
Archives: Gmedia Albums


Turbopump 3D CAD
3D CAD model images of the A4/V2 rocket engine’s steam turbine powered propellent pumps – all images by Ray Matter. To see Ray Matter’s blog 3D CAD modelling the V2 rocket turbopump introducing these images, just click the link.
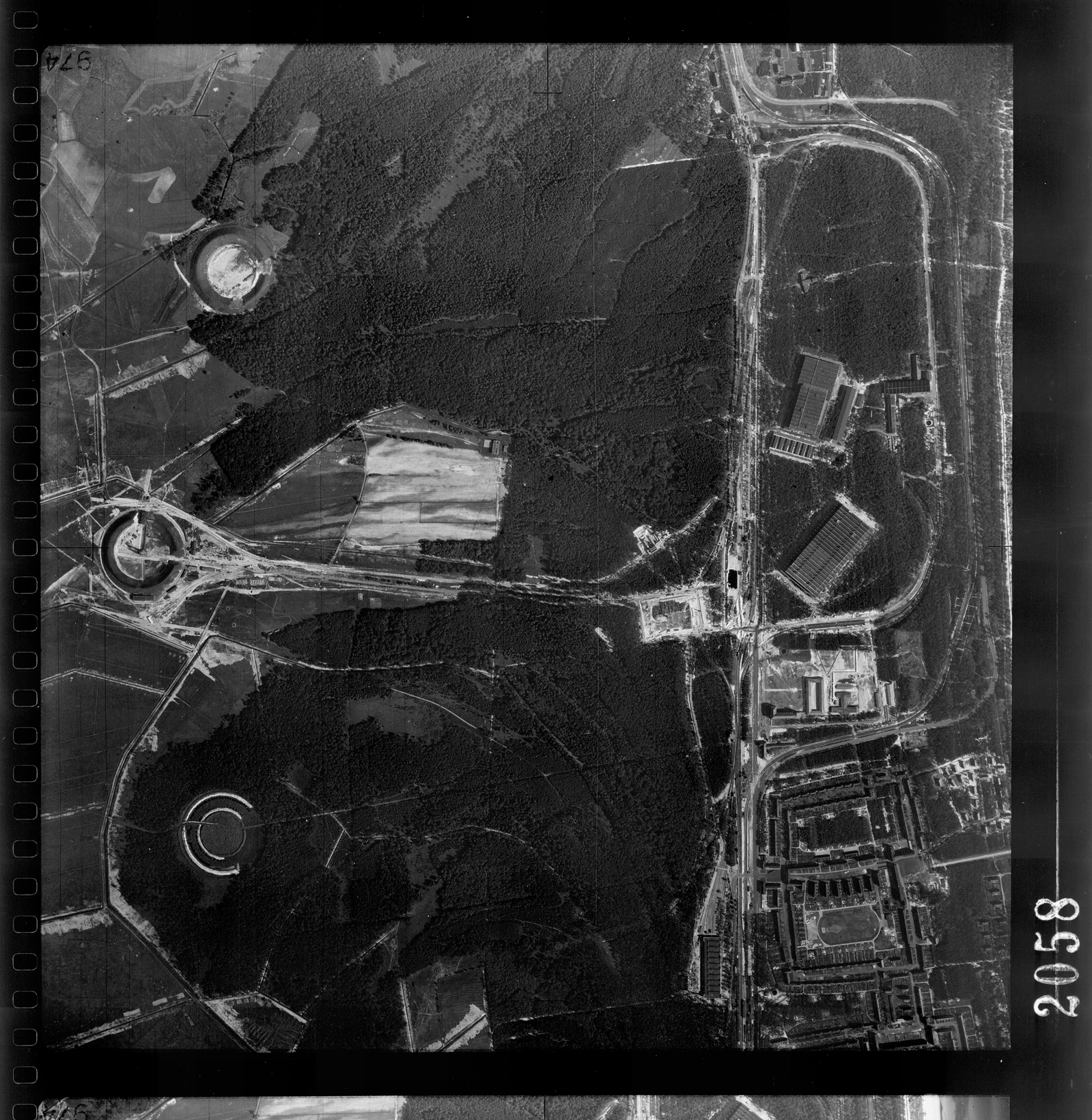
RAF reconnaissance photo showing the Werk Süd region with the F1 pre-production hall and to the north the IW repair and maintenance hall, centre right, and road rail links to Prüfstand XI (Test Stand 11, circular rampart centre left) heading directly left from F1. P-XI was conceived to provide engine test facilities for the nearby pre-production hall. Scroll down to see GPS map, the marker index is set to the centre of P-XI, click map and switch to satellite view and you will see that only a small section of the circular rampart remains visible. You can easily zoom out to cover the coast area where F1 and the equally large Repair & Maintenance Workshops are located. The area immediately surrounding P-XI is now contained within a commercial farming operation with sheep appearing to be the staple – or was anyway, at the time of our first visit to the vicinity in 2010 and our last in 2017 – none of the sheep seemed to recognise us though so they may have changed. (for access to restricted areas click here)
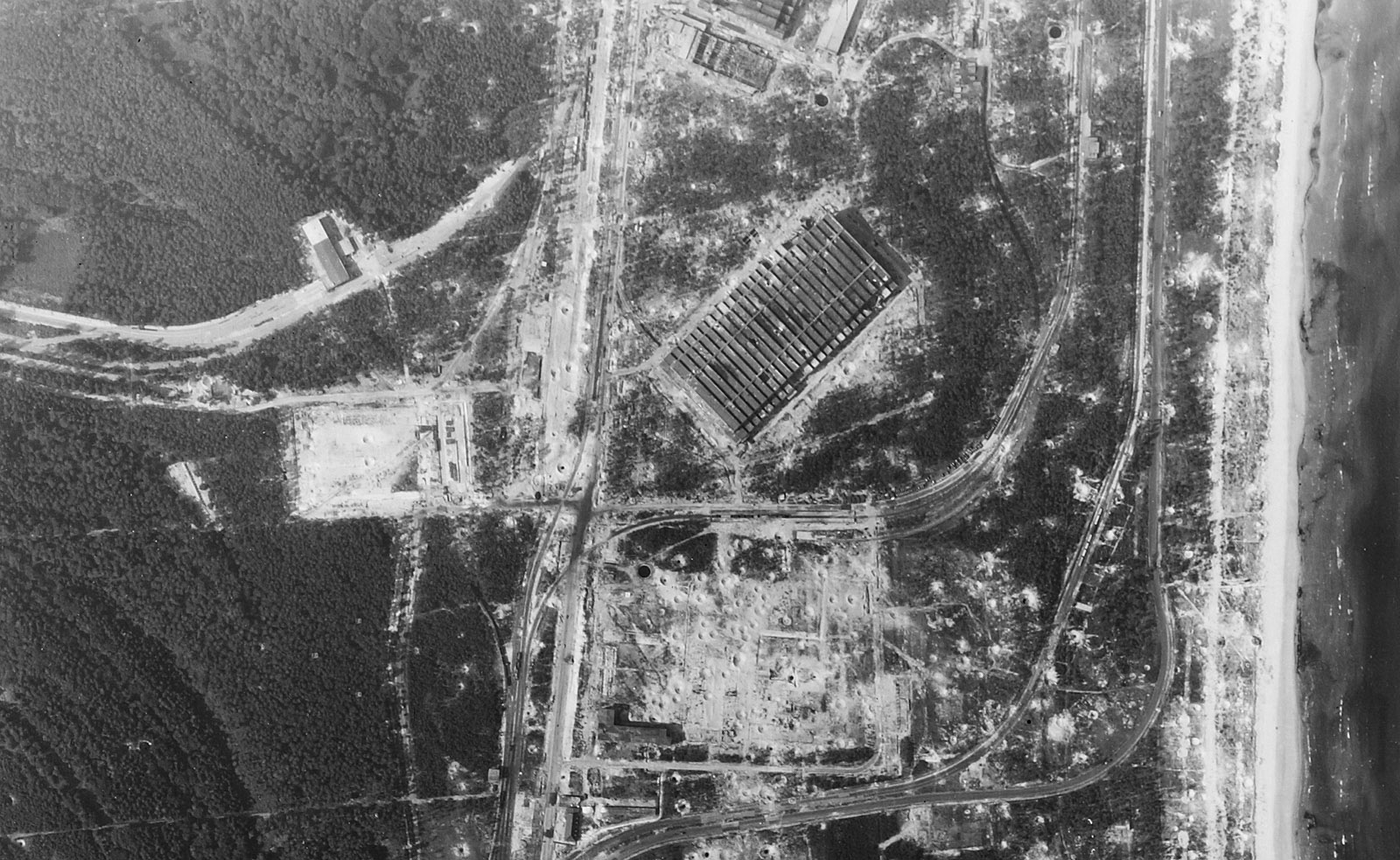
RAF Recce photo taken 21st August 1944 of region around F1. The GPS marker for this photo is pegged on the lowest of the three fire fighting cisterns clearly visible in the image (in the center about a third the way up from the bottom of the image). Scroll down below this text for map and switch to ‘Satellite view’ where the fire fighting cistern can still be clearly seen today.(for access to restricted areas click here)
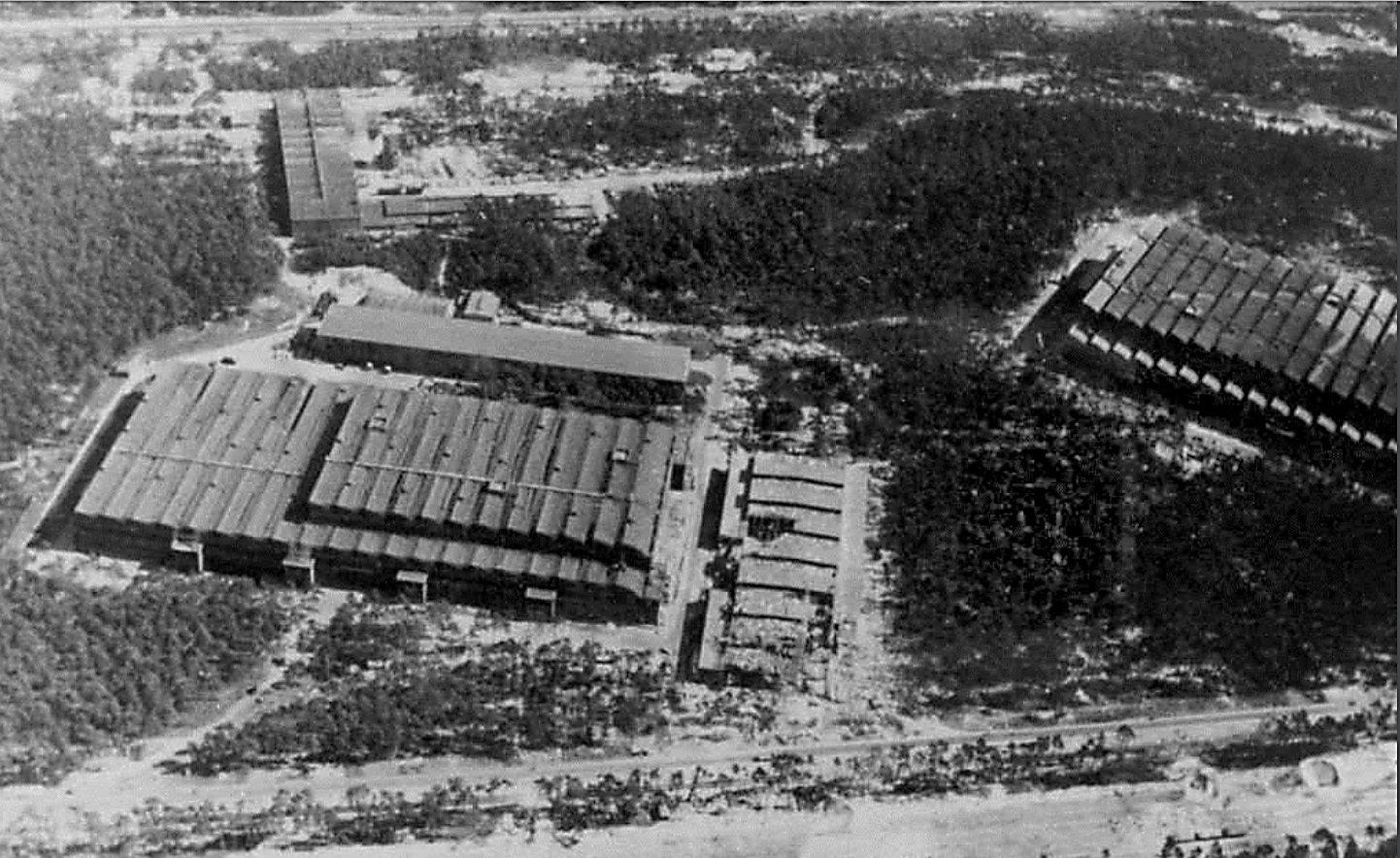
Photo showing Werk Süd with IW on the left and F1 on the right taken on 19th August 1943. The photo shows only light damage to the main halls, although F1 was actually hit at least 11 times, and hits to the separate single storey workshops to the right of the IW hall. The long storage (oil and paint?) shed above IW and the woodworking shop at the top of the picture appear undamaged. Anti-aircraft platforms (at least 3) can be seen on the roof of IW but that seem to be empty of guns. F1 shows two AAA platforms (there was at least 3 at this stage and maybe more) and they may have guns installed. General W. Dornberger mentions defensive AA artillery fire from the from the roof of F1 in his 1952 book V2 (1954 in English).
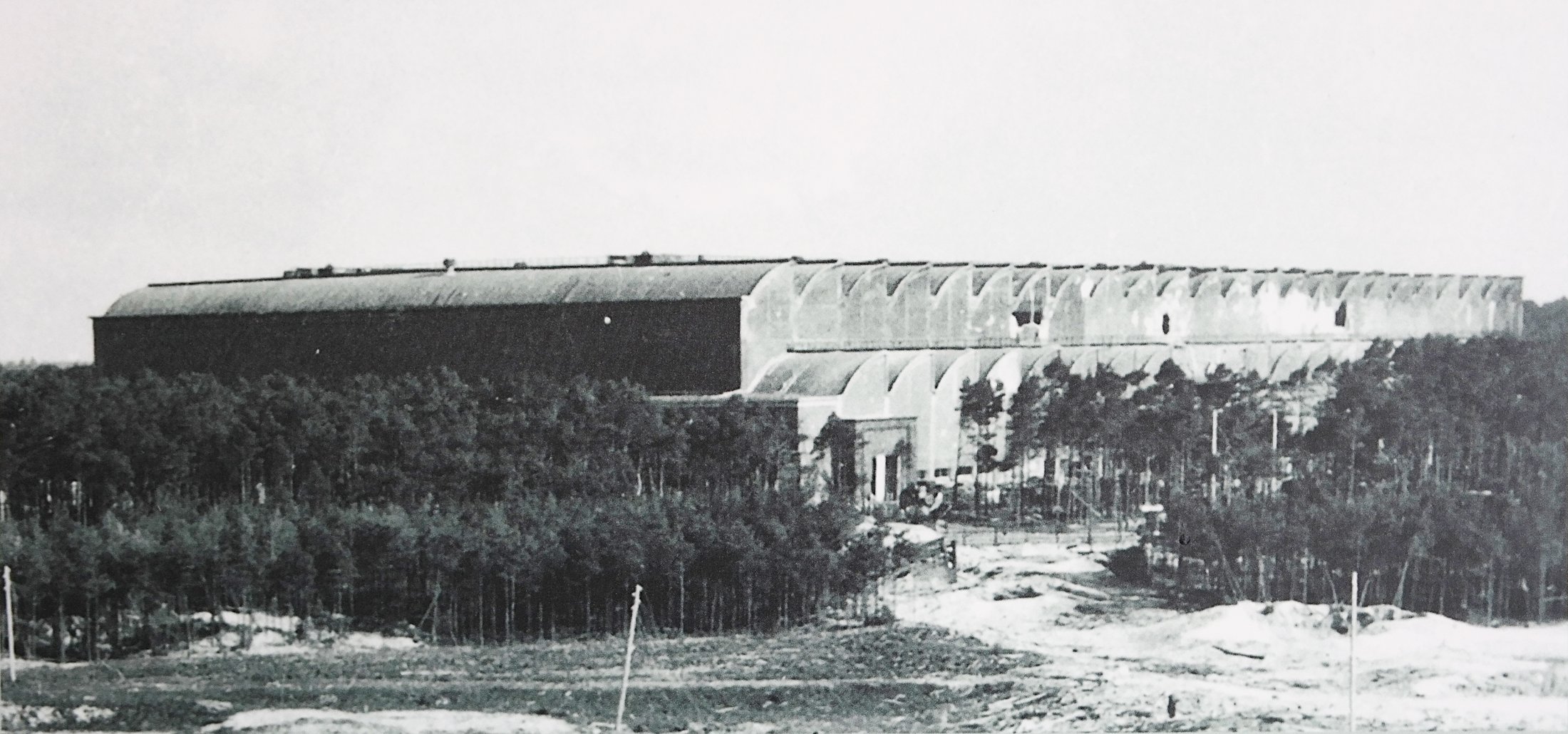
A rare photo of the giant F1 production hall taken not long after the RAF raid of 17/18th August 1943. F1 was a forced labour camp with at least 600 prisoners living within the factory and at least eleven were killed in the raid. Parts of the electrified barbed wire fence can be seen close to the factory building, in the clearing in the middle of the photo. Two anti aircraft gun emplacements can be seen on the roof at the front of the building. Holes in the side walls of the upper vaults can be seen as well as the damage to lower vaults 9 and 10 (counting from left) from a direct hit in this region. Also of note are the numerous guy ropes, attached to the upper roof of the front of the building – and running down towards the trees, that are just visible in the photo. These may be supports for camouflage netting that was in the process of being fitted (by prisoner gangs) just before the raid. The work was never completed.
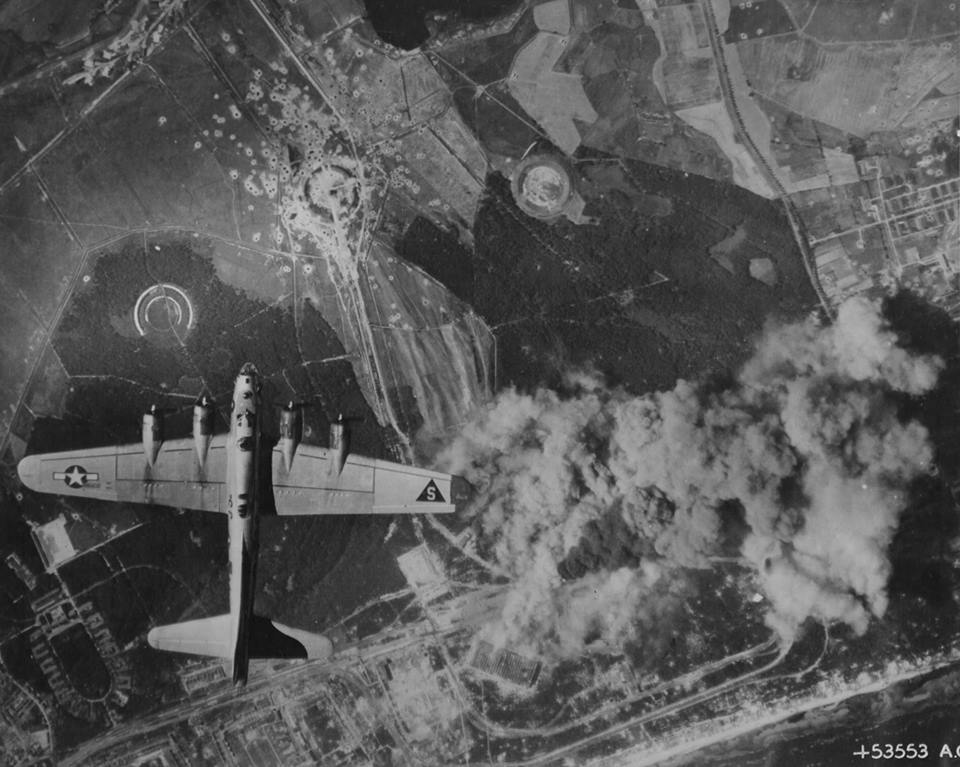
Peenemünde: Werk Sud attacked by US bombers August 1944 in a daring daylight raid. The two large halls F1 and IW in the lower middle of the photo are under direct attack and smoke can be seen originating from both buildings. Although the August 1944 raids did little to interrupt the volume manufacture of the V2, as virtually all manufacturing and assembly of the missile had moved to central Germany, the raids did bring to an almost complete halt the last small amount of manufacturing work still competed in the giant halls of Werk Sud.
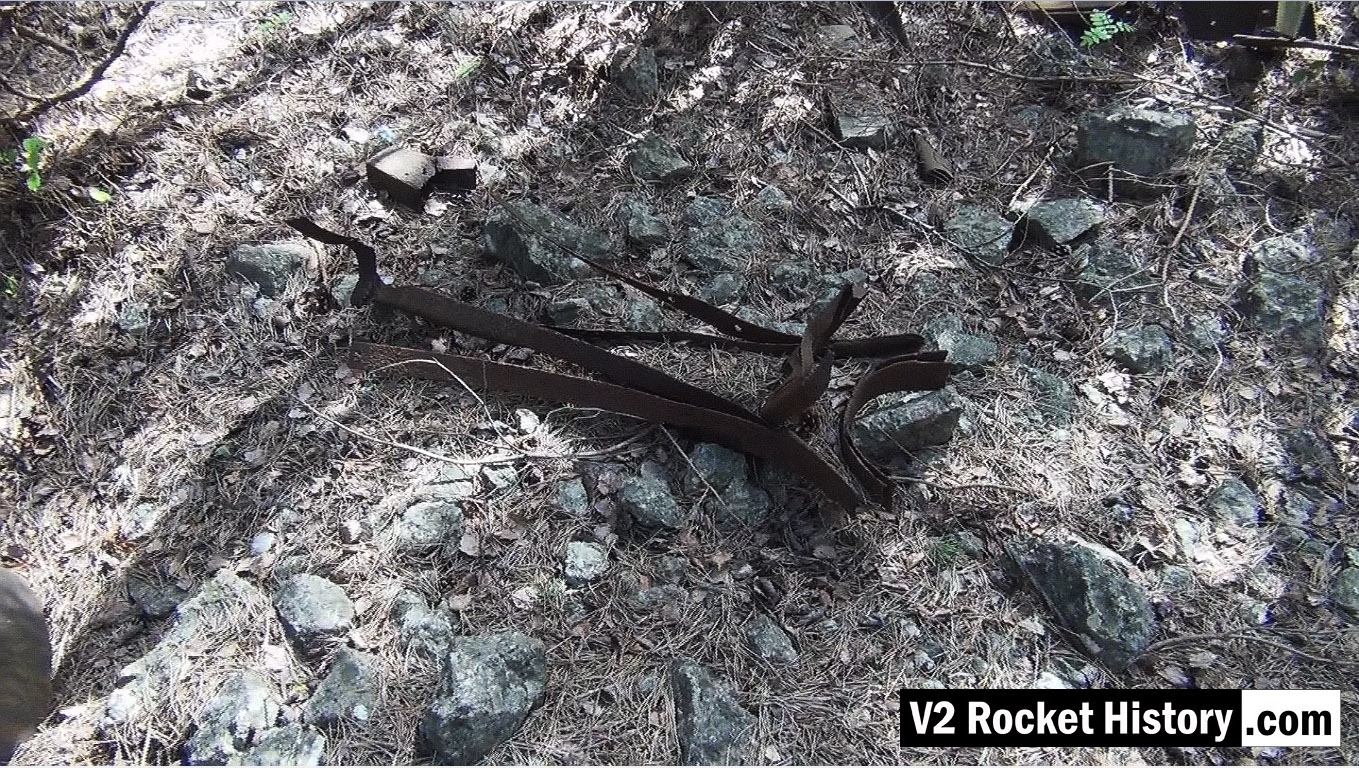
Picture shows parts of V2 missile fin structure laying on open ground near area between admin offices and F1 (near Admin. block railway platform, see map).
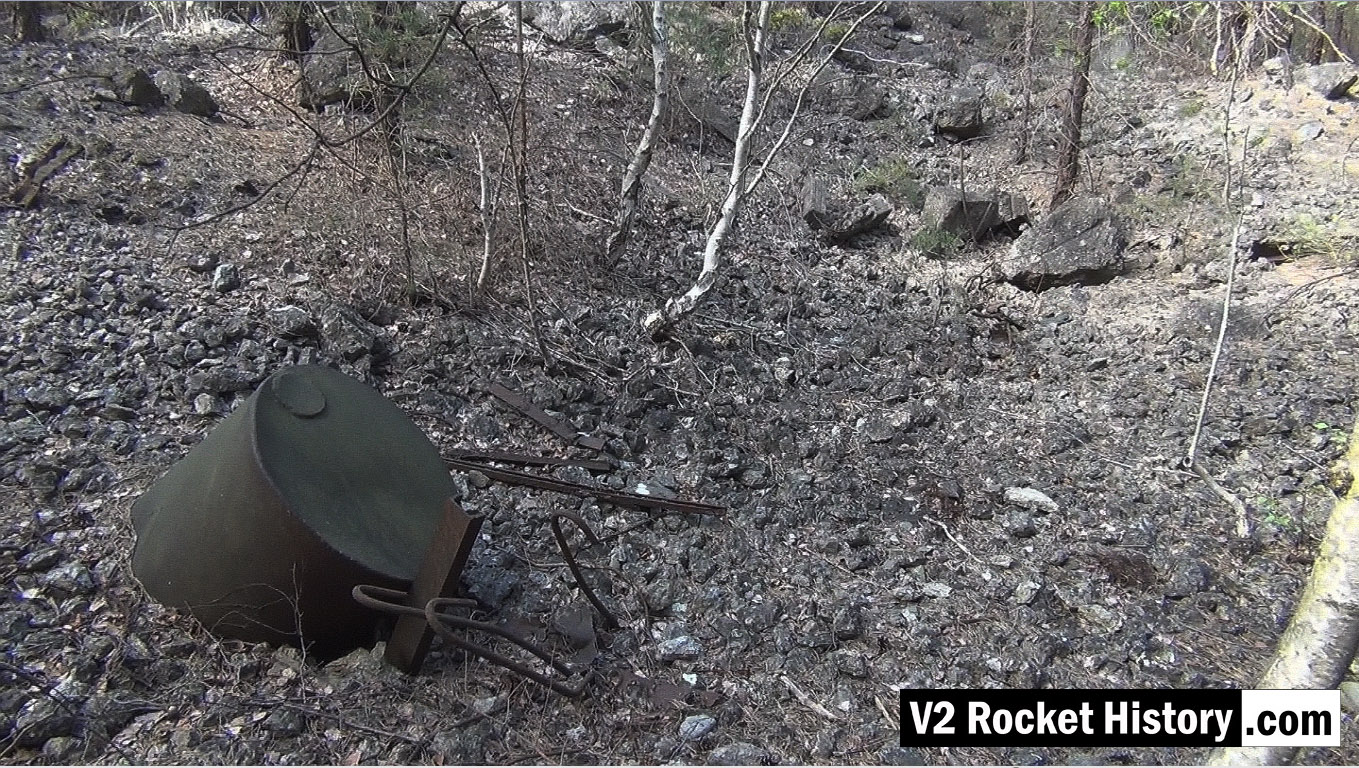
Picture shows metal debris within the F1 factory boundary walls. The purpose of the part buried liquid storage vessel in the foreground is unknown but it is not a vessel capable of being pressurised. Other assorted metal debris include pipe and cable wall cleats, as well as steel armature rods from reinforced concrete castings (powerful demolition explosions have freed the steel rods from the concrete). These reinforcement rods are a common sight in the environs of Fertigungshalle Eins (F1) and the nearby Repair & Maintenance Hall (R&MH).
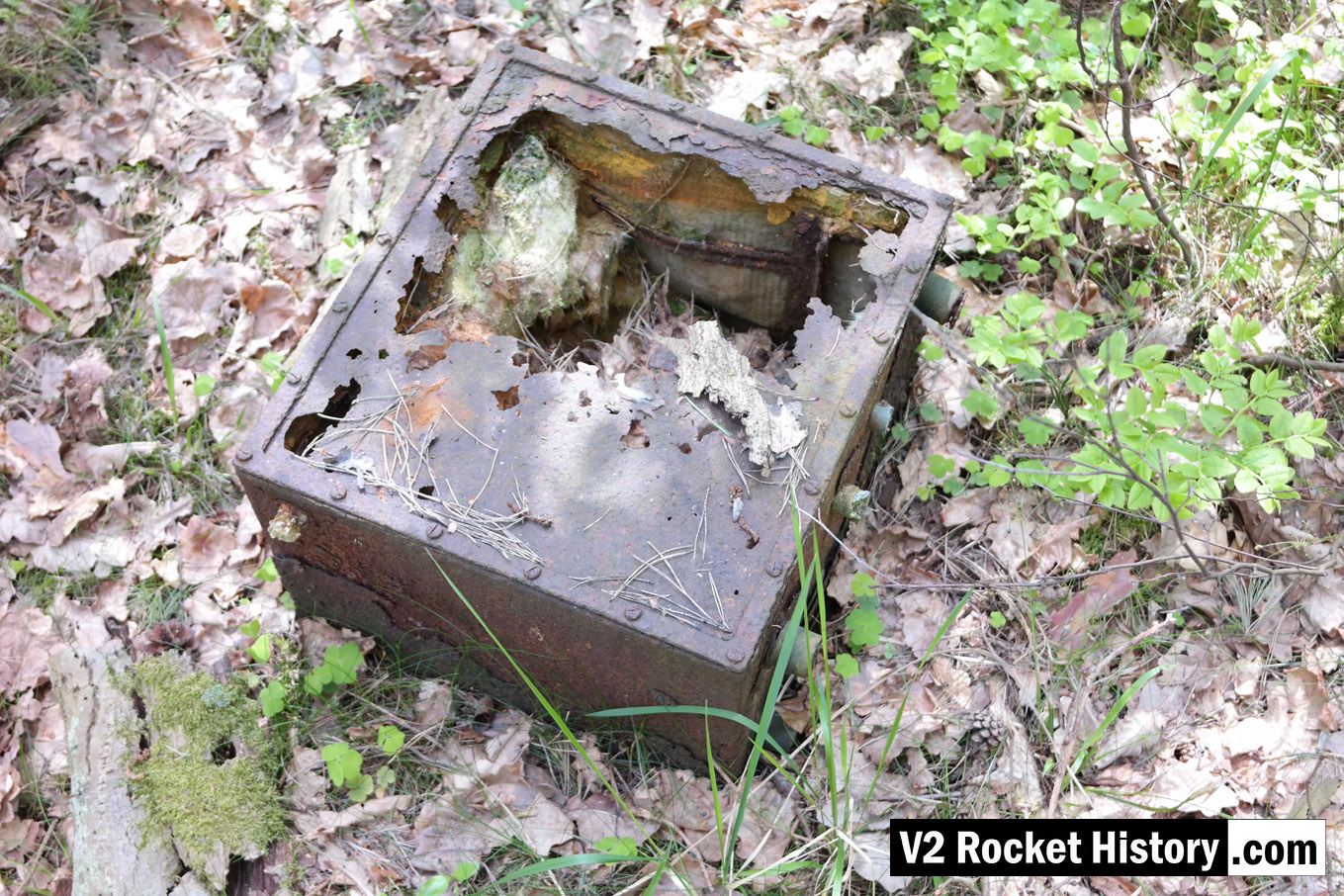
The photo shows a Lichtstrahl empfänger (In English: Light-beam receiver) environmental protection case, originally one of a group of 40 or so we first found in 2010 abandon in an area adjacent to the train platform for the administration block. On subsequent visits this number has declined to just ten or so, mostly very decayed examples. The environmental casing was vital to the Lorentz Light-Beam equipment on-board the V2 missile as the critical radio frequency would otherwise drift with the large change in temperature as the missile climbed into the stratosphere. The case was thickly insulated with rock wool or fibre-glass strands and designed to help maintain a stable temperature – indeed, the same temperature as the radio equipment was when at ground level when calibration and adjustment was completed before launch. The F1 pre-production hall is located about 200m North-West of the point where this photo was taken. Scroll down to see map below (click map and switch to ‘satellite view’ for clearer indication of location).

This picture shows a small debris field of steel fragments from the V2 missile 130m South-East of F1, and just 20m to the North East of the foundations of a small heat distribution building. Various body and frame parts can be seen and in the middle foreground a 350mm segment of curved missile body ring is visible. These parts have almost certainly been dug up and exposed by the action of metal detectorists. The metal fragments have been abandoned by their finders as they are perceived to have no financial value and hence are not worth removing from the site.
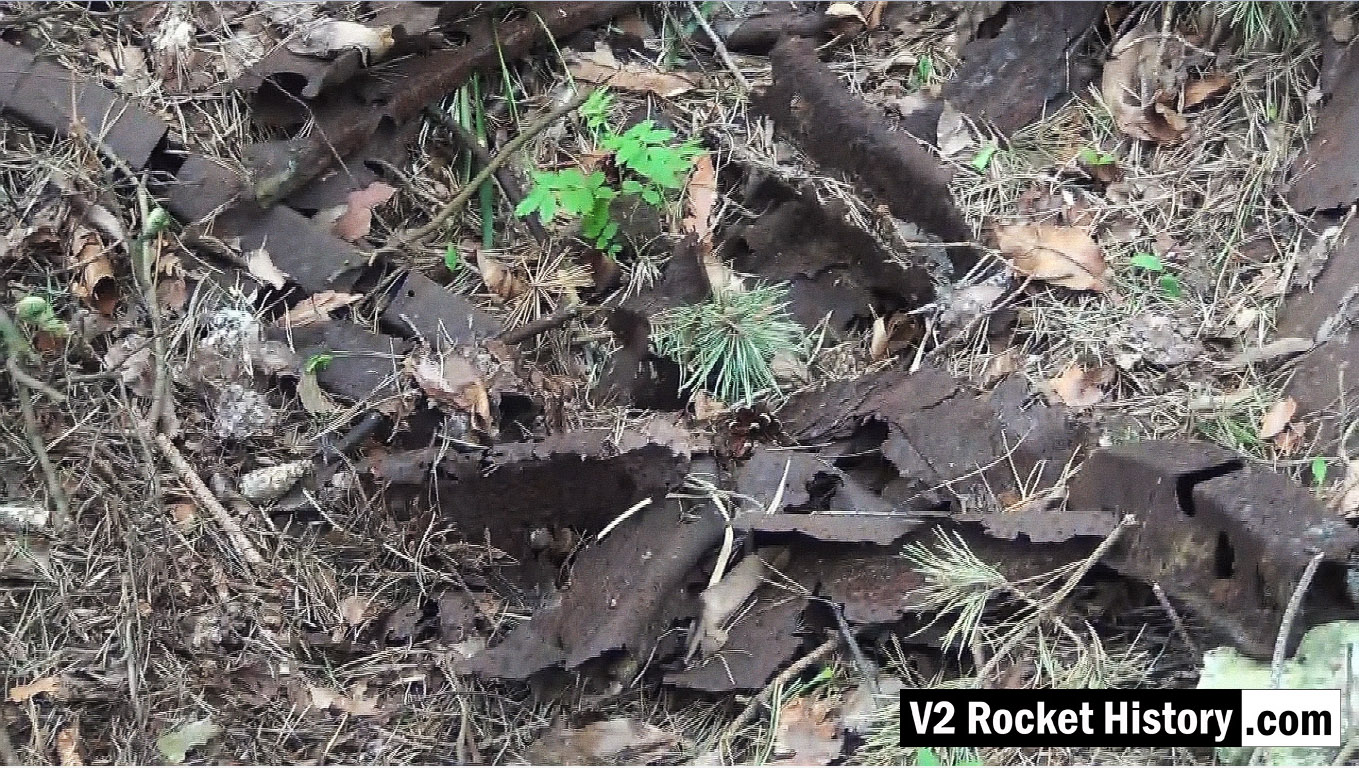
This picture shows a close up detail of parts in a small debris field of steel fragments from the V2 missile 130m South-East of F1, and just 20m to the North East of the foundations of a small heat distribution building. Various body and frame parts can be seen and in the upper left and two segments of curved missile body ring are visible. See previous.
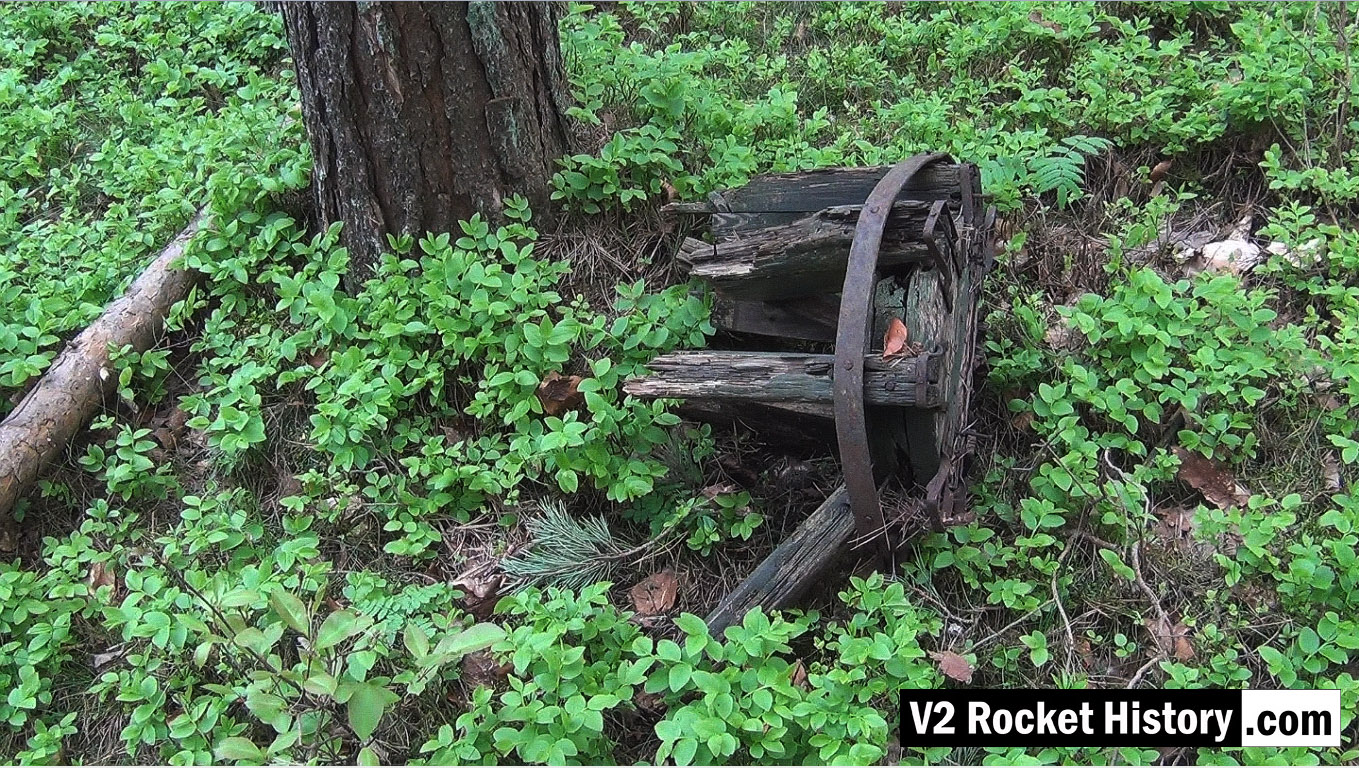
Wooden carboy frame from WW2 (possibly used for transporting small quantities of corrosive and dangerous liquids employed in the V2 steam plant, (such as T-Stoff) laying among trees 190m East of F1 in a location used as an emergency rail freight loading area to F1 due to damage caused by US air raids in August 1944.
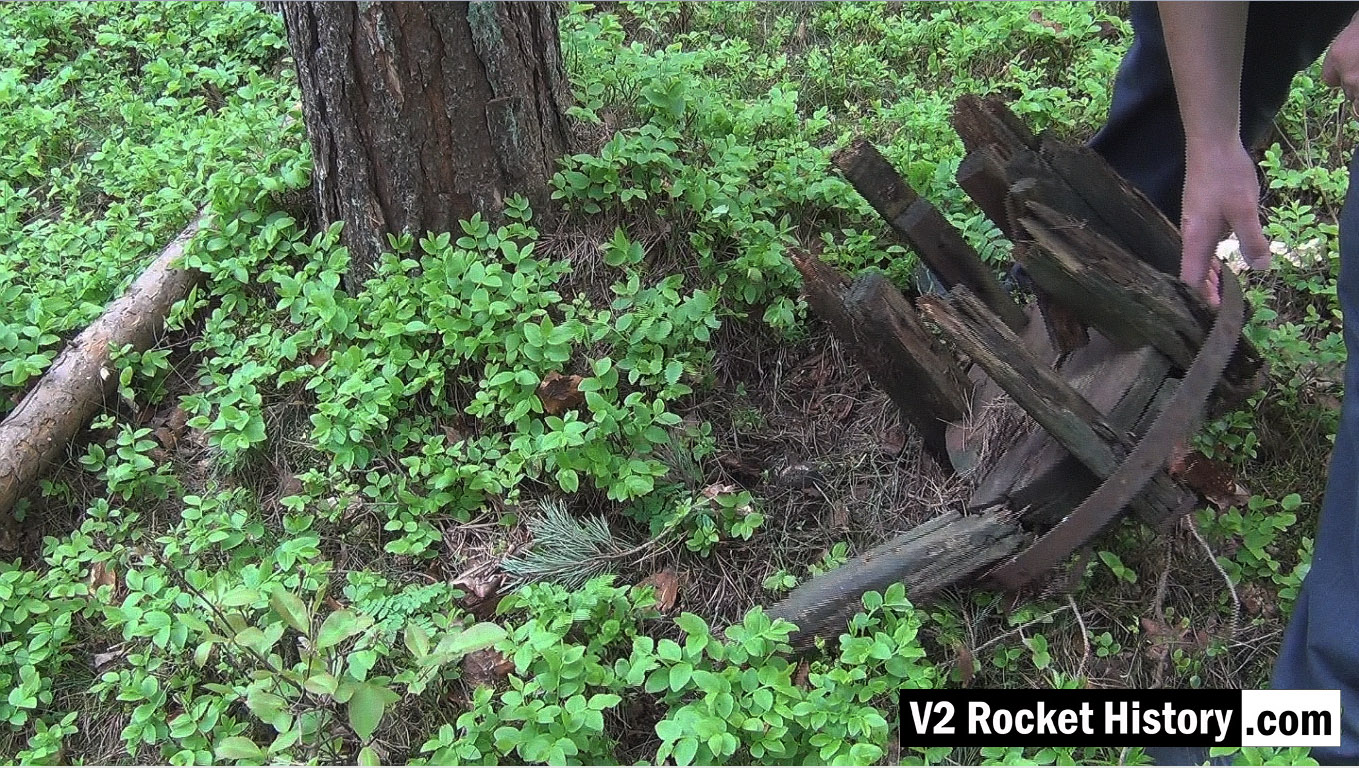
Wooden carboy frame from WW2 (possibly used for transporting small quantities of corrosive and dangerous liquids employed in the V2 steam plant (such a T-Stoff) laying among trees 190m East of F1 in a location used as an emergency rail freight loading area for F1 due to damage caused to rail track by US air raids in August 1944.
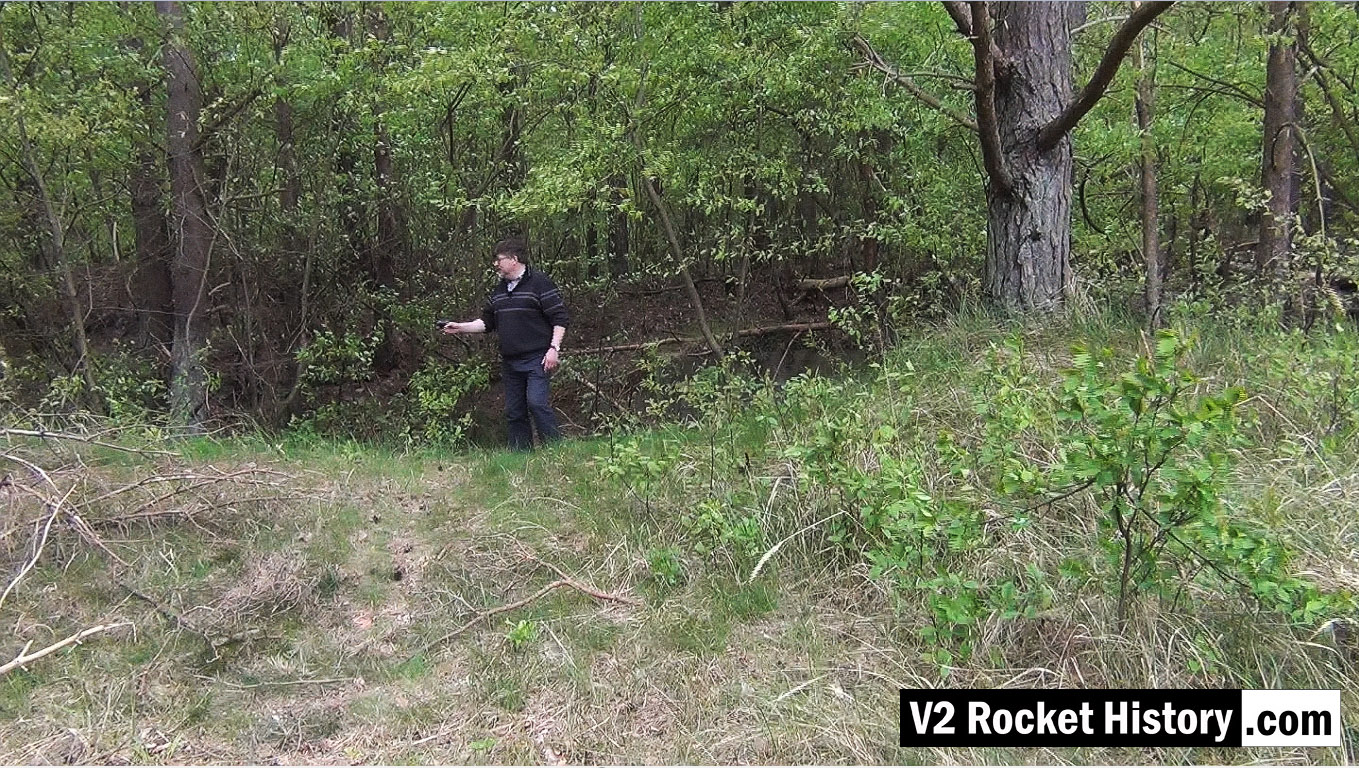
This picture shows Robert Dalby collecting GPS data with a mapping camera just North of the East end of the Admin office rail platform (near the ruins of the small admin/F1 heat distribution hub building). In all of our explorations we routinely collect GPS track and data points to be able to accurately locate finds and establish a precise correlation between areas of interest identified on historical reconnaissance photography and the modern ground terrain. In the picture Robert is pointing a Contour video camera at details of the terrain that automatically captures the camera’s GPS location information. This data can then be combined with satellite imagery, via Google maps, and provide a detailed graphic mapping track alongside the video footage.
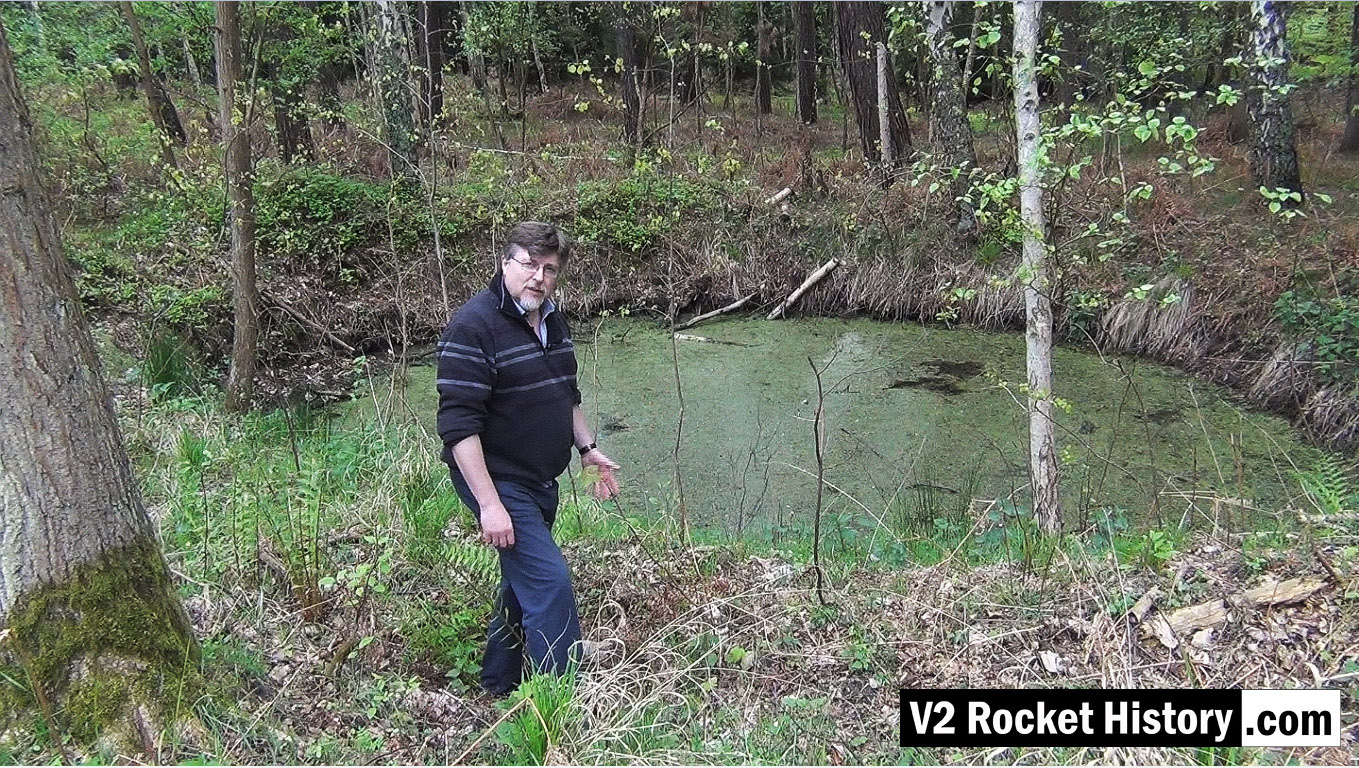
This video still shows Robert in front of a bomb crater on the West or opposite side of the rail lines and road that pass the Repair & Maintenance Hall (R&MH). The crater like so many others, created in a fraction of a second, in August 1944 during a US air raid, has developed in to a thriving eco-system that now teems with all kinds of life. After the passage of more than 70 years the crater is still deep and well defined. There are hundreds of craters like this in the area.

This video still shows the same bomb crater from a slightly different angle. The crater like so many others, created in a fraction of a second in August 1944 during a US air raid, has developed in to a thriving eco-system that now teems with all kinds of life. After the passage of more than 70 years the crater is still deep and well defined. There are hundreds of craters like this in the area.
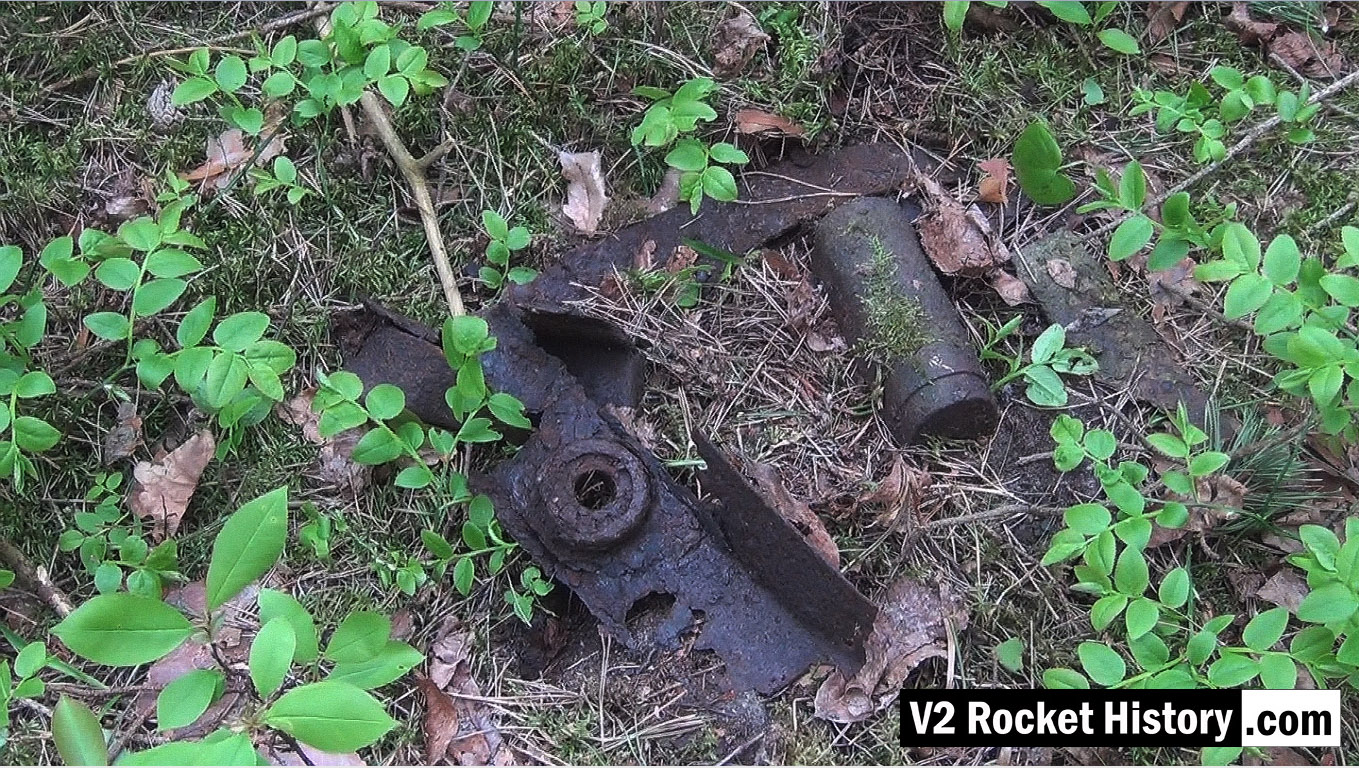
V2 missile parts in F1 prisoner turn-out or ‘free movement’ area. The location referred to is a large triangular shaped area situated on the South-East side of the pre-propuction hall Fertigungshalle Eins (F1). The area was fenced off with a high barbed wire fence (a portion of which was electrified) with guard towers every 60 metres.
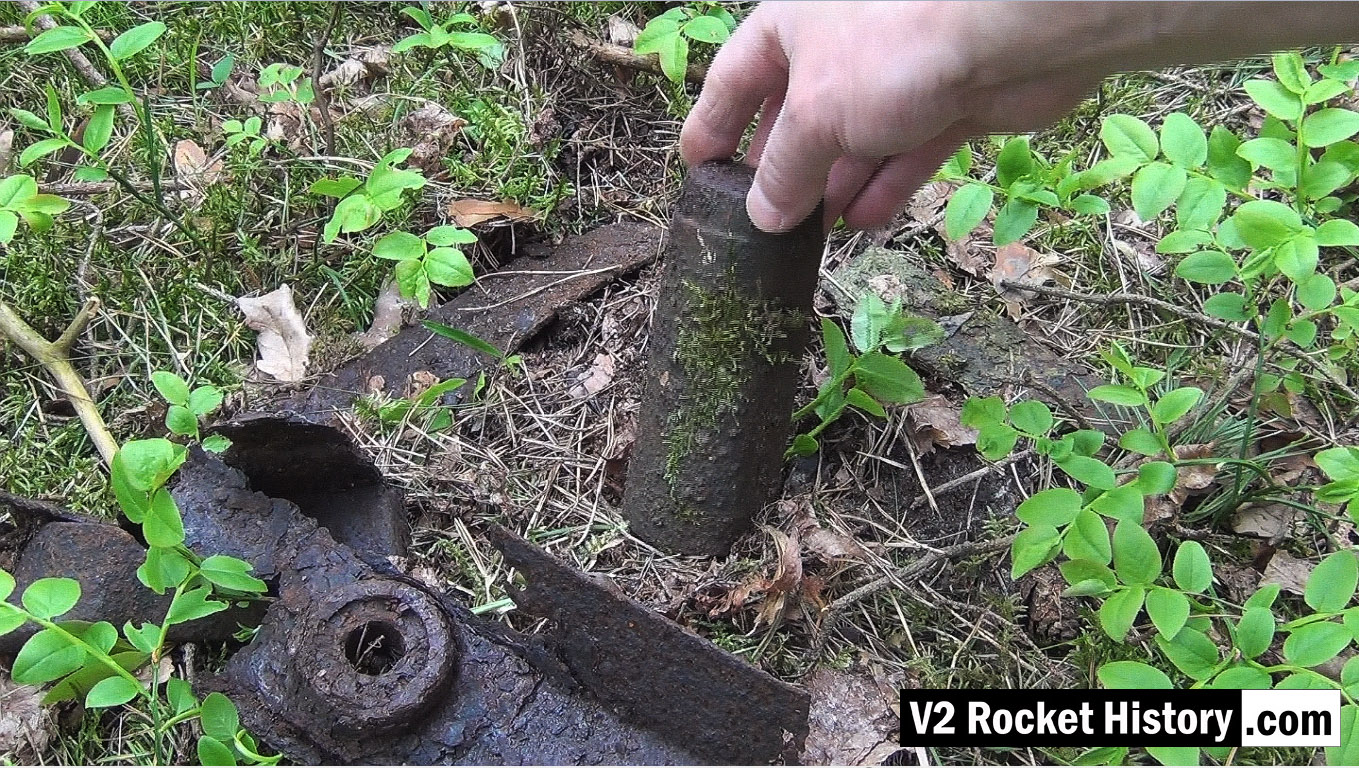
V2 missile parts in F1 prisoner ‘exercise’ area. Image grab from Fertigungshalle Eins (F1) video.
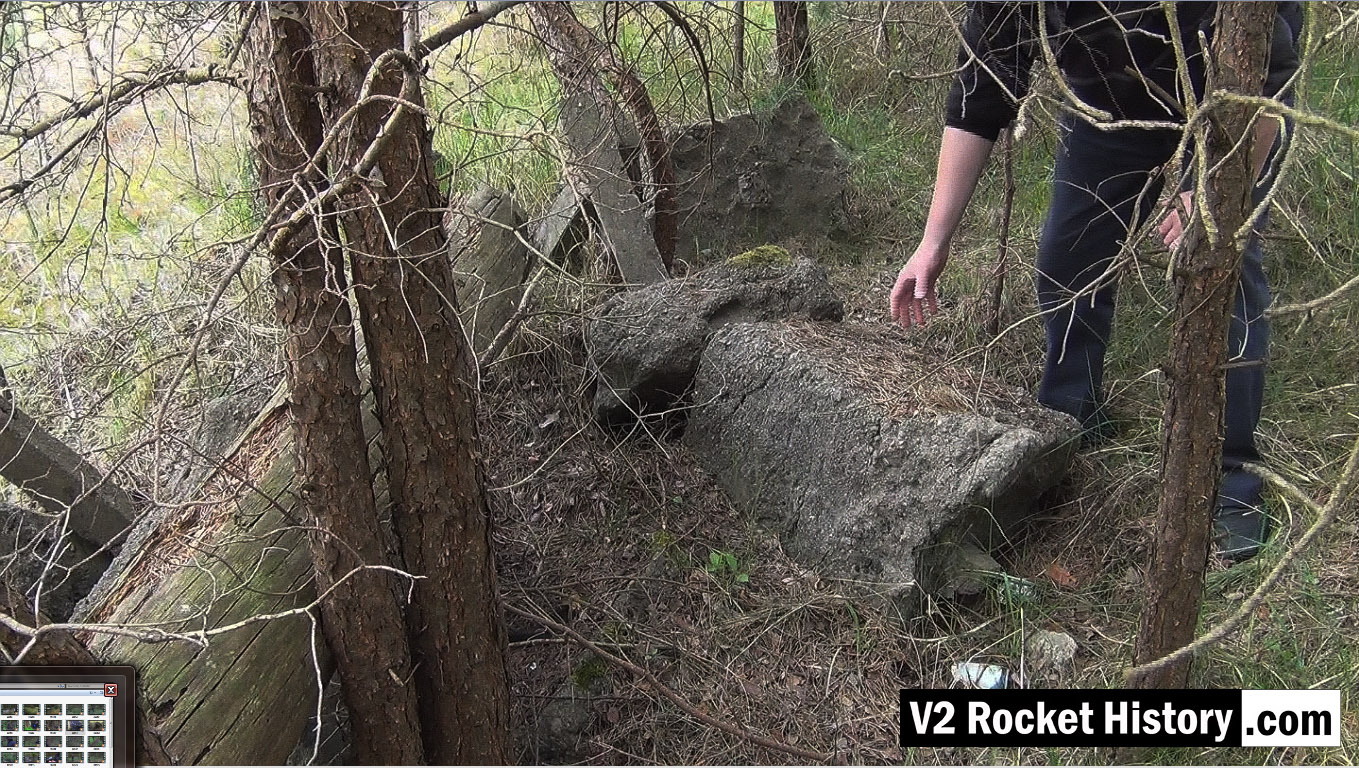
This image shows part of a pile of concrete castings that form the below ground foundations for part of the electrified fence that was built around F1 in the summer of 1943. The fence was built on the instructions of Arthur Rudolf, who was responsible for F1, by the first 200 forced labourers to arrive at the F1 labour camp in June 1943. These crude castings are the result of digging a narrow hole in the ground for the concrete fence post and filling the area around the post with the concrete mix. The sizable variation in the depths of the concrete castings, and the fact that in a number of casting blocks the post has plunged through the concrete mix and penetrated from 100 to 300mm into the ground below, strongly suggests this work was carried in hast and/or by men inexperienced in the normal procedures of this type of basic ground-work.
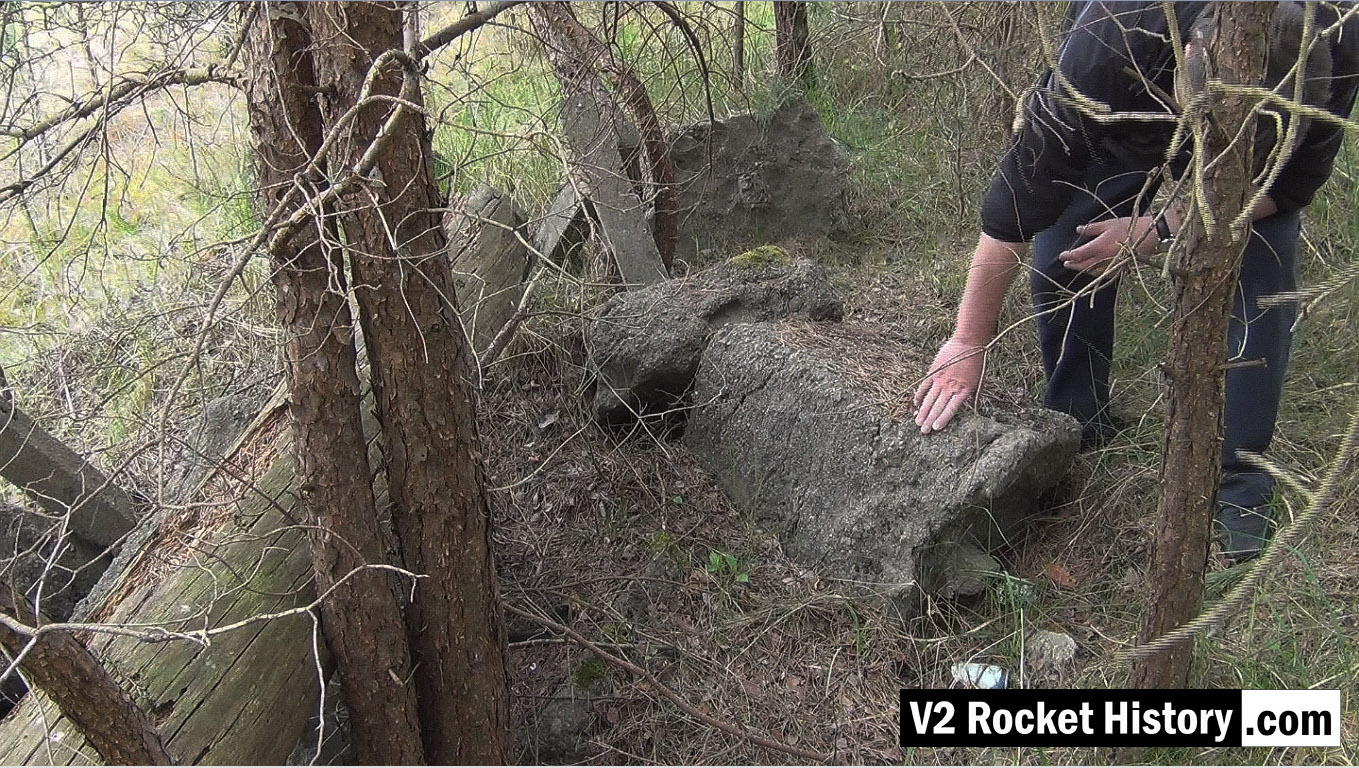
This image shows part of a pile of concrete castings that form the below ground foundations for part of the electrified fence that was built around F1 (see previous photo for details). You can see the area that these posts once secured in the second black and white recce image in this gallery. The fenced off area is the large triangular shape you can see joining the North-East South-East corners of F1 (ie the long wall of F1 facing the shore). Quite why and exactly when someone mustered men or machines to pluck these lumps of concrete out of the ground and move them 100 to 200m is beyond me – why not just bulldoze them under like everything else on this site?
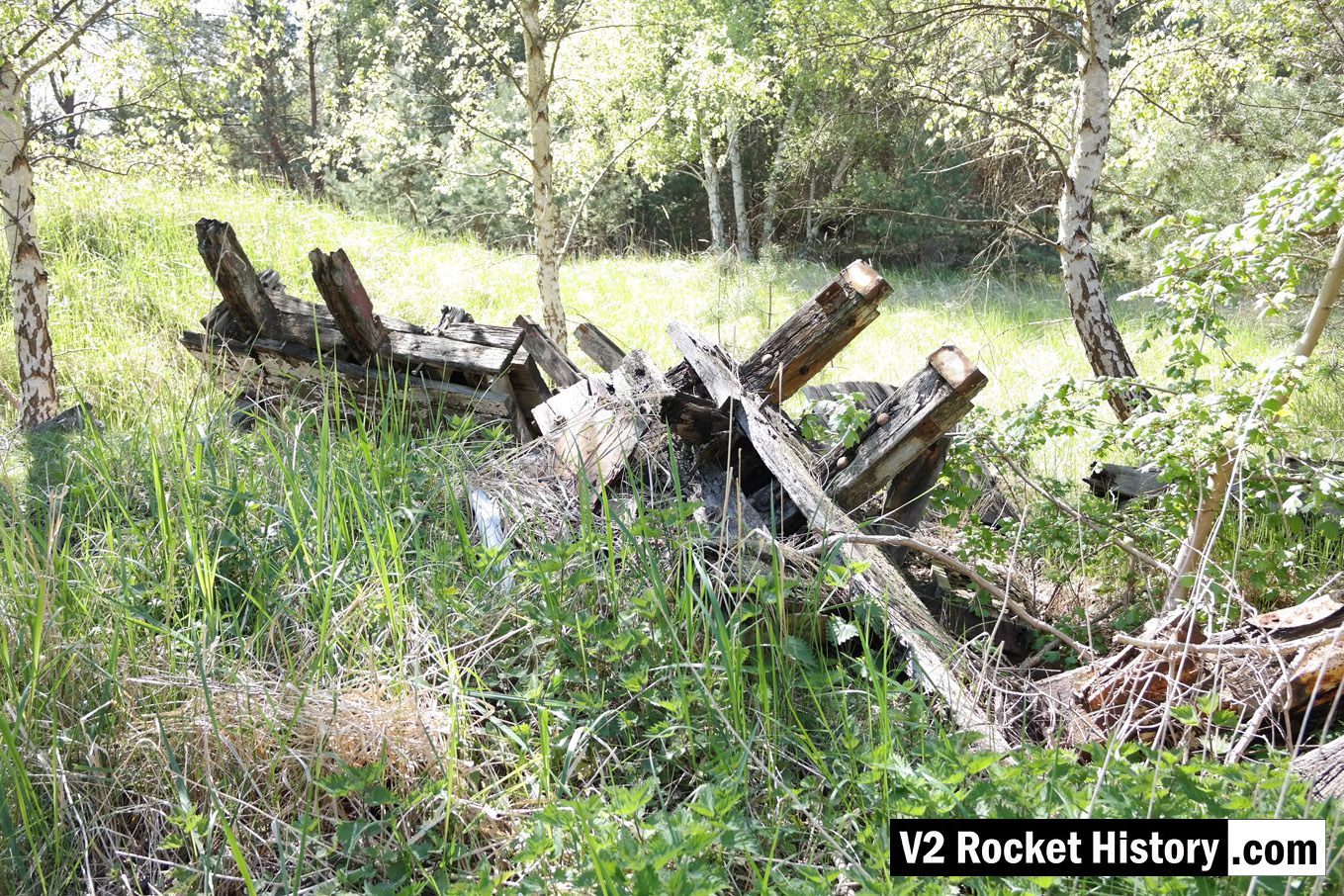
These timber parts, found just outside the North East corner of the F1 factory, are reminiscent of the wooden roof formers used to create the shuttering for the vaulted concrete roof of F1. However they differ in a number of respects and are assumed to be parts used in the final construction, repair, or modification activity perhaps after the RAF raid of 17/18 Aug 1943. Metal shoes and wear plates (shown in photo) indicate that the formers were intended for repeated use.
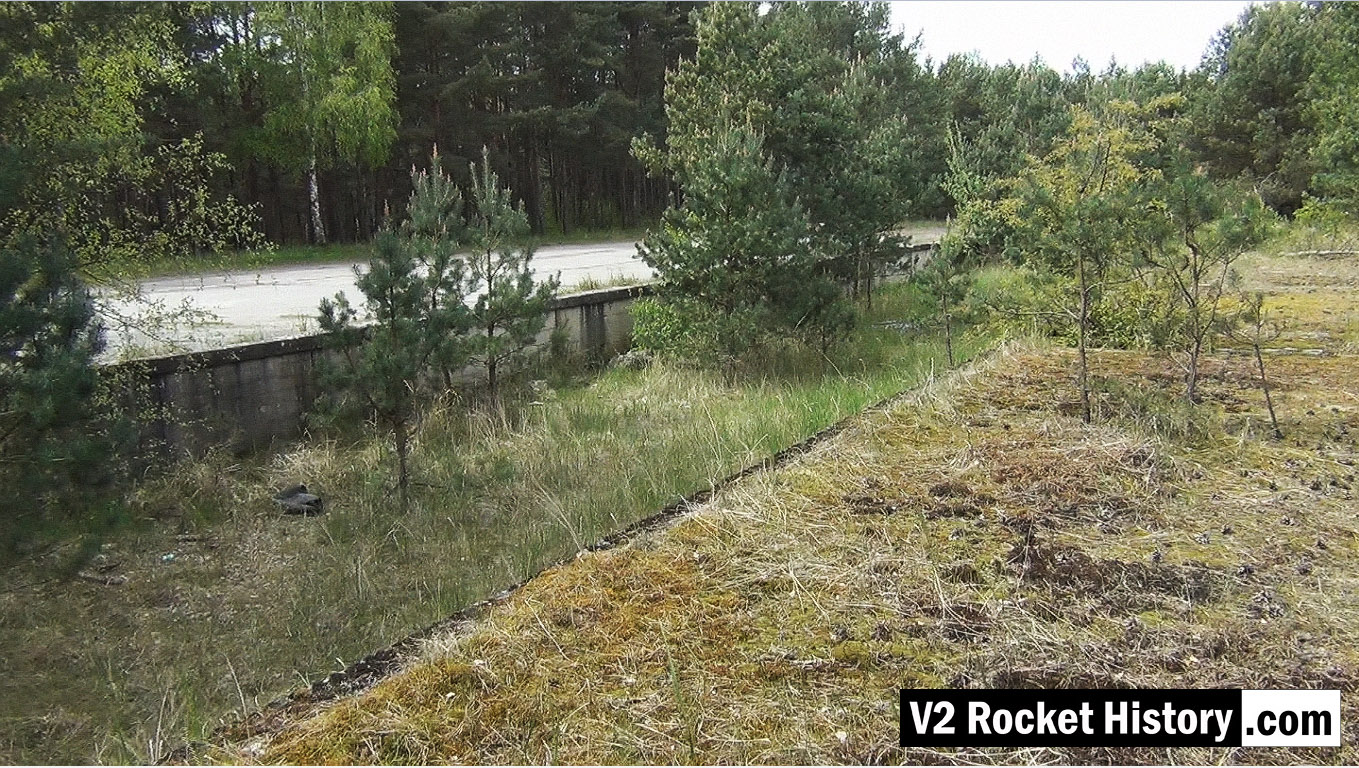
This video screen grab shows the rail and road loading station 9 (also called Die Verladerampen or in English, The loading ramps). The wall and light coloured concrete pan in the background is from the 1940s.
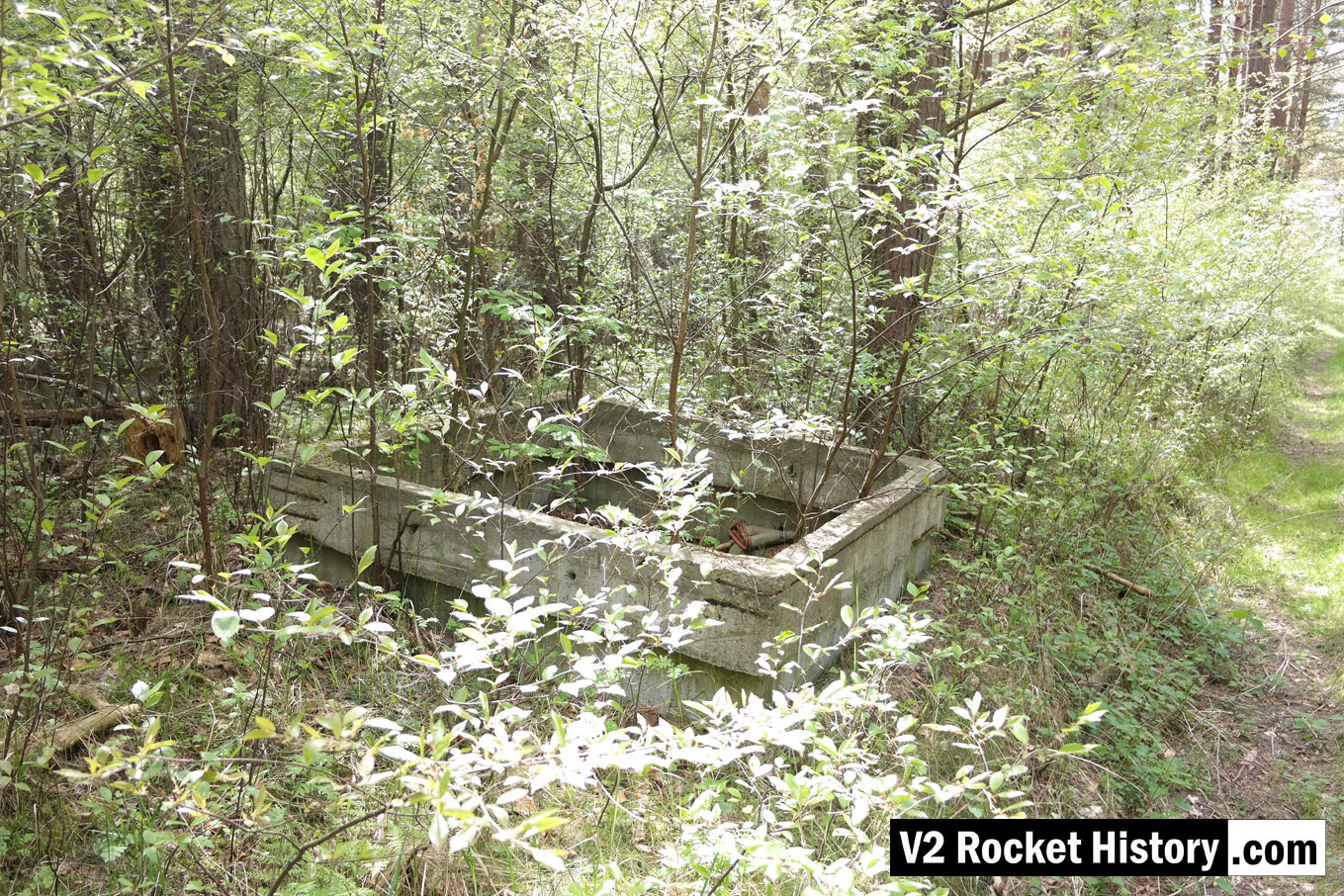
This small prefabricated concrete enclosure only has 800mm of wall section remaining. It is situated on the south side of the rail line and about 70m from the West end of the F1/Admin railway platform south of the factory (see map belew). Its function is not known to us but it may have housed electrical relay equipment.
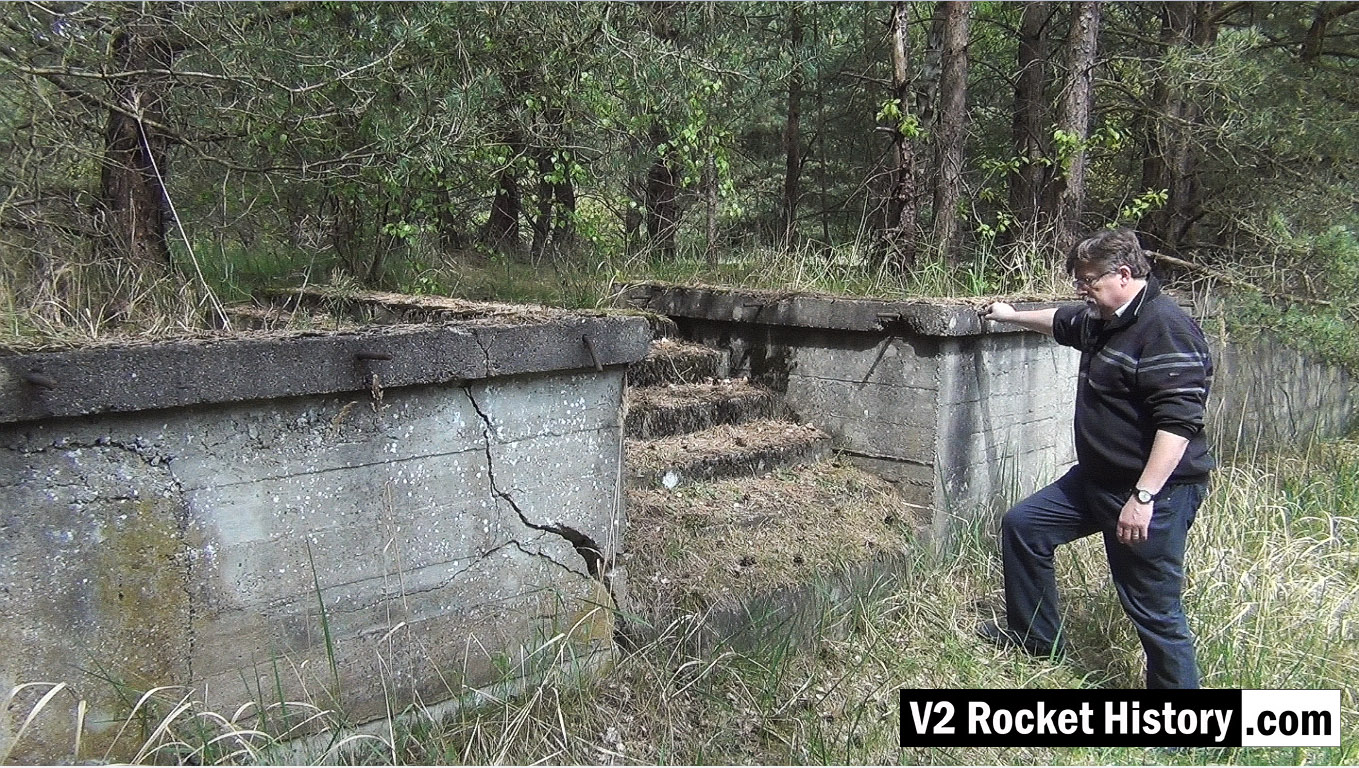
This video screen grab shows Robert about to climb the steps up onto the rail and road loading station 9 (also called Die Verladerampen or in English, The loading ramps). This storage and loading facility was never finished during the war and was intended to be a more elaborate with large storage buildings – but the pressure of war and constant use of the area prevented further development. The area is still surprisingly intact today with a strong correspondence between modern ground detail and historical reconnaissance photography.
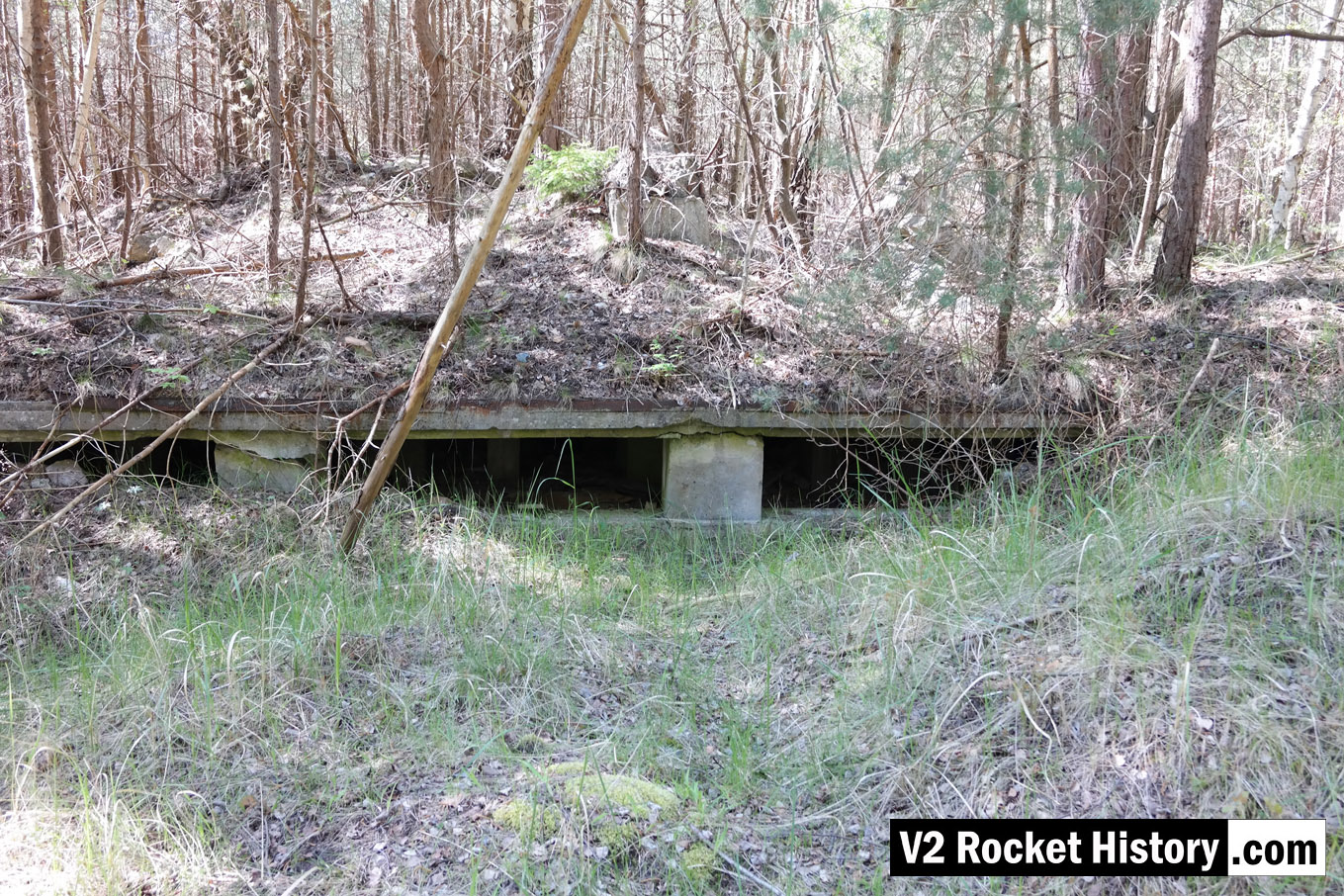
F1 Pre-Production Hall. The area below transformer station no2 (Trafo Station II). Prisoners are known to have hidden and slept in this narrow area. The first time we explored this very low and confined area in April 2011 we found the remains of two small mattresses. This is one of only a handful of areas among the ruins of F1 that still has a ceiling.
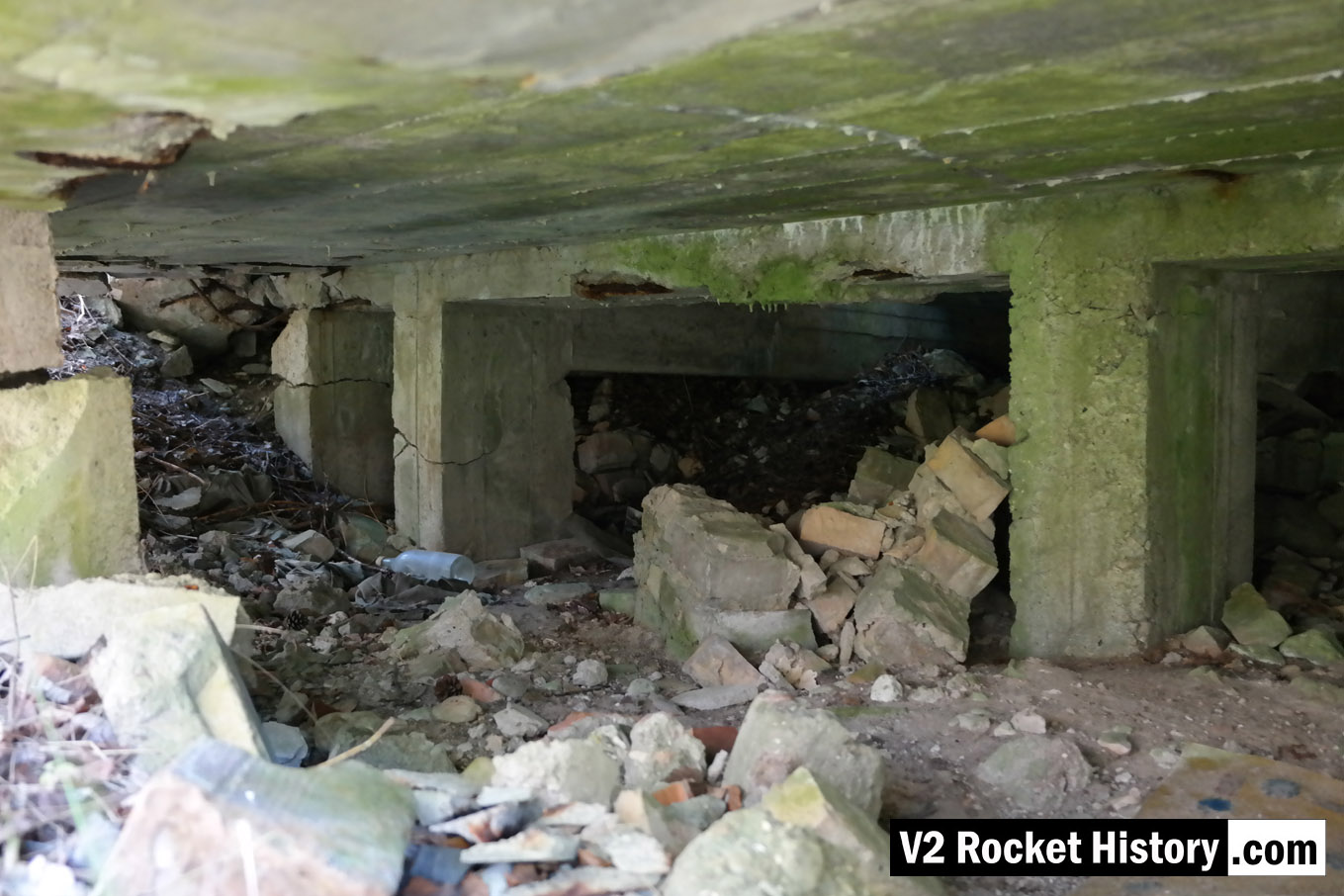
F1 Pre-Production Hall. The area below transformer station no2 (Trafo Station II) seen from inside. Prisoners are known to have hidden and slept in this narrow area. The first time we explored this very low and confined area in April 2011 we found the remains of two small mattresses. This is one of only a handful of areas among the ruins of F1 that still has a ceiling.
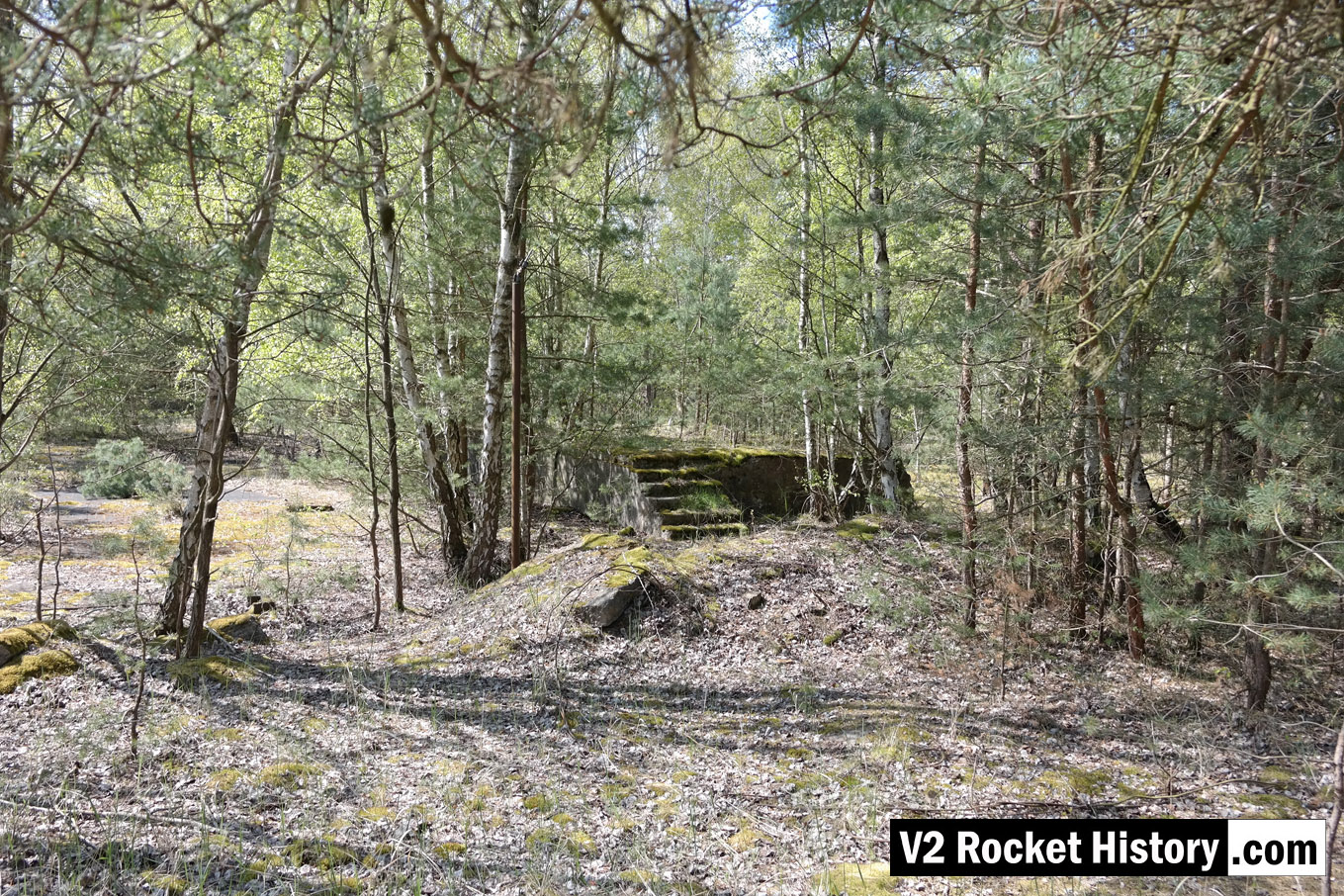
The remains of the a rail and truck loading stage located in the long oil storage shed adjacent to the IW repair and maintenance hall (IW R&MH) are substantial and have intact steadying chains along the south edge of the platform. There are access steps to the west and east ends (east shown). This loading stage was originally furnished with a wooden platform.
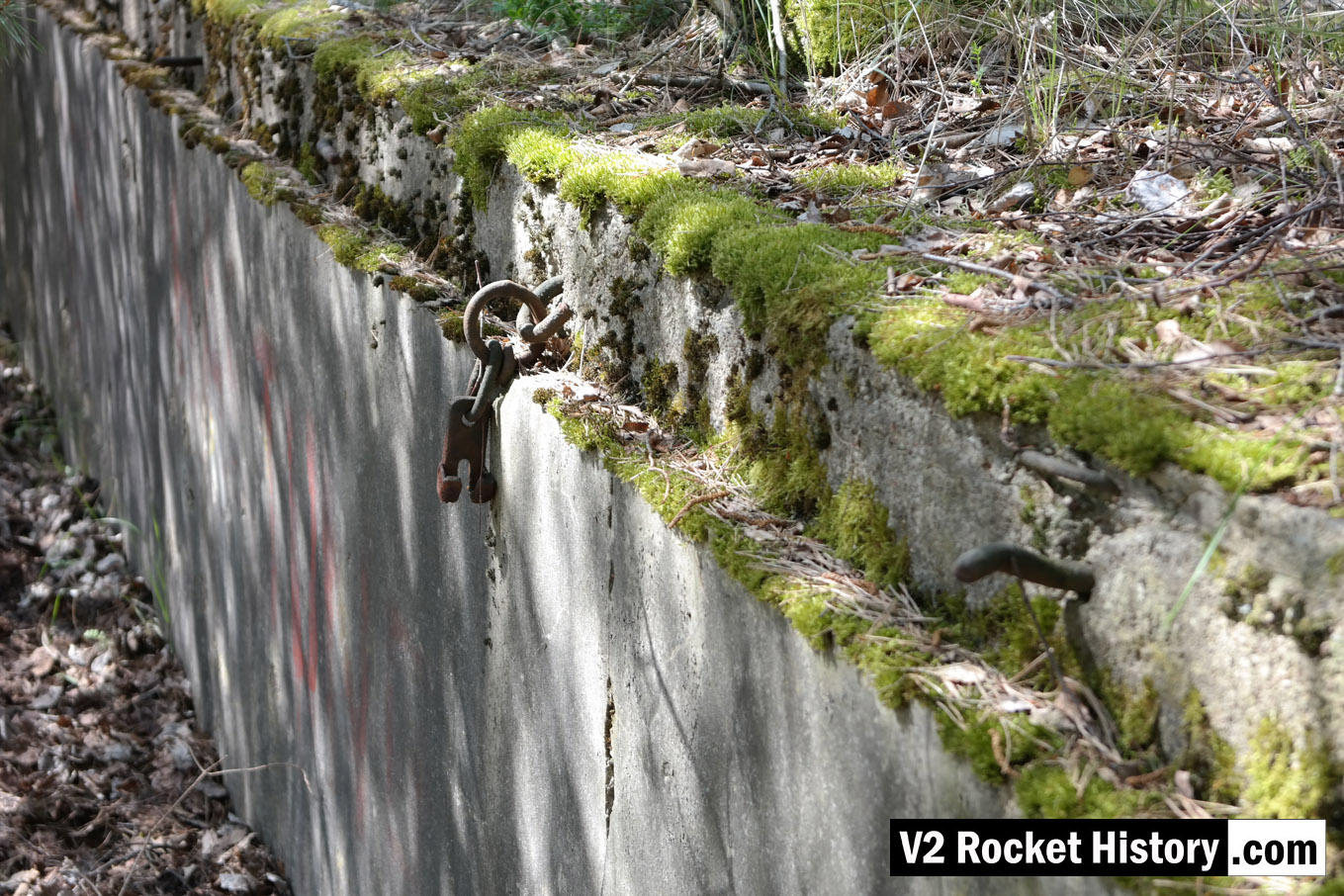
Another shot of oild shed rail and truck loading stage showing steadying chains along the south edge of the platform. Steel studs can be seen that originally held the timber framework of the platform.
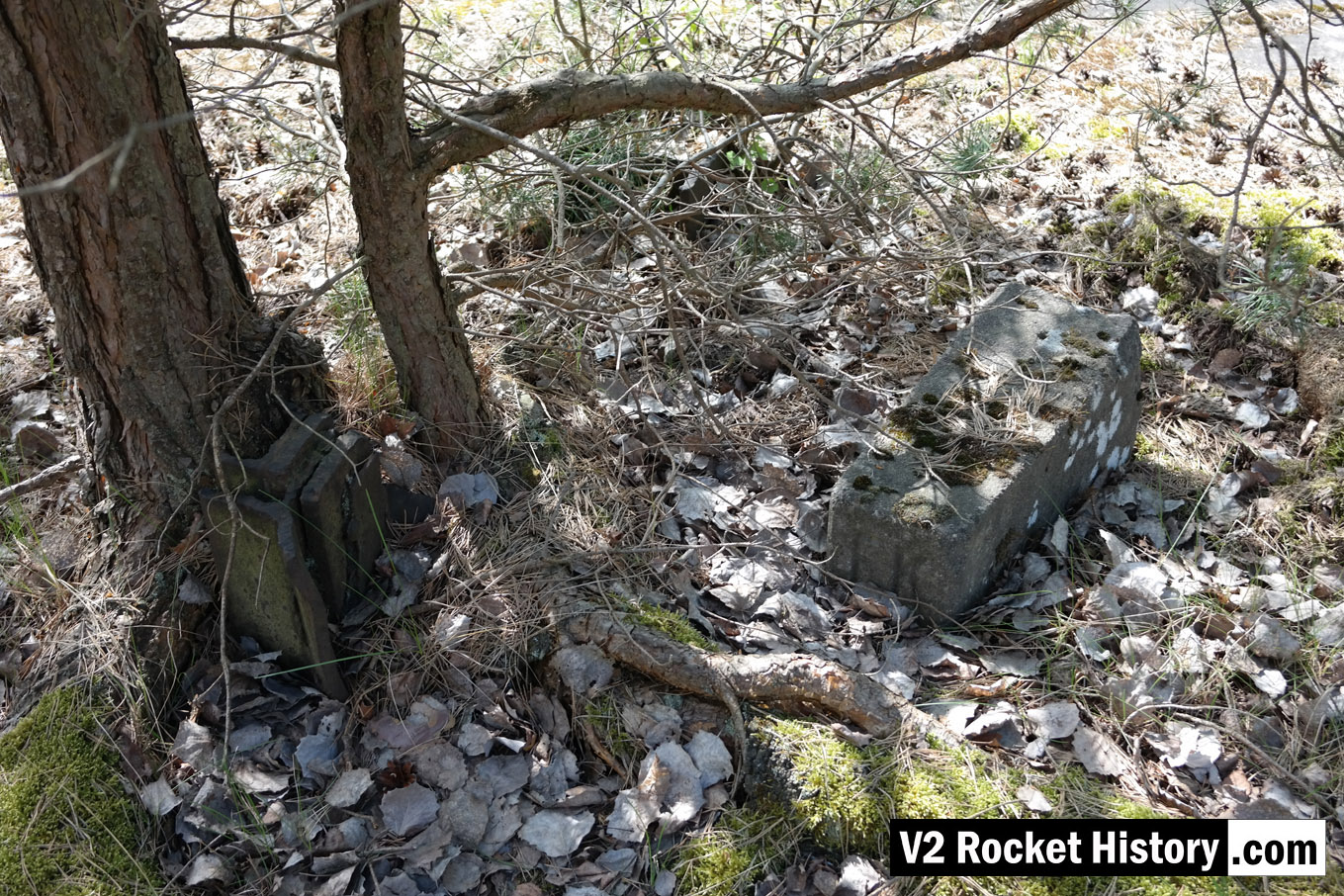
A gas and oxygen lance has been used to cut through the I-beams and girder supports that comprised the main wall and roof supports of the long ‘oil storage’ shed adjacent to the east-side of IW R&MH. The tapering stone with the letters FK moulded into the top, would appear to be a location marker – possibly to direct traffic to the correct doors of the main building. We found others like this in the vicinity.
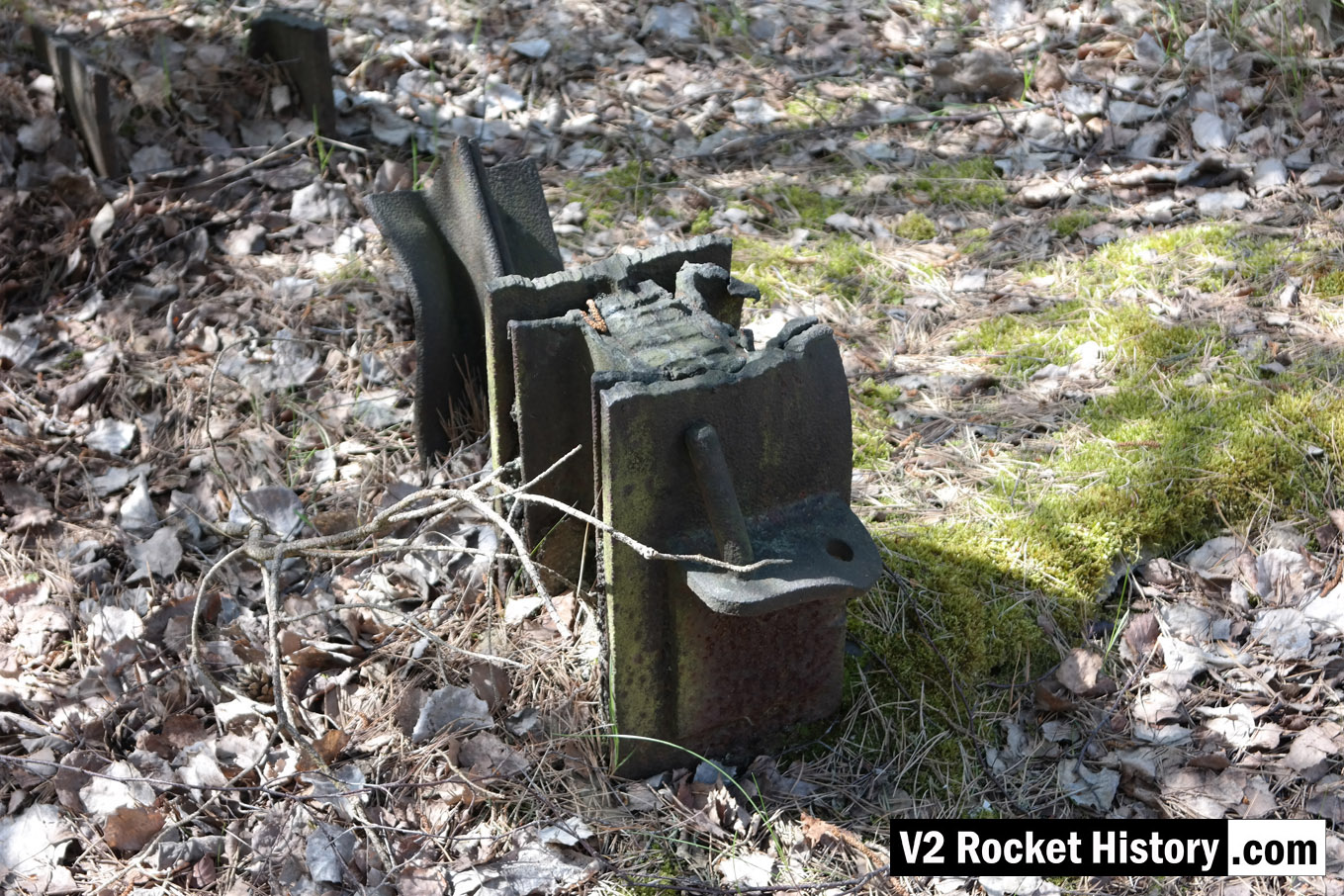
Photo shows the cut stump of an heavy upright support girder. The ragged profile of the cut shows that it has been cut down with an oxygen and gas torch or possibly a larger fuel and oxygen device like a thermal lance. The steel support still has the bottom support pin for a large door. Note that although the girders have been gas-cut there is a great deal of mechanical damage to the steel work that was not caused by the cutting work. Considerable force would be required to bend the middle girder in the way shown, even if it was much longer at the time the bend was created. The upper superstructure of the storage shed may have been part demolished using a bulldozer. Or perhaps the East German Army may have used the site for explosives training – signs of demolition explosive use are in evidence nearby. The map under the album presentation of this picture shows the exact location of the girders.
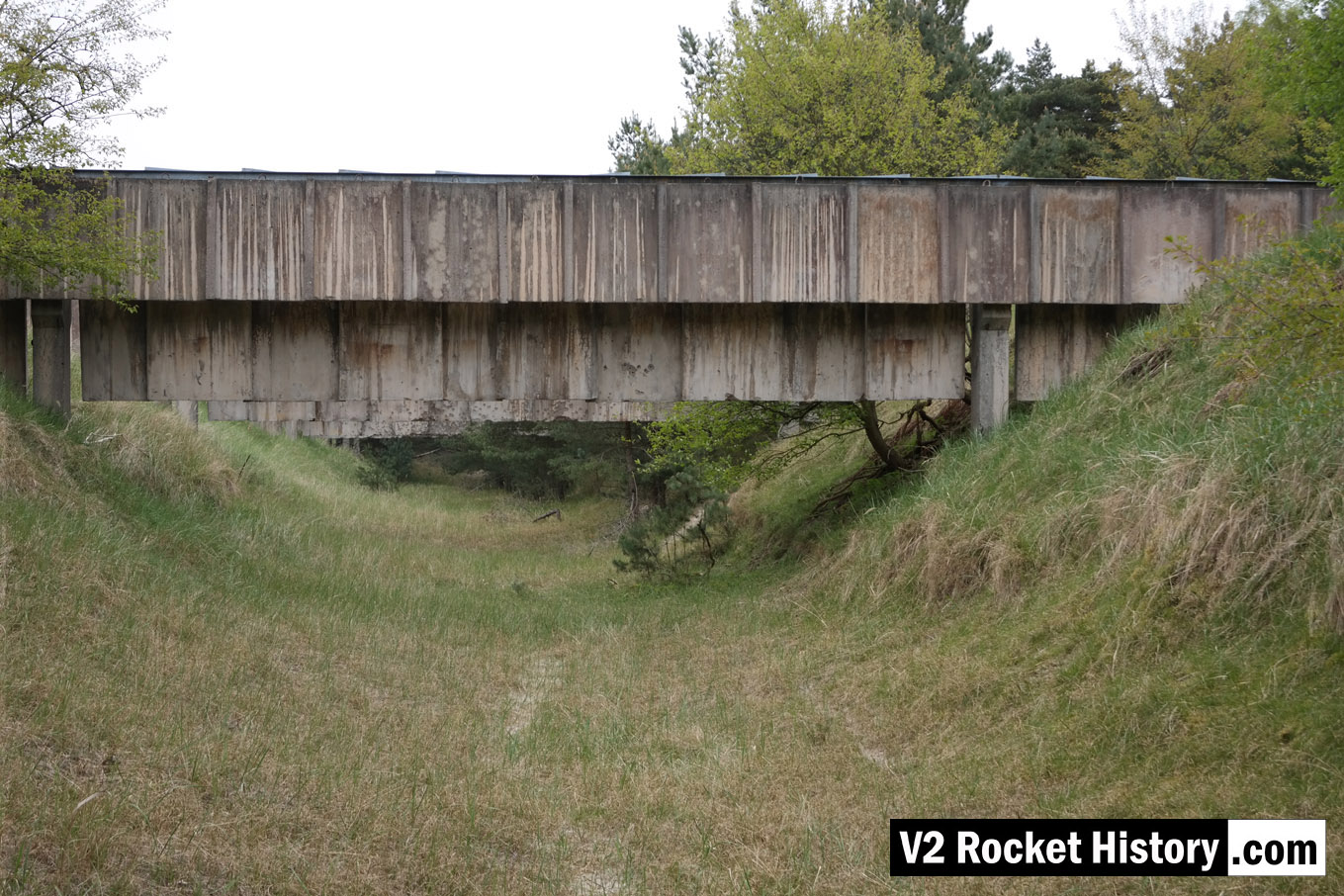
Photo shows the remains of a shooting range built by the East German Army. In 1944 the area about 200m in front of the camera and to the left of this picture is the emergency rail-loading area used after US air raids in August damaged rail lines and other regular freight loading infrastructure. Today, it is a peaceful thoroughfare used mostly by deer and rabbits.

Valves
Images of the main valves involved in the propellant flow of the A4 / V2 liquid fuelled rocket engine
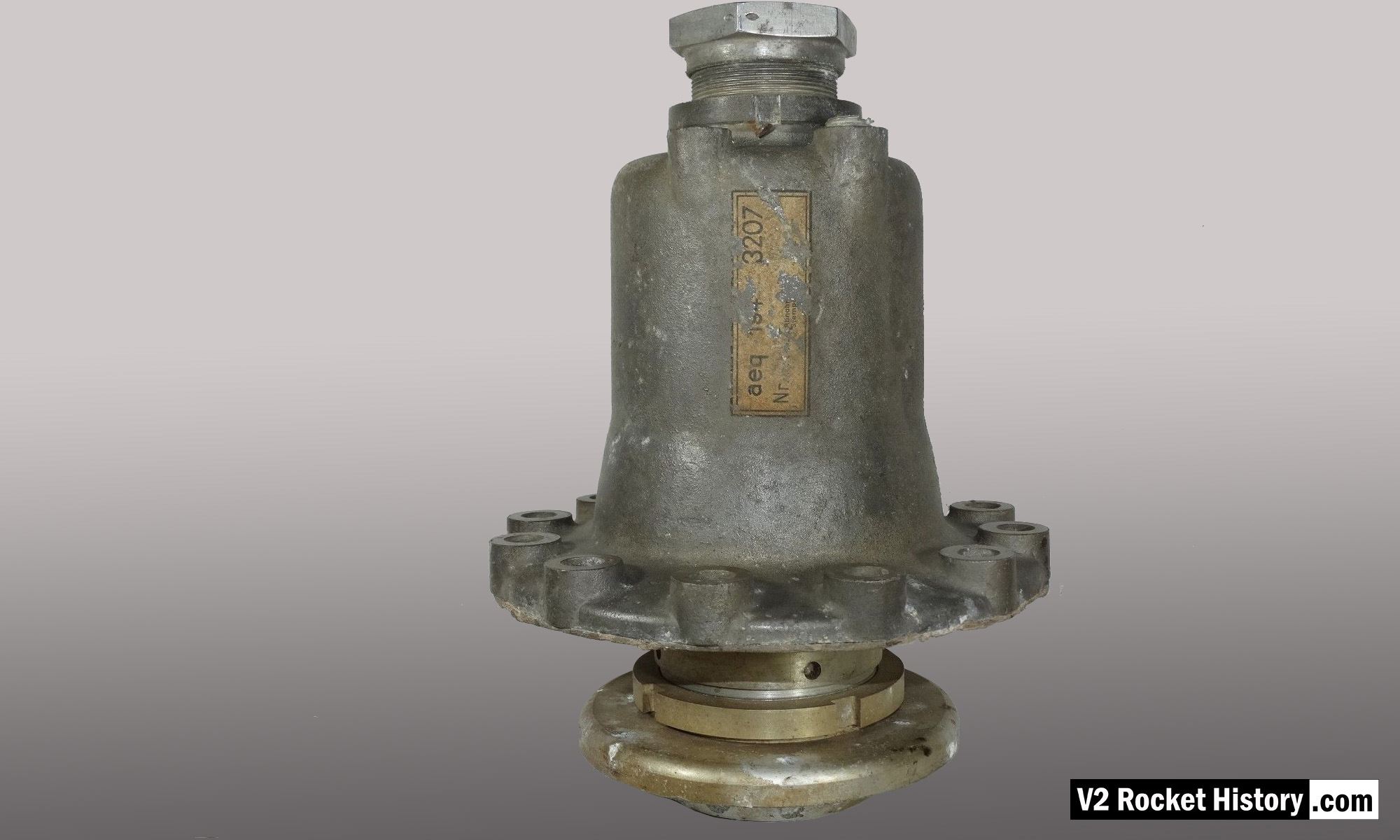
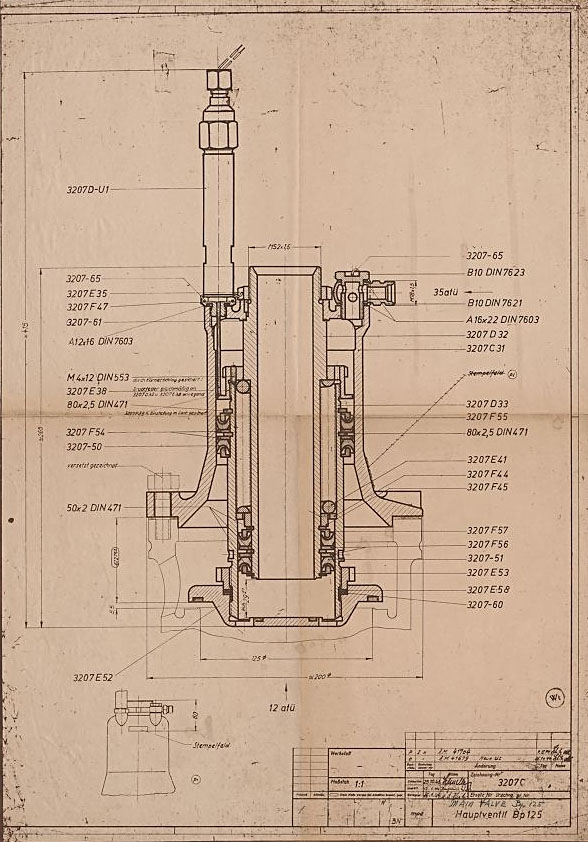
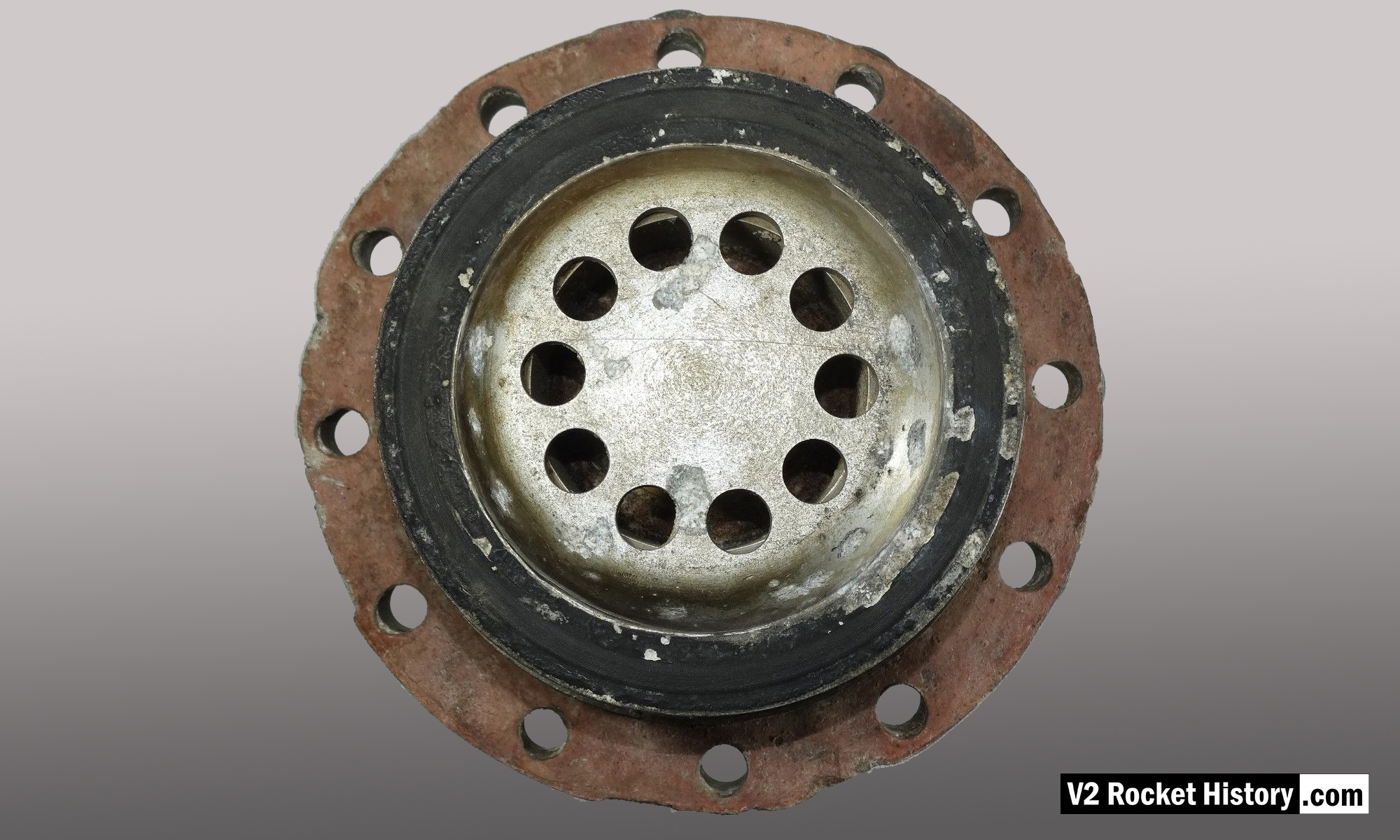
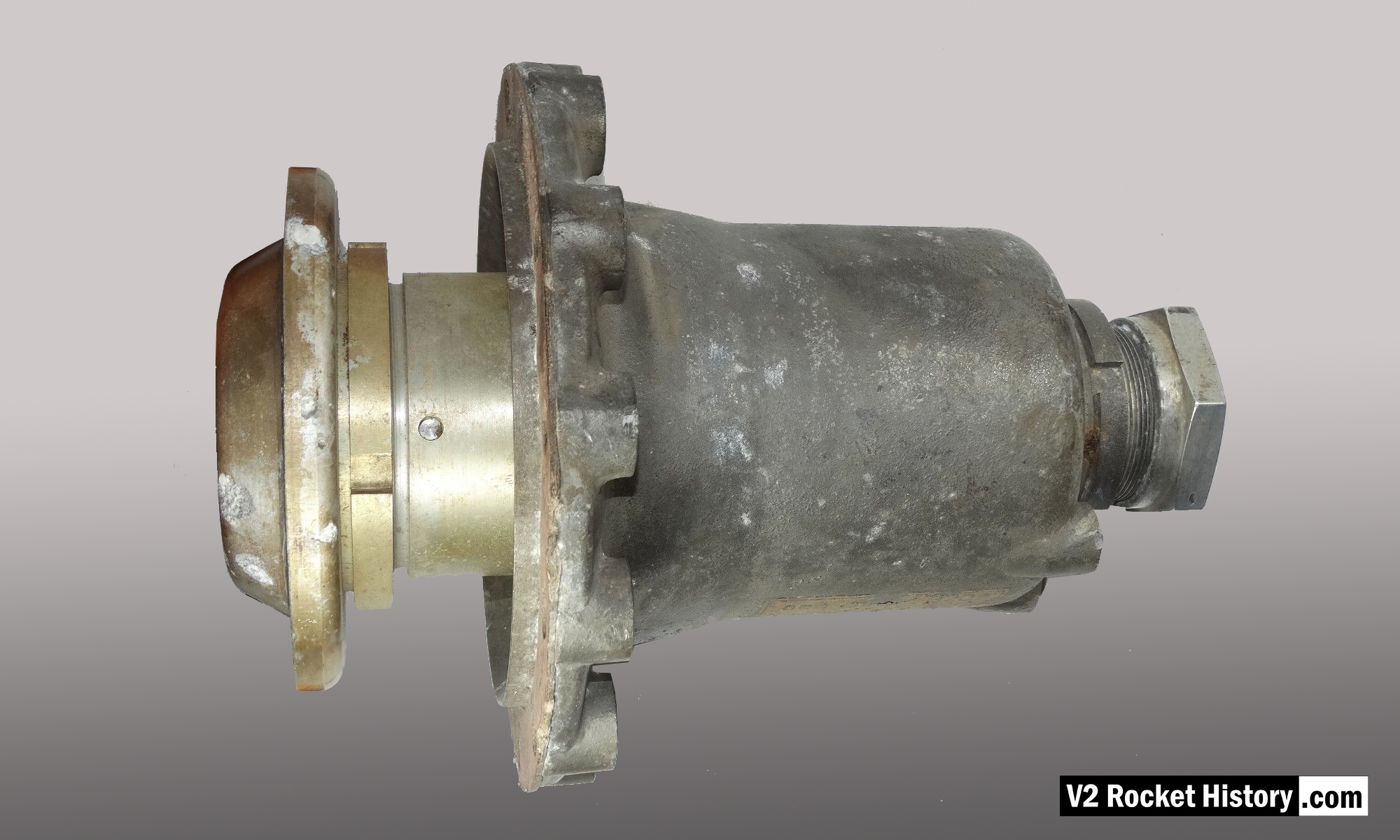
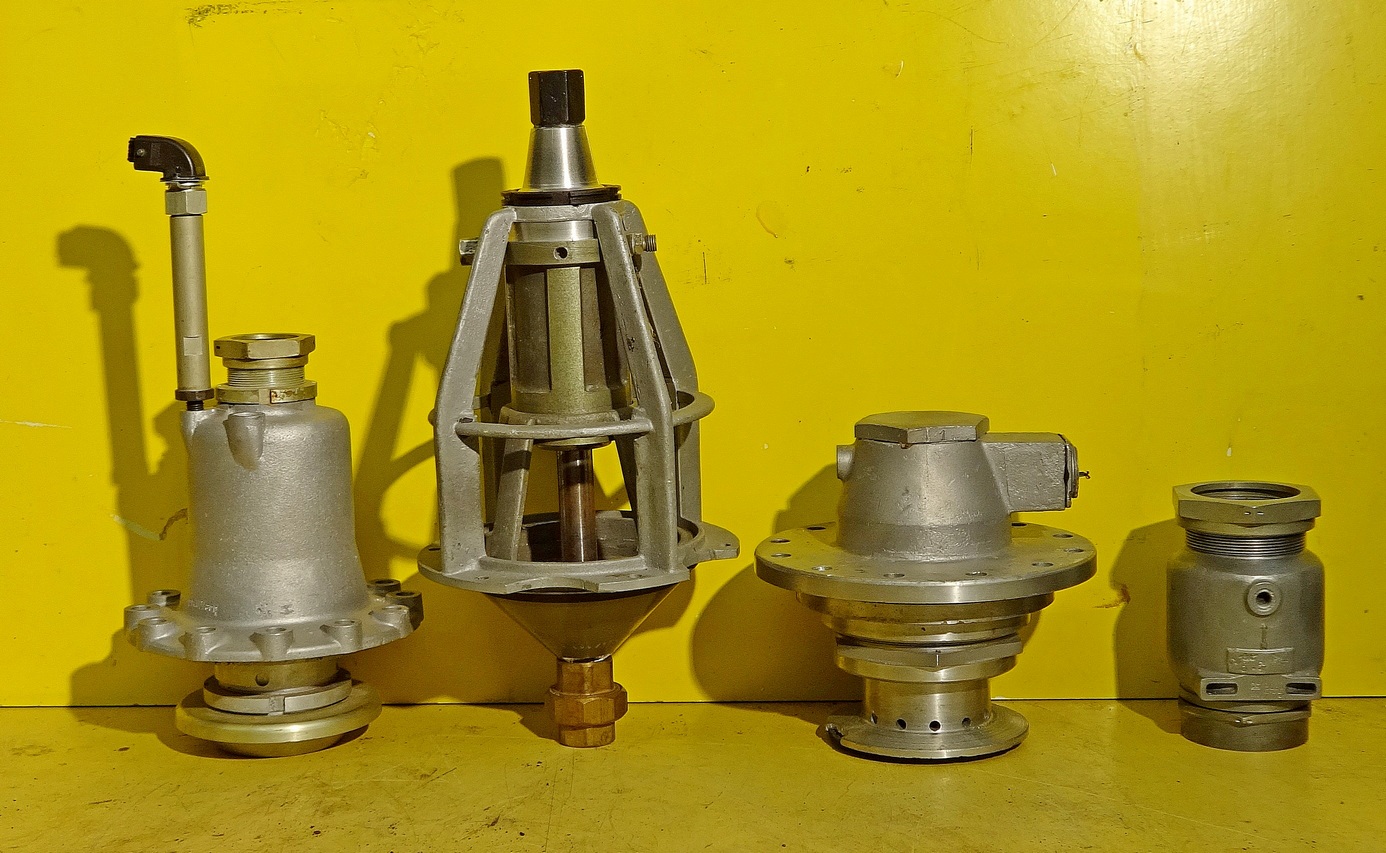
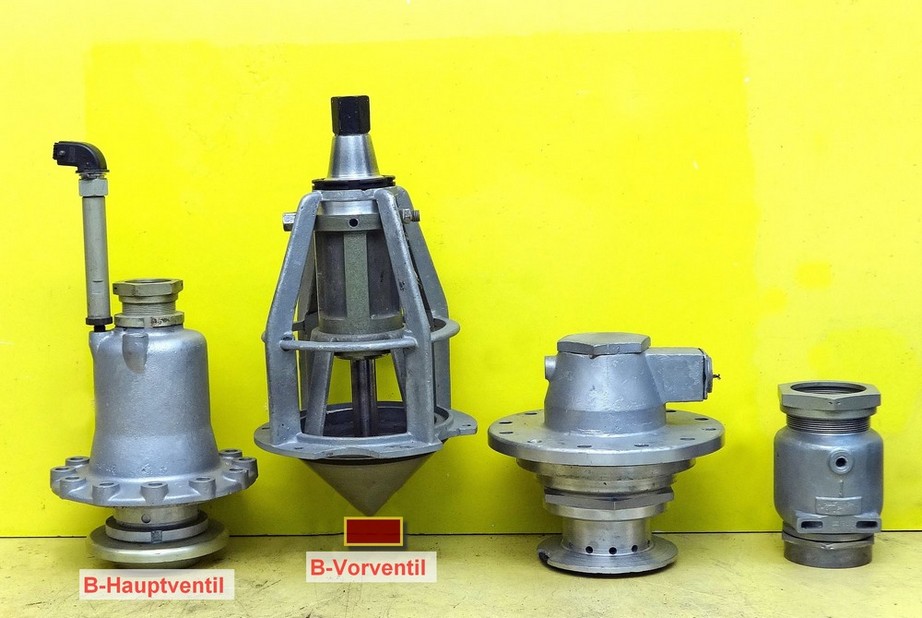
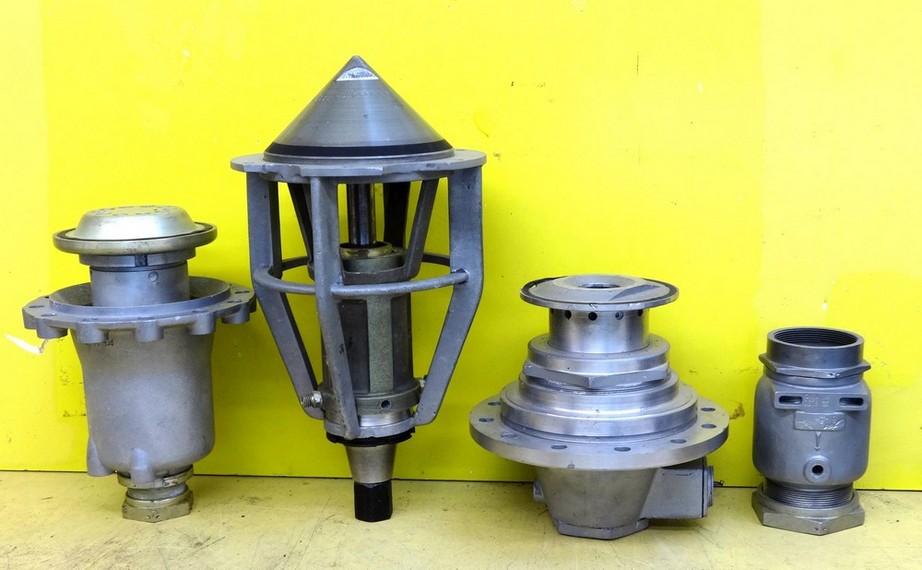
Images of the main valves involved in the propellant flow of the A4 / V2 liquid fuelled rocket engine
Relic of main alcohol valve with manufacturer code aeq (aeq = Bartoc & Co., Maschinenfabrik u. Giesserei Hedwikow,bei Caslau (Caslav) Czech Republic). An air (nitrogen) inlet pressure of 440 to 530 psi (30 to 36 Bar) was required to close this valve against its internal spring and the force of the turbo-pump. The large nut at the top is the connection for the fuel return (or ‘revolving’line) pipe, and the air and electrical input ports can be seen to the right (air), and left (elec.) just below this point. V2RH image

Anatomy of the V2: 18-pot injector head
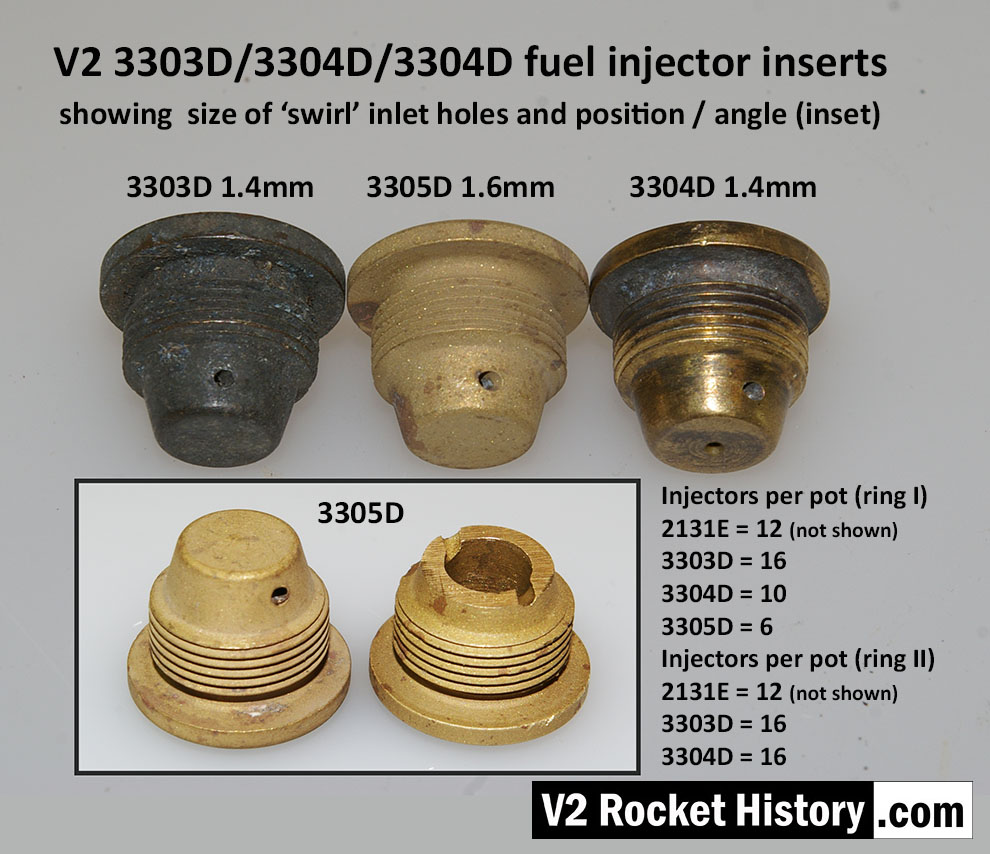
V2 fuel injector inserts 3303D, 3304D, and 3305D for injector pot echelons D and E. Photo shows swirl inlet aperture size and position.The total number of each insert type is shown, each of the 18 pots carried a total of 44 inserts. An additional 24 feed holes were drilled into the burner cup, occupying two rows B and C having 12 holes each. V2RH image
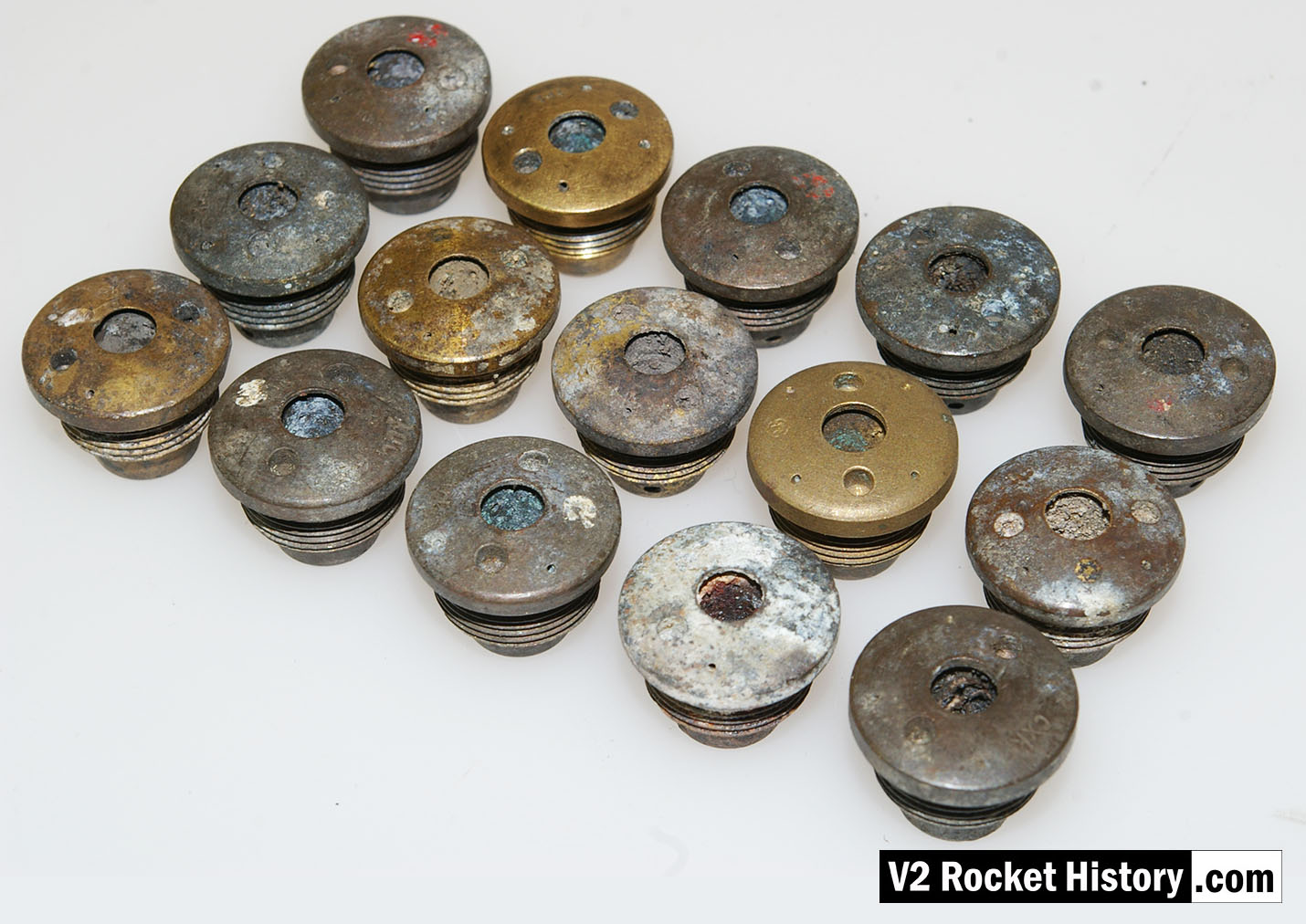
Sample set of 3303D type fuel injector inserts that were found in Peenemünde in part of a group that were bunched together in a space about 300mm in diameter with the remains of packaging. They appear to be manufacturing samples and and some have been graded with numbers 1,2,3, as well as with red and white paint to show the burner cup echelon position (C or D). Five different manufacturers are represented in this group. V2RH collection image
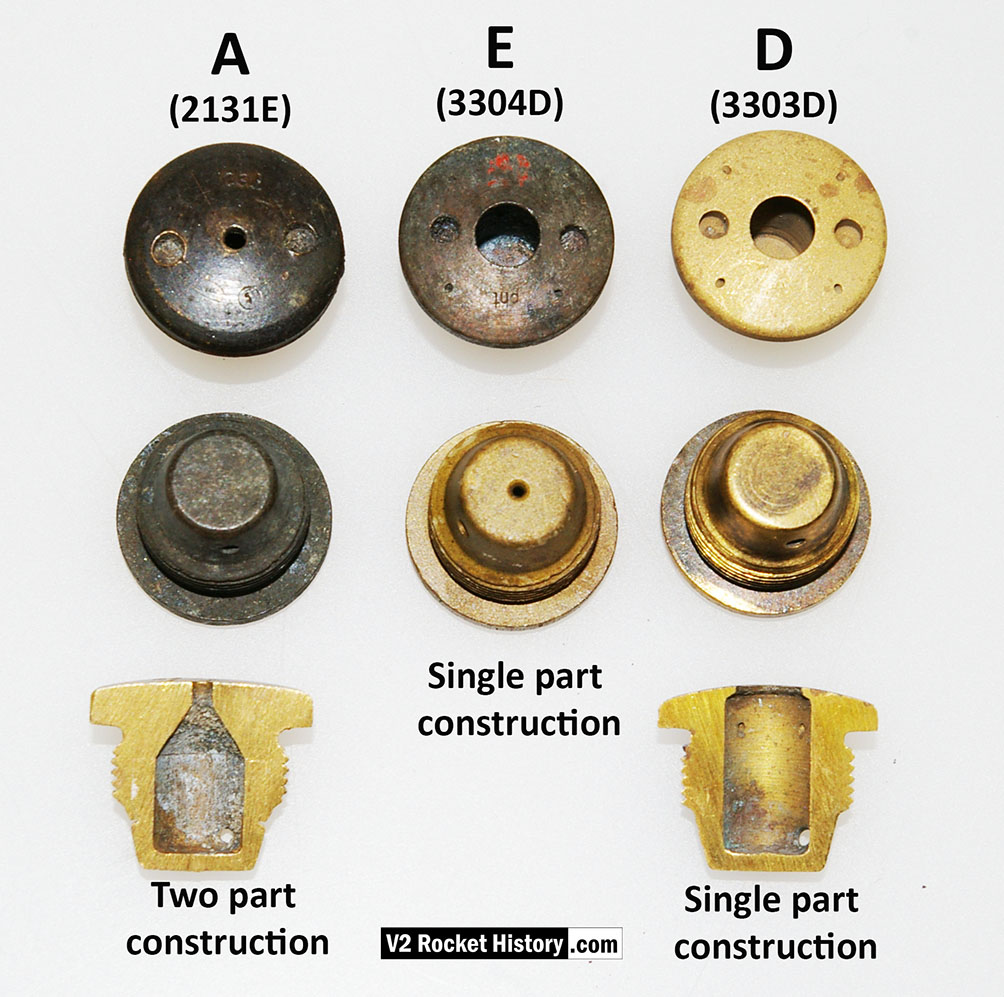
Fuel injector inserts for production series 18-pot injector head. The top row shows the injector face, second row shoes the same types from the rear. The lowermost insert have been halved to reveal the cavity shape, orifice edge, inlet and cooling apertures. Note that the insert in column A, 2131E, is two piece construction, and pressed together for assembly (see additional photo). On test, the parts had to remain together under a separation force of 300kg.
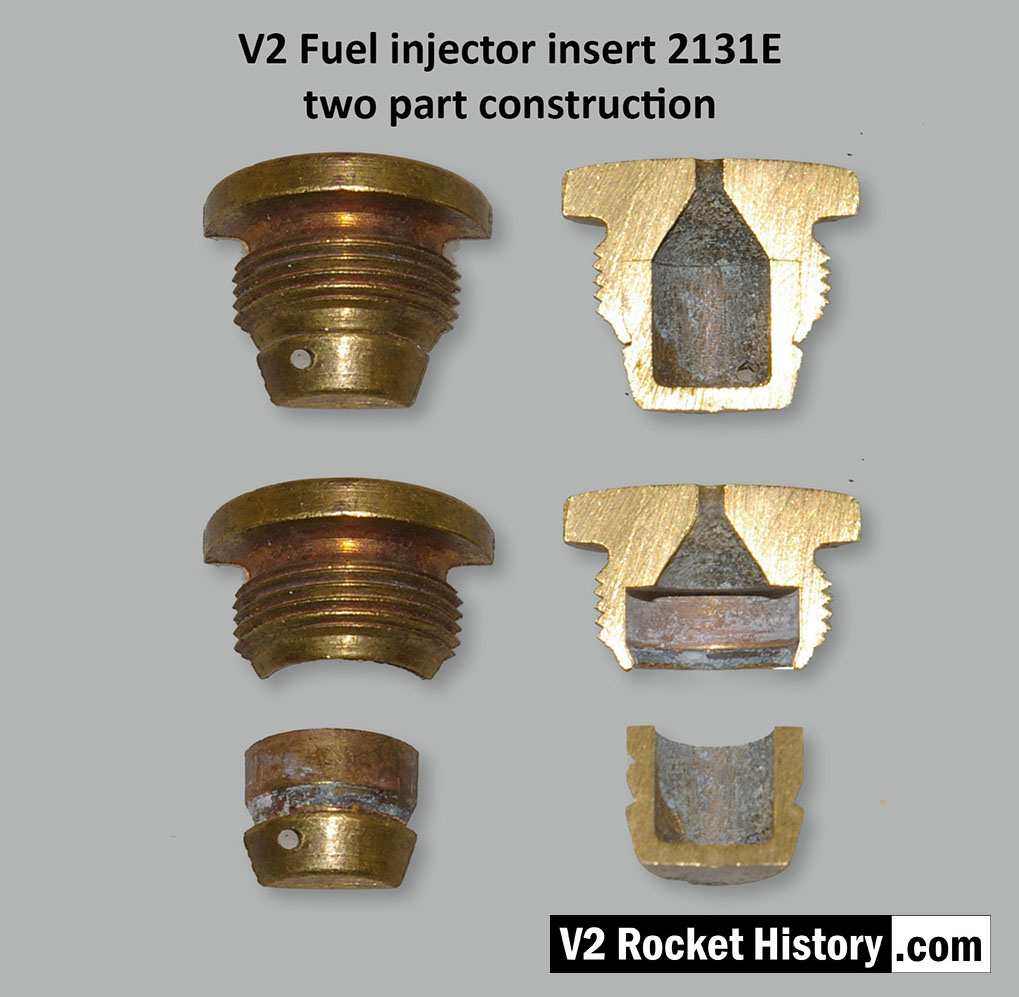
V2 Fuel Injector insert: part code 2131E from injector pot echelon A (nearest to LOX spray head). The push-together two part construction of the insert is shown here. The two parts were pushed together in a specially shaped tool set that compressed the thin skirt on the female part into a recess cut into the male part. The failure test for this component required that the mated parts resist a separating force of 300kg. The two part design was dictated by the small size of the 2mm exit orifice and the funnel shaped introduction to the exit orifice. In the case of the other three standard inserts, the large 6mm exit orifice allowed a sub 6mm milling cutter, with a thin support shaft and a top chamfer, to be used in such a way that the area below the exit orifice could be undercut to create an injector cavity with a diameter larger than the 6mm entry point.
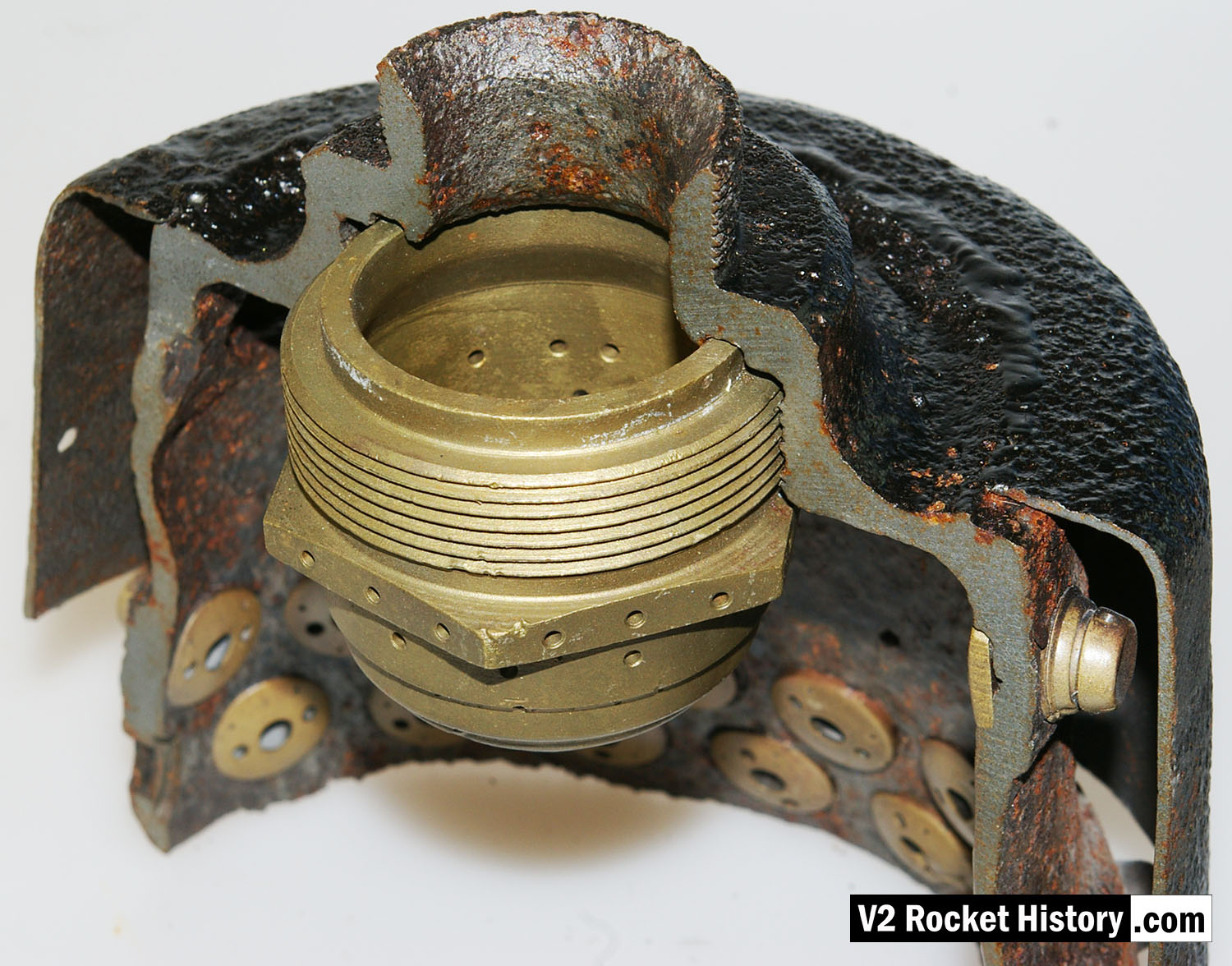
Cutaway section of fuel and liquid oxygen (LOX) injector pot. The exhibit shows the bell shaped thick inner wall of the burner with three tiers of fuel injector inserts (A,D, and E). The central copper alloy LOX spray injector is also well displayed in this image. The thin steel outer shell of the burner cup is shown and affords a good view of the head cavity that supplies fuel to the injector inserts – one A type injector is shown party cut through on the right, its rear portion showing inside the fuel cavity. V2RH image

Cutaway section of fuel and liquid oxygen (LOX) injector pot. The exhibit shows the bell shaped thick inner wall of the burner with three tiers of fuel injector inserts (A,D, and E). As well as the two rows of plain drilled apertures B and C. The central copper alloy LOX spray injector is also well displayed in this image and shows the three letter armament code of the manufacturer (elr = H.K. Rudolf, Pilsen) and the 1943 date of manufacture on one face of the hex nut. Note the close proximity of the tier A injector inserts to the LOX injector. The spary from these injectors plays directly onto the lower section of the LOX spray head. This section of the burner cap had the lowest temperature and as a result tier A insert did nor require cooling pres. See associated picture. V2RH image
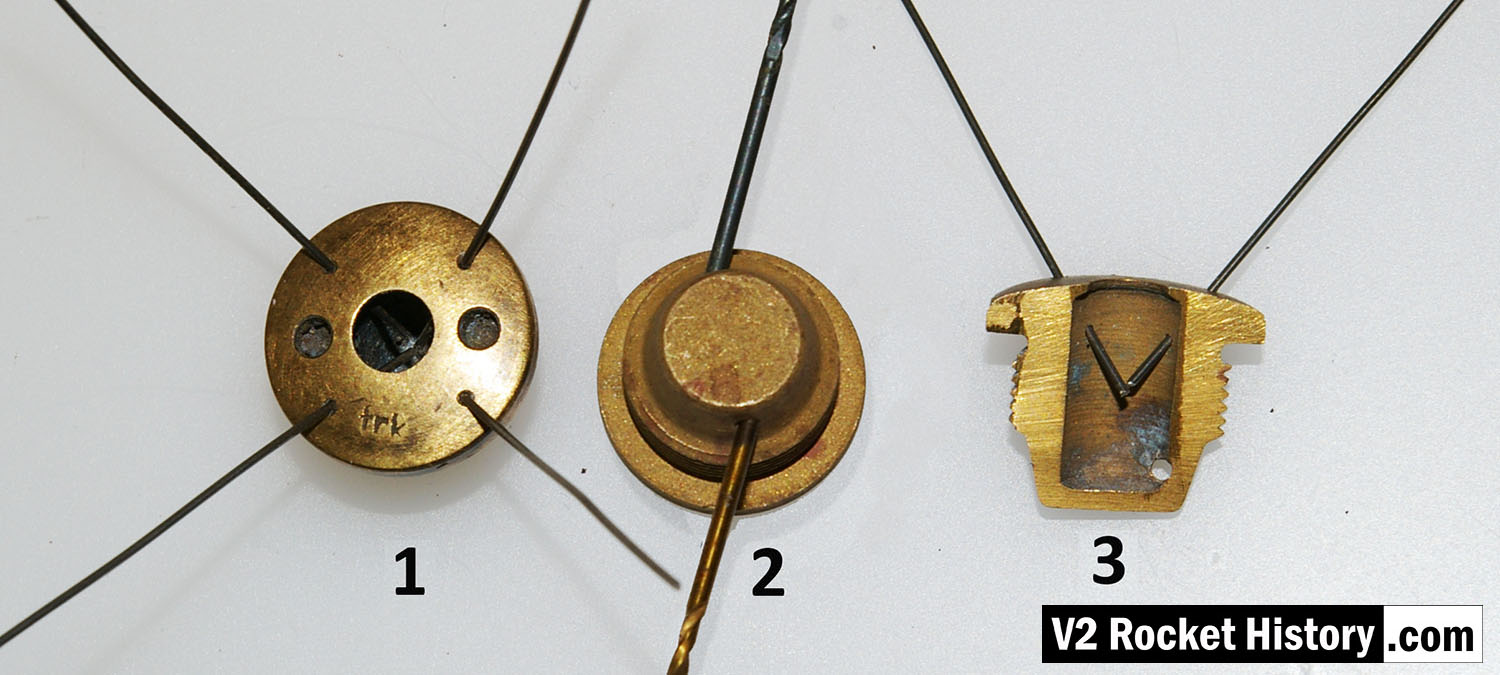
Standard fuel injector inserts for production series 18-pot injector head. Insert 1 (3304D/3305D) shows four thin wires demonstrating the angles of all four ‘cooling’ pores. Insert 2 (3305D/2131E) has two 1.3mm twist drill showing the edge bores for the gyroscopic swirl inlets. Insert 3 (3305D) shows another view of the cooling pore angle and origin. V2RH image

The injector head fragment shown here, is from an 4B 1000 kg thrust engine that was developed at Kummersdorf in 1938/39 by Dr Walter Thiel’s combustion research group. The fragment, clearly the remains of an explosion, was actually found in a scrap pile in Peenemüde but the engine was probably tested (and destroyed) at the Kummersdorf army testing station. V2RH collection image.

Relic of prototype A4 25-ton 1940/41 aluminium injector head basket (or pre-chamber) showing 68 copper alloy inserts in 5 rows. The standard configuration would later become 44 inserts in 3 rows 25 2mm diameter drilled holes in two rows situated at row 3 and 4 (counting from nearest the camera). Photo courtesy Host Beck Collection
Album | V2 rocket fuel injector inserts |
Categories | Anatomy of the V2, Combustion |

The injector head section of the 4B 1000kg thrust rocket engine is a precursor to the injector pot or ‘pre-chamber’ design used later for each of the 18-pots of the 25-ton V2 rocket engine. Most of the essential ingredients are shown in this drawing from 1940. Drawing no 1848E Deutsches Museum München online archive ref FA 014/12829
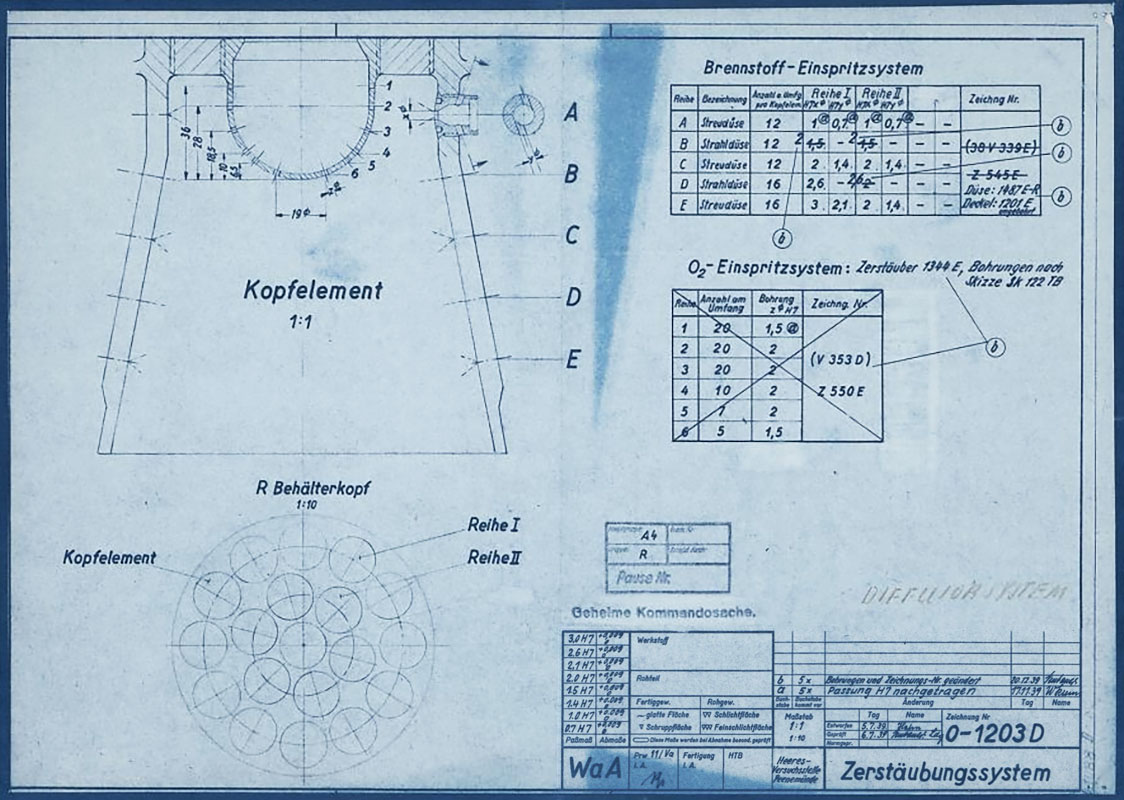
HVP drawing no 1203D showing burner cup ‘diffuser system’ disposition for 19-pot head (at this stage the 25 ton thrust injector head had nineteen so called ‘pre-chambers’ or pots as no central fuel valve was present). HVP drawing dated 1939.
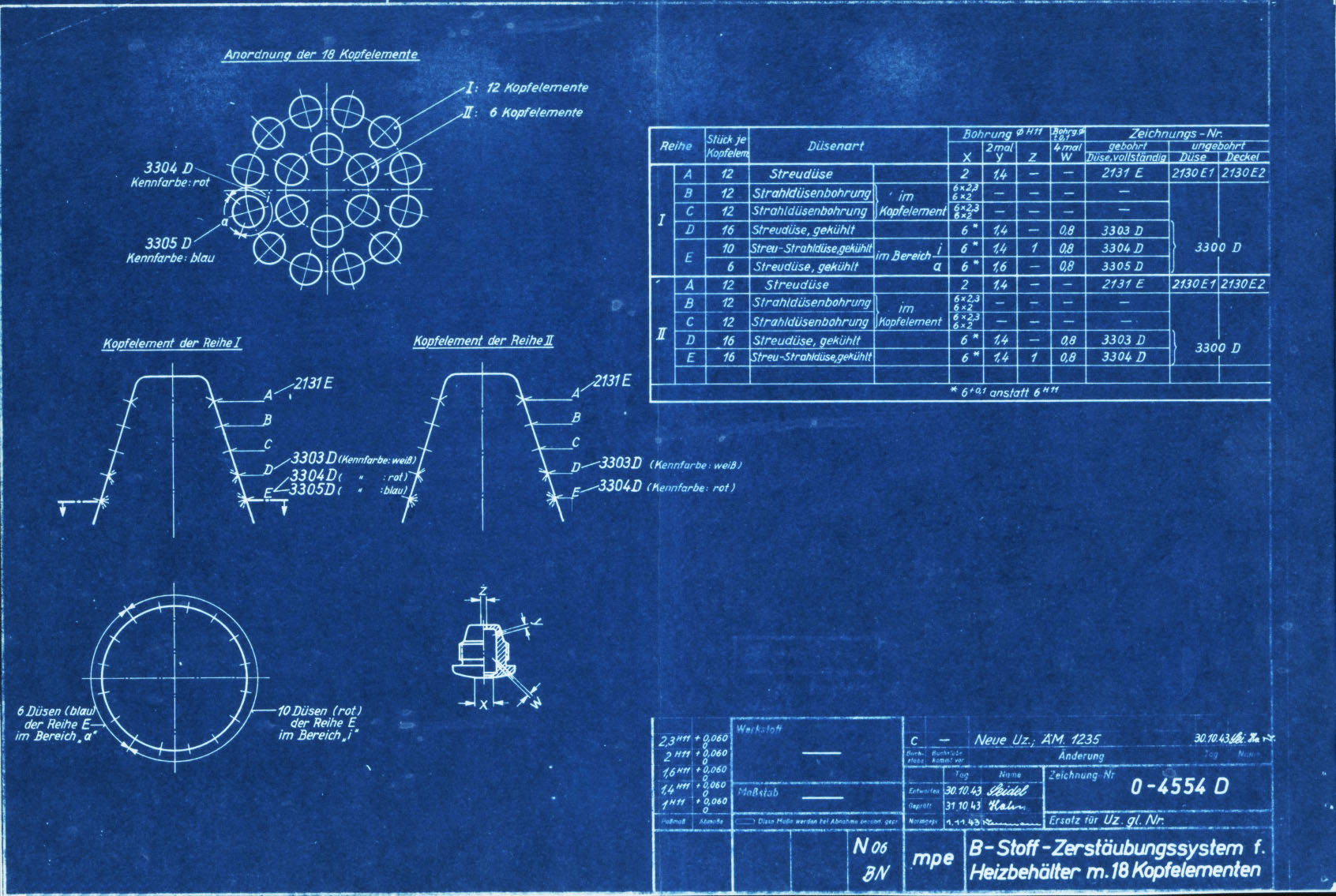
Specification for fuel injector inserts showing orifice size, type, and A to E echelon position. Peenemünde document dated 30th October 1943. Of note on this document is the combination of high and low volume injector inserts (3304D and 3305D) in the echelon E position of the 12 cups comprising outer ring I. It shows that each cup or pot on this outer ring had 16 inserts at the lowermost position E with 12 of the inserts with three inlet apertures (3305D) and 6 with only two inlet apertures (3304D being lower flow volume) positioned in the segment covering 165 degrees and closest to the outside edge of the head. HAP11 (Heimat-Artillerie-Park 11, AKA armament code: mpe), drawing number 4554D, Deutsches Museum München
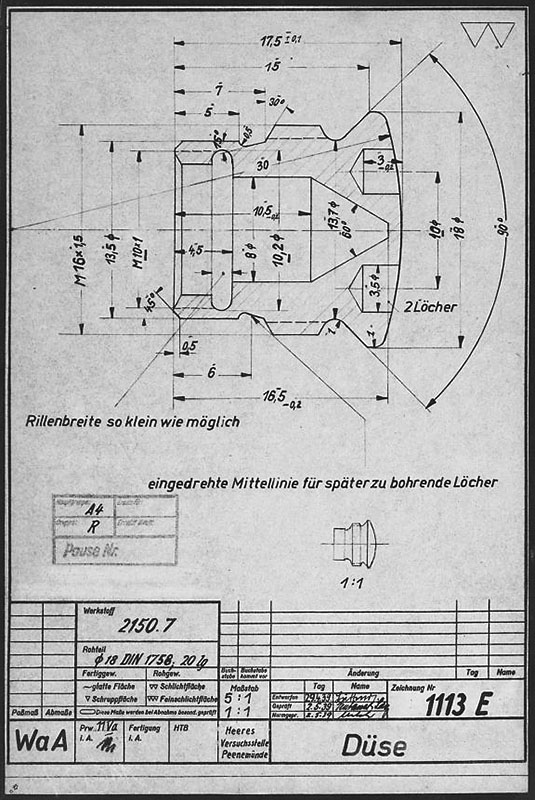
Drawing from the Army Experimental Station Peenemünde dated 1939. The specification describes an insert template that could be used for a range of outlet and inlet orifice sizes. The German text beginning (eingedrehte …) translates as ‘Center-line of screw used for holes to be drilled later’, and the hole dimensions are not specified on this document. HVP drawing number 1113 E, Deutsches Museum München
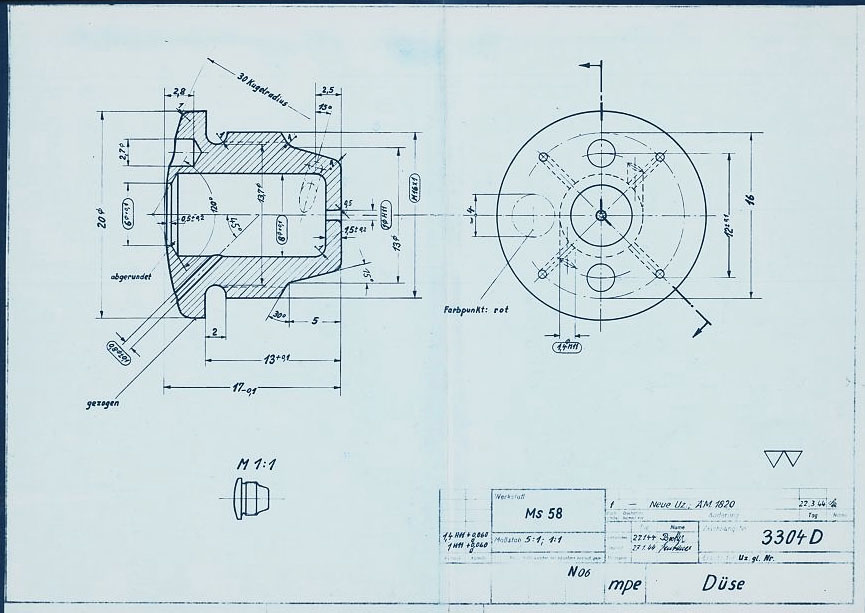
HAP11 drawing of standard 3304D fuel injector screw insert. showing details of primary swirl cavity and orrifice and all additional apertures including the four small cooling pores. HAP11 (Heimat-Artillerie-Park 11, AKA armament code: mpe), drawing number 4554D, Deutsches Museum München
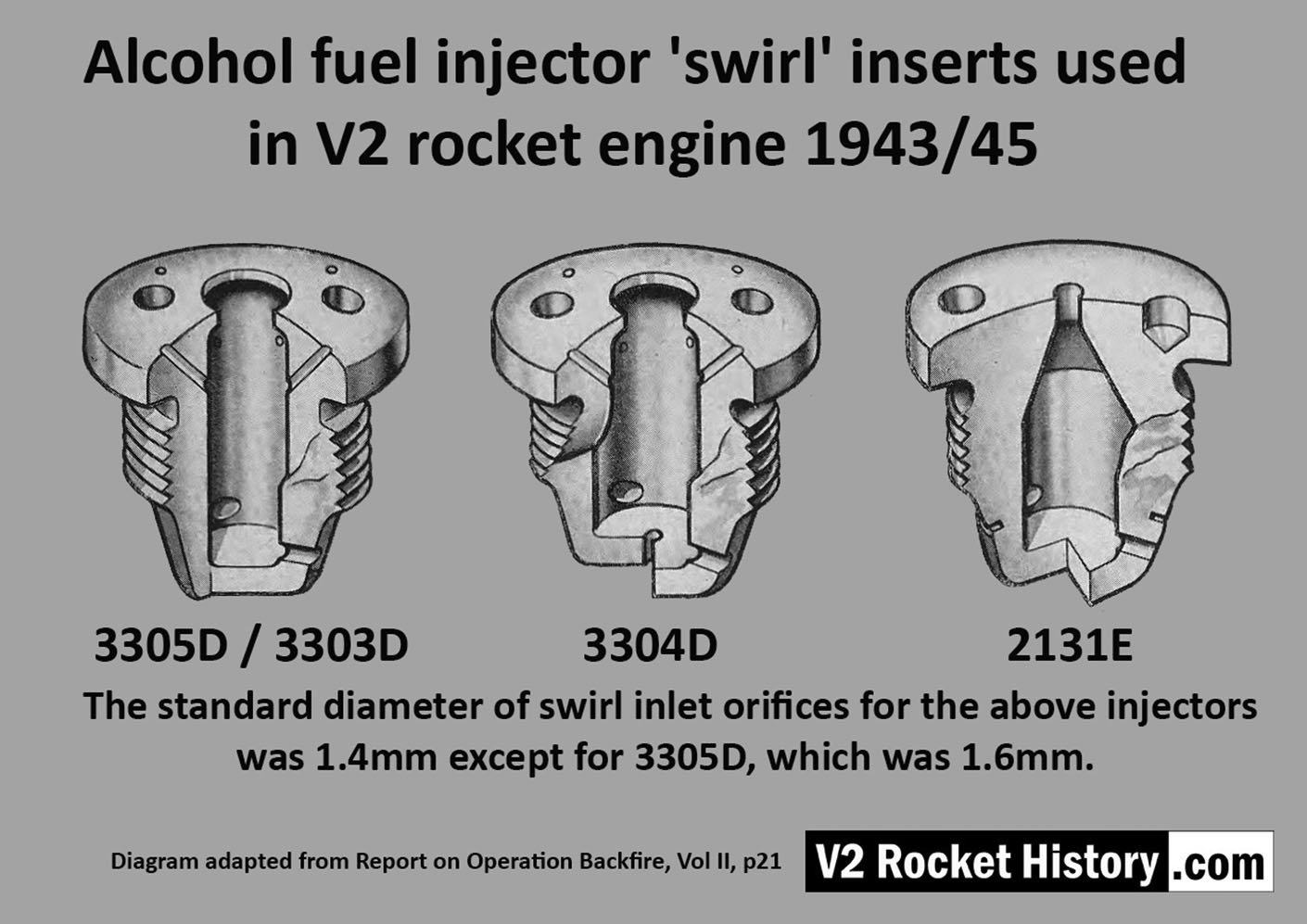
Diagram showing cut-away presentations of the settled configuration of standard four ‘swirl’ inserts used in the V2 rocket engine’s 18-pot head from 1943 until the end of the war. The inserts are shown with their drawing code identification. All of the insert types used in the injector head are shown, however there were additional screw-in type fuel supply inserts, used to provide a fuel cooling balance function, located radially in the lower part of the combustion cavity.
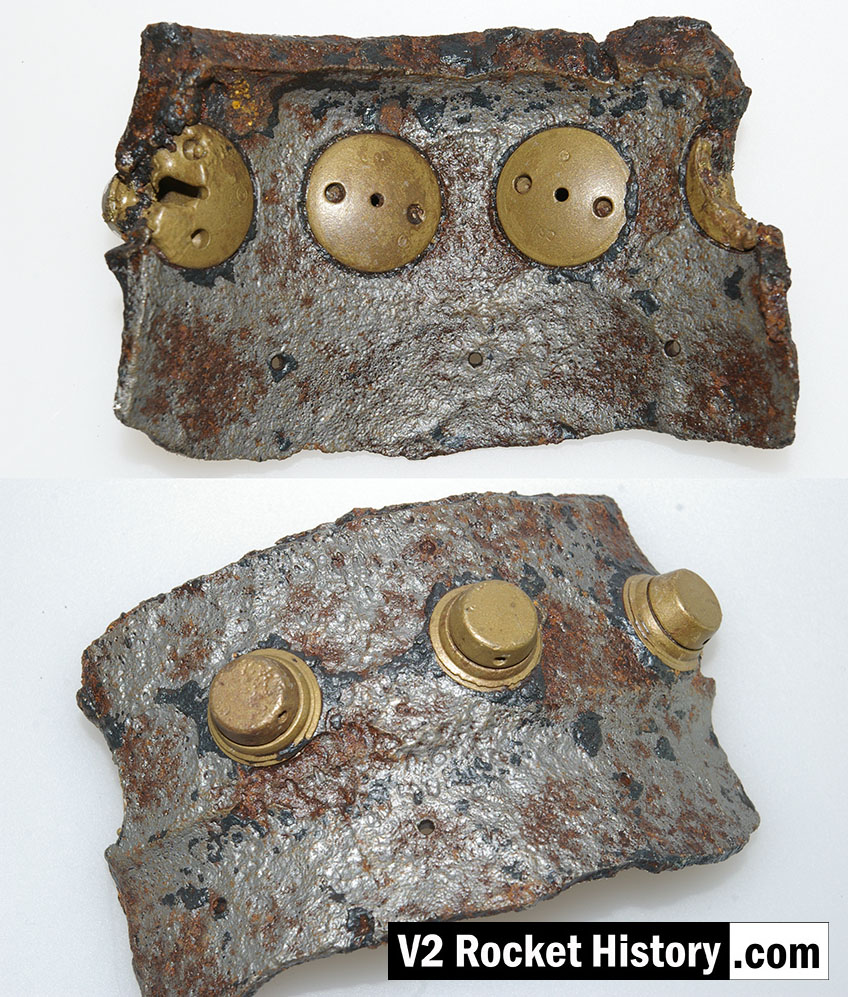
Photo shows a small section of the burner cup with row A (2131E) fuel injector inserts with three row B drilled holes below. The two undamaged inserts carry the armament code ‘csl’. The relic was found near a workshop in the Development works Pennemünde. Slag from the cutting flame and damage to the inserts at both ends of the relic would indicate that the section was cut from a steel burner cup using a gas cutter (fuel and oxygen) for purposes unknown. V2RH collection image
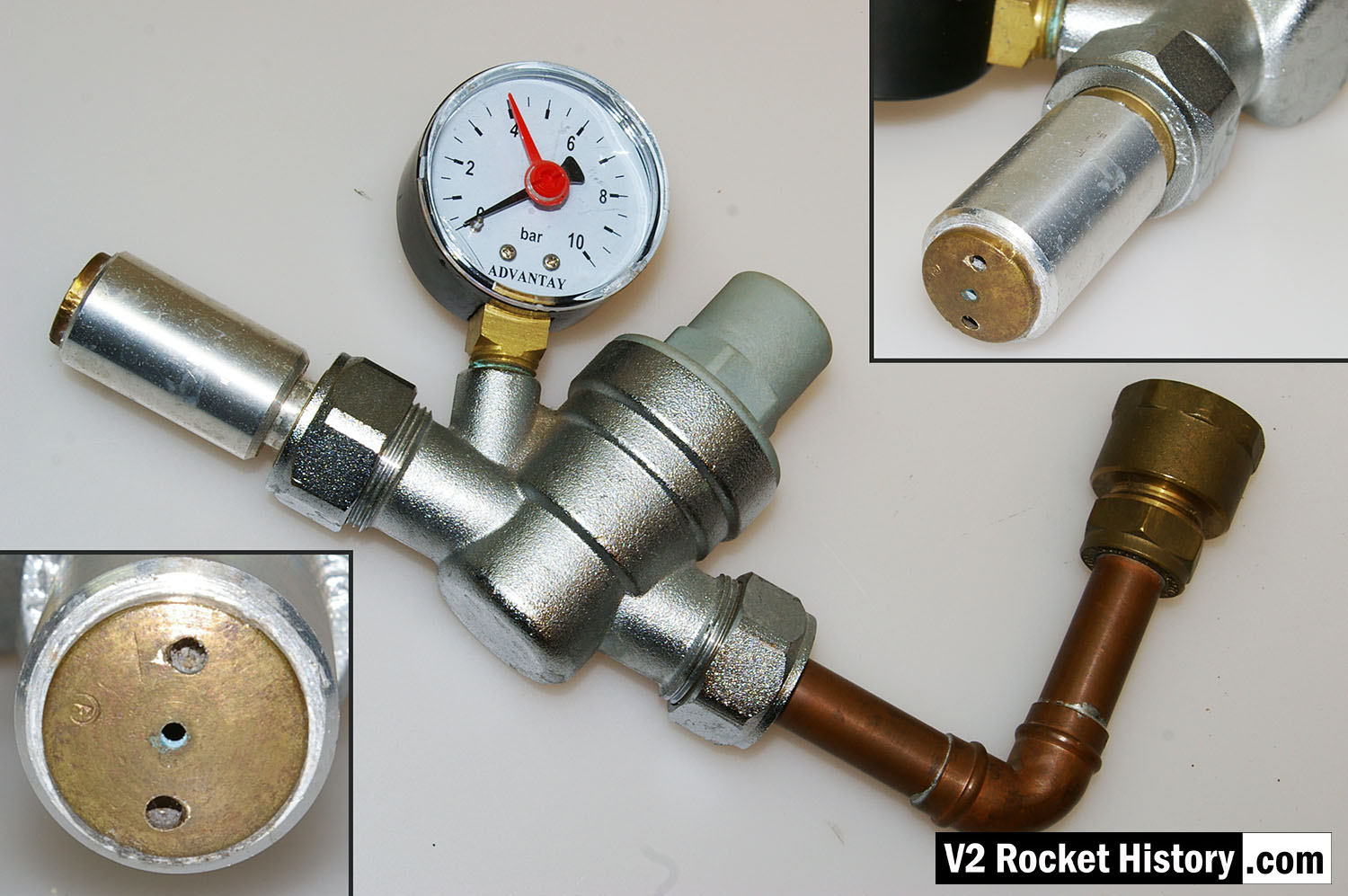
Single nozzle insert test rig used by V2 Rocket History to test spray shape and volume at supply pressures consistent with fuel pressures specified for the injector head of summer 1944. The test system features an adjustable pressure regulator and fluid pressure gauge. For test purposes the device was simply connected to a relatively high pressure mains water supply. And although water does not have the same viscosity of the 75% Ethenol to 25% water mix of the V2’s fuel it was considered close enough by the German technicians, who regularly used plain water as a substitute when testing issues related to furl flow rather than combustion. A 2131E fuel injector insert is shown installed in the holder at the front of the rig, but as the thread was the same on all inserts the nozzle can be changed for other models easily with aid of a pin spanner. See video for a demonstration of this simple test system.

Single nozzle insert test rig used by V2 Rocket History to test spray shape and volume at fluid supply pressures consistent with fuel pressures specified for the injector head of summer 1944. A 2131E fuel injector insert is installed in the holder at the front of the test rig, but as the thread was the same on all inserts the nozzle can be changed for other models easily with aid of a pin spanner. See video for a demonstration of this simple test system.
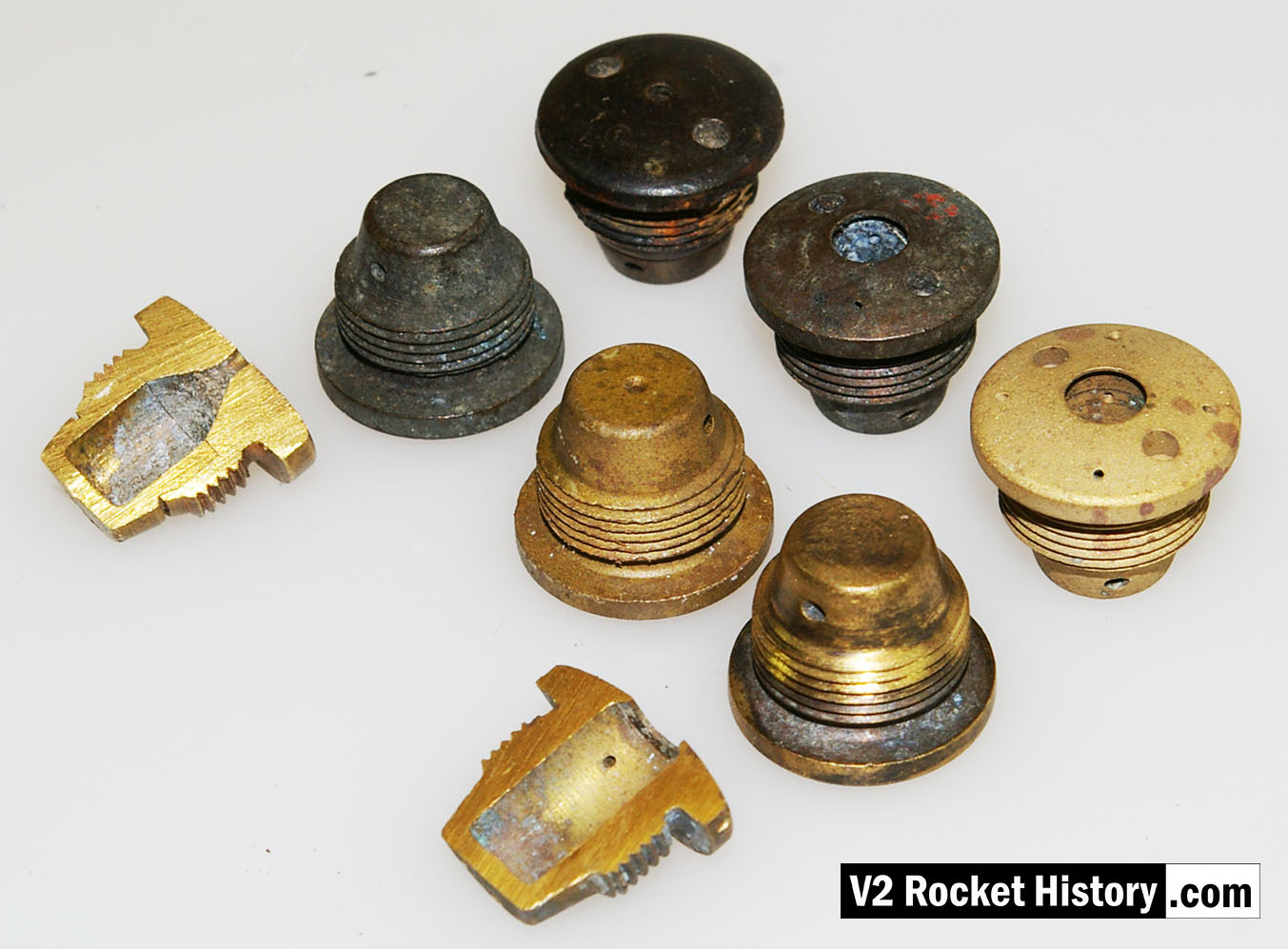
Fuel injector inserts for production series 18-pot injector head showing general shape and thread position. For further details see associated image. The lowermost insert have been halved to reveal the cavity shape, orifice edge, inlet and cooling apertures. V2RH image

Industrial magazine advert for Gustav Schlick printed in 1918 and showing graphic of steam boiler jets. The company, formed in 1902, had a wide expertise in all aspects of industrial spray technology and were able to steer the direction of fuel injector development along fruitful lines after they became consulting contractors to Dr Walter Thiel’s combustion research group in 1937.

Testing fuel injectors

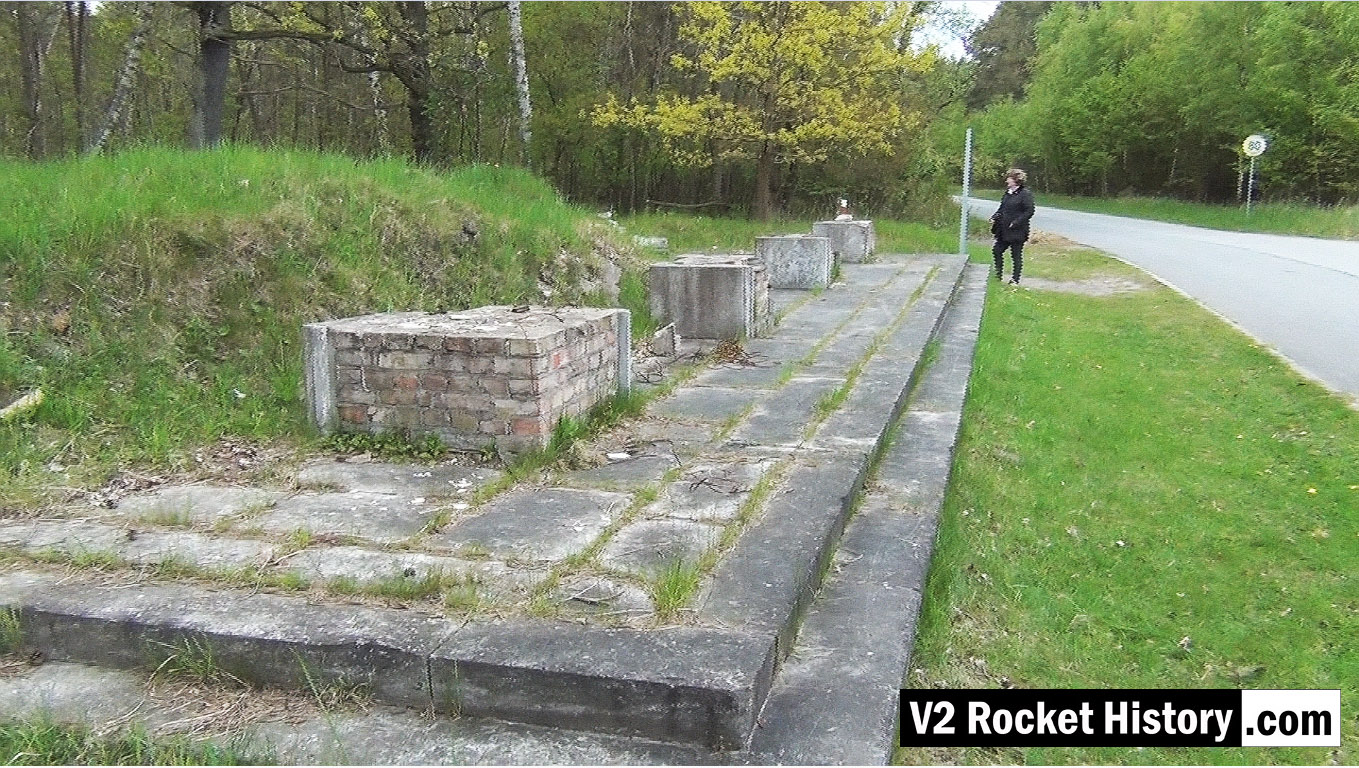
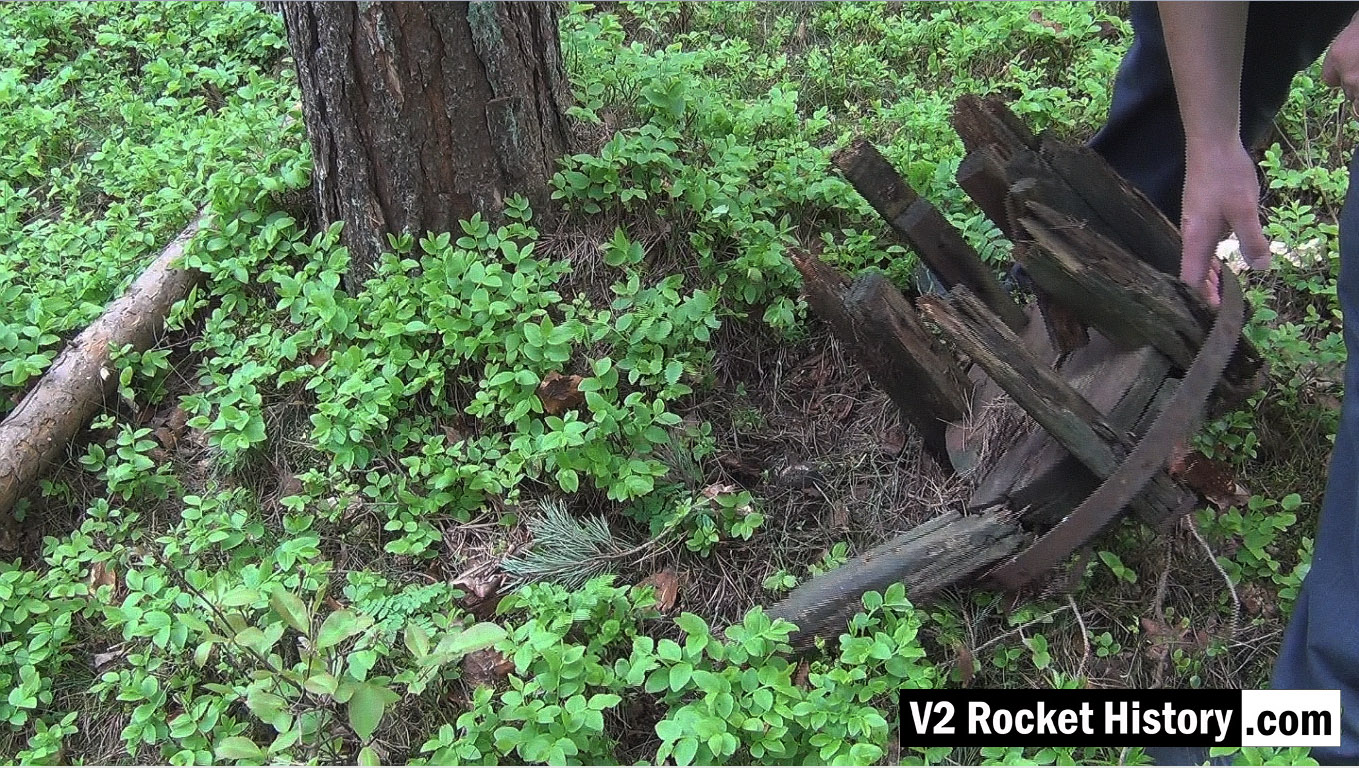
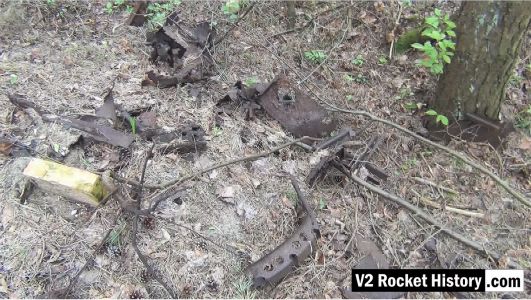
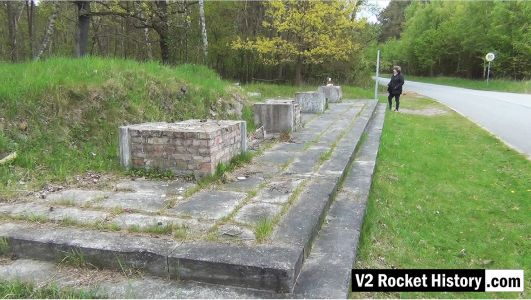
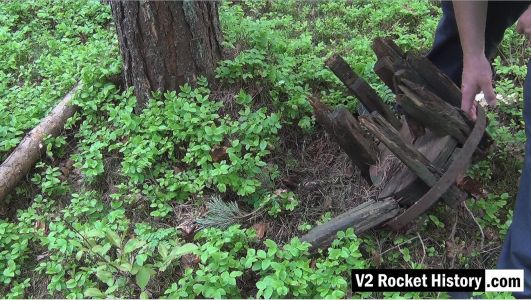
This picture shows a small debris field of steel fragments from the V2 missile 130m South-East of F1, and just 20m to the North East of the foundations of a small heat distribution building. Various body and frame parts can be seen and in the middle foreground a 350mm segment of curved missile body ring is visible. These parts have almost certainly been dug up and exposed by the action of metal detectorists. The metal fragments have been abandoned by their finders as they are perceived to have no financial value and hence are not worth removing from the site.