
Archives: Gmedia Albums


Turbopump 3D CAD
3D CAD model images of the A4/V2 rocket engine’s steam turbine powered propellent pumps – all images by Ray Matter. To see Ray Matter’s blog 3D CAD modelling the V2 rocket turbopump introducing these images, just click the link.

Sectioned general assembly view of the V2 turbo-pump (TP) dated September 1942. This image has been edited to show TP and document data closer together than the original.
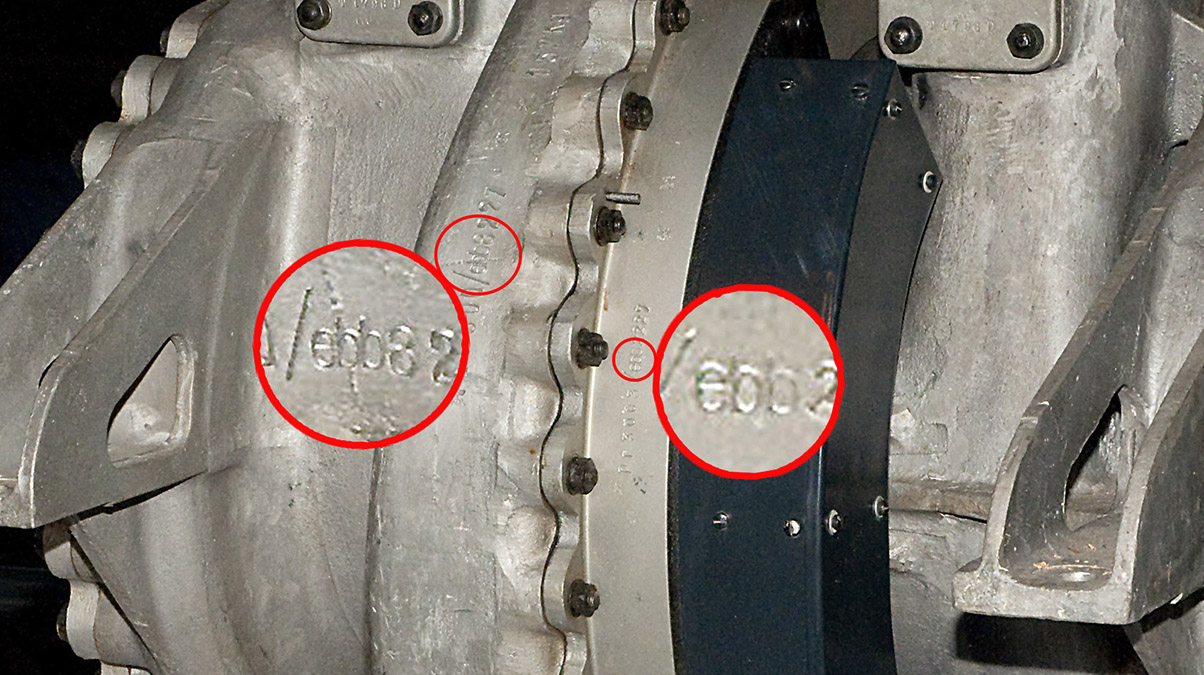
A complete V2 rocket turbo-pump on public display in the USA at the Smithsonian National Air and Space Museum in Washington DC showing Klein Schanzlin & Becker’s wartime contractor armament code – ebb. Smithsonian National Air and Space Museum exhibit.
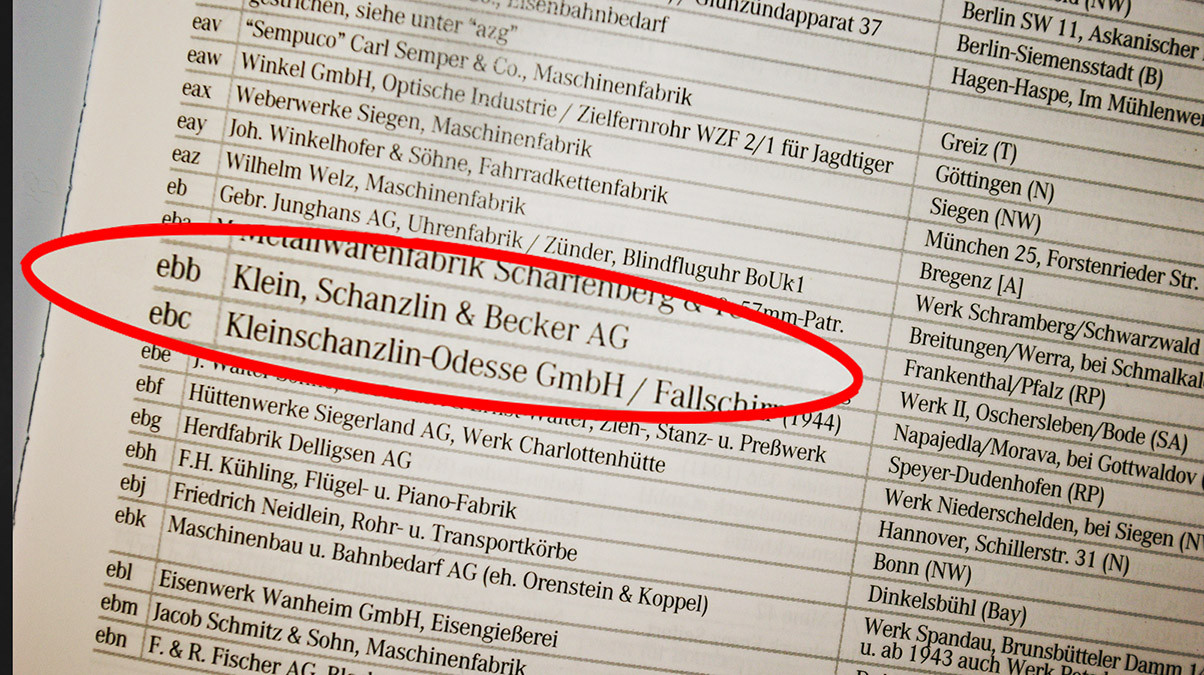
Page from the book, German Secret Armament Codes until 1945 by Michael Heidle (Visier Edition 2016) showing Klein Schanzlin & Becker’s wartime contractor armament code – ebb and Klein Schanzlin Odesse as ebc. ISBN: 978-3-944196-18-3
Album | Turbopump parts and relics |
Category | Turbo-pump |
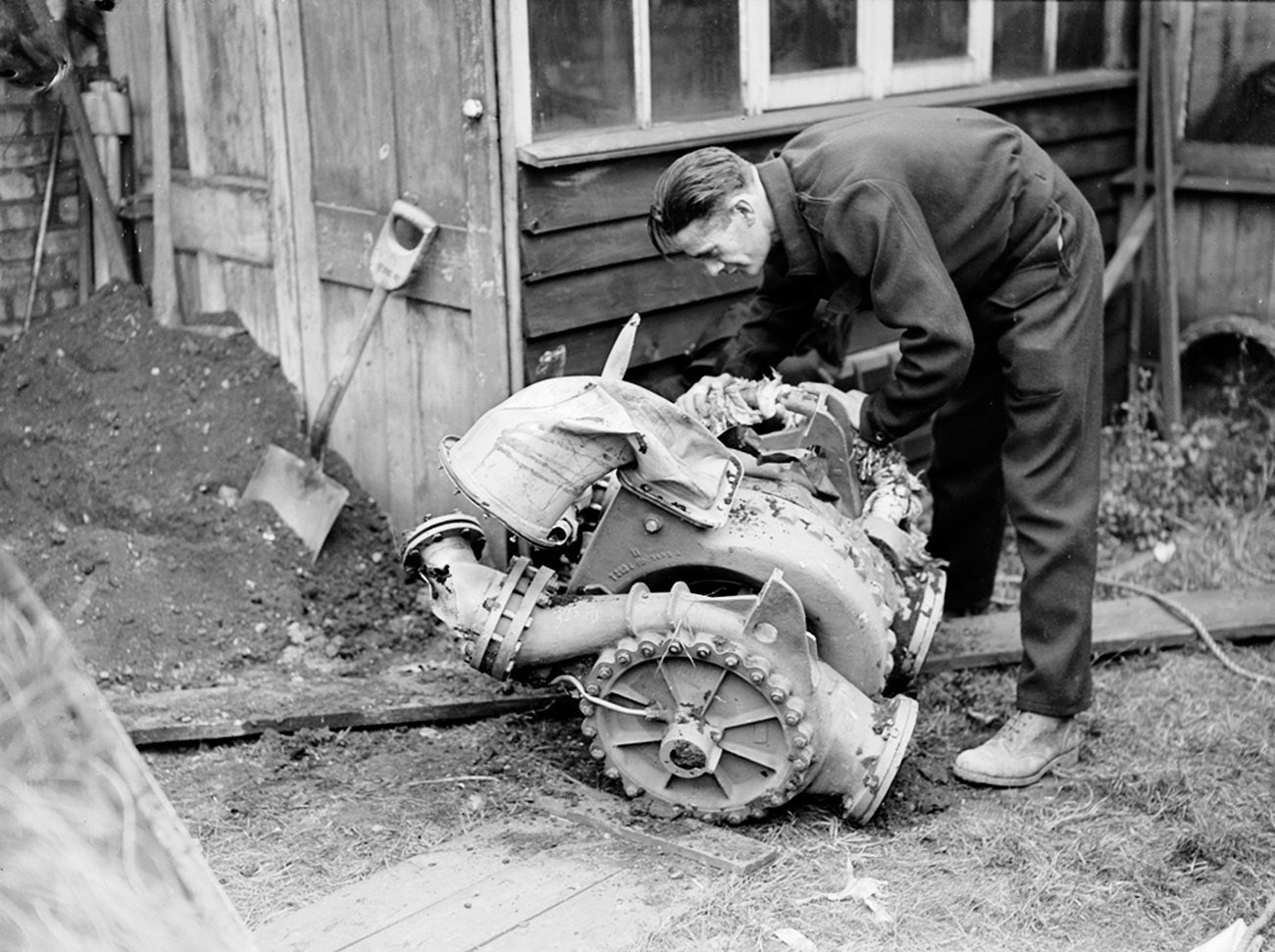
V2 rocket turbo-pump from a missile fired from Walcheren, Serooskerke, Vrederust, by battery no 444, at around 7am on September 17th 1944. The missile impacted East Ham with a direct hit on houses. Killing 6 people with 15 seriously injured. Much of the rocket debris was taken to the East Ham police station for examination by the military authorities. The serviceman in the picture is feeling the steam inlet manifold as it is still warm to the touch. Information porovided by www.v2rocket.com.
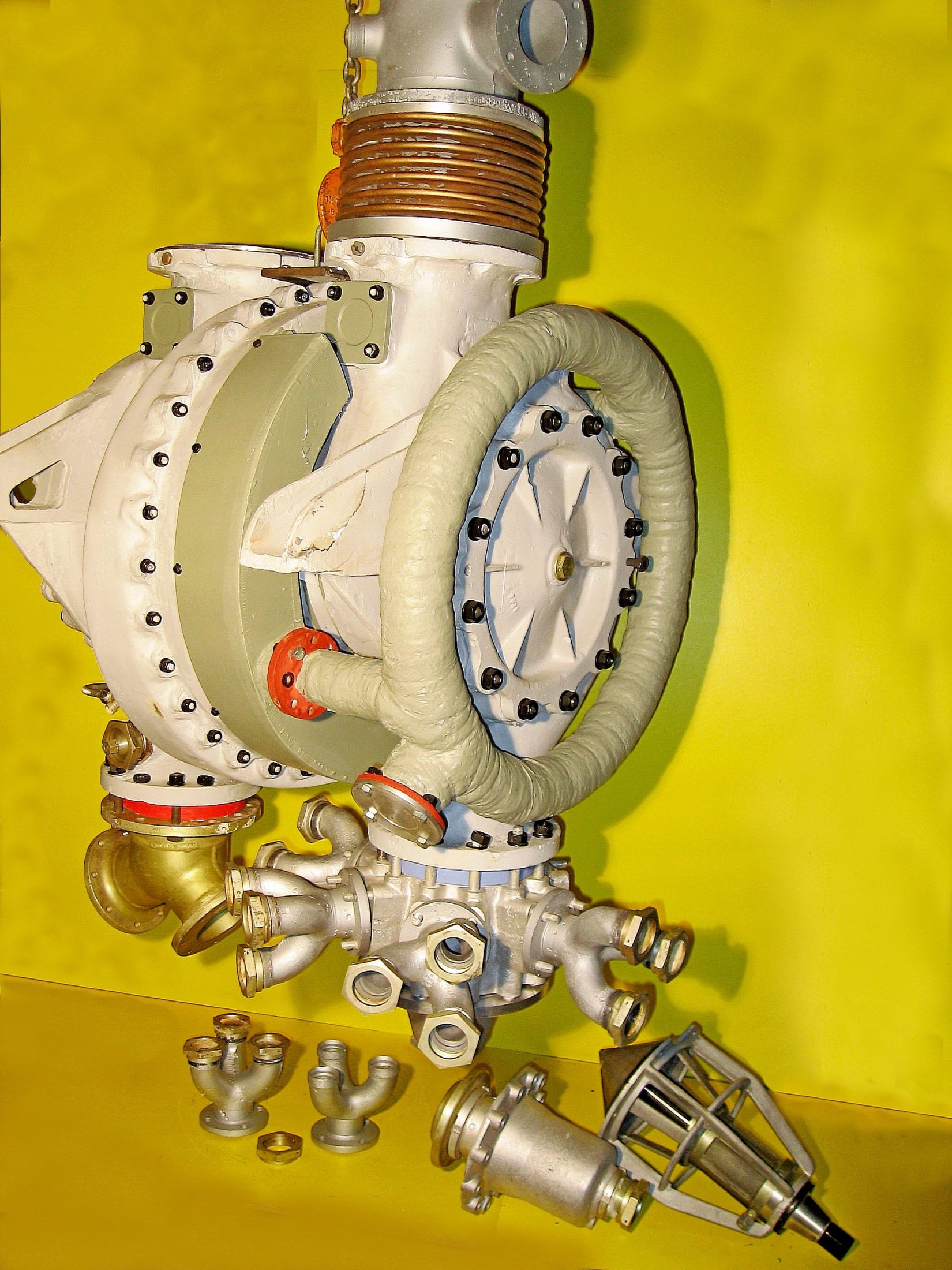
A4-V2 turbo-pump (TP) assembled from original unflown and refurbished flown parts by Horst Beck. Although this rebuilt TP is an accretion of parts from various origins and eras (from 1943 to 1945) the main cast parts of the TP, the turbine housing, and pump cases, were manufactured no earlier than December 1944.
The TP is orientated so that the LOX pump is to the right and the lagged steam inlet and distribution manifold is well shown, running around the circumference of the LOX pump face plate.
The manifold flange, that connects to the output of the steam generation plant, is shown capped off. One of the two TP steam inlet points can be seen above and to the left of this flange. The other inlet pipe can just be seen 180 degrees away on the other side of the manifold.
It is worth noting that he TP presented here is marked ebb (ebb = KSB) in various locations, if any demonstration was needed that KSB was still a primary supply contractor for this critical component in December 1944. See next image in this sequence for an explanation of the blue and red spacers that can be seen where the TP outlet flanges connect to the fuel and liquid oxygen (LOX) outlet splitters. Image courtesy Horst Beck Collection
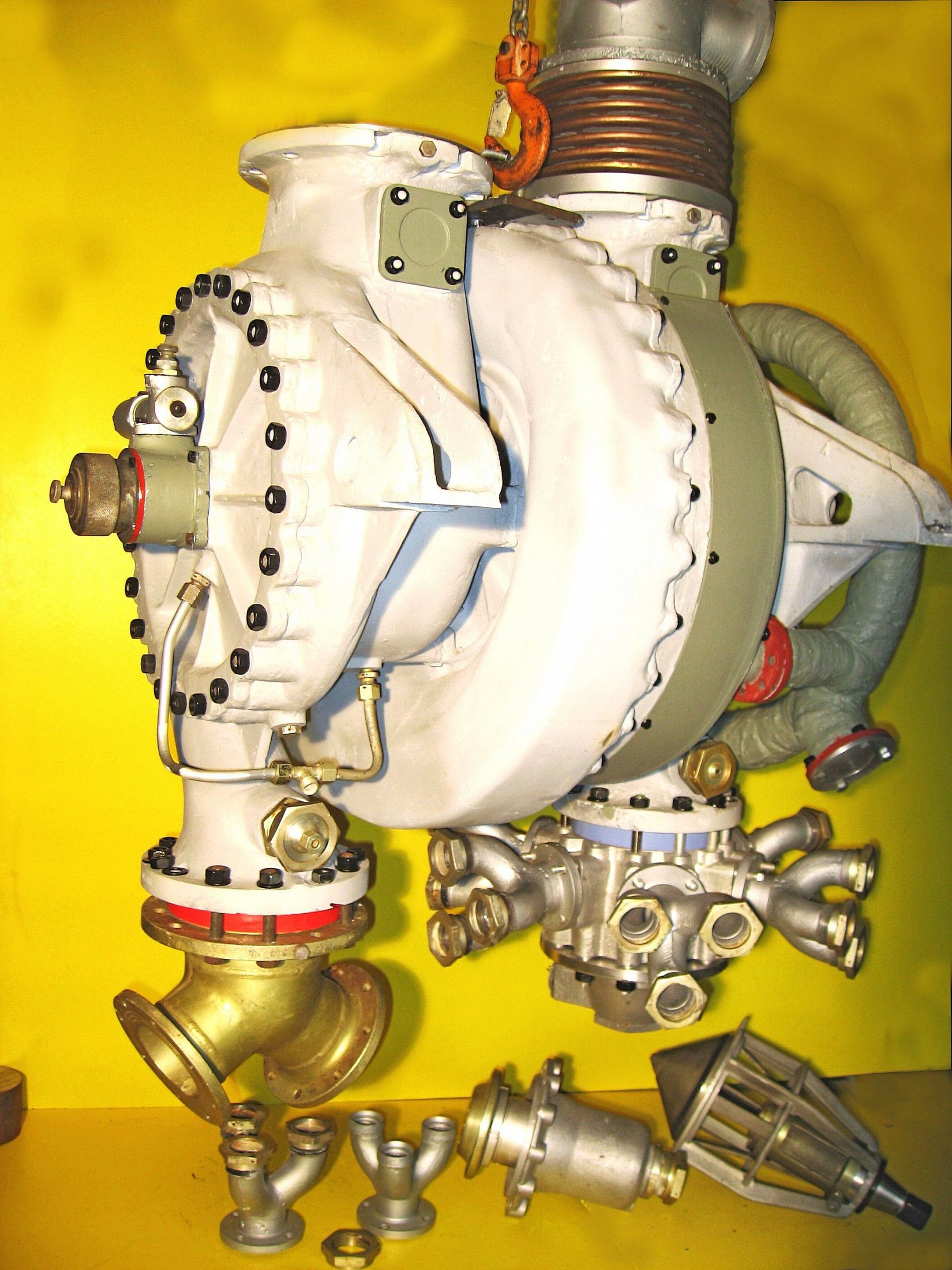
A4-V2 turbo-pump (TP) assembled from original and refurbished parts by Horst Beck. See previous image in this album for more details of TP.
The pale blue spacer that can be seen inserted between the lower LOX outlet flange (on the right of the TP) and the red spacer located in a similar position on the fuel outlet side (left) are critical adaptions to standardise the propellant flow on the basis of test runs performed on each TP. The red and blue spacers are chokes (essentially large washers) that were sized according to the needs of each individual pump. One or sometimes both spacer/washers would have a reduced holes to choke the flow volume to the correct rating relative to the other pump and the overall specifications.
The small pipe network, shown linking the underside of the fuel inlet case, with the bottom of the fuel pump (FP) case and the bearing area of the FP face plate, was used to allow a small continuous flow of propellant pass to the bearings as lubricant – the surplus was dumped overboard via the unconnected union in the middle of the pipework (and nearest viewer). A similar propellant lubrication system was used on the LOX pump – critically LOX can not be allowed to come into contact with conventional organic lubricants as there is a risk of an explosion. So using the material being pumped as the bearing lubricant is a good solution to this problem. Image courtesy Horst Beck Collection
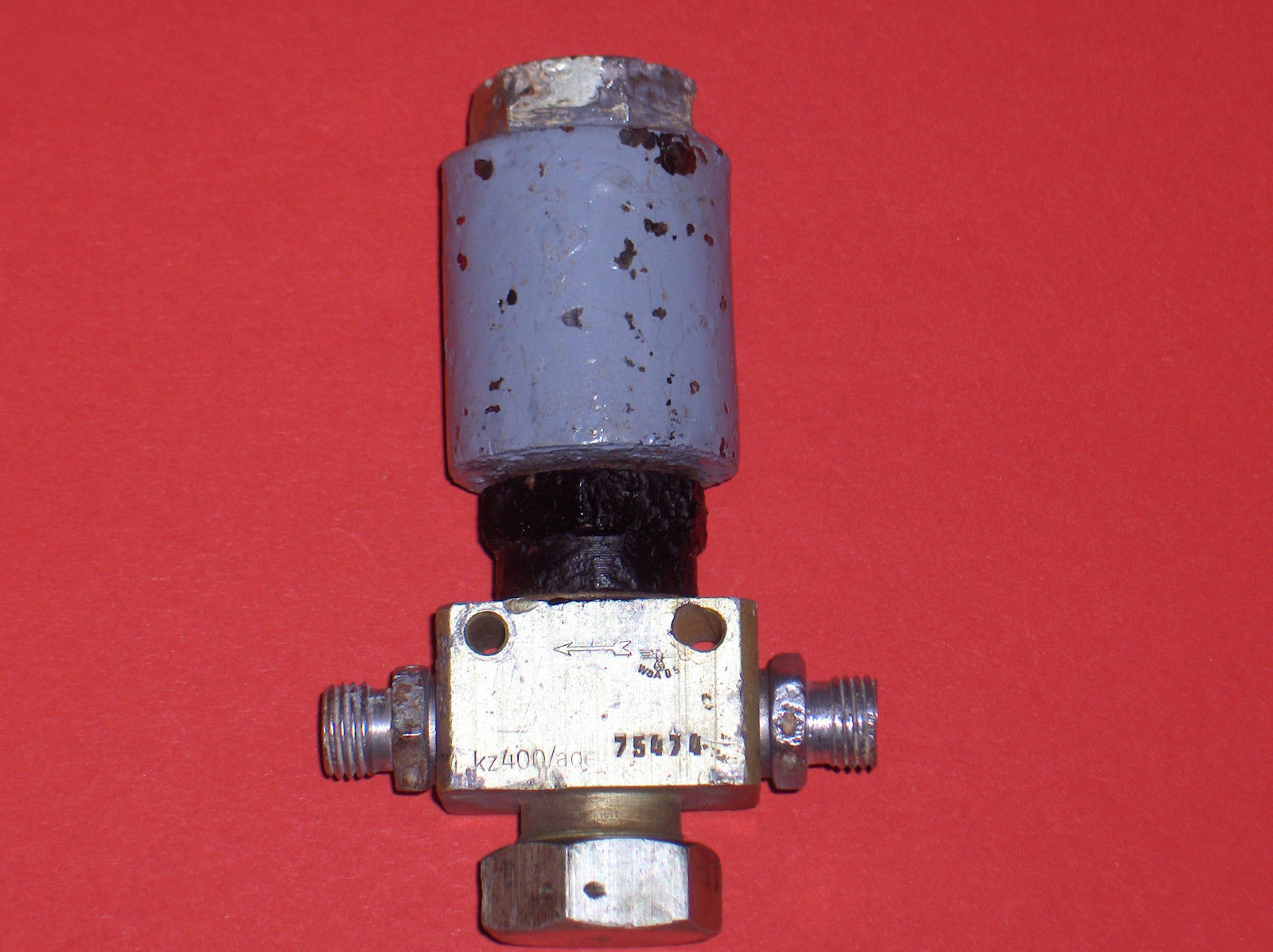
Solenoid electro-magnetic air valve. The This valve type is used numerous times to control equipment in the V2 missile. Variations of this electrically activated valve can be used to control high pressure air or fluids.
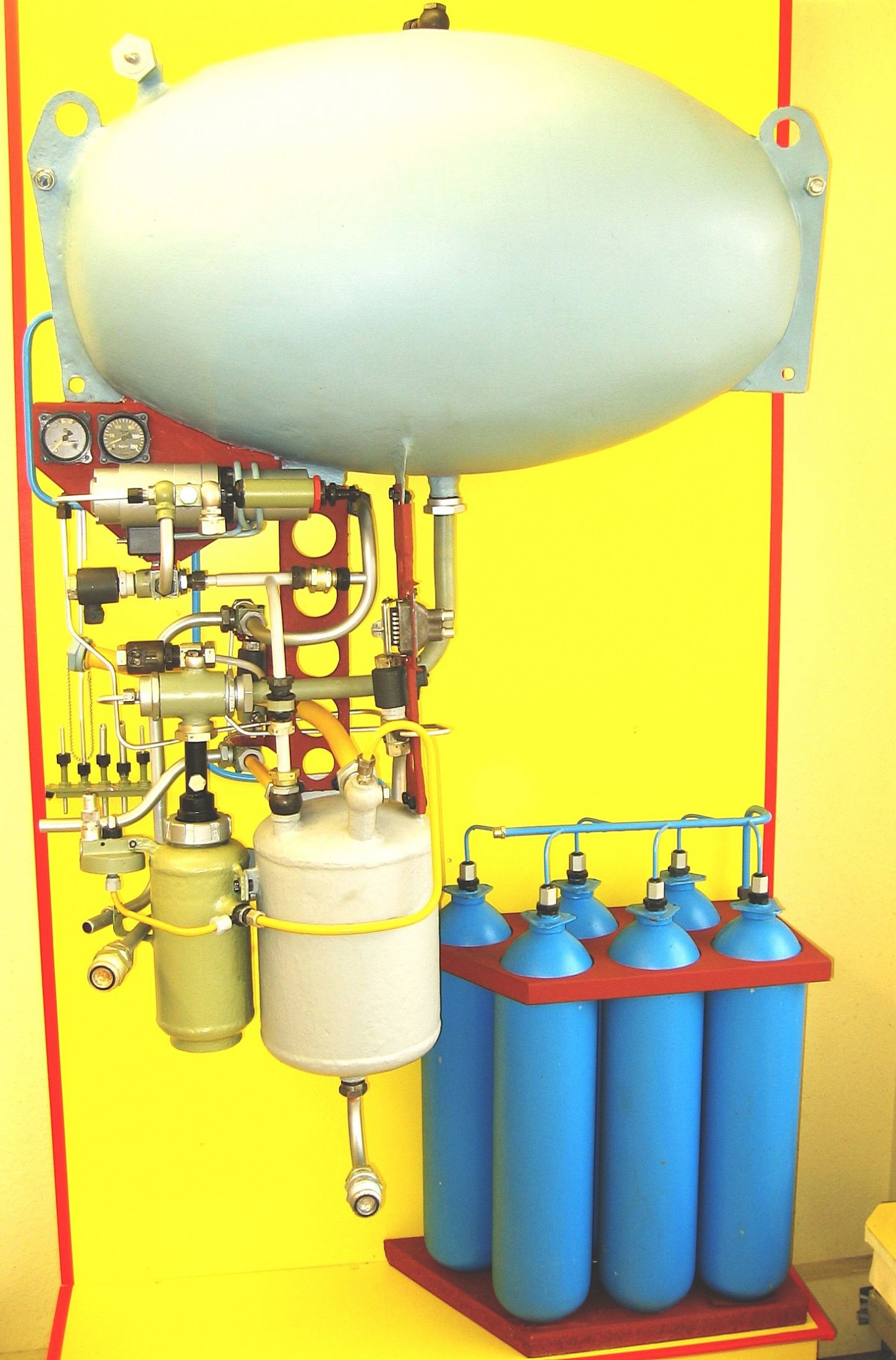
This photo shows an excellent presentation of the gas (steam) generation plant assembled from carefully refurbished flown and unflown V2 missile parts by Horst Beck.
The display shows the large elliptical H2O2 (80% test strength hydrogen peroxide) tank at the top of the assembly and the smaller sodium permangenate reservoir below. The smaller cylinder to the left of the sodium permanganate tank is the steam generation chamber sometimes referred to as ‘the disintegrator’. The rack of blue painted cylinders, that look and function just like ‘scuba’ tanks, are part of the V2’s on-board nitrogen gas (air) reservoir employed to power the missile’s various pneumatic control valves. A second nitrogen reservoir was held in the equipment bay near the top of the missile. Image courtesy Horst Beck Collection
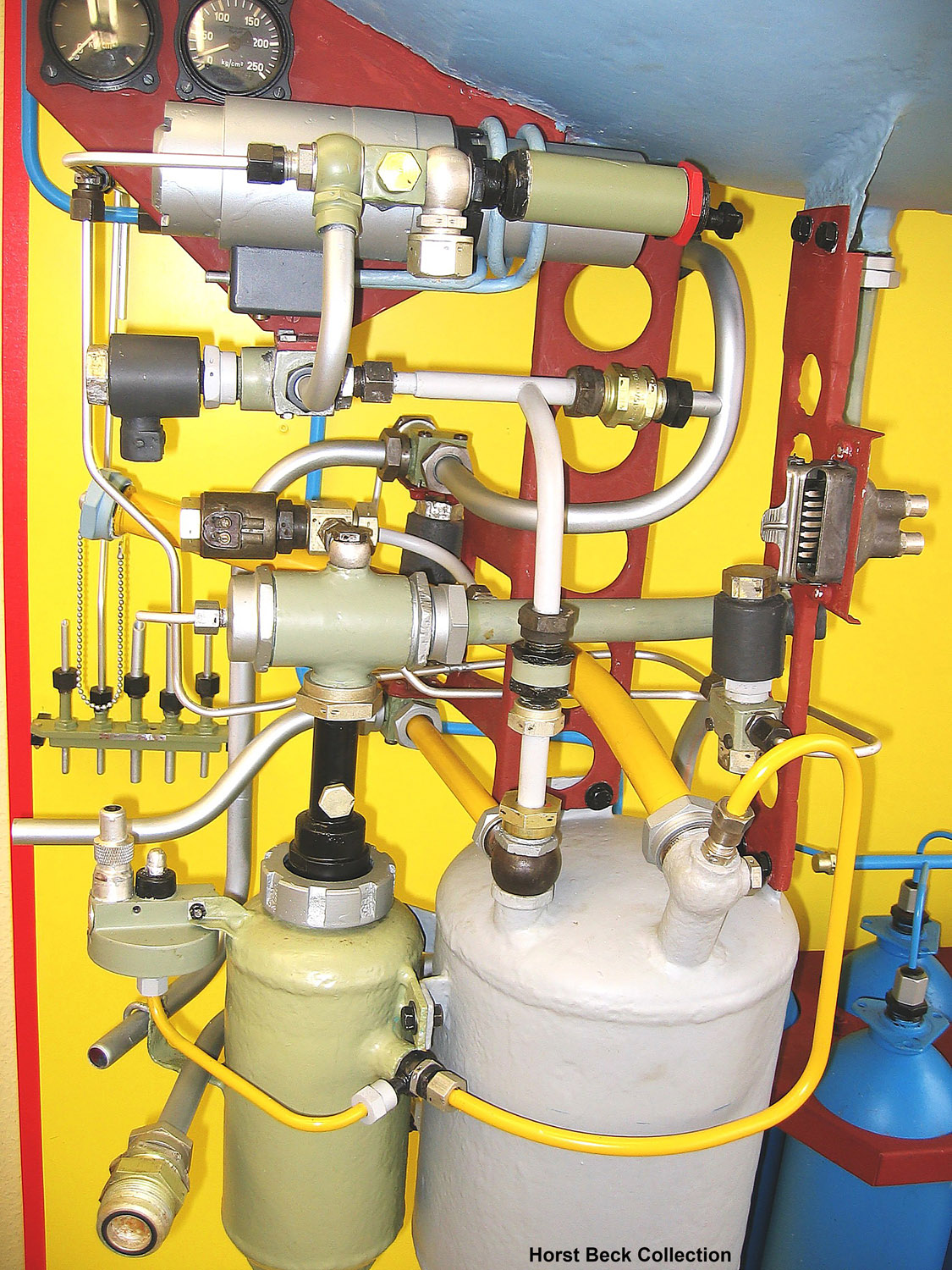
A4 missile steam generator detail. This excellent presentation was rebuilt from original refurbished parts by Horst Beck. See our video article The V2 Rocket Turbo-Pump for a technical exposition of the parts shown in this photo. Image courtesy The Horst Beck Collection
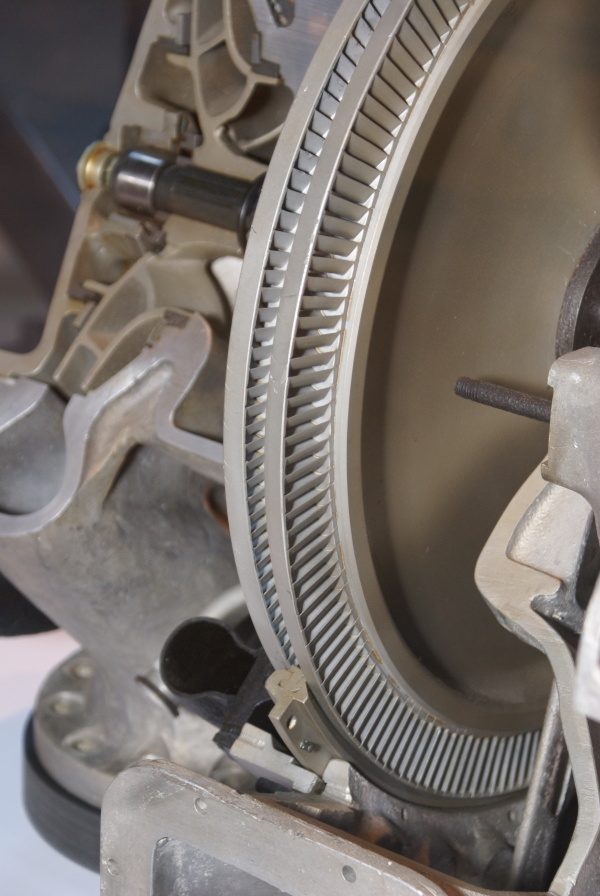
This image shows a cutaway of an A4-V2 turbo-pump. The section reveals the Curtis type 2-stage steam-turbine rotor and you can also see part of the stater inserted between the blades (bottom middle) and the adjacent steam distribution pipe (black open pipe on stater’s immediate left). Top left, a centrifugal pump rotor can be seen – cut through, it shows a multi-splined shaft running through the centre, simple bearing and end-cap.
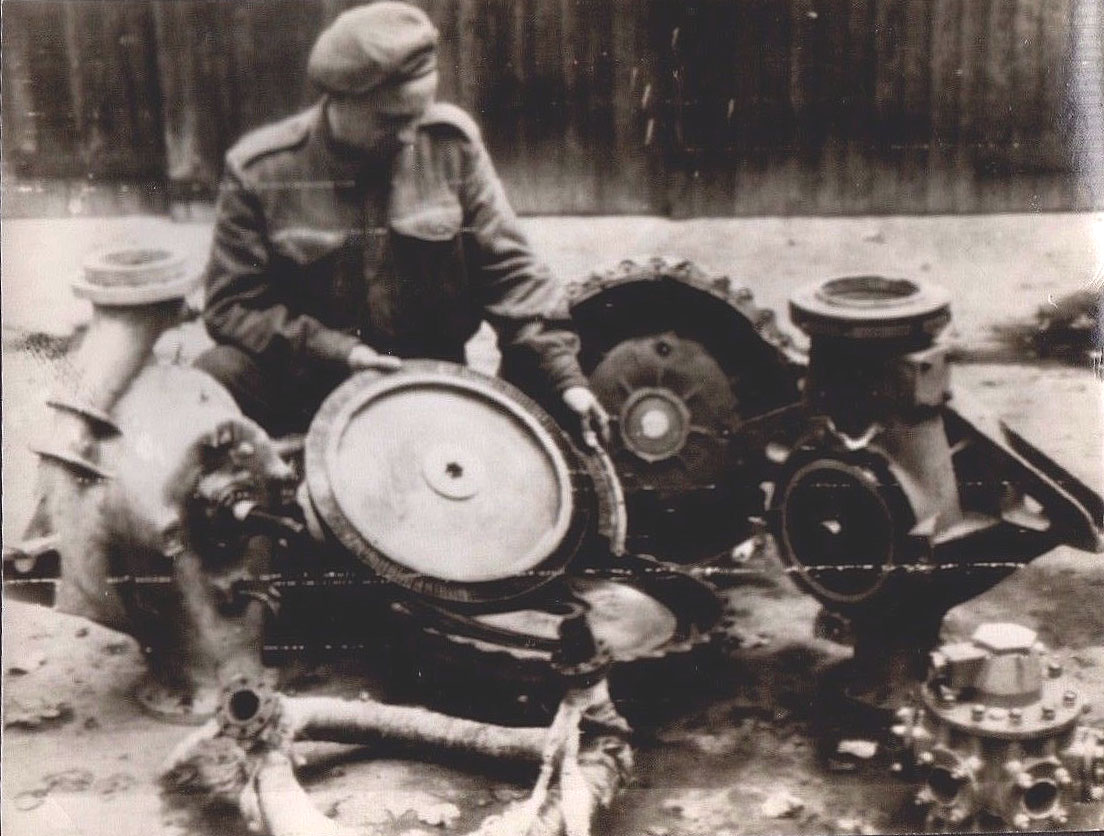
Image shows allied soldier examining remains of V2 rocket turbo-pump after impact. The soldier is holding the steam turbine rotor – the large size of this part is well shown in this photo. The still lagged steam inlet manifold can be seen in the left foreground and the LOX outlet manifold (and valve, topmost) can be seen in the lower right corner.
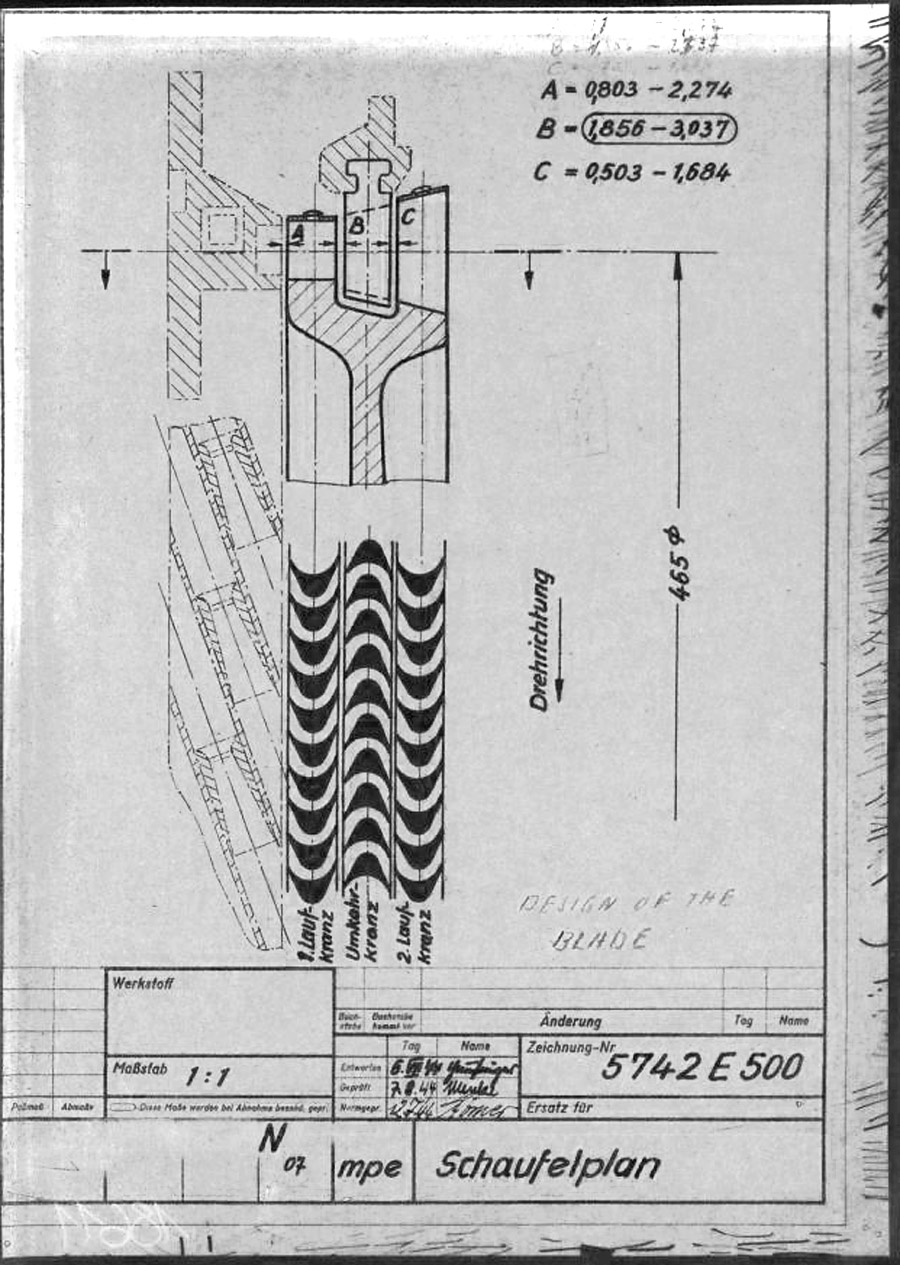
This mpe* drawing from 1945 shows the individual steam buckets or blades (labeled A and C) mounted to the rim of the rotor disk. As well as the fixed (i.e. stationary) stater blade B, positioned such that blades A & C can pass either side of it. The steam expansion is well shown by the increasing surface area of the blades from A to C, and growing larger, from left where the high pressure super heated steam enters the turbine, to right where it exits the blade pathway and passes in to the exhaust outlet. The lower graphic shows the way the super-heated high pressure steam is passed from the initial A blade and deflected by the reversed B stator blade for its energy to to be harvested for a second time by the C rotor blade. * mpe is the secret three letter armament code for Karlshagen, Werk Nord (North Works).
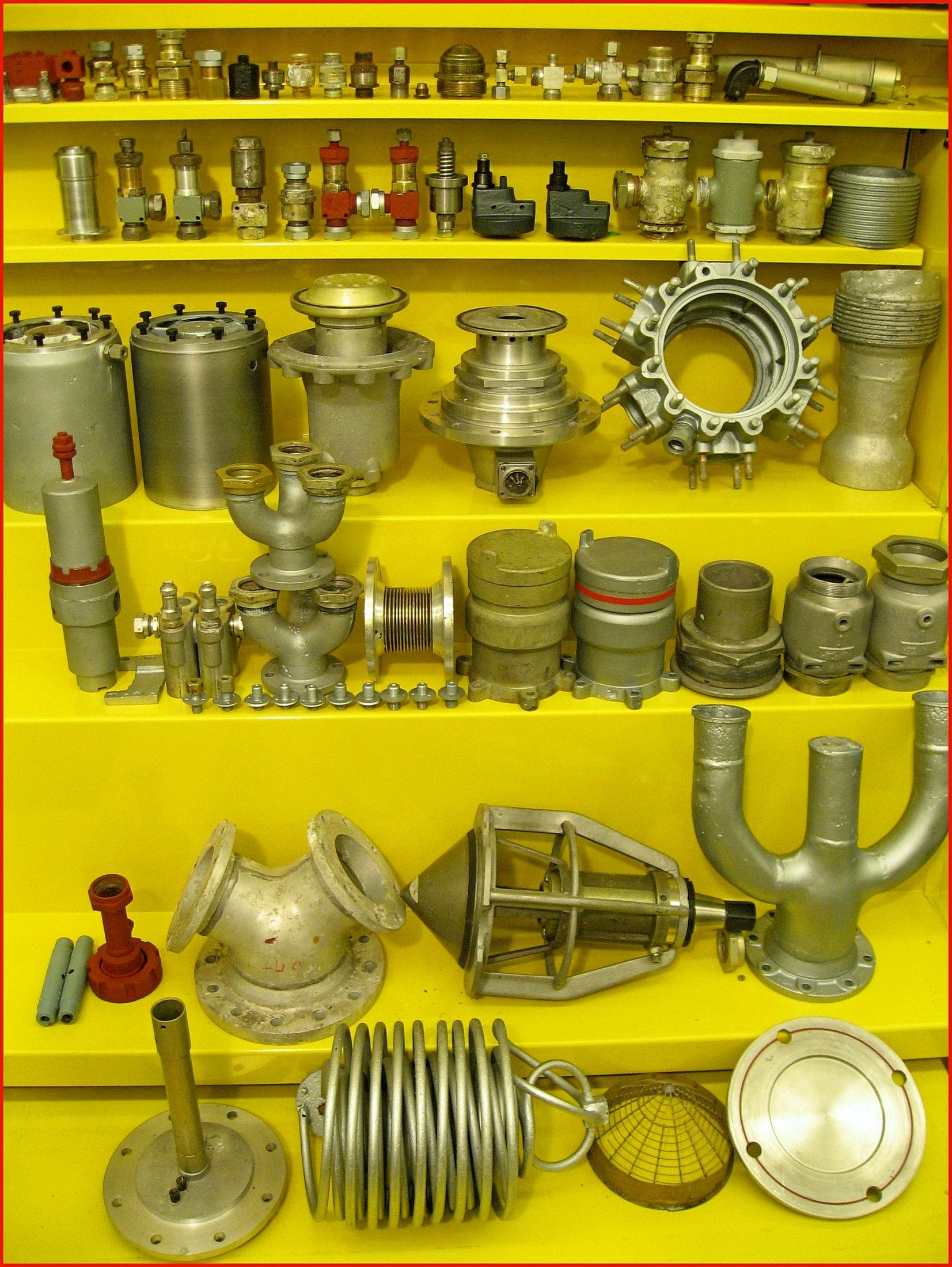
Looking rather like a a display in a V2 rocket shop window, this terrific display, centered on propellant supply parts, is part of the Horst Beck Collection and provides an unparalleled opportunity to view original A4-V2 missile components in a near-new condition and isolated from other equipment. Rare items include: a heat exchanger coil, for the volatilisation of LOX (2nd from left bottom shelf). An H²O² choke pipe and steam generator pot cap, (in red oxide paint, 2nd shelf up from bottom) Alcohol tank valve (2nd from right on the same shelf). Alcohol down-pipe 3-way splitter (1st item on right same shelf). LOX manifold 3 to 1 splitter (two with one resting on the other, 3rd shelf up on left). Two LOX main tank valves, (4th shelf up, first two item from left). Injector head main alcohol valve (same shelf, 3rd item from left). And on its right, a main Lox dual valve, and on its right LOX distribution body, minus valve. A ‘Preshona’ non-return valve can be seen (2nd shelf from top, 5th item from left). The two same shape black items (2nd shelf from top, middle) are two Sodium Permanganate diaphragm contact switches (Backfile code D2R). The next 3 items to the right of these are all H²O² 25ton valves. The large brass item in the middle of the top shelf is a LOX spray cap. Image courtesy Horst Beck Collection
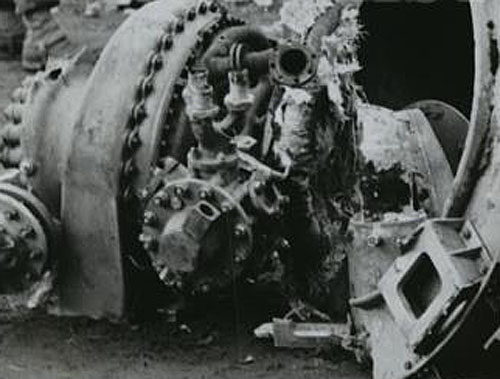
Picture shows tubo-pump debris from impact site. LOX manifold clearly seen (3 in 1 outlet pipes, upper center of image – the one to its right, 2 o’clock position, and left, 11 o’clock position are both broken off).The LOX flow electric control valve is also well displayed in this image (LOX valve head is slightly low and left of center, part nearest camera). The electrical connection to the LOX valve has broken away leaving its empty socket pointing upwards and to the right.
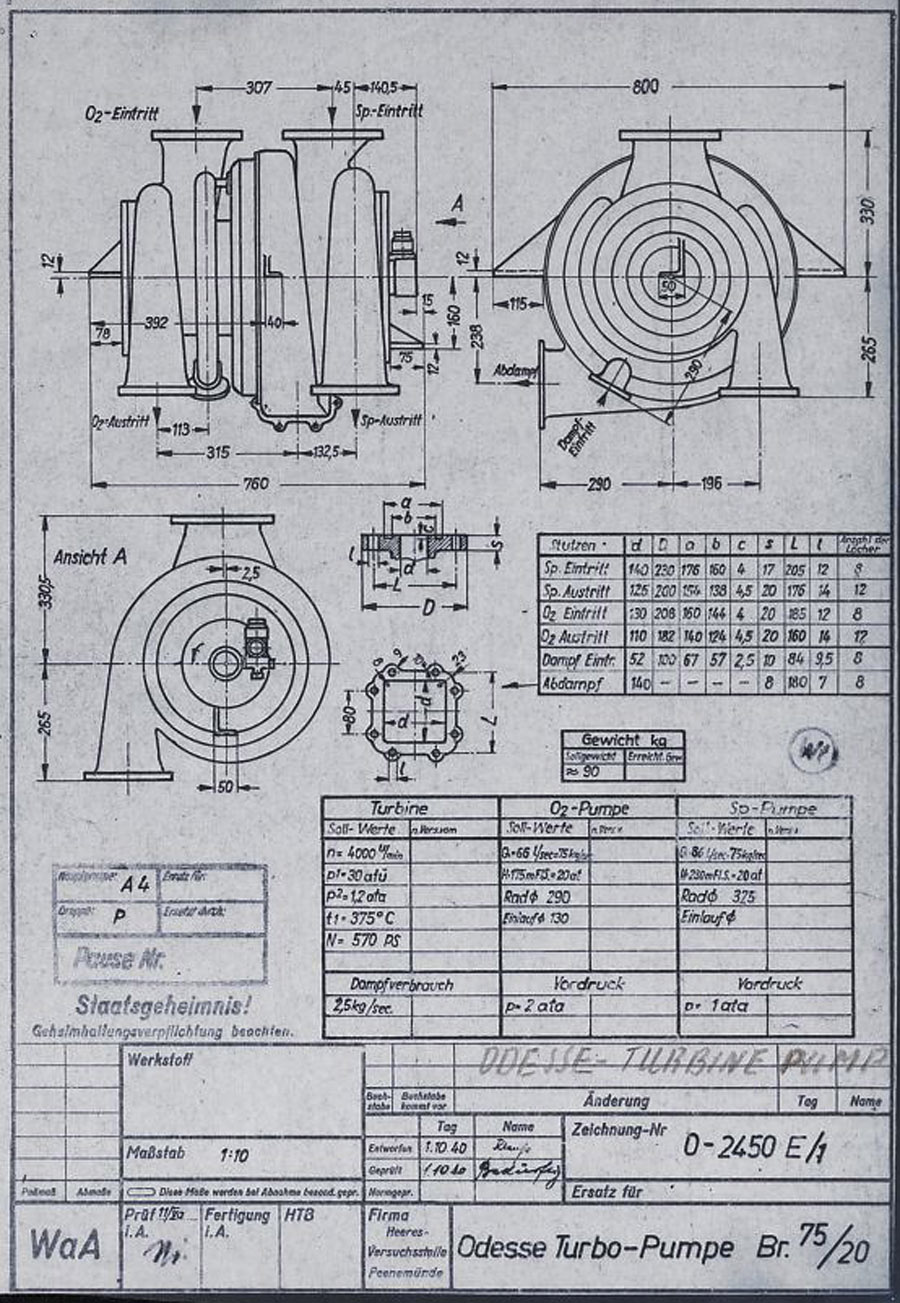
This HVP technical drawing from October 1940, shows a proposal from the Oddesse company – the full title of this company is KLEIN SCHANZLIN ODDESSE GmbH. Klein, Schanzlin & Becker A.G. (waffenamt code: ebb) took over Oddessa in 1929 and the company became formally known as KLEIN SCHANZLIN-ODDESSE GmbH (code ebc) in 1939. (NB: The company name has nothing to do with a similar sounding place name Odessa. The Oddesse trading name was formed from the partnership of English engineer Oddie, and German businessman Hesse.). The dual centrifugal turbo-pump shown in the drawing is a variant of a high pressure fire-fighting pump manufactured by Oddesse. Note the off-center outflow ports – not also that the outlet flanges are still level at this stage. Note also the incorrect spelling of the company name in the details panel lower right. (Digipeer.de image)
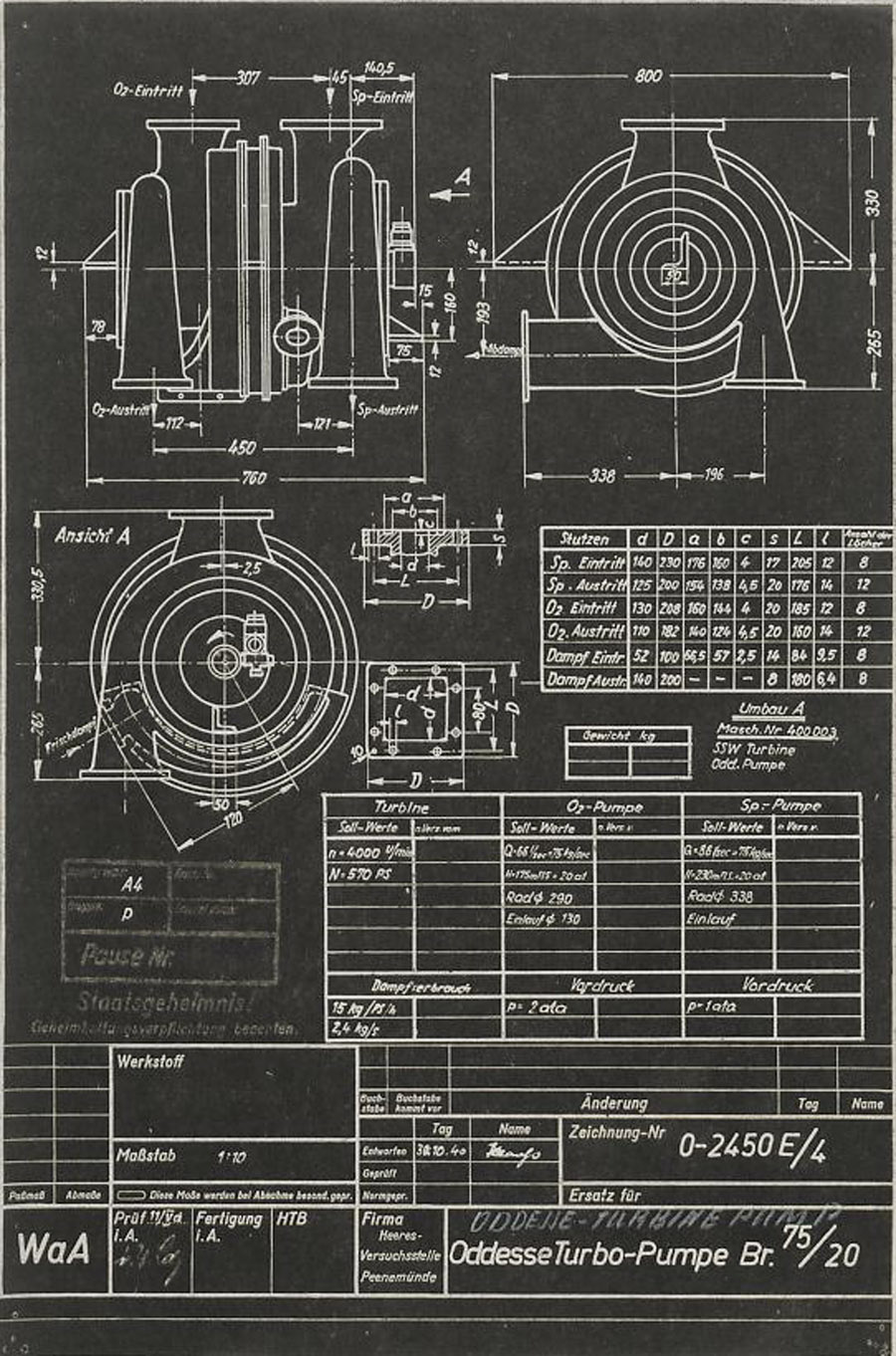
Another HVP technical drawing from later in October 1940, shows further data from the KLEIN SCHANZLIN ODDESSE (ebc) company A4-V2 turbo-pump project. See previous image for company details. The dual centrifugal turbo-pump shown in the drawing is a variant of a high pressure fire-fighting pump manufactured by Oddesse. Note the off-center outlet ports. Note also the corrected spelling of the company name in the details panel lower right (see previous Oddesse image) and the small note below the top table that indicates that the pumps are from Oddesse (ODD) and the turbine from a company indicated as SSW. (Digipeer.de image)

Signatur FA 014/21241 (Digipeer.de image)
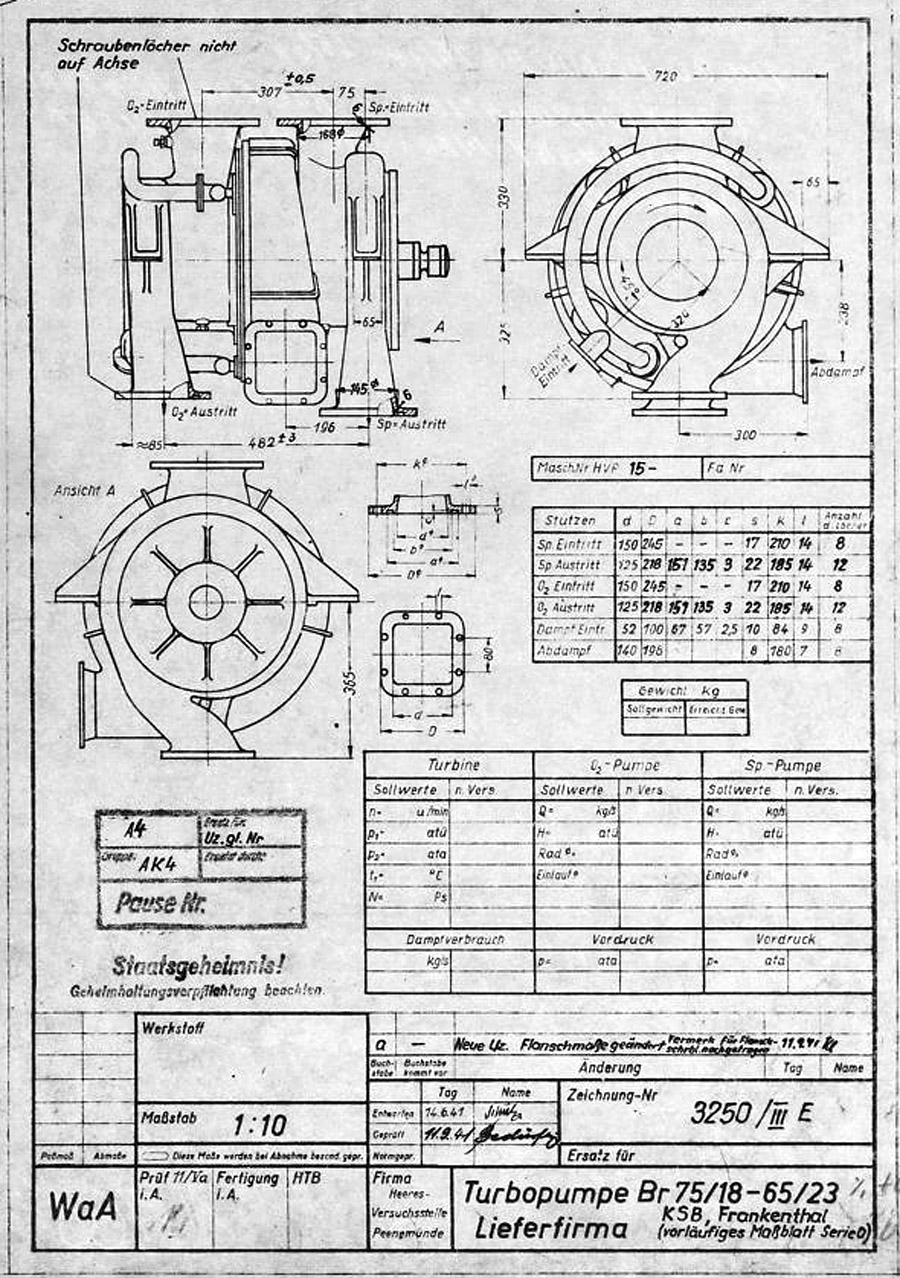
V2 rocket turbo-pump preliminary dimension sheet for O series, drawing. Many of the final elements of the turbo-pump design can be seen in this ‘preliminary’ drawing and table form 1941. The word lieferfirma in the data box btm right mean supply company – and this is indicated to be KSB or Klein Schanzlin & Becker AG, Frankenthal. Signatur FA 014/14769
(Digipeer.de image)
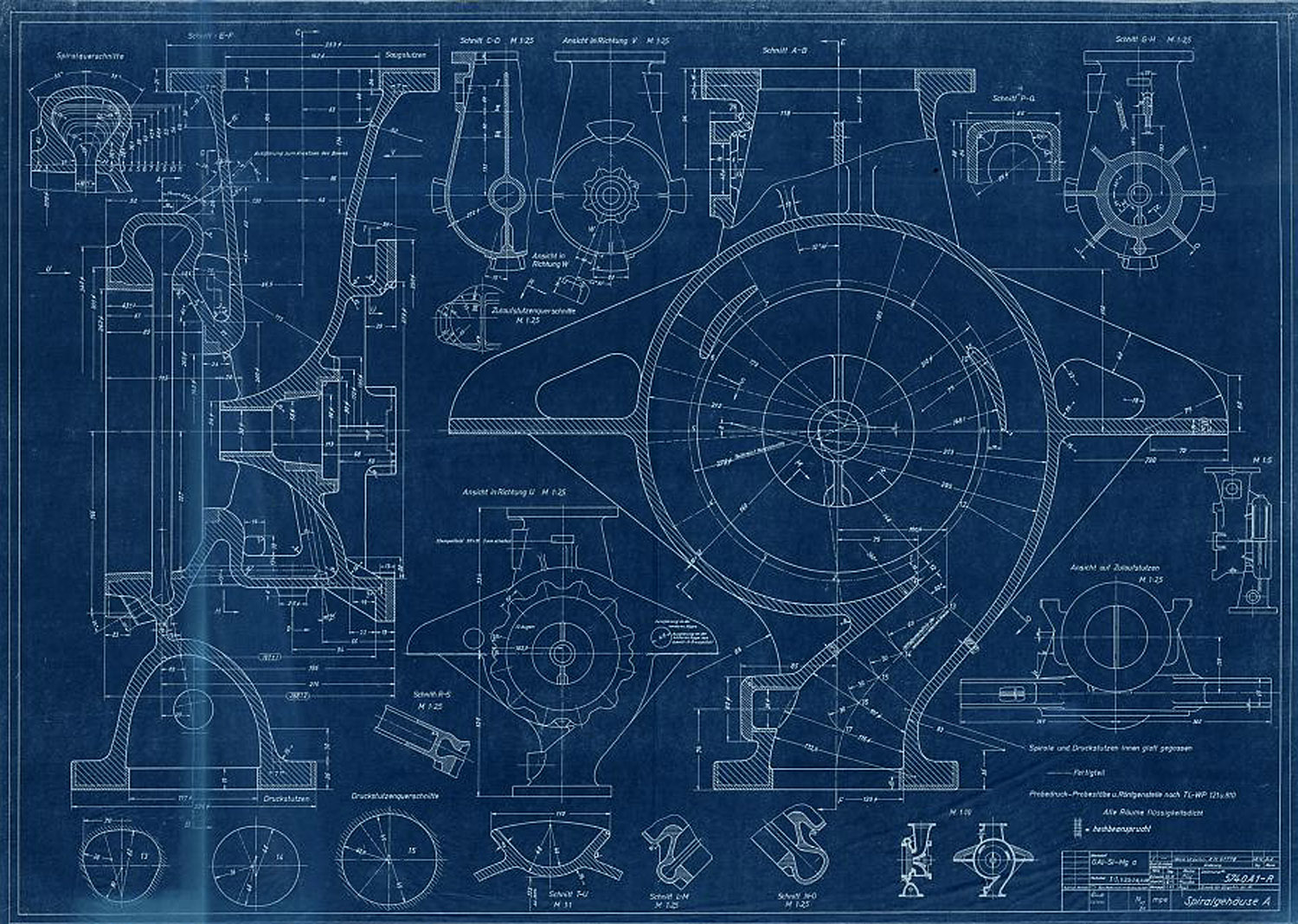
Signatur FA 014/02537
Abmessungen: 42,9×59,8
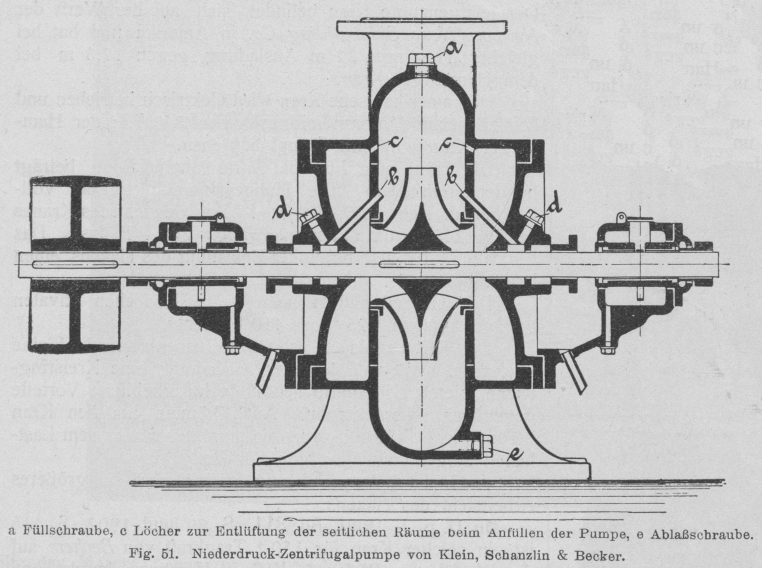
Early belt powered centrifugal pump by Klein Schanzlin & Becker. This schematic shows an early 20th century centrifugal pump designed and manufactured by KSB. The drawing appears to show auto-purge pathways at points marked C as well continuous lubrication pathways at B. Both of these important ideas would later feature in the propellant pump of the A4-V2 missile.
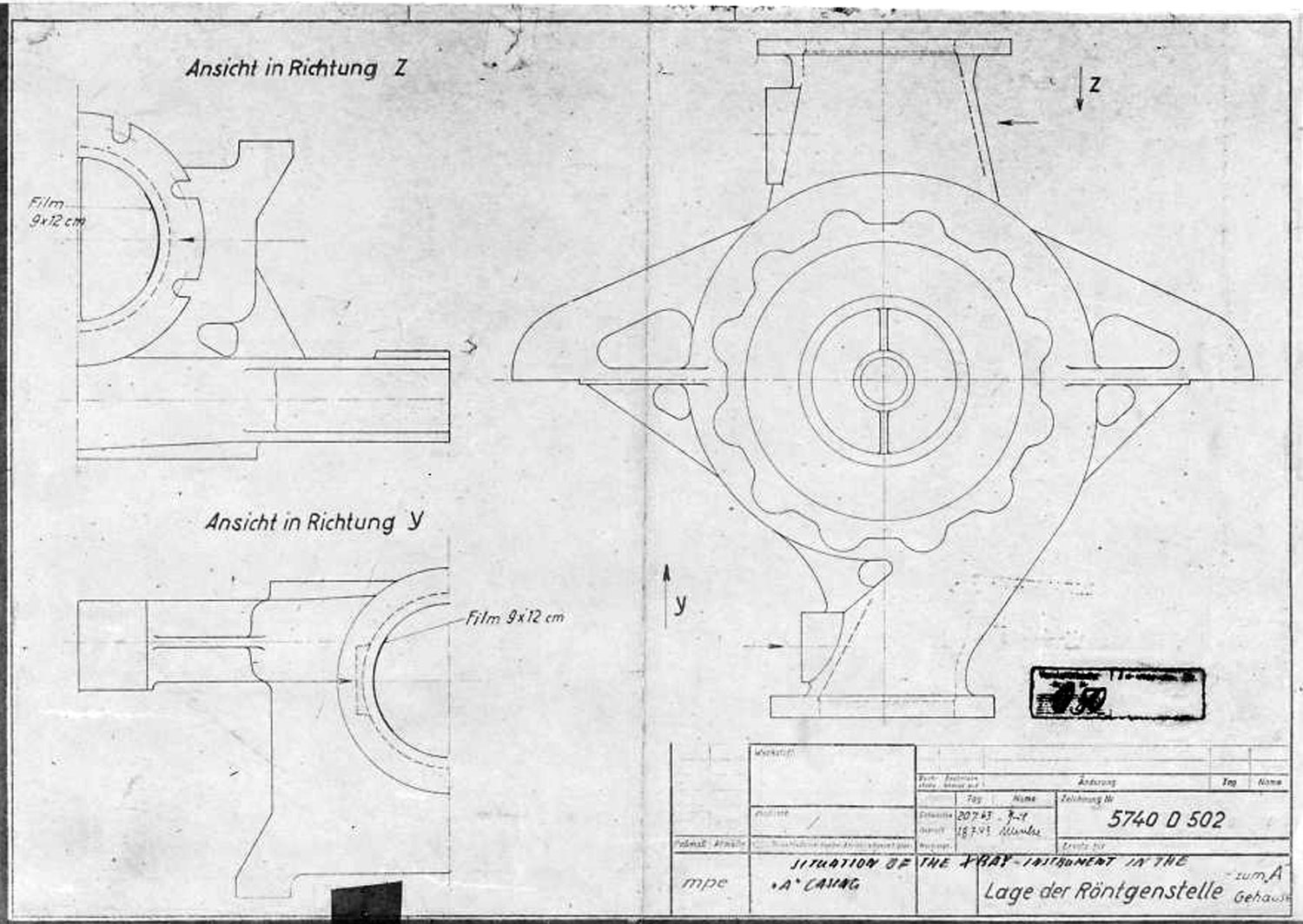
A Stoff (liquid oxygen) pump casing diagram showing stress points that require X ray quality control photography before use. The diagram shows the specific locations where photographic film is to be placed for X-ray analysis.
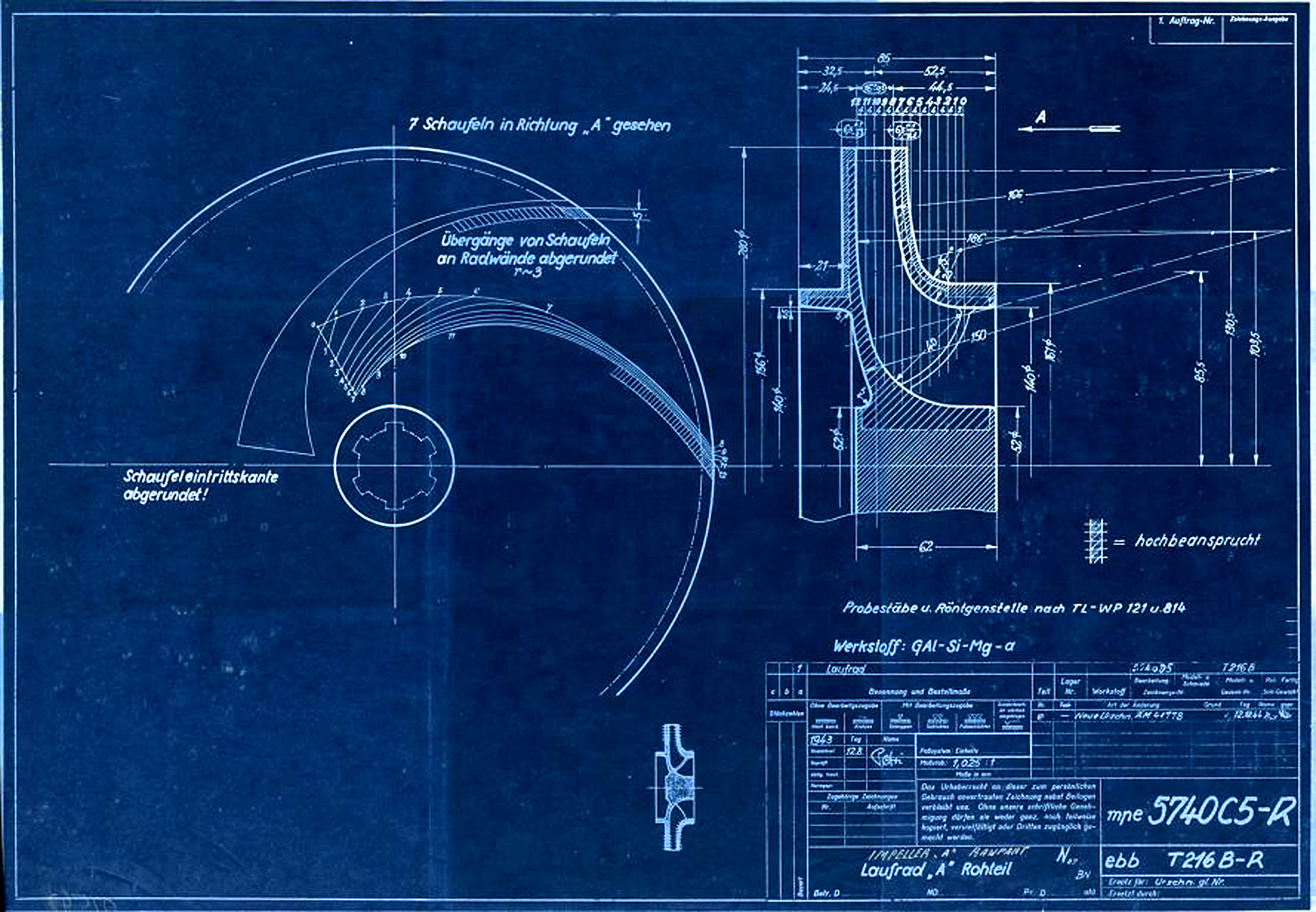
Centrifugal impeller for A or liquid oxygen (LOX) pump. The drawing originated in Aug 1943 and was superseded in December 1944. A key to the image hatching can be seen with the label ‘Hochbeansprucht’ which in English means Highly Stressed. Next to the drawing numbers two secret three letter armament codes can be seen indicating the ‘origination’ of the document. The top one mpe = Heimat Artillerie Park 11 (HAP or Army Artillery Range). The lower code ebb = Klein Schanzlin & Becker AG, Frankenthal.
Signatur FA 014/02542 (Digipeer.de image)
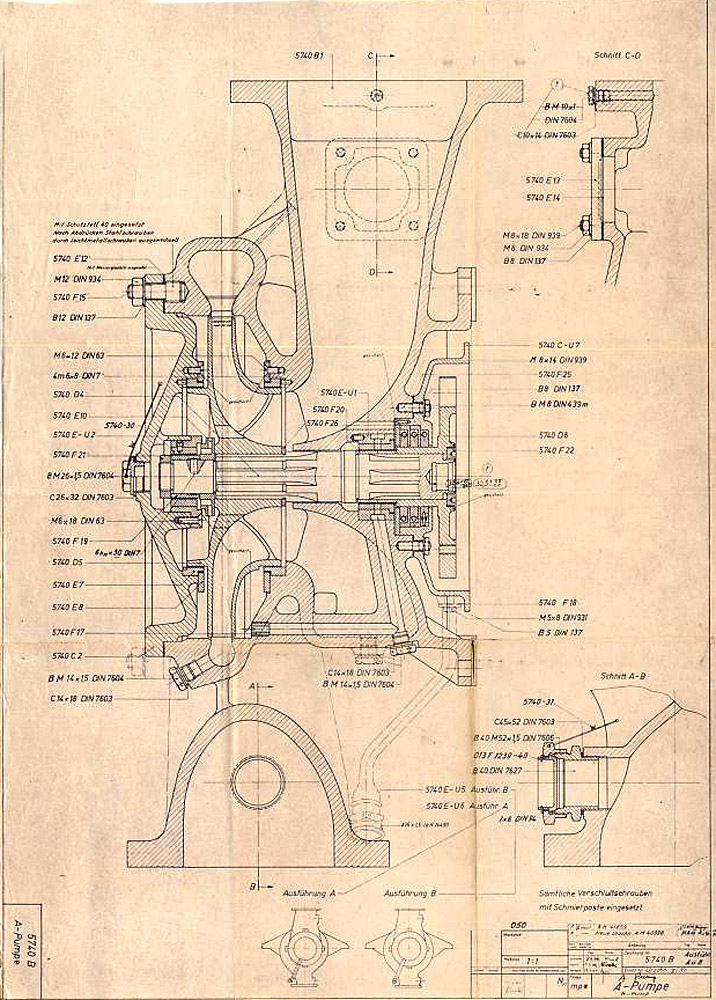
Signatur FA 014/02534
Abmessungen: 60,5×82,9
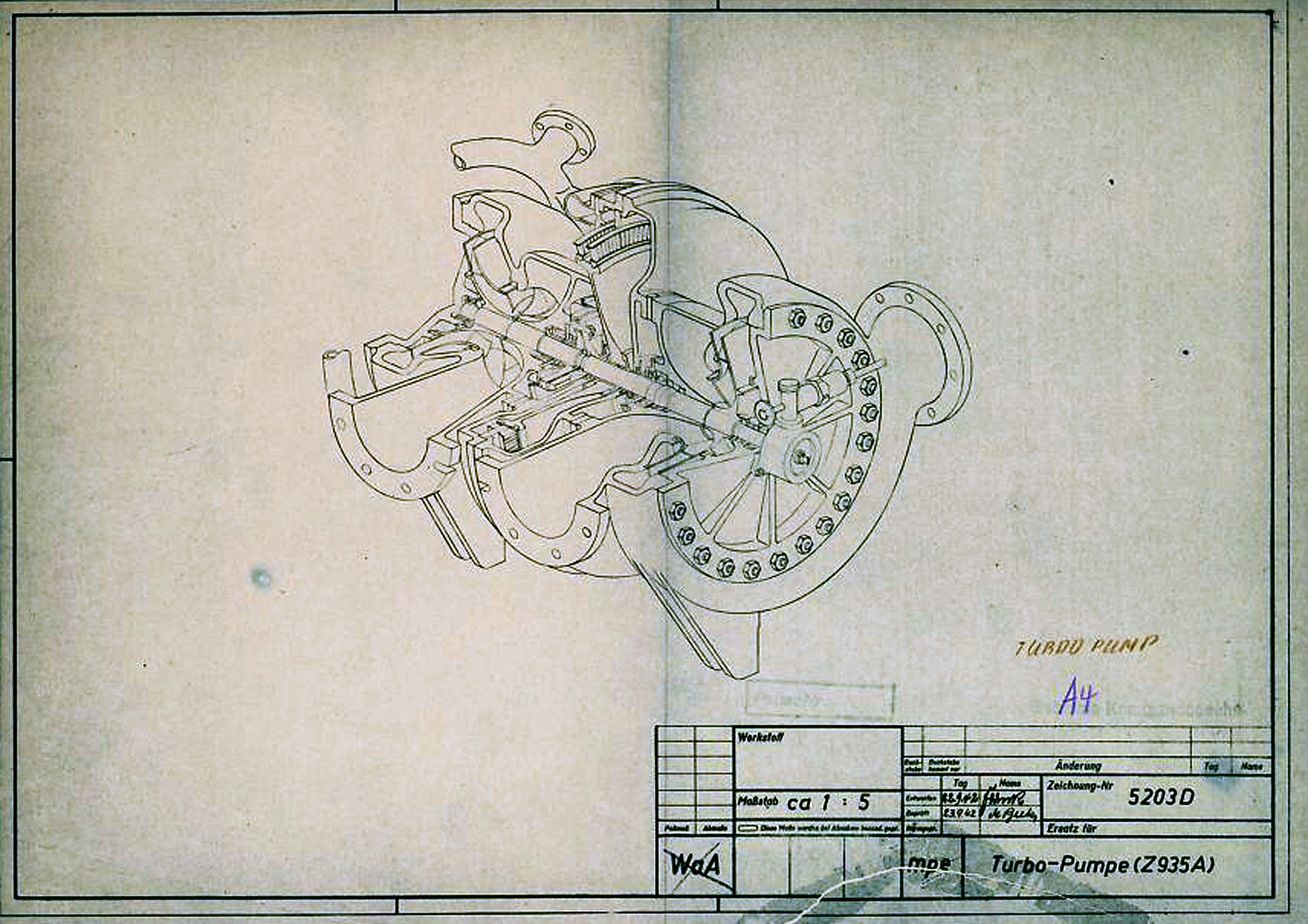
In this diagram the V2 Turbo-pump is shown in a cutaway presentation and rotated 90 degrees counter clockwise. The B stoff (fuel) pump is nearest the viewer – the over-speed device can be seen on the B stoff pump’s case end-plate. The low pressure inlet ports our shown to the left, and high-pressure outlet ports are on the right. The steam distribution manifold can be seen at the furthest point from the viewer – the steam inlet pipe flange can also be seen. The feed pipe from the steam generator attaches to thus flange.
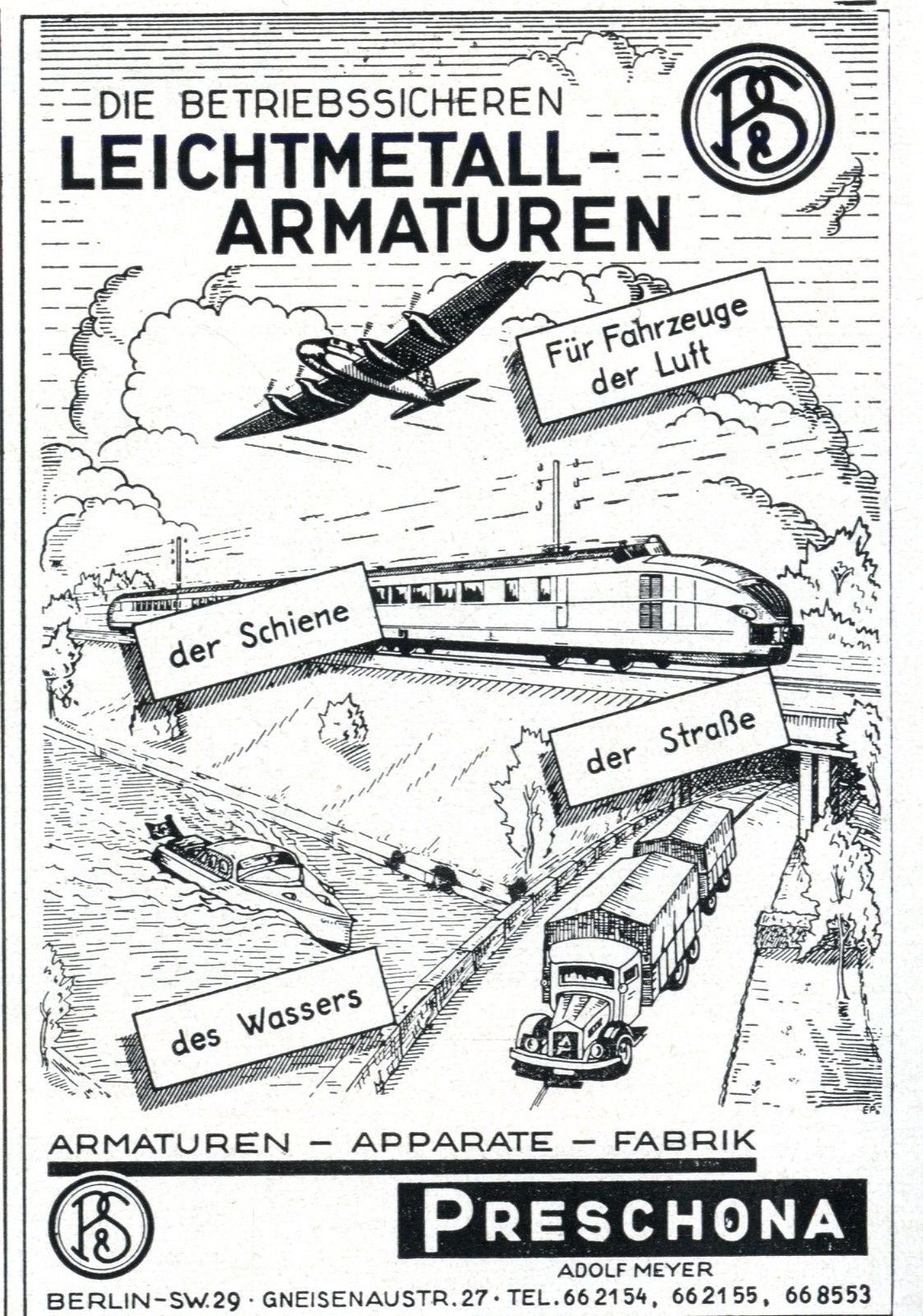
Trade literature advert for the Preschona company (Adolf Meyer) in Berlin, Germany. The company was a supply contractor and (among other items) manufactured the non-return valve for the steam turbine exhaust heat exchanger, employed to volatilise a small portion of liquid oxygen (LOX) to pressurise the LOX tank to maintain critical flow volume to the LOX turbo-pump.
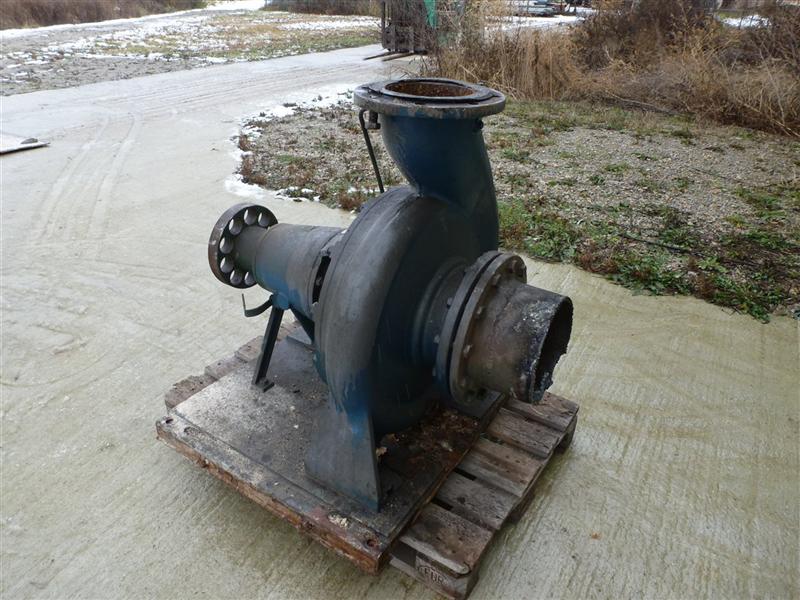
Large industrial volute case centrifugal pump by Klein Schanzlin & Becker. This image highlights the ‘genetic’similarity and family resemblance between KSB’s current and historical product range and the visible features of the A4-V2 missile Turbo-Pump (TP). Apart from the general shape of the cast spiral-volute case and its connection flanges, the ‘soft’ shaft connection (disk with holes on the extreme left of the pump) is very reminiscent of the semi-flexible shaft connection point linking one side the steam turbine rotor shaft to the shaft carrying a propellent pump rotor seen in the A4-V2 missile TP. Family photo? Industrial volute case centrifugal pump by KSB
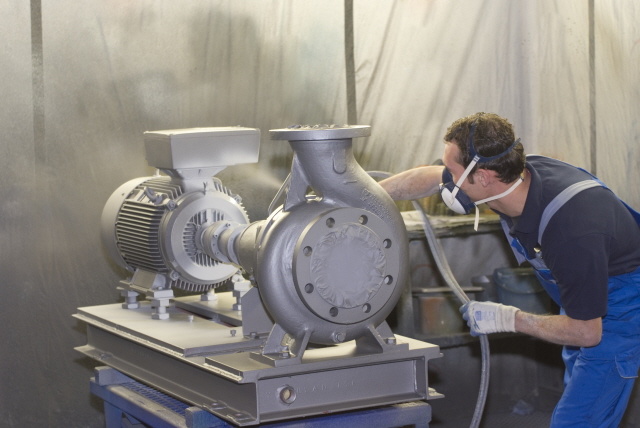
Electric industrial volute case centrifugal pump by Klein Schanzlin & Becker. This image highlights the ‘genetic’similarity and family resemblance between KSB’s current and historical product range and the visible features of the A4-V2 missile Turbo-Pump (TP). Assembly is shown being spray painted.
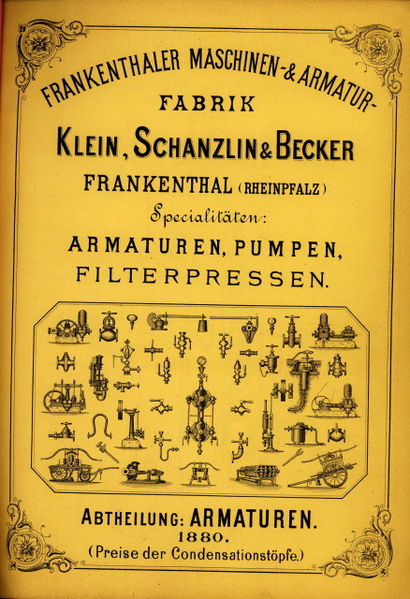
Cover of catalogue published in 1880 showing the KSB product range
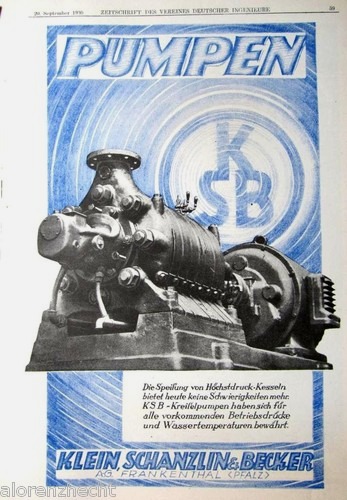
Klein Schanzlin & Becker electric centrifugal-pump advert.

Valves
Images of the main valves involved in the propellant flow of the A4 / V2 liquid fuelled rocket engine
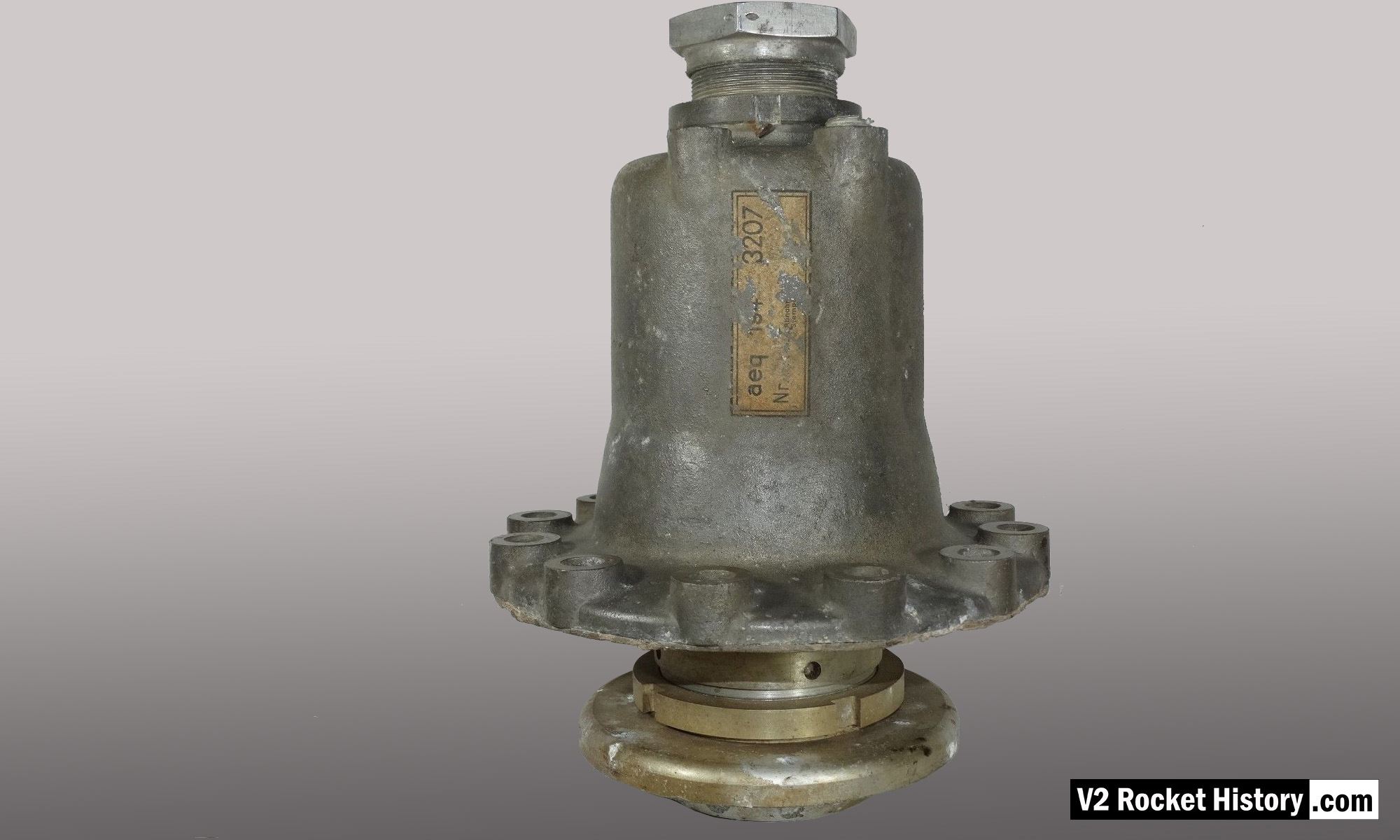
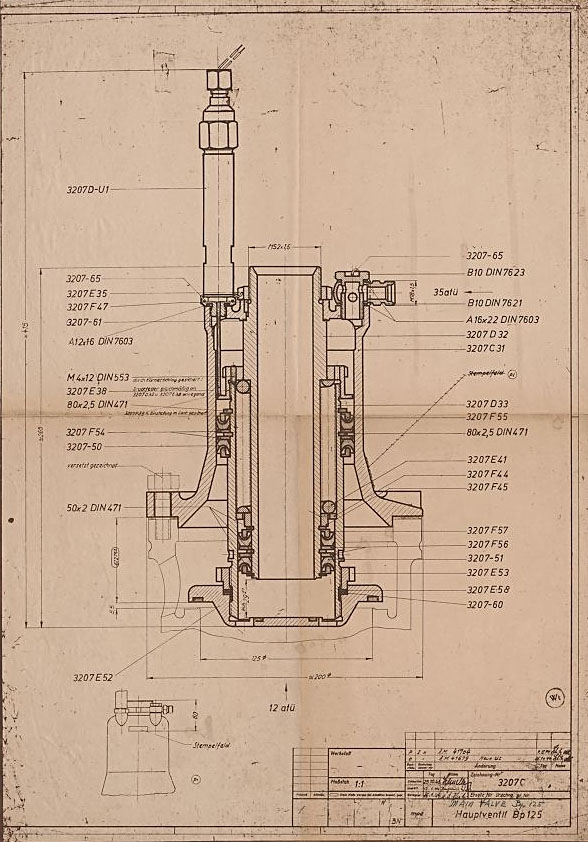
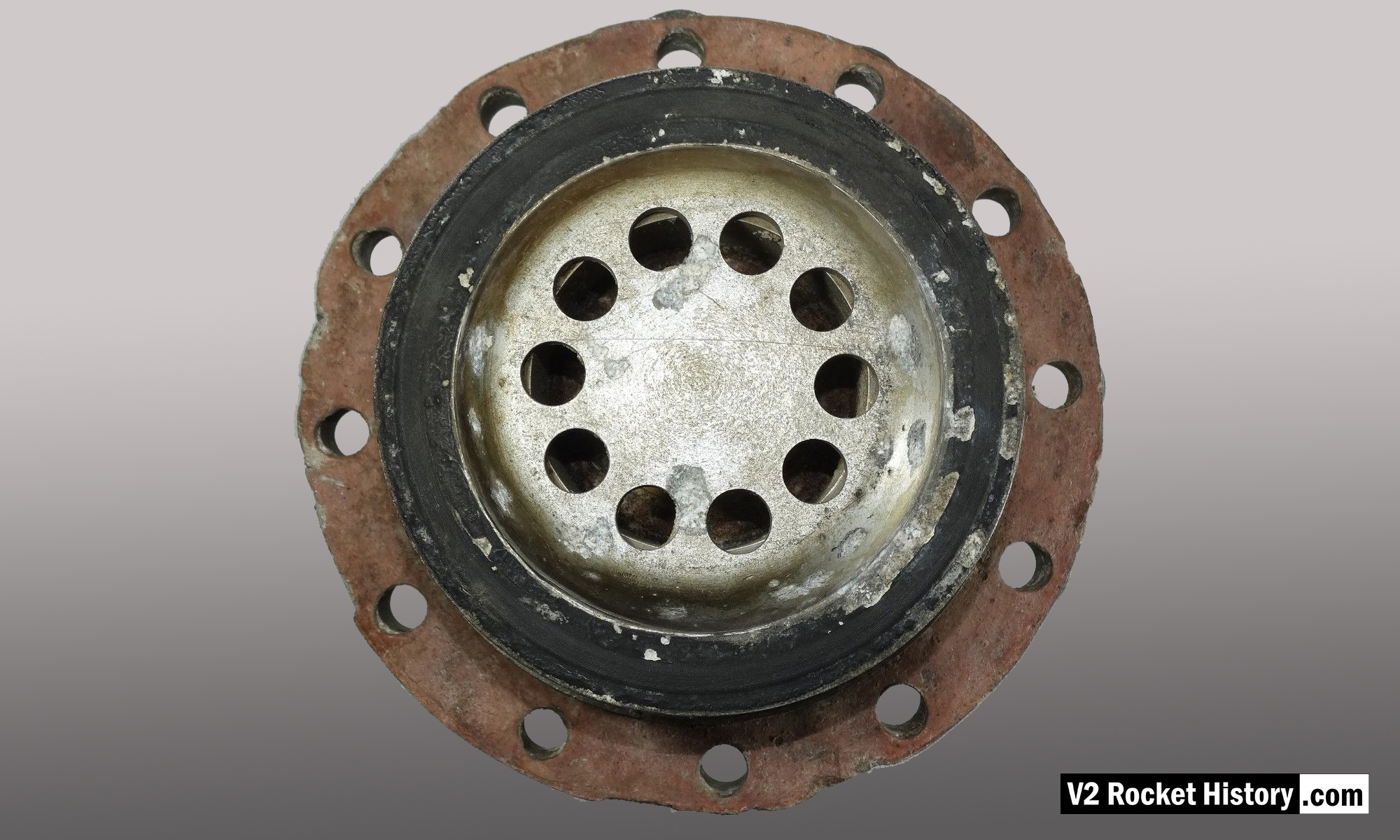
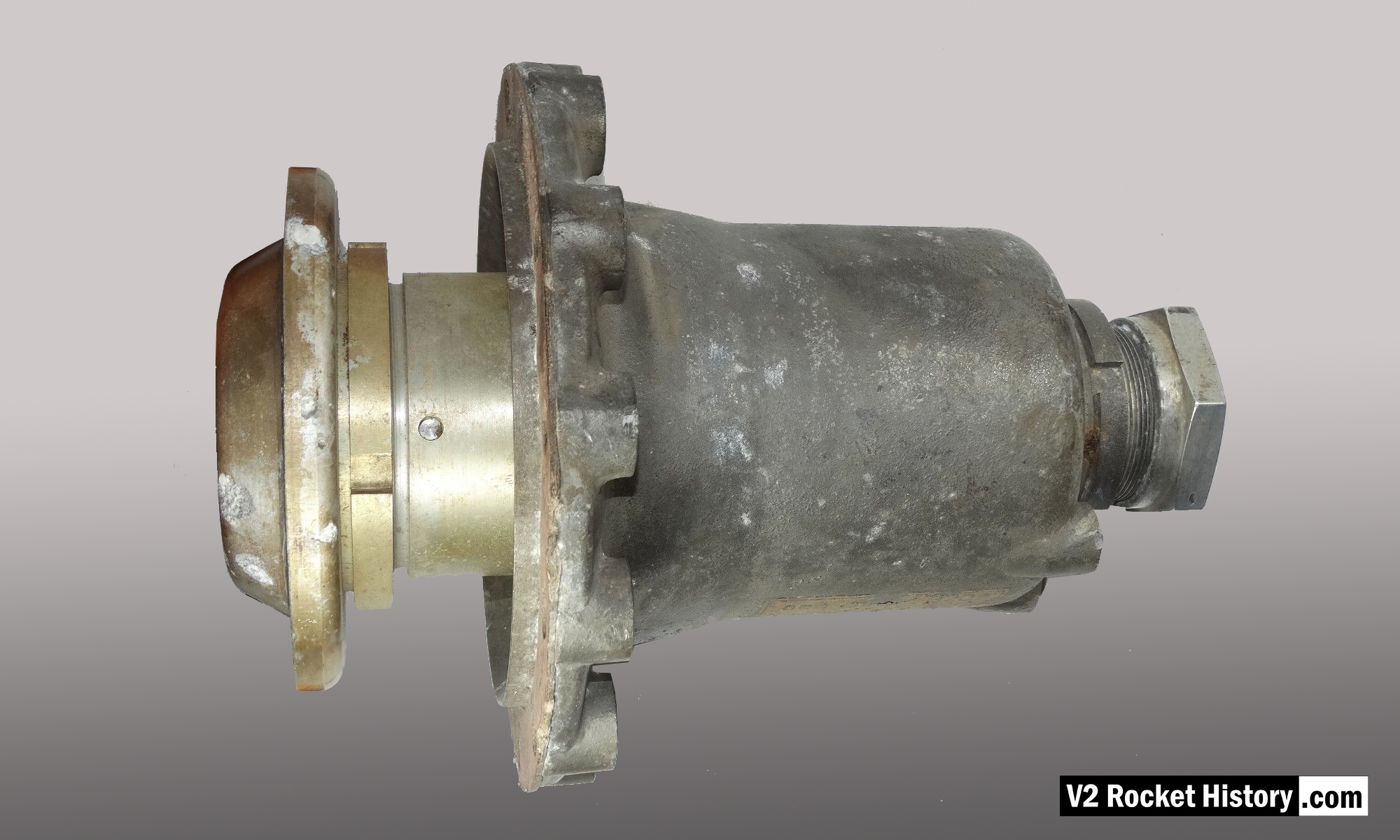
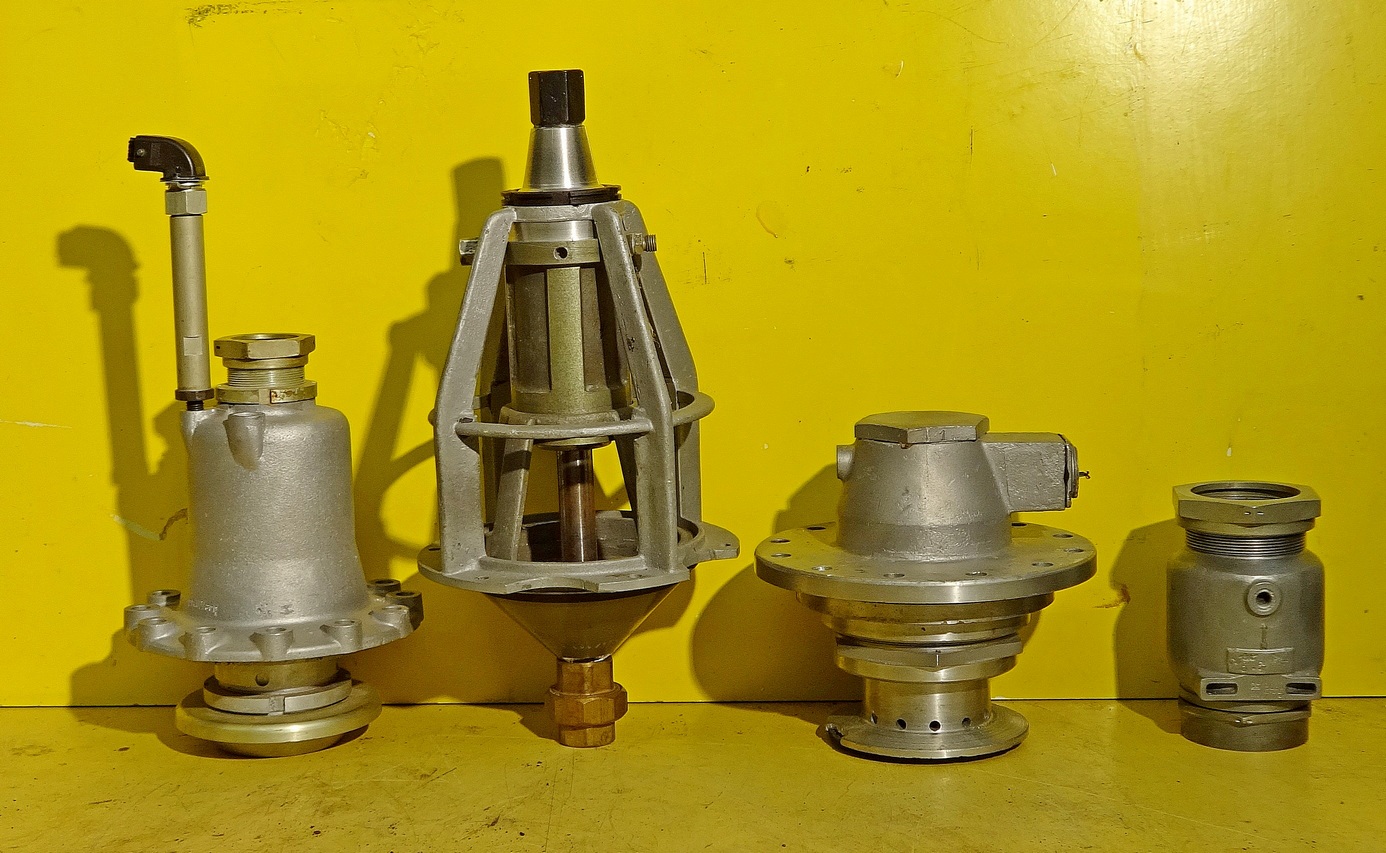
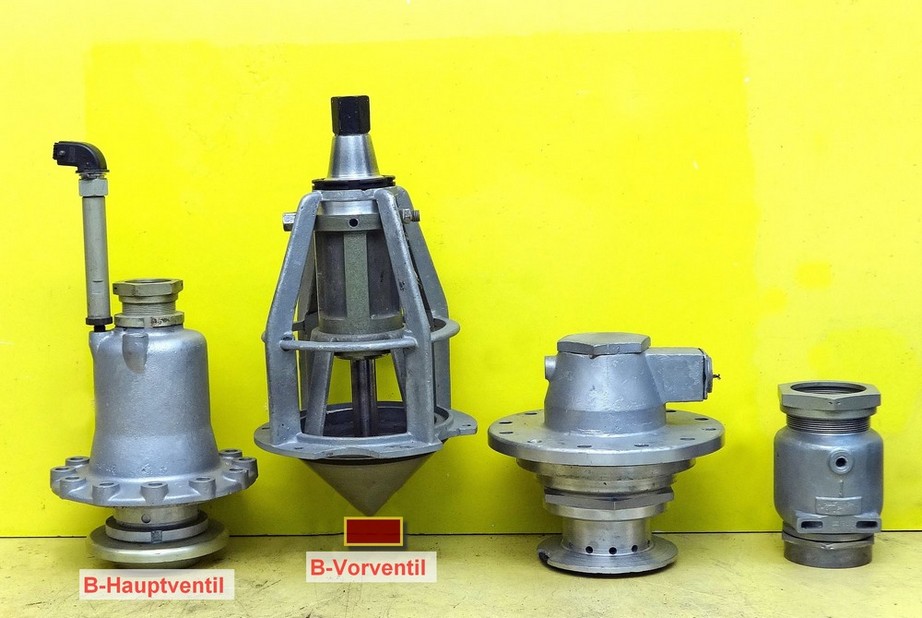
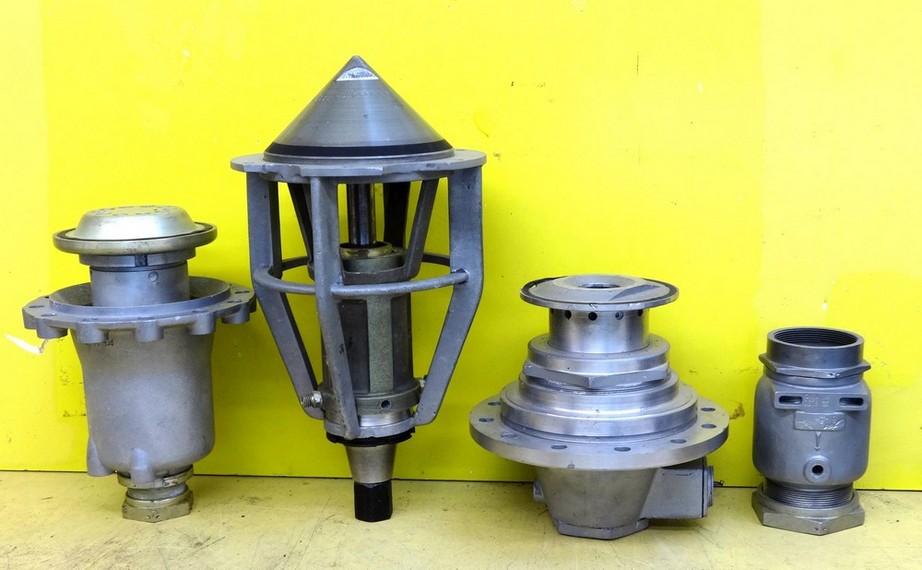
Images of the main valves involved in the propellant flow of the A4 / V2 liquid fuelled rocket engine
Relic of main alcohol valve with manufacturer code aeq (aeq = Bartoc & Co., Maschinenfabrik u. Giesserei Hedwikow,bei Caslau (Caslav) Czech Republic). An air (nitrogen) inlet pressure of 440 to 530 psi (30 to 36 Bar) was required to close this valve against its internal spring and the force of the turbo-pump. The large nut at the top is the connection for the fuel return (or ‘revolving’line) pipe, and the air and electrical input ports can be seen to the right (air), and left (elec.) just below this point. V2RH image

Anatomy of the V2: 18-pot injector head
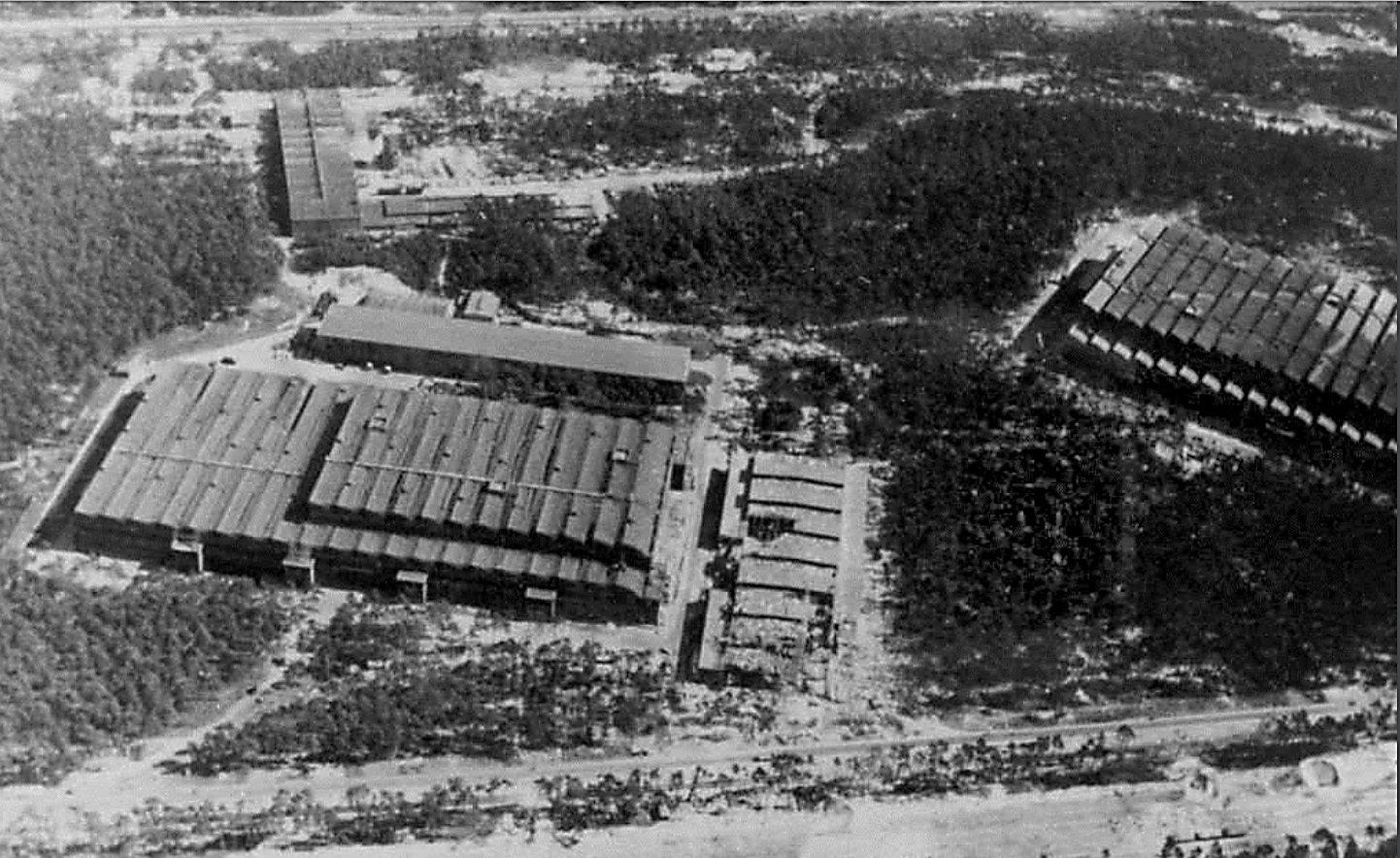
Photo showing Werk Süd with IW on the left and F1 on the right taken on 19th August 1943. The photo shows only light damage to the main halls, although F1 was actually hit at least 11 times, and hits to the separate single storey workshops to the right of the IW hall. The long storage (oil and paint?) shed above IW and the woodworking shop at the top of the picture appear undamaged. Anti-aircraft platforms (at least 3) can be seen on the roof of IW but that seem to be empty of guns. F1 shows two AAA platforms (there was at least 3 at this stage and maybe more) and they may have guns installed. General W. Dornberger mentions defensive AA artillery fire from the from the roof of F1 in his 1952 book V2 (1954 in English).
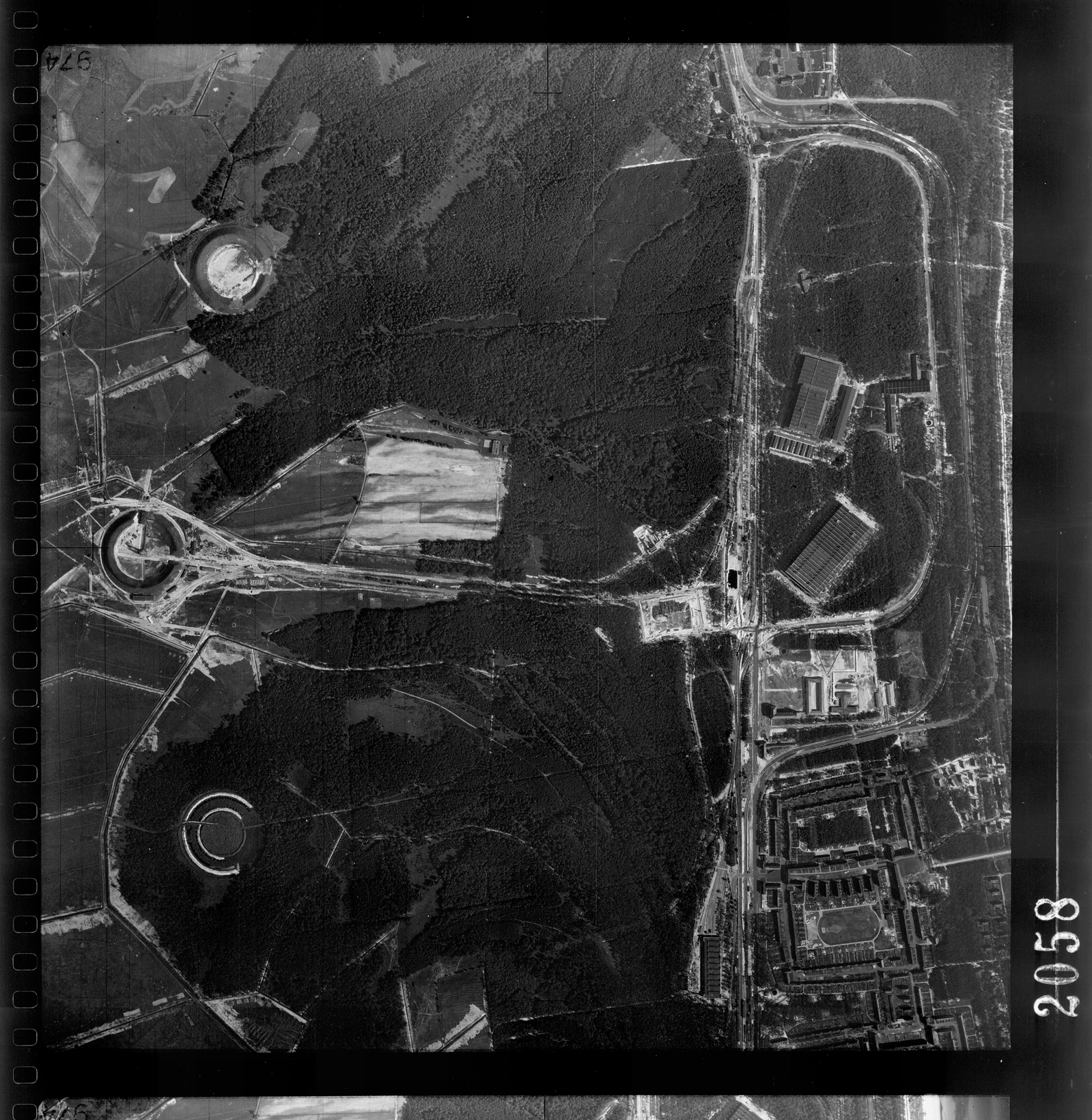
RAF reconnaissance photo showing the Werk Süd region with the F1 pre-production hall and to the north the IW repair and maintenance hall, centre right, and road rail links to Prüfstand XI (Test Stand 11, circular rampart centre left) heading directly left from F1. P-XI was conceived to provide engine test facilities for the nearby pre-production hall. Scroll down to see GPS map, the marker index is set to the centre of P-XI, click map and switch to satellite view and you will see that only a small section of the circular rampart remains visible. You can easily zoom out to cover the coast area where F1 and the equally large Repair & Maintenance Workshops are located. The area immediately surrounding P-XI is now contained within a commercial farming operation with sheep appearing to be the staple – or was anyway, at the time of our first visit to the vicinity in 2010 and our last in 2017 – none of the sheep seemed to recognise us though so they may have changed. (for access to restricted areas click here)
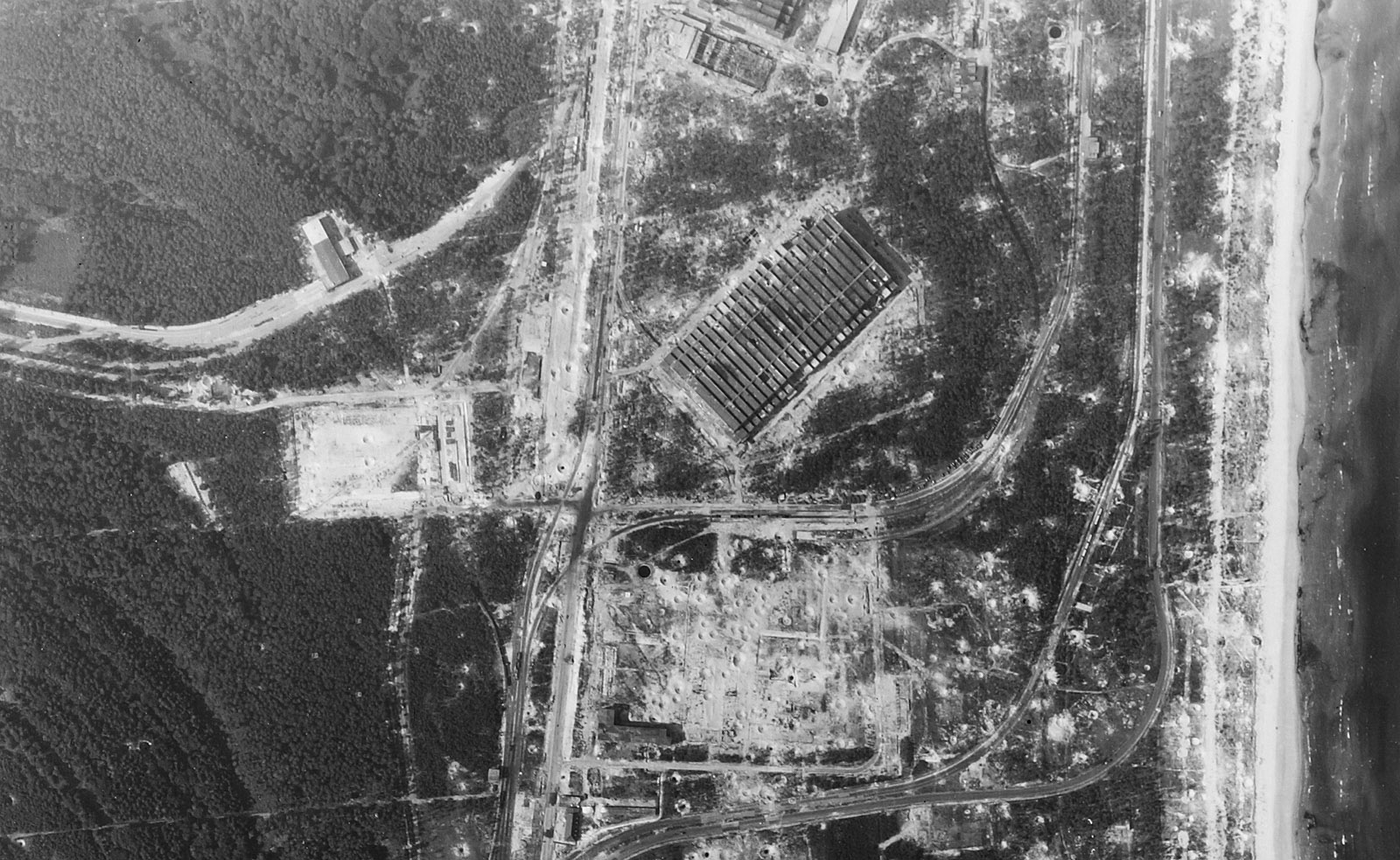
RAF Recce photo taken 21st August 1944 of region around F1. The GPS marker for this photo is pegged on the lowest of the three fire fighting cisterns clearly visible in the image (in the center about a third the way up from the bottom of the image). Scroll down below this text for map and switch to ‘Satellite view’ where the fire fighting cistern can still be clearly seen today.(for access to restricted areas click here)
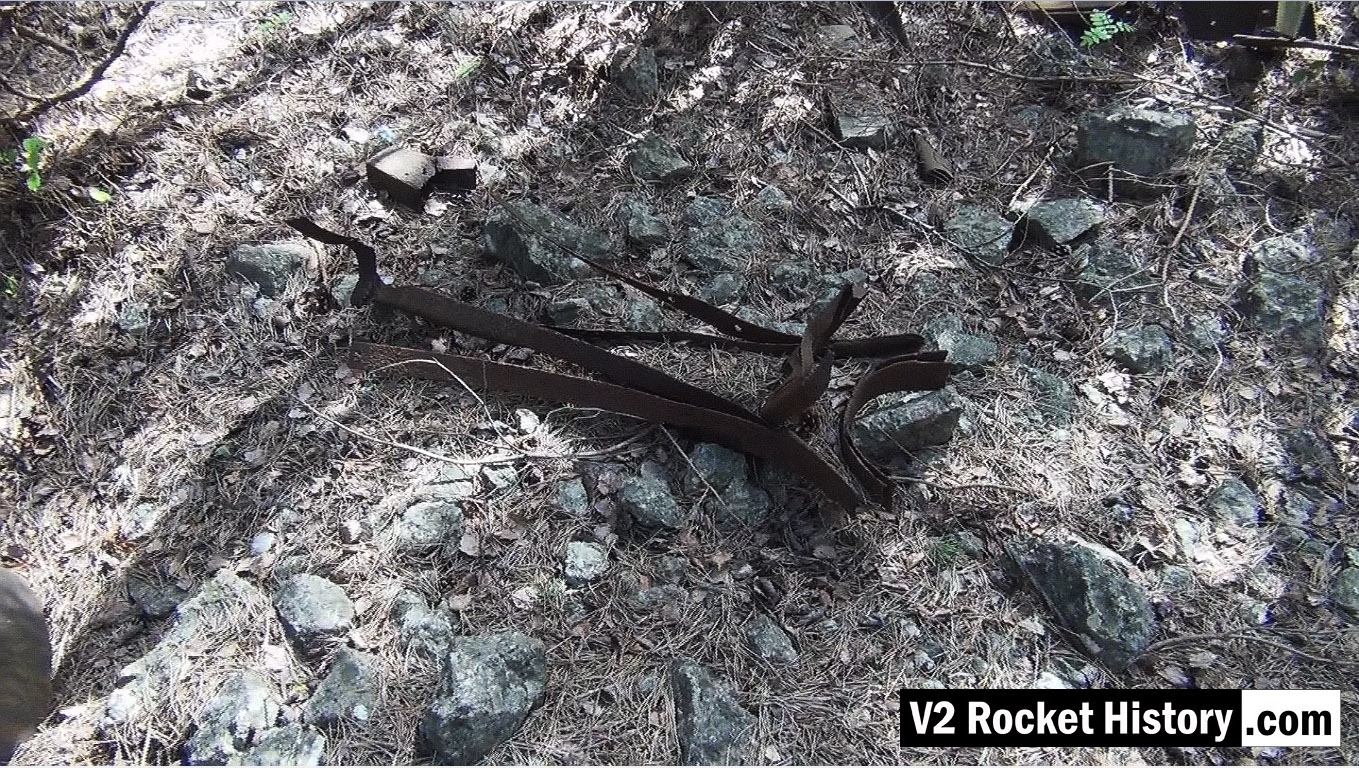
Picture shows parts of V2 missile fin structure laying on open ground near area between admin offices and F1 (near Admin. block railway platform, see map).
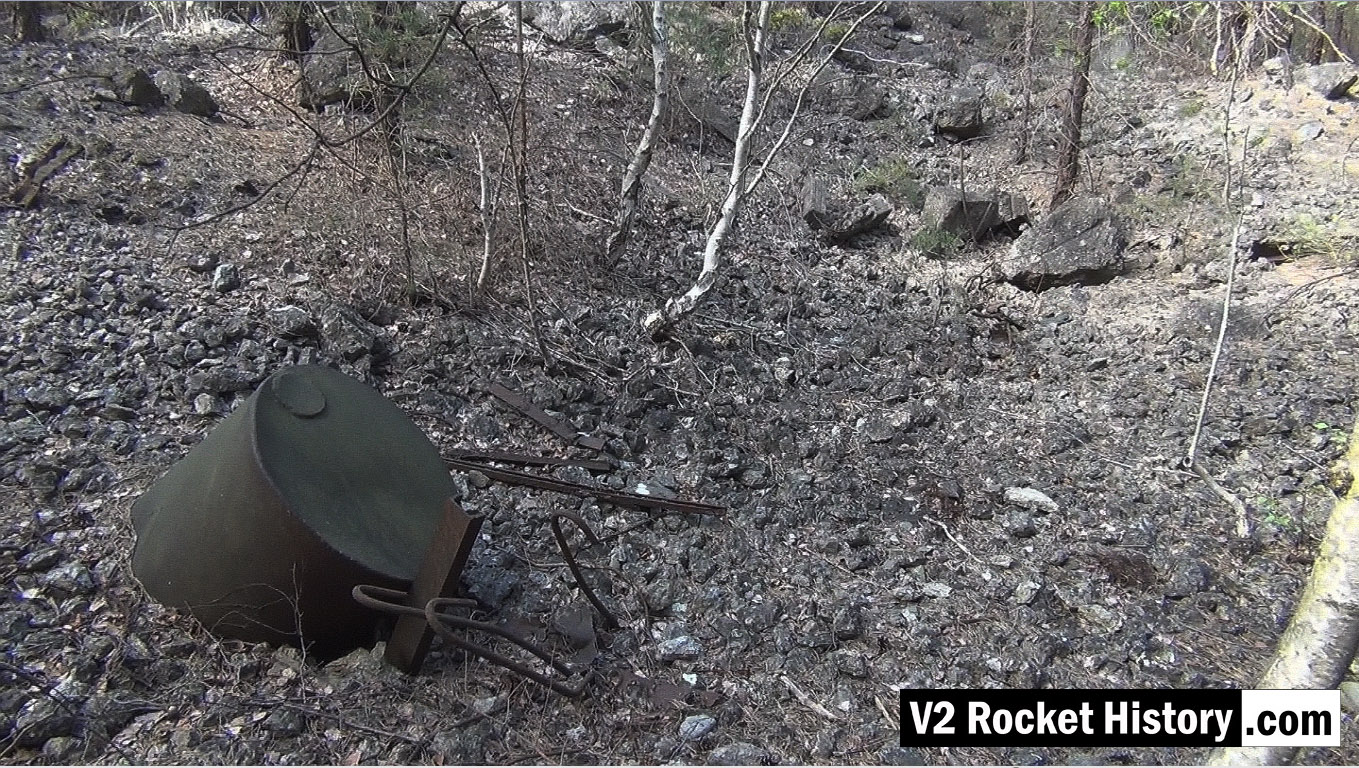
Picture shows metal debris within the F1 factory boundary walls. The purpose of the part buried liquid storage vessel in the foreground is unknown but it is not a vessel capable of being pressurised. Other assorted metal debris include pipe and cable wall cleats, as well as steel armature rods from reinforced concrete castings (powerful demolition explosions have freed the steel rods from the concrete). These reinforcement rods are a common sight in the environs of Fertigungshalle Eins (F1) and the nearby Repair & Maintenance Hall (R&MH).

This picture shows a small debris field of steel fragments from the V2 missile 130m South-East of F1, and just 20m to the North East of the foundations of a small heat distribution building. Various body and frame parts can be seen and in the middle foreground a 350mm segment of curved missile body ring is visible. These parts have almost certainly been dug up and exposed by the action of metal detectorists. The metal fragments have been abandoned by their finders as they are perceived to have no financial value and hence are not worth removing from the site.
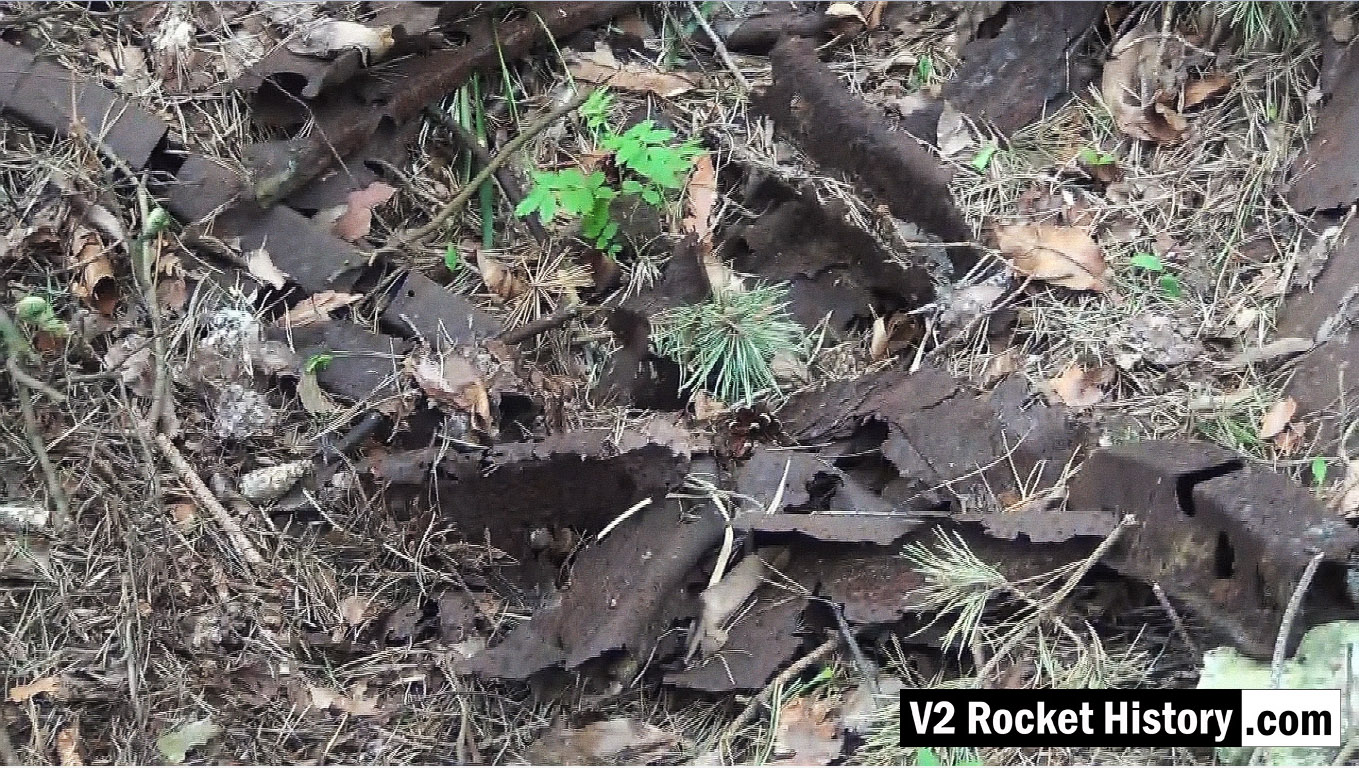
This picture shows a close up detail of parts in a small debris field of steel fragments from the V2 missile 130m South-East of F1, and just 20m to the North East of the foundations of a small heat distribution building. Various body and frame parts can be seen and in the upper left and two segments of curved missile body ring are visible. See previous.
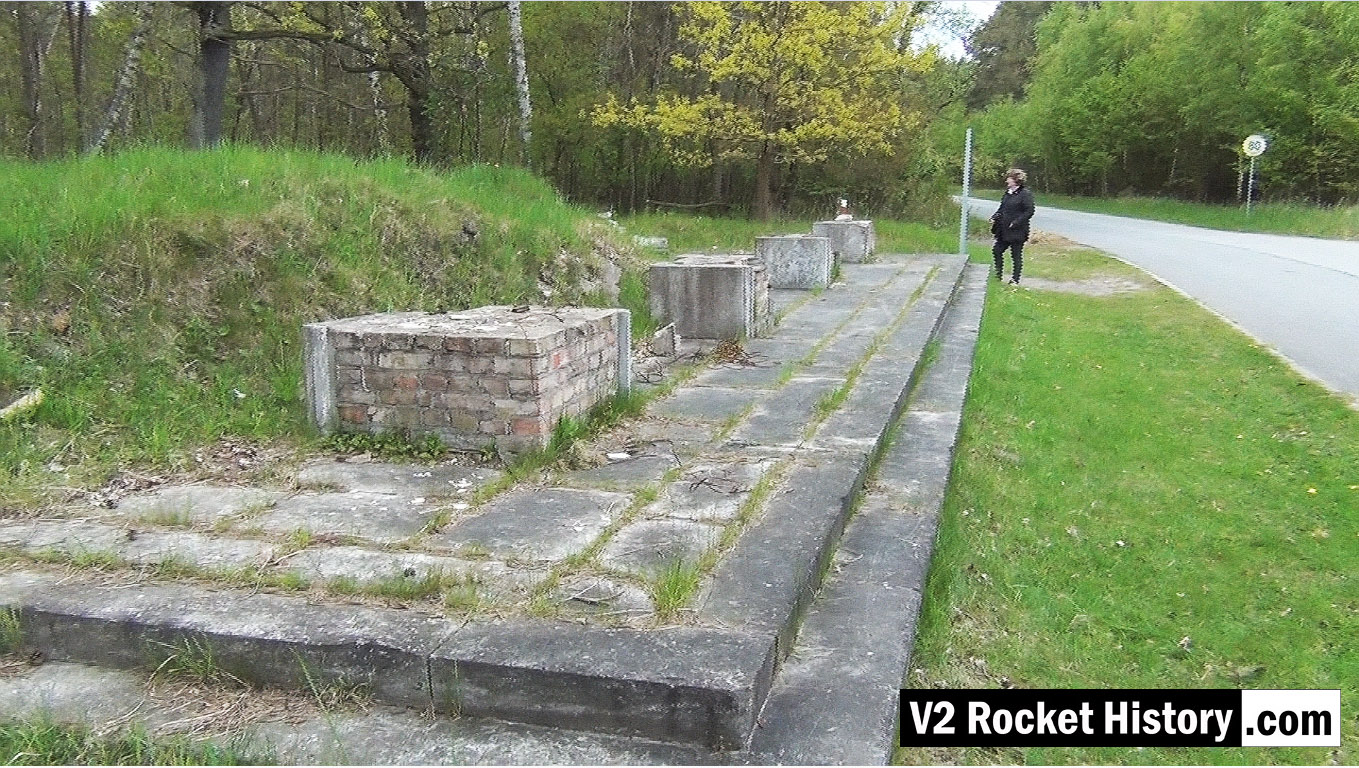
This picture shows the remains of the main South entrance to the Development Works. (also known as Station 7 – Die Hauptwache).
Album | Development works |
Category | Peenemünde-Usedom-locations |
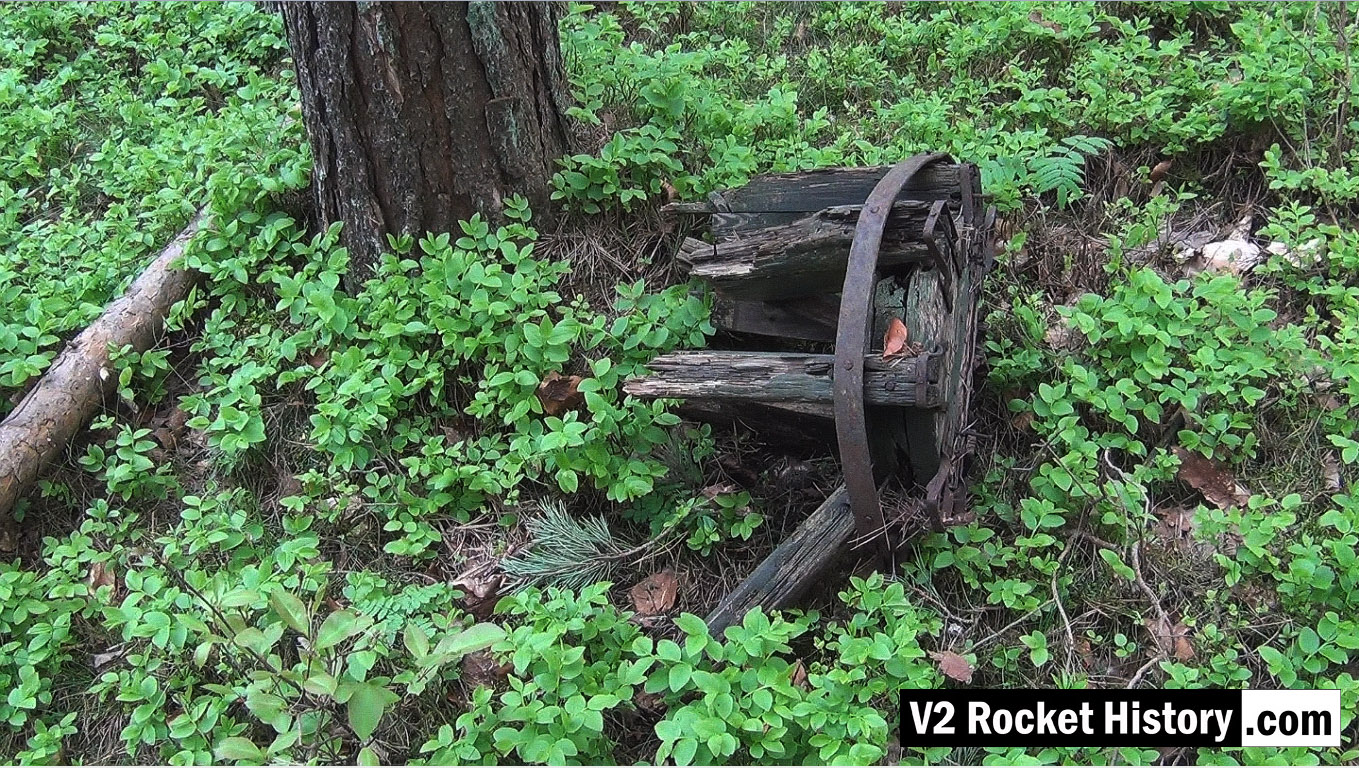
Wooden carboy frame from WW2 (possibly used for transporting small quantities of corrosive and dangerous liquids employed in the V2 steam plant, (such as T-Stoff) laying among trees 190m East of F1 in a location used as an emergency rail freight loading area to F1 due to damage caused by US air raids in August 1944.
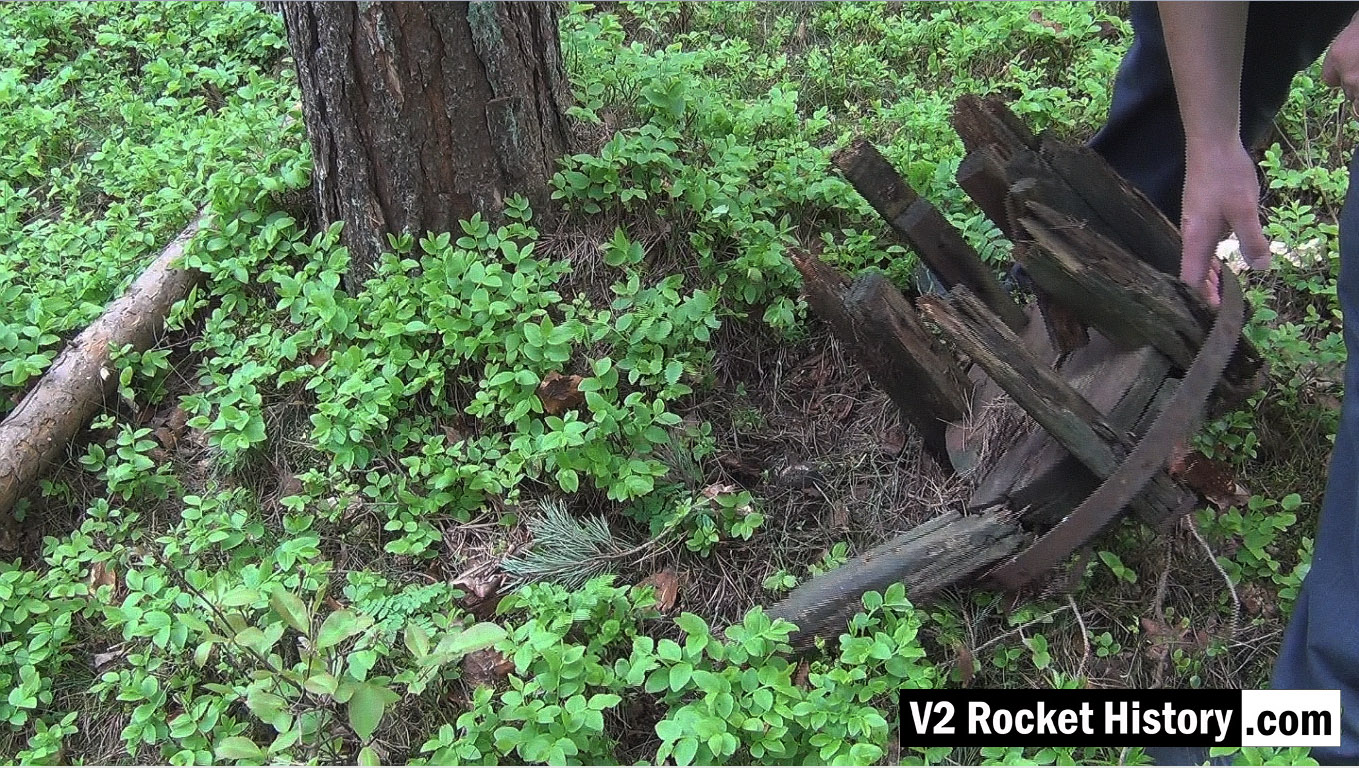
Wooden carboy frame from WW2 (possibly used for transporting small quantities of corrosive and dangerous liquids employed in the V2 steam plant (such a T-Stoff) laying among trees 190m East of F1 in a location used as an emergency rail freight loading area for F1 due to damage caused to rail track by US air raids in August 1944.
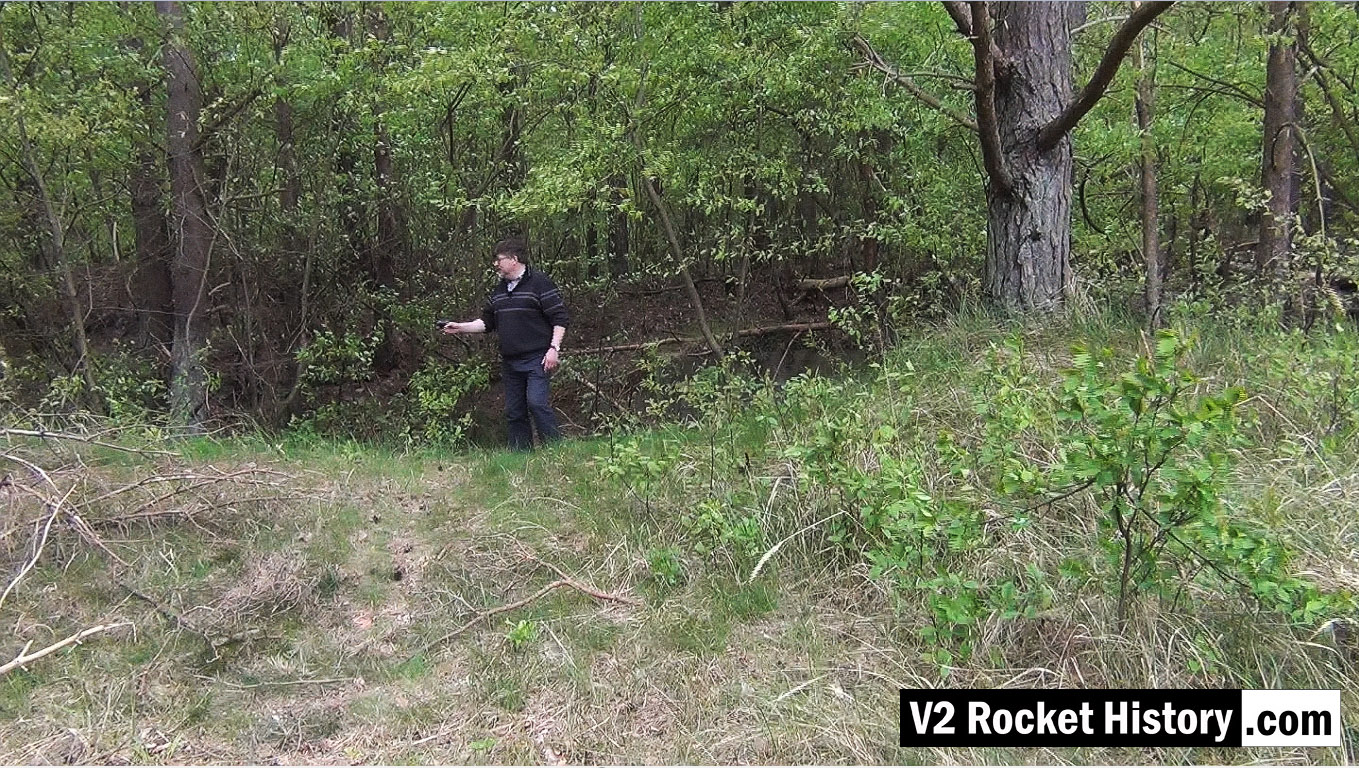
This picture shows Robert Dalby collecting GPS data with a mapping camera just North of the East end of the Admin office rail platform (near the ruins of the small admin/F1 heat distribution hub building). In all of our explorations we routinely collect GPS track and data points to be able to accurately locate finds and establish a precise correlation between areas of interest identified on historical reconnaissance photography and the modern ground terrain. In the picture Robert is pointing a Contour video camera at details of the terrain that automatically captures the camera’s GPS location information. This data can then be combined with satellite imagery, via Google maps, and provide a detailed graphic mapping track alongside the video footage.
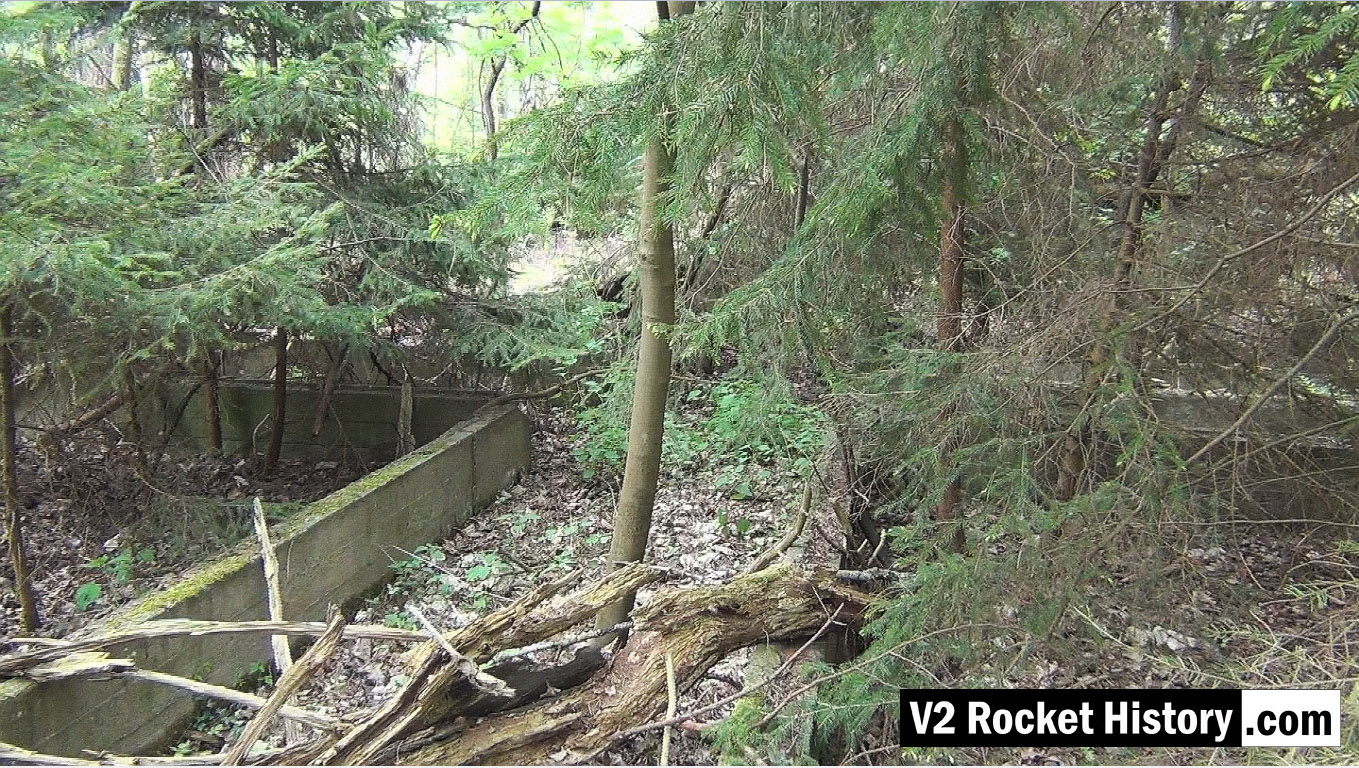
This picture shows some of the extensive ruins that were once part of the railway shed complex West of the railway lines heading to the Development Works. Screen grab from Karlshagen video.
Album | Karlshagen |
Category | Peenemünde-Usedom-locations |
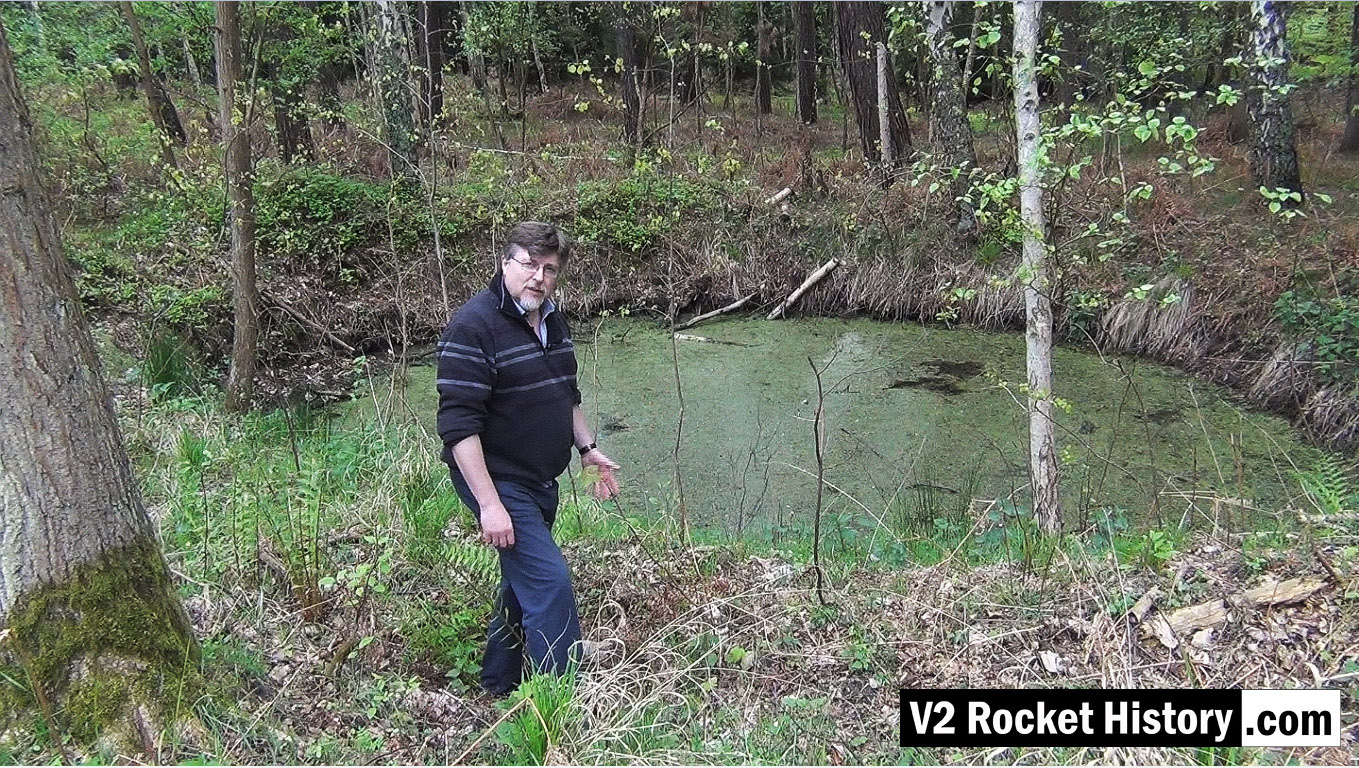
This video still shows Robert in front of a bomb crater on the West or opposite side of the rail lines and road that pass the Repair & Maintenance Hall (R&MH). The crater like so many others, created in a fraction of a second, in August 1944 during a US air raid, has developed in to a thriving eco-system that now teems with all kinds of life. After the passage of more than 70 years the crater is still deep and well defined. There are hundreds of craters like this in the area.

This video still shows the same bomb crater from a slightly different angle. The crater like so many others, created in a fraction of a second in August 1944 during a US air raid, has developed in to a thriving eco-system that now teems with all kinds of life. After the passage of more than 70 years the crater is still deep and well defined. There are hundreds of craters like this in the area.
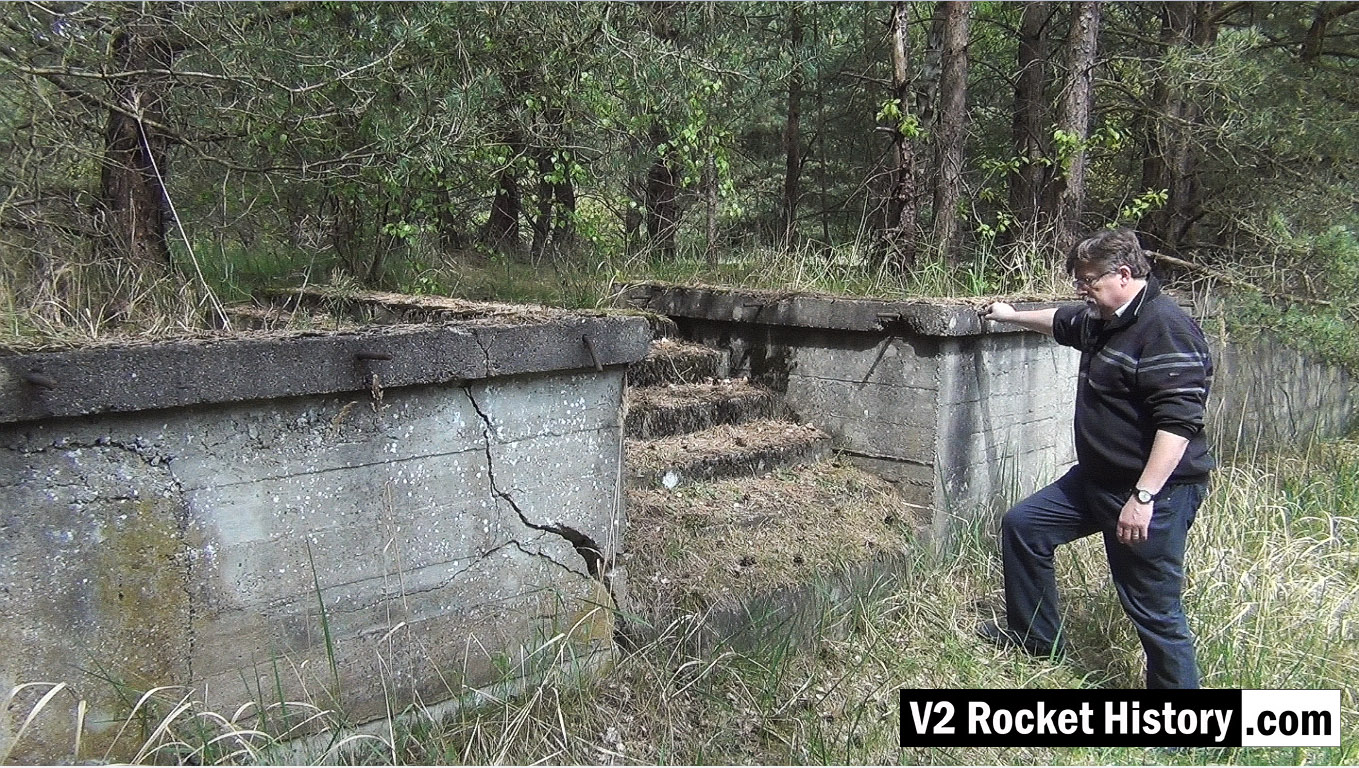
This video screen grab shows Robert about to climb the steps up onto the rail and road loading station 9 (also called Die Verladerampen or in English, The loading ramps). This storage and loading facility was never finished during the war and was intended to be a more elaborate with large storage buildings – but the pressure of war and constant use of the area prevented further development. The area is still surprisingly intact today with a strong correspondence between modern ground detail and historical reconnaissance photography.
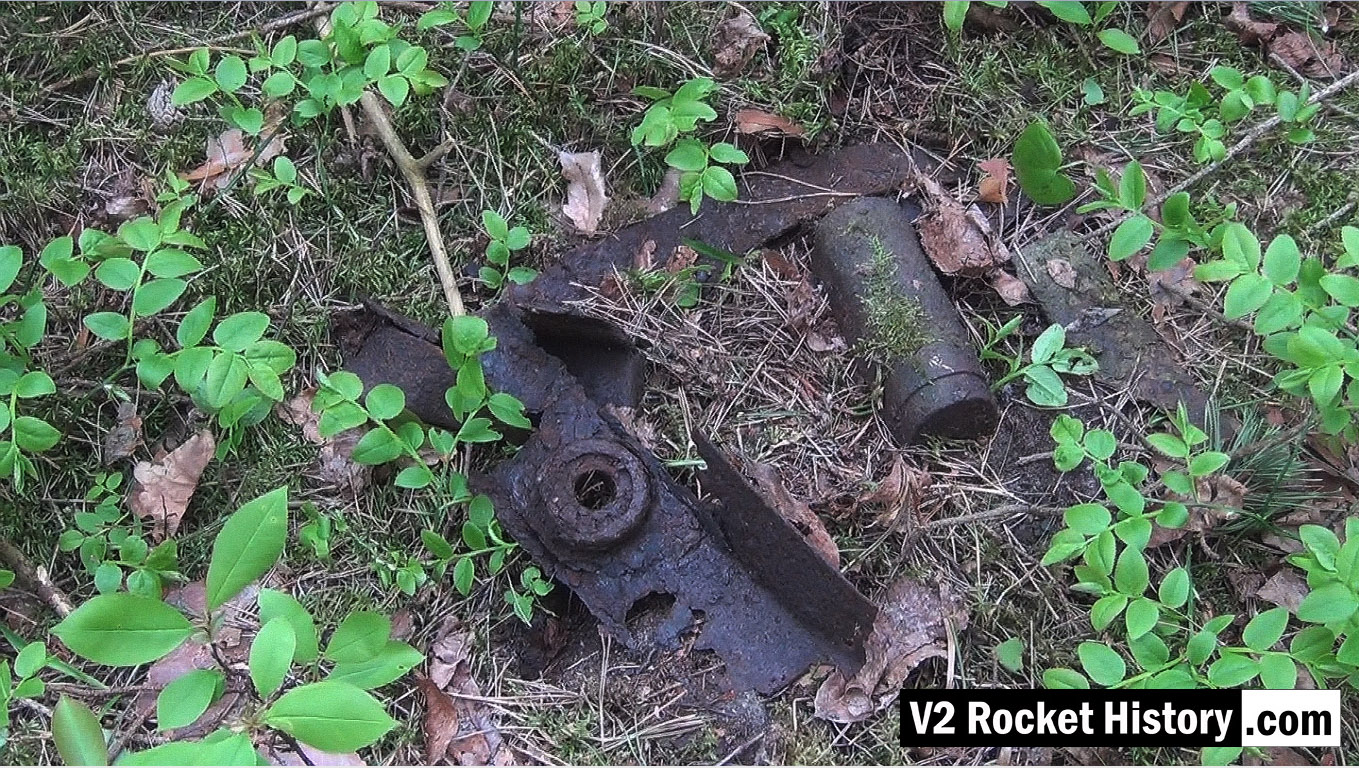
V2 missile parts in F1 prisoner turn-out or ‘free movement’ area. The location referred to is a large triangular shaped area situated on the South-East side of the pre-propuction hall Fertigungshalle Eins (F1). The area was fenced off with a high barbed wire fence (a portion of which was electrified) with guard towers every 60 metres.
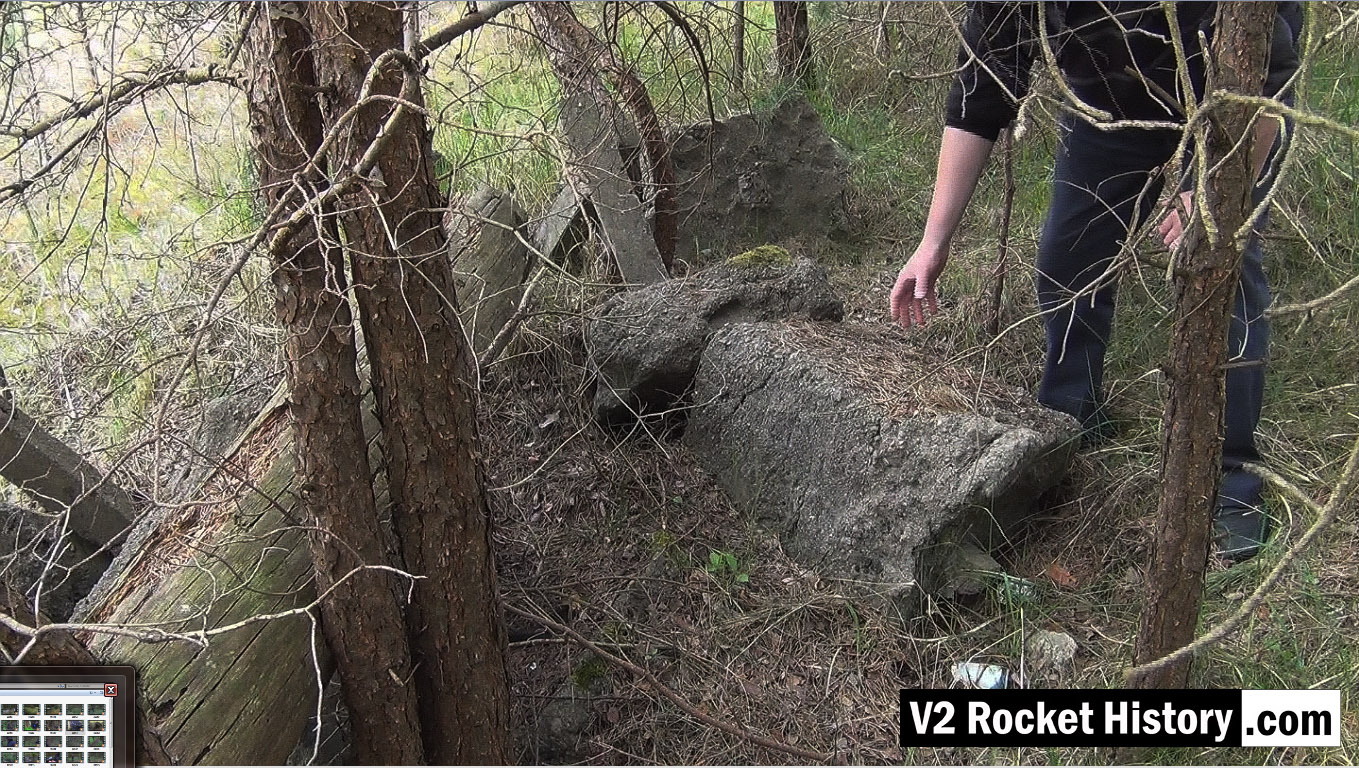
This image shows part of a pile of concrete castings that form the below ground foundations for part of the electrified fence that was built around F1 in the summer of 1943. The fence was built on the instructions of Arthur Rudolf, who was responsible for F1, by the first 200 forced labourers to arrive at the F1 labour camp in June 1943. These crude castings are the result of digging a narrow hole in the ground for the concrete fence post and filling the area around the post with the concrete mix. The sizable variation in the depths of the concrete castings, and the fact that in a number of casting blocks the post has plunged through the concrete mix and penetrated from 100 to 300mm into the ground below, strongly suggests this work was carried in hast and/or by men inexperienced in the normal procedures of this type of basic ground-work.
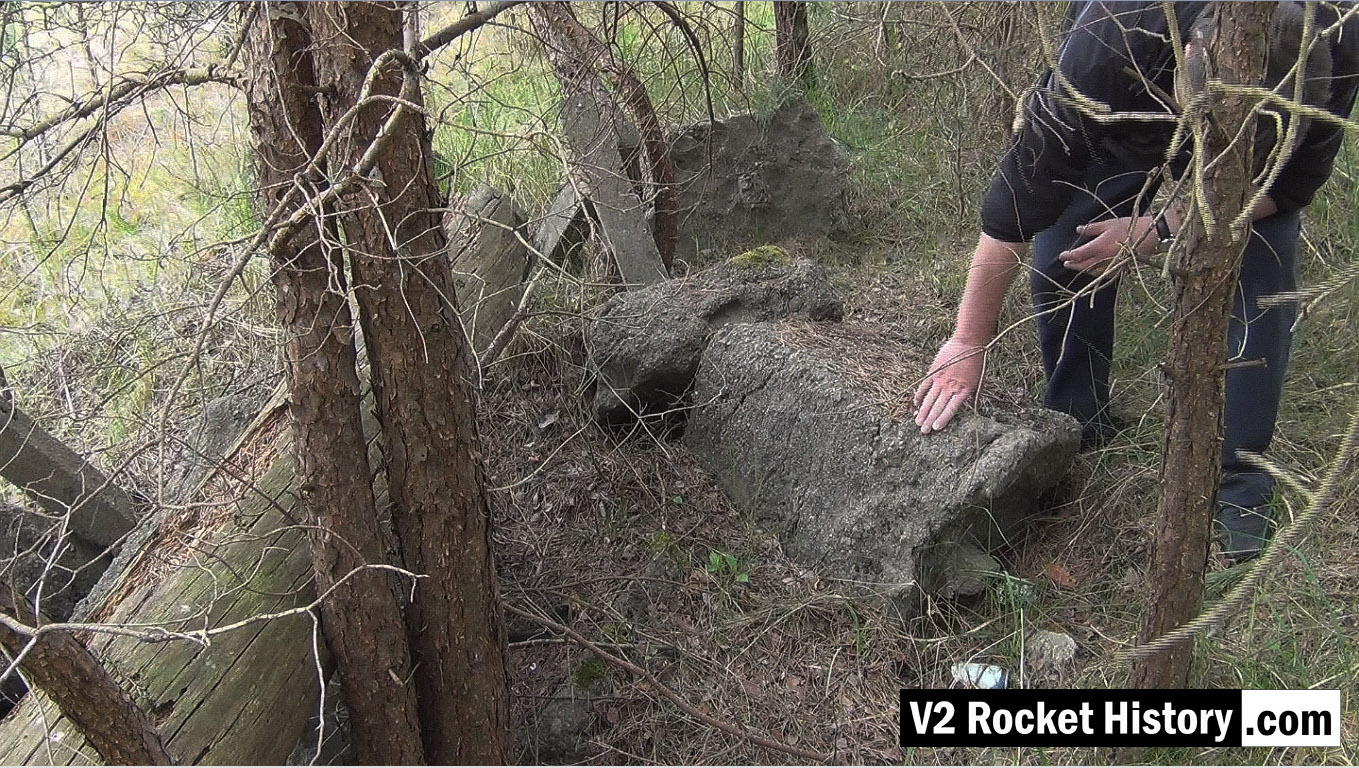
This image shows part of a pile of concrete castings that form the below ground foundations for part of the electrified fence that was built around F1 (see previous photo for details). You can see the area that these posts once secured in the second black and white recce image in this gallery. The fenced off area is the large triangular shape you can see joining the North-East South-East corners of F1 (ie the long wall of F1 facing the shore). Quite why and exactly when someone mustered men or machines to pluck these lumps of concrete out of the ground and move them 100 to 200m is beyond me – why not just bulldoze them under like everything else on this site?
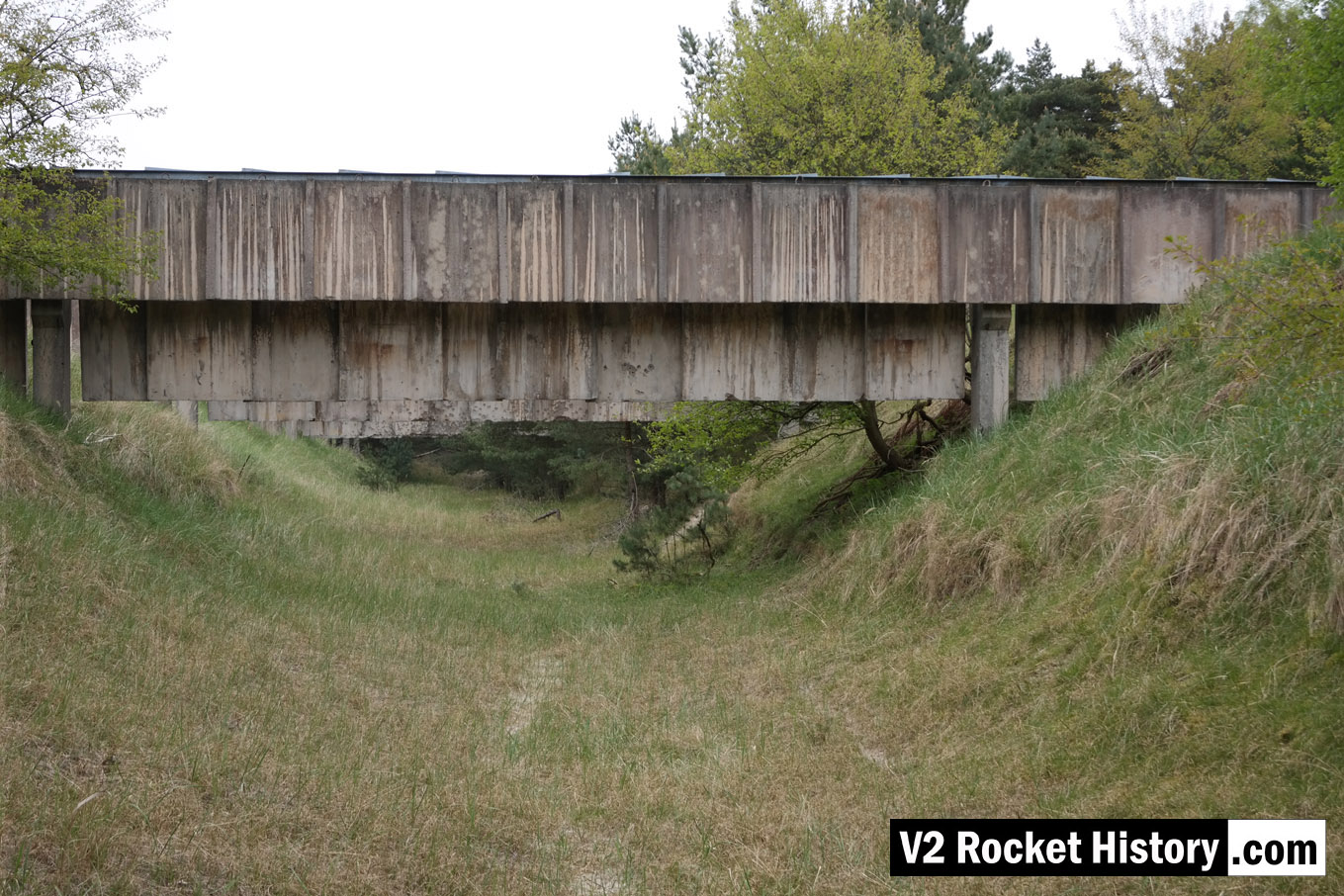
Photo shows the remains of a shooting range built by the East German Army. In 1944 the area about 200m in front of the camera and to the left of this picture is the emergency rail-loading area used after US air raids in August damaged rail lines and other regular freight loading infrastructure. Today, it is a peaceful thoroughfare used mostly by deer and rabbits.
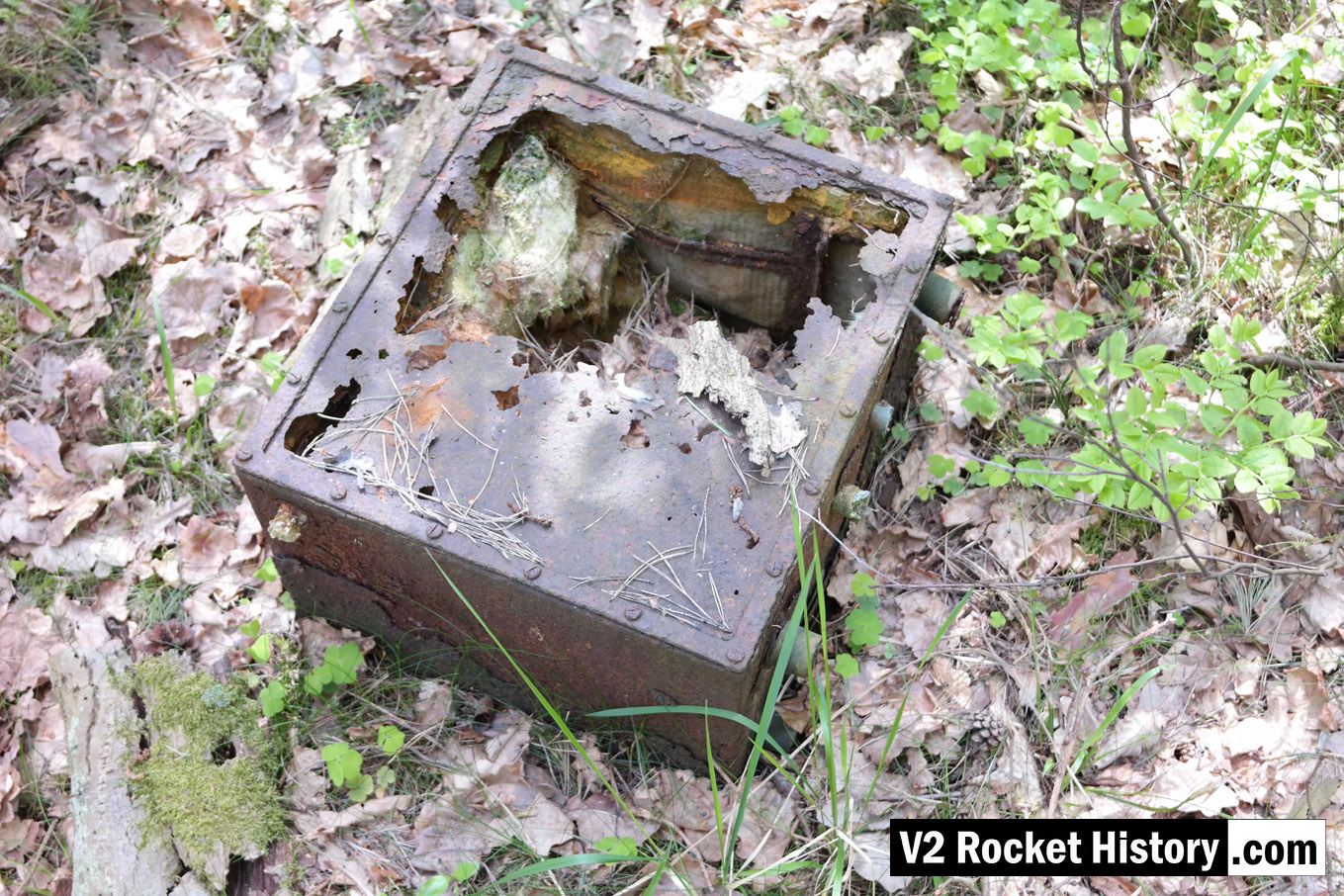
The photo shows a Lichtstrahl empfänger (In English: Light-beam receiver) environmental protection case, originally one of a group of 40 or so we first found in 2010 abandon in an area adjacent to the train platform for the administration block. On subsequent visits this number has declined to just ten or so, mostly very decayed examples. The environmental casing was vital to the Lorentz Light-Beam equipment on-board the V2 missile as the critical radio frequency would otherwise drift with the large change in temperature as the missile climbed into the stratosphere. The case was thickly insulated with rock wool or fibre-glass strands and designed to help maintain a stable temperature – indeed, the same temperature as the radio equipment was when at ground level when calibration and adjustment was completed before launch. The F1 pre-production hall is located about 200m North-West of the point where this photo was taken. Scroll down to see map below (click map and switch to ‘satellite view’ for clearer indication of location).
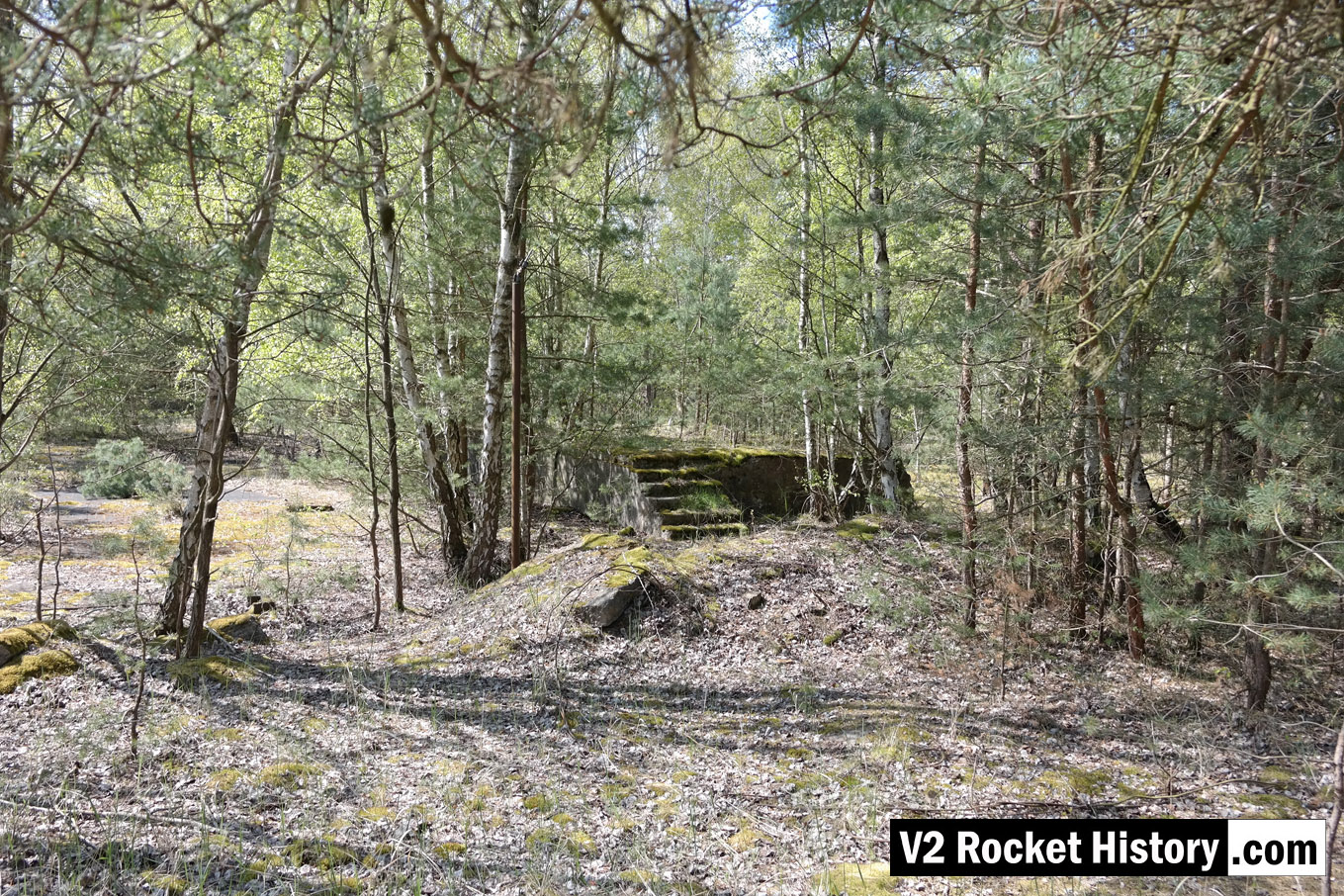
The remains of the a rail and truck loading stage located in the long oil storage shed adjacent to the IW repair and maintenance hall (IW R&MH) are substantial and have intact steadying chains along the south edge of the platform. There are access steps to the west and east ends (east shown). This loading stage was originally furnished with a wooden platform.
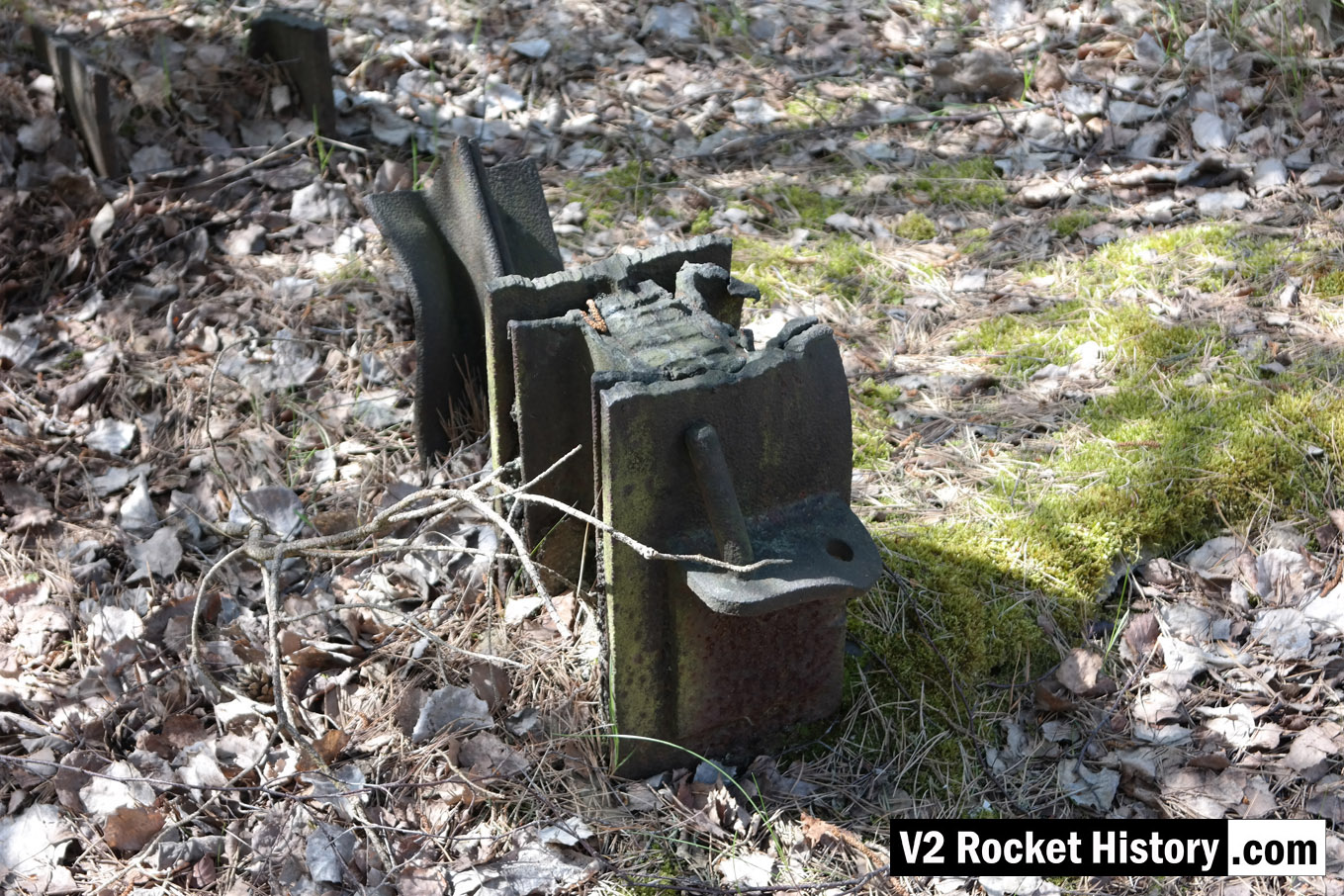
Photo shows the cut stump of an heavy upright support girder. The ragged profile of the cut shows that it has been cut down with an oxygen and gas torch or possibly a larger fuel and oxygen device like a thermal lance. The steel support still has the bottom support pin for a large door. Note that although the girders have been gas-cut there is a great deal of mechanical damage to the steel work that was not caused by the cutting work. Considerable force would be required to bend the middle girder in the way shown, even if it was much longer at the time the bend was created. The upper superstructure of the storage shed may have been part demolished using a bulldozer. Or perhaps the East German Army may have used the site for explosives training – signs of demolition explosive use are in evidence nearby. The map under the album presentation of this picture shows the exact location of the girders.

Ernst Steinhoff, chief of the BSM workshop (Guidance and Control) in the development works Peenemunde.
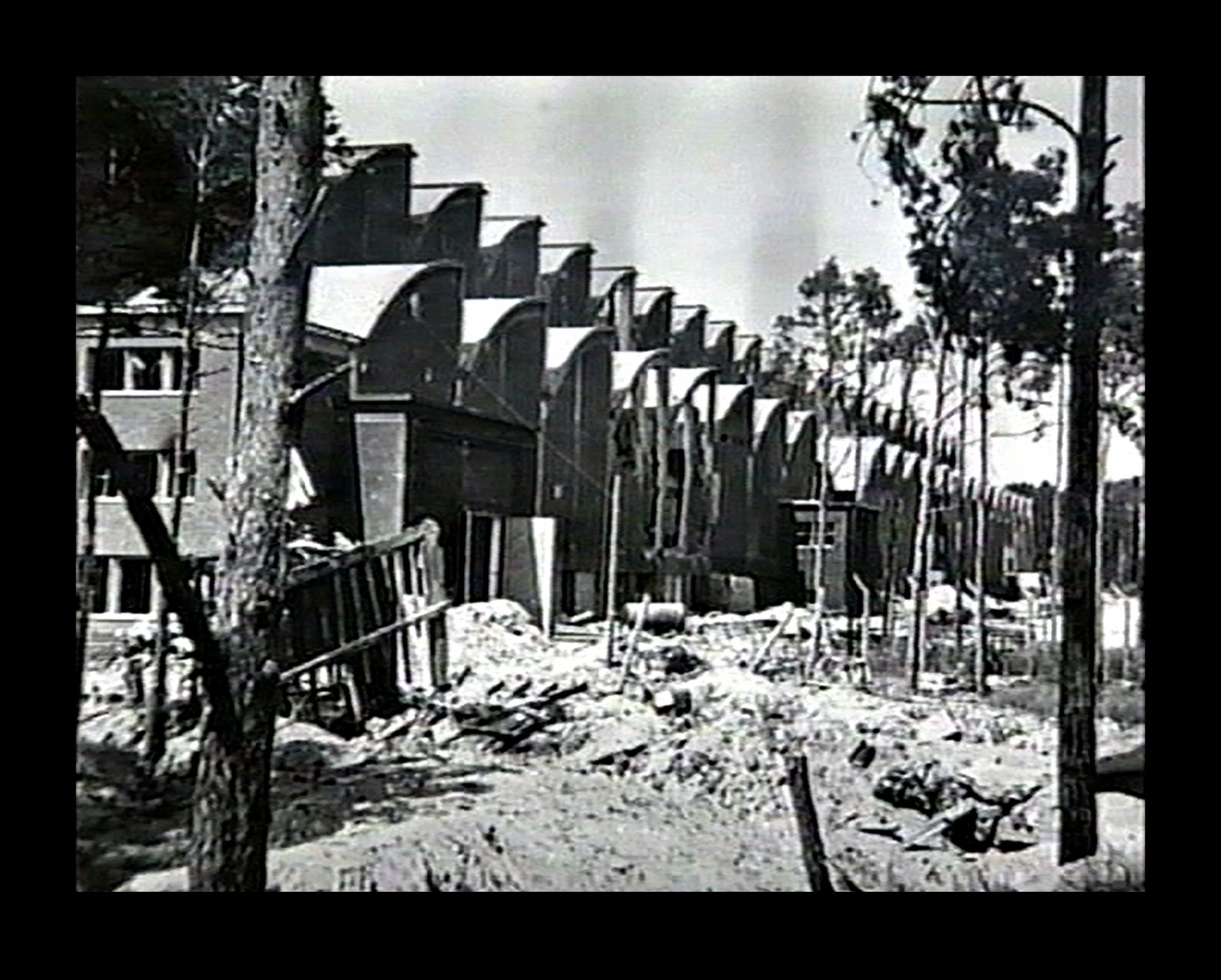
Bomb damaged F1 factory 1945. The huge V2 rocket factory shown badly damaged by air attack at the end of the war in May 1945
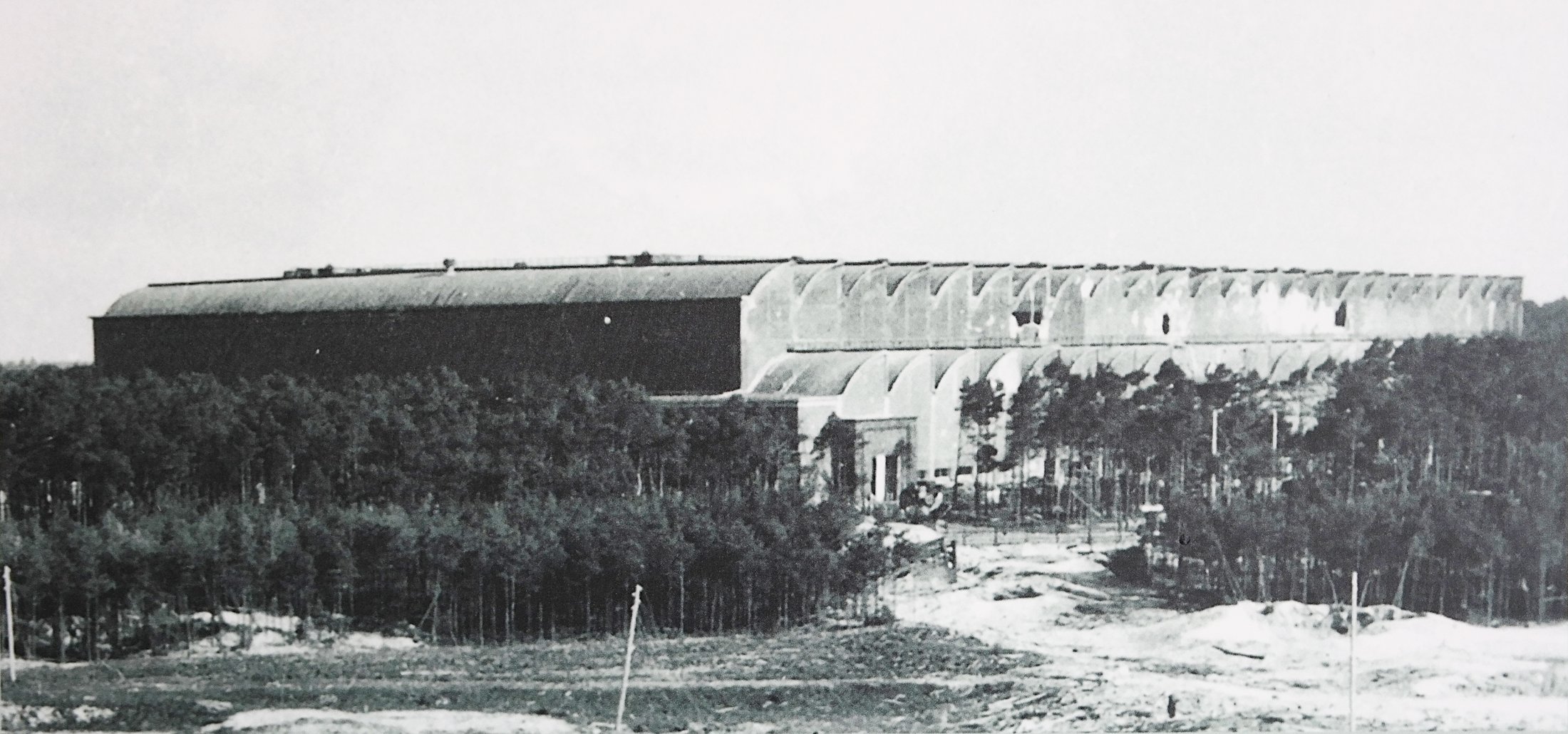
A rare photo of the giant F1 production hall taken not long after the RAF raid of 17/18th August 1943. F1 was a forced labour camp with at least 600 prisoners living within the factory and at least eleven were killed in the raid. Parts of the electrified barbed wire fence can be seen close to the factory building, in the clearing in the middle of the photo. Two anti aircraft gun emplacements can be seen on the roof at the front of the building. Holes in the side walls of the upper vaults can be seen as well as the damage to lower vaults 9 and 10 (counting from left) from a direct hit in this region. Also of note are the numerous guy ropes, attached to the upper roof of the front of the building – and running down towards the trees, that are just visible in the photo. These may be supports for camouflage netting that was in the process of being fitted (by prisoner gangs) just before the raid. The work was never completed.
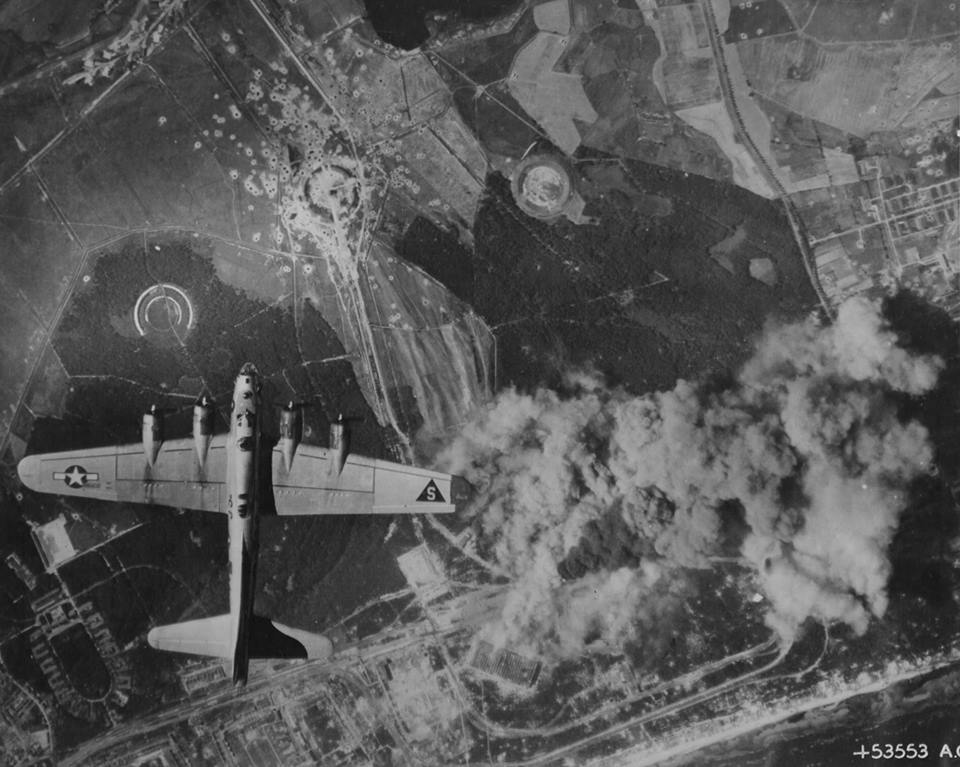
Peenemünde: Werk Sud attacked by US bombers August 1944 in a daring daylight raid. The two large halls F1 and IW in the lower middle of the photo are under direct attack and smoke can be seen originating from both buildings. Although the August 1944 raids did little to interrupt the volume manufacture of the V2, as virtually all manufacturing and assembly of the missile had moved to central Germany, the raids did bring to an almost complete halt the last small amount of manufacturing work still competed in the giant halls of Werk Sud.

Testing fuel injectors


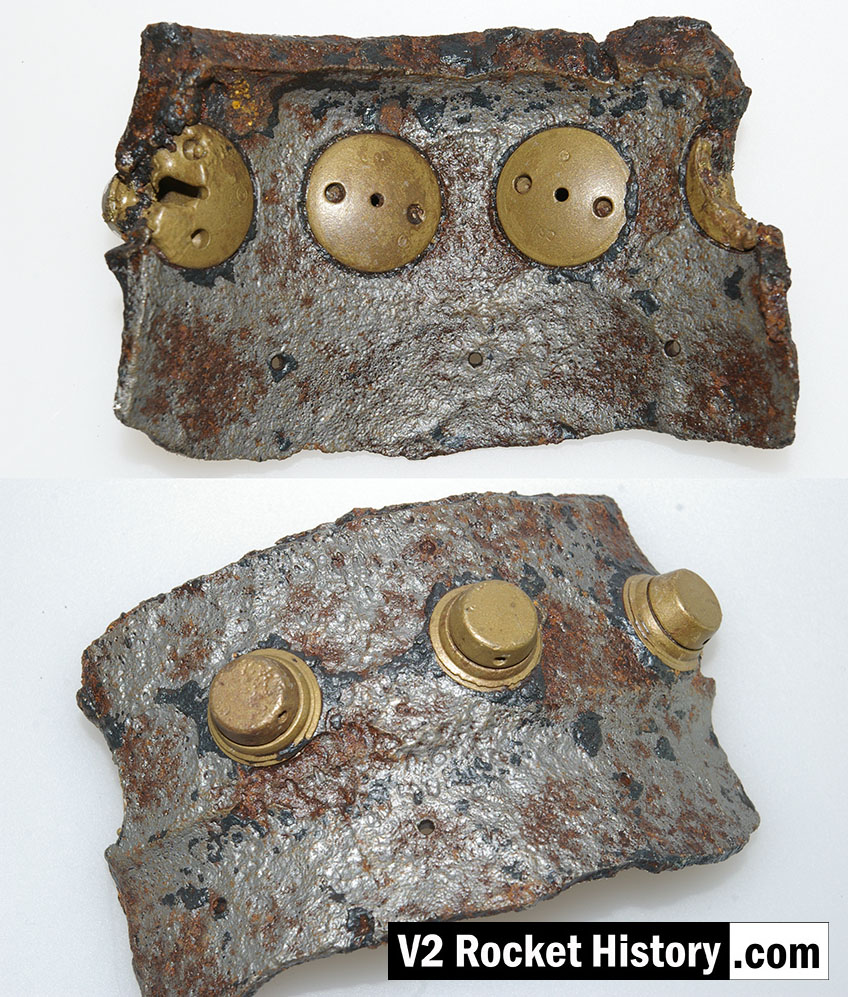
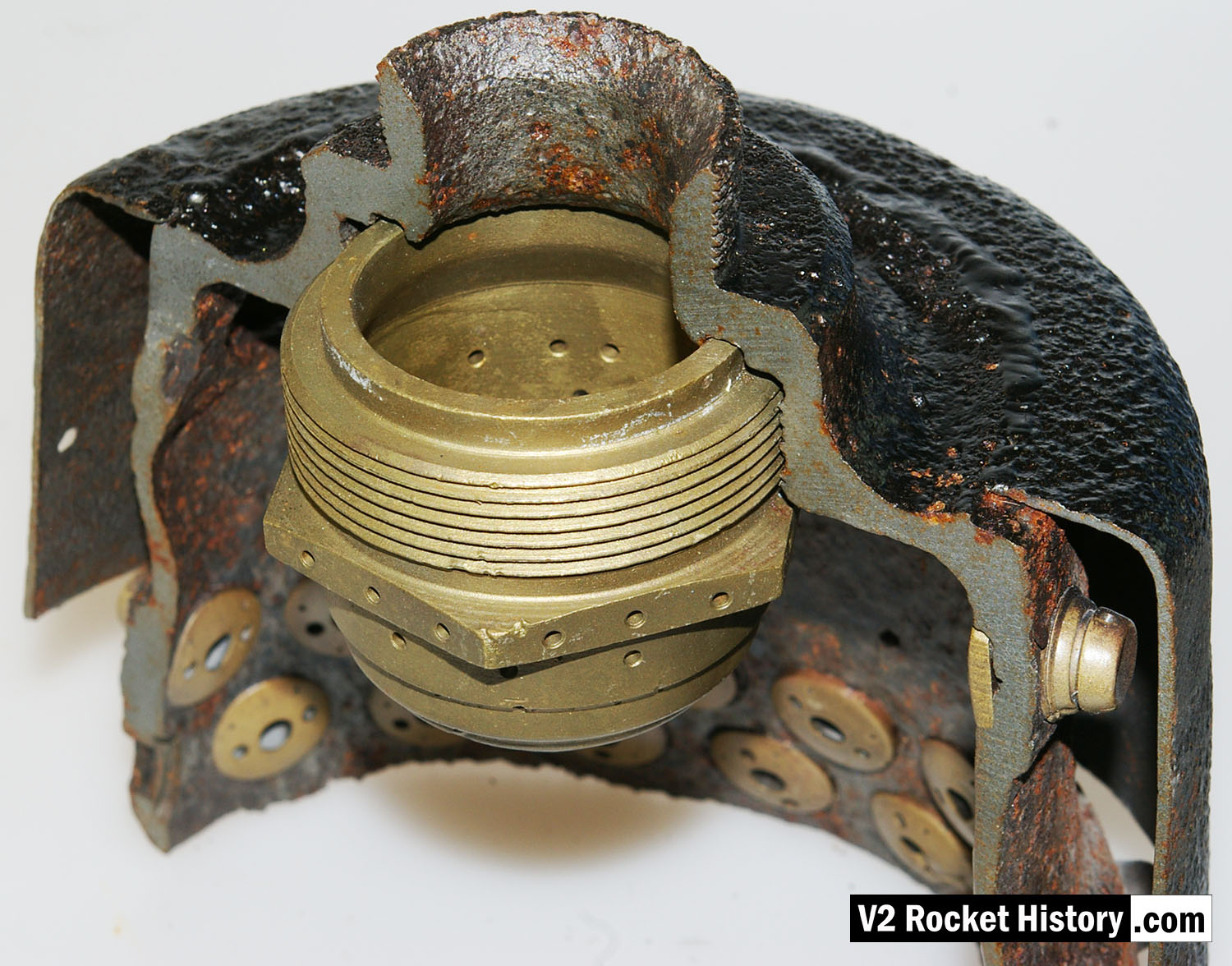
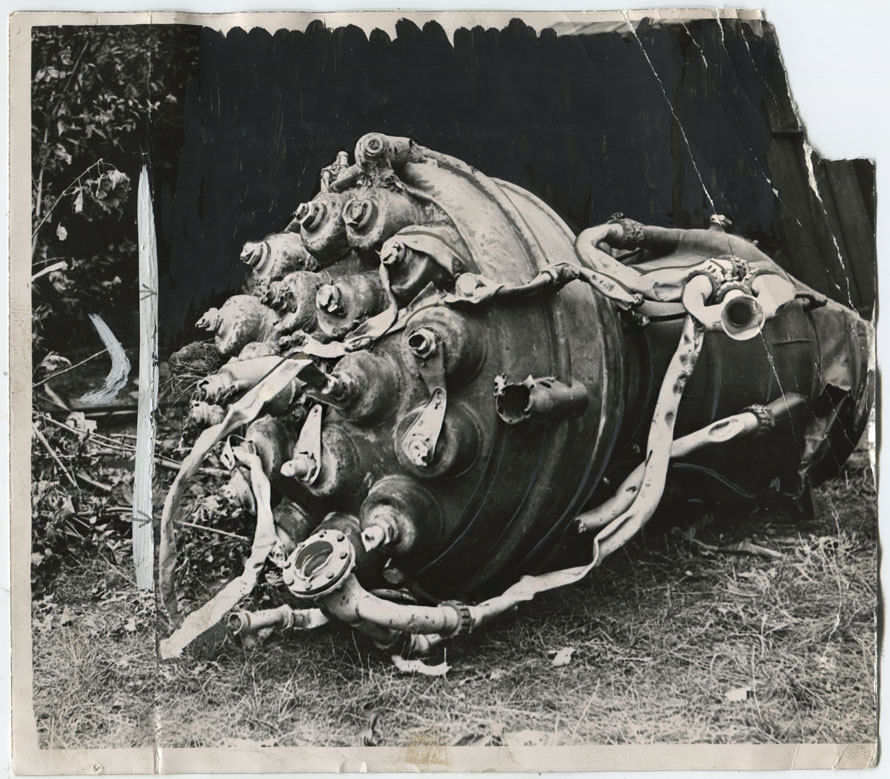
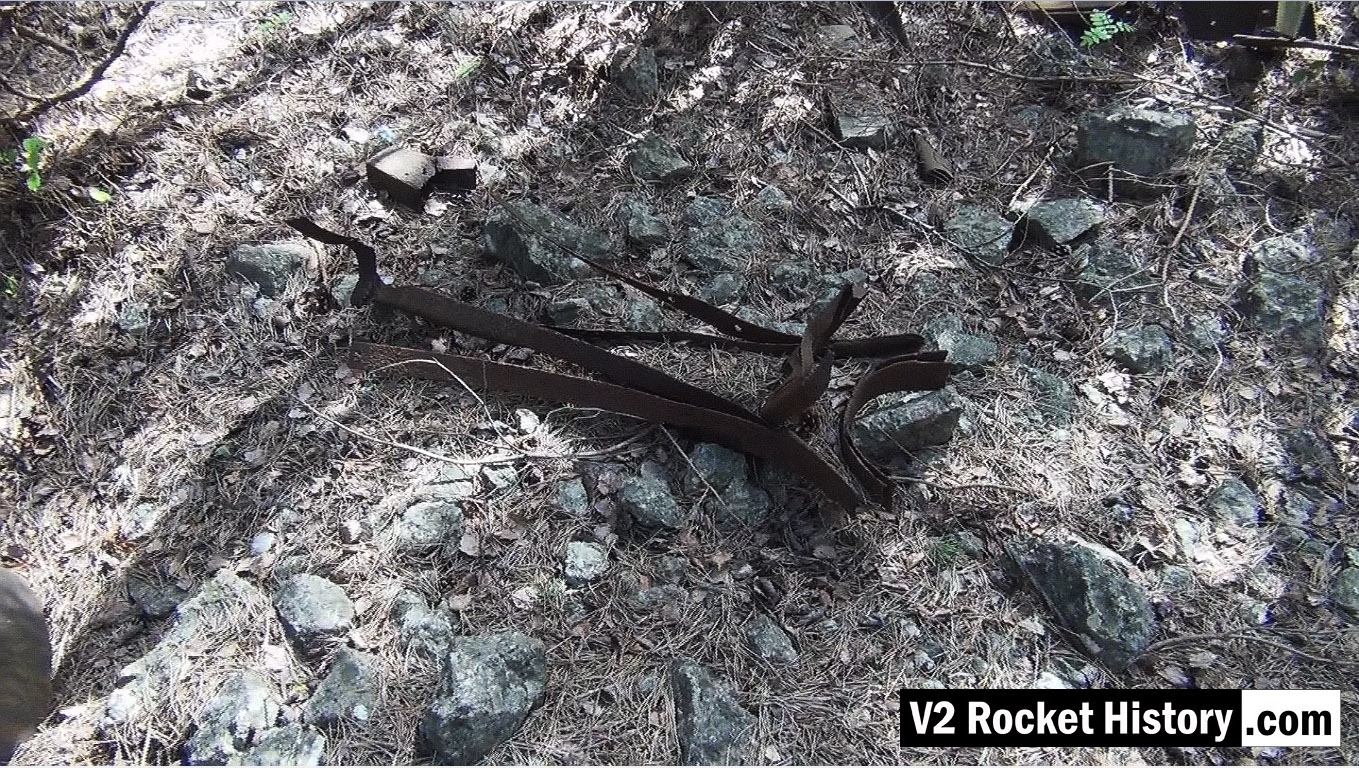

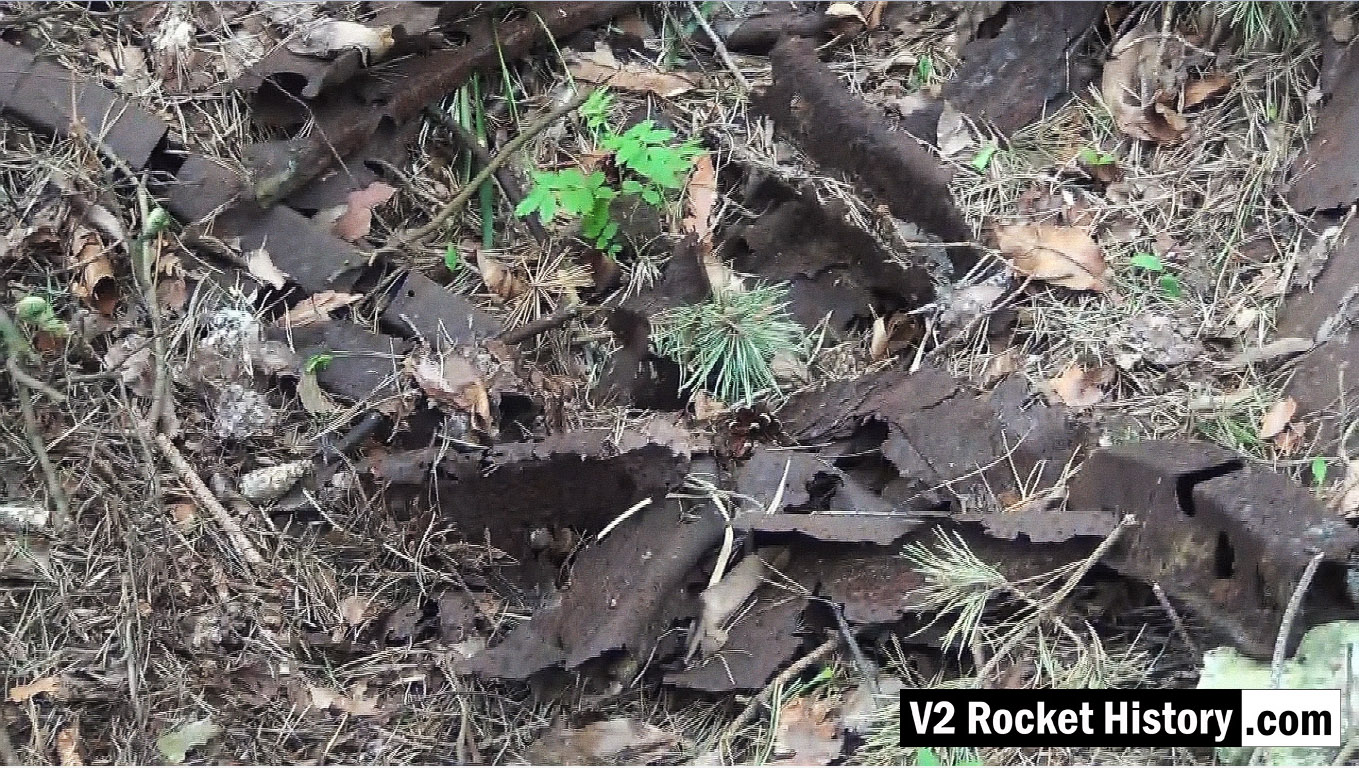
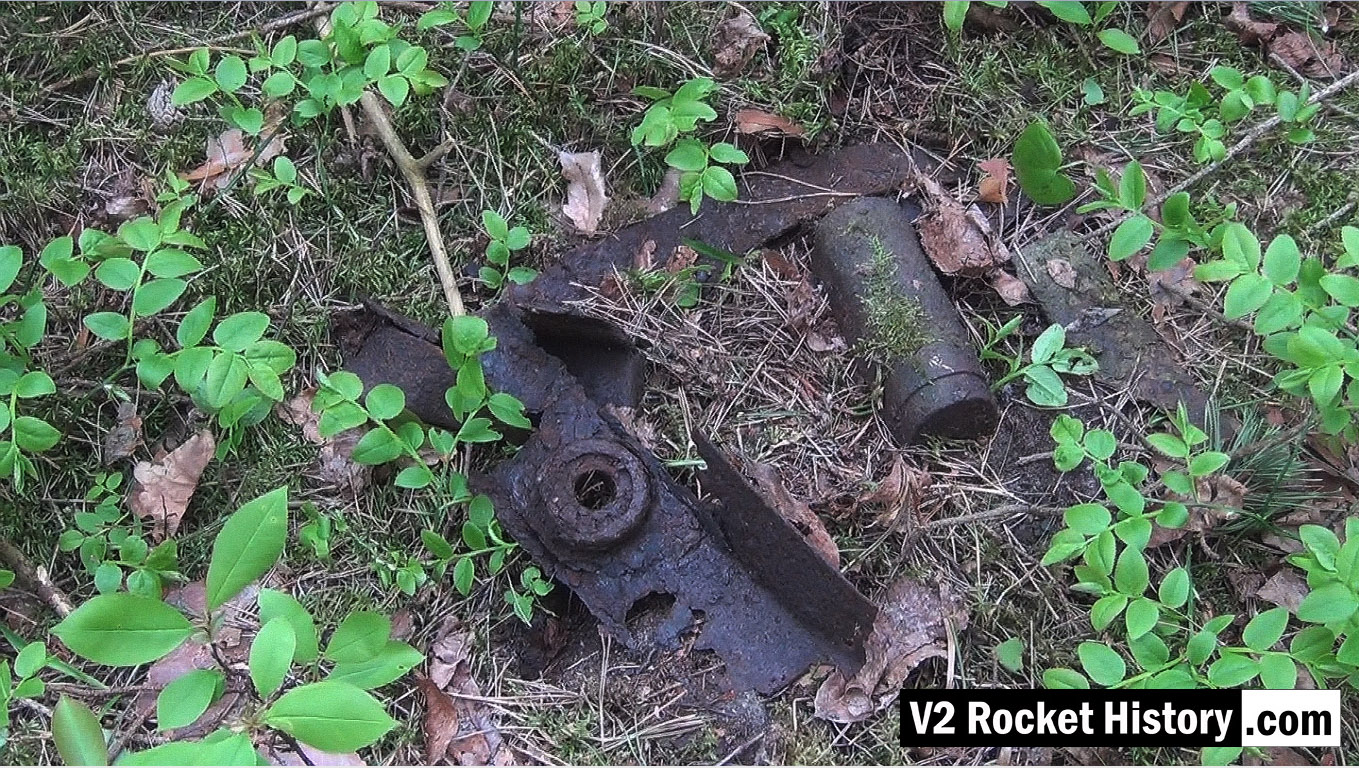
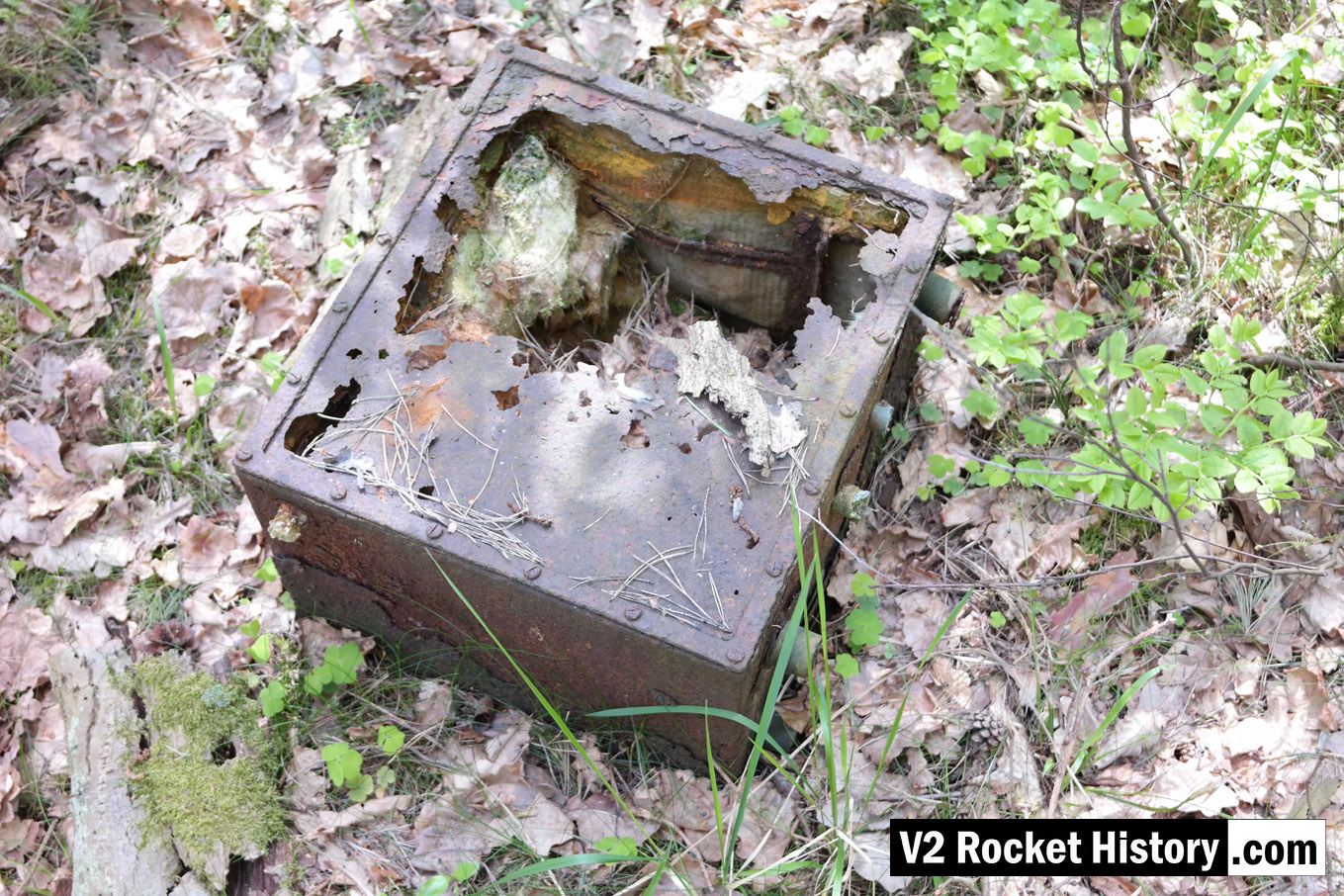
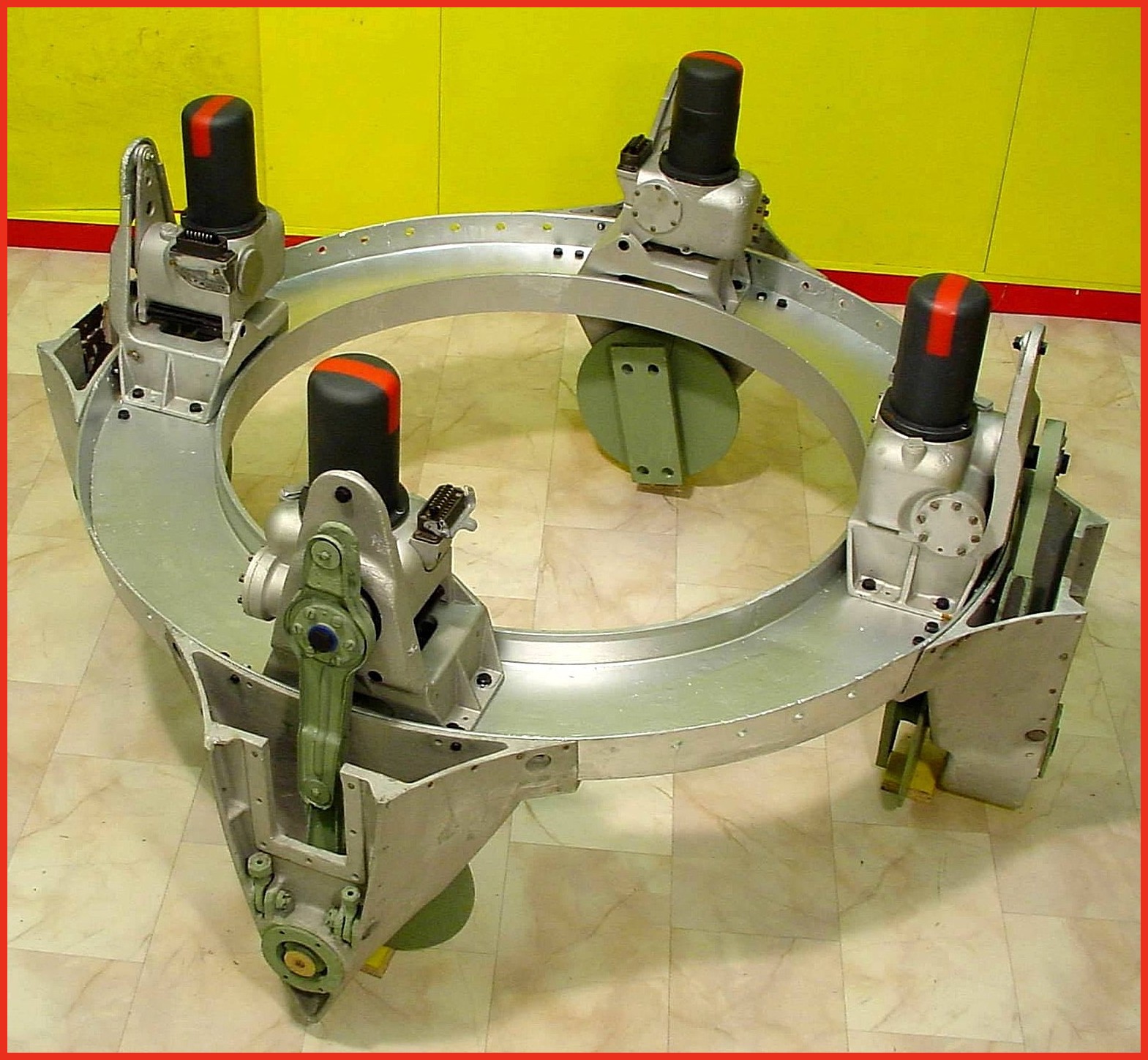
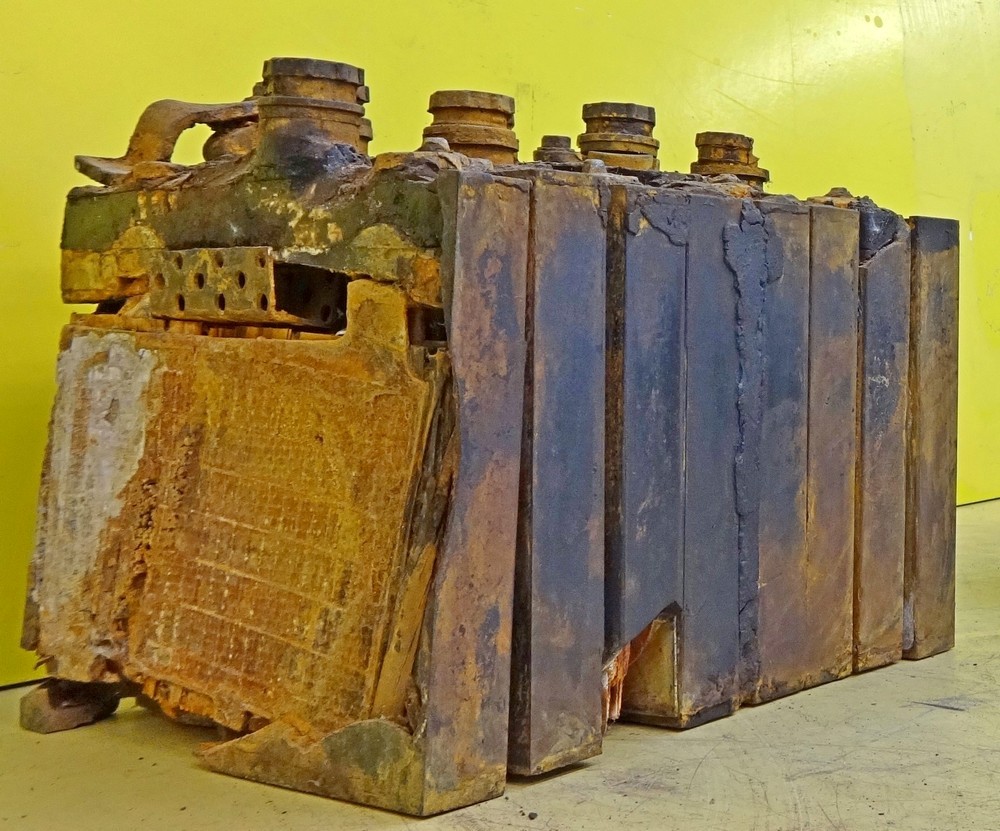
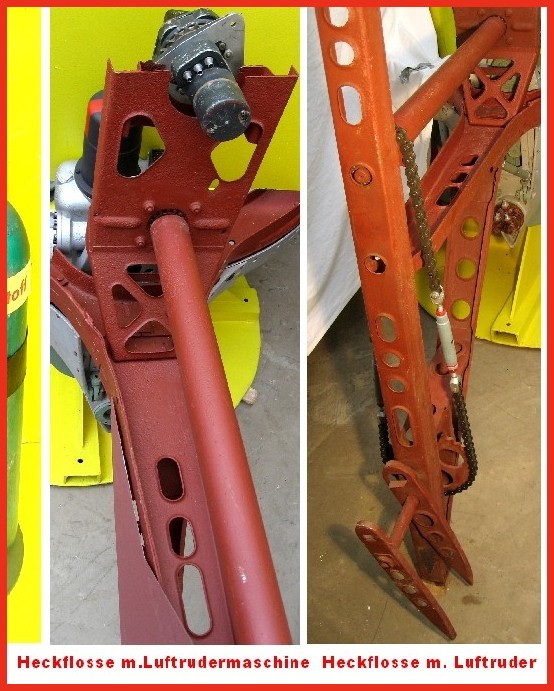
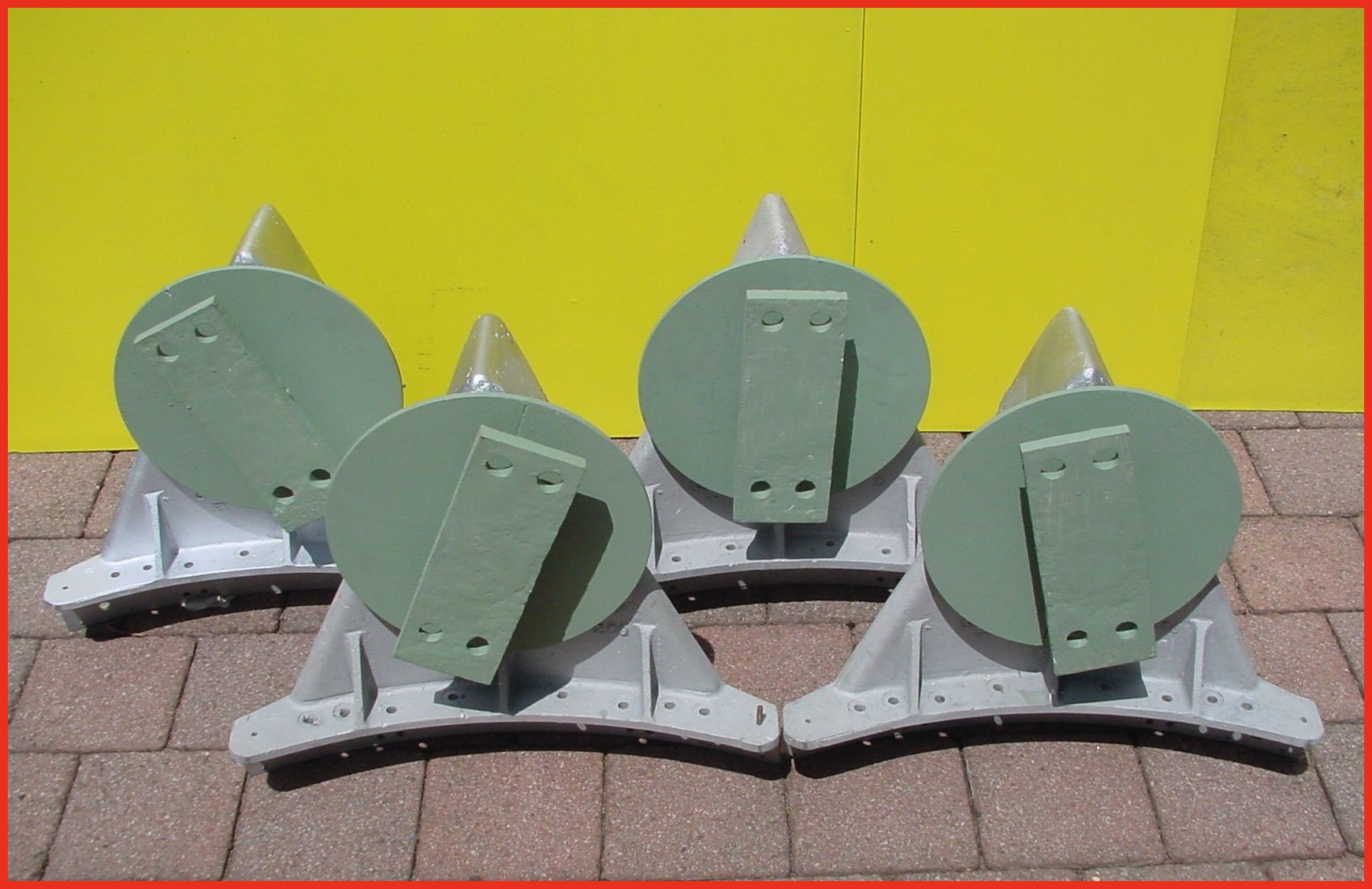
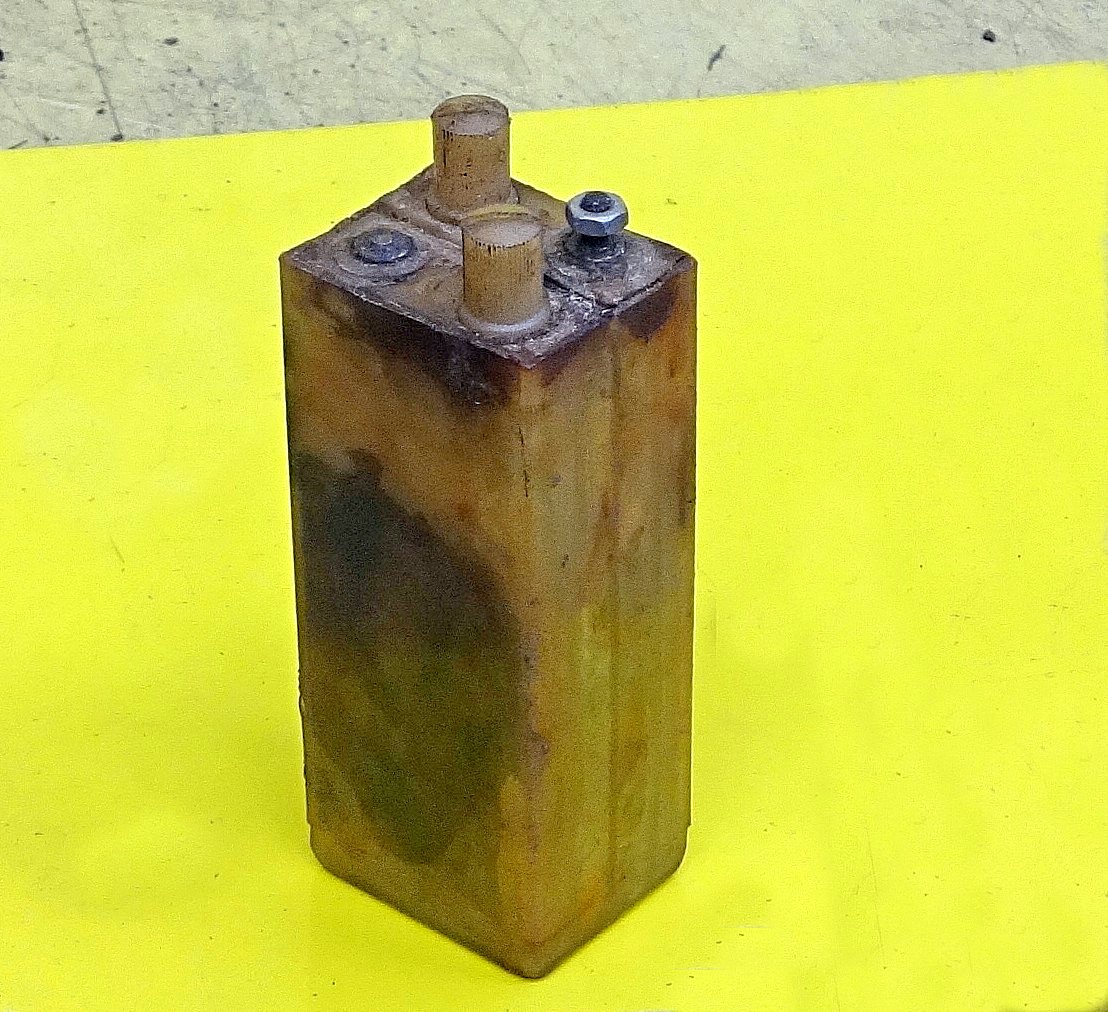
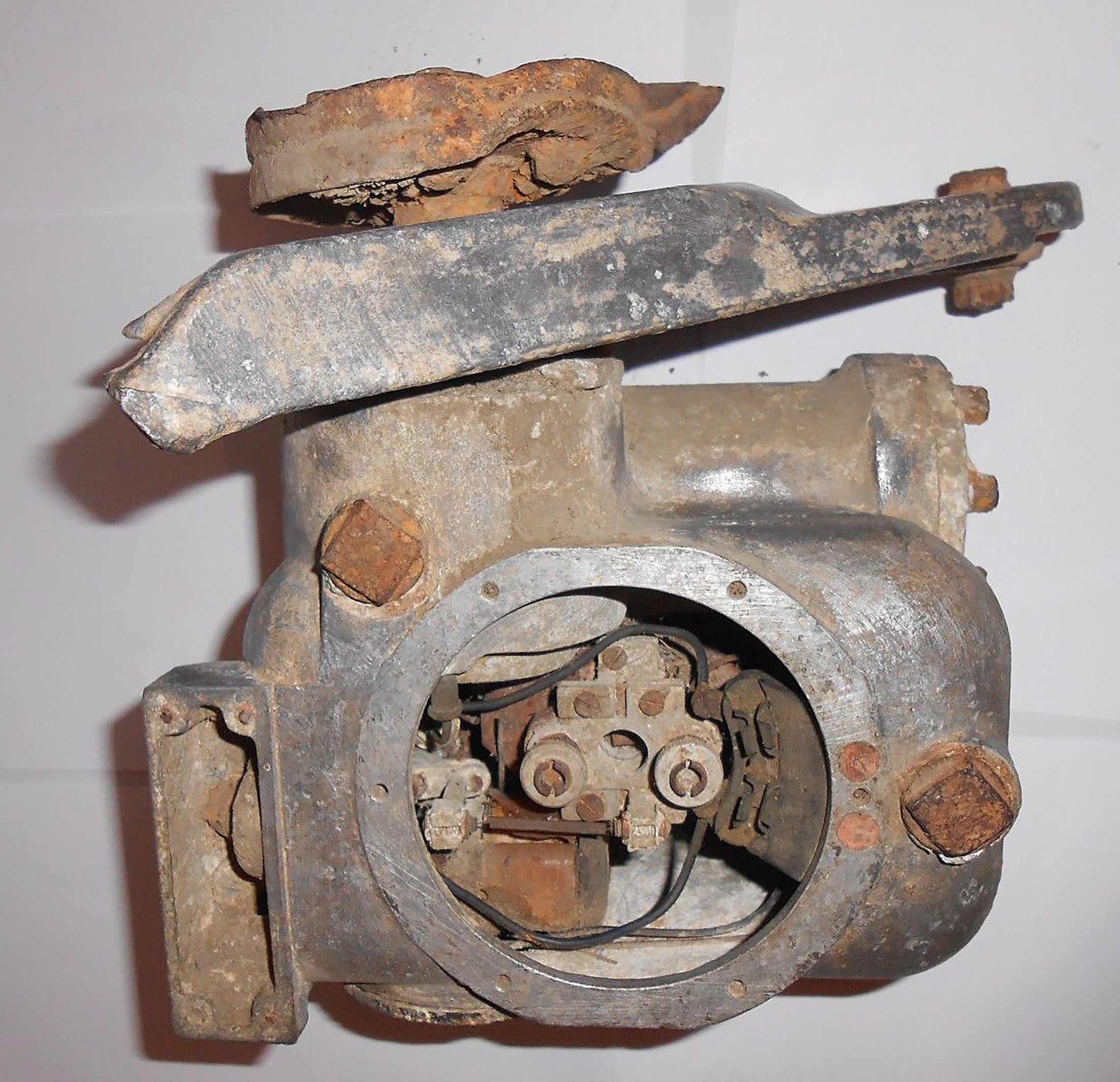
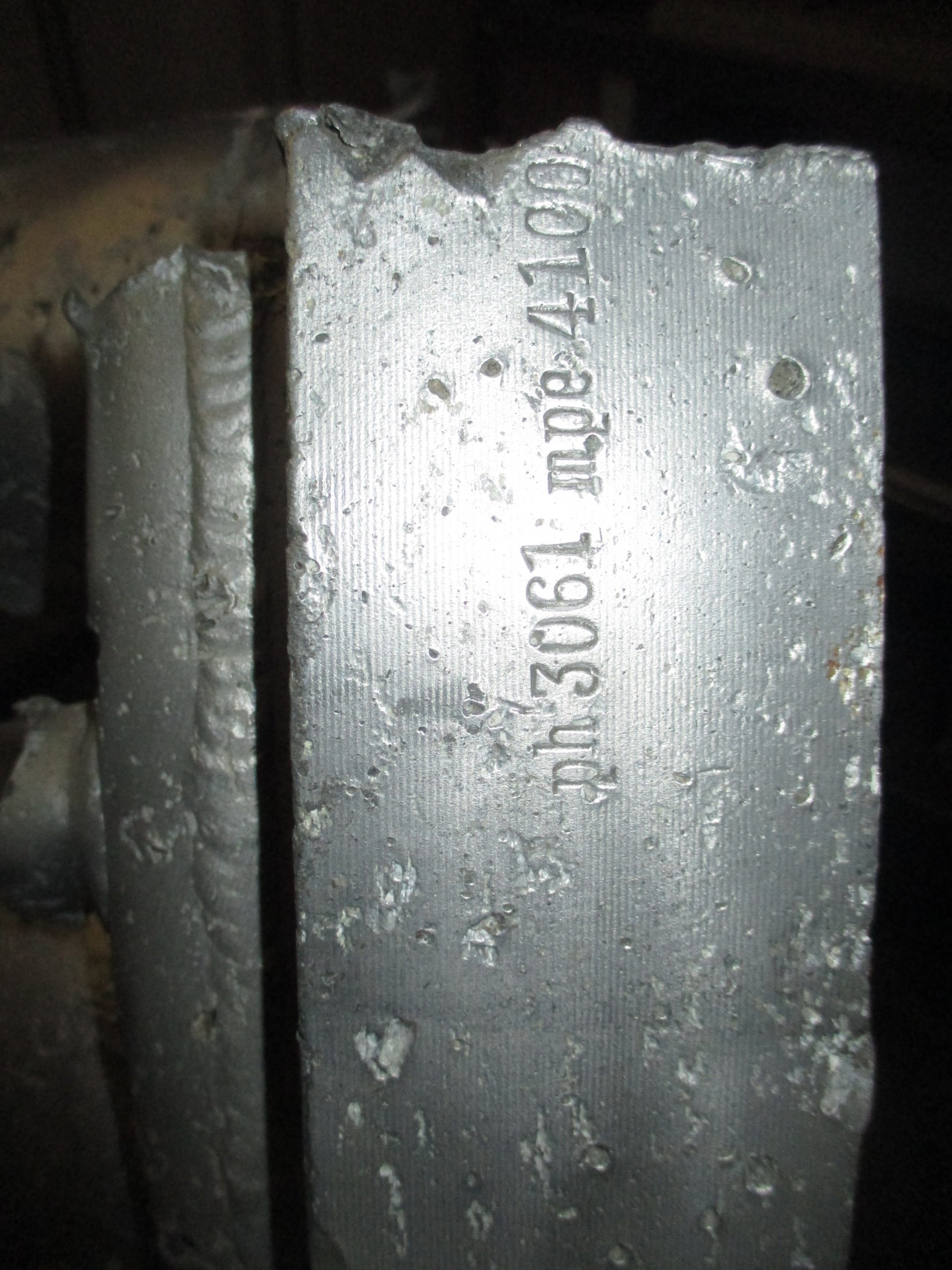
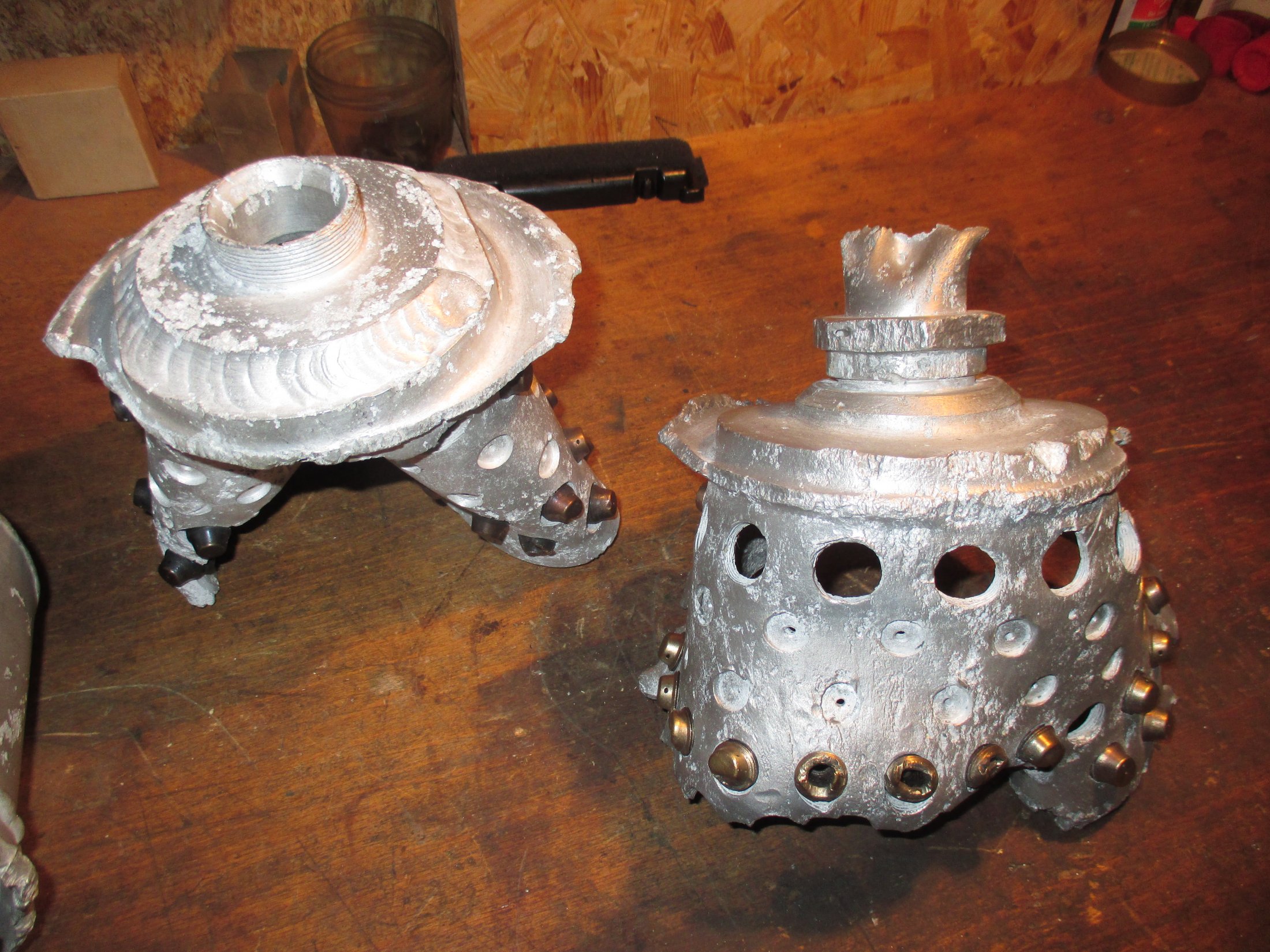
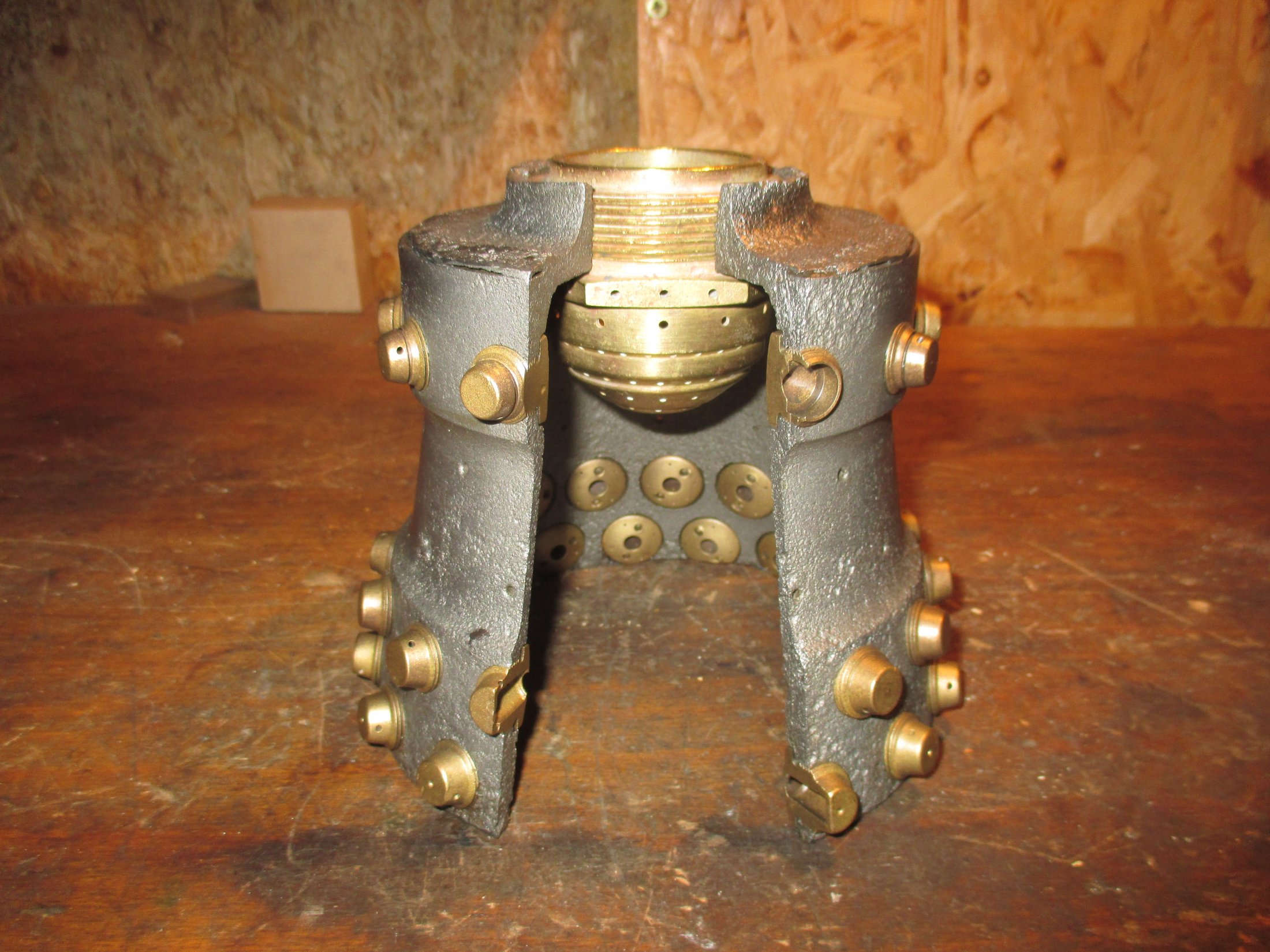
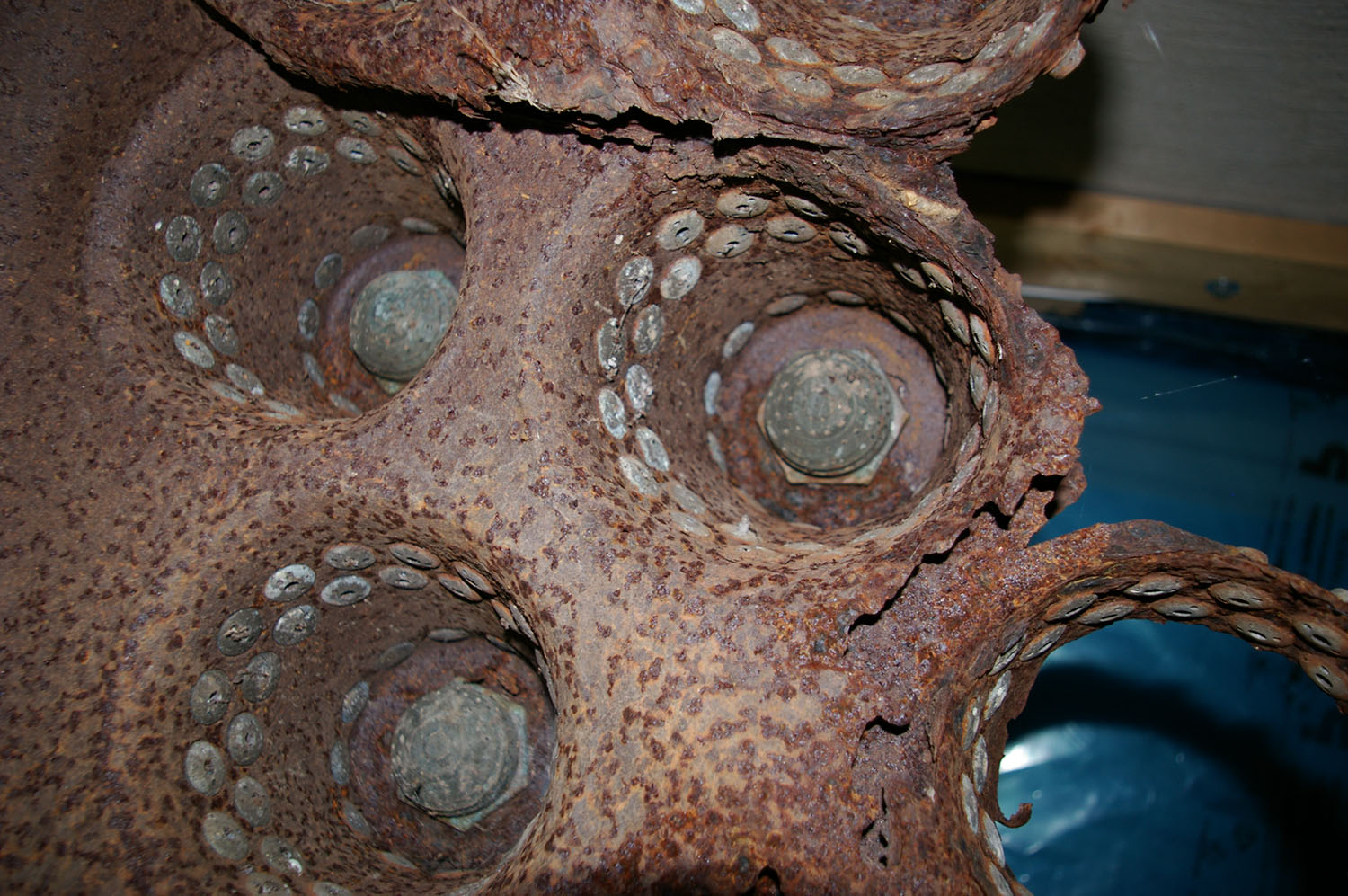
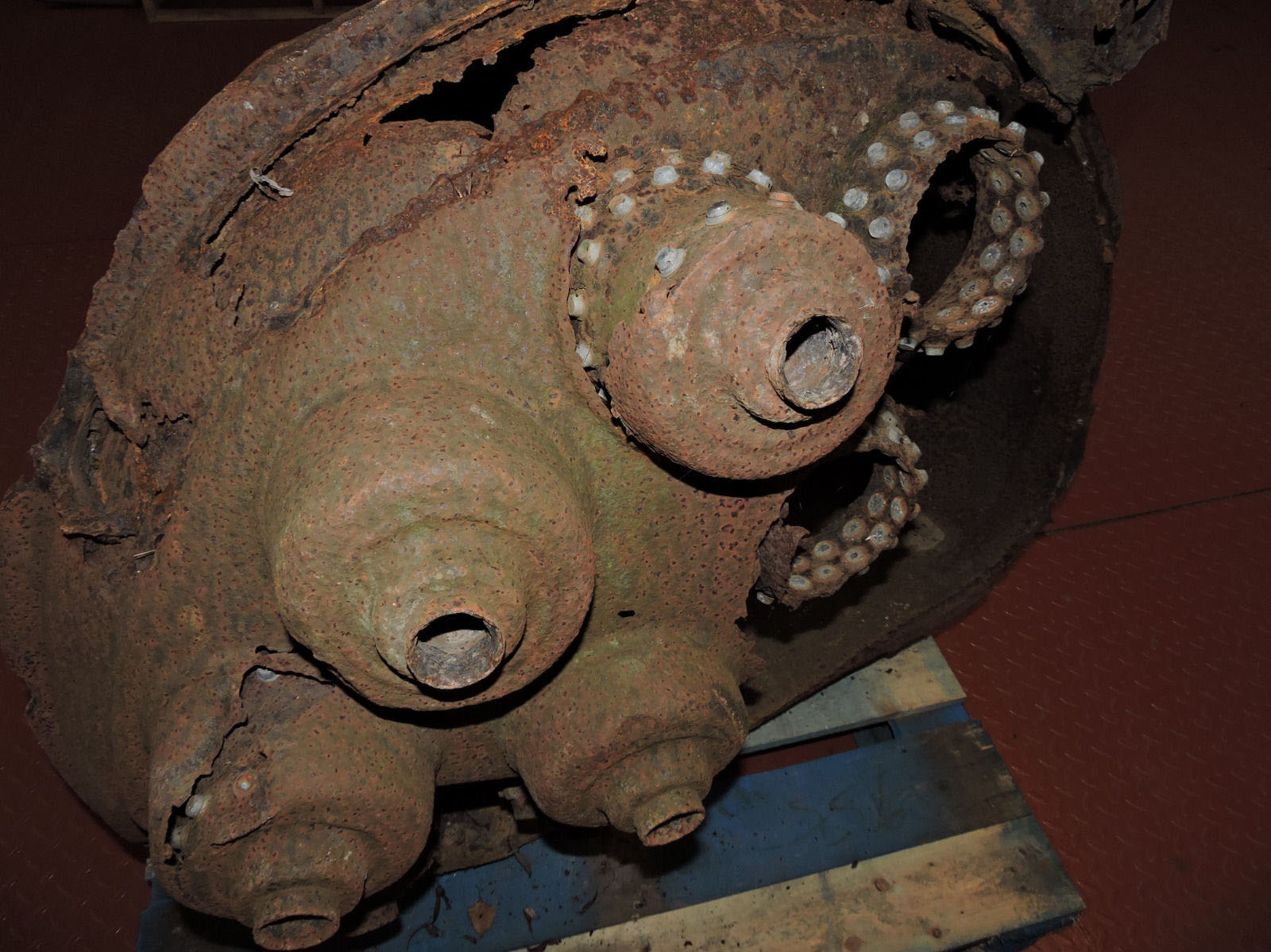
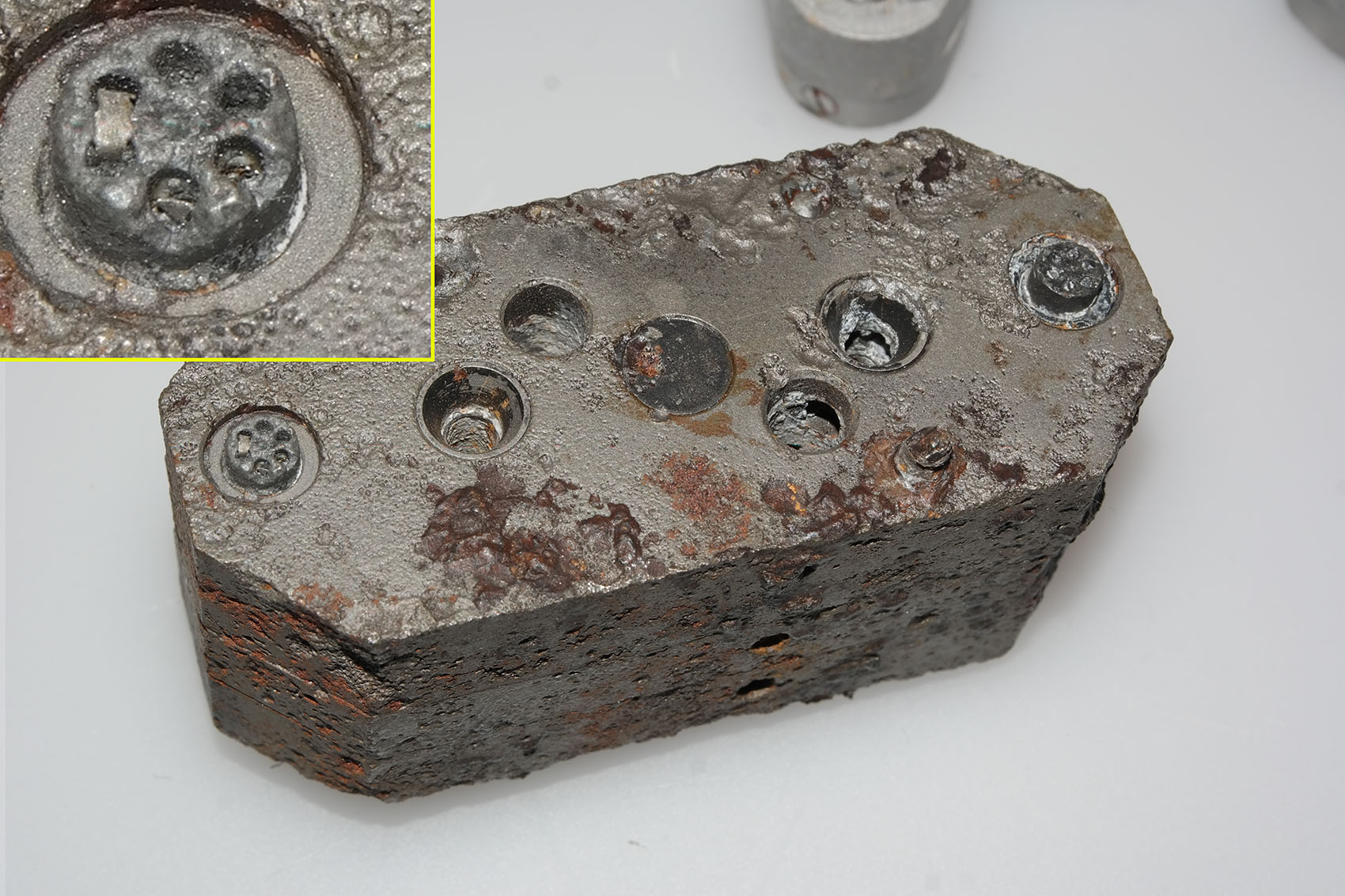
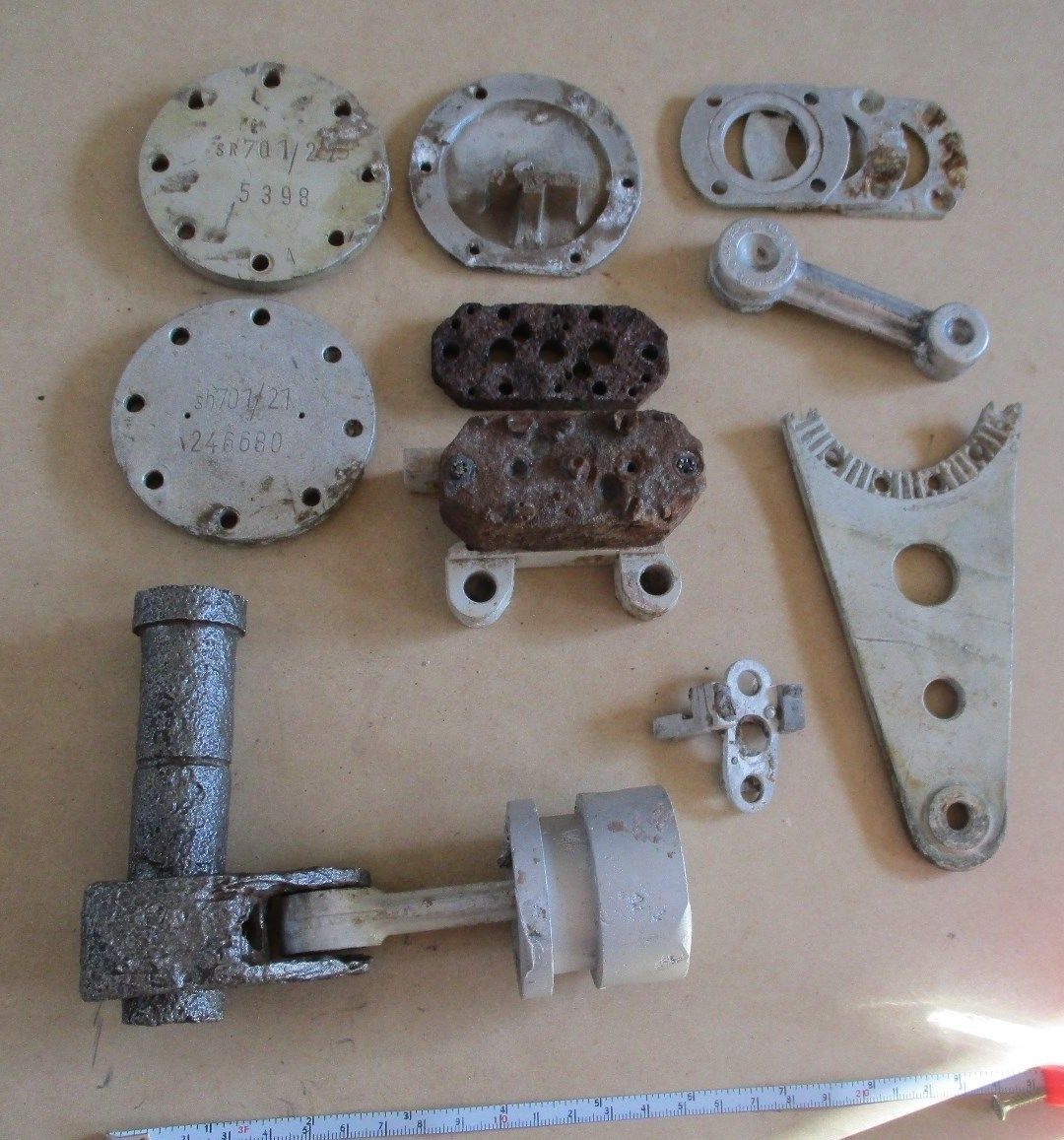
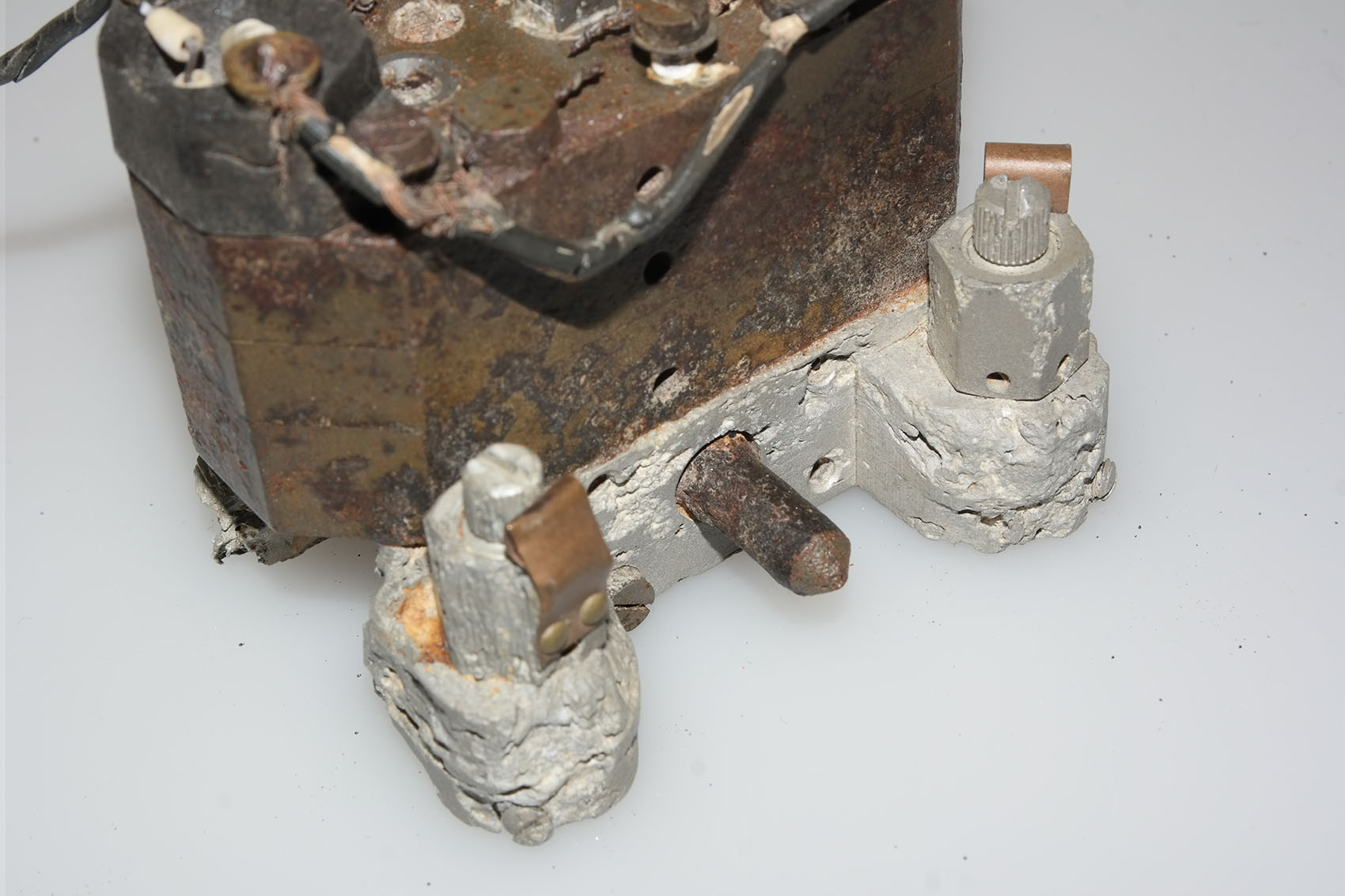
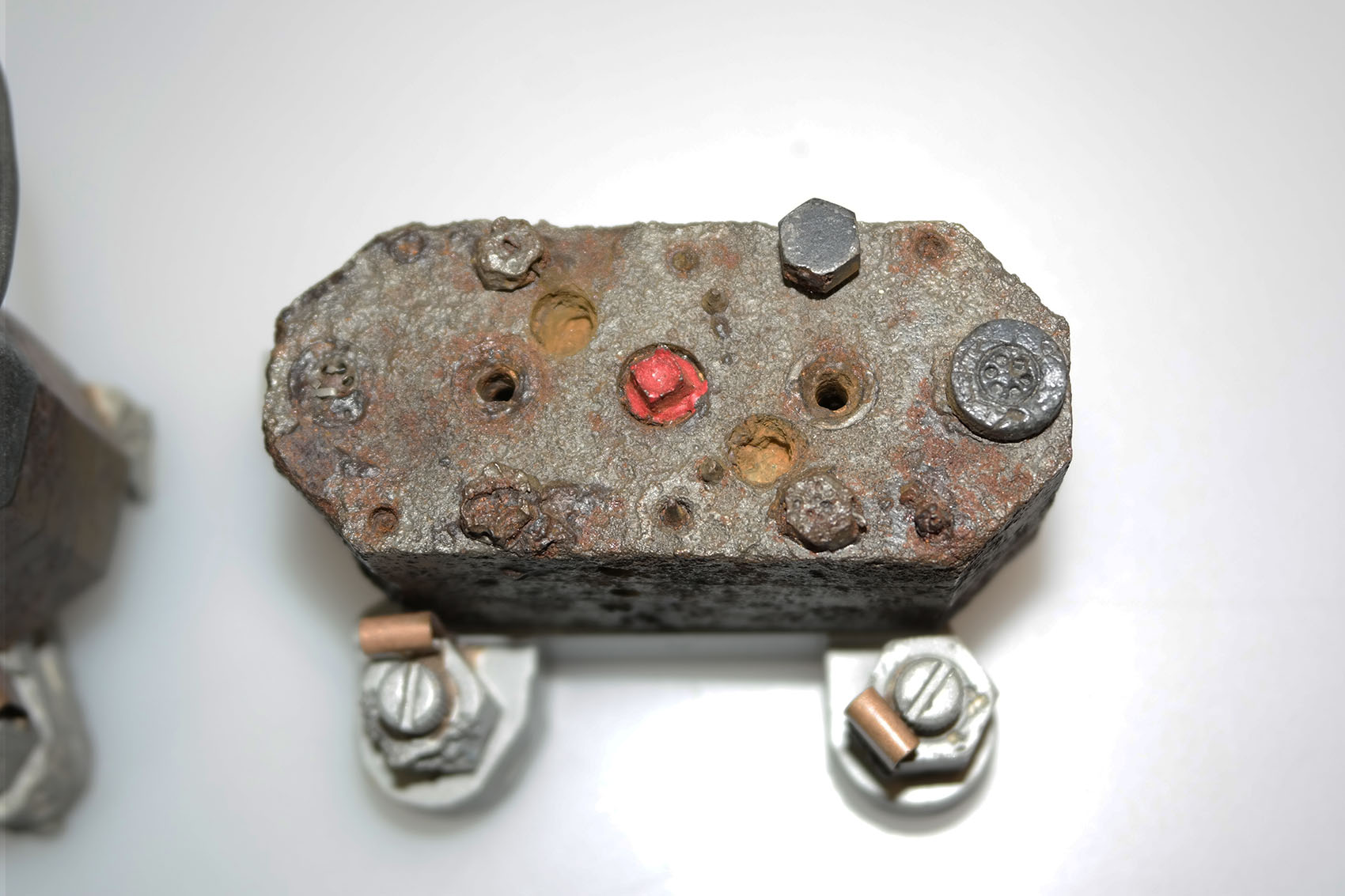
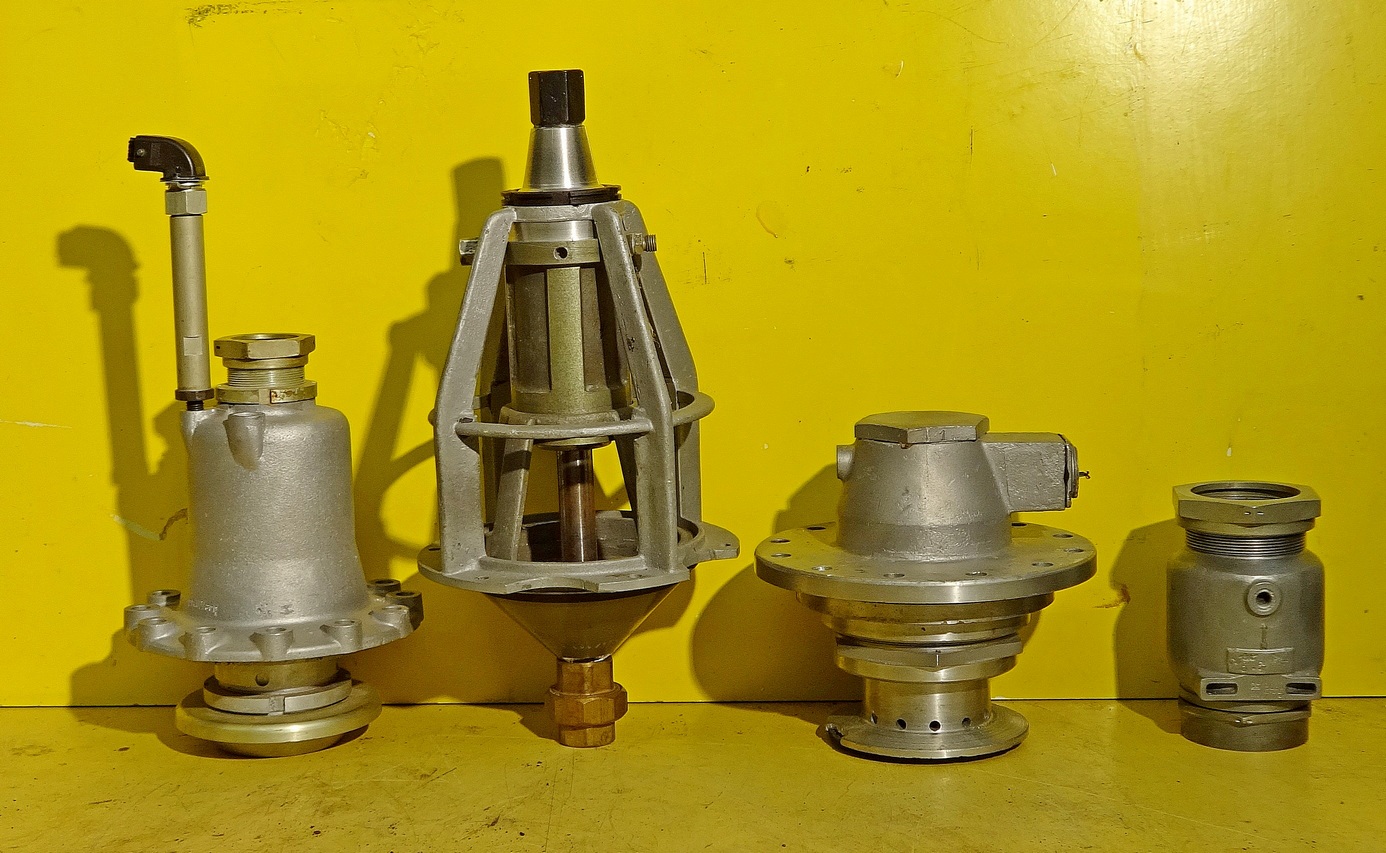
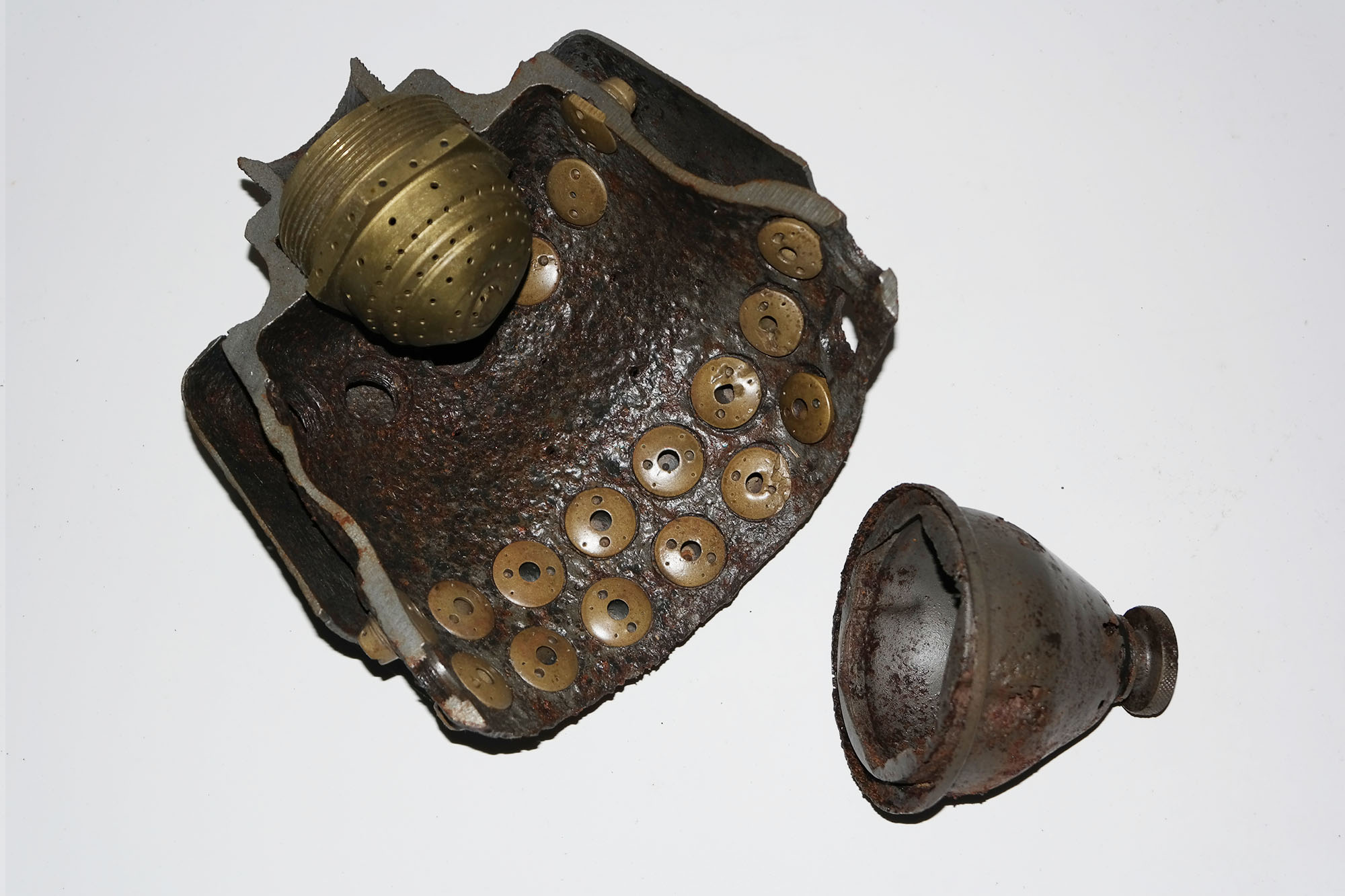
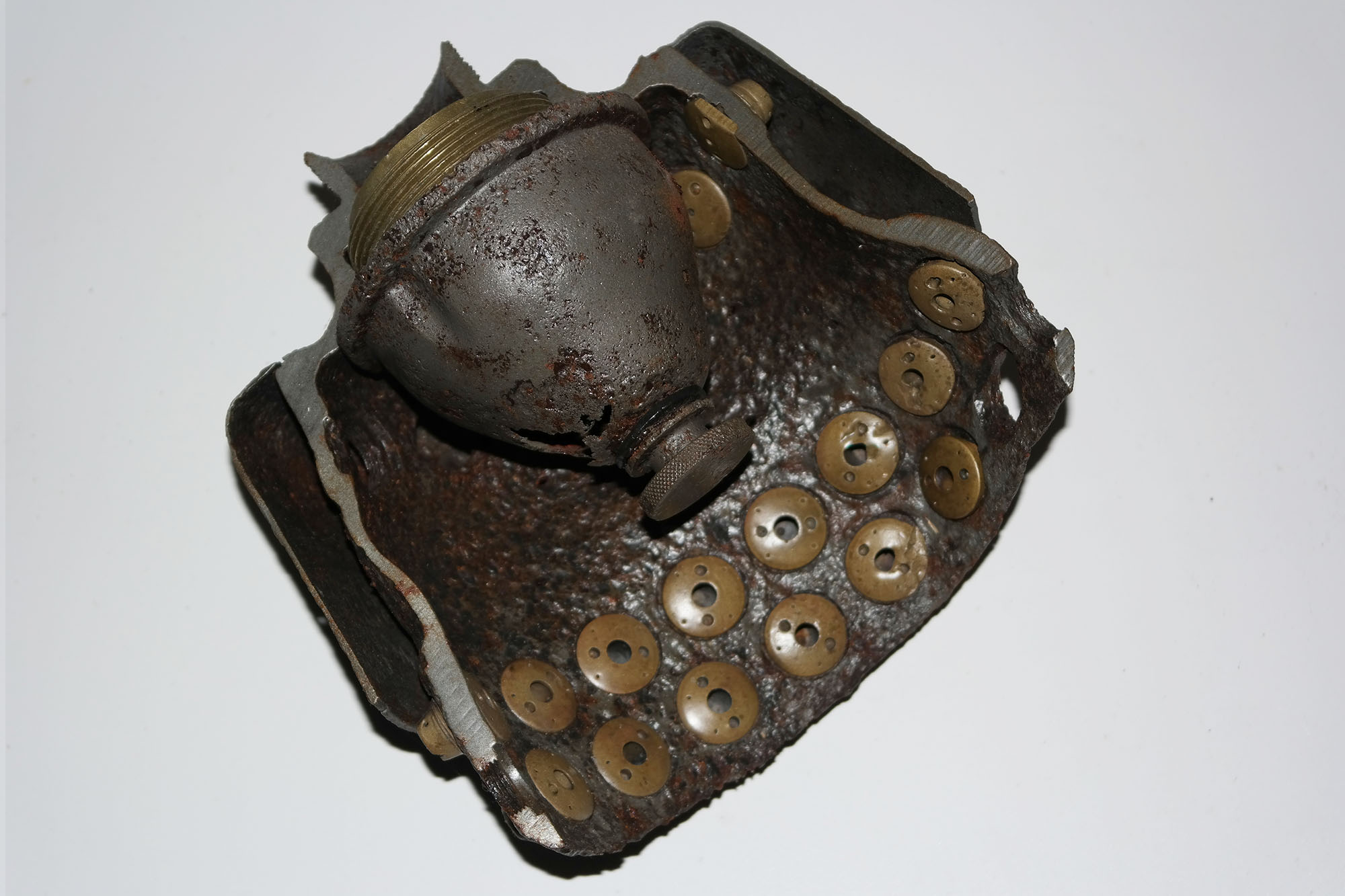
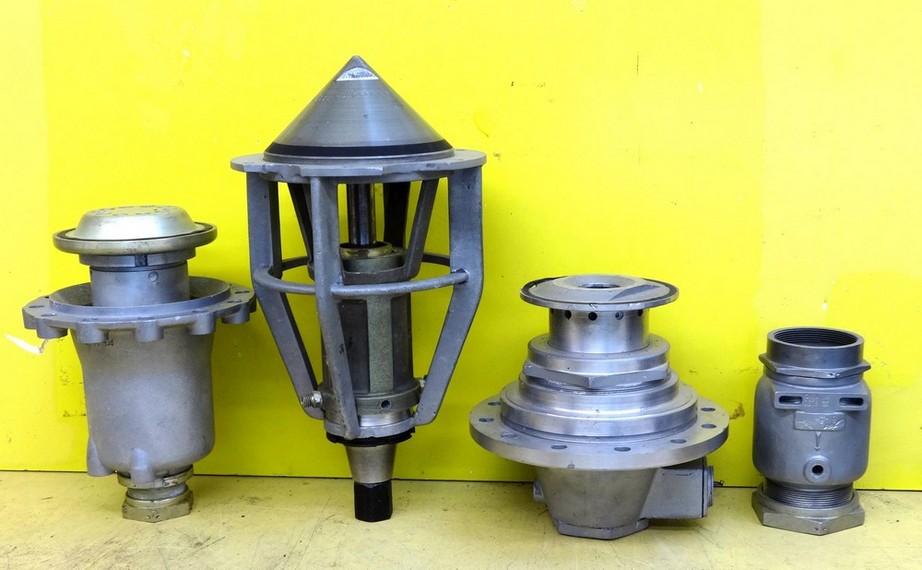
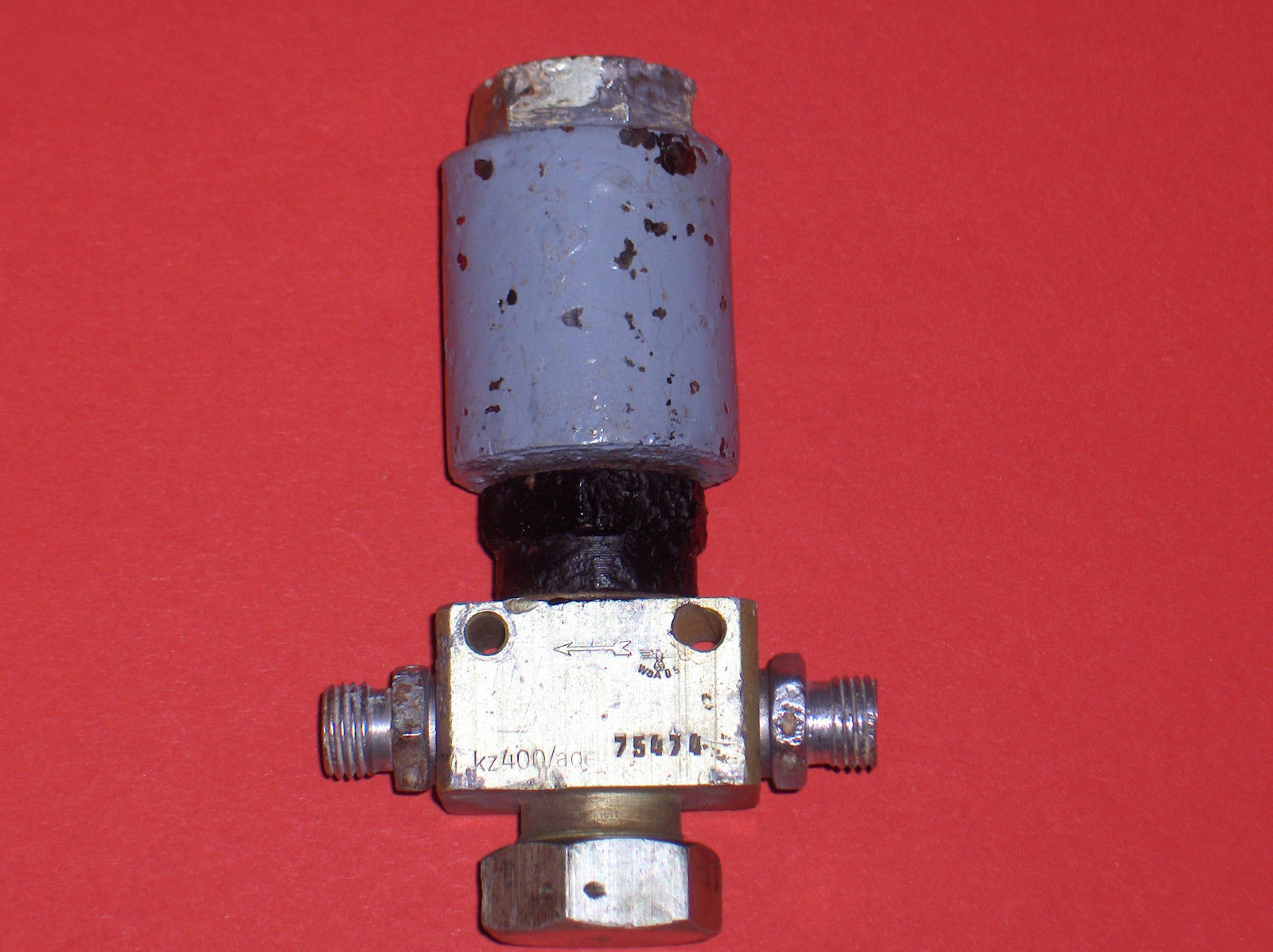
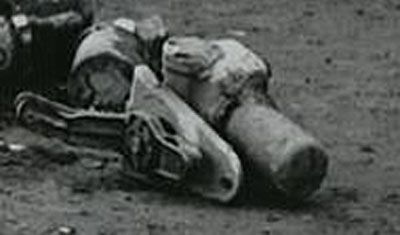
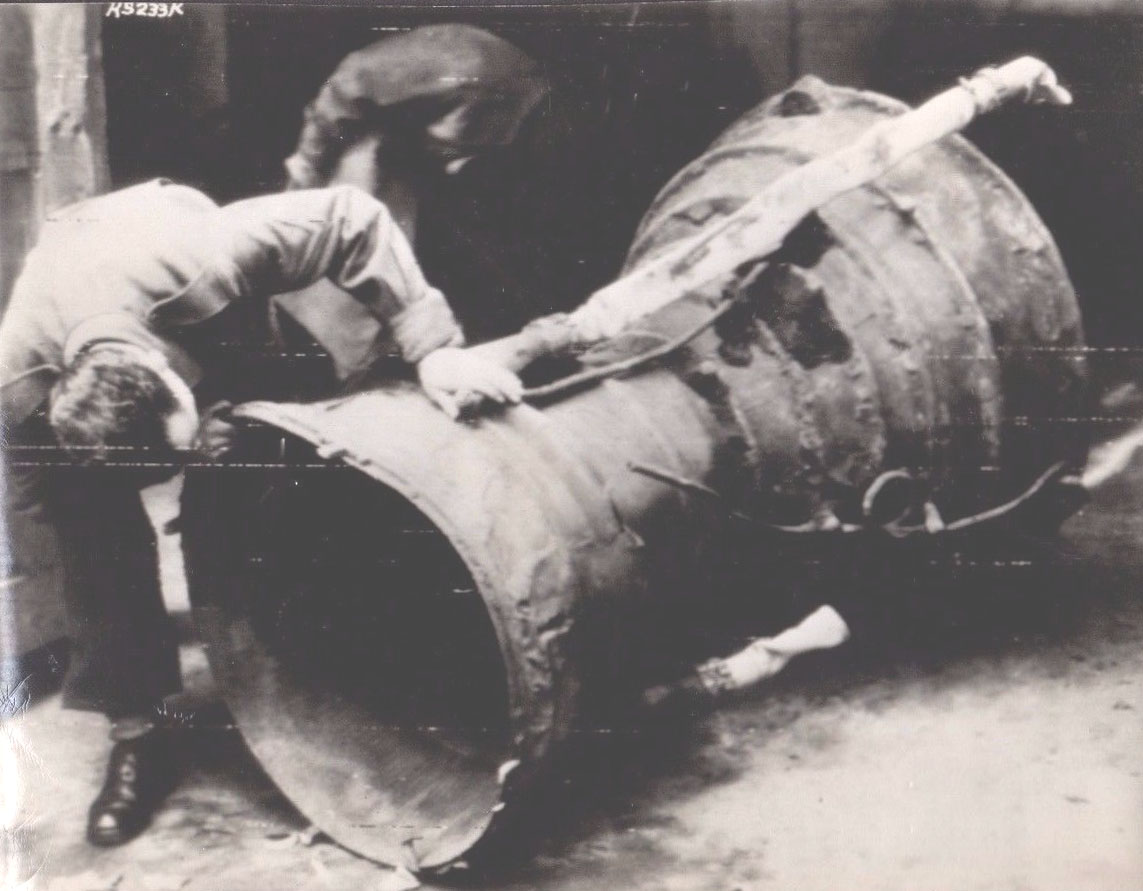
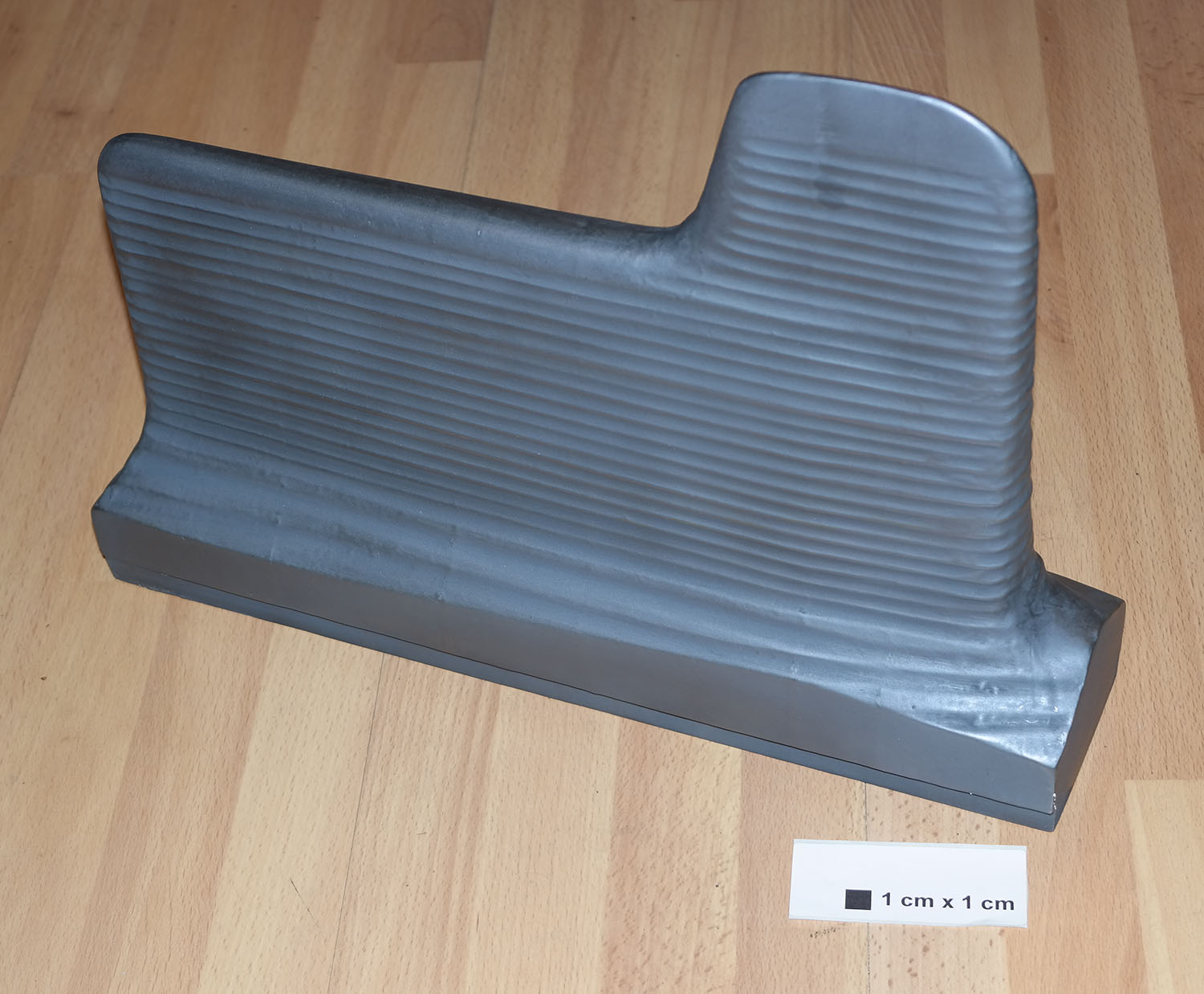
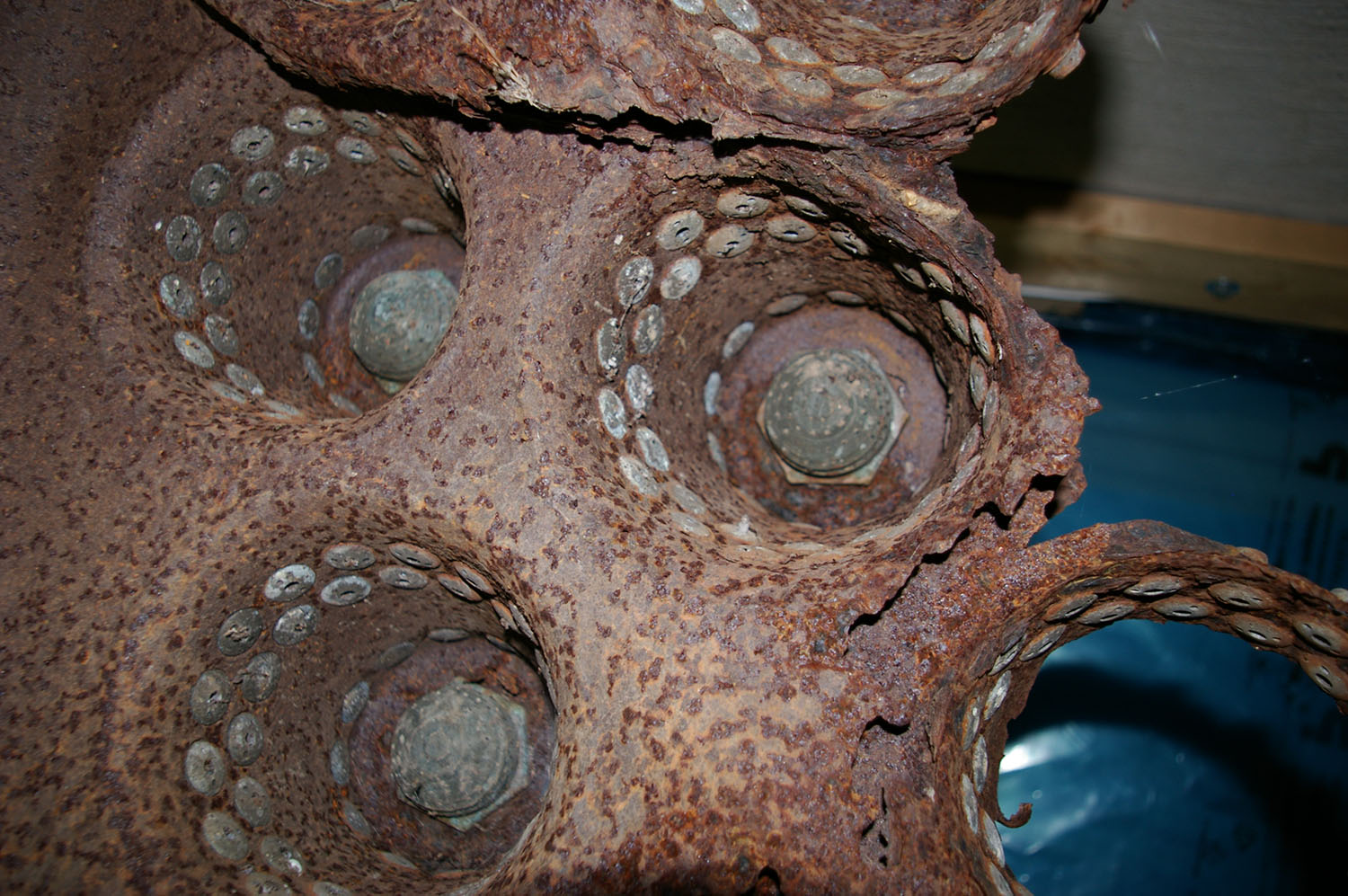
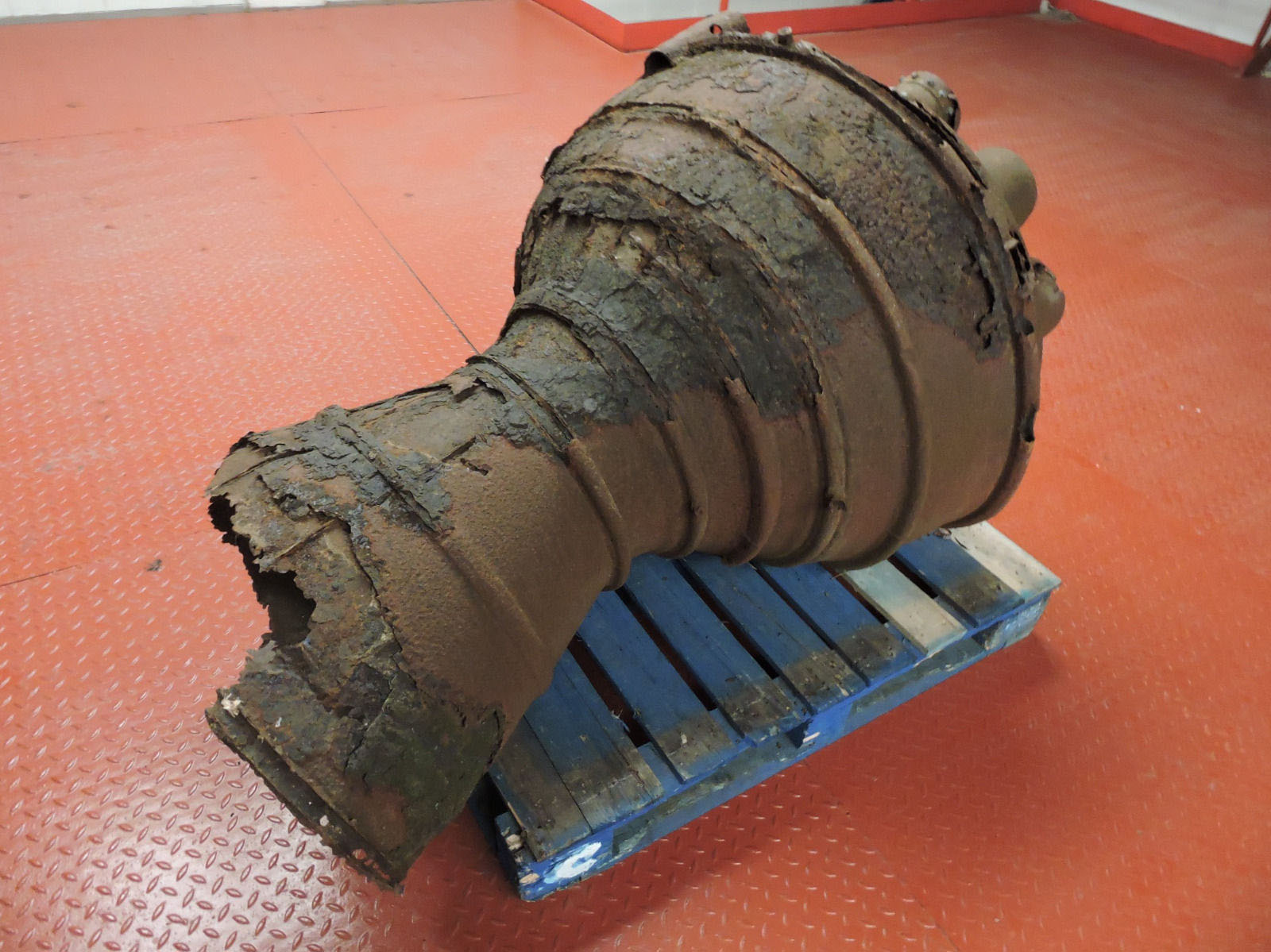
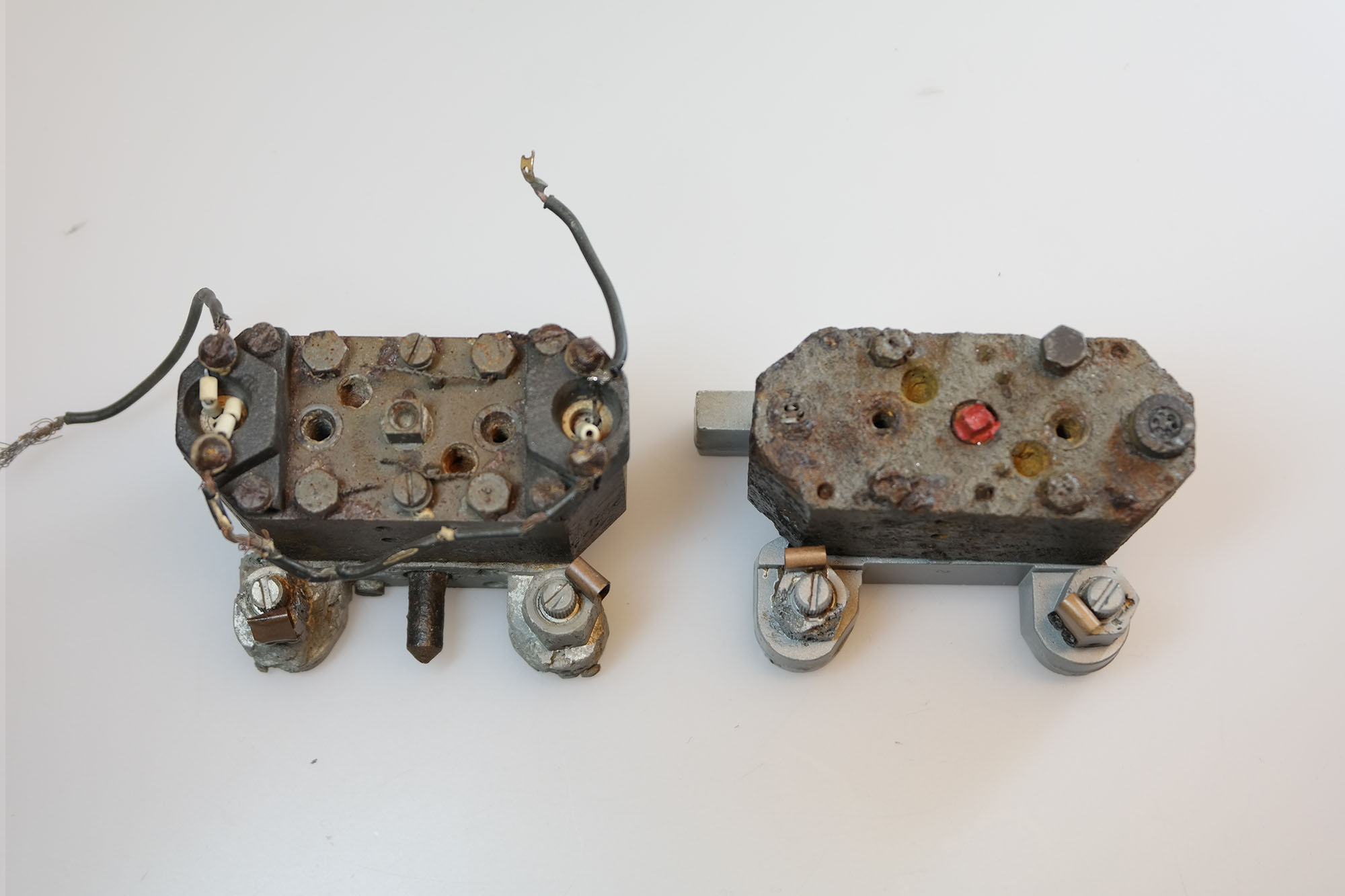
This is a collection of actual parts and sometimes images relating to parts and assemblies of the V2 missile.
Categories: Combustion, V2 Missile relics, Electrical connection, Peenemünde-Usedom-locations, Sub-assemblies, Missile guidence, Propellant flow, Guidence
Tags: #Combustion and injection #Propellent injector system #Test procedures #V2 Missile relics #Fertigungshalle Eins (F1) #HAP #HVP #Peenemünde #Werk Sud (South Works) #Usedom #light beam device #Control surface servos #LEV-3 gyroscope system #Mittelwerk Nordhausen #Propellant Valves #Steam generator #steam turbine #Thrust chamber #V2 in combat



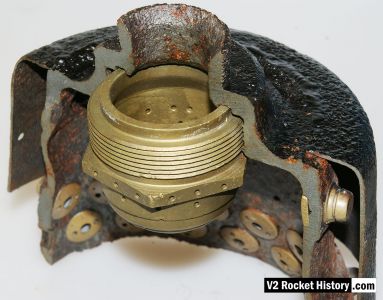
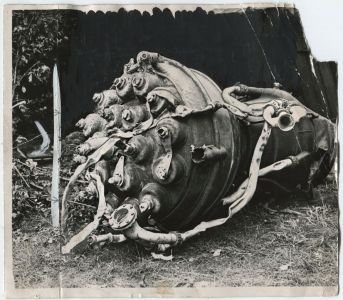
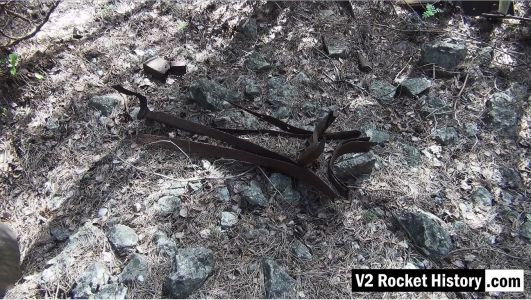
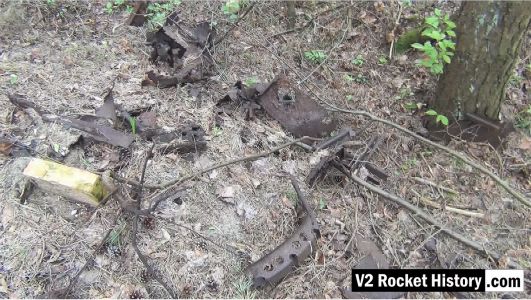
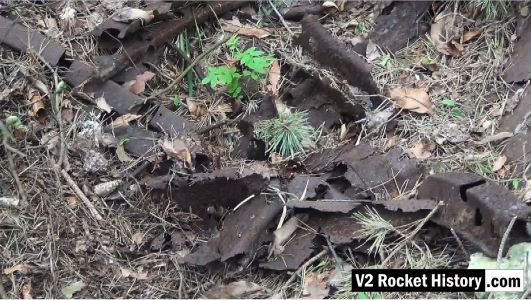
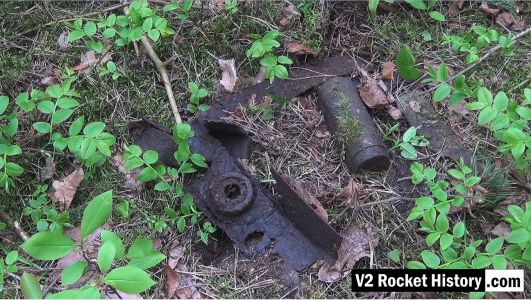
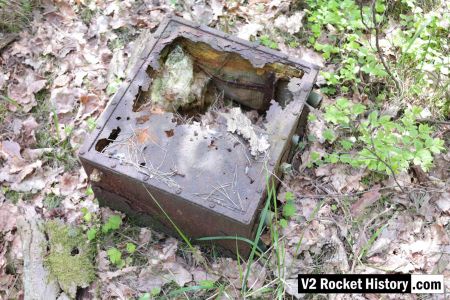
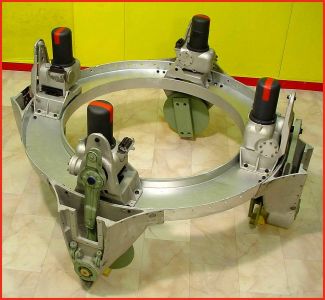
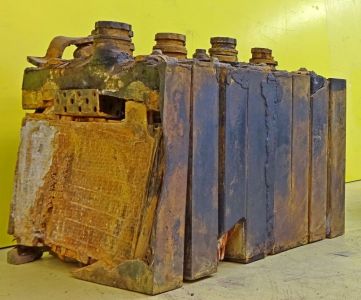
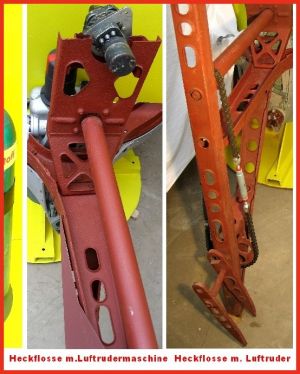
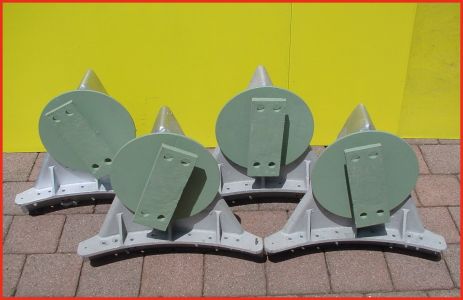
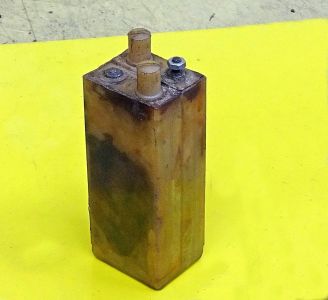
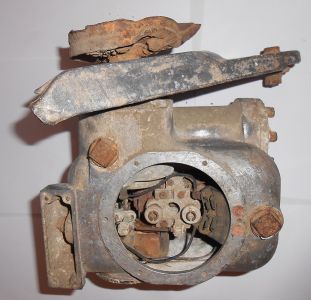
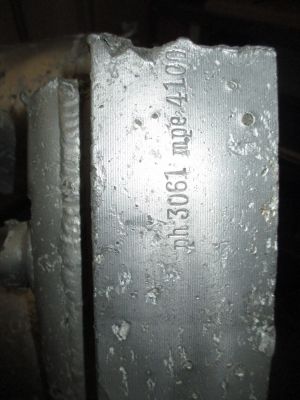
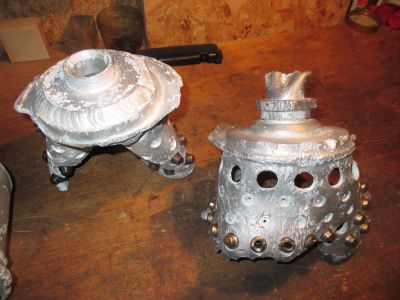
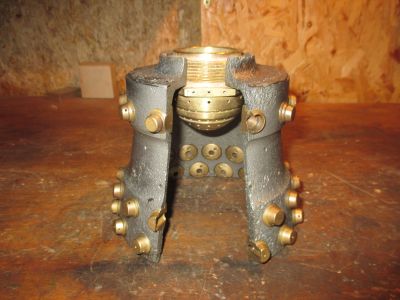
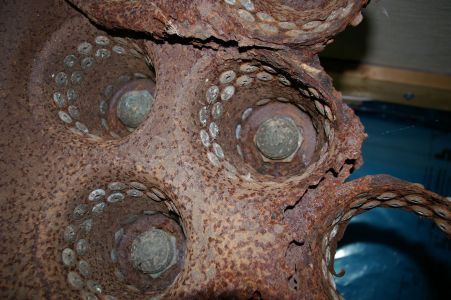
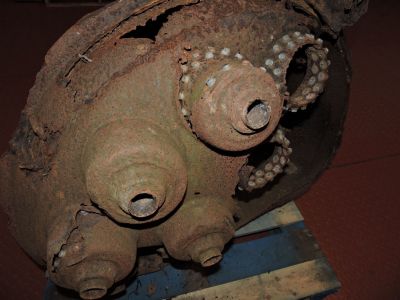
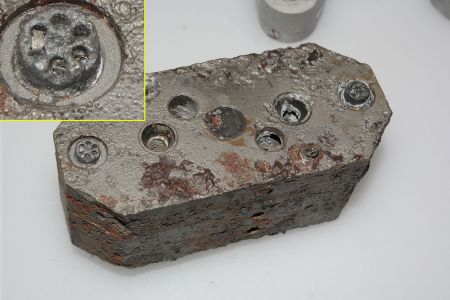

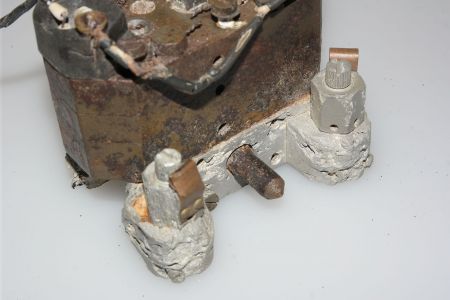
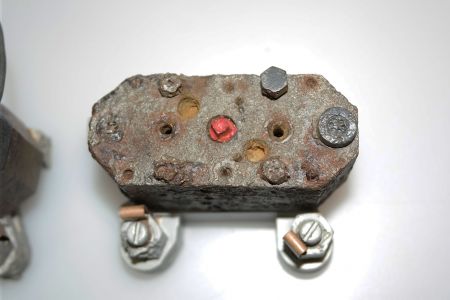
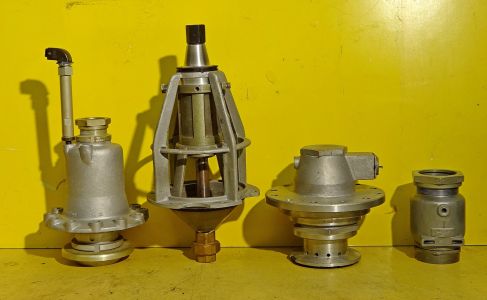
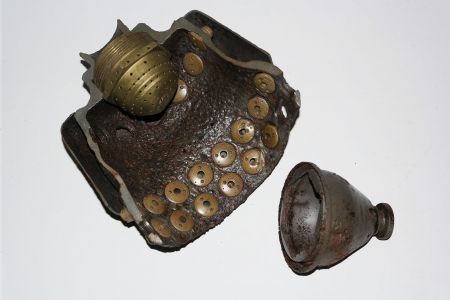
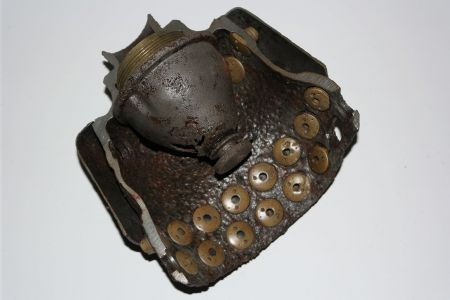
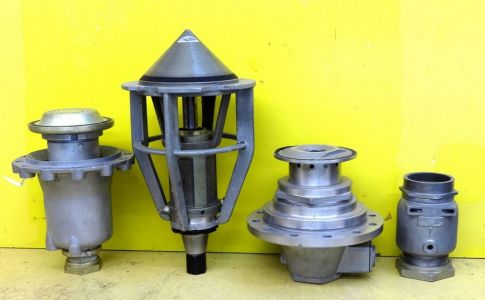
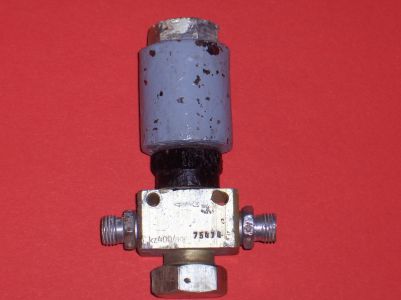
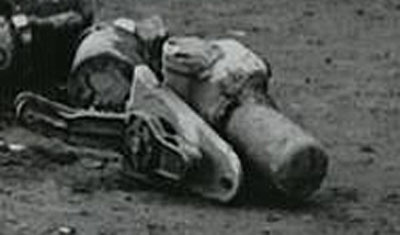
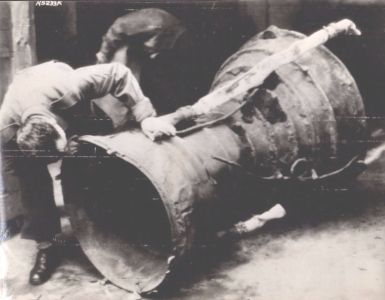
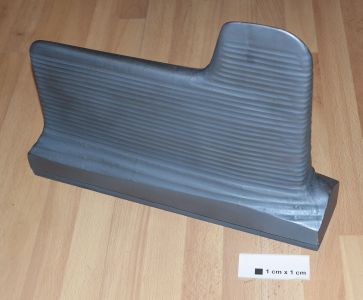
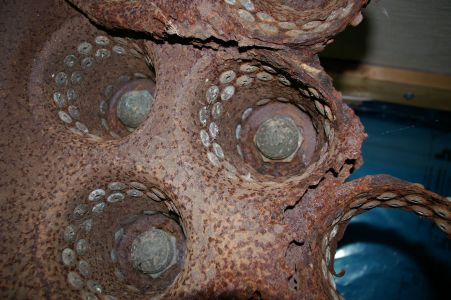
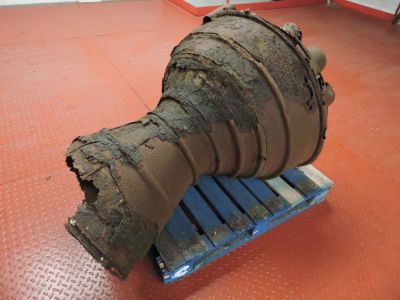
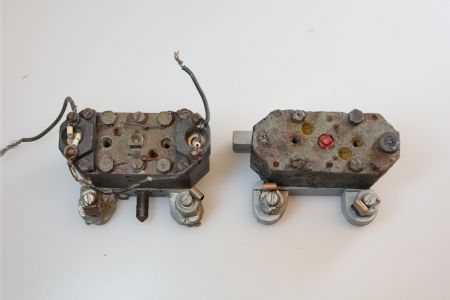
V2 rocket engine fuel injector inserts – a part of our collection used for the water tests with various types shown. The tool shown is a pin-wrench used to fit the inserts into the test apparatus. V2RH collection image