
Archives: Gmedia Albums


Turbopump 3D CAD
3D CAD model images of the A4/V2 rocket engine’s steam turbine powered propellent pumps – all images by Ray Matter. To see Ray Matter’s blog 3D CAD modelling the V2 rocket turbopump introducing these images, just click the link.
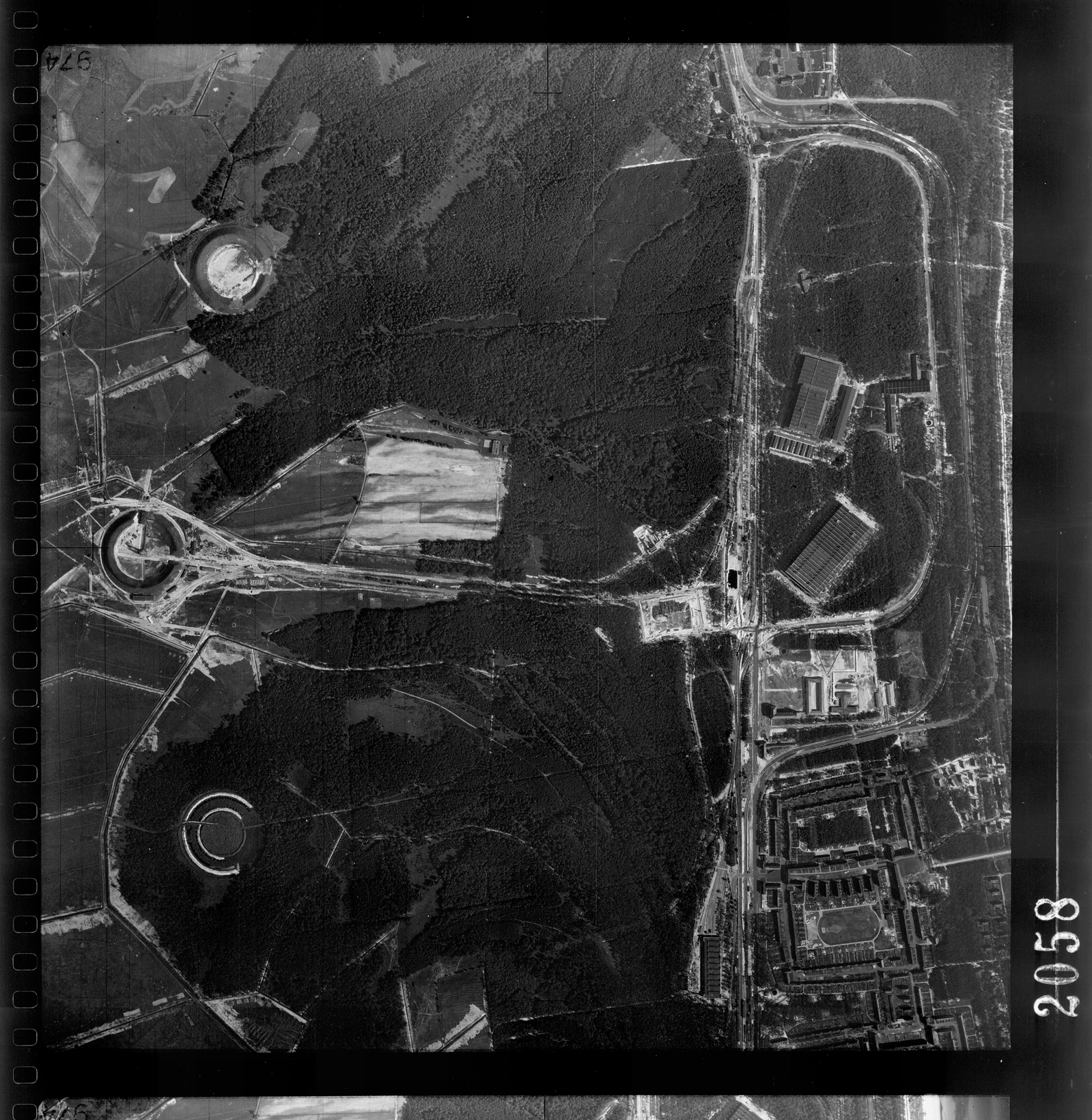
RAF reconnaissance photo showing the Werk Süd region with the F1 pre-production hall and to the north the IW repair and maintenance hall, centre right, and road rail links to Prüfstand XI (Test Stand 11, circular rampart centre left) heading directly left from F1. P-XI was conceived to provide engine test facilities for the nearby pre-production hall. Scroll down to see GPS map, the marker index is set to the centre of P-XI, click map and switch to satellite view and you will see that only a small section of the circular rampart remains visible. You can easily zoom out to cover the coast area where F1 and the equally large Repair & Maintenance Workshops are located. The area immediately surrounding P-XI is now contained within a commercial farming operation with sheep appearing to be the staple – or was anyway, at the time of our first visit to the vicinity in 2010 and our last in 2017 – none of the sheep seemed to recognise us though so they may have changed. (for access to restricted areas click here)
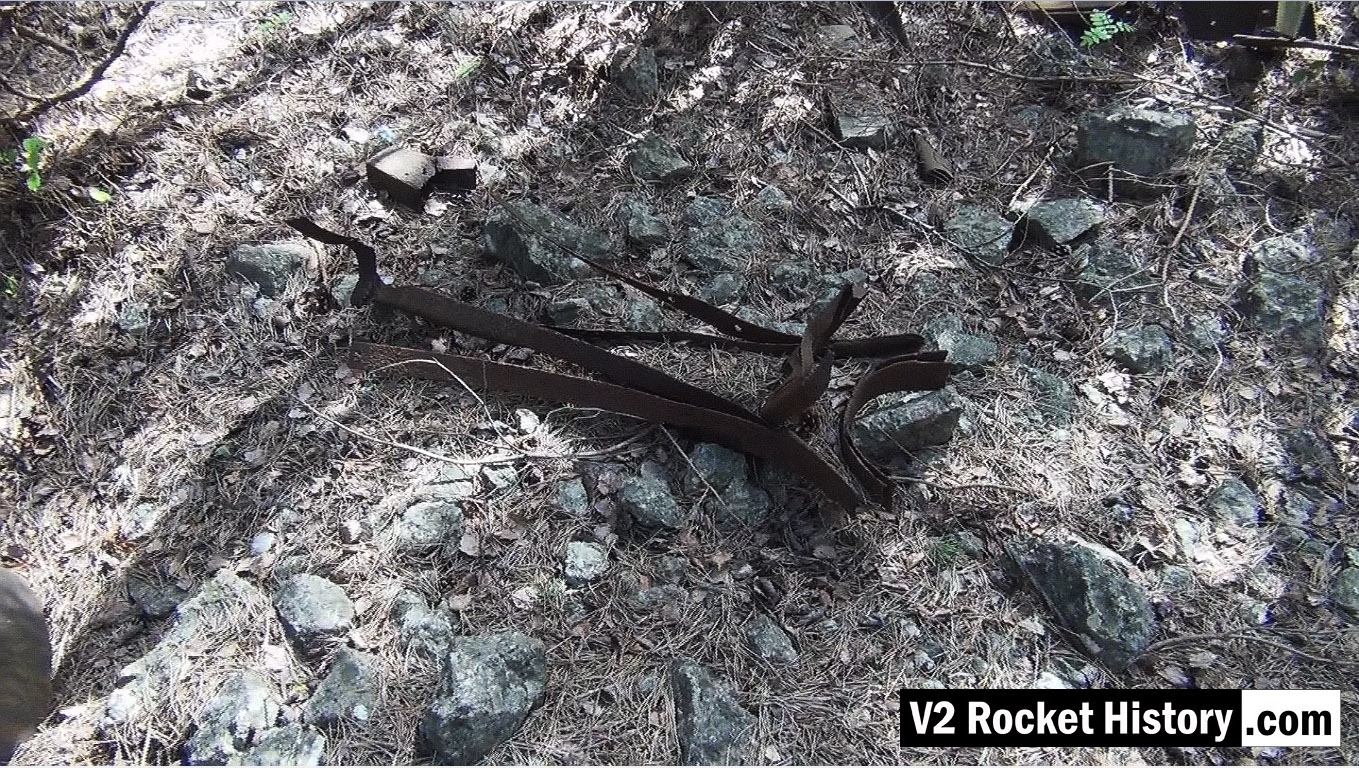
Picture shows parts of V2 missile fin structure laying on open ground near area between admin offices and F1 (near Admin. block railway platform, see map).
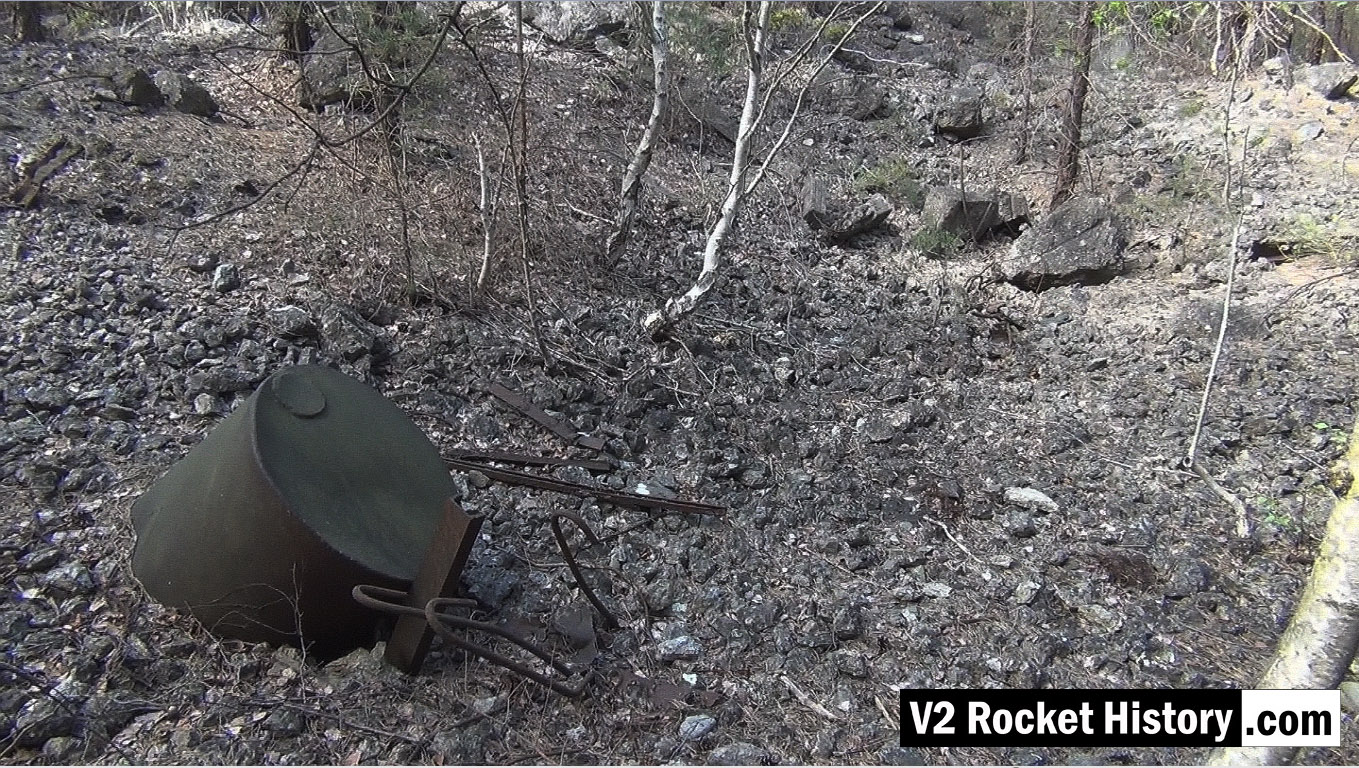
Picture shows metal debris within the F1 factory boundary walls. The purpose of the part buried liquid storage vessel in the foreground is unknown but it is not a vessel capable of being pressurised. Other assorted metal debris include pipe and cable wall cleats, as well as steel armature rods from reinforced concrete castings (powerful demolition explosions have freed the steel rods from the concrete). These reinforcement rods are a common sight in the environs of Fertigungshalle Eins (F1) and the nearby Repair & Maintenance Hall (R&MH).

This picture shows a small debris field of steel fragments from the V2 missile 130m South-East of F1, and just 20m to the North East of the foundations of a small heat distribution building. Various body and frame parts can be seen and in the middle foreground a 350mm segment of curved missile body ring is visible. These parts have almost certainly been dug up and exposed by the action of metal detectorists. The metal fragments have been abandoned by their finders as they are perceived to have no financial value and hence are not worth removing from the site.
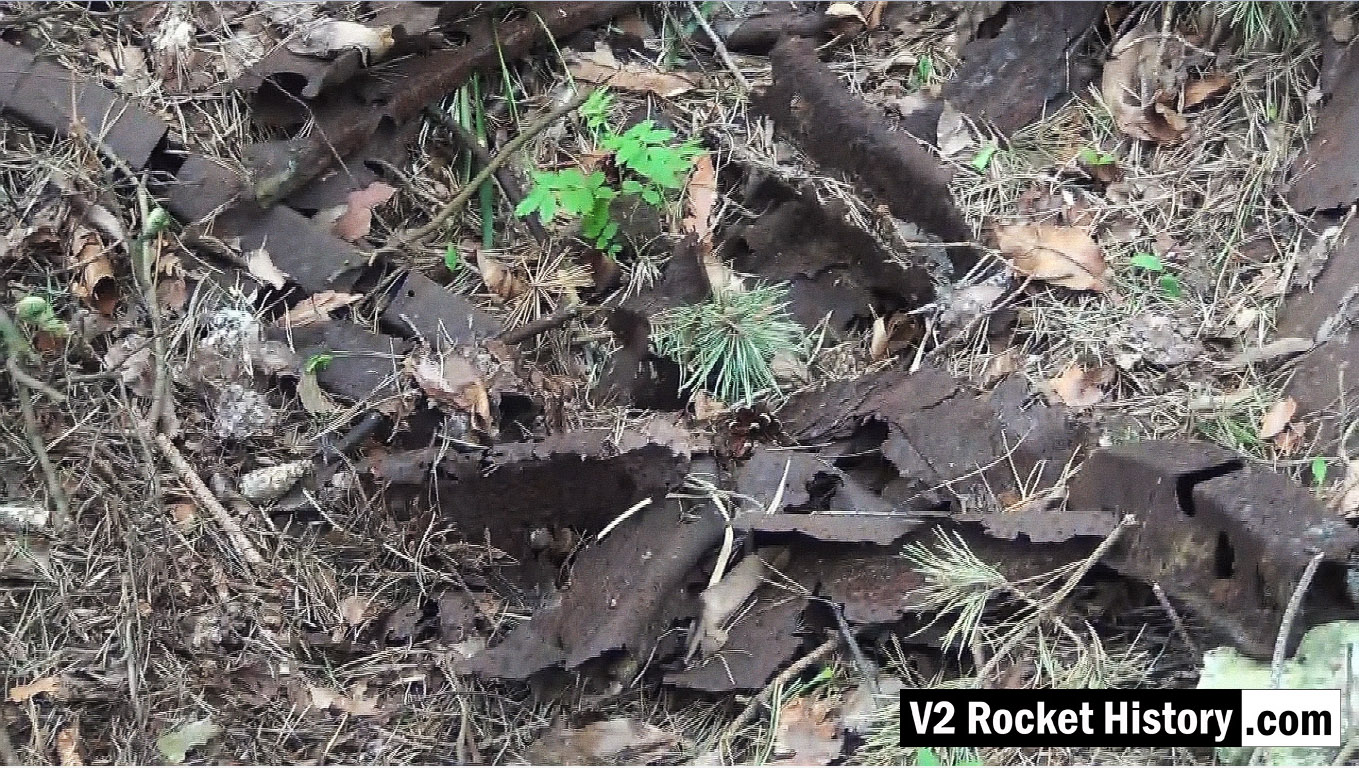
This picture shows a close up detail of parts in a small debris field of steel fragments from the V2 missile 130m South-East of F1, and just 20m to the North East of the foundations of a small heat distribution building. Various body and frame parts can be seen and in the upper left and two segments of curved missile body ring are visible. See previous.
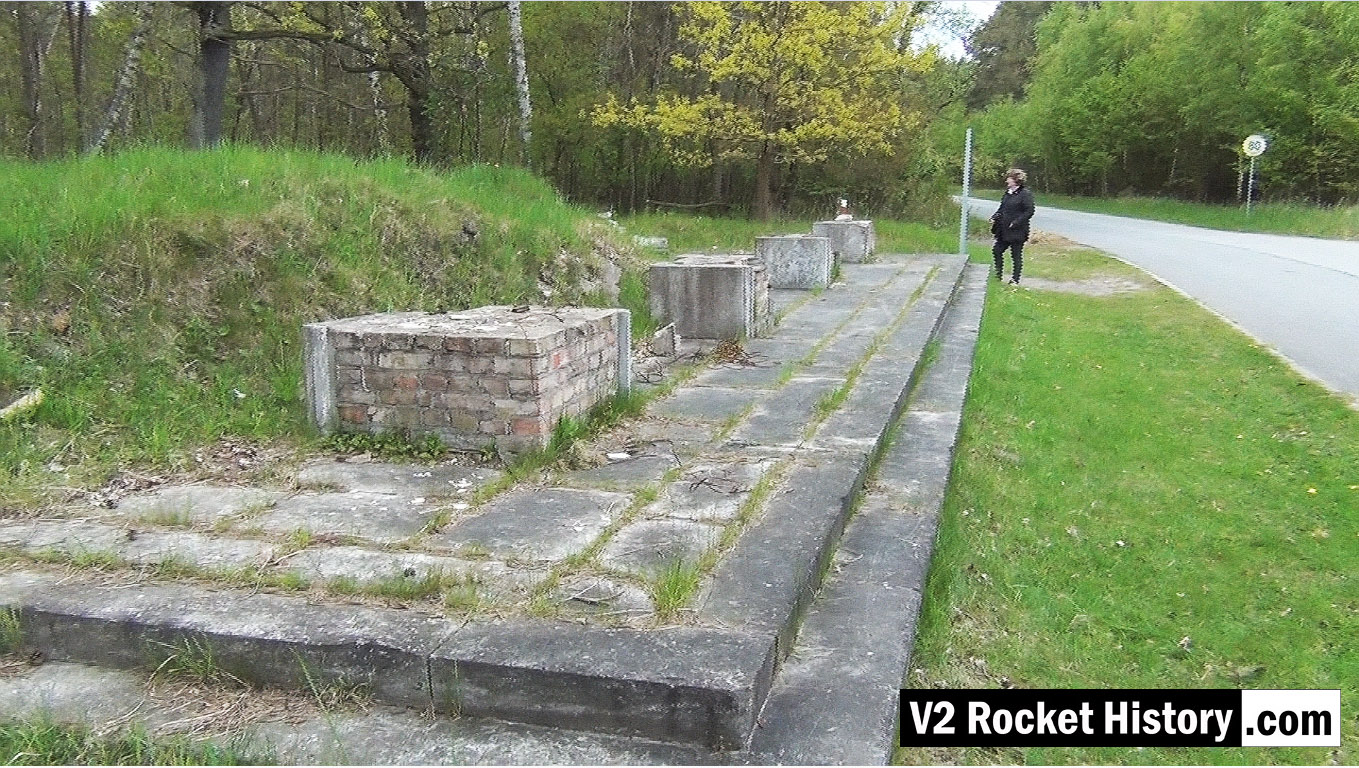
This picture shows the remains of the main South entrance to the Development Works. (also known as Station 7 – Die Hauptwache).
Album | Development works |
Category | Peenemünde-Usedom-locations |
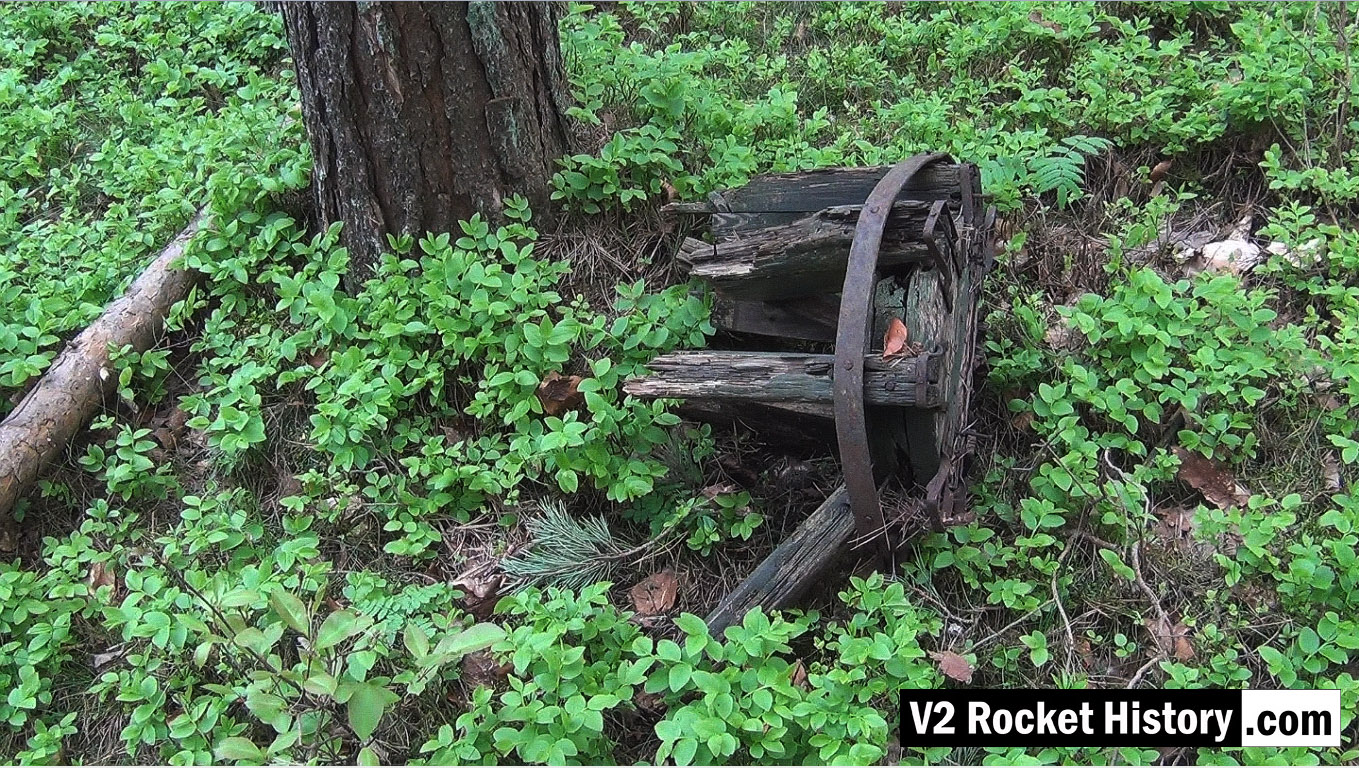
Wooden carboy frame from WW2 (possibly used for transporting small quantities of corrosive and dangerous liquids employed in the V2 steam plant, (such as T-Stoff) laying among trees 190m East of F1 in a location used as an emergency rail freight loading area to F1 due to damage caused by US air raids in August 1944.
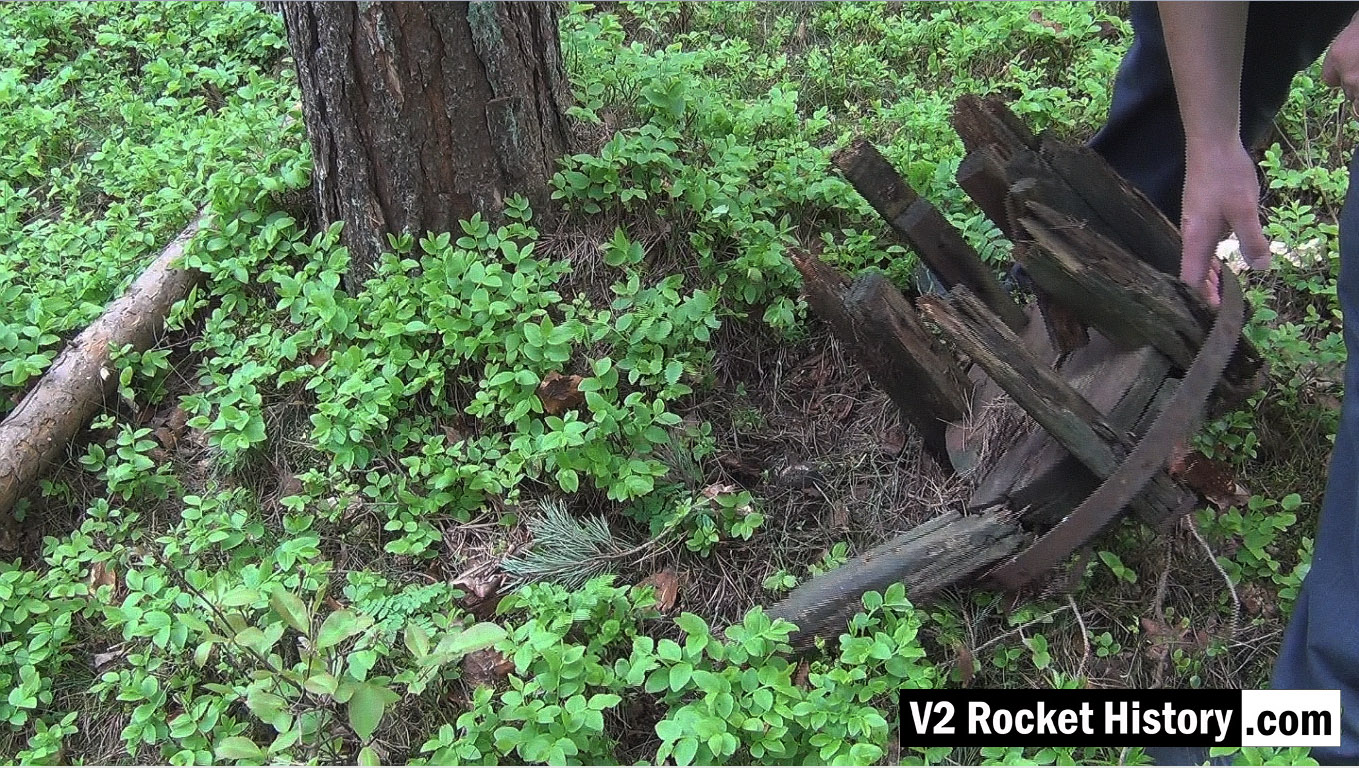
Wooden carboy frame from WW2 (possibly used for transporting small quantities of corrosive and dangerous liquids employed in the V2 steam plant (such a T-Stoff) laying among trees 190m East of F1 in a location used as an emergency rail freight loading area for F1 due to damage caused to rail track by US air raids in August 1944.
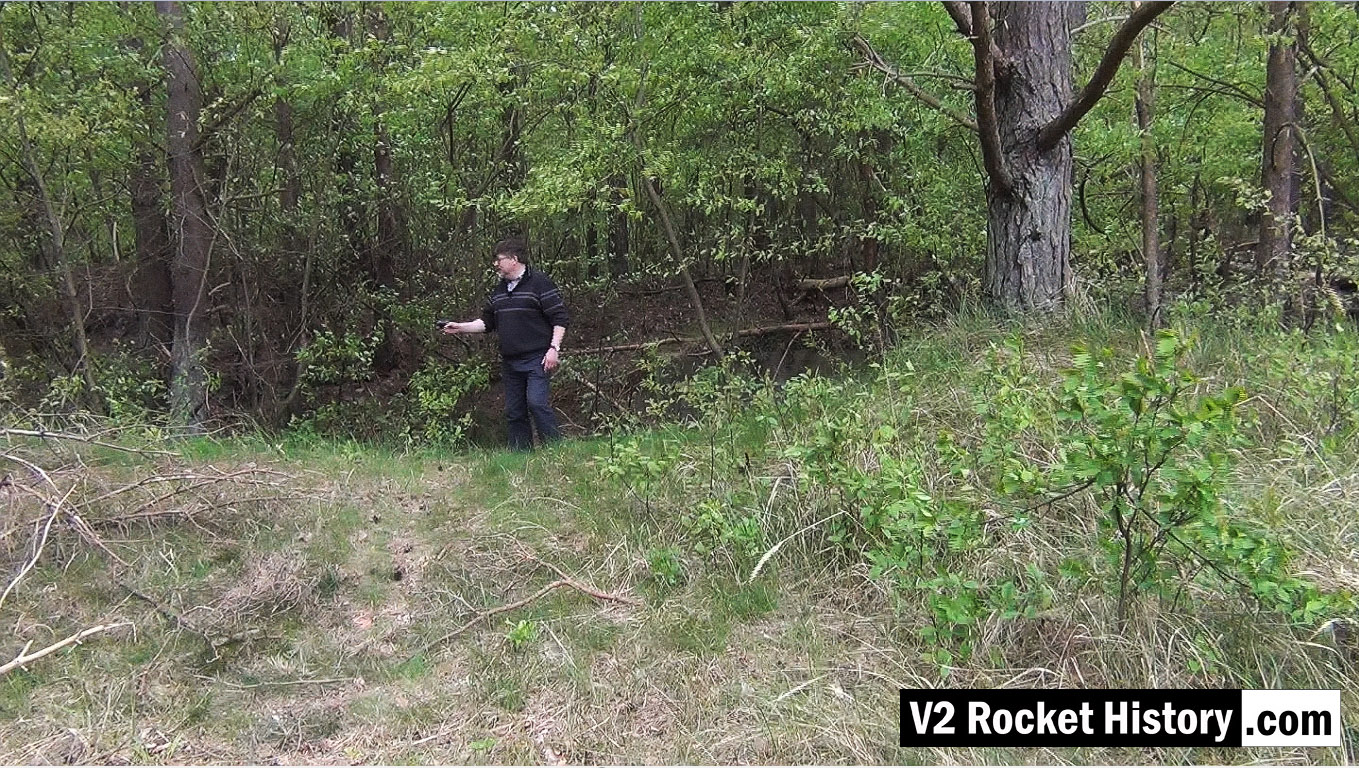
This picture shows Robert Dalby collecting GPS data with a mapping camera just North of the East end of the Admin office rail platform (near the ruins of the small admin/F1 heat distribution hub building). In all of our explorations we routinely collect GPS track and data points to be able to accurately locate finds and establish a precise correlation between areas of interest identified on historical reconnaissance photography and the modern ground terrain. In the picture Robert is pointing a Contour video camera at details of the terrain that automatically captures the camera’s GPS location information. This data can then be combined with satellite imagery, via Google maps, and provide a detailed graphic mapping track alongside the video footage.
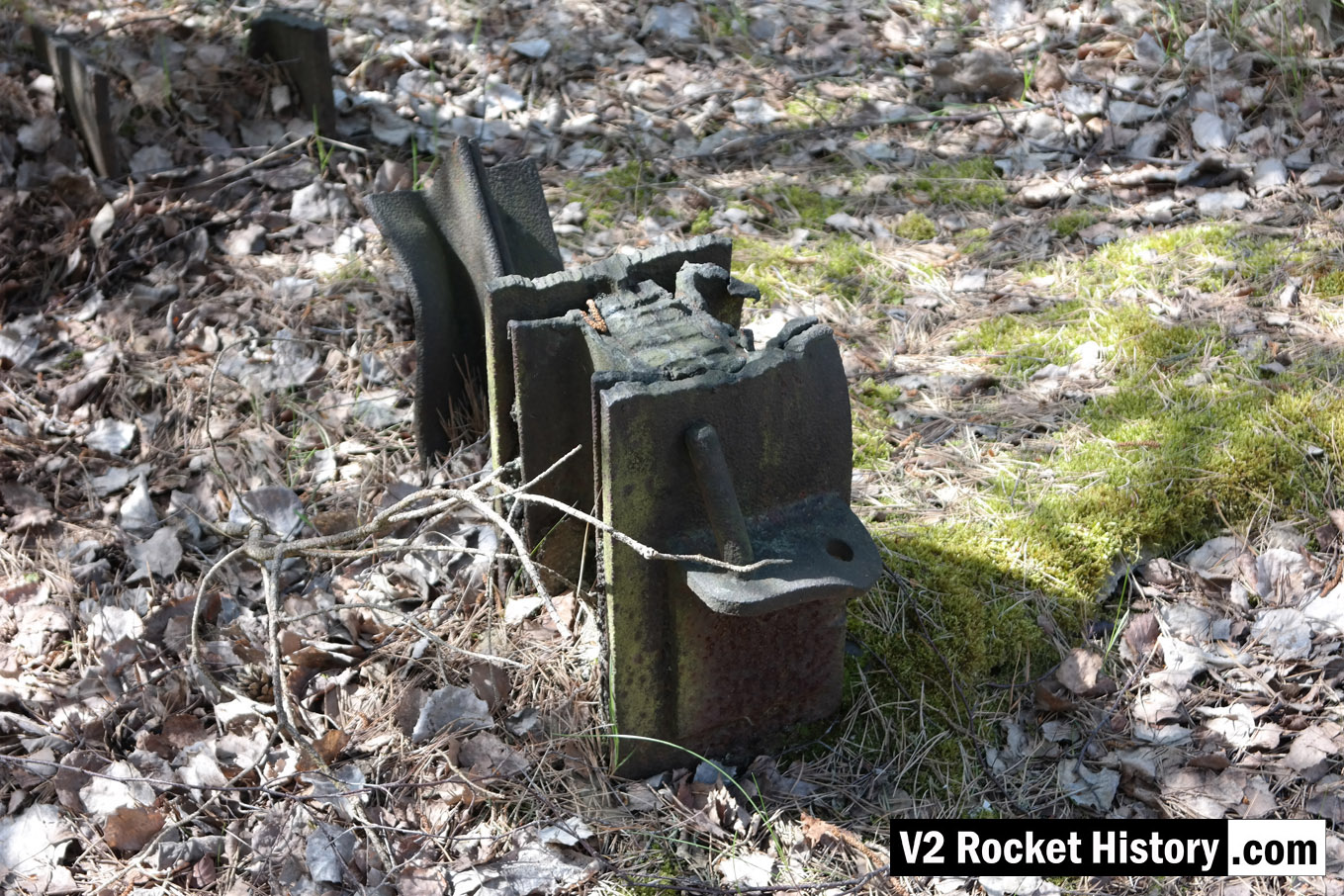
Photo shows the cut stump of an heavy upright support girder. The ragged profile of the cut shows that it has been cut down with an oxygen and gas torch or possibly a larger fuel and oxygen device like a thermal lance. The steel support still has the bottom support pin for a large door. Note that although the girders have been gas-cut there is a great deal of mechanical damage to the steel work that was not caused by the cutting work. Considerable force would be required to bend the middle girder in the way shown, even if it was much longer at the time the bend was created. The upper superstructure of the storage shed may have been part demolished using a bulldozer. Or perhaps the East German Army may have used the site for explosives training – signs of demolition explosive use are in evidence nearby. The map under the album presentation of this picture shows the exact location of the girders.

Valves
Images of the main valves involved in the propellant flow of the A4 / V2 liquid fuelled rocket engine
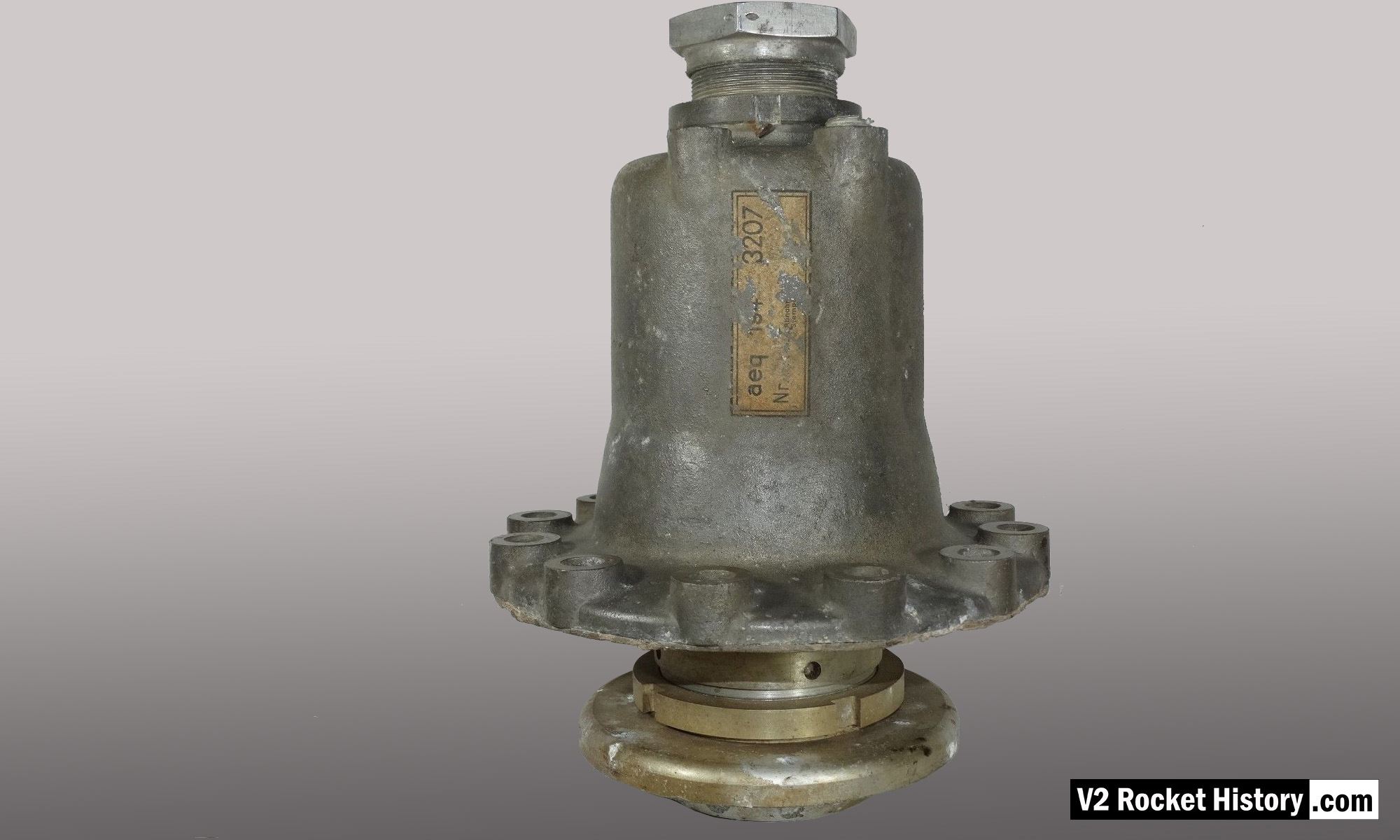
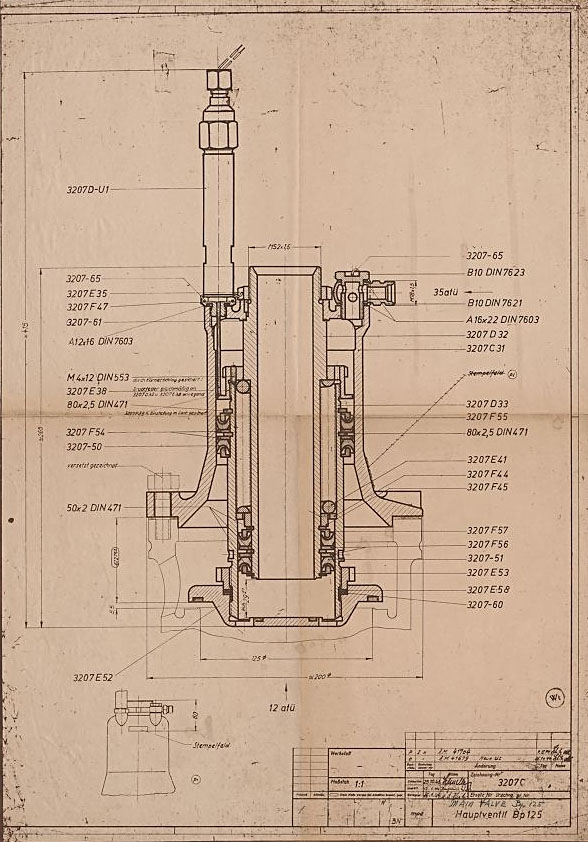
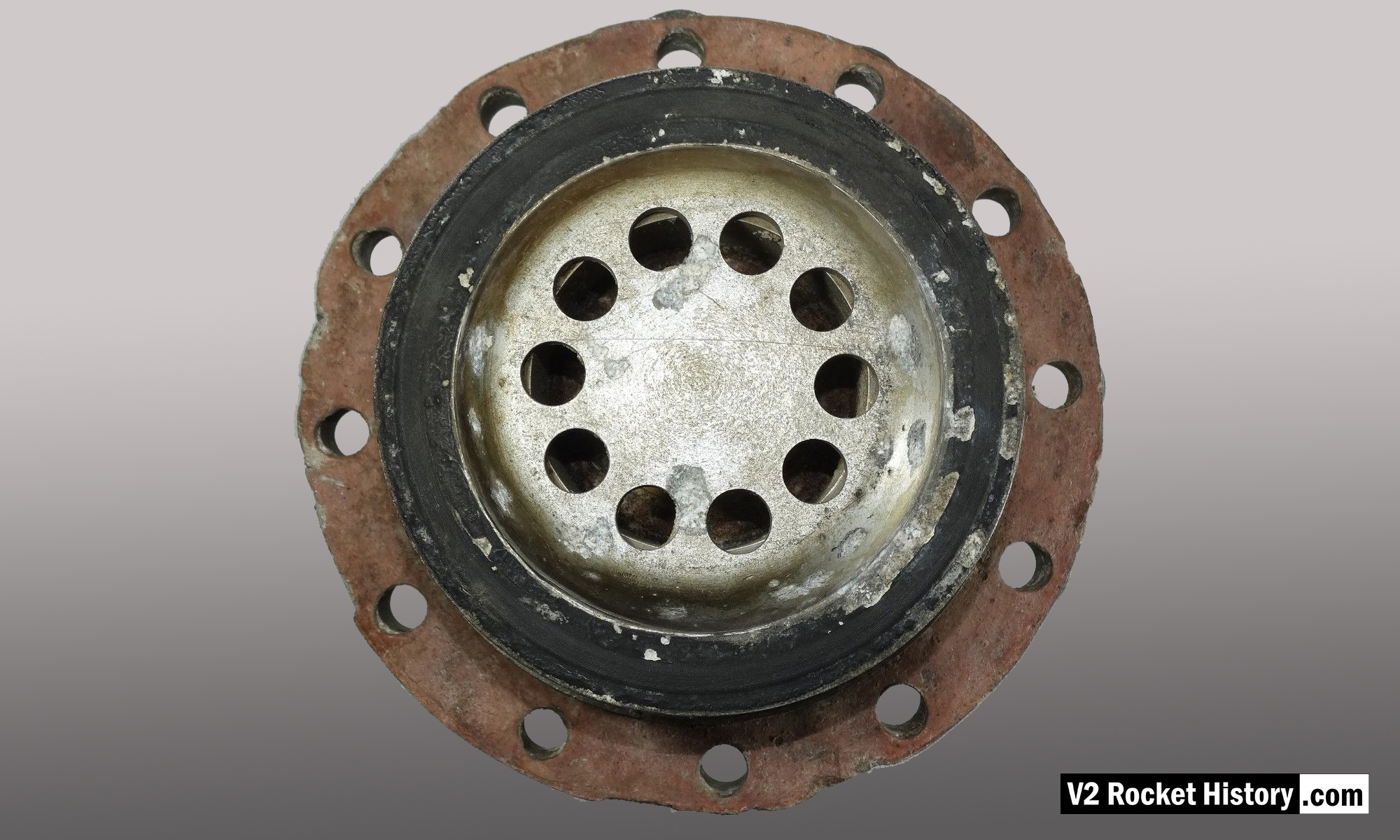
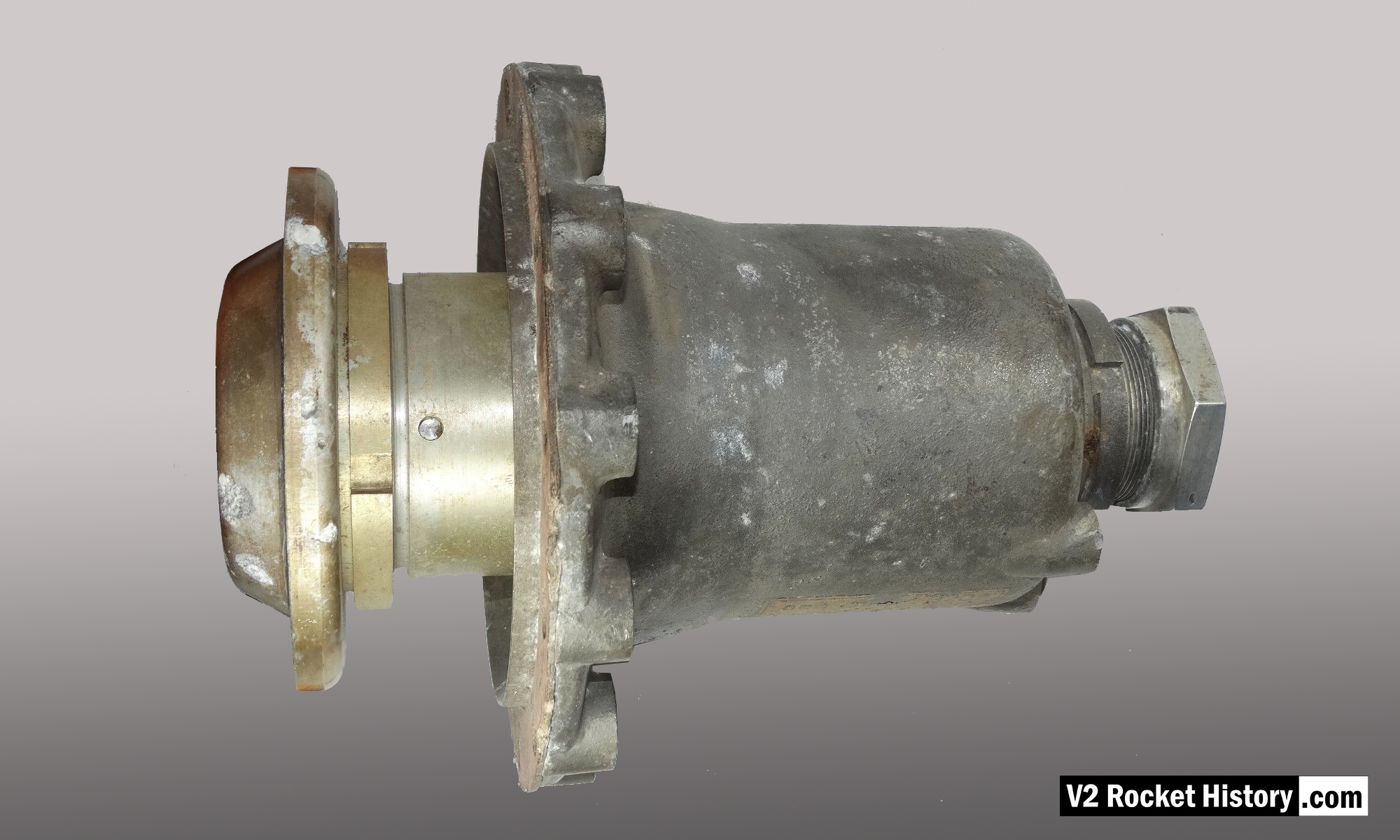
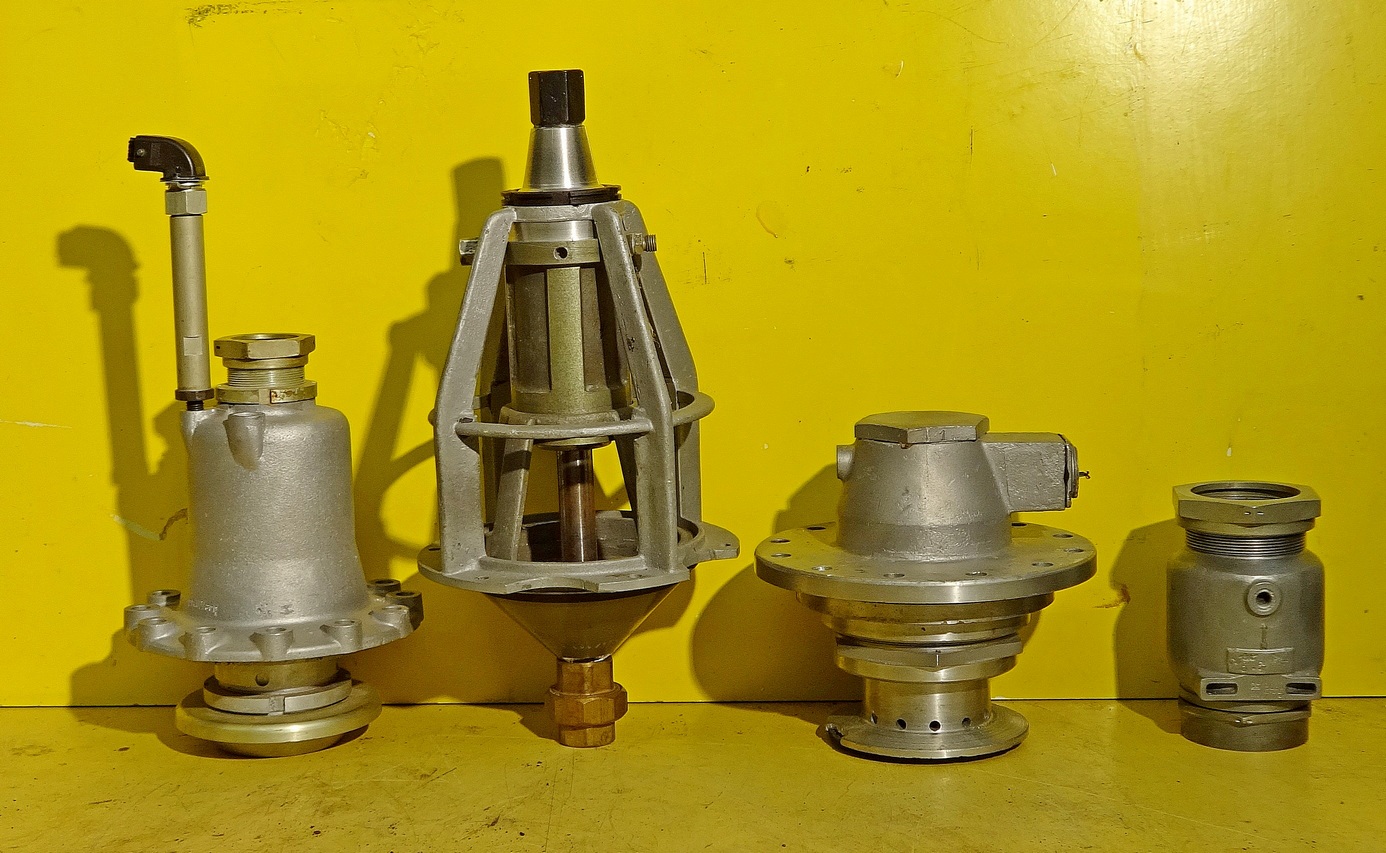
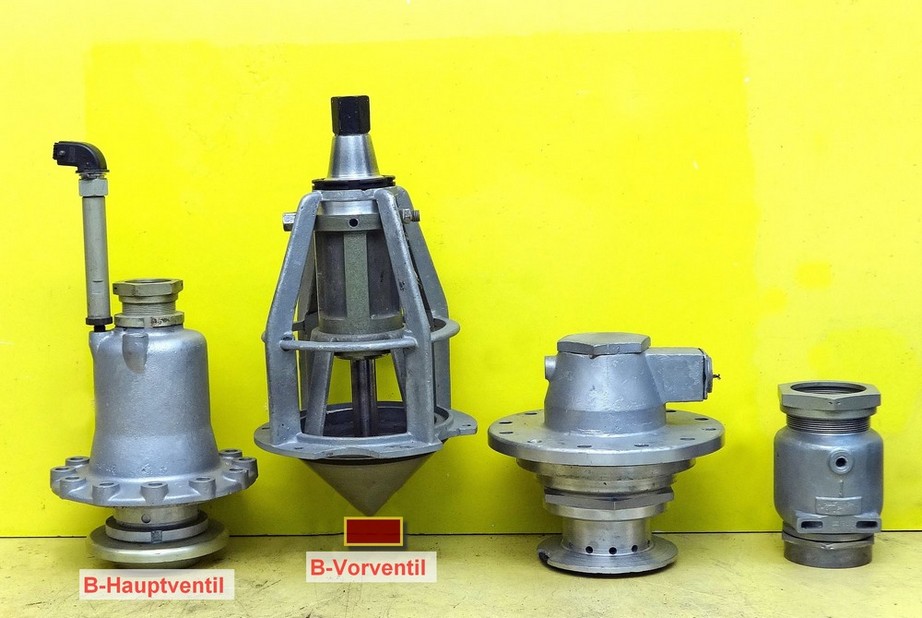
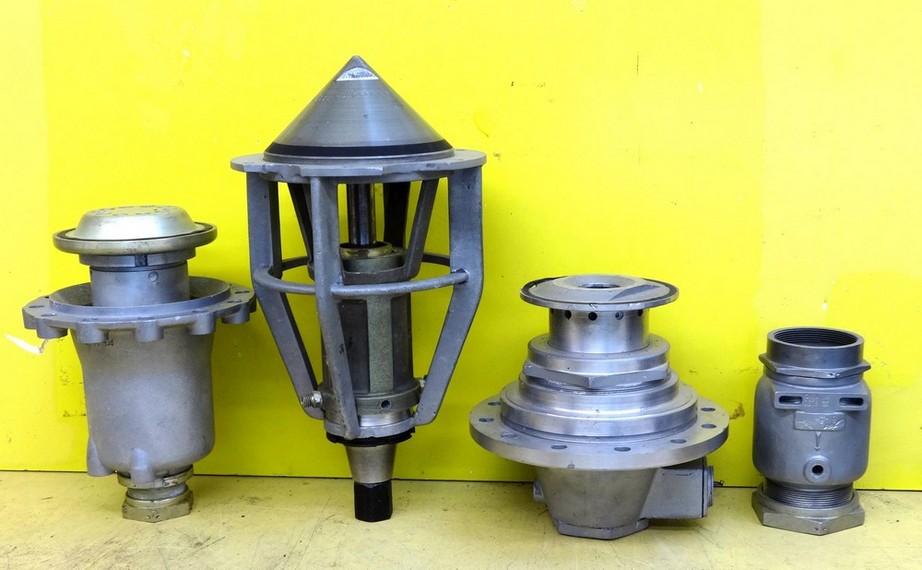
Images of the main valves involved in the propellant flow of the A4 / V2 liquid fuelled rocket engine
Relic of main alcohol valve with manufacturer code aeq (aeq = Bartoc & Co., Maschinenfabrik u. Giesserei Hedwikow,bei Caslau (Caslav) Czech Republic). An air (nitrogen) inlet pressure of 440 to 530 psi (30 to 36 Bar) was required to close this valve against its internal spring and the force of the turbo-pump. The large nut at the top is the connection for the fuel return (or ‘revolving’line) pipe, and the air and electrical input ports can be seen to the right (air), and left (elec.) just below this point. V2RH image

Anatomy of the V2: 18-pot injector head
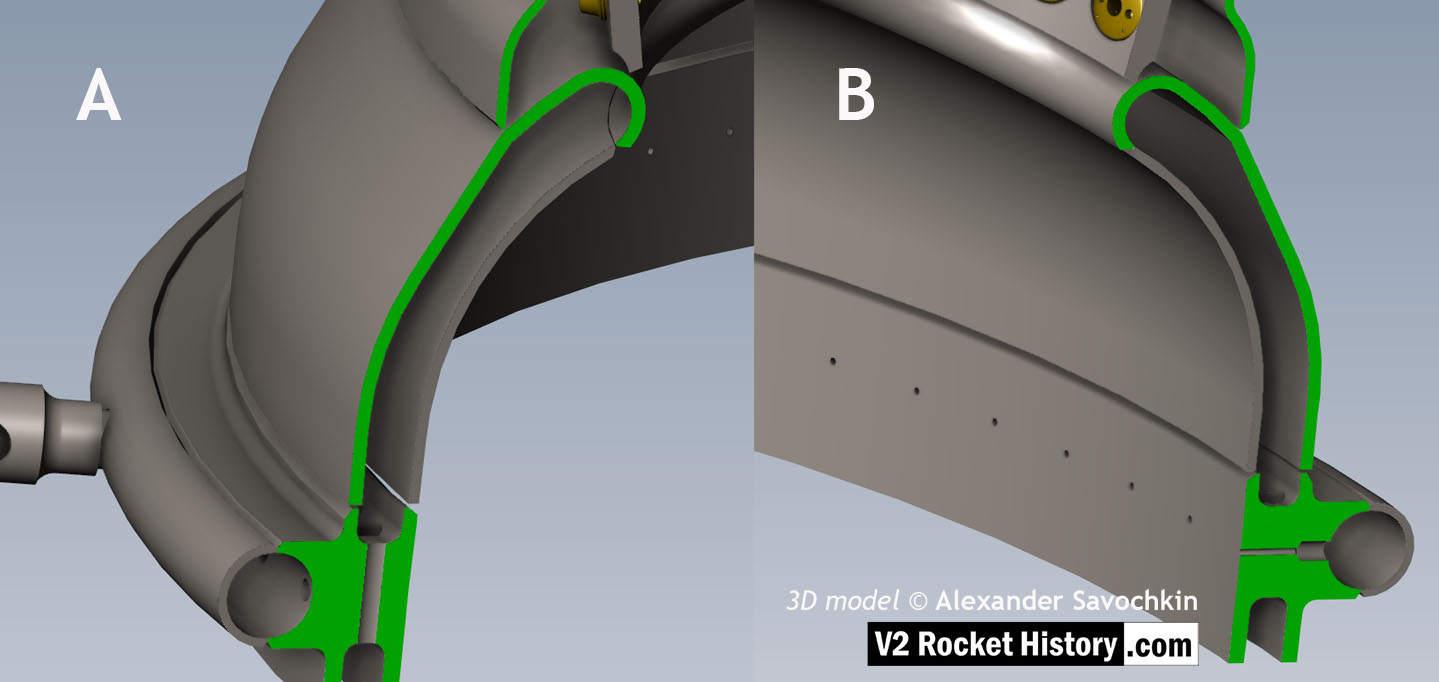
Close-up detail showing independent pathway for fuel passing into injector head and fuel passed down from the head to be used for veil cooling system. Fig. A shows vertical passages for overall fuel feed to the head and Fig.B shows horizontal pathway for veil coolant fed from the head via the veil coolant distributor ring or manifold. 3D model by Alexander Savochkin

View of injector head showing 18 liquid propellant (LOX and fuel) diffuser cups and head fuel valve seating ring at centre, (see other images for insert and position nomenclature). Visible immediately below the valve seat are the large connecting holes that allow fuel to flow from the inlet manifold and cooling jacket to the injector space (some brass injector inserts can be seen through the holes) after the head fuel valve is released to be opened by the turbo-pump supply pressure. The four veil cooling inlet connectors are well shown as are two of the outlet connection holes immediately above them. 3D model by Alexander Savochkin

A close-up view of the head fuel valve mounting flange (showing 12 fastener holes). Visible immediately below the top flange are the large connecting holes that allow fuel to flow from the inlet manifold and cooling jacket to the injector space (some brass injector inserts can be seen through the holes) after the head fuel valve is released to be opened by the turbo-pump supply pressure.
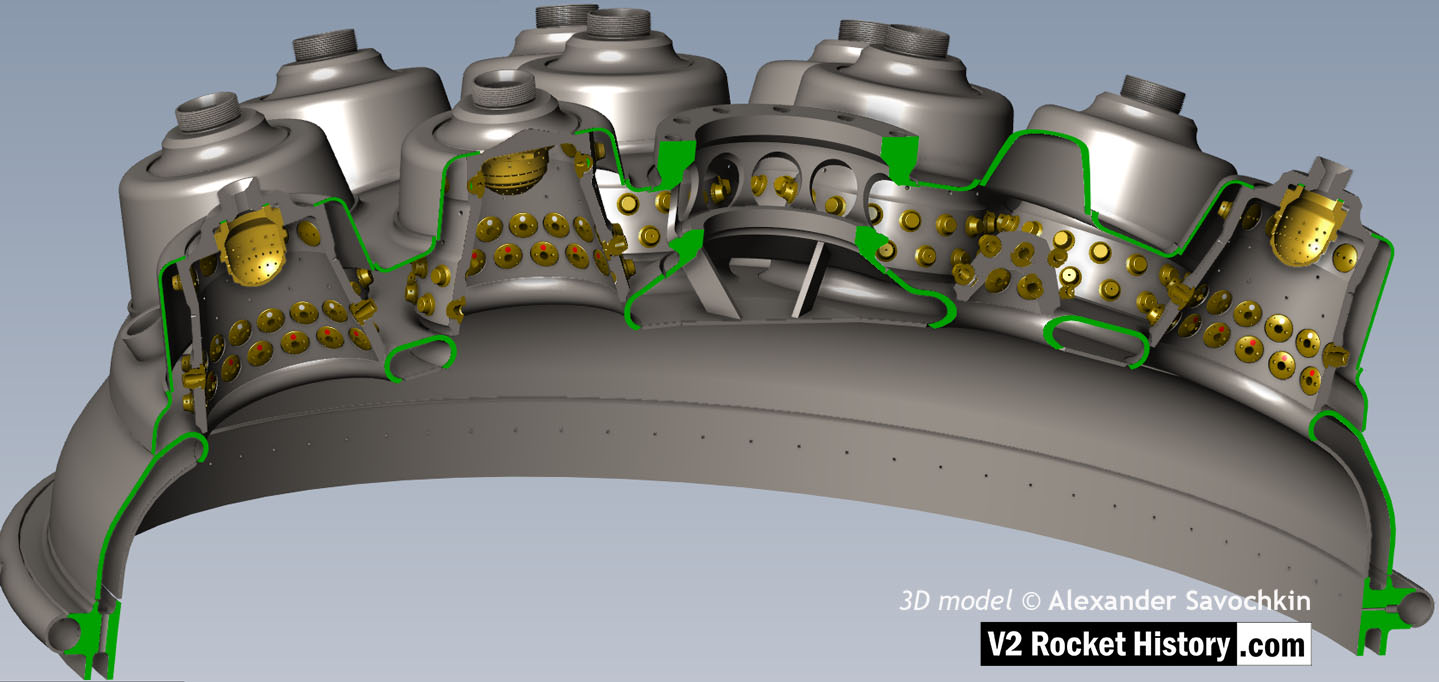
Here the 18-pot head model has been cutaway to show the fuel cooling and fuel delivery spaces. the cooling jacket layer can be seen in the lowermost area of the head – below the centrally positioned fuel valve seat, between each cup at the lowest point, and ruining down toward the first set of veil cooling pores and the topmost coolant distributor ring. Note that the veil cooling system does not communicate with the regenerative cooling jacket and has its own feed pipes drawing fuel from the head injector space and not the cooling space. Visible immediately above the valve seat are the large connecting holes that allow fuel to flow from the inlet manifold and cooling jacket to the injector space after the head fuel valve is released to be opened by the turbo-pump supply pressure. 3D model by Alexander Savochkin

Liquid propellent (LOX and fuel) diffuser cup, showing three rings or echelons (A,D,& E) of brass injector inserts as well as two rows of drilled fuel feed holes. The LOX spray head is shown in the centre. Note the simple ‘shower head or watering can’ design of the LOX diffuser. A sealing washer can be seen fitted between the LOX diffuser and the steel cup. 3D model by Alexander Savochkin

Testing fuel injectors
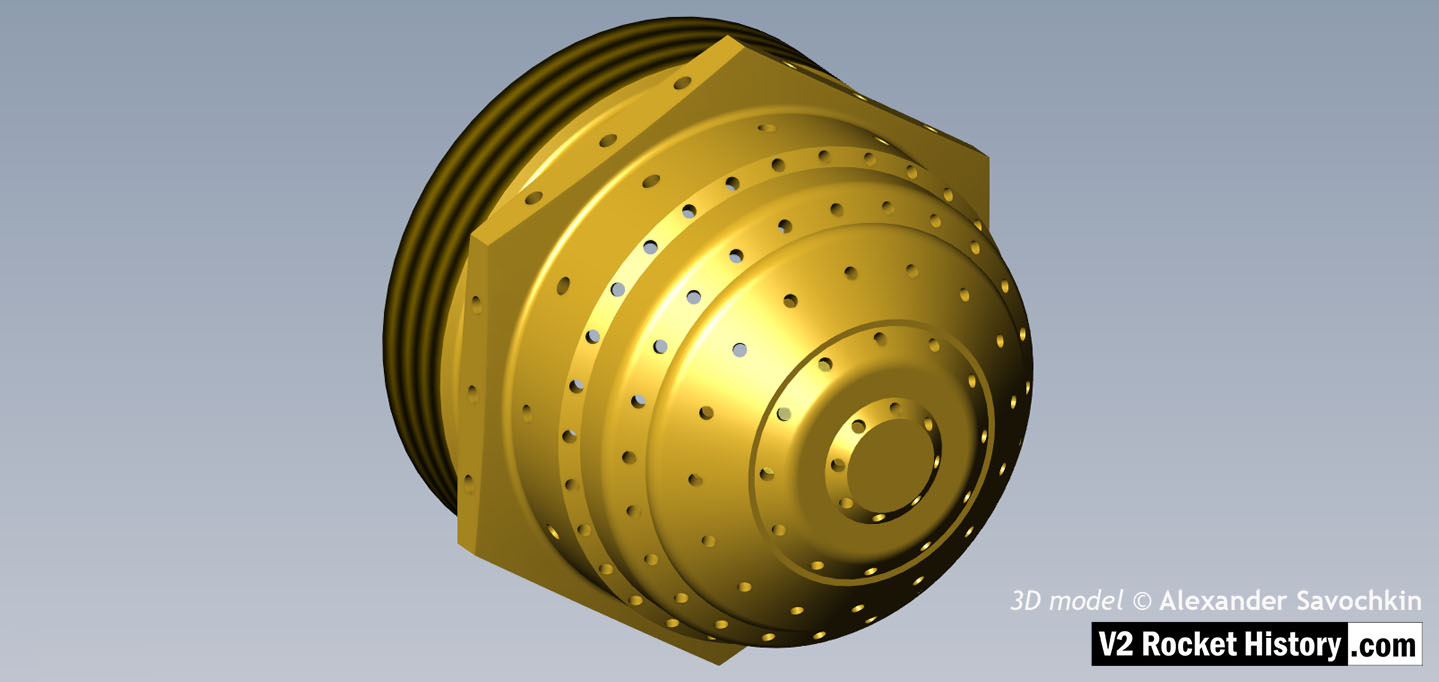
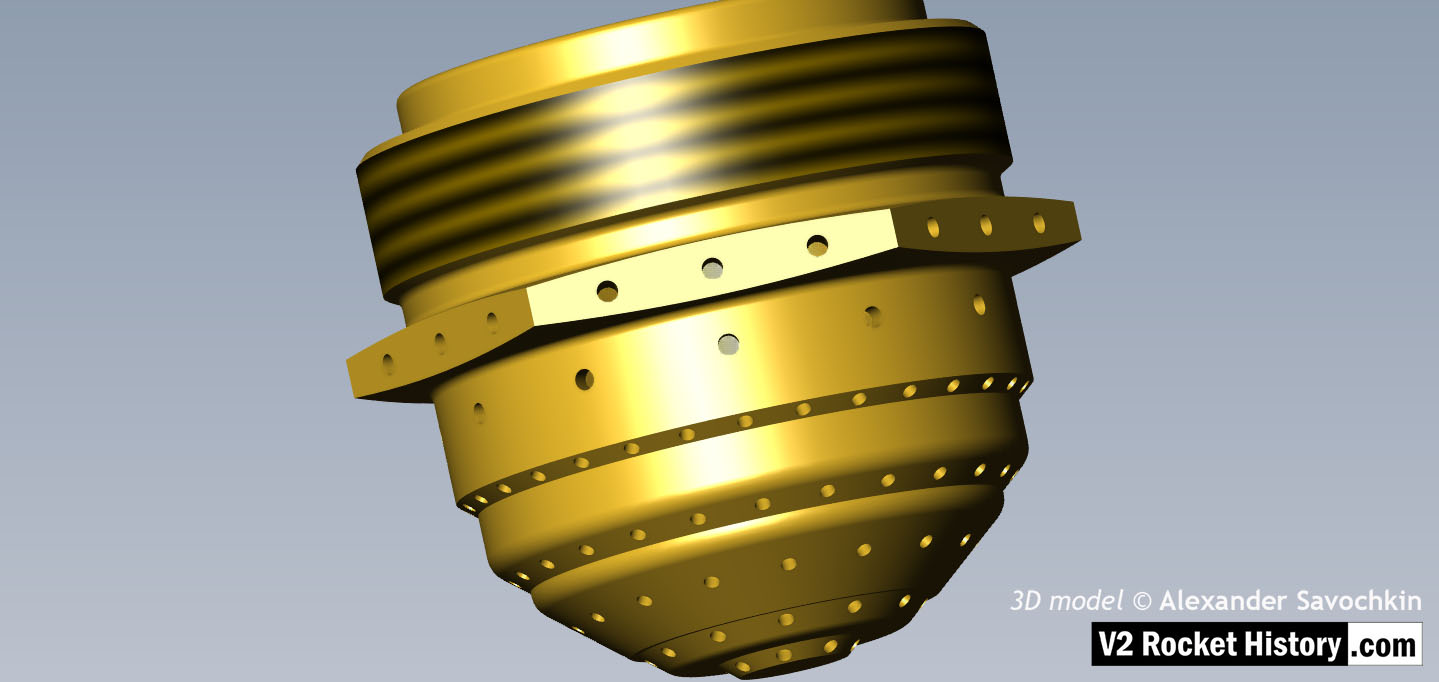

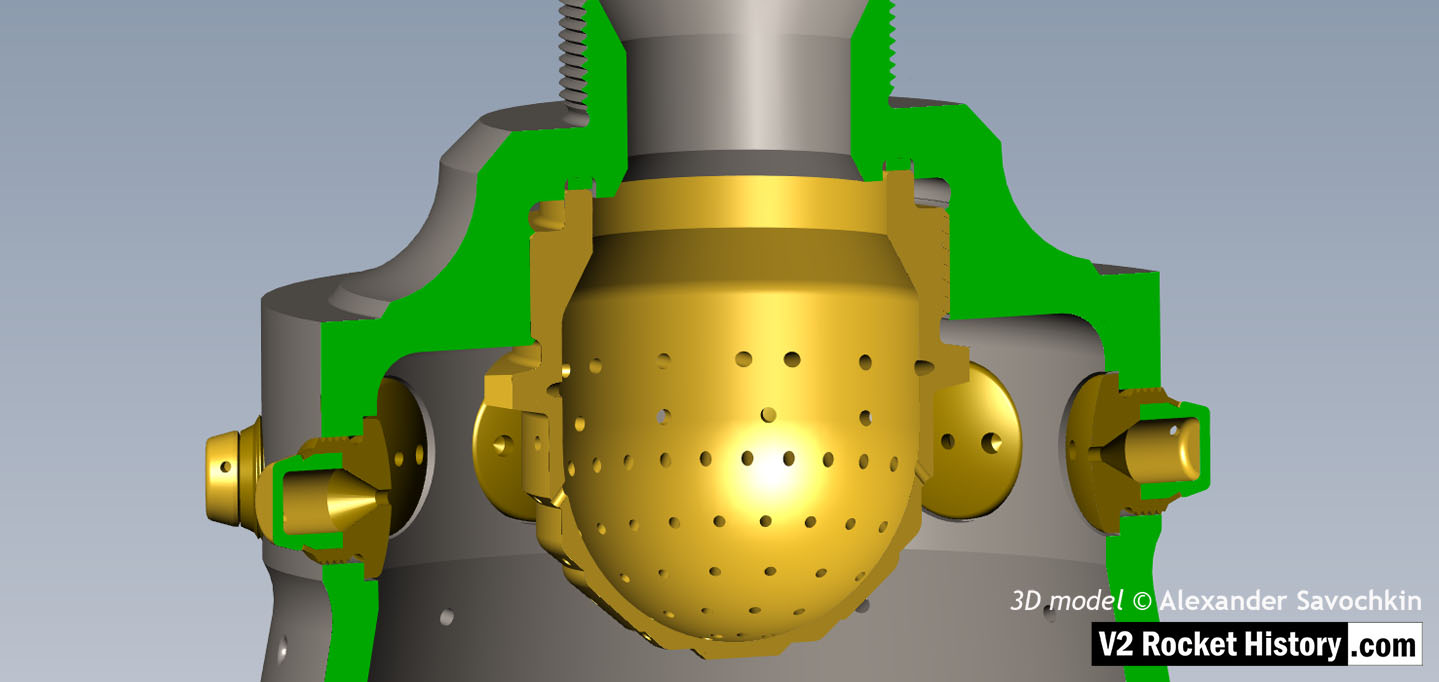
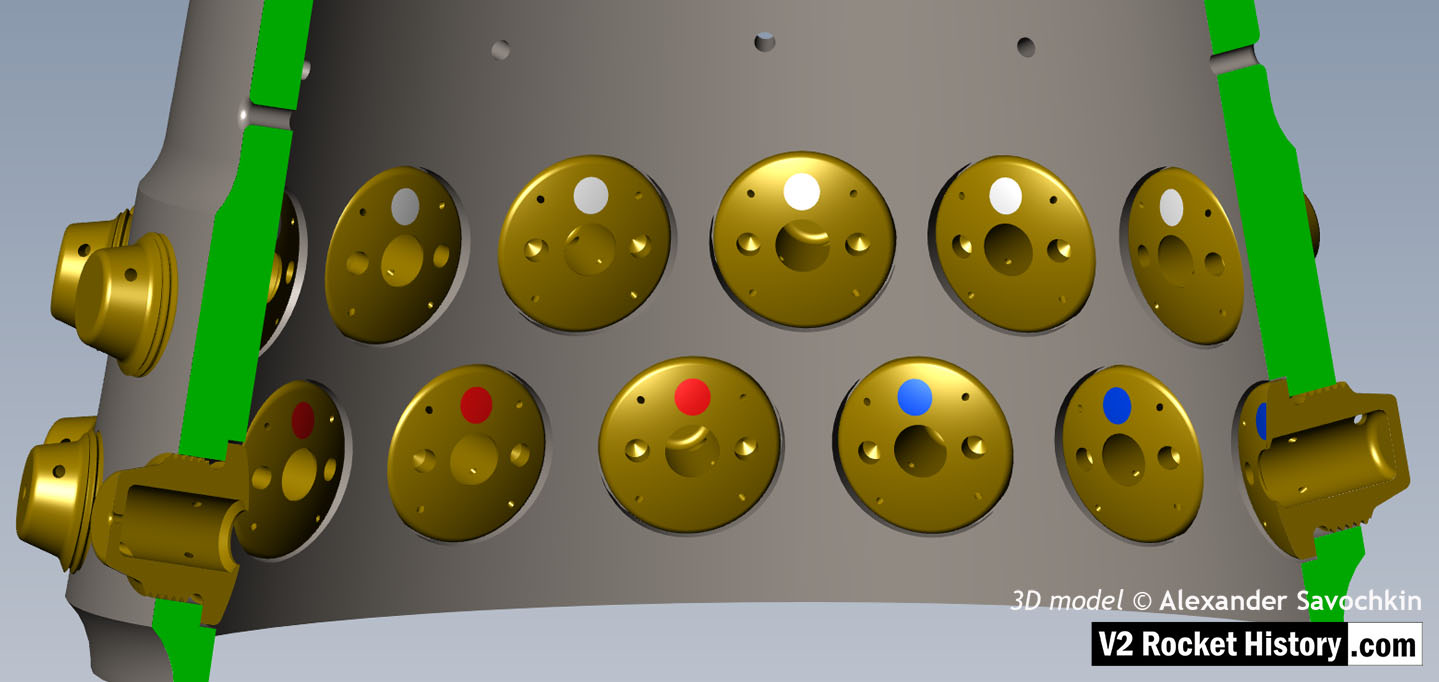

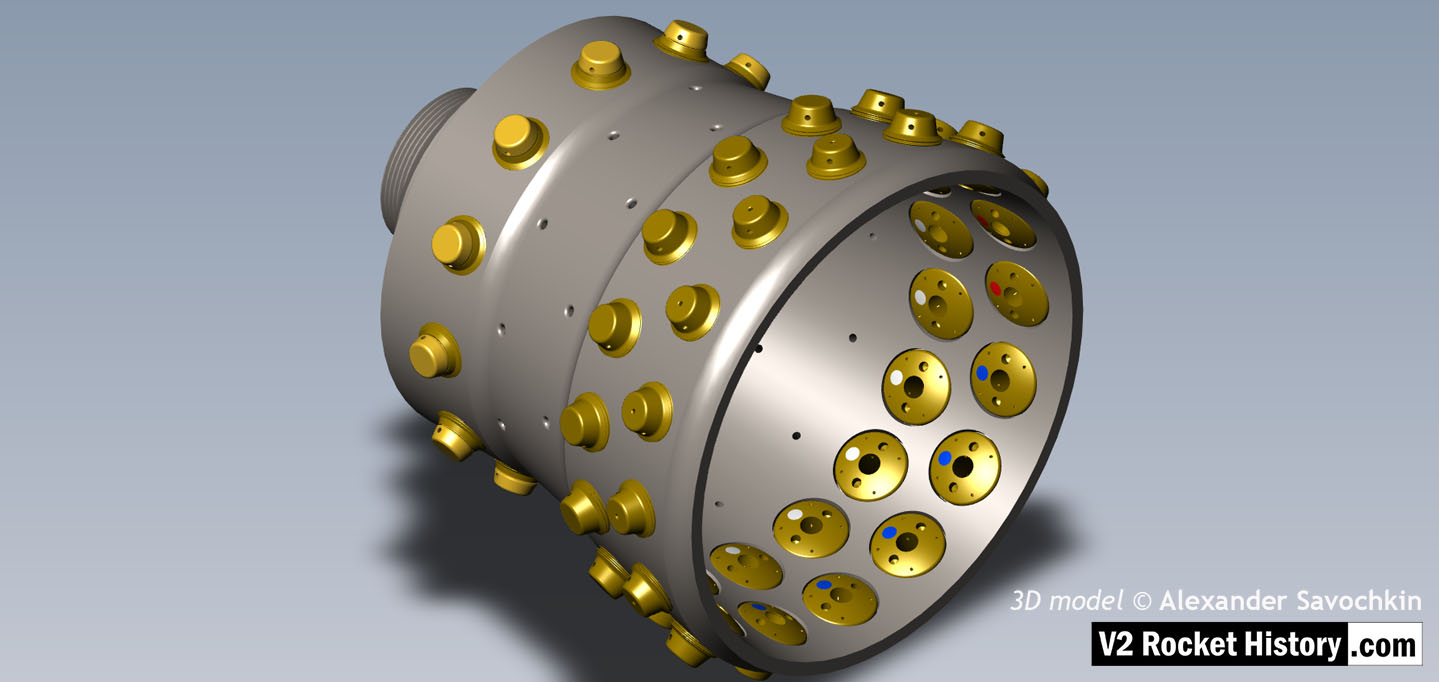
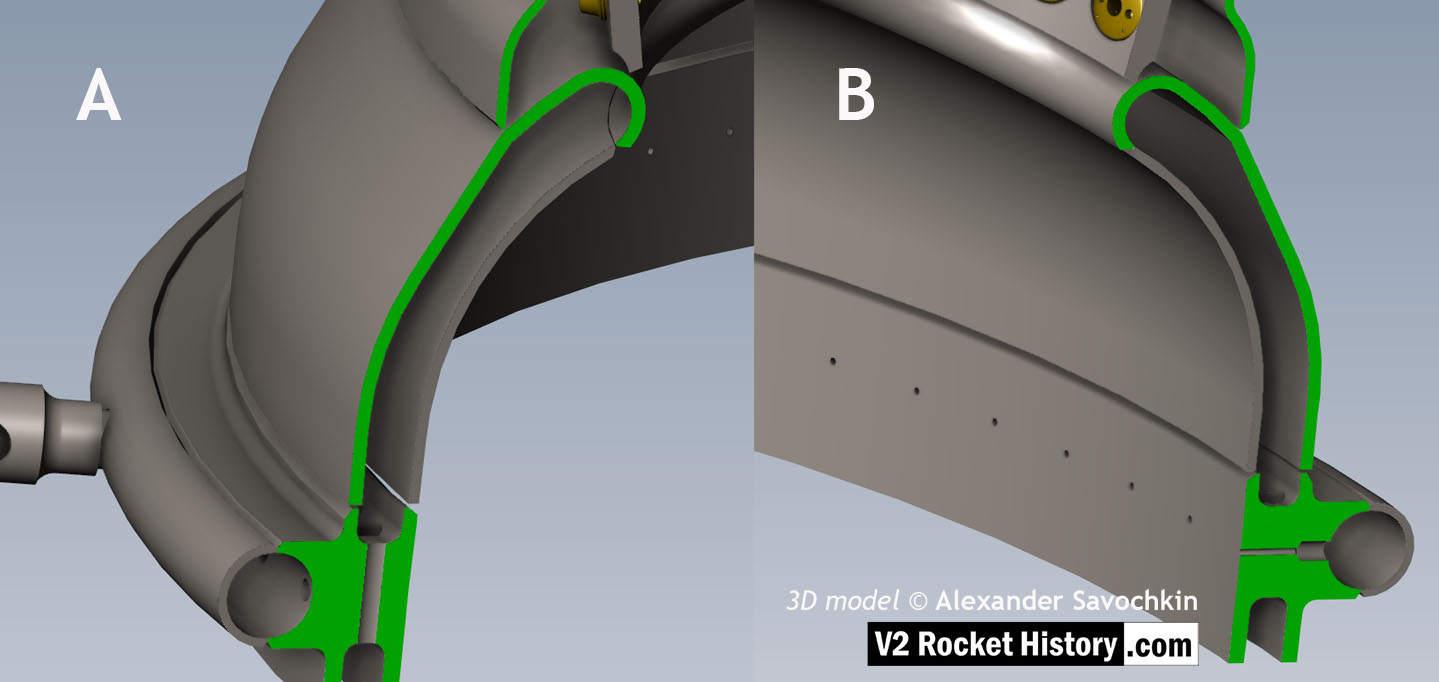




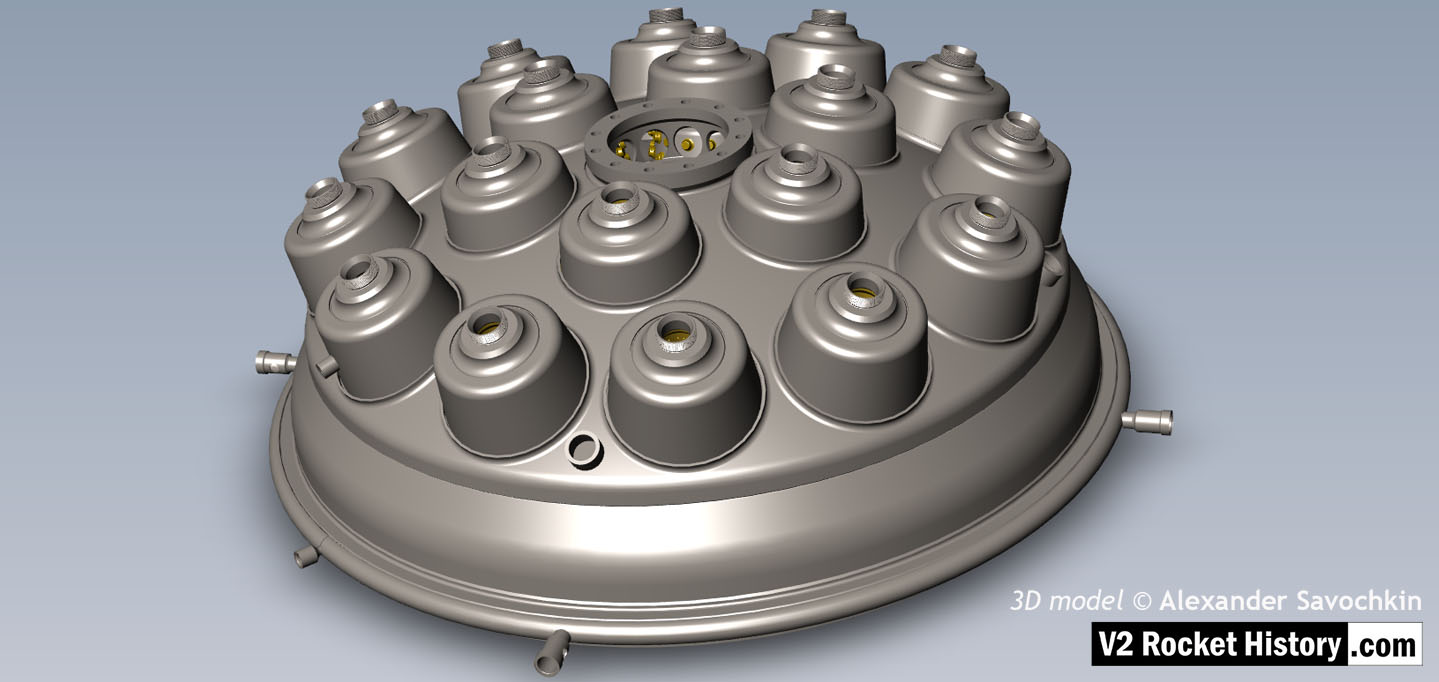

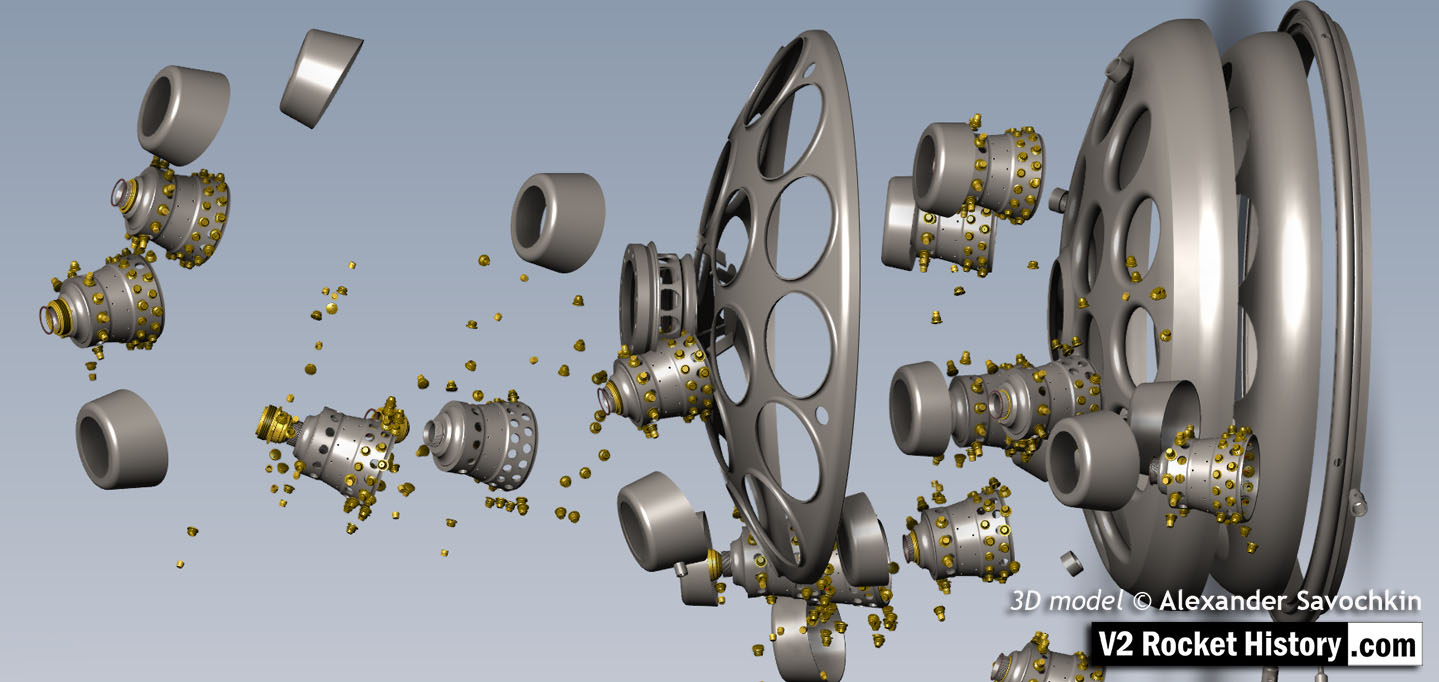
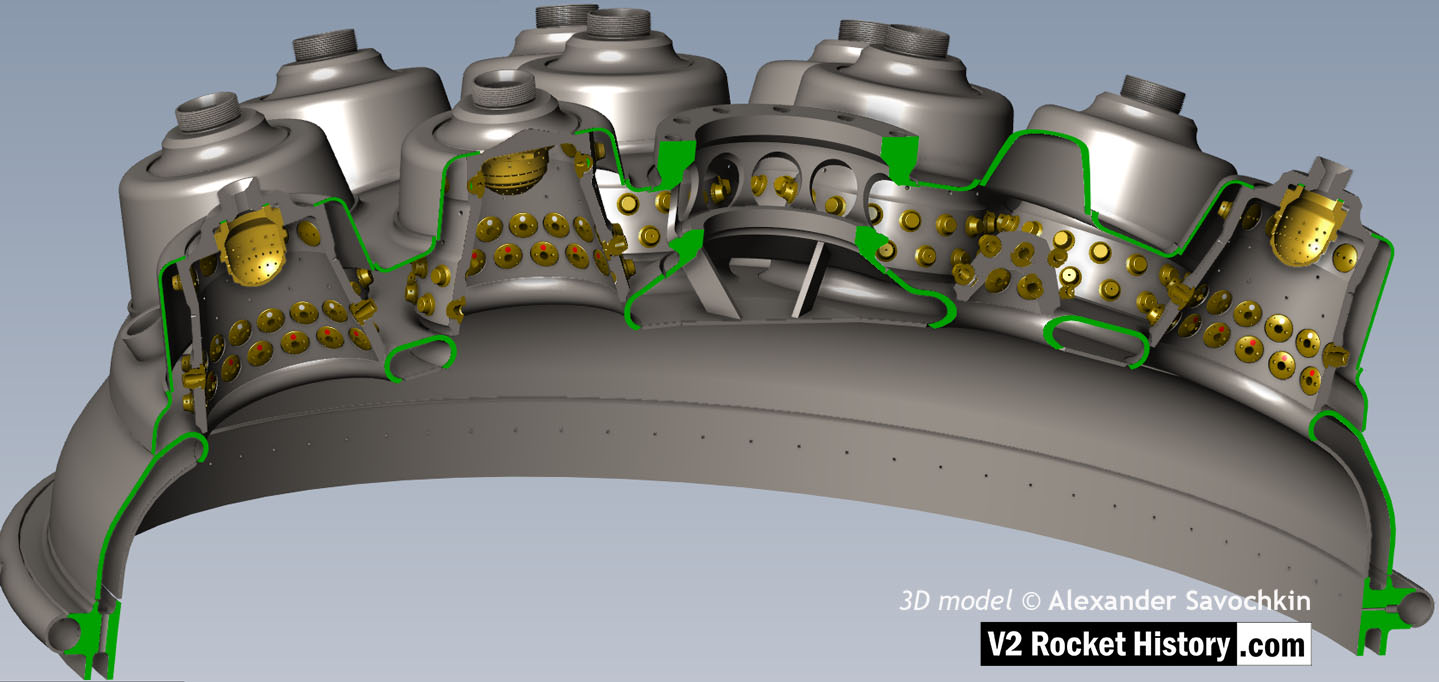


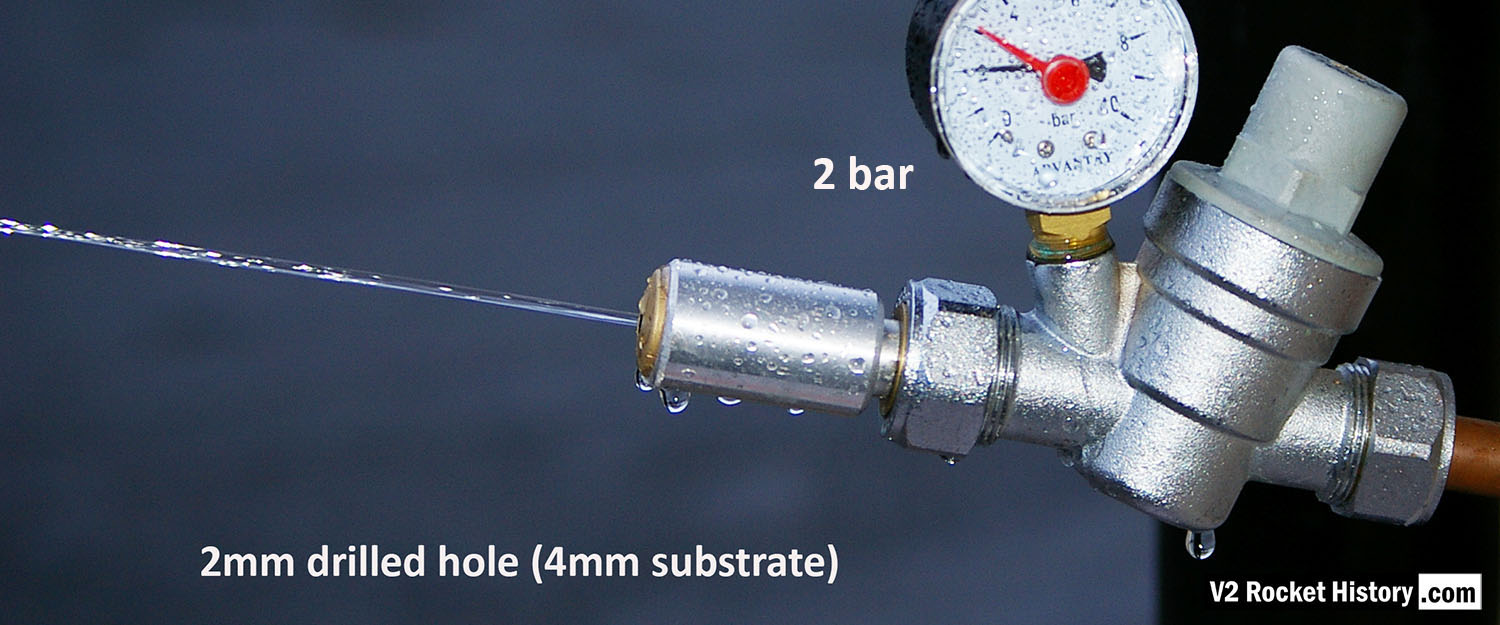

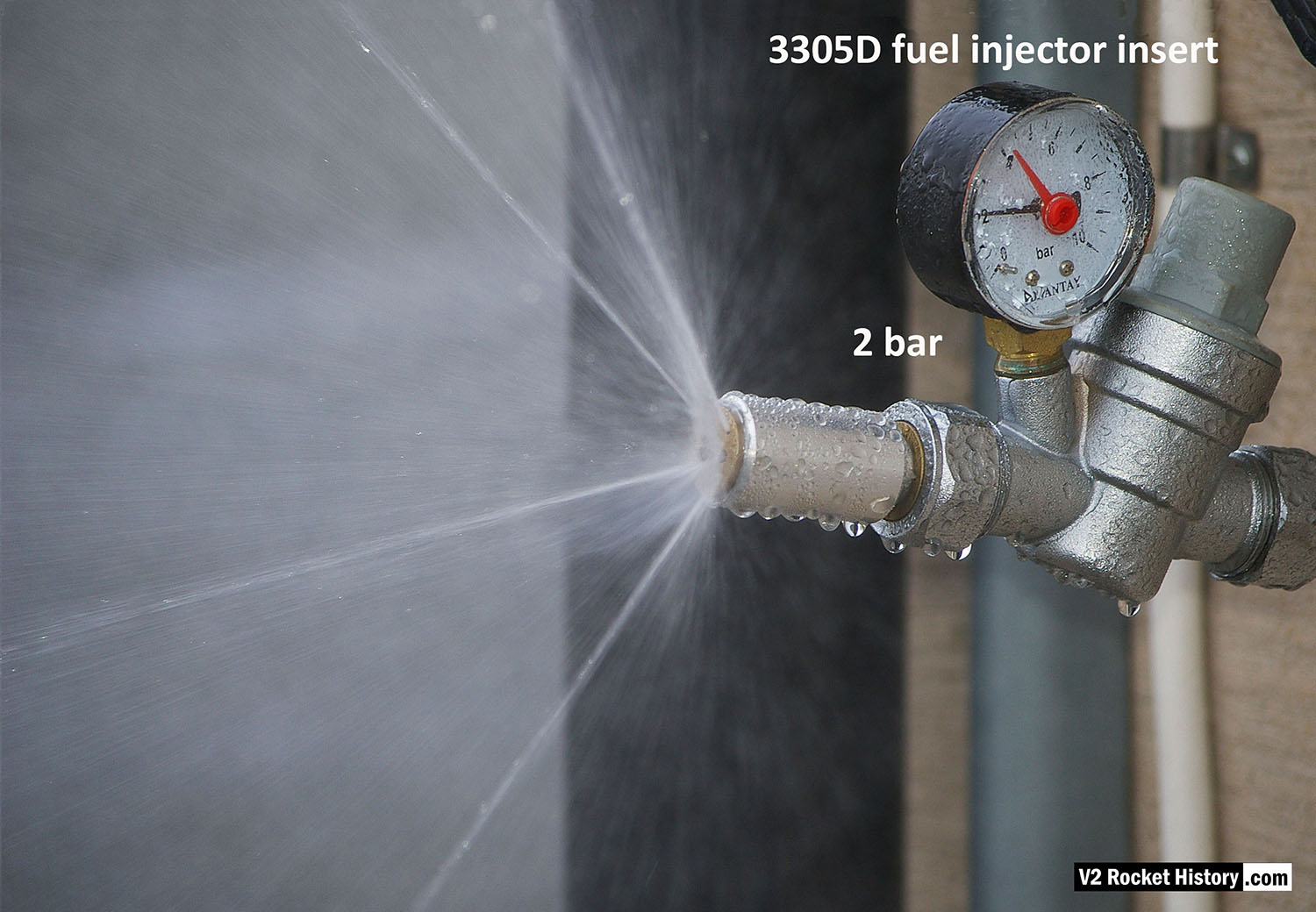
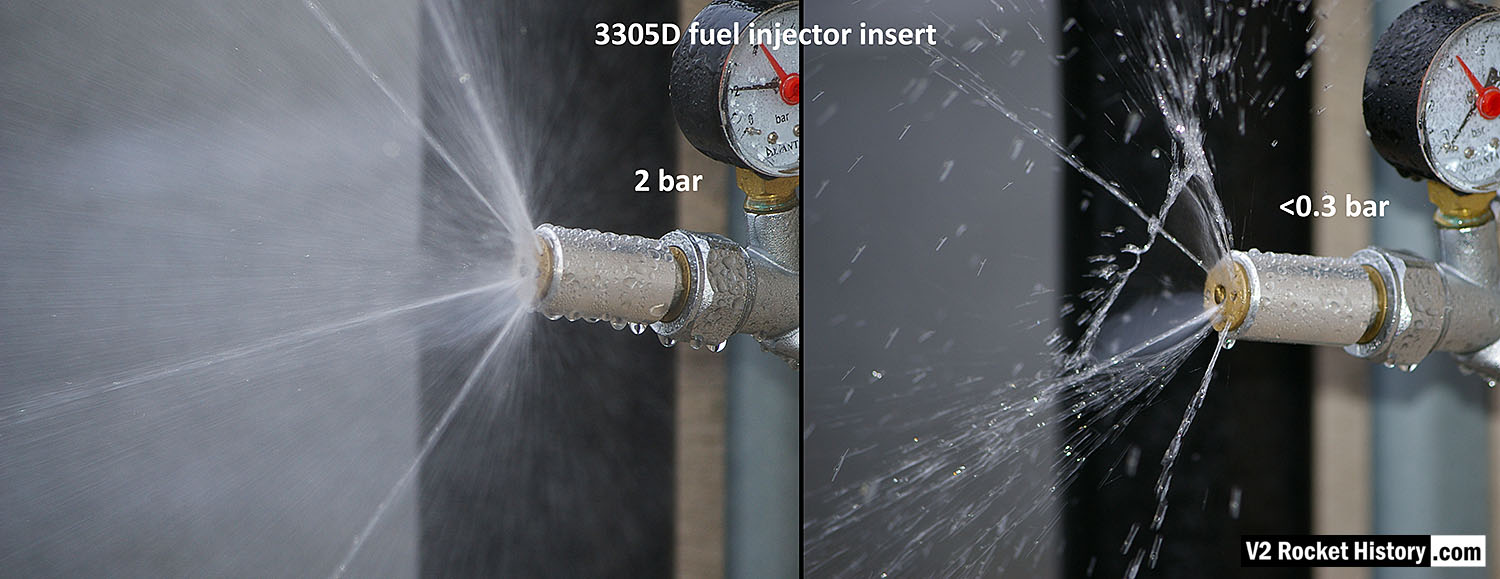
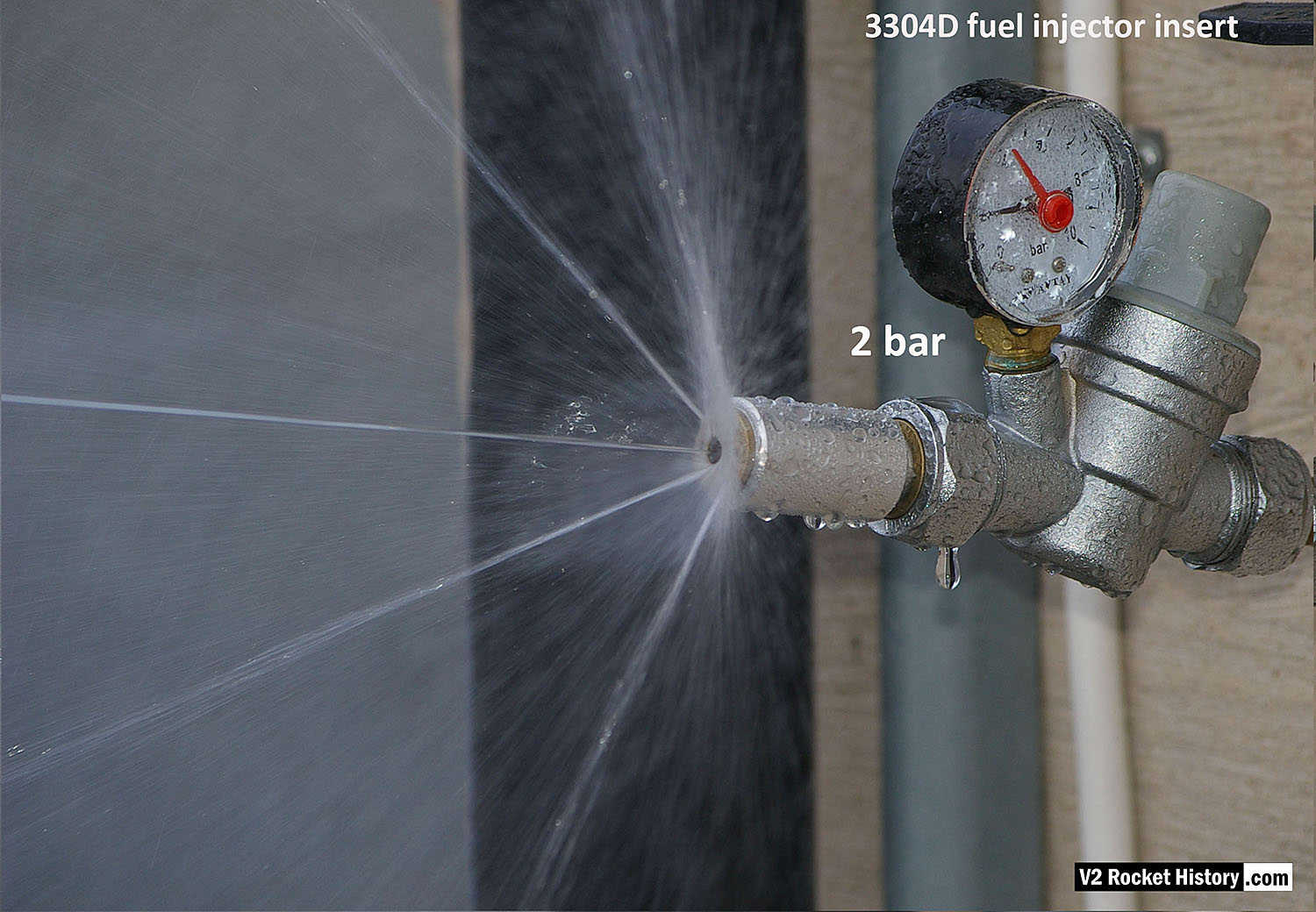
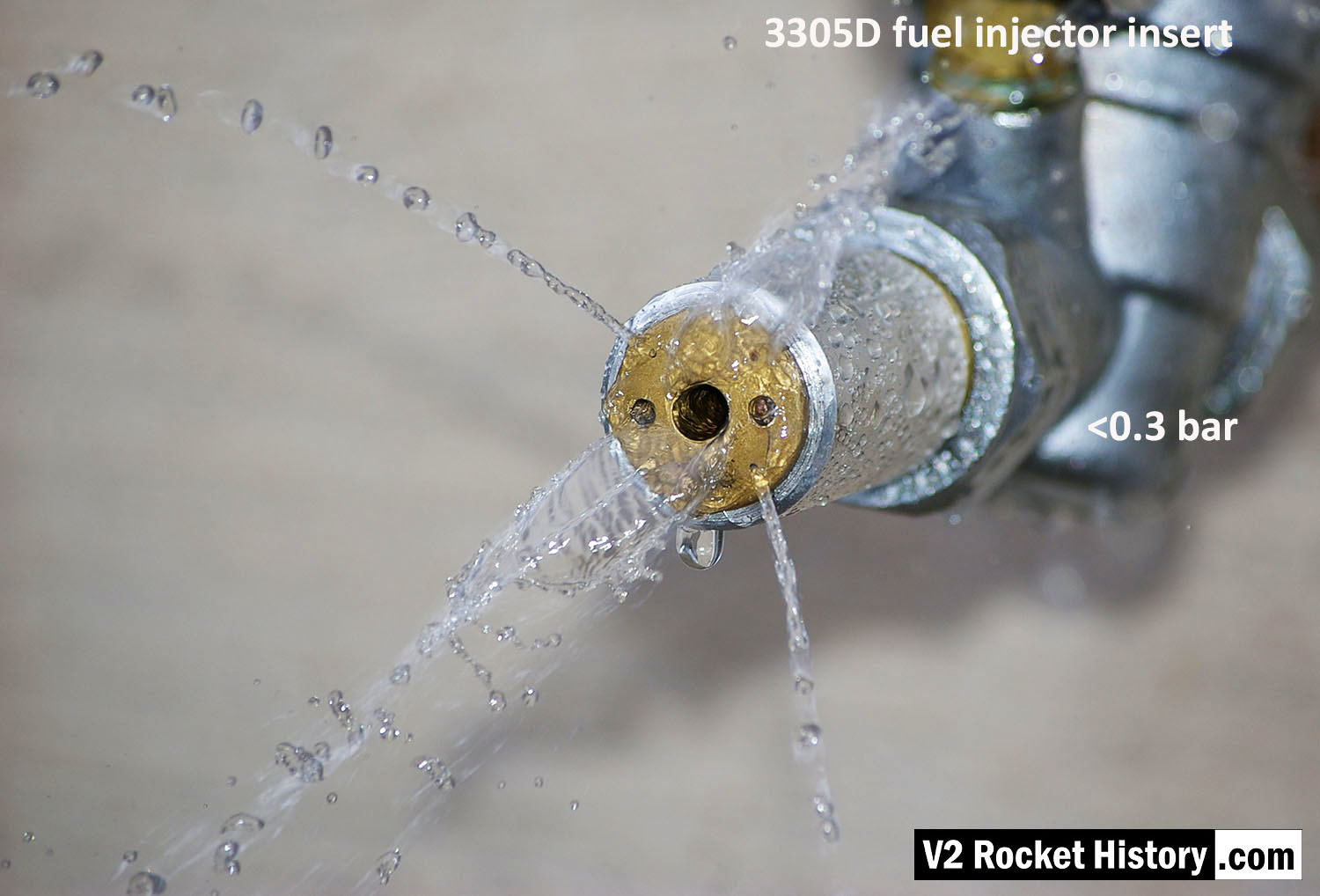
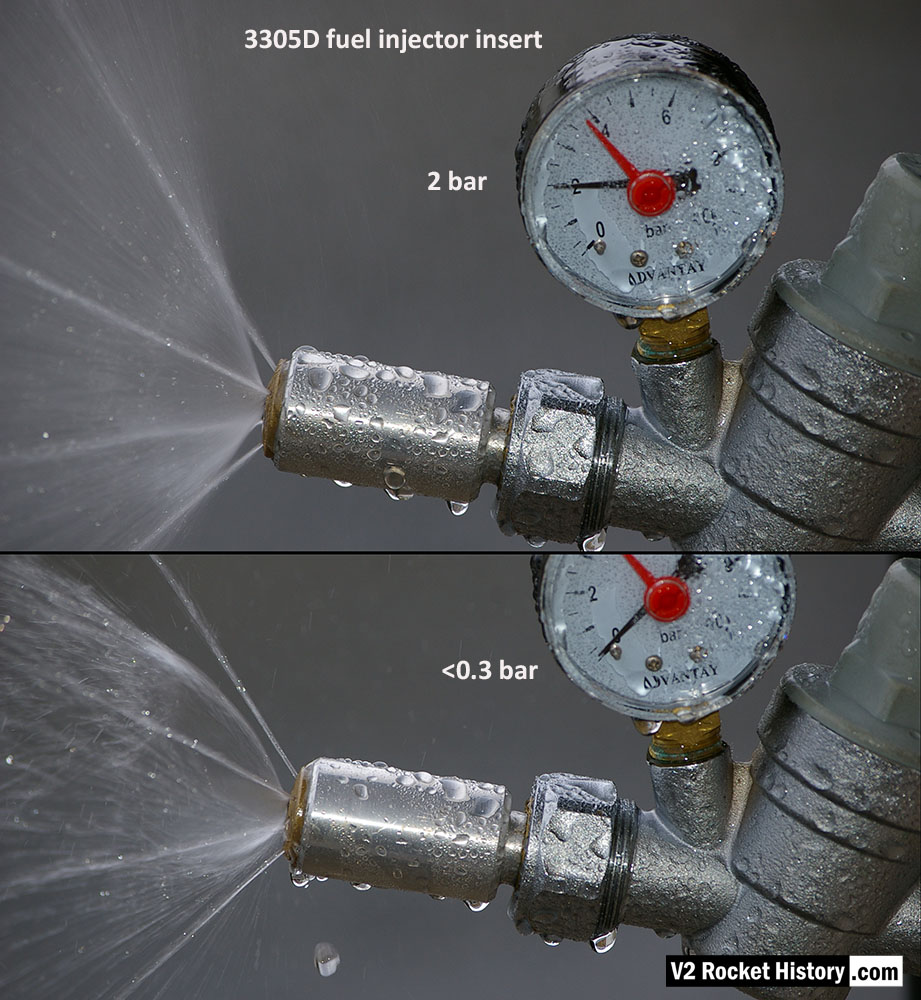
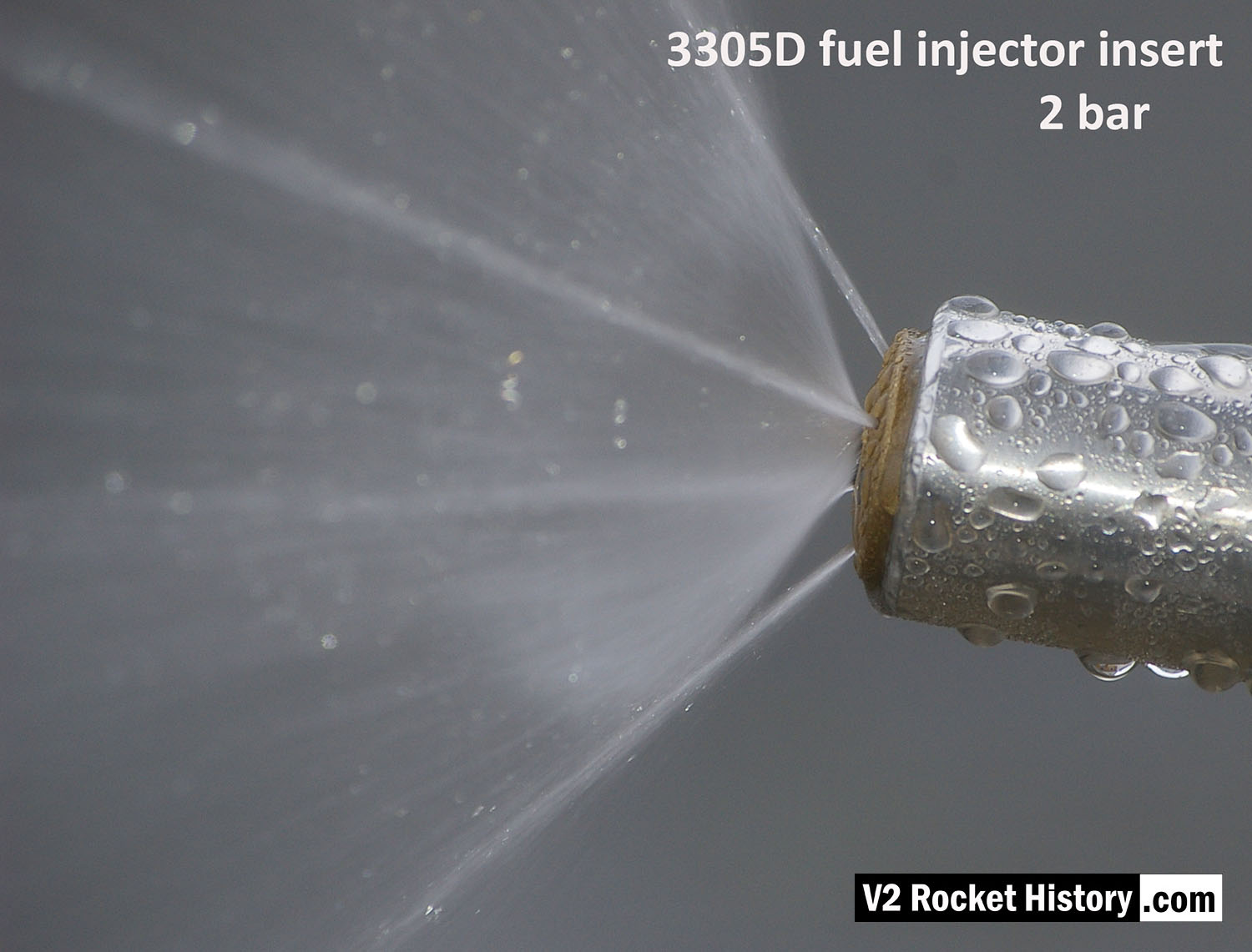
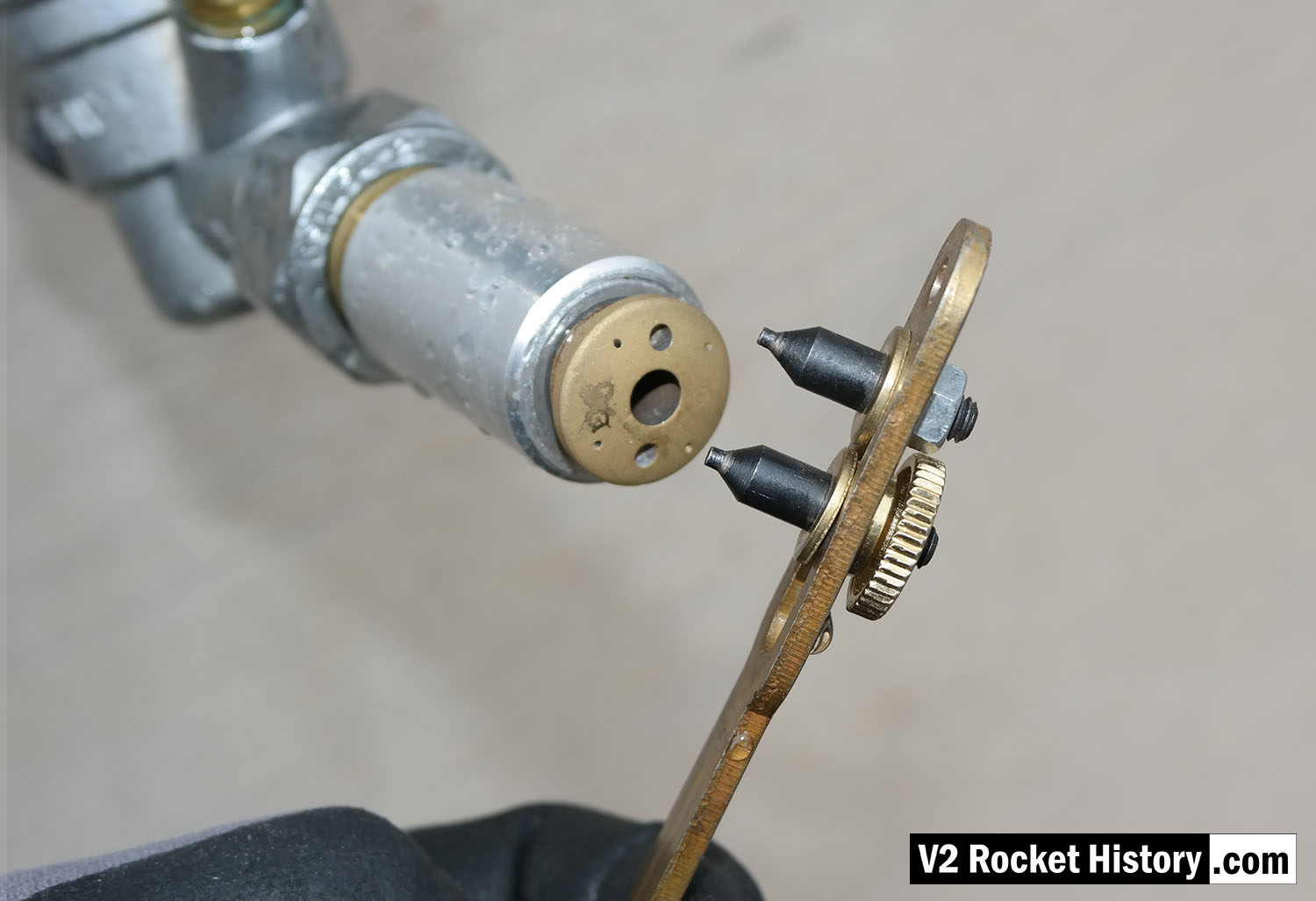

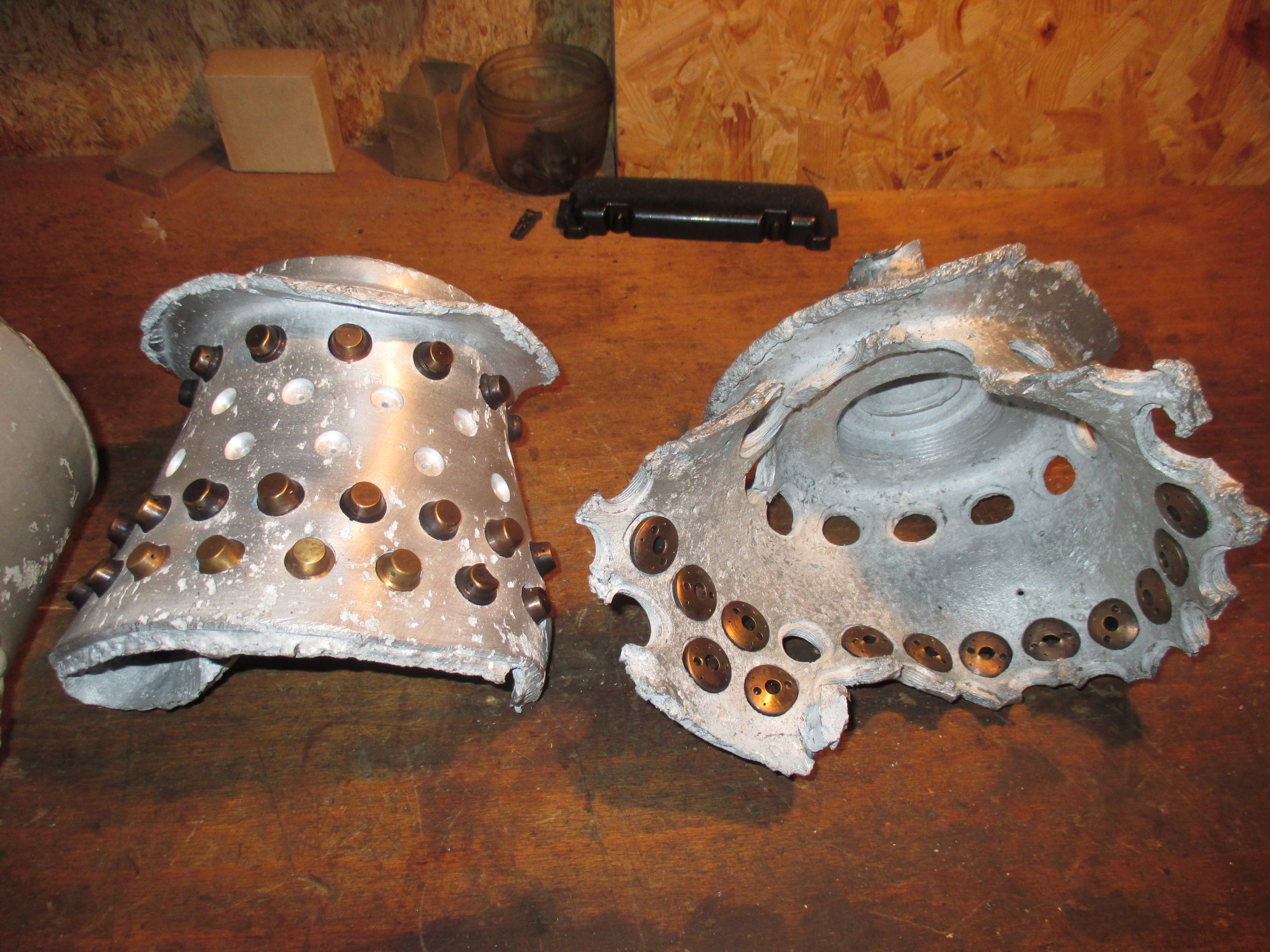

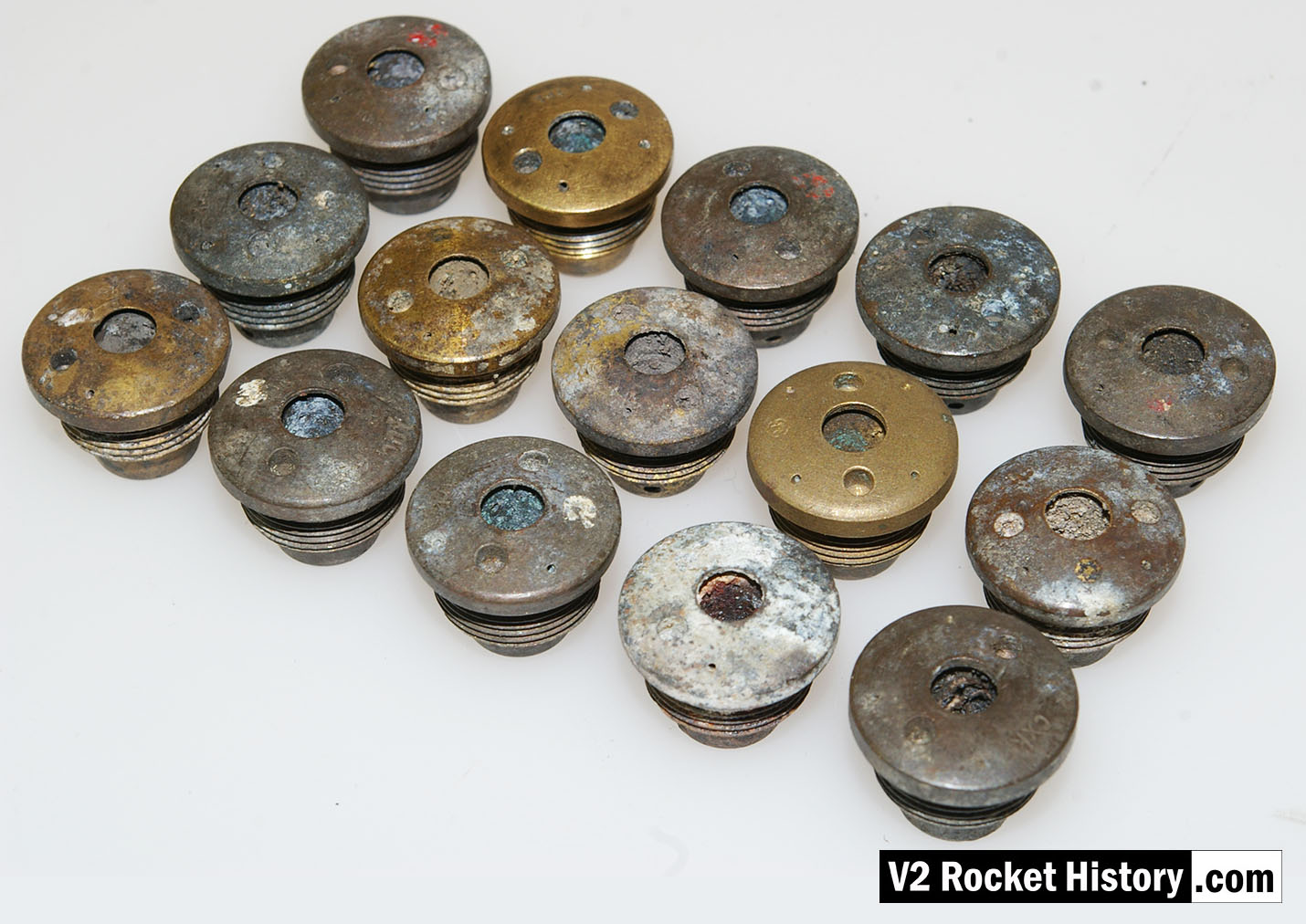


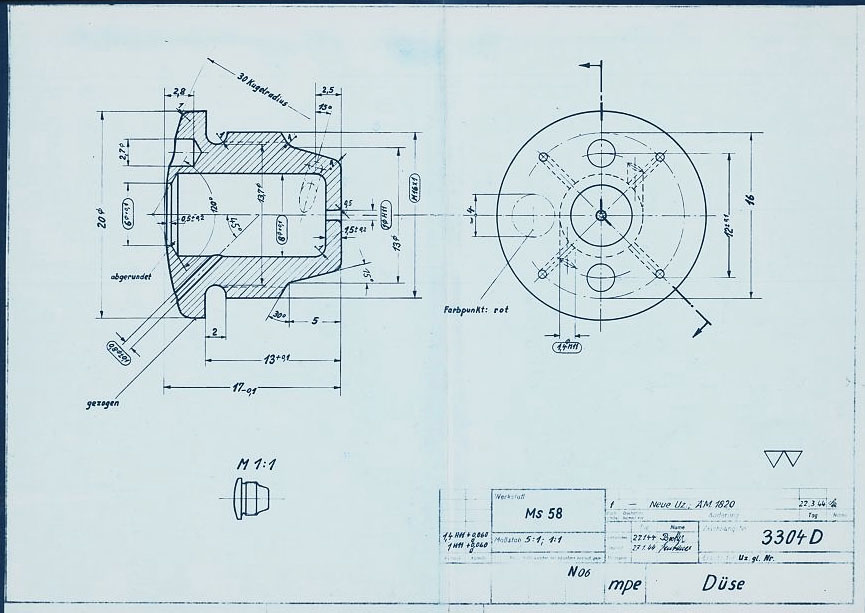
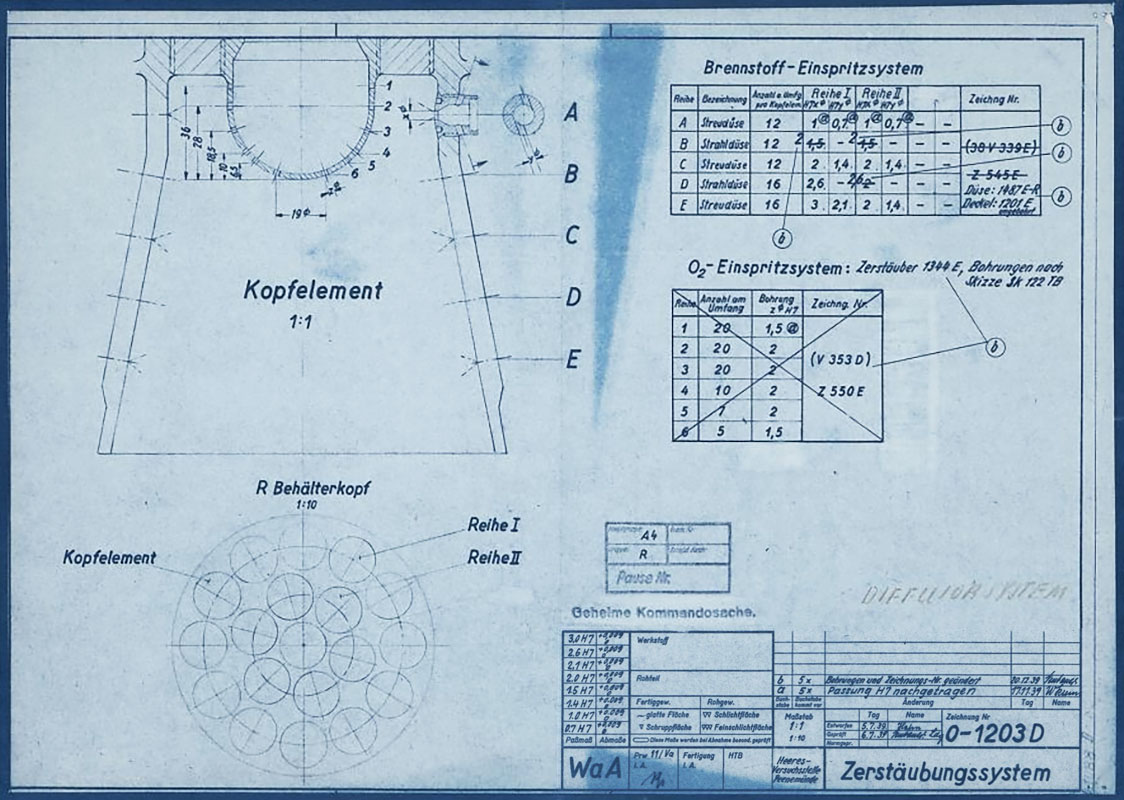
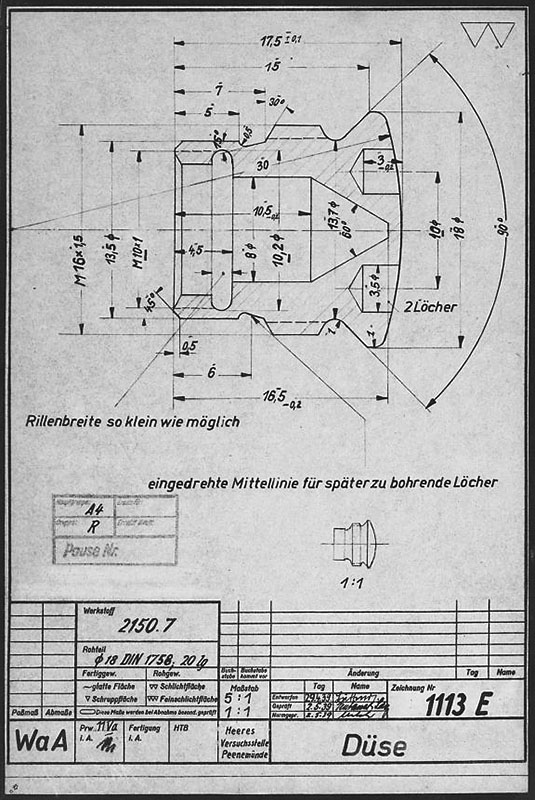
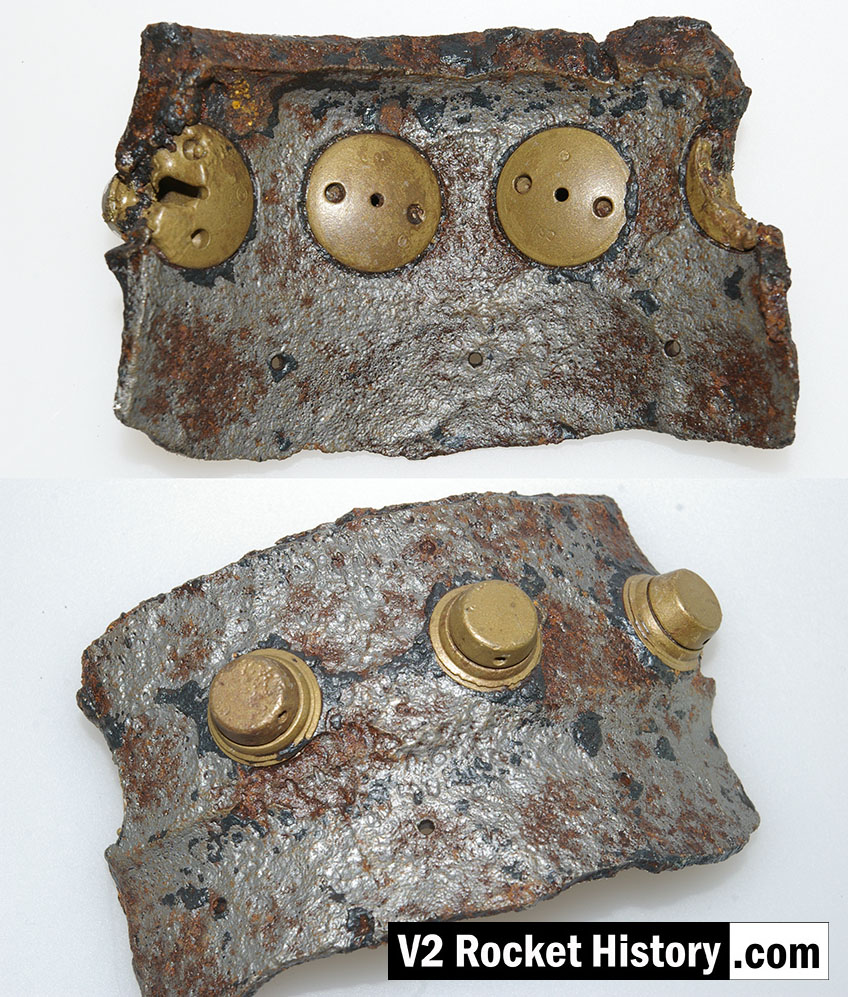
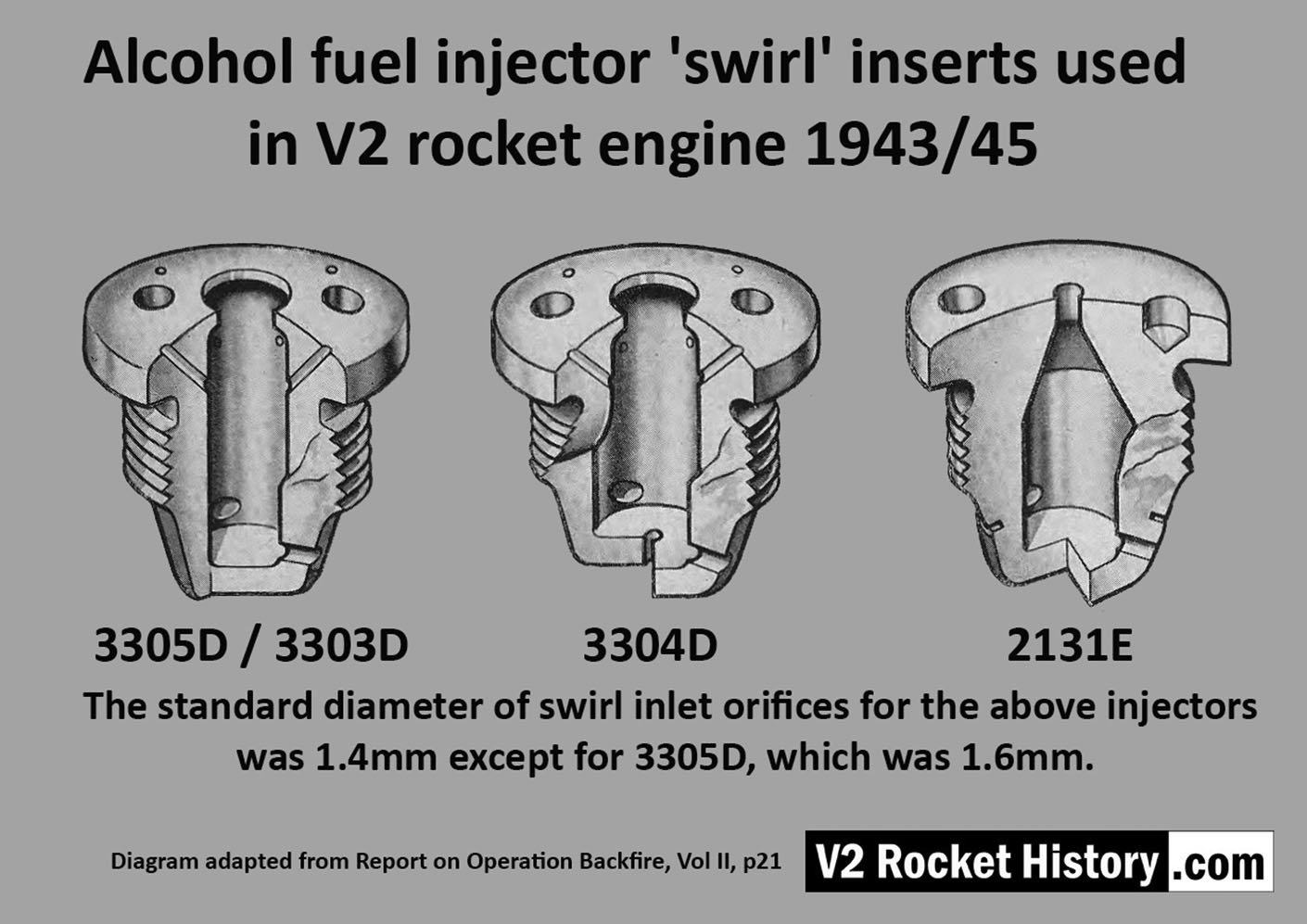
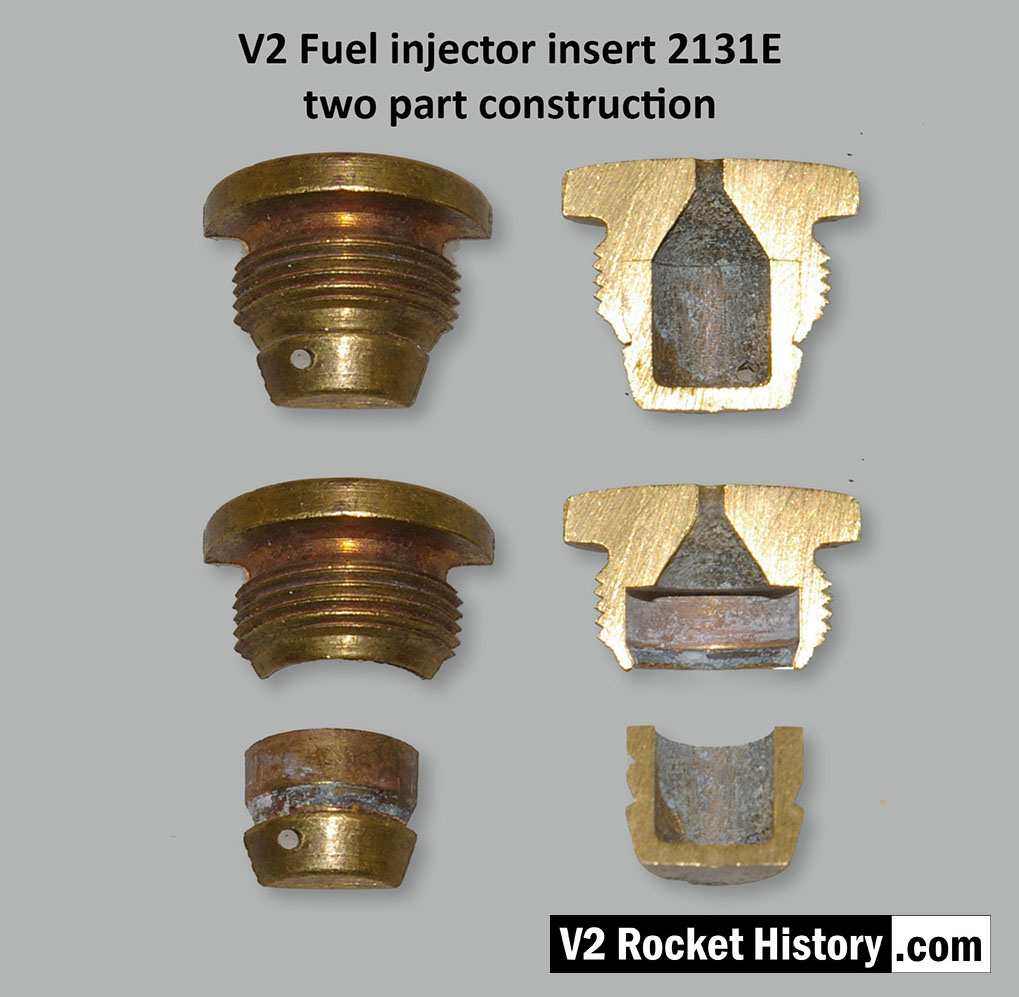

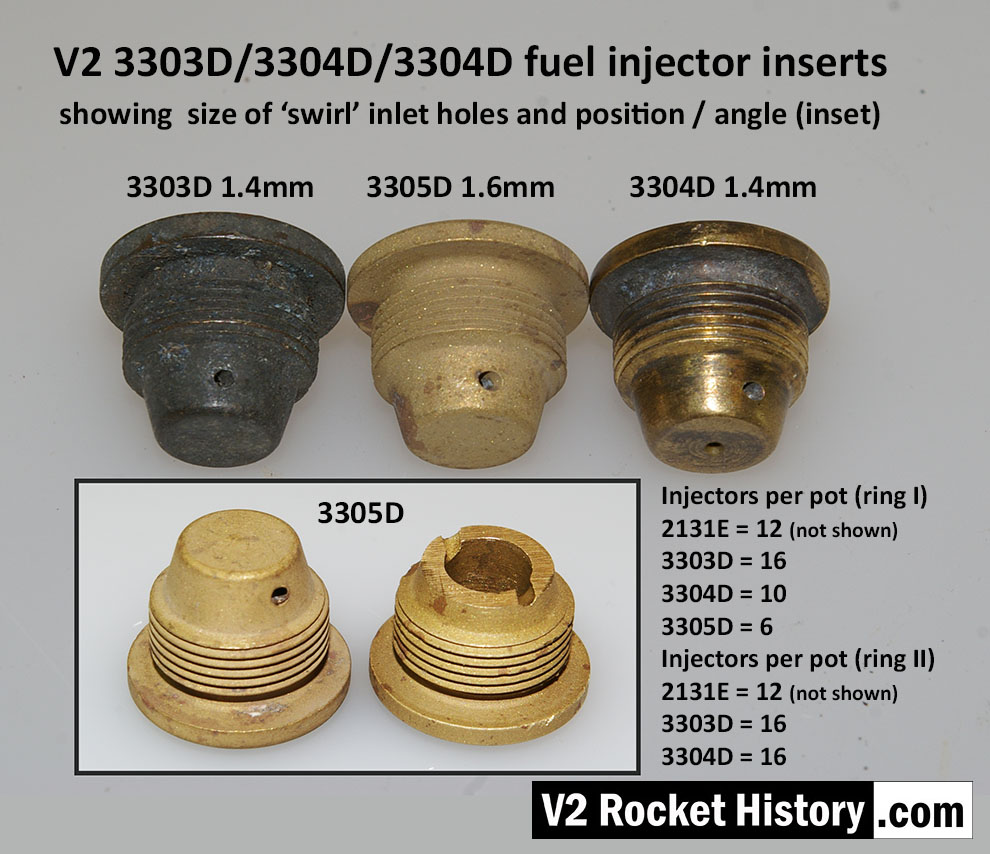
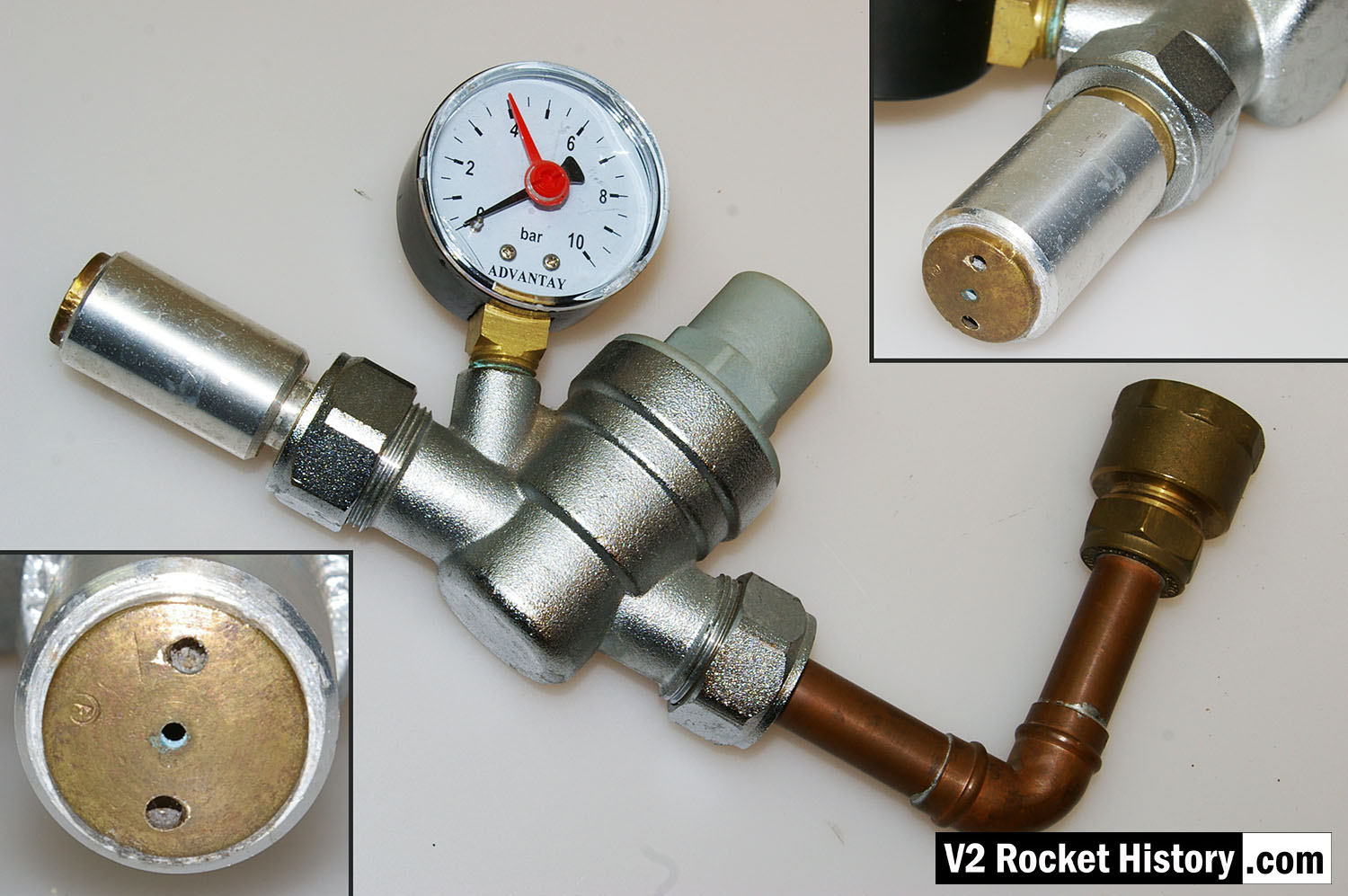
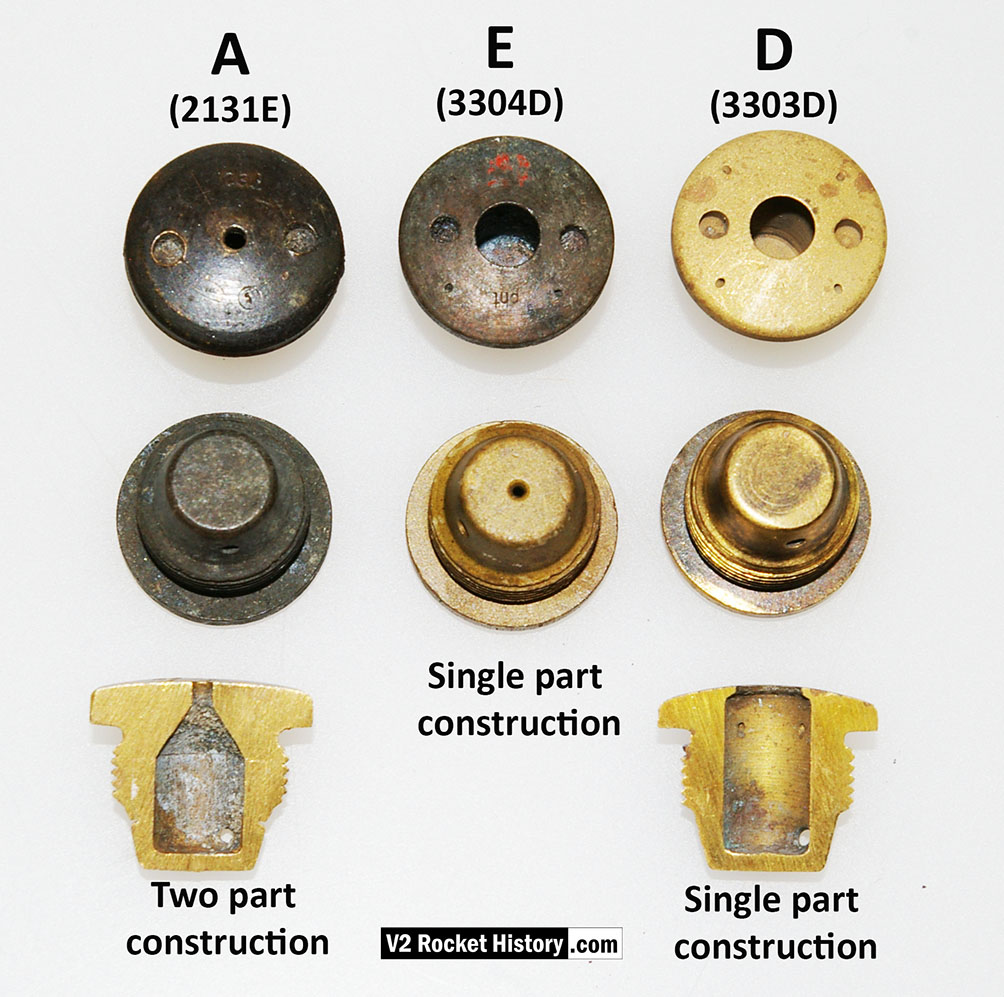
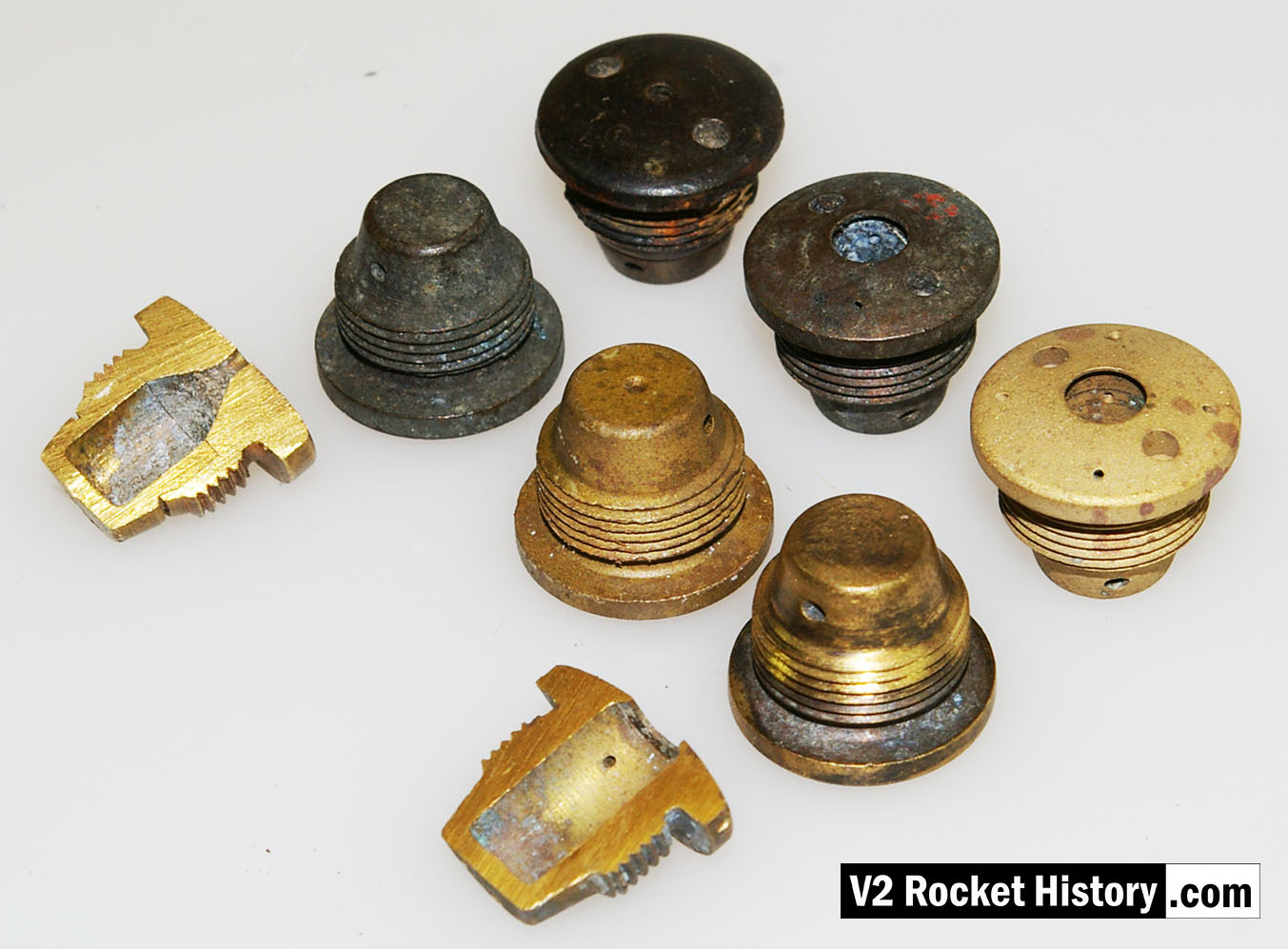
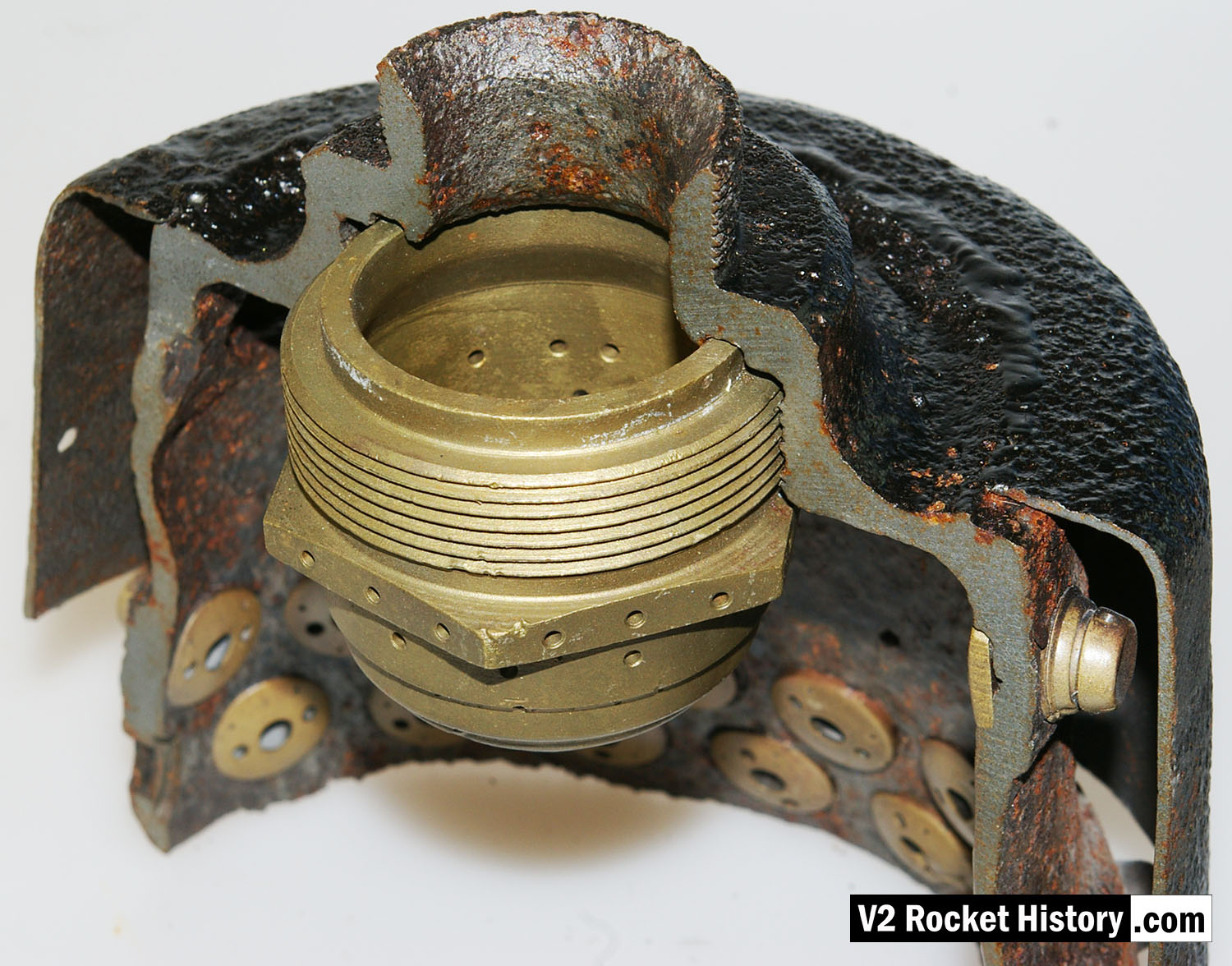

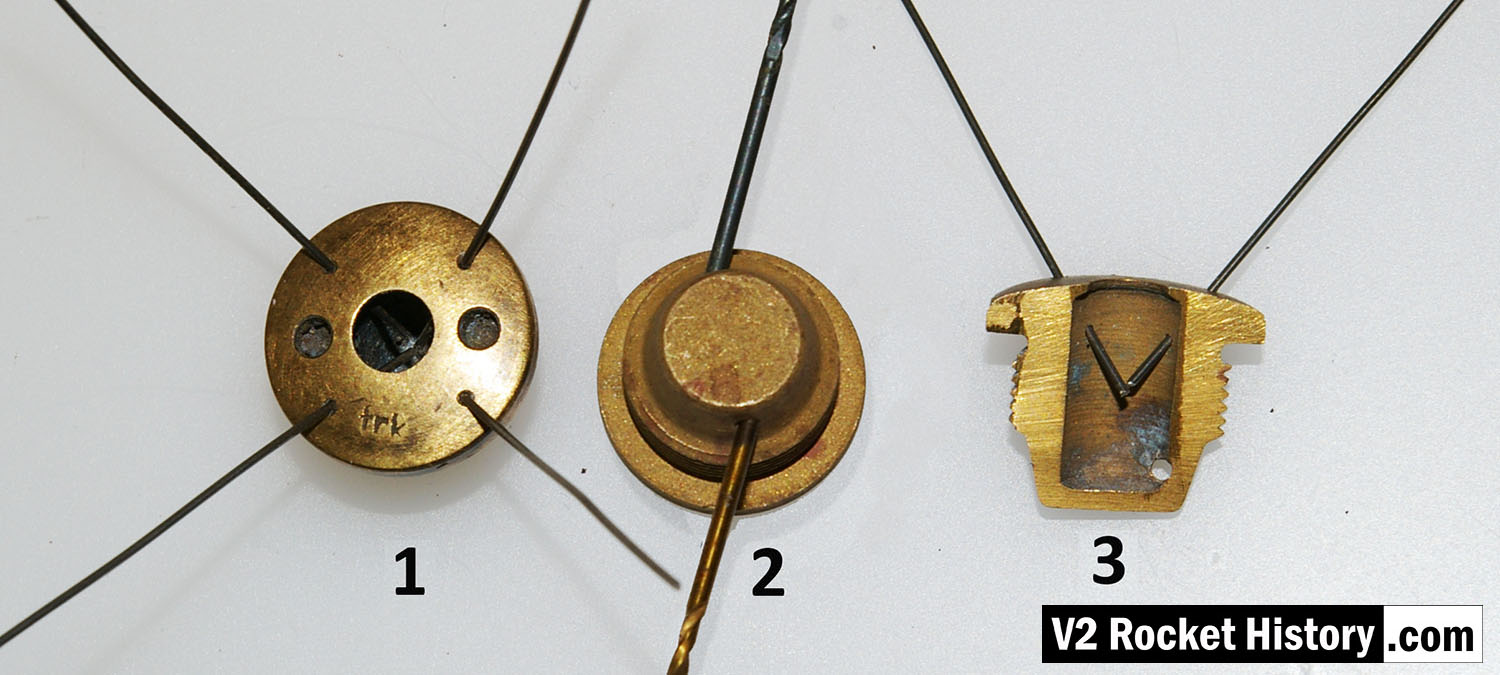
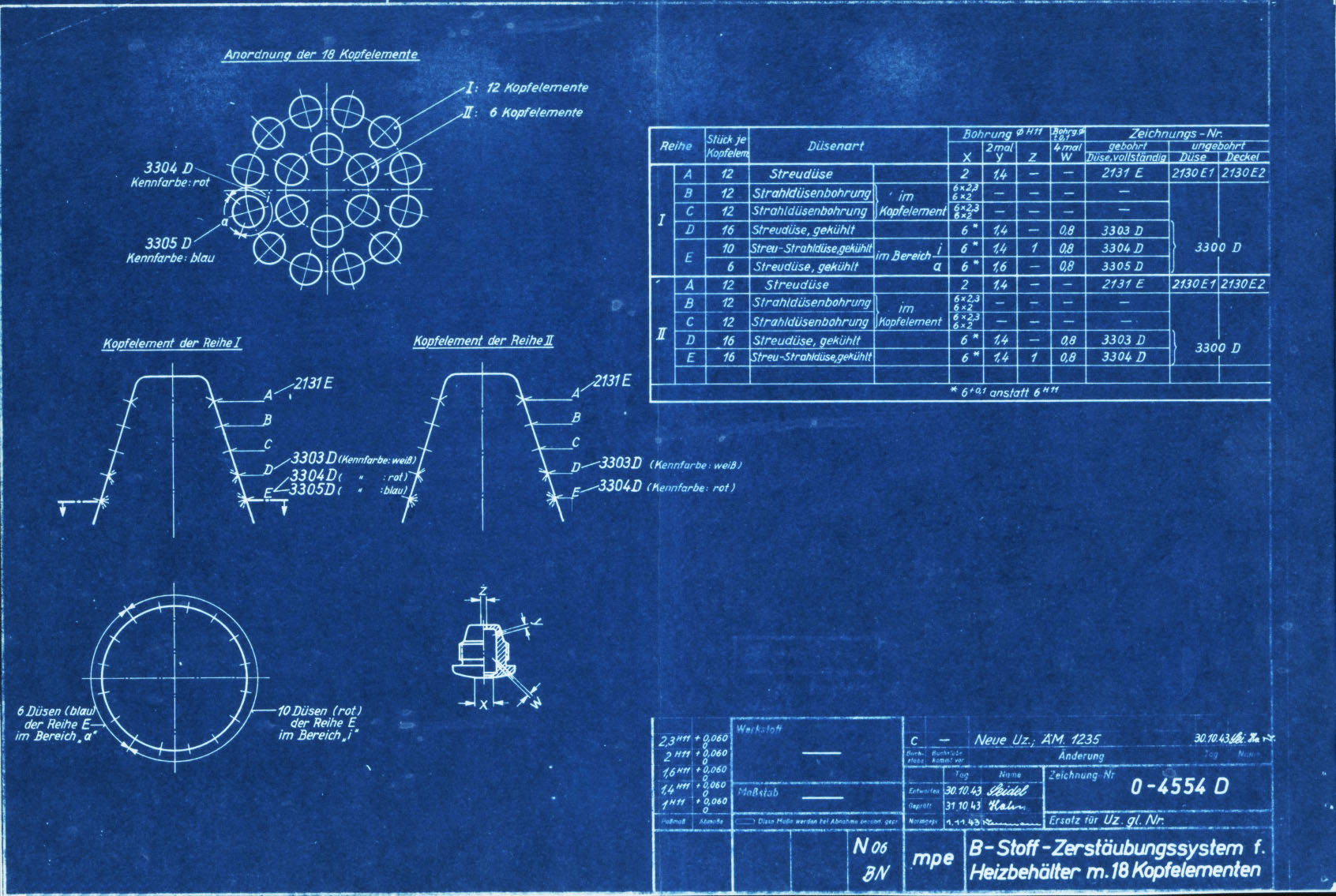
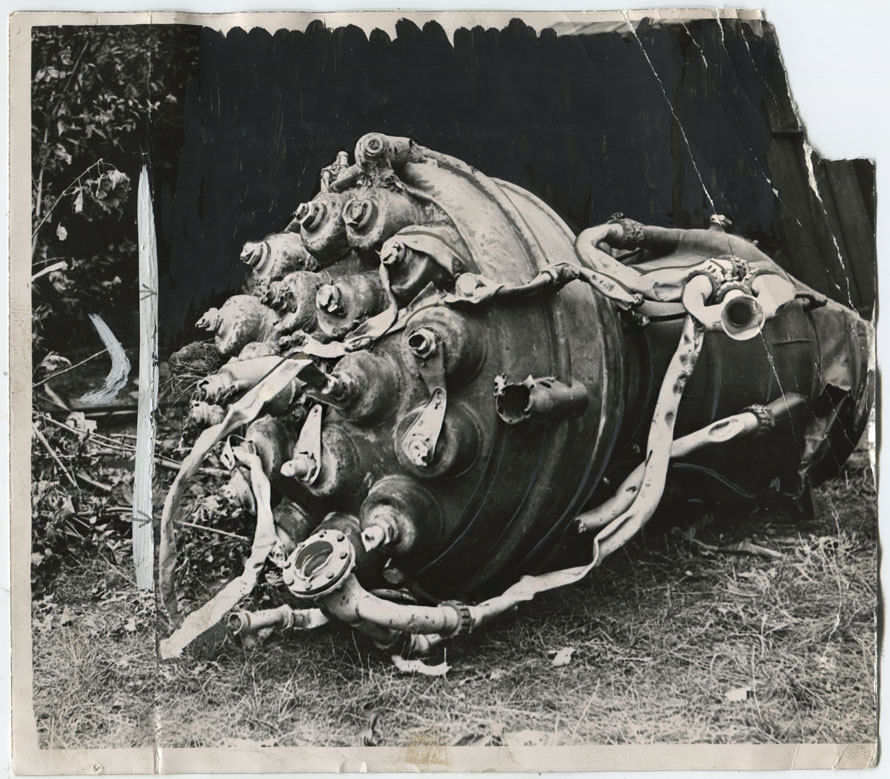
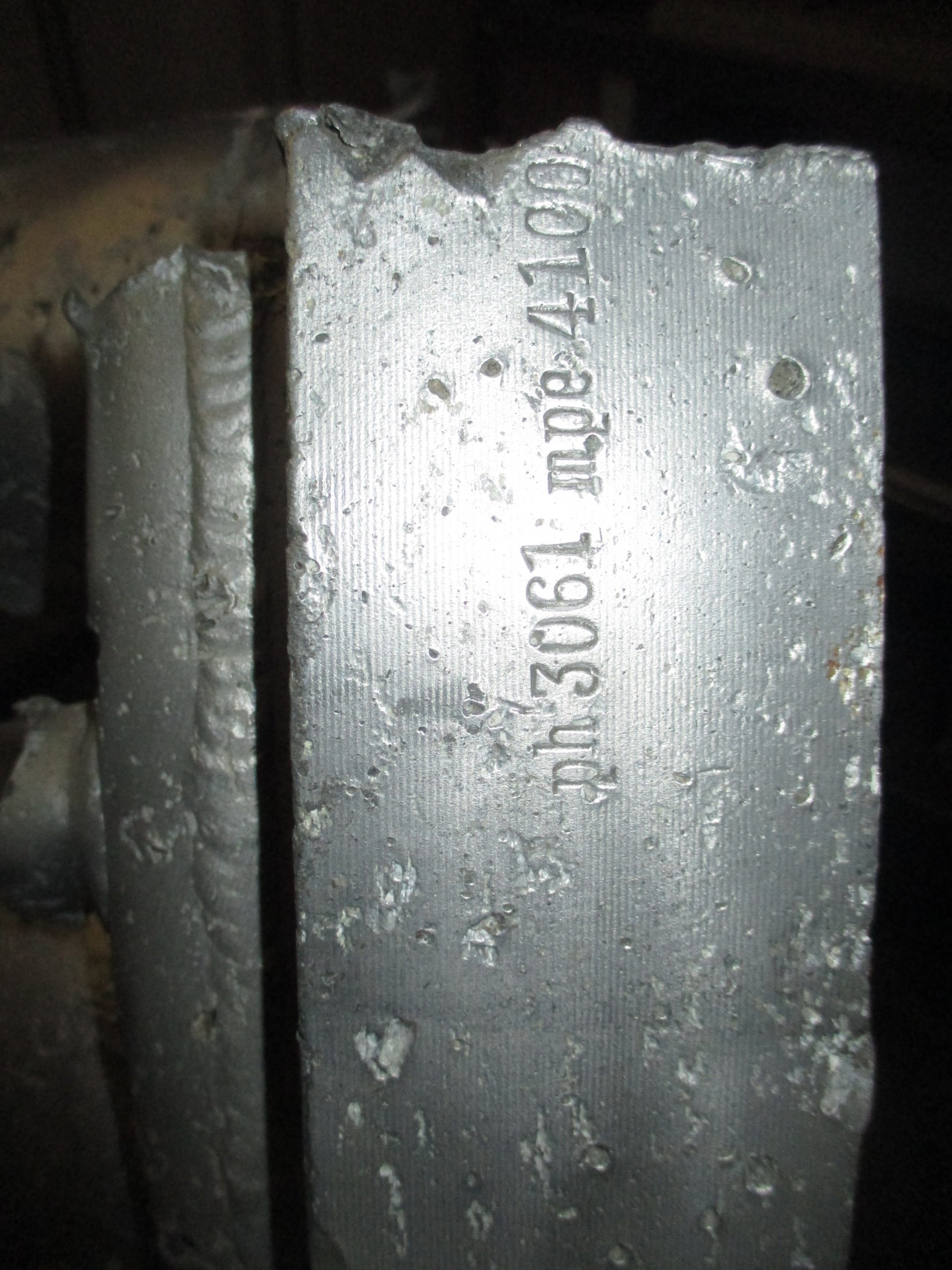
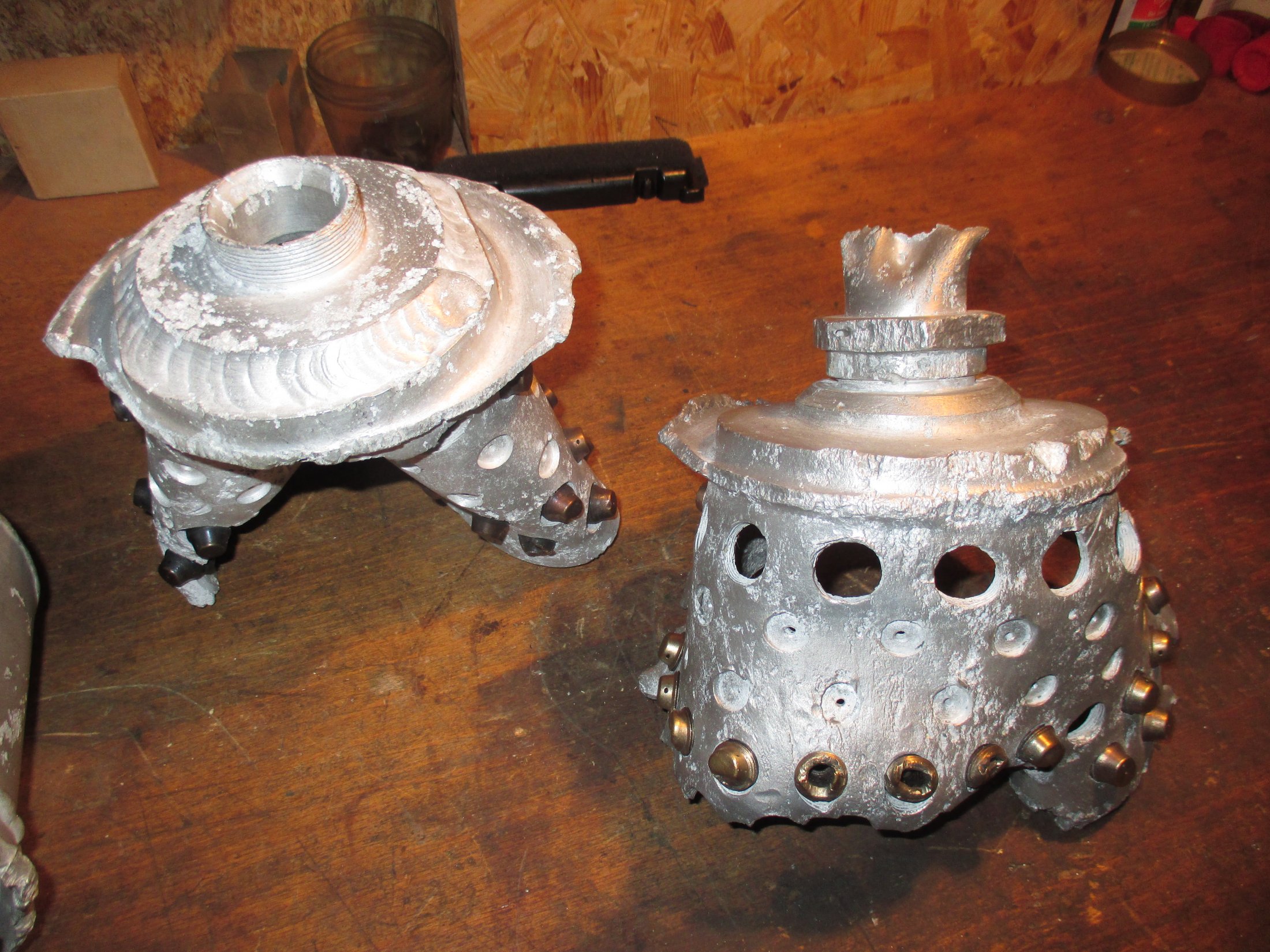
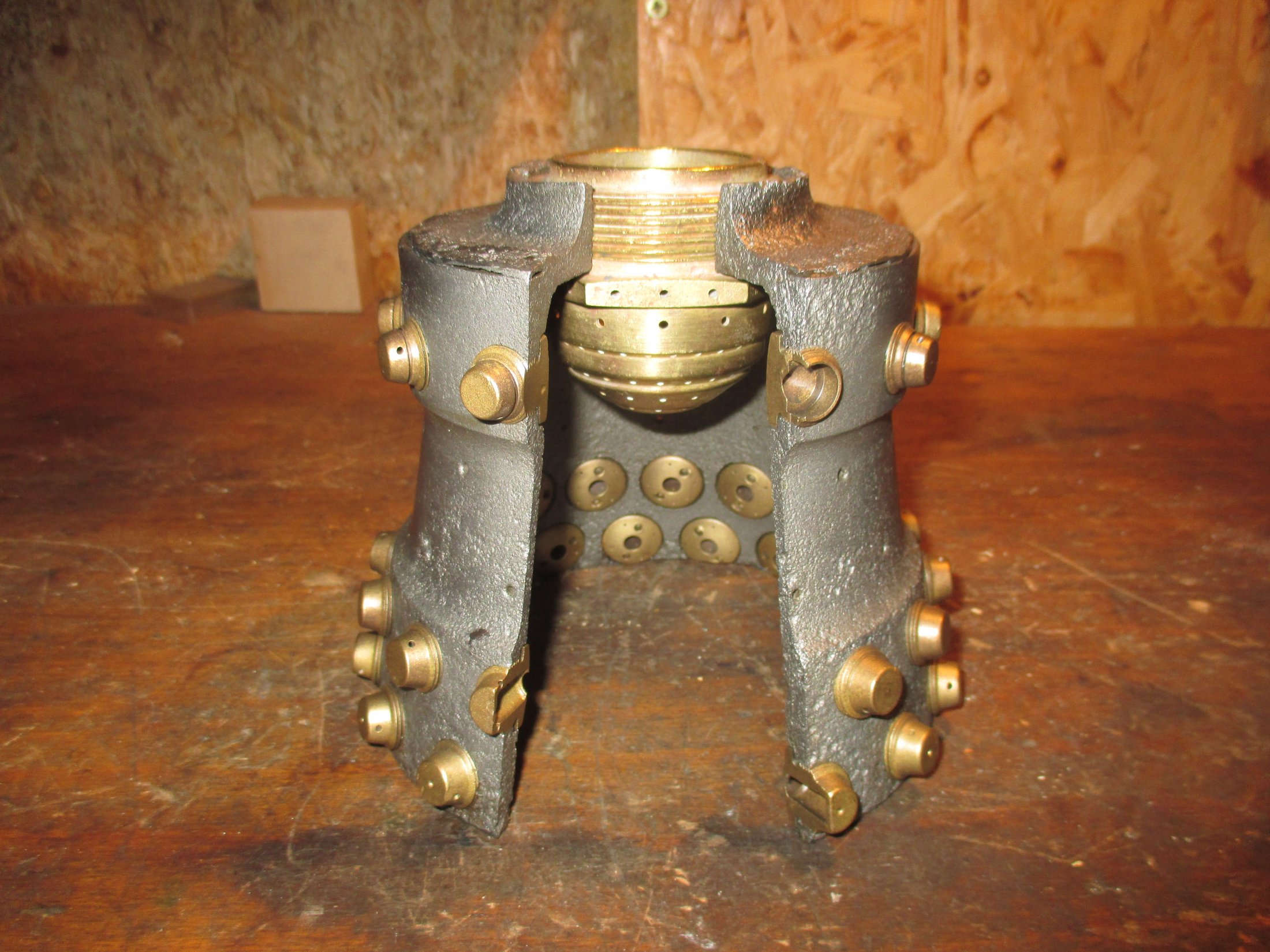
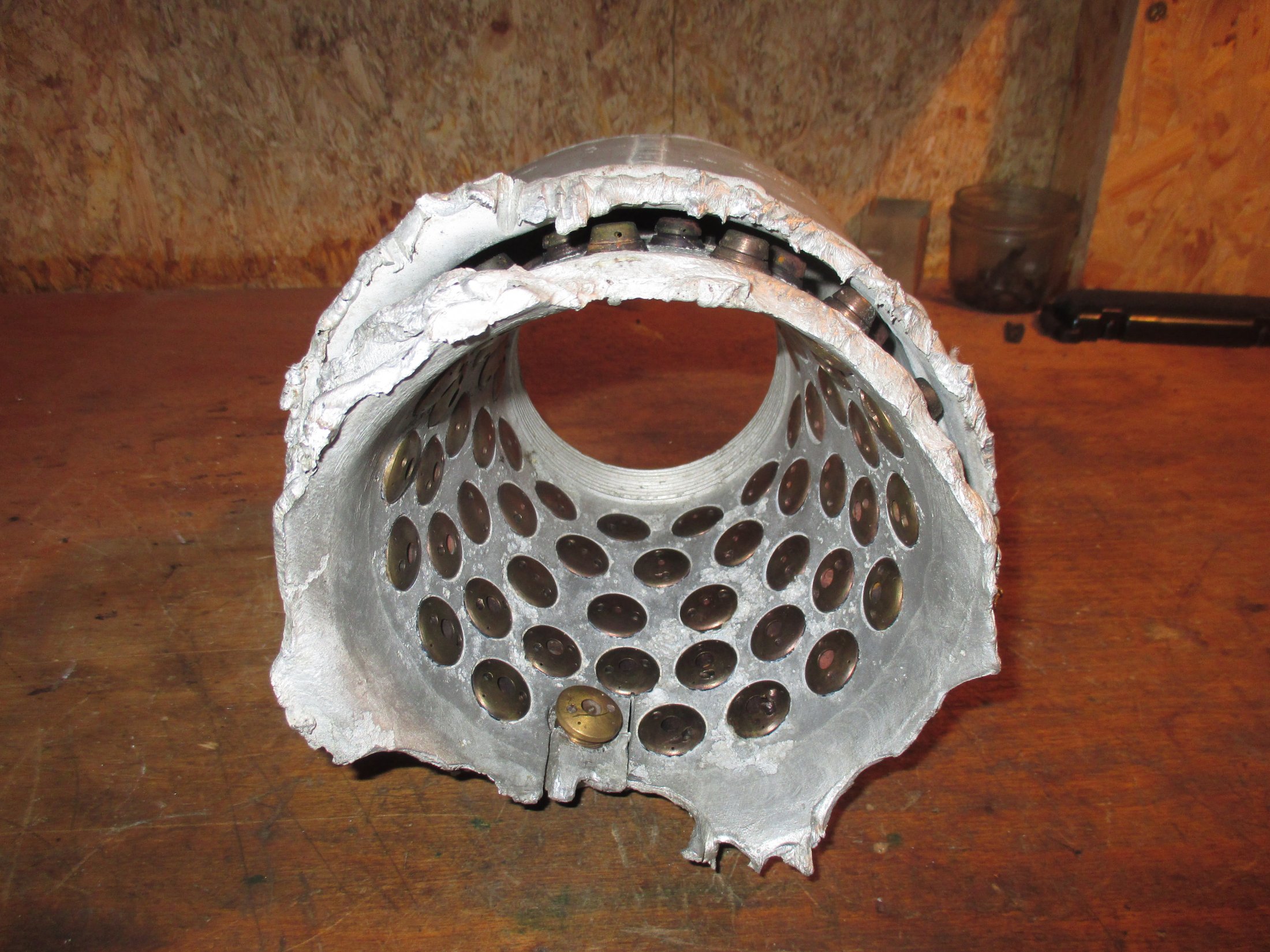
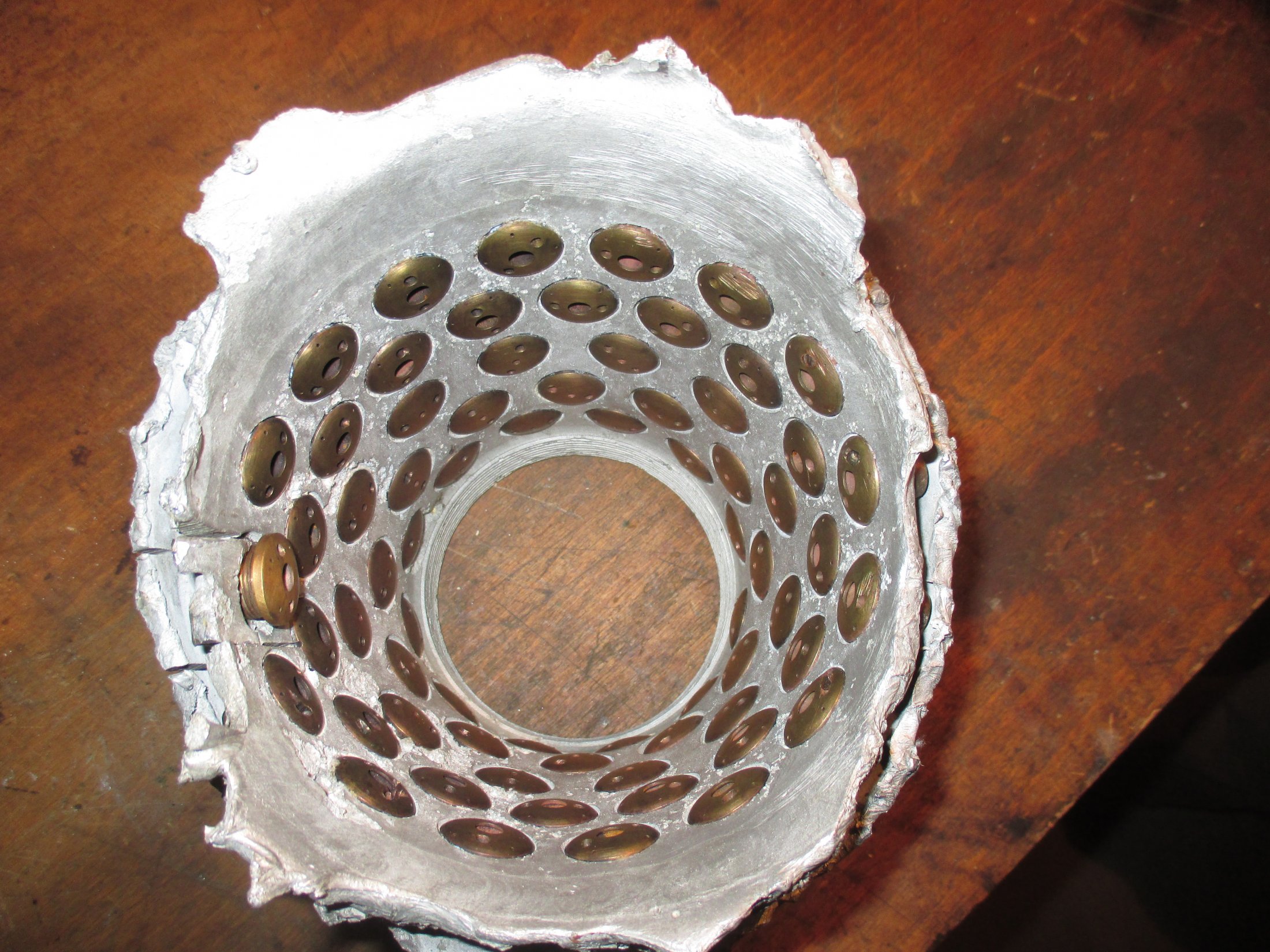
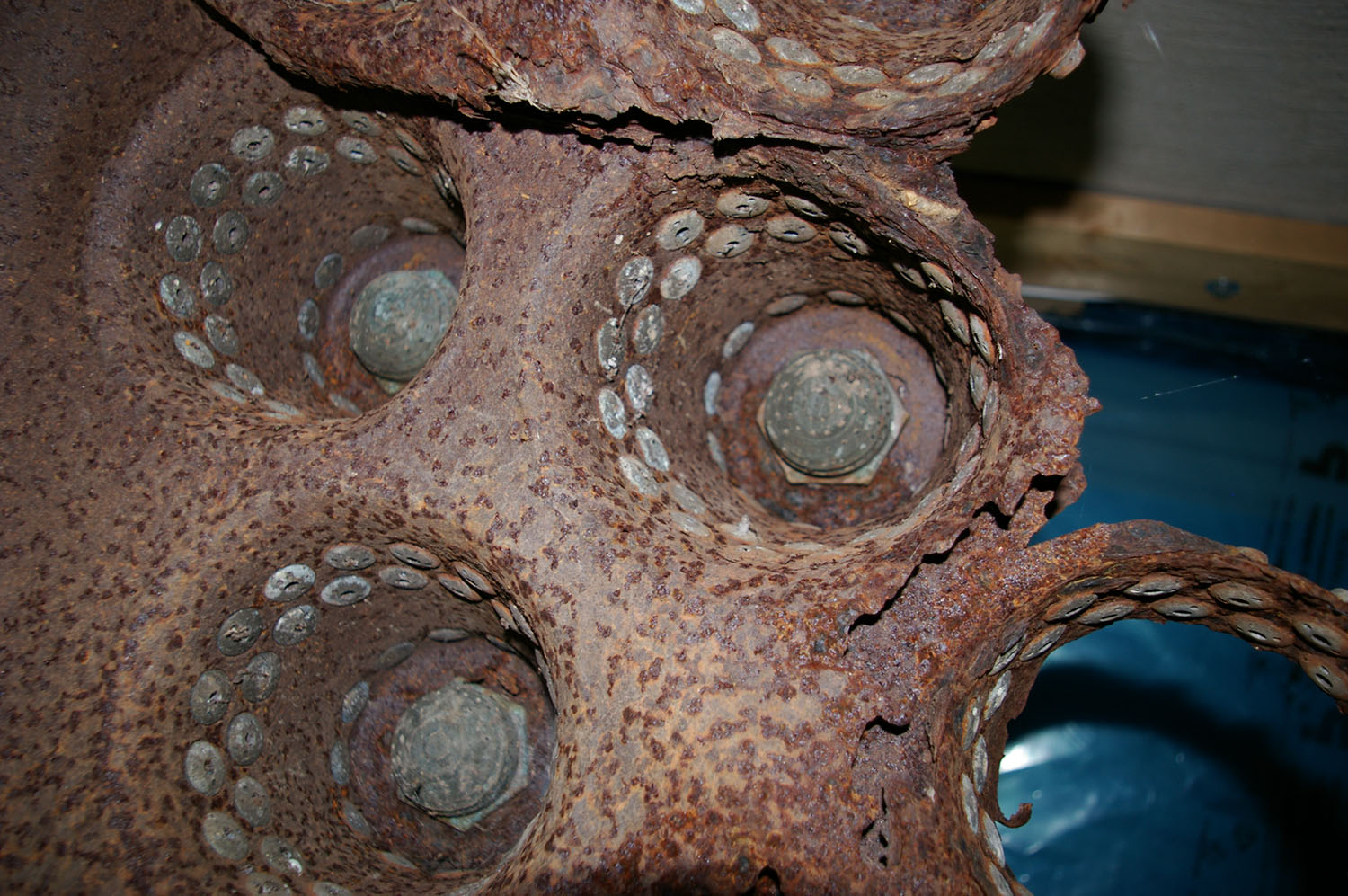
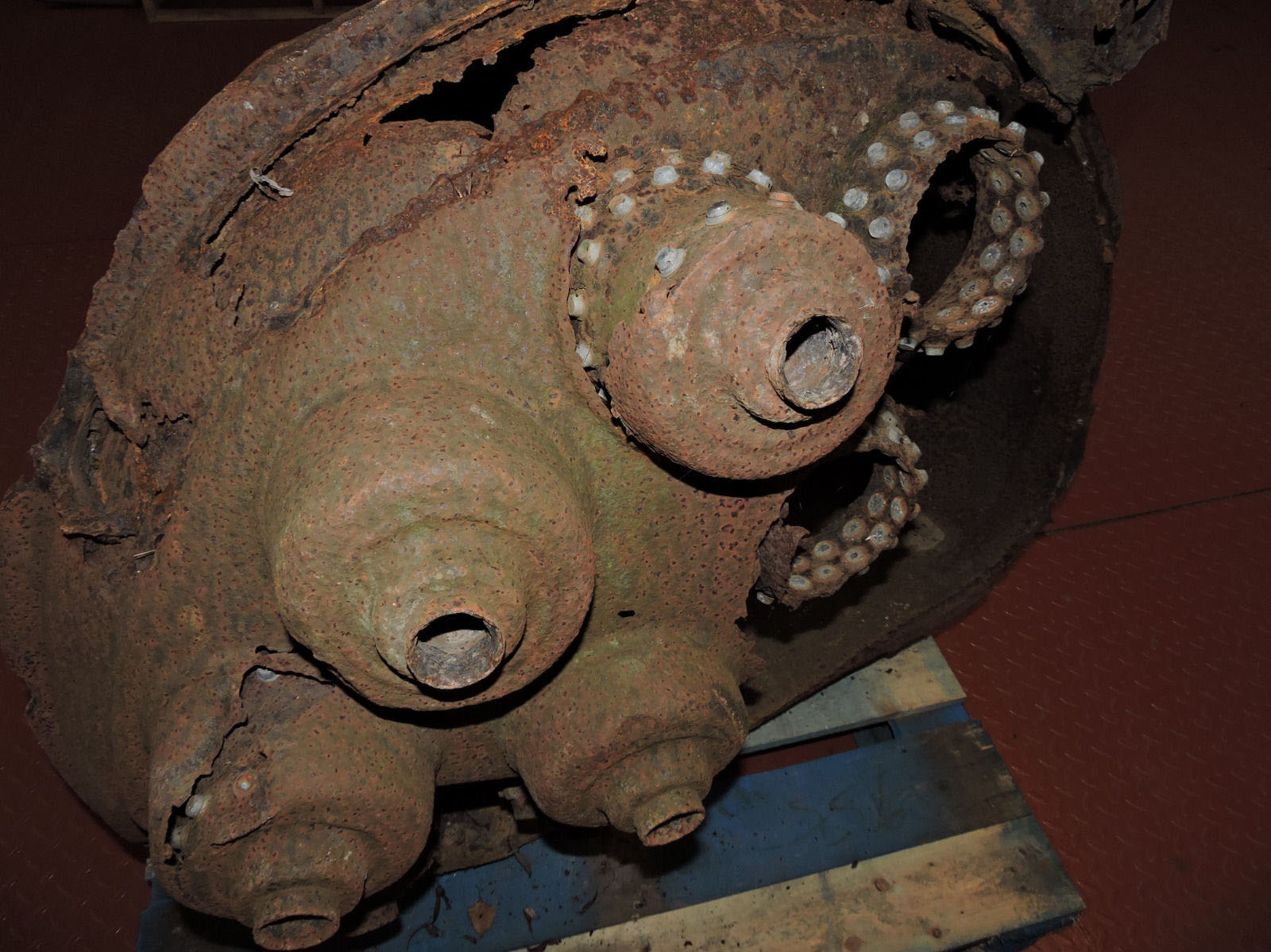
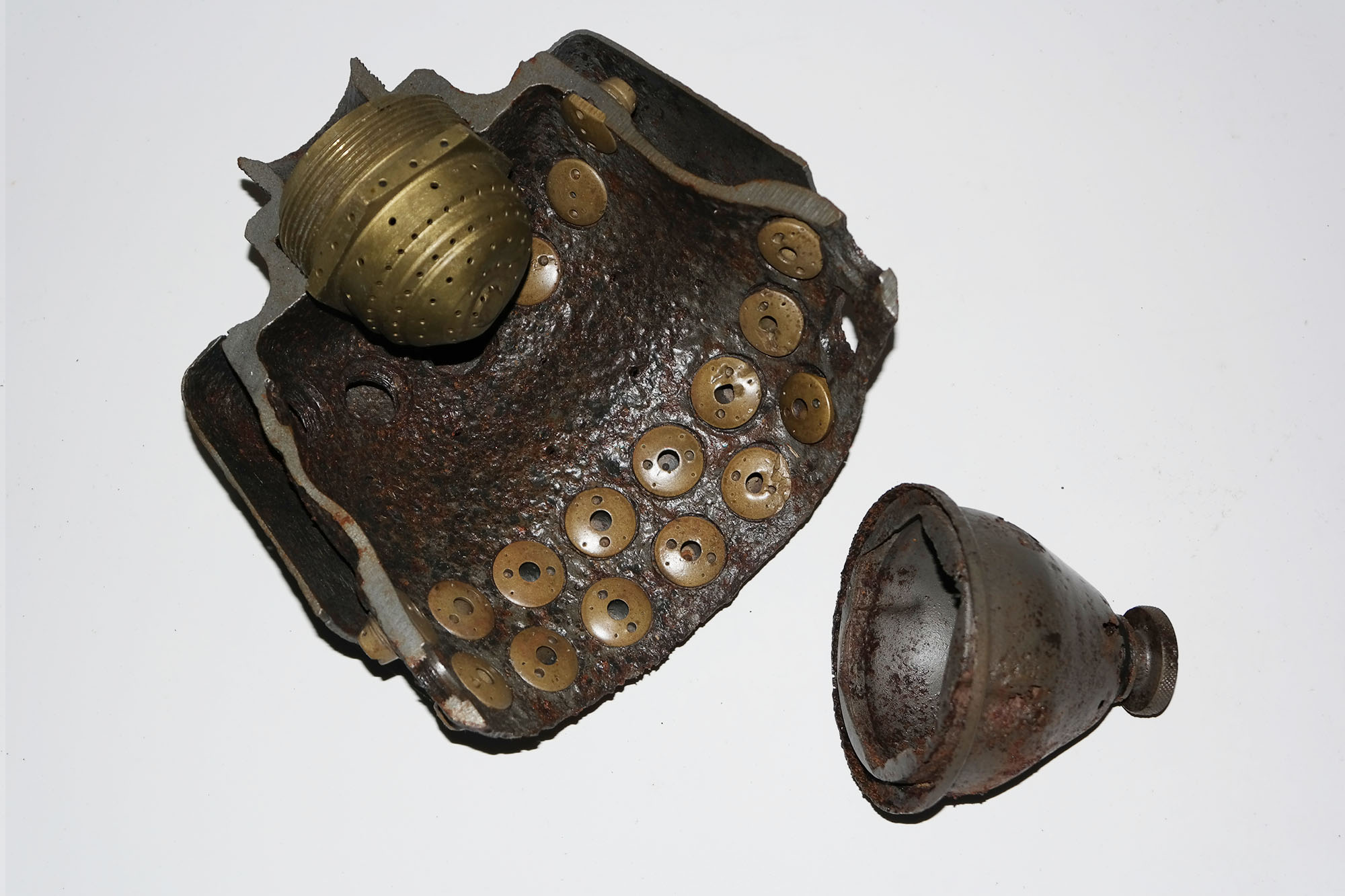
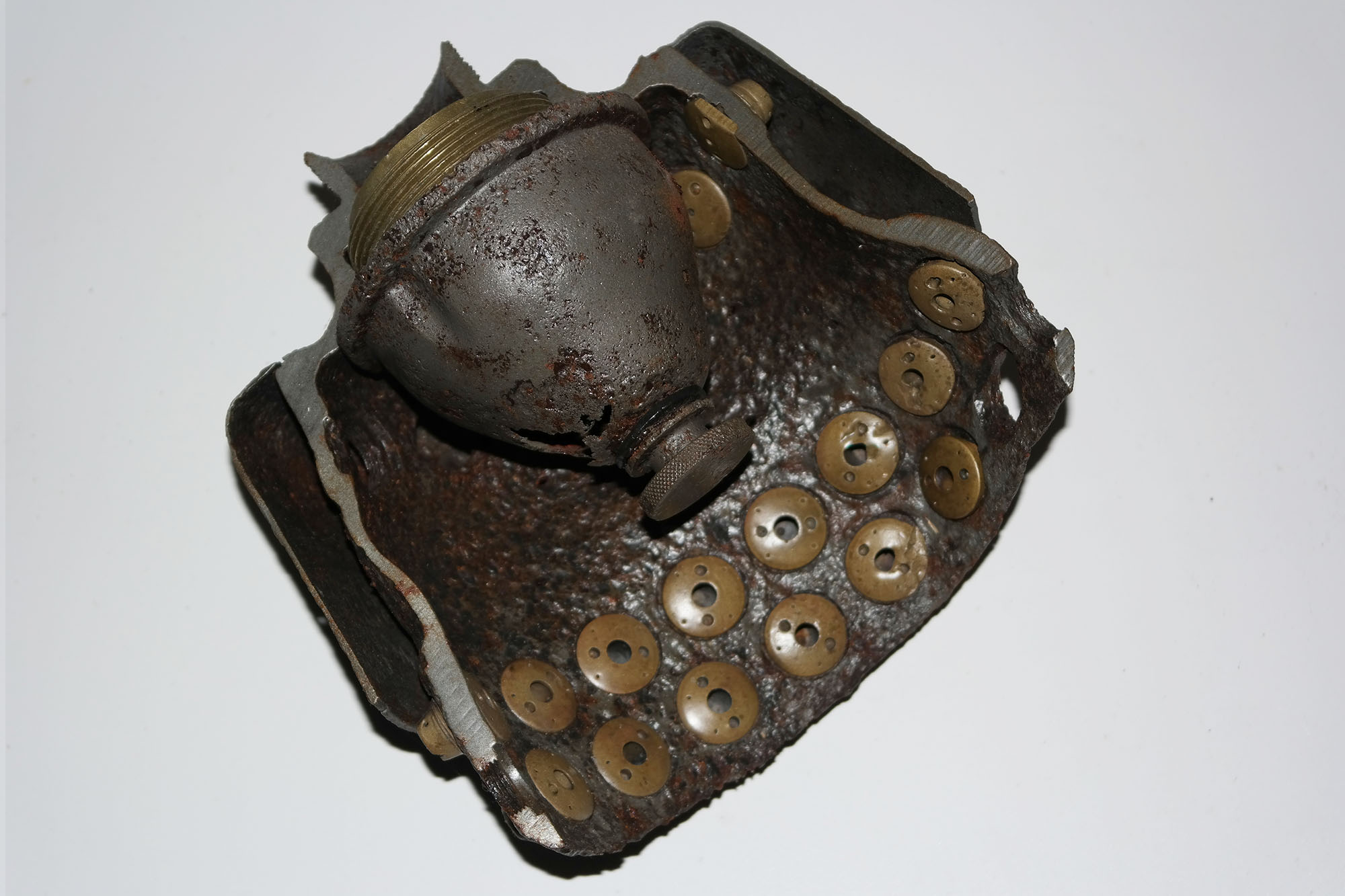
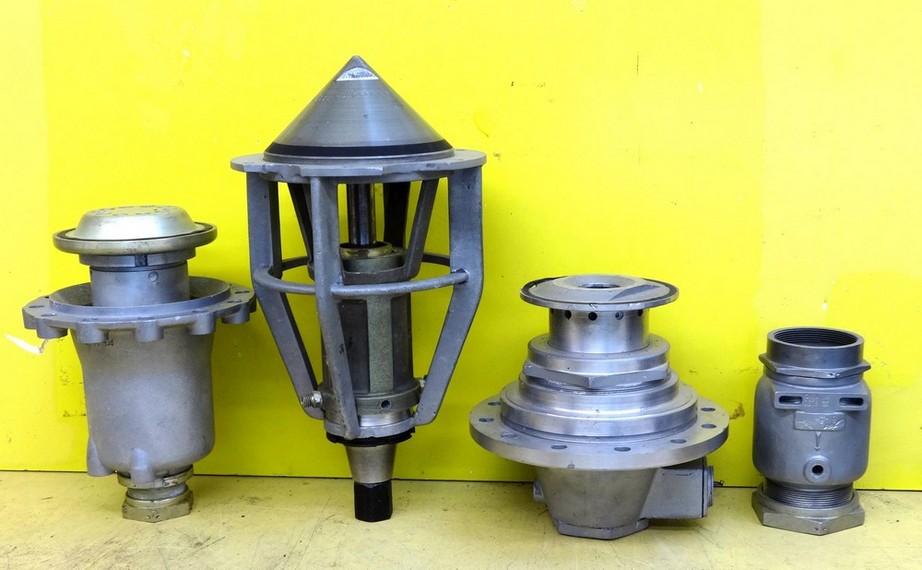
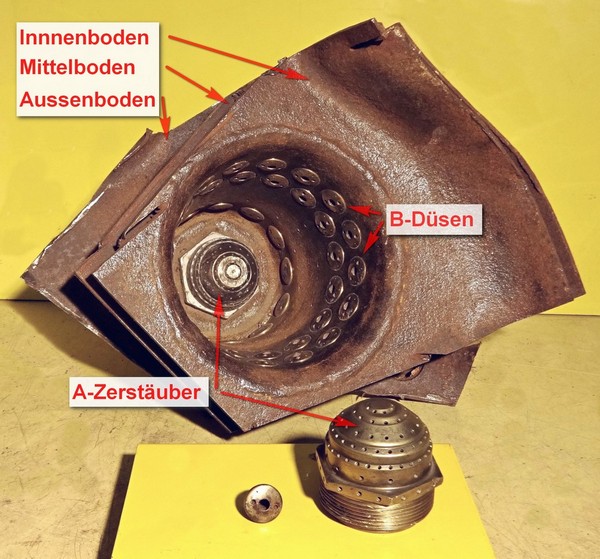
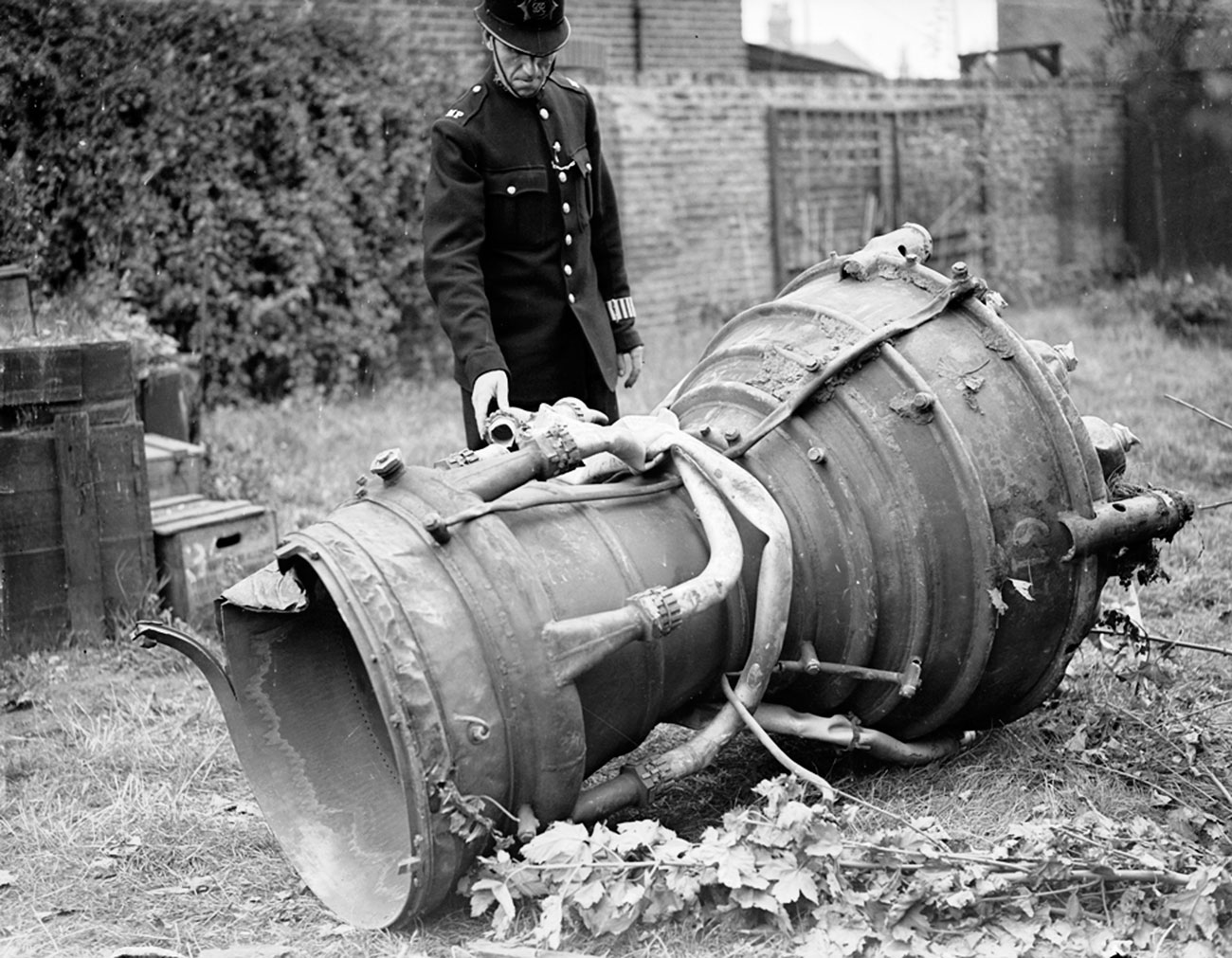
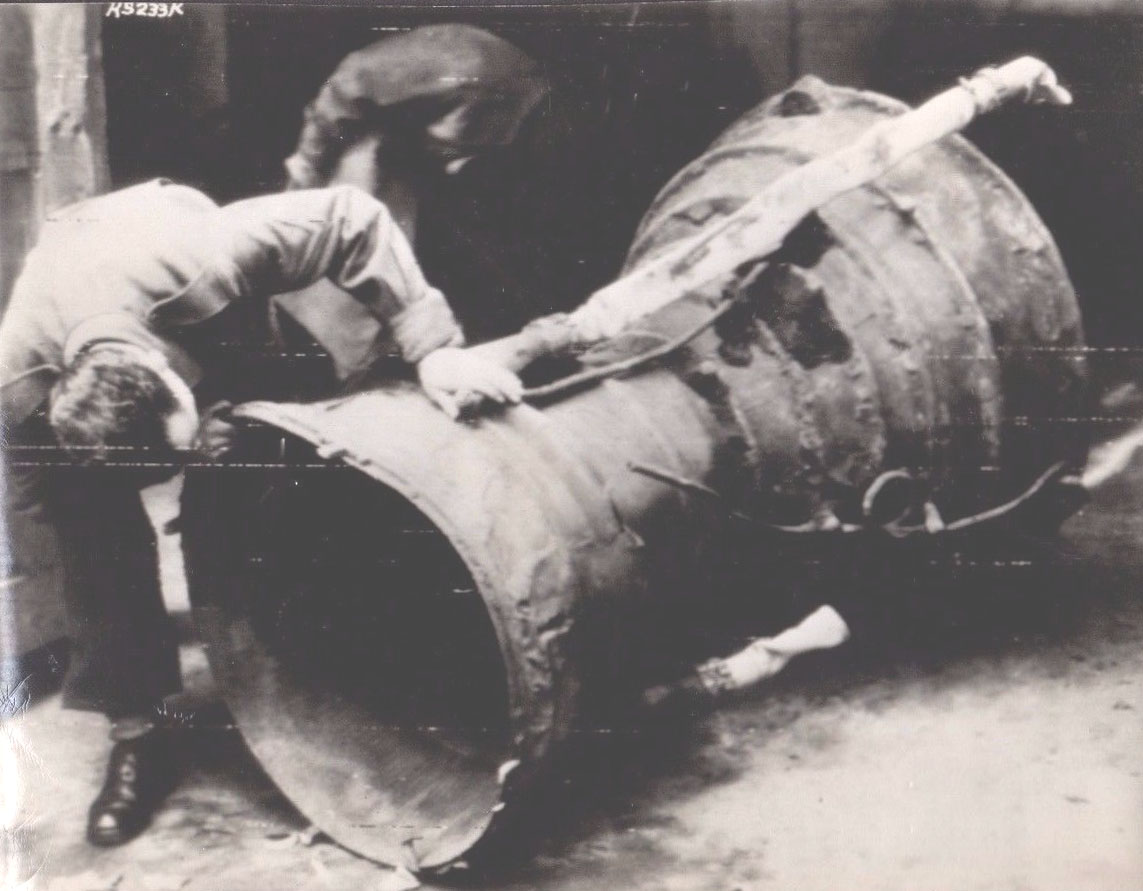
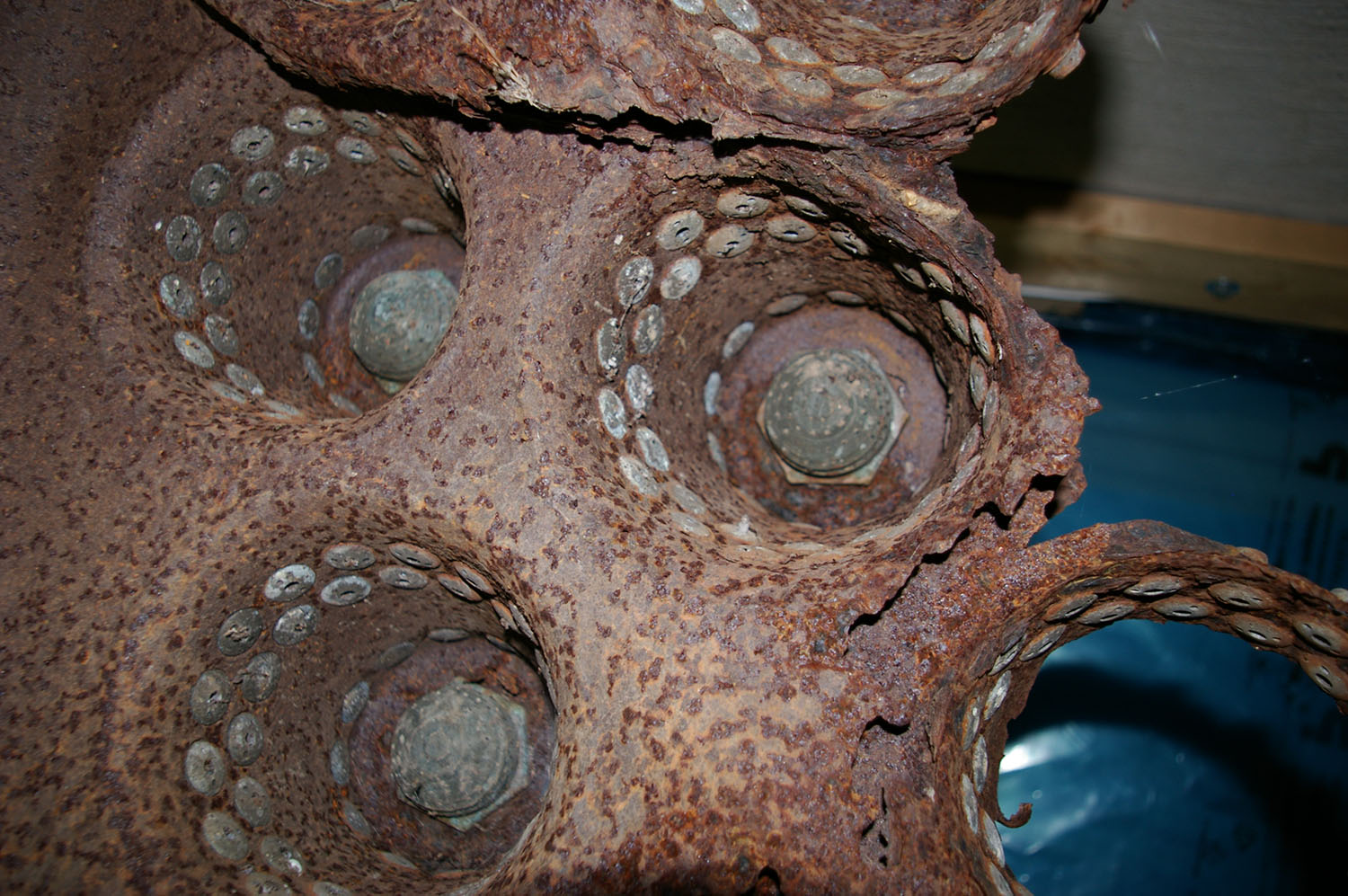
Categories: Anatomy of the V2, Combustion, Propellant flow, V2 Missile relics, Electrical connection
Tags: #Combustion and injection #chamber cooling #Test procedures #Propellent injector system #V2 Missile relics #A4-V2 supply contractor #V2 Technical Drawings #Propellant Valves #V2 in combat #Thrust chamber
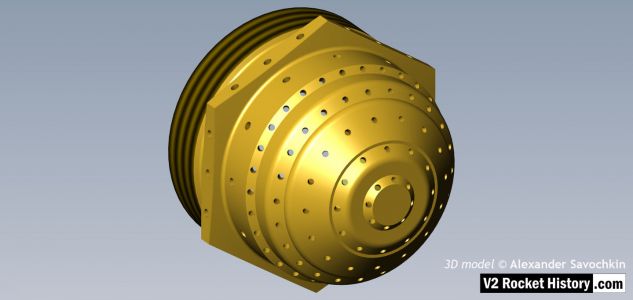
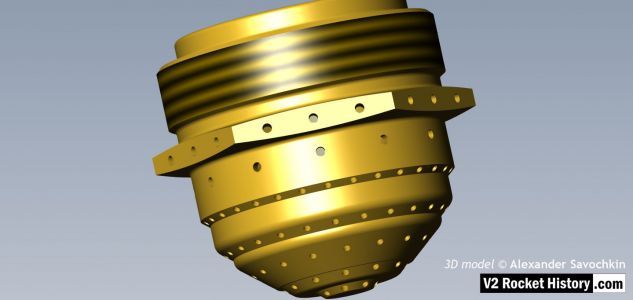
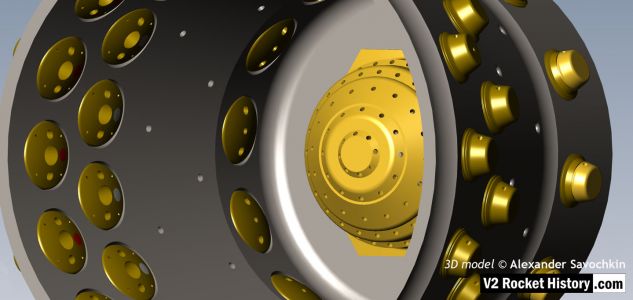
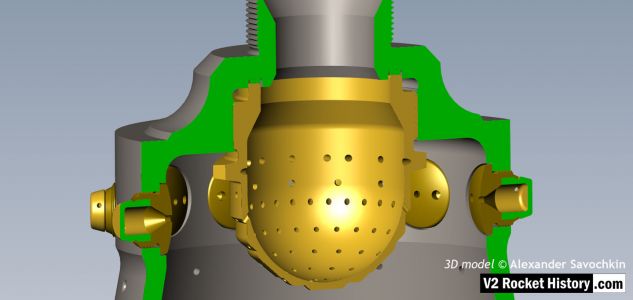
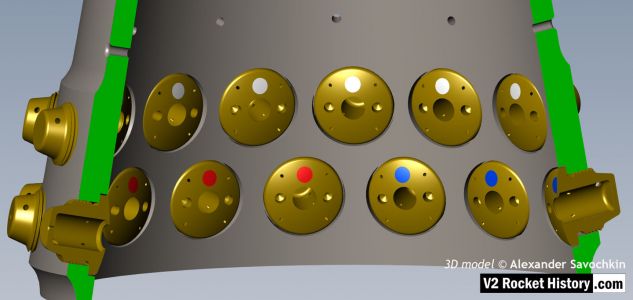
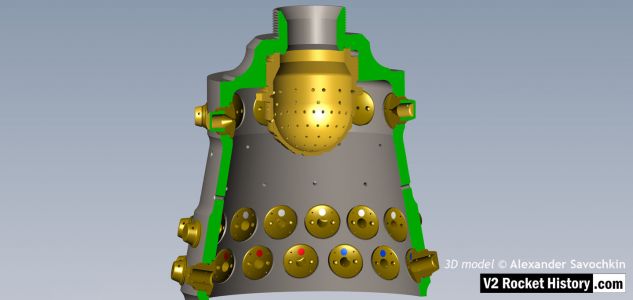
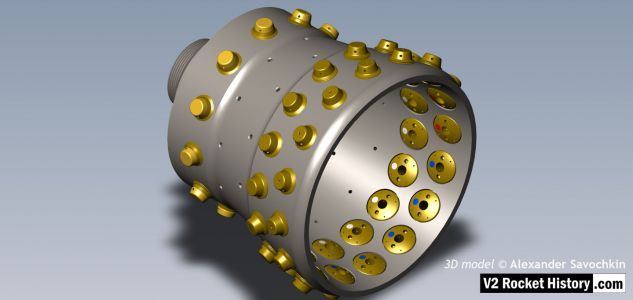
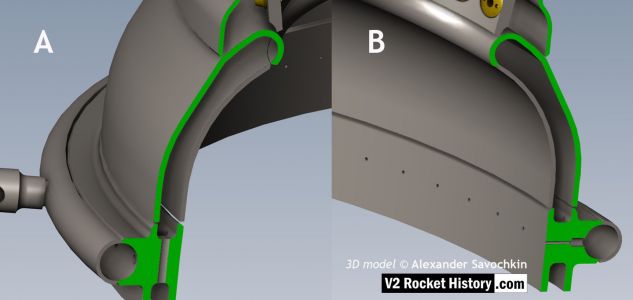
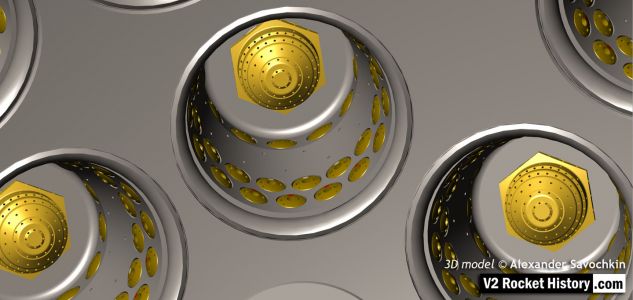
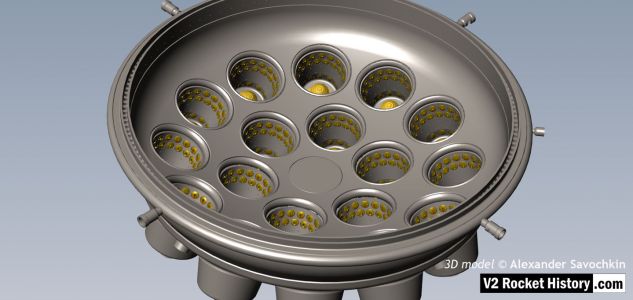
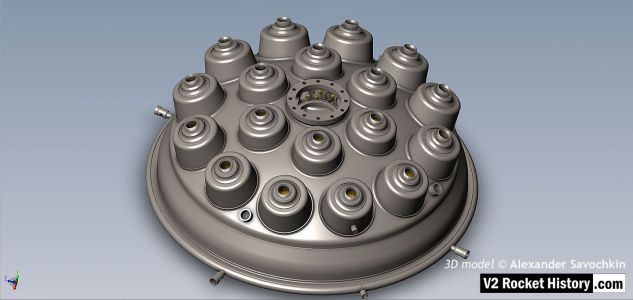
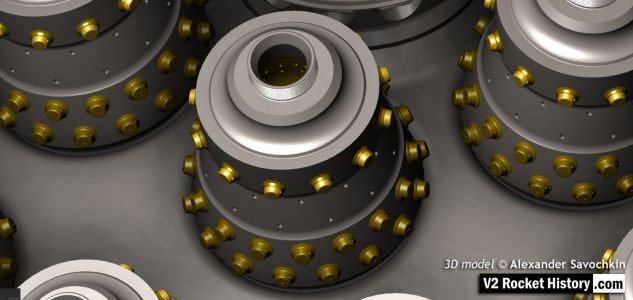
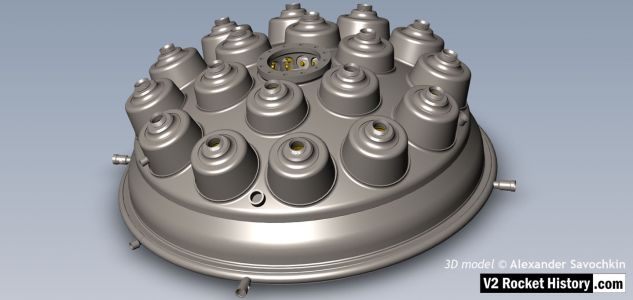
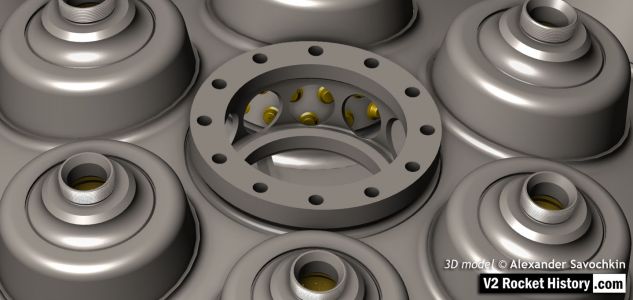
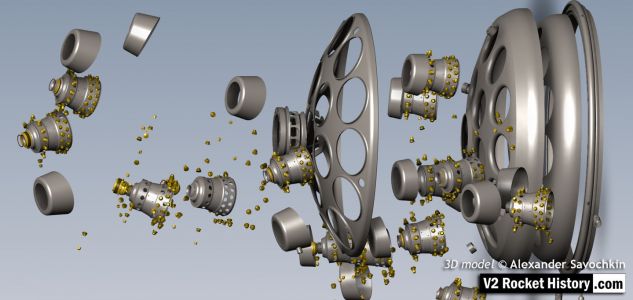
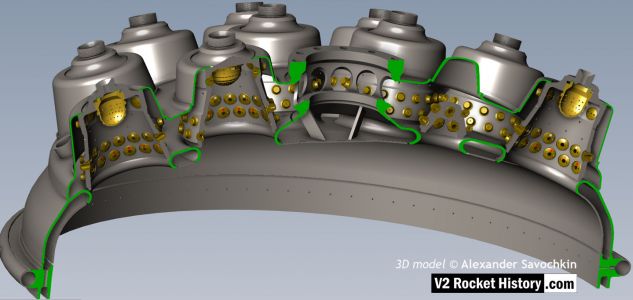
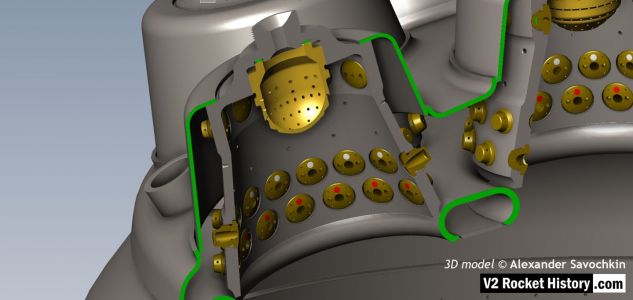

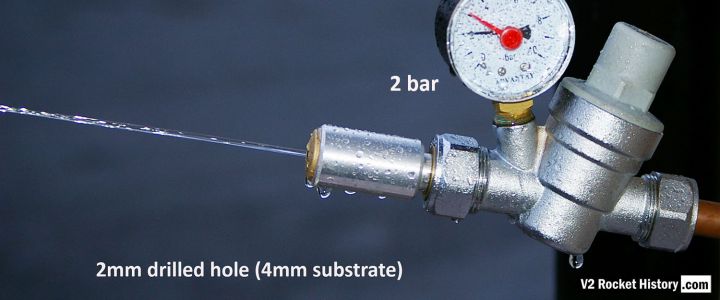

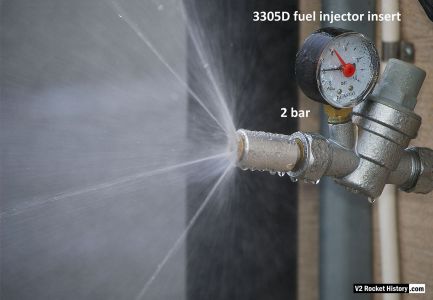
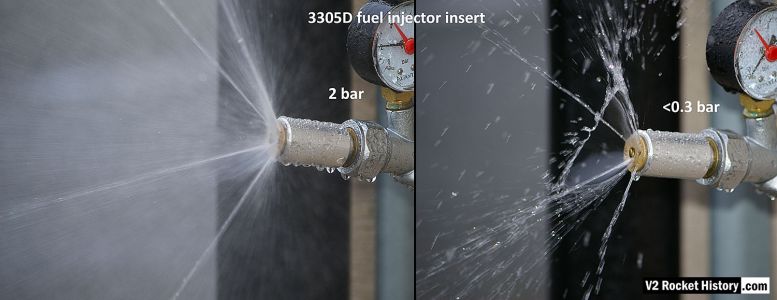
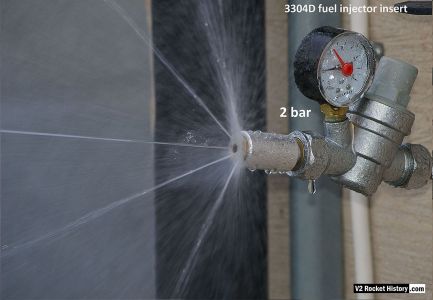
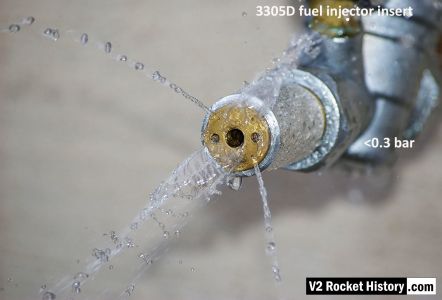
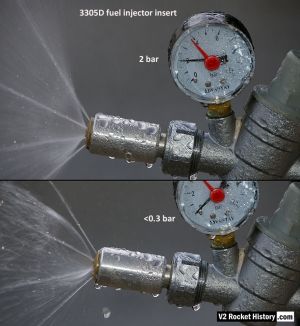
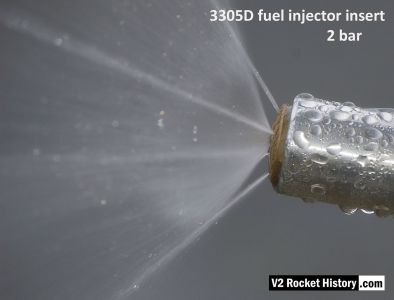
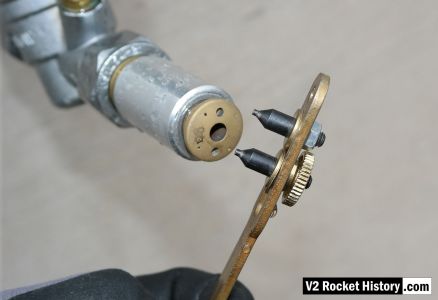
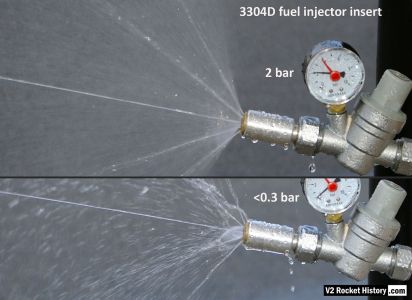
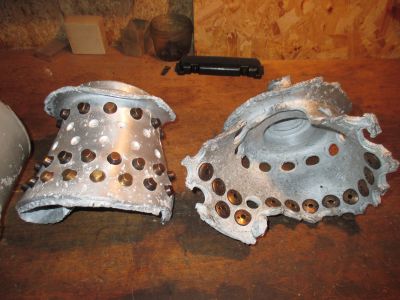

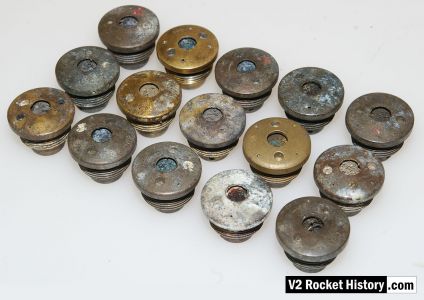


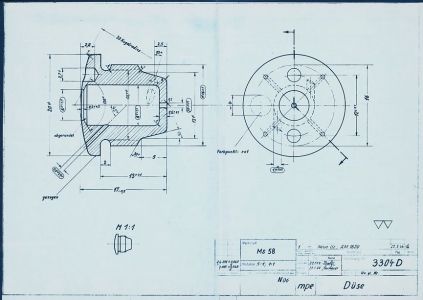
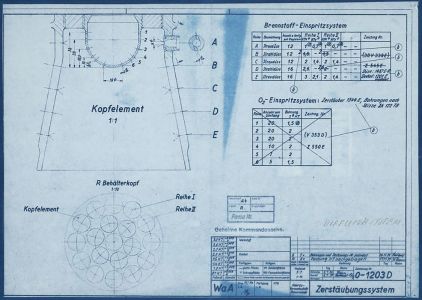
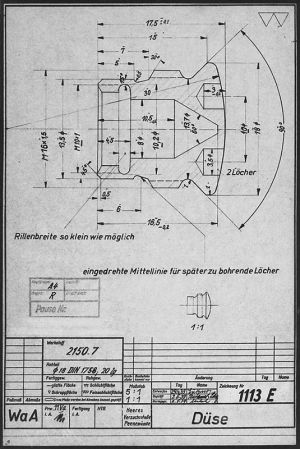

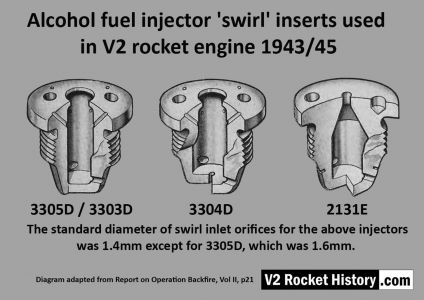
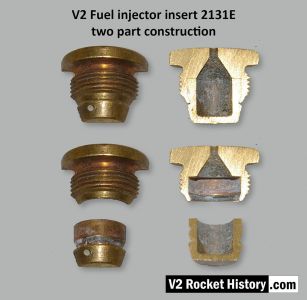

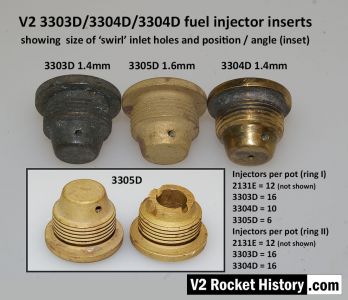
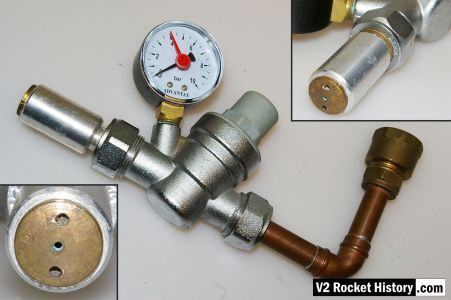
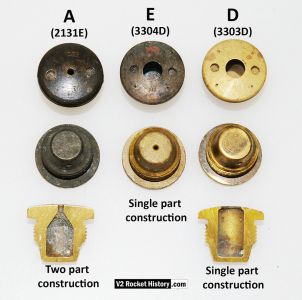
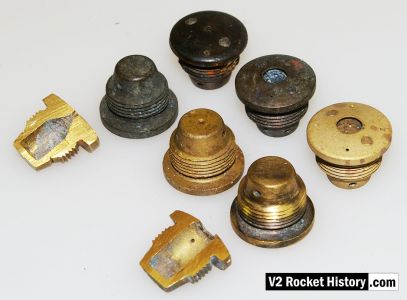
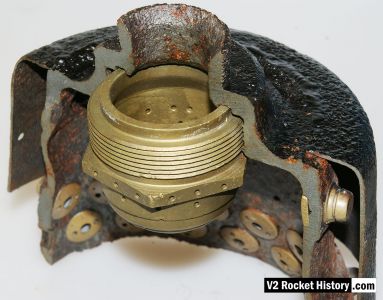
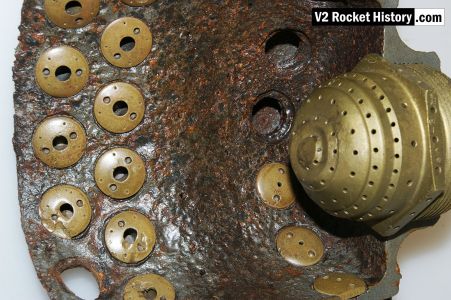
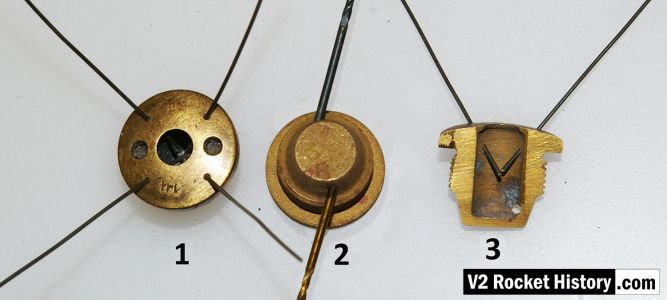
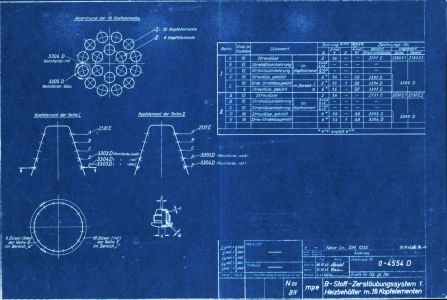
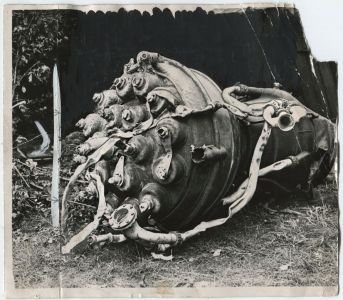
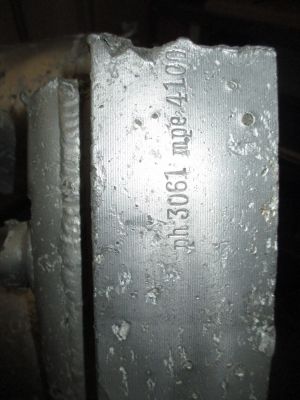
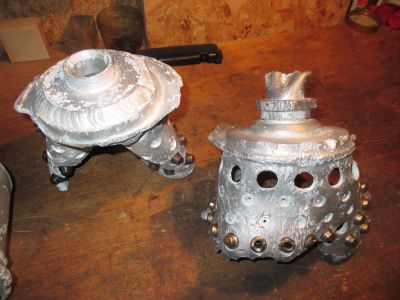
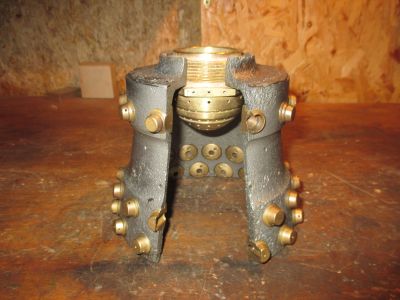
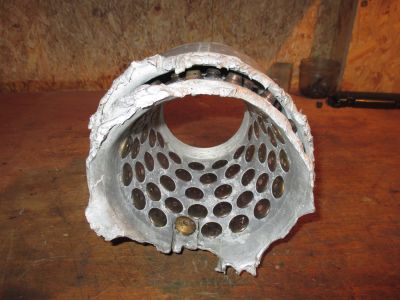
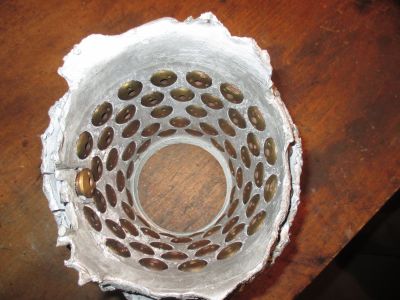
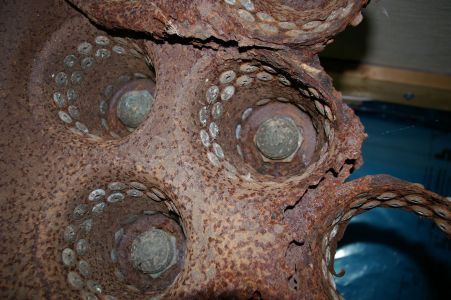
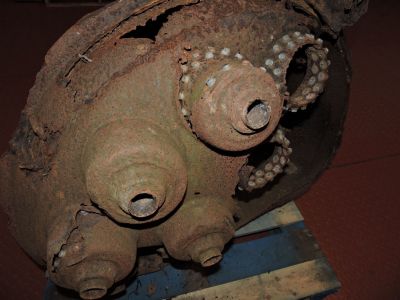
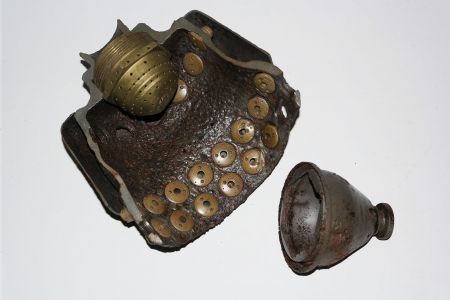
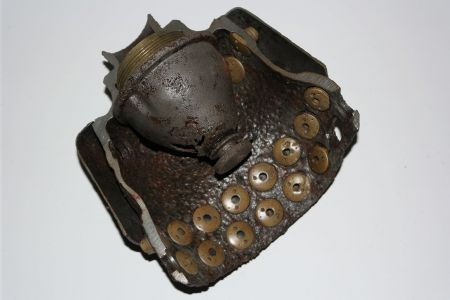
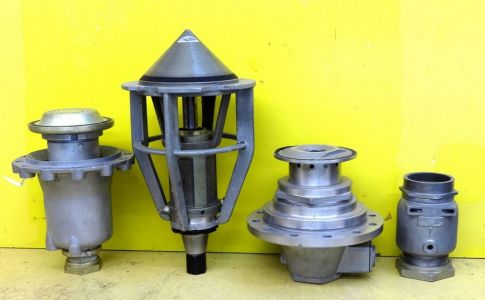
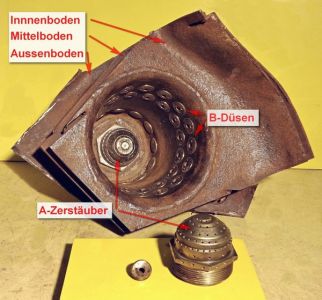
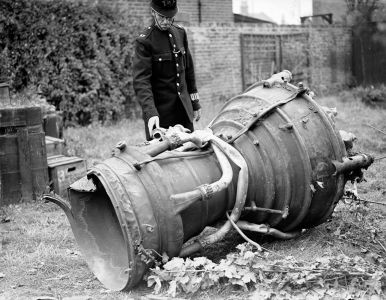
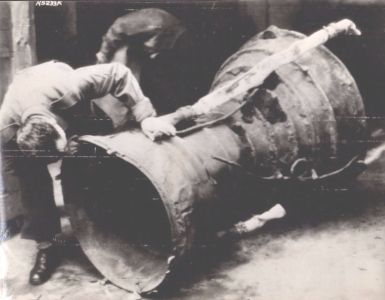
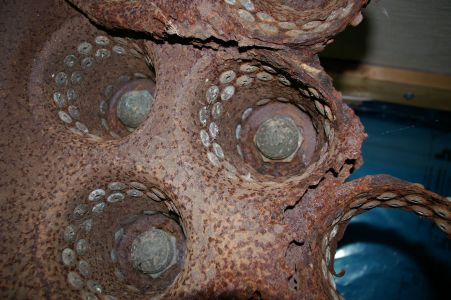
Brass liquid oxygen (LOX) spray nozzle.Note: the thread is shown in simplified graphic form. 3D model by Alexander Savochkin