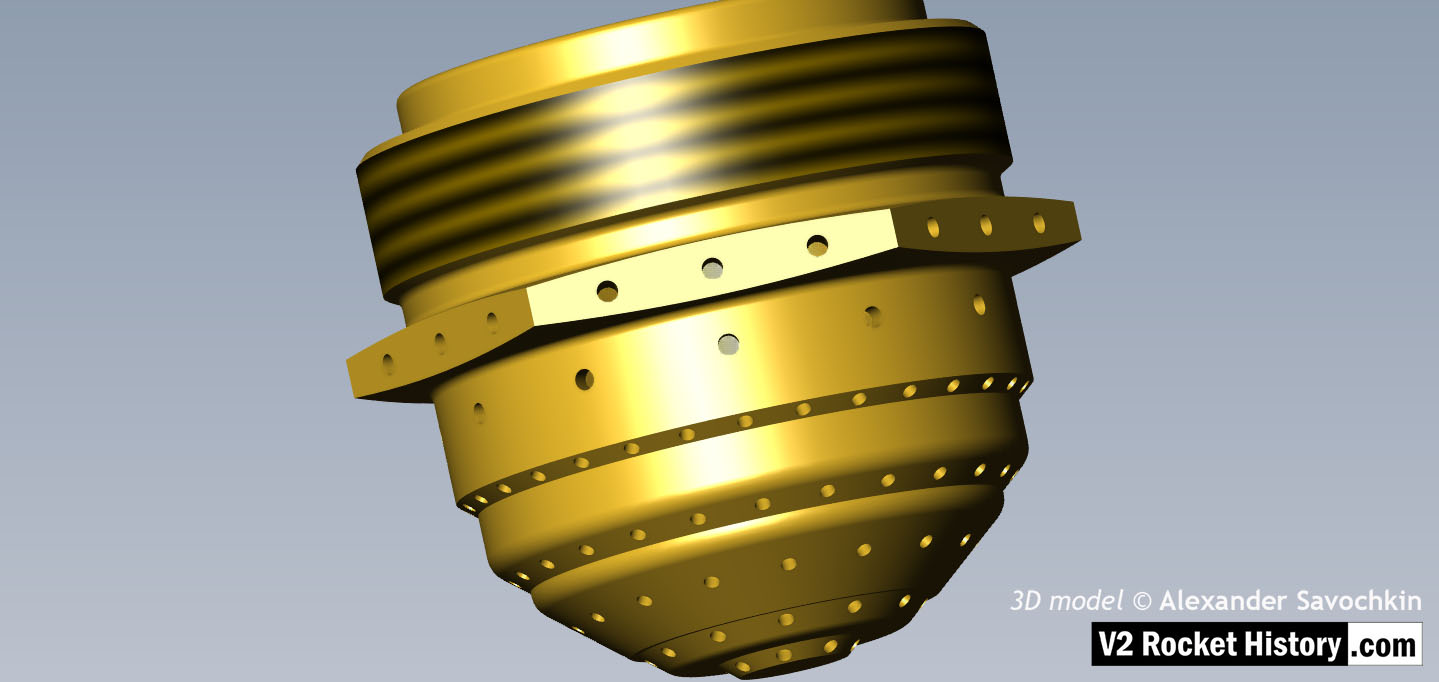

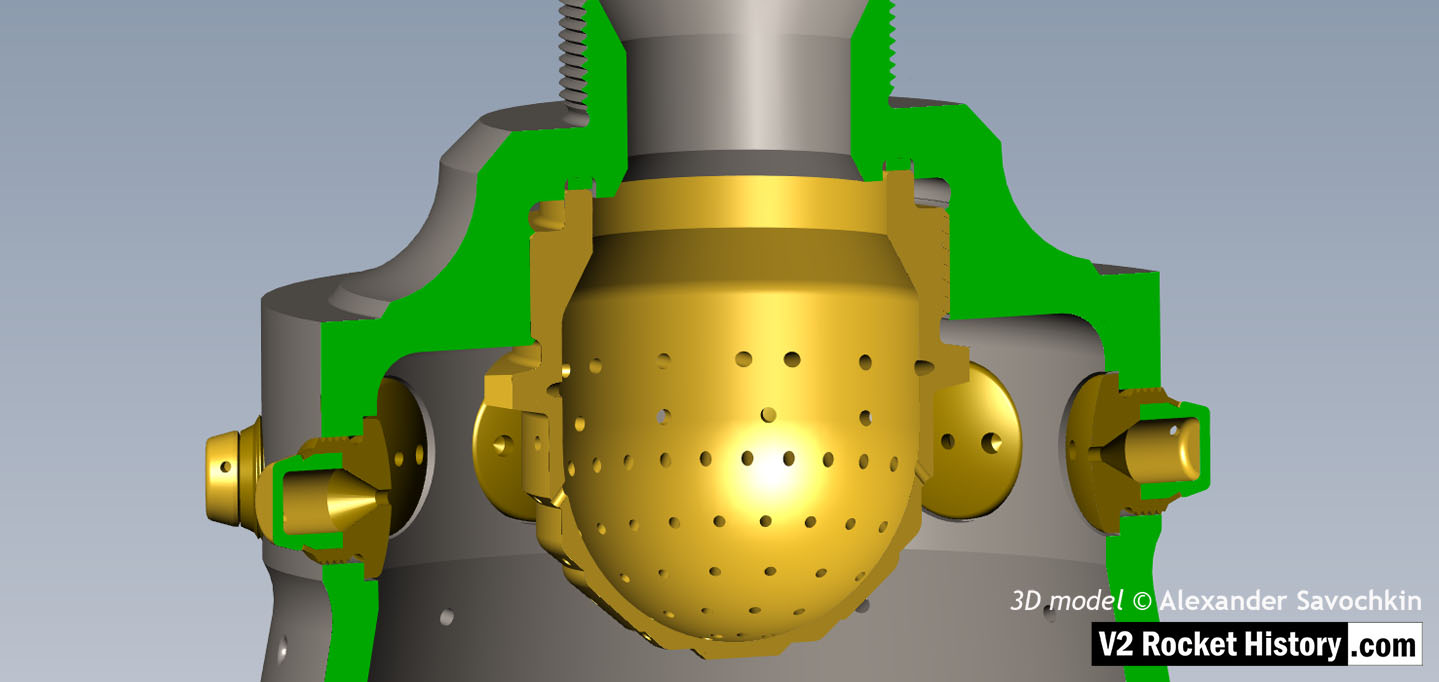
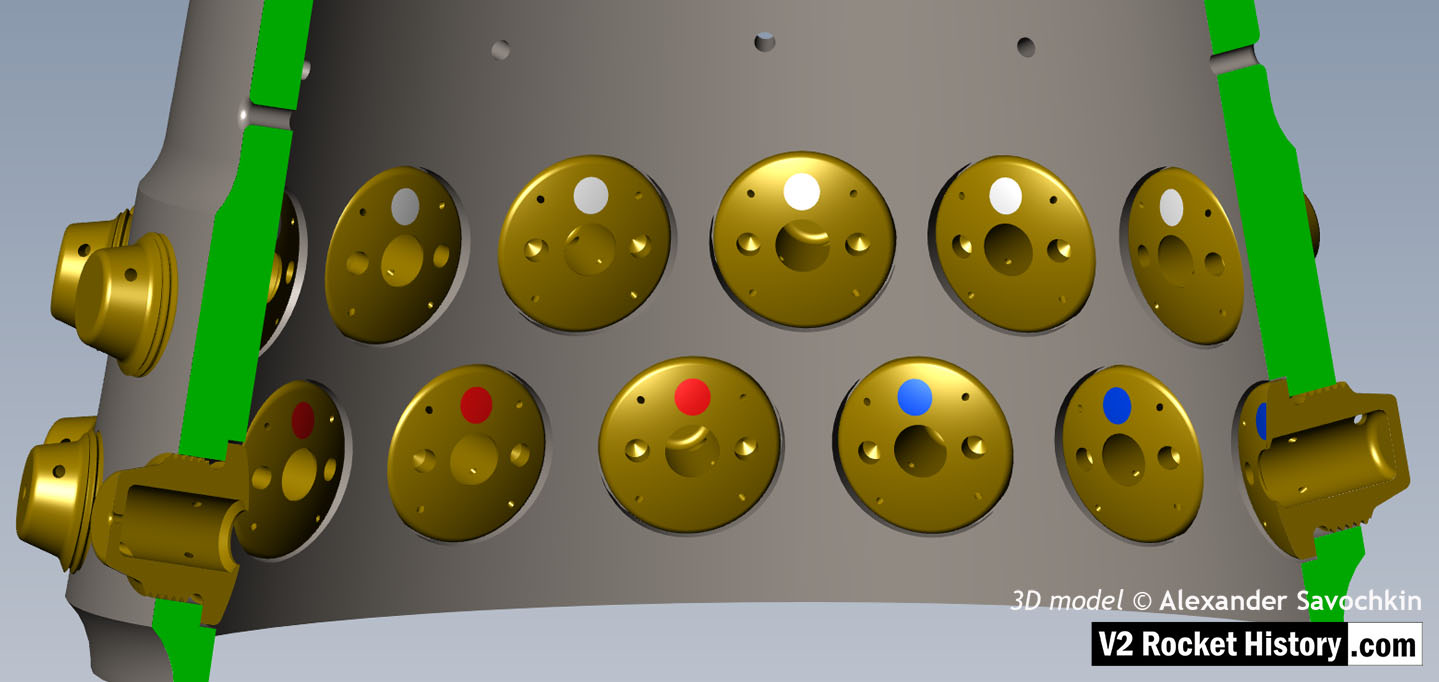

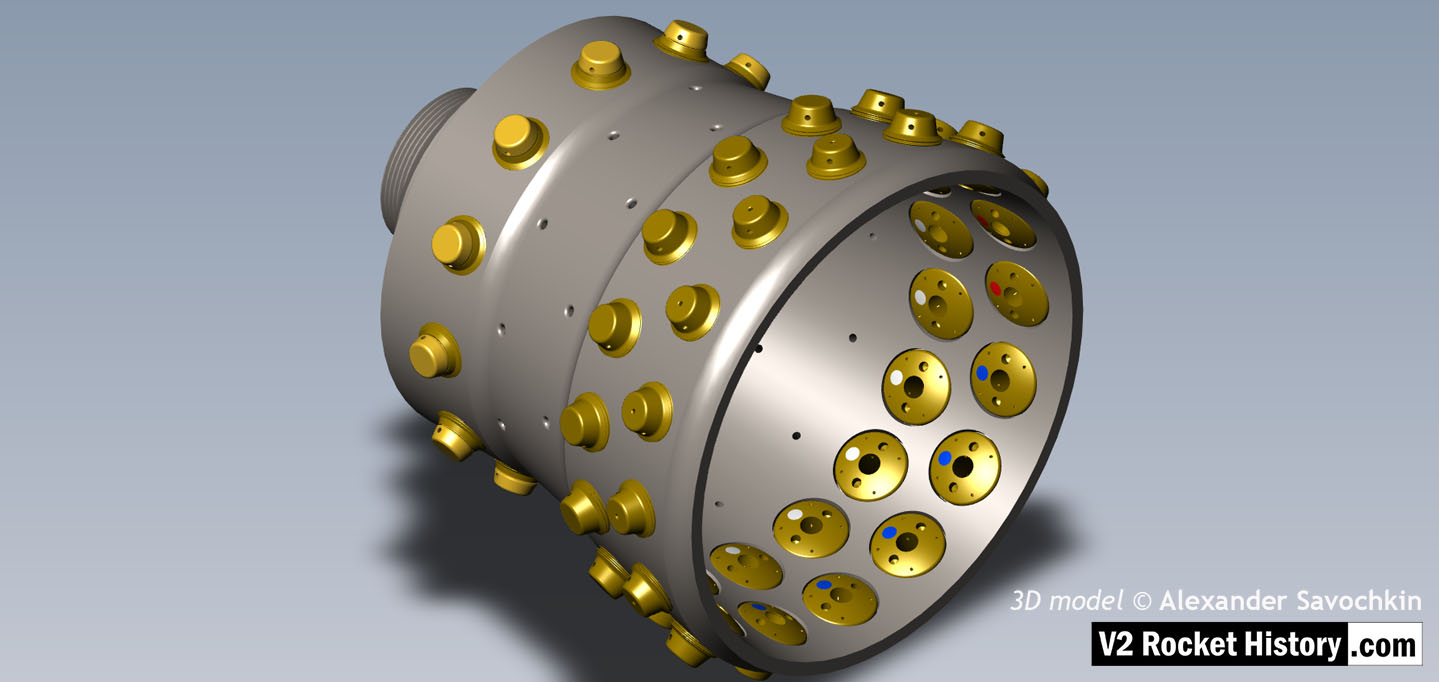
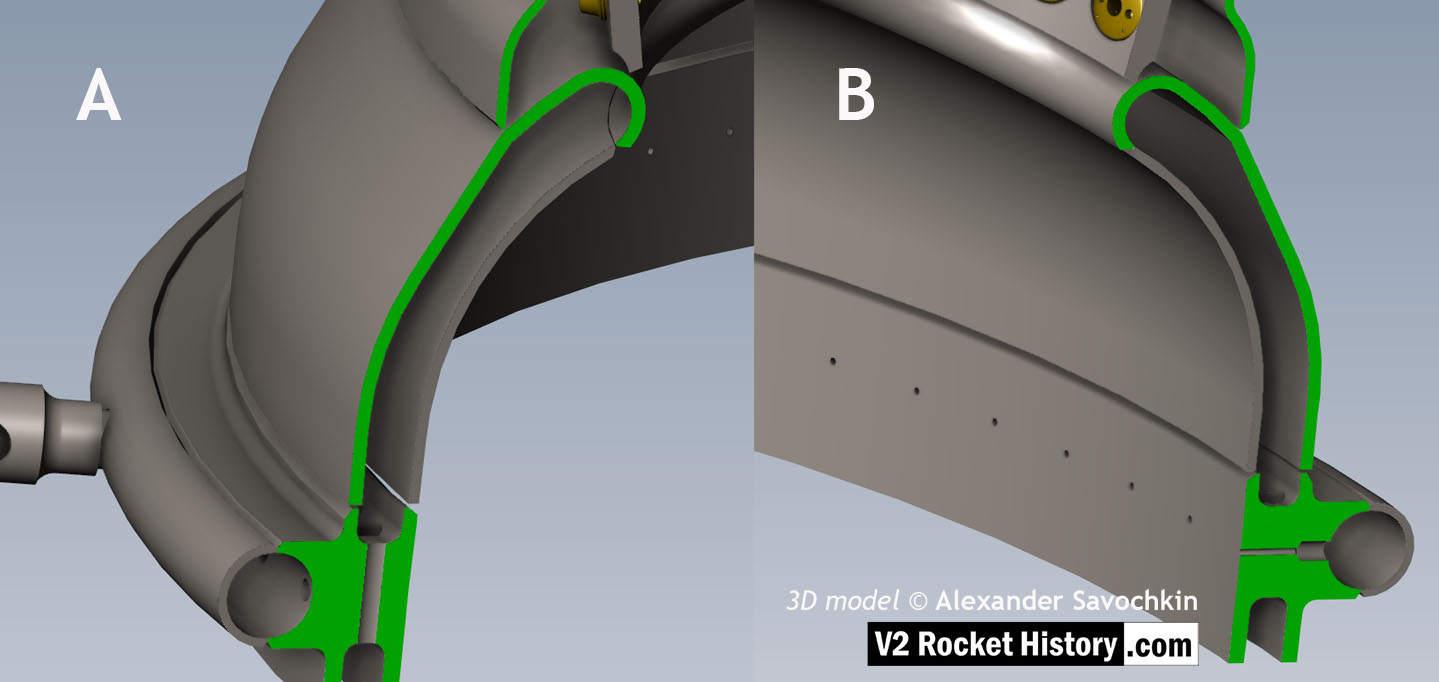




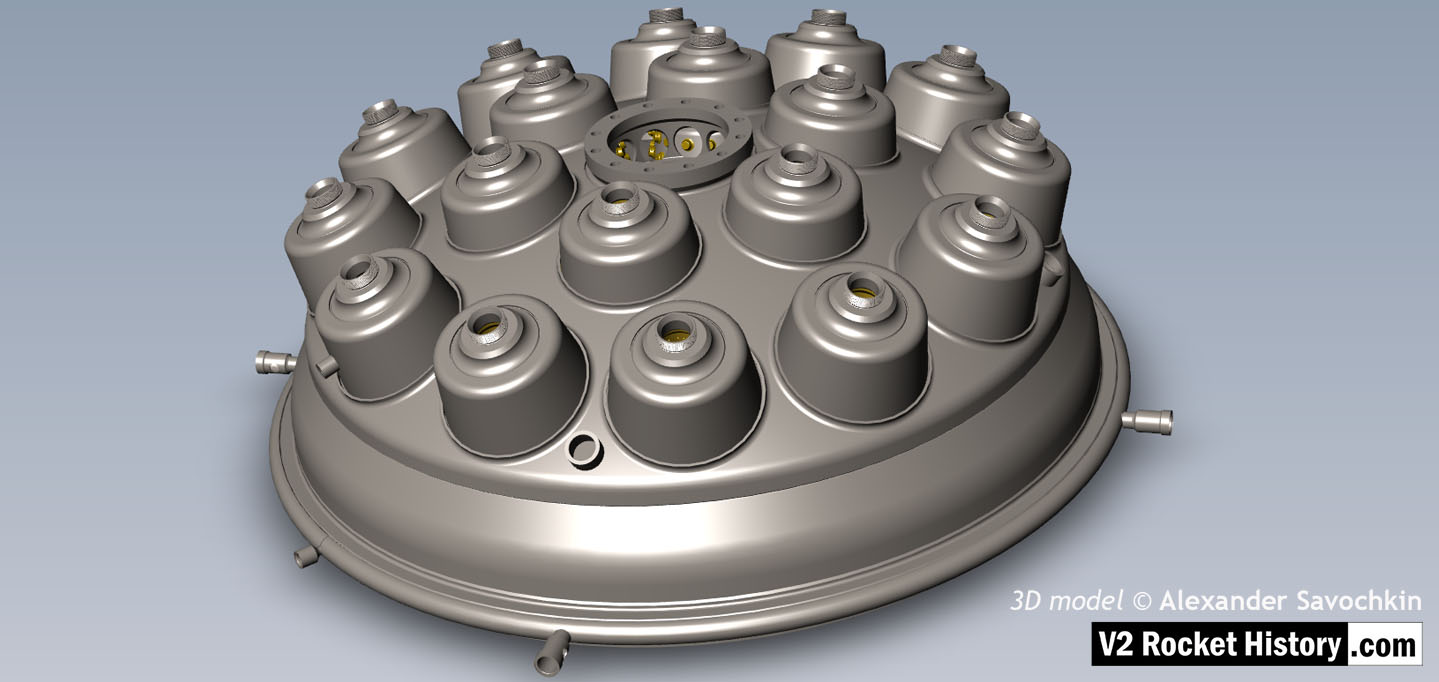

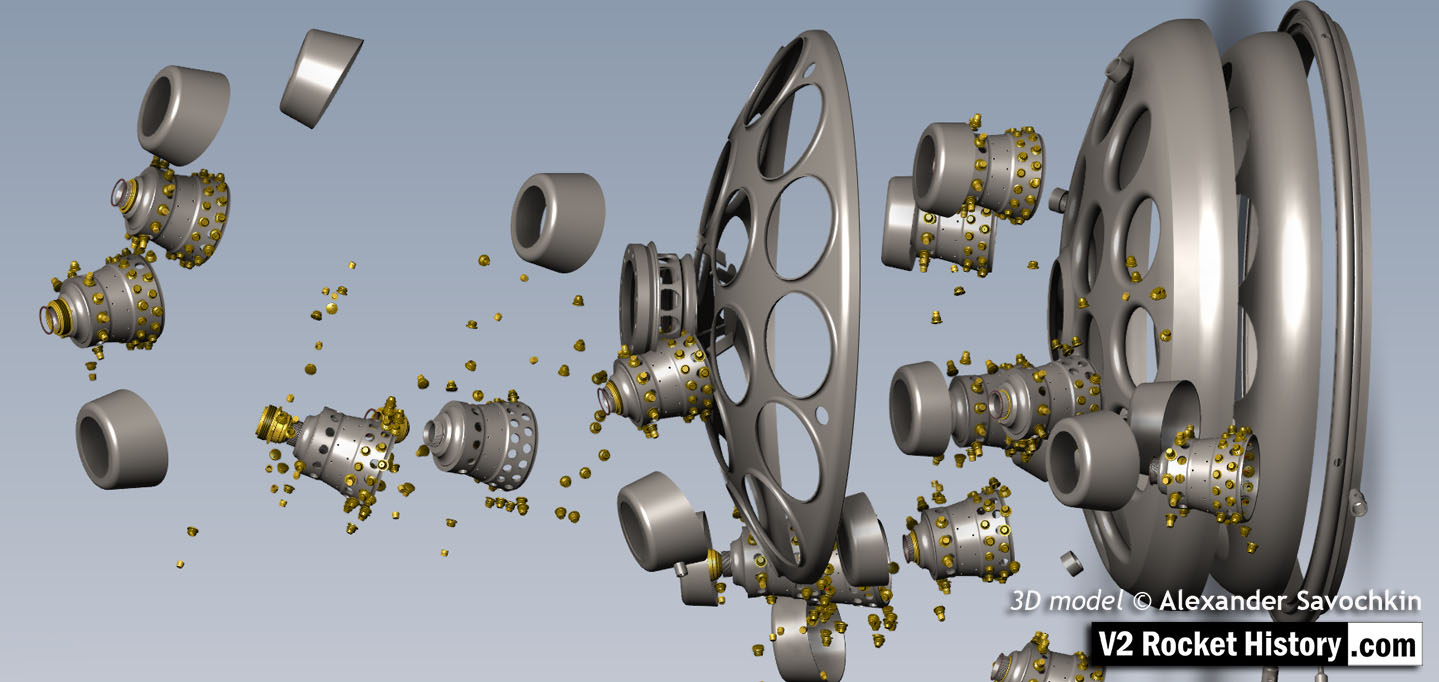
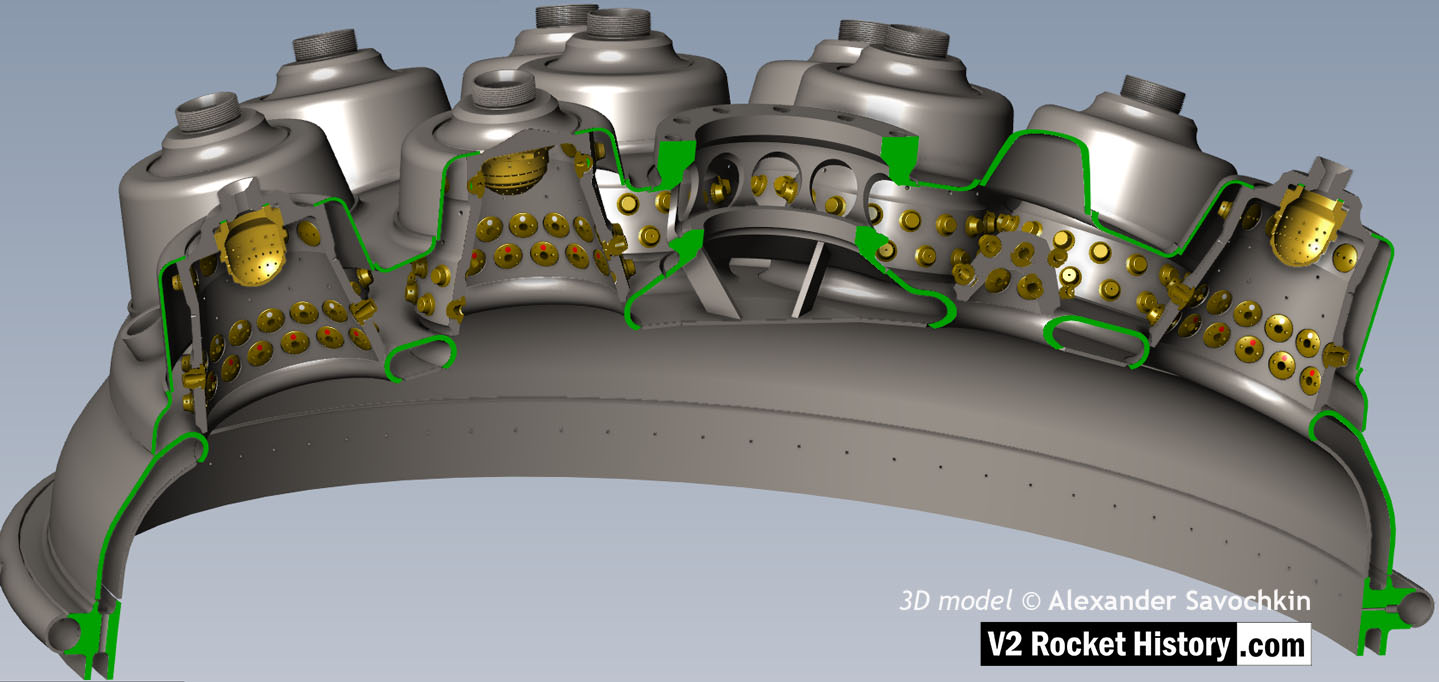


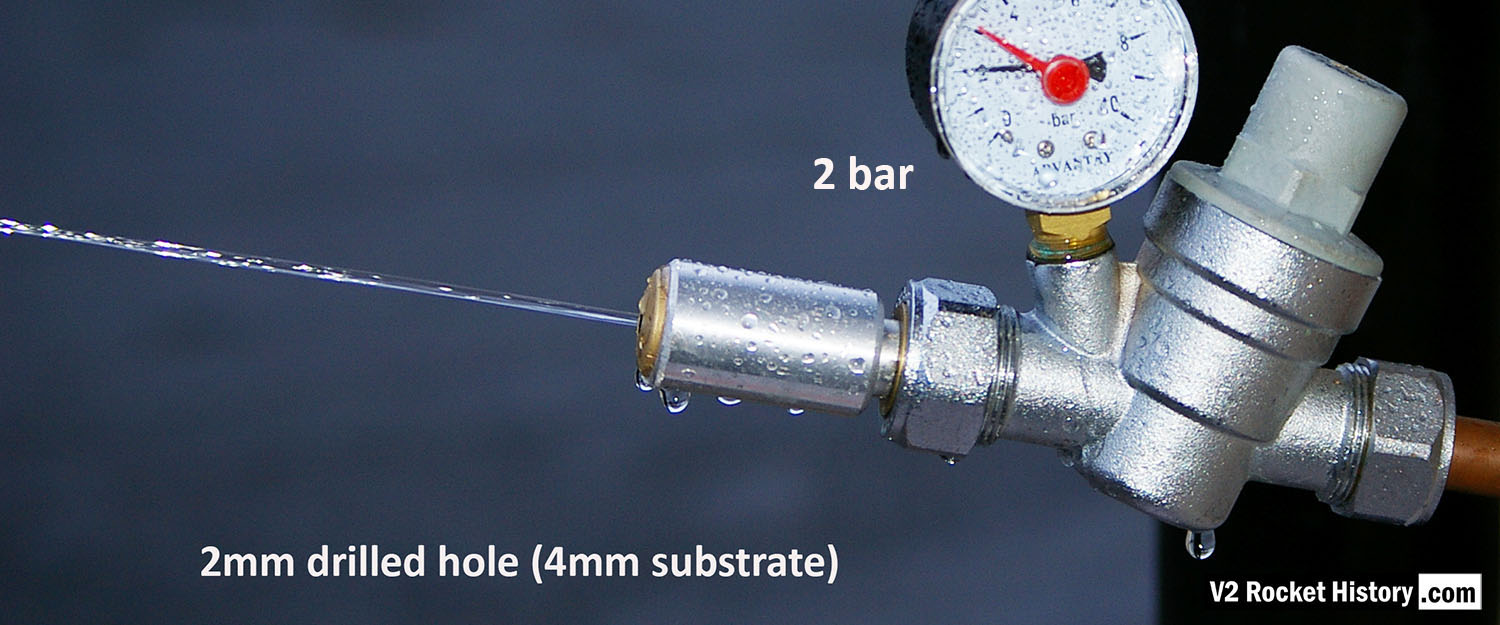

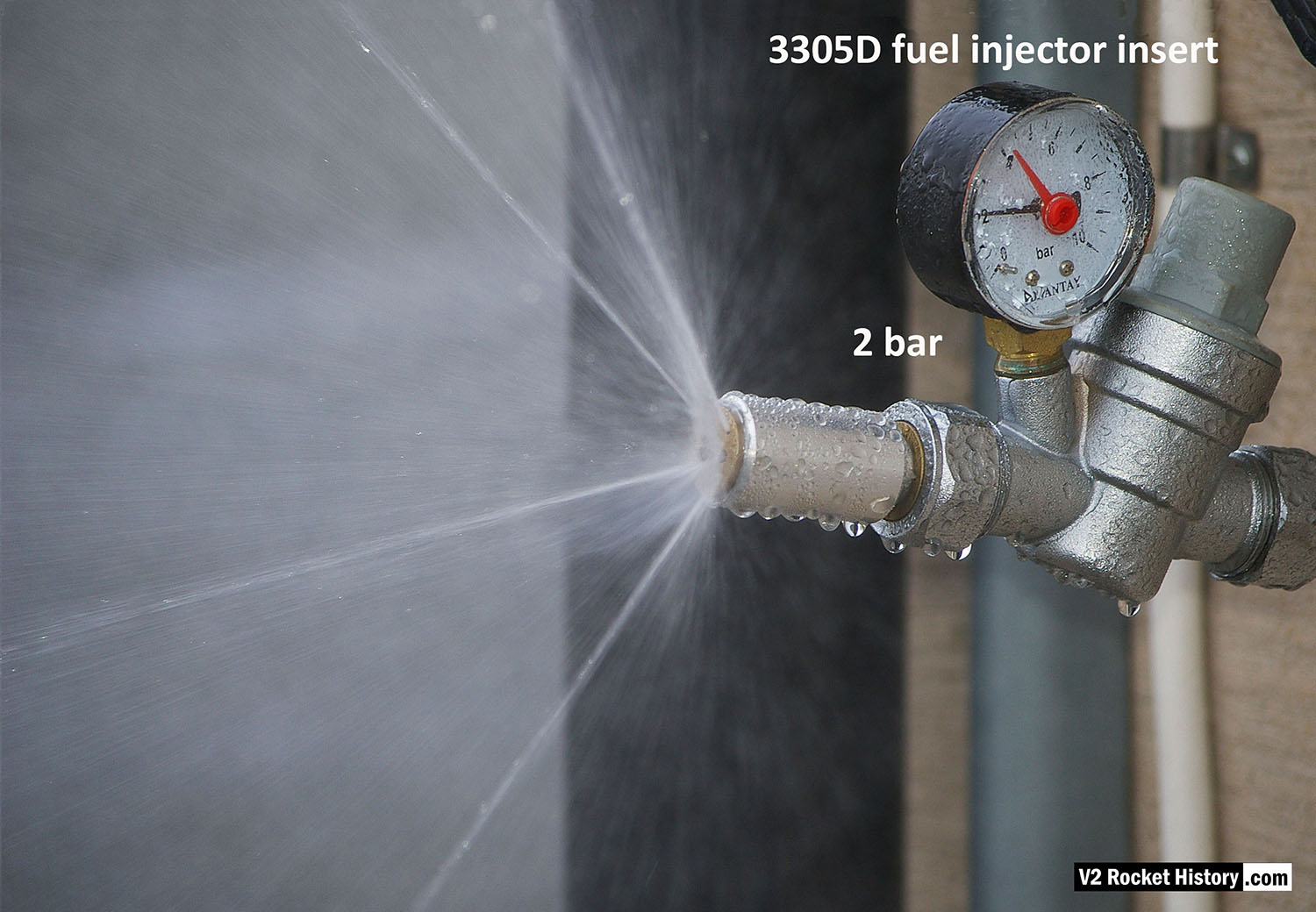
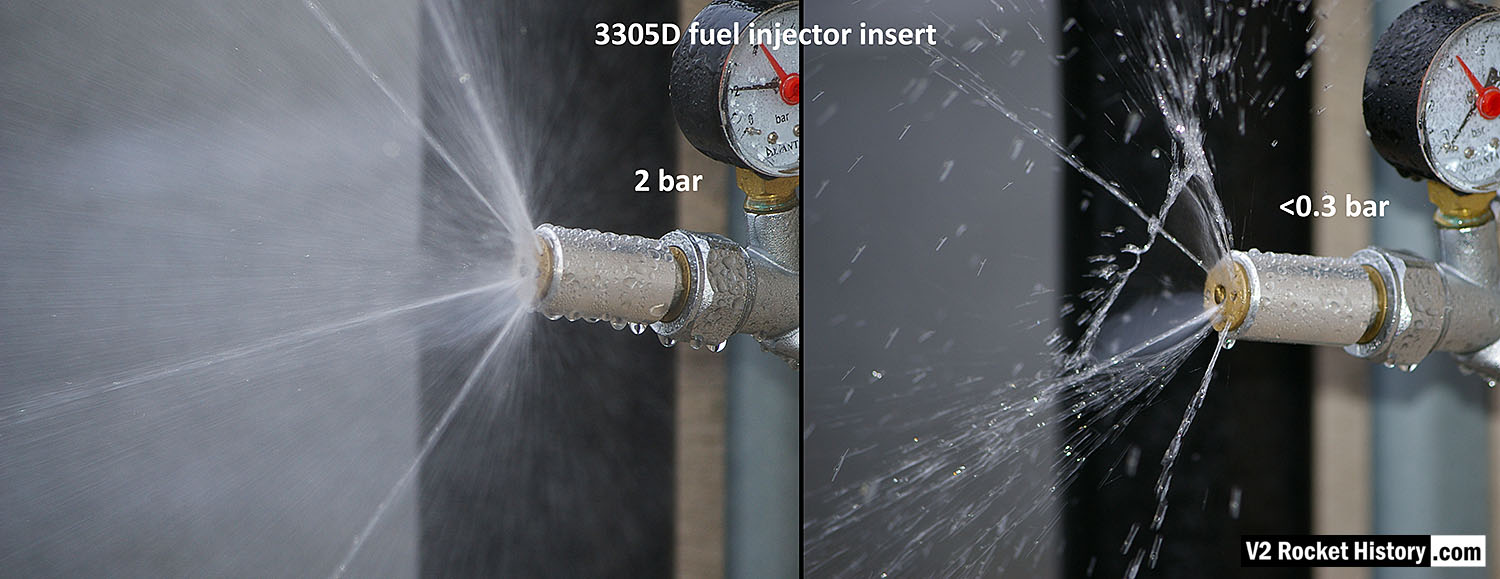
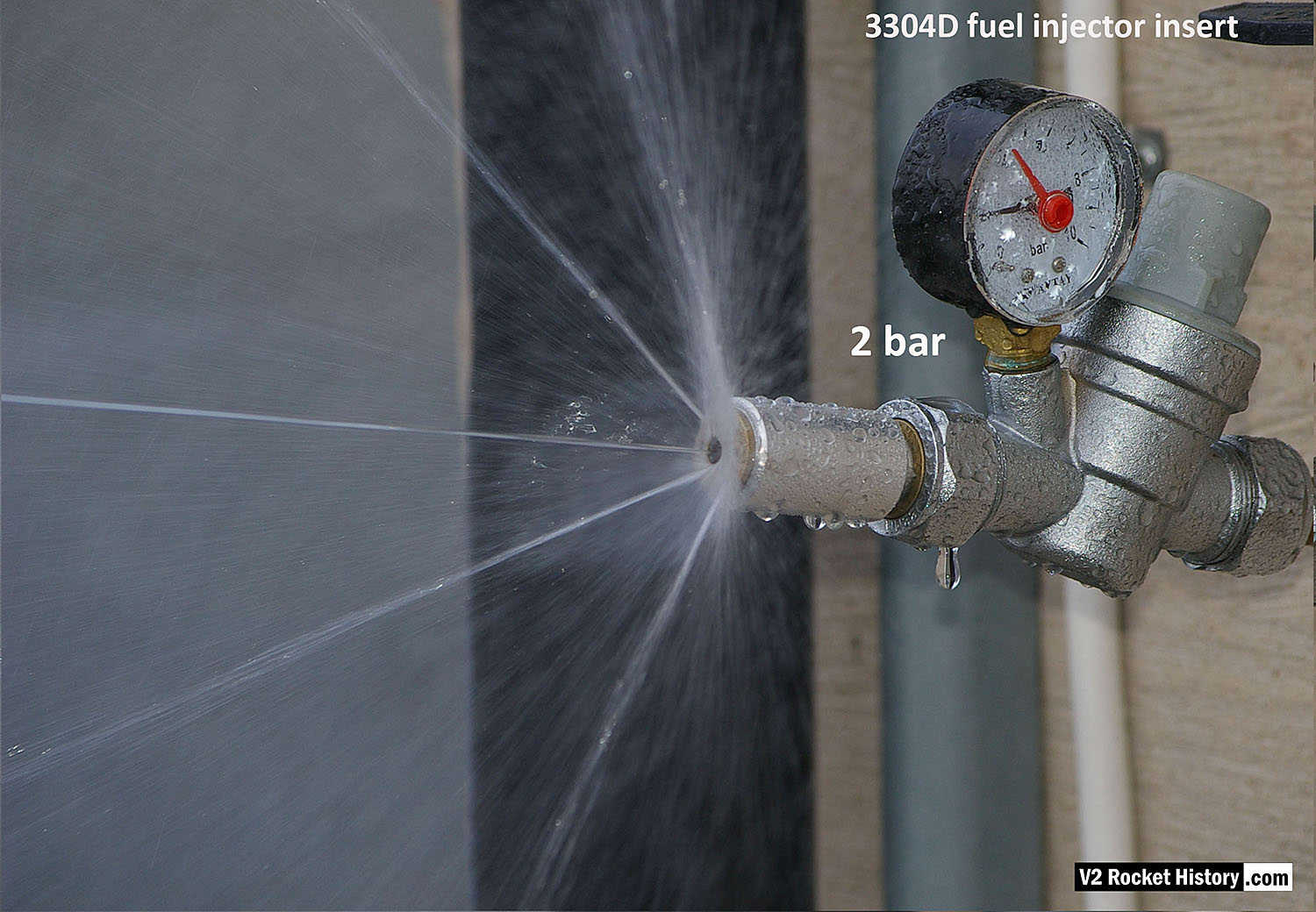
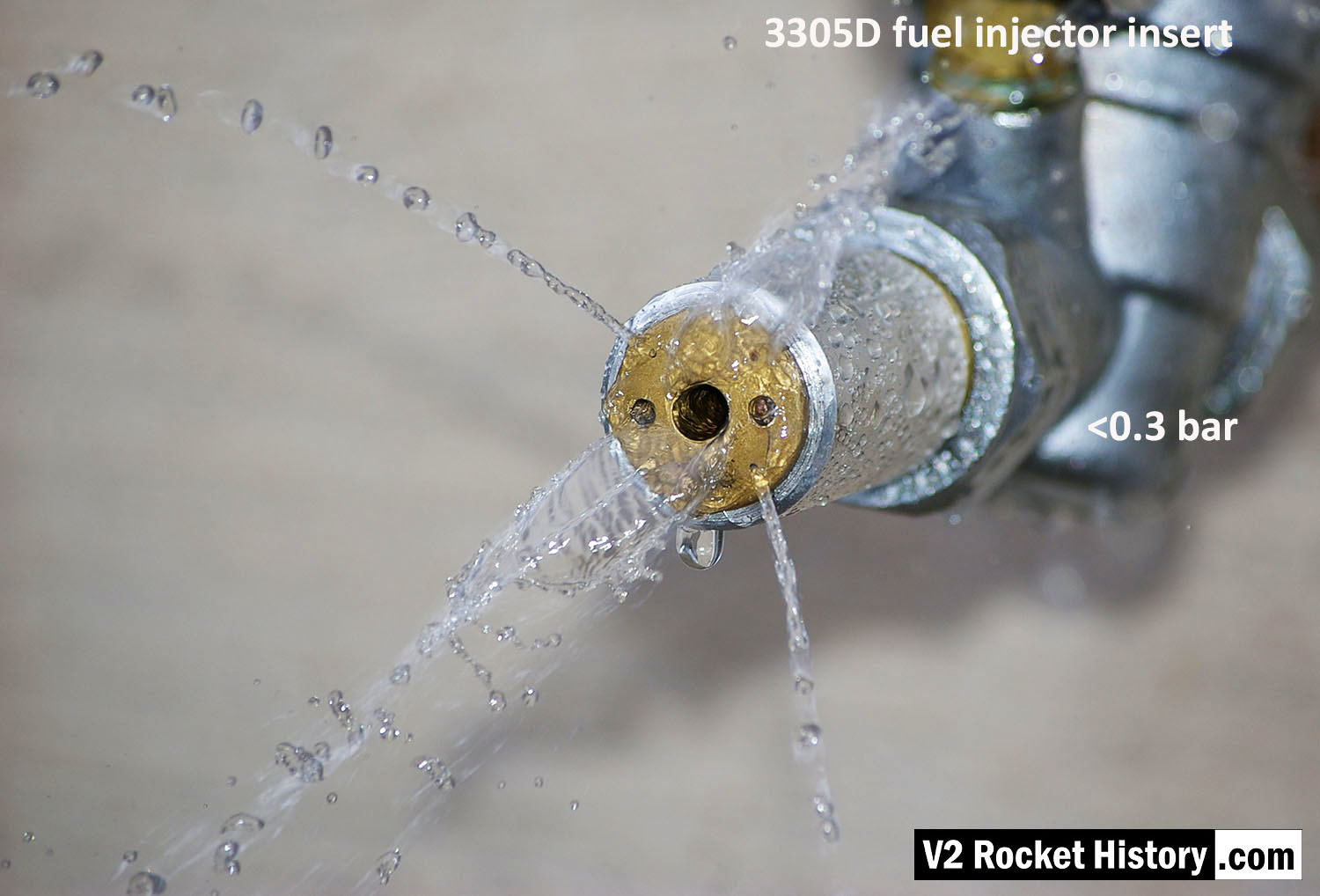
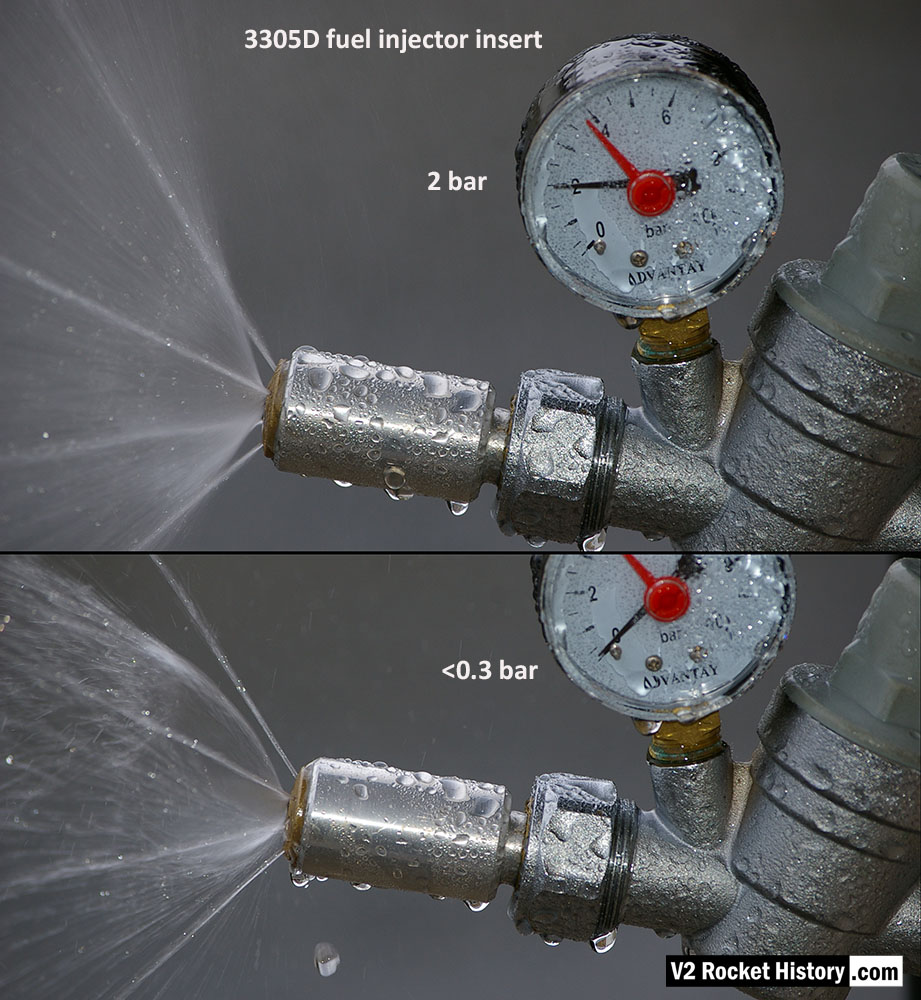
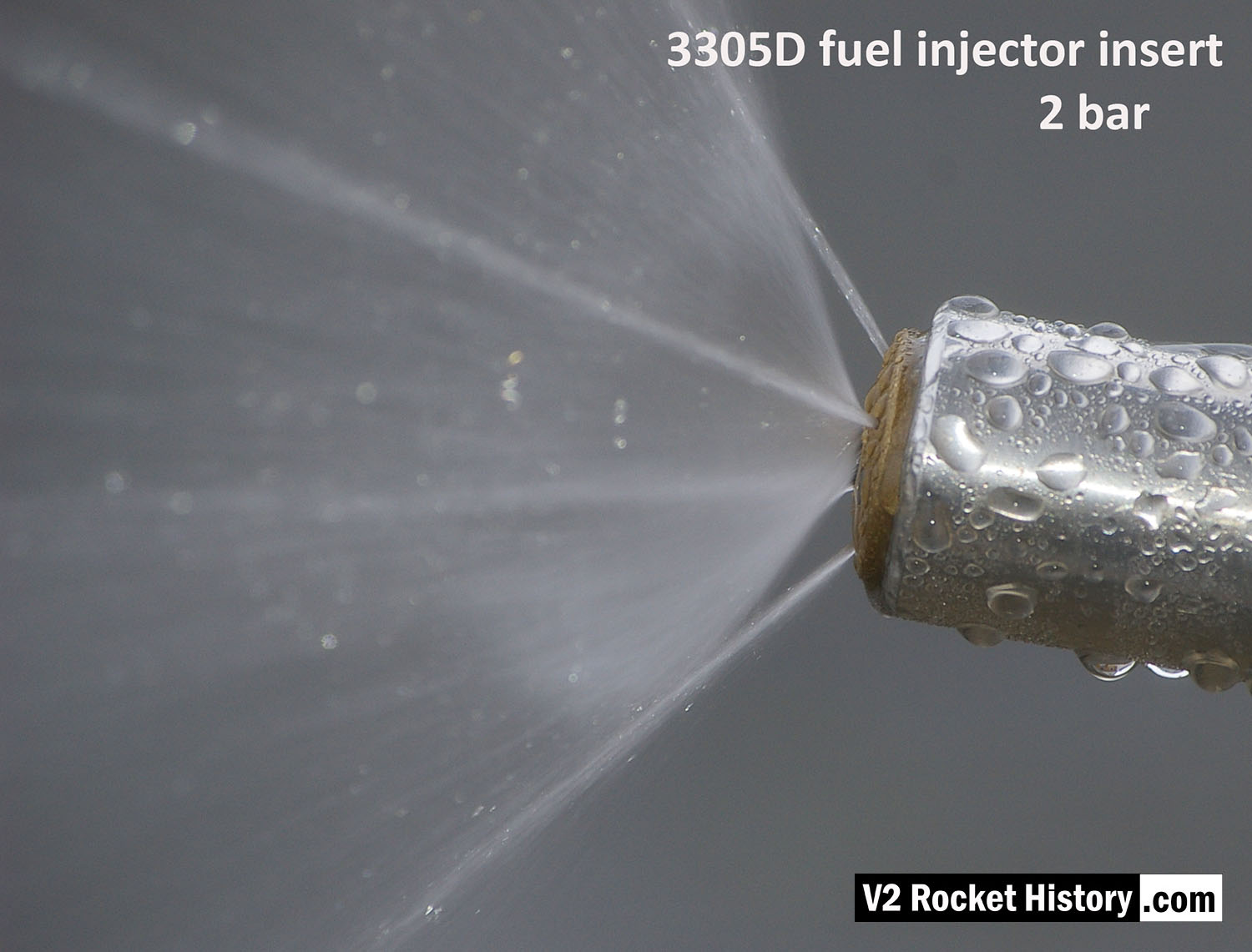
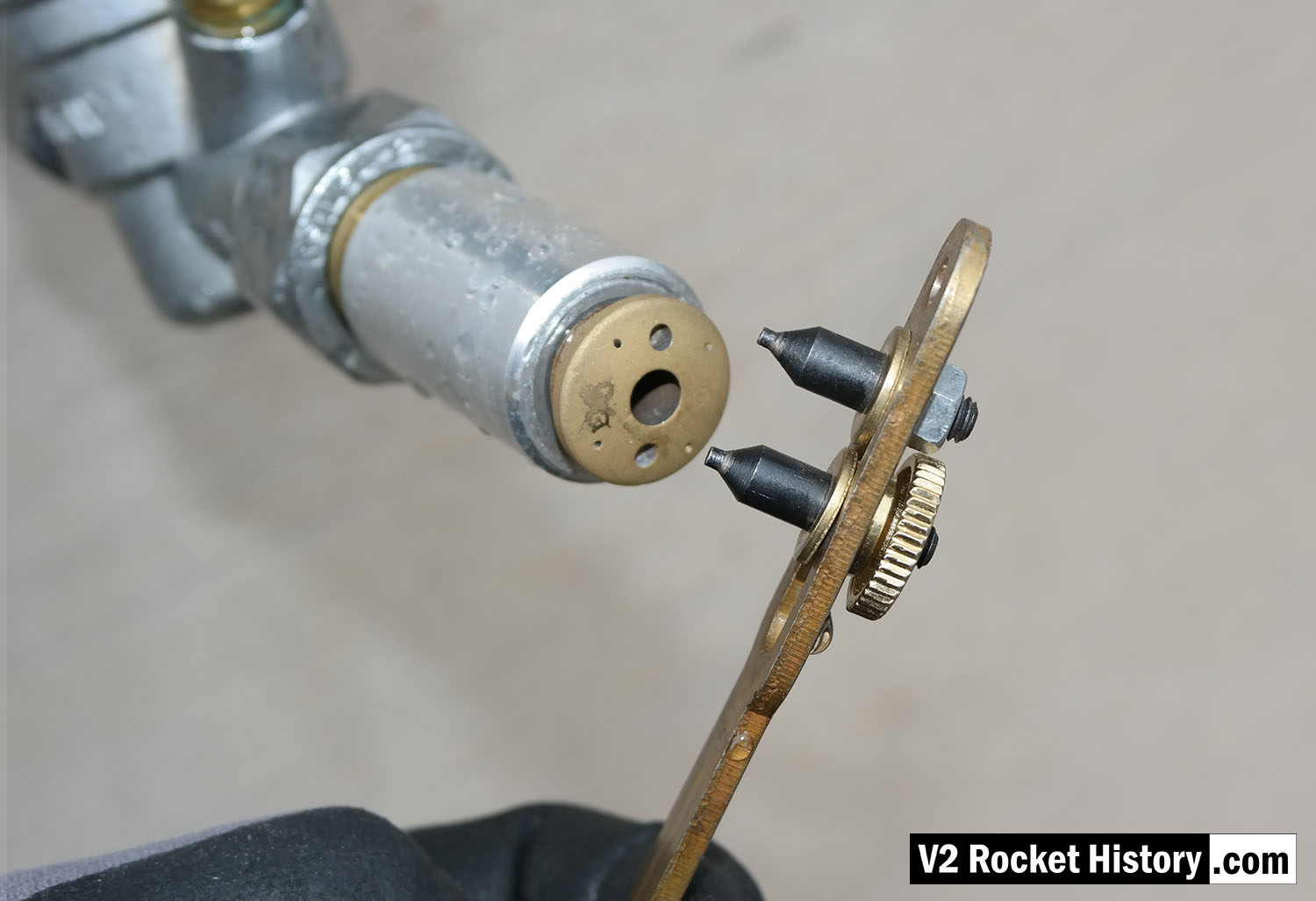

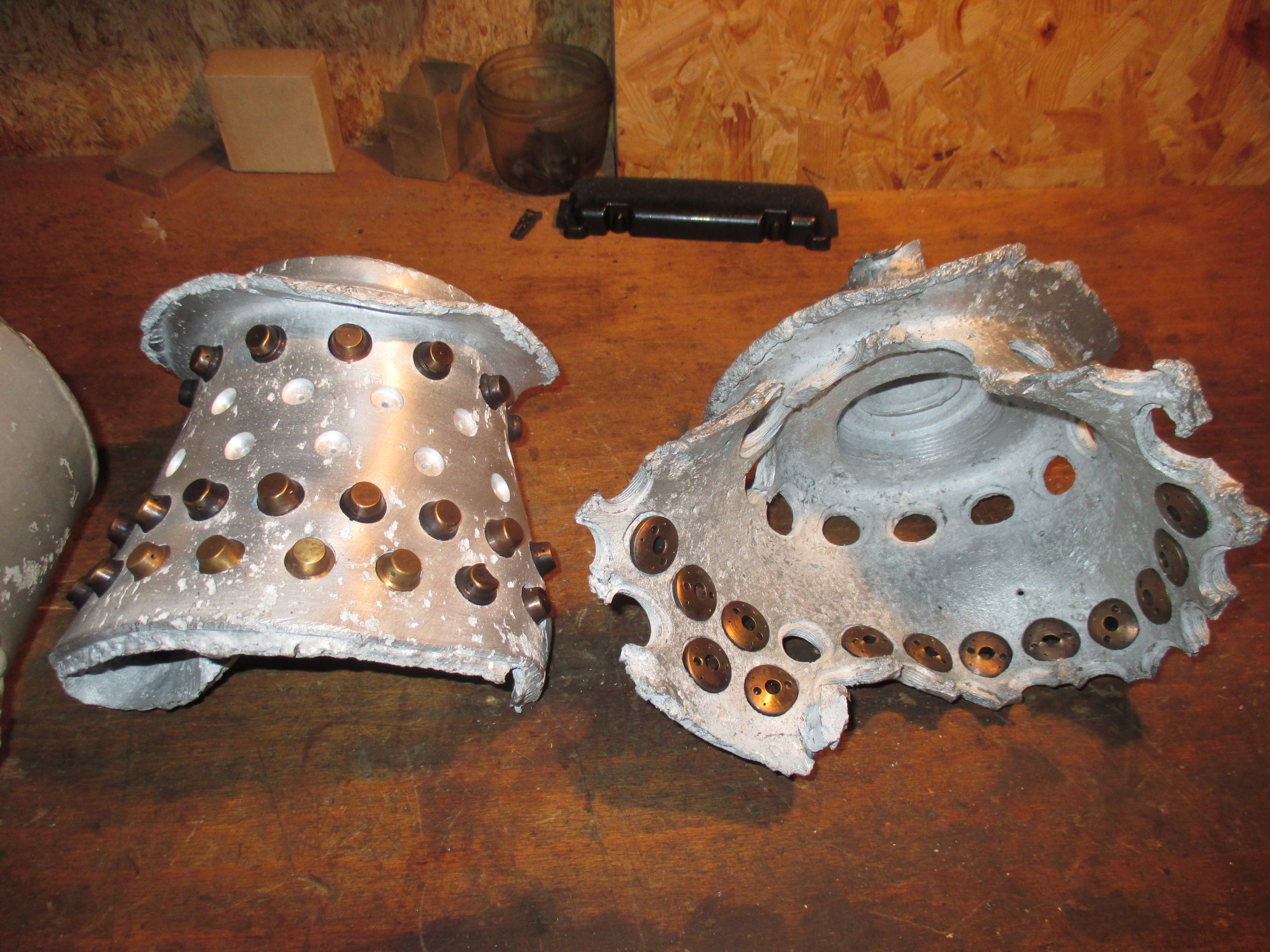

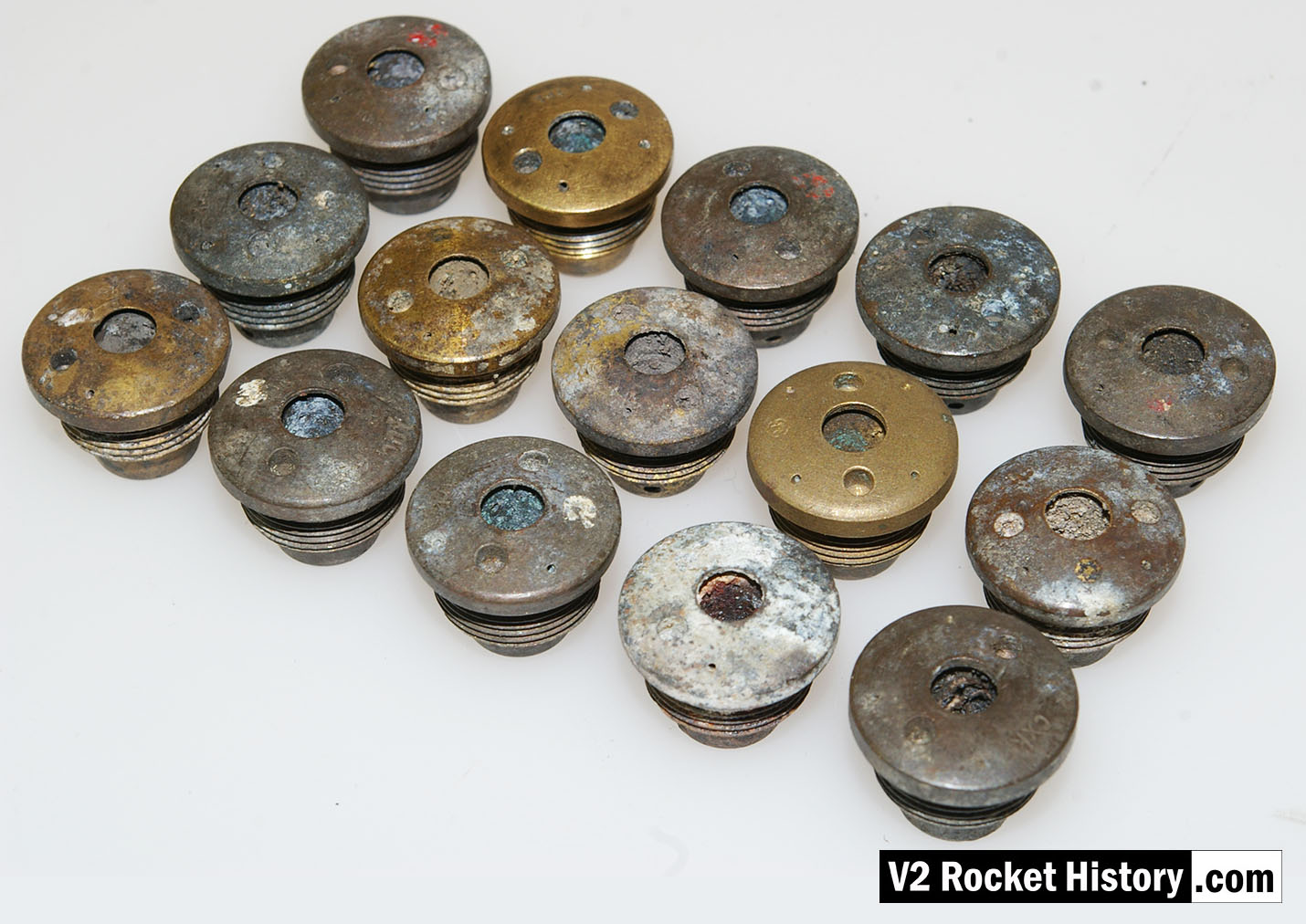


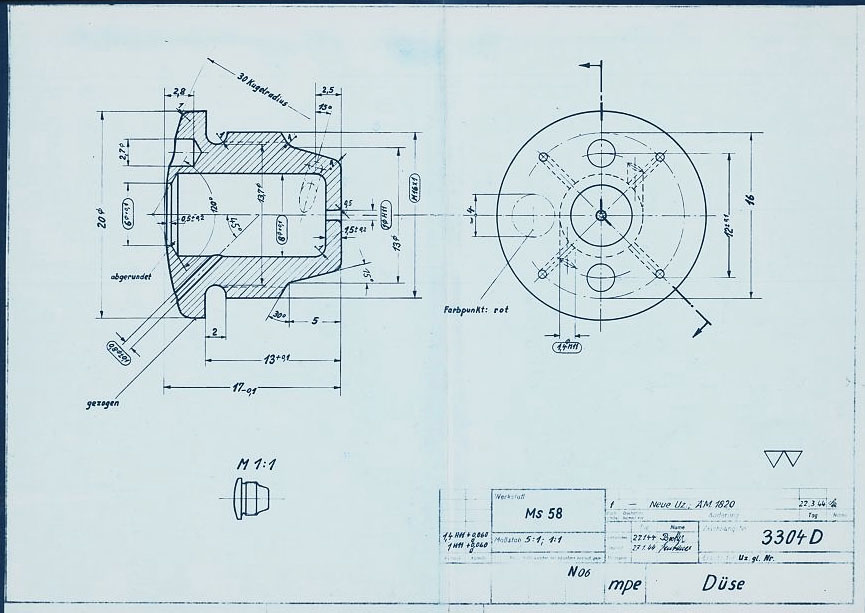
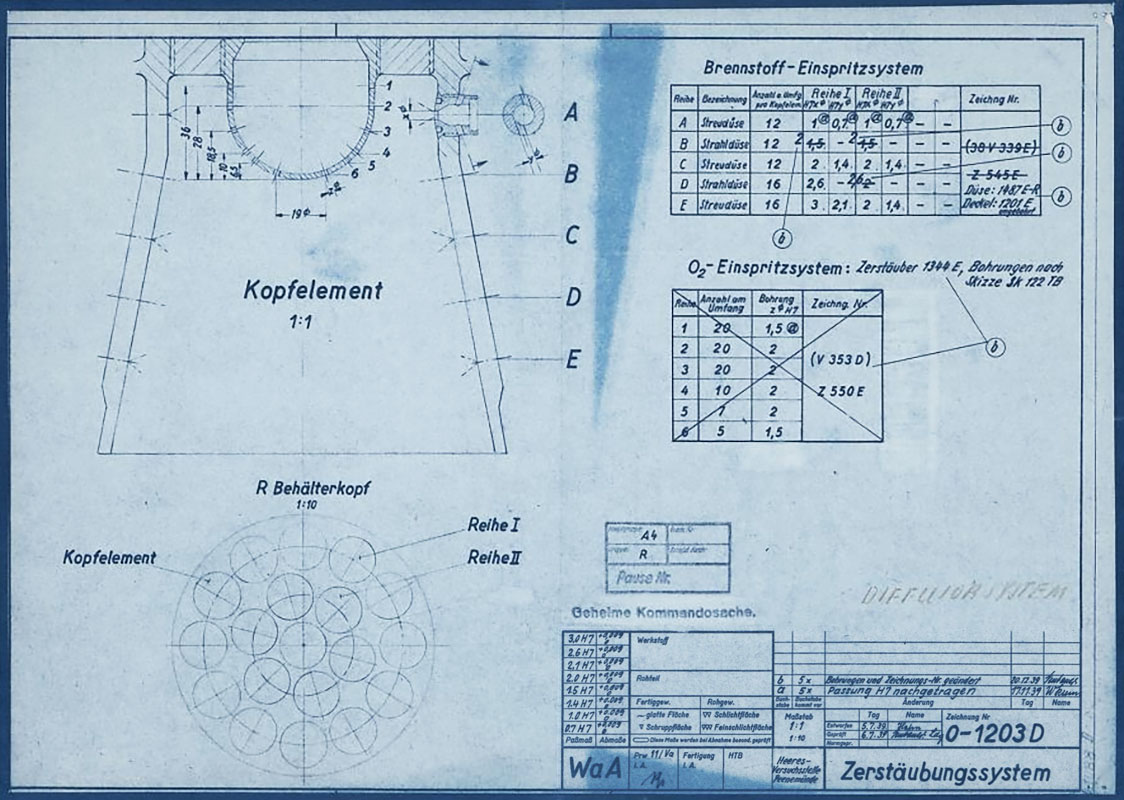
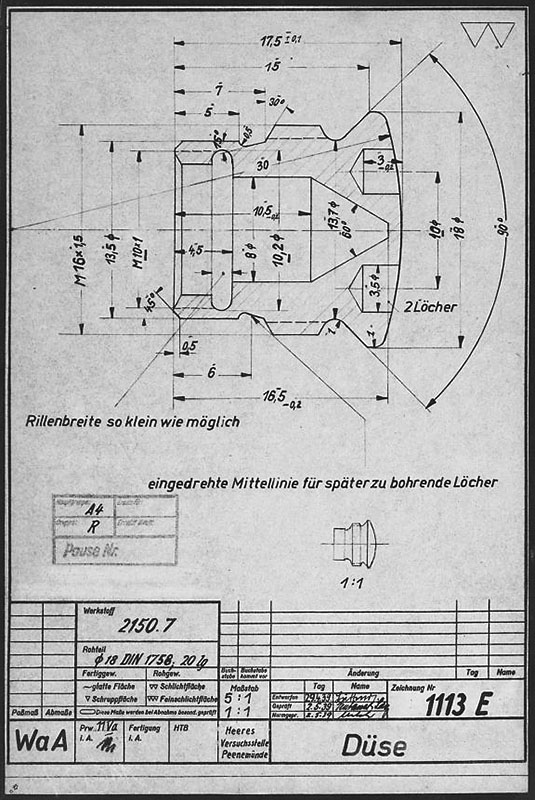
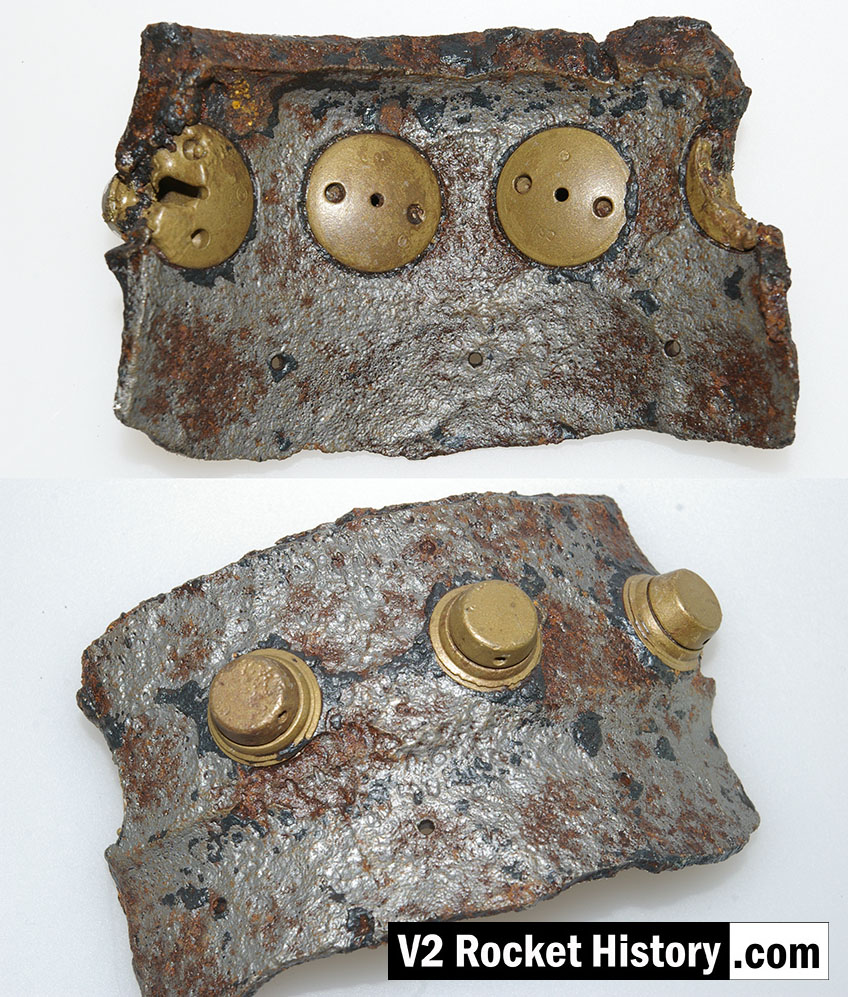
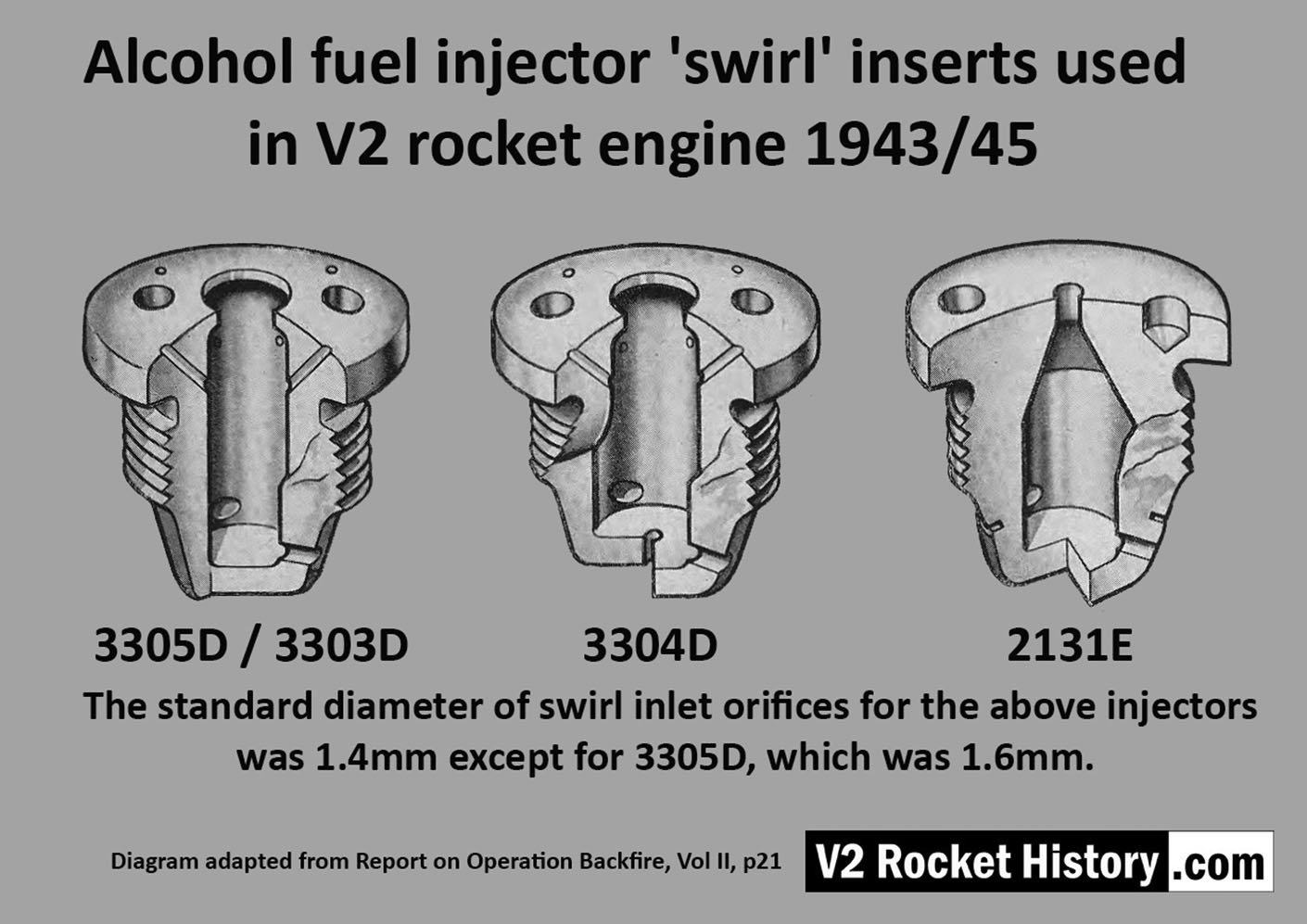
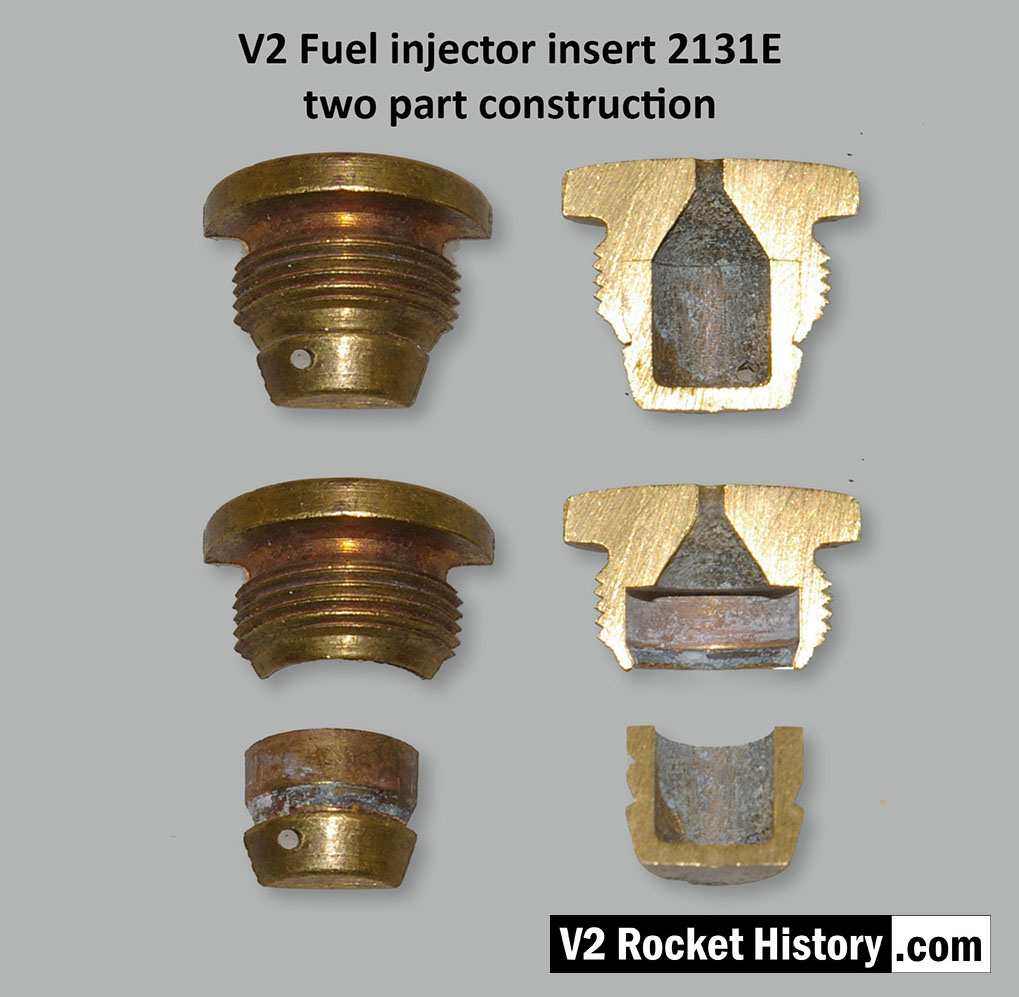

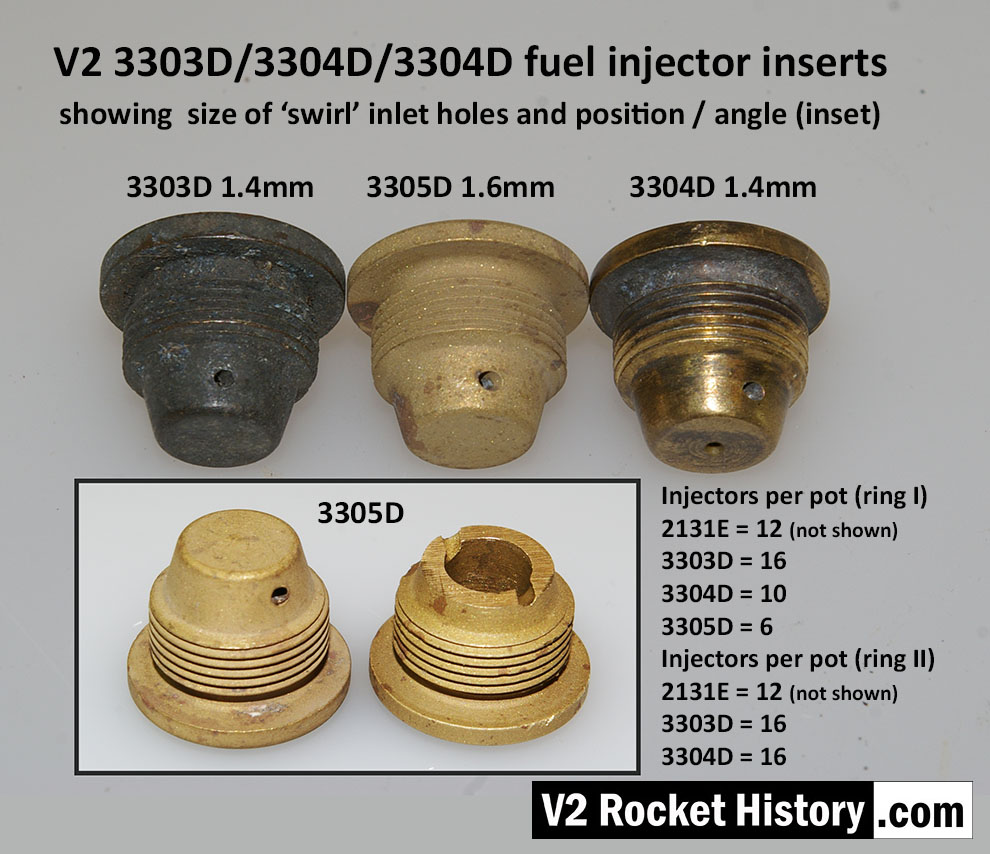
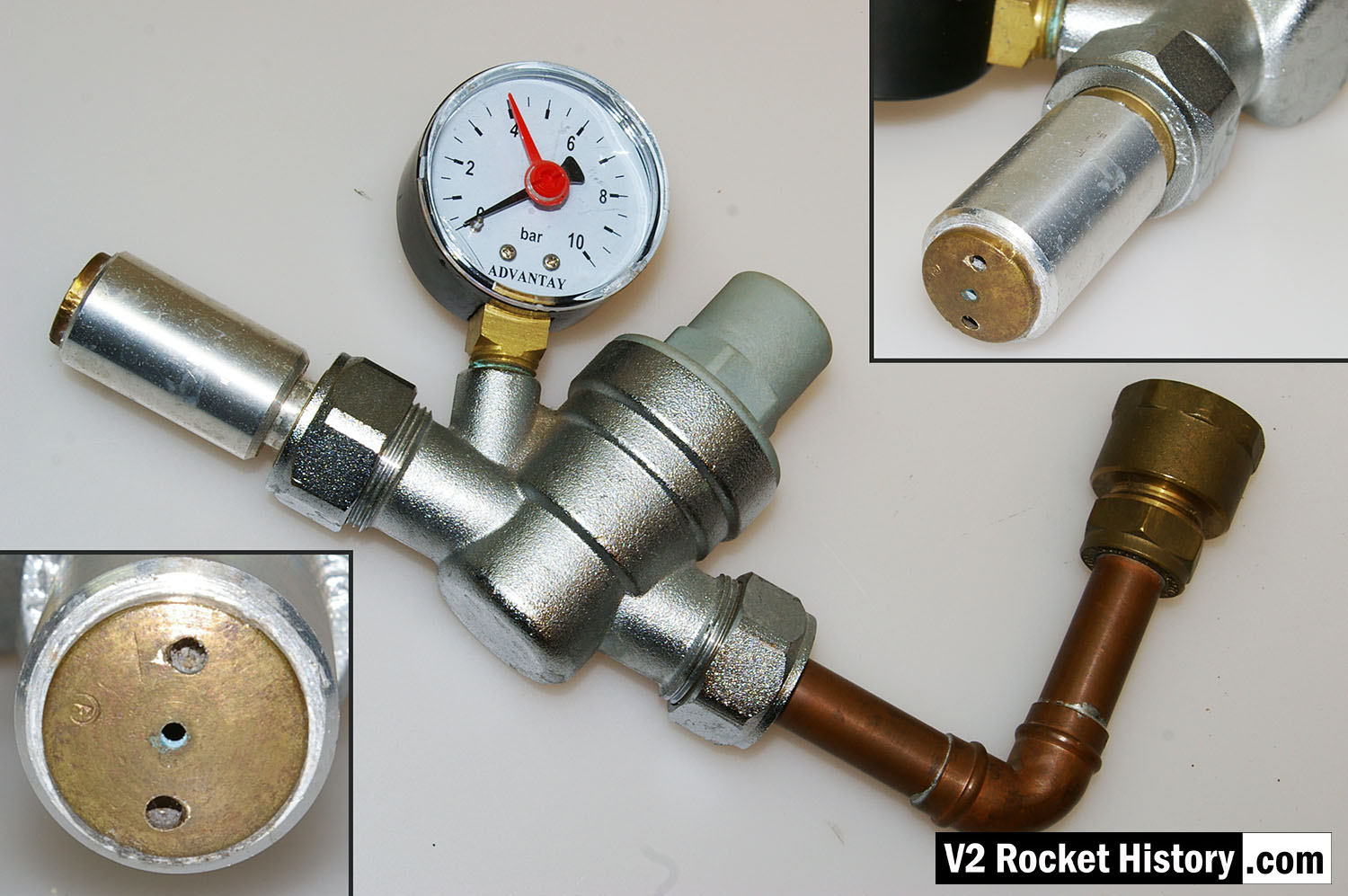
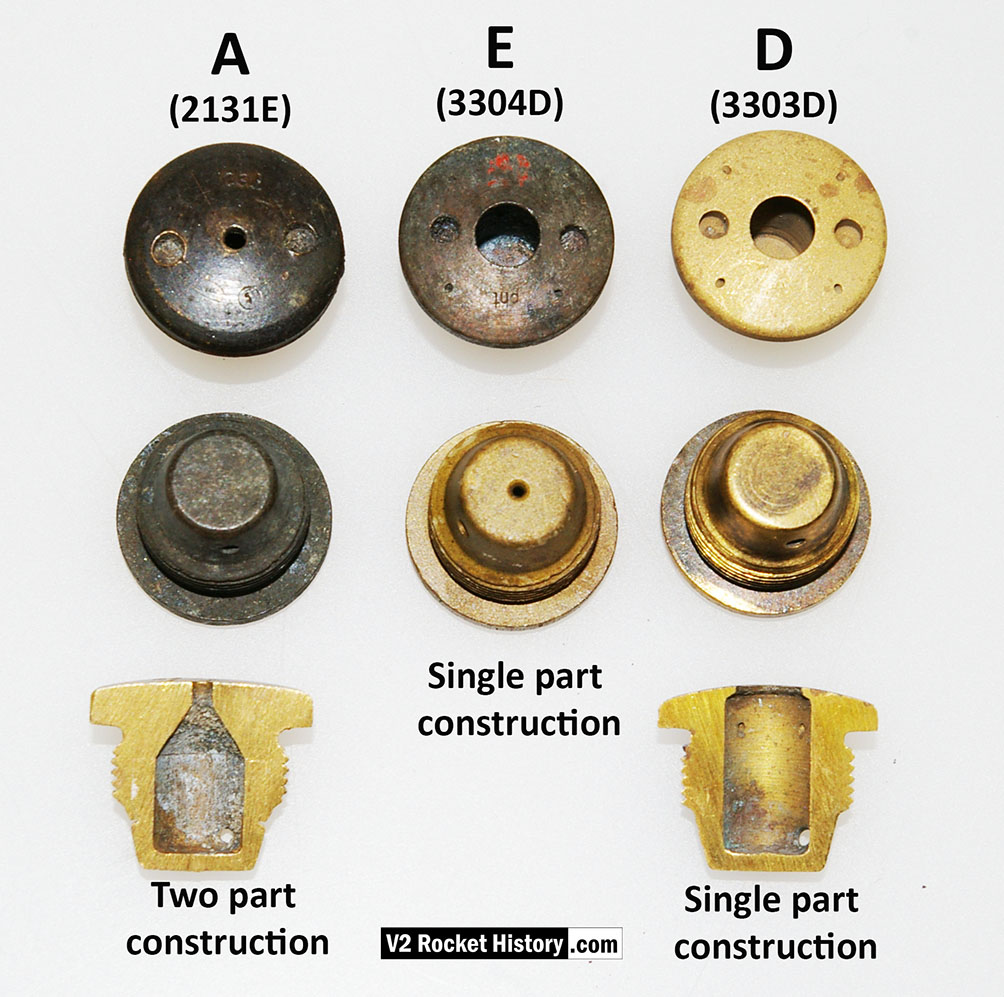
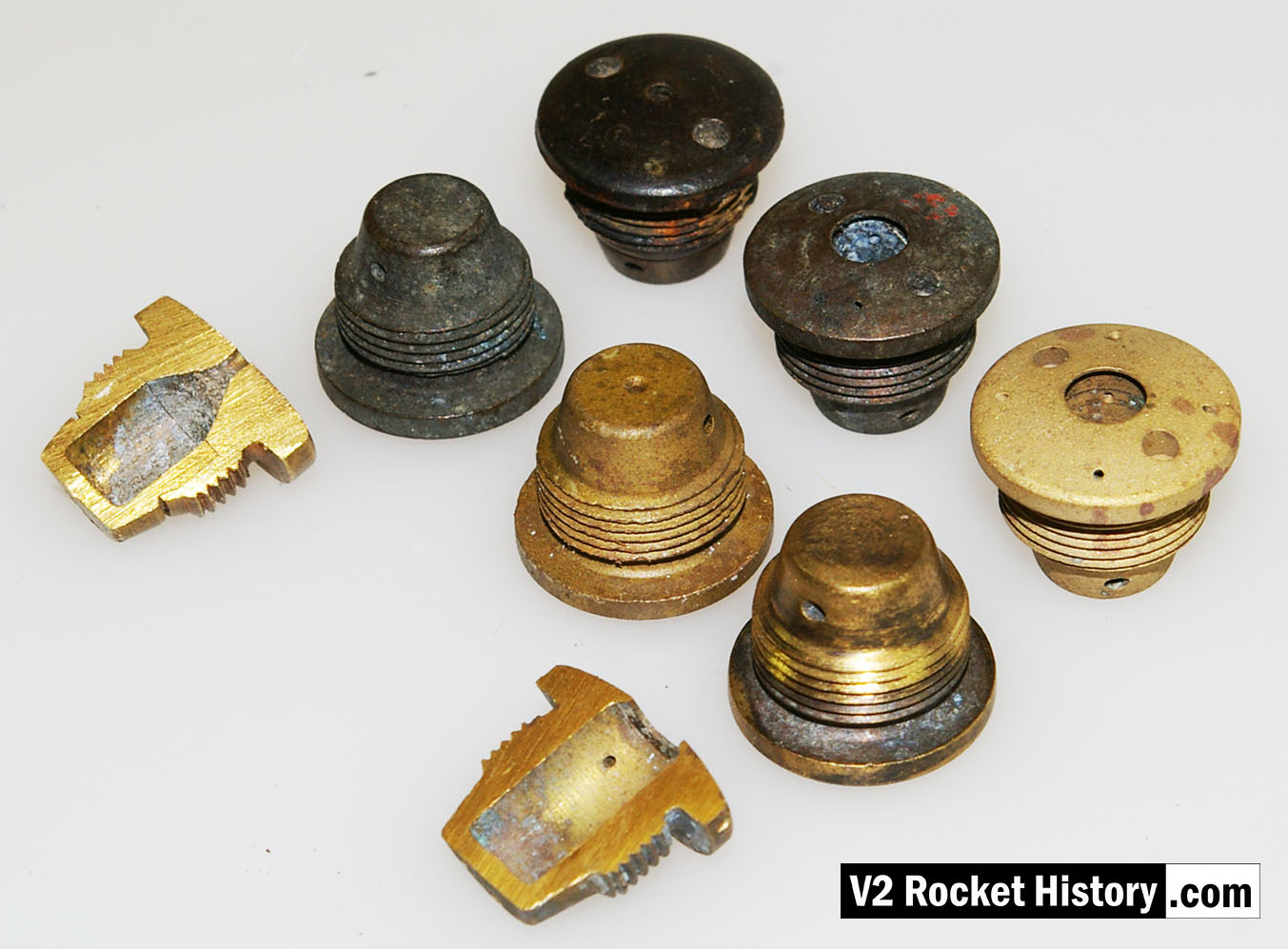
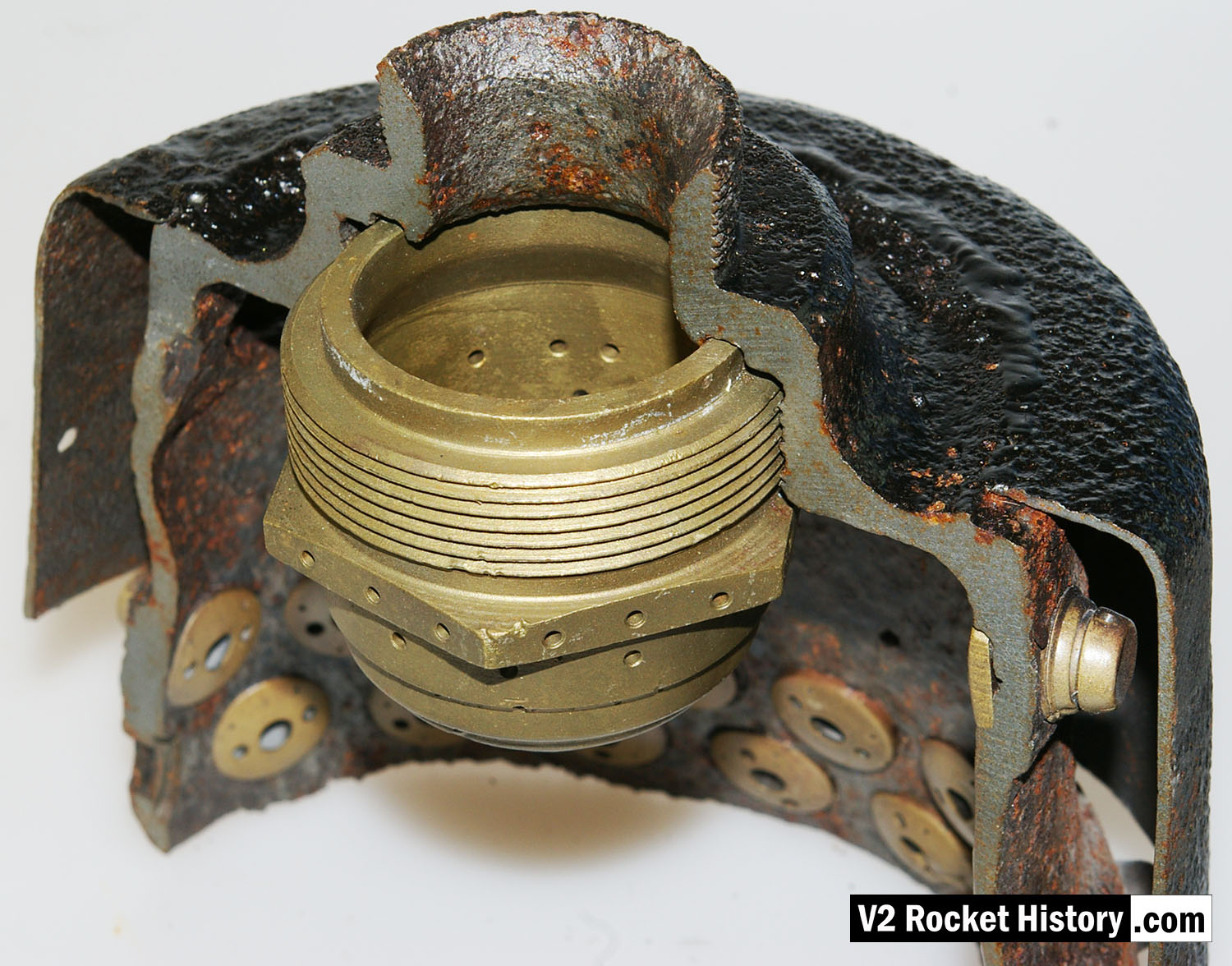

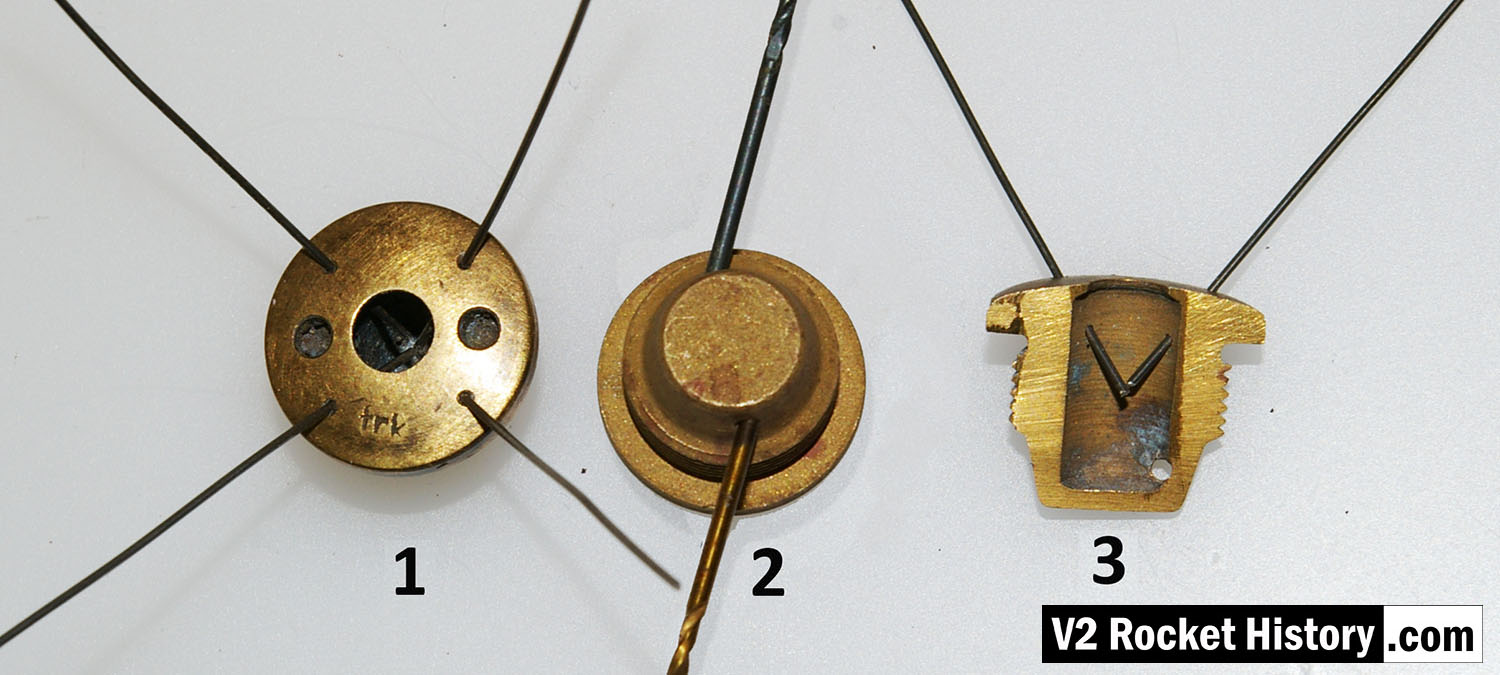
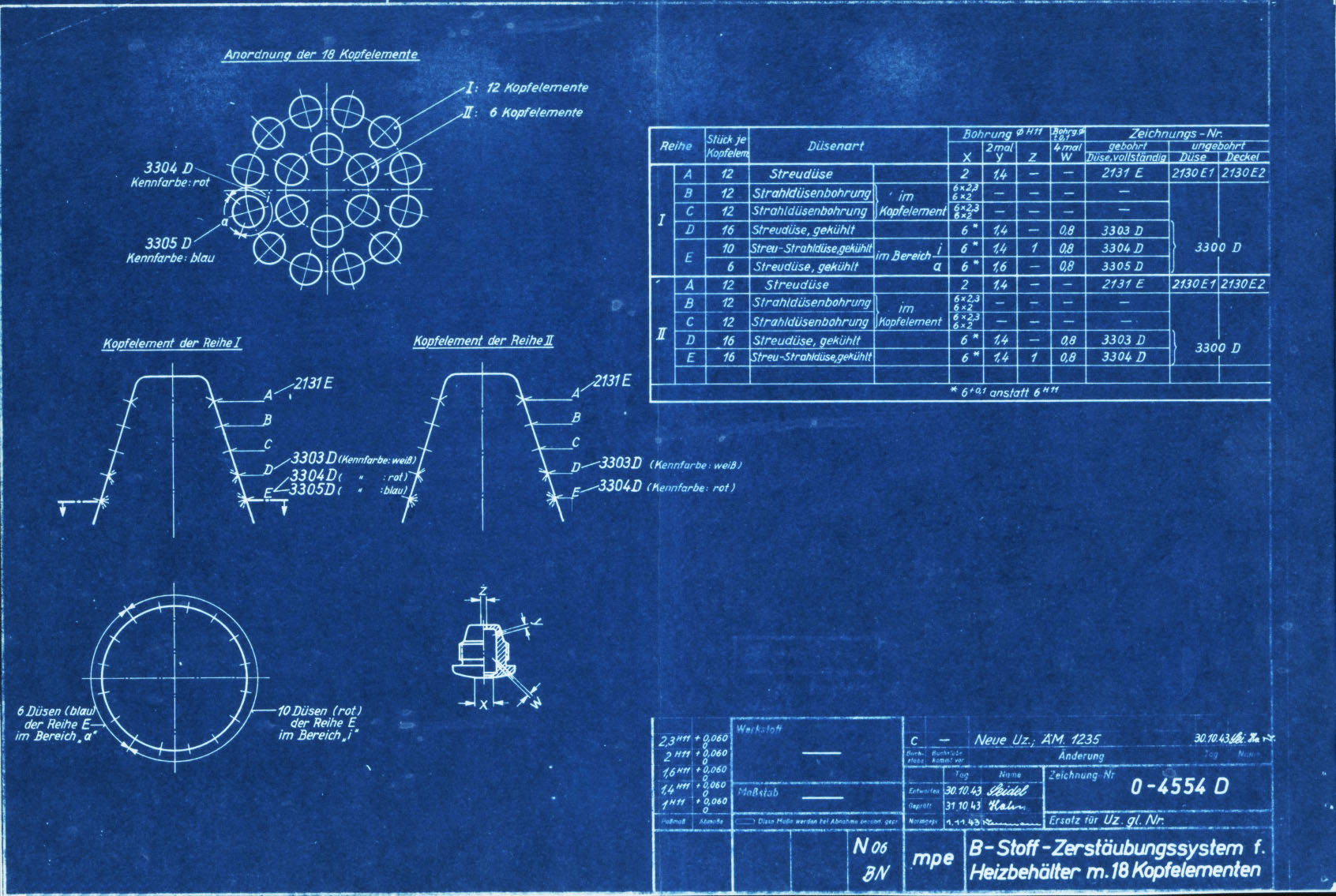
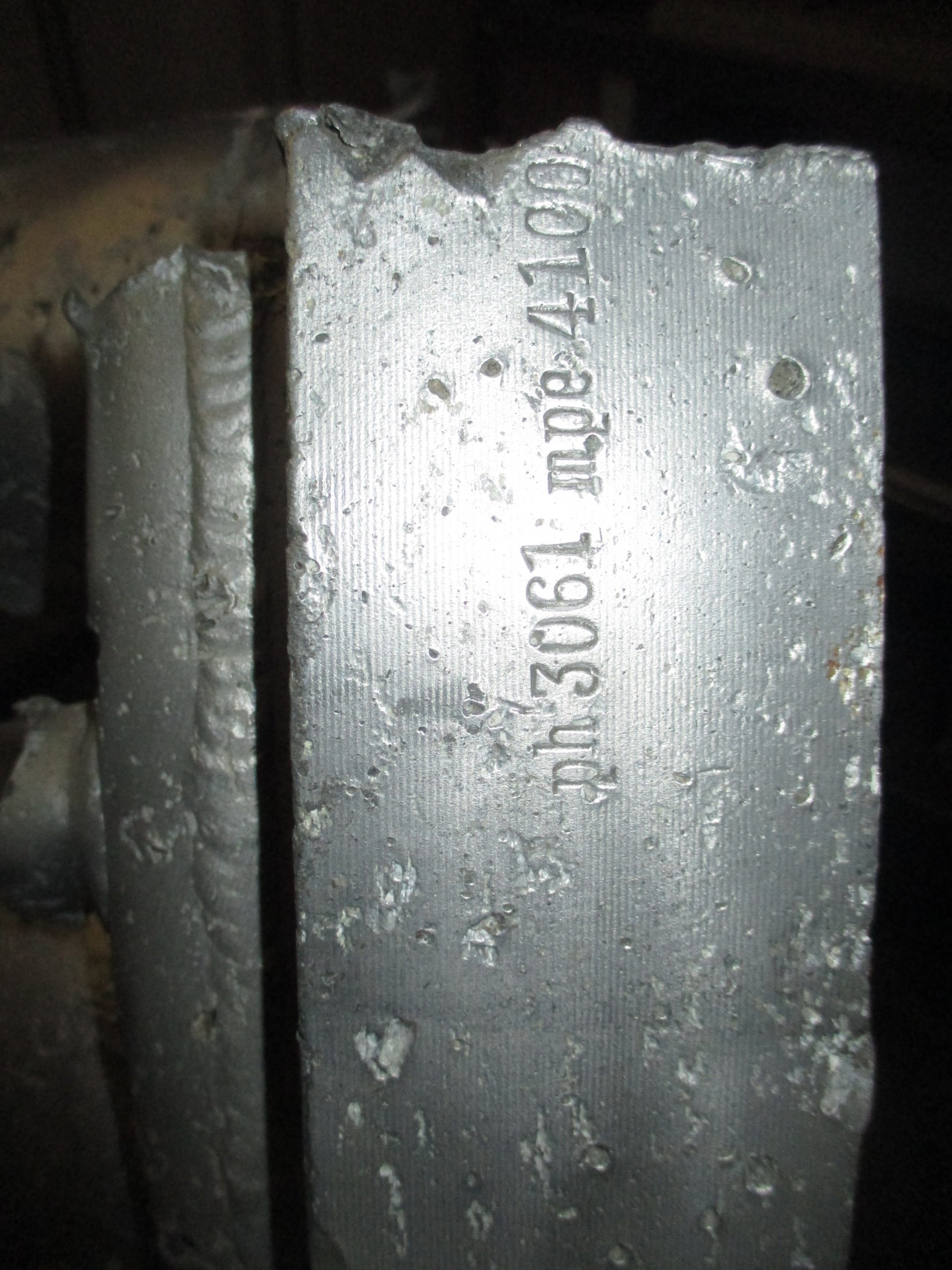
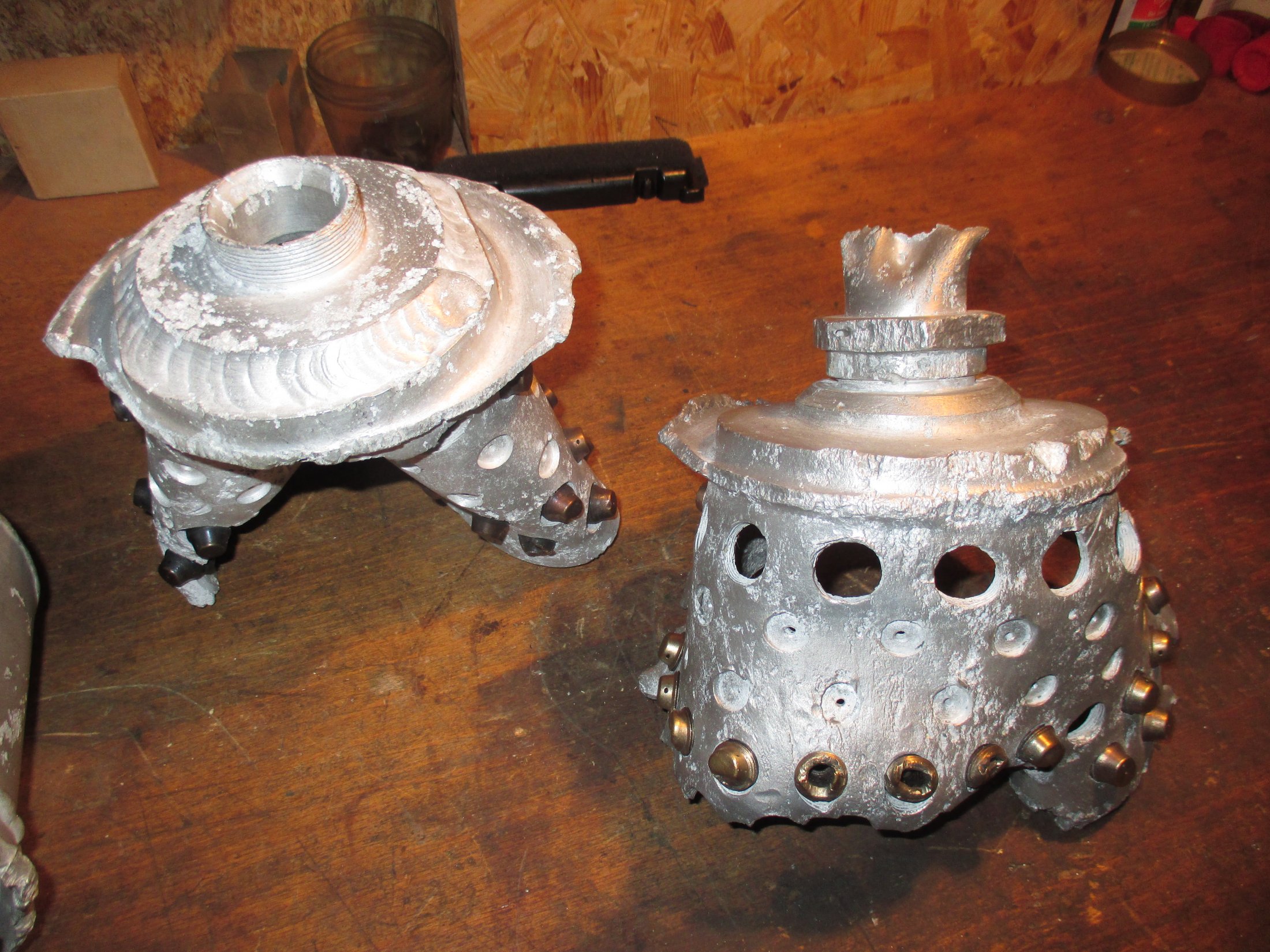
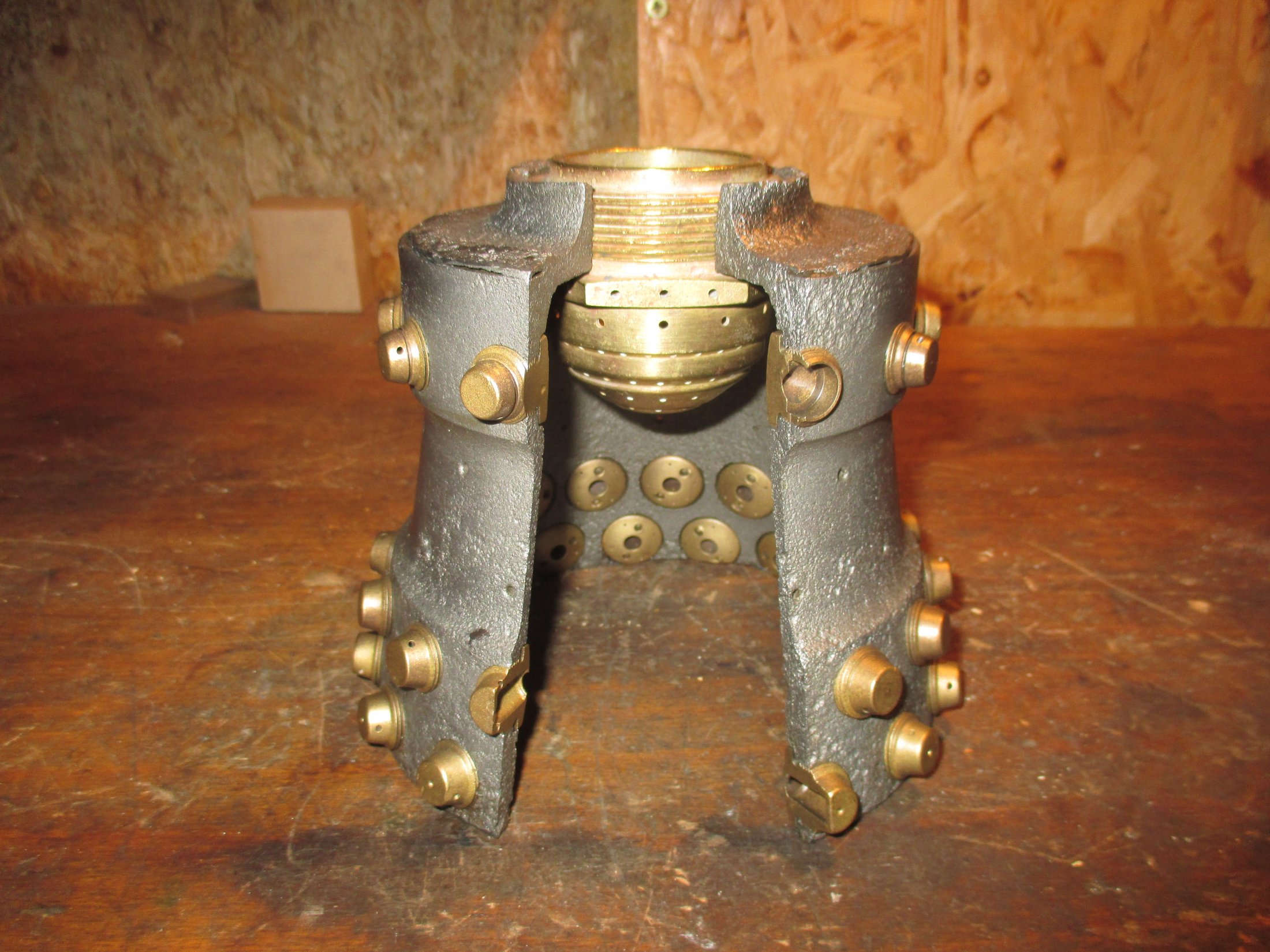
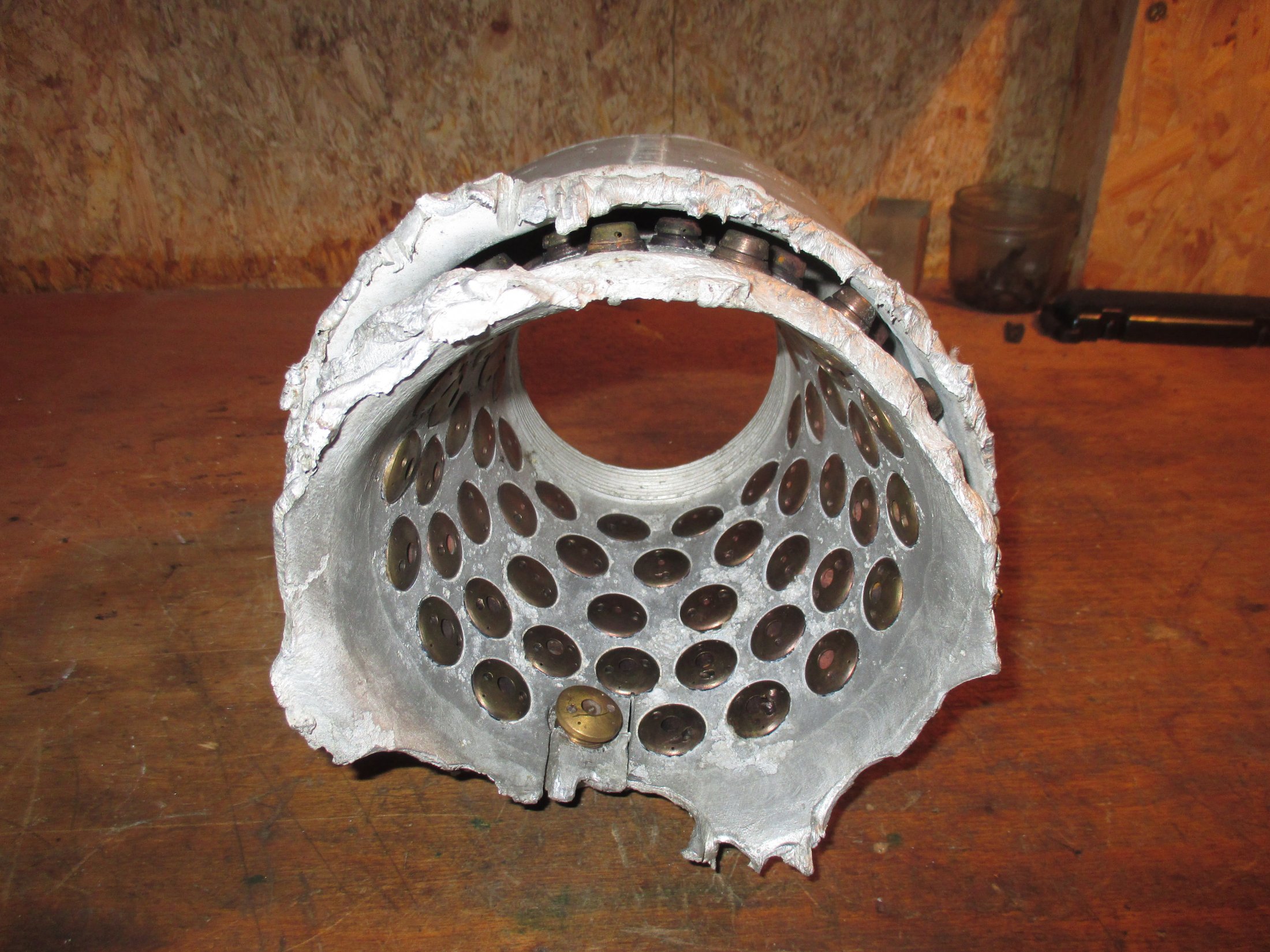
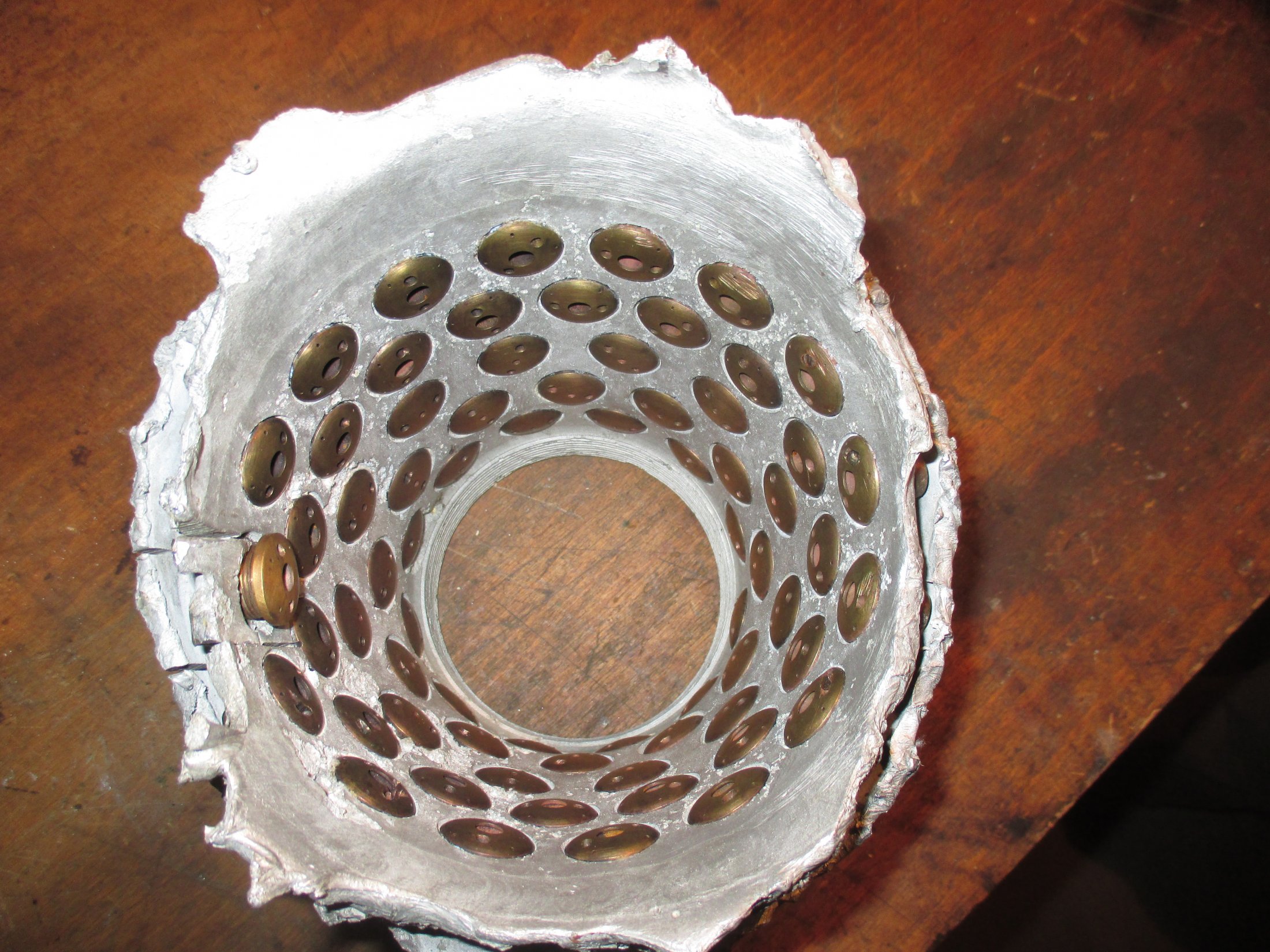
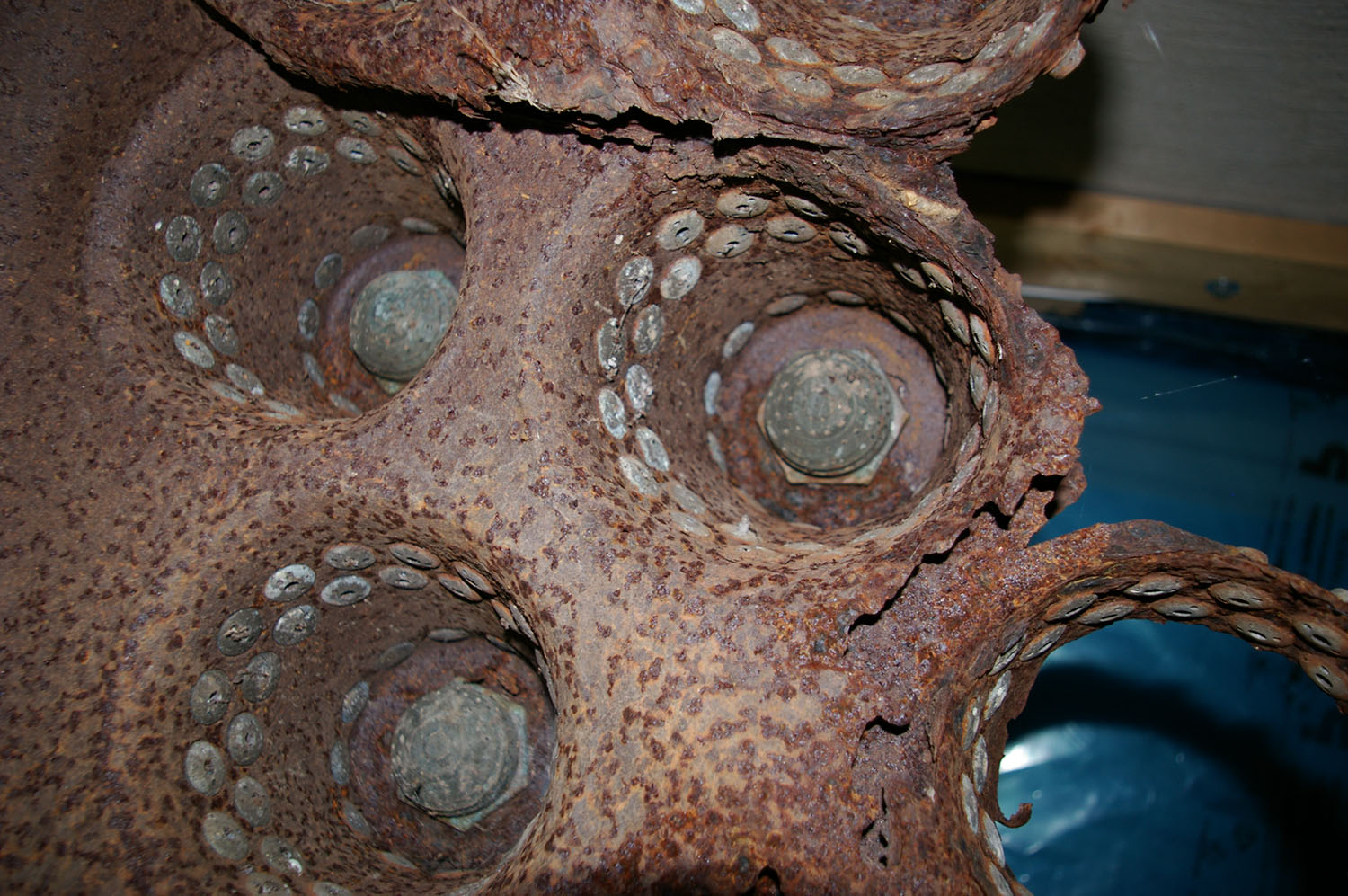
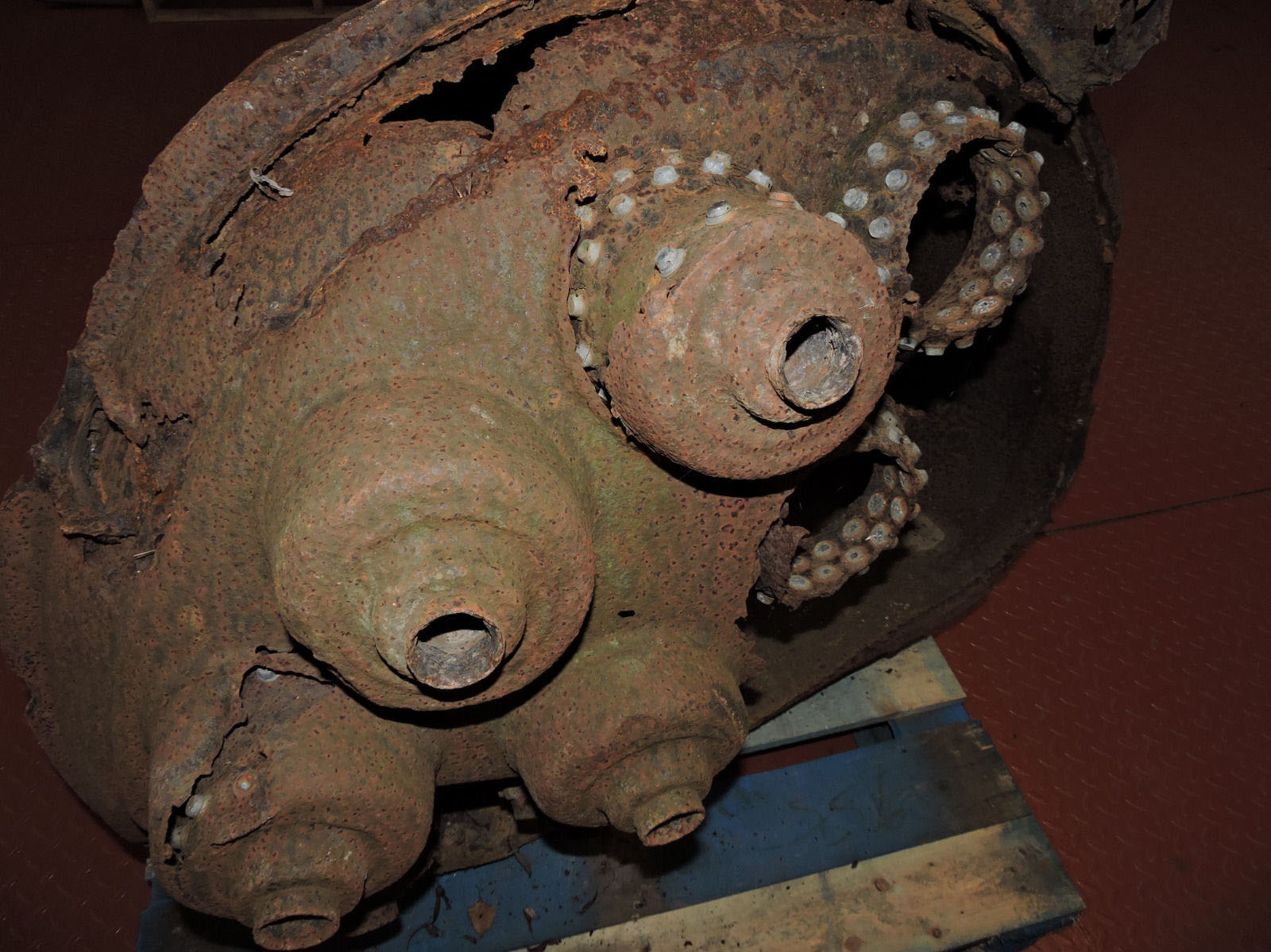
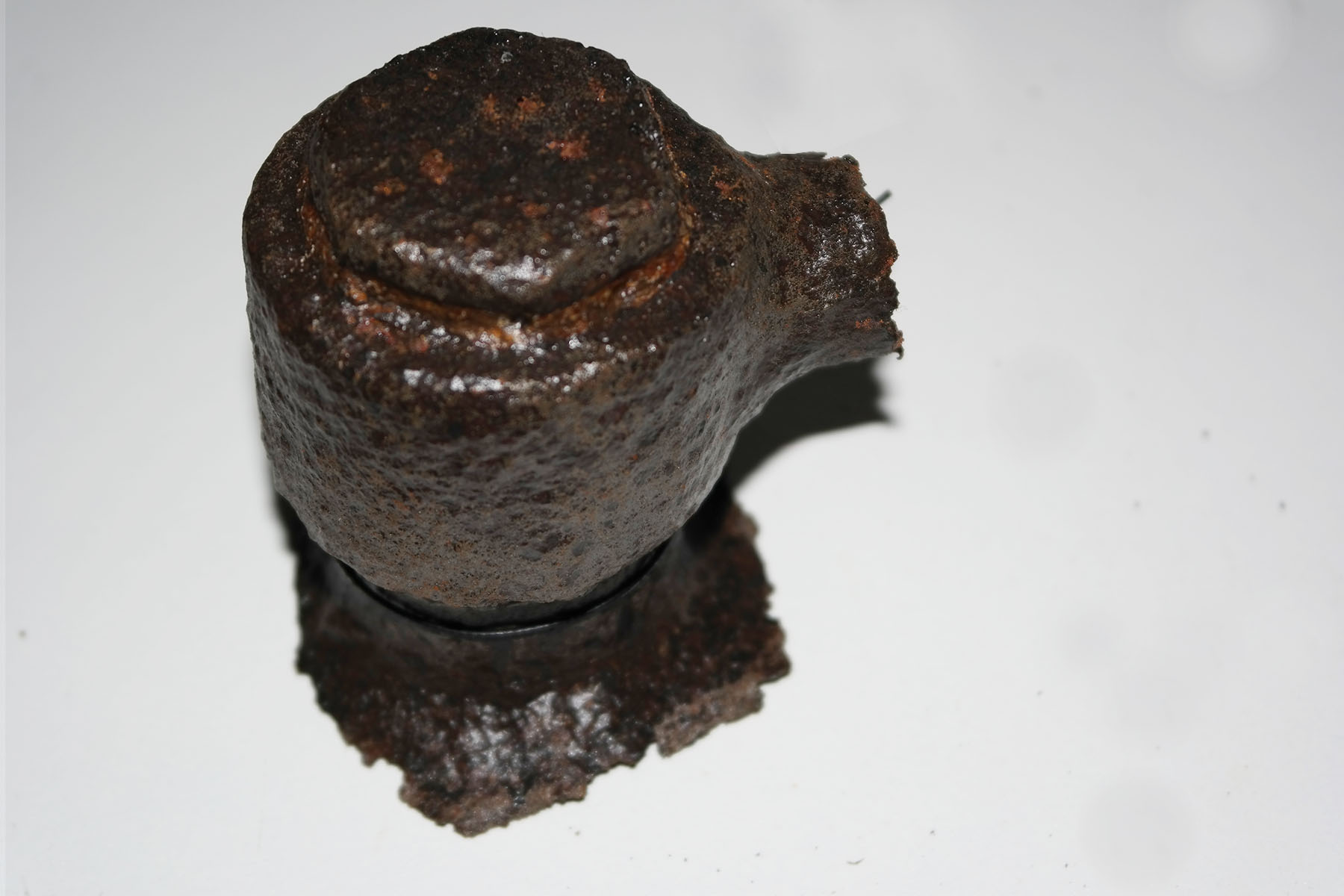
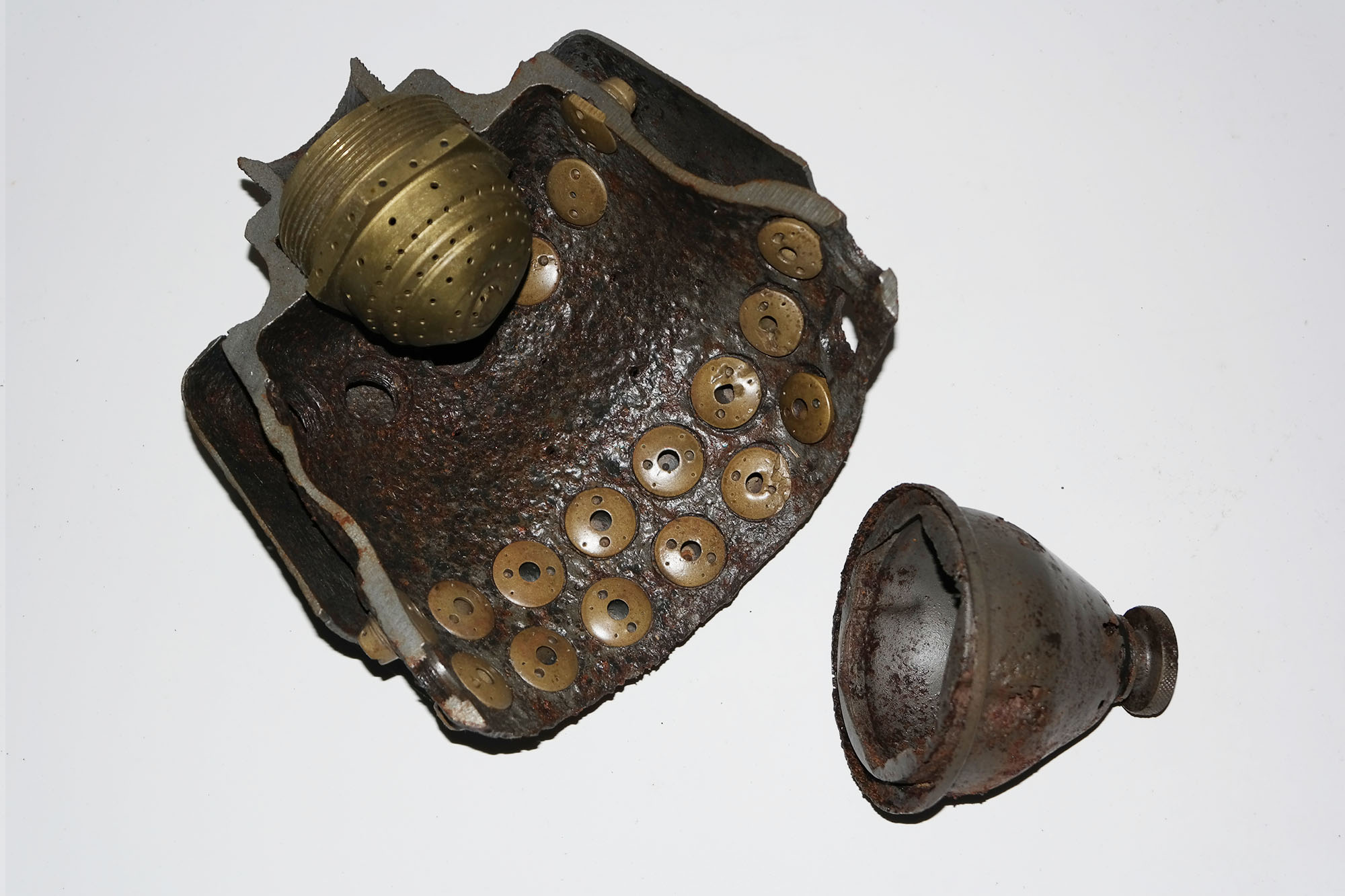
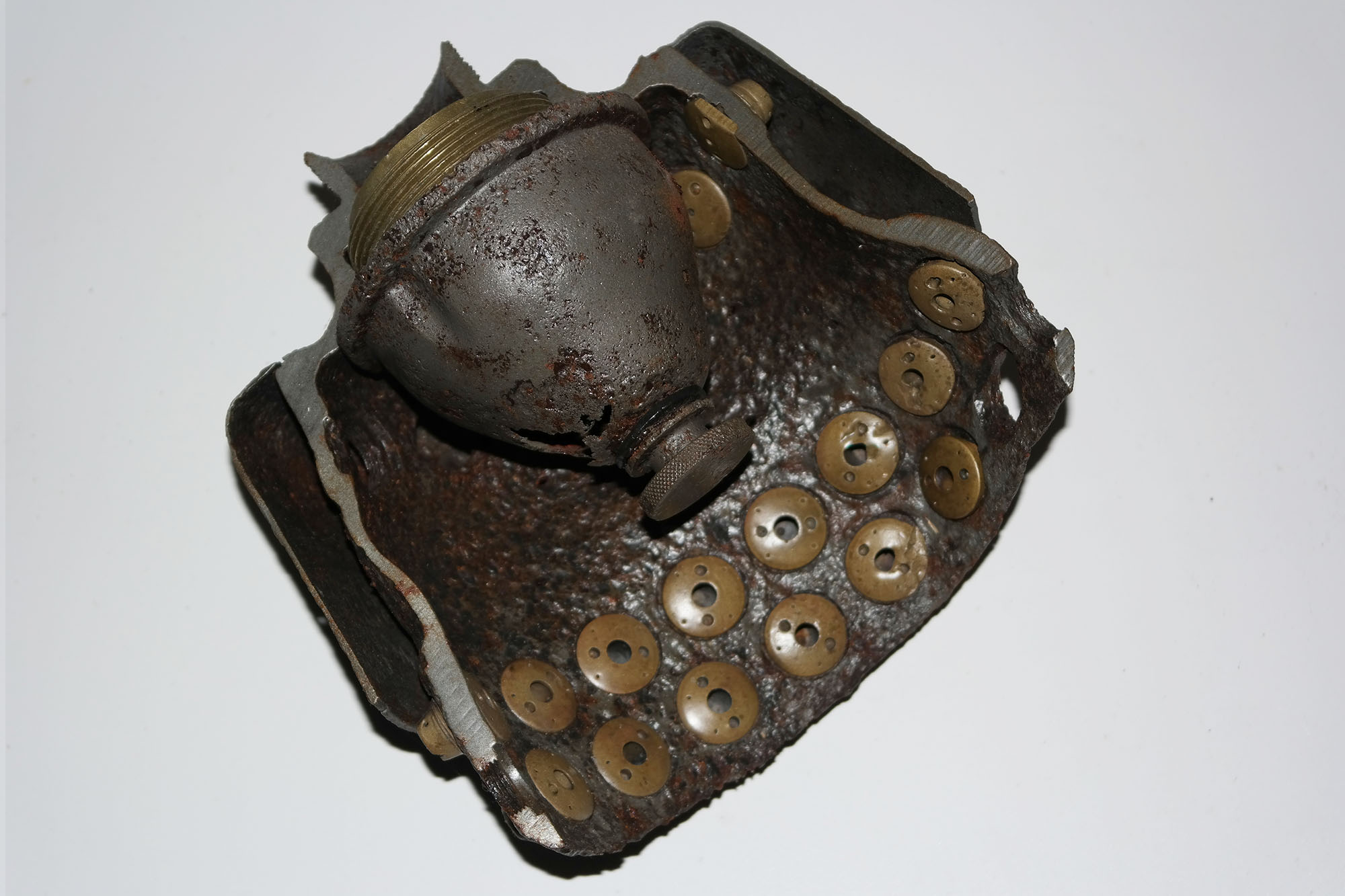
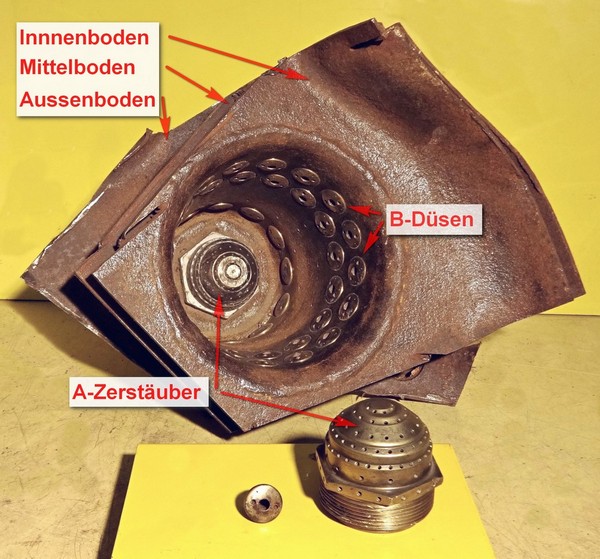
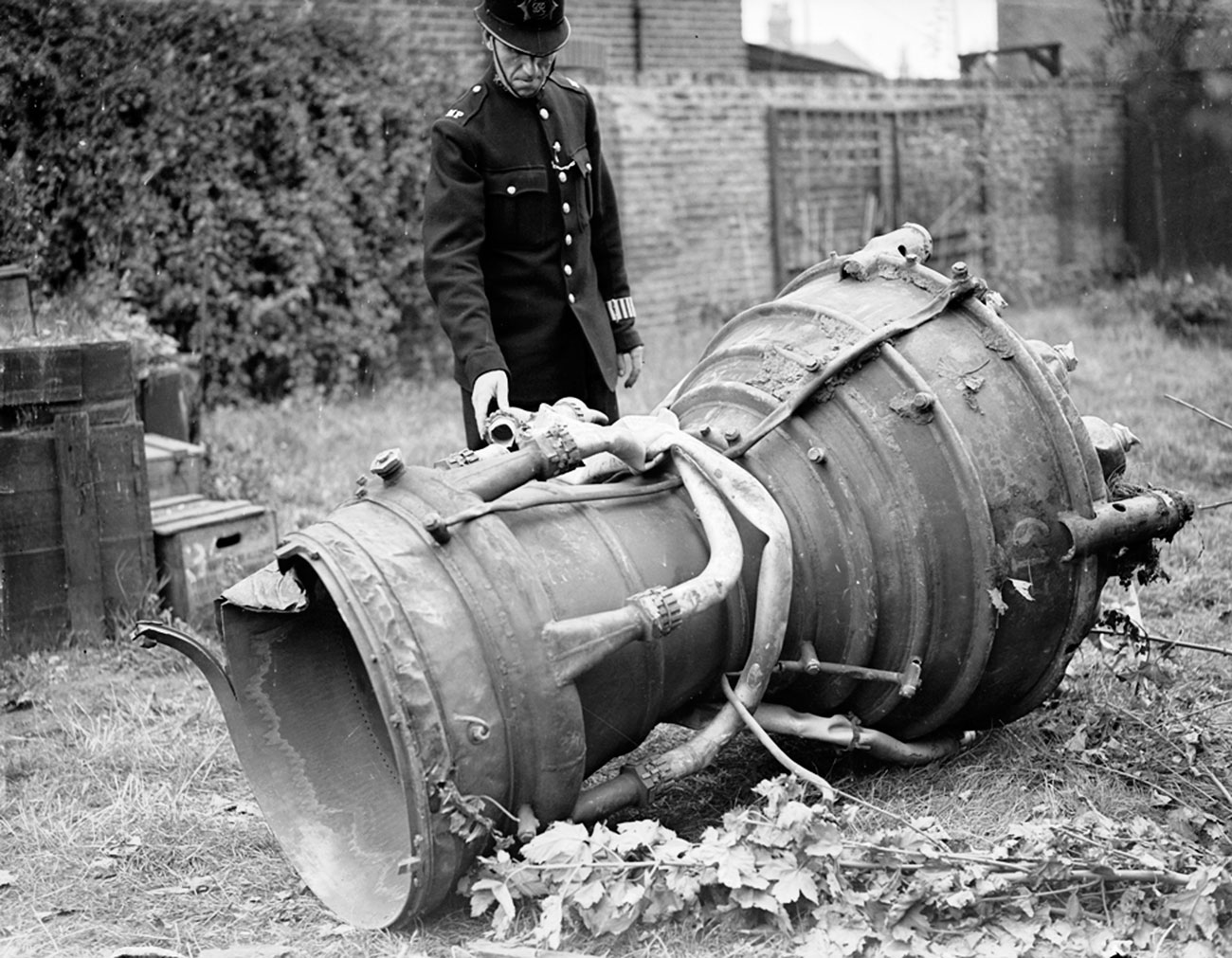
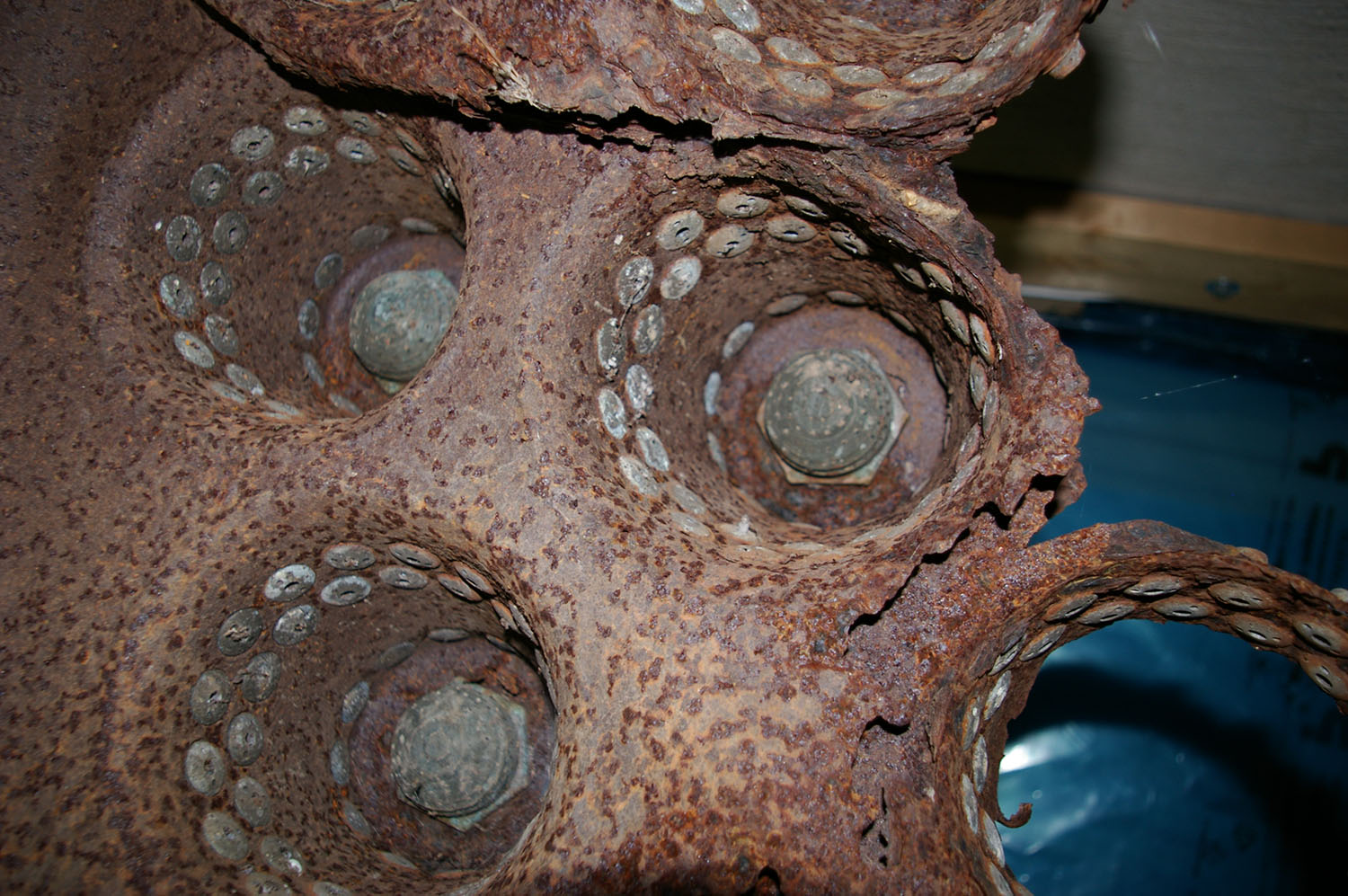
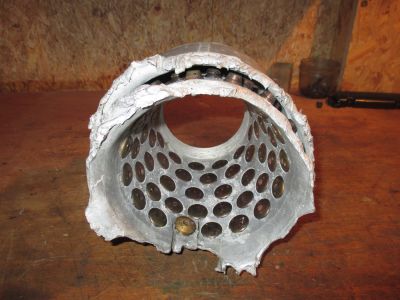
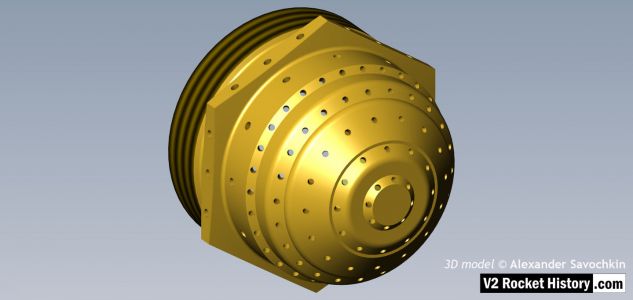
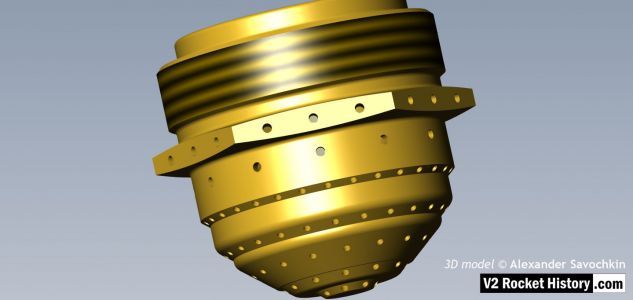
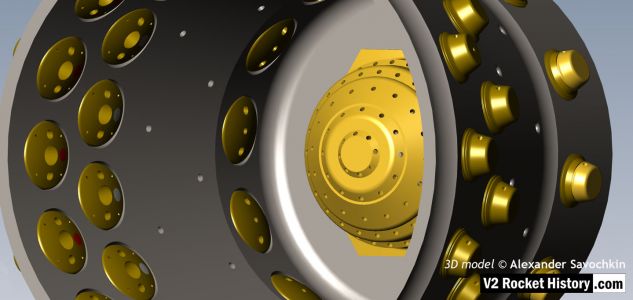
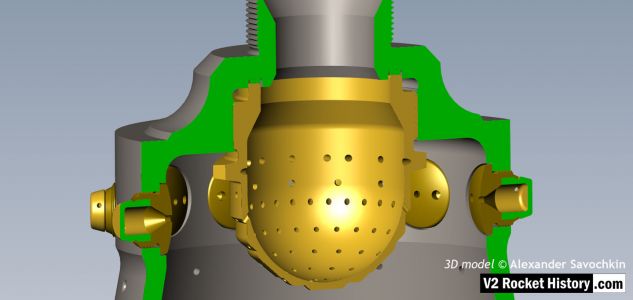
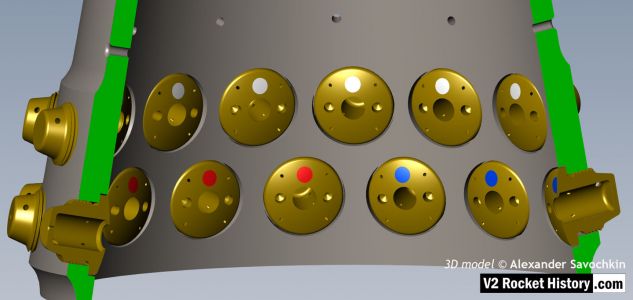
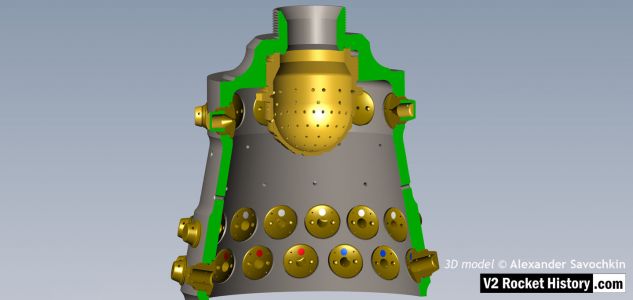
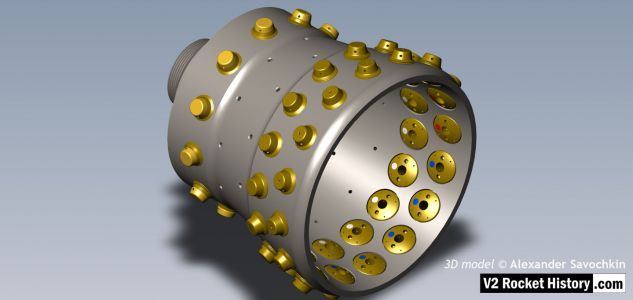
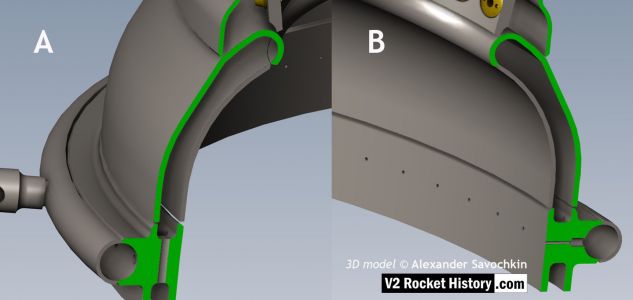
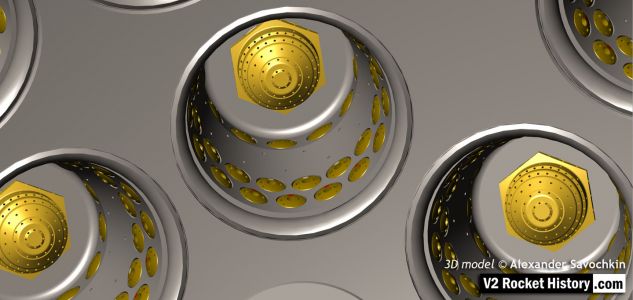
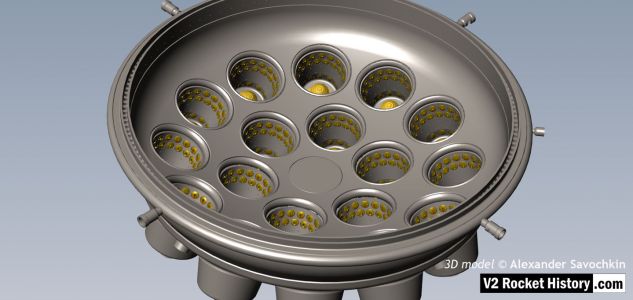
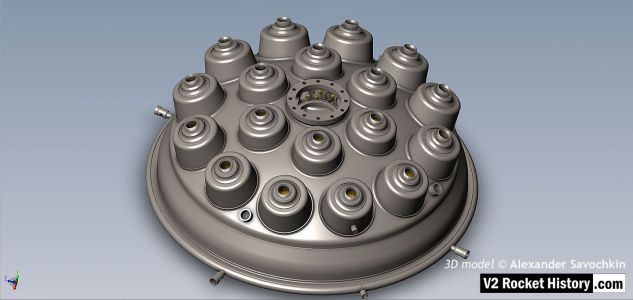
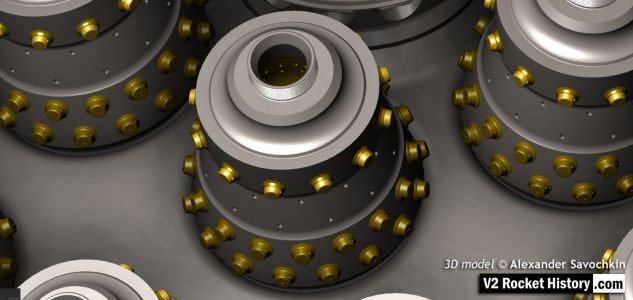
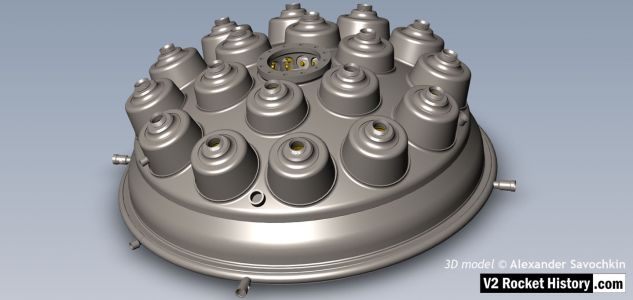
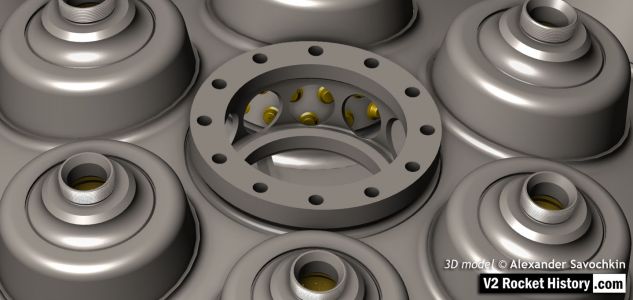
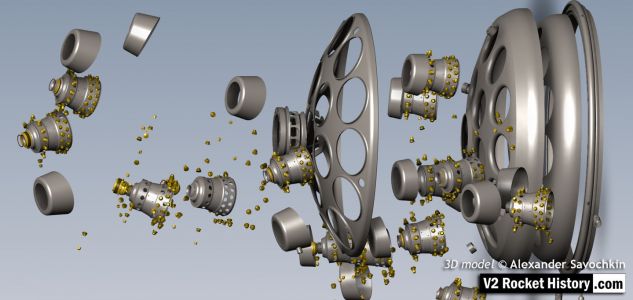
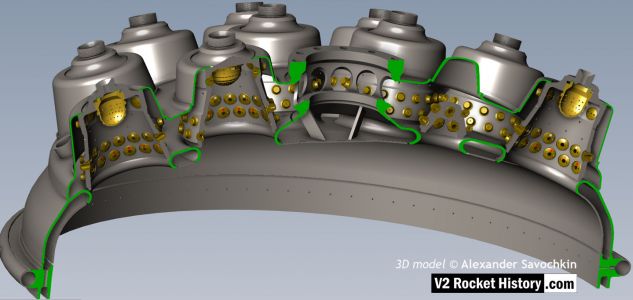
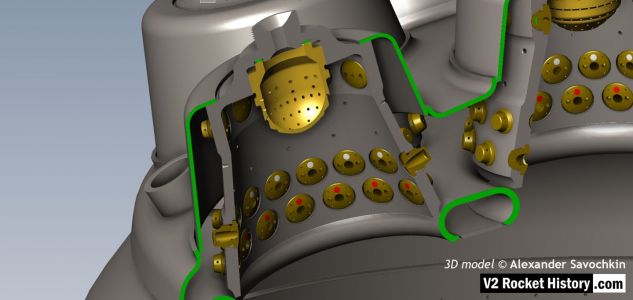

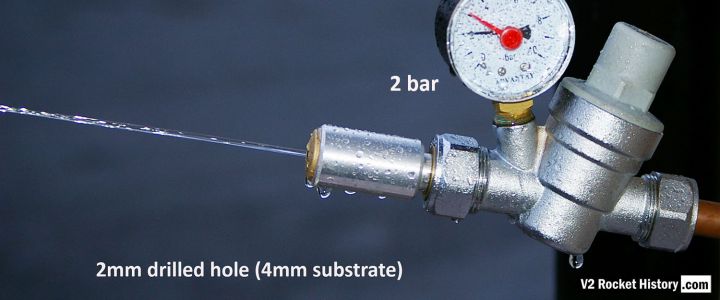

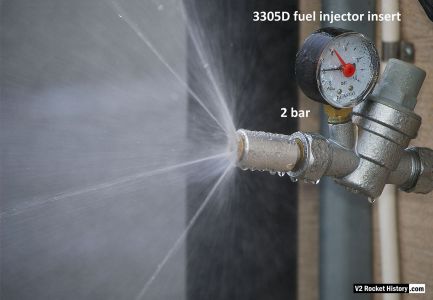
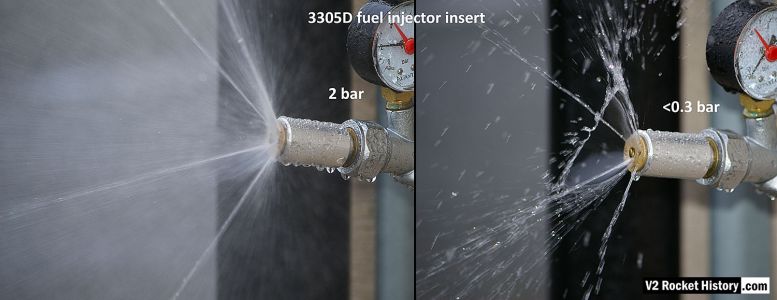
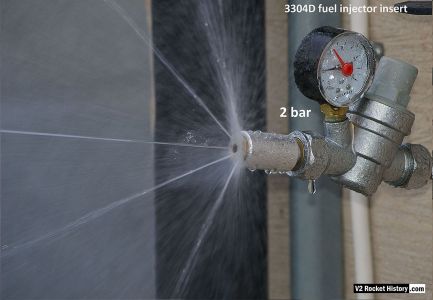
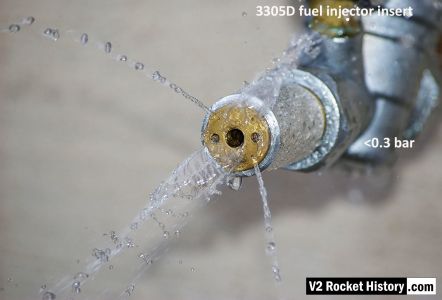
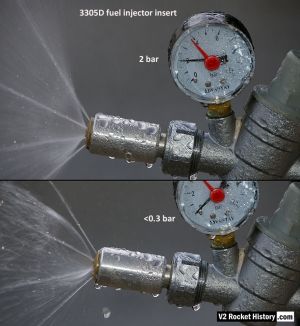
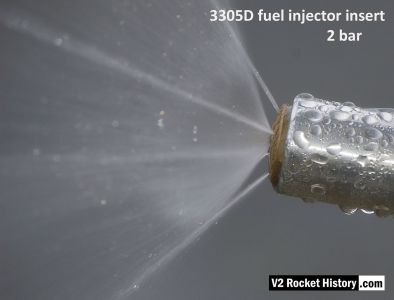
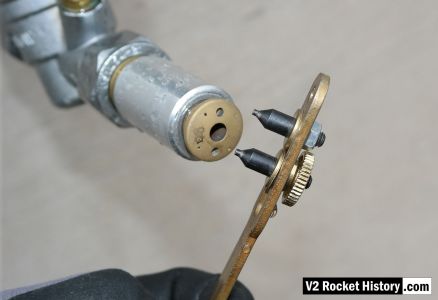
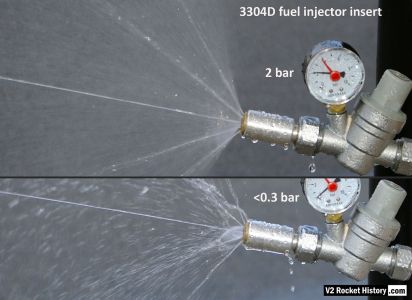
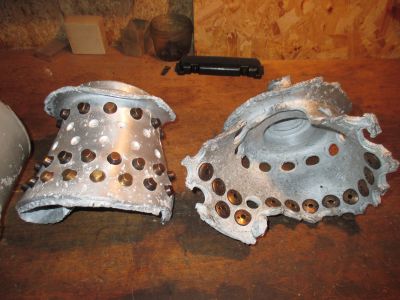

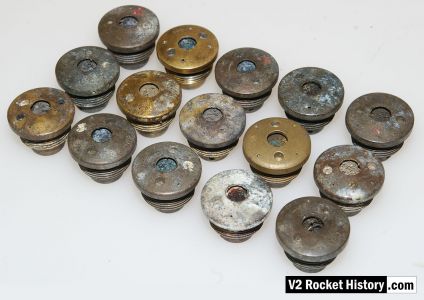


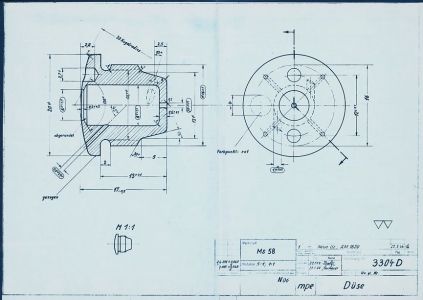
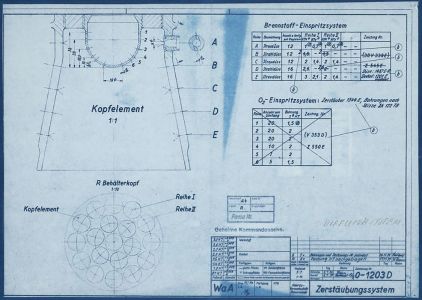
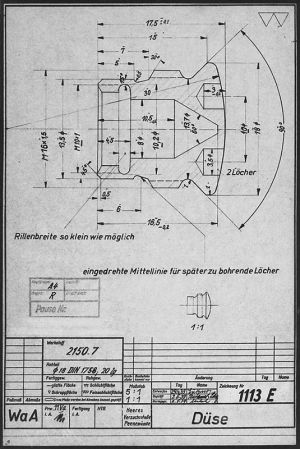

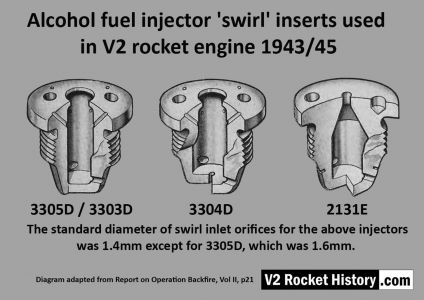
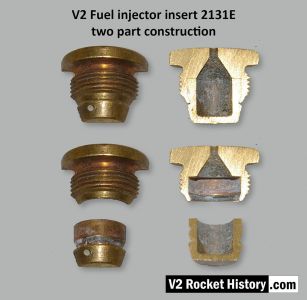

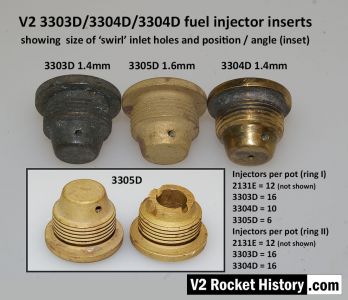
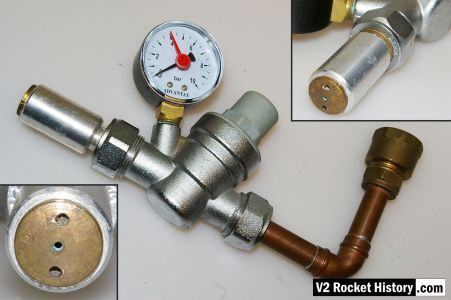
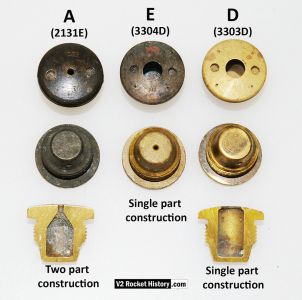
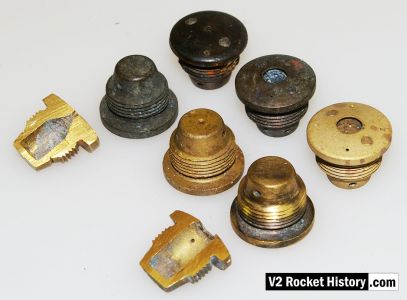
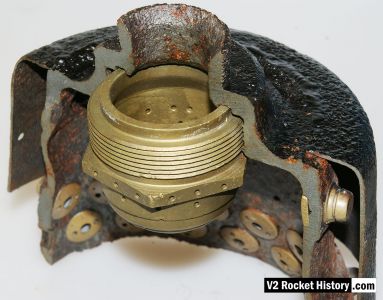
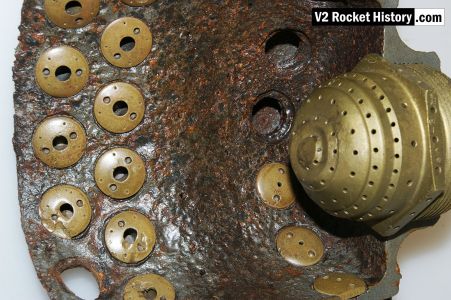
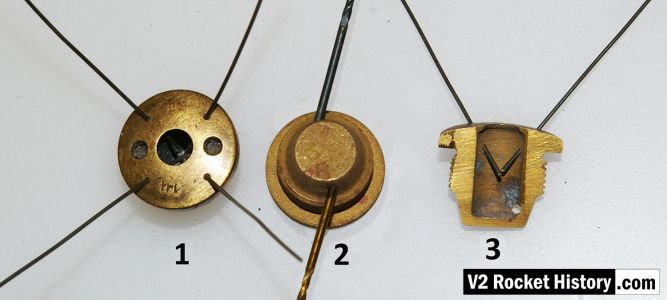
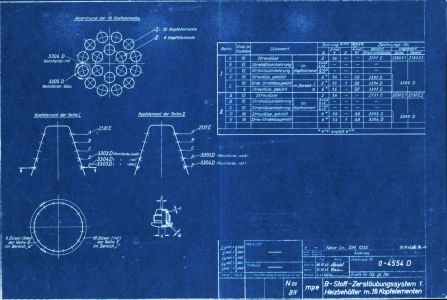
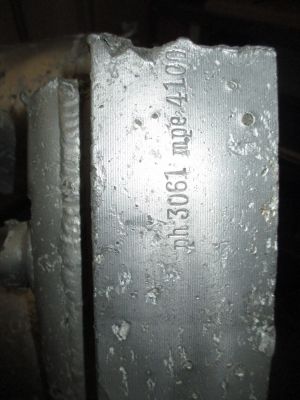
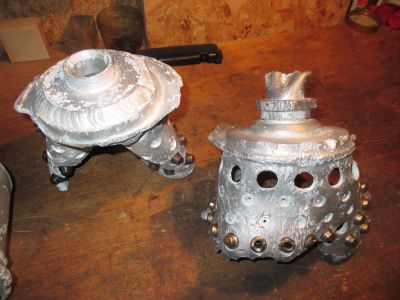
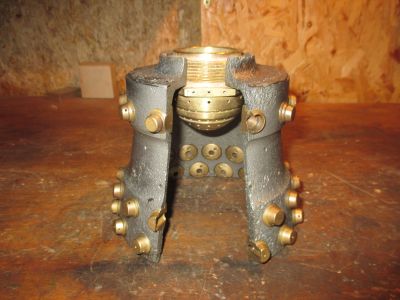
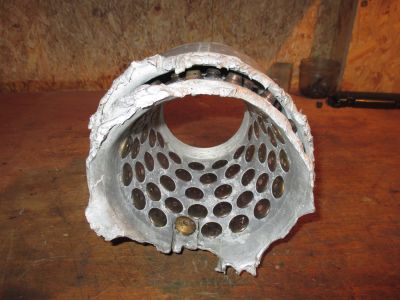
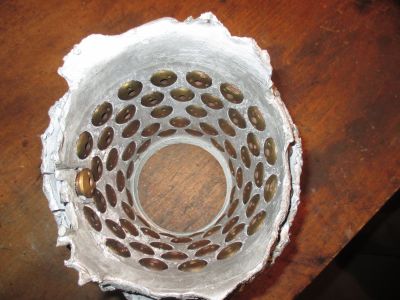
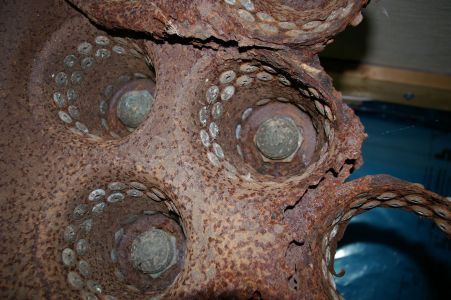
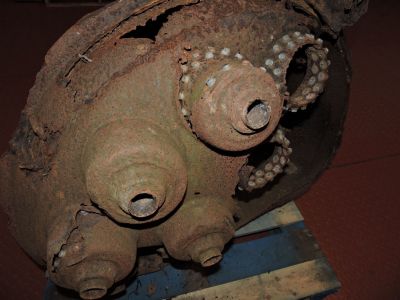
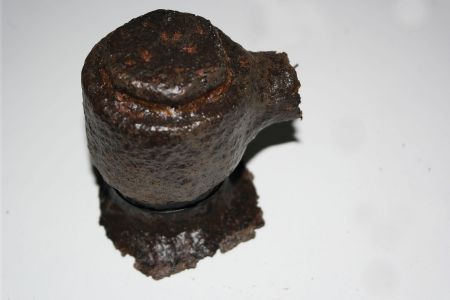
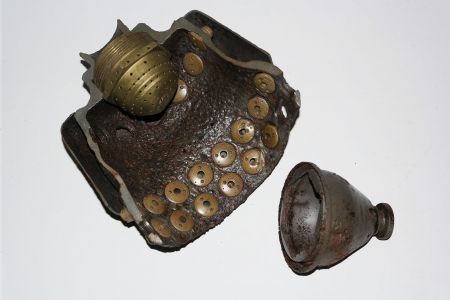
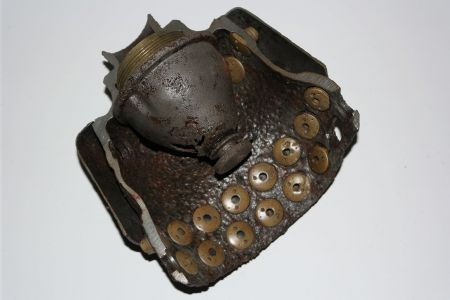
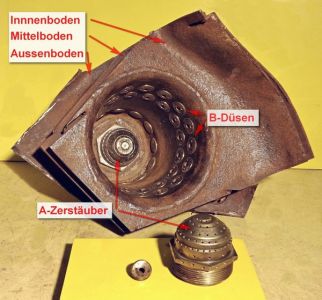
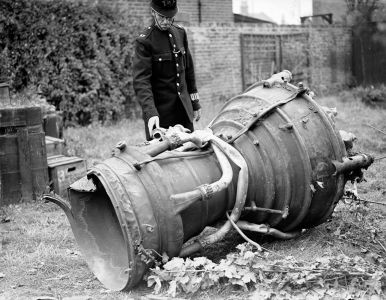
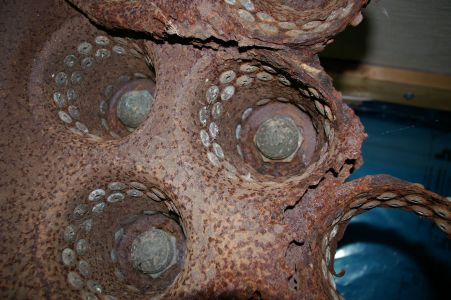
Relic of prototype A4 25-ton 1940/41 aluminium injector head basket (or pre-chamber) showing 68 copper alloy inserts in 5 rows. The standard configuration would later become 44 inserts in 3 rows 25 2mm diameter drilled holes in two rows situated at row 3 and 4 (counting from nearest the camera). Photo courtesy Host Beck Collection